1.干刻不良
干膜蚀刻不良特征图片f
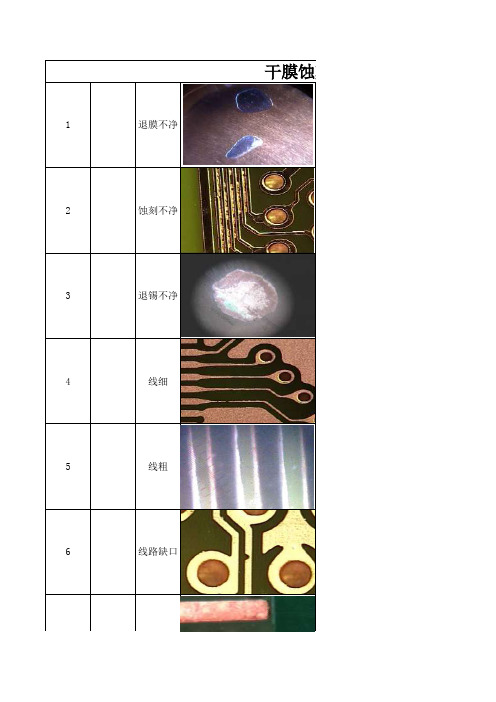
干膜蚀刻不1退膜不净2蚀刻不净退锡不净34线细5线粗6线路缺口7针孔78铜面污染针孔9线路锯齿1011干膜划伤短路线路划伤13焊前刮伤12膜碎返粘14干膜孔破15间距不足16蚀刻过度17焊盘残缺18线路残铜蚀刻不良特征分布1、喷嘴堵塞2、压力小3、药水浓度低4、速度快5、温度低1、清理喷嘴 2、检查调整压力 3、化验调整药水浓度 4、做退膜点确定调整速度 5、检测温度调整1、喷嘴堵塞2、压力小3、药水要求不在范围(比重)4、速度快5、温度低1、清理喷嘴 2、检查调整压力 3、化验调整药水比重 4、做退锡点(或首件)确定调整速度 5、检测温度调整1、喷嘴堵塞2、压力小3、药水要求不在范围(比重铜含量、氯离子、PH值)4、速度快5、温度低1、清理喷嘴 2、检查调整压力 3、化验调整药水浓度(比重铜含量、氯离子、PH值) 4、做蚀刻点(或首件)确定调整速度 5、检测温度调整1、压力大2、药水要求不在范围(比重铜含量、氯离子、PH值)3、速度慢4、温度高5、曝光不良1、、检查调整压力 2、化验调整药水浓度(比重铜含量、氯离子、PH 值) 3、做蚀刻点(或首件)确定调整速度 4、检测温度调整 5、制作曝光尺调整曝光能量1、喷嘴堵塞2、压力小3、药水要求不在范围(比重铜含量、氯离子、PH值)4、速度快5、温度低6、曝光不良1、清理喷嘴 2、检查调整压力 3、化验调整药水浓度(比重铜含量、氯离子、PH值) 4、做蚀刻点(或首件)确定调整速度 5、检测温度调整6、制作曝光尺调整曝光能量1、板面粘附异物显影不净2、显影膜碎反粘1、前处理、压膜按时保养清洁2、显影机按时保养清洁、使用合适匹配干膜压膜1、板面粘附异物显影不净2、显影膜碎反粘3、电镀不良1、前处理、压膜按时保养清洁2、显影机按时保养清洁、使用合适匹配干膜压膜3、检查电镀各项参数1、板面粘附异物显影不净2、显影膜碎反粘3、电镀不良1、前处理、压膜按时保养清洁2、显影机按时保养清洁、使用合适匹配干膜压膜3、检查电镀各项参数1、板面粘附异物显影不净2、显影后清洗不净1、前处理、压膜按时保养清洁2、显影机按时保养清洁3、转运放板工具按时清洁1、人员操作取拿搬运划伤线路2、工具不良造成划伤线路1、要求轻拿轻放,搬运不可拖拉、丢摔板 2、及时处理工具1、退膜温度高、速度慢2、退膜浓度高3、蚀刻温度高4、药水要求不在范围(比重铜含量、氯离子、PH 值)5、显影过度1、检测温度、调整速度 2、化验分析药水调整药水 3、检测温度调整4、化验调整药水浓度(比重铜含量、氯离子、PH值) 5、制作显影点调整速度1、人员操作取拿搬运划伤线路2、工具不良造成划伤线路1、要求轻拿轻放,搬运不可拖拉、丢摔板 2、及时处理工具1、喷嘴堵塞2、压力小3、药水浓度低4、速度快5、温度低6、水洗不净1、清理喷嘴 2、检查调整压力 3、化验调整药水浓度 4、做退膜点确定调整速度 5、检测温度调整 6、清洗更换水洗1、人员操作取拿搬运划伤线路2、工具不良造成划伤线路1、要求轻拿轻放,搬运不可拖拉、丢摔板 2、及时处理工具对位偏温湿度、更改底片 3、使用放大镜检查1、钻孔偏2、底片涨缩3、人员对位偏1、测量校正钻孔精度 2、管控调整温湿度、更改底片 3、使用放大镜检查1、喷嘴堵塞2、压力小3、药水要求不在范围(比重铜含量、氯离子、PH值)4、速度快5、温度低6、曝光不良1、清理喷嘴 2、检查调整压力 3、化验调整药水浓度(比重铜含量、氯离子、PH值) 4、做蚀刻点(或首件)确定调整速度 5、检测温度调整6、制作曝光尺调整曝光能量1、喷嘴堵塞2、压力小3、药水浓度低4、速度快5、温度低6、水洗不净1、清理喷嘴2、检查调整压力3、化验调整药水浓度4、做退膜点确定调整速度5、检测温度调整6、清洗更换水洗1、清理喷嘴2、检查调整压力3、化验调整药水浓度(比重铜含量、氯离子、PH值)4、做蚀刻点(或首件)确定调整速度5、检测温度调整6、制作曝光尺调整曝光能量7、调整退膜各项参数1、压力大2、药水要求不在范围(比重铜含量、氯离子、PH值)3、速度慢4、温度高5、曝光不良1、喷嘴堵塞 2、压力小 3、药水要求不在范围(比重铜含量、氯离子、PH值) 4、速度快 5、温度低6、曝光不良7、退膜不净1、、检查调整压力2、化验调整药水浓度(比重铜含量、氯离子、PH 值)3、做蚀刻点(或首件)确定调整速度4、检测温度调整5、制作曝光尺调整曝光能量。
常见的不良现象及解决方案

涂料不适用底漆 溶剂挥发不完全 固化不切底
更换相应的面漆 提高IR温度,延长流平时间,减少膜厚 增强UV能量
2.呈颗粒现象
原因: 涂料中颗粒 对策:用500目以上过滤或更换更好的涂料
镀膜后稍冷立即喷面漆 检查空气净化系统,达到标准要求 镀膜后放置时间 太久被污染 压缩空气和环境中灰尘
真空电镀常见外观不良及解决对策
Date: June 17th.2011 Editor: Jian Wu
----仅供参考!
底漆异常问题分析及改善
1.呈附着不良:(底材、漆膜、镀层之间的附着力不好而导致涂层脱落) 2.呈干燥不良现象(涂料固化不完全出现发白或发彩的现象) 3.呈针孔现象(化学物质挥发或底材与涂料之间的相应力差异产生) 4.呈彩虹现象(镀层膜产生相对移动) 5.呈缩针孔现象(漆膜表面出现火山口现象) 6.呈颗粒现象 7呈白雾现象 8.呈咬底现象(工件边缘或局部呈粗皮哑白现象) 9.呈桔皮现象
3.呈针孔现象(化学物质挥发或底材与涂料之间的相应力差异产生)
原因: 底涂后IR温度过高 基材表面不清洁 底漆溶剂挥发不完全 对策:IR温度设定不超过80度 彻底清洁基材表面脏污 提高IR温度,延长流平时间,减少膜厚
4.呈彩虹现象(镀层膜产生相对移动)
原因: 涂层过厚,内部干燥不完全 对策:调整底漆膜厚,使底涂固化彻底 底漆干燥不完全 底漆被面漆溶剂所溶解 底漆的流平不好 提高IR温度及UV能量 降低面漆IR温度或调整面漆的溶剂熔点性 改善底漆流平 对策:用超声波清洗或化学剂处理 清洁喷枪,空气管道 添加适量助剂或更换涂料 检查油水分离器,并清洁干净
2.呈干燥不良现象(涂料固化不完全出现发白或发彩的现象)
二氧化硅干刻选择比
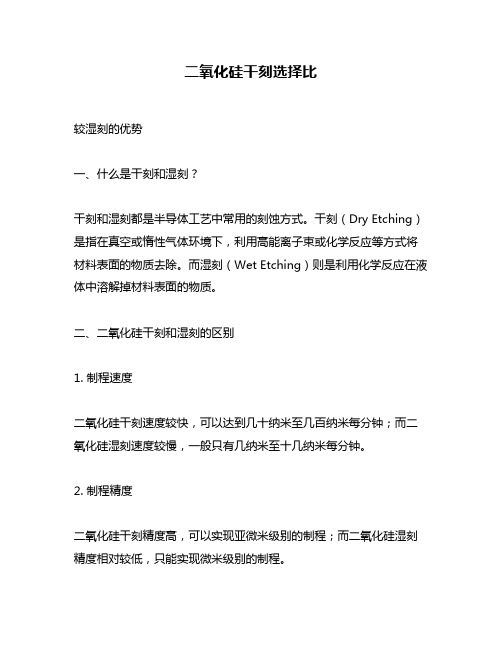
二氧化硅干刻选择比较湿刻的优势一、什么是干刻和湿刻?干刻和湿刻都是半导体工艺中常用的刻蚀方式。
干刻(Dry Etching)是指在真空或惰性气体环境下,利用高能离子束或化学反应等方式将材料表面的物质去除。
而湿刻(Wet Etching)则是利用化学反应在液体中溶解掉材料表面的物质。
二、二氧化硅干刻和湿刻的区别1. 制程速度二氧化硅干刻速度较快,可以达到几十纳米至几百纳米每分钟;而二氧化硅湿刻速度较慢,一般只有几纳米至十几纳米每分钟。
2. 制程精度二氧化硅干刻精度高,可以实现亚微米级别的制程;而二氧化硅湿刻精度相对较低,只能实现微米级别的制程。
3. 制程复杂度二氧化硅干刻需要更复杂的设备和工艺流程,成本也更高;而二氧化硅湿刻则相对简单,设备和工艺流程也较为简单,成本相对较低。
三、二氧化硅干刻选择比较湿刻的优势1. 制程速度快二氧化硅干刻速度快,可以大大缩短制程时间。
这对于半导体工艺来说非常重要,因为制程时间的缩短可以提高生产效率和降低成本。
2. 制程精度高二氧化硅干刻精度高,可以实现亚微米级别的制程。
这对于一些需要高精度加工的应用来说非常重要,如MEMS器件、微纳加工等。
3. 制程可控性好二氧化硅干刻可以通过调节离子束能量、功率等参数来控制刻蚀深度和形状。
这样可以实现更加精细的制程控制,从而提高产品质量和稳定性。
4. 制程兼容性强二氧化硅干刻可以与其他半导体工艺步骤兼容,如光刻、蒸镀等。
这样可以实现更加完整的工艺流程,并且不会影响其他步骤的质量和稳定性。
5. 环保性好二氧化硅干刻不需要使用任何液体溶剂,不会产生废水和废气等污染物。
这对于环保和可持续发展来说非常重要。
四、结论总的来说,二氧化硅干刻相比较湿刻具有制程速度快、制程精度高、制程可控性好、制程兼容性强、环保性好等优势。
但是,干刻设备和工艺流程更加复杂,成本也更高。
因此,在选择刻蚀方式时需要根据具体应用需求和经济效益进行权衡。
不良品看板精选文档

不 良 处 放 大
不良造成原因
1.底座有脏污(如图四) 2.底座面不平(如图五) 3.来料厚度不均 4.砂轮棒尺寸错误
3.擦架手法不正确,造成 3.产品轻拿轻放,垂直擦架,
产品碰撞(如图十)
一步放到位
4.清洗架未调好,造成产 品倒塌(如图十)
5.指甲过长,操作过程中 易与产品接触(如图八)
4.调试清洗架时检查螺丝是 否有滑丝,架条间距是否 合适
5.勤剪指甲并戴手指套作业
6.自检产品时,一手拿多 片玻璃(如图七)
7.多片产品堆叠在一起 (如图十五)
生产前先了解产品加工工艺和产品结构 不断提升自身的产品认识技能和品质意识 刀具:用废品打磨或更换新的; 生产前先了解产品加工工艺和产品结构
不 良 处 放 大
不良造成原因
预防措施
1.底座有脏污(如图四); 1.清理底座/重铣底座平面;
2.喷水节骨管加工时碰到 2.调试节骨管,保证在加工
玻璃表面(如图十三) 过程中不会碰到产品
预防措施
1.清理底座 2.重铣底座平面 3.检查来料厚度
6
不良种类——漏工艺
不良品图示
整 体 图 示
不 良 处 放 大
不良造成原因
1.断刀(如图十六) 2.调机产品未按要求放 入废品盒(如图九) 3.未经过加工便放入已 加工产品(图十二) 4.产品未加工完便暂停 取出 5.已加工、未加工未区 分(图十二) 6.自检产品不到位 7.对产品工艺和结构不 了解
干刻蚀对于不同负载效应造成选择比差异导致的缺陷分析与解决方案

随着工艺尺寸的逐渐缩小,不同的薄膜材质和结构使得干法刻蚀的制程的复杂性和工艺 难度大大提高。对于干法刻蚀的制程的四大研究对象的深入研究和探讨对进入纳米级的微电 子工艺显得越来越重要。然而负载效应的机理研究要基于其他三个研究对象。让我们先从干 法刻蚀的非等向蚀刻性,刻蚀率和选择比的研究来引出负载效应的成因。
作者简介: 赵弘鑫:男,1978 年 11 月出生,吉林人,上海交通大学硕士研究生,中芯国际集成电路制 造(上海)有限公司,Line C MFG Photo/Etch Section Manager. 程秀兰,女,1971 年 12 月出生,重庆市人,上海交通大学微电子学与固体电子学博士,上 海交通大学微电子学院副教授,主要研究方向:先进半导体器件与工艺技术、先进封装结构 设计与制造技术。
摘 要: 在半导体制造工艺的干法刻蚀(Dry Etching)中,对于刻蚀薄膜表面面积大小的差 异性会造成负载效应(Loading effect)。然而这种负载效应影响到干刻蚀的蚀刻率(Etch Rate) 和选择比(Selectivity)而在产品上出现严重的缺陷。本文阐述了负载效应的基本原理和造成选 择比差异性的成因以及对于由此产生产品缺陷的具体解决方案。 关键词:半导体制造, 干法刻蚀, 负载效应, 选择比, 缺陷 中图分类号:TN4; 文献标识码:B
Dry Etching Loading Effect Analysis and Solve Methods
Zhao hongxin1,2, Cheng Xiulan1
1Institute of Microelectronics, Shanghai JiaoTong University, Shanghai (200030) 2Semiconductor Manufacture International Corporation (Shanghai) LineC MFG, Shanghai
各工序不良品种类及排除方法
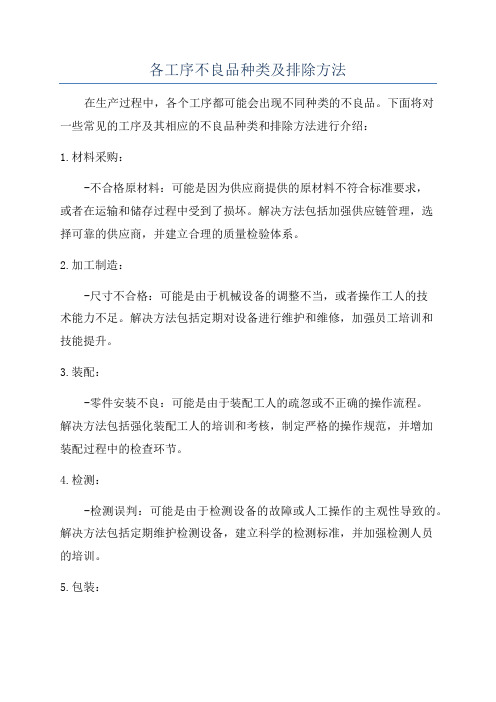
各工序不良品种类及排除方法在生产过程中,各个工序都可能会出现不同种类的不良品。
下面将对一些常见的工序及其相应的不良品种类和排除方法进行介绍:1.材料采购:-不合格原材料:可能是因为供应商提供的原材料不符合标准要求,或者在运输和储存过程中受到了损坏。
解决方法包括加强供应链管理,选择可靠的供应商,并建立合理的质量检验体系。
2.加工制造:-尺寸不合格:可能是由于机械设备的调整不当,或者操作工人的技术能力不足。
解决方法包括定期对设备进行维护和维修,加强员工培训和技能提升。
3.装配:-零件安装不良:可能是由于装配工人的疏忽或不正确的操作流程。
解决方法包括强化装配工人的培训和考核,制定严格的操作规范,并增加装配过程中的检查环节。
4.检测:-检测误判:可能是由于检测设备的故障或人工操作的主观性导致的。
解决方法包括定期维护检测设备,建立科学的检测标准,并加强检测人员的培训。
5.包装:-包装破损:可能是由于包装材料的质量不好或者操作工人的不慎导致的。
解决方法包括选择高质量的包装材料,加强包装工人的培训和操作规范。
6.运输:-运输损坏:可能是由于运输工具的不稳定或者操作工人的不慎导致的。
解决方法包括加强运输工具的维护和改进,制定严格的运输操作流程,并对运输工人进行培训。
7.售后:-安装不良:可能是由于安装人员对产品使用方法和安装流程不熟悉导致的。
解决方法包括加强售后服务团队的培训和技术支持,建立完善的售后服务流程。
8.用户使用:-操作不当:可能是由于用户对产品使用方法不了解或者不按照操作指南使用导致的。
解决方法包括加强产品宣传和用户教育,提供详细的产品使用说明书和常见问题解答。
针对不良品种类,企业可以采取以下排除方法:1.强化供应链管理,选择可靠的供应商,并建立严格的质量检验体系。
2.加强设备维护和维修,定期对设备进行检查和调整。
3.增加员工培训和技能提升,确保操作工人能够正确操作和调整设备。
4.制定严格的操作规范,并加强对操作流程的监控和检查。
志圣干刻故障维修手册

PRS基本故障与排除1、PRS 故障讯息2、故障原因排除故障原因与排除1.FAULT ! EXHAUST FAIL ! 故障!排气失败!原因: 早期PRS于PUNP排气端有加设EXHAUST (排气)负(背)压侦测,该负(背)压需小于-0.02torr,该读值可由PUMP排气端SMC gauge上读取。
(目前该设置均已取消)处理:1.确认PUMP排气端是否设有负压侦测器,若有则检查读值是否正确,确认厂务EXHAUST 是否开启,调整gauge设定测试gauge是否正常。
2.进入计算机程序系统,最高权限中『组件组合』项目,确认EXHAUST单元是否被勾选。
2.Fault : Total process time is large than setting time about 10 second故障!总制程时间大于设定时间约10秒。
原因:因系统警告或软件BUG造成制程动作延迟。
处理:进行软件修正BUG。
3.Fault : 测漏---- 不合格!原因: 进行系统测漏程序,其结果超出设定时发出。
处理: 1.重新确认测漏条件,抽气时间是否设定太短,漏率标准是否太高。
2.检查腔体内是否清洁,O-ring是否破损。
4.FAULT! ,ICP_RF Reflective power is large than setting value故障!射频反射功率大于设定值原因: 射频反射功率达到程序项目内设定之警告值。
处理: 1.腔体污染,请清洁腔体。
2.程序项目内参数异常,请检查a. RF Reflective power设定百分比过低! b.程序间延迟时间(delay time)过短! c.子程序顺序错误3.RF cable松脱、断线或短路。
4.Matcher box matching异常,Coil铜线松脱、断线、短路或氧化。
5.FAULT! ,ICP_RF's Forward power is large than setting value故障!射频输入功率大于设定值原因: 射频输入功率达到程序项目内设定之警告值。
常见印刷术语及印刷不良原因

常见印刷术语及印刷不良原因一. 印刷---印刷是将印版表面图象的印刷油墨转移到要进行图象复制的物体表面上的技术,它是以光学,机械,化工和电子技术为基础的一门综合性科学.平版印刷是利用油,水不相溶的原理,它是由给纸机构,印刷机构,供墨机构,湿润机构,收纸机构五大部份组成.二. 印刷术语1. 纸鸡(侧规):输纸台上,在驱动面或操作面一侧于前规协调对纸张进行推,拉动作,使纸张作侧向定位的设备.2. 牙口:刀纸牙咬住纸张进行压印传递的一边.3. 自反版:印完单面后,印单作左右反转,印版保持原版再印另一面,共用牙口的印刷版.4. 牙口反:印完单面后,印单作前后反转,印版不变,再印另一面牙口不共用的印刷方式.5. 正反版:牙口共用,正反面各有独立印刷版.6. 针位:前规与侧规的定位线.7. 出血位:为避免加工时因误差所产生的露白或歪斜等缺陷而在制版时设计的多余的色位(1-3mm).三. 印刷不良及原因.(一). 爆粉.---油墨粘度太大或纸张表面强度差而导致油墨将纸表面层剥篱而产生的白斑.(二). 粘花(过底):---油墨未干或堆压过重使印件之间互相粘贴而产生的斑痕现象.1. 喷粉效果不良.2. 油墨乾燥速度慢.3. 印刷纸张叠放太高.4. 油墨层太厚(油墨太大.5. 纸张吸水性太小.,油墨附著力差(三).颜色不对产生原因:1. 油墨流动性能不好.2. 墨辘未调好3. 墨辘不平4. 墨辘不干淨5. 湿润液供给不足6. 滚筒间压力不均匀.7. 纸张厚薄不均.8. 纸张上墨不良9. 油墨调色不均匀(2).颜色跟不上色稿1. 印墨厚薄未调好2. 油墨颜色偏差3. 纸张颜色偏差4. 晒版时间偏差5. 色序不当6. 套印不准7. 网点不同8. 润湿液调节不当9. 压力未调好10. 色稿有问题(双勾). (3).色差(一批产品中出现多种) 1. 机器老化(双钩)2. 洗胶布后行头纸未抹干淨3. 纸张起波浪4. 调墨不匀5. 机器性能不稳定6. 生产过程中调机7. 水干,水大8. 纸张颜色偏差(四).墨屎,纸毛.---因墨皮或纸毛堆积使油墨不能正常转移到纸上而产生斑块,小白圈现象.产生原因:1. 纸张掉粉,掉毛.2. 裁切边的纸张割裂粉抹.3. 在印机墨辘上两端的干印墨.4. 在印机水辘上两端的干印墨5. 印墨已在墨缸或木桶上面结皮,印墨转移印机之前,所有结皮未除去.6. 旧印墨结皮后处理不当混入.7. 印墨中杂质.8. 湿润液中杂块.(五). 凹胶布.---因胶布衬垫不均匀,某处凹陷,使压印时没有足够的压力致使橡皮上的油墨不能完全转移到纸上图文不清晰.(六). 粘胶布.---由于纸质强度不够,易破(撕)裂,在运转过程中被粘在胶布上,而产生的大块图像不著墨或墨层太厚.1. 由于油墨粘度太大,纸与墨的分离小于墨的粘度易使纸张被撕裂而产生粘胶布.2. 机器咬纸不稳定,使走纸不畅顺,导致粘胶布.(七).水干.---水量调控不当,产生水小不足以润湿印版,致使印版模糊导致印件脏污.产生原因:1. 水辘未落.2. 水辘可能变形.3. 没印刷水.4. 水辘调节不当.5. 印刷时水量过小.(八). 水大.---水量调不当,产生水大,使得某处墨色不鲜艳发白现象.(九).双勾.---因纸张伸缩变形或机械精密度原因使印迹产生重影或颜色偏.(十).鬼影.---墨位较大的实地版或网版,由于部份地方是空白的部份,墨辘上的墨没有转移而当其转移到图文部份时,其上墨量较大,而其他地方上墨均匀,则形成鬼影..(十一). 套印不正.1. 拼版不正.2. 叼纸牙磨损.3. 纸张的吸水性能不稳定,吸水后伸长不一.4. 机器性能不稳定.5. 摆动牙位置不当.6. 套印机械调节不当.7. 滚筒包衬不符合要求.8. 纸张含水量不匀,四边起波浪或紧边造成纸张伸缩或皱折.9. 印版供水量过大,使纸张伸长.10. 纸张丝绺不符合印刷要求.11. 环境,温度的改变,造成纸张伸缩.(十二). 重影.1. 滚筒衬垫没垫好..2. 因纸张伸长不一,导致套印不正而产生.3. 纸起波浪.4. 机器故障.5. 纸张厚薄不匀.(十三).擦花,打花.1. 由于收纸部件调校不当或因纸轻薄使纸张印件在收纸过程中纸于纸相互磨擦造成擦花.2. 工人拿纸过程中,拿纸方法不当产生.3. 排骨位打花.4. 纸张吸凤挚未调好.5. 纸张太细,太硬所致.6. 印反面时炮打花.7. 印刷纸机位擦花.8. 收纸时两张间擦花.9. 刮墨屎时打花.10. 抽纸不当擦花.(十四).喷粉大.1. 喷粉嘴故障,导致喷粉不匀,堆积.2. 因排风扇调节不当吹风不匀,导致喷粉扩散不匀,产生喷粉大.3. 喷粉剂量大.(十五).爆粉,纸毛.1. 因纸施胶度不够,纸质疏松不平滑,印刷时易起毛,爆粉,粘于印版或胶布上,进而转移到印件上形成纸毛.2. 因纸张表面强度不够,易使纸起毛,粘结到印版或胶布上,进而转移到印件上形成纸毛.(十六).滴粉.---由于机头喷粉堆积未清理乾净,而掉于印件产生.(十七).阴阳色.1. 晒版时因晒版机吸气不均匀造成菲林于印版接触不均匀,使得网点密度有变.2. 显影时显影液搅拌不匀,导致显影液浓度不匀,使得印版显影效果不一致.3. 印刷时因多处水墨量调控不匀,引起供墨量不同.(十八).版脏.1. 晒版时菲林(原版)未清洗乾净留有污渍.2. 晒版机玻璃未清洗乾净,留有污渍,杂质.3. 印刷时因杂质纸毛等粘贴于印版上.(十九).字崩.1. 植字时因针头灵敏度不稳定,导致字断线引起.2. 晒版时因灰尘等杂质落于菲林(在字上).3. 修版时不小心涂掉某处,使字断线.4. 纸毛(片)粘于印版上某处使不能正常转移导致.5. 胶布被压坏,凹进去导致油墨转移不到.(二十).版花.1. 复制菲林时刮花,晒版时未注意印版版花.2. 停机打墨屎或擦印版时因锋利器刮花印版而致.(二十一).缺字.1. 因电脑植字时漏植.2. 显影后,修版时不小心涂掉.3. 胶布被压坏.(二十二).墨杠.(墨辘痕)1. 因机器性能稳定,水辊于印版压力调节当(不均衡)影响某处供水量;2. 因机器性能不稳定,墨辊于印版压力调节当(不均衡)影响某处供墨量.(二十三).滴水.1. 水路调控不当;2. 水量大.3. 水斗空间形成的水蒸汽溶解,增加水量形成.(二十四). 墨杠.1. 水辘污脏.2. 橡皮布及水胶绒老化.3. 滚筒衬垫不当.4. 印刷压力过大.5. 滚筒间压力不均匀.6. 打墨屎所致.关注“印刷微盟”成员—汲取价值讯息。
影响印品质量的若干情况

害 最直 接 。 尤其 套 印 的产 品 ,一 旦 出现 上 下规 矩紊
乱 ,就 会 造 成 严 重 的 质 量 问题 和 浪 费 。 其 原 因 分 为
若 干种 ,归纳 起来 有 飞达 部 位 引 起 的 ,有输 纸 部位 引 起 的 , 有 侧 规 引 起 的 ,有 滚 筒 部 位 引 起 的 , 也 有
界 工 艺 技 术
2 1 .3 01
影响 质 量的若 干情况 印品
山 东人 民印刷 厂 苗 茵葆
过 程 中 发 生 重 叠 。 导 致 不 良 印 品 质 量 的 发 生 , 其 原
1 掉版
掉 版 是 在 印 刷 过 程 中 经 常 出 现 的 一 种 情 况 , 由
于 印 版 板 材 质 量 不 好 ,或 晒 版 工 序 对 印 版 烘 烤 的 时
摆 牙 和 压 印 牙 等 部 位 引 起 的 。 如 果 是 双 面 机 , 橡 皮
4 装 错 版
装 错 版 是 由于 操 作 人 员 麻 痹 大 意 , 而 人 为 导 致
印品质 量 事 故 的现 象 之 一 。 尤 其双 色机 在 换 版 时 ,
滚 筒 咬 牙 咬 纸 不 合 适 ,也 会 造 成 规 矩 不 好 。
2 轧 橡 皮
轧 橡 皮 是 在 印 刷 时 ,由于 滚筒 内进 入 多 张 纸 、
墨 ,更 容 易 出 现 背 面 粘 脏 。 严 重 的 会 造 成 印 品 报 废 。
7
色相 不 符
色相 不 符是指 印出的产 品色相 不 符合原 样标准 。
破 纸 , 或 掉 入 咬 纸 牙 牙 簧 , 递 纸 嘴 卡 子 以 及 其 它 异
德国药品不良反应损害救济制度简介
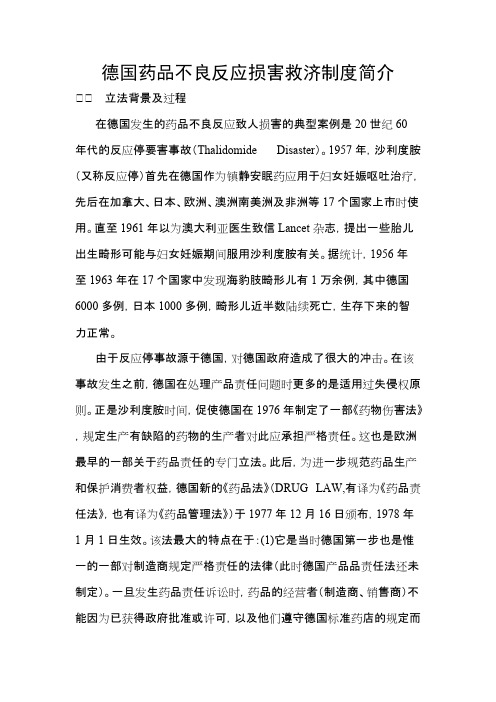
德国药品不良反应损害救济制度简介、、立法背景及过程在德国发生的药品不良反应致人损害的典型案例是20世纪60年代的反应停要害事故(Thalidomide Disaster)。
1957年,沙利度胺(又称反应停)首先在德国作为镇静安眠药应用于妇女妊娠呕吐治疗,先后在加拿大、日本、欧洲、澳洲南美洲及非洲等17个国家上市时使用。
直至1961年以为澳大利亚医生致信Lancet杂志,提出一些胎儿出生畸形可能与妇女妊娠期间服用沙利度胺有关。
据统计,1956年至1963年在17个国家中发现海豹肢畸形儿有1万余例,其中德国6000多例,日本1000多例,畸形儿近半数陆续死亡,生存下来的智力正常。
由于反应停事故源于德国,对德国政府造成了很大的冲击。
在该事故发生之前,德国在处理产品责任问题时更多的是适用过失侵权原则。
正是沙利度胺时间,促使德国在1976年制定了一部《药物伤害法》,规定生产有缺陷的药物的生产者对此应承担严格责任。
这也是欧洲最早的一部关于药品责任的专门立法。
此后,为进一步规范药品生产和保护消费者权益,德国新的《药品法》(DRUG LAW,有译为《药品责任法》,也有译为《药品管理法》)于1977年12月16日颁布,1978年1月1日生效。
该法最大的特点在于:(1)它是当时德国第一步也是惟一的一部对制造商规定严格责任的法律(此时德国产品品责任法还未制定)。
一旦发生药品责任诉讼时,药品的经营者(制造商、销售商)不能因为已获得政府批准或许可,以及他们遵守德国标准药店的规定而影响其承担民事或刑事责任。
换言之,即使厂商生产的或销售的药品已获政府批准或许可,而且符合德国标准药店的规定,只要服用这种药品的消费者能证明缺陷、伤害以及因果关系的存在,就可以使生产者和消费者承担损害赔偿责任。
(2)该法是德国产品责任法的特别法。
《德国有缺陷产品责任法》第十五条第一款规定:“由于使用一种确定人用的药品,而该药品是在《药品法》的施行内发给消费者并且已获得发放许可或以法令免除许可者,使用人死亡或其身体或健康受到伤害时,不适用《产品责任法》之规定”,即德国药品法对产品责任法有排除作用。
严重药物不良反应监测与报告管理制度

严重药物不良反应监测与报告管理制度一、背景与目的随着医疗水平的提高,药物在临床治疗中的作用越来越紧要。
然而,药物使用过程中也存在肯定的风险与不良反应。
为了及时发现、监测和报告药物的严重不良反应,确保患者的用药安全,维护医院药品管理的科学性与规范性,特订立本《严重药物不良反应监测与报告管理制度》。
二、适用范围本制度适用于本医院全部药品使用人员,包含临床医生、药师、护士等。
三、定义与分类1.严重药物不良反应:指在药物使用过程中,显现可能危及患者生命、健康或需要立刻干涉的不良反应,包含但不限于过敏反应、药物中毒等。
2.药物不良反应的监测与报告:指对患者使用药物后可能显现的不良反应进行监测和及时报告,以便及时采取相应的措施,确保患者的用药安全。
四、监测与报告责任1.医疗机构负责人:负责订立严重药物不良反应监测与报告管理制度,并进行相关政策法规的宣传与培训。
2.临床医生:在开展临床工作中,负责监测患者的用药情况和不良反应,及时发现严重不良反应,并及时采取相应措施并报告。
3.药师:负责药品的配置、药物治疗方案的订立与引导,并对患者用药过程进行监测,发现严重药物不良反应应及时报告。
4.护士:负责对患者用药情况进行记录,及时发现并报告严重不良反应,帮助医生和药师进行处理。
五、监测与报告流程1.监测流程(1)临床医生在患者用药过程中,要认真询问患者的过敏史、用药史等信息,并进行合理的用药选择和剂量调整。
(2)药师应依照医嘱准确配置药物,并对患者用药情况进行监测,重点关注患者是否显现不良反应。
(3)护士要依照医嘱准确给药,并在用药过程中注意察看患者的不良反应情形,及时记录。
2.报告流程(1)临床医生发现患者显现严重药物不良反应时,应立刻停止药物使用,并及时采取相应的抢救措施。
(2)医生应立刻向相关部门报告,包含药品管理部门和质控部门,报告内容包含患者基本信息、药物名称、用药情况及不良反应症状等认真信息。
(3)相关部门应及时进行调审核实,并订立相应的处理方案,以确保患者的用药安全。
干法刻蚀.
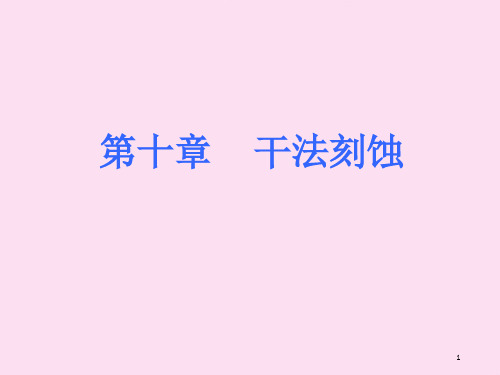
11Biblioteka 法刻蚀• 干法刻蚀的优点(与湿法刻蚀比) 1. 刻蚀剖面各向异性,非常好的侧壁剖面控制 2.最小的光刻胶脱落或粘附问题 3. 好的片内、片间、批次间的刻蚀均匀性 4. 化学品使用费用低
• 干法刻蚀的缺点(与湿法刻蚀比) 1. 对下层材料的刻蚀选择比较差 2. 等离子体诱导损伤 3. 设备昂贵
的目的。它是在硅片上复制图形的最后主要图形转移工艺。
刻蚀工艺分类:干法刻蚀和湿法刻蚀 ✓干法刻蚀:通过气体放电,使刻蚀气体分解、电离,由产生
的活性基及离子对基板进行刻蚀的工艺过程;刻蚀精度:亚 微米。 ✓湿法刻蚀:把要腐蚀的硅片放在化学腐蚀液里去除表面层材 料的工艺过程;刻蚀精度:大于3微米。
3
刻蚀参数
相关刻蚀参数: • 刻蚀速率 • 刻蚀剖面 • 刻蚀偏差 • 选择比 • 均匀性 • 聚合物 • 等离子体诱导损伤
4
刻蚀参数
1. 刻蚀速率
• 刻蚀速率是指刻蚀过程中去除硅片表面不需要的材料的速度。 刻蚀速率=ΔT/t(Å/min) 其中,ΔT=去掉的材料厚度(Å或μm) t=刻蚀所用时间(min)
20
反应离子刻蚀
➢ RIE (Reactive Ion Etch)机理
①进入真空反应室的刻蚀气体在射频电场的作用下分解电离形成等离 子体,等离子体由高能电子、反应正离子、自由基、反应原子或原 子团组成。
②反应室被设计成射频电场垂直于被刻蚀样片表面且射频电源电极 (称为阴极)的面积小于接地电极(称为阳极)的面积时,在系统 的电源电极上产生一个较大的自偏置电场。
15
干法刻蚀的机制
等离子体干法刻蚀机理及刻蚀参数对比
刻蚀参数 刻蚀机理 侧壁剖面
物理刻蚀 RF场垂直片面 物理离子溅射
干刻工艺的蚀刻原理

干刻工艺的蚀刻原理
为了制造出更复杂、更精细的图形,一种简便的方法是将掩模版上的图形转移到光敏化学胶液中。
这种胶是用一种极易分解的化学品配制而成,其配方是:
(1)2~4g/l NaOH (或Na2CO3);
(2)5~10g/l双氧水(或HNO3);
(3)1~3g/l三氯化铁(或三氯化铁);
(4)3~5g/l二甲基亚砜;
(5)2~4g/l过氧化氢。
在上述配方中, NaOH、HNO3和三氯化铁均为易溶性试剂,它们在化学上均属阳离子,可与硅反应形成可溶性化合物,再用双氧水或HNO3把它们分解掉,然后把生成的气体通入装有双氧水和三氯化铁的反应釜中。
在这个过程中,由于双氧水和三氯化铁都具有很强的氧化性,当它们接触到被掩模版上的硅时,就会发生剧烈反应。
由于是在光敏化学胶液中进行的反应,反应速度很快,而且发生化学反应时所释放出的热量也很高。
—— 1 —1 —。
不合格特征分类表

3.根据使用条件有可能造成轻微人身事故的不良 4.将来可能造成重大缺点的不良。
1.不影响性能、机能、寿命等的不良。 2.稍微超过限度样品的伤、凹痕、间隙、段差、色调 、 脏污、及其他的不良。 3.混入了不影响性能、机能、寿命的异物。
事故 举例
1、气密性要求产品漏气。 2、配合尺寸NG,影响实配。
3、运转以及操作中,易触摸地方的锐利的锋口。 4、不良的零件。 5、显著的伤痕、变形等外观不良以及零件损坏。 6、会影响产品机能的表面异物。
不良品分类和缺点程度区分一览表
缺点项 项 目
重 大 缺 点(CR)
主 要 缺 点(MA)
轻 微 缺 点(MI)
定 义
1.机能停止、或相当于机能停止的性能不良。 1.在实际使用过程中没有特别障碍的不良。
2.损坏商品价值外观(功能)的不良。
2.根据使用条件不同,可能发生的轻微的性能不良
。
3.一般的外观不良。
1、一般的擦伤、凹痕、间隙、段差等的外观不良。 2、机能部分的未拧紧、松驰、忘钉螺钉。 3、不违反法规范围的
干膜蚀刻不良特征图片f
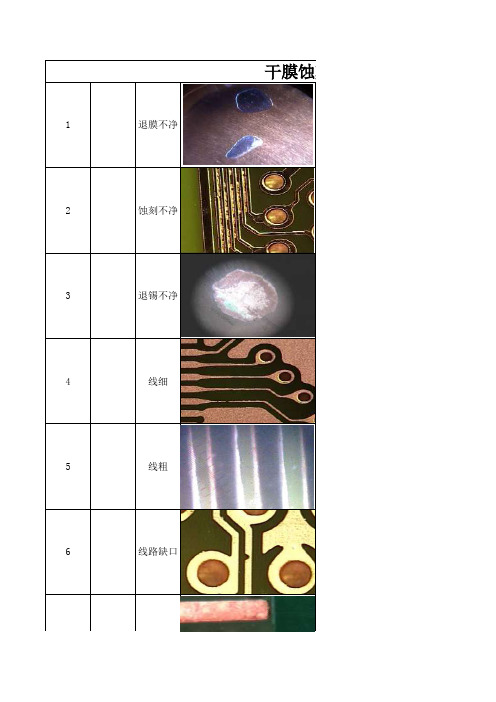
干膜蚀刻不1退膜不净2蚀刻不净退锡不净34线细5线粗6线路缺口7针孔78铜面污染针孔9线路锯齿1011干膜划伤短路线路划伤13焊前刮伤12膜碎返粘14干膜孔破15间距不足16蚀刻过度17焊盘残缺18线路残铜蚀刻不良特征分布1、喷嘴堵塞2、压力小3、药水浓度低4、速度快5、温度低1、清理喷嘴 2、检查调整压力 3、化验调整药水浓度 4、做退膜点确定调整速度 5、检测温度调整1、喷嘴堵塞2、压力小3、药水要求不在范围(比重)4、速度快5、温度低1、清理喷嘴 2、检查调整压力 3、化验调整药水比重 4、做退锡点(或首件)确定调整速度 5、检测温度调整1、喷嘴堵塞2、压力小3、药水要求不在范围(比重铜含量、氯离子、PH值)4、速度快5、温度低1、清理喷嘴 2、检查调整压力 3、化验调整药水浓度(比重铜含量、氯离子、PH值) 4、做蚀刻点(或首件)确定调整速度 5、检测温度调整1、压力大2、药水要求不在范围(比重铜含量、氯离子、PH值)3、速度慢4、温度高5、曝光不良1、、检查调整压力 2、化验调整药水浓度(比重铜含量、氯离子、PH 值) 3、做蚀刻点(或首件)确定调整速度 4、检测温度调整 5、制作曝光尺调整曝光能量1、喷嘴堵塞2、压力小3、药水要求不在范围(比重铜含量、氯离子、PH值)4、速度快5、温度低6、曝光不良1、清理喷嘴 2、检查调整压力 3、化验调整药水浓度(比重铜含量、氯离子、PH值) 4、做蚀刻点(或首件)确定调整速度 5、检测温度调整6、制作曝光尺调整曝光能量1、板面粘附异物显影不净2、显影膜碎反粘1、前处理、压膜按时保养清洁2、显影机按时保养清洁、使用合适匹配干膜压膜1、板面粘附异物显影不净2、显影膜碎反粘3、电镀不良1、前处理、压膜按时保养清洁2、显影机按时保养清洁、使用合适匹配干膜压膜3、检查电镀各项参数1、板面粘附异物显影不净2、显影膜碎反粘3、电镀不良1、前处理、压膜按时保养清洁2、显影机按时保养清洁、使用合适匹配干膜压膜3、检查电镀各项参数1、板面粘附异物显影不净2、显影后清洗不净1、前处理、压膜按时保养清洁2、显影机按时保养清洁3、转运放板工具按时清洁1、人员操作取拿搬运划伤线路2、工具不良造成划伤线路1、要求轻拿轻放,搬运不可拖拉、丢摔板 2、及时处理工具1、退膜温度高、速度慢2、退膜浓度高3、蚀刻温度高4、药水要求不在范围(比重铜含量、氯离子、PH 值)5、显影过度1、检测温度、调整速度 2、化验分析药水调整药水 3、检测温度调整4、化验调整药水浓度(比重铜含量、氯离子、PH值) 5、制作显影点调整速度1、人员操作取拿搬运划伤线路2、工具不良造成划伤线路1、要求轻拿轻放,搬运不可拖拉、丢摔板 2、及时处理工具1、喷嘴堵塞2、压力小3、药水浓度低4、速度快5、温度低6、水洗不净1、清理喷嘴 2、检查调整压力 3、化验调整药水浓度 4、做退膜点确定调整速度 5、检测温度调整 6、清洗更换水洗1、人员操作取拿搬运划伤线路2、工具不良造成划伤线路1、要求轻拿轻放,搬运不可拖拉、丢摔板 2、及时处理工具对位偏温湿度、更改底片 3、使用放大镜检查1、钻孔偏2、底片涨缩3、人员对位偏1、测量校正钻孔精度 2、管控调整温湿度、更改底片 3、使用放大镜检查1、喷嘴堵塞2、压力小3、药水要求不在范围(比重铜含量、氯离子、PH值)4、速度快5、温度低6、曝光不良1、清理喷嘴 2、检查调整压力 3、化验调整药水浓度(比重铜含量、氯离子、PH值) 4、做蚀刻点(或首件)确定调整速度 5、检测温度调整6、制作曝光尺调整曝光能量1、喷嘴堵塞2、压力小3、药水浓度低4、速度快5、温度低6、水洗不净1、清理喷嘴2、检查调整压力3、化验调整药水浓度4、做退膜点确定调整速度5、检测温度调整6、清洗更换水洗1、清理喷嘴2、检查调整压力3、化验调整药水浓度(比重铜含量、氯离子、PH值)4、做蚀刻点(或首件)确定调整速度5、检测温度调整6、制作曝光尺调整曝光能量7、调整退膜各项参数1、压力大2、药水要求不在范围(比重铜含量、氯离子、PH值)3、速度慢4、温度高5、曝光不良1、喷嘴堵塞 2、压力小 3、药水要求不在范围(比重铜含量、氯离子、PH值) 4、速度快 5、温度低6、曝光不良7、退膜不净1、、检查调整压力2、化验调整药水浓度(比重铜含量、氯离子、PH 值)3、做蚀刻点(或首件)确定调整速度4、检测温度调整5、制作曝光尺调整曝光能量。
产品不良分类

注射料成型的制件,在不良操作情况下,会出现不满、飞边、表面凹陷,尺寸变化等缺陷。
这些缺陷可能是模具设计,注射机台精度等造成,也可能是操作人员没有掌握好适当的工艺条件而造成。
因素错综复杂、变化纷繁,而又互为影响的。
在此,我们请教相关专业技术人员,搜集国内外解决此类缺陷资料希望能为您在生产过程中注塑成品率的提高有所帮助,这是我们的良好的目的。
但鉴于我们的能力,本公司发布的解决措施,仅供您参考。
我们不负任何的法律责任。
◆注塑成型部分产品不良的解决措施一、注塑成型部分(注塑成型时发生不良现象的主要原因)二、处理不良现象的措施1、模具的缺陷2、塑料树脂的缺陷3、不适合的成型制件4、产品设计的上问题5、对成型机性能的过大评价6、周围环境的变化1、表面起膜2、飞边3、透明性低下4、异色、褪色5、表面突起6、未填满7、流痕8、黑线9、成型收缩10、黑斑11、银线12、熔接线13、破裂、白化1. 表面起膜树脂的添加剂流经产品表面时,形成的白色、灰色的蔓延现象被称为表面起膜。
产生的主要原因:1、树脂内部的添加剂是主要原因1、造成过度应力的注塑条件等也是引发原因2. 飞边产生的主要原因1、注塑机加工不良2、注塑机容量不足3、加工条件不良4、锁模力不足5、模具贴得不紧6、模具的变形7、树脂流动太好8、Gas Vent过大9、注塑压力较大10、模具面上存在异物对成型品的尺寸产生影响的因素多种多样,其主要变数有模具、产品形状、成型条件及后工程、树脂的种类等。
3. 透明性低下PPS、SAN等透明产品出现的透明性低下的现象产生的主要原因1、脱模剂使用过多2、混入其它树脂3、混入其它型号4、模具的加工状态,模具温度等加工条件不合适。
4. 异色、褪色产品的颜色与标准颜色不同的现象。
树脂颜色不同为异色;注塑后颜色发生改变的现象为变色。
产生的主要原因1、着色错误2、树脂污染3、过多使用粉碎品4、注塑机污染5、树脂的热化等5. 表面突起产生的主要原因1、原料内混入异物2、颜料未分散3、模具加工状态4、使用再利用原料6. 未填满树脂没有填满Cavity的全部,冷却凝固后成型品的一部分出现不足的现象。
纸张的平面强度差表面偏酸性平滑度不良引起的印刷质量故障现象及解决方法
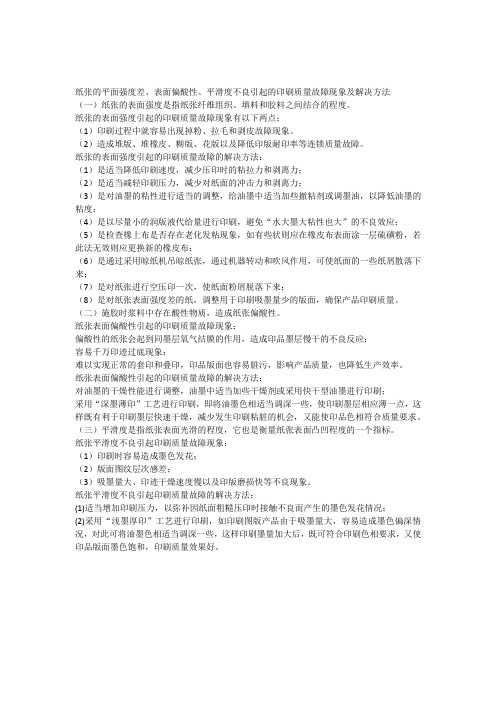
纸张的平面强度差、表面偏酸性、平滑度不良引起的印刷质量故障现象及解决方法(一)纸张的表面强度是指纸张纤维组织、填料和胶料之间结合的程度。
纸张的表面强度引起的印刷质量故障现象有以下两点:(1)印刷过程中就容易出现掉粉、拉毛和剥皮故障现象。
(2)造成堆版、堆橡皮、糊版、花版以及降低印版耐印率等连锁质量故障。
纸张的表面强度引起的印刷质量故障的解决方法:(1)是适当降低印刷速度,减少压印时的粘拉力和剥离力;(2)是适当减轻印刷压力,减少对纸面的冲击力和剥离力;(3)是对油墨的粘性进行适当的调整,给油墨中适当加些撤粘剂或调墨油,以降低油墨的粘度;(4)是以尽量小的润版液代给量进行印刷,避免“水大墨大粘性也大”的不良效应;(5)是检查橡上布是否存在老化发粘现象,如有些状则应在橡皮布表面涂一层硫磺粉,若此法无效则应更换新的橡皮布;(6)是通过采用晾纸机吊晾纸张,通过机器转动和吹风作用,可使纸面的一些纸屑散落下来;(7)是对纸张进行空压印一次,使纸面粉屑脱落下来;(8)是对纸张表面强度差的纸,调整用于印刷吸墨量少的版面,确保产品印刷质量。
(二)施胶时浆料中存在酸性物质,造成纸张偏酸性。
纸张表面偏酸性引起的印刷质量故障现象:偏酸性的纸张会起到同墨层氧气结膜的作用,造成印品墨层慢干的不良反应;容易千万印迹过底现象;难以实现正常的套印和叠印,印品版面也容易脏污,影响产品质量,也降低生产效率。
纸张表面偏酸性引起的印刷质量故障的解决方法:对油墨的干燥性能进行调整,油墨中适当加些干燥剂或采用快干型油墨进行印刷;采用“深墨薄印”工艺进行印刷,即将油墨色相适当调深一些,使印刷墨层相应薄一点,这样既有利于印刷墨层快速干燥,减少发生印刷粘脏的机会,又能使印品色相符合质量要求。
(三)平滑度是指纸张表面光滑的程度,它也是衡量纸张表面凸凹程度的一个指标。
纸张平滑度不良引起印刷质量故障现象:(1)印刷时容易造成墨色发花;(2)版面图纹层次感差;(3)吸墨量大、印迹干燥速度慢以及印版磨损快等不良现象。
印刷材料常见不良及对策
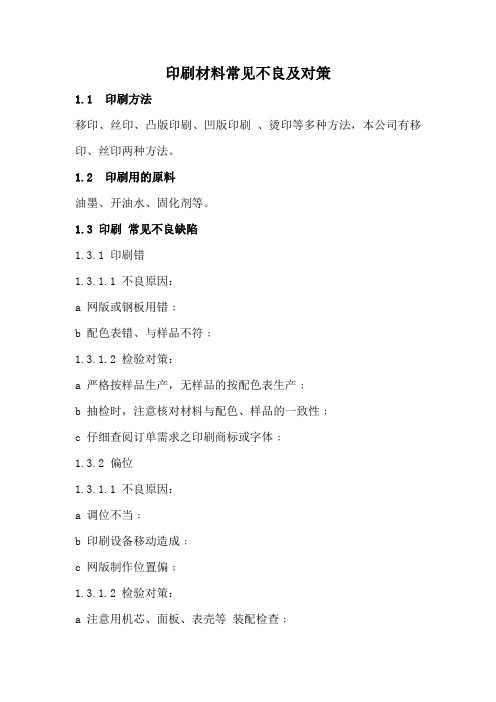
印刷材料常见不良及对策
1.1印刷方法
移印、丝印、凸版印刷、凹版印刷、烫印等多种方法,本公司有移印、丝印两种方法。
1.2印刷用的原料
油墨、开油水、固化剂等。
1.3 印刷常见不良缺陷
1.3.1 印刷错
1.3.1.1 不良原因:
a 网版或钢板用错﹔
b 配色表错、与样品不符﹔
1.3.1.2 检验对策:
a 严格按样品生产,无样品的按配色表生产﹔
b 抽检时,注意核对材料与配色、样品的一致性﹔
c 仔细查阅订单需求之印刷商标或字体﹔
1.3.2 偏位
1.3.1.1 不良原因:
a 调位不当﹔
b 印刷设备移动造成﹔
c 网版制作位置偏﹔
1.3.1.2 检验对策:
a 注意用机芯、面板、表壳等装配检查﹔。
- 1、下载文档前请自行甄别文档内容的完整性,平台不提供额外的编辑、内容补充、找答案等附加服务。
- 2、"仅部分预览"的文档,不可在线预览部分如存在完整性等问题,可反馈申请退款(可完整预览的文档不适用该条件!)。
- 3、如文档侵犯您的权益,请联系客服反馈,我们会尽快为您处理(人工客服工作时间:9:00-18:30)。
© 2014 天马微电子股份有限公司. All rights reserved
12
© 2014 天马微电子股份有限公司. All rights reserved
8
X2:halftone工艺
D/I PR-DE D/I CH-DE
因残膜不均一 ,沟道长也会 不均一
© 2014 天马微电子股份有限公司. All rights reserved
9
X2:halftone工艺
IDE&PRDE recipe
PRDE中的高功率长时间对MURA有影响,验证中。 问题点:同样的电极上5mask工艺和4mask(D/I)工艺对于 DE MURA有比较明显的差异,halftone工艺带来的干刻mura 现在尚无很好的办法控制。
© 2014 天马微电子股份有限公司. All rights reserved
5
X1:下部电极
同一张大玻璃上,对目测未发现点状mura的位置进行了KMAC测量,并对 所得数据进行了分析。
分析:同一张玻璃上,未发现点状mura的位置,其a-si残留量也不十分均匀,且 厚度分布的模式和有mura处有相同之处(薄-厚交替),只是其变化量大大减少, 仅有不到50A左右。
2
不良现象
不良描述
在IDE及CHDE后用 MMO检查或后端VT 检可见有直径2mm, 间距为5mm*5mm的 白点即为干刻 MURA
不良现象
© 2014 天马微电子股份有限公司. All rights reserved
3
X1:下部电极
电极结构
DE MURA
——050YF华为项目风险点
2015-02-1
© 2014 天马微电子股份有限公司. All rights reserved
目录 Contents
1
不良现象 X1:下部电极 X2:halftone工艺
2
3 4
© 2014 天马微电子股份有限公司. All rights reserved
新电极表面清洁,emboss均匀
旧电极表面由于长期附作物沉淀, emboss均匀度也受到影响
7
© 2014 天马微电子股份有限公司. All rights reserved
X2:halftone工艺(D/I工程)
D/I PR D/I DE
沟道残膜 6000-9000
© 2014 天马微电子股份有限公司. All rights reserved
因电极结构原因,有无 Emboss的刻蚀差是一定会 有的。
© 2014 天马微电子股份有限公司. All rights reserved
4
X1:下部电极
得到KMAC数据后对数据进行了分析
圆圈位置为 点状mura处
分析: 通过以上数据可看出,在点状mura处的a-si残留量相对于其他位置而言较少, 相差约为150A左右;其分布较为规律,与DE下部电极上的emboss相对应,有 EMBOSS的地方刻蚀量大。
© 2014 天马微电子股份有限公司. All rights reserved
6
X1:下部电极
结论:由以上分析可以看出,DE下部电极上的emboss,导致整张玻璃上产 生了模式相同的刻蚀不均,但对于电极,表面由于长期附作物沉淀,表面 emboss也不再均匀,造成其刻蚀不均严重层度不同,较为严重处出现了肉眼可 见的mura,较轻微处,mura便不可见。 新电极由于表面无沉积物,刻蚀不均的严重度轻微,mura便不可见。
© 2014 天马微电子股份有限公司. All rights reserved
10www.tianma.来自omX1:下部电极-控制方法
受控项目 DE mura(Y) 下部电极 (X) 测量方 法 良率数 据 DE mura监 控 MSA 控制方法 频率 信号 出现DE mura不 良 出现DE mura 措施 反馈 DE 下部电 极更换 流程 负责人 实施 日期 持续
可信
VT检 MMO DE mura检查 表
抽检
生产
可信
日检
DE全 员
持续
© 2014 天马微电子股份有限公司. All rights reserved
11
X2:halftone工艺
控制计划: 1.PRDE recipe验证,减少时间对减少MURA产生有效果。 2.沟道残膜均一性改善,验证中 3.电极更换频度变更为1年/1次。