IE教育-浪费教材
八大浪费与IE七大手法培训

八大浪费与IE七大手法培训一、浪费的概念在生产和管理过程中,浪费是指任何没有为顾客创造价值的活动、步骤或资源。
浪费通常会导致生产效率的下降、成本的增加以及顾客满意度的降低。
充分认识和理解浪费对于提高生产效率、降低成本以及提升企业竞争力具有重要意义。
八大浪费,也被称为“TOYOTA制造业中的八大浪费”,是在制造业领域中提出的浪费分类模型,可以帮助企业识别和减少浪费,提高生产效率。
八大浪费包括以下内容:1.过产:生产超出需求的产品,造成库存积压。
2.运输:物料、半成品或成品在生产过程中的多次搬运。
3.待货:产品在生产过程中停滞等待下一道工序。
4.加工:生产过程中的不必要操作和加工步骤。
5.库存:过量的物料或产品积压在仓库中。
6.功劳:工人在不必要的工作中造成的浪费。
7.运动:无效的工人或设备的移动。
8.等待:等待原材料、设备或其他资源的到达。
二、IE七大手法IE(Industrial Engineering)是一种运用工程技术和管理学原理改善生产过程的学科,旨在提高生产/操作效率,降低成本。
IE的七大手法是IE学科中常用的方法和工具,通过对生产过程进行分析和改进,以提高生产效率和减少浪费。
IE七大手法包括以下内容:1.工程作业分析:通过分析和记录工序中的每个步骤和活动,识别出浪费和低效的环节。
2.工序改进:基于工程作业分析的结果,优化和改进工序,提高生产效率。
3.布局设计:设计和优化工厂/车间的布局,使得物料和信息流动更加高效和顺畅。
4.工作标准化:制定和实施标准化的工作程序和操作规范,提高工作的一致性和效率。
5.工具和设备改进:引入新的工具和设备,或者对现有的工具和设备进行改进,提高生产效率。
6.人力资源管理:合理安排和管理人力资源,提高员工的工作效率和满意度。
7.进程控制:监控和控制生产过程,确保生产活动按照计划进行,减少浪费和延误。
三、浪费与IE七大手法培训浪费和IE七大手法是生产和管理中非常重要的概念和方法。
IE培训内容课件

4.分析一搬步骤
IE 教育
现象分析
原因分析
改善案导出
成果计算
1.稼动分析(运转分析) 1)工程单位构成表 2)W/S观测表 3)W/S观测统计 4)W/S分析表2.作业分析 —所有要素作业的时间分析表3.编程分析 —现况的Line Layout作成4.工程分析 —部品加工分析 --部品供给方式5.执行分析 —现在管理指数 (回收率\人时当生产量)
1. 作业分析概论2. 联合作业分析—连续观测法
第五章 作业分析
IE 教育
5.作业分析
1 作业分类(按精密度)
□ 对作业详细分解,发现平时感觉不到的很小的Loss □ 定量的了解事实,掌握现在的方法-□ 改善要素作业□ 改善作业所必需的JIG(夹具),加工条件,部品精密度等
Line
作业说明
作 业
主作业
主体作业
附属作
NO
日期 :
观测者
非作业
作业余量
管理余量
疲劳余量
个人余量
无作业
组装 部品的组装
焊接 人工焊接
固定 螺母,螺栓的固定
连接 连接电线,捆
--> -->-->-->-->
利用5W 1H的改善想法
4 改善原则的应用
5 要素作业分析表
IE 教育
5.作业分析
IE 教育
5.作业分析
二 要素作业的分析方法----连续观测法
观测记录和整理方法
观测时应先起动秒表开始
应连续观测作业的重复
读取的时间记录到观测用纸的摾奂茡栏中.
观测结束后整理时在表中记录 各要素作业的时间
>
工程
单位作业
>
IE——七大浪费

七大浪费生产线上的七种浪费第一种:等待的浪费主要因素表现为:作业不平衡,安排作业不当、待料、品质不良等。
第二种:搬运的浪费主要因素表现为:车间布置采用批量生产,依工作站为区别的集中的水平式布置所致。
(也就是分工艺流程批量生产),无流线生产的观念。
第三种:不良品的浪费主要因素表现为:工序生产无标准确认或有标准确认未对照标准作业,管理不严密、松懈所导致。
第四种:动作的浪费主要因素表现为:生产场地不规划,生产模式设计不周全,生产动作不规范统一。
第五种:加工的浪费主要因素表现为:制造过程中作业加工程序动作不优化,可省略、替代、重组或合并的未及时检查。
第六种:库存的浪费主要因素表现为:管理者为了自身的工作方便或本区域生产量化控制一次性批量下单生产,而不结合主生产计划需求流线生产所导致局部大批量库存。
库存的损害表现有:(1):产生不必要的搬运、堆积、放置、防护处理、找寻等浪费。
(2):使先进先出的作业困难。
(3):损失利息及管理费用。
(4):物品的价值会减低,变成呆滞品。
(5):占用厂房空间,造成多余的工场、仓库建设投资的浪费。
(6):没有管理的紧张感,阻碍改进。
(7):设备能力及人员需求的误判。
第七种:制造过多(早)的浪费主要因素表现为:管理者认为制造过多与过早能够提高效率或减少产能的损失和平衡车间生产力。
制造过多(早)的损害表现有:(1):提早用掉费用(材料费、人工费),不能创造利润。
(2):把“等待的浪费”隐藏起来,使管理人员漠视等待的发生和存在。
(3):自然而然地积压在制品,其结果不但会使制程的时间变长(无形的),而且会使现场工作的空间变大,机器间距离因此加大,逐渐地吞蚀利润。
(4):产生搬运,堆积的浪费,使得先进先出的作业产生困难。
七大浪费的对策结合大连三洋制冷推行精益生产方式的实际情况,重点论述生产现场的七种浪费和如何有效消除。
一、七种浪费之一:等待的浪费等待就是闲着没事,等着下一个动作的来临,这种浪费是无庸置疑的。
八大浪费与IE七大手法培训课件
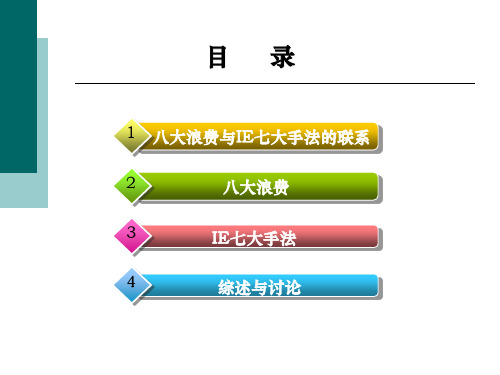
评论者: 指责别人这里也不对、那里也不对,却提不出改善建议或指导意见。
建设者: 不仅能够指出对方的问题,更能够提出中肯的改善方向、方法,甚至给出较为实用的方案。
作建设者而非评论者
!
*徒然要求改善而不讲求方法、技巧,事倍功半。 *不教而战,谓之杀。 *给人一条鱼吃,不如传授捕鱼的技术。 *要求捕更多的鱼,必须讲求捕鱼技术的传授与使用。 *IE七大手法(IE 7 TOOLS)就是协助我们改善工作的技术。
均衡化生产、一个流生产; 自动化及设备保养加强; 加强进料控制。
管理的浪费
定 义
表现与后果
基于工厂的管理和运作方式使公司不能获得最大利润而造成的浪费,是竞争力强弱的表现。
1 成员仪容不齐整,有损企业形象,影响士气。 2 设备布置不合理,半成品数目大,增加搬运和无效作业。 3 设备保养不当,易生故障,增加修理成本,影响品质。 4 物品随意摆放,易混料,寻找费时间,易成呆料。 5 通道不畅,作业不畅,易生危险。
产生原因
消除方法
认为提前生产是高效率的表现,有大量库存才保险; 空闲时多制造的部分; 设备状态良好时连续生产; 物流混乱,呆滞物品未及时处理。
库存意识的改革; 均衡化生产,看板管理的贯彻; 生产计划安排考虑库存消化; 加强物料管理、设置库存警示。
搬运的浪费
定 义
导致后果
不必要的搬运、移动、预置、改装和搬运的距离长、强度大造成的浪费。
为什么要有IE七大手法?
怎么改善呢?我要打坐! 我想!我想!我想想想!
改善四原则
改善四原则(ECRS)
原则
目标
例子
取消Eliminate
是否可以不做,如果不做会如何:排除不经济的作业,放弃不必要的作业
培训教材—IE八大浪费详解

•文件或信息放在桌上或在电脑内 等待决策或签字 •因安排不当造成项目进程过长 •做了没有价值的事情
管理的浪费
原因:
没有详细的计划安排 作业手续太复杂 重复劳动多 拖延、打扰和精力不集中
对策:
不要推迟进行对你不合意的工作 要有详细的工作计划,并分解成许多可操作的小任务,采取 “分而治之”的方法 利用科技的力量来提升效率 去除不必要的重复劳动,精简作业流程
改善手法
QC讲求的是“因果论”,要有因才有结果,有 过程才有产出;
IE讲求的是“方法论”,不同的方法有不同的 结果,越少的浪费效果越好;
VA讲求的是“价值论”功能越强,价值越高,成 本越低,价值越高。
改善手法
QC基本理念:事实与变异的理念,管理与改善的理念
事实的理念是指以事实为基础,而事实又以数据加以体现: 收集正确的数据,排列、整理数据,依数据行动
改善手法
VA基本理念:必要与不必要
国家标准GB8223-87关于VA之定义:通过各相关 领域的协作,对所研究对象的功能与费用进行系 统分析,不断创新,以提高所研究对象价值的思 想方法和管理技术
改善意识
现场、现物、现实的意识
现场指到问题发生的场所, 现物指对发生问题的对象进行确认, 现实指实实在在地进行分析,找出真正的原因。
5.库存的浪费
对策:
库存意识的改革 U型设备配置 均衡化生产 生产流程调整顺畅 看板管理的贯彻 快速换线换模 生产计划安排考虑库存消化
5.库存的浪费
注意:
库存是万恶之源 管理点数削减降低安全库存 消除生产风险降低安全库存
6.动作的浪费
额外动作的浪费
不必要的动作、无附加价值的动作,及较慢的动作
表现形式:
IE基础及七大浪费ppt课件
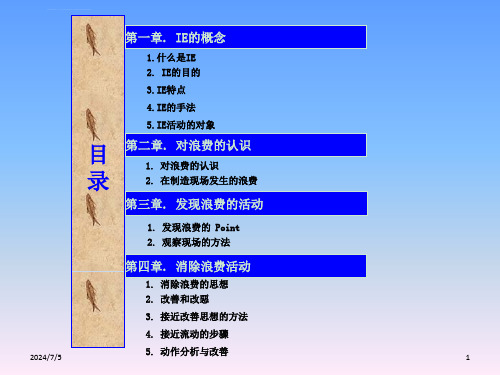
途也有寄托之所在.因此,简单地说IE就是代表“合理化及改善”的意义,为了顾及记忆
的方便,为什么就以中文”改善”来代表“I”的含义。
2024/7/5
2
经营者提供商品或者服务有欺诈行为 的,应 当按照 消费者 的要求 增加赔 偿其受 到的损 失,增 加赔偿 的金额 为消费 者购买 商品的 价款或 接受服 务的费 用
○ 更换JIG时,使用工具拆卸. (改善) 改成没有工具还能组装,拆卸的不倒翁式 Hole结构.
○ 更换JIG时,使用工具拆卸.
(改善) 改成没有工具还能组装,拆卸的Lever式 结构.
2024/7/5
- 17 -
15
经营者提供商品或者服务有欺诈行为 的,应 当按照 消费者 的要求 增加赔 偿其受 到的损 失,增 加赔偿 的金额 为消费 者购买 商品的 价款或 接受服 务的费 用
客观性
定量性
通用性
2024/7/5
3
经营者提供商品或者服务有欺诈行为 的,应 当按照 消费者 的要求 增加赔 偿其受 到的损 失,增 加赔偿 的金额 为消费 者购买 商品的 价款或 接受服 务的费 用
Ⅰ.IE的概念
5.IE活动的对象
1.工艺 2.作业 3.搬运 4.生产布局
5.设备 6.工装 7.材料 8.管理程序
2024/7/5
4
经营者提供商品或者服务有欺诈行为 的,应 当按照 消费者 的要求 增加赔 偿其受 到的损 失,增 加赔偿 的金额 为消费 者购买 商品的 价款或 接受服 务的费 用
Ⅱ.对浪费的认识
Ⅰ. 对浪费的认识
1. 对浪费的认识 1) 浪费是什么? 2) 浪费的类型 3) 区别浪费和附加价值 4) 工作和活动 5) 区别动作(四种动作)
某集团IE工业工程八大浪费培训

某集团IE工业工程八大浪费培训一、引言IE工业工程是一种以提高企业生产效率和降低生产成本为目标的管理方法,其中的核心理念之一就是减少浪费。
在IE工业工程中,有八大浪费被视为需要避免的行为,包括:过程中的等待、运输、工艺故障、库存积压、过度加工、不必要的移动、生产不足和质量问题。
本文将对某集团进行IE工业工程八大浪费培训进行介绍和分析。
二、过程中的等待过程中的等待是指在生产过程中,由于各种原因导致的工人、设备或原材料的等待时间。
这种等待时间不仅浪费了生产资源,还降低了生产效率。
在某集团的IE工业工程八大浪费培训中,应该重点强调减少等待时间的重要性,通过优化生产计划、提高设备利用率和优化物流流程等措施来降低等待时间的发生。
三、运输浪费运输浪费是指产品在生产过程中不必要的运输活动,例如原材料的搬运、半成品的转运等。
这种浪费不仅增加了生产过程中的物流成本,还增加了运输过程中的损耗和风险。
在某集团的IE工业工程八大浪费培训中,应该提倡优化物流流程,减少物料的运输距离和次数,提高运输效率,从而减少运输浪费。
四、工艺故障工艺故障是指在生产过程中由于设备故障、操作错误等原因导致的停工和生产中断。
这种故障不仅影响了生产进度,还会导致产品质量不稳定。
在某集团的IE工业工程八大浪费培训中,应该注重设备维护和巡检,提高设备的稳定性和可靠性,减少工艺故障的发生。
五、库存积压库存积压是指在生产过程中积累的过多的库存,这些库存不仅占用了公司的资金,还增加了管理和储存的成本。
在某集团的IE工业工程八大浪费培训中,应该引导员工根据需求进行生产,减少不必要的库存积压,提高资金利用率和仓储效率。
六、过度加工过度加工是指对产品进行不必要的加工工序,增加了生产成本和工时。
在某集团的IE工业工程八大浪费培训中,应该强调优化生产工艺,减少不必要的加工工序,提高生产效率和产品质量。
七、不必要的移动不必要的移动是指在生产过程中工人、设备或物料进行不必要的移动。
I.E基础与七大浪费培训课件(PPT 40页)

因材料不良、加工不良、 检查不当等原因而导致浪费
20
现在处理的工作是必不可少的吗?
Ⅰ. 对浪费的认识
社内限
① 生产过剩导致的浪费
生产过剩不仅产生更多的问题,也隐藏问题的根本原因。
若出现剩余人力或机器,即使不需要多生产,也利用这些剩余能力生产毫无必要的产品。 不仅如此,由于生产过剩还造成许多浪费,隐藏在工作现场所发生的问题,因而被称为“浪费的根源”。
社内限
第一章 I.E基础与七大浪费
SESS
1
社内限
第一节 I.E概要
SESS
2
1. IE的历史
社内限
泰勒 方式(F.W.Taylor 1856~1915)
他被称为“作业测定 (Work Measurement) ”之父 建议科学管理方法:运用时间研究、预定时间标准法或标准资料法等技术来确定合格 工人按规定的作业标准, 以此为基础可以进行有系统地生产管理。 所谓科学管理原理是指,用公平的方法分配由劳资双方的合作得到的利润。
◇ 管理技术: 使固有技术发挥力量的综合技术,应用技术。 有效利用多种资源的原则或技术体系。 IE,QC,VE,ORDLIX,PAC,TPM,CIM,JIT,6 SIGMA等等
生
6 SIGMA/KM
产
BPR/SCM/TOC
效
JIT/TPM
率
管理技术
IE/VE/QC
1911
1924
固有技术
1947
1990 年
○当更换JIG时,使用工具来拆卸。 (改善)使用控制杆来改善工作方式,以不使用工具 而直接组装和拆卸。
SESS
19
社内限
Ⅰ. 对浪费的认识
社内限
3) 在制造第一线发生的7种浪费
IE七大手法八大浪费培训课件

IE七大手法八大浪费一、IE人员主要从事的七个方向,它们是:1.研究与开发管理;2.生产系统设计与控制;3.效率工程;4.质量控制与质量保证;5.实施规划与物流分析;6.工业卫生与安全;7.人力资源管理。
二、基础IE里的东西:IE手法包括:方法研究(程序分析、动作分析),作业测定,布置研究,Line Balance等,但好象不够七个。
在现场IE里,IE七大手法包括:程序分析、动作分析,搬运分析,动作经济原则,作业测定,布置研究,Line Balance。
三、台湾公司教材里面的1、工程分析。
2、搬运工程分析。
3、运动分析(工作抽查 work sampling)4、生产线平衡。
5、动作分析。
6、动作经济原则。
7、工厂布置的改善。
四、其它的各种说法 1、IE七大手法为:作业分析、程序分析(运用ECRS 技巧)、动作分析(动作经济原则)、时间分析、稼动分析、布置搬动分析、生产线平衡2、七大手法:流程分析法、动作分析法、动作经济原则、时间研究、工作抽查法、人机配置法、工作简化法3、七大手法:动作改善法(动改法)、防止错误法(防错法)、5*5W1H法(五五法)、双手操作法(双手法)、人机配合法(人机法)、流程程序法(流程法)、工作抽样法(抽样法)4、七大手法:程序分析、时间分析、动作分析、流水线分析、稼动分析、物料分析、环境分析。
IE的八大浪费浪费的定义在JIT生产方式中,浪费的含义与社会上通常所说的浪费有所区别。
对于JIT来讲,凡是超出增加产品价值所绝对必须的最少量的物料、设备、人力、场地和时间的部分都是浪费。
因此,JIT生产方式所讲的浪费不仅仅是指不增加价值的活动,还包括所用资源超过“绝对最少”界限的活动。
各种各样的浪费现象在很多尚未实行5S活动的企业中普遍存在,如表1-1所示。
为了杜绝工厂中的浪费现象,首先需要发现不合理的地方,然后才是想办法解决问题,这就需要推行5S、JIT等较为先进的管理方法。
表1-1 未实施5S活动的企业中的浪费常见的八大浪费在工厂中最为常见的浪费主要有八大类,分别是:不良、修理的浪费,过分加工的浪费,动作的浪费,搬运的浪费,库存的浪费,制造过多?过早的浪费,等待的浪费和管理的浪费。
IE的八大浪费
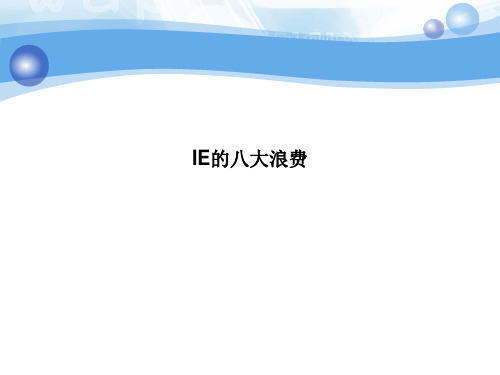
7、等待的浪费
造成等待浪费的原因:
➢ 生产线的品种切换; ➢ 每天的工作量变动很大; ➢ 时常因缺料而使机器闲置; ➢ 上工序延误导致下工序闲置; ➢ 机器设备时常发生故障; ➢ 生产线未能取得平衡; ➢ 存在劳逸不均的现象。
8、管理的浪费
管理的浪费指的是问题发生以后,管理人员才采取 相应的对策来进行补救而产生的额外浪费。
如果降低库存,就能将下述问题彻底暴露出水面,进而能 够逐步地解决这些库存的浪费。
6、制造过 多 的浪费
制造过多或过早,提前用掉了生产费用,不但没有 好处,还隐藏了由于等待所带来的浪费,失去了持续 改善的机会。
有些企业由于生产能力比较强大,为了不浪费生产 能力而不中断生产,增加了在制品,使得制品周期变 短,空间变大,还增加了搬运,堆积的浪费。此外制 造过多或过早,会带来庞大的库存量,不可避免地增 加了贬值的风险。
也有一些企业利用传送带或机器搬运的方式来减少人工搬 运,这种作法是花大钱来减少工人体力的消耗,实际上并没 有排除搬运本身的浪费。
5、库存的浪费
JIT的观点认为,库存是没有必要的,甚至认为库存是万 恶
之源,由于库存很多。将故障,不良品,缺勤,点点停,计 划有误,调整时间过长,品质不一致,能力不平衡等问题全 部掩盖住了。
4、搬运的浪费
从JIT的角度来看,搬运是一种不产生附加价值的动 作,而不产生价值的移动,整列等动 作浪费,由此而带来物品移动所需空间的浪费,时间的 浪费和人力工具的占用等不良后果。
国内目前有不少企业管理者认为搬运是必要的,不是浪费。 因此,很多人对搬运浪费视而不见,更谈不上去消灭它。
管理浪费是由于事先管理不到位而导致的问题,科 学的管理应该是具有相当的预见性,有合理的规划,并 在事情的推进过程中加强管理,控制和反馈,这样就可 以在很大程度上减少管理浪费现象的发生。
IE的大浪费PPT课件

•10
•.
6、制造过 多
制造过多或过的早浪,提费前用掉了生产费用,不但没有
好处,还隐藏了由于等待所带来的浪费,失去了持续 改善的机会。
有些企业由于生产能力比较强大,为了不浪费生产 能力而不中断生产,增加了在制品,使得制品周期变 短,空间变大,还增加了搬运,堆积的浪费。此外制 造过多或过早,会带来庞大的库存量,不可避免地增 加了贬值的风险。
•3
•.
■浪费的定义
在JIT生产方式中,浪费的含意与社会上通常所说的浪费 有所区别。对于JIT来讲,凡是超出增加产品价值所绝对必须 的最少量的物料,设备,人力,场地和时间的部分都是浪费。
具体来说,浪费的含义: 1、不增加价值的活动,是浪费 2、尽管是增加价值的活动,所用的资源超过了“绝对最 少”的界限,也是浪费 总而言之,凡是超过生产产品所绝对必要的最少量的设 备、材料、零件和工作时间的部分,都是浪费。
•5
•.
2、加工的浪费
定义:加工过剩的浪费也叫过分加工的浪费, 是指在品质、规格及加工过程上的投入主动超过客 户需求从而造成企业资源浪费的情况。
加工过剩浪费分四种情况:过分精确品质带来 的浪费(过剩品质)、过分加工带来的浪费(过剩 加工)、过分检验带来的浪费(过剩检验)、冗余 设计带来的浪费(过剩设计)
也有一些企业利用传送带或机器搬运的方式来减少人工搬 运,这种作法是花大钱来减少工人体力的消耗,实际上并没 有排除搬运本身的浪费。
•9
•.
5、库存的浪费
JIT的观点认为,库存是没有必要的,甚至认为库存是万恶 之源,由于库存很多。将一致,能力不平衡等问题全 部掩盖住了。
IE基础与七大浪费详细概述

IE基础与七大浪费详细概述1. 引言在软件开发过程中,我们经常会遇到一些浪费,这些浪费会导致效率低下、资源浪费以及项目延期等问题。
IE基础与七大浪费是软件开发中常见的问题之一。
本文将详细概述IE基础与七大浪费的概念、原因以及解决方案。
2. IE基础IE(Incremental Encapsulation)基础是一种软件开发的基本原则和方法论,旨在减少变更的影响、增加代码的可维护性和可测试性。
IE基础的核心思想是将变更尽可能小的引入到系统中,并通过封装和抽象来解耦模块之间的依赖关系。
IE基础的实践包括分层架构、接口定义、单元测试等,这些实践可以使系统更易于扩展和维护,也为后续介绍的七大浪费提供了基础。
3. 七大浪费3.1 人力浪费人力浪费是指在软件开发过程中由于各种原因导致人力资源没有得到合理利用的情况。
常见的人力浪费包括:•重复劳动:开发人员在完成一个任务之后需要重复完成相同或相似的任务,导致劳动力资源的浪费。
•无效会议:开发团队频繁举行无效会议,占用了开发人员宝贵的工作时间,同时会议内容没有明确的目标和决策。
解决人力浪费的方法包括优化工作流程、合理分配任务和明确会议目标。
3.2 等待浪费等待浪费是指开发人员在软件开发过程中由于等待其他资源导致的时间浪费。
常见的等待浪费包括:•等待开发环境的搭建和配置。
•等待上游团队的交付,如设计团队提供设计稿等。
解决等待浪费的方法包括优化开发环境搭建流程、提前沟通并协调上游团队的工作计划。
3.3 运动浪费运动浪费是指在软件开发过程中无意义的活动和操作导致的资源浪费。
常见的运动浪费包括:•重复的文件移动和复制操作。
•多次编译和构建代码。
解决运动浪费的方法包括优化工作流程、利用自动化工具来减少不必要的操作。
3.4 传输浪费传输浪费是指在软件开发过程中由于数据传输的不合理导致的资源浪费。
常见的传输浪费包括:•网络传输的延迟和带宽浪费。
•大量不必要的数据拷贝和传输。
解决传输浪费的方法包括优化网络环境和减少不必要的数据拷贝。
富士康IE学院-八大浪费教材

原來﹕10人 1日 100個
現在﹕10人 1日 125個(假效率)
現在﹕ 8 人 1日 100個(真效率)
***稼動率和可動率的追求.
IE 學院 PJF 20070403
八 大 浪 費 介 紹
(二) 浪費的產生:
過量計划(Schedule)﹕信息不准﹔計划錯誤﹔計划失 當﹔信息傳遞不暢﹔制程反應速度慢﹔
IE 學院 PJF 20070403
八 大 浪 費 介 紹
合理化布局設計的要點
1﹑輔助生產線的終點﹐應盡量接近供給對象 的主生產線工序﹔
2﹑充分探討供應各工序零部件的方法﹔ 3﹑研究空卡板﹑包裝箱﹑夾具的返回方法﹔ 4﹑沿生產線設置大小適當的零部件暫放場
所﹔ 5﹑不要忘記在生產線中設置檢查工序和修理
大 2.等待的浪費﹔
浪 3.在制品的浪費﹔
4.空間的浪費。 如何善待輸送帶
費
1.邊送邊做﹔
介
2.划分節距線﹔ 3.依產距時間設定速度;
紹
4..設立停線按紐。
IE 學院 PJF 20070403
八 大 浪 費 介 紹
(二) 浪費的產生: 工廠布局(Layout)﹕物流動線設計﹔設備 局限﹔工作地布局﹔前后工程分離﹔ 設計兼容性(Compatibility)﹕業務擴充→ 新增工序或設備﹔設備或物料變換→不適 合﹔前景不明→未作整體規划﹔ (三)改善方向﹕ 1﹑合理化布局﹔ 2﹑搬運手段的合理化。
費 傳送帶﹔ 定量搬運和定時搬運。
介 搬運工具的合理化。 紹 現場布置
IE 學院 PJF 20070403
八 五﹑在庫量過多的浪費
大 (一)產生原因﹕制造業的工廠﹐存在著原材 料﹑零部件﹑半成品﹑成品等在庫﹐在庫發
IE-认识浪费
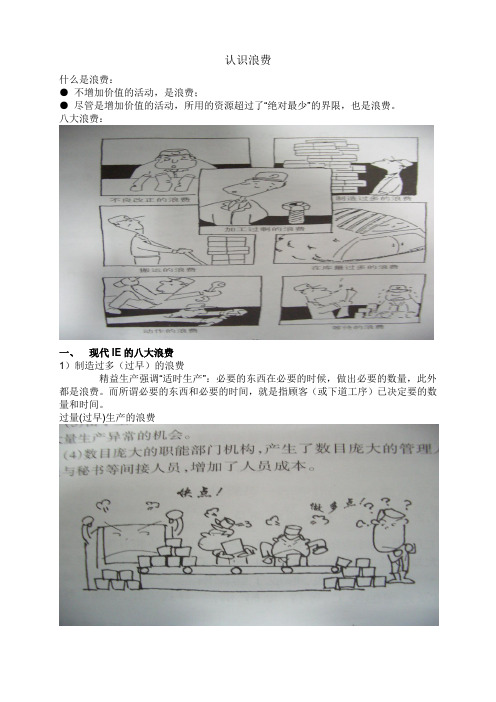
认识浪费什么是浪费:●不增加价值的活动,是浪费;●尽管是增加价值的活动,所用的资源超过了“绝对最少”的界限,也是浪费。
八大浪费:一、现代IE的八大浪费1)制造过多(过早)的浪费精益生产强调“适时生产”:必要的东西在必要的时候,做出必要的数量,此外都是浪费。
而所谓必要的东西和必要的时间,就是指顾客(或下道工序)已决定要的数量和时间。
过量(过早)生产的浪费2)库存的浪费(包含中间在制品)●产生不必要的搬运、堆积、放置、防护、寻找等浪费动作;●使先入先出作业困难;●资金占用(损失利息);●物品的价值衰减,变成呆料、废料;●掩盖问题,使管理不善的问题掩盖起来。
如机器经常发生故障、设备调整时间太长、设备能力不平衡、工人缺勤、备件供应不及时等问题,由于库存水平高,不易被发现。
●没有改善的紧迫感,阻碍改善的活性化。
●设备能力及人员需求的误判;库存掩盖大量问题3)搬运的浪费搬运是不产生附加值的动作。
搬运的损失分为放置、堆积、移动、整列等动作浪费。
生产流水化同步化是减少搬运的根本之道。
4)不良改正的浪费是指企业内发生不良品造成的各种质量成本及由此造成的相关浪费。
5)过分精确加工的浪费实际加工精度比加工要求高,造成资源的浪费。
工程内搬运的浪费)动作的浪费(动作的12种浪费)⑵、一只手空闲的浪费(一只手在工作,一只手在休息)⑶、作业动作停止的浪费(身体每动作一次停止一次,动作不连续)。
⑷、作业动作太大的浪费(动作幅度太大,勉强费劲)⑸、拿的动作变化的浪费(动作交替变换来适应安装)⑹、步行的浪费道具的位置远了(零件位置远了的浪费)⑺、活动角度太大的浪费(最适合的角度为45度以内)⑻、动作与动作之间没有配合好的浪费(非[连续作业] 的浪费)⑼、不懂技巧的勉强、浪费作业修正、不习惯的浪费(有很好做的时候和做不到的时候)⑽、伸背动作的浪费(零件、作业位置太高)⑾、弯腰动作的浪费(零件、作业位置太低)⑿、重复动作的浪费(同样的动作两次以上地重复操作)7)等待的浪费因断料、作业不均衡、计划不当等造成无事可做的等待,也称之为停滞的浪费。
- 1、下载文档前请自行甄别文档内容的完整性,平台不提供额外的编辑、内容补充、找答案等附加服务。
- 2、"仅部分预览"的文档,不可在线预览部分如存在完整性等问题,可反馈申请退款(可完整预览的文档不适用该条件!)。
- 3、如文档侵犯您的权益,请联系客服反馈,我们会尽快为您处理(人工客服工作时间:9:00-18:30)。
⑦ 不良生产浪费
一个不良等于不能生产两个产品. 一个不良等于不能生产两个产品. □ 作业的错误会带来不良, 生产不良品会导致对公司的不满. □ 增加检查人员能稍微减少不良. 但减少不良并不意味着能改善发生不良的原因. □ 检查不能生产附加价值而只不过是浪费. 检查不能生产附加价值而只不过是浪费.
- 17 -
- 16 -
Ⅰ.对浪费
认识
⑤ 库存浪费
应该丢弃掌握库存可以避免许多问题的概念. 应该丢弃掌握库存可以避免许多问题的概念.
□ 库存不仅是材料,配件,组装品等物品处于停滞状态,即在仓库中的库存.它还包含正在加工中的 产品的库存.
⑥ 动作浪费
作业大部分是活动,而具有附加价值的工作只占其中一部分. 作业大部分是活动,而具有附加价值的工作只占其中一部分. □ 动作浪费在机械设备的布置, 配件或工具的排列不对时也会发生.
- 11 -
Ⅰ.对浪费
认识
2. 在制造现场中发生的浪费现象
为什么发生浪费? 1) 为什么发生浪费?
由于『不一致』『不均衡』『不合理』 由于『不一致』『不均衡』『不合理』的要素而发生许多的浪费 』『不均衡』『不合理
不一致
实际与标准(基准) 实际与标准(基准)不一致
○ ○ ○ ○ 不合常规的作业 任意作业 与基准及作业条件不符 未遵守规则 - 5S(3定) 等……
- 2 -
Ⅰ.对浪费
认识
1. 对浪费的认识
浪费是什么? 1) 浪费是什么? 浪费是指在制造过程中不产生附加价值以及低附加价值的任何行为
浪 纯附加价 值动作 单纯 动作 费
利用最少的设备,材料,部件,空间,作业时间等是创造附加价值 所绝对必要的要素.但是如果这些不能使产品生成附加价值, 则产生浪费.
2.动作经济的基本原则 2.动作经济的基本原则 -配件,工具易使用而容易 放原位.
- 19 -
Ⅰ.对浪费
认识
□ 等待的浪费
浪费 发现问题 1.缺配件和 1.缺配件和材料 1.注意订货, 交给, 1.注意订货, 交给, 注意订货 管理适当库存 2.Line的Unbalance和 2.Line的Unbalance和 作业者的作业散布 作业者的作业散布 2.预防错误 2.预防错误 ① 货的等待 -构筑不会发生不良的系统 3.发生 不良以及设备的故障 以及设备 3.发生 不良以及设备的 ② 人的等待 4.作业者等着设备的动作 4.作业者等着设备的动作 作业者等着设备 4.讯号(即时对付) 4.讯号(即时对付) 讯号 ③ 机械(设备)的等待 5.使用搬运车和叉车中 5.使用搬运车和叉车中 -机械故障, 缺材料等 等待作业 5.担当多 5.担当多的生产线 担当 6.作业中使用两只手的不均衡 6.作业中使用两只手的不均衡 作业 -缺勤, 早退 ,人员变化等 3.维修活动(重视运转率) 3.维修活动(重视运转率) 维修活动 改善方法
□ 不必要的搬运,取下.放置,重堆放,材料再处理,物件移动,物质流动,搬运距离及搬运活性度变坏 等问题不仅会降低生产效率,还会使产品的刮痕及损伤等不良增加.
④ 加工本身的浪费
所谓工作,只要稳定下来,本来的功能便会被遗忘,只留下“在作业”的行为. 所谓工作,只要稳定下来,本来的功能便会被遗忘,只留下“在作业”的行为. □ 需要考虑在作业方法.环境,条件方面是否有不必要的作业. □ 考虑能不能减少或消除现在做的作业.
人员增加 - 14 不良增加
Ⅰ.对浪费
认识
的原因? □ “过盈生产”的原因? ● 重视看得到的运转率. ● 以为停止Line是不好. ● 设备故障, 良, 材料缺货,担心交货期限延迟,对付作业者缺勤.
生産” 由于“ □ 由于“過盈生産”发生的浪费类型 ● 早用完材料,配件(即, 太早制造不需要的而加重利息的负担) ● 材料,产品的 Pallet缺以及箱子的增加. ● 叉车等手推车增加. ● 很多的费用是隐藏的.(人事费用,折旧费,管理费等) ● 隐藏浪费,消除改善必要性的最大敌人
工具太多, 工具太多,太复杂
- 12 -
Ⅰ.对浪费
认识
3) 制造现场的七种浪费.
虽然在工厂中生产的产品各不相同, 但可以发现其典型的浪费类型却十分相似.
①过盈生产带来的浪费
卖不 出去!
②库存浪费
可以 放心 了.
③等待的浪费
④动作的浪费
生产出比市场需中想以库存避免相关 诸多问题而带来的浪费
Ⅰ.对浪费
认识
4) 七个浪费改善的方法 □ 移动和搬运的浪费
浪费 发现问题 改善方法
1.存放处之间的距离 1.存放处之间的距离 -仓库与存放处与生产线有距离 搬运货的浪费 2.保留很多库存 2.保留很多库存 -存放处有太多库存. 1.接近生产线 -在生产线内做存放处. -在不用走路去拿的地方做 存放处. 1.直纳 -入库 = 供给给生产线.
- 15 -
Ⅰ.对浪费
认识
② 等待的浪费
不要以为只有人或设备的等待才是浪费. 不要以为只有人或设备的等待才是浪费.
□ 等待材料投入作业. □ 产品在工艺流程中停滞下来. □ 材料或产品堆放在仓库内,也是浪费.
搬运的浪 ③ 搬运的浪費
由于不合理的Layout, 过盈生产, 库存等而发生. 由于不合理的Layout, 过盈生产, 库存等而发生.
① 把Case拿来 ④ 把PCB拿来
□浪费 √
□价值 □浪费 √
② 消除包装 ⑤ 组装PCB
□价值 √
□价值 □浪费 √
⑧ 交替Box
□浪费
□价值 □浪费 √
③ 开始检查 ⑥把 Driver拿来
□价值 □浪费 √
⑨抽出不良品
□价值 □浪费 √
- 7 -
Ⅰ.对浪费
认识
4) 工作与活动
只创造纯附加价值的动作
等待材料,等待作业或多余 时间带来的浪费.
单纯的移动手,脚,身体并不能 创造附加价值.
⑤搬运的浪费
⑥不良品生产浪费
不良
⑦加工本身的浪费
临时储存在仓库,移动推积, 为了使用而搬运带来的浪费.
材料不良,加工不良,检查 不良等带来的浪费.
现在的作业是真的需要的作业吗? 为什么要那样做?应该对作业抱有反问.
不均衡
制造产品不均衡
○ 工作量不公平 -Line unbalance ○ 常更改Rule(标准) ○ 发生作业散布 (作业时间不一定)
不合理
不合理的方法 内部因素] [内部因素]
○ 产品,资财再处理 ○ 作业困难,不便
[外部因素] 外部因素]
○ 资财供过于求 ○ 材料处理不方便 - 方法与位置方面
OO工具(材料)在哪儿! OO工具(材料)在哪儿! 工具 找不到! 找不到! 我用类似的工具吧. 我用类似的工具吧.
制 造 活 动
单纯动作 浪费钱的动作
活 动
附带动作 不能收费的动作
- 4 -
Ⅰ.对浪费
认识
• 制作动作方面的浪费
几个动作集合成一个工作 , 因此在这个角度来分解各个动作而必须知道在各个动作中 发生什么样的浪费.
从配件箱子里 拿出配件来
把配件拿到作业台来
把配件固定在 设备上
把手柄下降下去
把完成品放在 箱子里
工 作
低效 附加价值 动作
制造 活动
活 动
附带 浪 动作
工作” 浪费 = 活动 + 低效的 “工作”
费
- 3 -
Ⅰ.对浪费
认识
2) 浪费的类型 • Cost(成本)方面的浪费 Cost(成本) 成本
附加价值动作 可收费的动作( 可收费的动作(大)
工 作
低效的动作 可收费的动作( 可收费的动作(小)
- 9 -
Ⅰ.对浪费
认识
□ 单纯动作 √ □ 附带动作 □ 低效附加价值 □ 纯附加价值
拿起落地的材料 在改锥 TIP 夹SCREW
□ 单纯动作 □ 附带动作 √ □ 低效附加价值 □ 纯附加价值
□ 单纯动作 □ √ 附带动作
□ √
单纯动作
□ 附带动作 □ 低效附加价值 □ 纯附加价值
拿起叉车的隔板
组装 焊接 涂装 加工
与作业无关的动作
等待作业. 闲谈. 随意走动.(流动) 周期性发生
浪 纯附加价值 动作 单纯 动作 费
工 作
低效 附加价值 动作
制造 活 活动 动
附带 浪 动作
为了创造附加价值 不得不伴随的动作
低效附加价值的动作
[人] 手工紧固 不良生产 [设备] 性能降低(加工能力) 配件磨损(TIP) 不良生产
我的工具 在哪儿呢?
昨天的约 会怎么样?
为了保管在别的地方 挪动.
检查, 包装, Label作业是浪费 作业是浪费. 容易错觉的浪费 : 检查, 包装, Label作业是浪费.
- 6 -
Ⅰ.对浪费
认识
3)区别浪费和附加价值 3)区别浪费和附加价值
□价值 √ □浪费
⑦ 固定Screw
□ 价值 □价值 □ 浪费 √
- 13 -
Ⅰ.对浪费
认识
① 过盈生产的浪费
过盈生产将产生更多问题,而问题的真正原因却被隐藏下去. 如果发生多余的人或机械, ,就会产生不必要的东西,在不需要的时候,又会变的多余浪费 过盈生产还会造成其他诸多浪费,会掩盖在现场中发生的问题,因此可以被称为浪费的根源.
仓库增加
处理增加
支付利息
过盈生产
- 20 -
Ⅰ.对浪费
认识
□ 加工本身的浪费
浪费 发现问题 改善方法 改善方法
1.不需要加工 1.不需要加工 不需要 1.看加工的本质. 1.看加工的本质. 看加工的本质 -加工本身不需要的 -为什么需要其加工? -消除制模Flash (3现和5Why) 以及修改等…… ① 不需要加工的浪费 2.代替方法 2.代替方法 代替 ② 目前加工的浪费 -确认有没有Cost(成本)较 -是否有别的方法? 便宜的别的方法 (Screw → 胶水) 2.代替方法 2.代替方法 代替