来料不良鱼骨图
鱼骨图-测试不良率高分析

物料
测试中产生 静电造成 测试中异常断电 人员作业错误 线材无防呆 零件短路 维修甩锡 印锡量过多 焊接品质异常 待测机器线 材不良 接口不良 使用次数超多 测试需求大 接口磨损不良 突发性治具不良 发料没有校验 治具发料错误 载具材质太差 程式变更未通知 操作步骤生疏 很久没有生产 人员离岗 新人作业 操作错误 测试SOP遗失 人员故意为之 未按SOP作业 人员更换 去洗手间 支援其他岗位 人员调配不合理 人力不足 工位暂时缺人 新SOP未正式发布 测试服务器当机 测试程式未正式发布 TE疏忽 测试SOP未定义 申请签合未完成 PE疏忽 测试程式没有更新 TE人员疏忽 没有接到ECN通知 测试程式异常 治具来料不良 线材插反
设备
拿取时脱手 运输不当 治具使用坏 使用次数超长 保养不及时
治具掉落摔坏
测试主板不良
锡膏漏印 零件脚氧化 零件空焊
治具数量少 载具磨损
线材脱落 设计时未考虑 成本便宜 线材虚插
为 什 么 测 试 不 良 率 高
测试交换机重启
PSU接口不良 机器温度过高
网络不稳定
工作Loading太大 散热不够
人员
方法
鱼骨图排列图PPT课件
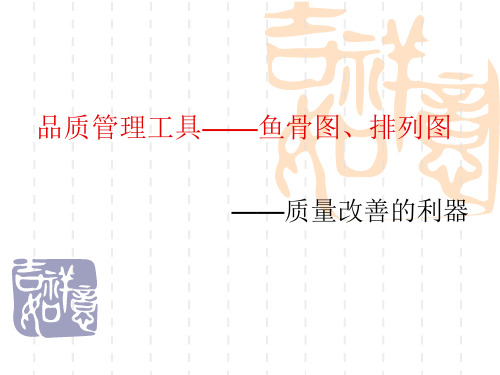
▪ C类属于一般问题,在累计百分比90~100%左右。在实际 应用中,切不可机械地按80%来确定主要问题。它只是根 据“关键的少数、次要的多数”的原则,给以一定的划分 范围而言。A、B、C三类应结合具体情况来选定。
▪ 主要问题项目(A类),可以用划线及“A”表示,或用阴 影线、文字叙述等来表示。在排列图上,一般只分析标注 主要问题(A类)即可。
▪ 搜集数据 搜集一定时期内的质量数据, 按不同用途加以分层、统计。选择用来
进行质量分析的度量单位
项目 办公费 电话费 接待费 差旅费 水电费 宣传推广费 交通费 餐钦费
数量 108.2 40
33.5 30.6 16.4
14.3
(万元)
49
10
表1
排列图的作图法
▪ 作缺陷项目统计表 为简 化计算和作图,把频数较 少的交通费和餐钦费合并 为“其它”项,其频数为 59。
You Know, The More Powerful You Will Be
谢谢大家
荣幸这一路,与你同行
It'S An Honor To Walk With You All The Way
演讲人:XXXXXX 时 间:XX年XX月XX日
▪ 后来,美国质量管理专家朱兰,把这个“关键的 少数、次要的多数”的原理应用于质量管理中, 便成为常用方法之一(排列图),并广泛应用于 其它的专业管理。目前在仓库、物资管理中常用 的ABC分析法就出自排列图的原理。
适用范围
▪ 对问题进行分析 ▪ 找出关键因素 ▪ 或对问题的原因进行分析
排列图的作图法
➢ 画左纵坐标,表示频数(件数、全额等)。确 定原点为0和坐标的刻度比例,并标出相应数 值,
鱼骨图排列图PPT

——质量改善的利器
▪ 查检收数据 ▪ 管制防变异 ▪ 直方显分布 ▪ 柏拉抓重点 ▪ 散布找相关 ▪ 层别找差异 ▪ 特性找要因
鱼骨图(特性要因图、石川图)
▪ 一个问题的特性受到一些要因的影响时,我们 交这些要因加以整理,成为有相互关系而且有 条理的图形,這个图形称为特性要因图.
▪ 因很像一支吃完鱼肉,只剩骨头的鱼所以又称 鱼骨图
▪ 它是1952年日本品管权威学者石川馨博士所发 明,又称“石川图”.
用发散整理法制作特性要因图
▪ 决定问题或品质的特征 ▪ 尽可能找出所有可能会影响结果的因素 ▪ 找出各种原因之间的关系,在鱼骨图中用箭头联接 ▪ 根据对结果影响的重要程度,标出重要因素 ▪ 在鱼骨图中标出必要信息 ▪ 此方法包括两项活动:一找原因;二系统整理出这些原因 ▪ 注意事项:
➢ 严禁批评他人的构想和意見. ➢ 意见愈多愈好. ➢ 欢迎自由奔放的构想. ➢ 顺着他人的创意或意见发展自已的创意.
用逻辑推理法制作特性要因图
▪ 确定品质的特征 ▪ 将品质特性写在纸的右侧,从左至右画一箭头(主骨),将结
果用方框框上. ▪ 列出影响大骨(主要原因)的原因,也就是第二层次原因作
为中骨,接着列出第三层次原因 ▪ 根据对结果影响的重要程度,标出重要因素 ▪ 在魚骨图中标出必要信息 ▪ 注意事项:
▪ 二、5W1H法(what where when why who ▪ 三、4M1E法(人、机、料、法、环、测量) ▪ 四、系统图法
how)
所 谓
WHY:为什么必要 WHAT:目的何在 WHERE:在何处做
51
W
WHEN:何时做
就是H
WHO:谁來做 HOW:如何做
质量异常原因分析篇:手把手教你如何使用鱼骨图(实用干货)
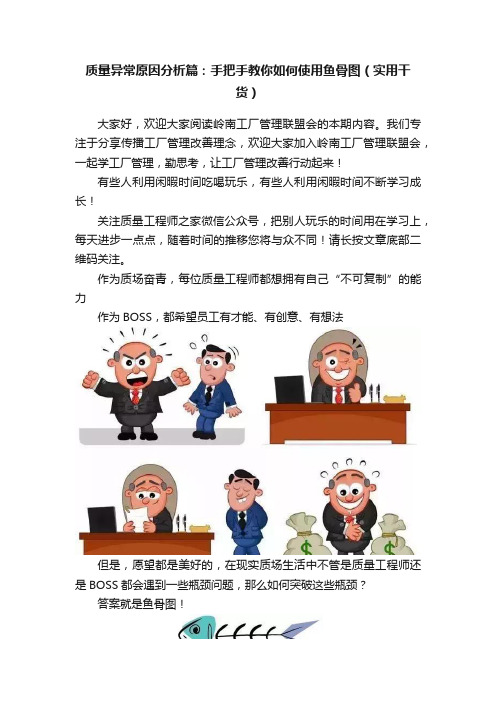
质量异常原因分析篇:手把手教你如何使用鱼骨图(实用干货)大家好,欢迎大家阅读岭南工厂管理联盟会的本期内容。
我们专注于分享传播工厂管理改善理念,欢迎大家加入岭南工厂管理联盟会,一起学工厂管理,勤思考,让工厂管理改善行动起来!有些人利用闲暇时间吃喝玩乐,有些人利用闲暇时间不断学习成长!关注质量工程师之家微信公众号,把别人玩乐的时间用在学习上,每天进步一点点,随着时间的推移您将与众不同!请长按文章底部二维码关注。
作为质场奋青,每位质量工程师都想拥有自己“不可复制”的能力作为BOSS,都希望员工有才能、有创意、有想法但是,愿望都是美好的,在现实质场生活中不管是质量工程师还是BOSS都会遇到一些瓶颈问题,那么如何突破这些瓶颈?答案就是鱼骨图!第一部分鱼骨图分析法介绍1、鱼骨图的由来及含义鱼骨图是由日本管理大师石川馨先生所发明出来的,故又名石川图。
鱼骨图是一种发现问题“根本原因”的方法,它也可以称之为“Ishikawa”或者“因果图”。
问题的特性总是受到一些因素的影响,我们通过头脑风暴法找出这些因素,并将它们与特性值一起,按相互关联性整理而成的层次分明、条理清楚,并标出重要因素的图形就叫特性要因图。
因其形状如鱼骨,所以又叫鱼骨图(以下称鱼骨图),它是一种透过现象看本质的分析方法。
同时,鱼骨图也用在生产中,用来形象地表示生产车间的流程。
2、鱼骨图的三种类型A、整理问题型鱼骨图(各要素与特性值间不存在原因关系,而是结构构成关系)B、原因型鱼骨图(鱼头在右,特性值通常以“为什么……”来写)C、对策型鱼骨图(鱼头在左,特性值通常以“如何提高/改善……”来写)第二部分鱼骨图的绘作和使用一、鱼骨图的制作1、分析问题原因/结构A、针对问题点,选择层别方法(如:人、机、料、法、环等)B、按头脑风暴分别对各层别类别找出所有可能原因(因素)C、将找出的各要素进行归类、整理,明确其从属关系D、分析选取重要因素E、检查各要素的描述方法,确保语法简明、意思明确2、分析要点a、确定大要因(大骨)时,现场作业一般从“人机料法环”着手,管理类问题一般从“人事时地物”层别,应视具体情况决定。
各种鱼骨图

来料
环境
WII
裂DIE
人
机器
实用文档
(鱼骨图)尾数混料
人
未确认尾数印字
机
扎LOT不干净留有上LOT原
Rofine laser第一粒无印字
子粒子目检员工未检出机器卡原子粒
转有字/无字未确认
混原子粒
补尾数料中有字 无字相混 未行空带 未行空带
光线不足 包装人员未检查尾数
料 ComB LOT相混
法
环
噪音太大
实用文档
环境
料 法
产品之间相互
机器之间间 距窄
做假检查记录
pass
不按程序做走捷径
混 料
灯光不好
同时处理两个LOT
机器不稳定
盛装物料容 新员工多操作不熟练
机器卡原子粒 器未清理
,容易遗漏细节
5S未做好,
自动跳印字
机
员工意识差 开LOT员未核对生产资料 ,选用不正确的程式
机位执LOT不干净
人
实用文档
人 机
员工培训不足 执LOT不干净 忘换字片 拿错字片
跳印字
印
错
字
来料印字面脏
印字看不清
料 组员从人,机,实料用分文档析了关于印错字的可能原因
贴错Label问题分析鱼骨图
Man
补打Label未检 查和核对仔细
机位未仔细核对
Machin e
包装前后未核对好资料
出Lot时未 仔细核对
新员工品质意识 和技能不够
Material
Metho d
Environment
实用文档
QA REJ&上带退料问题用鱼骨图分析:
人
机
鱼骨图排列图
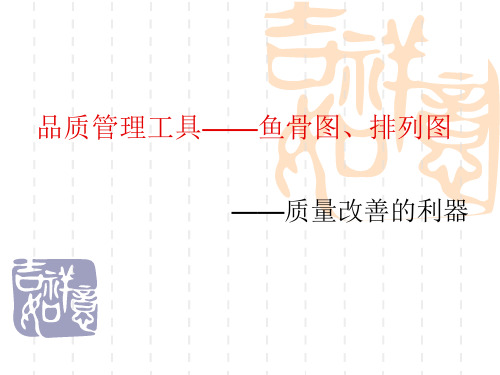
完善相关 品质系统
导入品管 新技术
提升品管 人员素质
相关产品 购买读码器
参观兄弟单位5次
改善系统 导入SPC 流程改善 文件
100%认 开始研究 证上岗 APQP
教育培训 140hr/人/年
达 成
组织学习FMEA 改善品质
IPQC与FQC 换岗学习
年
记录稽核
度
每日首件确认
首件确认 情况反馈
随时问题反馈 工艺问 题反馈
➢ 严禁批评他人的构想和意見. ➢ 意见愈多愈好. ➢ 欢迎自由奔放的构想. ➢ 顺着他人的创意或意见发展自已的创意.
用逻辑推理法制作特性要因图
▪ 确定品质的特征 ▪ 将品质特性写在纸的右侧,从左至右画一箭头(主骨),将结
果用方框框上. ▪ 列出影响大骨(主要原因)的原因,也就是第二层次原因作
为中骨,接着列出第三层次原因 ▪ 根据对结果影响的重要程度,标出重要因素 ▪ 在魚骨图中标出必要信息 ▪ 注意事项:
▪ 按表1的表头计算累计频
数和累计百分比。并填入
宣传推广费
其他
14.3 59
243 302
统计表2中。
Total
302
11.1
60.1
10.1
70.2
5.4
75.6
4.7
80.5
19.5
100
表2
排列图的作图法
▪ 绘制排列图
➢ 画横坐标,标出项目的等分刻度。本例共七个 项目。按统计表的序号,从左到右,在每个刻 度间距下填写每个项目的名称,
为什么 饭菜不 好吃?
特性要因图之画法
三、原因分类成几个大类,并且圈起來---中骨 四、加上箭头的大分枝,约60°插到母线--子枝
5S鱼骨图

设备
设备移动 不方便
工装操
休息或空闲 时间无管控
人员Biblioteka 开展的活不能够维持5S成果 没有良好的5S意识 人员执行力不强
没有专业人员
设备设计 不合理 设备点检 不到位
管理人员 不重视 没有持续
没有系统的5S培训
没有保护产品和 车间物品的意识
没有培训材料
来料包装 不合理 来料包装 没有5S
良品不良品的 区分不明确
5S的点检表分 类不够详细
5S现状 分析
人员搬运物料的方
5S作业的方法不明
物料
物料部件
方法
垃圾处理的流程不
鱼骨图分析培训教材
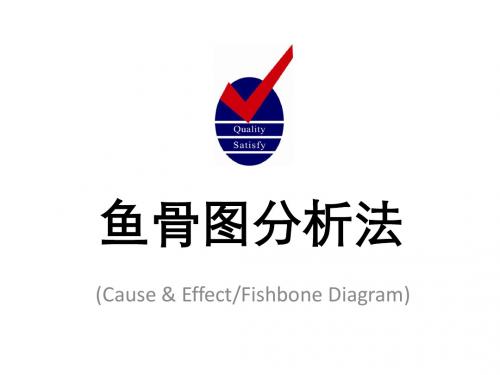
大骨
孙骨
4
小骨
曾孙骨
中骨
鱼骨图分析方法培训
⑤记入中骨、小骨、孙骨的“要点”。
• 要因记入 [没有对策的反馈」。 例:「没有照明」 「没有报警」 「学习不足」 「没有盖子」 「没有干劲」 「注意不足」
• 反复寻找为什么,摸索探询的话比较好
• 要因是 「主语+谓语」的形式比较好。
例:「软管 → 软管长」 「涂料 → 涂料飞溅」
不知道是不良品,所以放任自流
所以
鱼骨图分析方法培训
特性:例4
改善活动不活泼
不能发现职场的问题点 只教授自工程作业 没有作业训练计划 不了解前后工程 提案件数少
临时工 不活泼是为什么 事实 件数少是为什么 推定 不能发现是为什么 推定 不了解作业是为什么 推定 不教授是为什么 推定 没有作业训练计划 只教授自工程作业 不了解前后工程 不能发现问题点
原因。
• 下面介绍一种分析方法,教我们如何正确找出产生问题 的真正原因。
鱼骨图
(Cause & Effect/Fishbone Diagram)
鱼骨图是由日本管理大师石川馨先生所发展出 来的,故又名石川图。 鱼骨图是一种发现问题“根本原因”的方法, 它也可以称之为“因果图”。 因其形状如鱼骨,又叫鱼骨图。 它是一种透过现象看本质的分析方法。
中骨【事实】 所以
改善提案件数少
所以 所以 所以 所以
鱼骨图分析方法培训
特性:例5
区别针安装不良多
枪的打点方法不好 反手拉设备 皮坐椅上有褶皱 打时身体倾斜 区别针开了
方法 不良过多是为什么 事实 为什么开了 推定 为什打的方法不好 推定 为什么身体倾斜 推定 为什么反手拉设备 推定 皮坐椅上有褶皱 反手拉设备 打时身体倾斜 枪的打点方法不好
鱼骨图图参考案例

3
无塑壳残留
3.1蒋其丰 3.2罗刚 3.3蒋其丰
8月30日
何毅
乐捐300元
9
全塑型产品≤6天行动计划表
序 号 行动举措 成果要求 责任 人 完成时间 检查人 未完成赞助
4
出现品质异常时要求质保中心 和技术开发中心在10分钟内必 须到达发生现场,30分钟内提 出解决方案,如无法解决者在2 小时内出应急预案,并在一天 内回复永久解决措施
朱继军 各工序 工序长
7.15日完 成 7. 20日起 执行
何毅
俯卧撑30个
朱继军
俯卧撑30个
14
采用拉动式生产系统,准时制生产方式(JIT) 14.1制定拉动式生产系统培训资料(PPT),在 7月10日完成 14.2对所有工序长、带班、库管员进行拉动式 生产系统培训并做好培训记录,在7月20日完成 14.3从8月1日起实施 14.4在9月1日验证
13.采购根据技术研发中心制定 的材料要求开发两家以上最优 材料供应商进行采购,不得随 意更换供应商
10、技术开发部严格审核工艺,确 定无误后再下发生产部门
14.指定专门检验员对铜片来料严格按照 工艺要求用“V”型块进行测量,确保铜 片无毛刺、无弯曲现象,侧面光滑、铜 片无铜粉,如有以上一项不符合严格按 照内部供应连制度执行
7、要求一分厂对常规、 通用铜片建立铜片超市
5、制定特殊人员的应 急预案(多能工培养)
17、制定水、电、气 、火灾的应急预案
14、采用拉动式生 产系统,准时制生 产方式(JIT) 15、要求计划物控中心按公司 规定下达特殊订单≤5个/月
12、接到订单三天内验证一切 生产辅料,并填写作业前准备 记录表上交生产计划员处
成果要求
鱼骨图图参考案例
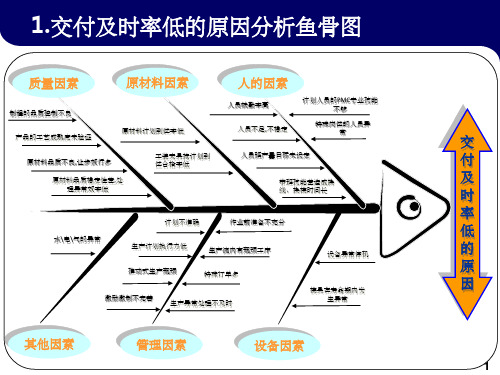
各工序长
从7月1日 持续
王在超 吴新波
俯卧撑20 个
每季度末对工序长、带班进行一次快速换模培训
4
4.1. .按工序制作快速换模培训资料(PPT)在8月10日前完 成 4.2.在9月28日完成第一次的快速换模专业技能培训并形 成记录
提高换线、换 模速度,减少 员工等待时间
2.3. 验证培训效果,10月30日完成
满足工艺要求
品质保障
工艺保障
影 响 全 塑 型 产 品 交 期 的 原 因
7
1.1.全塑型产品交期≤6天对策鱼骨图 注:紫色字体为重点
模具、设备保障
品质保障
排片保障
1.保证无塑壳残留的情况下,取
6.开发中心和精密事业制造部所设计 和制造的模具所生产的全塑型产品同 心度达到≤0.05mm,外径≤ 0.04mm,端 面无粉皮、钩子两侧无粉皮,无气孔
质量保障
原材料保障
人员保障
3、各工序长每天对每 位员工进行班产量考核
1、增加计件产品单价,提高员工福利
8、原材料质量不 良让步放行每月不 超过2批次
6、实行外部供应链管理
4、每季度末对带班 进行快速换模培训
2、每季度初对计划员进行PMC专 业技能培训
交 付
9、提高检验员巡检频次
及
从原来两小时一次提升 为1.5小时一次,防止大
提高员工薪资 待遇,使员工 流失率≤8%
1.1-1.2朱 继军1.3方
玉波
7月30日 前
1.3.人力资源中心在7月30日前完成审批并下发至分厂执
行
何毅
乐捐100元
每季度初对2名计划员进行PMC专业技能培训 2.1.制作PMC培训资料(PPT)在6月30日前完成 2 2.2.在7月10日完成第一次的PMC专业技能培训并形成记 录
错漏反原因分析-鱼骨图

收尾不彻底、两款产品同时放 线
机 方法
奖惩不分明、作 业员无积极性
环境
ቤተ መጻሕፍቲ ባይዱ
材料
材料标识错误
线后,未分类标识放
错漏反频频发生
工资待遇低, 作业环境差 车间区域划分不明 确,无尾数区、返 修区 加班多、作业员 不能充分休息 工艺不平衡、产品堆积
环境
人员 作业员变动频繁,技能不 足,缺乏培训,且未经考 核上岗 管理(班组长)人员,安排人员时 未对作业员的能力做充分评估, 且安排后未对作业员的作业成果 进行检查 作业员品质意识差,无自检互检意 识,无视上工序产生的不良 机台本身无防呆及报警 装置,出现错漏反不能 及时报警 机台老化 自动化程 度低
管理人员,对现场管控不到位,对 于所在区域存在的品质隐患没有及 时处理,解决; 来料错误、混料 材料设计缺陷、不易区分
材料
材料标识错误 物料上线后,未分类标识放 置 作业方法不当,未对易产 生错漏反的物料点数防呆 未按照SOP要求操 作
工资待遇低, 作业环境差 车间区域划分不明 确,无尾数区、返 修区
鱼骨图分析讲解

测量 误差大
比例界限 范围大
润滑油 配比不准
作图步骤:
1) 明确问题的内容; 2) 确定与问题相关的方面(人、机、料、 法、环)或过程或主要在原因;
3) 从问题这个结果出发,依靠与会人员集 思广益,由表及里,逐步深入,列明所 有可能的原因项目; 4) 根椐所列明的项目,加以比较讨论或以与 会人员投票方式,确定问题的主要原因 (作适当标识)为止。
案例分析:
机器
不规范 老化 冲床 损坏
6.此项应归属“机器”方 7.此项与“机器”无包含关 面; 系; 8.选定项目应为最底层内容; 9.划水平线与60度斜线;
7 3
设备 未保养 损坏
2人 4
杂事多
新人 经验少 技术不足 凭经验 怕麻烦 意识差 作业不规范 偷懒 怕累
9
漏油
能力不足 心情不好
5
无标准 夹料 未教育 调整方法不统一
其他因素者 1.异常材料的突然入侵. 2.日夜班精神上的困扰等. 3.工作人员的疏忽. 4.未按操作标准作业. 5.机械的自然磨损. 6.操作条件的突然变化. 7.计算的错误. 8.操作标准不完备. 9.不随机抽样法.
此诸原因常在管制图上出现,如有系统 可寻,则利用分层方法加以分析;如不规 则出现,则易被发现,而予以消除.
5 5 天 天 结 结 帐 帐 问 问 题 题
其他
工作
管理
■因果图
用电量
照明用电未控制 空压机用电量大
案例4 案例4 设备科
电价
生活用电未控制 柴油价格高 市电、 市电、发电比例不当 生产设备用电浪费 中央空调用电量大
水电费过高
发电机用水量大 空调用水量大 生活用水量大
用水量
特性要因圖
错漏反原因分析 鱼骨图

材料
材料设计缺
机台本身无防呆及报警装 置,出现错漏反不能及时
机台老化自动 化程度低
作业方法不当,未对易产生错 漏反的物料点数防呆
工资待遇低,作
未按照SOP要求操作
车间区域划分不明确, 无尾数区、返修区
收尾不彻底、两款产品同时放线
奖惩不分明、作业
机
方法
环境
材料
材料标识错误
后,未分类标识放置
错漏反频频发生
工资待遇低,作
车间区域划分不明确, 无尾数区、返修区
加班多、作业员不 工艺不平衡、产品堆积
环境
人员
作业员变动频繁,技能不足, 缺乏培训,且未经考核上岗
管理(班组长)人员,安排人员时未 对作业员的能力做充分评估,且安 排后未对作业员的作业成果进行检
作业员品质意识差,无自检互检意识, 无视上工序产生的不良
管理人员,对现场管控不到位,对于 所在区域存在的品质隐患没有及时处 理,解决;
来料错误、混料
TFT结构不良鱼骨图

②内部RA实验条件 加严,检测频率提高
*②同原因引起 不良及时规避
整机干涉
检测加严
经验总结
白 斑 白 点 不 良 改 善 目 标
上一年30%
<8%
/
பைடு நூலகம்
3、鱼骨图
设计优化
*①提升产品结构强度 *②加大受力
下压空隙 *③优化产品平整度
选材改进
*②LCD选用市场上大量 在使用的成熟资源
*①TP盖板使用厚度≥0.7t
*②同原因引起 不良及时规避
检测加严
经验总结
上一年15%
*②框贴结构口子胶 压住偏光片0.4mm
*④背光遮光胶和 胶框之间间隙
*①LCD选用边框≥1.2mm资源
漏
光
*③框贴结构口子胶 *⑤导光板的
厚度不超过0.5mm
边缘效果处理
②背光遮光胶选用 粘性较强的黑黑胶
不 良
改
善
①不良总结培训,
目
①对背光、LCD来料
经验共享
标
严格检测、管控
<5%
②样品阶段暗房环境下 多角度进行检测
①前壳中框与LCM 背面的预留空隙
①对来料平整性的 严格检测、管控
①不良总结培训, 经验共享
②前壳平整度, 与FPC焊盘等的干涉
②样品阶段提高 按压强度进行测试
*②同原因引起 不良及时规避
整机干涉
检测加严
经验总结
水 波 纹 不 良 改 善 目 标
上一年20%
<6%
3、鱼骨图
设计优化
选材改进
*①TP VA距离LCD边缘≥0.8mm
3、鱼骨图
设计优化 *①提升产品结构强度
不合格品管控-PDCAPPT课件
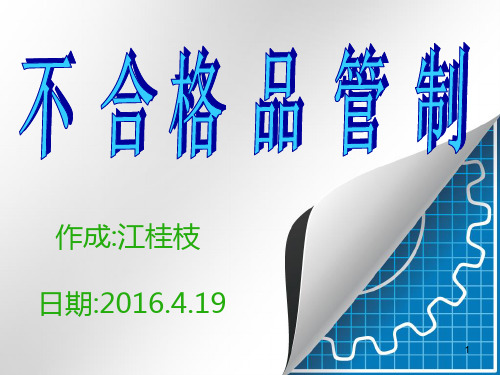
不合格品的控制
5
产品需分类做好标示
6
严防误用或误装!!!!
不合格品隔离.doc
7
品质异常联络单
全检结果联络单
8
6 当量较大时,或对公司信誉和资金等有一定影响时需组织相关部门 相关人员对不合格品进行评审,最终以评审的结果进行处置.
纠正 纠正
9
10
鱼骨图分析法
11
12
13
14
15作成:江桂枝 日期:216.4.191什么是不合格品/为什么管制?
不合格品给生产带来以下影响:
2
不合格品处理不当存在的隐患
3
不合格品发生的类型
一,按来源分: 来料不良,制造不良,设计不良
二,按性能分: 外观不良,功能不良,尺寸不良
三,按数量分: 偶发不良,批量不良
四,按原因分: 人为因素和非人为因素(鱼骨图分析)
16
17
18
SMT常见不良鱼骨图分析ppt课件

過久 劑含 徑過 過期 度 屬性
量大
高低
吃錫
印刷 角度 刮刀 壓力 速度
精度 不夠
行程 不足
印刷 厚度
錫膏 印刷
不良
不佳 不平 不當 過快 刮刀
錫膏機
變形 硬度 平行度 不佳
間隙 錫量 參數設 脫模 不當 不足 定不當 速度
軌道 爐膛
張力 表面 開口 鋼板
過長
錫膏廠商
上料不 冷卻 速度 內有 溫區
不足 磨損 粗糙 厚度
PCB
濕度影響 錫膏特性
包裝後氧化 灰塵多 靜電排放
熟練程度 手放散料
鋼板未擦拭干淨 鋼板
缺乏品質意識
開口
開口
PCB PAD兩邊 有異 零件規格與 PAD 變形 不一致 物 PAD不符 氧化
錫膏添加不及時 鋼板未及時清洗 零件掉落地上
缺錫
形狀 方式
零件 過大 過重
丟失零件 找回後重 新使用
腳 彎
厚度差異 零件 過保
氧化 有異 有損 位置
不良
物
不當
通設風備溫手備度印料手高厚時印薄料台手手不帶錫手印印均過膏放手台缺力緊作散上抹搖錫度態料錫錫動不度不膏夠/均情I緒PA上 用手錫 量放手量 過錫零印過 多膏手件錫多 添印P位膏C加錫B移位印不尖移刷及過零狀時長件況檢受 潮查不吃錫性關夠仔元細過周期件與重量P零PAA件DD不 吃有符錫一不邊特良殊退距零冰不件時夠間有異物新屬 低金性零助焊劑使時長件用間厚存條不度黏度高放件好不錫變錫本特均膏干膏身性暮錫膏
機器置件不穩定 MTU振動過大
加熱器風量過大 料架振動過大
SOP不完善
操作不正確
MTU吸空Tray時將 下層零件吸繙面
料架推料過快
鱼骨图20190530

MEBody
Wenhua Li
19/11/2019 Strictly Confidential V1.0
6 7…
5
3
…
4
1
2
特性
主骨
特性
ME培员工参与度低
4
ES8四门外漏铝焊针/缩孔原因分析
机
电极帽
设计/材 质不合
理
修磨参 机器人
问 题
焊枪正负极设定不合 理
板间间隙异常
/
图例
现场可控因素
反向作用
CLD Seal Margin
能量损失
设计因素
设计啮合力
胶条反力
安装误差:上下铰链同轴度
不 利
锁扣/锁舌啮合力
车体排气面积 胶条空气压阻
因 素
安装误差:锁舌/锁扣Z向误差
气阻
排气阀面积
设计摩擦损耗
限位器摩擦
安装误差:侧围与门安装点Z向误差
设计摩擦损耗
有 利
铰链倾角
限位器助力
因
车门重力作用
素
质量 重心
关门能量分解(VE仿真计算)
正向作用
铰链摩擦
关 门 能 量
• 影响因素分析 有利因素主要为车门重力作用 不利因素主要为整车气阻和胶条反力
• 优化方向 降低胶条反力 降低安装误差------待现场调查
机
人
环
工装base及 传感器支架 位置不合理
差
板材表面 杂质,灰
尘
零件过期材料 性能无法保证
胶体流动性差
结构胶性 能不达标
料
修磨点数设 置不合理
焊接工艺焊接 顺序不合理
焊接参数 设置不合理 材料问题