棒材四切分问题及解决方法
四切分技术培训笔记
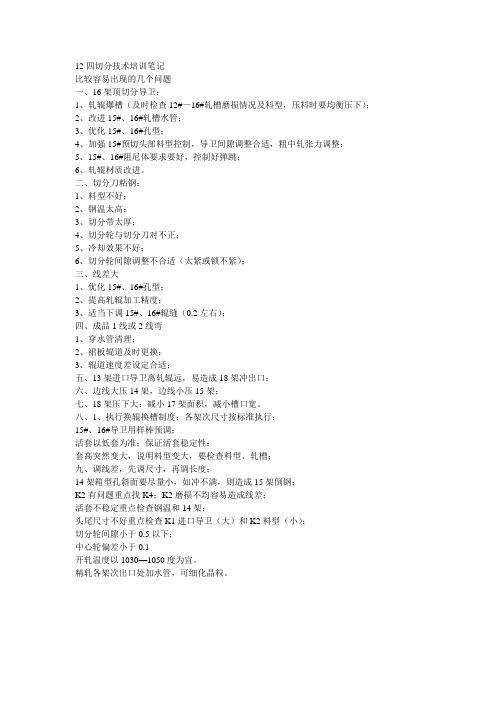
12四切分技术培训笔记比较容易出现的几个问题一、16架顶切分导卫:1、轧辊爆槽(及时检查12#—16#轧槽磨损情况及料型,压料时要均衡压下);2、改进15#、16#轧槽水管;3、优化15#、16#孔型;4、加强15#预切头部料型控制,导卫间隙调整合适,粗中轧张力调整;5、15#、16#阻尼体要求要好,控制好弹跳;6、轧辊材质改进。
二、切分刀粘钢:1、料型不好;2、钢温太高;3、切分带太厚;4、切分轮与切分刀对不正;5、冷却效果不好;6、切分轮间隙调整不合适(太紧或锁不紧);三、线差大1、优化15#、16#孔型;2、提高轧辊加工精度;3、适当下调15#、16#辊缝(0.2左右);四、成品1线或2线弯1、穿水管清理;2、裙板辊道及时更换;3、辊道速度差设定合适;五、13架进口导卫离轧辊远,易造成18架冲出口;六、边线大压14架,边线小压15架;七、18架压下大:减小17架面积,减小槽口宽。
八、1、执行换辊换槽制度;各架次尺寸按标准执行;15#、16#导卫用样棒预调;活套以低套为准;保证活套稳定性;套高突然变大,说明料型变大,要检查料型、轧槽;九、调线差,先调尺寸,再调长度;14架箱型孔斜面要尽量小,如冲不满,则造成15架倒钢;K2有问题重点找K4;K2磨损不均容易造成线差;活套不稳定重点检查钢温和14架;头尾尺寸不好重点检查K1进口导卫(大)和K2料型(小);切分轮间隙小于0.5以下;中心轮偏差小于0.1开轧温度以1030—1050度为宜。
精轧各架次出口处加水管,可细化晶粒。
棒材生产切分工艺的优化与应用
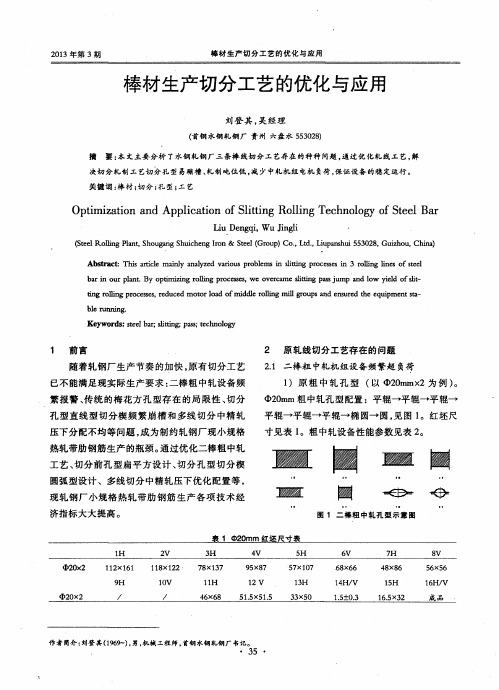
决 切 分 轧 制 工 艺 切 分 孔 型 易 蹦槽 、 轧 制 吨 位低 , 减 少 中轧机 组 电机 负荷 , 保 证 设 备 的稳 定 运行 。 关键词 : 棒材 ; 切分 ; 孔型 ; 工艺
Op t i mi z a t i o n a n d Ap p l i c a t i o n o f S l i t t i n g Ro l l i n g T e c h n o l o g y o f S t e e l B a r
时达 到 1 4 O %( 非 轧件 头 部 ) ; ( 2 )钢坯 加 热 温 度 高, 加 热 炉燃 耗 大 ; ( 3 ) 轧 线 影 响时 间 长 、 机 时 产 量低 、 轧机 作业 率低 。 3 ) 原 因分 析 。( 1 ) 进粗 轧温 度为 9 8 0  ̄ C 时, 粗 中轧 轧 机负 荷见 表 3 。从 表 3中以可 看 出 , 生 产
盈
《# 》 }
图 1 二 棒粗 中轧 孔 型 示 意 图
0 mm 红坯 尺寸 表
作 者 简介 : 刘登其( 1 9 6 9  ̄ ) , 男, 机械工程师 。 首钢水钢轧钢厂书记。 35 ・
・
水 钢 科技 S HU I G A NG S C I E NC E& T E C H N O L O G Y
b a r i n o u r p l nt a . B y o p t i mi z i n g r o l l i n g p r o c e  ̄ e s , we o v e r c a me s l i t t i n g p a s s j u mp a n d l o w y i d d o f s l i t -
第1 2 5期
2 ) - 棒 生 产 中存 在 的问题 。( 1 ) 轧制过 程 中
四切分轧制Ф12mm螺成品勾头冲出口故障的处理
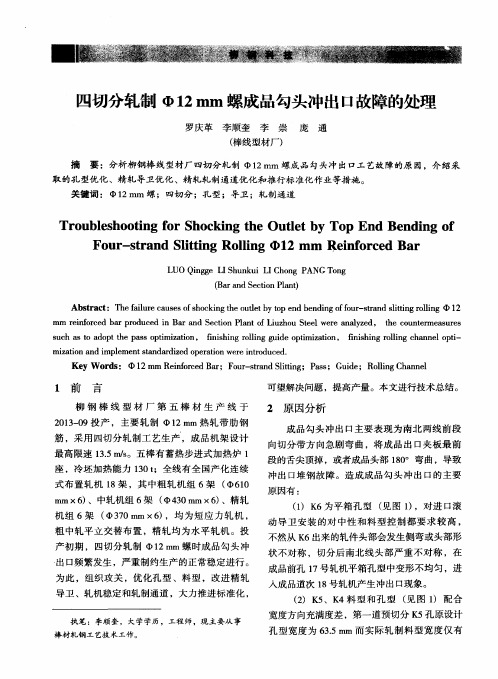
2 原 因分析
成 品勾头冲 出口主要表现为南北两线前段
向切 分 带 方 向急 剧 弯 曲 ,将 成 品 出 口夹 板 最 前
段 的舌 尖顶 掉 ,或者 成 品头部 1 8 0 。 弯 曲 ,导致
座 ,冷 坯 加 热 能 力 1 3 0 t ;全 线 有 全 国产 化 连 续 式布置轧机 1 8架 ,其 性 和 料 型 控 制 都 要 求 较 高 , 不然 从 K 6出来 的轧 件 头部 会发 生侧 弯 或 头部 形 状 不 对 称 ,切 分 后 南 北 线 头 部 严 重 不 对 称 ,在
出 口频繁发生 ,严重制约生产的正常稳定进行。
为 此 ,组织 攻 关 ,优 化 孔 型 、料 型 ,改 进 精 轧 导卫 、轧机 稳定 和轧制 通 道 ,大 力推 进 标 准化 ,
Fo u r - s t r a n d S l i t t i n g Ro l l i n g 01 2 m m Re i n f o r c e d Ba r
L U O Q i n g g e L I S h u n k u i L I C h o n g P A NG T o n g ( B a r a n d S e c t i o n P l nt a )
1 前
言
可 望解决 问题 ,提 高产 量 。本 文进行 技 术总 结 。
柳 钢 棒 线 型 材 厂 第 五 棒 材 生 产 线 于 2 0 1 3 — 0 9投 产 ,主要 轧 制 ①1 2 m m 热 轧 带 肋 钢 筋 ,采 用 四切 分 轧 制 工 艺 生产 ,成 品 机架 设 计
Ke y W o r d s :
带肋钢筋四切分轧制常见故障及处理措施(酒钢科技)
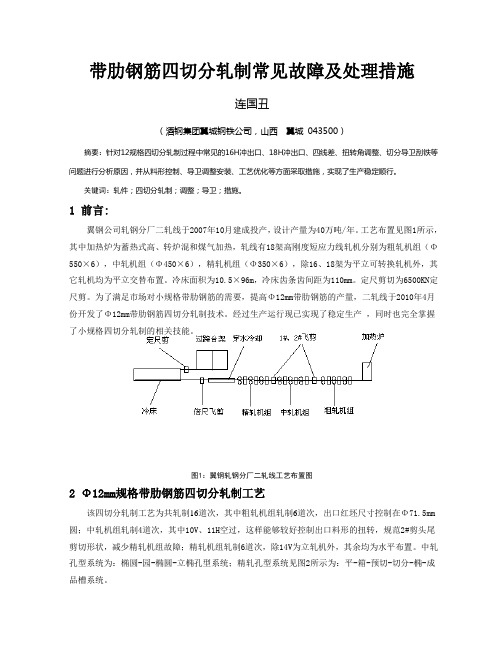
带肋钢筋四切分轧制常见故障及处理措施连国丑(酒钢集团翼城钢铁公司,山西翼城043500)摘要:针对12规格四切分轧制过程中常见的16H冲出口、18H冲出口、四线差、扭转角调整、切分导卫刮铁等问题进行分析原因,并从料形控制、导卫调整安装、工艺优化等方面采取措施,实现了生产稳定顺行。
关键词:轧件;四切分轧制;调整;导卫;措施。
1 前言:翼钢公司轧钢分厂二轧线于2007年10月建成投产,设计产量为40万吨/年。
工艺布置见图1所示,其中加热炉为蓄热式高、转炉混和煤气加热,轧线有18架高刚度短应力线轧机分别为粗轧机组(Φ550×6),中轧机组(Φ450×6),精轧机组(Φ350×6),除16、18架为平立可转换轧机外,其它轧机均为平立交替布置。
冷床面积为10.5×96m,冷床齿条齿间距为110mm。
定尺剪切为6500KN定尺剪。
为了满足市场对小规格带肋钢筋的需要,提高Φ12mm带肋钢筋的产量,二轧线于2010年4月份开发了Φ12mm带肋钢筋四切分轧制技术。
经过生产运行现已实现了稳定生产,同时也完全掌握了小规格四切分轧制的相关技能。
图1:翼钢轧钢分厂二轧线工艺布置图2 Φ12mm规格带肋钢筋四切分轧制工艺该四切分轧制工艺为共轧制16道次,其中粗轧机组轧制6道次,出口红坯尺寸控制在Φ71.5mm 圆;中轧机组轧制4道次,其中10V、11H空过,这样能够较好控制出口料形的扭转,规范2#剪头尾剪切形状,减少精轧机组故障;精轧机组轧制6道次,除14V为立轧机外,其余均为水平布置。
中轧孔型系统为:椭圆-园-椭圆-立椭孔型系统;精轧孔型系统见图2所示为:平-箱-预切-切分-椭-成品槽系统。
图2:精轧机组孔型系统3 常见故障分析:四切分轧制固然能大幅度提升小规格带肋钢筋的产量,但因其工艺的复杂对设备性能,生产准备,导卫安装调整,料形的精准控制,张力调整和钢温等过程控制的要求非常高。
Φ12mm热轧带肋钢筋四线切分轧制工艺存在问题及解决措施

度 是 固定 的 , 而起 套辊起 套后 轧件 高度是 变 化 的 , 导
致 活套起 套后 轧件 经压 辊导 向与 下一架次 进 口导 板 发 生摩 擦 。 () 2 导板 无 冷 却水 , 件 与 导 板 摩 擦 后 导 板 温 轧
度过高 。
( ) D E双 排 导 卫 导 板 上 下 配 合 后 插 入 导 34 4
s i us w o e i r v s ero r n g oo e .
Ke o ds: ot—r ln yW r h olig;fn s i g r li i ih n olng; p o e sp o lm ;m e s r s r c s r b e aue
1
前 言
总第 11 9 期 21 0 1年 第 1 1期
河 北冶金
H EBE M E AL U R GY I T L
Toa l l tl 9
2 01 , u b r 1 1 N m e 1
1 mm 热 轧 带肋 钢 筋 2 四线切 分 轧 制 工 艺存 在 问题 及 解 决 措 施
轴窜 。
造成 切分架 次 出 口堆钢 的 主要 原 因有 切偏 头 、 切分 刀粘 钢等 。
9 . % 。针对 生产 初 期存 在 的粘 钢 、 钢等 问题 进 71 堆 行 了改 进 , 得 了 比较好 的效 果 。 取
2 四 线 切 分 轧 制 原 理
架 , 中 1 、8 2 其 6 1 、0架 为平 立 可转换 轧 机 , 、 粗 中轧 机
组 出 口设 有 1 、 # # 2 飞剪 , 于 轧制 过 程 中切 头 尾 和 用
收 稿 E 期 :0 1 7— O t 2 1 —0 2
的两切 分 , 过 这 两 个 步骤 实 现 四线 切 分 。与 传 统 通 的单 线 轧制工 艺 和二 、 线切 分轧 制工艺 相 比较 , 三 四
制棒过程中常出现问题以及解决的方法

制棒过程中常出现问题以及解决的方法制棒过程中常出现问题以及解决的方法1、出棒粗糙、烟多且从棒的四周冒烟气,继而不出棒:原料过干、温度过高或螺杆与套筒配合间隙过大。
2、出棒密度差且速度快:螺杆调整过长或温度过高。
3、出棒不顺利且放炮:原料过湿、温度过低或配合间隙不合适。
4、不出棒且螺杆拧住:温度太低、螺旋过矮或磨损。
5、不出棒而螺杆空转:螺杆太短或已磨损。
6、出棒有硬度、密度,但一折就断且断面有亮光:螺旋前沿初始处过高过陡。
7、返气:原料太湿或因其它原因不走棒时机器长时间空转。
8、弯棒:原料湿度稍大。
9、同样的原料用在两台制棒机上,在一台上好用而在另一台上不好用甚至无法用:套筒和螺杆配合间隙不合适。
10、同样原料而换螺杆后出棒速度变慢:螺杆第一道螺旋过高。
11、温度高了炭化、低了不走棒:套筒磨损严重。
12、堵眼、不断放炮、出棒太慢或不正常:螺旋前沿跟部、螺旋前沿磨损严重或套筒磨损严重。
特别提醒:出棒不正常,一般与原料和原料的干湿度、螺杆在套筒内的长短度(配合间隙)、制棒时加热温度的高低有关。
要准确把握好“三度”,需要一段时间的摸索。
机制炭常见问题解常见问题解答:1、机制木炭技术有何特殊要求,比如操作人的文化程度和相专业知识水平?答:技术有一定难度,但没有太特殊的要求,生产流程中不同环节对人员要求不同。
1.原料采购和烘干环节使用的是不怕脏不怕累的为好。
2.制棒环节使用年轻一些的最好,需要的是有一定接受和理解能力和反应快,能随机应变的人,可以说有些象司机这职业。
3.烧炭的要至少一个责任心强一些的,能指挥别人,休息时间能不固定的人,所以上岁数的会好一些。
4.成品检验和包装需要的是认真负责的,最好农村妇女。
5.设备维护(可以兼职),有较好电焊或者气焊基础,有学习能力和钻研精神的。
2、机制木炭全套机器是否需经常维修,易损件是什么,修起来难不难,平均生产一吨要维修费多少?答:如果人员按照技术要领和操作规程去操作的话,只有制棒机是需要经常维修的.烘干和窑等一般不用,易损件是推进器螺杆,也可以包括成型套筒。
四线切分导卫的创新修配法

作者单位 :河北钢铁集 团唐钢公司第二钢轧厂 , 河北 唐山 030 600
切分辊预装
预装要点
为了易 于计 算修 正因切分 辊制造误 差造成 的位
置偏移 , 导辊轴定位侧必须使用厚 度为 4 l 的端盖 , T ml
4 0
念磊 2 1 年第1 曹辱 0 2 期
ቤተ መጻሕፍቲ ባይዱ
修配操 作步骤
备件准备 对 备件做 好清洗 、测量 、筛选分类 ,主要 备件 包括 : 切分辊 、导辊轴 、端盖 、调整 片 、油气管 。
技术装 备投 产后 ,由于 四线切 分导卫 的修 配工艺不 成熟 及技术 水平 的差距 ,四切 分架 次的堆 钢问题一 直是制约 1 螺 生产 的关键环节 。为降低导卫 的投入 2
劳誓经 骝
三 艺 装譬
四线切分导卫的创新修配法
T eNe M eh do o r n sCu t gDie to u p h w t o f u e ti r cin Eq i F Li n
供稿l 良朋/ I i gp n 牛 N U La —eg n
唐 钢棒材 厂引进 的德 国巴登钢铁公 司 四线切分
切分辊预装顺序 图
筛选 ; 精确 预装 ,检 验备件 尺寸 ,对 尺寸有 微量差 异 的备件 合理 组合 进行 装配 ,达到快 速组 装效 果 ; 精密 组装 ,各 预装 部件组装 后仔 细校 验 、调整 ,确 保 达到使用 精度标 准 ; 精细 检验 ,对 组装好 的导 卫
进行 位置精 度及 附件功能 的全 面检查 ,确保 所有 功
费用 ,唐钢决定 由国内厂家进行测绘制造 。
由于 四线 切分 导卫 装配 和 使用 精度 要 求很 高 , 而 国产 导卫在 材质选 用 、加工精 度方 面与进 口导卫
龙钢公司轧钢厂棒二线Φ16四切分轧制工艺浅析

龙钢公司轧钢厂棒二线Φ16 四切分轧制工艺浅析摘要四线切分轧制技术是在两线和三线切分轧制技术的基础上开发的,该工艺是把加热后的坯料先轧制成扁坯,然后再利用孔型系统把扁坯加工成四个断面相同的并联轧件,并在精轧道次上沿纵向将并联轧件切分为四个尺寸面积相同的独立轧件的轧制技术。
四线切分轧制技术的核心是先完成并联轧件的三切分,再完成并联轧件的两切分,通过这两个步骤实现四切分的目的。
四线切分轧制工艺与传统的单线轧制工艺和二、三线切分轧制工艺相比,在坯料控制、导卫调整、速度控制、轧机准备等方面都有更大的难度。
龙钢公司轧钢厂棒二线Φ16 四切分轧制工艺于 2019 年 8 月开发和投产,至今相关工艺已经逐步成熟,产量相对稳定,为以后的小规格五线及以上切分轧制工艺的开发奠定了基础。
关键词:四线切分;轧制技术;孔型系统一、棒线材切分轧制工艺概述切分轧制原理是在轧制过程中,将轧件用轧辊或者其他设备沿纵向切分成两条或多条轧件的一种轧制方式。
(一)发展过程1.年代初期,加拿大钢铁公司国际公司首先应用和发展切分轧制技术,日本钢管公司 ( N K K ) 于 1977 年 3 月由加拿大钢铁公司引进切分轧制新技术生产棒材 , 经过研究改进 , 在东伸钢铁公司姬路厂建立起切分轧制生产线。
1979 年 N K K 公司向国内大安公司和山口平有限公司等出售切分轧制技术 , 该项技术用于生产棒材。
70 年代初期 , 英国在斯德哥尔摩技术研究所专门的 Triplet 轧机上采用立轧法把板坯变成方坯。
首先是在板坯中间轧一条沟槽 , 然后用火焰将板坯切割成两条,最后轧成方坯。
我国从 50 年代起开始应用切分轧制技术,目前多数还是坯料切分,然后生产成型材和线材 , 切分的方式主要是:辊切切分、切分轮切分,现在已着手研究和应用在连轧机组上,充分发挥切分轧制提高生产率等优势。
(二)工艺特点1.生产率高轧制钢坯时的生产率为:⁄(1-2-1)A = 36001轧制成品时的生产率为:⁄(1-2-2)A = 36001式中:A——轧机生产率,t/h;——坯料重量,t;——轧机利用系数;1——轧制周期,s;——成材率,%。
轧钢工个人总结
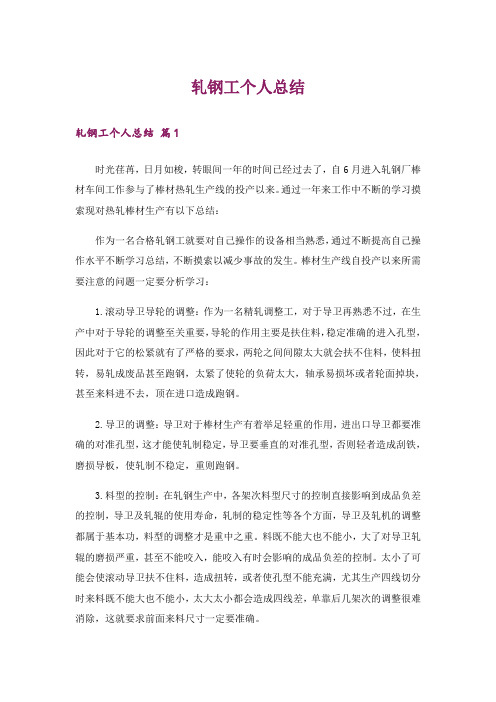
轧钢工个人总结轧钢工个人总结篇1时光荏苒,日月如梭,转眼间一年的时间已经过去了,自6月进入轧钢厂棒材车间工作参与了棒材热轧生产线的投产以来。
通过一年来工作中不断的学习摸索现对热轧棒材生产有以下总结:作为一名合格轧钢工就要对自己操作的设备相当熟悉,通过不断提高自己操作水平不断学习总结,不断摸索以减少事故的发生。
棒材生产线自投产以来所需要注意的问题一定要分析学习:1.滚动导卫导轮的调整:作为一名精轧调整工,对于导卫再熟悉不过,在生产中对于导轮的调整至关重要,导轮的作用主要是扶住料,稳定准确的进入孔型,因此对于它的松紧就有了严格的要求,两轮之间间隙太大就会扶不住料,使料扭转,易轧成废品甚至跑钢,太紧了使轮的负荷太大,轴承易损坏或者轮面掉块,甚至来料进不去,顶在进口造成跑钢。
2.导卫的调整:导卫对于棒材生产有着举足轻重的作用,进出口导卫都要准确的对准孔型,这才能使轧制稳定,导卫要垂直的对准孔型,否则轻者造成刮铁,磨损导板,使轧制不稳定,重则跑钢。
3.料型的控制:在轧钢生产中,各架次料型尺寸的控制直接影响到成品负差的控制,导卫及轧辊的使用寿命,轧制的稳定性等各个方面,导卫及轧机的调整都属于基本功,料型的调整才是重中之重。
料既不能大也不能小,大了对导卫轧辊的磨损严重,甚至不能咬入,能咬入有时会影响的成品负差的控制。
太小了可能会使滚动导卫扶不住料,造成扭转,或者使孔型不能充满,尤其生产四线切分时来料既不能大也不能小,太大太小都会造成四线差,单靠后几架次的调整很难消除,这就要求前面来料尺寸一定要准确。
在棒材生产中还有许多需要注意掌握的知识,如活套器的正确使用,轧机速度的微调,轧机冷却水管的安装布置,跑钢后正确处理事故的方法,以及安全生产的重要性等。
棒材车间以后将以生产四线切分为主,这就要求我们充分的掌握四线切分的操作要领,包括控轧控冷的基本知识,怎样减小甚至消除四线差,怎样消除波浪弯,怎样使成品稳定的上冷床而不跑钢,怎样提高成材率,怎样降本增效,这些都是我们目前亟待解决的问题。
“四切分轧制”的生产技术要点
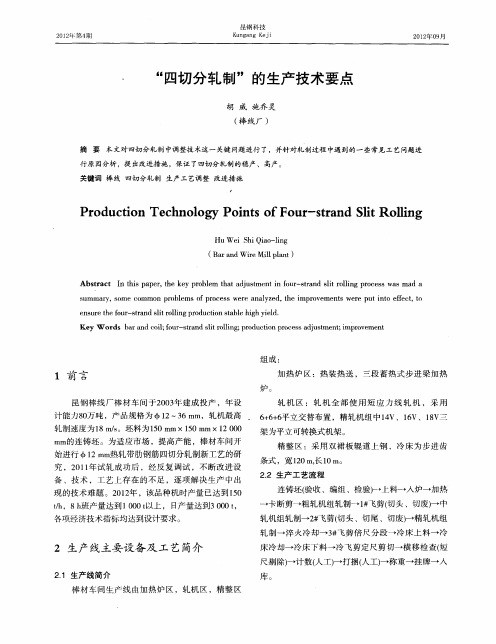
坏 ;2 分刀粘钢 :造成切分刀粘钢主要原因有 :①开 切
轧温度过高 ,切分带形状不规则 ,引起切分刀粘钢 ;
②切分刀被封闭在箱体 内,由于冷却不足 ,刀片两侧
会粘 附氧化铁皮 。③切分箱的安装 必须保证切分 环 、 切分轮 、切分刀三点一线 ,对中 良好 ,若 安装不 正 ,
1 四切 分 生 产 工 艺 相 对 于其 他 钢 种 较 为 复 2 杂 ,对 坯料质 量 、加热温 度及 轧制要 求都 很 高 。特 别 是 轧 制 过 程 中 ,更 是 需 要对 料 形 尺 寸 、轧 制 速 度 、导 卫调整 严格 要求 ,而且 需要 职工过 硬 的操作
水 平 。料形控 制是 四切分 生产 工艺 中最 为重要 的环 节 ,料 型 的控 制 又牵涉 到轧制 温度 、速度 、导 卫 、
H i h Q a—i u We S i i —n olg
( a n r lpa t B r dWi Mi ln ) a e l
Ab ta t nti p p r tek ypo lm a du t n nfu - t n l ol gpo e sw sma sr c I hs a e, h e rbe t t j s h a me t o r sr dsi rln rc s a da i a t i
行 原 因分析 ,提 出改进措施 ,保证 了四切分轧制的稳产 、高产。
关 键 词 棒 线 四切 分 轧制 生产 工 艺调 整 改 进 措 施
Pr u to c no o y Po n so o r。ta d S i Rol od c i n Te h l g i t fF u ‘sr n l l ng - t i
Φ12螺纹钢四切分轧制技术在棒材厂的应用与改进

Φ12螺纹钢四切分轧制技术在棒材厂的应用与改进摘要:本文叙述了棒材厂φ12螺纹钢生产的工艺选择、试轧时出现的问题和工艺改进以及对切分技术的成果分析和切分技术的展望。
关键词:螺纹钢四切分轧制孔型系统导卫1 前言切分轧制是在轧机上利用特殊的轧辊孔型和导卫或者其他切分装置,将原来的一根坯料纵向切成两根以上的轧件,进而轧制多根成品或中间坯的轧制工艺。
采用切分轧制技术可缩短轧制节奏,提高机时产量,显著提高生产效率,降低能耗和成本。
目前棒材φ12mm螺采用三切分轧制工艺,终轧速度为15米/秒,其最高小时产量为57.4支/小时,平均小时产量为50支/小时,平均日产为2380吨/天,与其他规格的平均日产2903—3189吨/天存在较大的差异。
为了更好的发挥切分轧制的经济效益,结合市场对小规格螺纹钢需求量较大的实际,棒材厂决定开展φ12螺纹钢四切分生产工艺改造。
这将大幅度提高小规格产能和生产效率,降低生产成本,提高经济效益。
2 主要设备概况2.1 加热炉加热炉为步进式加热炉,最大加热能力为11Ot/h。
采用钢坯尺寸为150mm ×150mm ×12000mm,重约2075kg。
2.2 轧机一棒轧线上共有20架轧机,粗轧6架550轧机(1-6架)、中轧6架420轧机(7-12架),精轧8架350轧机(7-20架,其中17、18架轧机为平立转换轧机);二棒轧线上共有18架轧机,粗轧6架550轧机(1-6架)、中轧6架420轧机(7-12架),精轧6架350轧机(7-18架),一棒采用平立交替布置,粗、中轧为无扭微张力轧制,精轧采用活套无张力轧制,粗中轧、中精轧之间各有一台飞剪,精轧后设有一台倍尺飞剪。
2.3 冷床冷床为126米齿条步进式冷床,可收集和冷却剪成倍尺的棒材。
2.4 冷剪冷剪剪切能力为850T,可将成排棒材按定尺剪切,剪切范围6~12米。
3 四切分技术的应用与改进四切分轧制,即在轧制过程中通过孔型,将1根轧件轧成具有4个相同形状的并联轧件,再通过切分导卫及孔型将并联轧件沿纵向切分成4个单根轧件。
莱钢12mm热轧带肋钢筋四切分轧制技术的开发
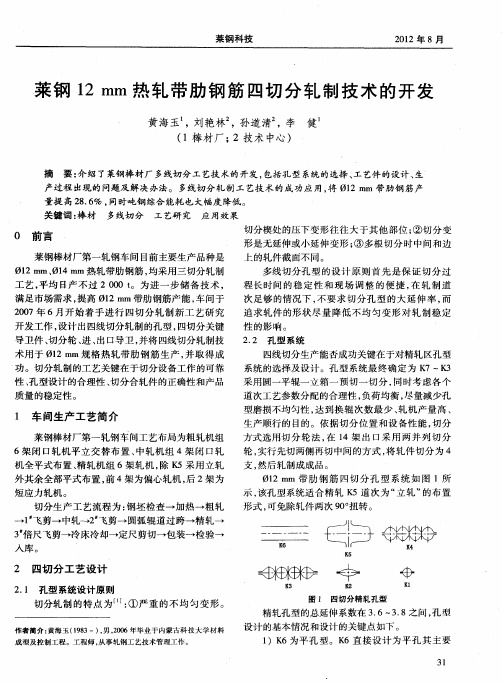
第 4期 ( 总第 10期 ) 6
作用 为将 来料压 宽 。K 6机架 采用 平辊 , 分利 用平 充
辊轧 制 的特点 : 宽 度 限制 、 无 调整 量 大 , 辊 利 用率 轧 高 的 < 5轧件 的
上下 对应 的 , 分楔 两侧 的压下 量是 基本 相 同 的 , 切 即
莱钢 科技
21 0 2年 8月
莱 钢 1 m 热 轧 带 肋 钢 筋 四切 分 轧 制技 术 的开 发 m 2
黄海 玉 ,刘艳林 ,孙道清 ,李 健
( 1棒材厂 ; 2技术 中心)
摘
要 : 绍 了莱钢棒 材 厂 多线切 分 工 艺技 术的 开发 , 介 包括孔 型 系统 的选择 、 工艺件 的设计 、 生
采用 立 轧
外其余全部平式布置 , 4架为偏心轧机 , 2 前 后 架为
切分 生 产 工艺 流 程 为 : 坯 检 查一 加 热 一 粗 轧 钢 一 1飞剪一 中轧
入库 。
飞 剪一 圆弧辊 道 过 跨一 精 轧 一
3倍 尺 飞 剪一 冷床 冷却一 定 尺剪 切 一包 装 一 检验 一
是遵 循尽 量减 小不均 匀 变形 的设 计 原则 。从 图 中可 以直观地 看 出 , 中间孔 的压缩 面积 比两侧 孔 大 , 且 并
中间孔 没有金 属横 向流 动 的空 间 , 这种情 况 , 必然 导 致K 3中间 孔 两 侧 的切 分 楔 壁 磨 损 速 度 较 两 侧 孔
快, 中间孔 的面积 和宽度 在 轧制过 程 中越来 越大 , 虽
性 、 型设 计 的合 理性 、 分合 轧件 的 正确性 和 产 品 孔 切
质量 的稳 定性 。
1 车 间生产 工艺简介
莱钢 棒材 厂第 一 轧钢 车 问工艺 布局 为粗 轧 机组 6架 闭 口轧 机 平 立 交 替 布 置 、 中轧 机 组 4架 闭 口轧
浅析唐钢棒材厂四线切分轧制技术

圆形 轧件进 平辊 时不 会产 生不 均匀 变形 。中轧 机 新 增加 的第 1 # 机与精 轧 机 1 # 机 的距离 缩短 到 9 4轧 5轧
m, 而且 由于 1 # L 的孔 型 为 立 箱形 , 4  ̄机 采用 小 压 下
量, 主要 作用 是 使 1 # 辊 加 工 出 来 的 鼓 形 断 面 轧 3平
DI SCUS ON SI ABOUT FOUR —L E PLI S TD ROLL玎 G G D TAN G TEEL S
Ni a g e g,G e Ya o u Li n p n d ng, Ya g Ba h ng n oz o
( . te l n l,Ta g h n Io n te mp n No 2S elRol g Mi i l n sa rn a dS e l Co a y,He e rn a d Se lGru b i o n te o p,T n s a ,He I a gh n — bi030 e , 6 0 0)
虽 然表面 现象 都 是 切 分架 次 堆 钢 , 是 导 致 切 但
分架 次堆 钢频 繁 的原 因有多种 。按 照切 分架 次堆 钢
的原 因分类 , 有如 下几 种 :
3 2 1 切 分 架 次钢 料 形状 不 好 ..
与三线切分 轧制相 比 , 四线 切分轧制 对轧辊 的精 度要 求更高 。在 现有 条件允许 的前提下 , 为最 大限度
在 K 3孔 ( 分孔 型 ) 工 成 断 面积 相 同 的 并 联 轧 切 加
9’
件, 连接 带厚 度一 般 为 1 0 mm, . 经过 切 分 导 卫 的加 工分 成 四条独 立 的轧件 , K 在 2孔加工 成 四条扁椭 形
螺纹钢14四切分问题汇总

螺纹钢?14四切分经验总结螺纹钢?14四切分工艺难度大,在开发阶段精轧机组跑钢频繁,现将开发过程中遇到的问题以及解决方案整理如下:一、存在问题:17#冲出口(架次K3)原因:1、K3、K4料型不规范,K3、K4料型不稳定,中轧来料不规范2、导卫安装不规范。
3、导卫或导卫梁紧固不牢,在钢的冲击下导卫发生轻微的摆动或扭动,导致冲出口。
4、K4(16#)进口导卫梁导卫座太窄,过钢时头部冲击力大,进口导卫不稳定容易晃动。
解决方法:1、K3、K4不能错辊、窜辊。
2、K3、K4划料必须均匀,不能有毛边。
3、中轧圆料头尾不能带耳朵,以确保K3、K4料型头尾规范。
4、必须确保中轧不能拉钢。
5、养成K4试小样的习惯,以确认进出口导卫是否在一条直线上。
6、安装K3切分导卫时切分刀、切分轮、轧辊切分尖必须在一条直线上。
7、K3、K4导卫、导卫梁上的锁紧螺栓、螺母,必须紧固好。
8、与导卫厂家协商,导卫梁导卫座加宽,导卫锁紧改成中轧锁紧样式。
二、存在的问题:K3掉块现象比较严重原因:1、K3、K4压下量分配不合理,K3机架的电流应为K4电流的一半,而我厂K3、K4电流几乎一样(设计原因)。
2、K3、K4轧槽缺水(其他架次也存在同样的问题)。
解决方法:1、尝试修改K4孔型,增加K4压下量,减少K3负荷。
三、存在的问题:K1冲出口原因:1、导卫或导卫梁紧固不牢,在钢的冲击下导卫发生轻微的摆动或扭动,导致冲出口。
2、钢头弯顶出口导板,主要原因是K3切分出的料型不好(头部一侧尖),经18#扭转导卫扭转后尖头在上或下,尖头必然先碰到轧辊(K1);尖头先碰到上辊,成品钢头就朝上弯;尖头先碰到下辊,成品钢头就朝下弯。
解决方法:1、导卫、导卫梁上的锁紧螺栓、螺母,必须紧固好。
2、新换K4轧辊或槽,开轧之前试小样,确保K3、K4料型。
四、存在的问题:K3出口导卫切分刀、出口导卫下铲嘴粘钢。
可能原因:1、正常过钢时K3切分尖磨损较快,导致撕裂带太厚。
Ф12mm螺四切分轧制工艺的优化
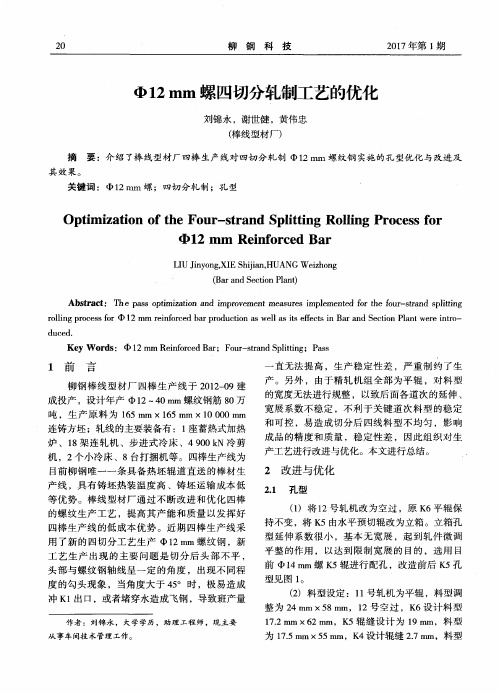
其 效果 。 关键 词 :
Op t i mi z a t i o n o f t h e Fo u r - s t r a n d S p l i t t i n g Ro l l i n g Pr o c e s s f o r
1 2 mm Re i n or f c e d Ba r
2 0 1 7年第 1 期
刘锦永等:中 1 2 m m螺四切分轧制工 艺的 优化
2 1
度 均 匀 性 ,轧 制 温 度 控制 以 2号 飞 剪 处 温 度 为
准 ,控制在 1 0 4 0℃ ±1 0℃;上冷床温度 :6 9 0 ℃~ 7 0 0℃。三是开展轧制线对 中,重点对活套 架 进 出 口导槽 ,喇 叭 口 ,导 卫 进 出 口安 装 ,K1
1 前
言
直 无 法 提 高 ,生 产 稳 定 性 差 ,严 重 制 约 了生
柳 钢 棒 线 型材 厂 四棒 生 产 线 于 2 0 1 2 — 0 9建 成 投产 ,设计 年 产 1 2~ 4 0 m m 螺纹 钢筋 8 0万
吨 ,生 产 原 料 为 1 6 5 mm ×1 6 5 mm ×1 0 0 0 0 m m
( 2 ) 料型设 定 :1 1 号 轧机 为 平辊 ,料 型调
整为 2 4 mm×5 8 m m,1 2号 空 过 ,K 6设 计 料 型 1 7 . 2 m m×6 2 m m,K 5辊缝 设 计 为 1 9 mm,料 型 为1 7 . 5 mm×5 5 m m,K 4设计 辊缝 2 . 7 mm,料 型
出 口至 穿 水 管 进 口 ( 空 过竹 节 管 导 槽 ) 水 平 校
对 ,避 免 与 K l出 口不水平 造 成钢 头 碰对 盖板 或
Ф12mm螺四切分轧制成品勾头冲出口故障处理分析
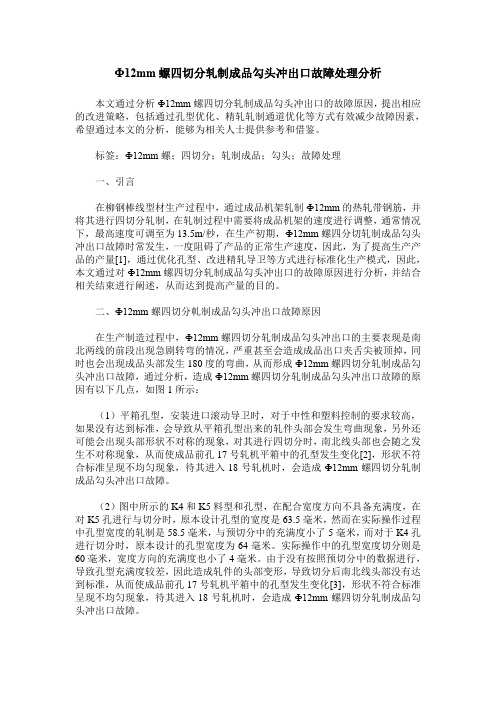
Ф12mm螺四切分轧制成品勾头冲出口故障处理分析本文通过分析Ф12mm螺四切分轧制成品勾头冲出口的故障原因,提出相应的改进策略,包括通过孔型优化、精轧轧制通道优化等方式有效减少故障因素,希望通过本文的分析,能够为相关人士提供参考和借鉴。
标签:Ф12mm螺;四切分;轧制成品;勾头;故障处理一、引言在柳钢棒线型材生产过程中,通过成品机架轧制Ф12mm的热轧带钢筋,并将其进行四切分轧制,在轧制过程中需要将成品机架的速度进行调整,通常情况下,最高速度可调至为13.5m/秒,在生产初期,Ф12mm螺四分切轧制成品勾头冲出口故障时常发生,一度阻碍了产品的正常生产速度,因此,为了提高生产产品的产量[1],通过优化孔型、改进精轧导卫等方式进行标准化生产模式,因此,本文通过对Ф12mm螺四切分轧制成品勾头冲出口的故障原因进行分析,并结合相关结束进行阐述,从而达到提高产量的目的。
二、Ф12mm螺四切分軋制成品勾头冲出口故障原因在生产制造过程中,Ф12mm螺四切分轧制成品勾头冲出口的主要表现是南北两线的前段出现急剧转弯的情况,严重甚至会造成成品出口夹舌尖被顶掉,同时也会出现成品头部发生180度的弯曲,从而形成Ф12mm螺四切分轧制成品勾头冲出口故障,通过分析,造成Ф12mm螺四切分轧制成品勾头冲出口故障的原因有以下几点,如图1所示:(1)平箱孔型,安装进口滚动导卫时,对于中性和塑料控制的要求较高,如果没有达到标准,会导致从平箱孔型出来的轧件头部会发生弯曲现象,另外还可能会出现头部形状不对称的现象,对其进行四切分时,南北线头部也会随之发生不对称现象,从而使成品前孔17号轧机平箱中的孔型发生变化[2],形状不符合标准呈现不均匀现象,待其进入18号轧机时,会造成Ф12mm螺四切分轧制成品勾头冲出口故障。
(2)图中所示的K4和K5料型和孔型,在配合宽度方向不具备充满度,在对K5孔进行与切分时,原本设计孔型的宽度是63.5毫米,然而在实际操作过程中孔型宽度的轧制是58.5毫米,与预切分中的充满度小了5毫米,而对于K4孔进行切分时,原本设计的孔型宽度为64毫米。
圆钢剪切缺陷原因分析及改进措施
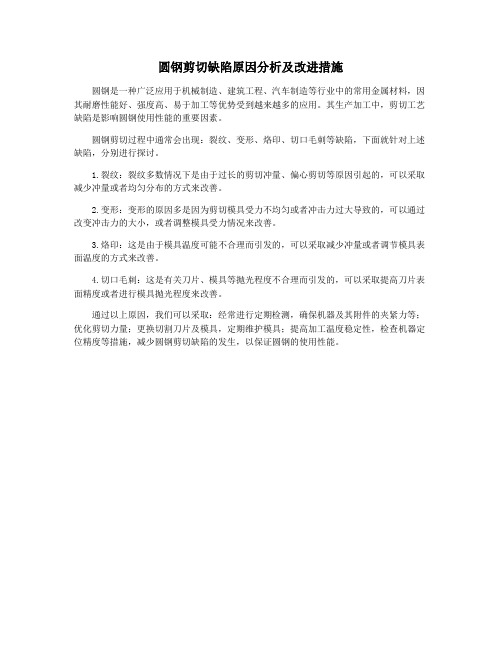
圆钢剪切缺陷原因分析及改进措施
圆钢是一种广泛应用于机械制造、建筑工程、汽车制造等行业中的常用金属材料,因其耐磨性能好、强度高、易于加工等优势受到越来越多的应用。
其生产加工中,剪切工艺缺陷是影响圆钢使用性能的重要因素。
圆钢剪切过程中通常会出现:裂纹、变形、烙印、切口毛刺等缺陷,下面就针对上述缺陷,分别进行探讨。
1.裂纹:裂纹多数情况下是由于过长的剪切冲量、偏心剪切等原因引起的,可以采取减少冲量或者均匀分布的方式来改善。
2.变形:变形的原因多是因为剪切模具受力不均匀或者冲击力过大导致的,可以通过改变冲击力的大小,或者调整模具受力情况来改善。
3.烙印:这是由于模具温度可能不合理而引发的,可以采取减少冲量或者调节模具表面温度的方式来改善。
4.切口毛刺:这是有关刀片、模具等抛光程度不合理而引发的,可以采取提高刀片表面精度或者进行模具抛光程度来改善。
通过以上原因,我们可以采取:经常进行定期检测,确保机器及其附件的夹紧力等;优化剪切力量;更换切割刀片及模具,定期维护模具;提高加工温度稳定性,检查机器定位精度等措施,减少圆钢剪切缺陷的发生,以保证圆钢的使用性能。
圆钢剪切缺陷原因分析及改进措施

圆钢剪切缺陷原因分析及改进措施圆钢是一种常见的金属材料,广泛应用于机械制造、建筑工程、汽车制造等领域。
在生产过程中,圆钢剪切缺陷是一个常见的问题,不仅会影响产品质量,还可能导致安全事故。
对圆钢剪切缺陷的原因进行分析,并提出改进措施,具有重要的实际意义。
一、圆钢剪切缺陷的原因分析1. 设备问题:圆钢剪切过程中使用的设备如果存在磨损、老化或者不合理的设计,都会导致剪切缺陷的产生。
比如刀具磨损不均匀、切割速度过快等问题都可能引起剪切缺陷。
2. 材料问题:圆钢的质量和性能会直接影响到剪切的效果,如果材料本身存在缺陷或者不符合标准要求,也会导致剪切缺陷的产生。
比如材料硬度不均匀、内部夹杂物等都可能引起剪切不良。
3. 操作问题:操作人员的技术水平和工作细节也是引起剪切缺陷的重要原因之一。
比如操作不规范、工作失误、操作疏忽等都可能导致剪切不良。
4. 环境问题:生产环境的干扰和影响也会对剪切缺陷产生影响。
比如温度、湿度、粉尘等环境因素都可能引起剪切不良。
二、圆钢剪切缺陷的改进措施1. 加强设备维护:定期对剪切设备进行检查和维护,确保刀具的锋利度和机器的正常运行。
对设备进行合理的调整和改进,能够提高剪切的效果。
2. 优化材料选择:对圆钢的材料选择和采购过程进行严格把控,保证材料的质量和性能符合标准要求。
对材料的质量进行检测,排除有缺陷的材料。
3. 加强操作培训:提高操作人员的技术水平和工作细节,确保操作的规范和精准。
对操作人员进行相关知识和技能的培训,提高其对剪切工艺的认识和理解。
4. 控制生产环境:加强生产现场的管理,保证生产环境的整洁、安全和稳定。
对生产环境的温度、湿度等参数进行严格的控制,减少外部环境对剪切的影响。
三、结语圆钢剪切缺陷是一个需要引起重视的问题,只有通过对其产生原因进行深入分析,并采取相应的改进措施,才能够有效地解决这一问题。
通过加强设备维护、优化材料选择、加强操作培训和控制生产环境等措施,可以有效地减少圆钢剪切缺陷的产生,提高产品的质量和安全性。
影响棒材定尺率的原因分析及改进措施

影响棒材定尺率的原因分析及改进措施摘要:本文结合轧钢棒材生产过程特点,总结分析了影响棒材定尺率的主要因素,并提出相应的改进措施。
关键词:定尺率;钢坯定重;热装率1 引言螺纹钢占据建筑用钢一半以上的产量,目前也是陕钢集团汉中钢铁有限责任公司主要产品之一,年生产量约160万吨,产品规格主要为Φ12-40mm。
螺纹钢筋通常情况下均以定尺出售,由于棒材在剪切精整过程中会产生较多的非定尺,非定尺材与定尺材每吨有较大差价,且非定尺材的市场需求量少,销售较困难,影响钢材的使用价值,也对成材率有一定影响。
在钢铁企业提质增效、追求效益最大化的情况下,最大程度的降低成本、提高经济效益成为企业提高竞争力、生存发展的关键。
因此提高定尺率是轧钢降低成本的有效措施,可有效增加棒材产品效益,本文总结分析了影响棒材定尺率的主要因素,并提出相应的改进措施。
2 影响棒材定尺率的原因分析2.1 钢坯重量钢坯轧制不同规格螺纹钢后,倍尺飞剪会剪切成固定的长度,同时会产生尾钢,这些尾钢通常就是非定尺。
根据金属平衡,同样重量的钢坯轧制为不同规格的棒材后其非定尺的长短不同,在其他条件不变时,钢坯重量相同,其切后的非定尺长短一定。
所以钢坯重量对定尺率的影响是直接的决定因素【1-2】,钢坯重量稳定性是提升定尺率的前提。
2.2 钢坯热装率钢坯在加热炉中如果氧化烧损和加热温度不一致时,会对轧制过程的延伸率有一定的影响,在轧制工艺参数不变的情况下影响成品长度的变化,从而会影响到非定尺的长短。
一般情况下热坯所轧制成品长度较冷坯较长。
2.3 头尾切损根据金属平衡,轧制过程头尾切损越大,成品的总长度就会相应的变短,可能会使部分定尺变为非定尺。
切损量越小,成材率越高;切损量越稳定,越有利于尾钢长度控制。
因此控制轧制过程的切损量也是提高定尺率的关键因素。
2.4 负差控制在相同钢坯重量的情况下,负偏差对成品长度影响较大,负偏差越大,成品长度越长;负差稳定性越差,成品长度波动越大,尾钢长度越不宜控制,因此负差的稳定控制对定尺率也很关键。
- 1、下载文档前请自行甄别文档内容的完整性,平台不提供额外的编辑、内容补充、找答案等附加服务。
- 2、"仅部分预览"的文档,不可在线预览部分如存在完整性等问题,可反馈申请退款(可完整预览的文档不适用该条件!)。
- 3、如文档侵犯您的权益,请联系客服反馈,我们会尽快为您处理(人工客服工作时间:9:00-18:30)。
棒材四切分问题及解决方法
编写作者:邱世浦
一切分刀粘钢
切分刀粘钢是指切分轧制生产过程中,切分刀两侧或一侧粘渣,最终导致切分故障的现象,切分刀粘钢的原因主要有以下几个方面;1.开轧温度过高。
如果开轧温度过高,在精轧区切分过程中,切分楔处压下量非常大时,因急剧变形产生大量的热,造成局部金属温度迅速升高和切分带形状不规矩,引起切分刀粘钢。
2.来料过大或过小,切分轧制遵循斧头原理,来料必须与16架切分楔处角度匹配。
15料形过大或过小,都会造成切分困难,导致切分带过大,轧件前进过程中,切分带与切分刀发生摩擦,引起粘钢。
3.切分轮切偏或没对准轧槽。
切分导卫安装,必须保证切分楔,切分轮,切分刀三点一线,对中良好,如果安装不正,导致料与切分轮不能对正而切偏,造成切分带过大,与切分刀发生摩擦,引起粘钢。
4. 切分刀冷却不好,切分导卫必须保证充分冷却,尤其是切分刀,正常生产过程中因坯料,轧槽磨损等原因,造成轧件表面带细小氧化铁皮,切分带形状不规矩,与切分刀摩擦粘在两边,如果冷却效果不好,就会越粘越多,最终导致冲出导卫堆钢,和下游轧机无法调整。
5. 切分刀间距不合适,轧件进入切分盒后,成一定的角度,如切分刀间距未设定好,就会出现轧件与切分刀发生摩擦而粘钢。
6. 切分孔型设计不合理,15,16架孔型系统设计非常重要,切分角设计必须匹配。
7.轧机刚性差,弹跳大,料形控制差。
8.切分刀长度不合适,三切分更为明显,离切分轮过近造成排渣不方便,引起粘钢。
9.切分轮角度设计不合理,切分不顺利。
10. 12到18架料形没有控制好,料发生偏斜扭转,过大过小,头大尾大造成粘钢。
11.钢坯自身有问题有夹杂气泡开花。
12.关键架次轧槽老化或蹦槽。
13.关键架次导卫梁和导卫未对正轧制中心。
14.各架次张力没控制好或钢温不稳定。
15. 导板或导板磨损过度或导卫导槽装配有问题。
切分刀粘钢解决方案:
1. 按工艺要求控制好钢温,在满足主电机负荷的情况下,钢温应控制在1000到1050摄氏度,最好不要超过1100摄氏度。
2. 严格按工艺要求控制好料型尺寸,粗轧六架料型尺寸偏差控制在±0.5 mm以内,中轧尺寸偏差控制在±0.3mm以内,精轧尺寸偏差控制在0.2 mm以内。
预切分和切分架次料型应严格按工艺要求控制。
保证切分架次的充满度。
3. 切分导卫安装要精确,保持切分刀,切分轮,切分槽在同一直线上,同时加强切分导卫及轧槽的冷却,及时观察料型的转钢程度。
4,设计人员对孔型要做好设计校对工作。
4.切分刀的间距是一定的,仔细检查切分刀间距是否合适。
5.按要求控制好各道次料型。
6.及时做好轧线在线检查。
正确安装导卫及导卫梁。
二.切分轧制线四线差问题。
切分轧制工艺虽然有效提高了作业率,使产量大幅度上升,但是受钢温波动,轧槽磨损,孔型系统设计,导卫安装,轧槽加工精度等各方面因素影响,每根轧件尺寸都不可能完全一样,即存在线差,若在获得较高经济效益的同时,又要求保证钢材质量,这就要求必须通过各种手段来缩小各线差距。
线差产生的主要原因有以下几个方面;1. 预切分15架或切分16架进口导卫没对正轧线,偏向一侧,此时来料被切分后偏向的一侧由于断面积大,导致此线成品尺寸大。
2. 孔型磨损不一致。
由于轧槽冷却不一致,前道次料形不规矩或导卫孔型设计等各方面因素影响,磨损严重的一线断面积就会增大,造成成品尺寸的。
3. 两侧辊缝不一致。
在换辊调试时,由于15—18架两侧辊缝控制不一致,辊缝大的一侧孔型面积就大,从而导致成品存在差异。
4. 轧槽加工精度不高。
这主要与轧辊材质,制修车间成型刀具磨损及修复精度,加工方式有关。
5. 12---16架次料形控制有问题。
切分生产非常注重12—16架次料形的匹配,匹配不好就会造成线差。
6. 线差的主要原因一般集中表现为K4轧槽老化问题,和K3K4导卫对正问题,以及K6料形变化问题。
四线差的解决方法
1.准确安装导卫。
在换辊前要预调好导卫,确保各方位对中,并固定好。
2.改进15,16架冷却水管,加强冷却效果,生产过程中做好点检。
3.换辊时点动轧机,用同样的焊条测两侧辊缝,偏差控制在0.1mm 以内。
4.改进轧辊材质,15,17,18采用高速钢轧辊。
联系加工部门提高加工精度。
5.严格按工艺要求控制好各道次料形,按要求用样棒调整导卫间隙。
三.18架顶出口故障
切分轧制生产过程中,18架顶出口故障发生较为常见,是制约四切分生产的一个主要故障点,主要表现为内侧或外侧两线钢前端向切分带方向急剧弯曲,将导管的舌尖顶掉,或弯曲180度从出口冲出来卡在导槽内堆钢。
产生这种现象的主要原因有以下几个方面;
1. 孔型设计存在缺陷,主要是孔型设计时参数的分配存在问题,造成调整难度过大,对职工整体素质和操作水平要求极高。
2. 17架孔型槽口设计过大,切分带无法很好加工。
3. 料形控制不准确。
15架充满度不好,或16架料形过小,切分后两线前端严重不对称,在17架变形不均匀,且对切分带加工不好,进入18架产生顶出口现象,或者12—16架料形过大,18架变形剧烈且不均匀,造成顶出口现象。
4. 15架16架导卫间隙控制不合适对中性不好,轧件前端弯曲在切分
时切偏,造成头部尺寸过大或过小,经17架后,造成18架顶出口。
5. 切分带处温度较高,在18架不易脱槽。
6. 导卫设计有问题或18架出口内腔尺寸过大,离轧辊相对较远,不能有效阻止18架头部形状变化。
7. 18架轧机导卫,导卫梁未按要求装配对正。
8. 17架料形与进口导板安装配合不好。
9. 切分导卫未按要求装配,或切分轮偏心方向不对或方向不统一。
10. 前面架次间转钢,尤其12—13架之间。
11. 17架出口扭转角度没调好。
12. 轧槽磨损严重。
13. 切分轮和切分导卫设计问题。
14. 连接轴间隙太大。
18架顶出口故障的解决方案
1.优化孔型系统,重新分配各道次压下量。
确定生产工艺。
2.摸索最佳工艺,重点是加热参数,各架次料形尺寸,各架次速度及电流参数,形成标准在各班组严格执行。
3.提高轧机导卫装配水平,重点做好精轧15-16架轧机导卫的装配,确保轧机刚性及轴向稳定性。
严格做好导卫预调及安装工作。
4.对切分带进行重点冷却。
5.改进18架导卫形式和内腔尺寸,控制在一定范围,使舌尖尽量靠近变形区,提高导向性。
6.17架料形与进口导板安装应遵循以下原则;17架孔型未充满时,
导板不易偏向切分带。
17架孔型充满时,导板应偏向切分带反方向. 7.及时检查轧辊磨损情况。
8.改变导卫形式。
l还有三号剪信号,穿水,孔型设计,初中轧张力控制,精轧调整,导卫设计,标注制定,料形控制原则,冷床上钢齐头等多种问题,详细可技术交流。