连轧管机主传动稀油润滑系统的改进
轧钢液压和润滑系统的维护与检修
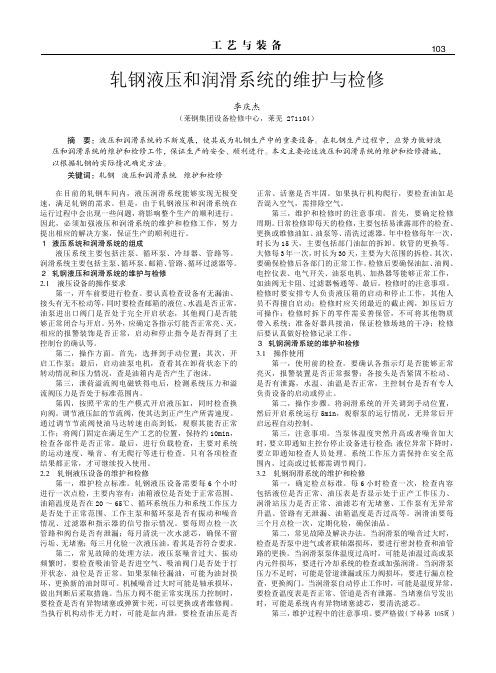
在目前的轧钢车间内,液压润滑系统能够实现无极变速,满足轧钢的需求。
但是,由于轧钢液压和润滑系统在运行过程中会出现一些问题,将影响整个生产的顺利进行。
因此,必须加强液压和润滑系统的维护和检修工作,努力提出相应的解决方案,保证生产的顺利进行。
1 液压系统和润滑系统的组成液压系统主要包括注泵、循环泵、冷却器、管路等。
润滑系统主要包括主泵、循环泵、邮箱、管路、循环过滤器等。
2 轧钢液压和润滑系统的维护与检修2.1 液压设备的操作要求第一,开车前要进行检查。
要认真检查设备有无漏油、接头有无不松动等,同时要检查邮箱的液位、水温是否正常,油泵进出口阀门是否处于完全开启状态,其他阀门是否能够正常闭合与开启。
另外,应确定各指示灯能否正常亮、灭,相应的报警装饰是否正常,启动和停止指令是否得到了主控制台的确认等。
第二,操作方面。
首先,选择到手动位置;其次,开启工作泵;最后,启动油泵电机,查看其在卸荷状态下的转动情况和压力情况,查是油箱内是否产生了泡沫。
第三,泄荷溢流阀电磁铁得电后,检测系统压力和溢流阀压力是否处于标准范围内。
第四,按照平常的生产模式开启液压缸,同时检查换向阀。
调节液压缸的节流阀,使其达到正产生产所需速度。
通过调节节流阀使油马达转速由高到低,观察其能否正常工作;将阀门固定在满足生产工艺的位置,保持约10min,检查各部件是否正常。
最后,进行负载检查,主要对系统的运动速度、噪音、有无爬行等进行检查。
只有各项检查结果都正常,才可继续投入使用。
2.2 轧钢液压设备的维护和检修第一,维护检点标准。
轧钢液压设备需要每6个小时进行一次点检,主要内容有:油箱液位是否处于正常范围、油箱温度是否在20~65℃、循环系统压力和系统工作压力是否处于正常范围、工作主泵和循环泵是否有振动和噪音情况、过滤器和指示器的信号指示情况。
要每周点检一次管路和阀台是否有泄漏;每月清洗一次水滤芯,确保不留看其是否符合要求。
当压力阀不能正常实现压力控制时,可以更换或者维修阀。
冷连轧机组打滑分析及工艺润滑优化

冷连轧机组打滑分析及工艺润滑优化前言轧制过程中出现的打滑现象,即带材和轧辊之间发生的相对滑动,其实质是带钢的变形区完全由前滑区或后滑区所取代。
发生打滑现象轻则影响带钢的表面质量和产量,重则引起断带堆钢事故,因此,如何避免冷连轧机高速轧制时发生打滑是提高轧机生产能力的一个重要课题①。
X钢冷轧厂完成酸洗与轧机联机改造后,冷连轧机组的打滑现象非常突出,严重制约机组的生产。
本文针对X钢冷轧厂冷连轧机组的打滑现象,结合打滑因子相关理论及工业试验给予分析,提出了工艺冷却润滑系统优化。
1冷连轧机组打滑特征通过对冷连轧机组的打滑进行跟踪发现,X钢冷连轧机组的打滑具有以下特点:1)轧辊粗糙度偏低打滑下机工作辊的表面粗糙度明显偏低,轧制吨位和轧制公里数明显减少。
通过对正常下轧机的轧辊辊面粗糙度(接近更换周期的轧辊)进行测量;并与打滑时的机架下机工作辊辊面粗糙度测量进行对比,对比情况见图一:图一轧辊粗糙度对比图从图一中可以看出:正常工作辊辊面粗糙度一般在Ra>0.3μm;发生打滑的轧辊辊面均在Ra≤0.3μm。
对比发现打滑的下机工作辊表面粗糙度进行了严重的衰减。
导致轧辊的换辊周期明显缩短,有的甚至缩短到原来的三分之一。
2)2#机架打滑明显在轧制过程中,品种规格发生变化时,尤其大变形料轧制时,打滑趋势明显。
打滑现象多发生在2#机架,少量出现在1#和3#机架。
X钢冷连轧机组仅有四机架,1#机架和2#机架基本承担了55~70%的总变形量。
因1#机架考虑带钢咬入问题,总变形的40%左右由2#机架承担。
一年时间内各机架打滑频次统计见图二:图二各机架打滑频次统计图从图二可以看出:打滑现象主要发生在2#机架,占到打滑发生次数的72%。
3)轧制参数出现异常波动,轧制出现异响。
出现打滑时,张力波动较大,同时出现发闷的声音,用手接近牌坊时,明显感觉牌坊有异常振动。
2 冷连轧机组的打滑分析一般来说,打滑是指在冷连轧过程中,轧辊的圆周速度超过带钢的出口速度,带钢和轧辊之间发生相对滑动。
冶金轧钢设备润滑问题的解决
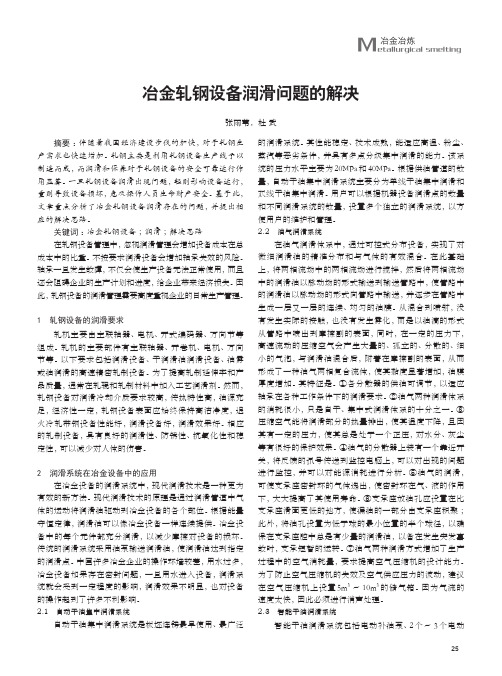
M etallurgical smelting冶金冶炼冶金轧钢设备润滑问题的解决张雨苇,杜 武摘要:伴随着我国经济建设步伐的加快,对于轧钢生产需求也快速增加。
轧钢主要是利用轧钢设备生产线予以制造而成,而润滑和保养对于轧钢设备的安全可靠运行作用显著。
一旦轧钢设备润滑出现问题,轻则影响设备运行,重则导致设备损坏,危及操作人员生命财产安全。
基于此,文章重点分析了冶金轧钢设备润滑存在的问题,并提出相应的解决思路。
关键词:冶金轧钢设备;润滑;解决思路在轧钢设备管理中,忽视润滑管理会增加设备成本在总成本中的比重。
不按要求润滑设备会增加轴承失效的风险。
轴承一旦发生故障,不仅会使生产设备无法正常使用,而且还会阻碍企业的生产计划和进度,给企业带来经济损失。
因此,轧钢设备的润滑管理需要高度重视企业的日常生产管理。
1 轧钢设备的润滑要求轧机主要由主联轴器、电机、开式编码器、万向节等组成。
轧机的主要部件有主联轴器、开卷机、电机、万向节等。
以下要求包括润滑设备、干润滑油润滑设备、油雾或油润滑的高速精密轧制设备。
为了提高轧制延伸率和产品质量,通常在轧辊和轧制材料中加入工艺润滑剂。
然而,轧钢设备对润滑冷却介质要求较高,传热特性高,油源充足,经济性一定,轧钢设备表面应始终保持高洁净度,退火冷轧带钢设备性能好,润滑设备好,润滑效果好。
相应的轧制设备,具有良好的润滑性、防锈性、抗氧化性和稳定性,可以减少对人体的伤害。
2 润滑系统在冶金设备中的应用在冶金设备的润滑系统中,现代润滑技术是一种更为有效的新方法。
现代润滑技术的原理是通过润滑管道中气体的运动将润滑油驱动到冶金设备的各个部位。
根据能量守恒定律,润滑油可以像冶金设备一样连续提供。
冶金设备中的每个元件都充分润滑,以减少摩擦对设备的损坏。
传统的润滑系统采用油泵输送润滑油,使润滑油达到指定的润滑点。
中国许多冶金企业的操作环境较差,用水过多,冶金设备如果存在密封问题,一旦用水进入设备,润滑系统就会受到一定程度的影响,润滑效果不明显,也对设备的操作起到了许多不利影响。
设备润滑管理问题分析及改进措施

冶金动力2015年第10期综合设备润滑管理问题分析及改进措施张涛(宣化钢铁有限责任公司设备能源部,河北张家口075100)【摘要】分析了企业设备润滑管理中存在的计划、人员、油品、检测、培训等方面存在的问题,从制度与技术方面提出了7条改进措施。
【关键词】设备润滑;问题;改进措施【中图分类号】TH117【文献标识码】B【文章编号】1006-6764(2015)10-0072-02Analysis of Management Problems in Equipment Lubricationand Improvement MeasuresZHANG Tao(Xuangang Equipment and Energy Dept.of Hebei Iron and Steel Group,Zhangjiakou,Hebei075100,China)【Abstract】Problems in the aspects of planning,personnel,oils,inspection and training in equipment lubrication management at enterprises are analyzed and seven improvement mea-sures involving system establishment and technology are put forward.【Keywords】equipment lubrication;problem;improvement measure1引言保证设备良好润滑,是企业设备润滑管理者不断思考、不断探索的一项重要工作。
据统计,大约有40%以上设备故障由润滑不良引起的,搞好设备润滑管理工作,对设备正常运行起着重要作用。
2设备润滑管理中存在的问题2.1设备润滑管理机构不健全,人员不固定由于设备润滑管理缺少长期计划,无固定的设备润滑管理机构,使得润滑管理给企业带来的效益是滞后的,长期的。
探讨轧钢液压和润滑系统的维护

探讨轧钢液压和润滑系统的维护1 概述随着液压和润滑技术的不断发展,液压和润滑系统在轧钢生产中已成为不可缺少的重要设备。
在轧钢生产线中,做好液压和润滑系统设备的维护和检修是非常重要的。
下面主要对轧钢生产线液压和润滑系统的维护与检修做详细论述。
2 液压和润滑系统的组成液压系统主要包括工作主泵、循环泵、油箱、冷却器、主回油过滤器、循环过滤器、管路、油缸、阀台等。
润滑系统主要包括工作主泵、循环泵、油箱、冷却器、主回油过滤器、循环过滤器、管路等。
3 轧钢液压设备的维护与检修3.1 轧钢液压设备的操作使用3.1.1 开车前检查。
第一,检查系统设备、管路有无泄漏,各接头是否紧固不松动。
第二,检查油箱液位、油温、水温是否正常,选择控制按钮位置是否得当,油泵进出口阀门是否完全开启,其他各阀门是否处于正确状态。
第三,确认各指示灯亮/灭正常,各报警装置工作正常。
第四,启、停指令应与主控台操作人员确认好。
3.1.2 操作步骤。
第一,选择开关打到手动位置。
第二,操作工作泵启动按钮,点动数次之后启动油泵电机,使泵在卸荷状态下运转,观察泵的转动情况、卸荷压力是否在允许数值之内,油箱油液是否有泡沫。
第三,卸荷溢流阀电磁铁得电后,检查系统压力是否处于设计要求范围之内,溢流阀的安全设定压力是否符合设计要求。
第四,空载试车:执行机构试动。
按生产工艺流程或按试车指挥员的命令试动液压缸。
操作换向阀,检查液压缸动作是否灵活,有无爬行;检查换向阀是否工作正常。
调节液压缸的节流阀,使其速度满足生产工艺要求。
调试油马达,通过调节节流阀使其转速由高到低,观察其工作是否平稳正常,最后将其转速锁定在满足工艺要求位置。
将系统在额定工作压力下保压10分钟,检查系统各部是否工作正常无外泄露。
第五,负载试车:负载试车是为了检查液压系统在工作状态下能否实现预定的工作要求。
在负载状态下,检查运动速度是否正常;噪音、振动是否在允许范围内,有无爬行、跳动等现象,如一切正常,方允许交操作方使用。
冷轧厂轧机油气润滑系统优化及改进

冷轧厂轧机油气润滑系统优化及改进摘要:本文重点探讨了油气润滑的特点和工作原理,阐述了REBS油气润滑系统在某冷轧厂轧机工作辊和中间辊径向轴承润滑中的应用及优化,并简单介绍了应用中油气润滑系统存在的不足和改善措施。
关键词:油气润滑;径向轴承;原理;优化;改善措施前言油气润滑是新型的“气流两相流体”技术的典型工业应用。
油气润滑因具有润滑效果好、耗油量低、可精确计量给油、可实现高速自动控制和可使用润滑油品黏度范围大等优点,在自动化程度高的工业领域得到了广泛应用,尤其是在高温、高速、重载和使用环境恶劣的冶金领域的辊道运输线、单机架和串列机架冷轧机、线材轧机的高速转动导向装置以及连铸设备等。
1.油气润滑的工作原理1.1 油气润滑的形成和本质在一个管状的空间内,连续间断给定的润滑油被2~4bar的压缩空气从一端吹向另一端的连续作用下,润滑油在“附壁效应”的作用下从颗粒状态逐渐吹散和变薄,形成无雾化沿管壁连续流动的气动波浪油膜,即形成了“气液两相流体”中的油气。
单相流体油和单相流体压缩空气混和后就形成了两相油气混合流,两相油气混合流中油和压缩空气并不真正融合,而是在压缩空气的流动作用下,带动润滑油沿管道内壁不断地螺旋状流动并形成一层连续油膜最后以精细的连续油滴的方式喷到润滑点。
1.2 油气润滑的润滑机理沿管壁连续流动的气动波浪油膜到达润滑点后,在摩擦副表面形成油膜,隔绝相互摩擦的表面,使干摩擦状态变为液体摩擦状态或准液体摩擦状态;流动的压缩空气可以冷却摩擦副,带走热量,阻止润滑油高温碳化。
同时压缩空气使摩擦副腔内形成正压,可避免外部环境中的赃物和腐蚀流体侵入摩擦副,保证了摩擦副良好的工作环境。
2.油气润滑的特点油气润滑就是应用“气液两相流体”原理进行工作的,与传统的润滑方式(如干油、稀油和油雾润滑)相比,主要特点可归结为:(1)润滑效率高,可以大幅提高轴承的使用寿命。
由于油气润滑在供油量、轴承温度和摩擦三者间找到了最佳平衡点,即用最小的供油量达到降低轴承温度和有效润滑的最佳效果,润滑剂的利用率几乎达100%。
热轧工艺润滑问题与改进措施

热轧工艺润滑问题与改进措施摘要:随着科技发展,轧制润滑工艺得到大力发展,成为轧钢生产中改善产品质量、降低消耗、提高产量的一个极其重要的技术环节。
为了更好的在激烈的市场竞争中,不断拓宽产品结构、提升产品质量、降低产品成本,持续提升企业的核心竞争力,热轧工艺润滑提升热轧带钢表明质量、实现薄规格轧制高效稳定。
基于此,本文主要就热轧工艺润滑问题进行了分析,并提出了改进措施。
关键词:热轧工艺;设备;润滑引言热轧工艺润滑通常是指在轧制变形区进行润滑油膜的建立,当值发生辊面与轧件间的“金属—金属”接触,对轧制过程进行改善,提升产品的质量。
目前,市场是对于热轧板带的质量要求不断提升,生产效率也不断提升,这就需要进行钢材种类的开发,确保金属轧制以及设备的逐渐成熟,拓展轧制范围,改善热轧工作辊的工作环境。
要想提升轧制质量,确保作业效率的提升,需要延长轧辊的寿命以及耐磨耐性。
1热轧润滑机理热轧润滑是一个动态过程,轧制变形区润滑剂的变化很难通过实验模拟。
一般认为,润滑可以在轧件进入轧辊间隙之前在轧件表面形成润滑膜。
润滑膜的一部分在高温下燃烧。
燃烧产生的剩余碳留在轧制表面,残余碳与轧制之间的摩擦小于轧制与轧制之间的摩擦;润滑膜的另一部分在轧制变形区迅速蒸发分解,形成高温、高压气垫,分离轧制与轧辊表面。
会最大程度的减少气体以及液体的摩擦,剩余的润滑膜会以液体的形式进行呈现,进而进入到辊缝,进行润滑。
对于热轧变形力而言,其和轧件变形抗力、变形程度、变形温度、变形速度、摩擦力具有重要的关联性。
如果其他的条件具有一致性,润滑剂会对轧制变形区域的摩擦状况进行改善,降低轧制力。
2工艺润滑设备及润滑方式热轧工艺润滑系统采用专用喷嘴系统,以水为载体将油水混合后喷射在轧辊上,使热轧润滑达到最佳的使用效果,此系统容易控制、运行可靠、维护方便故障率低。
热轧工艺润滑油喷出后与高温带钢接触,燃烧后形成灰分,因而工艺润滑油不能重复利用,采用非循环方式。
轧机主轴承油气润滑系统分析及改进措施

关键词 : 轧机 ; 轴承 ; 油 气 润 滑
中 图分 类 号 : TG 2 4 2 文献标识码 : A
1 轴 承 润 滑 的机 理
润 滑 是 用 润 滑 剂 减 少 摩 擦 副 的摩 擦 和 降低 温
度, 或 改善 其他 形 式 的 表 面破 坏 的措施 。合 理选 择
有 实际 意义 。轧机 的轴 承润 滑大致 分 以下几 个发 展
阶段 : 一 是油脂 润 滑 阶 段 , 轧 制 过程 中 , 乳 化 液 和 碎
v =3 U _80m/ s
屑 与润 滑脂接 触 , 会降 低润 滑膜粘 着力 , 润滑 膜脱 落
后 轴承 表面 温度 会显 著提 高 , 当轧制 速度超 过 1 2 0 0
第 3 O卷第 1 期 2 0 1 4年 2月
有 色 矿 冶
N 0N — F ERR oUS MI NI NG AN D M ET A LL U RG Y
V o1 . 3 O .№ 1
Fe br ua r y 2 0 1 4
文章 编 号 : l O O 7 —9 6 7 X( 2 o 1 4 ) O l 一0 0 4 0 —0 3
粘 度≤ 7 6 0 mm。 / s ( 4 0 ℃) , 相 当于粘度 牌号 N6 8 0以
速度 , 系统 温度 不断 升高 , 随着 温度 的升 高散 热速 度 则 在不 断加 快 , 当产 热 速 度 在 某 一 时 刻等 于 系 统 的
散 热速 度 , 系统 的温 度 达 到一 个 恒 定 值 。这 个 温 度 值 是选 择润 滑 油 的关 键 , 如果 润滑 油选 择不恰 当 , 则 会 导致 润滑 油膜 破 裂 , 润滑 失 效 。 而散 热 速 度 又 与
1780mm热连轧R2粗轧机主电机止推装置分析与改进

3 主电机止推轴承发热改进措施及振动 阻尼装置改进
振动阻 尼原理 :R 主 电机 振动阻 尼采 用液体阻尼减振 ,在 主电 2 机转子尾部联接推力盘 ( 中序号 图 ) 振动阻 尼轴承座( 8, 图中序号
2 、2 ) 0 1 上安装有止推瓦( l 、 序号 3 1 ,安装在轴承座两 侧位置) 9 ,推
内由顶 部油箱 通过单 向液压油管供 油, 两腔 室通过外接 阀门控制开 口
度。当电机转子有轴 向窜动时 ,推 力盘随电机转子移动 ,在移动过程 中压缩 液压油产生反作用力给推力 改 后的 2 轧 适 R 粗 机主电 振 尼装 机 动阻 王 盘 ,通过两腔 室相通 的液压 阀开 口度来调节压缩液压缸的压力达到 减
压力给 电机转子一个反方向的力。改进后 电机止推轴承发热现 象周期 由之前 的3 天延长至 l天 ,效果有 改善 , 0 但未 从根本上解决止推轴承
发热的问题 ,仍然影响正常生产轧制 。 () 4 止推 轴承材质较软 ,强度 及耐磨性差 ;安装时止推轴承精
经过R 粗 轧机 主 电机振动阻尼装置 的改进 ,试运转6 2 个月来 ,主 电机止推装置及振动阻尼装 置运行平稳 ,主 电机频繁报警并联锁停机 现象消除 , 果十分 明显 ,很好的服务了正常生产轧制。 效
原因排除。
( )止推轴承稀 油润滑流量较 小 ,无法满足工况要求 。针对 此 3
求 。以主 电机磁力中心线为基准 ,调整振 动阻尼止推瓦两侧间隙各 为 3m . m,传动侧止推轴承两 侧间隙各为3 m 0 . m,保 留传动侧止推轴承 5 温度报警功能 ,在线随时监控传动侧止推轴承温度 ,相反可反映振动 阻 尼装置工作状态 。改后振动阻尼盘表面积为l m ,1 P 工况下 即 m2 Ma
润滑系统改造实施方案

润滑系统改造实施方案一、前言。
润滑系统作为机械设备的重要组成部分,对设备的正常运行起着至关重要的作用。
然而,随着设备运行时间的增长,原有的润滑系统可能出现老化、损坏或者不适用于新的工况等问题,因此需要对润滑系统进行改造,以确保设备的正常运行和延长设备寿命。
本文将就润滑系统改造的实施方案进行详细阐述。
二、改造目标。
1. 提高润滑效果,通过改造,使润滑系统能够更好地对设备进行润滑,减少摩擦和磨损,提高设备的运行效率和稳定性。
2. 降低能耗,优化润滑系统结构,减少能耗,降低运行成本。
3. 增强设备安全性,改造后的润滑系统应能够提高设备的安全性,减少故障率,降低维护成本。
三、改造方案。
1. 确定改造范围,首先需要对润滑系统所涉及的设备进行全面的调研和分析,确定需要改造的范围和内容。
2. 优化润滑油选择,根据设备工作条件和要求,选择合适的润滑油,保证其润滑效果和稳定性。
3. 更新润滑设备,对润滑系统的润滑设备进行更新,选择更加先进和适用的设备,如自动润滑装置、润滑油循环系统等。
4. 完善润滑系统管道布局,重新设计润滑系统的管道布局,确保润滑油能够准确、及时地输送到设备的各个部位。
5. 强化润滑系统监测,增加润滑系统的监测装置,实时监测润滑油的质量和流量,及时发现问题并进行处理。
6. 建立完善的维护保养制度,制定润滑系统的维护保养计划,定期对润滑系统进行检查和维护,确保其长期稳定运行。
四、实施步骤。
1. 制定改造计划,根据改造方案,制定详细的改造计划,包括改造范围、时间节点、人员分工等。
2. 采购改造设备和材料,根据改造方案,进行设备和材料的采购工作,确保所采购的设备和材料符合改造要求。
3. 进行设备改造,按照改造方案,对润滑系统的设备进行改造和更新,确保改造工作的质量和进度。
4. 完善管道布局,重新设计润滑系统的管道布局,确保润滑油能够准确、及时地输送到设备的各个部位。
5. 加强监测装置安装,增加润滑系统的监测装置,确保润滑系统能够及时发现问题并进行处理。
平整开卷机稀油润滑回油管改造
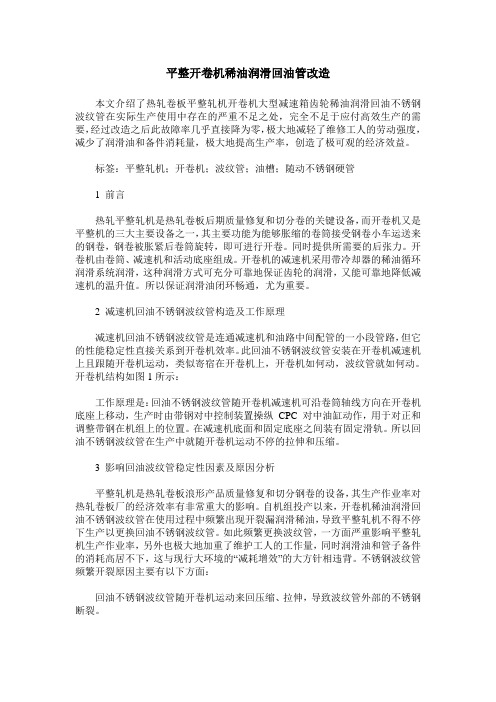
平整开卷机稀油润滑回油管改造本文介绍了热轧卷板平整轧机开卷机大型减速箱齿轮稀油润滑回油不锈钢波纹管在实际生产使用中存在的严重不足之处,完全不足于应付高效生产的需要,经过改造之后此故障率几乎直接降为零,极大地减轻了维修工人的劳动强度,减少了润滑油和备件消耗量,极大地提高生产率,创造了极可观的经济效益。
标签:平整轧机;开卷机;波纹管;油槽;随动不锈钢硬管1 前言热轧平整轧机是热轧卷板后期质量修复和切分卷的关键设备,而开卷机又是平整机的三大主要设备之一,其主要功能为能够胀缩的卷筒接受钢卷小车运送来的钢卷,钢卷被胀紧后卷筒旋转,即可进行开卷。
同时提供所需要的后张力。
开卷机由卷筒、减速机和活动底座组成。
开卷机的减速机采用带冷却器的稀油循环润滑系统润滑,这种润滑方式可充分可靠地保证齿轮的润滑,又能可靠地降低减速机的温升值。
所以保证润滑油闭环畅通,尤为重要。
2 减速机回油不锈钢波纹管构造及工作原理减速机回油不锈钢波纹管是连通减速机和油路中间配管的一小段管路,但它的性能稳定性直接关系到开卷机效率。
此回油不锈钢波纹管安装在开卷机减速机上且跟随开卷机运动,类似寄宿在开卷机上,开卷机如何动,波纹管就如何动。
开卷机结构如图1所示:工作原理是:回油不锈钢波纹管随开卷机减速机可沿卷筒轴线方向在开卷机底座上移动,生产时由带钢对中控制装置操纵CPC 对中油缸动作,用于对正和调整带钢在机组上的位置。
在减速机底面和固定底座之间装有固定滑轨。
所以回油不锈钢波纹管在生产中就随开卷机运动不停的拉伸和压缩。
3 影响回油波纹管稳定性因素及原因分析平整轧机是热轧卷板浪形产品质量修复和切分钢卷的设备,其生产作业率对热轧卷板厂的经济效率有非常重大的影响。
自机组投产以来,开卷机稀油润滑回油不锈钢波纹管在使用过程中频繁出现开裂漏润滑稀油,导致平整轧机不得不停下生产以更换回油不锈钢波纹管。
如此频繁更换波纹管,一方面严重影响平整轧机生产作业率,另外也极大地加重了维护工人的工作量,同时润滑油和管子备件的消耗高居不下,这与现行大环境的“减耗增效”的大方针相违背。
轧钢设备的润滑故障及改进措施 窦子学

轧钢设备的润滑故障及改进措施窦子学摘要:对于轧钢企业来说,对轧钢设备进行润滑管理是日常生产中极为重要的一环。
润滑对于轧制设备长久稳定的运作有着不可忽视的意义。
本文分析了轧制设备对润滑的要求。
分析了轧制设备中经常发生的润滑故障及其原因。
关键词:轧钢设备;润滑;管理轧钢企业的领导及技术负责人需要从思想意识、操作水平及管理监督方面对润滑管理工作进行重视与加强。
企业还应该不断对内部管理制度进行建设完善,落实责任分配至,以及加强人力资源方面的培训,确保员工具有足够的操作能力,激发员工工作的积极性与严格遵守安全操作规程的意识,让企业的日常生产经营中能够不留下风险隐患。
1轧钢设备的介绍1.1轧钢机械设备概述一般情况下,轧钢机械设备根据其作用被分为主要设备和辅助设备两大类别。
主要设备是企业的大型轧钢机械,其主要通过轧辊之间的往复运动来实现金属的塑性变形,以此来得到某种形状或者某种性能要求的金属制品。
而所谓的辅助设备,则是指的一些与轧钢相关的配套设备的统称,其在这个工序中主要承担辅助和调节的作用,这样有效的辅助促进整个流程更加的和谐和快捷。
1.2 轧钢设备的润滑要求轧机主要由主联轴器、电机、开卷机、万向节等组成。
轧机的主要组成部分有主联轴器、开卷机、电机、万向节等等部件。
在滚动润滑方面有下述要求:润滑设备;干燥润滑油、润滑设备;在高速精密滚动设备上使用油雾或油气润滑。
为了提高轧钢的延伸率和产品质量,通常在轧辊和轧制材料中加入工艺润滑油。
但轧钢设备对于润滑冷却介质的要求是较高的,要求冷却介质具有较高的传热特性,油源充足且具有一定的经济性;轧钢设备表面需随时保持较高的清洁度,在润滑过程中油性保持适中;退火冷轧带钢设备良好;过滤润滑设备良好;润滑。
相应的轧制设备,具有良好的润滑性、防锈性、抗氧化性和稳定性,它可以减少对人体的伤害。
2 存在的问题及原因分析现阶段,就目前我国轧钢企业的管理现状来看,明显的存在很多的疏漏之处,这些会直接导致轧钢机械设备故障频发。
关于轧钢液压和润滑系统的维护与检修探析

关于轧钢液压和润滑系统的维护与检修探析摘要:在轧钢车间中液压润滑系统可以实现无级变速,从而满足轧钢的需求,但是由于轧钢液压与及润滑系统之间会存在许多的问题,经常会引起设备故障,为此必须要加强对于液压以及润滑系统进行定期的维护与检修,这样才能够保证液压和润滑系统的稳定运行,提高轧钢车间的生产效率。
本文通过对于液压和润滑系统在检修过程中存在的问题和不足进行分析,能够有效提高润滑系统维修检测的质量与水平。
关键词:轧钢液压和润滑系统;维护与检修;主要策略随着液压和润滑系统的快速发展,已经逐渐被轧钢车间所采用。
但是如果液压和润滑系统的运行出现问题不仅会影响轧钢的正常生产,而且也会导致出现安全事故,为了维护轧钢车间的正常运转,必须要针对液压和润滑系统进行全面的检修保证工作效率。
一、轧钢液压和润滑系统的主要功能轧钢液压和润滑系统能够独立的在生产线控制系统中进行工作,并且承担着轧钢液压上装置的主要控制任务,可以更好的提高生产精度。
CPU具有2个PROFIBUS-DP接口,通过利用西门子S7-400系列CPU S7-414-2DP系统,构建能够将整个生产控制系统,由DP从站通过PROFIBUS-DP1接口,采用1. 5Mb/s的通讯速率,与产品的主CPU构成DP主从通讯,主要完成整个生产线的启/停控制及轧钢前后主传动装置的速度、张力等数据传输任务,保证轧钢的传动装置可以即时进行数据信息传输。
而轧钢CPU也能够在PROFIUS-DP2网络中作为DP主站,完成轧钢液压上功能,可以实现数据信息实时显示,数据归档和故障报警等多种功能,有效提高了轧钢的工作质量[1]。
(一)位置闭环控制当轧钢液压和润滑系统处于位置闭环模式时,开辊缝和闭辊缝期间,轧辊旋转的同时需要操作侧与传动侧的油缸实现快速响应,为了提高油缸响应动作的整体同步性,轧钢的CPU可以在上位机上进行读取,并且通过位置传感器进行实时的位置信息传输,通过利用输出信号作为主给定,保证伺服放大器驱动伺服阀动作顺利实现。
热连轧机油膜轴承润滑系统的改造
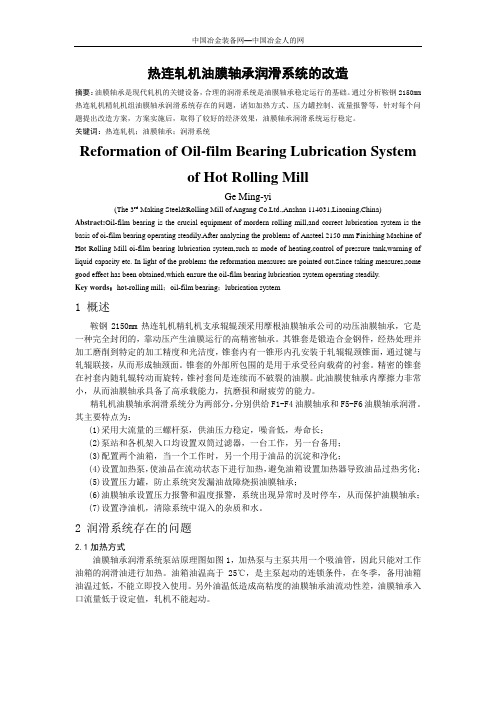
热连轧机油膜轴承润滑系统的改造摘要:油膜轴承是现代轧机的关键设备,合理的润滑系统是油膜轴承稳定运行的基础。
通过分析鞍钢2150mm 热连轧机精轧机组油膜轴承润滑系统存在的问题,诸如加热方式、压力罐控制、流量报警等,针对每个问题提出改造方案,方案实施后,取得了较好的经济效果,油膜轴承润滑系统运行稳定。
关键词:热连轧机;油膜轴承;润滑系统Reformation of Oil-film Bearing Lubrication Systemof Hot Rolling MillGe Ming-yi(The 3rd Making Steel&Rolling Mill of Angang Co.Ltd.,Anshan 114031,Liaoning,China)Abstract:Oil-film bearing is the crucial equipment of mordern rolling mill,and correct lubrication system is the basis of oi-film bearing operating steadily.After analyzing the problems of Ansteel 2150 mm Finishing Machine of Hot Rolling Mill oi-film bearing lubrication system,such as mode of heating,control of pressure tank,warning of liquid capacity etc. In light of the problems the reformation measures are pointed out.Since t aking measures,some good effect has been obtained,which ensure the oil-film bearing lubrication system operating steadily.Key words:hot-rolling mill;oil-film bearing;lubrication system1 概述鞍钢2150mm热连轧机精轧机支承辊辊颈采用摩根油膜轴承公司的动压油膜轴承,它是一种完全封闭的,靠动压产生油膜运行的高精密轴承。
连铸机润滑系统优化

连铸机润滑系统优化摘要:润滑管理工作是连铸各工作中的核心之一。
润滑不充分直接影响设备使用寿命和铸坯表面质量,润滑过量造成浪费同时也成为极大地安全隐患。
润滑系统工作的稳定、给油量的大小、给油时间控制以及管路的合理性,直接影响设备运行状态,所以优化润滑系统能提高设备使用寿命、降低事故率、提高铸坯表面质量以及降低成本。
关键词:连铸机润滑Abstract: Lubrication management is the core of each part of continuous casting. The insufficient lubrication will directly affect the service life of the equipments and the surface quality of casting blank. And the stability of the lubrication system, the amount of oil, oil time control and the rationality of the pipeline will directly influence the running state of the equipment. So, optimizing the lubrication system can improve the service life of the equipment, reduce the accidents, improve the surface quality of casting blank and reduce costs.Key words: continuous caster; lubrication前言承钢120吨转炉升级改造工程,设有165*165方坯八流,165*400~525板坯4流,铸坯供中宽带轧钢生产线及棒材生产线,连铸机的整体设计由中冶连铸负责,中钢衡重负责安装调试。
关于高速线材精轧机稀油润滑的问题研究

关于高速线材精轧机稀油润滑的问题研究摘要:高速线材轧制中对线材轧制速度影响最大的是精轧机。
精轧机的最大轧制速度一般直接影响到整个高线的轧制速度。
关键词:高速线材精轧机稀油润滑因为高速线材生产线是有大量的高压水来冷却的,如需冷却,就必须经过精轧机润滑系统。
油液中有一定的水分(如乳化水、溶解水、游离水等),会给运行带来一定的运行影响。
如:使润滑效果变差,促使油品氧化变质,轴承腐蚀,加速有机酸对金属的腐蚀,低温时使油品流动性变差,高温时汽化,产生气阻,造成油品粘度升高。
此外油中含水量超标还会导致油箱内含大量气泡,而出现浮动吸油口吸空等故障现象。
1、对高速线材轧机生产工艺特点分析高速线材轧机以其合理的孔型系统和高适应性的机电设备及布置方式,使其产品规格范围远比常规线材轧机的大。
其发展是由改造线材轧机的精轧机组和控冷工艺开始的。
高速轧机生产技术成熟以后可广泛应用于小型和线材轧机的改造,这是因为精轧机组无论是在生产效率上,还是产品质量上都大大优于横列式轧机。
通常高速线材轧机的工艺特点可以概括为连续、高速、无扭和空冷,其中高速轧制是最主要的工艺特点。
大盘重高精度性能优良则是高速线材轧机的产品特点。
在轧制速度取得突破性进展以后,人们仍追求更高的轧制速度。
因为轧制速度高,生产效率就高,成本就低,所以速度就是效益。
2、高速线材精轧机稀油润滑站内容分析高速线材精轧机稀油润滑站共供应三个部分的润滑,一是高速线材精轧机前夹送辊、碎断剪等设备的区域;二是高速线材精轧机后吐丝机及其夹送辊的区域;三是精轧机及其传动增速箱的区域。
高速线材精轧机共十对轧辊,由于每对轧辊的供油管和回油管尺寸、长度基本一致,所以系统在每对轧辊前的供油管上仅仅设置了一个测压点,而在主供油管的末端设置了一个压力继电器和一个压力表,用来观测精轧机供油的情况。
3、对高速线材精轧机稀油润滑的重要性分析如今,在高速轧机的轴承润滑上,使用油气润滑是比较普遍的一种润滑方法。
- 1、下载文档前请自行甄别文档内容的完整性,平台不提供额外的编辑、内容补充、找答案等附加服务。
- 2、"仅部分预览"的文档,不可在线预览部分如存在完整性等问题,可反馈申请退款(可完整预览的文档不适用该条件!)。
- 3、如文档侵犯您的权益,请联系客服反馈,我们会尽快为您处理(人工客服工作时间:9:00-18:30)。
机才能正常工作 。 连轧管机的轧制中心线标高约 1 m,
1 ,3 ,5 一 轧 辊 ;7 ,9 减速 箱 ;1 ,1 , 1 ,1一 电机 ; ,2 ,4 ,6 ,8 一 0 1 2 3 1一 油 箱 ;1 ,2 ,2 ,2 ,3 ,3 ,3一 流量 计 ;1一 闸阀 ; 6 8 3 4 5 6 7 8 9 1 ,2 ,2 ,2 一 电子 压 力 继 电器 ;2 ,2 ,2一 截 止 阀 ; 7 0 1 2 7 8 9 3 ,3 ,3一 润 滑 泵 ;3 ,3~ 电子 压 力继 电器 ;3 ,4 ,4一 开 启 闸 阀 ; O 1 2 3 5 9 0 1
稀油润滑系统改进后投人运行 ,主操作 室显示
各减 速 箱人 口的润 滑油 流 量 和压 力 均达 到 工艺 设 计
润滑油泵供送各部位 的所有减速箱 的稀油润滑 。由 于各个减速箱的布置位置及其配管不尽相同 ,所以 每个方位的减速箱很难分配到其所需 的理论流量 , 很可能有的过量 , 的不足 ,这便是上述故障发生 有
4 应用效 果
拆开摩擦副附近的管接头 。发现有部分管子流 油不充分 ,有的甚至断流。初步断定故 障产生的原 因为润滑油量不足 ,所以才出现部分轴承被烧损 的 故障。 由理论计算得知 :左轧辊和右轧辊减速箱所需
的润 滑油 量 相 同 ,且 不 同 于上轧 辊 减速 箱 。 3 方 个 位 的 9个减 速 箱共用 图 1中的稀油 润 滑站 ,由 l台
油 口约 1 . m。 5 2 故 障发生 及技 术分 析
图 2 改进后 稀油润滑原理
改进后的稀油润滑系统工作原理如下 : 开启闸阀 ,启 动润滑泵 ,压力油 P 进入上轧 l 辊方位减速箱 ,减速箱入 口安装有截止阀、流量计
及 电子压 力 继 电器 ;同理 ,开启 闸 阀 ,压 力 油 进入
Ke r s y wo d :ma d e l n r l mi ;man t n miso ;r l i lb c t g s se l i r s s in o l l u r a i y t m a ;o i n
●用技术l
1 个右辊减速箱 ,轧辊由电机经减速箱传动。 图1 示出了改进前连轧管机主传动轴 的稀油润
滑 系统控 制原 理 。
的主要原 因。 3 改进 后 的稀油 润稀油润滑原理改
进 ,得 到 图 2所示 的稀油 润滑原 理 。
稀油润滑系统由稀油润滑站、减速箱人 口的电 子压力继电器及连接油管组成 。稀油润 滑站 中包含润滑油泵装 置 、油箱装置 、 电子 压 力 继 电器 、流 量 计 、闸 阀 , 滑 润
Ja W e- o g i id n
( eh o g etr T iu n Hev n h ty C .L d ay a 3 0 4 C ia T c n l y C ne, ay a ay Id s o, t,T iu n 00 2 hn ) o r
Ab t a t n t i a r h u h r b e y i t d c d wo k n r cp e o i l b c t g s se .Th n h e a t o e p y a ‘ sr c :I h s p pe,t e a t o r f n r u e r ig p n i l f o l u r ai y tm i l o i i n e ,t u r d e l n h a y e a l n p ro f t si g o q i me t n u o wa d p a t a e o mi g s h me lz d f u t i e d o e t f e u p n ,a d p t f r r r ci l r f r n c e ,wh c b an d e c l n e u t. s i n c ih o t ie x el t r s l e s
站还有冷却及过滤装置 , 图中未示出。
稀油润滑系统的工作原理如下 :
完全 开启 闸阀 ,启 动润 滑 油泵 ,压
力油 P分 三路分别进 人减速 箱进行 润
滑 ,减速箱 的回油到稀油润滑站的油箱
一
内。连轧管机工作过程 中,稀油润滑站 直处于运行状态 。只有主传动减速箱 中各润滑部位得到充分润滑后 .连轧管
T ,T ,T 回 油 口 ;P ,P ,P 压 力 油 1 2 厂 1 2 厂
上轧辊主传动减速箱 的标高约 7 m,左 轧辊 和右轧辊 主传 动减 速箱 的标高相同 ,约为负
5m。 由于稀 油 润 滑站 为 自回油 ,所 以润 滑 站 放 置 于 地坑 内 ,润滑 站 的 回油 口低 于左 右辊 减速 箱 的 回
左轧辊方位和右轧辊方位的减速箱 .减速箱入 口分
别 安 装 有截 止 阀 ,流 量 计 和 电子 压 力 继 电器 。3个
设备在用户调试期间,出现部分轴承被磨损或
烧 坏 的现 象 。严重影 响了连轧 管机 的正 常工作 。
方位减速箱 的回油汇集一处流由 T口流 回油箱 。 3条压力油路完全独立工作 ,调节每个减速箱 人 口的截止 阀,可调节进入该减速箱 的润滑油量 : 各减速箱入 口和稀油润滑站各支路压力油的压力和 流量均可通过电子压力继电器和流量计在 主操作室 模拟显示并加以控制。
要求 . 再没发生上述类似故障,很好地保证了连轧 管机的正常工作 ,得到用户的认可。
( 实习编辑 高 腾)
I p o i g Oi Lu r c t g S se o a n Tr n m iso f a d e i m r vn l b i a i y t m f n M i a s si n o n r l l M M l