电子齿轮之概念
南京科远HCSE系列交流伺服用户手册(V1.02)
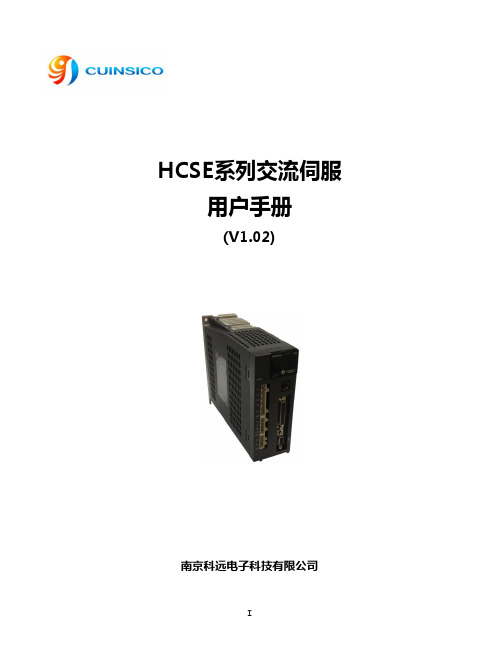
若在电源和伺服驱动器输入端之间加装接触器,则不允许用此接触器来控制伺服驱动器的启停。一定需要用该接触器控制 伺服驱动器的启停时,间隔不要小于一个小时。频繁的充放电易降低伺服驱动器内电容的寿命。若输出端和电机之间装有接触 器等开关器件,应确保伺服驱动器在无输出时进行通断操作,否则易造成伺服驱动器内模块损坏。 ■ 三相输入改成两相输入
HCSE系列交流伺服 用户手册
(V1.02)
南京科远电子科技有限公司
I
电机机型设置
用户拿到伺服驱动器和电机第一次运行时,请参照适配机型表(如果适配机型表中没有对 应的电机型号,请根据所用电机的额定转速和额定电流,来选择电机机型),确认电机机型设 置是否正确,如果不正确,运行时电机可能会出现振动或误报警现象,不能达到期望的控制效 果。机型参数为Pn223,属于隐藏参数,需要解锁方能进入,在数码管为“run”、”bb”或报 警状态显示界面下,按“上下下下”(一次UP键,三次DOWN键)即可解锁。机型设置正确后, 需重新上电,方可运行电机。以后如果电机型号有变动,则需重新设置。
1314面板按键操作说明1441按键的名称与功能1442基本模式的选择与操作1543状态显示16431位数据显示内容16432省略符号显示内容1644辅助功能模式下的操作fn17441辅助功能执行模式的用户参数一览及其功能17442显示伺服报警记录18443微动jog模式运行18444用户参数设定值进行初始化1945用户参数设定模式下的操作pn20451用户参数的设定2046监视模式下的操作un21461监视模式一览及其功能21462顺序用输入输出信号的监视显示22463指令脉冲计数器反馈脉冲计数器的监视显示2451试运行2452通用功能的设定25521伺服on设定25522超程设定25523伺服off时的停止方法选择2553位置控制运行25531用户参数的设定26532电子齿轮的设定27533编码器反馈信号输出分频系数27534位置指令28535平滑29537外部扭矩限制3054其他31541旋转检测速度31542超速报警功能31543数字输入接脚di输入滤波使能31544伺服控制信号输入input管脚功能配置
电子齿轮比计算公式

对于那些想学习PLC的人来说,第一件事就是控制伺服电机。
要控制伺服电机,必须联系电子传动比的概念。
这是从初学者到初学者的门槛。
很多人被困在这里,无法进入。
虽然你可以通过别人的文章或介绍粗略地设置电子传动比,但总是毫无意义。
因此,今天笔者将详细介绍电子传动比的相关概念和设置方法,为大家解决难题。
1齿轮传动比我相信每个人都熟悉齿轮。
通常,齿轮成对出现。
两个齿轮的模数相同,但齿数不同。
这样,旋转后就会形成速度差。
通常,产生这种速度差的方法称为传动比:干货:电子传动比的超详细计算方法在上图中,大齿轮和小齿轮的传动比为2:1,因此传动比为1:2。
小轮旋转两次,大轮子旋转一次。
电动机驱动小轮,小轮作驱动轮,大轮作从动轮,减速比为1:2。
2电子传动比在物理上理解了传动比后,更容易理解电子传动比,因为电机的控制是由上位机发送的脉冲,电机的转速是由编码器测量的。
然而,当伺服电机旋转时,主机发送的脉冲数与测量到的脉冲数之间没有一一对应关系。
它们之间有一个比率,叫做“比率”。
干货:电子传动比的超详细计算方法改变干货:电子传动比的超详细计算方法第一种情况:伺服电机直接连接到丝杠上干货:电子传动比的超详细计算方法此时减速比为1:1,螺距设置为5mm,伺服电机编码器的分辨率为131072。
当我们要上位机发送脉冲时,丝杠移动0.001mm,螺杆移动5mm,上位机需要发送5000个脉冲,电机旋转一次,编码器采集的值为131072,电子传动比为:干货:电子传动比的超详细计算方法由于分子和分母同时除以最大公约数8,电子齿轮的分子为16384,分母为625。
当然,你也可以直接写分子为131072,分母为5000在第二种情况下,伺服电机和丝杠通过减速机构连接干货:电子传动比的超详细计算方法假设减速比为2:3,伺服电机旋转3次,丝杠旋转2次,计算减速比,使每5000脉冲达到5mm。
丝杠旋转一圈(5mm),电机旋转1.5圈(3/2=1.5),编码器采集的实际值为131072*3/2,电子传动比为干货:电子传动比的超详细计算方法分子是24576分母是625。
电子齿轮比计算公式

想要学习PLC的朋友的第一件事就是控制伺服电机。
要控制伺服电机,您必须联系电子齿轮比的概念。
这是从初学者到初学者的门槛。
许多人被困在这里,无法进门。
尽管您可以通过其他人的文章或介绍来大致设置电子齿轮比,但这始终毫无意义。
因此,今天我将详细介绍与电子齿轮比相关的概念和设置方法,以供大家解决难题。
1,齿轮比我相信每个人都熟悉齿轮。
通常,齿轮成对出现。
两个齿轮的模数相同,但齿数不同。
这样,旋转后会形成速度差。
通常,产生这种速度差的方法称为齿轮比:干货:电子齿轮比的超详细计算方法在上图中,大齿轮和小齿轮的齿数比为2:1,因此速比为1:2。
小轮旋转两次,大轮旋转一圈。
如果电动机驱动小轮,小轮作为驱动轮,大轮作为从动轮,则减速比为1:2。
2,电子齿轮比在物理上理解了齿轮比之后,就更容易理解电子齿轮比了,因为电动机的控制是上位计算机发送的脉冲,电动机的旋转由编码器测量。
但是,上位机发送的脉冲数与伺服电机旋转时测得的脉冲数不是一一对应的,它们之间存在一个比率,称为“比率”。
干货:电子齿轮比的超详细计算方法更改干货:电子齿轮比的超详细计算方法第一种情况:伺服电机直接与丝杠连接干货:电子齿轮比的超详细计算方法此时,减速比为1:1,螺丝螺距设置为5mm,伺服电机编码器的分辨率为131072。
当我们希望上位机发送脉冲时,丝杠移动0.001mm,螺丝移动5mm,上位机需要发送5000个脉冲,电机旋转一次,编码器采集的值为131072,则电子齿轮比为:干货:电子齿轮比的超详细计算方法由于分子和分母同时被最大公约数8除,因此电子齿轮的分子为16384,分母为625。
当然,也可以直接将分子写为131072,将分母写为5000在第二种情况下,伺服电机和丝杠通过减速机构连接干货:电子齿轮比的超详细计算方法假设减速比为2:3,伺服电机旋转3次,丝杠旋转2圈,则应计算减速比,以使每5000个脉冲达到5 mm。
当丝杠旋转一圈(5毫米)时,电动机旋转1.5圈(3/2 = 1.5),编码器收集的实际值为131072 * 3/2,则电子齿轮比为干货:电子齿轮比的超详细计算方法因此分子是24576,分母是625,这是电子齿轮比的算法。
步进电机伺服电机

7.3.1 认知步进电机及驱动器1、步进电动机简介步进电动机是将电脉冲信号转换为相应的角位移或直线位移的一种特殊执行电动机。
每输入一个电脉冲信号,电机就转动一个角度,它的运动形式是步进式的,所以称为步进电动机。
(1)步进电动机的工作原理下面以一台最简单的三相反应式步进电动机为例,简介步进电机的工作原理。
图7-10是一台三相反应式步进电动机的原理图。
定子铁心为凸极式,共有三对(六个)磁极,每两个空间相对的磁极上绕有一相控制绕组。
转子用软磁性材料中制成,也是凸极结构,只有四个齿,齿宽等于定子的极宽。
图7-10 三相反应式步进电动机的原理图当A相控制绕组通电,其余两相均不通电,电机内建立以定子A相极为轴线的磁场。
由于磁通具有力图走磁阻最小路径的特点,使转子齿1、3的轴线与定子A相极轴线对齐,如图7-10(a)所示。
若A相控制绕组断电、B相控制绕组通电时,转子在反应转矩的作用下,逆时针转过30°,使转子齿2、4的轴线与定子B相极轴线对齐,即转子走了一步,如图7-10(b)所示。
若在断开B相,使C相控制绕组通电,转子逆时针方向又转过30°,使转子齿1、3的轴线与定子C相极轴线对齐,如图7-10(c)所示。
如此按A—B—C—A的顺序轮流通电,转子就会一步一步地按逆时针方向转动。
其转速取决于各相控制绕组通电与断电的频率,旋转方向取决于控制绕组轮流通电的顺序。
若按A—C—B—A的顺序通电,则电动机按顺时针方向转动。
上述通电方式称为三相单三拍。
“三相”是指三相步进电动机;“单三拍”是指每次只有一相控制绕组通电;控制绕组每改变一次通电状态称为一拍,“三拍”是指改变三次通电状态为一个循环。
把每一拍转子转过的角度称为步距角。
三相单三拍运行时,步距角为30°。
显然,这个角度太大,不能付诸实用。
如果把控制绕组的通电方式改为A→AB→B→BC→C→CA→A,即一相通电接着二相通电间隔地轮流进行,完成一个循环需要经过六次改变通电状态,称为三相单、双六拍通电方式。
电子齿轮的实现方法

电子齿轮的实现方法1电子齿轮的用途在运动控制装置中,当机械系统的结构确定以后,电机跟机械装置的传动关系也就固定了,电机每转一圈产生的机械位移量也就固定了,而位置控制命令通常由上位机产生一定数量的定位脉冲来实现的,这些脉冲称为指令脉冲。
在大多数情况下,指令脉冲当量(单个脉冲对应的机械系统位移量)和位置反馈脉冲当量(单个位置反馈脉冲对应的机械系统的位移量)是不相同的,需要采用电子齿轮来匹配二者的对应关系,使指令当量折算到定位控制回路后与反馈脉冲当量相等,因此,电子齿轮就是指令脉冲当量与电机编码器反馈脉冲当量的一个比值。
光电编码器是伺服电机常用的位置反馈元件,其码盘的刻线数量决定了伺服电机的控制精度。
在实际应用中,不同的机械系统有不同的传动参数,有了电子齿轮,就可以随意设定一个指令脉冲所对应的电机转动量。
例如:车床用10mm螺距的丝杠,电机每旋转一圈,机械装置移动10mm,每移动0.001mm就需要电机旋转1/10000圈(0.001/10),如果连接5mm的丝杠,每0.001mm的移动量就需要电机旋转1/5000转,对于同一个伺服电机,1/10000和1/5000确定了这二个机械系统的指令脉冲当量,反馈脉冲当量由编码器刻线数量决定,是固定不变的,不能更改,为了满足这二个机械系统的要求,通过改变电子齿轮的参数设置,就可以获得指令脉冲当量与反馈脉冲当量所对应的准确的比例关系。
换句话说,有了电子齿轮,伺服电机才能够以固定的反馈脉冲当量来适应不同的机械系统。
为了实现一定精度的定位控制,指令脉冲当量ΔL在数值上往往远大于反馈脉冲当量ΔM,或者说需要很多个ΔM才能与ΔL等价,如果ΔL在数值上小于或者与ΔM相仿,那控制系统的定位控制精度就无法得到保障,这就是编码器刻线数量越做越高的原因。
假定传动机构的螺距为W,光电脉冲编码器每转脉冲数为P,且电机轴和传动丝杠是直接相连的,则位置反馈脉冲当量ΔM为:ΔM=W/(4P)(1)上式中的4表示对光电编码器的输出脉冲做4倍频处理。
伺服系统位置控制中的“电子齿轮”分析
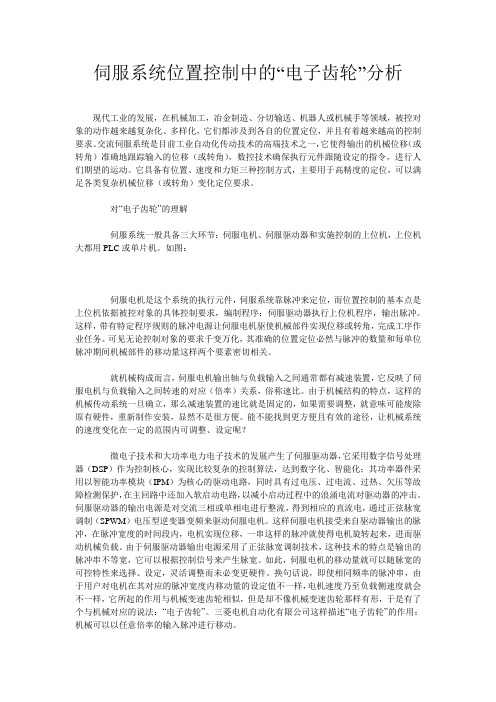
伺服系统位置控制中的“电子齿轮”分析现代工业的发展,在机械加工,冶金制造、分切输送、机器人或机械手等领域,被控对象的动作越来越复杂化、多样化,它们都涉及到各自的位置定位,并且有着越来越高的控制要求。
交流伺服系统是目前工业自动化传动技术的高端技术之一,它使得输出的机械位移(或转角)准确地跟踪输入的位移(或转角),数控技术确保执行元件跟随设定的指令,进行人们期望的运动。
它具备有位置、速度和力矩三种控制方式,主要用于高精度的定位,可以满足各类复杂机械位移(或转角)变化定位要求。
对“电子齿轮”的理解伺服系统一般具备三大环节:伺服电机、伺服驱动器和实施控制的上位机,上位机大都用PLC或单片机。
如图:伺服电机是这个系统的执行元件,伺服系统靠脉冲来定位,而位置控制的基本点是上位机依据被控对象的具体控制要求,编制程序;伺服驱动器执行上位机程序,输出脉冲。
这样,带有特定程序规则的脉冲电源让伺服电机驱使机械部件实现位移或转角,完成工序作业任务。
可见无论控制对象的要求千变万化,其准确的位置定位必然与脉冲的数量和每单位脉冲期间机械部件的移动量这样两个要素密切相关。
就机械构成而言,伺服电机输出轴与负载输入之间通常都有减速装置,它反映了伺服电机与负载输入之间转速的对应(倍率)关系,俗称速比。
由于机械结构的特点,这样的机械传动系统一旦确立,那么减速装置的速比就是固定的,如果需要调整,就意味可能废除原有硬件,重新制作安装,显然不是很方便。
能不能找到更方便且有效的途径,让机械系统的速度变化在一定的范围内可调整、设定呢?微电子技术和大功率电力电子技术的发展产生了伺服驱动器,它采用数字信号处理器(DSP)作为控制核心,实现比较复杂的控制算法,达到数字化、智能化;其功率器件采用以智能功率模块(IPM)为核心的驱动电路,同时具有过电压、过电流、过热、欠压等故障检测保护,在主回路中还加入软启动电路,以减小启动过程中的浪涌电流对驱动器的冲击。
电子齿轮表工作原理
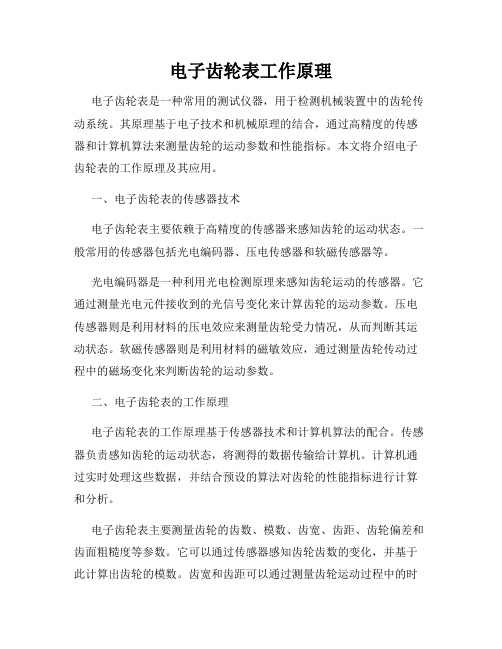
电子齿轮表工作原理电子齿轮表是一种常用的测试仪器,用于检测机械装置中的齿轮传动系统。
其原理基于电子技术和机械原理的结合,通过高精度的传感器和计算机算法来测量齿轮的运动参数和性能指标。
本文将介绍电子齿轮表的工作原理及其应用。
一、电子齿轮表的传感器技术电子齿轮表主要依赖于高精度的传感器来感知齿轮的运动状态。
一般常用的传感器包括光电编码器、压电传感器和软磁传感器等。
光电编码器是一种利用光电检测原理来感知齿轮运动的传感器。
它通过测量光电元件接收到的光信号变化来计算齿轮的运动参数。
压电传感器则是利用材料的压电效应来测量齿轮受力情况,从而判断其运动状态。
软磁传感器则是利用材料的磁敏效应,通过测量齿轮传动过程中的磁场变化来判断齿轮的运动参数。
二、电子齿轮表的工作原理电子齿轮表的工作原理基于传感器技术和计算机算法的配合。
传感器负责感知齿轮的运动状态,将测得的数据传输给计算机。
计算机通过实时处理这些数据,并结合预设的算法对齿轮的性能指标进行计算和分析。
电子齿轮表主要测量齿轮的齿数、模数、齿宽、齿距、齿轮偏差和齿面粗糙度等参数。
它可以通过传感器感知齿轮齿数的变化,并基于此计算出齿轮的模数。
齿宽和齿距可以通过测量齿轮运动过程中的时间和位移来计算得出。
齿轮偏差则是通过传感器测量齿轮的偏移情况,并进行相应的修正。
齿面粗糙度可以通过传感器测量齿轮表面的微小起伏来判断。
三、电子齿轮表的应用电子齿轮表广泛应用于机械制造领域,尤其是对齿轮精度要求较高的行业。
它可以对不同类型和尺寸的齿轮进行精确测量,可以检测齿轮的精度级别,从而保证齿轮传动系统的正常工作。
在机械制造过程中,电子齿轮表可以用于对齿轮进行质量检验和评估。
通过测量齿轮参数,可以判断齿轮的加工质量和装配精度,并及时调整和纠正。
在齿轮的设计和研发过程中,电子齿轮表可以用于验证设计参数的准确性,并辅助优化齿轮结构,提高齿轮的工作效率和可靠性。
此外,电子齿轮表还可以应用于设备的维修和维护。
齿轮的概念
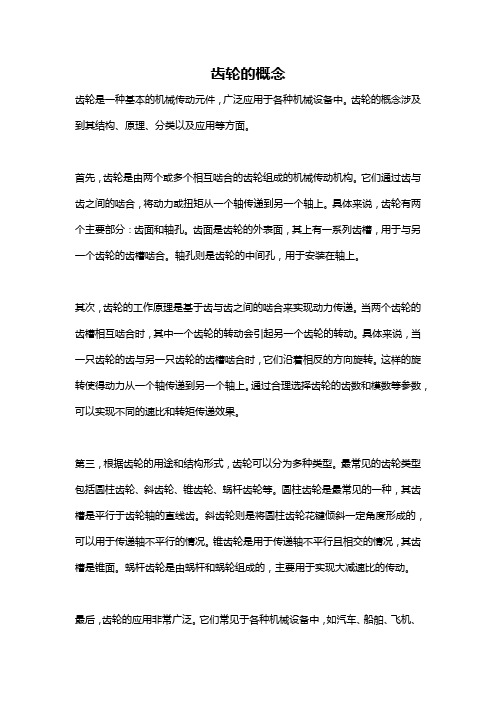
齿轮的概念齿轮是一种基本的机械传动元件,广泛应用于各种机械设备中。
齿轮的概念涉及到其结构、原理、分类以及应用等方面。
首先,齿轮是由两个或多个相互啮合的齿轮组成的机械传动机构。
它们通过齿与齿之间的啮合,将动力或扭矩从一个轴传递到另一个轴上。
具体来说,齿轮有两个主要部分:齿面和轴孔。
齿面是齿轮的外表面,其上有一系列齿槽,用于与另一个齿轮的齿槽啮合。
轴孔则是齿轮的中间孔,用于安装在轴上。
其次,齿轮的工作原理是基于齿与齿之间的啮合来实现动力传递。
当两个齿轮的齿槽相互啮合时,其中一个齿轮的转动会引起另一个齿轮的转动。
具体来说,当一只齿轮的齿与另一只齿轮的齿槽啮合时,它们沿着相反的方向旋转。
这样的旋转使得动力从一个轴传递到另一个轴上。
通过合理选择齿轮的齿数和模数等参数,可以实现不同的速比和转矩传递效果。
第三,根据齿轮的用途和结构形式,齿轮可以分为多种类型。
最常见的齿轮类型包括圆柱齿轮、斜齿轮、锥齿轮、蜗杆齿轮等。
圆柱齿轮是最常见的一种,其齿槽是平行于齿轮轴的直线齿。
斜齿轮则是将圆柱齿轮花键倾斜一定角度形成的,可以用于传递轴不平行的情况。
锥齿轮是用于传递轴不平行且相交的情况,其齿槽是锥面。
蜗杆齿轮是由蜗杆和蜗轮组成的,主要用于实现大减速比的传动。
最后,齿轮的应用非常广泛。
它们常见于各种机械设备中,如汽车、船舶、飞机、工业机械等。
齿轮的应用可以实现不同的目的,如转速变换、扭矩放大、方向改变等。
例如,在汽车中,齿轮传动用于将发动机转速传递到车轮,实现汽车的前进和倒退。
在船舶中,齿轮传动用于传递发动机的功率到螺旋桨,推动船只行进。
在工业机械中,齿轮传动被广泛应用于各种机床、输送设备、风力发电机组等。
总之,齿轮作为一种基本的机械传动元件,在机械领域扮演着十分重要的角色。
通过齿轮的啮合传动,动力和扭矩可以有效地传递和转换,实现不同的运动效果和功能。
齿轮的应用范围广泛,不仅可以实现传动功能,还可以用于变速、变扭矩、方向转换等,为各种机械设备的性能提供了重要的支持和保障。
电子齿轮

电子齿轮的设置
一、电子齿轮的概念:
通过调整电子齿轮(通过设置参数PA06、PA07)可以使伺服放大器的设置与机械位移相匹配。
同样,通过改变电子齿轮的值可以使机器以任意的加速比移动至伺服放大器设定的位移。
⎩
⎨⎧07PA :CDV 06PA :CMX 参数参数
公式 1000
r n Pt S Pt CDV CMX ⋅π⋅⋅=∆= 其中:n 是电机减速器中的减速比,n=NL/NM
Pt 是伺服电机的分辨率,可查
二、例子
我们采用的是传送带方式,以下是传送带方式下电子齿轮的设置的例子:
参数:
1减速比: n=1/3
2皮带轮的直径: r=160(mm)
3 伺服电机分辨率:Pt=262144(pulse/rev)
套入公式:
20944
3276861.16755126214410001603/12621441000r n Pt S Pt CDV CMX ≈=⋅π⋅⋅=⋅π⋅⋅=∆= 所以,将PA06的值设为32768,将PA07的值设为20944。
以上还需查询伺服电机的参数Pt ,和计算减速器的减速比的参数n 。
三、应用
我们项目中的参数:
1 减速比n=1/88
2 皮带轮直径r=268mm
3 伺服电机分辨率Pt=4000~16000,这里我们先取4000
带入公式:
84194735200083.841946352000100026888/140001000r n Pt S Pt CDV CMX ≈=⋅π⋅⋅=⋅π⋅⋅=∆= 所以将参数PA06设置为352000,参数PA07设置为841947。
电子齿轮原理及实现方法

·南京工程学院李宁南京埃斯顿自动化技术公司徐俊王晓伟王帆·文章分析了数字式交流伺服系统中的电子齿轮环节的作用,介绍了电子轮的基本原理。
给出了一种在数字式交流伺服系统中实现电子齿轮功能的方法,同时介绍了大规模可编程逻辑器件在这方面的应用。
最后分析了电子齿轮的控制精度。
电子齿轮原理及实现方法本文来自2003年第8期“伺服专栏”上 ,已经被阅读过379次1 概述全数字交流伺服系统具有以往的模拟式伺服系统所无法具有的一系列新的功能,如电子齿轮功能,自动辨识电机参数的功能,自动整定调节器控制参数功能,自动诊断故障的功能等。
正是由于具有这一系列新的功能,用户灵活掌握和调整的余地更大了,使用更为便利,同时也提高了性能,因而使全数字交流伺服系统得到了迅速的推广应用。
从1997年以来,我们一直从事全数字交流伺服系统的研制工作,目前已取得了阶段性成功。
本文将介绍全数字交流伺服系统中电子齿轮的原理及实现方法。
2 电子齿轮的原理数字交流伺服系统具有位置控制的功能,上位控制机向伺服系统发出位置指令脉冲。
位置指令脉冲具有3种形式:①方向信号+脉冲序列;②CCW脉冲序列+CW脉冲序列;③正交二相脉冲序列。
如图1所示。
图l 位置指令脉冲指令脉冲序列包含了两方面的信息,一是指明电机运行的位移,二是指明电机运行的方向。
通常指令脉冲单位是0.001 mm或0.01 mm等,而伺服系统的位置反馈脉冲当量由检测器(如光电脉冲编码器等)的分辨率,以及电机每转对应的机械位移量等决定。
当指令脉冲单位与位置反馈脉冲当量二者不一致时,就可使用电子齿轮使二者完全匹配。
使用了电子齿轮功能,可以任意决定一个输入脉冲所相当的电机位移量。
发出指令脉冲的上位控制装置无须关注机械减速比和编码器脉冲数就可以进行控制。
图2是具有电子齿轮功能的伺服系统结构。
图2 伺服系统结构图在图2中,机械传动机构的螺距为W,指令脉冲当量为ΔL,光电脉冲编码器每转脉冲数为P,一般电机轴与传动丝杠是直接相连的,这样就可以确定位置反馈脉冲当量ΔM。
电子齿轮
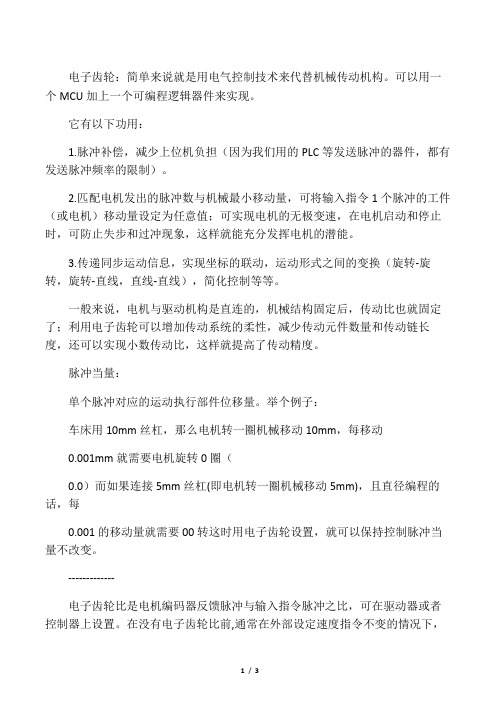
电子齿轮:简单来说就是用电气控制技术来代替机械传动机构。
可以用一个MCU加上一个可编程逻辑器件来实现。
它有以下功用:1.脉冲补偿,减少上位机负担(因为我们用的PLC等发送脉冲的器件,都有发送脉冲频率的限制)。
2.匹配电机发出的脉冲数与机械最小移动量,可将输入指令1个脉冲的工件(或电机)移动量设定为任意值;可实现电机的无极变速,在电机启动和停止时,可防止失步和过冲现象,这样就能充分发挥电机的潜能。
3.传递同步运动信息,实现坐标的联动,运动形式之间的变换(旋转-旋转,旋转-直线,直线-直线),简化控制等等。
一般来说,电机与驱动机构是直连的,机械结构固定后,传动比也就固定了;利用电子齿轮可以增加传动系统的柔性,减少传动元件数量和传动链长度,还可以实现小数传动比,这样就提高了传动精度。
脉冲当量:单个脉冲对应的运动执行部件位移量。
举个例子:车床用10mm丝杠,那么电机转一圈机械移动10mm,每移动0.001mm就需要电机旋转0圈(0.0)而如果连接5mm丝杠(即电机转一圈机械移动5mm),且直径编程的话,每0.001的移动量就需要00转这时用电子齿轮设置,就可以保持控制脉冲当量不改变。
-------------电子齿轮比是电机编码器反馈脉冲与输入指令脉冲之比,可在驱动器或者控制器上设置。
在没有电子齿轮比前,通常在外部设定速度指令不变的情况下,通过改变电机轴输出侧的机械齿轮的比值来改变电机的转速,而通过电子齿轮比的参数值设定可以在机械齿轮外部设定速度指令不变的情况下灵活的改变电机的速比以匹配用户实际应用,由于是通过电子器件来实现的类似机械齿轮的速比变化所以称为电子齿轮比。
电子齿轮比只能改变速比,并不具备机械齿轮的速比变化同时的转矩变化,所以在需要将电机输出转矩进行低速放大时还要使用机械齿轮才可以。
------------在非超载的情况下,电机的转速、停止的位置只取决于脉冲信号的频率和脉冲数(导电次数),和占空比没有关系。
伺服电机电子齿轮比的算法完整版

伺服电机电子齿轮比的算法HEN system office room 【HEN16H-HENS2AHENS8Q8-HENH1688】伺服电机电子齿轮比的算法一般来说主要由三大因素组成:1、要知道电机转一圈雕刻机的X/Y/Z走多少距离;2、上位机脉冲当量的单位:“毫米/脉冲”还是“脉冲/毫米”;3、伺服电机电子齿轮比的分子与分母。
而分子的基数一般是固定的,只需输入此值就行,而常见的国内分体的伺服电机,它的分子的值与编码器精度有关,精度说法不外乎有两种:一、讲多少线的,比如常见的为2500线,那么它的分子的值为2500的四倍,即10000,如我司分体的就是这样算的。
二、讲多少位,位是指2的幂次方,比如安川的17位、20位就是2的17或20次方。
第1个:要知道电机转一圈雕刻机的X/Y/Z走多少距离1、丝杆机:这个简单,只要知道丝杆的导程(现场一般叫螺距,但书面上来说两者的是不一样的概念。
我们可从它们的相同点来说只要是单头螺纹的丝杆这两者的说法就无区别),然后知道传动比(这又分为减速的传动比还是加速的传动比),然后按以下算法:电机转一圈距离=导程X传动比注:减速传动比一般分子比分母小,如1/3、1/5等等,加速传动比般为分子比分母大,如3/1、5/1等等。
2、齿轮齿条机;按以下算法:电机转一圈距离=齿轮模数X齿轮齿数传动第2个:“毫米/脉冲”与“脉冲/毫米”转换关系如下:“毫米/脉冲”转“脉冲/毫米”:脉冲/毫米=1 /输入的“毫米/脉冲”数值,比如输入值为,那么就等于100脉冲/毫米。
“脉冲/毫米”转“毫米/脉冲”:毫米/脉冲=1 //输入的“脉冲/毫米”数值,比如输入值为100,那么就等于毫米/脉冲第3个:电子齿轮比的分母或脉冲当量(单位为毫米/脉冲)的算法电子齿轮比的分母=电机转一圈距离/脉冲当量从这个算法公式可看出,电子齿轮比的分母或脉冲当量这两者必须有一个是人为任意设置一个数值(只要不超过说明书的许可范围,一般电子齿轮比的分母不超过分子,脉冲当量不超过),另一个才可能求出。
驱动器电子齿轮比

驱动器电子齿轮比1、什么是电子齿轮?他是怎么改变脉冲频率的?2、电子齿轮其实质就是一个二进制计数器:1)17位二进制计数器,我们从最低位编号,17位二进制计数器由1位、2位、3位、……、17 位构成,就和大家熟悉的十进制数位一样,有个位、十位、百位、千位、……一样2)二进制计数器,每一位只能输出0或者1,记数时各数位不断由0变为1,再由1变成0,这时就输出一个矩形脉冲;3)当我们给计数器输入矩形脉冲时,计数器对输入的脉冲开始计数,你会发现,各数位输出的脉冲数不同:3、电子齿轮改变频率的原理就是,二进制计数器分频就是由低位改到高位输出,倍频就是由高位改到低位输出;例如:当我们输入131072个脉冲时,各数位输出的脉冲数分别是:1位:1310722位: 655363位: 327684位: 163845位: 81926位: 40967位: 20488位: 10249位: 51210位: 25611位: 12812位: 6413位: 3214位: 1615位: 816位: 417位: 24)当我们给17位二进制计数器,输入的脉冲频率为131072个/s,那么计数器各位的输出脉冲频率就是:1位:131072个/s2位: 65536个/s……16位: 4个/s17位: 2个/s5)那么18位、19位、20位、21位计数器,各位脉冲频率是:1位:131072个/s 262144 524288 1048576 20971522位: 65536个/s 131072 262144 524288 10485763位: 32768个/s 65536 131072 262144 5242884位: 16384个/s 32768 65536 131072 2621445位: 8192个/s 16384 32768 65536 1310726位: 4096个/s 8192 16384 32768 655367位: 2048个/s 4096 8192 16384 327688位: 1024个/s 2048 4096 8192 163846)你发现了没有,实际你花大价钱买的20位的编码器,只是计数器的1位输入的脉冲数、脉冲频率不同而已;7)17位、18位、19位、20位、21位编码器,本质是一样的,结构是一样的,他可以随便把17位的编码器随便说成20位的编码器;8)当然18位、19位、20位、21位计数器是相同的,但是编码器的刻线不同,就是转一周输入计数器的脉冲数不同;9)所以编码器的刻线数多,工艺复杂,价格高,而重点不是多少“位”的问题;4、电子齿轮改变频率,可以改变编码器的输出频率,也可以改变上位机输出的频率;5、如果电子齿轮二进制计数器安装到编码器上,那么改变编码器输出的反馈脉冲频率方便;6、如果电子齿轮二进制计数器安装到上位机上,那么改变上位机输出的指令脉冲频率方便;八、所以大家明白了其中的道理,就不必用一种方法去否定另外一种方法,原理都是相通的!1.当上位机满额发出脉冲时,伺服恰好额定速度运行,这时的电子齿轮比:电子齿轮比=反馈脉冲频率/上位机满额发出脉冲频率2、如果电子齿轮比是1:1)上位机发出的1个脉冲=编码器输出检测反馈的1个脉冲:2)上位机发出脉冲能力时发出的脉冲频率=200×1000/s;3)伺服电机的转速是=200×1000/s×60/131072= 91.55 r/min3、如果丝杆螺距是10mm,1)要求上位机每发一个指令脉冲,工件移动0.001mm,即指令脉冲当量为0.001mm,也可以说指令脉冲单位为0.001mm:2)如果伺服转一周,丝杆转一周,减速比是1;3)丝杆转一周,上位机应该发出的指令脉冲为10mm/0.001mm=10000(个);4)伺服转一周,编码器检测反馈脉冲为131072(个);5)电子齿轮比=编码器检测反馈脉冲/上位机发出的指令脉冲=131072/10000=13.7012;1、以上计算是不同的一种电子齿轮概念的计算方法,在这个计算里,电子齿轮比是根据需要任意确定的;2、虽然在电子齿轮比=1时,电机转的慢,可是当电子齿轮比升高到3.2768时,电机的速度就已经额定速度了;3、当我们根据加工工艺的需要,任意选用0.1mm、0.01mm、0.001mm、0.0001mm、…… 电子齿轮比分别是1370.12、137.012、13.7012、1.37012 ……跟着变化,电机的速度也会跟着快起来;4、所以,不能因为电子齿轮比=1时,电机转的慢,误认为电机在其它情况下的速度也很慢;5、例如本例,电子齿轮比从1增大到32.768,电机的速度就达到额定速度;6、本例的电子齿轮是一个换算率,不同于电子齿轮是二进制记数分倍频器的概念;7、本例的电子齿轮是一个换算率,这个概念在设定需要的指令脉冲,给用户提供了很方便的平台;8、本主题说的电子齿轮,是二进制计数器分、倍频构成的电子齿轮,笨鸟慢飞说的“让电机不能转的块一点”,利用电子齿轮直接将编码器的输出脉冲调低成相应的二进制反馈脉冲的方法,是另外一种伺服,与2楼计算实例伺服不同;9、用笨鸟慢飞说的安装在编码器上的电子齿轮,计算时脉冲当量是结果,而且计算的脉冲当量不一定就是需要的,更难过的是脉冲当量都不是0.01、0.001、……这样的长度计量的最小单位,伺服工艺操作带来很多麻烦;。
电子齿轮之概念及伺服马达转一圈所需之pulse计算
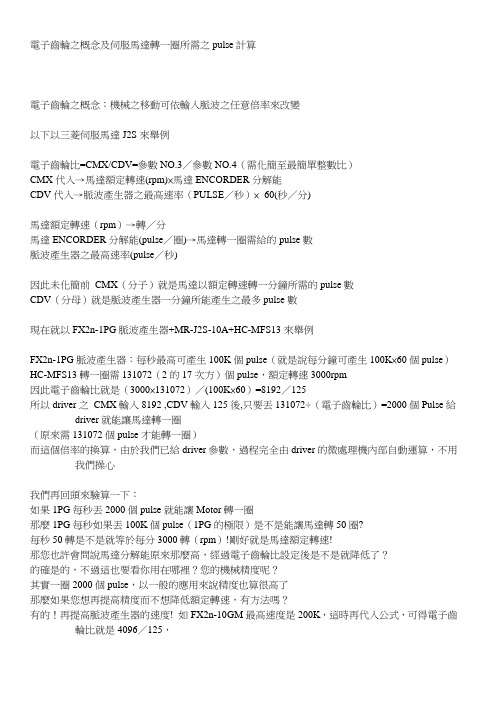
電子齒輪之概念及伺服馬達轉一圈所需之pulse計算電子齒輪之概念:機械之移動可依輸入脈波之任意倍率來改變以下以三菱伺服馬達J2S來舉例電子齒輪比=CMX/CDV=參數NO.3/參數NO.4(需化簡至最簡單整數比)CMX代入→馬達額定轉速(rpm)×馬達ENCORDER分解能CDV代入→脈波產生器之最高速率(PULSE/秒)×60(秒/分)馬達額定轉速(rpm)→轉/分馬達ENCORDER分解能(pulse/圈)→馬達轉一圈需給的pulse數脈波產生器之最高速率(pulse/秒)因此未化簡前CMX(分子)就是馬達以額定轉速轉一分鐘所需的pulse數CDV(分母)就是脈波產生器一分鐘所能產生之最多pulse數現在就以FX2n-1PG脈波產生器+MR-J2S-10A+HC-MFS13來舉例FX2n-1PG脈波產生器:每秒最高可產生100K個pulse(就是說每分鐘可產生100K×60個pulse)HC-MFS13轉一圈需131072(2的17次方)個pulse,額定轉速3000rpm因此電子齒輪比就是(3000×131072)/(100K×60)=8192/125所以driver之CMX輸入8192 ,CDV輸入125後,只要丟131072÷(電子齒輪比)=2000個Pulse給driver就能讓馬達轉一圈(原來需131072個pulse才能轉一圈)而這個倍率的換算,由於我們已給driver參數,過程完全由driver的微處理機內部自動運算,不用我們操心我們再回頭來驗算一下:如果1PG每秒丟2000個pulse就能讓Motor轉一圈那麼1PG每秒如果丟100K個pulse(1PG的極限)是不是能讓馬達轉50圈?每秒50轉是不是就等於每分3000轉(rpm)!剛好就是馬達額定轉速!那您也許會問說馬達分解能原來那麼高,經過電子齒輪比設定後是不是就降低了?的確是的,不過這也要看你用在哪裡?您的機械精度呢?其實一圈2000個pulse,以一般的應用來說精度也算很高了那麼如果您想再提高精度而不想降低額定轉速,有方法嗎?有的!再提高脈波產生器的速度! 如FX2n-10GM最高速度是200K,這時再代入公式,可得電子齒輪比就是4096/125,現在要讓馬達轉一圈需要從脈波產生器丟出4000個pulse,額定轉速依然不變是3000rpm 要再提高精度嗎?可以!還有500K的脈波產生器,甚至有更高的!只是這時,脈波產生器的預算,就不是很友善了!伺服馬達驅動器每輸出1 PULS 時,其移動之距離計算引用:(a)皮帶輪齒數比為2:1,即馬達旋轉2圈時,導螺桿只轉動1圈。
电子齿轮比

电子齿轮比电子齿轮比是指在电子设备中用来传递动力或控制转速的一种重要元件。
它可以将电机的转速和扭矩传递到其他部件,从而实现各种功能,比如驱动机械装置、控制航空器的舵面、调节汽车变速箱等。
在电子设备中,电子齿轮比的设计和应用对设备的性能和功能起着至关重要的作用。
电子齿轮比的原理和设计。
电子齿轮比的原理和传统机械齿轮比类似,都是通过齿轮的大小和齿数来实现不同的传动比。
但是,电子齿轮比不是通过物理齿轮的相互啮合来实现的,而是通过电子控制系统来调节电机的转速和扭矩,从而实现不同的传动比。
这种设计可以实现更加灵活和精确的控制,适用于各种复杂的应用场景。
电子齿轮比的应用。
电子齿轮比广泛应用于各种电子设备中,比如汽车、航空器、工业机械等。
在汽车中,电子齿轮比可以实现自动变速箱的控制,提高燃油经济性和驾驶舒适性。
在航空器中,电子齿轮比可以控制舵面的转动,实现飞行姿态的调整。
在工业机械中,电子齿轮比可以实现精确的转速控制,提高生产效率和产品质量。
电子齿轮比的优势。
与传统机械齿轮比相比,电子齿轮比具有以下几个优势:1. 灵活性,电子齿轮比可以通过软件控制来实现,可以根据不同的需求和工况来调整传动比,实现更加灵活的控制。
2. 精确性,电子齿轮比可以实现更加精确的控制,可以实现微小的调整,适用于对转速和扭矩要求较高的应用场景。
3. 效率,电子齿轮比可以实现更加高效的能量转换,可以提高设备的能效和性能。
4. 可靠性,电子齿轮比不需要机械齿轮的啮合,可以减少零件的磨损和故障,提高设备的可靠性和使用寿命。
电子齿轮比的发展趋势。
随着电子技术和控制技术的不断发展,电子齿轮比在未来将会有更加广阔的应用前景。
首先,随着电机和传感器技术的不断进步,电子齿轮比的控制精度和响应速度将会进一步提高,可以适用于更加复杂和高性能的应用场景。
其次,随着智能化和互联网技术的发展,电子齿轮比可以实现远程监控和智能化控制,可以实现更加智能化和自动化的生产和运营。
电子齿轮的原理和应用
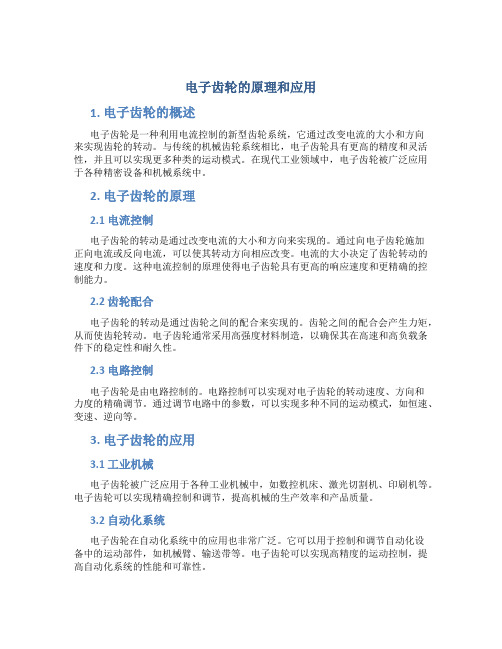
电子齿轮的原理和应用1. 电子齿轮的概述电子齿轮是一种利用电流控制的新型齿轮系统,它通过改变电流的大小和方向来实现齿轮的转动。
与传统的机械齿轮系统相比,电子齿轮具有更高的精度和灵活性,并且可以实现更多种类的运动模式。
在现代工业领域中,电子齿轮被广泛应用于各种精密设备和机械系统中。
2. 电子齿轮的原理2.1 电流控制电子齿轮的转动是通过改变电流的大小和方向来实现的。
通过向电子齿轮施加正向电流或反向电流,可以使其转动方向相应改变。
电流的大小决定了齿轮转动的速度和力度。
这种电流控制的原理使得电子齿轮具有更高的响应速度和更精确的控制能力。
2.2 齿轮配合电子齿轮的转动是通过齿轮之间的配合来实现的。
齿轮之间的配合会产生力矩,从而使齿轮转动。
电子齿轮通常采用高强度材料制造,以确保其在高速和高负载条件下的稳定性和耐久性。
2.3 电路控制电子齿轮是由电路控制的。
电路控制可以实现对电子齿轮的转动速度、方向和力度的精确调节。
通过调节电路中的参数,可以实现多种不同的运动模式,如恒速、变速、逆向等。
3. 电子齿轮的应用3.1 工业机械电子齿轮被广泛应用于各种工业机械中,如数控机床、激光切割机、印刷机等。
电子齿轮可以实现精确控制和调节,提高机械的生产效率和产品质量。
3.2 自动化系统电子齿轮在自动化系统中的应用也非常广泛。
它可以用于控制和调节自动化设备中的运动部件,如机械臂、输送带等。
电子齿轮可以实现高精度的运动控制,提高自动化系统的性能和可靠性。
3.3 机器人技术电子齿轮在机器人技术中发挥着重要作用。
它可以用于控制机器人的关节运动,实现机器人的各种复杂动作。
电子齿轮可以实现高速、高精度的运动控制,提高机器人的工作效率和准确性。
3.4 医疗设备电子齿轮在医疗设备中的应用也非常重要。
它可以用于控制医疗设备的运动部件,如手术机器人、影像设备等。
电子齿轮的精确控制能力可以提高医疗设备的性能和操作效率。
3.5 汽车工业电子齿轮在汽车工业中的应用也越来越广泛。
电子齿轮分子分母计算个人笔记
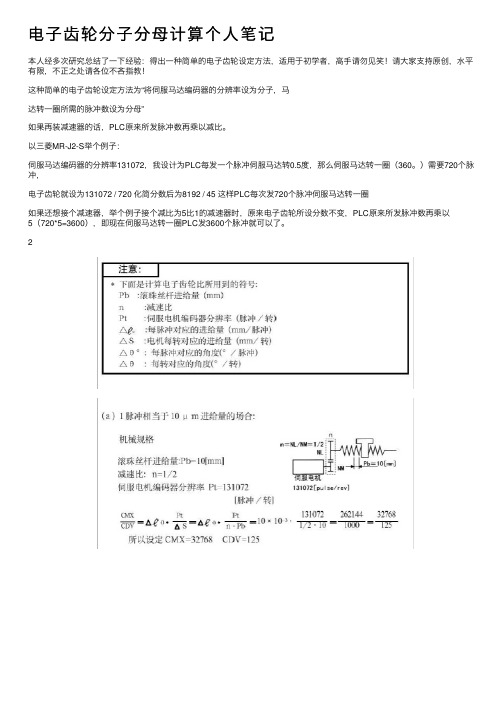
电⼦齿轮分⼦分母计算个⼈笔记本⼈经多次研究总结了⼀下经验:得出⼀种简单的电⼦齿轮设定⽅法,适⽤于初学者,⾼⼿请勿见笑!请⼤家⽀持原创,⽔平有限,不正之处请各位不吝指教!这种简单的电⼦齿轮设定⽅法为“将伺服马达编码器的分辨率设为分⼦,马达转⼀圈所需的脉冲数设为分母”如果再装减速器的话,PLC原来所发脉冲数再乘以减⽐。
以三菱MR-J2-S举个例⼦:伺服马达编码器的分辨率131072,我设计为PLC每发⼀个脉冲伺服马达转0.5度,那么伺服马达转⼀圈(360。
)需要720个脉冲,电⼦齿轮就设为131072 / 720 化简分数后为8192 / 45 这样PLC每次发720个脉冲伺服马达转⼀圈如果还想接个减速器,举个例⼦接个减⽐为5⽐1的减速器时,原来电⼦齿轮所设分数不变,PLC原来所发脉冲数再乘以5(720*5=3600),即现在伺服马达转⼀圈PLC发3600个脉冲就可以了。
23电⼦齿轮⽐(CMX/CDV)的计算及其意义刘志斌2011.03.21已知:1)上位机发出脉冲能⼒为200Kp/S,200×1000/s,200×1000×60/min;2)电机额定转速为3000R/ min,3000/60s;3)伺服电机编码器分辨率是131072;4)丝杆螺距是10mm;求:1、电机额定转速运⾏时的电⼦齿轮⽐?2、如果电⼦齿轮⽐是1,伺服电机的转速?3、⽣产时,设定指令脉冲当量,确定电⼦齿轮⽐?解:1、当上位机满额发出脉冲时,伺服恰好额定速度运⾏:1)电机额定转速为3000r/ min,3000r/60s=50r/s;2) 伺服电机编码器分辨率是131072;3)电机额定转速时编码器输出检测反馈脉冲频率是131072×50r/s;;4)上位机发出脉冲能⼒时发出的脉冲频率=200×1000/s;5)当上位机满额发出脉冲时,伺服恰好额定速度运⾏,这时的电⼦齿轮⽐:电⼦齿轮⽐=反馈脉冲频率/上位机满额发出脉冲频率=(131072×50r/s)/ 200×1000/s=6553600/200000=3.27682、如果电⼦齿轮⽐是1:1)上位机发出的1个脉冲=编码器输出检测反馈的1个脉冲:2)上位机发出脉冲能⼒时发出的脉冲频率=200×1000/s;3)伺服电机的转速是=200×1000/s×60/131072= 91.55 r/min3、如果丝杆螺距是10mm,1)要求上位机每发⼀个指令脉冲,⼯件移动0.001mm,即指令脉冲当量为0.001mm,也可以说指令脉冲单位为0.001mm:2)如果伺服转⼀周,丝杆转⼀周,减速⽐是1;3)丝杆转⼀周,上位机应该发出的指令脉冲为10mm/0.001mm=10000(个);4)伺服转⼀周,编码器检测反馈脉冲为131072(个);5)电⼦齿轮⽐=编码器检测反馈脉冲/上位机发出的指令脉冲=131072/10000=13.7012;说明:反馈脉冲:伺服电机编码器的解析度,伺服本⾝的脉冲。
一看就会的电子齿轮比解说

即数据关系要满足如下要求:
指令脉冲输入 = 有效指令脉冲
Pr010 Pr009
=
反馈至驱动器脉冲数
Pr011
= 驱动器反馈输出脉冲数
Pr503
同时,上图的“指令脉冲输入 ”由控制器的“位置反馈解析度”
的数据决定,控制器的“位置反馈解析度”参数表示每一圈控制器要发送 和接收的脉冲数量。由我们接线的方式,“驱动器反馈输出脉冲数”就是 控制器接收到的反馈脉冲数。
6553600 / 2 = 3276800 < 4000000
所以将控制器参数“位置反馈解析度”设定为原来的一半 98304是可以让DD马达的转速达到2000r/m的。
但前述等式中“反馈至驱动器脉冲数”为196608
所以:
指令脉冲输入 = 有效指令脉冲
98304
不变
=
Pr010 Pr009
反馈至驱动器脉冲数
也可以设定为196608,驱动器中的指令分倍频 前提背景:松下390最大接收频率为 4MHZ
指令脉冲输入 = 有效指令脉冲
和反馈齿轮比均设定为1:1,这样就可以得到 但前述等式中“反馈至驱动器脉冲数”为196608
DD马达接线线路示意图 DD马达的齿轮个数为384个,分割器的分割倍数是512,故上图中“反馈至驱动器脉冲数”固定为384*512=196608 。
具体数据说明:
更改电子齿轮比设定可以解D决问D题马达的齿轮个数为384个,分割器的分 割倍数是512,故上图中“反馈至驱动器脉冲数” 更改电子齿轮比设定可以解决问题
DD马达码盘齿轮数量为384个,分割器分割倍率为512,故DD马达每转一圈反馈的脉冲数量为384*512=196608。 松下390最大接收频率=2000*196608/60=6553600
- 1、下载文档前请自行甄别文档内容的完整性,平台不提供额外的编辑、内容补充、找答案等附加服务。
- 2、"仅部分预览"的文档,不可在线预览部分如存在完整性等问题,可反馈申请退款(可完整预览的文档不适用该条件!)。
- 3、如文档侵犯您的权益,请联系客服反馈,我们会尽快为您处理(人工客服工作时间:9:00-18:30)。
电子齿轮之概念:机械之移动可依输入脉波之任意倍率来改变
以下以三菱伺服马达J2S来举例
电子齿轮比=CMX/CDV=参数NO.3/参数NO.4(需化简至最简单整数比)
CMX代入→马达额定转速(rpm)×马达ENCORDER分解能
CDV代入→脉波产生器之最高速率(PULSE/秒)× 60(秒/分)
马达额定转速(rpm)→转/分
马达ENCORDER分解能(pulse/圈)→马达转一圈需给的pulse数
脉波产生器之最高速率(pulse/秒)
因此未化简前CMX(分子)就是马达以额定转速转一分钟所需的pulse数
CDV(分母)就是脉波产生器一分钟所能产生之最多pulse数
现在就以FX2n-1PG脉波产生器+MR-J2S-10A+HC-MFS13来举例
FX2n-1PG脉波产生器:每秒最高可产生100K个pulse(就是说每分钟可产生100K×60个pulse)
HC-MFS13转一圈需131072(2的17次方)个pulse,额定转速3000rpm
因此电子齿轮比就是(3000×131072)/(100K×60)=8192/125
所以driver之CMX输入8192 ,CDV输入125后,只要丢131072÷(电子齿轮比)=2000个Pulse给driver就能让马达转一圈
(原来需131072个pulse才能转一圈)
而这个倍率的换算,由于我们已给driver参数,过程完全由driver的微处理机内部自动运算,不用我们操心
我们再回头来验算一下:
如果1PG每秒丢2000个pulse就能让Motor转一圈
那么1PG每秒如果丢100K个pulse(1PG的极限)是不是能让马达转50圈?
每秒50转是不是就等于每分3000转(rpm)!刚好就是马达额定转速!
那您也许会问说马达分解能原来那么高,经过电子齿轮比设定后是不是就降低了?
的确是的,不过这也要看你用在哪里?您的机械精度呢?
其实一圈2000个pulse,以一般的应用来说精度也算很高了
那么如果您想再提高精度而不想降低额定转速,有方法吗?
有的!再提高脉波产生器的速度!如FX2n-10GM最高速度是200K,这时再代入公式,可得电子齿轮比就是4096/125,
现在要让马达转一圈需要从脉波产生器丢出4000个pulse,额定转速依然不变是
3000rpm
要再提高精度吗?可以!还有500K的脉波产生器,甚至有更高的!
只是这时,脉波产生器的预算,就不是很友善了!。