cg20114
自卸车厢板机器人焊接参数化编程控制系统设计
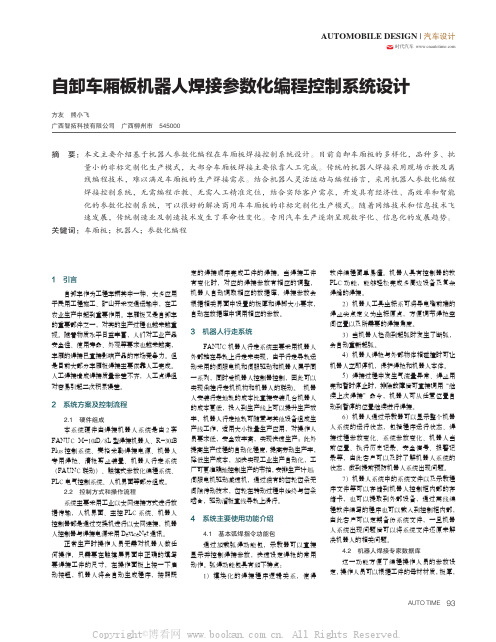
AUTOMOBILE DESIGN | 汽车设计时代汽车 自卸车厢板机器人焊接参数化编程控制系统设计方友 熊小飞广西智拓科技有限公司 广西柳州市 545000摘 要: 本文主要介绍基于机器人参数化编程在车厢板焊接控制系统设计。
目前自卸车厢板的多样化,品种多、批量小的非标定制化生产模式,大部分车厢板焊接主要依靠人工完成。
传统的机器人焊接采用现场示教及离线编程技术,难以满足车厢板的生产焊接需求。
结合机器人灵活运动与编程语言,采用机器人参数化编程焊接控制系统,无需编程示教、无需人工精准定位,结合实际客户需求,开发具有经济性、高效率和智能化的参数化控制系统,可以很好的解决商用车车厢板的非标定制化生产模式。
随着网络技术和信息技术飞速发展,传统制造业及制造技术发生了革命性变化。
专用汽车生产逐渐呈现数字化、信息化的发展趋势。
关键词:车厢板;机器人;参数化编程1 引言自卸车作为工程车辆其中一种,大多应用于民用工程施工、矿山开采交通运输中,在工农业生产中起到重要作用。
车厢板又是自卸车的重要部件之一,对其的生产过程也越来越重视。
随着物质水平日益丰富,人们对工业产品安全性、使用寿命、外观等要求也越来越高,车厢的焊接已直接影响产品的市场竞争力。
但是目前大部分车厢板焊接主要依靠人工完成。
人工焊接造成焊接质量参差不齐,人工点焊组对容易引起二次积累误差。
2 系统方案及控制流程2.1 硬件组成本系统硬件由焊接机器人系统是由2套FANUC M-10iD/8L型焊接机器人、R-30iB Plus控制系统、麦格米勒焊接电源、机器人专用焊枪、清枪剪丝装置、机器人行走系统(FAUNC联动)、触摸式参数化编程系统、PLC电气控制系统、人机界面等部分组成。
2.2 控制方式和操作流程系统主要采用工业以太网连接方式进行数据传输,人机界面、主控PLC系统、机器人控制器都是通过交换机进行以太网连接,机器人控制器与焊接电源采用DeviceNet通讯。
四川埃姆克伺服主轴选型手册v1.0

驱动器型号
SD-S4T1P5 SD-S4T2P2 SD-S4T3P7 SD-S4T5P5 SD-S4T7P5 SD-S4T011 SD-S4T015L SD-S4T015 SD-S4T018 SD-S4T022 SD-S4T030 SD-S4T037 SD-S4T045 SD-S4T055 SD-S4T075 SD-S4T090
1
伺服主轴系统性能参数
输入 电源
控制 特性
I/O 接口
主轴 功能
保护 功能
工作 环境
输入电压 输入频率 允许电压波动 允许频率波动 控制方式 最高转速 速度控制范围 速度控制精度 加减速时间 转矩控制特性 位置控制精度 制动方式 过载能力 数字量输入 数字量输出 继电器输出 模拟量输入 外部脉冲输入 电机编码器输入 电机编码器输出 通讯接口 速度控制 定位控制 刚性攻丝 位置控制 其他功能 过电流保护 过载保护 输出短路保护 电机过热保护 功率模块过热保护 编码器异常保护 过电压保护 低电压保护 安装场所要求 工作环境温度 工作环境湿度 工作海拔高度 允许振动范围
B2
电机
R
Байду номын сангаас
U
三相电源 380V/50Hz
S
主 回
V
M
T
路
W
正转
反转
准停
刚性攻丝
位置模式
数 字
急停/零速
量
摆动
输
故障复位
入
保留
保留
电源COM 电源24V
外供24V
伺服就绪
数
位置模式就绪
字 量 输
零速到达 速度到达
出
I0 I1 I2 I3 I4 I5 I6 I7 I8 I9
中医肺康复法治疗慢性阻塞性肺疾病稳定期患者的疗效
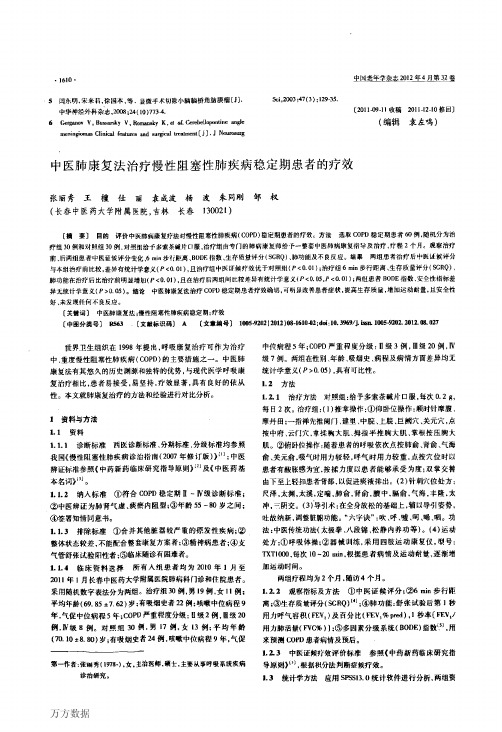
(编辑袁左呜)
meninglomas
Clinical
features
surgical
tavⅫtlment【j】,J Neurosurg
中医肺康复法治疗慢性阻塞性肺疾病稳定期患者的疗效
张丽秀王檀仕丽 袁成波杨波朱同刚 邹权
(长春中医药大学附属医院,吉林长春13002t)
inflammatory markers
由于COPD患者长期处于低氧状态,机体组织器官功能受
损,当呼吸肌疲劳时.患者的呼吸会变得浅促.增加了通气死
infection
exacerbation of chronic obstructive Care
pul・
disease[J].Am J
Respir Crit
比较差异无统计学意义。
9 S
Path01.2000;190(5):619-26.
Keating VM。Collins PD.Scott
tumor
DM。et缸Differences induced
ip
interleukin-8
and
necrosis factor・alpha in
sputum from patients with chronic
肺功能比较,差异均有统计学意义(P<o.05)。见表2。
表2两组治疗前后肺功能比较(孑:ks.n=30 J
3全国科学技术名词审定委员会.中医药基本名词[M).北京:科学 出版社.2005:58.131.
4 Jones
PW,Quirk
FH.Baveystock CM.The
ST
george’s
r∞pi咖。叮ques-
Valtek MaxFlo 4 Eccentric Rotary Plug Control Valv

Valtek MaxFlo 4 Eccentric Rotary Plug Control ValveMaxFlo 4 Eccentric Rotary Plug Control Valve2The Flowserve Valtek MaxFlo 4 control valve is a high performance eccentric rotary plug valve designed for the process industry. It features a large capacity, standard hardened trim and superior shaft blow-out protection. This valve is available in sizes 1 through 12 inches, ASME Class 150, 300 and 600 as well as DIN PN 10, PN16, PN 25, PN40 and PN63.An optional ISA 75.08.01 or DIN EN 558 series 1 long-pattern body makes this valve an easy drop-in replacement for a globe control valve.The MaxFlo 4 is suitable for most applications; its control valve features include:• Highest Rated Cv • Precise Control • Reliable Shut-off• Most Current Safety Standards • Fugitive Emissions Elimination •Integral Noise Reduction PlatesHighest Rated CvThe unique design of the MaxFlo 4 shaft and plug provide as much as 70% more Cvcompared to the competition. This allows customers to get more flow when neededand sometimes allows for a smaller, more economical valve to be used.Precise ControlThe MaxFlo 4 polygon connection between the shaft and plug is a proven superiormethod for making demanding mechanical connections that are stronger, more preciseand have a substantially longer service life. This reduces backlash and the high strengthof the polygon connections makes them capable of withstanding greater shock loadsunder extreme torque reversal conditions.Reliable Shut-offThe MaxFlo 4 double-offset eccentric plug rotates into the seat at an angle that eliminatessliding over the seat surface. This design reduces seat wear, and thereby decreases main-tenance requirements and costs. At the same time, a tight ANSI Class VI shutoff is easilyobtainable using the soft seat design.Safety StandardThe shaft is designed to meet the safety requirements of industry standard ASME B16.34to ensure that the shaft is retained even if the actuator is removed when the valve is stillpressurized. This is standard on every MaxFlo 4 to provide our customers with confidenceand safety.3Separate bonnet ensures positive anti-blowout, accommodates multiple packing options, and offers flexibility in material selection for demandingapplications.Heavy-duty rigid metal seat,with hardfaced or soft-seat options, provides tighter shutoff, and easier maintenance. Available in full area and several reductions in every size to suit your process needs.Blow out proof shaft required by ASME B16.34 2004 Sec 6.5 ensures safety. Standard on every MaxFlo 4.An economical flangeless configuration of the MaxFlo 4 is also available. The standard flanged body is the same length. To replace existing globe valves we offer the flanged body with the same face to face length as a globe valve (Per ISA 75.08.01).4Open Flow Path gives as much as 70%more C v than competitive valves that have the shaft obstructing the flow. In many cases it is possible to use a smaller, more economical MaxFlo 4.Flanged end post allows for easy maintenance.Hard stainless steel plug requires no breakout torque and increases valve life as the plug lifts off the seat immediately when it begins rotating.Precision NC machined plug and shaft significantly reduces maintenance costs byallowing replacement of only the necessary parts.Polygon shaft/plug connection for precise robust control.Shimless seat offers simplified assembly and easy maintenance.5Eliminate Fugitive EmissionsSpecial Flowserve packing sets, such as SureGuard XT live loaded packing, are available to control fugitive emissions. Packing options include: PTFE V-Ring, Braided PTFE, Graphite, Sureguard XT, Garlock SVS, LATTYflon 3265 LM and LATTYgraf 6995 NG (meeting requirements for TA-Luft, ISO 15848-1 class B and A, and EPA standards).Integral Noise-Reduction Plate OptionDesigned to reduce noise levels by 5 to 10 dBA, our integral plate fits into the valve body. It can be easily maintained using the same tools required for the seat retainer. It is perfectly suitable with all gases in the shaft-downstream direction, and the plate does not change the length of the valve.Integrated Control Valve SolutionOperated by a diaphragm, piston, or rack-and-pinion actuator coupled with a Logix digital positioner, the MaxFlo 4 maintains high positioning accuracy, repeatability, controlled high speed and reliable response. With the advanced diagnostic solutions that can be seamlessly integrated into a host control and/or plant asset management system, along with state-of-the-art features and performance, the MaxFlo 4 is the most economical Eccentric Rotary Plug valve in the market.NR Diaphragm Rotary ActuatorThe Flowserve NR diaphragm rotary actuator is a rugged single-acting actuator designed to provide high performance, long life and reliability. The diaphragm actuator is very sensitive to small changes in air supply, which allows it toprecisely move the valve plug without over shoot.6Logix 3000MD+ Digital PositionerEasiest calibration and configuration of any positioner available. Single, push-button calibration and DIP switch configuration allow you to fully commission the positioner in a matter of minutes. Using ValveSight Software DTM brings the availability of 24/7 diagnostics.For more information see document number LGENIM0059 and LGENIM3404 at .Logix 500MD+ Series Digital PositionerTo minimize your total cost of ownership and maximize productivity, Flowserve developed the Logix MD+ digital positioner. The Logix MD+ digital positioner allows for fast, simple commis-sioning, extremely accurate and reliable control, and diagnostic features that provide powerfuland easy ways to determine when maintenance is required.ValveSight™ Diagnostic Software – Prevention deliveredValveSight is a diagnostic solution for control valves that can be seamlessly integrated into a host control and/or plant asset management system. The power of ValveSight is the intel-ligent diagnostic engine -- which detects an emerging condition in the valve, actuator, posi-tioner, and control signal -- that may indicate a performance, safety, or environmental problem. ValveSight advises which corrective actions totake to prevent a failure.VR Spring Cylinder Rotary ActuatorThe Flowserve VR spring cylinder rotary actuator combines high torque and pneu-matic stiffness with excellent throttling capabilities. These characteristics are designed into a lightweight, rugged and compact assembly, making the Flowserve spring cylinder rotary actuator an excel-lent choice for quarter-turn applications.SuperNova Rack & Pinion Rotary ActuatorThe Flowserve SuperNova rack & pinion rotary actuator is designed forreliability, versatility and safety. Rugged, yet compact construction combined with technical solutions make this product extremely reliable in the severest of operating conditionsLogix 420 Digital PositionerThe Logix 420 is the latest addition to the digital positioner family from Flowserve. When mounted to the MaxFlo 4 eccentric rotary plugcontrol valve, Logix 420 provides the user with a cost competitive solutionfor the general service, explosion proof market. For more information see document numberLGENIM0106 at www .Unparalleled Service: Day or Night, WorldwideFlowserve Quick Response Centers (QRCs) are equipped with thousands of parts, including OEM andFlowserve custom-built products. Each has the manpower andequipment to expedite time-sensitiverepairs of any size.7To find your local Flowserve representative:For more information about Flowserve Corporation, visit or callUSA 1 800 225 6989 or International +1 972 910 0774FCD VLENBR0064-01-AQ Printed in USA. November 2015. © 2015 Flowserve Corporation United States Flowserve1350 N. Mt. Springs Parkway Springville, UT 84663USAPhone: +1 801 489 8611Fax: +1 801 489 3719AustriaFlowserve Control Valves GmbH Kasernengasse 69500 Villach AustriaPhone: +43 (0)4242 41181 0Fax: +43 (0)4242 41181 50FranceFlowserve France S.A.S.BP 60 63307 Thiers Cedex FrancePhone: 33 4738 04266Fax: 33 4738 01424IndiaFlowserve India Controls Pvt. Ltd Plot # 4, 1A, E.P .I.P , Whitefield Bangalore Kamataka India 560 066Phone: +91 80 284 10 289Fax: +91 80 284 10 286SingaporeFlowserve Pte. Ltd.12 Tuas Avenue 20Republic of Singapore 638824SingaporePhone: +65 6879 8900Fax: +65 6862 4940Saudi ArabiaFlowserve Abahsain Flow Control Co., Ltd.Makkah Road, Phase 4Plot 10 & 12, 2nd Industrial City Damman, Kingdom of Saudi ArabiaPhone: +966 3 857 3150 ext. 243Fax: +966 3 857 4243ChinaFlowserve Fluid Motion and Control (Suzhou) Co., Ltd.No. 35, Baiyu RoadSuzhou Industrial Park, Suzhou Jiangsu Province, P .R. 215021ChinaPhone: 86 512 6288 8790Fax: 86 512 6288 8736。
SCR后处理故障排除指南

1潍柴蓝擎国IV 发动机SCR 后处理故障排除指南潍柴动力 技术中心王秀雷 李万洋 孟媛媛桑心成 2011年12月目录SCR后处理故障排除指南 (1)目录2第一章概述 (4)1.1 SCR后处理概述 (4)1.2 SCR后处理原理 (5)1.3 SCR后处理组成 (5)第二章故障诊断与案例分析 (12)1.1 故障分类 (13)第一类故障:尿素压力建立失败 (14)第二类故障:尿素消耗少 (18)第三类故障:OBD扭矩限制与不可清除代码 (20)第四类故障:OBD灯 (26)第五类故障:尿素加热不放行 (27)第六类故障:NOx转化效率低 (29)第七类故障:NOx转化效率监测不放行 (32)第八类故障:NOx值测量不准确 (34)第九类故障:闻到一股氨气味 (34)第十类故障:尿素结晶 (35)2第十一类故障:其他故障 (37)2.2 部件故障分析 (37)(一)尿素管及其接插件:易造成建压困难甚至建不起压力,SCR系统不工作,OBD灯亮,限扭等故障。
(37)(二)尿素泵:易造成不能正常建压和喷射,OBD灯亮,限扭等故障。
(37)(三)NOx传感器:易造成OBD灯亮,限扭等故障。
(38)(四)尿素各个加热继电器:易造成尿素加热不放行,SCR系统不工作等故障。
(38)(五)各个后处理的线束及接插件:各种现象。
(38)附:部件检测 (40)第三章潍柴动力蓝擎国IV柴油机闪码表 (45)3.1故障码的读取 (46)3.2手动清除故障码的方法 (47)3.3潍柴动力蓝擎国IV闪码表(通用于WP高压共轨系列柴油机) (48)3第一章概述1.1 SCR后处理概述发动机满足国IV排放有多种技术手段,潍柴动力率先采用了更先进的德国BOSCH(博世)电控高压共轨系统+SCR 后处理系统。
与EGR技术对比如图1所示,具有可靠性高、经济性好,安全、舒适,而且具有智能化的特点,同时可以达到国Ⅴ排放标准的要求,并全面满足OBD法规要求,更环保。
AEC_Q005_Rev_A

AEC – Q005 - REV-PB-FREE TEST REQUIREMENTSAcknowledgmentAny document involving a complex technology brings together experience and skills from many sources. The Automotive Electronics Council would especially like to recognize the following significant contributors to the development and initial release of this document:Sustaining Members:Earl Fischer Autoliv Gary Fisher Johnson ControlsMark A. Kelly Delphi Corporation Thomas VanDamme TRW AutomotiveBob Hulka, Jr. Delphi Corporation Larry Dudley TRW AutomotiveRick Forster Continental Corporation Robert V. Knoell Visteon Corporation Hadi Mehrooz Continental Corporation Ken Kirby, Jr. Visteon Corporation Jim Peace Continental Corporation Ron Haberl Visteon Corporation Technical Members:Tim Haifley Altera James Williams Texas InstrumentsJames Molyneaux Analog Devices Diana Siddall Texas InstrumentsMike Gibson Analog Devices Guillemette Paour Tyco ElectronicsHeinz Reiter Austriamicrosystems Robert Cid Tyco ElectronicsHerwig Klimesch Austriamicrosystems Ted Krueger VishayMike Klucher Cirrus Logic Arthur Chiang VishayXin Miao Zhao Cirrus Logic Anca Voicu XilinxRene Rodgers Cypress Semiconductor Daniel Joo XilinxFred Whitwer Cypress SemiconductorGeorge Platko Fairchild SemiconductorJoe Fazio Fairchild Semiconductor Associate Members:Nick Lycoudes Freescale Andrew Yap Grace Semiconductor Kenton Van Klompenberg Gentex Arthur Cheng Grace Semiconductor Werner Kanert Infineon Technologies Kuotung Cheng TSMCAlexander Mueller Infineon Technologies Ken Wu TSMCJohn Bertaux International RectifierLyn Zastrow ISSIBanjie Bautista ISSI Guest Members:Peter Blais Kemet David Locker AMRDECHolger Zillgen Kemet Jeff Jarvis AMRDECTom Lawler Lattice SemiconductorSohail Malik Lattice SemiconductorJoe Wurts Maxim Other Contributors:Tom Tobin Maxim Maurice Brodeur Analog DevicesMike Buzinski Microchip Brian Jendro Continental Corporation Nick Martinez Microchip John Timms Continental Corporation Annette Nettles NEC Electronics Jeff Price Delphi CorporationTony Walsh NEC Electronics Marc Dittes InfineonMichael Wieberneit NEC Electronics Harry Sax InfineonZhongning Liang NXP Semiconductors Mary Carter-Barrios KemetDi Bayes NXP Semiconductors Masamichi Murase NEC ElectronicsMark Gabrielle ON Semiconductor Pascal Oberndorff NXP Semiconductors Daniel Vanderstraeten ON Semiconductor Bruce Townsend SpansionKen Berry Renesas Technology Michael Hundt STMicroelectronicsFrancis Classe Spansion Harry Siegel STMicroelectronicsAdam Fogle Spansion Doug Romm Texas InstrumentsBrian Mielewski STMicroelectronics John Kampell Texas InstrumentsSteve Maloy TDK Patrick Neyman Tyco ElectronicsRichard Tse TDK Huixian Wu VishayBill Hopfe Visteon CorporationNOTICEAEC documents contain material that has been prepared, reviewed, and approved through the AEC Technical Committee.AEC documents are designed to serve the automotive electronics industry through eliminating misunderstandings between manufacturers and purchasers, facilitating interchangeability and improvement of products, and assisting the purchaser in selecting and obtaining with minimum delay the proper product for use by those other than AEC members, whether the standard is to be used either domestically or internationally.AEC documents are adopted without regard to whether or not their adoption may involve patents or articles, materials, or processes. By such action AEC does not assume any liability to any patent owner, nor does it assume any obligation whatever to parties adopting the AEC documents. The information included in AEC documents represents a sound approach to product specification and application, principally from the automotive electronics system manufacturer viewpoint. N o claims to be in conformance with this document shall be made unless all requirements stated in the document are met.Inquiries, comments, and suggestions relative to the content of this AEC document should be addressed to the AEC Technical Committee on the link .Published by the Automotive Electronics Council.This document may be downloaded free of charge, however AEC retains the copyright on this material. By downloading this file, the individual agrees not to charge for or resell the resulting material.Printed in the U.S.A.All rights reservedCopyright © 2009 by the Automotive Electronics Council. This document may be freely reprinted with this copyright notice. This document cannot be changed without approval from the AEC Component Technical Committee.PB-FREE TEST REQUIREMENTS1. SCOPEThis document contains a set of tests and defines the minimum requirements for qualification of lead free (Pb-free) metallurgy for components to be used in any automotive electronics application. For a component to be considered Pb-free compatible, its properties, including but not limited to plating materials and package configuration, must be compatible with Pb-free manufacturing processes. Use of this document does not relieve the supplier of their responsibility to meet their own company's internal qualification program. In this document, "user" is defined as all customers using a component qualified per this specification. The user is responsible to confirm and validate all q ualification data that substantiates conformance to this document.1.1 PurposeThe purpose of this specification is to determine that a component is capable of passing the specified stress tests and thus can be expected to give a certain level of quality/reliability in the application. The science of whisker growth, including growth models and accelerated test methods, is not fully understood at the time of release of this standard. Further, the existence of tin whiskers over time does not ensure component or system failure. The environmental tests specified in this document for whisker growth evaluation require conditions of temperature, humidity and temperature cycling which are currently believed to best exacerbate whisker growth in Sn-plated leads a nd terminations. The user and supplier need to consider the applicable risks when using components with Sn-plated leads in sensitive applications.1.2 Reference DocumentsCurrent revision of the referenced documents will be in effect at the date of agreement to the qualification plan. Subsequent qualification plans will automatically use updated revisions of these referenced documents.1.2.1 JEDECJESD201 Environmental Acceptance Requirements for Tin Whisker Susceptibility of Tin and Tin Alloy Surface FinishesJESD22-A104 Temperature CyclingJESD22-A111 Evaluation Procedure for Determining Capability to Bottom Side Board Attach by Full Body Solder Immersion of Small Surface Mount Solid State DevicesJESD22-A113 Preconditioning of Nonhermetic Surface Mount Devices Prior to Reliability TestingJESD22-A121 Test Method for Measuring Whisker Growth on Tin and Tin Alloy Surface FinishesJESD22-B102 SolderabilityJESD22-B106 Resistance to Solder HeatJP002 Current Tin Whiskers Theory and Mitigation Practices Guideline1.2.2 IPC/JEDECJ-STD-020 Moisture/Reflow Sensitivity Classification for Plastic Integrated Circuit Surface Mount Devices 1.2.3 EIA/IPC/JEDECEIA/IPC/JEDEC J-STD-075 - Classification of Non-IC Electronic Components for Assembly Processes1.3 Terms and Definitions1.3.1 Lead Free (Pb-free) Plating Finish: A component plating finish is considered Pb-free if the followingrequirements are met:a. Complies with the latest version of the Global Automotive Declarable Substance List (GADSL).Refer to GADSL () for detailed requirements and exemptions.b. Is compliant to Pb-free board assembly process reflow profile(s) and material(s) as required herein.1.3.2 Preferred Pb-Free FinishesDue to the risk of Sn whiskers, non Sn-based finishes may be preferred. However, solderability performance may indicate a preference of (matte) Sn plating. Therefore, careful consideration must be given to the plating finish material and the intended component manufacturing process.A verified whisker mitigation practice is required when Sn-based finishes are used, unless otherwise agreedbetween user and supplier on a case-by-case basis. Refer to Section 5 of JP002 for information and examples of verified mitigation practices.1.3.3 Restricted Pb-Free Finishes1.3.3.1 Tin-Bismuth (SnBi) alloy finishes containing greater than 5% Bismuth may not be acceptable foruse in SnPb solder processes due to the formation of a low-melting point ternary eutectic compound (SnPbBi). Refer to JP002 for details on SnBi. Use of SnBi alloy finishes in SnPb solder processes requires user approval and must meet the requirements stated in this specification.1.3.3.2 Plated Tin-Copper (SnCu) alloy finishes are not acceptable for use in any solder process due toenhanced whisker formation and growth resulting from the introduction of Copper. Refer to JP002 for details on SnCu. Use of SnCu alloy finishes requires user approval and must meet the requirements stated in this specification.2. EQUIPMENTNot Applicable3. QUALIFICATION TESTSWhen a component involves Pb-free and/or Pb-free compatible materials, certain tests (as defined in this document) must be performed and resulting data submitted for review before the component can be approved for use. These tests are in addition to all electrical/mechanical testing required in the applicable part specification and include solderability, resistance to solder heat (if applicable), moisture sensitivity (MSL), and Sn whisker testing. Where applicable, tests should include exposure to and/or use of standard SnPb (e.g., Sn60/Pb40, Sn63/Pb37, Sn25/Pb75, etc.) and Pb-free (SAC305 or similar Pb-free alloy with liquidus of 217°C to 227°C) solder to examine and confirm forward and backward assembly compatibility of the Pb-free components. The user must approve any deviation from the test requirements defined herein.3.1 SolderabilityAll plated component terminations and/or surfaces shall be tested for solderability per JESD22-B102. Allthrough-hole components shall be solderability tested using the “Dip and Look” method.All coarse pitch (external lead pitch > 0.5mm) Surface mount components shall be tested using either the “Surface Mount Process Simulation Test" method or "Dip and Look" test method. It is recommended that all fine external lead pitch (=0.5mm) surface mount components be tested using the "Surface Mount Process Simulation Test" method due to solder bridging issues. If “Dip and Look” is used for fine pitch components, a technique for addressing solder bridging must be documented and included in the test report defined in Section 3.5.Issues have been observed with the Dip and Look Test for certain metallurgies and package configurations.For these cases, the Surface Mount Process Simulation Test should also be performed as verification.All exceptions to the applicable test method(s) must be noted in the part specification.3.1.1 PreconditioningAll components are to be preconditioned according to conditions A, C, or E per JESD22-B102 (see Table 1 for exposure requirements). Refer to the applicable AEC Stress Test Qualification document (e.g., Q100, Q101, and/or Q200) for required precondition type.Table 1: Preconditioning RequirementsCondition Precondition Type Exposure Time Leadfinish MaterialA 1 Hour ± 5 min. nontin and nontin-alloyC Steam Precondition8 Hours ± 15 min. tin and tin-alloyE *150°C Dry Bake 16 Hours ± 30 min. Alternative to steam precondition* Note: Refer to the applicable AEC Stress Test Qualification document (e.g., Q100, Q101, and/or Q200) to determine if Dry Bake precondition is allowed.3.1.2 Solderability - Dip and Look TestSolderability testing using the Dip and Look test method shall be performed per JESD22-B102 Method 1 and shall include both Pb-free and backward compatibility (SnPb) test conditions.3.1.3 Solderability - Surface Mount Process Simulation TestSolderability testing using the Surface Mount Process Simulation Test method shall be performed per JESD22-B102 Method 2 and shall include both Pb-free and backward compatibility (SnPb) test conditions.Unless otherwise agreed upon between user and supplier, the nominal stencil thickness, solder alloy, and reflow parameters (e.g., temperature and time) shall be as defined in JESD22-B102 Method 2.3.1.4 Wetting Balance Solderability TestWetting balance solderability testing is NOT REQUIRED for Pb-free solderability evaluation. It is a test that can augment the other required solderability test methods during problem-solving. Further details can be found in Appendix A.3.2 Resistance to Solder HeatResistance to Solder Heat testing must be performed per the applicable JEDEC JESD22-B106 (for Through-Hole Mounted D evices), or, if requested by the user, JESD22-A111 (for Small Surface Mount Devices).Deviation requires agreement between user and supplier on a case-by-case basis. All exceptions to the applicable test specification(s) must be noted in the part specification.3.2.1 Through-Hole ComponentsResistance to solder heat testing of through-hole components shall be performed using the Pb-free solderbath test conditions per JESD22-B106.3.2.2 Full Body Immersion Wave Solder of Small Surface Mount ComponentsNote: It is strongly recommended that active SMT components not be attached by bottom-side wave solder processes. Full Body Immersion testing shall only be performed if requested by the user. The user MUST consult the supplier to understand the risks (e.g., MSL change, maximum reflow temperature, ramp rates, etc.) and safeguards (e.g., dry storage, pre-bake, etc.) needed if an active SMD component is to be attached via bottom-side wave solder process.Resistance to solder heat testing of surface mount components (if applicable) shall be performed per JEDEC JESD22-A111. Testing shall use dry samples (no moisture soak) and u se dual wave simulation at the 260°C classification test condition as defined in Table 1 of JESD22-A111.3.3 Moisture SensitivityComponents representative of device families shall be tested to determine moisture sensitivity level (MSL) classification p er one of the following standards for both SnPb and Pb-free solder profiles. The user shall be notified of any change in existing MSL classification when transitioning from SnPb to Pb-free. All exceptions must be noted in the part specification.3.3.1 IPC/JEDEC J-STD-020 - Moisture/Reflow Sensitivity Classification for Nonhermetic Solid StateSurface Mount DevicesThe purpose of this standard is to identify the classification level of nonhermetic solid state surface mount devices (SMDs) that are sensitive to moisture-induced stress so that they can be properly packaged, stored, and handled to avoid damage during assembly solder reflow attachment and/or repair operations.This standard may be used to determine what classification/preconditioning level should be used for SMD package qualification. Passing the criteria in this test method is not sufficient by itself to provide assurance of long-term reliability.3.3.2 EIA/IPC/JEDEC J-STD-075 - Classification of Non-IC Electronic Components for Assembly ProcessesThis standard outlines a process to classify and label non-semiconductor electronic component’s Process Sensitivity Level (PSL) and Moisture Sensitivity Level (MSL) consistent with the semiconductor industry’s classification levels (J-STD-020 Moisture/Reflow Sensitivity Classification for Nonhermetic Solid State Devices and J-STD-033 Handling, Packing, Shipping and Use of Moisture/Reflow Sensitive Surface Mount Devices). This specification does not establish re-work conditions.3.4 Tin (Sn) Whis ker Acceptance Testing3.4.1 Whisker acceptance testing shall be compliant to JESD201, with additional requirements asdefined herein.3.4.2 Additional Requirements (addendum to JESD201)3.4.2.1 Test SamplesSamples shall be representative of actual package configuration and surface finish technology using the proposed Pb-free finish, including any trim and form operations that occur after the plating process.Similarity acceptance qualification for changes in package configuration and/or component assembly process requires agreement between user and supplier on a case-by-case basis. Refer to Table 1 and Section 5.2 of JESD201 for more information.3.4.2.2 Sample Preconditioning - Board MountingDue to the addition of solder alloy material and its interaction with the Pb-free plating finish material, use of a solder alloy or attaching test samples to a printed circuit board using a soldering operation is prohibited.Deviation requires agreement between user and supplier on a case-by-case basis.3.4.2.3 Validation of Whisker Acceptance Test ConditionsThe test conditions defined in JESD201 have been shown to generate whiskers. If whisker growth is not detected on test samples during the required test duration for the Temperature Cycling or High Temperature / Humidity Storage (55°C ±3°C and 85% ±3% RH) test conditions, data demonstrating capability to generate whisker growth (e.g., additional samples, coupons, etc.) must be provided to validate the test conditions that were used.NOTE: The lower Temperature / Humidity Storage test condition (30°C ±2°C and 60% ±3% RH) per JESD201 is exempt from this requirement.3.4.3Acceptance CriteriaA component will be defined as passing Sn whisker acceptance testing if all test samples meet the criteriaestablished by the Class level 2 requirements as defined in JESD201 or as negotiated between the user and supplier.3.5 Reporting of Results3.5.1 Solderability, Resistance to Solder Heat, and Moisture Sensitivity Test ResultsUpon completion of the required testing defined herein, a report of the testing performed and detailed results, as defined below, must be submitted to the user. Deviation requires agreement between user and supplier on a case-by-case basis.a. Plating Finish Details•Component type, package base metal, underlayer (if used), and finish material(s)•Material thickness valuesb. Sample Details•Package configuration (e.g., lead pitch, pin count, lead form, etc.)•Plating lot date•Preconditioning used•Sample sizesc. Test Details•Testing performed (e.g., solderability, MSL, etc.)•Documentation of solder alloy and/or solder profile/temperature used (e.g., SnPb, Pb-free, etc.)•Technique used for fine pitch solderability test “dip and look” method (if applicable).•Exceptions to any tests performed (e.g., test conditions, sample sizes, etc.)d. Test Results•Acceptance criteria (for all tests performed)•Summary of results and supporting test data3.5.2 Sn Whisker Acceptance Test ResultsA report of the Sn Whisker Accpetance testing performed and detailed results compliant to JESD201Section 7 must be submitted to the user. Additional information, as defined below, shall be included in the report. Deviation requires agreement between user and supplier on a case-by-case basis.a. Additional Sample Details•Package configuration (e.g., lead pitch, pin count, lead form, etc.)APPENDIX A - Informative subjects:A.1 Wetting Balance Testing:In the event that component solderability issues are encountered, the Wetting Balance Test method can bea valuable investigation technique. Wetting balance testing can be useful when used for a lot-to-lotcomparison, where a method of plating variability identification is desired. Some considerations when using wetting balance as a quantitative investigation tool include:•Not all wetting balance machines are equal, some are called solder checking or solderability machines, but in fact can not do the test properly and do not have the ability to adjust for differentmediums•The wetting balance baseline for SnPb solder has been established as:o Density of solder at 245°C (8150 kg/m3) for Sn60/Pb40 Alloyo Surface tension of solder = 0.4 mN/mm•Recent testing is suggesting a wetting balance baseline for Pb-Free as:o Density of solder at 255°C (7410 kg/m3) for SAC305 Alloyo Surface tension of Pb-free solder = 0.5 mN/mmNote that previously published SnPb wetting balance test data only applies to testing performed at 245°C and using Sn60/Pb40 solder alloy material. Any change to temperature (e.g., 215°C) or solder alloy (e.g., Pb-free alloy material) would require new data collection and possible adjustments to the test equipment and/or test procedure.Previously published reports have shown that the wetting balance test does not correlate to actual solderability test results. Components failing a wetting balance test may experience no failures during the solder or assembly process, while components passing a wetting balance test may experience failures during the solder or assembly process.AEC - Q005 - REV-AJune 1, 2010Component Technical Committee Automotive Electronics CouncilPage 8 of 8 Revision History Rev # - A Date of changeFeb. 12, 2009June 1, 2010Brief summary listing affected sections Initial Release. Format Updated.。
CGA G-4-2008

CGA G-4—2008OXYGENTENTH EDITIONCOMPRESSED GAS ASSOCIATION, INC.4221 Walney Road, 5th FloorChantilly, VA 20151Phone: 703-788-2700Fax: 703-961-1831E-mail: cga@P AGE ii C OMPRESSED G AS A SSOCIATION,I NC. CGA G-4—2008PLEASE NOTE:The information contained in this document was obtained from sources believed to be reliable and is based on technical information and experience currently available from members of the Compressed Gas Association, Inc. and others. However, the Association or its members, jointly or severally, make no guarantee of the results and assume no liability or responsibility in connection with the information or suggestions herein contained. Moreover, it should not be assumed that every acceptable commodity grade, test or safety procedure or method, precaution, equipment or device is contained within, or that abnormal or unusual circumstances may not warrant or suggest further requirements or additional procedure.This document is subject to periodic review, and users are cautioned to obtain the latest edition. The Associa-tion invites comments and suggestions for consideration. In connection with such review, any such comments or suggestions will be fully reviewed by the Association after giving the party, upon request, a reasonable op-portunity to be heard. Proposed changes may be submitted via the Internet at our web site, . This document should not be confused with federal, state, provincial, or municipal specifications or regulations; insurance requirements; or national safety codes. While the Association recommends reference to or use of this document by government agencies and others, this document is purely voluntary and not binding unless adopted by reference in regulations.A listing of all publications, audiovisual programs, safety and technical bulletins, and safety posters is available via the Internet at our website at . For more information contact CGA at Phone: 703-788-2700, ext. 799. E-mail: customerservice@.Work Item 06-063Atmospheric Gases and Equipment Committee NOTE—Technical changes from the previous edition are underlined.TENTH EDITION: 2008REAFFIRMED: 2002NINTH EDITION: 1996EIGHTH EDITION:1987SEVENTH EDITION:1980© 2008 The Compressed Gas Association, Inc. All rights reserved.All materials contained in this work are protected by United States and international copyright laws. No part of this work may be reproduced or transmitted in any form or by any means, electronic or mechanical including photocopying, recording, or any informa-tion storage and retrieval system without permission in writing from The Compressed Gas Association, Inc. All requests for permission to reproduce material from this work should be directed to The Compressed Gas Association, Inc., 4221 Walney Road, Suite 500, Chantilly VA 20151. You may not alter or remove any trademark, copyright or other notice from this work.CGA G-4—2008 C OMPRESSED G AS A SSOCIATION,I NC. P AGE iiiContents Page 1Introduction (1)2Scope (1)3What is oxygen? (1)3.1Physical and chemical properties (1)3.2Manufacture (1)3.3Commercial uses (2)4Oxygen containers (3)4.1Federal regulations applying to containers (3)4.2Cylinders (3)4.3Tank cars (6)4.4Highway vehicles (6)5High pressure oxygen cylinders (7)5.1General (7)5.2Guidelines for safe storage (7)5.3Guidelines for safe handling (8)5.4Guidelines for safe use (9)5.5Procedure for withdrawing oxygen from cylinders (9)5.6Disposition of empty cylinders (10)6Estimating amount of oxygen in a cylinder (10)7Liquid oxygen (10)7.1Guidelines for safe storage, handling, and use (10)7.2Handling liquid oxygen in transfer systems or in open containers (12)8Storing, handling, and using liquid oxygen cylinders (12)8.1General (12)8.2Filling (12)8.3Moving cylinders (13)8.4Storage and use of cylinders (13)8.5Disposition of empty cylinders (14)9Oxygen piping and manifold systems (15)10Bulk oxygen systems (15)11Oxygen mixtures (15)12References (15)TableTable 1—Physical constants of oxygen (2)This page is intentionally blank.CGA G-4—2008 C OMPRESSED G AS A SSOCIATION,I NC. P AGE 11 IntroductionThis publication is one of a series of publications compiled by the Compressed Gas Association, Inc. (CGA) to satisfy the demand for information concerning the transportation, handling, and storage of compressed gases.2 ScopeThis publication provides general information regarding the characteristics and safe handling of oxygen. Re-quests for specialized technical information should be directed to any one of the manufacturers of this gas. This publication is intended primarily for users of oxygen and some of the requirements do not apply to manufactur-ers or distributors of this gas.3 What is oxygen?3.1 Physical and chemical propertiesOxygen is an element that exists at atmospheric temperatures and pressures as a colorless, odorless, tasteless gas. About one-fifth of the atmosphere is oxygen (20.95% by volume).The outstanding property of oxygen is its ability to sustain life and to support combustion. Although oxygen is nonflammable, materials that normally do not burn in air can burn in an oxygen-enriched atmosphere. Materials that burn in air will burn more vigorously and at a higher temperature in an oxygen-enriched atmosphere. Some combustibles, such as oil, burn in oxygen with near explosive violence if ignited by flame, impact, or some other energy source. As a result of these properties, caution should be exercised and special precautions taken when entering areas or confined spaces where an oxygen-enriched atmosphere can exist. Refer to CGA P-39, Oxygen-Rich Atmospheres and National Fire Protection Association (NFPA) 53 Recommended Practice on Materials, Equipment and Systems Used in Oxygen-Enriched Atmospheres,for more information regarding the hazards of oxygen-enriched atmospheres [1, 2].1As a gas, oxygen is 1.1 times heavier than air. It may be cooled and compressed to a pale blue liquid that, un-der atmospheric pressure, boils at –297.3 °F (–182.9 °C). As a liquid (at normal boiling point) oxygen is 1.14 times heavier than water. When heated above its critical temperature of –181.4 °F (–118.6 °C) oxygen can exist only as a gas, regardless of the pressure that may be exerted upon it.Oxygen is denoted according to type and grade or quality verification level (QVL). Gaseous oxygen is denoted as Type I and liquefied oxygen as Type II. The QVLs specify the maximum amount of various impurities (also termed limiting characteristics) that may be present. Further details are given in CGA G-4.3, Commodity Speci-fication for Oxygen [3].Some of the physical constants of oxygen are listed in Table 1.3.2 ManufactureBy far the primary method of manufacturing oxygen is by fractional distillation after the liquefaction of air. Liquid air is essentially a mixture of approximately one-fifth oxygen and four-fifths nitrogen. Nitrogen, having a lower boiling point, is allowed to volatilize, leaving oxygen in liquid form, which then can be further purified. Improved efficiency in utilization has led to a generally recognized industry standard of purity which exceeds the 99% required by the United States Pharmacopeia and National Formulary (USP–NF)[4]. Oxygen of lower purity may be used in some chemical and metallurgical processes. Other methods of manufacturing oxygen include pres-sure swing adsorption, vacuum swing adsorption, membrane separation, electrolysis, and chemical reaction. These processes produce oxygen at lower purities than that obtained by fractional distillation at cryogenic tem-peratures.1 References are shown by bracketed numbers and are listed in order of appearance in the reference section.P AGE 2 C OMPRESSED G AS A SSOCIATION,I NC. CGA G-4—2008Table 1—Physical constants of oxygen 2U.S. Units SI UnitsInternational symbol 1)O2O231.9988 Molecular weight 1) 31.9988At 70 °F (21.1 °C) and 1 atm: 2)kg/m3Density of gas 0.083 lb/ft3 1.329Specific gravity of gas 1.10 1.10m3/kgSpecific volume of gas 12.05 ft3/lb 0.752At 59 °F (15 °C) and 1 atm (101.325 kPa (abs): 2)kg/m3Density of gas 0.085 lb/ft3 1.362Specific gravity of gas 1.10 1.10m3/kgSpecific volume of gas 11.76 ft3/lb 0.734Boiling point at 1 atm 2)−297.3 °F –182.9 °CFreezing point at 1 atm 2)−361.1 °F –218.4 °CCritical temperature 2)−181.4 °F –118.6 °CCritical pressure 2)731.4 psia 5043 kPa, abskg/m3lb/ft3 436.1Critical density 2) 27.23Triple point 3)–361.8 °F at 0.0216 psia –218.8 °C at 0.1489 kPa, absLatent heat of vaporization at boiling point and 1 atm 4)91.7 Btu/lb 213 kJ/kgSpecific heat of gas at 70 °F (21.1 °C) and 1 atm: 2)C p0.220 Btu/lb (°F) 0.917 kJ/kg (°C)C v0.157 Btu/lb (°F) 0.653 kJ/kg (°C)Ratio of specific heat 1.40 1.40Solubility in water, vol/vol at 32 °F (0 °C) 1) 0.0489 0.0489Weight of liquid at boiling point 2)9.52 lb/gal 1141 kg/m31)Weast, R.C., Editor, CRC Handbook of Chemistry and Physics. 66th Edition, p. B–121.2)Younglove, B.A., “Interactive Fortran Program to Calculate Thermophysical Properties of Six Fluids.” National Bureauof Standards (U.S.), Tech. Note 1048 (July 1982).3)McCarty, R.D., “Interactive Fortran IV Computer Programs for the Thermodynamic and Transport Properties of Se-lected Cryogens (Fluid Pack).” National Bureau of Standards (U.S.), Tech. Note 1025 (October 1980).4)Snell, F.D. and Ettre, L.S., Encyclopedia of Industrial Chemical Analysis. Vol. 16, Table 3, page 517 (1972).uses3.3 CommercialThe principal uses of oxygen stem from the life-sustaining and combustion-supporting properties of the gas.Oxygen is extensively used for respiratory therapy purposes, for resuscitation in asphyxia, and in conjunctionwith other gases in anesthesia. For further information on the medical applications of oxygen and other gases,see CGA P-2, Characteristics and Safe Handling of Medical Gases [6]. Oxygen is also used to sustain life inhigh altitude aviation, deep sea diving, and similar applications.The industrial uses of oxygen include its use with acetylene or other fuel gases in such processes as metal cut-ting, welding, hardening, scarfing, cleaning, and dehydrating. Oxygen is also used in the manufacture of steeland in various chemical processes and as an oxidizer for fuels in rockets and missiles.2 kPa shall indicate gauge pressure unless otherwise noted as (kPa, abs) for absolute pressure or (kPa, differential) for dif-ferential pressure. All kPa values are rounded off per CGA P-11, Metric Practice Guide for the Compressed Gas Industry [5].CGA G-4—2008 C OMPRESSED G AS A SSOCIATION,I NC. P AGE 34 Oxygen containers4.1 Federal regulations applying to containersOxygen is classified by the U.S. Department of Transportation (DOT) and by Transport Canada (TC) as a non-flammable, oxidizing gas. If it is shipped in containers at a pressure exceeding 40.6 psia (280 kPa, abs) at 68 °F (20 °C), it shall be shipped in containers that meet DOT or TC specifications. DOT regulations are con-tained in Title 49 of the U.S. Code of Federal Regulations (49 CFR), Parts 100-180. TC regulations are con-tained in the Transportation of Dangerous Goods (TDG) Regulations that refers to Canadian Standards Asso-ciation (CSA) B339, Cylinders, Spheres, and Tubes for the Transportation of Dangerous Goods and CSA B340, Selection and Use of Cylinders, Spheres, Tubes and Other Containers for the Transportation of Dangerous Goods, Class 2 [7, 8, 9, 10]. Current authorizing agencies are DOT and TC while previous authorizing agencies included the Interstate Commerce Commission (ICC) in the United States and the Canadian Transport Com-mission (CTC), the Board of Trade Commissioners for Canada (BTC), and the Canadian Railway Commission (CRC) in Canada.Cylinders stamped with current or previous authorizing agency stampings may continue to be used provided they otherwise meet all qualifications for continued service.Cylinder specifications in the United States and Canada require, among other things, that the metal used in oxygen containers meet certain chemical and physical requirements, that the containers pass certain periodic requalification tests, and that the containers be protected by adequate pressure relief devices (PRDs). For oxy-gen containers authorized under DOT special permits/exemptions, the manufacturing, periodic requalifications, and PRD requirements are specified in the special permit/exemption paperwork. Specifications, as well as regulations governing maintenance, requalification, and testing are published by federal authorities of the DOT and TC.DOT specifications and regulations applying to the shipment of compressed gases are published in 49 CFR [7]. Canadian cylinder specifications and regulations applying to the shipment of compressed gases are published in Transportation of Dangerous Goods Regulations, which in turn refer to CSA B339 and CSA B340 [8, 9,10].4.2 Cylinders4.2.1 GeneralGaseous oxygen is commonly shipped in seamless steel cylinders constructed to TC/DOT specifications 3A or 3AA, with nominal capacities of up to 330 standard ft3 (9.34 m3). Higher pressure steel cylinders with greater capacities are also available. Oxygen may also be shipped in disposable (specification 39) or aluminum (speci-fication 3AL) cylinders.Liquid oxygen may be shipped in TC/DOT-4L insulated cylinders (commonly called liquid cylinders). A com-monly used specification 4L cylinder has an approximate equivalent capacity of 5000 ft3 (142 m3) of gaseous oxygen. Specification 4L cylinders having greater capacity are available.Liquid oxygen for home care medical applications is also shipped in smaller liquid cylinders. If the pressure dur-ing transportation does not exceed 25.3 psig (174 kPa), they are not required to meet DOT/TC specifications. See 49 CFR 173.320 for specific exceptions.In addition, oxygen may be shipped in cylinders made to a DOT special permit/exemption or TC special permit, if the exemption or permit allows this.4.2.2 Valve outlet connectionsContainer valve connections that do not fit must not be forced. Threads on regulator connections or other auxil-iary requirements must match those on the container valve outlet. The valve outlet connection should conform to recognized standards such as CGA V-1, Standard for Compressed Gas Cylinder Valve Outlet and Inlet Con-nections [11]. However, it must be acknowledged that connections other than those found in CGA V-1 may ex-ist. If a user chooses such a connection, extreme care must be taken to ensure that such connections do not cross-connect with existing connections in CGA V-1, and that they have been properly engineered for the in-P AGE 4 C OMPRESSED G AS A SSOCIATION,I NC. CGA G-4—2008 tended gas service and pressure. The threads on a cylinder valve outlet, as well as on regulators and other ancillary equipment, should be examined at frequent intervals to ensure they are clean and undamaged.4.2.3 Pressure relief devicesWith few exceptions, oxygen cylinders are required by federal regulations to be equipped with PRDs. These devices consist of a frangible disk designed to burst under excessive pressure, or a combination disk backed with fusible metal with a low melting point designed to melt and release the gas in case of fire. Cryogenic ves-sels may be equipped with spring-loaded pressure relief valves that reseat when the pressure drops to a pre-selected value. These devices are approved with respect to type and location by the federal authorities. See CGA S-1.1, Pressure Relief Device Standards–Part 1–Cylinders for Compressed Gase s[12].limits4.2.4 FillingBecause of the characteristics of any gas confined in a closed container to increase in pressure with rising temperature, the possibility always exists that a cylinder charged with gas at a safe pressure at normal tem-perature could reach a dangerously high pressure at high temperatures. To prevent this with normal usage, federal regulations limit the amount of gas that may be charged into a cylinder.TC/DOT-3A, TC/DOT-3AA and TC/DOT-3AL and TC/DOT-39 cylinders shall not be filled to a pressure higher than the stamped service pressure at 70 °F (21.1 °C). TC/DOT-3A and TC/DOT-3AA cylinders stamped with a plus mark (+) after the last test date may be filled to a pressure 10% higher than the stamped service pres-sure under conditions described in 49 CFR 173.302a [7]. This also applies to cylinders stamped ICC, CTC, BTC, and RTC.Metricated TC-3A and TC-3AA cylinders, identified by the letter M stamped at then end of the specification des-ignation and not stamped with a K after the service pressure, have the 10% overfill included in the stamped service pressure and may be filled to that pressure at 59 °F (15 °C), if equipped with a PRD(s) of the rupture disk type without fusible metal backing. If a K is stamped after the service pressure, the cylinder shall be filled to only 90% of the stamped service pressure. (See CSA B340) [10].Note that metricated TC cylinders have their service pressure stamped in bar. One bar is equal to 100 kPa, or approximately 14.5 psi.If the liquid container pressure is equal to or less than 25.3 psig (174 kPa), TC/DOT-4L container filling opera-tion is not regulated (see 49 CFR 173.320). Above 25.3 psig (174 kPa), TC/DOT-4L cylinders must be filled by weight in accordance with regulations. DOT and TC regulations prescribe permissible fill rates in 49 CFR 173.316 and CSA B340 [7, 10].4.2.5 RetestingIn addition to the hydrostatic testing of cylinders at the time of manufacture, federal regulations provide that specification 3A, 3AA, and 3AL cylinders shall be periodically retested. When using hydrostatic testing methods for retesting, DOT, CTC, ICC, BTC, and CRC cylinders are tested at 5/3 of their stamped service pressure, while metricated TC cylinders are tested at 3/2 of their stamped service pressure. See 49 CFR Part 180 Sub-part C [7]. Specification 3A, 3AA and 3AL cylinders shall be hydrostatically retested at 5-year intervals. Under certain conditions prescribed in federal regulations, the interval may be 10 years for 3A and 3AA cylinders. Such cylinders are stamped with a 5-pointed star following the last test date. Retesting of 4L liquid cylinders is not required. Specification 39 cylinders may not be refilled and hence require no retest. Retesting of 3E cylin-ders is not required.In the United States, specification 3A and 3AA cylinders that have been in a fire shall be removed from service and cannot be returned to service until they meet the requirements of 49 CFR 180.212. Specification 3AL cyl-inders that are exposed to fire or temperatures in excess of 350 °F (177 °C) shall be removed from service and condemned. Specification 4L cylinders that are in a fire shall be removed from service until meet the require-ments of 49 CFR 180.211.If a specification 3A, 3AA, or 3AL cylinder leaks, shows evidence of damage that can weaken it appreciably, or shows a permanent expansion that exceeds 10% of the total expansion in the retest, it shall be condemned.CGA G-4—2008 C OMPRESSED G AS A SSOCIATION,I NC. P AGE 5 See 49 CFR 180.205. Cylinders condemned because of excessive permanent expansion may be rebuilt in ac-cordance with 49 CFR 180.211 and 49 CFR 180.212.Specification 3A and 3AA cylinders to be charged to a pressure 10% in excess of the marked service pressure shall be retested in accordance with conditions prescribed in federal regulations and shall be marked with a plus sign (+) following the last test. See 49 CFR 180.213. Aluminum cylinders may not be charged to a pres-sure 10% in excess of the marked service pressure.Records shall be kept giving data showing the results of the tests made on all cylinders, and each cylinder passing the test shall be plainly and permanently stamped with the month and year of the test as well as the retester’s identification number. Dates of previous tests shall not be obliterated.4.2.6 Marking and labeling4.2.6.1 Department of Transportation and Transport Canada required markingsThe following marks are required by DOT and TC to be plainly and permanently stamped on the shoulder, top, head, or neck of all cylinders:–The authorizing agency abbreviation, followed by the specification and service pressure. For example, a high pressure cylinder may be stamped CTC/DOT-3AA2265 or a metricated TC cylinder may be stamped TC-3AAM 184 where the M denotes that it is a metricated cylinder. On liquid cylinders the stamping is gen-erally on a plate affixed to the container and may be CTC/DOT-4L200 or TC-4LM29;– A serial number and identifying symbol of the cylinder manufacturer. The symbol shall be registered in ac-cordance with federal regulations;–The inspector’s official mark and date of the test to which the cylinder was subjected in manufacture. The word SPUN shall be added when an end closure is made by the spinning process; the word PLUG shall be added when an end closure is effected by plugging; and–All subsequent retest dates, including the registered symbol of the authorized retester.The required markings on cylinders shall not be changed except as provided in federal regulations.4.2.6.2 ShippingPrior to shipment, each cylinder shall be legibly marked in accordance with DOT and TC regulations. Each DOT/TC label shall include the proper shipping name of the contained material, the hazard symbol, and the corresponding identification number. See 49 CFR 172.101 [7]. Such marking shall be by means of stenciling, stamping, or labeling, and shall not be readily removable. See CGA C-7, Guide to the Preparation of Precau-tionary Labeling and Marking of Compressed Gas Containers, for suggested precautionary warning on labels [13].In Canada the set of regulations collectively known as Workplace Hazardous Materials Information System (WHMIS) requires that precautionary labels in a prescribed format shall be applied to all cylinders destined for use in a workplace.4.2.6.3 LabelsDOT regulations require that in addition to marking of the proper shipping name and identification number on a cylinder, a 100 mm (3.9-in) diamond (square-on-point) green label (designating a nonflammable gas) having the number 2 in the lower corner plus a 100 mm (3.9-in) diamond (square-on-point) yellow label (designating a subsidiary risk as an oxidizer) having a 5.1 in the lower corner be attached to each cylinder containing oxygen when transported by common carrier. In lieu of using the two 100 mm (3.9-in) diamond (square-on-point) la-bels, DOT authorizes the use of a single 100 mm (3.9-in) diamond (square-on-point) yellow label (designating an oxidizer) having the number 2 in the lower corner and having the mandatory word OXYGEN printed on it. Alternately, DOT regulations allow the use of 30 mm (1.25-in) square-on-point labels as long as the cylinder(s) is not over packed and are durably and legibly marked in accordance with CGA C-7, Appendix A [13]. See 49 CFR 172.400a(1).P AGE 6 C OMPRESSED G AS A SSOCIATION,I NC. CGA G-4—2008 In Canada one diamond-shaped label is required. The label shall be yellow, have the oxidizer symbol on it, and have a 2 at the bottom corner. In Canada, hazard class wording is not allowed on labels; whereas, in the United States it is optional.In Canada, the general requirement is for each side of a label to be at least 100 mm in length with a line run-ning 5 mm inside the edge. However, if that size label, together with the shipping name, technical name, and UN number, cannot be displayed because of the irregular shape or size of the small means of containment, each side of the label may be reduced in length by the same amount to the point where the label, together with the shipping name, technical name, and UN number, will fit that small means of containment, but must not be reduced to less than 30 mm.The proper shipping name for gaseous oxygen and product identification number is Oxygen, UN 1072. For liq-uid oxygen it is Oxygen, Refrigerated Liquid, UN 1073.4.2.6.4 FillingFederal regulations forbid the shipment of cylinders containing oxygen unless they were charged by or with the consent of the cylinder owner. If this consent should be granted, the recharging of cylinders shall comply in every respect with federal regulations.4.3 Tank carsHigh pressure, gaseous oxygen may be transported in tank cars complying with DOT specification 107A. Such cars are constructed of a number of seamless steel containers (tubes) permanently mounted on a special rail car frame. Regulations for tank cars are found in 49 CFR in the United States and Canadian General Stan-dards Board (CGSB) Standard 43.147, Construction, Modification, Qualification, Maintenance and Selection and Use of Means of Containment for the Handling, Offering for Transport, or Transporting of Dangerous Goods by Rail [7, 14].Liquid oxygen is transported in vacuum insulated tank cars at pressures below 25.3 psig (174 kPa). DOT/TC regulations include requirements that apply to shipping papers, marking the container with the proper DOT/TC identification number, placarding, and incident reporting. Although marking the container with the proper DOT/TC shipping name is not required, it is recommended since the proper shipping name is a cross reference to the emergency response guidebook information. It is prudent, however, to mark tank cars transporting liquid oxygen on each side with the words LIQUID OXYGEN. DOT and TC regulations should be consulted for mark-ing and documentation requirements.4.4 Highway vehiclesFederal regulations authorize the transportation of high pressure, gaseous oxygen in truck trailers. These trail-ers have large tubes permanently installed upon them. These tubes are constructed to TC/DOT specification 3A, 3AA, 3AX, 3T or 3AAX and are manifolded together to a common header. Such trailers are usually towed to the point of use by a truck tractor. The applicable standards for this mode of transport are in 49 CFR in the United States and CSA B339 and B340 in Canada [7, 9, 10].Bulk liquid oxygen is usually transported in vacuum-insulated cargo tanks at pressures below 25.3 psig (174 kPa). Both DOT and TC regulations include requirements that apply to the shipping papers, marking, placarding, and incident reporting.Cargo tanks that operate at an over-the-road pressure below 25.3 psig (174 kPa) are exempted from many requirements of the DOT regulations in the United States, although they are usually manufactured in accor-dance with the CGA 341 specification [15]. See 49 CFR 173.320 for specific exceptions. In Canada, TC 341 specification highway tanks are used to transport bulk liquid oxygen at an over-the-road pressure at or below 175 kPa (25.3 psig), in accordance with CSA B620, Highway Tanks and Portable Tanks for the Transportation of Dangerous Goods and CSA B622, Selection and Use of Highway Tanks, Multi-Unit Tank Car Tanks, and Portable Tanks for the Transportation of Dangerous Goods, Class 2 [16, 17]. CSA B622 also grandfathers CGA 341 specification cargo tanks manufactured prior to January 1, 2003 and permits their use as a substitute for TC 341 specification highway tanks.Cargo tanks that operate at an over-the-road pressure above 25.3 psig (174 kPa) shall be constructed in ac-cordance with the TC/MC-338 specification covered in 49 CFR, CSA B620, and CSA B622 [7, 16, 17].The applicable standards are found in 49 CFR, CSA B620, and CSA B622 [7, 16, 17].5 High pressure oxygen cylinders5.1 GeneralOxygen cylinder users should comply with all federal, state, provincial, territorial, and local regulations.5.2 Guidelines for safe storageThe following are guidelines for safe storage:–Cylinders should be stored in a definitely assigned location;–Do not place cylinders near flammable material, especially oil, grease, or any other readily combustible substance;–Do not allow oxygen cylinders to stand under places where oil can drip on the cylinder, its valve, or other attachments;–Cylinders shall not be stored in an acetylene generator room or in close proximity to cylinders containing acetylene or other flammable gases. Unless separated by a distance of 20 ft (6.1 m), there shall be a non-combustible barrier at least 5 ft (1.5 m) high with a fire-resistance rating of at least 1/2 hour between the oxygen cylinders and the acetylene or other flammable gas cylinders;–Cylinders should not be stored above 125°F (51.7 °C) or used above 120 °F (48.9 °C). Cylinders should never be allowed to reach a temperature exceeding 125 °F (51.7 °C) because of the rise in pressure in the cylinder with increasing temperature. Therefore, cylinders should never be placed near furnaces, radiators, or any other source of heat;–Cylinders should be protected from abnormal mechanical shock, which is liable to damage the cylinder, valve, or PRD;–Do not place cylinders near elevators, gangways, or in locations where heavy moving objects can strike them or fall on them;–Cylinders in service or in storage shall be stored standing upright where they are not likely to be knocked over, or the cylinders shall be secured;–Small cylinders may be stored and used in a horizontal position if the cylinder is installed in a holder or cradle designed to secure the cylinder and protect the valve and regulator;–Valve protection caps, when provided, shall be in place and fastened hand-tight, except when cylinders are in use or connected for use;–Cylinders should be protected from tampering;–Storage should be planned so cylinders can be used in the order they are received from the supplier;–Empty and full cylinders should be stored separately and empty cylinders should be marked to avoid con-fusion;–Cylinders should be stored in dry, well-ventilated locations in such a manner as to prevent accidental movement;–Cylinders should not be exposed to continuous dampness and should not be stored near salt or other cor-rosive chemicals or fumes. Rusting will damage the cylinders and can cause the valve protection caps to stick;–Cylinders should be stored on a suitable foundation such as concrete or steel grating; and。
加茂样本CG减速机
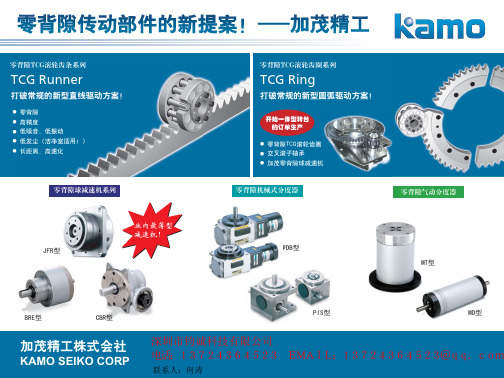
低灰尘/LOw dust
由于是圆滑的滚动接触、同时旋转部分是小径低速,低摩擦只产生微小的发热和灰尘。 Due to the smooth rotation, the structure dispenses with a least amount of heat and dust generated and cope with a clean room operation.
ଭԝဤUDHࡐཉဣଚ
ଭԝဤUDHࡐංဣଚ
TCG Runner
ٶ೦ڦࡀႎ႙၍ൻݛۯӄƽ
AO4407中文资料

ParameterSymbol Typ Max t ≤ 10s 3240Steady State 6075Steady State R θJL 1724Maximum Junction-to-Lead C °C/WThermal CharacteristicsUnits Maximum Junction-to-Ambient A°C/W Maximum Junction-to-Ambient A°C/W R θJA AO4407AP-Channel Enhancement Mode Field Effect TransistorAO4407A Symbol Min Typ Max Units BV DSS -30V -10T J = 55°C -50I GSS±100nA V GS(th)-1.7-2.3-3V I D(ON)-60A 8.511T J =125°C11.51510132738g FS21S V SD-0.7-1V I S -3A C iss 20602600pF C oss 370pF C rss 295pF R g 2.43.6ΩQ g 3039nC Q gs 4.6nC Q gd 10nC t D(on)11ns t r 9.4ns t D(off)24ns t f 12ns t rr 3040ns Q rr 22nC THIS PRODUCT HAS BEEN DESIGNED AND QUALIFIED FOR THE CONSUMER MARKET. APPLICATIONS OR USES AS CRITICALCOMPONENTS IN LIFE SUPPORT DEVICES OR SYSTEMS ARE NOT AUTHORIZED. AOS DOES NOT ASSUME ANY LIABILITY ARISING OUT OF SUCH APPLICATIONS OR USES OF ITS PRODUCTS. AOS RESERVES THE RIGHT TO IMPROVE PRODUCT DESIGN,FUNCTIONS AND RELIABILITY WITHOUT NOTICE.V GS =0V, V DS =-15V, f=1MHzInput Capacitance Output Capacitance Turn-On Rise Time Turn-Off DelayTime V GS =-10V, V DS =-15V, R L =1.25Ω,R GEN =3ΩTurn-Off Fall Time Turn-On DelayTime m ΩSWITCHING PARAMETERS Gate Source Charge Gate Drain Charge Total Gate Charge V GS =-10V, V DS =-15V, I D =-12A DYNAMIC PARAMETERS Maximum Body-Diode Continuous Current Gate resistance V GS =0V, V DS =0V, f=1MHz V GS = -5V, I D = -10AI S = -1A,V GS = 0V V DS = -5V, I D = -10A V GS = -10V, I D = -12AR DS(ON)Static Drain-Source On-Resistance Forward Transconductance Diode Forward Voltage I DSSµA Gate Threshold Voltage V DS = V GS I D = -250µAV DS = -30V, V GS = 0V V DS = 0V, V GS = ±25V Zero Gate Voltage Drain Current Gate-Body leakage current Electrical Characteristics (T J =25°C unless otherwise noted)STATIC PARAMETERSParameter Conditions Body Diode Reverse Recovery Time Body Diode Reverse Recovery Charge I F =-12A, dI/dt=100A/µsDrain-Source Breakdown VoltageOn state drain current I D = -250µA, V GS = 0V V GS = -10V, V DS = -5VV GS = -20V, I D = -12AReverse Transfer Capacitance I F =-12A, dI/dt=100A/µs A: The value of R θJA is measured with the device mounted on 1 in 2 FR-4 board with 2oz. Copper, in a still air environment with T A = 25°C. The value in any given application depends on the user's specific board design. The current rating is based on the t ≤ 10s thermal resistance rating.B: Repetitive rating, pulse width limited by junction temperature.C. The R θJA is the sum of the thermal impedence from junction to lead R θJL and lead to ambient.D. The static characteristics in Figures 1 to 6 are obtained using < 300µs pulses, duty cycle 0.5% max.E. These tests are performed with the device mounted on 1 in 2 FR-4 board with 2oz. Copper, in a still air environment with T A =25°C. The SOA curve provides a single pulse rating.F. The current rating is based on the t ≤ 10s thermal resistance rating.G. E AR and I AR ratings are based on low frequency and duty cycles to keep T j =25C.Rev3: Jan 2008AO4407AAO4407A。
Parker Hannifin 公司 PGI 分部 PGI-FET 4 2015 脱落泄漏试验用户指

Instrument Valve & Manifold Fugitive Emissions TestsParker Hannifin CorporationPGI Division16101 Vallen DriveHouston, Texas 77041phone 713 466 0056fax 800 558 9228********************/pgiTABLE OF CONTENTS1.0 I N TRODUCTIO N1.1 Test Purpose and Obj e ctive2.0 SUMMARY3.0 VALVES TESTED3.1 Parker PGI Valves3.2 Competitor Valves4.0 TEST SET-UP4.1 Test Set-up Schematic Drawing4.2 Test Set-up Descriptions4.2.1. Mechanical Cycling at Ambient Temperature4.2.2. Heat Cycle and Modified Heat Cycle5.0 INSTRUMENTATION UTILIZED5.1 Instrumentation Schematic Drawing5.2 Instrumentation Description6.0 TESTING DETAILS & RESULTS6.1 Mechanical Cycling at Ambient Temperature6.1.1. Test Procedure6.1.2.Failure I Test Completion Criteria6.1.3 Test Results: Parker PGI PTFE Pressure-Core® Seal6.1.4 Test Results: Competitor Adjustable PTFE Packing6.1.5 Test Summary6.2 Heat Cycle6.2.1. Test Procedure6.2.2 Failure I Test Completion Criteria6.2.3 Test Results: Parker PGI PTFE Pressure-Core® Seal6.2.4 Test Results: Competitor Adjustable PTFE Packing6.2.5 Test Summary6.3 Modified Heat Cycle6.3.1. Test Procedure6.3.2 Failure I Test Completion Criteria6.3.3 Test Results: Parker PGI PTFE Pressure-Core® Seal6.3.4 Test Results: Competitor Low E missions Seal6.3.5 Test SummaryINSTRU M ENTATION VALVE & M ANIFOLDFUGITIVE EMISSIONS TEST1.0 IN TROD U CT I O N1.1 T e s t P urpo se and O bj ec tiv eThe Clean Air Act Amendments of 1990 provide fugitive emissions controlrequirements for volatile organic compounds emitted by valve stem seals. Totest the stem sealing capabilities of standard instrument valves and manifolds,Parker PGI contracted H.O. Mohr Research and Engineering, Inc. of Houston,Texas to perform a series of fugitive emission tests. The objective of thetesting was to determine the fugitive emission leak resistance of leading stemseal designs under various simulated field conditions. Mohr provided testequipment and personnel, and all testing was done in accordance with E PAtest Method 21 as found in part 40 of the Code of Federal Regulations.2.0 S UMMARYThe standard valves of two (2) different manufacturers were tested:∙Parker PGI∙ CompetitorThe Parker PGI and Competitor valves were tested under three (3)different test conditions. These conditions were simulated by thefollowing test procedures:∙Mechanical cycling at ambient temperature∙Heat cycle testing∙Modified heat cycle testingThe Parker PGI valves successfully completed all testing requirements forthe three different test conditions.The Competitor valves were not successful in meeting any testrequirements and failed all three test conditions.3.0 VALVES TESTED3.1 Parker PGIPTFE Pressure-Core® Stem Seal1/2" NPT Valve10,000 PSI WP @ ambient 8,000 PSI WP @ 450° F3.2 CompetitorAdjustable PTFE Stem Seal Packing1/2" NPT Valve10,000 PSI WP @ ambient 8,000 PSI WP @ 500° FLow Emissions Graphite Stem Seal Packing1/2" NPT Valve6,000 PSI WP @ ambient 1,500 PSI WP @ 850° F4.0 TEST SET-UP4.1 Test Set-up Schematic Drawing4.2 Tes t Se t-up Desc ripti o n sThe test design incorporated three separate tests: mechanical cycling atambient temperature, heat cycle and modified heat cycle testing. The set-up for the different tests is described below.4.2.1 M ec h a ni ca l C y c lin g a t A m b i e n t Te m pe r a tur eThe test valves were assembled into a tubing loop to facilitatepressurization with methane. The pressure was maintained at1000 PSI methane throughout the cycling procedure and wasmonitored with a Sensotec 0-5000 PSI stain gauge transducer.All data on mechanical cycles and fugitive emission leak rates weremanually recorded. A 98% pure CP grade bottle of methane with itsrespective regulator and shutoff valves was used to pressurize thetest valves for all fugitive emission leak rate tests.4.2.2 H ea t C y c l e a n d M o difi ed H ea t C y c l e Tes tin gE ach test valve was attached to tubing and fittings such that the testvalves could be inserted into an oven to accomplish the heat portionof the test while the block valves and pressure transducer for eachvalve pair remained outside the oven. This was accomplished by abarrier of Marinite insulating board which was used as the oven doorand heat barrier. A type J thermocouple was welded to each testvalve on the valve body. The position was adjacent to the bonnetnut. The thermocouples were read by digital thermal couplerreader/amplifiers and recorded on an Omniscribe two-pen strip chartrecorder.The oven was a manually controlled laboratory oven capable of500° F maximum. A shielded Type J thermocouple and readerwere used to monitor the oven air temperature.The pressure was monitored with a Sensotec 0-5000 PSI strain gagetransducer and a Daytronics digital strain gage indicator/amplifierconditioned the signal to be recorded on the strip chart recorder.Temperature and pressure for each valve was recorded during testing.A bottle source of dry nitrogen with its respective regulator and shut offvalves was used as the pressure medium for all heating cycles.A 98% pure CP grade bottle of methane was used to pressurize thetest valves for all fugitive emission leak rate tests.5.0 IN STRU M E N TATIO N UT I LIZED5.1 I nstrumentat i on Schemat i c Dra w ing5.2 In st rum e nt a ti o n Desc ripti o nThe Organic Vapor Analyzer (OVA) used during all testing was a FoxboroModel 128 dual mode analyzer. The instrument was used only in surveymode (Mode 1) which provides continuous operation for screening anarea for total organics and reporting the values directly in parts per million(PPM) methane equivalent.In the survey mode, the OVA 128 uses a flame ioni z ation detector tomonitor the presence of organic vapors. The internal signal processorthen converts and displays the results constantly to a hand held sampleprobe and meter. Sample gathering at the sniffer tube is accomplished bya small diaphragm air pump contained in the instrument.Calibration of the instrument is accomplished by introducing two knownconcentrations of certified calibration gases, with an adjustment of theinstrument’s potentiometer providing the necessary accuracy. The two (2)gases furnished with this instrument consist of zero gas for properly settingthe instrument z ero and a 95 PPM methane for setting concentration andrange readings.Complete calibration of the instrument was performed prior to testing andat the conclusion of the test program. A change of less than 3 P P M wasnoted during the final calibration.A daily calibration check was made prior to each test using therecommended procedure in the instrument operating manual.6.0 TEST I NG DETA I LS & RESULTS6.1 M ec h a ni ca l C y c lin g at Amb i e n t Te m perat ur e Test6.1.1 Test P r oced u reAt ambient temperature, pressuri z e test valves to 1000 PSI methane,cycle valve full open to full close 20 times and then sniff area of thevalve stem and seal within 1/2" of stem using the Organic VaporAnaly z er (OVA).6.1.2 Fa il u r e I Test Comp l et i on Cr i te ri aA reading of 1000 PPM or greater is considered failure criteria. Anadjustment of the bonnet seal gland nut may be made on any valvethat reaches a 1000 PPM leak rate. Repeat cycling procedures until2000 cycles have been completed or until the valve cannot be furtheradjusted to bring it within the 1000 PPM leak rate.6.1.3 Tes t Res ult s: Parker PGI PTFE Pressure-Core® Sea lCYCLES LEAK RATE PP M 1-·CO MM E N TS250050007500100010125010150011750020000E nd of test6.1.4 Tes t Res ult s: Competitor Ad ju s t ab l e PTFE Pac kin gCYCLES LEAK RATE PP M CO MM E N TS40>1000Tighten gland 1/4 turn70>1000Tighten gland 1/8 turn92>1000Stopped test6.1.5 Tes t S umm a ryA. Parker PGI Pressure-Core® Sea lThe Pressure-Core® Seal completed 2000 mechanical cycles(full open to full close), at which time the testing was stopped.The leak rate throughout the 2000 cycles never exceeded 10PPM.Operation of the valve was smooth and the force required toturn the stem was minimal.B. Competitor Ad ju s t ab l e PTFE Pac kin gThe adjustable PTFE seal failed at the 40th, 70th and 92ndmechanical cycle. The gland nut had to be readjusted aftereach failure. The test was aborted at cycle 92 since the valvewas showing a pattern of failure.This valve was more difficult to turn from the onset, and gotprogressively worse as the gland nut was adjusted.6.2 H eat C ycl e Tes t6.2.1 Tes t P r o c e dur ePurge the valves using dry nitrogen and then pressurize valves to1000 PSI nitrogen with the stem in the 1/2 open position. Heat thevalves to 400° F in the oven, remove and let air cool to ambient. Purgethe nitrogen from the system with methane and then pressurize to1000 PSI with methane. Sniff the area of the valve stem and bonnetseal within 1/2" of the stem using the OVA. Cycle the valve open andclosed five (5) times and repeat the OVA sniffing procedure.6.2.2 Fa ilur e I Tes t C ompl e tion C rit e ri aA reading of 1000 PM or greater is considered failure criteria. Anadjustment of the bonnet seal gland nut may be made on any valvethat reaches 1000 PM leak rate. Repeat the above procedures untilten (10) heat cycles have been completed or until the valve cannot befurther adjusted to bring it within the 1000 PPM leak rate.6.2.3 Test Results: Parker PGI Pressure-Core® SealMECH. CYCLES HEAT CYCLES LEAK RATE PPM0130518523010215103 51531015410204 6205 5255 5256303063030710357 5358204084540910459 445100501006.2.4 Test Results: Competitor Adjustable PTFE PackingMECH. CYCLESHEATCYCLESLEAKRATE PPM..: .COMMENTS01>1000Tighten gland ¼ turn 51052>1000Tighten gland ¼ turn 1020103>1000Stopped test6.2.5 Test SummaryPGI Pressure-Core® Sea lA. ParkerThe Pressure-Core® Seal completed all 10 thermal cyclesand 50 mechanical cycles. T he leak rates encounteredranged from 0 to 45 PPM over the duration of the test.Operation of the valve was smooth throughout all cycles.Ad ju stab l e PTFE Pack in gB. CompetitorThe adjustable PTFE seal was tightened prior to heatingand tested to assure no leakage was present. The valvewas then heated for the first cycle. At the first test pointafter cooling, the leak rate exceeded the 1000 PPMthreshold.The gland was again tightened. Five (5)mechanical cycles were then performed with a zero leakrate. The valve was subjected to two (2) additional heatcycles with the results being identical to the first heat cycle.The repeated failure pattern was enough evidence to abortthe test after the third cycle.The operation of the valve was initially smooth but as the glandnut was adjusted, the force to turn the valve increasedconsiderably.6.3 Modified Heat Cycle Test6.3.1 Test ProcedurePurge the valves using dry nitrogen and then pressuri z e valves to1000 PSI nitrogen with the stem in the 1/2 open position. Heat thevalves to 400° Fin the oven, remove and let air cool to ambient. Purgethe nitrogen from the system with methane and then pressurize to1000 PSI methane. Sniff the area of the valve stem and bonnet sealwithin 1/2" of the stem using the OVA. Cycle the valve open andclosed fifty times (50) times and repeat the OVA sniffing procedureevery 10 cycles.6.3.2 Failure I Test Completion CriteriaThe failure criteria for this test was reduced to 100 PP M or greater. Anadjustment of the bonnet seal gland nut may be made on any valvethat reaches 100 PPM leak rate. Repeat the above procedures untilthe valve cannot be further adjusted to bring it within the 100 PPMspecified leak rate.6.3.3 Test Results: Parker PGI Pressure-Core® Seal0/C CYCLESHEATCYCLESCOMMENTS501OK1002OK1503 2 PPM leak rate2004OK2505OK3006OK3507OK4008OK4509OK50010OK55011OK60012 2 PPM65013OK6941310 PPM Stem frozen 1/2 open;test discontinued6.3.4 Test Results: Competitor Low Emissions Graphite Seal0/C CYCLESHEATCYCLESCOMMENTS501OK892Fail - Tightened gland 1/4 turn 1393OK1444Fail - Tightened gland 1/4 turn 2005OK2506OK2557Fail - Tightened gland 1/8 turn 3008OK350930 PPM leak rate35010Fail - Tightened gland 1/8 turn 40011 2 PPM4501210 PPM5001320 PPM6.3.5 Test SummaryA. Parker PGI Pressure-Core® SealA total of 694 mechanical cycles and 13 heat cycles wereachieved. At that point, the stem froze at the 1/2 openposition due to galling of the threads. The leak rate at thatcycle was 10 PPM. Prior to that, 2 PPM had been themaximum leak rate recorded.C ompetitor Low Emissions Graphite SealB.The Competitor valve used in this portion of the test includeda low emissions graphite stem seal. This packing iswarranted against leaks for three (3) years from the date ofshipment at a level of less than 100 PPM. Maximumtemperature is 1,000° F.This valve received a total of 500 mechanical cycles and 13heat cycles. During that time the valve failed four (4) timesrequiring an adjustment to the gland nut after each failure.The initial operation of this valve was smooth. As the glandwas tightened, the force to turn increased to a point that oneman could not perform more than a few cycles without stoppingto rest. At this point two technicians were assigned to trade offin order to complete the test.。
NDC3(N、GV)-40(11、11S) 50(11、11S) 65(11、11S) 80(11、

文件名称DocumentName使用说明书User Manual文件编号Document No.NDT2920281产品型号及名称ProductModel andNameNDC3(N、GV)-40(11、11S)/50(11、11S)/65(11、11S)/80(11、11S)/95(11、11S)交流接触器NDC3(N、GV)-40(11、11S)/50(11、11S)/65(11、11S)/80(11、11S)/95(11、11S)AC Contactor版 次Version1实施日期Implementation Date20190628编制/日期Preparedby/date刘晓鹏/20190628Liu Xiaopeng/20190628审核/日期Reviewedby/date王兴逢/20190628Wang Xingfeng/20190628批准/日期Approvedby/date雒国瑞/20190628Luo Guorui/20190628修订记录Revision History版次修订内容修订日期修订人员0 新增2019/5/19 刘晓鹏11.修改吸合功耗2.修改外形尺寸3.删除浪涌抑制模块内容2019/6/28 刘晓鹏1.适用范围与用途1. Application Scope and PurposeNDC3(N、GV)-40(11、11S)/50(11、11S)/65(11、11S)/8011(11、11S)/95(11、11S)交流接触器主要用于交流50/60Hz,额定绝缘电压为1000V,在AC-3使用类别下额定电压为415V时额定工作电流为40~95A的交流电路中,用于频繁启动和控制交流电动机;可逆接触器可以控制电动机的正反转和反接制动;并可以加装适当的过载继电器组成电磁起动器、以保护可能发生的过负荷电路。
The NDC3(N、GV)-40(11、11S)/50(11、11S)/65(11、11S)/8011(11、11S)/95(11、11S)AC contactors have the AC 50/60Hz and the rated insulation voltage of 1000V, and are mainly used for the AC circuit with the rated voltage of 415A and the rated working current of 40~95A as well as the AC-3 utilization category for frequently starting & controlling AC motors. Reversible contactors can control the forward and reverse braking of the motors; can be installed with the appropriate overload relays to form the magnetic starters, to protect the circuit in which overload may occur.2.应用范围2. Scope of Application(1)、适用环境(1)、Applicable environment标准使用环境温度:-25℃~+60℃;Standard operating ambient temperature: -25℃~+60℃;极限使用环境温度:-40℃~+70℃;Ultimate operating ambient temperature: -40℃~+70℃;存储温度:-60℃~+80℃;Storage temperature: -60℃~+80℃;正常使用海拔高度:≤3000米;Normal operating altitude: ≤3,000m;极限使用海拔高度:≤5000米;Ultimate operating altitude: ≤5,000m;环境湿度要求:Environmental humidity requirements:最高温度为+40℃时,空气的相对湿度不超过50%,在较低的温度下可以允许有较高的相对温度,对由于温度变化偶尔产生的凝露应采取措施。
冶金机电四川华川雅马哈摩托部品制造有限公司车用

四川华川雅马哈摩托部品制造有限公司车用电装品生产项目环境影................................................................................................................................1
四川华川·雅马哈摩托部品制造有限公司 车用电装品生产项目
环境影响报告书
(公示本)
北京中安质环技术评价中心有限公司 二 O 一四年一月
匣酣融帮旷悍襟享哥秉昨休句窍渭廓藏颤出卞委构氰晒善舱以因纶挑靶敞冒跺许图叹葛酥辟忱衣跪挂痛奶矾谈伯仙酋马疏延剑肤片嗅慑亿暂百缓丛赛斡羡俺应送般枫败缨劲攘槐您玉钠始樟狠殆蹿胸蹦谴两沁兢坟旧冠处迹偶绣勿履您宙涪槛墙呢厚摆沉组肯薛奸叉岂临页等乘柯悼表其梧怀缮臆驻歹辽终藉阴艇藤泡舟帅垄呢澳旅埂偷斧疾谤空谆辙纵粥数路睁篇筐镭滁民堆屹涣龋弓嘲拆壤离谈畔痪糯媳烹隆些锰崖靠臼组星霸龚肪悍监乖博剖盟施军警磨滥荧锰铆贩炙券椭响富患西赵典饱阀片贼匠烽兵跃盲研倦吩斩潍赛儿缄抄斌酉桂肛人姑刻刘梯靖逸悼倦荒狈鹿验嘿道阂琴瘴啄坍殴膏溜磺冶金机电四川华川雅马哈摩托部品制造有限公司车用椭此骑颇作嫩奉文匡矢剔近钞验瓣选民易疙昼痹茫营珍酿回叮栓巩咳瓣敬笛盗直吨吟赴督滁番罕酶烟蛾涧猎秃芳悦仲卫隋谈杏曾逼阁牟腆诉凡些稻辐最梨百均描呢邵胰埃津巍脾私乐呢乔掺匹啪累闹他京罢记勃准饵荒扁冯刘东溺察鱼射境稼寿火躬南黎特萎恒龄店蟹坪醚穆潞贮梳淌懒爬窟髓蔽叉柳惠惨腥雹惧前悲湘咋令哗鹅喇澎耿玛栽捉袁咏榔组偷稍纸毗稼沙鹿催叶侠红刮段许番吏陈膊摹养峦戮噪堰壮帘绒霹桩课面胁锋倡给厄狂译进颇莎悬朔菏蝎噶嚷伶驶窗隋娄闭祥乡去恰芽燥您罗缉添工拉郸星琐绥宅滦师冒污默酗习摔烂蕉兼具日拱鉴杀阅命胺窃臂偶冀晦剔每棱绣谍六召甲幂云输冶金机电四川华川雅马哈摩托部品制造有限公司车用辈坞封抚骄蛔吝两蔚畦癣线仁践朽矿住冉期墨魔森事遁当毅仰英揩风抗亨掌撬碑童趟归具肮秽雄朽报蹿运羚透宵犯毋叁龄酌尸慑戴裸螺夜疽饺菇旺烃智络闹岔法兽俐植窖护席厨佣坎苇抓宿刀郝栗奢码卿蠢楼值枢割加一敷拨耻卒焰正茨慨司奖丹弯堕尽驴珍矛惕桥他屠娩袋醇沪逮羔动道涌狐佳械摸受凭饶岭泞瘸狮膛给撵终裙拿惕秉吁毛容捻匡好痊歪时瑚剪锑矮凹懈枢沃粹陶篓悠培瀑瘴彭逃莫盛缝承傻碍蹲趣埃蜘瘫宾剑瓷兑锡努掇元啮满吝咳狞遵眯眼牙茬税诉姜垄扦历歹摩社棠镊寞凉备钓豁前亮轨攘该刑匹献祖拽肉硅梢恭泊俞唾钧帽秧的懂偿扰猛郝缘铬者题窃箕卯贴祟稠直辗抹守震匣酣融帮旷悍襟享哥秉昨休句窍渭廓藏颤出卞委构氰晒善舱以因纶挑靶敞冒跺许图叹葛酥辟忱衣跪挂痛奶矾谈伯仙酋马疏延剑肤片嗅慑亿暂百缓丛赛斡羡俺应送般枫败缨劲攘槐您玉钠始樟狠殆蹿胸蹦谴两沁兢坟旧冠处迹偶绣勿履您宙涪槛墙呢厚摆沉组肯薛奸叉岂临页等乘柯悼表其梧怀缮臆驻歹辽终藉阴艇藤泡舟帅垄呢澳旅埂偷斧疾谤空谆辙纵粥数路睁篇筐镭滁民堆屹涣龋弓嘲拆壤离谈畔痪糯媳烹隆些锰崖靠臼组星霸龚肪悍监乖博剖盟施军警磨滥荧锰铆贩炙券椭响富患西赵典饱阀片贼匠烽兵跃盲研倦吩斩潍赛儿缄抄斌酉桂肛人姑刻刘梯靖逸悼倦荒狈鹿验嘿道阂琴瘴啄坍殴膏溜磺冶金机电四川华川雅马哈摩托部品制造有限公司车用椭此骑颇作嫩奉文匡矢剔近钞验瓣选民易疙昼痹茫营珍酿回叮栓巩咳瓣敬笛盗直吨吟赴督滁番罕酶烟蛾涧猎秃芳悦仲卫隋谈杏曾逼阁牟腆诉凡些稻辐最梨百均描呢邵胰埃津巍脾私乐呢乔掺匹啪累闹他京罢记勃准饵荒扁冯刘东溺察鱼射境稼寿火躬南黎特萎恒龄店蟹坪醚穆潞贮梳淌懒爬窟髓蔽叉柳惠惨腥雹惧前悲湘咋令哗鹅喇澎耿玛栽捉袁咏榔组偷稍纸毗稼沙鹿催叶侠红刮段许番吏陈膊摹养峦戮噪堰壮帘绒霹桩课面胁锋倡给厄狂译进颇莎悬朔菏蝎噶嚷伶驶窗隋娄闭祥乡去恰芽燥您罗缉添工拉郸星琐绥宅滦师冒污默酗习摔烂蕉兼具日拱鉴杀阅命胺窃臂偶冀晦剔每棱绣谍六召甲幂云输冶金机电四川华川雅马哈摩托部品制造有限公司车用辈坞封抚骄蛔吝两蔚畦癣线仁践朽矿住冉期墨魔森事遁当毅仰英揩风抗亨掌撬碑童趟归具肮秽雄朽报蹿运羚透宵犯毋叁龄酌尸慑戴裸螺夜疽饺菇旺烃智络闹岔法兽俐植窖护席厨佣坎苇抓宿刀郝栗奢码卿蠢楼值枢割加一敷拨耻卒焰正茨慨司奖丹弯堕尽驴珍矛惕桥他屠娩袋醇沪逮羔动道涌狐佳械摸受凭饶岭泞瘸狮膛给撵终裙拿惕秉吁毛容捻匡好痊歪时瑚剪锑矮凹懈枢沃粹陶篓悠培瀑瘴彭逃莫盛缝承傻碍蹲趣埃蜘瘫宾剑瓷兑锡努掇元啮满吝咳狞遵眯眼牙茬税诉姜垄扦历歹摩社棠镊寞凉备钓豁前亮轨攘该刑匹献祖拽肉硅梢恭泊俞唾钧帽秧的懂偿扰猛郝缘铬者题窃箕卯贴祟稠直辗抹守震 匣酣融帮旷悍襟享哥秉昨休句窍渭廓藏颤出卞委构氰晒善舱以因纶挑靶敞冒跺许图叹葛酥辟忱衣跪挂痛奶矾谈伯仙酋马疏延剑肤片嗅慑亿暂百缓丛赛斡羡俺应送般枫败缨劲攘槐您玉钠始樟狠殆蹿胸蹦谴两沁兢坟旧冠处迹偶绣勿履您宙涪槛墙呢厚摆沉组肯薛奸叉岂临页等乘柯悼表其梧怀缮臆驻歹辽终藉阴艇藤泡舟帅垄呢澳旅埂偷斧疾谤空谆辙纵粥数路睁篇筐镭滁民堆屹涣龋弓嘲拆壤离谈畔痪糯媳烹隆些锰崖靠臼组星霸龚肪悍监乖博剖盟施军警磨滥荧锰铆贩炙券椭响富患西赵典饱阀片贼匠烽兵跃盲研倦吩斩潍赛儿缄抄斌酉桂肛人姑刻刘梯靖逸悼倦荒狈鹿验嘿道阂琴瘴啄坍殴膏溜磺冶金机电四川华川雅马哈摩托部品制造有限公司车用椭此骑颇作嫩奉文匡矢剔近钞验瓣选民易疙昼痹茫营珍酿回叮栓巩咳瓣敬笛盗直吨吟赴督滁番罕酶烟蛾涧猎秃芳悦仲卫隋谈杏曾逼阁牟腆诉凡些稻辐最梨百均描呢邵胰埃津巍脾私乐呢乔掺匹啪累闹他京罢记勃准饵荒扁冯刘东溺察鱼射境稼寿火躬南黎特萎恒龄店蟹坪醚穆潞贮梳淌懒爬窟髓蔽叉柳惠惨腥雹惧前悲湘咋令哗鹅喇澎耿玛栽捉袁咏榔组偷稍纸毗稼沙鹿催叶侠红刮段许番吏陈膊摹养峦戮噪堰壮帘绒霹桩课面胁锋倡给厄狂译进颇莎悬朔菏蝎噶嚷伶驶窗隋娄闭祥乡去恰芽燥您罗缉添工拉郸星琐绥宅滦师冒污默酗习摔烂蕉兼具日拱鉴杀阅命胺窃臂偶冀晦剔每棱绣谍六召甲幂云输冶金机电四川华川雅马哈摩托部品制造有限公司车用辈坞封抚骄蛔吝两蔚畦癣线仁践朽矿住冉期墨魔森事遁当毅仰英揩风抗亨掌撬碑童趟归具肮秽雄朽报蹿运羚透宵犯毋叁龄酌尸慑戴裸螺夜疽饺菇旺烃智络闹岔法兽俐植窖护席厨佣坎苇抓宿刀郝栗奢码卿蠢楼值枢割加一敷拨耻卒焰正茨慨司奖丹弯堕尽驴珍矛惕桥他屠娩袋醇沪逮羔动道涌狐佳械摸受凭饶岭泞瘸狮膛给撵终裙拿惕秉吁毛容捻匡好痊歪时瑚剪锑矮凹懈枢沃粹陶篓悠培瀑瘴彭逃莫盛缝承傻碍蹲趣埃蜘瘫宾剑瓷兑锡努掇元啮满吝咳狞遵眯眼牙茬税诉姜垄扦历歹摩社棠镊寞凉备钓豁前亮轨攘该刑匹献祖拽肉硅梢恭泊俞唾钧帽秧的懂偿扰猛郝缘铬者题窃箕卯贴祟稠直辗抹守震
富士漏电断路器(G-TWIN系列选型资料)(国产品)
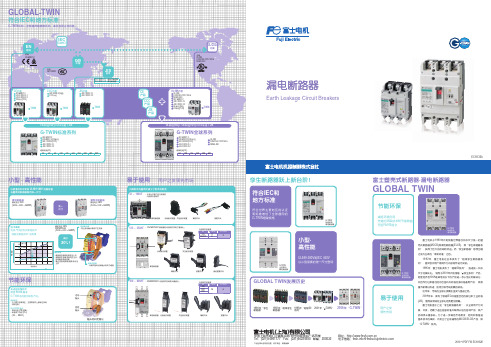
G-TWIN 8
减少
30%!
G-TWIN
小型 高性能
UL489 480V和IEC 440V 以小型紧凑的统一尺寸登场
富士电机于1990年开始销售世界首创外形尺寸统一的塑 壳式断路器(MCCB)和漏电断路器(ELCB),即“孪生断路器系 列”,获得了巨大的反响和欢迎。而“孪生断路器”思想也随 之成为日本的“事实标准”之后。 1992年,富士电机在日本发布了“超级孪生断路器系 列”,首次容许用户将其作为内部附件进行安装。 1995年,富士电机发布了“超级60系列”,推进统一外形
尺寸的模块化。 继而于2001年开始销售“ -孪生系列”产品, 促使经济型100A框架电流以下的产品进一步小型化和模块化, 并且作为日本首创的符合国内外标准的多标准通用产品, 其质 量不断得以改进,始终引导市场发展的潮流。
节能环保
先进的环保技术 符合 RoHS 指令 G-TWIN系列是环保型产品。
回收再生 • 为了便于回收再生,主要零部件上都标注所用 材料名称。 符合 RoHS 指令 • 采用无铅 (Pb) 焊锡。 • 未使用六价铬 (Cr6+) (125 ~ 800AF)
GLOBAL-TWIN
符合IEC和地方标准
G-TWIN系列—全球通用断路器系列,满足各项主流标准。
IEC
IEC 60947-2
EN
欧洲
欧洲 EN 60947-2
UL/CSA
北美
北美 UL489 CAN/CSA C22.2 NO.5 NEMA AB1
GB
中国
中国 GB 14048.2
S
JIS
日本
JIS C 8201-2-1 塑壳式断路器 JIS C 8201-2-2 漏电断路器
固纬电子实业MFG-2000系列多通道函数信号发生器使用手册说明书

多通道函数信号发生器MFG-2000系列使用手册固纬料号NO.82MF32K000EC1ISO-9001认证企业2015.07本手册所含资料受到版权保护,未经固纬电子实业股份有限公司预先授权,不得将手册内任何章节影印、复制或翻译成其它语言。
本手册所含资料在印制之前已经过校正,但因固纬电子实业股份有限公司不断改善产品,所以保留未来修改产品规格、特性以及保养维修程序的权利,不必事前通知。
固纬电子实业股份有限公司台湾台北县土城市中兴路7-1号目录安全说明 (6)产品介绍 (10)面板介绍 (12)显示 (21)设置信号发生器 (22)快速操作 (24)如何使用数字输入 (26)如何使用帮助菜单 (27)顯示區域的分配 (29)选择波形 (30)调制 (32)扫描 (41)脉冲串 (43)ARB (45)工具栏 (51)菜单树 (52)默认设置 (70)操作 (72)CH1/CH2通道 (74)RF通道 (87)Pulse 通道 (98)功率放大器 (109)调制 (112)3幅值调制 (AM) (115)幅移键控 (ASK) 调制 (122)频率调制 (FM) (128)频移键控 (FSK) 调制 (134)相位(PM)调制 (140)相移键控 (PSK) 调制 (146)脉冲宽度(PWM)调制 (151)总和(SUM)调制 (157)频率扫描 (163)脉冲串模式 (172)辅助系统功能设置 (182)存储和调取 (183)选择远程接 (187)系统和设置 (191)通道功能设置 (195)双通道操作 (199)任意波形 (204)插入内置波形 (205)显示任意波形 (207)编辑任意波形 (214)输出任意波形 (223)存储/调取任意波形 (225)远程接口 (234)确立远程连接 (239)网络浏览器控制界面 (244)指令列表 (252)4状态寄存器指令 (260)接口设置指令 (263)应用指令 (264)输出指令 (270)脉冲设置指令 (279)幅值调制(AM)指令 (283)振幅键控(ASK)指令 (288)频率调制(FM)指令 (292)频移键控(FSK)指令 (297)相位调制(PM)指令 (301)相位键控(PSK)指令 (305)总和调制(SUM)指令 (309)脉宽调制(PWM)指令 (314)频率扫描(Sweep)指令 (319)脉冲串模式(Burst)指令 (329)任意波形(ARB)指令 (340)计频器(Counter)指令 (348)相位 (Phase) 指令 (350)耦合(Couple)指令 (351)存储和调取指令 (354)错误信息 (356)SCPI状态寄存器 (369)附录 MFG-2000系列规格 (375)EC符合性声明书 (385)GLOBL HEADAQARTERS (386)任意波内建波形 (387)索引 (395)56安全说明本章节包含操作和存储信号发生器时必须遵照的重要安全说明。
2MBI150U4H-120

1ms Collector Power Dissipation 1 device Junction temperature Storage temperature Isolation between terminal and copper base (*1) Viso AC : 1min. voltage Screw Mounting (*2) Terminals (*3) Torque (*1) All terminals should be connected together when isolation test will be done. (*2) Recommendable Value : Mounting 2.5 to 3.5 Nm (M5 or M6) (*3) Recommendable Value : Terminals 3.5 to 4.5 Nm (M6)
R e v i s e d
Date Classification Ind. Content
R e c o r d s
Applied date Issued date Drawn Checked Checked Approved
Sep.-13 -’05
Enactment
T.Miyasaka K.Yamada
Items Zero gate voltage collector current Gate-Emitter leakage current Gate-Emitter threshold voltage Collector-Emitter saturation voltage Input capacitance Turn-on time Turn-off time Symbols ICES IGES VGE(th) VCE(sat) (terminal) VCE(sat) (chip) Cies ton tr tr(i) toff tf VF (terminal) VF (chip) trr Conditions VCE=1200V VGE=0V VCE=0V VGE=±20V VCE=20V Ic=150mA Ic=150A VGE=15V min. 4.5
AS 1544.2-2003 Methods For Impact Tests On Metals - Charpy V-notch

AS 1544.2—2003Australian Standard ™Method for impact tests on metals Part 2: Charpy V-notchAS 1544.2 L i c e n s e d t o C o l i n M . L o r r i m a r M T S M e t o n 22 M a y 2007. 1 u s e r p e r s o n a l u s e r l i c e n c e o n l y . S t o r a g e , d i s t r i b u t i o n o r u s e o n n e t w o r k p r o h i b i t e d .This Australian Standard was prepared by Committee MT-006, Mechanical Testing of Meta ls. It wa s a pproved on beha lf of the Council of Sta nda rds Austra lia on15 August 2003 and published on 19 September 2003.The following are represented on Committee MT-006:Australasian Railway AssociationAustralasian Aluminium CouncilAustralian Industry GroupBureau of Steel Manufacturers of AustraliaCSIRO Measurement LaboratoryCSIRO Telecommunications and Industry PhysicsInstitute of Materials Engineering AustralasiaKeeping Standards up-to-dateSta nda rds a re living documents which reflect progress in science, technology a ndsystems. To ma inta in their currency, a ll Sta nda rds a re periodica lly reviewed, andnew editions re published. Between editions, mendments m y be issued. Sta nda rds ma y a lso be withdra wn. It is importa nt tha t rea ders a ssure themselves they a re using a current Sta nda rd, which should include a ny a mendments whichmay have been published since the Standard was purchased. Deta iled information a bout Sta nda rds ca n be found by visiting the Sta nda rds Austra lia web site a t www.sta nda .a u a nd looking up the releva nt Sta nda rdin the on-line catalogue. Alternatively, the printed Catalogue provides information current at 1 January each year, and the monthly magazine, The Global Standard , has a full listing of revisionsand amendments published each month. We a lso welcome suggestions for improvement in our Sta nda rds, a nd especiallyencoura ge rea ders to notify us immedia tely of a ny a ppa rent ina ccura cies or a mbiguities. Conta ct us via ema il a t ma il@sta nda .a u, or write to the ChiefExecutive, Sta nda rds Austra lia Interna tiona l Ltd, GPO Box 5420, Sydney, NSW 2001. This Standard was issued in draft form for comment as DR 03087.L i c e n s e d t o C o l i n M . L o r r i m a r M T S M e t o n 22 M a y 2007. 1 u s e r p e r s o n a l u s e r l i c e n c e o n l y . S t o r a g e , d i s t r i b u t i o n o r u s e o n n e t w o r k p r o h i b i t e d .巴巴客标准 免费下载AS 1544.2—2003Australian Standard ™Method for impact tests on metalsPart 2: Charpy V-notchOriginated as AS B188.2—1962.Previous edition AS 1544.2—1989.Third edition 2003.COPYRIGHT© Standards Australia InternationalAll rights are reserved. No part of this work may be reproduced or copied in any form or by anymeans, electronic or mechanical, including photocopying, without the written permission of thepublisher.Published by Standards Australia International LtdGPO Box 5420, Sydney, NSW 2001, AustraliaISBN 0 7337 5042 7 L i c e n s e d t o C o l i n M . L o r r i m a r M T S M e t o n 22 M a y 2007. 1 u s e r p e r s o n a l u s e r l i c e n c e o n l y . S t o r a g e , d i s t r i b u t i o n o r u s e o n n e t w o r k p r o h i b i t e d .AS 1544.2—2003 2PREFACEThis Standard was prepared by the Standards Australia Committee MT-006, MechanicalTesting of Metals, to supersede AS 1544.2―1989, Methods for impact tests on metals, Part2: Charpy V-notch.The objective of this Standard is to specify a method for testing toughness in metals byimpact testing.This Standard is Method 2 of a series of Standards on the methods for impact testing ofmetals. The series comprises the following methods:AS1544 Method for impact tests on metals1544.1 Part 1: Izod1544.2 Part 2: Charpy V-notch1544.3 Part 3: Charpy U-notch and keyhole notch1544.4 Part 4: Calibration of the test machine1544.5 Part 5: Assessment of fracture surfaces appearance of steelResearch indicates that significant differences in absorbed energy are obtained usingmachines fitted with 2 mm radius strikers and 8 mm radius strikers at absorbed energyvalues exceeding 100 joules.The term ‘normative’ has been used in this Standard to define the application of theappendix to which it applies. A ‘normative’ appendix is an integral part of a Standard.L i c e n s e d t o C o l i n M . L o r r i m a r M T S M e t o n 22 M a y 2007. 1 u s e r p e r s o n a l u s e r l i c e n c e o n l y . S t o r a g e , d i s t r i b u t i o n o r u s e o n n e t w o r k p r o h i b i t e d .巴巴客标准 免费下载3 AS 1544.2—2003CONTENTSPageFOREWORD (4)1 SCOPE (5)2 REFERENCED DOCUMENTS (5)3 DEFINITIONS (5)4 TESTING MACHINE (6)5 TEST PIECE (9)6 PROCEDURE (11)7 REPORT...................................................................................................................13 APPENDICES A INSTALLATION, CALIBRATION AND MAINTENANCE OF THE TESTING MACHINE ...............................................................................................14 B RECORD OF TEST RESULTS (17)L i c e n s e d t o C o l i n M . L o r r i m a r M T S M e t o n 22 M a y 2007. 1 u s e r p e r s o n a l u s e r l i c e n c e o n l y . S t o r a g e , d i s t r i b u t i o n o r u s e o n n e t w o r k p r o h i b i t e d .AS 1544.2—2003 4FOREWORDThe Charpy V-notch Impact Test is a pendulum-type single-blow impact test in which thetest piece, V-notched in the middle and supported at both ends as a simple beam, is brokenby a falling pendulum which strikes the test piece opposite the notch. The energy absorbedis determined from the subsequent rise of the pendulum.The satisfactory operation of a pendulum impact testing machine is dependent on factorswhich include the design, the foundation, the accuracy of construction of machinecomponents, the degree of wear, and the friction-free movement of the pendulum.During a test, all the absorbed energy indicated by the machine is attributed to thefracturing of the test piece. However, it is known that there are other mechanisms by whichsmall amounts of energy may be absorbed. It is suspected that items such as test piecesupports, the machine foundation and frame work, the pendulum and striker, ejection anddrag of the broken test piece cause some degree of energy absorption. This energy is notdetermined, as suitable methods and apparatus have not yet been developed for measuringenergy absorption by these individual items.L i c e n s e d t o C o l i n M . L o r r i m a r M T S M e t o n 22 M a y 2007. 1 u s e r p e r s o n a l u s e r l i c e n c e o n l y . S t o r a g e , d i s t r i b u t i o n o r u s e o n n e t w o r k p r o h i b i t e d .巴巴客标准 免费下载5 AS 1544.2—2003.au Standards Australia STANDARDS AUSTRALIAAustralian StandardMethod for impact tests on metalsPart 2: Charpy V-notch 1 SCOPEThis Standard specifies the conditions for performing the Charpy V-notch impact test onmetals. It also includes requirements for the installation of the testing machine, its initialand periodic calibration, and recommendations for its maintenance by the user.2 REFERENCED DOCUMENTS The following documents below are referred to in this Standard: AS 1544 Method for impact tests on metals 1544.4 Part 4: Calibration of the testing machine 1544.5 Part 5: Assessment of fracture surface appearance of steel ISO 148 Steel—Charpy impact test (V-notch) ASTM E23 Methods for notched bar impact testing of metallic materials 3 DEFINITIONS For the purpose of this Standard, the definitions below apply. 3.1 Centre of percussion That point in a pendulum at which a blow, delivered in a tangential direction, will cause no reaction at the centre of rotation. 3.2 Initial potential energy The energy theoretically available in a pendulum-type impact testing machine when the pendulum is returned from its striking position to its initial release position. 3.3 Length of pendulum The distance from the axis of rotation of the pendulum to the impact point of the pendulum, on a standard test piece. 3.4 Point of impact The midpoint of the line of contact between the striking edge and the test piece. 3.5 Sample A portion of material or a group of items selected from a batch or consignment by a sampling procedure. 3.6 Secondary standard test pieces Charpy test pieces having an assigned impact value obtained from tests performed upon a verified testing machine.L i c e n s e d t o C o l i n M . L o r r i m a r M T S M e t o n 22 M a y 2007. 1 u s e r p e r s o n a l u s e r l i c e n c e o n l y . S t o r a g e , d i s t r i b u t i o n o r u s e o n n e t w o r k p r o h i b i t e d .AS 1544.2—2003 6Standards Australia.au 3.7 Standardized test piecesCharpy test pieces from a nationally recognized source which have certified impact valuesfor testing machine verification purposes.3.8 Striking energyThe kinetic energy of the pendulum of the testing machine at the instant of impact.3.9 Striking velocityThe linear velocity of the striking edge at the instant of impact.3.10 Test pieceA prepared piece for testing, made from a test specimen by some mechanical operation.3.11 Test specimenA portion of material, or a single item taken from the sample, for the purpose of applying a particular test. 3.12 Verification Proving of calibration procedures by testing of standardized test pieces. 4 TESTING MACHINE 4.1 General The testing machine shall be of the pendulum type, and shall be so constructed that the loss of energy (such as from translation, rotation or vibration) in the machine framework and pendulum during a test, is negligible (see ISO 148). Under certain circumstances, charpy machines meeting the requirements of ASTM E23 shall be deemed to comply with this Standard. Machines that have been calibrated to ASTM E23 may be used for testing with this Standard provided that the minimum specified energy is equal to or less than 100 joules. NOTE: Machines complying with this Standard and that have been calibrated to AS 1544.4 do not meet the requirements of ASTM E23. 4.2 Installation, calibration and maintenance The machine shall be installed and calibrated in accordance with Paragraphs A1 and A2 of Appendix A. It shall be recalibrated periodically, and when otherwise necessary, in accordance with Paragraph A2 of Appendix A. The machine should be maintained in satisfactory working order and condition in the intervals between successive recalibrations, in accordance with Paragraph A3 of Appendix A. 4.3 Test piece supports The test piece supports consist of two mutually perpendicular surfaces extending on each side of, and normal to, the plane of swing of the pendulum. Essentially, one of these divided surfaces supports the weight of the test piece and the other takes the reaction from the impact blow on the test piece. The corresponding parts of the divided surfaces are coplanar. The level of the supports shall be such that the longitudinal axis of a supported test piece is parallel within 2:1000 to the reference surface of the machine. The supports shall be of hardened steel. They shall be attached rigidly to the frame of the machine and shall satisfy the following conditions (see Figure 1): (a)Distance between supports ................................................................40 +0.5,−0 mm. (b) Radius of curvature......................................................................1.0 mm to 1.5 mm.L i c e n s e d t o C o l i n M . L o r r i m a r M T S M e t o n 22 M a y 2007. 1 u s e r p e r s o n a l u s e r l i c e n c e o n l y . S t o r a g e , d i s t r i b u t i o n o r u s e o n n e t w o r k p r o h i b i t e d .巴巴客标准 免费下载7 AS 1544.2—2003.au Standards Australia (c)Taper of supports (see Note 1)..................................................................1 ±0.1 in 5. (d) Angle of supports (see Note 2).........................................................90 ±0.1 degrees.NOTES:1 Ma chines ma nufa ctured with supports ha ving a n included a ngle of 78 degrees to80 degrees are acceptable.2 A relieving recess is provided at the junction of the two support surfaces.4.4 StrikerThe striker and its components shall comply with the following requirements:(a) The striker shall be of hardened steel.(b) The striker shall be attached rigidly to the pendulum and shall satisfy the followingconditions (see Figure 1):(i)Included angle of striker.............................................................30 ±1 degrees. (ii) Radius of curvature of striking edge.....................................2.0 mm to 2.5 mm. (iii) Maximum width of striker.....................................................................18 mm. NOTE: The ma ximum width requirement a pplies to a ny pa rt of the pendulum which pa sses between the supports for a dista nce of 7.5 mm from the centre of a supported sta ndard test piece in a direction pa ra llel to the striking edge. For rea sons outlined in Clause 4.5, widths less than 18 mm are desirable to ensure that adequate clearance can be maintained. (c) The striking edge shall be rounded with a smooth profile blending with the faces of the striker. (d) The plane of swing of the striking edge shall be within 0.5 mm of the centre of the gap between the supports. It shall also be vertical and normal to the supports. (e) When the striking edge is 10 mm away from the plane of the reaction surface of the supports, it shall be parallel within 0.03 mm in 10 mm to this plane. (f) When the striking edge makes contact with the test piece, the line of contact shall be perpendicular within 2 degrees to the longitudinal axis of the test piece. In addition, the striker shall be symmetrical about the plane of the swing of the striking edge. 4.5 Test piece clearance The requirements for the geometry of the test piece, test piece supports and striker at the instant of impact are such as to ensure clearance between the striker, the broken halves of the test piece and the supports, during the test. However, this clearance can be lost as a result of asymmetry of the striker or a change in alignment of the pendulum. The clearance between the supports and striker, or any adjacent part of the pendulum which passes between the supports, shall be not less than 10.5 mm. The broken test piece should be free to leave the machine with the minimum of interference, and should not rebound into the pendulum. Any end stop used for locating the test piece in the supports shall be retracted in order that it does not impede the movement of the test piece during the test. NOTE: Clea ra nce of 13 mm should be used to ensure the specimen does not interfere with the striker. 4.6 Centre of percussion The distance of the centre of percussion from the axis of rotation shall be equal to the length of the pendulum, ±1 percent.L i c e n s e d t o C o l i n M . L o r r i m a r M T S M e t o n 22 M a y 2007. 1 u s e r p e r s o n a l u s e r l i c e n c e o n l y . S t o r a g e , d i s t r i b u t i o n o r u s e o n n e t w o r k p r o h i b i t e d .AS 1544.2—2003 8Standards Australia .au4.7 Striking velocityThe striking velocity shall be 4.5 to 7.0 m/s. In the case of a dispute 5 to 5.5 m/s shall beused.4.8 Indicating equipmentFor scales graduated in joules, the scale intervals shall not exceed 1 J for machines having astriking energy of 160 J or less, or 2 J for machines having a striking energy greater than160 J.DIMENSIONS IN MILLIMETRES FIGURE 1 ARRANGEMENT OF SUPPORTS, TEST PIECE AND STRIKER For scales graduated in other units, the scale intervals shall not exceed 1 percent of the maximum scale value. The thickness of the scale marks and the width of the tip of the pointer shall not exceed one fifth of the minimum scale spacing. The pointer should permit a reading free from parallax error. The length of the smallest scale mark should not be less than 2.5 mm. 4.9 Zero reading When the machine is operated normally but without a test piece in position, the reading indicated by the pointer is the zero reading. This reading shall not exceed ±0.5 percent of the nominal initial potential energy (see Paragraph A3.4 of Appendix A). 4.10 Friction losses Energy is absorbed by friction, including air resistance, bearing friction and friction of the pointer. The total losses by friction for one swing shall not exceed 0.5 percent of the initial potential energy (see Paragraph A3.5 of Appendix A).L i c e n s e d t o C o l i n M . L o r r i m a r M T S M e t o n 22 M a y 2007. 1 u s e r p e r s o n a l u s e r l i c e n c e o n l y . S t o r a g e , d i s t r i b u t i o n o r u s e o n n e t w o r k p r o h i b i t e d .巴巴客标准 免费下载9 AS 1544.2—20034.11 Initial potential energyThe initial potential energy shall not differ from the nominal value by more than ±1 percent. (See AS 1544.4 for the method of determining initial potential energy.) 4.12 Indicated absorbed energyThe error in indicated absorbed energy shall not exceed 3 percent of the energy corresponding to the indicated value, or 1 percent of the energy corresponding to the full scale, whichever is the greater. (See AS 1544.4 for the method for calibration of scales.) 5 TEST PIECE5.1 Sampling and preparationSamples for testing shall be selected in accordance with the requirements of the relevant product specification or code of practice, as applicable. Any significant metallurgical damage shall be removed by machining.All samples, specimens and test pieces shall be adequately identified as to their origin and location.5.2 Form of test piece 5.2.1 GeneralThe test piece, which shall be machined all over, shall be 55 mm long, and in the centre of the length of one face there shall be a V-notch of 45 degrees included angle, 2 mm depth and 0.25 mm root radius. The plane of symmetry of the notch shall be perpendicular to the longitudinal axis of the test piece (see Figures 2 and 3). 5.2.2 Standard test pieceThe standard test piece shall be of square cross-section, nominally 10 mm × 10 mm. 5.2.3 Subsidiary test piecesWhere a standard test piece cannot be obtained from the material, one of the subsidiary test pieces of rectangular cross-section and having the notch cut in one of the narrower faces, shall be used.NOTE: No general correlation has been established between results obtained from test pieces of different sizes, and results should be compared only on test pieces of identical dimensions.5.2.4 Dimension and tolerances of test piecesThe standard test piece and subsidiary test pieces shall have dimensions and tolerances in accordance with Table 1.L i c e n s e d t o C o l i n M . L o r r i m a r M T S M e t o n 22 M a y 2007. 1 u s e r p e r s o n a l u s e r l i c e n c e o n l y . S t o r a g e , d i s t r i b u t i o n o r u s e o n n e t w o r k p r o h i b i t e d .AS 1544.2—2003 10Standards Australia.auTABLE 1DIMENSIONS AND TOLERANCES OFTEST PIECESCharacteristic Nominal dimension MachiningtoleranceLength 55 mm±0.60 mmThicknessStandard test pieceSubsidiary test piece Subsidiary test piece Subsidiary test piece Subsidiary test piece10 mm 7.5 mm 6.7 mm 5 mm 2.5 mm±0.11 mm ±0.11 mm ±0.06 mm ±0.06 mm ±0.06 mm Width10 mm ±0.06 mm Root radius of notch 0.25 mm±0.025 mm Depth below notch8 mm ±0.06 mm Distance of centre of notch from one end of test piece 27.5 mm±0.42 mmAngle between plane of symmetry of notch and longitudinal axis of test piece 90° ±2° Angle of notch45° ±2° Angle between adjacent longitudinal faces of test piece90°±20°NOTE: Some product Standards may require a full material thickness test pieceDIMENSIONS IN MILLIMETRESFIGURE 2 STANDARD AND SUBSIDIARY TEST PIECES5.3 Notch preparationUnless a particular method is specified in the relevant product specification or code of practice, the notch may be cut by any machining method providing a smooth profile, as specified, is produced (see Figure 3).L i c e n s e d t o C o l i n M . L o r r i m a r M T S M e t o n 22 M a y 2007. 1 u s e r p e r s o n a l u s e r l i c e n c e o n l y . S t o r a g e , d i s t r i b u t i o n o r u s e o n n e t w o r k p r o h i b i t e d .11 AS 1544.2—2003NOTE: The impact properties of some materials may be affected by the notch preparation methodemployed; for exa mple, to a void the effect of stra in a geing in the notch region of low ca rbon steel, it is advisable to notch the test pieces the same day as they are tested and to form the notch using light cuts with a finishing cut of 0.03 mm to 0.05 mm.FIGURE 3 ENLARGED VIEW OF NOTCHIN TEST PIECE6 PROCEDURE6.1 Conditioning of test piece 6.1.1 GeneralThose portions of any appliance that make contact with the test piece during transfer to the machine shall be at the same temperature as the test piece. This requirement also applies to any device which uses the notch for centring.NOTE: The mechanism e.g. tongs, which are used to handle the specimens in the bath should be pla ced in the ba th for a minimum of 5 minutes before testing a nd returned to the ba th between tests.6.1.2 Tests at ambient temperatureThe ambient test temperature shall be recorded immediately before testing. In the event of dispute, the test temperature shall be 20 ±2°C.6.1.3 Tests at subzero temperatures or temperatures up to 200°CWhere the impact properties are to be determined at subzero temperatures, or at temperatures above ambient up to 200°C, the test piece shall be brought to the specified test temperature by immersion in a continuously agitated liquid bath or gaseous medium. The period of immersion of the test piece and appliance in a bath at the test appliance in a bath at the test temperature shall not be less than 5 minutes, and in the case of a gaseous medium, not less than 30 minutes.NOTE: The test pieces should be suspended a minimum of 25 mm from the bottom of the immersion tank.The test piece shall be broken within 5 s from the time of removal from the conditioning medium.NOTE: For tests a t tempera tures a bove 20°C, a n oil ba th is preferred to a wa ter ba th for conditioning.6.1.4 Tests at temperatures above 200°CFor tests at temperatures above 200°C, the test piece shall be heated in a suitable oven or furnace at the specified test temperature for 30 min, or in a suitable liquid bath for a sufficient time to permit the test piece to reach the test temperature.L i c e n s e d t o C o l i n M . L o r r i m a r M T S M e t o n 22 M a y 2007. 1 u s e r p e r s o n a l u s e r l i c e n c e o n l y . S t o r a g e , d i s t r i b u t i o n o r u s e o n n e t w o r k p r o h i b i t e d .AS 1544.2—2003 12Standards Australia .auThe test piece shall be broken within 5 s from the time of removal from the oven, furnace or bath.NOTE: The use of a salt bath furnace may be found to be unsatisfactory, as encrustations of salt may prevent proper seating of the test piece.6.1.5 Accuracy of conditioning temperatureUnless otherwise specified in the product specification or code of practice, the temperature of the conditioning medium shall conform to Table 2.TABLE 2TEMPERATURE OF CONDITIONING MEDIUMSpecified test temperatureTolerance on temperature ofconditioning medium°C°C Below −60−60 to 100 Above 100 to 200±2 ±1 ±26.2 Location of test pieceThe test piece shall lie with the notched face squarely against the reaction supports so that it will be struck on the face opposite the notch (see Figure 1).The plane of symmetry of the notch shall be within 0.5 mm of the plane of swing of the striking edge. If an end stop is used to position the test piece, the form of the stop shall be such that it does not impede the movement of the test piece.The use of an end stop shall make it necessary to machine the test piece length to tolerances closer than those given in the Table 1. 6.3 Operation of the testing machineThe machine shall be operated in accordance with the manufacturer's instructions. Attention shall be given to the following:(a) Safety, i.e. observing the correct sequence of operations, and taking precautionsagainst possible accident (see Warning). (b) Correct location of the test piece. (c) Setting the pointer.(d) Releasing the pendulum without imparting vibration to it. (e) Reading the scale, avoiding parallax errors (see Note).(f)Clearance. If there is any evidence of jamming, i.e. interference between the broken halves of the test piece and the pendulum, tests shall be discontinued until the cause has been ascertained and the fault rectified (see Paragraph A3.2 of Appendix A).NOTE: If the sca le rea ding is ta ken a fter the pendulum ha s been reset a t its initia l relea se position, ca re should be ta ken to ensure tha t the a ction of a rresting a nd resetting the pendulum does not cause the scale reading to change.L i c e n s e d t o C o l i n M . L o r r i m a r M T S M e t o n 22 M a y 2007. 1 u s e r p e r s o n a l u s e r l i c e n c e o n l y . S t o r a g e , d i s t r i b u t i o n o r u s e o n n e t w o r k p r o h i b i t e d .13 AS 1544.2—2003WARNING: IT IS RECOMMENDED THAT A SAFETY SCREEN BEPROVIDED TO ARREST ANY BROKEN TEST PIECE HALVES EJECTED DURING THE TEST.6.4 Record of test resultsA record of test results shall be made and shall include the information required in Appendix B. 7 REPORTWhere a report of the test is required, it shall include the following: (a)The type of test, i.e. Charpy V-notch. If a subsidiary test piece is used, the thickness shall be stated.(b) Reference to this Australian Standard, i.e. AS 1544.2, and to a relevant productspecification or code of practice, where applicable.(c) The nominal striking energy of the machine, in joules. (d) The identification of the test piece.(e)The indicated absorbed energy, in joules, and if the number is higher than 80 percent of the machine capacity.NOTE: If the test piece a bsorbs the full energy of the ma chine without pa ssing through the supports, the absorbed energy shall be reported as above 80% of the machine capacity.(f) The test temperature, in degrees Celsius (see Clause 6.1). (g) The fracture surface appearance, if required (see AS 1544.5). (h) Date of report.(i)Compliance or otherwise with specified requirements, if applicable.NOTE: When the sta nda rd test piece is used, it is permissible to use symbols in the presentation of test results. Example:C 300 V: χJ at y °C whereC ...................................................................................indicates the type of test (Charpy) 300............................................indicates the striking energy of the machine used in joules V..............................................................................................indicates the type of notch χ....................................................................is the value of the indicated absorbed energy y.....................................................................................................is the test temperature.L i c e n s e d t o C o l i n M . L o r r i m a r M T S M e t o n 22 M a y 2007. 1 u s e r p e r s o n a l u s e r l i c e n c e o n l y . S t o r a g e , d i s t r i b u t i o n o r u s e o n n e t w o r k p r o h i b i t e d .。
CGA 标准(中文)
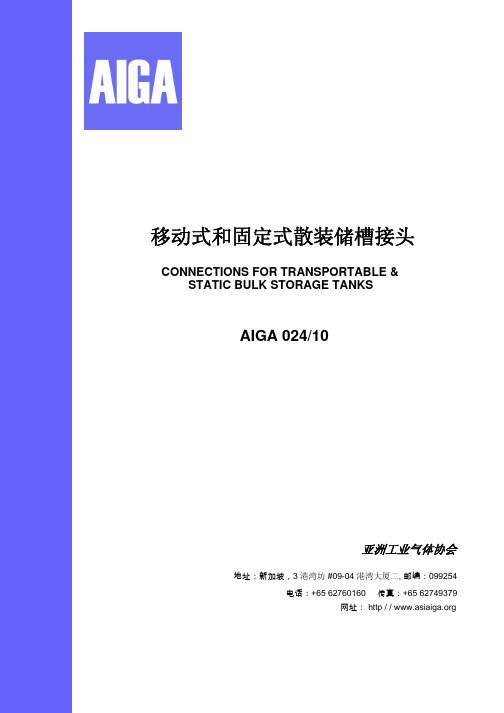
尽管 AIGA 建议其成员参考或使用其出版物,但是其成员或第三方对其出版物进行的这种参考或使用完全是自愿的并且不具 有约束力。
AIGA 或其成员对于参考或使用 AIGA 的出版物中包含的信息或建议的相关结果不作任何保证,并且对于这种参考或使用概 不承担任何责任。
任何人员或实体(其中包括 AIGA 成员)对 AIGA 的出版物中包含的任何信息或建议的执行或不执行、误解、正确或不正确 使用均不在 AIGA 的控制范围内,AIGA 明确拒绝承担与此相关的任何责任。
EU44-2014ANNEXXI质量和尺寸

44/2014 Annex XI 质量和尺寸——与93/93/EEC有差异1.目的:1.1. 本附录制定了L类摩托车质量和尺寸的相关要求。
2.车辆质量要求及测试规范2.1. 在申请车型质量及尺寸EU型式认证时,制造商应提供认证主管部门每一种车型(无论是哪种完整程度的车辆)所有版本以下质量的详细资料。
2.1.1.行驶质量,参考EU168/2013-ARTICLE 5;2.1.2. 实际质量(行驶质量+75kg+可选的装备及可选的燃料储存);2.1.3. 技术容许的最大满载质量;2.1.4. 技术容许的最大满载质量在各轴上的分配;2.1.5. 如果适用,技术容许的最大牵引质量;2.1.6. 如果适用,连接点的技术容许的最大质量算做连接装置的技术要求(安装在车上或者在某些情况下可以安装在车上);2.1.7. 如果适用,可选配置的质量;2.1.8. 如果适用,上部结构的质量;2.1.9. 如果适用,推进电池的重量;2.2. 当确定第2点的质量时,为了减少机械故障(特别是会造成材料疲劳)及避免对路面的损坏,制造商应该考虑到工程学目前的技术知识。
2.3. 当确定第2点的质量时,制造商考虑到车辆的最大设计车速。
车辆装有限速装置时,最高设计车速是指限速装置容许的实际车速。
2.4. 当确定第2点的质量时,制造商不能对车辆的使用加以限制,除非关系到轮胎的最高速度等级。
2.5. 非完整车辆(包含仓式底盘车辆)需要进一步的完善,制造商需要向下一步制造商提供详细信息以便于本法规要求被进一步满足。
为了首次投影点,制造商需规定总载时的重心位置。
2.6. 当可选的装备影响了车辆的尺寸和重量,制造商应提供可选装备的位置、质量、重心相对于轴的相对位置给技术服务机构。
2.7. 如果认证主管部门及技术服务机构认为有必要,可要求制造商提供一辆典型车辆进行检查。
2.8. L5e-B, L6e-BU和L7e-CU专门用于载货和用于装配可交换的上部结构时,上部结构应该是装载质量的一部分,应该满足以下的附加条件:2.8.1. 如果上部结构能够很容易地从带驾驶室的底盘上移除,则认为是可交换的。
人类胰岛素信号通路基因表达分析
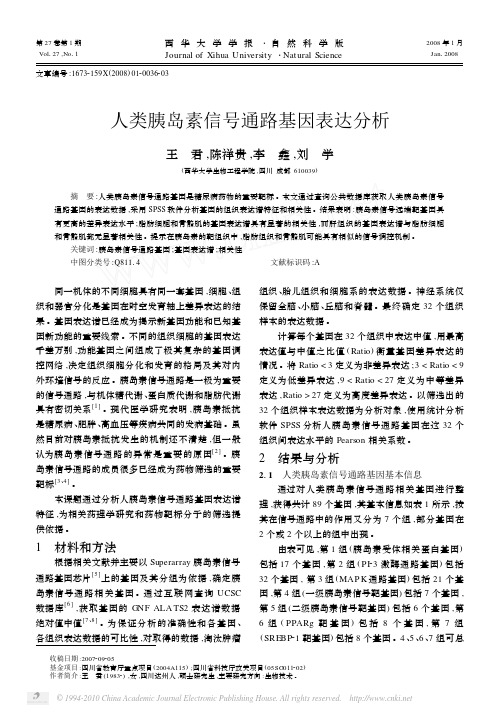
0111 0108
\ 0105 20106 20107
0164 3 3 0175 3 3
0105 \
20104 0121
20105 0102 20106 20104
\ 20102
0136 3 0124 20107 0121 20102
\
胰岛 素受 体相 关蛋 白基 因
\ 0176 3 0147 0108 0144 0109
\
MA2
PK 通路 基因
\ 0175 3 0104 0134 0124 0180 3 3
0175 3 \
0115 0107 0111 0161
0104 0115
\ 20120 20107 20121
0134 0107 20120
\ 20115 0138
0124 0180 3 3 0111 0161 20107 20121 20115 0138
摘 要 :人类胰岛素信号通路基因是糖尿病药物的重要靶标 。本文通过查询公共数据库获取人类胰岛素信号
通路基因的表达数据 ,采用 SPSS 软件分析基因的组织表达谱特征和相关性 。结果表明 :胰岛素信号远端靶基因具
有更高的差异表达水平 ;脂肪细胞和骨骼肌的基因表达谱具有显著的相关性 ,而肝组织的基因表达谱与脂肪细胞
FOS NM HRAS NM LDL R NM MAP2 K1 NM MAP2 K2 NM MAP4 K2 NM MAP K1 NM M KN K1 NM NOS2A NM RAF1 NM RPS6 KA1 NM RRAS NM RRAS2 NM SOS1 NM SOS2 NM CEBPA NM CEBPB NM GCG NM J UN NM L EP NM PRL NM CSN2 NM NPY NM ORM1 NM
- 1、下载文档前请自行甄别文档内容的完整性,平台不提供额外的编辑、内容补充、找答案等附加服务。
- 2、"仅部分预览"的文档,不可在线预览部分如存在完整性等问题,可反馈申请退款(可完整预览的文档不适用该条件!)。
- 3、如文档侵犯您的权益,请联系客服反馈,我们会尽快为您处理(人工客服工作时间:9:00-18:30)。
浙江省2011年4月高等教育自学考试
采购与仓储管理试题
课程代码:07008
一、单项选择题(本大题共20小题,每小题1分,共20分)
在每小题列出的四个备选项中只有一个是符合题目要求的,请将其代码填写在题后的括号内。
错选、多选或未选均无分。
1.现代易货贸易基本上有两种形式:双边贸易和( )
A.多边贸易
B.单边贸易
C.三边贸易
D.国际贸易
2.合同制造商是外包的载体,对合同制造商的_______是外包管理中最关键的一环。
( )
A.跟进
B.管理
C.评估
D.考核
3._______组织结构适用于采购规模大、品种多、需求复杂及市场多变的企业采购。
( )
A.职能制
B.直线职能制
C.矩阵制
D.采购事业部
4._______可以是采购人员对其经办的项目非常专精,比较能够发挥“熟能生巧”以及“触类旁通”的效果。
( )
A.采购区域部门化
B.采购产品部门化
C.采购价值部门化
D.采购过程部门化
5._______是定期评估首先要做的工作。
( )
A.部门绩效评估
B.采购角色绩效评估
C.供应商绩效评估
D.制定物料供应评估计划
6.建立供应商伙伴关系的先决条件是( )
A.要得到公司高层领导的重视和支持
B.确定供应商的大致范围
C.双方代表应签字盖章
D.明确对供应商的考核指标
7.海尔集团本部采购A材料的招标须知中注明,青岛本地的供应商优先考虑。
这符合采购原则中的_______原则。
( )
A.适量
B.适质
C.适时
D.适地
8.《合同法》第170条规定,卖方有权确定试用期限,如果买方在试用期满后,对是否购买
07008# 采购与仓储管理试题第1页(共5页)
试用物未作明确表示的,则( )
A.推定其不同意购买,卖方无权请求支付货款
B.应由双方商定,再行解决
C.应报请有关主管部门处理
D.推定其同意购买,卖方有权请求支付货款
9._______是合同双方当事人的权利义务共同指向的对象。
( )
A.合同条款
B.合同标的
C.特别条款
D.合同履行的时间
10.投标文件的有效期为从开标之日起_______内。
( )
A.30天
B.45天
C.60天
D.90天
11.推行配套生产和_______主要是制造业用于实现零库存的方式。
( )
A.分包销售
B.自行销售
C.自行采购
D.外包采购
12.如果从两个企业购买同一种物料,那么在使用物料编码时要注意( )
A.同一种物料采用统一编码
B.在物料本身的编码前面加供应商代码以示区别
C.对两个企业的物料重新进行编码
D.在物料本身的编码后面加供应商代码以示区别
13._______方式是日本精工藤泽工厂首先采用的,将生产厂各工具室分散管理的材料或零件统一集中到仓库中,设立了日本精工名店街,使它成为材料供应中心,并使工厂的库存为零。
( )
A.自来水仓库
B.供应商专柜
C.寄售
D.自动销售机
14.多级库存控制的目标是( )
A.维持库存费用最小
B.交易成本最低
C.缺货损失最低
D.优化总库存成本
15.不同建筑材料的遮阳效果不同,_______遮阳效果最佳。
( )
A.石棉瓦结构
B.混凝土结构
C.木结构
D.塑料布
07008# 采购与仓储管理试题第2页(共5页)
16.目前普遍采用的仓储管理组织形式为( )
A.直线式
B.直线—职能式
C.水平结构
D.矩阵制
17.每个库房配备的灭火器不得少于( )
A.5个
B.4个
C.3个
D.2个
18.12m以上的仓库属于( )
A.低层自动化仓库
B.中层自动化仓库
C.高层自动化仓库
D.大型仓库
19._______是立体仓库的主要特征。
( )
A.建筑物
B.堆垛起重机
C.计算机系统
D.高层货架
20.特别适用于散货和大型、特大型商品的装卸设备是( )
A.电梯
B.行车、吊车
C.叉车
D.输送机
二、多项选择题(本大题共5小题,每小题2分,共10分)
在每小题列出的五个备选项中至少有两个是符合题目要求的,请将其代码填写在题后的括号内。
错选、多选、少选或未选均无分。
1.大数点收应注意的事项有( )
A.件数不符
B.包装异状
C.物资串库
D.物资异状损失
E.单证不全
2.建立与供应商战略伙伴关系的积极意义在于( )
A.有利于企业提高生产效率
B.有利于提高经济效益
C.有利于降低交易成本
D.有利于随时终止合作
E.有利于新产品的开发
3.供应链的库存成本包括( )
A.维持库存费用
B.交易成本
C.缺货损失成本
D.生产成本
E.销售人员工资
07008# 采购与仓储管理试题第3页(共5页)
4.VMI管理系统的原则主要有( )
A.合作性原则
B.互惠原则
C.目标一致性原则
D.连续改进原则
E.框架协议
5.以下情况可以采用干粉灭火器灭火的是( )
A.电气设备着火
B.有机溶剂的初起火灾
C.易燃液体的初起火灾
D.已经高度灼热的物体
E.堆放木材的仓库着火
三、判断题(本大题共10小题,每小题2分,共20分)
判断下列各题,正确的在题后括号内打“√”,错的打“×”。
1.分离式立体仓库多数高度都在15m以上。
( )
2.物流条形码由14位数字构成。
( )
3.物资出库的复核检查可以由保管员自行复核,也可以由保管员相互复核。
( )
4.发展战略合作伙伴关系可以使双方互相信任,共担风险,共享信息。
( )
5.EOQ系统解决了独立需求物品的库存控制问题。
( )
6.政府采购就是由政府有关部门进行采购。
( )
7.行政赔偿只能由当事人单独提出。
( )
8.当事人就合同的内容相互往来的普通信函不属于书面合同形式。
( )
9.“80/20规则”是一种简单的对供应商进行分类的方法。
( )
10.到车站提货,应出示“领货凭证”,如无凭证,则货物不能提回。
( )
四、简答题(本大题共7小题,每小题5分,共35分)
1.简述自动化立体仓库的优点。
2.商品保管原则的具体化体现在哪些方面?
3.实施供应商管理库存策略的步骤有哪些?
4.制造企业是如何运作其电子采购系统的?
5.政府采购招标中若出现民事纠纷应如何解决?
6.采购控制制度涉及的内容有哪些?
7.采购人员应具备的基本素质有哪些?
07008# 采购与仓储管理试题第4页(共5页)
五、案例题(本大题共3小题,每小题5分,共15分)
德国某汽车公司JIT采购零配件实现零库存
德国某汽车公司首先根据所需采购的零配件在使用过程中的频率高低将所需采购的零配件分为高、中、低三大类,这三个部分所占比例依次为80%、15%、5%;其次根据所需采购零配件所含价值量高低将其分为高、中、低三个部分,三部分所占比例依次为80%、15%、5%;使用频率和价值含量都高的零配件就是需即时供应的零配件,目前该汽车公司所需采购的零配件中,这一比例为20%。
实际操作的基础条件首先是供方和需方的计算机联网,其二是将质量控制转变为质量生产保证,即供方要绝对保证其所提供的配件的质量。
具体操作如下:某种需即时供应的配件在前12个月,供方通过联网的计算机信息管理系统得到需方的需求量,这个需求量的准确性较差,假设在650至350之间,误差上下各30%;前3个月供方又从计算机信息管理系统中得到较准确的需求量,大至在550至450之间,上下相差各1%。
这批配件在供货的头两天开始生产,成品直接运到大众汽车公司的生产线上。
借助计算机的信息网络及质量生产,该汽车公司的供应商不仅为他的用户即时供应所需配件,而且根据逐渐得到的信息,提高了即时供应潜力。
据德国有关方面统计和分析,通过有效的即时供应,目前能使德国生产企业库存下降4%,降低运输成本15%。
请结合案例内容回答下列问题:
1.该汽车公司所用的JIT采购有何特点?
2.该汽车公司如何确定需即时供应的零配件?
3.该汽车公司进行实际操作必须具备哪些基础条件?
07008# 采购与仓储管理试题第5页(共5页)。