细纱工序质量控制要点
细纱工序质量管理

细纱工序质量管理袁志刚(河南豫北纺织有限责任公司)摘要:从当前细纱工序存在的弊端入手,从设备的维护与管理、优化纺纱工艺、重视运转管理等方面介绍了提高细纱工序质量管理的具体措施。
指出适宜的工作环境、好的设备状态、性能优异的纺专器材加上正确的上车工艺是细纱工序提高管理水平的重要环节,同时应加强操作工水平及责任心。
关键词:细纱质量;设备;工艺;操作;管理细纱生产是棉纺厂成纱的最后一道工序。
该工序的质量好坏、产量高低、消耗多少、劳动生产率和设备生产率水平,综合反映棉纺厂生产技术管理水平的优劣。
细纱工序质量管理是一项综合性很强的工作。
产品质量问题涉及到车间的各项管理工作。
质量管理应首先从原料、设备、工艺、操作和空调五大基础管理抓起。
1 加强设备和工艺管理1.1 设备的维护与修理1.1.1 周期管理国产细纱设备维修一般采用固定周期,大小修理周期为4 a和6个月,部分保全(校锭子)周期,根据生产状况和车速一般为3个月。
保养工作范围大、面积广、部件标准化、统一化要求高。
因设备一直处于运转状态,重点检修周期应适当缩短,应掌握在8 d~12 d,每天每人检修两台车。
轮班保养工作要抓紧,运转检修工要加强巡回检修、处理好停台工作,做到当班无空锭,生产无坏车,确保设备经常处于良好生产状态。
揩车的目的主要是防止牵伸、卷绕部件飞花阻塞及罗拉轴承内缺油,导致罗拉、胶圈阻力大造成抖动而影响产品质量,及时清除下胶圈积花保证胶圈正常灵活回转,揩车周期一般掌握在15 d以内。
维修计划的编排要注意间隔均匀,避免邻台干扰。
做到平、揩、检区域对口,分工协作,各负其责,相互督促,接交验收。
1.1.2 质量检查为了确保各项维修工作全面达到规定的质量标准,必须进行质量检查,查出问题要分析原因,及时处理,做好记录。
质量检查的内容应力求全面:除接交技术条件、完好技术条件和检修技术条件中规定的必查项目外,还应包括根据生产需要增加的部分机件磨损限度、安装公差以及与生产质量有关的其它项目。
细纱质量问题的原因分析及措施
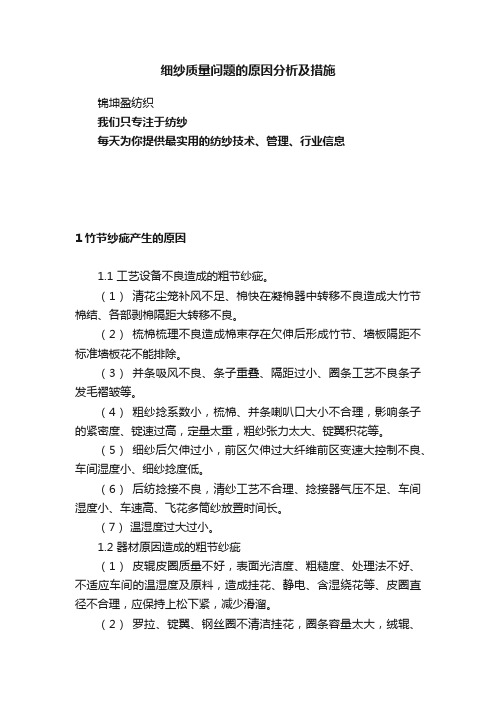
细纱质量问题的原因分析及措施锦坤盈纺织我们只专注于纺纱每天为你提供最实用的纺纱技术、管理、行业信息1竹节纱疵产生的原因1.1 工艺设备不良造成的粗节纱疵。
(1)清花尘笼补风不足、棉快在凝棉器中转移不良造成大竹节棉结、各部剥棉隔距大转移不良。
(2)梳棉梳理不良造成棉束存在欠伸后形成竹节、墙板隔距不标准墙板花不能排除。
(3)并条吸风不良、条子重叠、隔距过小、圈条工艺不良条子发毛褶皱等。
(4)粗纱捻系数小,梳棉、并条喇叭口大小不合理,影响条子的紧密度、锭速过高,定量太重,粗纱张力太大、锭翼积花等。
(5)细纱后欠伸过小,前区欠伸过大纤维前区变速大控制不良、车间湿度小、细纱捻度低。
(6)后纺捻接不良,清纱工艺不合理、捻接器气压不足、车间湿度小、车速高、飞花多筒纱放置时间长。
(7)温湿度过大过小。
1.2 器材原因造成的粗节纱疵(1)皮辊皮圈质量不好,表面光洁度、粗糙度、处理法不好、不适应车间的温湿度及原料,造成挂花、静电、含湿绕花等、皮圈直径不合理,应保持上松下紧,减少滑溜。
(2)罗拉、锭翼、钢丝圈不清洁挂花,圈条容量太大,绒辊、集合器、喇叭口位置不正。
(3)原料问题,涤棉、人棉短绒、浆块、束丝多。
(4)操作清洁不到位造成竹节纱疵。
2 出硬头的影响因素(1)隔距块规格影响中区摩擦力界的分布。
应结合粗纱定量、捻系数的大小、后区隔距及后区牵伸合理选择。
(2)粗纱的定量大,在同样的胶辊状态和后区牵伸倍数及粗纱捻系数情况下,相应细纱牵伸时的胶圈钳口握持力增加,以满足牵伸力握持力的匹配。
(3)胶辊的表面处理方式和胶辊胶圈的表面摩擦系数影响握持力和牵伸力的大小匹配。
不粘缠的情况下尽量加大胶辊的表面摩擦系数,控制胶圈滑溜的情况下适当减小胶圈的表面摩擦系数,以稳定中区牵伸力。
(4)温湿度过大,使须条中纤维间的摩擦阻力相应增加,导致须条中纤维抱合力增加,造成牵伸力大小波动而造成牵伸不稳定的现象。
(5)粗纱假捻器表面磨损,造成须条内纤维的抱合力差异而带来握持力的大小波动。
细纱质量检测与控制

3)在正常生产情况下,绝大多数绽
子在一落纱中没有断头,只在个别 锭子上出现重复断头,这是由于机 械状态不良而造成纺纱张力突变而 引起的。 (4)当锭速增加或卷装增大时,纺 纱张力也会随着增大,断头一般也 随着增加。
三、细纱断头原因分析
1、某类品种大面积突然断头增加的
原因 (1)原棉波动大 (2)温湿度控制不良 (3)工艺设计不当 (4)并粗齿轮缺陷
纺纱强力:纺纱段纱线所具有的强力。
纺纱张力:纺纱轴线方向所承受的力。
2. 降低断头的主攻方向: 控制、稳定纱 线张力,提高纺纱强力、降低强力不
7
二、成纱后断头的规律如下:
在正常条件下成纱前的断头较少,
生产中主要是成纱后断头。成纱后 断头的规律如下: (1)落纱中的断头分布,一般是小 纱最多、大纱次之、中纱最少。其 比例5:3:2 (2)成纱后断头较多的部位在纺纱 段(称为上部断头),在钢丝圈至 筒管间断头(称下部断头)出现较
2、整台细纱机断头增加的原因
(1)钢领衰退
(2)钢丝圈重量过重或过轻 (3)细纱机最大气圈高度未控制好
(4)吸棉装置真空度不够 (5)细纱牵伸齿轮、卷绕齿轮不良或啮合不 良
3、个别锭子断头增加的原因
(1)机械原因
(2)操作原因 (3)半制品或成纱质量不良
四、减少细纱断头的措施
3、 成纱线毛羽的因素:
(1)
纤维的物理性质: (2) 纺纱的密度和捻度 (3) 胶辊、胶圈的表面精度 (4) 细纱机的锭速 (5) 纺纱区的磨擦效应 (6) 主要纺纱器材不良影响:
1、合理配棉、优选工艺、提高成纱质量
2、严格设备维修、改善设备状态 3、加强运转管理、提高操作水平 4、加强温湿管理
细纱质量控制

2、牵伸力 牵伸力随着喂入纱条的不匀和摩擦力界分布的 不匀而波动,引起纤维变速点的不稳定而影响纱条 条干均匀度。 牵伸力大时,可适当减小粗纱捻系数,以降低 纤维间的紧密度,减小快速纤维从慢速纤维中抽出 时的阻力,降低牵伸力适当加大后区牵伸倍数使进 入前区须条的紧密度降低而达到降低牵伸力,使之 与握持力相适应 在加压偏轻时,可适当增加前罗拉的加压量, 使握持力与牵伸力相适应 在握持力与牵伸力相适应的前提下,适当加强 皮圈钳口压力对稳定牵伸力有一定效果。同时还必 须适当加强皮圈中部的摩擦力界以稳定皮圈中部的 纤维运动
3、皮辊:
• 皮辊表面要光洁、滑爽,具有足够的摩擦系数及 一定的吸放湿和抗静电性能,以减少绕花;丁氰 橡胶包覆物要具有适当的硬度,富有弹性,耐磨、 耐油、耐老化,丁腈橡胶分子结构要均匀,套差 要小,防止变形偏心,减少皮辊对细纱条干的影 响
• 皮辊圆整度要好。同一副皮辊上左右两只皮辊的 直径要一致,差异一般控制在0.05mm以内,磨 损、变形、偏心跳动等不允许超过公差范围,以 减少机械因素对牵伸不匀造成的影响,提高细纱 质量
重量不匀
乌斯特 细纱质量控制指标 条干不匀 结构不匀 捻度不匀 断头率 毛羽量 成行不良
纱线不匀
改善细纱不匀的措施
1、牵伸罗拉
• 罗拉直径应与所纺纤维的长度、罗拉加压 量、罗拉的轴承型式相适应,有足够的抗 弯和抗扭刚度;具有正确的沟槽齿形和符 合要求的表面光洁度,能充分握持又不损 伤纤维 • 减少因罗拉偏心、弯曲等机械因素引起的 纱条不匀;
• 将理想波普图与实际波普图比较,计算不 匀指数,了解纺纱设备的老化程度,确定 设备的更新与使用
毛羽
危害:如果毛羽过多会影响织造效率、布面风格 和质量、染色效果 产生:1、钢领和钢丝圈配套不合理 2、细纱捻系数偏低 3、细纱工序相对湿度过低,纱线发 毛 4、细纱锭子歪斜、隔纱板松动歪斜、 钢领板定位松动、导纱钩松动等会产生歪气圈
纺织厂细纱工序安全操作规程

纺织厂细纱工序安全操作规程
1、上班时要把头发束好,不能赤脚。
2、机台运转时,不能随意打开防护门。
3、细纱机开机时,一定要看清周围是否有无人。
(如维修的请有关人员把电制关掉)
4、清锭子回丝一定要刹车,以免碰伤手指。
5、机台转动时,清洁一定要用工具清。
6、清洁前罗拉花时,不能将手指伸得太入。
处理较严重的缠罗拉必须停机。
7、推单锭小车时,不能与流动风机碰撞,以免风管脱落伤人。
8、上粗纱时一定要挂稳才能放手,以免粗纱打伤人。
9、机台卸纱时一定要把粗纱抓稳。
10、挑纱脚时,一定要注意使用钩刀的方法。
11、任何情况下都不能挨傍机台,以免造成设备伤人事故。
12、纱箱不能堆放过高(不得超过五个)
13、物件按指定地方摆放好,不能乱摆乱放。
14、运纱工运纱时不能拉两车,运完一车再运一车(每车只能运6箱)。
15、落纱工推车一定要注意前方有无人,不能过急、不能用力过大,以免造成伤人事故的发生。
16、清洁吸风口时盖板一定要及时盖好。
17、听到机台有异响,闻到机台有异味,必须立即停机,并通知管理人员及保全工等。
18、绒棍车用完一定要把电制关好。
19、相邻两台风机不能并行。
20、上班后必须注意力集中,严格执行安全操作规程。
细纱工序质量控制要点

细纱工序质量控制要点探讨细纱工序提高纺纱质量的技术措施。
分析了影响细纱工序纺纱质量的主要因素,从细纱机的机械运行状态、牵伸专件器材的选用、上机工艺参数的优化、加捻卷绕器材的应用、运转操作管理及车间温湿度控制等方面提出了相应的解决方法。
指出:在实际生产中要根据纺纱品种的具体情况和用户的标准找准思路和对策,以保证纱线条干、粗节、细节、棉结等指标的长期稳定。
认为:细纱工序的精细化管理是成纱质量稳定的关键。
关键词细纱工序;专件;器材;工艺优化;运转操作管理;车间温湿度纺纱质量管理是一项综合性很强的工作,细纱工序是纺纱的关键工序,不仅影响后道工序的加工生产,也会影响面料的使用性能。
细纱工序的纺纱质量必须引起我们的重视。
我公司是拥有20 万纱锭的细号纱生产企业,细纱工序设备多、纺纱品种多,设备的运行状况对纺纱质量的影响较大。
成纱条干CV、CVb、细节、粗节、棉结、毛羽、强力等质量指标是衡量纺纱质量的重要指标,而影响这些指标的因素有很多,在实际生产管理中,我们要综合考虑,从根本上找到影响这些指标的原因,并采取相应的改善措施,以提高纺纱质量。
1 设备运行状态对纺纱质量的影响细纱机是提高纺纱质量和产量的主要设备,性能好坏、运行状态对纺纱质量影响较大。
设备运行状况是纺纱的基础,要强化设备管理,加强对设备状态的日常检查和维护工作,做好周期性的平车、揩车,设备人员要做好自己日常的包机和检查工作,保持细纱机运行状态良好,对细纱机的牵伸、加捻、卷绕过程重点进行关注,车头传动部分、齿轮啮合要良好,各种键、轴、轴承配合到位。
对细纱机进行周期性的状态检查、揩车维修能及时发现设备出现的问题,并对变形的机件及专件器材按周期更换或维修,能降低设备的故障率,以保证细纱机的正常运行,稳定纺纱质量。
由于FA1530 型细纱机机电一体化、自动化程度高,设备人员要多了解一些机电方面的知识,自动落纱部分要保持状态良好,加强日常的维修。
结合平车、揩车清除罗拉沟槽内所嵌的杂质和罗拉表面棉蜡、油渍等,确保前罗拉中弯和偏心不大于0.03mm ,避免造成成纱规律性条干不匀。
技术 细纱质量问题的原因分析及措施
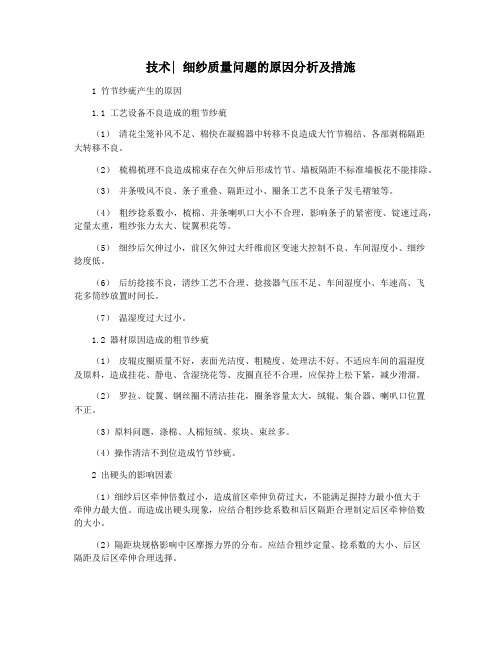
技术| 细纱质量问题的原因分析及措施1 竹节纱疵产生的原因1.1 工艺设备不良造成的粗节纱疵(1)清花尘笼补风不足、棉快在凝棉器中转移不良造成大竹节棉结、各部剥棉隔距大转移不良。
(2)梳棉梳理不良造成棉束存在欠伸后形成竹节、墙板隔距不标准墙板花不能排除。
(3)并条吸风不良、条子重叠、隔距过小、圈条工艺不良条子发毛褶皱等。
(4)粗纱捻系数小,梳棉、并条喇叭口大小不合理,影响条子的紧密度、锭速过高,定量太重,粗纱张力太大、锭翼积花等。
(5)细纱后欠伸过小,前区欠伸过大纤维前区变速大控制不良、车间湿度小、细纱捻度低。
(6)后纺捻接不良,清纱工艺不合理、捻接器气压不足、车间湿度小、车速高、飞花多筒纱放置时间长。
(7)温湿度过大过小。
1.2 器材原因造成的粗节纱疵(1)皮辊皮圈质量不好,表面光洁度、粗糙度、处理法不好、不适应车间的温湿度及原料,造成挂花、静电、含湿绕花等、皮圈直径不合理,应保持上松下紧,减少滑溜。
(2)罗拉、锭翼、钢丝圈不清洁挂花,圈条容量太大,绒辊、集合器、喇叭口位置不正。
(3)原料问题,涤棉、人棉短绒、浆块、束丝多。
(4)操作清洁不到位造成竹节纱疵。
2 出硬头的影响因素(1)细纱后区牵伸倍数过小,造成前区牵伸负荷过大,不能满足握持力最小值大于牵伸力最大值。
而造成出硬头现象,应结合粗纱捻系数和后区隔距合理制定后区牵伸倍数的大小。
(2)隔距块规格影响中区摩擦力界的分布。
应结合粗纱定量、捻系数的大小、后区隔距及后区牵伸合理选择。
(3)粗纱的定量大,在同样的胶辊状态和后区牵伸倍数及粗纱捻系数情况下,相应细纱牵伸时的胶圈钳口握持力增加,以满足牵伸力握持力的匹配。
(4)胶辊的表面处理方式和胶辊胶圈的表面摩擦系数影响握持力和牵伸力的大小匹配。
不粘缠的情况下尽量加大胶辊的表面摩擦系数,控制胶圈滑溜的情况下适当减小胶圈的表面摩擦系数,以稳定中区牵伸力。
(5)温湿度过大,使须条中纤维间的摩擦阻力相应增加,导致须条中纤维抱合力增加,造成牵伸力大小波动而造成牵伸不稳定的现象。
学习控制细纱质量、降低细纱不匀,看这一篇就够了!
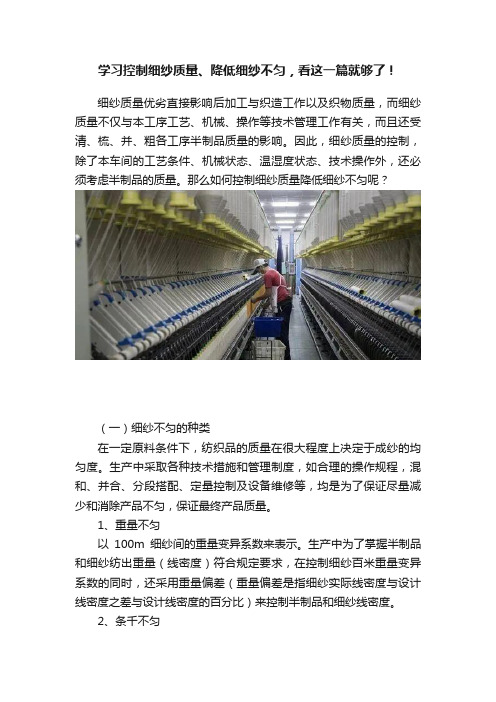
学习控制细纱质量、降低细纱不匀,看这一篇就够了!细纱质量优劣直接影响后加工与织造工作以及织物质量,而细纱质量不仅与本工序工艺、机械、操作等技术管理工作有关,而且还受清、梳、并、粗各工序半制品质量的影响。
因此,细纱质量的控制,除了本车间的工艺条件、机械状态、温湿度状态、技术操作外,还必须考虑半制品的质量。
那么如何控制细纱质量降低细纱不匀呢?(一)细纱不匀的种类在一定原料条件下,纺织品的质量在很大程度上决定于成纱的均匀度。
生产中采取各种技术措施和管理制度,如合理的操作规程,混和、并合、分段搭配、定量控制及设备维修等,均是为了保证尽量减少和消除产品不匀,保证最终产品质量。
1、重量不匀以100m细纱间的重量变异系数来表示。
生产中为了掌握半制品和细纱纺出重量(线密度)符合规定要求,在控制细纱百米重量变异系数的同时,还采用重量偏差(重量偏差是指细纱实际线密度与设计线密度之差与设计线密度的百分比)来控制半制品和细纱线密度。
2、条千不匀细纱的条干不匀代表细纱短片段粗细差异程度。
细纱按规定绕在黑板上与标准样照对比观测十块黑板所得的结果,即代表细纱短片段的条干质量;或用条干均匀度试验仪测出条干不匀率,简称条干CV值。
3、结构不匀细纱结构上的差异称为结构不匀。
如细纱横截面或纵向一定区域内纤维的混和不匀、批与批之间原纱色调不一以及由于条干不匀而引起的捻度不匀等,都属于细纱结构不匀。
细纱的重量不匀或条干不匀,当用仪器测试时,常表现一种波动形态,具有一定的波长和波幅。
当产品的不匀波形接近周期性波动时,通常称周期性不匀。
如由于罗拉或皮辊偏心、齿轮啮合不良所形成的不匀,其波形表现为周期性的波动,且具有相近的波长和波幅。
周期性的不匀在成纱制品中若波形较短,在数十毫米以内的不匀常影响产品的条干均匀度;若波形较长,如几十米或更长片段,这种不匀影响产品的重量不匀率。
由随机性或偶然性因素所形成的不匀波形,常没有明显规律,这种不匀称非周期性不匀。
细纱工序安全操作规程
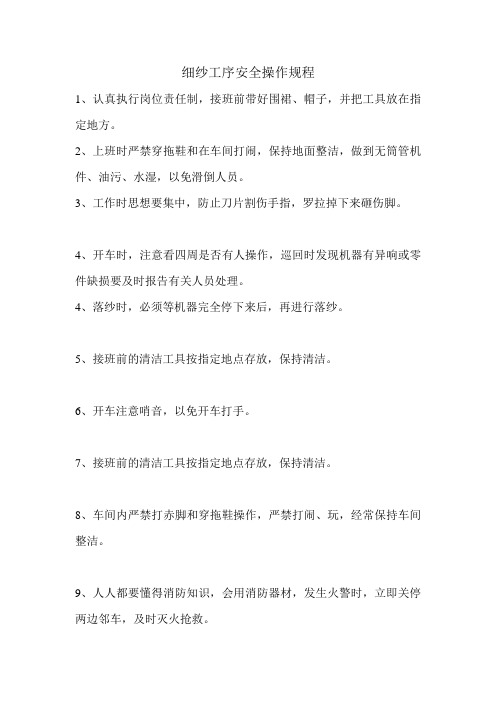
细纱工序安全操作规程
1、认真执行岗位责任制,接班前带好围裙、帽子,并把工具放在指定地方。
2、上班时严禁穿拖鞋和在车间打闹,保持地面整洁,做到无筒管机件、油污、水湿,以免滑倒人员。
3、工作时思想要集中,防止刀片割伤手指,罗拉掉下来砸伤脚。
4、开车时,注意看四周是否有人操作,巡回时发现机器有异响或零件缺损要及时报告有关人员处理。
4、落纱时,必须等机器完全停下来后,再进行落纱。
5、接班前的清洁工具按指定地点存放,保持清洁。
6、开车注意哨音,以免开车打手。
7、接班前的清洁工具按指定地点存放,保持清洁。
8、车间内严禁打赤脚和穿拖鞋操作,严禁打闹、玩,经常保持车间整洁。
9、人人都要懂得消防知识,会用消防器材,发生火警时,立即关停两边邻车,及时灭火抢救。
深度分析如何控制细纱质量降低细纱不匀

深度分析如何控制细纱质量降低细纱不匀细纱是目前纺织品市场上一种非常重要的原材料,它不仅应用于纺织品、服装等领域,还用于医疗卫生、建筑、汽车等各个行业。
然而,由于细纱本身的特殊性质,其制作过程中很容易出现不匀的现象,这不仅影响到纱线的质量,更会对下游产品的品质产生很大影响。
因此,如何控制细纱质量并降低细纱不匀已成为纺纱生产中的一个重要课题。
一、分析细纱质量与不匀的原因在制作细纱时,出现不匀现象的原因主要有以下几个方面:1.纤维不均匀纤维是制作细纱的原材料,如果纤维本身就存在一定的不均匀性,那么在制作细纱的过程中就很难保证纱线的均匀度。
例如,在制作棉纱时,由于棉质纤维可以从不同的地区采集而来,其颜色、长度和粗细等方面的差异就很大,如果对这些纤维不进行组合,那么细纱的均匀度就会受到影响。
2.纺纱工艺的问题另外,细纱的不匀还与纺纱工艺的水平有很大关系。
纺纱工艺中使用的设备和机械很可能存在生产制造方面的差异,这些差异包括设备的型号、大小、质量、维护情况等等,这些都会对细纱的质量和均匀度产生影响。
3.质量控制的不严格还有一种可能是因为生产厂家对细纱的质量把控不够严格,或者是因为规定不严格、执行不力等原因导致细纱的不匀。
二、如何控制细纱质量降低不匀1.采用质量最优的原料为了避免纤维本身的不均匀性对细纱的影响,我们需要选择质量最优的纤维,这样能够增加细纱的均匀度。
同时,还需要注意不同纤维种类之间的组合,这样也能够降低纱线不匀的可能性。
2.加强纺纱工艺面对工艺的不同问题,我们可以尝试加强纺纱工艺的管理和规范,包括对设备的维护保养、质量的检测和控制等方面的严格管理。
这样可以通过调整喷气力、旋转速度等因素,使细纱质量得到有效的提升。
3.完善质量控制标准为了确保细纱能够达到质量要求,我们可以逐步完善质量控制标准,规范生产流程,做到质量口径统一,依据科学的质量管理理念进行精确的质量控制,从而达到降低细纱不匀的目的。
三、结语细纱是目前市面上非常重要的纺织品原材料,其制作过程中很容易出现不匀的现象。
细纱工工作总结:质量管理,打造高品质产品

细纱工工作总结:质量管理,打造高品质产品2023年,细纱工作将依然是一个需要高度关注细节和质量管理的行业。
作为一名细纱工作者,我深刻认识到,只有通过不断优化流程和提高质量,才能持续提升企业竞争力,打造高品质产品。
下面,我将结合自己的经验和体会,对质量管理和打造高品质产品进行总结。
一、质量管理1. 强化原材料检测与入库管理一个高品质细纱的基础就是优质原材料的保障。
因此,在入库之前应该进行严格的检测,防止次品材料进入生产流程。
同时,对于每一批原材料,都应该有合格的检测报告,并严格按照规定存储、标识和分类管理,确保各类原材料的使用安全和可溯源性。
2. 完善生产过程控制环节质量管理的另一个重点就是生产过程的控制。
在生产的各个环节都要进行质量把控。
从原材料转变为成品的整个过程,要严格控制每个环节的标准和流程,确保产品符合质量标准。
同时,要加强生产工人的培训,让他们确保每个工序的标准化操作,提高质量稳定性。
3. 加强产品检验与成品发货前检测生产完成后,对于每一批次的产品都必须进行严格的检验,确保没有任何质量问题。
尤其是对于颜色、大小、线密度等关键指标的检测,必须通过专业仪器进行精准测试。
只有检验通过的产品才能发货,避免因出现质量问题而造成的不必要损失和影响。
二、打造高品质产品1. 根据客户需求和市场趋势进行产品设计和研发市场需求和客户口碑是我们设计研发的原动力,因此,我们应该紧密关注市场趋势和客户需求,进行不断产品创新和研发。
要以客户的喜好和需求为出发点,打造更具竞争力的产品。
2. 优化生产流程降低人工成本生产过程是直接关系到产品质量的基础,因此必须通过不断优化流程降低人工成本,提高生产效率。
减少无谓的浪费和不必要的环节,从而提升生产效率和质量稳定性,提高企业的竞争力。
3. 提高产品包装和运输的安全性产品的包装和运输环节也同样重要。
要从包装材料的选择、包装形式和包装标志等方面入手,加强包装规范和标准化。
并加强货物的追踪和安全性检测,确保客户在收到产品后,能够完好无损地使用。
细纱现场质量把关必须要做的24项工作!

细纱现场质量把关必须要做的24项工作!1. 皮辊表面状态是否良好、规格是否符合要求、轴承运转是否正常、是否有返花现象。
有无三绕现象。
绕花后邻纱是否处理。
2. 皮圈是否良好、无损坏、无缺失。
无皮圈带花,不得有皮圈龟裂、有裂缝现象。
3. 气圈是否正常。
有无歪锭子、歪导纱钩。
4. 清洁装置状态是否良好,作用是否正常。
绒辊清洁、隔纱板处清洁、牵伸区清洁要按规定的工具与方法清洁,保证机台清洁。
5. 牵伸通道是否清洁、无挂花、无积花等,粗纱表面是否有附着粗纱头、飞花等。
6. 锭带运行是否正常。
有无打扭、跑上跑下、跳动等不良现象。
7. 风箱花是否执行清洁时间,换粗纱是否执行操作规程。
8. 导纱动程是否符合规定范围,是否有跑偏现象。
浮游区大小是否合适,皮辊进出位置是否得当,对皮辊歪斜,小铁辊缺油都要经常检查与防范。
9. 粗纱斜面是否清洁无粘花、有无毛粗纱,粗纱掉地要处理干净。
10. 标识是否相符。
11. 细纱管是否符合使用要求,卷绕成形是否正常。
12. 吸棉笛管状态、位置是否正常,有无堵塞。
防止吸棉风道漏风、勾挂现象,保证吸棉笛管吸风正常,笛管光洁不挂花、不堵塞。
13. 坏锭、差锭处理是否符合要求。
14. 毎落纱是否检查有煤灰纱等坏纱存在。
15. 细纱断头异常,机械空锭。
16. 皮圈张力钩松弛或过紧、张力钩内缠花皮圈起拱现象都要防止。
17. 牵伸部位清洁、粗纱斜面清洁和其他清洁情况。
18. 有无错支错管情况。
19. 钢丝圈挂花、钢丝圈清洁器积花。
20. 工艺上机情况。
21. 操作是否按规定操作法执行。
22. 保证粗纱良好供应,防止空粗纱。
23. 尽量保证粗纱包卷、细纱接头合乎标准。
24. 导纱杆生锈、有毛刺的看能否镀铬处理。
资料来源:网络整理。
纺纱质量控制

纺纱质量控制
纺纱质量控制是纺织行业中非常重要的环节,主要包括原料筛选、纺纱工艺控制、纺纱设备维护以及纺纱成品检验等方面。
1. 原料筛选:在纺纱过程中,原料的质量直接影响成品的质量。
因此,对纳入生产的原料进行严格的筛选,排除掉质量不符合要求的原料。
2. 纺纱工艺控制:纺纱过程中的工艺参数设置和控制,对于纺纱质量的稳定性和一致性起着关键的作用。
包括纺纱机的转速、张力控制、料位控制等。
3. 纺纱设备维护:纺纱设备的正常运转和良好状态,对于纺纱质量的控制也非常重要。
需要定期对纺纱设备进行维护保养,包括清洁、润滑和性能检查等。
4. 纺纱成品检验:对纺纱成品进行全面和细致的检验,确保成品的质量达到要求。
包括各项物理性能测试、外观检查和纺纱工艺参数检测等。
此外,纺纱过程中还需要加强技术人员的培训和交流,提高他们的纺纱技能水平和质量意识,以提高整体纺纱质量的稳定性和可控性。
提高细纱质量的有效途径

提高细纱质量的有效途径细纱是一种常用于纺织品制作的细薄纱线,其质量直接影响着最终产品的质量和性能。
为了提高细纱的质量,需要从多个方面进行改进和优化。
下面将介绍一些有效的途径来提高细纱的质量。
1.原材料选择:细纱的质量受到原材料的影响。
选择高质量的纺织原料,如优质的棉花、丝绸等,可以确保细纱的品质。
此外,还应注意原材料的纤维长度、纤维强度等指标,选择适合细纱生产的原材料。
2.纺纱工艺改进:纺纱是将纺织原料加工成细纱的过程,纺纱工艺的改进可以有效提高细纱的质量。
首先,应根据纤维的特性和产品要求确定合适的纺纱工艺参数,如纺纱机的转速、张力、卷绕方式等。
其次,采用先进的纺纱设备和技术,如自动控制系统、空气动力纺纱等,可以提高纺纱的效率和质量。
3.控制纺纱湿度:细纱的湿度对其质量有很大影响。
湿度过高或过低都会导致纤维的破损和断裂,影响细纱的均匀性和强度。
因此,在纺纱过程中要控制好湿度,保持适当的湿度水平,可以通过加湿或除湿等方式进行调节。
4.丝锭设备优化:丝锭是纺纱机上用于纺细纱的重要部件,其设计和优化对细纱质量具有重要影响。
应选择高质量的丝锭材料,采用先进的加工工艺,提高丝锭的精度和稳定性。
此外,在丝锭的设计中,还应考虑纤维的输送、拉伸和卷绕等因素,以提高细纱的均匀性和强度。
5.质量检测与控制:质量检测和控制是提高细纱质量的重要手段。
通过建立完善的质量检测体系,对细纱的各项指标进行监测和分析,及时发现问题并采取措施加以解决。
同时,还应加强对纺纱工艺参数和设备状态的监控,确保纺纱过程的稳定性和可控性。
提高细纱质量的有效途径包括选择优质的原材料、改进纺纱工艺、控制纺纱湿度、优化丝锭设备以及加强质量检测与控制等措施。
通过综合应用这些方法,可以提高细纱的品质和性能,满足市场需求,提升企业竞争力。
抓好并条工序的这几方面,降低细纱质量不匀率

抓好并条工序的这几方面,降低细纱质量不匀率并条工序是提高纤维伸直平行度,保证细纱正常牵伸,提高成纱强力的重要工序。
对细纱质量不匀率及形成长片段细节都有较大影响,需重点抓好以下几项技术措施:增加并合数对生条质量波动较大的品种,并条并合数可由6×8改为8×8。
提高并合效果,改善末并质量不匀率。
降低熟条质量CV值① 重视生条质量的控制;② 适当增加半熟条质量检验次数;③ 运转三班每班检验三次质量,以每次质量CV进行控制;④ 质量CV超标时及时进行追踪分析,分清是输入棉条质量差异偏高造成,还是胶辊或加压机构、断条或缺条自停机构、牵伸机构吸尘吸风太大并不稳定等缺陷所造成,要有针对性地采取措施;⑤ 温湿度控制稳定。
防止由并条工序不良因素造成细纱长细节纺出由并条经过粗纱约7.5倍牵伸,细纱约40倍牵伸共300倍总牵伸造成细纱长经节的缺陷在粗纱、细纱工序是无法解决的,因此,并条工序应在消灭长细节的前提下降低熟条条干CV。
这涉及工艺设计是否合理、牵伸元件与加压机构是否正常、运转管理与机台清整洁是否良好等。
合理配置牵伸工艺,提高纤维伸直度和平行度根据经验:头并后区牵伸为1.75倍,前区牵伸在3.5倍以内,末并后区牵伸为1.25倍左右,相应前区牵伸为6.5倍至7倍,使进入前区纤维数量增加由此牵伸力增加。
特别注意:前胶辊握持力是否大于牵伸力,防止因握持力的最小值大于或等于牵伸力的最大值的临界状态。
当机后输入棉条的质量或状态结构发生波动造成细纱产生长细节和长粗节纱疵时,可适当放大后区牵伸倍数或罗拉隔距,这是降低牵伸力的消极方法,有条件的可采用增加握持力的积极方法更加合理。
消除并条机械波并条工序的机械波,不一定会明显恶化细纱条干CV,但经各工序高倍牵伸后会形成长片段的粗细节。
如果在棉纱质量偏轻纱段又与条干不均的细节重叠将使棉纱强力下降出现强力弱环。
因此,一定要杜绝熟条发生机械波。
做好管理工作① 定期检校断条缺条自停机构的灵敏度,挡车工发现缺条灵敏度不良应及时维修;② 加强运转管理,提高挡车工操作水平,严禁搭条,防止棉要包卷不良、输入棉条交叉重叠,对输出轻条等疵品清除干净,保持机台整洁杜绝种花附入棉条;③ 每天或每班测全部机台熟条条干CV,对机械波和条干CV恶化机台应及时维修,对常发这类缺点的机件、工艺等问题应研究改进;④ 严禁挡车工用刀割伤胶辊、处理不当轧伤胶辊,专人定期检查胶辊与轴承的运行状态,运转挡车工定期可用防绕专用清洗剂擦除胶辊表面棉蜡熔化油污。
细纱质量检测与控制资料

❖ (1)机械原因 ❖ (2)操作原因 ❖ (3)半制品或成纱质量不良
四、减少细纱断头的措施
❖ 1、合理配棉、优选工艺、提高成纱质量 ❖ 2、严格设备维修、改善设备状态 ❖ 3、加强运转管理、提高操作水平 ❖ 4、加强温湿管理
五出硬头
❖ 出硬头:又称为吐硬头,是细纱车间常发性 问题之一,出硬头是指牵伸装置输出未能牵 伸开的须条,由此造成通道阻塞形成断头或 硬块、粗节等纱疵的一种问题。
❖(2)成纱后断头较多的部位在纺纱 段(称为上部断头),在钢丝圈至 筒管间断头(称下部断头)出现较
❖3)在正常生产情况下,绝大多数绽 子在一落纱中没有断头,只在个别 锭子上出现重复断头,这是由于机 械状态不良而造成纺纱张力突变而 引起的。
❖(4)当锭速增加或卷装增大时,纺 纱张力也会随着增大,断头一般也 随着增加。
❖ (2) 纤维的两端卷入纱条,中间伸出纱条 主体表面。
❖ (3) 纤维的中间卷入纱条,两端伸出纱条 主体表面。
❖ (4) 浮游纤维:附着于纱条表面的松散纤 维。
3、 成纱线毛羽的因素:
❖ (1) 纤维的物理性质: ❖ (2) 纺纱的密度和捻度 ❖ (3) 胶辊、胶圈的表面精度 ❖ (4) 细纱机的锭速 ❖ (5) 纺纱区的磨擦效应 ❖ (6) 主要纺纱器材不良影响:
细纱质量检测与控制 细纱断头
一、降低细纱断头率
(一)降低细纱断头的意义
1.成纱质量差
2.细纱产量低
3.劳动强度大
4.用棉量越大
2
(二)细纱断头分析 1、断头率指标
(1)表示方法:细纱千锭时的断头 数。
(2)指标:细纱断头数的部分标准 为:纯棉纱为50根(8tex以下70根); 涤棉(65/35)30根。
细纱工序中的质量管理

细纱工序中的质量管理摘要:介绍了细纱工序质量管理的内容和具体措施。
加强设备维修管理,选择牵伸元件,对纺纱质量较差的细纱机进行牵伸改造;采用软弹胶辊等纺专器材提升纺纱质量;优化纺纱工艺;加强运转操作管理和操作法创新;合理调节温湿度,做好煤灰纱的防治工作等,均能有效控制细纱质量。
关键词:细纱质量;设备;工艺;操作;空调细纱是棉纺厂生产成纱的最后一道工序。
该工序的质量好坏、产量高低、消耗多少、劳动生产率和设备生产率水平,是棉纺厂生产技术管理水平优劣的综合反映。
纺纱质量是决定企业生存和发展的关键。
细纱工序质量管理是一项综合性很强的管理工作。
产品质量问题的解决和提高,涉及到车间的各项管理工作。
技术管理中的原料、设备、工艺、操作、空调等五大基础管理首先是围绕质量管理而开展的。
1加强设备和工艺管理, 提高产品质量1.1设备的维护与修理1.1.1周期管理国产细纱设备维修一般采用固定周期,大小修理周期为4年和6个月,部分保全(校锭子)周期,根据生产状况和车速一般按三个月的周期。
保养工作范围大、面积广、部件标准化、统一化要求高。
因设备一直处于运转状态,重点检修周期应适当缩短,应掌握在8~12天,每天每人检修两台车。
轮班保养工作要抓紧,运转检修工要加强巡回检修、加油检查、处理停台工作,做到当班无空锭,生产无坏车,确保设备经常处于完好状态。
揩车周期的制订主要是防止牵伸、卷绕部件飞花阻塞及罗拉轴承内缺油,罗拉、胶圈阻力大造成抖动而影响产品质量,及时清除下胶圈积花保证皮圈正常灵活回转,一般掌握在15天以内。
维修计划的编排要注意间隔均匀,避免邻台干扰。
平、揩、检区域对口,工作中分工协作,各负其责,相互督促,便于接交验收。
1.1.2质量检查为了确保各项维修工作质量全面达到规定的标准,必须进行质量检查。
查出问题要分析原因,及时修复,做好记录。
质量检查的内容应力求全面。
除接交技术条件、完好技术条件和检修技术条件中规定的必查项目外,还应包括根据生产需要增加的部分机件磨损限度、安装公差以及与生产质量有关的其他项目。
提高细纱质量的有效途径

提高细纱质量的有效途径
提高细纱质量是纺织生产中的重要环节,它直接影响着织物的质量和性能。
在生产过程中,有一些有效的途径可以帮助提高细纱质量,从而得到更好的织物产品。
要注意纱线的选材。
选择高质量的原材料是保证细纱质量的基础。
优质的棉花、涤纶等纤维能够保证纱线的均匀性和强度,从而提高织物的质量。
此外,要注意纱线的纺制工艺,控制好纺纱机的转速和张力,避免出现纱头断裂或断裂等问题,确保纱线的质量稳定。
要加强纺纱工艺的监控和调整。
在纺纱过程中,要定期检查纺纱机的运行情况,及时发现并解决问题。
调整好纺纱机的参数,保持纺纱机的稳定性和一致性,避免出现纱线粗细不均匀、扭曲等问题。
此外,要根据不同纤维的特性和要求,合理选择纺纱工艺,保证纱线的质量符合要求。
要加强纱线的整理和处理。
纱线的整理包括浸润、拉伸、扭转等过程,这些过程对纱线的质量有着重要影响。
要控制好整理过程中的温度、湿度和张力等参数,确保纱线的均匀性和强度。
同时,要对纱线进行适当的润滑和处理,减少纱线之间的摩擦和损耗,提高纱线的质量和使用性能。
要加强对纱线的质量检测和控制。
建立完善的纱线质量检测体系,定期对纱线进行抽检和检测,及时发现并解决问题。
同时,要加强
对纱线质量的控制,确保纱线符合产品标准和要求,提高织物的质量和市场竞争力。
总的来说,提高细纱质量需要从选材、工艺、整理和检测等多个方面入手,全面提升纱线的质量和性能。
通过科学管理和技术创新,不断优化生产流程,提高细纱质量,为纺织行业的发展和进步做出贡献。
纺织厂细纱管理方法

纺织厂细纱管理方法
首先是人员管理。
要想管好质量,最好有一个专人是总体负责细纱车间质量的,关于质量方面的问题全部是他的管理范畴。
其次是工艺管理。
制作合理的工艺是工艺管理的任务之一,而对工艺的研究和工艺档案的管理则是工艺管理中最重要的内容。
很可惜,现在90%的纺织企业都反过来了,主要任务是做工艺,导致产品上机后还要做很多方面的调整。
很多工艺人员很可笑,只知其然,不知其所以然,对着老师教的东西照葫芦画瓢,从来不问问自己为什么。
温湿度控制。
不用多说,做纺织的人都知道重要性。
设备保养。
设备是质量的基础,务必要养成定期保养的习惯,即使产量再多,交期再忙,但只要到了设定的校验期,那就该平车的必须平车,该校正的必须校正。
磨刀不误吹柴功,抢那点产量没有。
很多企业为了赶交期,车都不保养了,时间久了,导致的结果就是车坏了,产量也没有了,制度作废了,质量不好了,所有人更忙了,产量更低了,质量更坏了。
得不偿失啊。
人员培训。
目前的纺织厂人员素质参差不齐,尤其是一些小企业。
那就想办法营造一个重视质量的氛围。
这需要通过一定的活动形式;另外,对主要负责质量管理人员进行管理方法的培训,这是个长时间才会慢慢起到效果的事情,看似不紧要,但却对企业的未来有用。
其他方面还请高人指点。
- 1、下载文档前请自行甄别文档内容的完整性,平台不提供额外的编辑、内容补充、找答案等附加服务。
- 2、"仅部分预览"的文档,不可在线预览部分如存在完整性等问题,可反馈申请退款(可完整预览的文档不适用该条件!)。
- 3、如文档侵犯您的权益,请联系客服反馈,我们会尽快为您处理(人工客服工作时间:9:00-18:30)。
细纱工序质量控制要点侯长勇(山东聊城华润纺织有限公司,山东聊城,252000)摘要: 探讨细纱工序提高纺纱质量的技术措施㊂分析了影响细纱工序纺纱质量的主要因素,从细纱机的机械运行状态㊁牵伸专件器材的选用㊁上机工艺参数的优化㊁加捻卷绕器材的应用㊁运转操作管理及车间温湿度控制等方面提出了相应的解决方法㊂指出:在实际生产中要根据纺纱品种的具体情况和用户的标准找准思路和对策,以保证纱线条干㊁粗节㊁细节㊁棉结等指标的长期稳定㊂认为:细纱工序的精细化管理是成纱质量稳定的关键㊂关键词: 细纱工序;专件;器材;工艺优化;运转操作管理;车间温湿度中图分类号:T S101.9 文献标志码:B 文章编号:1000-7415(2019)03-0053-04K e yQ u a l i t y C o n t r o l P o i n t s i nS p i n n i n g P r o c e s sH O UC h a n g y o n g(S h a n d o n g L i a o c h e n g H u a r u nT e x t i l eC o.,L t d.,S h a n d o n g L i a o c h e n g,252000)A b s t r a c t T e c h n o l o g y m e a s u r e s t o i m p r o v e s p i n n i n g q u a l i t y i n s p i n n i n gp r o c e s sw e r e d i s c u s s e d.M a i n f a c t o r s a f f e c t i n g s p i n n i n gq u a l i t y i n s p i n n i n gp r o c e s sw e r e a n a l y z e d.C o r r e s p o n d i n g s o l u t i o n sw e r e p u t f o r w a r d f r o ma s-p e c t s o fm e c h a n i c a l o p e r a t i o n s t a t e o f s p i n n i n g f r a m e,s e l e c t i o no f s p e c i a l d r a f t i n gp a r t s a n d a c c e s s o r i e s,o p t i m i z a-t i o no f s p i n n i n gp a r a m e t e r,a p p l i c a t i o no f t w i s t i n g a n dw i n d i n g a c c e s s o r i e s,o p e r a t i o n m a n a g e m e n t a n dt h e t e m-p e r a t u r e&h u m i d i t y c o n t r o l i nw o r k s h o p.I t i s p o i n t e do u t t h a t i na c t u a l p r o d u c t i o n,i d e a s a n dc o u n t e rm e a s u r e s s h o u l db e f o u n do u t a c c o r d i n g t o s p e c i f i c c o n d i t i o n so f s p i n n i n g v a r i e t i e sa n du s e r s t a n d a r d s,s oa s t oe n s u r e t h e l o n g-t e r ms t a b i l i t y o f y a r ne v e n e s s,t h i c k p l a c e s,t h i n p l a c e s,n e p s a n do t h e r i n d e x.I t i s c o n s i d e r e d t h a t f i n em a n-a g e m e n t i n s p i n n i n gp r o c e s s i s t h ek e y t o s t a b l e y a r n q u a l i t y.K e y W o r d s S p i n n i n g P r o c e s s,S p e c i a lP a r t s,A c c e s s o r y,P r o c e s s O p t i m i z a t i o n,O p e r a t i o n M a n a g e m e n t, T e m p e r a t u r e&H u m i d i t y i n W o r k s h o p纺纱质量管理是一项综合性很强的工作,细纱工序是纺纱的关键工序,不仅影响后道工序的加工生产,也会影响面料的使用性能㊂细纱工序的纺纱质量必须引起我们的重视㊂我公司是拥有20万纱锭的细号纱生产企业,细纱工序设备多㊁纺纱品种多,设备的运行状况对纺纱质量的影响较大㊂成纱条干C V㊁C V b㊁细节㊁粗节㊁棉结㊁毛羽㊁强力等质量指标是衡量纺纱质量的重要指标,而影响这些指标的因素有很多,在实际生产管理中,我们要综合考虑,从根本上找到影响这些指标的原因,并采取相应的改善措施,以提高纺纱质量㊂作者简介:侯长勇(1975 ),男,技师,3167282457@q q.c o m收稿日期:2018-11-121 设备运行状态对纺纱质量的影响细纱机是提高纺纱质量和产量的主要设备,性能好坏㊁运行状态对纺纱质量影响较大㊂设备运行状况是纺纱的基础,要强化设备管理,加强对设备状态的日常检查和维护工作,做好周期性的平车㊁揩车,设备人员要做好自己日常的包机和检查工作,保持细纱机运行状态良好,对细纱机的牵伸㊁加捻㊁卷绕过程重点进行关注,车头传动部分㊁齿轮啮合要良好,各种键㊁轴㊁轴承配合到位㊂对细纱机进行周期性的状态检查㊁揩车维修能及时发现设备出现的问题,并对变形的机件及专件器材按周期更换或维修,能降低设备的故障率,以保证细纱机的正常运行,稳定纺纱质量㊂由于=================================================F A1530型细纱机机电一体化㊁自动化程度高,设备人员要多了解一些机电方面的知识,自动落纱部分要保持状态良好,加强日常的维修㊂结合平车㊁揩车清除罗拉沟槽内所嵌的杂质和罗拉表面棉蜡㊁油渍等,确保前罗拉中弯和偏心不大于0.03mm,避免造成成纱规律性条干不匀㊂要按照平车㊁揩车制定的内容加强对细纱机的保养,直接包机到人,运转值车工在巡回中发现的问题,要及时反馈到设备包机人,由包机人及时进行维修,以保证细纱机运行状态良好㊂2 专件牵伸器材对纺纱质量的影响细纱工序是控制条干C V㊁C V b㊁细节㊁粗节㊁棉结㊁毛羽㊁强力等纺纱指标的重点㊂而专件器材是影响这些纺纱指标的核心,专件器材的优劣直接影响到纺纱质量㊂它不仅是细纱机正常运行的基础牵伸部件,还是影响纺纱指标的关键部件,因此专件牵伸器材要优化选择使用㊂2.1 胶辊胶圈胶辊胶圈是牵伸的 小心脏”,在纺纱过程中与罗拉组成罗拉钳口,共同对须条握持牵伸,稳定摩擦力界㊂胶辊胶圈的质量㊁使用性能㊁选配的合理性及使用状态与成纱条干㊁强力㊁断头率㊁胶辊缠花关系很大,对成纱指标影响也较大㊂不同型号胶辊胶圈的性能和特点也不相同,要根据纺纱品种㊁纤维性能和纺纱质量的要求来选用合适硬度㊁弹性的胶辊胶圈,既要稳定纺纱质量,又要保证专件器材的使用周期,同一品种㊁同一批纱线,胶辊胶圈的直径硬度要统一,要使用同一个型号㊁同一个生产厂家,按工艺要求调整摇架压力并保持大小一致,胶辊胶圈要有优良的弹性和适当的硬度,以保证同一个纺纱品种质量无差异㊂胶辊胶圈的使用可分品种㊁分区域进行管控,其内径㊁外径㊁厚度要符合纺纱品种的要求㊂回磨后胶辊的圆整度要不大于0.03mm,粗糙度要根据纺纱品种来合理掌握,不同胶辊表面的粗糙度在一定的摇架加压情况下对纤维的握持力不同,这种差异有可能影响到牵伸效率㊂同一品种胶辊的上机直径不能差异太大,确保锭差稳定,要根据纺纱质量的要求情况,合理制定胶辊胶圈的使用周期㊁调换周期㊁淘汰周期,胶辊胶圈不能同时进行更换,避免条干恶化,影响质量㊂在生产中要控制好须条的握持力,新旧胶圈搭配上机,要使用内花纹胶圈使内层的摩擦因数增加,内花纹凹凸网状结构与罗拉沟槽的咬合使接触面积增加,稳定纺纱质量㊂要控制好胶辊胶圈的保养周期,保证纺纱质量的一致性,必要时可对纺差别化纤维㊁化纤等原料品种使用的胶辊表面进行紫外光照处理或涂料微处理,以达到胶辊表面光滑爽燥,可减少摩擦产生的静电,并能阻碍表面吸附纤维,减少缠花和断头㊂在纺超细号纺纱品种时,我公司使用的J-463A型㊁WR C-365型倚丽特集聚纺胶辊,需先在其他纯棉品种上机10天~15天,再调换到超细号品种上㊂由于胶辊已磨合数天,胶辊表面较滑爽,能进一步降低断头率,提高产质量㊂采用高弹性㊁低硬度㊁免处理胶辊有利于提高前钳口的握持力,使前钳口的握持力更加稳定㊂胶辊的硬度㊁回弹性技术指标及胶辊表面状态对纺纱牵伸很关键,如果处理不好,有可能恶化成纱质量指标或造成机台生产不顺利㊂在使用新型胶辊胶圈上机时,要进行小面积的试验㊁试纺,确定上机稳定㊁质量指标无差异后,再进行上机推广使用,以免引起纱线质量指标的波动,造成纺纱质量下降,用户进行投诉㊂2.2 上下销上下销也是细纱机牵伸机构中一个重要的部件㊂上销具有对钳口压力起弹性自调作用的特点,与中铁辊㊁上胶圈㊁压力棒隔距块共同组成弹性钳口,支撑上胶圈处于一定的工作位置㊂在细纱双区牵伸系统中,前牵伸区是主牵伸区,有一对中罗拉和上下胶圈钳口形成中部摩擦力界对牵伸区的移动纤维进行控制,由于受上销位置及摇架压力等因素的影响,上下销前缘至前罗拉钳口的浮游区,摩擦力强度相对较弱,对浮游纤维的控制减弱,从而扩大浮游纤维变速点分布范围和纤维运动的不稳定性[1]㊂上销支撑上胶圈与下胶圈销形成握持纤维进行牵伸,上下胶圈在运转中产生一定的附加摩擦力界阻止纤维提前变速,对稳定短纤维并控制它与罗拉钳口组成的牵伸,能有效地控制浮游纤维,减少牵伸的意外波动,进一步改善条干的均匀度,提高纺纱质量㊂我公司部分机型使用了一些新型下销,该下销改变了曲面部分与平面部分的比例(将曲面部分合理延长,平面直线部分缩短),增强了中部摩擦力界,加强了上下胶圈之间对纤维的控制能力,改变了胶圈的张力,使牵伸区摩擦力界的分布更=================================================加合理,纤维的变速点稳定,能有效改善纺纱指标㊂上下销的使用需要合理的工艺配置和适当的摇架压力,确保发挥新型上下销的作用㊂2.3 压力棒隔距块压力棒隔距块是一根直径光滑的压力棒,把原浮游区分配成两个浮游区㊂当须条从压力棒下通过时,因须条受到压力使摩擦力界得以加强,使纤维变速点前移,部分弯钩纤维得到更好的牵伸㊂使用压力棒隔距块后,在前区又形成了曲线牵伸形式,须条在压力棒下形成一段包围弧,从而加强了前区对纤维的控制,使纤维变速点分布集中,稳定靠近钳口,有利于改善条干均匀度,提升纺纱水平[2]㊂压力棒隔距块的使用型号具体要根据纺纱品种和纺纱质量的要求,纺纱过程中防止须条从压力棒上面通过,压力棒处容易积花,造成纱疵,要及时做好清洁;要调整好工艺隔距,防止须条牵伸不开和压力棒摩擦前胶辊㊂3 纺纱工艺对纺纱质量的影响工艺设计是细纱工序生产的主要依据㊂同品种㊁同机型工艺设计应统一㊂根据原料对季节变化的要求,制定出合理的工艺方案,有计划地进行试验,达到要求后逐步推广㊂同时必须加强对纺纱工艺生产参数的设计,加强工艺创新和工艺对比试验,从中找到最佳的生产工艺㊂根据纺纱品种选择合理的罗拉隔距和牵伸倍数,前中罗拉隔距关系到前区握持力与牵伸力平衡,关系到前区浮游纤维长度的大小,直接影响到条干C V㊂在实际生产中应根据棉纤维长度选择前中罗拉隔距,纤维长度长宜选用较大的罗拉隔距,反之选择小的罗拉隔距;随着前胶辊加压的增加,纱线条干C V又有减少的趋势,后区牵伸工艺在生产中一般采用小的后区牵伸工艺㊂对浮游区的调整要做到大小一致,压力棒位置居中㊂压力棒位置靠后会出现浮游区过大,不能有效地控制纤维;压力棒位置靠前,不能发挥压力棒的作用㊂在生产中,胶辊的前冲约2mm~3mm,前冲量不宜过大,容易形成反包围弧,造成质量下降,断头增加㊂要确保上机工艺的合理性,一方面可以提高纺纱质量,另一方面可以减少断头,减轻值车工劳动强度㊂4 加捻卷绕器材对纺纱质量的影响钢领与钢丝圈是纺纱过程中关键的加捻卷绕器材,是一对摩擦副,钢领是钢丝圈运行的轨道,钢丝圈由纱线带动沿着轨道高速运转,共同完成加捻卷绕,对稳定控制气圈张力㊁减少断头和毛羽㊁提高纺纱产质量非常重要㊂钢领和钢丝圈要合理搭配,才能充分发挥两者的性能㊂4.1 钢领采用G c r15轴承钢制定㊁高精度及研磨抛光处理的钢领,其具有耐磨和抗疲劳性能,圆整度不大于0.01mm,使用寿命长㊂一般根据纺纱品种和工艺的要求选用合适型号和材质的钢领,其中高精度轴承钢钢领耐磨性较好,使用寿命长,在纺纱过程中断头少,纺纱质量稳定而被多数纺纱企业所采用㊂4.2 钢丝圈钢丝圈是细纱加捻卷绕的主要器材㊂钢丝圈在高速运行时因离心力的作用,其内脚紧压在钢领圆环的内侧面上,要求其张力小,突变张力小且稳定㊂钢丝圈通道要滑爽,散热性能要好[3],与钢领的摩擦发热量要小㊂上机后观察气圈形态及其稳定性,关注接头手感张力和落纱断头分布情况,若钢领钢丝圈配合合理,手感张力均匀,气圈形态分布合理,断头较少㊂钢丝圈轻重搭配原则:在断头不增加的情况下,选号数较大的钢丝圈,能有效减少钢丝圈烧毁或飞圈,以气圈不碰纱管头为宜,能有效减少断头和毛羽㊂合理设定钢丝圈清洁器隔距,隔距过小,钢丝圈会阻隔气圈形成气流,影响钢丝圈的正常运行,造成气圈张力不稳,容易断头;隔距过大,容易造成钢丝圈挂花㊂要根据纺纱品种的要求来设定钢丝圈清洁器隔距,一般隔距为1.5mm~2.0mm,气圈张力较稳定,有利于减少断头,减少挂花,提高产量,稳定纺纱质量㊂4.3 锭子锭子是细纱机上主要的加捻卷绕部件,它在纺纱过程中的运行状态是影响纱线捻度不匀的重要因素㊂保证锭子运行平稳,减少锭速差异和纱线捻度不匀主要取决于锭速差异的大小,锭速不匀是造成纱线捻度不匀的主要原因㊂锭子的振动对细纱断头和捻度不匀都有很大的影响,应减少锭子在运行中的振动,保证锭子良好的润滑状态㊂纱管要与锭子配合良好,在保养检查时剔除不合格纱管,值车工在接头拔纱时应使用纱锭器,避免造成对纱管的磨损,进而使纱管运行不稳定㊂及时清理锭杆中的回丝积花,保证锭子运行稳定,张力盘下面重锤的刻度应调整一致,以减少锭带张=================================================力的变化[4]㊂有试验表明,锭带的伸长率应小于1%,锭带松弛,锭带张力会变小,出现弱捻纱的几率增大㊂强捻和弱捻都会造成纱线强力的变化,捻度均匀度差会影响到整经㊁织造等后工序㊂我公司的F A1520型细纱机使用铝套管锭子,为实现纱管和锭子的紧密配合,保护锭子和纱管,要求值车工接头拔纱必须使用纱锭器,以减少锭子和纱管的损伤,防止纱管摇头㊁跳动,影响设备运行状态㊂5 运转操作管理运转操作人员的操作水平直接影响到纺纱质量㊂要保证值车工能将全项操作㊁机台清洁㊁防疵捉疵有计划的安排在每一巡回工作中去,并能熟悉本工序的设备机械性能,以降低纱疵率;对新员工进行有计划的培训㊂现代纺纱企业细号纱在不断增加,运转操作管理也应不断创新㊂由于值车工操作水平参差不齐,用户对产品质量要求也不同,可把用户对产品质量的要求与值车工的操作水平相匹配㊂对产品质量要求较高的选择操作能手进行值车,对操作水平差的要进行操作水平培训,提升操作水平,使一级操作选手率达到95%以上㊂制定目标细化考核,不同品种安排不同的清洁进度表,做到机台清洁分段㊁按顺序做,使纺纱质量再上一个新的台阶㊂6 车间温湿度的控制温湿度的变化对细纱工序纺纱质量影响较大,也是影响毛羽的重要因素㊂调节好细纱空调设备,控制好细纱车间环境温湿度,不仅关系到纺纱的产量和质量,还影响到细纱效率[5]㊂温度对纤维表面棉蜡的软硬㊁纤维的吸放湿特性产生影响㊂温度过高纤维表面棉蜡溶化,纤维易于吸湿,使纤维表面发黏,容易黏缠胶辊胶圈;温度过低纤维表面棉蜡脆硬,纤维不易吸湿,纤维间抱合力差,纤维在加工过程中容易断裂,增加短绒㊂另外,空气中的水气与温度低的胶辊表面易凝结成一层水薄膜,造成短绒黏附胶辊㊁胶圈㊁罗拉㊂相对湿度会影响纤维表面摩擦力㊁导电性能等指标㊂车间相对湿度过大,易增加纤维与摩擦机件(胶辊㊁罗拉等工艺部件)的黏合力,形成黏缠;相对湿度过低,纤维与工艺部件易产生摩擦和静电,飞花㊁短绒增多,纱条松散㊂由于温湿度影响到纤维的物理性能,合理调节车间温湿度可改善纺纱的生产状况㊂要加强空调的技术管理,并做好温湿度记录,发现异常及时调节㊂生产中根据纺纱品种㊁纤维性能的要求合理调整,温度一般为28℃~34℃㊁相对湿度控制在50%~60%㊁回潮率控制在6.5%~7.0%㊂具体可根据纺纱品种不同㊁季节不同进行调整㊂7 结语提高纺纱质量是一个系统工程,它涉及到许多方面,影响的因素也较多㊂在实际生产过程中,要根据纺纱品种,认真分析影响纺纱质量的因素,并采取相应的技术措施㊂如保证细纱机运行状态的稳定㊁纺专器材的合理定位㊁上机工艺参数的合理选择㊁提高运转操作管理效率㊁控制好车间温湿度等,最大限度稳定纺纱质量,满足用户需求,使纺纱质量迈上一个新的台阶㊂参考文献:[1] 徐建.B X-6839D型上销纺纱实践[J].纺织器材,2018,45(1):46-47.[4] 孙辉,陆平,单学礼,等.细纱工序采用压力棒隔距块提高成纱质量的实践[J].上海纺织科技,2008,36(10):31-32.[3] 郭占军,范轩云鹏,叶戬春.2017年纺纱关键器材性能及品牌应用情况分析[J].棉纺织技术,2018,46(8):1-7.[4] 计万平,梅剑香,蔡文华,等.浅谈细纱锭子运行状态对纱线捻度不匀的影响[J].纺织器材,2018.45(1):51-56.[5] 马开斌.细纱车间环境控制实践[J].棉纺织技术,2014,42(1):63-66.=================================================。