消隙式新型蜗杆传动研究毕业设计说明书
机械设计课程设计_蜗轮蜗杆减速器设计说明书
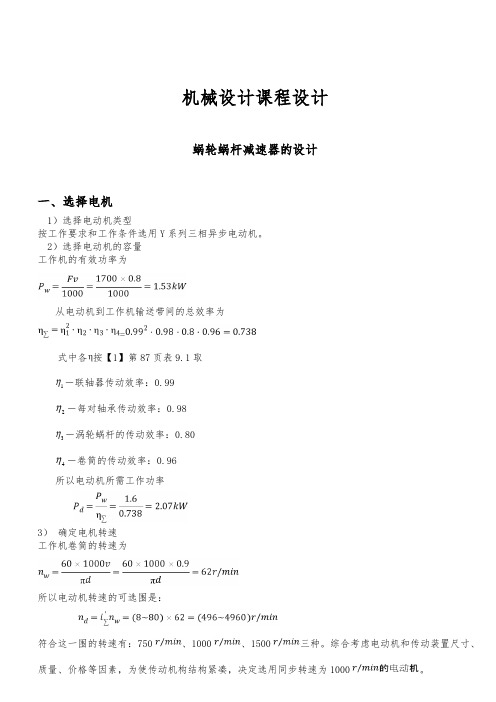
机械设计课程设计蜗轮蜗杆减速器的设计一、选择电机1)选择电动机类型按工作要求和工作条件选用Y系列三相异步电动机。
2)选择电动机的容量工作机的有效功率为从电动机到工作机输送带间的总效率为=式中各按【1】第87页表9.1取η-联轴器传动效率:0.991η-每对轴承传动效率:0.982η-涡轮蜗杆的传动效率:0.803η-卷筒的传动效率:0.964所以电动机所需工作功率3)确定电机转速工作机卷筒的转速为所以电动机转速的可选围是:符合这一围的转速有:750、1000、1500三种。
综合考虑电动机和传动装置尺寸、质量、价格等因素,为使传动机构结构紧凑,决定选用同步转速为1000。
根据电动机的类型、容量、转速,电机产品目录选定电动机型号Y112M-6,其主要性能如下表1:表1 Y112M-6型电动机的主要性能型号额定功率满载时质量/kg转速/(电流/A(380V)效率/%功率因数Y112M-6 2.2 940 5.6 80.5 0.74 2.0 452 确定传动装置的总传动比和分配传动比:总传动比:3 计算传动装置各轴的运动和动力参数:1)各轴转速:Ⅰ轴Ⅱ轴卷筒轴2)各轴输入功率:Ⅰ轴Ⅱ轴卷筒轴3)各轴输入转矩:电机轴的输出转矩Ⅰ轴Ⅱ轴卷筒轴运动和动力参数结果如下表:轴名功率P/kW转矩T/)转速n/传动比i效率/电机轴 2.07 940 115.610.990.80.971轴 2.06 9402轴 1.65 62卷筒轴 1.60 62二、涡轮蜗杆的设计1、选择材料及热处理方式。
考虑到蜗杆传动传递的功率不大,速度也不高,蜗杆选用45号刚制造,调至处理,表面硬度220250HBW;涡轮轮缘选用铸锡磷青铜,金属模铸造。
2、选择蜗杆头数和涡轮齿数i=15.16 =2 =i=215.16303、按齿面接触疲劳强度确定模数m和蜗杆分度圆直径1)确定涡轮上的转矩,取,则2)确定载荷系数K=根据工作条件确定系数=1.15 =1.0 =1.1K==1.15 1.0 1.1=1.2653)确定许用接触应力由表查取基本许用接触应力=200MPa应力循环次数 N=故寿命系数4)确定材料弹性系数5)确定模数m和蜗杆分度圆直径查表取m=6.3mm,=80mm4、计算传动中心距a。
蜗轮蜗杆传动设计说明
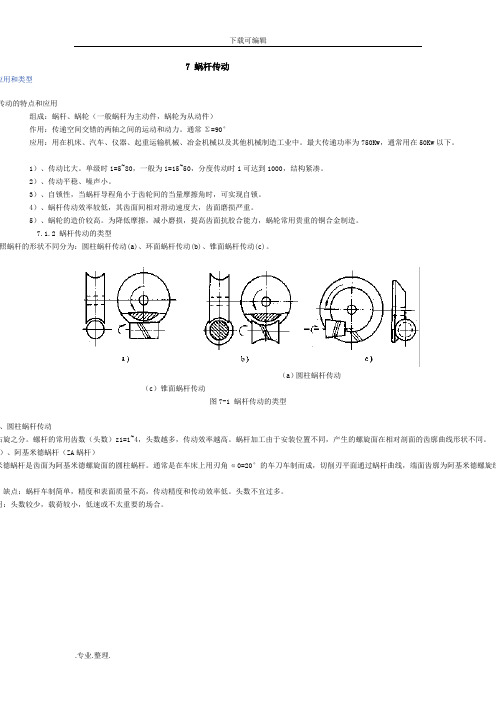
7 蜗杆传动应用和类型传动的特点和应用组成:蜗杆、蜗轮(一般蜗杆为主动件,蜗轮为从动件)作用:传递空间交错的两轴之间的运动和动力。
通常Σ=90°应用:用在机床、汽车、仪器、起重运输机械、冶金机械以及其他机械制造工业中。
最大传递功率为750Kw,通常用在50Kw以下。
1)、传动比大。
单级时i=5~80,一般为i=15~50,分度传动时i可达到1000,结构紧凑。
2)、传动平稳、噪声小。
3)、自锁性,当蜗杆导程角小于齿轮间的当量摩擦角时,可实现自锁。
4)、蜗杆传动效率较低,其齿面间相对滑动速度大,齿面磨损严重。
5)、蜗轮的造价较高。
为降低摩擦,减小磨损,提高齿面抗胶合能力,蜗轮常用贵重的铜合金制造。
7.1.2 蜗杆传动的类型照蜗杆的形状不同分为:圆柱蜗杆传动(a)、环面蜗杆传动(b)、锥面蜗杆传动(c)。
(a)圆柱蜗杆传动(c)锥面蜗杆传动图7-1 蜗杆传动的类型、圆柱蜗杆传动右旋之分。
螺杆的常用齿数(头数)z1=1~4,头数越多,传动效率越高。
蜗杆加工由于安装位置不同,产生的螺旋面在相对剖面的齿廓曲线形状不同。
)、阿基米德蜗杆(ZA蜗杆)米德蜗杆是齿面为阿基米德螺旋面的圆柱蜗杆。
通常是在车床上用刃角α0=20°的车刀车制而成,切削刃平面通过蜗杆曲线,端面齿廓为阿基米德螺旋线、缺点:蜗杆车制简单,精度和表面质量不高,传动精度和传动效率低。
头数不宜过多。
用:头数较少,载荷较小,低速或不太重要的场合。
图7-2 阿基米德蜗杆2)、法向直廓蜗杆(ZN蜗杆)杆加工时,常将车刀的切削刃置于齿槽中线(或法向剖面,端面齿廓为延伸渐开线。
点:常用端铣刀或小直径盘铣刀切制,加工简便,利于加工多头蜗杆,可以用砂轮磨齿,加工精度和表面质量较高。
:用于机场的多头精密蜗杆传动。
)、渐开线蜗杆(ZI蜗杆)杆是齿面为渐开线螺旋面的圆柱蜗杆。
用车刀加工时,刀具切削刃平面与基圆相切,端面齿廓为渐开线。
缺点:可以用单面砂轮磨齿,制造精度、表面质量、传动精度及传动效率较高。
蜗轮蜗杆传动及其优化设计设计说明说书
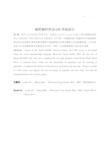
43 1蜗轮蜗杆传动CAD系统设计摘要基于AutoCAD2007软件平台,应用Microsoft Visual Studio 2005编程语言和ObjectARX2007开发工具对CAD系统进行二次开发,本课题完成了机械传动中蜗轮蜗杆传动设计的参数计算和参数绘图两大功能模块以及两大模块之间的数据传递。
二次开发后的CAD系统能够极大的提高设计效率,同时,它也能够确保产品的设计质量。
Abstract Based on the AutoCAD2007 software terrace, the CAD system is developed using the visual programming language Microsoft Visual Studio 2005 and the tool of ObjectARX2007.The topic have completed the two great modules of the Worm Wheel Worm Drive of machine drive, which are the calculation of parameter and the drawing of parameter ,in addition the deliver of data between calculation and drawing . Design secondly to CAD system can improve the rate of design in multiples and also make sure that the designed products are of good quality.关键词AutoCAD ;ObjectARX ;Microsoft Visual Studio 2005;MFC;蜗轮蜗杆传动Keywords AutoCAD ;ObjectARX ;Microsoft Visual Studio 2005;MFC;Worm Wheel Worm Drive1绪论1.1研究目的和意义机械工业肩负着为国民经济各个部门提供技术装备的重要任务。
毕业设计-蜗轮蜗杆减速器

设计二级蜗杆—锥齿轮减速器摘要机械传动已经伴随人们走过了几千年的历史,无论是在生活还是生产方面,它都为人类的发展进程作出了巨大的贡献。
如今,随着电子技术、信息技术的广泛应用,使机械传动也进入了一个新的发展阶段。
机械传动系统在高速、高效、节能、环保以及小型化等方面有了明显的改进。
现在,单纯的机械或电气传动似乎更多地加入了流体技术、智能控制技术部分,机械、电子、传感器技术、软件的合成已成为一种重要的趋势。
社会生活的各个角落,无不在享受着新技术发展所带来的便利,高科技越发达,相对的对机械行业的需求就越大。
我国减速机制造企业更应该跟上时代,多元化地发展。
目前国际上最先进的各种减速机加工及检测设备,包括各种滚齿机、磨齿机、热处理炉、齿轮检测中心、三坐标测量仪等,均不同程度地使用了微电子技术和信息技术。
国外的机械传动行业随着微电子技术、信息技术的发展也在进行着与之相应的多元化的改变。
而我国的基础行业包括减速机行业则相对还很落后,基本上处于先进国家上世70、80年代的水平。
优化人与环境的概念在现代的生产生活中越发受到重视,在工业领域,节能、低噪声、环保也是机械制造的发展趋势,机械传动行业应如何在材质的选择、结构的设计等诸多方面去突破以满足这些要求。
效率低自然容易产生热量,耗费能源。
而产品的大型化,则会对传动效率产生很大的影响,同时,材料的费用,包装的费用也会随之上升,增加成本。
因此,而要改善这一切,必须在加工精度、机械加工和热处理上有所改进。
机械传动系统正日益基于标准或准标准的元件和系统,如何提高机械传动部件的标转化、提高配套件的互换性的同时,满足不同客户的具体要求以迫在眉睫。
如今我在这设计二级蜗杆—锥齿轮减速器仅供参考。
关键词:二级蜗杆、锥齿轮、减速器目录摘要 (1)第一章绪论 (4)1.1齿轮减速器的发展史 (4)1.2二级蜗杆—锥齿轮减速器的特点 (5)1.3本课题的研究意义 (5)第二章关于二级蜗杆—锥齿轮减速器的设计 (6)2.1设计内容 (6)2.2设计思路 (6)2.3设计步骤 (7)第三章减速器传动零部件设计 (8)3.1简述 (8)3.2小锥齿轮设计 (8)3.3锥齿轮轴设计 (10)3.4蜗杆设计 (12)3.4.1蜗杆设计思路 (12)3.4.2蜗杆设计成品 (13)3.5蜗杆参数化模型 (13)3.5.1设计思路 (14)3.5.2设计步骤 (14)3.6减速器传动机构子装配及中间轴设计 (21)3.6.1简述 (22)3.6.2减速器传动机构装配 (22)3.6.3中间轴设计 (23)3.7内圈零件库设计 (24)第四章减速器整机装配及其他零部件设计 (27)4.1说明 (27)4.2箱体设计 (27)4.3下箱体设计步骤 (27)4.4上箱体、窥油孔盖设计 (29)4.5箱体的装配 (29)第五章物理模拟 (31)5.1简述 (31)5.2爆炸图配置文件 (31)参考文献 (33)1.致谢 (33)2.附件一 (34)3.附件二 (34)第一章绪论齿轮减速器是原动机和工作机之间的独立的闭式传动装置,用来降低转速和增大转矩,以满足工作需要,在某些场合也用来增速,称为增速器。
涡轮蜗杆设计说明书

减速器设计说明书郭燕芳机自0413班20042206目录1 设计任务书 (2)2 电动机的选择计算 (2)3 传动装置的运动和动力参数的选择和计算 (3)4 传动零件的设计计算 (4)4.1蜗轮蜗杆的设计计算 (4)4.2滚子链传动 (8)4.3选择联轴器 (10)5 轴的设计计算 (10)6 滚动轴承的选择和寿命验算 (17)7 键联接的选择和验算 (19)8 减速器的润滑方式及密封形式的选择润滑油牌的选择及装油量的计算 (20)9 参考资料 (20)1 设计任务书1.1 题目:胶带输送机的传动装置滚筒圆周力F=19000N;带速V=0.45m/s;滚筒直径D=300mm;滚筒长度L=400mm。
1.2工作条件:A工作年限8年;工作班制2班;工作环境清洁;载荷性质平稳;生产批量小批。
图1 胶带运输机的传动方案2 电动机的选择计算2.1 选择电动机系列按工作要求及工作条件选用三相异步电动机,封闭式结构,电压380V,Y系列。
2.2 选择电动机功率卷筒所需有效功率P W=F×V/1000=1900×0.45/1000=0.855kW P W=0.855kW 传动装置总效率:η=η1×η2×η23×η4×η5×η6按参考资料[2](以下所有的“参考资料[1]”和“参考资料[2]”都统一简称为“[1]”和“[2]”)表4.2-9取弹性联轴器效率η1=0.99蜗杆传动效率η2=0.75(暂定蜗杆为双头)一对滚动轴承效率η3=0.99开式滚子链传动效率η4=0.9运输滚筒效率η5=0.96滑动轴承效率η6=0.97则传动总效率η=0.99×0.75×0.992×0.9×0.96×0.97=0.635 η=0.635 所需电动机功率P r =P W /η=0.855/0.635=1.35kw P r =1.35kW查[2]表4.12-1,可选Y 系列三项异步电动机Y100L-6型,额定功率 P 0=1.5kW 。
蜗杆轴设计说明书
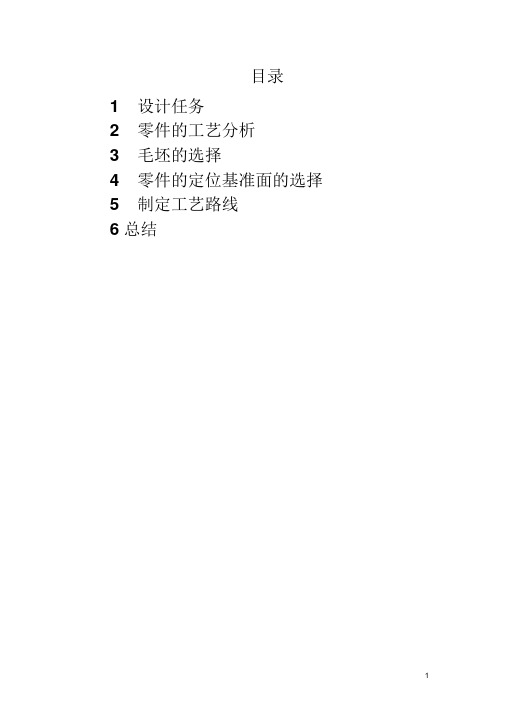
目录1 设计任务2 零件的工艺分析3 毛坯的选择4 零件的定位基准面的选择5 制定工艺路线6 总结蜗杆轴加工工艺规程设计1设计任务:本次所要加工的零件为蜗杆轴,示意图如图:I WttCt2•眦3. JM 换图12:零件的工艺性分析:由零件图可知,主要加工表面有:(1) ①12,①17①25,①13,①20,①16的圆周面; (2) M16的螺纹 (3) ①18的蜗杆面 (4) M6的内螺纹(5) L=14深度为2.5宽度为4的键槽零件尺寸比较完整,可以加工。
由上述可知, 蜗杆轴可以通过车外形,键槽则在铳床上用专用夹具定位就可以铳出来。
用热处理调质处理既可以满足硬度的要求。
其中①12①17①16的外圆的精度可在磨床上磨削可以达到精度要求 3:毛坯的选择:考虑到零件的经济性蜗杆轴硬度等方面的和综合性能要求,零件材料为45。
毛坯①30x230UNHl11加第1imBe 删轍til1tw'-116测用diIStil »110mui*M! 曲社f.WtlUfpKOCR1IK?IWlUfeflmlmf mutual J L3*34%縮曲f *CIS图24:零件的定位基准面的选择基准面的选择是工艺规程设计中重要的工作之一,基准面选择的正确与否,可以使加工质量得到保证,使生产力得到提高,否则,不但加工工艺过程中的问题百出,更有甚者,还会造成零件的大批量报废,使生产无法正常进行。
(1).基准面的选择粗基准的选择要保证粗基准定位所加工出的精基准有较高的精度,通过精基准定位使后续各被加工表面具有较高的均匀的加工余量,并与非加工表面保持应有的相对位置精度。
在确定粗基准时,要保证相对位置精度要求和加工表面余量合理分配原则,在本零件中,先以右端面基准面为粗基准,加工25圆、13外圆、18圆、13圆、20圆、16圆,且保证各轴段的长度尺寸,粗加工的时候留有0.5毫米的加工余量。
粗加工如图3:A图3调头以后以左端面为基准面来加工17外圆表面、16圆以及12外圆表面,精加工的时候基准面选择同。
蜗杆传动设计说明书

=916.5mm
Amax=a+0.03Ld
=1029mm 6.1.6 验算小带轮包角α1
α1=180`-(Dd2-Dd1)/a*57.3`
=172.5`>120` 6.1.7 确定 V 带根数
Z>=Pc/(P0+ΔP0)KaKl 查文献【2】表 3.5 得 B 型带单根 V 带的基本额定功率 Pc=2.2--1.93KW 根据 Dd1=125mm,n1=1460r/min,查文献【2】表 3.5,用内插 法得:
1 / 20
设计说明书
传动方案分析
本设计是蜗杆涡轮减速器的设计,该设计主要针 对执行机构的运动展开,为了达到要求的运动精 度和生产率,必须要求传动系统具有一定的传动 精度并且各传动元件之间应满足一定的关系,以 实现各零部件的协调工作。 该设计均采用模块化设计,设计内容包括传动件 的设计,执行机构的设计以及设备零部件等的设 计。
则 P 出=F*V=5.652KW
查文献【1】表 2.3 得:
V 带的η=0.96,
η球轴承(油润滑)的η=0.99
η滚子轴承的η(油润滑)=0.98,
η双头蜗杆(油润滑)的η=0,75
代入上式得η总=0.58
故电动机的 P 电=9.74KW,
因载荷平稳,电动机额定功率只需略大于输出功率 P 出即可。
α1=172.5`
P0=1.93+(2.2-1.93)/(1460-1200)*(1460-1200)
=2.2KW 由公式得ΔP0=Kbn1(1-1/Ki)
式中 Kb------弯曲影响系数,见文献【2】表 3--6 Ki------普通 V 带传动系数,见文献【2】表 3--7
-3
查文献【2】表 3-6 得 Kb=2.6494*10
双蜗轮蜗杆消隙的原理
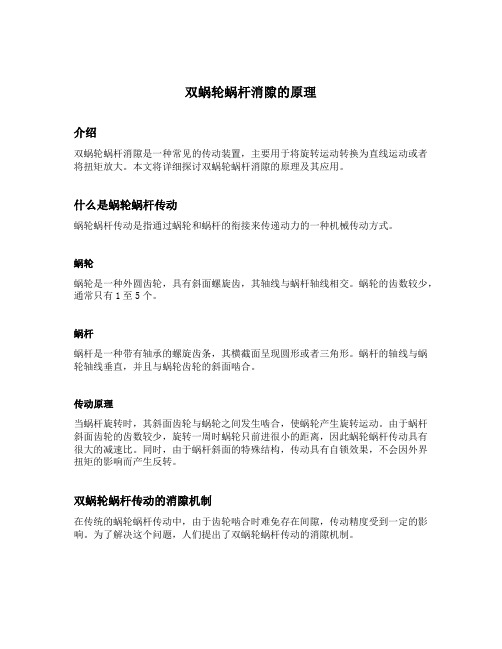
双蜗轮蜗杆消隙的原理介绍双蜗轮蜗杆消隙是一种常见的传动装置,主要用于将旋转运动转换为直线运动或者将扭矩放大。
本文将详细探讨双蜗轮蜗杆消隙的原理及其应用。
什么是蜗轮蜗杆传动蜗轮蜗杆传动是指通过蜗轮和蜗杆的衔接来传递动力的一种机械传动方式。
蜗轮蜗轮是一种外圆齿轮,具有斜面螺旋齿,其轴线与蜗杆轴线相交。
蜗轮的齿数较少,通常只有1至5个。
蜗杆蜗杆是一种带有轴承的螺旋齿条,其横截面呈现圆形或者三角形。
蜗杆的轴线与蜗轮轴线垂直,并且与蜗轮齿轮的斜面啮合。
传动原理当蜗杆旋转时,其斜面齿轮与蜗轮之间发生啮合,使蜗轮产生旋转运动。
由于蜗杆斜面齿轮的齿数较少,旋转一周时蜗轮只前进很小的距离,因此蜗轮蜗杆传动具有很大的减速比。
同时,由于蜗杆斜面的特殊结构,传动具有自锁效果,不会因外界扭矩的影响而产生反转。
双蜗轮蜗杆传动的消隙机制在传统的蜗轮蜗杆传动中,由于齿轮啮合时难免存在间隙,传动精度受到一定的影响。
为了解决这个问题,人们提出了双蜗轮蜗杆传动的消隙机制。
消隙原理双蜗轮蜗杆传动的消隙机制是通过两个蜗轮的反向旋转来消除齿轮啮合时的间隙。
具体原理如下:1.两个蜗轮分别与一个蜗杆啮合,但其相对位置相反。
2.当两个蜗轮一起转动时,由于其相对位置的差异,一个蜗轮的齿轮啮合处将向前移动,而另一个蜗轮的齿轮啮合处将向后移动。
3.通过合理的设计,两个蜗轮的位移可以正好抵消彼此的间隙。
这样,整个传动系统的效率和精度都将得到提高。
优点双蜗轮蜗杆传动的消隙机制具有以下优点:•提高传动精度:通过消除齿轮啮合时的间隙,传动精度得到提高。
•减小噪声:由于齿轮间隙的消除,传动过程中的摩擦和噪声减小。
•增加传动效率:传统蜗轮蜗杆传动由于间隙存在,会产生一定的传动损失;而双蜗轮蜗杆传动通过消除间隙,能够提高传动效率。
双蜗轮蜗杆传动的应用双蜗轮蜗杆传动由于其消隙机制的特殊性,被广泛应用于许多领域。
工业机械双蜗轮蜗杆传动在工业机械中被广泛应用于需要较高传动精度和效率的场合,如机床、起重装置等。
双蜗轮蜗杆消隙的原理

双蜗轮蜗杆消隙的原理双蜗轮蜗杆消隙是利用两个蜗轮齿轮及一个蜗杆设计的一种机构,用于减小齿轮传动的啸叫和振动噪声。
该装置又称为双蜗轮减振机。
蜗轮蜗杆传动是一种带有隙的传动,这会导致传动过程中齿轮与蜗杆之间不断地碰撞与摩擦,产生振动及噪声。
双蜗轮蜗杆消隙机构的出现,就是为了解决这个问题。
原理及结构:双蜗轮蜗杆消隙机构是由两个蜗轮和一个蜗杆组成。
蜗轮采用正面的螺旋线,与蜗杆的侧面螺旋线形成啮合齿轮副,传动形式为蜗杆传动。
在蜗轮副中添加一个间隙消除机构,在蜗轮副中安装前部和后部蜗轮就能使蜗轮副中隙的方向与传动方向保持一致并减小传动过程中的冲击、噪声及振动。
这种机构主要的目的就是通过两个蜗轮齿轮的组合和蜗杆的啮合,可以有效的消除齿轮传动中的隙间,从而提高传动的精度和稳定性。
在传动系统中添加这个机构可以有效消除隙间,使得机械传动过程更加稳定,减少传动中的噪声,提高传动效率和可靠性。
优点及应用:1、工作稳定:通过消隙装置来提高传动的稳定性,减少传动中的噪声和振动,提高传动效率和精度。
2、可靠性高:消隙机构可以有效地减少传动过程中的磨损和损伤,从而提高机械传动系统的可靠性和寿命。
3、适用范围广:目前该机构已广泛应用于各种工业设备,如机床、风电、冶金等领域,具有广阔的应用前景。
双蜗轮蜗杆消隙机构是现代机械传动中不可或缺的一个组成部分,可以保证机械传动的稳定性和可靠性,提高机械传动的效率,广泛应用于各个领域。
在使用过程中,双蜗轮蜗杆消隙机构不仅可以减少机械传动中的噪音和振动,还可以提高传动效率和精度。
其在不同领域中都得到了广泛的应用。
在风电领域中,蜗杆减速器被广泛应用于风电机组的旋转传动系统中。
风能是清洁、可再生的能源,但风力发电机的运转稳定性和可靠性受到风速等环境因素的影响。
如何保证传动的精度和运转稳定性成为关键。
双蜗轮蜗杆消隙机构的使用可以让整个传动系统更为平稳、稳定、低噪音,同时提高系统的可靠性和耐久性。
在物流行业中,蜗轮减速器被广泛应用于输送带传动系统中。
- 1、下载文档前请自行甄别文档内容的完整性,平台不提供额外的编辑、内容补充、找答案等附加服务。
- 2、"仅部分预览"的文档,不可在线预览部分如存在完整性等问题,可反馈申请退款(可完整预览的文档不适用该条件!)。
- 3、如文档侵犯您的权益,请联系客服反馈,我们会尽快为您处理(人工客服工作时间:9:00-18:30)。
目录1 前言 (1)1.1选题目及研究意义 (1)1.2相关领域的研究现状、发展趋势、研究方法及应用领域 (2)1.2.1 蜗轮蜗杆研究现状 (2)1.2.2 蜗杆传动的发展趋势 (2)1.2.3、研究方法 (2)1.2.4 应用领域 (3)1.3数控工作台的设计思想 (3)2 OTT蜗轮蜗杆结构分析.................... 错误!未定义书签。
2.1OTT蜗轮蜗杆的调隙结构及工作原理 .................. 错误!未定义书签。
2.1.1 OTT蜗轮蜗杆的结构特点 ........................ 错误!未定义书签。
2.1.2 OTT蜗轮蜗杆消隙的原理以及消隙的特点 .......... 错误!未定义书签。
2.2OTT蜗轮蜗杆传动装置的优点及应用场合 .............. 错误!未定义书签。
2.2.1 OTT蜗轮蜗杆传动装置的优点 .................... 错误!未定义书签。
2.2OTT蜗轮蜗杆副的参数计算 ........................... 错误!未定义书签。
3 涡轮蜗杆的创建 ......................... 错误!未定义书签。
3.1蜗轮的创建......................................... 错误!未定义书签。
3.1.1 蜗轮的建模分析................................. 错误!未定义书签。
3.1.2 蜗轮的建模过程................................. 错误!未定义书签。
3.2蜗杆的创建......................................... 错误!未定义书签。
3.2.1 蜗杆的建模分析................................. 错误!未定义书签。
3.2.2 蜗杆的建模过程................................. 错误!未定义书签。
4 数控立式铣镗床数控转台的结构设计........ 错误!未定义书签。
4.1数控回转工作台结构设计方案的优化选择.............. 错误!未定义书签。
4.2数控回转工作台结构及参数设计...................... 错误!未定义书签。
4.3传动系统的设计.................................... 错误!未定义书签。
4.3.1 设计任务...................................... 错误!未定义书签。
4.3.2 传动系统方案设计.............................. 错误!未定义书签。
4.4电动机的选择...................................... 错误!未定义书签。
4.5OTT G1型蜗轮蜗杆安装说明.......................... 错误!未定义书签。
5 机械部件的设计 ......................... 错误!未定义书签。
5.1蜗轮蜗杆的设计.................................... 错误!未定义书签。
5.2蜗杆传动的热平衡计算.............................. 错误!未定义书签。
5.3蜗杆传动强度计算................................... 错误!未定义书签。
5.3.1涡轮齿面接触疲劳强度计算 ....................... 错误!未定义书签。
5.3.2 涡轮齿根弯曲疲劳强度计算...................... 错误!未定义书签。
5.4蜗杆刚度的计算.................................... 错误!未定义书签。
5.5精度等级、公差和表面粗糙度的确定.................. 错误!未定义书签。
5.6其它零部件的选择与校核............................ 错误!未定义书签。
6 润滑油的选择 ........................... 错误!未定义书签。
7其它几种常见的消隙装置.................. 错误!未定义书签。
7.1双导程蜗杆传动.................................... 错误!未定义书签。
7.1.1 双导程蜗轮蜗杆结构及间隙调整原理.............. 错误!未定义书签。
7.1.2 双导程蜗杆的优点.............................. 错误!未定义书签。
7.1.3 双导程蜗杆的缺点.............................. 错误!未定义书签。
7.1.4 双导程蜗轮蜗杆在机床设计中的应用.............. 错误!未定义书签。
7.2高精度弧面蜗杆-球面蜗轮副的加工方法............... 错误!未定义书签。
7.3一种新型蜗轮蜗杆.................................. 错误!未定义书签。
7.3.1 一种新型蜗轮蜗杆消隙装置...................... 错误!未定义书签。
7.3.2 工作原理...................................... 错误!未定义书签。
7.3.3 新型与现有技术相比............................ 错误!未定义书签。
7.4正平面一次包络环面蜗杆传动........................ 错误!未定义书签。
7.5侧隙可调式变齿厚平面蜗轮包络环面蜗杆传动.......... 错误!未定义书签。
7.6分体蜗杆结构...................................... 错误!未定义书签。
7.7双蜗杆传动机构.................................... 错误!未定义书签。
总结 ..................................... 错误!未定义书签。
致谢 ..................................... 错误!未定义书签。
参考文献 ................................. 错误!未定义书签。
1 前言1.1选题目的及研究意义1.1.1选题目的蜗轮蜗杆传动机构由于它具有传动比大、传动平稳以及结构尺寸紧凑等优点,所以在各类机械设备的传动系统及伺服驱动系统中有着广泛的应用。
随着现代传动技术的发展,对蜗杆传动的侧隙要求越来越高,以往对于像精密机床回转工作台这样有分度及定位精度要求的场合,对其蜗轮副的侧隙有较高的要求,而如今在许多机械传动场合,如制药机械、轻工食品机械、包装机械、自动传输机械等,对蜗轮蜗杆的啮合侧隙提出越来越高的要求;另一方面,由于蜗杆传动的啮合原理所决定,其不可避免地存在磨损较严重的问题,往往会出现在机器正常使用一段时间后,其啮合侧隙明显增大、传动精度降低,甚至整个设备无法正常使用。
因此,有必要对蜗轮蜗杆的啮合侧隙根据使用情况,做不断的调整,以使其始终保持在最佳状态。
由于蜗轮蜗杆传动机构都有传动副侧隙存在,侧隙用来防止由于误差和热变形而使轮齿卡住,并且给齿面间的润滑油膜留有空间。
但侧隙同时又给机构在反转时带来空程,使机构不能准确定位,从而影响了传动精度。
为了减少或消除侧隙给机构带来的不利影响,需要采用消隙系统。
在某些机械传动系统中,特别是伺服驱动系统中,对间隙的要求越来越严格,通常要求零间隙传动,这是因为传动间隙对开环伺服控制系统而言直接影响到启动及反向控制精度。
为了改善蜗轮蜗杆传动间隙,人们想了许多办法,例如,双蜗杆传动,以及改变蜗轮蜗杆的中心距法,但后者的结构较复杂,并且要有足够的实施空间,因此使用范围受到限制。
通过研究与实践,现再介绍一种可减小蜗轮蜗杆传动间隙的新方法。
1.1.2研究意义采用此传动减小蜗轮蜗杆传动间隙,调整间隙时不影响蜗轮蜗杆齿面的啮合状态,这种蜗轮副的消隙装置具有结构简单紧凑,制造容易,调整方便的优点,因而在广泛用于要求连续精确分度的结构中。
经实际使用,效果非常理想,尤其适用于空间受限制的结构中。
目前,对机床中某些要求准确传递运动的场合,如加工齿轮、花键轴等机床的分度副和一些机床的读数机构,为避免由于制造误差和蜗轮磨损所形成的过大侧隙影响传动精度,往往采用此蜗杆传动。
该蜗轮蜗杆副中的蜗杆包括两部分,蜗杆轴和蜗杆套,蜗轮的齿面有一个大的齿顶高系数,这使得蜗杆轴和蜗杆套的作用线可以分离,蜗杆轴沿蜗轮的方向旋转,而蜗杆套沿相反的方向旋转,蜗杆的一半参与驱动,而另一半则吸收蜗轮反行程的运动,这样的运动要求在很多旋转工艺中用到,特别是在机床制造业中。
1.2相关领域的研究现状、发展趋势、研究方法及应用领域1.2.1 蜗轮蜗杆研究现状近二十年来,蜗杆传动的研制取得了较大的进展,出现了各种新型的蜗杆传动与变态蜗杆传动,如滚锥、指锥或球面的二次包络环面蜗杆传动,曲率可控点接触蜗杆,超环面行星蜗杆传动等已经达到相当的水平。
尤其是利用计算机技术与图形功能参考蜗杆传动的啮合状态、齿面接触状态进行分析,对参数进行优化等方面的研究都取得了突破性的进展。
1.2.2 蜗杆传动的发展趋势目前,蜗杆传动的发展趋势主要表现在改善蜗杆传动质量的途径与措施的研究方面,主要措施有:(1)改善蜗杆副啮合瞬时接触线的形状,增大齿面接触点处的诱导曲率半径。
近出现的各种新型蜗杆传动及变态蜗杆传动,都是朝着这方面努力的结果。
(2)在共轭齿面作出“人工油涵”,为连续充分供油创造条件,使共轭齿面具备形成动压油膜的条件。
(3)重视正式使用前的低速轻载跑合规律的研究。
(4)其他措施优化设计参数;降低蜗杆、蜗轮齿面的粗糙度;合理选择蜗杆、蜗轮的材料及热处理方法;合理选择润滑的种类、粘度及润滑方式;考虑箱体散热及通气问题;采用挖窝或“b传动”等办法,除去蜗轮齿面上接触线不理想的区域;采用非对偶法加工蜗轮轮齿,以控制啮合区;使线接触的共轭齿面变为可控点接触的共轭齿面。
1.2.3、研究方法由于蜗轮与蜗杆的外形比较复杂,如果应用传统方法经行绘制,不仅过程繁琐,效率低,而且容易出错。
随着计算机辅助设计技术的发展,三维造型与复杂曲面造型技术的应用越来越广泛。
PRO/E是由美国PTC公司推出的一款CAD/CAM软件,其单一数据结构特点实现了零件的三维参数设计和尺寸驱动。
所以应用PRO/E软件进行蜗轮蜗杆的三维参数化设计,可以很好地解决二维CAD技术设计中最别捏的几个问题,如复杂的投影线生成问题、设计的更新与修改问题、数据的有效再利用问题等等,大大提高了设计效率。