最新度化工及危险化学品事故分析0223汇总
2023年全国安全生产事故案例

2023年全国安全生产事故案例1. 矿井透水事故:2023年某省一座煤矿发生了一起严重的透水事故,导致多名矿工被困井下,其中几人不幸遇难。
事故原因是矿井管理不善,未及时进行井下排水处理,导致地下水涌入井下,使矿工无法及时逃生。
2. 建筑坍塌事故:2023年某城市一座正在施工的高楼项目发生了坍塌事故,多名工人被埋压,造成重大人员伤亡。
事故的主要原因是施工方在施工过程中存在违规操作,导致建筑结构不稳定,最终导致楼体坍塌。
3. 化工厂爆炸事故:2023年某化工厂发生严重爆炸事故,造成大量有毒气体泄漏和火灾,并对周边居民造成严重影响。
事故起因是化工厂管理不善,未能及时发现和处理设备故障,导致事故的发生。
4. 交通事故:2023年某高速公路发生连环交通事故,多辆车相撞,造成多人伤亡。
事故的主要原因是驾驶员超速行驶,并且存在疲劳驾驶、违规变道等交通违法行为。
5. 工业火灾事故:2023年某工业区一家化工企业发生火灾,火势迅速蔓延,造成大面积厂房被烧毁,多名工人被困。
事故的起因是企业未按照相关安全规定进行火灾防控措施,导致火灾无法及时扑灭。
6. 建筑起重机倾倒事故:2023年某城市一处建筑工地发生起重机倾倒事故,导致周围建筑物受损,多人受伤。
事故原因是起重机操作不当,超负荷作业,导致起重机失稳倾倒。
7. 化学品泄漏事故:2023年某化学品仓库发生泄漏事故,大量有毒化学品外泄,造成周边居民中毒和环境污染。
事故起因是仓库储存管理不善,未能及时发现和处理泄漏情况。
8. 网络安全事故:2023年某大型互联网企业遭受黑客攻击,导致用户的个人信息泄露,引发广泛关注和用户恐慌。
事故原因是企业网络安全措施不足,未能及时发现并阻止黑客入侵。
9. 船只沉没事故:2023年某海域一艘客轮发生沉没事故,导致多名乘客和船员失踪或遇难。
事故原因是船只维护不当,航行时遭遇恶劣天气,无法应对突发状况。
10. 高空坠落事故:2023年某施工现场发生高空坠落事故,一名工人从高处坠落身亡。
2023版危险化学品典型事故案例汇编

2023版危险化学品典型事故案例汇编序尊敬的读者:在过去的几十年间,危险化学品事故时有发生,给人民裙众的生命财产安全带来了严重的危害。
为了更好地总结和借鉴过去的事故经验,预防和减少类似事故的发生,特编撰了《2023版危险化学品典型事故案例汇编》。
该汇编旨在通过对典型事故案例的详细描述和分析,为相关行业和部门提供宝贵的经验和教训,帮助大家更好地认识和防范危险化学品事故,确保人民裙众的生命财产安全。
一、案例一:某化工企业爆炸事故在某化工企业生产车间内,由于操作人员操作不当,导致有机溶剂泄漏,引发了一起严重的爆炸事故。
事故发生后,有机溶剂蒸气弥散到了整个车间,火源一触即燃,造成了严重的人员伤亡和财产损失。
二、案例二:危险品运输车辆事故某危险品运输车辆在行驶途中因超速、疲劳驾驶等原因失控侧翻,导致危险品泄漏,污染了周围环境,对当地居民造成了严重的危害。
三、案例三:储罐泄漏事故某化工园区内的储罐因腐蚀严重,发生泄漏。
由于施工作业不当,泄漏的危险化学品流入了周围的水源,造成了严重的环境污染和生态损害。
四、案例四:化学品火灾事故某化工厂的仓库发生了化学品火灾,由于应急措施不力,火势迅速蔓延,造成了大面积的火灾灾害,严重威胁到了周边居民的生命财产安全。
五、案例五:化学品中毒事故某化工企业的员工因接触到有毒化学品,导致中毒,严重危害了员工的身体健康。
后续调查发现,是由于化工企业没有做好有毒化学品的防护措施和培训教育工作。
六、案例六:化学品溢漏污染事故某化工企业的成品仓库发生了化学品溢漏事故,导致周围环境受到了污染,当地居民的生活受到了严重的影响。
七、案例七:危险化学品事故应急处理不当某企业发生了危险化学品事故后,应急处理不当,导致了事故的扩大化和严重后果。
相关部门因为缺乏应对危险化学品事故的经验,未能及时采取有效措施,造成了不必要的损失。
八、案例八:危险化学品事故隐瞒失实某企业发生了危险化学品事故后,企业隐瞒了真相,导致了公众的恐慌和不信任。
化工行业安全事故案例分析报告

化工行业安全事故案例分析报告化工行业安全事故案例分析报告一、案例概述该案例是发生在某化工公司的一起重大安全事故。
事故发生在某年某月某日,造成了重大人员伤亡和财产损失。
事故的起因是某操作工不按规程操作,导致化学反应错误,再加上相关设备的故障,最终引发了一系列爆炸和火灾。
二、事故原因分析1.操作工不按规程操作:事故发生时的操作工因为工作经验不足和对操作规程不熟悉,没有按照规定的步骤进行操作,导致了化学反应的错误。
2.设备故障:与操作工的错误操作相结合,事故中发生了设备故障,导致反应条件的控制失效,反应产生的能量无法得到及时和有效的排放,进而引发了爆炸和火灾。
3.安全管理不到位:化工公司在工艺设计、设备维修和人员培训等方面的安全管理措施不到位。
工艺设计中应该有考虑设备的安全性和稳定性,并设置合适的技术和管理措施。
设备维修应及时维护,确保设备运行的正常和安全。
人员培训应强调工作流程和操作规程,确保员工对于化工操作的安全意识和操作能力。
三、事故影响及教训1.人员伤亡:事故导致多名员工和附近居民受伤,其中包括数名员工重伤和一些居民中毒。
这是一起十分严重的人身伤害事故,提醒我们在化工行业安全管理中,更要重视人身安全。
2.财产损失:事故导致了大量的生产设备损坏和化工品泄漏,造成了巨大的经济损失。
这一点提醒我们在安全管理中注重资源的保护和风险的控制。
3.环境污染:爆炸和火灾导致了大量的有毒气体和废水的排放,对周边的土壤、水源和空气环境造成了严重的影响。
化工行业必须要考虑环境保护和可持续发展,确保生产过程中不对环境造成不可逆转的损害。
四、防范措施和对策1.完善安全管理制度:加强安全管理,建立健全的安全管理制度和工艺管控体系,明确责任划分和操作规程,确保员工按照规定进行操作,减少人为失误的发生。
2.提高员工技能和安全意识:加强员工培训,提高员工的操作技能和安全意识,确保操作人员具备足够的知识和技能,理解危险源及应对方法。
2023年度山东省化工及危化品事故分析报告
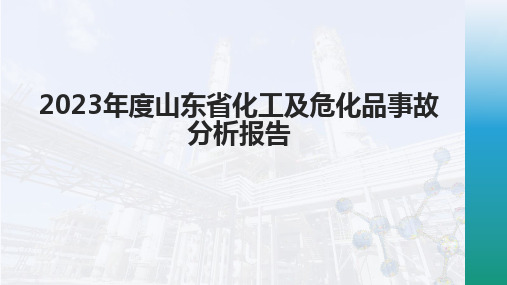
Catalogue
目录
一、2023年全省危化领域事故基本情况 二、事故分布情况 三、典型事故案例 四、事故原因分析 五、事故防范措施和建议
2023年全省危化领域事故基本情况
(一)事故基本情况
2023年,全省化工行业和危险化学品领域共发生事 故13起、死亡21人,同比(2022年9起、10人)事故起 数增加4起,上升44.4%;死亡人数增加11人,上升 110%。其中一般事故11起、死亡7人;较大事故1起、死 亡4人;重大事故1起、死亡10人。涉及危险化学品企业 事故7起,一般化工企业事故6起。另外,全年接报火灾 险情6起(按规定未纳入事故统计范围),均未造成人 员伤亡。
(二)事故概况
时间 2023年5月18日 2023年7月28日 2023年9月14日 2023年9月26日
2023年11月15日
2023年12月23日
全省化工行业和危险化学品领域事故(13起) 事故概况
山东润中药业有限公司发生一起一般伤害事故,造成1人中指受伤,直接经济损失1500余元。 威海市明珠硅胶有限公司筛选车间一名员工作业时触电受伤,送医经抢救无效死亡,直接经济损失约150万元。 东明旭阳化工有限公司二期双氧水装置纯化单元发生爆炸事故,未造成人员伤亡,直接经济损失约378.7万元。 山东惠亚环保科技有限公司亚氯酸钠固体车间西侧发生一起轻微伤事故,造成1人受伤。 山东莱州福利泡花碱有限公司在拆除3#泡花碱生产线窑炉过程中发生坍塌事故,造成4人死亡、4人受伤,事故 直接经济损失约702万元。 中国石化齐鲁分公司烯烃厂发生裂解气泄漏闪爆,造成1人死亡、4人受伤。
临淄区凤凰镇的淄博齐龙化工有限公司发生一起火灾事故,直接经济损失5万元。
危险化学品事故案例分析大全

危险化学品事故案例分析大全危险化学品事故是指在化学品生产、储存、运输、使用等过程中,因违反安全操作规程或存在安全隐患而导致的爆炸、火灾、泄露等事故。
这些事故不仅对人员和环境造成了严重伤害,也给社会稳定和经济发展带来了巨大的负面影响。
以下是几起危险化学品事故案例分析。
1.天津港危险化学品仓库爆炸事件天津港危险化学品仓库在2024年8月发生了一起严重爆炸事故,造成173人死亡,数百人受伤。
这起事故的起因是仓库管理不规范,存储大量违规进口的危险化学品,并未进行充分的安全检查和储存措施。
同时,港口当地政府监管不力,对危险化学品行业缺乏有效监管,导致了这起重大事故的发生。
2. 美国Bhopal化工厂泄漏事件1984年12月,印度Bhopal市的一家化工厂发生了致命的气体泄漏事故,导致数千人死亡和成千上万人受伤。
这是当时世界上最严重的化学品事故之一、事故的起因是化工厂不当操作和缺乏安全设备,导致甲醛和异氰酸甲酯等危险物质泄漏。
此外,厂方对泄漏事故上报和紧急响应不及时,加剧了事故的严重程度。
3.日本东京地铁沙林毒气袭击1995年3月,日本东京地铁系统发生了一起恐怖袭击,成员来自Aum Shinrikyo新興宗教组织。
他们在地铁中同时释放了沙林毒气,导致12人死亡和上千人受伤。
沙林是一种神经毒剂,对人体具有极高的毒性。
这次事件揭示了国内恐怖主义和化学武器的威胁,引起了全球的关注。
这些事故案例揭示了危险化学品事故的起因和影响。
首先,不合规操作和缺乏有效的安全措施是事故发生的主要原因。
许多事故是由于违反操作规程、使用不合格设备或仓库管理不善而导致的。
其次,政府和监管机构的监管不力也是事故发生的原因之一、缺乏有效的监管和处罚制度使得安全隐患不能及时发现和纠正。
此外,恐怖主义和化学武器的威胁也需要引起全球的高度警惕。
为预防和减少危险化学品事故的发生,我们应该加强对危险化学品行业的监管和安全管理。
厂家要建立完善的安全管理系统,确保在生产和储存过程中遵循规范操作和使用合格设备。
2023年危险化学品典型事故案例操作工反思

2023年危险化学品典型事故案例操作工反思一、案件概述1.1 事故背景2023年某化工企业发生了一起严重的危险化学品事故,导致了严重的人员伤亡和环境污染。
该企业生产的化学品是一种高度腐蚀性的物质,事故发生在生产车间。
据初步调查,事故原因是操作工在操作过程中未能遵守相关安全操作规程,导致化学品泄漏,引发爆炸并造成严重后果。
1.2 事故影响此次事故导致了多人逝去、伤残,另外环境污染严重,损失巨大。
造成了巨大的社会影响和舆论压力,也给企业及相关责任人带来了严重的法律及经济上的问题。
二、事故原因分析2.1 安全制度不健全该企业在安全管理方面存在着明显的问题,安全制度不够完善,相关人员对安全规定的重视程度不够,也缺乏相关的安全培训,从而导致了操作人员对于化学品操作的认识不足,安全意识不强。
2.2 操作工作作风不严谨操作工在操作过程中存在很多不规范的行为,比如未戴防护装备、操作疏忽大意等,这些都是直接导致事故发生的原因。
2.3 缺乏事故应急预案在事故发生后,该企业缺乏有效的事故应急预案和措施,导致了事故的进一步恶化和后果扩大。
三、操作工反思3.1 安全意识不强在此次事故中,操作工的安全意识明显不够强,未能将安全放在首位,导致了事故的发生。
操作工应该明白安全是第一位的,任何操作都要以安全为前提。
3.2 对安全规定的漠视在日常工作中,操作工对于安全规定的漠视现象十分严重,很多操作工认为戴防护装备等只是多此一举的规定,未能真正理解安全规定的重要性。
3.3 规范操作行为操作工应该认真对待每一个操作步骤,尤其是在操作危险化学品时,更应该严格按照操作规程来进行,不能大意马虎。
3.4 加强安全培训企业应该加强对操作工的安全培训,让操作工明白安全的重要性,并通过教育让他们养成良好的安全习惯。
四、预防措施4.1 完善安全制度企业应该完善安全制度,将安全作为企业生产经营的首要任务,建立健全的安全管理制度,对相关人员进行严格的安全教育和培训。
化工厂事故报告总结范文

一、事故概述2023年3月10日,某市某化工厂发生一起爆炸事故,造成5人死亡、8人受伤,直接经济损失约1000万元。
事故发生后,市政府高度重视,立即成立了事故调查组,对事故原因进行了深入调查。
现将事故调查结果及总结报告如下。
二、事故原因分析1. 直接原因(1)设备老化:事故发生地点的设备使用年限较长,部分部件存在磨损、腐蚀等问题,导致设备承载能力下降。
(2)违规操作:事故发生时,操作人员未按照操作规程进行操作,违反了“先通风、再检测、后作业”的原则。
(3)安全意识淡薄:部分员工安全意识不强,对事故隐患视而不见,未及时报告。
2. 间接原因(1)管理不到位:企业安全管理责任制不明确,安全教育培训不到位,安全检查制度不健全。
(2)监管不到位:相关部门对化工厂的监管力度不够,未能及时发现和消除事故隐患。
三、事故处理及整改措施1. 事故处理(1)对事故责任人进行严肃处理,追究其刑事责任。
(2)对事故遇难者家属进行慰问,给予合理赔偿。
(3)对受伤人员给予救治,确保其生命安全。
2. 整改措施(1)加强设备维护保养,及时更换老化设备,提高设备承载能力。
(2)强化安全教育培训,提高员工安全意识,确保操作规程得到严格执行。
(3)完善安全检查制度,加强日常安全检查,及时发现和消除事故隐患。
(4)落实企业安全管理责任制,明确各级管理人员的安全职责。
(5)加大监管力度,对化工厂进行全面排查,确保安全生产。
四、事故总结本次化工厂爆炸事故暴露出企业在安全生产管理方面存在的问题,为防止类似事故再次发生,必须采取以下措施:1. 提高安全生产意识,加强安全教育培训。
2. 完善安全生产管理制度,落实企业安全管理责任制。
3. 加强设备维护保养,提高设备承载能力。
4. 加大监管力度,确保安全生产。
5. 强化应急处理能力,提高事故应急处置水平。
通过本次事故的总结,我们深刻认识到安全生产的重要性,将进一步强化安全生产意识,落实安全生产责任,为全市安全生产形势稳定作出贡献。
2022年15个化工行业安全事故典型案例解析

另外再延伸一下,固废处理车间也属于环保设施的范畴,最近两年,确实发生了不少环保设 施的事故案例,基于此,在2022年12月23日,国务院安委办和生态环境部、应急管理部联合发布 了17号文《关于进一步加强环保设备设施安全生产工作的通知》,旨在加强化工企业内环保设施 和设备的安全管理,相信在2023年期间,各类型的环保设施类工程项目,应该会面临和主体工程 同样的监督管理,包括三同时制度、专篇审核、风险评估论证等等。
2022年4月16日5时,位于淄博市临淄区的中国 石油化工股份有限公司齐鲁分公司炼油厂发生一 起坍塌事故,造成1人死亡,直接经济损失180万 元。
事故阶段 关键装置 作业环节 涉及行业 涉及危化品
运行
罐区
违章操作
冶金
煤焦油
开停工
工艺装置
违章操作
石油化工
乙烯、丙烯、 乙烷、丙烷
检维修
工艺装置
有限空间 作业
石油化工 冶金 精细
涉及危化品 蒽油 \ 石脑油
玻璃鳞片 甲醇、氨气
事故案例概况
事故名称
时间
开远市龙腾冶炼厂 “3·23”煤焦油储 罐火灾事故
2022/3/2 3
中国石油化工股份有 限公司茂名分公司 “3·30”一般油化工股份有 限公司齐鲁分公司 “4·16”坍塌事故
受伤。
运行
实验室
违章操作
石油化工
茂金属催 化剂
广西奕安泰药业有限公 司“10·4”一般着火 事故
危险化学品事故案例分析与教训总结
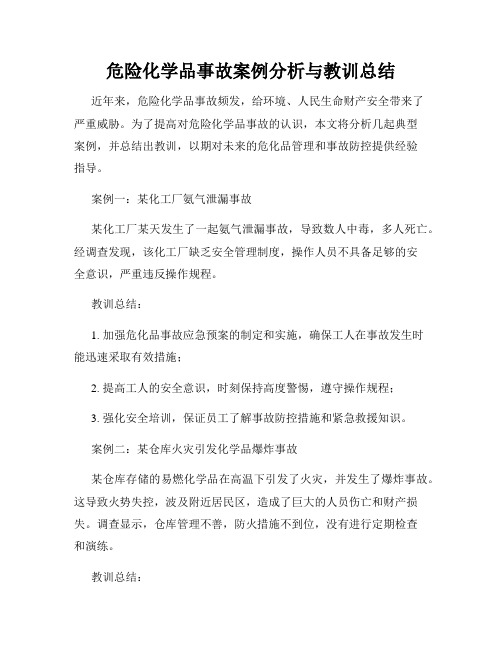
危险化学品事故案例分析与教训总结近年来,危险化学品事故频发,给环境、人民生命财产安全带来了严重威胁。
为了提高对危险化学品事故的认识,本文将分析几起典型案例,并总结出教训,以期对未来的危化品管理和事故防控提供经验指导。
案例一:某化工厂氨气泄漏事故某化工厂某天发生了一起氨气泄漏事故,导致数人中毒,多人死亡。
经调查发现,该化工厂缺乏安全管理制度,操作人员不具备足够的安全意识,严重违反操作规程。
教训总结:1. 加强危化品事故应急预案的制定和实施,确保工人在事故发生时能迅速采取有效措施;2. 提高工人的安全意识,时刻保持高度警惕,遵守操作规程;3. 强化安全培训,保证员工了解事故防控措施和紧急救援知识。
案例二:某仓库火灾引发化学品爆炸事故某仓库存储的易燃化学品在高温下引发了火灾,并发生了爆炸事故。
这导致火势失控,波及附近居民区,造成了巨大的人员伤亡和财产损失。
调查显示,仓库管理不善,防火措施不到位,没有进行定期检查和演练。
教训总结:1. 强化仓库管理,确保存储的危险化学品符合规范,做好危险品分类存放和标识;2. 加强防火措施,确保防火设施完善、灭火准备充分;3. 定期进行火灾演练和应急预案的训练,增强员工逃生和灭火的能力。
案例三:某化工企业泄露毒性气体事故某化工企业由于管道泄漏,导致毒性气体泄露,数十名员工中毒,数人死亡。
经查,企业缺乏管道泄漏的监测系统,员工缺乏及时正确的应急处理方案。
教训总结:1. 建立完善的气体泄漏监测系统,及时发现危险情况;2. 提供员工给予及时有效的应急处理培训;3. 定期检查和维护管道,确保安全运营。
结语:以上案例仅仅是危险化学品事故中的几个典型例子,通过这些案例的分析和总结,我们得出了一些重要的教训。
危险化学品事故的发生往往是由于管理不善、操作不当和监管不到位所导致。
因此,为了防止危化品事故的发生,我们要加强安全管理,提高员工安全意识,定期进行培训和演练,并加大监管力度,确保危化品行业的安全运营。
化工行业安全事故案例及分析

化工行业安全事故案例及分析目录一、化工行业安全事故概述 (2)1.1 行业特点与安全风险点介绍 (3)1.2 事故频发原因分析 (4)1.3 安全事故造成的严重后果 (5)二、典型化工安全事故案例分析 (6)2.1 爆炸事故案例分析 (7)2.1.1 事故经过与救援过程 (9)2.1.2 事故原因调查结果 (10)2.1.3 预防措施与教训总结 (10)2.2 泄漏事故案例分析 (12)2.2.1 泄漏事故的类型与特点 (13)2.2.2 典型泄漏事故案例分析 (13)2.2.3 泄漏事故预防措施 (15)2.3 火灾事故案例分析 (17)2.3.1 火灾事故成因及危害 (18)2.3.2 化工火灾的扑救难点 (19)2.3.3 火灾事故案例详解 (21)2.3.4 防火措施与建议 (22)三、事故原因深度分析 (24)3.1 设备故障与安全事故关系 (25)3.1.1 设备缺陷与事故发生概率 (27)3.1.2 设备维护与检测的重要性 (28)3.1.3 设备故障导致的事故案例分析 (29)3.2 人为因素与安全事故关联分析 (30)3.2.1 操作失误对事故的影响 (31)3.2.2 安全培训与人员管理的重要性 (32)3.2.3 人为因素导致的事故案例分析 (33)四、安全事故应急救援与处置策略探讨 (34)4.1 应急救援体系建设现状与挑战 (35)4.1.1 现有应急救援体系存在的问题分析 (36)4.1.2 加强应急救援体系建设的必要性 (37)4.1.3 国内外先进救援经验借鉴 (38)4.2 事故现场应急处置技术与方法探讨 (40)4.2.1 常见化工事故现场处置技术介绍 (42)4.2.2 不同类型事故的处置策略探讨 (43)4.2.3 现场指挥与协调的重要性及方法论述 (44)五、化工行业安全事故预防措施与建议措施实施方案设计研究 (46)一、化工行业安全事故概述随着化工行业的快速发展,生产过程中的安全问题日益凸显。
化工安全管理中的事故案例与教训总结
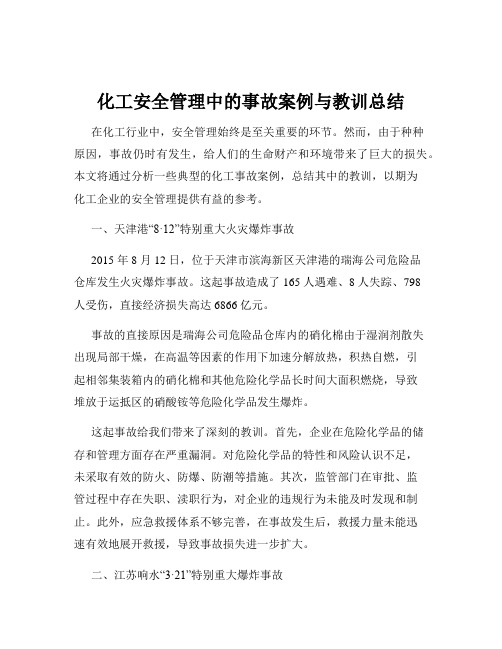
化工安全管理中的事故案例与教训总结在化工行业中,安全管理始终是至关重要的环节。
然而,由于种种原因,事故仍时有发生,给人们的生命财产和环境带来了巨大的损失。
本文将通过分析一些典型的化工事故案例,总结其中的教训,以期为化工企业的安全管理提供有益的参考。
一、天津港“8·12”特别重大火灾爆炸事故2015 年 8 月 12 日,位于天津市滨海新区天津港的瑞海公司危险品仓库发生火灾爆炸事故。
这起事故造成了 165 人遇难、8 人失踪、798人受伤,直接经济损失高达 6866 亿元。
事故的直接原因是瑞海公司危险品仓库内的硝化棉由于湿润剂散失出现局部干燥,在高温等因素的作用下加速分解放热,积热自燃,引起相邻集装箱内的硝化棉和其他危险化学品长时间大面积燃烧,导致堆放于运抵区的硝酸铵等危险化学品发生爆炸。
这起事故给我们带来了深刻的教训。
首先,企业在危险化学品的储存和管理方面存在严重漏洞。
对危险化学品的特性和风险认识不足,未采取有效的防火、防爆、防潮等措施。
其次,监管部门在审批、监管过程中存在失职、渎职行为,对企业的违规行为未能及时发现和制止。
此外,应急救援体系不够完善,在事故发生后,救援力量未能迅速有效地展开救援,导致事故损失进一步扩大。
二、江苏响水“3·21”特别重大爆炸事故2019 年 3 月 21 日,江苏省盐城市响水县陈家港镇化工园区内的江苏天嘉宜化工有限公司发生特别重大爆炸事故,造成 78 人死亡、76 人重伤,640 人住院治疗,直接经济损失达 19863507 万元。
事故的直接原因是天嘉宜公司长期违法贮存的硝化废料持续积热升温导致自燃,燃烧引发爆炸。
从这起事故中,我们可以看到企业安全意识淡薄,为了追求经济利益,无视安全生产法规和标准,违规储存危险化学品。
同时,地方政府和相关部门在安全监管方面存在宽松软的问题,对企业的违法违规行为监管不力。
此外,企业在安全风险评估和隐患排查治理方面存在严重不足,未能及时发现和消除潜在的安全隐患。
2023年危险化学品典型事故案例反思

2023年危险化学品典型事故案例反思近年来,我国化学工业发展迅速,危险化学品的使用和生产也日益增加。
然而,由于管理不善、监管不力等原因,一些危险化学品企业发生了严重事故,造成了严重的人员伤亡和环境污染。
为了避免类似的事故再次发生,我们有必要对2023年发生的几起典型危险化学品事故进行反思和总结。
一、事故概况1.1 事故12023年某省某化工企业发生爆炸事故,造成了十几人逝去,数十人受伤,直接经济损失数百万元。
据初步调查,该企业生产的危险化学品存储管理存在严重安全隐患,事故原因正在进一步调查中。
1.2 事故2同年某市一化工厂发生泄漏事故,数十吨有毒化学品外泄,造成周边居民疏散,环境受到污染。
据初步调查,事故是由于化工厂未能及时发现管道泄漏,导致有毒化学品外泄。
二、事故原因分析2.1 企业管理不善在事故1中,该化工企业存储管理的危险化学品存在严重安全隐患,缺乏必要的监测和保障措施。
企业管理层对危险化学品的重要性和安全性认识不足,缺乏相关的管理经验和技术支持,导致安全事故发生的可能性增加。
2.2 监管不力在事故2中,化工厂未能及时发现管道泄漏,这表明监管部门在化工厂的监管与督促方面存在一定的疏漏。
监管部门对危险化学品企业的安全生产监管不到位,缺乏有效的监测手段和技术支持,导致事故的发生和处理不及时。
三、反思与总结3.1 加强企业管理危险化学品企业应加强对危险化学品的管理,建立健全的安全生产管理体系,加强对危险化学品的储存、运输、使用和处理的监测和保障措施,提高企业管理层和员工的安全生产意识,确保企业生产运营的安全稳定。
3.2 加强政府监管政府监管部门应加强对危险化学品企业的监管与督促,建立完善的监测手段和监管体系,确保危险化学品企业的安全生产,及时发现和处理安全隐患,加大对违规企业的处罚力度,提高监管的有效性。
3.3 完善法律法规国家应进一步加强对危险化学品的管理和法规制定,完善相关法律法规,规范危险化学品的生产、储存、运输和使用,提高危险化学品企业的管理水平和技术水平,加强对危险化学品企业的安全生产监督与指导。
2023年化工企业典型事故案例分析

2023年化工企业典型事故案例分析概述化工企业是一种高风险的行业,常常涉及到危险化学品的生产、储存和运输。
然而,由于一系列因素,化工企业在生产过程中往往会发生事故。
本文将分析2023年发生的一起化工企业典型事故案例,揭示案例中的原因和教训,以期提醒行业从业人员重视安全,并加强事故防范。
案例描述2023年5月,某化工企业发生了一起重大事故,导致多人死亡和严重的环境破坏。
该企业是一家生产硫酸的化工厂,拥有先进的生产设备和工艺。
然而,在该事故中,一台新装的设备发生了爆炸,导致硫酸泄漏,造成了重大后果。
据初步调查,事故的起因是该新装设备的设计缺陷以及操作人员的错误操作。
设备的设计缺陷导致了操作不当的风险增加,而操作人员对于设备的使用和维护了解不足,进一步加剧了事故的发生。
案例分析1.设备设计缺陷在该事故中,新装设备的设计存在缺陷。
这个缺陷可能是由于设计师对设备性能不了解导致的。
设计师应对设备进行更充分的测试和验证,以确保其安全性和稳定性。
在设计阶段,还应该考虑到设备的可靠性和易用性,以降低事故发生的概率。
2.操作人员的错误操作另一个导致事故发生的因素是操作人员的错误操作。
操作人员对新装设备的操作和维护了解不足,无法妥善处理设备出现的异常情况。
在这种情况下,操作人员应该接受更全面的培训,并且需要有更严格的标准操作程序来规范操作行为。
此外,还应定期进行设备操作和维护的演练,以提高操作人员的应急处理能力。
3.安全管理不到位事故的发生还暴露出企业的安全管理不到位。
可能是因为企业重视度不够,没有将安全管理纳入到企业发展战略中。
在化工企业中,安全管理应该是每个人的责任,包括管理层、员工和相关合作伙伴。
企业应该建立完善的安全管理体系,并定期进行安全培训和检查。
教训和改进措施从这起事故案例中,我们可以得出以下教训和改进措施:1.设备设计阶段应更加重视安全性和稳定性,进行全面的测试和验证。
2.操作人员应接受全面的培训,并且需要有更严格的标准操作程序来规范操作行为。
2023年化工企业安全事故总结心得

2023年化工企业安全事故总结心得(____字)1.引言2023年是化工企业安全事故频发的一年, 一系列重大安全事故不仅造成了人员伤亡和财产损失, 也对社会环境产生了严重影响。
通过对这些安全事故的总结和分析, 我们能够汲取教训并从中吸取经验, 进一步提高化工企业的安全管理水平, 预防类似事故的再次发生。
本文将总结2023年发生的化工企业安全事故, 并提出相关的心得和建议。
2.事故总结2.1 事故一: XX化工厂爆炸事故2023年6月, XX化工厂发生了一起爆炸事故, 造成3人死亡, 数十人受伤。
经调查发现, 这起事故是由于操作工人在生产过程中未按照操作规程操作, 并且存在违规操作的情况, 导致反应釜发生爆炸。
2.2 事故二: XX石化公司泄漏事故2023年9月, XX石化公司发生了一起化学品泄漏事故, 造成周边地区空气污染, 大量农作物受损。
经调查发现, 事故是由于管道老化和设备维护不当引起的, 漏油措施不及时导致泄漏。
2.3 事故三: XX化工公司火灾事故2023年12月, XX化工公司发生了一起火灾事故, 造成2人死亡, 重要设备和产品受损。
经调查发现, 该公司安全生产管理混乱, 未进行火灾演练和危险品储存管理, 且没有建立完善的应急预案, 导致火灾无法及时有效控制。
3.事故分析3.1 工艺风险管理不到位在发生的化工企业安全事故中, 存在工艺风险管理不到位的情况。
操作工人未按照操作规程进行操作, 违规操作导致了事故的发生。
此外, 设备老化和维护不当也是事故发生的重要原因。
3.2 安全管理缺乏监管和执行力度在事故调查中, 发现部分化工企业安全管理存在一定问题。
例如, 未能建立完善的应急预案, 没有进行日常的安全巡检和培训, 未组织定期的演练等。
这些管理上的疏漏导致事故发生后无法及时、有效地应对。
4.心得与建议4.1 加强安全管理体系建设化工企业应建立完善的安全管理体系, 包括制定安全管理制度、明确安全生产责任、落实安全培训和考评等方面。
危险化学品的事故案例分析与教训总结
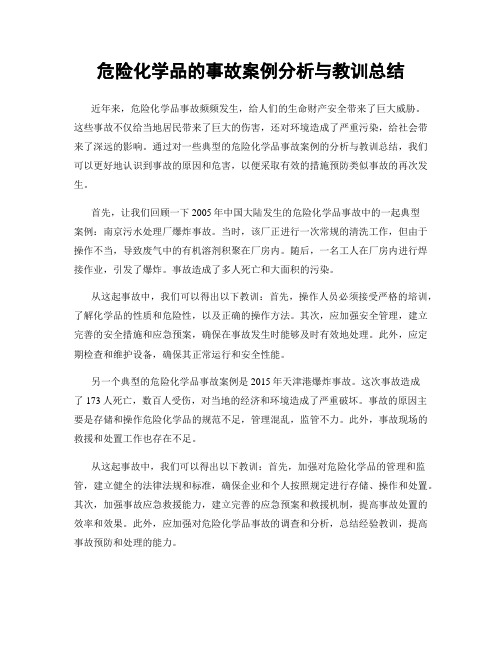
危险化学品的事故案例分析与教训总结近年来,危险化学品事故频频发生,给人们的生命财产安全带来了巨大威胁。
这些事故不仅给当地居民带来了巨大的伤害,还对环境造成了严重污染,给社会带来了深远的影响。
通过对一些典型的危险化学品事故案例的分析与教训总结,我们可以更好地认识到事故的原因和危害,以便采取有效的措施预防类似事故的再次发生。
首先,让我们回顾一下2005年中国大陆发生的危险化学品事故中的一起典型案例:南京污水处理厂爆炸事故。
当时,该厂正进行一次常规的清洗工作,但由于操作不当,导致废气中的有机溶剂积聚在厂房内。
随后,一名工人在厂房内进行焊接作业,引发了爆炸。
事故造成了多人死亡和大面积的污染。
从这起事故中,我们可以得出以下教训:首先,操作人员必须接受严格的培训,了解化学品的性质和危险性,以及正确的操作方法。
其次,应加强安全管理,建立完善的安全措施和应急预案,确保在事故发生时能够及时有效地处理。
此外,应定期检查和维护设备,确保其正常运行和安全性能。
另一个典型的危险化学品事故案例是2015年天津港爆炸事故。
这次事故造成了173人死亡,数百人受伤,对当地的经济和环境造成了严重破坏。
事故的原因主要是存储和操作危险化学品的规范不足,管理混乱,监管不力。
此外,事故现场的救援和处置工作也存在不足。
从这起事故中,我们可以得出以下教训:首先,加强对危险化学品的管理和监管,建立健全的法律法规和标准,确保企业和个人按照规定进行存储、操作和处置。
其次,加强事故应急救援能力,建立完善的应急预案和救援机制,提高事故处置的效率和效果。
此外,应加强对危险化学品事故的调查和分析,总结经验教训,提高事故预防和处理的能力。
除了以上两起典型的危险化学品事故案例,还有许多其他的事故也给我们敲响了警钟。
例如,2013年美国德克萨斯州的一起化学品仓库爆炸事故,事故导致多人死亡和大面积的破坏。
事故的原因主要是存储和操作危险化学品的安全管理不当,监管不力。
2023危化事故总结

2023危化事故总结引言2023年是危化事故频发的一年,各地发生了多起严重的危化事故,给环境和人民的生命财产带来了巨大的损失。
本文将对2023年发生的危化事故进行总结,探讨其原因和教训,并提出预防危化事故的建议。
一、事故概述在2023年,全球范围内发生了多起大规模的危化事故,其中包括工厂爆炸、油罐车事故、化学品泄漏等。
这些事故造成了大量的人员伤亡和环境污染,给社会带来了巨大的影响。
1. 工厂爆炸事故2023年期间,全球多个工业区发生了多起工厂爆炸事故。
这些爆炸造成了严重的人员伤亡和财产损失,同时也引发了环境污染问题。
2. 油罐车事故油罐车事故是2023年危化事故中另一个重要的组成部分。
在运输过程中,由于各种原因,油罐车发生泄漏或爆炸,导致油料泄漏,污染环境。
3. 化学品泄漏事故化学品泄漏事故也属于2023年的危化事故的一部分。
在化工厂和仓库等地,由于操作不当或设备故障,导致有害化学品泄漏,危及周围环境和人员的安全。
二、事故原因分析2023年发生的危化事故,往往可以归咎于以下几个主要原因:1. 管理不善部分事故的发生可以追溯到企业的管理不善。
一些企业存在安全生产意识不强,缺乏有效的安全管理制度和培训措施,导致事故的发生。
2. 设备老化危化事故中的一部分事故可以归因于设备老化。
一些企业没有及时对设备进行检修和更换,设备运行过程中出现故障,从而导致事故的发生。
3. 人为失误部分事故是由于人为失误所致。
操作人员对操作规程不熟悉、违章操作、驾驶员疲劳驾驶等因素都可能导致事故的发生。
三、事故教训和启示从2023年的危化事故中,我们可以得到以下教训和启示:1. 加强安全管理企业应加强对安全管理的重视,建立健全的安全管理制度,加强员工的安全意识和培训,确保安全生产。
2. 加强设备维护和更换企业应定期检修设备,确保设备的可靠性和安全性。
同时,当设备达到安全寿命时,应及时更换,避免设备老化引发事故。
3. 严格执行操作规程操作人员应严格执行操作规程,提高操作规范性和安全意识,避免因为操作不当而导致事故的发生。
2022年度危险化学品安全事故典型案例解析

2022年度危险化学品安全事故典型案例解析
纵观整个2022年,化工企业安全生产的总体形势还是比较平稳的,全国范围内未发生一起涉及危险化学品的重特大事故。
另外2022年也是国务院安委办《危险化学品安全专项整治三年行动实施方案》的收官之年,可以说,经过三年坚持不懈的努力,危险化学品企业安全生产事故从根本上得到了有效遏制,国家对危险化学品企业的安全风险防范和化解取得了明显成效,且危险化学品企业自身的安全管理水平得到了大幅度提升。
这来之不易的成就背后,更是离不开应急管理部门的持续监管、专家指导服务的辛勤付出和行业协会机构的赋能支持。
当然2022年度依然发生了不少危险化学品安全事故,其中不少事故也是非常令人遗憾和惋惜的,一个个鲜活的生命戛然而止,回顾这一幕幕令人痛心疾首的事故,唯有吸取事故的惨痛教训,保持对安全的永恒敬畏,才是我们对事故最好的缅怀!
2022年度最具典型性的危险化学品事故案例,一共收录了15个案例,先以PPT的形式在这里分享给大家。
化工企业安全生产事故案例分析汇总
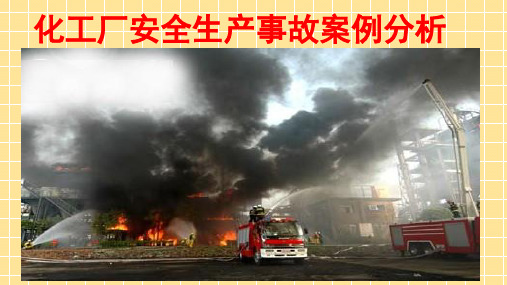
危险化学品企业的特点决定:
在作业活动中,一旦操作条件(温度、压力、液位、 流速)变化,工艺过程受到干扰产生异常或人为因 素造成误操作,设备及其附属附件和人员管理不 当或使用不合理等,潜在的危险(风险)就会发 展成为灾害性事故。
事故案例目录
第一章:叉车事故案例及分析
视
频: 叉车司机教育片
事故发生后,一车间被全部炸毁,北侧地面被炸 成一东西长14.70米,南北长13.50米的椭圆形爆坑, 爆坑中心深度3.67米。8台反应釜中,两台被炸 碎,三台被炸成两截或大片,三台反应釜完整。 一车间西侧的二车间框架主体结构损毁严重,设 备、管道严重受损;东侧动力站西墙被摧垮,控 制间控制盘损毁严重;北侧围墙被推倒;南侧六 车间北侧墙体受损;整个厂区玻璃多被震碎。经 计算,事故爆炸当量相当于6.05吨TNT。
事故案例目录
第三章:生产事故案例分析 • 案例1: 违反安全管理规定施工构成重大责任事故罪 • 案例2 :没有按规定对所负责的有毒气体报警器进行例行维护保
养 导致事故构成重大劳动安全事故罪 • 案例3 :辽宁省某化工厂违反操作规程引起自燃导致爆炸 • 案例4 :山东菏泽某化工违反操作规程导致爆炸 • 案例5: 丽水市南明化工维修作业中违反有关安全管理规定,发
事故原因: 1、无驾驶资格驾驶叉车; 2、行驶速度过快,拐弯时急转弯; 3、钥匙没有拔下,管理疏忽。 事故对策: 1、叉车的小转弯机动性比轿车好,因此在转弯时应 降低速度; 2、叉车必须只限于持有驾照(特种作业许可证)的 人驾驶;
3、妥善管理叉车,务必注意不要忘记拔下钥匙。
事故举例二:
人站在叉车上以平衡重量,摔落。 事故状况 叉车叉起堆有货物的托
事故原因 1.自认为工作场地内没人,在视野被挡住的 情况下仍向前行驶 2.未通知相关人员在正式作业前有临时作业, 此属管理上的问题。 事故对策 1.装载货物导致不能确认前方视野时应倒退 行驶。 2.不得不在视野被遮挡的情况下行驶时,应 安排引导员等,建立万全的监视体制。 3.即使是临时作业,也应制定作业计划,并 将作业内容详细通知相关人员。
典型化工厂安全事故概况及案例分析(2022~2023)

典型化工厂安全事故概况及案例分析(2022~2023)化工厂作为重要的生产基地,承载着社会经济发展的重要责任。
然而,近年来我们不幸目睹了一系列化工厂的安全事故,严重危害了人民生命财产安全,对环境造成了严重污染。
本文旨在概述典型化工厂安全事故的现状及其案例分析,以期引起广泛的关注与反思。
2022年,全国范围内发生了多起化工厂安全事故,主要原因包括人为疏忽、设备故障、管理不到位等。
这些事故造成了多人死亡,大量有毒有害物质泄漏,造成了严重的生态环境问题。
2023年,化工厂安全事故依然屡禁不止,反映出化工厂安全生产形势的严峻。
尽管政府加强了监管力度,推行了一系列安全措施,但仍然无法根除隐患和事故的发生。
1.案例一:XX化工厂爆炸事故事故概述:2022年XX月,位于XX地的XX化工厂发生爆炸事故,造成多人伤亡和大量有毒化学品泄漏。
事故原因初步判断为设备老化、管理不到位导致操作错误。
影响分析:该化工厂爆炸事故导致周边居民疏散,造成环境严重污染,长期影响社会经济发展。
改进措施:加强设备维护更新、完善安全管理制度,提高员工培训和意识。
事故概述:2023年XX月,位于XX地的XX化工厂发生毒气泄漏事故,导致多人中毒甚至死亡。
事故原因初步判断为操作失误和安全设施不完善。
影响分析:该化工厂毒气泄漏事故引起了社会广泛关注,震动了全国化工行业。
倍受质疑的化工行业的声誉再次受到打击。
改进措施:加强操作规范和员工培训,检查和维护安全设施的完整性。
典型化工厂安全事故的概况及案例分析显示出当前化工行业安全生产形势的严峻性。
为了有效防范化工厂安全事故,我们需要采取以下措施:1.政府加大对化工厂的监管力度,加强安全检查和执法。
对于违反安全规定的企业,应严肃处理,甚至追究法律责任。
2.化工企业应加强自身安全管理体系的建设,推行安全生产责任制,建立健全的安全纪律和制度。
3.员工应严格遵守操作规程,加强安全意识和培训,增强事故应急处理能力。
- 1、下载文档前请自行甄别文档内容的完整性,平台不提供额外的编辑、内容补充、找答案等附加服务。
- 2、"仅部分预览"的文档,不可在线预览部分如存在完整性等问题,可反馈申请退款(可完整预览的文档不适用该条件!)。
- 3、如文档侵犯您的权益,请联系客服反馈,我们会尽快为您处理(人工客服工作时间:9:00-18:30)。
2011年度化工及危险化学品事故分析02232011年度全省化工行业及危险化学品领域事故分析2011年,全省化工行业和危险化学品领域共发生事故22起,死亡40人;其中,重大事故1起,死亡15人;较大事故1起,死亡3人。
这些事故发生的原因主要有:违章指挥、违章作业和违反劳动纪律,无正规设计或设备、工艺有缺陷,检维修环节安全作业管理制度和标准规程不健全、不落实,安全教育培训不到位等。
为认真吸取事故教训,推动安全生产管理工作,现将事故有关情况汇总分析如下:一、事故发生特点(一)爆炸(爆燃)、火灾和中毒窒息事故多发。
全部事故中,爆炸(爆燃)、火灾事故有12起,死亡29人,分别占总数的54.6%和72.5%;中毒窒息事故5起,死亡6人,分别占总数的22.7%和15%;机械伤害及高处坠落事故有5起,死亡5人,分别占总数的22.7%和12.5%。
(二)检维修作业环节(包括受限空间、动火等作业)事故多发。
共发生事故9起,死亡25人,分别占总数的40.9%和62.5%;其中,发生重大事故1起,死亡15人。
(三)蒸馏等产品后处理过程事故多发。
共发生事故7起,死亡10人,分别占总数的31.8%和25%;其中,硝基物蒸馏工序发生较大事故1起,死亡3人。
(四)“三违”现象是事故发生的主要原因。
全部事故中,有15起发生的直接原因是“三违”,死亡18人,分别占总数的68.2%和45%。
(五)设备设施缺陷或管理不严格是事故发生的重要原因之一。
共发生事故9起,死亡23人,分别占总数的40.9%和57.5%。
(六)无正规设计或设计缺陷是事故发生的重要原因之一。
全部事故中,无正规设计或设计缺陷引发的事故有6起,造成7人死亡,分别占总数的27.3%和17.5%。
(七)安全生产责任制、规章制度和操作规程不健全是事故发生的重要间接原因。
全部事故中,有8起发生的重要原因是安全生产责任制、规章制度和操作规程不健全,死亡24人,分别占总数的36.4%和60%。
二、暴露出的主要问题(一)事故隐患排查治理不彻底。
近几年来,各级安监部门和化工企业持续深入开展隐患排查治理工作,但去年事故起数和死亡人数同比呈上升趋势,暴露出部分企业不履行隐患排查治理职责,隐患排查治理机制不完善、排查不彻底,主要设备设施(尤其是特种设备)及其安全附件的维护、保养和定期检测检验不按规定执行和落实,对各级安监部门和企业自查检查出的隐患不够重视,整改不及时、不到位等问题。
(二)中小型企业安全管理基础仍然较差。
去年我省中小型化工生产企业事故居高不下,暴露出许多中小型企业仍然延续着过去习惯性管理和建设模式,安全意识差,安全投入不足,管理水平、技术水平明显滞后,安全生产责任制、规章制度和操作规程不健全、不落实,缺少高素质的安全管理人员,从业人员素质较低,隐患排查治理不全面、不彻底,特别是一些建厂较早的老企业,生产设备设施简陋,安全设施欠账较大,现场操作人员过多,易发生群死群伤的重特大事故。
(三)检维修环节各项安全作业管理制度和标准规程不健全、落实不到位。
近几年来,我省化工企业检维修作业环节,包括受限空间、动火作业环节事故连年多发,主要原因是一些化工企业对检维修作业环节的安全生产重视不够,检维修安全管理规章制度不健全,安全作业规范执行不严格,安全作业前未实施风险分析、未采取和落实预防和控制措施,对外来检维修施工队伍安全管理不到位等。
(四)蒸馏等产品后处理系统(特别是硝基物蒸馏工艺系统)安全控制措施不完善,安全操作规程执行不严格。
一些企业涉及高温、高压、易燃、易爆和有毒有害物料(特别是硝基化合物)蒸馏系统,没有严格控制温度、压力、液位、进料量、回流量等操作参数,忽视重要工艺参数之间的相互制约、相互影响,设备自动化程度低,人为操作失误多,导致事故频发。
(五)化工装置未经正规设计存在安全隐患的问题突出。
一些化工企业特别是中小型化工企业早期建设的化工装置,由于没有设计或者未经具备相应资质的设计单位进行设计,导致工艺装备存在着许多缺陷或安全隐患,主要是生产工艺流程不能满足安全生产的要求,主要设备、管道、管件选型(材)不符合相关标准要求,装置布局不合理等,造成生产安全事故多发。
(六)企业安全教育培训工作不到位,没有针对性。
从去年发生的事故情况看,大部分事故企业不重视安全教育培训工作,走过场、针对性不强,甚至个别化工企业从未组织过安全培训。
从业人员对危险化学品安全管理和操作的基本知识和技能缺乏系统了解和掌握,安全意识淡薄,安全素质较差,违反化工企业安全生产41条禁令,违反劳动纪律、违反操作规程、违章指挥的“三违”现象时有发生。
(七)一些企业安全标准化工作流于形式。
近年来,我省大力推进企业安全标准化建设,取得了一定成效,但是从2011年情况统计分析,部分企业满足于安全标准化达标,并未全面正确运用于实际安全管理中,甚至出现违章、违规操作,离企业本质安全水平还有很大差距,致使标准化企业事故时有发生。
三、有关对策措施(一)扎实推进隐患排查治理工作。
按照全省统一部署和“企业自查自纠、政府挂牌督办、专家现场诊断、科技手段检测”的工作机制,认真抓好隐患排查治理工作。
组织各级安监部门,指导、督促企业严格执行隐患定期自查、自评、自纠、自报制度,按时、按要求填报《企业安全隐患自查自纠报告表》。
认真落实政府挂牌督办制度,限期整改重大隐患。
采取政府购买安全技术服务的方式,发挥行业管理部门或行业协会的专家作用,组织专家深入企业生产现场,对生产工艺、设施设备进行安全诊断。
发挥安全生产检测检验机构的作用,对危险化学品重大危险源、输送管道、剧毒化学品储存设备设施等进行检测检查,发现存在重大隐患及时进行整改。
(二)加快推进化工装置设计安全诊断工作。
按照省安监局《关于开展化工装置设计安全诊断工作的意见》,继续推进化工装置设计安全诊断工作,严厉查处拒不开展设计安全诊断和隐患整改工作、拒不执行隐患整改指令等行为。
今年8月份前后,组织召开全省化工装置设计安全诊断工作现场会,推广经验,推进工作,确保年底以前完成全省所有未经正规设计的化工装置设计安全诊断和隐患整改工作。
今年四季度,省安监局对各市设计安全诊断工作情况进行一次全面督查。
指导、督促设计单位,落实《化工建设项目安全设计管理导则》(AQ/T3033-2010),开展初步设计和施工图设计安全审查。
(三)突出抓好重点品种和重大危险源安全监管。
根据国家安监总局公布的重点危险化学品名单,研究制定更加严格的生产、储存、购买和销售、运输安全管理措施。
组织各级安监部门,进一步排查确定泄漏后呈气态的易燃、易爆和有毒危险化学品、大型危险化学品储罐区和毗邻城乡人口密集区的化工企业,实施重点监管,防范重特大事故。
部署开展对重点危险化学品生产、储存设施和重大危险源自动化监控系统的调查摸底,研究制定措施,启动相关自动化监控系统改造完善工作。
贯彻落实国家安监总局《危险化学品重大危险源监督管理暂行规定》,加强对重大危险源的安全监管。
(四)组织开展化工装置检维修环节安全专项整治活动。
针对近年来全省化工装置检维修作业环节事故多发问题,组织开展安全专项整治活动,从检维修作业的安全管理规章制度、作业安全规范、风险分析、安全条件确认、现场安全控制和对外来检维修施工队伍管理等六个方面,督促企业整治存在的问题和隐患,严格执行动火、进入受限空间、破土、临时用电、高处、断路、吊装、抽堵盲板等危险作业安全规范,加强检维修作业环节安全管理,落实重大检维修作业报告制度,有效遏制检维修环节事故发生。
(五)推动提升化工企业工艺安全管理水平。
在大型石油化工企业,试点推广应用危险与可操作性分析(HAZOP)方法,组织开展辅导活动,培养企业分析人员,提高企业安全管理水平。
在石油化工企业,广泛宣传和推动落实《化工企业工艺安全管理实施导则》(AQ/T3034-2010),不断提高化工企业工艺安全管理水平,从源头上减少事故发生。
组织开展风险分析活动,督促企业建立风险管理制度,从工艺、设备、仪表、控制、应急响应等方面开展系统的工艺过程风险分析,加强化工过程安全管理,预防各类事故的发生。
(六)进一步强化对安全标准化创建工作的指导。
组织开展对安全生产标准化达标创建和评审工作的专项督查活动,突出对企业安全生产标准化运行情况的监督检查,坚决防止重创建、轻运行、安全标准化工作流于形式的现象。
根据国家有关氯碱、合成氨、硫酸、涂料、溶解乙炔等行业的安全标准化实施指南,针对不同的行业特点和生产工艺特征,细化和补充完善安全生产标准化评审标准,力争在今年底前,全省危险化学品企业达到安全标准化三级以上水平。
(七)进一步强化安全生产教育培训工作。
深刻吸取近年来省内外化工企业发生的事故教训,组织开展“安全生产警示教育”活动,对全省化工企业的主要负责人、其他负责人、安全生产管理人员和全体员工,进行一次安全生产警示教育培训,提高认识,统一思想,推动企业安全生产主体责任落实。
组织修订全省危险化学品安全生产培训教材和考试题库,制订危险化学品新增特种作业人员的培训教材。
加强对企业全员安全培训工作的督查,督促企业认真做好安全生产规章制度和操作规程、安全生产禁令和安全标准规范的培训教育,提高全体员工的安全素质。
四、事故基本情况(一)青岛龙图化工有限公司“3.1”爆燃事故2011年3月1日上午11时30分左右,青岛龙图化工有限公司发生爆燃事故,造成1人死亡,2人受伤,直接经济损失100万元。
青岛龙图化工有限公司成立于2009年6月,注册地址为胶州市马店镇大杜戈庄村,总投资300万元,法定代表人冷延韶,一般经营项目:塑料增塑剂、PVC改性材料制造、销售,批发、零售等。
现有从业人员10人。
主要原料:大豆油、甲酸、低度双氧水、尿素。
环氧大豆油年生产能力约3000吨。
2011年3月1日是该企业春节后的第一次生产。
大约8时许,生产厂长、技术负责人勾公平带领卢成友、徐怀章等4名新招来的从业人员(以前均无相似操作经验)进行复工试生产,在9立方的反应釜中加入4吨大豆油,200公斤甲酸(配方比例为4%-10%)。
9时许,开始滴注浓度27.5%的双氧水2吨(配方比例为40%-80%),3小时滴完,滴注双氧水过程中用水循环冷却(事故发生时冷水系统已经打开)。
大约11时30分许双氧水剩余约半吨,徐怀章、卢成友发现温度超过70度,徐怀章就到办公室向勾公平汇报,勾公平回到车间检查原因,发现温度达到150度了。
这时徐怀章看到勾公平用力拉了一下通气阀门,同时说:“危险”,于是他们就往外跑。
在他们3人快要撤出车间时发生爆炸燃烧,导致勾公平死亡,卢成友、徐怀章受轻伤。
经调查,事故发生的直接原因是:违章指挥、违规操作。
生产厂长、技术负责人勾公平在往反应釜里抽入大豆油和甲酸后未打开通气阀,随着反应的进行,釜内温度逐渐升高,未反应的双氧水、甲酸分解加快,釜内压力逐渐升高,当温度升至100度以上时,导致釜内双氧水、水份大量分解,同时反应加剧,体积急剧膨胀,引起爆炸,后起火燃烧。