液压式轮胎硫化机介绍分析共34页
轮胎硫化机结构简介

轮胎硫化机结构简介除了A型硫化机采用平移式的装胎机构外,其他均采用摇臂式装胎机构。
PC-X硫化机的装胎机构也属摇臂式,但有其结构特点。
其装胎器在回转时由二个回转中心而不是由一个回转中心控制,见图11中的A和B。
这使装胎定位依靠一个三角形珩架ABC,而不是依靠一单梁。
有效地增加了定位刚性,保证定位精度。
4 合模力的获得液压式硫化机合模力的获得完全来源于油的压力。
一般均用较低压力、较快速度、较长行程的油缸控制开合模。
合模以后用一定的方式(插销、锁环、或锁紧块)将上下模部分锁住,组成一个闭环受力系统,然后再用高压、短行程的油缸使上下模受到合模力。
PC-X 硫化机获得合模力的方式有其结构特点,PC-X硫化机属于框架式结构,下模部分固定在框架的底座上。
先由固定在框架上部的开合模泊缸带动上模部分合模,这时上模部分与框架上横梁之间出现一空间。
在框架侧面装有一摆臂定位立柱,合模后此立柱转进模具中心线位置,填满上横梁与上模部分的空间,形成一闭环受力系统。
这时装在框架上横梁模具中心线位置的高压、短行程合模力油缸通过定位立柱加压于上模部分,从而获得合模力。
这种结构形式用上部一个油缸代替了一般液压式硫化机下部4个或6个小油缸。
结构简单,便于检验。
加上合模力以后,在整个硫化周期内,有一个保压题目。
有的液压式硫化机在硫化周期内油泵继续工作以保持压力,有的则采用蓄能器来补偿硫化过程中可能出现的压力降。
PC-X 硫化机则采用空气一液压增压器来解决,见图12。
在PC-X硫化机上采用的油泵压力为8.33~8.82MPa。
合模以后,油泵即停止工作,而利用与0.49MPa的压缩空气产生21.56MPa的高压油注进合模力油缸获得所要求的合模力,同时在整个硫化过程中起保压作用。
这种形式既可使油泵用较低的工作压力,合模后油泵又不需继续工作,也不需要任何蓄能装置。
因此节省能源,油缸使用寿命长,便于维护保养。
5 卸胎器和后充气装置PC-X硫化机的卸胎器采用摇臂式卸胎机构替换传统的卸胎方式,见图13。
液压轮胎硫化机热结构耦合分析

- 一 0 fk ) 一  ̄ (
边 界条 件如 下 :
T( Y, )一 z, z, £ )
析 , 根据 分析结 果对结 构进 行 了相 应改进 , 并 降低
了生 产成 本 ; 建 良等l 采 用 ! A 陈 2 - DE S软件 将 轮
胎定 型硫 化机分 为 上 横梁 和底 座 相关 的两部 分 ,
分别进 行有 限元 分 析 , 明 了硫 化 机设 计 的 安全 证 性要 求 ; 冬梅 等[ 对 电 动螺 旋 轮胎 定 型 硫 化机 焦 3 ] 的上 横梁进 行 了有 限元分 析 , 对 上横 梁 结 构肯 在
费大量 建模 时 问 , 而且 影响 网格划 分 的质量 , 进而 增 大计算 过 程 的收 敛 难 度 , 响计 算 结 果 的 正确 影
性 。另 外 , 考虑 到并列 机架 实体模 型 的相似性 , 本
研 究 只构建 一个机 架 的实体 模型 , 图 2所示 。 如
r 一 是 ) ( ) 瓦一 a 瓦 (筹 一 是 一 T
( I z y f d d { d y d Qd t 、 dd yzx { xd ) t Vd : c d T+ f x z y+ f p Vd dd d 一曲d d 4 z x- -
如
1 1 1 三维传 热数 学模 型 ..
硫化 机在稳 定 运 行 时 , 能通 过 上下 热 板 以 热
定 的基 础上 提 出了相应 的改进 措施 。 上述 分析都 没 有 考虑 温 度 的影 响 , 了得 到 为 硫化 机在 真实环 境 中的工况 , 本研 究对热 、 结构共 同作 用情 况下硫 化 机 的 应力 、 移 和位 置 精 度进 位
行研 究 。
图 1 分 析 流 程
轮胎定型硫化机

充氮硫化的轮胎硫化机中心机构
充氮硫化的轮胎硫化机的中心机构,其大部分 部件与现有的充氮硫化的轮胎硫化机的中心机 构的相应部件相同,所不同的是,缸筒上口装 有缸盖和法兰盖,其环形凹槽喷射蒸气和氮气 的喷口方向分别呈水平偏下向与水平偏上向, 同时,在法兰盖上还装有一吸水胶管,其吸嘴 可吸取胶囊中的冷凝水通过出水管流出。该中 心机构用硫化机硫化轮胎,其硫化室内的蒸气 和氮气混合均匀,能及时排除冷凝水,保证硫 化室温度均匀稳定,从而提高硫化质量。
活络模是把两半模改为胎冠部位可径向分合的 几个小块,在合模时,活络模块能自动的径向 合拢,包住胎坯;卸胎时,活络模块可以径向 分离,脱离硫化的轮胎,这样保证胎体和胎冠 的完整和硫化质量,有利于装卸轮胎。
但是,活络模的结构复杂、制造成本高,因此 目前只在硫化子午线轮胎中采用。
活络模的结构类型较多,可分为:平面导向活 络模、圆锥面导向活络模球面导向活络模、径 向活络模、杠杆式活络模等。目前使用较多的 活络模具为平面导向活络模和圆锥面导向活络 模。
现在人们发现了利用氮气可以解决上述问题,它采用
190—210℃高压饱和蒸汽充入胶囊升温之后,再向胶囊充 入2.0—2.6MPa压力的高纯氮气的增压办法,以达到高温高
压的硫化条件,从而实现了上述目标。
近年来,蒸汽/氮气介质硫化方式发展很快,目前在美国、 日本等主要轮胎生产厂家新建项目已基本采用氮气硫化的 方式。
在模中硫化,胶囊上下夹环 在硫化位置。两个水平气缸
锁住中心机构
硫化结束。开模, 将轮胎顶离下模。
卸胎器转入, 抓住硫化好的轮胎
卸胎器转出,将硫化好的 轮胎送到后充气工位或卸胎 辊道。装胎器转入,将新胎坯
送到硫化工位
到达硫化位置, 胶囊出囊筒
机械式和液压式轮胎定型硫化机
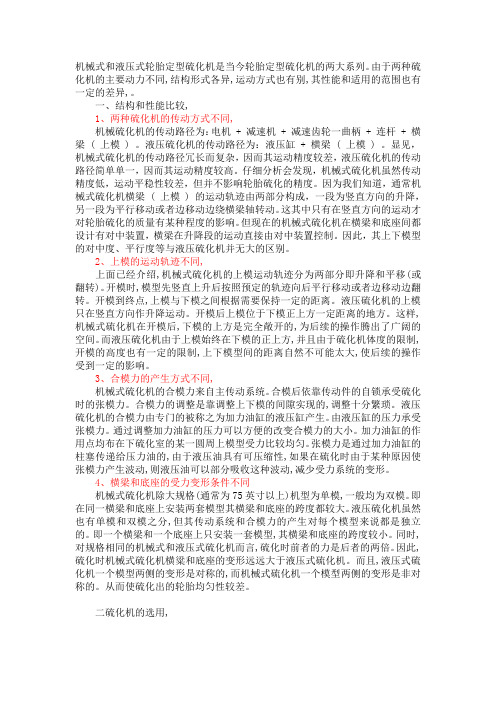
机械式和液压式轮胎定型硫化机是当今轮胎定型硫化机的两大系列。
由于两种硫化机的主要动力不同,结构形式各异,运动方式也有别,其性能和适用的范围也有一定的差异,。
一、结构和性能比较,1、两种硫化机的传动方式不同,机械硫化机的传动路径为:电机 + 减速机 + 减速齿轮一曲柄 + 连杆 + 横梁 ( 上模 ) 。
液压硫化机的传动路径为:液压缸 + 横梁 ( 上模 ) 。
显见,机械式硫化机的传动路径冗长而复杂,因而其运动精度较差,液压硫化机的传动路径简单单一,因而其运动精度较高。
仔细分析会发现,机械式硫化机虽然传动精度低,运动平稳性较差,但并不影响轮胎硫化的精度。
因为我们知道,通常机械式硫化机横梁 ( 上模 ) 的运动轨迹由两部分构成,一段为竖直方向的升降,另一段为平行移动或者边移动边绕横梁轴转动。
这其中只有在竖直方向的运动才对轮胎硫化的质量有某种程度的影响。
但现在的机械式硫化机在横梁和底座间都设计有对中装置,横梁在升降段的运动直接由对中装置控制。
因此,其上下模型的对中度、平行度等与液压硫化机并无大的区别。
2、上模的运动轨迹不同,上面已经介绍,机械式硫化机的上模运动轨迹分为两部分即升降和平移(或翻转)。
开模时,模型先竖直上升后按照预定的轨迹向后平行移动或者边移动边翻转。
开模到终点,上模与下模之间根据需要保持一定的距离。
液压硫化机的上模只在竖直方向作升降运动。
开模后上模位于下模正上方一定距离的地方。
这样,机械式硫化机在开模后,下模的上方是完全敞开的,为后续的操作腾出了广阔的空间。
而液压硫化机由于上模始终在下模的正上方,并且由于硫化机体度的限制,开模的高度也有一定的限制,上下模型间的距离自然不可能太大,使后续的操作受到一定的影响。
3、合模力的产生方式不同,机械式硫化机的合模力来自主传动系统。
合模后依靠传动件的自锁承受硫化时的张模力。
合模力的调整是靠调整上下模的间隙实现的,调整十分繁琐。
液压硫化机的合模力由专门的被称之为加力油缸的液压缸产生。
轮胎定型硫化机简介

轮胎定型硫化机概述作者:桂林橡胶机械厂一、用途轮胎定型硫化机主要用于汽车外胎、飞机外胎、工程外胎及拖拉机外胎等充气轮胎的硫化。
也有用小规格的定型硫化机硫化摩托车胎、力车胎、自行车胎的。
二、轮胎定型硫化机的现状轮胎定型硫化机是在普通个体硫化机的基础上发展起来的。
在本世纪二十年代出现了普通个体硫化机,四十年代出现寇型硫化机。
它简化了工艺操作过程,在同一机台上可完成装胎、寇型、硫化、卸胎及后充气冷却,便于工艺过程的机械化和自动化。
近代的定型硫化机,一般对内温、内压、蒸汽室温度均能测量、记录和控制。
此外有定型控制系统、清扫模型、涂隔离剂等装置。
整个生产周期可自动进行。
如配以自动运输和电子计算机控制,可使轮胎硫化实现自动化生产。
因此定型硫化机的机械化自动化程度和生产效率均较高、劳动强度低、产品质量好,在现代化轮胎厂中获得了广泛的应用。
三、分类和型号的表示方法(一)分类轮胎定型硫化机按采用的胶囊形式分为三种类型。
1. A 型〈或称AFV 型〉轮胎定型硫化机 胶囊从外胎中脱出时,胶囊在推顶器的作用下,往下翻人下模下方的囊筒内。
开模方式为升降平移型。
2. B 型〈或称BOM 型〉轮胎寇型硫化机 胶囊从外胎中脱出时,胶囊在中心机构的操纵下,在抽真空收缩后向上拉直。
开模方式有升降型,升降平移型和升降翻转型。
3. AB 型〈AUB0型〉轮胎定型硫化机 胶囊从外胎中脱出时,胶囊在胶囊操纵机构和囊筒作用下,上半部作翻转而整个胶囊由囊筒向上移动收藏起来。
开模方式有升降型和升降翻转型。
按传动方式可分为连杆式定型硫化机和液压式定型硫化机。
溢压式B型定型硫化机的开摸方式为升降型。
按加热方式可分为蒸锅式、夹套式定型硫化机和热板式定型硫化机。
按用途可分为普通胎定型硫化机和子午胎定型硫化机。
自动化程度较高的定型硫化机,普通胎和子午线胎可通用。
按整体结构又可分为定型硫化机和定型硫化机组。
目前一般是根据胶囊形式进行分类。
(二)型号的表示方法轮胎定型硫化机型号表示方法常以硫化机的保护罩或蒸汽室的名义内径、模型数量及总压力表示。
《轮胎定型硫化机》课件

应用领域
汽车制造业
轨道交通
轮胎定型硫化机是汽车制造业中不可 或缺的设备,用于生产各种类型的汽 车轮胎。
轨道交通车辆如火车和地铁的轮胎也 需要使用轮胎定型硫化机进行生产。
航空工业
在航空工业中,高性能的轮胎定型硫 化机用于制造飞机轮胎,要求具有高 强度和耐高温的特性。
发展趋势
智能化
随着工业4.0和智能制造的发展 ,轮胎定型硫化机将更加智能化 ,实现自动化控制和远程监控。
常见故障及排除方法
故障一
加热系统不工作。排除方法: 检查加热元件是否损坏,电源
和气源是否正常供应。
故障二
加压系统失灵。排除方法:检 查加压泵和液压系统是否正常 ,排除液压油泄漏等问题。
故障三
模具温度不均匀。排除方法: 检查加热管是否有损坏,检查 模具是否清洁,确保加热介质 流通顺畅。
故障四
轮胎定型不良。排除方法:检 查装胎和定位是否正确,调整 加压和加热参数,确保轮胎定
03
轮胎定型硫化机组成
主机部分
主机框架
用于支撑和固定硫化机的其他部 分,通常采用高强度钢材焊接而
成。
加热室
用于对轮胎进行加热,通常由耐高 温材料制成,并配备有温度控制装 置。
模具
用于硫化轮胎的模具,通常由金属 制成,具有精确的尺寸和形状。
液压系统
01
02
03
液压泵
用于提供液压动力,通常 由电动机驱动。
加热元件
通常采用电热管或电热板 ,用于对加热室内的空气 或液体进行加热。
温度控制装置
用于控制加热元件的功率 输出,从而精确控制加热 温度。
冷却系统
用于在需要时对加热元件 进行冷却,以防止过热。
液压双模轮胎硫化机的发展与性能简介

泛 推广 阶段 。
3 液压 硫化 机 替代机 械 式硫 化机 已成 必然 趋势
杭 州 中策橡 胶有 限公 司是 液 压 硫化 机 的坚 定 支持 者 , 司半 钢 乘 用 轮胎 主 要 定位 为高 等级 轮 公 胎, 硫化主要 采用 液压 硫 化 机 。从 使用 效果 看 , 生
度 的波动将 造 成合模 力 的波 动 。 液压硫 化 机 能 克 服 机 械 式 硫 化 机 的 固 有 弱
对 机械 式硫 化机 与液压 硫 化 机 的成 本 进行 比 较 , 须 要 综 合 考 虑 配置 、 能 、 机 率 、 务 、 必 性 开 服 生
产率及维修费用等。据克虏伯专家介 绍 , 在欧洲 , 若 在相 同的 配置 下 , 压 硫 化 机 比机 械 式 硫 化 机 液 更便宜。
其硫 化机全 部 为液压 式 。我 国液压 硫 化机 主要 型
号 有 15 、 1 0 1 2 、 3 0 10 、 7 0 12 、 0 0 14 、 2 0 1 1 、 6 0 1 O 、 7 5
液 压 硫化 机是 在机 械式 硫化 机 的基 础 上 发 展
起来的。它具有精度 和 自动化程度高、 硫化 的轮 胎均匀 质优 、 用 于 子 午 线 轮 胎 尤 其是 高等 级 子 适
化 机 的 比重 已超 过 7 % , 且 呈 递 增 的 趋 势 。我 0 并 国的液 压硫 化机 开发 工作 始 于 6 0年代 末 期 , 步 起 时间不 比工 业 发 达 国家 慢 , 是 当时 国 内 的液 压 但 技 术水 平 限制 了液压 硫化 机 的发展 。
B型液压硫化机技术介绍

作者简介:丁振堂(1969-),男,高级工程师,硫化机行业内专家学者,中国高分子材料专家委员会委员,青岛科技大学高性能聚合物研究院研究员。
收稿日期:2023-06-291 研发背景轮胎硫化是轮胎生产过程中的最后一道工序,也是决定成品轮胎质量的工序之一。
各个橡胶机械制造厂家争相开发生产性能好、可靠性好的轮胎定型硫化机,尤其侧重机内定型、热工管道系统、润滑系统、自动控制系统、胶囊设计制造、过热水出氧、专用电机及安全防护等功能。
从国外引进63.5"机械式轮胎定型硫化机并进行了消化吸收后,国内轮胎定型硫化机的开发和生产,开始走上快速发展的道路。
国内硫化机厂家百家争鸣、百花齐放,机械式定型硫化机发展迅猛,形成了系列化、专业化。
国产液压轮胎定型硫化机的发展,经历了一个认识和转变的过程,后来,随着国产液压轮胎定型机技术水平的提高和质量的保证,成为轮胎企业硫化高等级子午胎的首选设备。
在市场大力发展高等级子午胎的前景下,对液压轮胎定型硫化机需求日增。
青岛软控机电工程有限公司也加入了液压轮胎定型硫化机的研发制作队伍,并根据不同用户群,研发出不同结构种类的液压硫化机,本文重点介绍B 型液压轮胎定型硫化机。
该机型是框架式结构,是最早研发的液压硫化机机型之一,因其硫化全钢子午线轮胎性能稳定可靠,操作方便快捷,尤其受老牌国内轮胎厂家的青睐,成为液压硫化机的主力机型。
2 B 型液压硫化机的总体结构、特点、动作原理、参数等介绍B 型液压硫化机是软控集多年研发设计、制作、安装、调试、使用、维护精心打造的机型。
因其结构B 型液压硫化机技术介绍丁振堂,郭良刚,张元胜,季付高,尹相迎(青岛软控机电工程有限公司,山东 青岛 266200)摘要:简要介绍了B 型液压硫化机研制背景、工艺参数、技术参数、主要结构、检测标准等,其优点是硫化子午线轮胎提高产品质量,降低能源消耗,实现自动化、机械化,产品的性价比最优等。
关键词:中心机构;热工阀组;装胎机械手;卸胎机械手;工艺路线;自动化中图分类号:TQ330.47文章编号:1009-797X(2024)02-0013-06文献标识码:B DOI:10.13520/ki.rpte.2024.02.004稳定、操作方便、价格公道、性价比高、性能优良等受市场用户好评,成为国内外用户的主力机型。
国内外液压轮胎硫化机水平浅析

国内外液压轮胎硫化机水平浅析1 引言汽车是衡量一个国家经济水准的标志之一,各国都积极发展自己的汽车工业,且迅速成为国家发展的“支柱产业”,先进的欧美国家无一例外,我国近年来也将汽车工业列为重点大力加以发展,“轿车进入家庭”己是中国老百姓可望而可及的事情。
轮胎作为汽车的重要配套之一,对汽车的质量和水平有着很大的影响,各国对轮胎制造给予高度重视,在这方面国外总体水平高于我国,差距是明显的。
我国轮胎与国外轮胎相比档次低,品种少,轮胎设备也落后,在中、高档的汽车制造厂,为了提高自己的产品整体水平,宁可进口或采用独资企业的轮胎,也不采用国内品牌轮胎,质量成为国内轮胎发展的“瓶颈”之一。
例如,沪宁高速公路开通的半个月,发生了近百起事故,其中由于轮胎原因引起的事故约占3/4。
为确保生产高档次轮胎的要求,必须加速提高轮胎机械水平。
下面谈谈液压轮胎硫化机的一些优点及国外的水平,再来回顾一下我国液压轮胎硫化机的发展历程,知己知彼,争取在较短时间内迎头赶上。
2 液压轮胎硫化机的优点过去有不少文章,从结构上谈到机械式轮胎硫化机的不足,以及液压式轮胎硫化机的优点,例如:机械式的滑动轴承受重负荷作用,不可避免的造成铜套的不均匀和较严重的磨损,而铜套的磨损进一步降低硫化机的合模精度;机械式的上下模间受到的合模力不均,对双模定型硫化机而言,总是两外侧的受力大于两内侧受力;机械式的合模力是由各受力构件的弹性变形量所决定的,而温度变化将使受力构件尺寸发生变化,生产过程中环境温度或工作温度的波动将造成合模力的波动等,而所有这些机械式硫化机所固有的弱点在液压式硫化机上较彻底的解决了。
下面着重从能源消耗、产品质量和生产率三个方面来谈。
2.1 能源消耗当今轮胎工业和设备供应厂商双方都在集中精力,千方百计设法节约硫化能,亦即力争改善热传导和减少热损失。
自从世界性范围的能源涨价以来,这已成为一个起决定作用的因素。
据有关资料,硫化乘用轮胎所需的蒸汽消耗量,大约相当于每公斤轮胎产品消耗4kg蒸汽。
轮胎定型硫化机液压系统常见故障与解决措施(2)
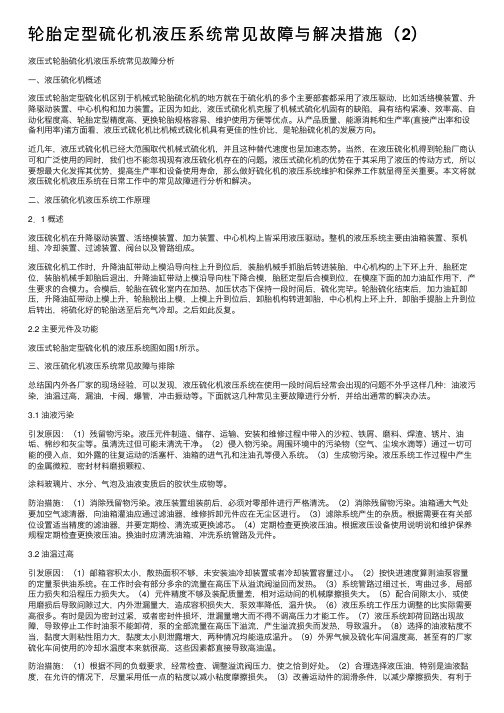
轮胎定型硫化机液压系统常见故障与解决措施(2)液压式轮胎硫化机液压系统常见故障分析⼀、液压硫化机概述液压式轮胎定型硫化机区别于机械式轮胎硫化机的地⽅就在于硫化机的多个主要部套都采⽤了液压驱动,⽐如活络模装置、升降驱动装置、中⼼机构和加⼒装置。
正因为如此,液压式硫化机克服了机械式硫化机固有的缺陷,具有结构紧凑、效率⾼、⾃动化程度⾼、轮胎定型精度⾼、更换轮胎规格容易、维护使⽤⽅便等优点。
从产品质量、能源消耗和⽣产率(直接产出率和设备利⽤率)诸⽅⾯看,液压式硫化机⽐机械式硫化机具有更佳的性价⽐,是轮胎硫化机的发展⽅向。
近⼏年,液压式硫化机已经⼤范围取代机械式硫化机,并且这种替代速度也呈加速态势。
当然,在液压硫化机得到轮胎⼚商认可和⼴泛使⽤的同时,我们也不能忽视现有液压硫化机存在的问题。
液压式硫化机的优势在于其采⽤了液压的传动⽅式,所以要想最⼤化发挥其优势,提⾼⽣产率和设备使⽤寿命,那么做好硫化机的液压系统维护和保养⼯作就显得⾄关重要。
本⽂将就液压硫化机液压系统在⽇常⼯作中的常见故障进⾏分析和解决。
⼆、液压硫化机液压系统⼯作原理2.1 概述液压硫化机在升降驱动装置、活络模装置、加⼒装置、中⼼机构上皆采⽤液压驱动。
整机的液压系统主要由油箱装置、泵机组、冷却装置、过滤装置、阀台以及管路组成。
液压硫化机⼯作时,升降油缸带动上模沿导向柱上升到位后,装胎机械⼿抓胎后转进装胎,中⼼机构的上下环上升,胎胚定位,装胎机械⼿卸胎后退出,升降油缸带动上模沿导向柱下降合模,胎胚定型后合模到位,在模座下⾯的加⼒油缸作⽤下,产⽣要求的合模⼒。
合模后,轮胎在硫化室内在加热、加压状态下保持⼀段时间后,硫化完毕。
轮胎硫化结束后,加⼒油缸卸压,升降油缸带动上模上升,轮胎脱出上模,上模上升到位后,卸胎机构转进卸胎,中⼼机构上环上升,卸胎⼿提胎上升到位后转出,将硫化好的轮胎送⾄后充⽓冷却。
之后如此反复。
2.2 主要元件及功能液压式轮胎定型硫化机的液压系统图如图1所⽰。
液压轮胎硫化机介绍

装胎位时装胎器中心对下热板中心同 轴度 Φ0.4mm 装胎位时装胎器中心对下热板中心同 轴度的重复精度 Φ0.2mm 装胎位时装胎器盘面对下热板的平行 度 0.2mm 装胎位时装胎器盘面对下热板平行度 的重复精度 0.1mm
3、结构特点
导柱卡环锁模式液压双模轮胎定型硫 化机为我公司自主开发的新型液压轮胎硫 化机,在开合模、锁模、加压等部件中均 采用了新颖而简单的结构,各动作功能协 调安全可靠。可应用于28“以上52“以下系 调安全可靠。可应用于28“以上52“以下系 列产品。目前已开发出48“。以下结合 列产品。目前已开发出48“。以下结合 48“简单介绍该类硫化机的结构特点。 48“简单介绍该类硫化机的结构特点。
可选用R型、C 可选用R型、C型、 或标准油缸B 或标准油缸B型中心 机构
3、6 其他用直线导轨; 用直线导轨; 液压系统一拖一;
爪盘 直线导轨 机械手升降油缸
谢谢!
3、2 采用新式锁模系统
适用于不同 模具高度的 环槽 加压油缸及 加压部件 锁模机构
双导柱卡环式锁模系统 开合模导向用的双导柱, 开合模导向用的双导柱,在其上加工了适应 不同高度的环槽, 不同高度的环槽,用以锁模机构的卡环卡紧、 锁模,加工非常容易,精度很容易保证, 不必调整,确保了模具各点均匀受力。 由于采用双立柱结构形式,模具周围 完全敞开,加压油缸等零部件很容易更换, 大大降低了维护成本及时间。各种维护, 均可在不拆机的情况下进行。
3、3 采用简单快速的调模功能
首先,控制开合模油缸收缩位置,使卡板卡在双 导柱的不同环槽内,实现初步的间断调模;其次, 利用加压油缸行程,实现各间断调模范围内的连 续调模。 从机械角度看,该系统仅在导柱上多车几 道锁模环槽、加压油缸行程加大几厘米而已。因 此结构非常简单实用。大大降低了机器维护量及 维护成本。
液压式硫化机承力部件结构强度与疲劳分析

作者简介:刘玉龙(1988-),男,中级工程师,硕士研究生,主要从事结构力学、结构动力学和流体力学的研究工作。
收稿日期:2021-12-140 引言随着汽车工业的发展,对轮胎性能的要求越来越高,同时硫化是影响轮胎成品的重要工序之一。
良好的硫化工艺装备对提升成品轮胎的各项性能起着重要作用。
硫化机的稳定及可靠程度影响轮胎的生产效率及轮胎质量。
液压式硫化机是通过液压油缸驱动上横梁带动上模具做垂直运动,液压硫化机承力部件的位移、应力以及疲劳强度直接影响硫化机的可靠性。
有限元分析作为现代机械产品设计的有效手段,通过有限元分析可以缩短产品设计周期及风险,提高一次设计成功率。
目前有限元分析在硫化机关键部件的强度疲劳分析方面得到了较为广泛的应用。
唐谷枫[1]利用理论计算、有限元分析的方法对大吨位多层平板硫化机的结构进行了优化设计,将工作板从实心平板结构优化为框架结构有效的增加刚度并减轻了结构重量。
刘志刚等[2]则利用Hypermesh 和Ansys 对多接触面轮胎定型硫化机进行了模态分析、应力和应变分析,同时改进了硫化机的结构,达到了消除应力集中、提高硫化机抗振性和工作稳定性的目的。
胡海明等[3]应用Abaqus 软件对硫化工况下的轮胎模具底座进行了热力耦合和力学性能分析,应用Fe-Safe 软件对不同厚度和滑板结构的底座进行疲劳损伤和使用寿命计算,研究发现可以通过增大底座和U 形螺旋槽厚度的方法延长硫化机使用寿命。
张正罗液压式硫化机承力部件结构强度与疲劳分析刘玉龙 ,杨慧丽,官炳政(软控股份有限公司,山东 青岛 266045)摘要:硫化机承力部件的位移、应力以及疲劳强度对于整个硫化机性能可靠性和使用寿命起着关键作用。
利用有限元分析的方法对液压式硫化机的结构强度及疲劳强度进行计算,研究了承力部件的位移、应力及疲劳强度。
分析结果表明:液压式硫化机承力部件的变形符合安全许用标准,各承力部件最大应力均小于材料的许用屈服强度,各承力部件的疲劳安全系数最小值均满足疲劳强度要求.液压式硫化机结构设计和材料选择均符合安全规范。
探究液压式轮胎硫化机机械设计

探究液压式轮胎硫化机机械设计摘要:硫化机根据用途不同,其体积也是大小不一,小型硫化机所需空间如同一张办工桌大小,大型机犹如一座小房子。
虽然其体积不同,但硫化机执行的工艺却基本相同。
在轮胎生产工艺中,硫化是制造轮胎工艺的最后一道工序。
作为一种热压模制品,轮胎的产品外观质量、轮胎最终的均匀性以及企业的生产效率几乎全由轮胎硫化设备来决定。
因此轮胎硫化设备常被视为轮胎生产现代化水平的象征和标志,如何优化硫化工艺、改进并研发新型硫化设备一直都是人们关注的热点。
关键词:发展势头;类型;市场定位引言随着我国汽车工业和轮胎工业的发展对轮胎均匀性提出越来越高的要求,硫化机的工作精度越来越被人们所重视,液压硫化机的优越性开始得到充分的显现。
液压硫化机克服了机械式硫化机固有的弱点,吸收了机械式硫化机的优点。
一、发展势头1.1硫化机发展历程目前,液压硫化机的优越性在我国已被轮胎企业广泛认可,尤其是高等级子午胎项目倾向于选用液压硫化机趋势明显。
上世纪50年代以来我国机械式硫化机推广应用取代硫化罐是轮胎硫化的第一次飞跃,那么液压硫化机替代机械式硫化机便是轮胎硫化的第二次飞跃。
我国的液压硫化机开发工作始于20世纪60年代末,国家“八五”规划期间,将液压硫化机列入“子午胎关键设备一条龙”项目,许多橡机厂都看好这条“龙”的潜力,相继着手研制液压硫化机。
当时参与研究的厂家有五六家,但因我国轮胎工业那时尚未形成使用液压硫化机的大气候,轮胎企业基本没有直接使用经验,对液压硫化机的认识不够,加上国产液压元件也不过关,随后的十多年时间都没有形成大批量生产。
随着我国汽车工业和轮胎工业的发展对轮胎均匀性提出越来越高的要求,硫化机的工作精度越来越被人们所重视,液压硫化机的优越性开始得到充分的显现。
现我国液压硫化机被轮胎及橡机企业采用的比重逐渐增加,进入了快速产业化发展阶段。
1.2液压硫化机产业化势头液压硫化机是在机械式硫化机的基础上发展的,它克服了机械式硫化机固有的弱点,吸收了机械式硫化机的优点。
液压硫化机液压原理的设计
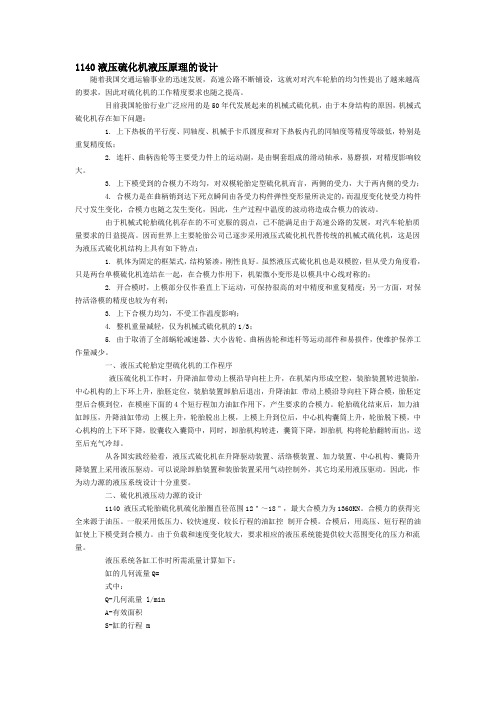
1140液压硫化机液压原理的设计随着我国交通运输事业的迅速发展,高速公路不断铺设,这就对对汽车轮胎的均匀性提出了越来越高的要求,因此对硫化机的工作精度要求也随之提高。
目前我国轮胎行业广泛应用的是50年代发展起来的机械式硫化机,由于本身结构的原因,机械式硫化机存在如下问题:1. 上下热板的平行度、同轴度、机械手卡爪圆度和对下热板内孔的同轴度等精度等级低,特别是重复精度低;2. 连杆、曲柄齿轮等主要受力件上的运动副,是由铜套组成的滑动轴承,易磨损,对精度影响较大。
3. 上下模受到的合模力不均匀,对双模轮胎定型硫化机而言,两侧的受力,大于两内侧的受力;4. 合模力是在曲柄销到达下死点瞬间由各受力构件弹性变形量所决定的,而温度变化使受力构件尺寸发生变化,合模力也随之发生变化,因此,生产过程中温度的波动将造成合模力的波动。
由于机械式轮胎硫化机存在的不可克服的弱点,已不能满足由于高速公路的发展,对汽车轮胎质量要求的日益提高。
因而世界上主要轮胎公司已逐步采用液压式硫化机代替传统的机械式硫化机,这是因为液压式硫化机结构上具有如下特点:1. 机体为固定的框架式,结构紧凑,刚性良好。
虽然液压式硫化机也是双模腔,但从受力角度看,只是两台单模硫化机连结在一起,在合模力作用下,机架微小变形是以模具中心线对称的;2. 开合模时,上模部分仅作垂直上下运动,可保持很高的对中精度和重复精度;另一方面,对保持活洛模的精度也较为有利;3. 上下合模力均匀,不受工作温度影响;4. 整机重量减轻,仅为机械式硫化机的1/3;5. 由于取消了全部蜗轮减速器、大小齿轮、曲柄齿轮和连杆等运动部件和易损件,使维护保养工作量减少。
一、液压式轮胎定型硫化机的工作程序液压硫化机工作时,升降油缸带动上模沿导向柱上升,在机架内形成空腔,装胎装置转进装胎,中心机构的上下环上升,胎胚定位,装胎装置卸胎后退出,升降油缸带动上模沿导向柱下降合模,胎胚定型后合模到位,在模座下面的4个短行程加力油缸作用下,产生要求的合模力。
探究液压轮胎硫化机应用
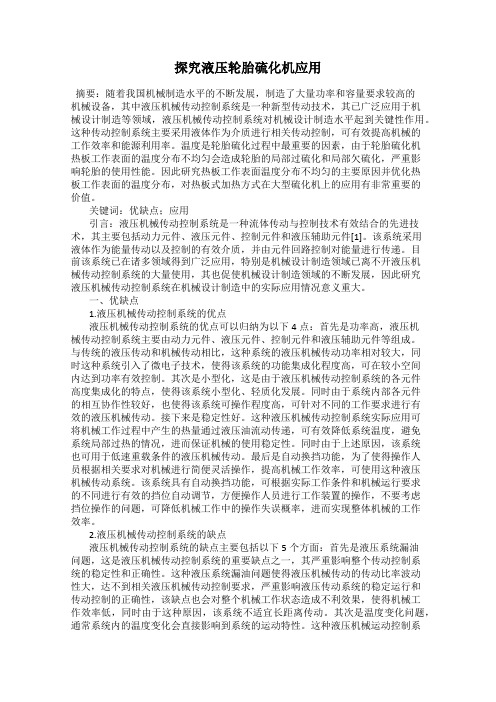
探究液压轮胎硫化机应用摘要:随着我国机械制造水平的不断发展,制造了大量功率和容量要求较高的机械设备,其中液压机械传动控制系统是一种新型传动技术,其已广泛应用于机械设计制造等领域,液压机械传动控制系统对机械设计制造水平起到关键性作用。
这种传动控制系统主要采用液体作为介质进行相关传动控制,可有效提高机械的工作效率和能源利用率。
温度是轮胎硫化过程中最重要的因素,由于轮胎硫化机热板工作表面的温度分布不均匀会造成轮胎的局部过硫化和局部欠硫化,严重影响轮胎的使用性能。
因此研究热板工作表面温度分布不均匀的主要原因并优化热板工作表面的温度分布,对热板式加热方式在大型硫化机上的应用有非常重要的价值。
关键词:优缺点;应用引言:液压机械传动控制系统是一种流体传动与控制技术有效结合的先进技术,其主要包括动力元件、液压元件、控制元件和液压辅助元件[1]。
该系统采用液体作为能量传动以及控制的有效介质,并由元件回路控制对能量进行传递。
目前该系统已在诸多领域得到广泛应用,特别是机械设计制造领域已离不开液压机械传动控制系统的大量使用,其也促使机械设计制造领域的不断发展,因此研究液压机械传动控制系统在机械设计制造中的实际应用情况意义重大。
一、优缺点1.液压机械传动控制系统的优点液压机械传动控制系统的优点可以归纳为以下4点:首先是功率高,液压机械传动控制系统主要由动力元件、液压元件、控制元件和液压辅助元件等组成。
与传统的液压传动和机械传动相比,这种系统的液压机械传动功率相对较大,同时这种系统引入了微电子技术,使得该系统的功能集成化程度高,可在较小空间内达到功率有效控制。
其次是小型化,这是由于液压机械传动控制系统的各元件高度集成化的特点,使得该系统小型化、轻质化发展。
同时由于系统内部各元件的相互协作性较好,也使得该系统可操作程度高,可针对不同的工作要求进行有效的液压机械传动。
接下来是稳定性好。
这种液压机械传动控制系统实际应用可将机械工作过程中产生的热量通过液压油流动传递,可有效降低系统温度,避免系统局部过热的情况,进而保证机械的使用稳定性。