如何学丰田
丰田生产方式学习笔记

丰田生产方式书荐丰田生产方式的强势究竟是什么?有三个层次:初级者认为“减少库存,甚至是零库存”;中级者认为“发现问题,提高生产率,提升产品质量”;高级者认为“在为解决出现的问题而反复作业期间,没有发现问题会产生不安,大家都在拼命地发现问题”。
中文版序一丰田生产方式总结为“精益生产理念”,说它“是一种不做无用功的精干型生产系统”。
丰田生产方式的本质是工业工程与日本丰田文化和管理模式相结合的产物。
丰田生产方式体系的每一个组成部分:改善;准时化;(包括人的因素的)自働化;看板管理;标准作业等都体现了上述的特点并具有很好的可操作性。
丰田生产方式不仅吸纳了通用公司“多品种少批量生产”的理念,还采纳了福特公司“彻底的合理化和成本降低”的思想。
中文版序二创新力经济是,由创新的想象力和创新力主宰的新的经济,即通过自主创新推动经济的发展。
获取与提升各类组织自主创新力的四大技术群:支持竞争目标、战略和决策的“竞争情报技术”;指导组织成功创新的“创新设计与管理的理论和方法”;系统保证创新质量的“现代质量管理与六西格玛法”;支撑创新力经济的生产方式“丰田生产方式”。
丰田生产的理念、系统与方法:“从(顾客的)需求出发”、“彻底杜绝浪费”是丰田生产方式的基本思想;“丰田生产方式是以多品种少批量方法制造出便宜的产品”,而这种生产方式是丰田公司今天成为世纪汽车领头羊的根本原因;丰田生产方式是对福特生产流水线和美国超市运作管理的继承和发展;“准时化和自働化”是贯穿其中的两大支柱;“丰田生产方式是一种生产方式,而看板则是一种管理方式”;“彻底杜绝浪费”的要点是“提高效率只有与降低成本结合起来才有意义”,以及“(生产线的)每个环节都要提高,(才能)收到整体效果”;“丰田生产方式在形式上属于拉动方式”,而并非只与拉式生产方式对应;丰田生产方式能有今天优异成果的原因是“不可拘泥于形式或个别现象”;正视自己的生产现场,改进企业的素质才能“谋求提高生产效率”。
《丰田工作法》学习心得体会
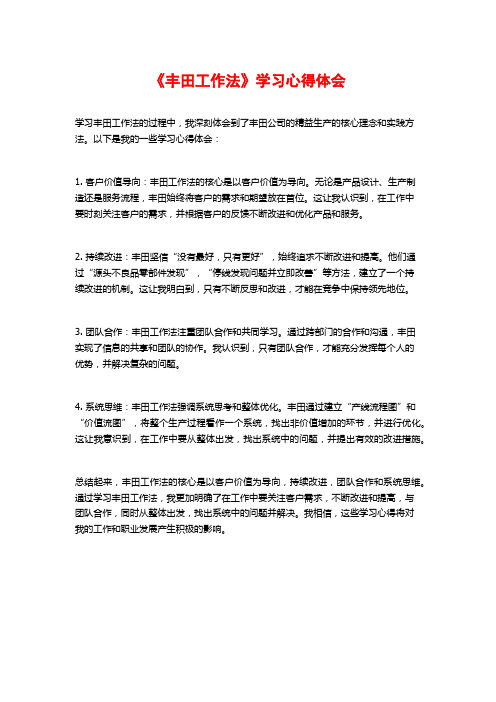
《丰田工作法》学习心得体会
学习丰田工作法的过程中,我深刻体会到了丰田公司的精益生产的核心理念和实践方法。
以下是我的一些学习心得体会:
1. 客户价值导向:丰田工作法的核心是以客户价值为导向。
无论是产品设计、生产制
造还是服务流程,丰田始终将客户的需求和期望放在首位。
这让我认识到,在工作中
要时刻关注客户的需求,并根据客户的反馈不断改进和优化产品和服务。
2. 持续改进:丰田坚信“没有最好,只有更好”,始终追求不断改进和提高。
他们通
过“源头不良品零部件发现”,“停线发现问题并立即改善”等方法,建立了一个持
续改进的机制。
这让我明白到,只有不断反思和改进,才能在竞争中保持领先地位。
3. 团队合作:丰田工作法注重团队合作和共同学习。
通过跨部门的合作和沟通,丰田
实现了信息的共享和团队的协作。
我认识到,只有团队合作,才能充分发挥每个人的
优势,并解决复杂的问题。
4. 系统思维:丰田工作法强调系统思考和整体优化。
丰田通过建立“产线流程图”和“价值流图”,将整个生产过程看作一个系统,找出非价值增加的环节,并进行优化。
这让我意识到,在工作中要从整体出发,找出系统中的问题,并提出有效的改进措施。
总结起来,丰田工作法的核心是以客户价值为导向,持续改进,团队合作和系统思维。
通过学习丰田工作法,我更加明确了在工作中要关注客户需求,不断改进和提高,与
团队合作,同时从整体出发,找出系统中的问题并解决。
我相信,这些学习心得将对
我的工作和职业发展产生积极的影响。
学习丰田精益管理的基础多能工培养
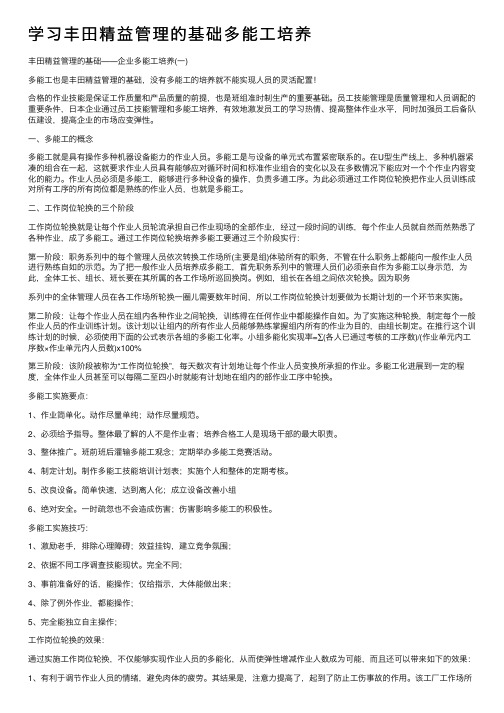
学习丰⽥精益管理的基础多能⼯培养丰⽥精益管理的基础——企业多能⼯培养(⼀)多能⼯也是丰⽥精益管理的基础,没有多能⼯的培养就不能实现⼈员的灵活配置!合格的作业技能是保证⼯作质量和产品质量的前提,也是班组准时制⽣产的重要基础。
员⼯技能管理是质量管理和⼈员调配的重要条件,⽇本企业通过员⼯技能管理和多能⼯培养,有效地激发员⼯的学习热情、提⾼整体作业⽔平,同时加强员⼯后备队伍建设,提⾼企业的市场应变弹性。
⼀、多能⼯的概念多能⼯就是具有操作多种机器设备能⼒的作业⼈员。
多能⼯是与设备的单元式布置紧密联系的。
在U型⽣产线上,多种机器紧凑的组合在⼀起,这就要求作业⼈员具有能够应对循环时间和标准作业组合的变化以及在多数情况下能应对⼀个个作业内容变化的能⼒。
作业⼈员必须是多能⼯,能够进⾏多种设备的操作,负责多道⼯序。
为此必须通过⼯作岗位轮换把作业⼈员训练成对所有⼯序的所有岗位都是熟练的作业⼈员,也就是多能⼯。
⼆、⼯作岗位轮换的三个阶段⼯作岗位轮换就是让每个作业⼈员轮流承担⾃⼰作业现场的全部作业,经过⼀段时间的训练,每个作业⼈员就⾃然⽽然熟悉了各种作业,成了多能⼯。
通过⼯作岗位轮换培养多能⼯要通过三个阶段实⾏:第⼀阶段:职务系列中的每个管理⼈员依次转换⼯作场所(主要是组)体验所有的职务,不管在什么职务上都能向⼀般作业⼈员进⾏熟练⾃如的⽰范。
为了把⼀般作业⼈员培养成多能⼯,⾸先职务系列中的管理⼈员们必须亲⾃作为多能⼯以⾝⽰范,为此,全体⼯长、组长、班长要在其所属的各⼯作场所巡回换岗。
例如,组长在各组之间依次轮换。
因为职务系列中的全体管理⼈员在各⼯作场所轮换⼀圈⼉需要数年时间,所以⼯作岗位轮换计划要做为长期计划的⼀个环节来实施。
第⼆阶段:让每个作业⼈员在组内各种作业之间轮换,训练得在任何作业中都能操作⾃如。
为了实施这种轮换,制定每个⼀般作业⼈员的作业训练计划。
该计划以让组内的所有作业⼈员能够熟练掌握组内所有的作业为⽬的,由组长制定。
丰田工作法:丰田的工作哲学与方法大全_札记

《丰田工作法:丰田的工作哲学与方法大全》阅读随笔目录一、丰田工作法的核心理念与特点 (2)1. 丰田的哲学思想和工作文化 (2)1.1 精益求精,追求卓越品质 (4)1.2 团队合作,全员参与管理 (5)1.3 注重创新,适应变革环境 (6)1.4 客户至上,满足用户需求 (7)2. 丰田工作法的特点分析 (8)2.1 目标明确,计划性强 (9)2.2 注重细节,精益求精 (10)2.3 强调执行力,追求实效 (12)2.4 持续改进,不断优化 (13)二、丰田工作法的具体实践方法 (14)1. 生产流程优化与管理 (15)1.1 精益生产流程的建立与实施 (17)1.2 标准化作业与生产效率提升 (18)1.3 生产线平衡与在制品控制 (20)1.4 生产过程中的质量控制 (21)2. 人才培养与团队建设 (22)2.1 丰田式人才培养理念及方法 (24)2.2 团队建设与沟通技巧培训 (25)2.3 员工职业生涯规划与支持 (26)2.4 多元化背景下的文化融合 (27)三、丰田工作法在汽车产业中的应用实例 (28)一、丰田工作法的核心理念与特点丰田工作法,作为丰田生产方式(Toyota Production System, TPS)的精髓,其核心理念在于持续改进、尊重个性、全员参与以及精益求精。
这一工作法并非仅仅关注生产效率的提升,更强调在每一个环节中寻求最佳实践,以实现产品质量、成本控制、交货期等多方面的均衡优化。
丰田工作法的特点尤为显著,它注重个性化定制,即根据每位员工的技能和特长来分配工作任务,从而激发员工的创造力和责任感。
丰田工作法倡导全员参与,鼓励员工在工作中不断发现问题、解决问题,通过持续的改进过程提升工作效率和质量。
丰田工作法还强调对细节的极致追求,无论是生产线的布局还是设备的维护,都力求做到尽善尽美。
丰田工作法是一种以人为本、追求卓越的工作哲学和方法论。
它引导人们在工作中不断学习、创新和进步,最终实现个人和企业的共同发展。
丰田车辆使用技巧教程
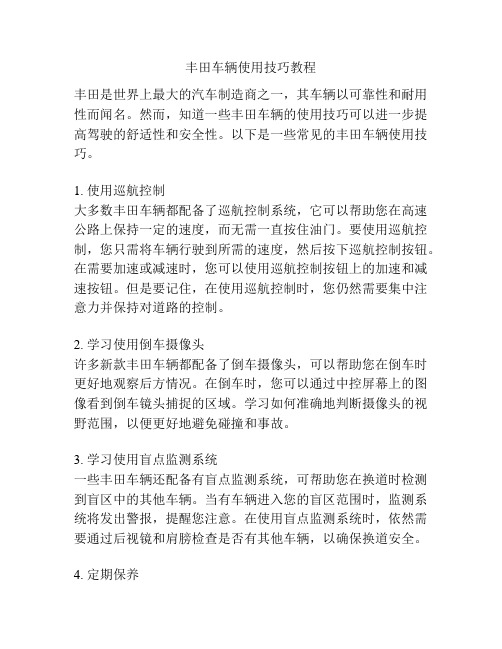
丰田车辆使用技巧教程丰田是世界上最大的汽车制造商之一,其车辆以可靠性和耐用性而闻名。
然而,知道一些丰田车辆的使用技巧可以进一步提高驾驶的舒适性和安全性。
以下是一些常见的丰田车辆使用技巧。
1. 使用巡航控制大多数丰田车辆都配备了巡航控制系统,它可以帮助您在高速公路上保持一定的速度,而无需一直按住油门。
要使用巡航控制,您只需将车辆行驶到所需的速度,然后按下巡航控制按钮。
在需要加速或减速时,您可以使用巡航控制按钮上的加速和减速按钮。
但是要记住,在使用巡航控制时,您仍然需要集中注意力并保持对道路的控制。
2. 学习使用倒车摄像头许多新款丰田车辆都配备了倒车摄像头,可以帮助您在倒车时更好地观察后方情况。
在倒车时,您可以通过中控屏幕上的图像看到倒车镜头捕捉的区域。
学习如何准确地判断摄像头的视野范围,以便更好地避免碰撞和事故。
3. 学习使用盲点监测系统一些丰田车辆还配备有盲点监测系统,可帮助您在换道时检测到盲区中的其他车辆。
当有车辆进入您的盲区范围时,监测系统将发出警报,提醒您注意。
在使用盲点监测系统时,依然需要通过后视镜和肩膀检查是否有其他车辆,以确保换道安全。
4. 定期保养为了确保丰田车辆的正常运行,定期保养是必不可少的。
根据您的车辆型号和使用情况,您可以参考车辆使用手册中的保养建议,例如定期更换机油、检查轮胎及制动系统、清洁空气滤清器等。
定期保养将延长车辆的使用寿命,并确保驾驶的安全和舒适。
5. 学习安全驾驶技巧最后,无论是丰田车辆还是其他品牌的车辆,掌握安全驾驶技巧都是至关重要的。
例如,遵守交通规则,保持安全行驶速度,保持安全驾驶距离以及提前预测其他车辆和行人的行为等。
此外,不要驾驶时玩手机或疲劳驾驶,确保您的注意力集中在驾驶任务上。
综上所述,这些丰田车辆使用技巧可以帮助您更好地驾驶丰田汽车,并提升驾驶经验的安全性和舒适性。
无论您是新手还是有经验的驾驶员,了解这些技巧都是非常有益的。
记住,安全驾驶是最重要的,随时关注道路情况,并适应不同的驾驶环境。
《丰田模式教材》课件
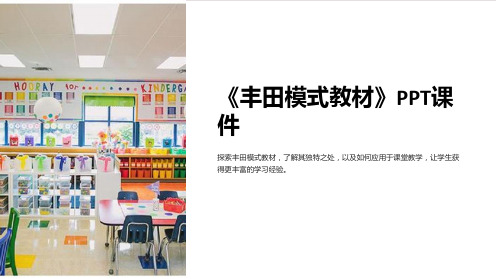
《丰田模式教材》PPT课 件
探索丰田模式教材,了解其独特之处,以及如何应用于课堂教学,让学生获 得更丰富的学习经验。
丰田模式教材简介
丰田模式教材是一种创新的教学方法,灵感来源于丰田汽车公司的生产流程管理。它强调高效率、持续改进和 团队合作的重要性。
丰田模式教材的特点
精确性
丰田模式教材注重每一个细节,以确保学生获得准确的知识和技能。
2 2. 设计活动和课程
根据学习目标设计具有挑战性和实践性的活 动,以提供丰富的学习体验。
3 3. 实施教学活动
根据设计的活动和课程安排进行教学实施, 引导学生参与和合作。
4 4. 评估和反馈
通过评估学生的学习成果和反馈,改进教学 方法和活动设计。
总结和要点
丰田模式教材是一种创新的教学方法,通过团队合作、持续改进和问题解决来提高学生的学习效果和能力。
大学课堂使用丰田模式教材可以培养学
生团队合作和领导能力,并提供实际项
目和案例来应用所学知识。
3
应用于职业培训
丰田模式教材可以帮助培训学员提高生 产和管理效率,使他们成为职场上的高 绩效团队成员。
丰田模式教材的实施步骤
1 1. 分析学习目标
明确学习目标和预期结果,以便制定合适的 教学方法和评估标准。
灵活性
适应不同的教学场景和学习需求,丰田模式教材可以根据实际情况进行调整和改进。
可持续性
倡导学习的持续改进和不断追求卓越,使学生能够不断提升自己的能力和品质。
丰田模式教材的主要内容
团队合作
鼓励学生通过小组合作来解决问 题,培养团队协作和沟通能力。
持续改进
问题解决
通过反思和不断优化的循环过程, 帮助学生提高学习效果和成果。
浅谈学习丰田模式的几点体会
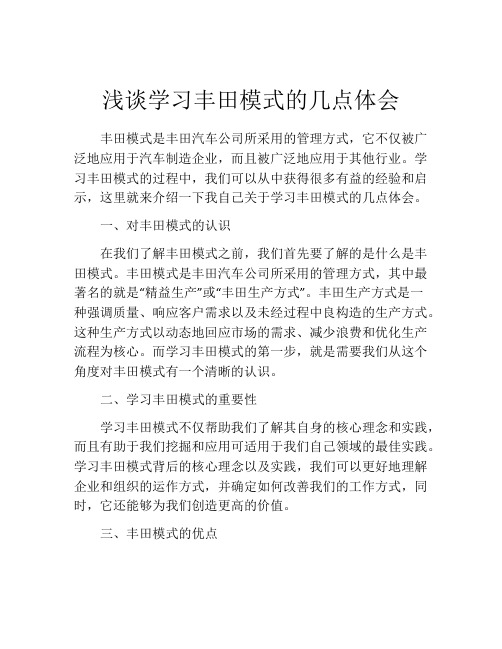
浅谈学习丰田模式的几点体会丰田模式是丰田汽车公司所采用的管理方式,它不仅被广泛地应用于汽车制造企业,而且被广泛地应用于其他行业。
学习丰田模式的过程中,我们可以从中获得很多有益的经验和启示,这里就来介绍一下我自己关于学习丰田模式的几点体会。
一、对丰田模式的认识在我们了解丰田模式之前,我们首先要了解的是什么是丰田模式。
丰田模式是丰田汽车公司所采用的管理方式,其中最著名的就是“精益生产”或“丰田生产方式”。
丰田生产方式是一种强调质量、响应客户需求以及未经过程中良构造的生产方式。
这种生产方式以动态地回应市场的需求、减少浪费和优化生产流程为核心。
而学习丰田模式的第一步,就是需要我们从这个角度对丰田模式有一个清晰的认识。
二、学习丰田模式的重要性学习丰田模式不仅帮助我们了解其自身的核心理念和实践,而且有助于我们挖掘和应用可适用于我们自己领域的最佳实践。
学习丰田模式背后的核心理念以及实践,我们可以更好地理解企业和组织的运作方式,并确定如何改善我们的工作方式,同时,它还能够为我们创造更高的价值。
三、丰田模式的优点丰田模式的优点体现在其高度优化、生产效率高、协作性强等方面。
这些特点使其获得了企业的成功并帮助企业提高了质量、效率和生产力。
故而,在学习丰田模式的过程中,我们可以将这些优点运用于我们自己的实际工作中,从而获得更好的效果。
四、学习丰田模式的步骤首先,我们要充分了解企业执行丰田模式以达到更好的运营结果,并深入研究丰田模式在典型企业中的实践。
其次,在这个过程中,我们需要更加深入地了解企业的总体运作方式和各个应用领域的侧重点。
最后,我们需要把丰田模式的实践运用到我们的工作中。
总之,成为一名丰田模式的实践者需要一定的技能和经验,但只要将其应用于实践中,我们的工作就会得到更好的改进和提升。
五、学习丰田模式的重点在学习丰田模式的过程中,我们需要关注以下几个重点。
首先,我们需要了解整个流程、每一个切入点,尤其是丰田模式实施背景和目的的细节。
5Why问题分析法
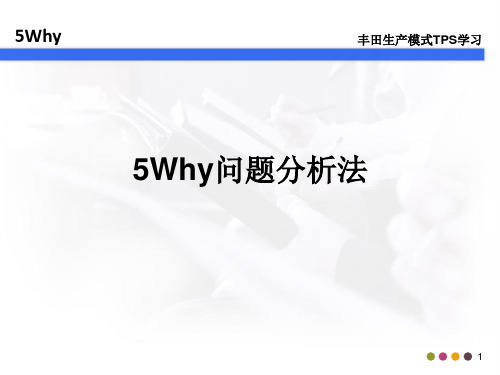
原因点 原因点 原因点
Why? 1 原因1
Why? 2 原因2
Why? 3 原因3
Why? 4 原因4
Why? 5
根本原因
纠正措施
吸取教训
系统解决问题 5WHY
丰田生产模式TPS学习
为什么会流出 (检验/试验/抽检)
问题点识别(大的、模糊的、复杂的) 阐明问题 已定位原因区
原因点 原因点 原因点
Why? 1 原因1
传统的方法
系统方法
不采用
问题
解决方法 (“快速解决“
)
采用
问题
D0
D1
D2
Why
D3
Why
D4
Why
D5
Why D6
Why
D7 D8
解决方法 (一劳永逸)
16
5Why
丰田生产模式TPS学习
为什么要学习和使用5why:
系统的问题解决方法和传统的质量控制工具均有助于改
善业绩,但并非唯一的途径。
问题比率
丰田生产模式TPS学习
第二部分 — 原因调查:
第六步:识别和确认异常事件的直接原因 如果原因明显,验证它。如果原因不明显,考虑潜在的
原因和检查类似事故,以事实为基础确认直接原因。 问: • 问题为什么发生? • 我能看到问题的直接原因吗? • 如果不能,我猜想潜在原因是什么? • 我怎么核实最可能的潜在的原因? • 我怎么确认直接原因?
如果不想这样! 千万别忘记第一步
27
5Why
丰田生产模式TPS学习
第一部分 — 把握现状:
第一步:识别问题 在过程的第一步,你可以意识到问题可能是大的、含糊
的或是复杂的,你有一些信息,但没有详细事实。 问: • 我了解什么?
学习丰田生产方式的心得体会

Remember, only your smile can make you find light in the endless darkness.(页眉可删)学习丰田生产方式的心得体会学习丰田生产方式的心得体会1日本的产品在世界上一向以简洁小巧、精致、质量好、功能先进等优点著称。
为了持续产品竞争力的不断提升,务必降低产品价格,同时保证产品品质持续原有水平,甚至超越原有产品,因此想方设法降低成本、提高科技含量,成为了日本公司重点研究的课题。
对于大批量制造,从流水线上生产出的产品而言,原材料成本和管理成本构成了日本产品的主要成本。
由于日本资源有限,产品的原材料大多进口,成本不容易控制,因此如何控制管理成本是决定产品价格能否下降的主要因素。
"即使是干燥的毛巾,如果动脑筋也能让它挤出水",这句名言出自丰田汽车工业社长丰田英二。
多数企业在谈到如何改善管理提高效率时总以人员配备合理、生产效率已经很高等等的理由来表示公司的效率已没有能够提升的空间。
然而用丰田的生产方式来对照企业现有的生产方式仍然能够发现有许多不足,似乎还有许多"水分"能够拧出。
消除浪费是丰田生产方式的唯一目的。
消除浪费是降低成本的有效手段。
在制造过程成本中,丰田总结了7种浪费。
生产过剩的浪费、制造不良品的浪费、停工等活的浪费、动作上的浪费、搬运的浪费、加工本身的浪费、库存的浪费。
丰田将浪费的定义范围扩大化,把只使成本增加而不产生附加价值的作业都称为浪费,以上7种浪费即是"干毛巾中的水分".丰田认为控制并改善这些浪费就能提高效率并且高品质的生产。
丰田生产实现消除浪费的两大支柱是,及时化与自化。
及时化是指在需要的时候按照需要的量生产需要的产品供给各工序。
多数企业认为机器及员工在8小时内不停工作,生产商品就是机器利用率以及人工效率最大化了。
丰田则认为这样会生产出很长一段时间销售不出去的产品,这样的结果有两个缺点:1、流动资金占用率提高了。
学习丰田“5问”法,心得体会

学习丰田“5问”法,心得体会人生在世,难免遇到各种问题。
人生,就是一场遇到问题、解决问题、再遇到新问题、解决新问题……的旅行。
很多时候,问题难以解决,并不是我们缺乏改变的意愿,也不是缺少知识或者方法技能,而是没有找准问题,找到最根本的问题。
爱因斯坦说,人们不能在制造问题的层次来解决问题。
1、没法坚持跑步,怎么办?曾经有个朋友很苦恼,想坚持跑步,买了书和音频视频课,加入了各种训练营,打卡,交保证金,可惜,最终都没有坚持下来。
折腾几次以后,这位朋友很受挫,苦恼,觉得自己毅力真差。
后来,她找人咨询,和教练展开了一番对话:教练问:你为什么要去跑步?她回答:因为跑步能让我更健康。
教练问:为什么跑步能让你更健康呢?她回答:因为跑步能燃烧卡路里,减少脂肪教练问:为什么要燃烧卡路里,减少脂肪?她回答:因为那样能减肥,保持身材苗条。
教练问:你为什么要减肥?她回答:因为我有点胖教练问:为什么会胖?她回答:因为我饮食习惯不好。
教练问:为什么饮食习惯不好?她回答:因为我喜欢吃油炸的、高热量的食物,晚上还会吃夜宵。
问到这里,她恍然大悟。
表面上,她的问题是“没法坚持跑步”;但是她内心深处真正想要的,并不是养成跑步的习惯,而是保持苗条的身材。
所以,表面上她羡慕那些坚持跑步的人,但当她看到那些每年跑步几千公里的大神的分享,她内心也没有多大动力,所以她经常三天打鱼两天晒网。
导致她难以实现“保持苗条身体”的主要原因,也不是跑步量不够,而是饮食习惯不好。
对她而言,要实现目标,最简单的方式,可能是想办法“调整饮食习惯”。
很多时候,我们难以解决某个问题,并不是因为我们缺乏知识,很有可能是我们并没有找准问题,没有找出深层次的问题。
以上故事,改编自田俊国老师的《组织学习新范式》中,定义问题起点的章节,感谢田老师。
2、丰田五问这个提问方法,源自大名鼎鼎的丰田公司,5个“why”,江湖人称“丰田五问”。
这个方法看起来很简单,就是连续追问五个为什么。
丰田车4C钥匙学习方法

丰田车4C钥匙学习方法丰田, 钥匙, 学习丰田, 钥匙, 学习1)插入原钥匙2)把钥匙插入点火开关,在15秒内转动到ON位置5次,最后停在ON位置在20秒内打开并关闭司机门6次,头一次打开并关闭司机门要在15秒内,20秒内拿走原钥匙,10秒钟内插入要增加的钥匙,10秒钟内转动点火开关到ON位置,并且保持60秒,从点火开关中拔出钥匙,然后打开再关闭司机门,编码结束。
丰田凌志430遥控匹配方法丰田, 凌志2000年8月以后的LS430(车型代码UCF30),2001年5月以后的SC430(车型代码UZZ40)车型。
设定方法:(1)驾驶员侧车门打开未上锁,从点火开关中拔出点火钥匙(2)在5s内将点火钥匙插入点火开关中并拔出2次;(3)在40s内关闭并打开驾驶员侧车门2次;(4)插入点火钥匙并拔出;(5)在40s内再次关闭并打开驾驶员侧车门2次;(6)将点火钥匙插入点火开关;(7)关闭车门;(8)将点火钥匙从OFF到ON再回到OFF位置,选取所需模式,间隔时间大约1s:1次表示添加模式;2次表示改写模式;3次表示确认模式;5次表示禁止模式;(9)拔出点火钥匙(10)除禁止模式外,确认所选的模式。
门锁自动上锁、开锁的循环次数与步骤(8)相一致。
若选择确认模式,门锁将自动循环的次数(2s间歇)与当前所登记遥控器的数量一致,打开车门将完成操作程序。
若选择禁止模式,打开车门将完成操作程序。
(11)对于添加或改写模式,确认门锁在40s内进行。
①同时按下遥控器上的上锁和开锁按钮约1~1.5s然后松开。
②在3s内,按下遥控器上的上锁按钮1s以上,然后松开。
③若遥控器设定成功,电动门锁将自动上锁-开锁循环1次,若上述过程出现问题,门锁将循环2次,这时须返回并重复步骤①和②。
④如果有多个遥控器设定,重复步骤①和③。
(12)打开驾驶员侧车门,完成操作程序。
匹配通用方法遥控器, 丰田适用于丰田佳美2。
4,皇冠锐志2。
5,RAV4,新卡罗拉。
《丰田生产方式》及《丰田汽车精益模式的实践》学习心得

《丰田生产方式》及《丰田汽车精益模式的实践》学习心得作为日本汽车制造行业中的领军企业,丰田汽车公司的成功并非偶然。
其以“精益生产”为核心理念,实行了一套独特的生产管理模式,称为“丰田生产方式(TPS)”。
在《丰田生产方式》及《丰田汽车精益模式的实践》中,作者详细介绍了丰田汽车公司的生产管理模式和实践经验,对于国内企业学习丰田汽车公司的先进经验起到了很好的启示和促进作用。
首先,TPS是一种基于“精益生产”的生产管理体系。
它通过不断地改进,实现了生产过程中的“浪费物”减少,从而提升了生产效率。
TPS体系实施的核心是“拉动生产”,而不是“推动生产”,这意味着只有在客户提交订单之后,企业才会采购原料,生产产品,使得生产过程更加高效。
其次,丰田汽车公司通过“精益生产”的管理模式,提高了高效协作以及产品质量的方面。
企业员工作为核心资源,不仅仅在在生产过程中发挥了关键作用,同时还倡导员工参与产品设计、流程改进和生产主管等业务决策中。
通过激发员工创新思维,提高企业的领先竞争力。
另一个值得一提的是,丰田汽车公司的管理模式非常注重持续改进。
精益生产管理模式的一个特点是不断的排错,从而逐步完善生产过程。
丰田汽车公司将错误视为改进生产过程的机遇,不断寻找并解决整个生产过程中的问题。
这种“持续改进”模式,为企业赢得了改善和提高产品质量的机遇,打造出了高效的生产流程。
总的来说,学习丰田汽车公司的生产管理模式,需要注重以下几点。
首先,TPS是一种精益生产管理模式,需要企业所管理的人员具备创新思维和精益生产技能。
其次,企业要注重客户需求,推行“拉动式”生产。
最后就是要不断循环,在生产过程中寻找和解决问题,不断完善生产能力。
总之,《丰田生产方式》及《丰田汽车精益模式的实践》这两本书向我们展示了丰田公司成功的管理模式,以及该模式的实施方法。
通过学习丰田公司的经验,我们可以不断提高企业的管理水平,为企业的未来发展起到重要的促进作用。
学习丰田十意识8D管理方法心得体会
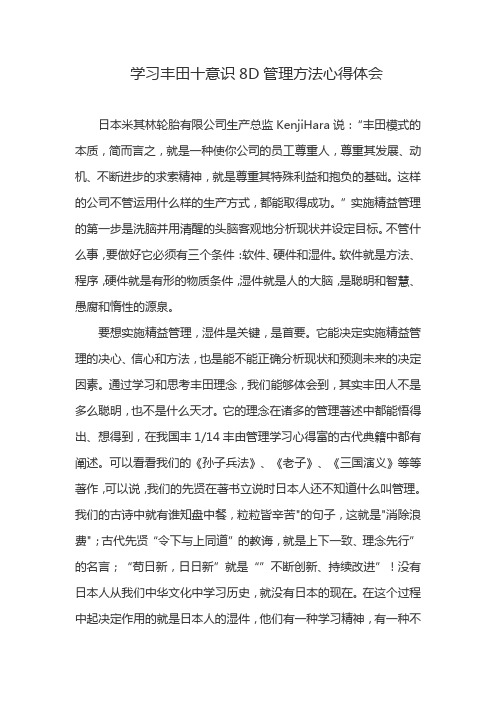
学习丰田十意识8D管理方法心得体会日本米其林轮胎有限公司生产总监KenjiHara说:“丰田模式的本质,简而言之,就是一种使你公司的员工尊重人,尊重其发展、动机、不断进步的求索精神,就是尊重其特殊利益和抱负的基础。
这样的公司不管运用什么样的生产方式,都能取得成功。
”实施精益管理的第一步是洗脑并用清醒的头脑客观地分析现状并设定目标。
不管什么事,要做好它必须有三个条件:软件、硬件和湿件。
软件就是方法、程序,硬件就是有形的物质条件,湿件就是人的大脑,是聪明和智慧、愚腐和惰性的源泉。
要想实施精益管理,湿件是关键,是首要。
它能决定实施精益管理的决心、信心和方法,也是能不能正确分析现状和预测未来的决定因素。
通过学习和思考丰田理念,我们能够体会到,其实丰田人不是多么聪明,也不是什么天才。
它的理念在诸多的管理著述中都能悟得出、想得到,在我国丰1/14丰由管理学习心得富的古代典籍中都有阐述。
可以看看我们的《孙子兵法》、《老子》、《三国演义》等等著作,可以说,我们的先贤在著书立说时日本人还不知道什么叫管理。
我们的古诗中就有谁知盘中餐,粒粒皆辛苦"的句子,这就是"消除浪费";古代先贤“令下与上同道”的教诲,就是上下一致、理念先行”的名言;“苟日新,日日新”就是“”不断创新、持续改进”!没有日本人从我们中华文化中学习历史,就没有日本的现在。
在这个过程中起决定作用的就是日本人的湿件,他们有一种学习精神,有一种不服输的意念,有一种坚决执行的忠诚!丰田的U”形线、“一个流”,不也是学习美国汽车生产过程后进行改进的结果吗?这就是湿件的作用。
所以我们学习丰田经验应该首先研究一下丰田人是怎么学习的,首先解决我们的湿件问题。
这个问题不决定,不管学习什么经验也不会有明确的目标、可行的计划,也不会有踏实的行动和明显的效果。
因为湿件的定位决定行为的定位。
学习丰田管理模式与4R管理分享

把选经人营、模用式人、 规育则人形、成留文人化
让人进入 责任状态
结论:
百分百责任来自于个人的成就感和危 机感!
:流程和组织不断改善
在检查的过程中找瓶颈,并不断突破!
(用显微镜找出你执行中的瓶颈)
即时激励 Reward
检查跟踪 Review
结果定义 Result
一对一责任 Responsibility
结果定义
客 户 价 值
价值兑现
结果思维:
双赢 客户价值
任务 做到
服务
客户
结果 营销
结论:
● 成功没有捷径,为了明天必须经过黑 夜!这就是规律!
● 双赢的客户价值是持续的关键!
2:百分百责任(心态)
结果定义 Result
即时激励 Reward
一对一责任 Responsibility
检查跟踪 Review
R4:即时激励(文化——仪式、证书)
即时激励 Reward
结果定义 Result
一对一责任
Responsibility
检查跟踪 Reviw
结论
商务(企业管理)活动如果不是建立 在道德的基础上,便不但于社会(企业)无 益,而且会像所有其他不道德的人和事一样, 终将被人们所摒弃!
——C.马克斯.基兰
•
2.变化太快.
2.有战略眼光.
•
3.太容易变化.
3.学习力强.
•
4.对公司业务不太熟悉.
4.思维快.
•
5.一杆子杆到底.
5.行动快.
•
6.很辛苦很累.
6.生命人才的能力强.
•
7.学习要有针对性.
7.尊重人性学习团队打造强.
学丰田的三大关键门槛

人认 为 :中国企业真 正需要 学 习的 ,
同时也是 最难学的 , 是其具体 管理方
理要效益 的阶段 。 这或许是我 国企 业 定青山不放松 ”的 - t 筋 ” -  ̄ 精神 ,以 .
学习丰 田的最大 障碍。
法 、技术 背后 的 管理 思 想和 管理 思
须等到客户订 单完全确定 、不会更改 的 内在精髓 。其主要特征 :
9 中外管理 20 1 2 07.0
维普资讯
延续 , 不利于 ” 传统 ”的养成和传承 。
续 改善 ” 的动 机 。
—
—
企 业对 员工权利较大而责任较小 ,
第二 它具有 “ 整体 性” 属性 , 是 包含诸 多要 素和环节 、内部 高度一体 “ 能力” ,还是 “ 绩效”?
维普资讯
学丰田的三大关键门槛
文 /施 炜
主国全些真 需要堂 ~ 匝时 是最 堂 , 一 _ 堇 黄卮的笪理星丝 一 及 眭的笪理 辑
今年 6月 , 我随 《 中外管 理》访 险 必须按必要数量 多频次 时 ” 准 采 续 改善 ” 团队行 为 , 是 而非个 人行为;
化 信息 化 集成化 的制造设备也 为 ” 均衡生产 ” 工序 中保证质量 ” 提供 了条件和 支持 。 都成长于改革 开放 的特殊 时期 : 场 市 机 会爆发性涌现 ;土地 劳动供给 获
的规范 精 细行为 ,而非 随意 、运动 其二 ,它是一种精神状态 。即探 究规律 追求完美 、 注重细节 、 坚持不 懈 的内驱意志力及思维方式 。 持续改
日研 修第三 团 赴 日本 丰田公司参观 购 , 有这 样才能使有 限的资金周转 只 它是工 作时间 内的必要行 为 , 而非业 而非短期 、不连续行 为;它是积 累信
- 1、下载文档前请自行甄别文档内容的完整性,平台不提供额外的编辑、内容补充、找答案等附加服务。
- 2、"仅部分预览"的文档,不可在线预览部分如存在完整性等问题,可反馈申请退款(可完整预览的文档不适用该条件!)。
- 3、如文档侵犯您的权益,请联系客服反馈,我们会尽快为您处理(人工客服工作时间:9:00-18:30)。
如何学习丰田“葫芦画瓢”是无效的!在同行业中规模位居世界第三的丰田,2005年度销售额达到21.04万亿日元(约合1830亿美元);利润为1.8783万亿日元(约合163亿美元),已连续6年创历史新高;其净利润达到1.37万亿日元(约合119亿美元),已连续第四年创新高。
根据今年第一财季(3-6月)的优异表现,丰田预计2006年度利润还将创新高。
同时,丰田还是标准普尔信用的最高等级(AAA),也是全球惟一拥有该评级的汽车制造商。
而丰田一骑绝尘的背后,却是美国汽车公司纷纷陷入亏损泥潭无力自拔——“老大”通用汽车,去年竟巨亏86亿美元!而“老二”福特,去年虽盈利20亿美元,今年一季度便巨亏12亿美元跌入谷底;“老四”戴姆勒·克莱斯勒去年利润也不过61亿美元……也就是说,丰田一家的净利润,就比欧美三大汽车公司的利润总和还多!我们应该学习丰田管理。
丰田专家堀切俊雄这样说:“我在中国还没有看到一家企业学习丰田学得好。
中国的很多CEO都很重视学习丰田,但中国企业学习丰田的最大障碍,正是CEO自身,也就是他采取的推进方式。
对于推广TPS,采用‘树样板’的方式是根本无效的。
TPS要推进,就必须是全员推进、全线推进。
当然,不同部门可以推进不同的TPS内容,但落实到行动,形成互相竞争的气氛是很重要的。
而且也只有激发起全员的热情,CEO自己才能更轻松些。
”我认为推进丰田生产管理需要专设机构,但不可都指望它,关键还是全员参与,实现“活性化”。
“读书”是徒劳的!用看书的方法学丰田,是绝对不行的!因为还没有一本书能把丰田的精髓准确表达出来,反而误解很多。
照着这些书学,只会走偏。
如果把TPS当作知识来学,当作培训来做,那就是毫无意义的。
TPS的实质,就是去“行动”。
没有行动的思想,根本就不是思想。
只有行动中的改善,才是真正的改善,否则都会反弹。
不能用计划来修订计划,一定要用行动。
不要追求完美再行动,只要有六成把握就去做,在做的过程中不断改善。
TPS在哪里?在我们大家的心里!一定要动员大家一起做!警惕惩罚文化中国企业普遍存在的“惩罚文化”也是实践TPS的重要障碍。
佐佐木元反对中国企业在管理中一出现失误就罚款。
管理中不出现失误是不可能的,管理者要允许员工失误。
当我们指责员工没有按照规章去做时,我们有没有反省企业是否制定了有利于员工执行的规章?员工不能执行的真正原因是什么?要由此入手改善工作标准,而不是惩罚。
急需培养一批管理人才我认为我们企业已经培养出了一批经营人才、技术人才,但却缺少管理人才,特别是能在管理现场识破浪费存在、协调改进生产的管理人才。
我认为我们现在,应该是着力培养管理者的时候了,尤其是集团下设的子公司更是迫切地需要这样的人才。
TPS对于人才的培养方式,就是在人才富余之后进行骨干抽离,从而迫使管理者创新用人结构,用全新的视角审视自己原有的工作方式。
这一方面可以增加基层新人被提升的机会,同时也锻炼了他的创新精神。
“这样是有风险的。
但只有知道管理风险,管理才能创新,这需要上层具有勇气。
”佐佐木元说。
多问“Why”,少问“How”我们现在学习丰田管理,应多问“Why”,少问“How”!也就是:多问丰田为什么要这样做,而不是纠缠于它如何去做。
因为只有前者是可以拿来借鉴的,而后者一定是不适合自己企业的。
我们要把握这次学习的契机,深化改革,把丰田理论用到实处,更好地实现自身价值。
向丰田学什么?作者:天津友发钢管集团有限公司总经理李茂津尽管已取得了巨大的成功,管理也已经做到精益化,但丰田却“永远把今天的水平看成是最差的”。
2006年7月,我们一行40余人赴日本丰田、达登、电装等公司参观学习。
通过参观,我们感受到了世界一流企业的高度机械化,管理的人性化。
整洁有序的现场生产环境和强烈的环保意识。
通过专家授课,我们对TPS(丰田生产方式)及包括杜绝浪费、标准化作业、6S管理和持续改进为主要内容的精益生产效果有了较为深入的了解,更认清了我们的企业与世界一流企业的差距。
下面我结合所见所闻所学,谈点感受。
全员参与持续改进丰田汽车的产量虽然只有美国汽车产量的三分之一,但每年赚数十亿甚至上百亿美元,目前已超过美国三大汽车巨头(通用、伏特、克莱斯勒)利润和总和,任何时候都有300亿-500亿美元的现金储备,这些足以使任何人相信这家公司一定做对了些什么。
尽管已经取得了巨大的成功,管理也已经做到精益化,但丰田却“永远把今天的水平看成是最差的”。
2005年丰田共接到员工的60多万条建议,其中99%被采纳。
建议被采纳的,每条奖励建议人500-200000日元(按目前汇率,100日元约合人民币6.44元)。
可以说丰田今天在精益生产上的一切成果都是通过激励员工持续改进带来的。
正如我们在车间看到的一句口号:“好产品好主意”。
这就是丰田对员工的要求。
友发也鼓励员工提合理化建议,但并未形成风气,还远未成为员工的习惯和自觉行动,加上处理方法、程序不很成熟,执行力度不够,因而效果不很明显。
结合丰田的具体做法,我领悟到:第一,改善首先从小事做起,不要总想着做大的变革,而是马上把力所能及的小事做好,常此下去就会有惊人的结果。
巧迟不如拙速;第二,改善后的效果要让企业和每个人明显看的见;第三,拿出因改善而增效部分的一定比例回馈给改善者,并且改善者要被认可、表扬甚至提升,以此作为改善者及其他员工下次创新的动力;第四,对改善的评价和表扬不仅要针对个人,也要针对部门或班组;第五,对工作本身设定标准,才能显现改善的效果;第六,除精神鼓励外,对改善者要提供物质和技术上的支持;第七,要允许失败。
企业的发展本来就是进一步退半步的过程;第八,要建立和完善提案制度及建议评价执行体系,是评价的人积极认真、公平公正地对待建议;第九,改善需要持之以恒。
杜绝一切浪费,降低成本给我们授课的丰田生产方式专家佐佐木元先生说:“我经常到中国,到中国企业看,到处都是钱。
”他的意思是说我们的企业浪费太多。
对此我深有感触。
企业的利润=销售额—总成本。
产品销售不是由企业决定的,而是由市场决定的。
既然我们无法决定售价,要想获得更多的利润,只有降低成本。
生产企业降低成本只有两个途径:科技创新和杜绝浪费。
科技创新要靠持续改进和发明创造形成。
那么如何杜绝浪费呢?要杜绝浪费首先要认识浪费和看到浪费。
白天开灯是浪费,而安全、质量、时间、空间、人力、动作、资金、库存等很多方面都存在着浪费。
例如真正给企业带来价值的时间只是生产线上的加工过程,时间很短暂。
但往往企业用了上百倍甚至上千倍的时间周转,这都是巨大的浪费。
既然认识了浪费,就不应对浪费视而不见,要把浪费做到可视化,让大家对浪费一眼能看见。
丰田在现场走廊上安了看板和写有各工位号的显示灯,显示应该出多少台实际出了多少台。
各工位上方有根绳,如果上道工序或本工序出了问题,一拉绳,整个生产线就会停下来,彩色指示灯就会亮,所有人都会一眼看出问题在哪,是谁造成了浪费。
所以,员工都力争用最快的时间解决问题,把灯熄灭。
为了深入找出浪费,丰田成立了生产调查组,把生产的每个环节、员工的每一个动作(如转身需要用0.5秒)都用秒表算出来。
丰田正是用这种把浪费做到可视化,再通过认真研究持续改进的方法,使一切浪费得以杜绝(例如用两只手4秒钟要组装的两个部件,通过持续改进,变成用一只手在1秒内完成,省出另一只手再干别的工作)。
丰田还认为库存是浪费的根源。
库存掩盖了设备故障、停顿、生产切换花费的时间和生产组织机构不完备等问题。
因此丰田从各种配件到汽车成品都追求零库存。
丰田追求的是稳定生产。
只有生产是稳定的,才能使生产秩序有条理地进行,才能最大限度地杜绝浪费。
事故本身就是巨大的浪费。
丰田强调:同样的事故只能出一次,不管是安全事故、质量事故还是设备事故。
要做到这一点,首先要树立“事故只能出一次”的思想,其次要对每次事故作彻底的分析,找出原因,拿出多种预防和解决方案,并在其中选定最佳方案,出台相应的管理制度并严格执行。
关爱员工,实现人性化管理丰田总部的上班时间从早晨6点到晚上12点,不管几点来,只要做完自己的工作就可以;丰田不赞成惩罚文化,当员工犯错误时,首先被认为是领导的错误;员工的安全是最重要的,因此丰田的安全得到彻底的保障;丰田的食堂和卫生间可够得上五星级卫生标准;现场环境整洁有序,让员工感到轻松愉快;所有笨重的或有危险的工作一律机械化,最大限度的降低劳动强度、解放劳动力、保障劳动安全;数量庞大的劳保用品一定按时发放、但员工在工作时竟然乐意不穿工作服。
任何成功的企业无一例外地体现着对员工的高度关爱。
企业做大了就是社会的、就是大家的。
只有让员工都有家的感觉,企业才有凝聚力,才能得到长足发展。
认真想一想:除了发效益工资以外,我们为员工还做了一些什么呢?工伤频出(有的甚至是同地点、同原因),员工的安全得到彻底的保障了吗?员工厕所与办公楼里的一样干净吗?食堂的卫生行吗?你问过员工对饭菜质量满意吗?员工的住宿条件好吗?对累得要死的工种采取相应措施了吗?员工病了你去问候过了吗?当员工个人或家庭遇到重大困难是我们帮忙了吗?其实这些否是我们应该想到并做到的。
如果我们的每位干部都时刻关爱员工,我们的凝聚力将给企业带来更大的成功。
丰田的TPS管理丰田经过多年的实践与探索,把自己的精益生产总结成一种模式,那就是丰田的TPS管理。
它包括两部分:一是准时化生产,二是自动化。
准时化生产就是以卖出去的速度安排生产节奏,以达到生产的稳定的合理化。
以后工序拉动前工序,由后向前传递看板,避免了推动式生产可能造成的库存浪费,并实现小批量多品种生产。
所谓自动化不只是机械化,而是在机械化的前提下杜绝不良品,当任一工序出现不合格品时,整个生产系统会自动停下来。
友发的生产管理比创业初期有了很大的提高,成本也大幅度降低了。
但随着友发规模的不断扩大,行业第一目标的逐步接近,生产管理也必须跟上来。
如何像麦当劳一样做到标准化管理?如何真正把质量做到万无一失?如何杜绝一切浪费把生产成本继续大幅度降低?现在研究丰田的TPS管理,把它的理论与我们的行业特点相结合,不正是我们提升生产管理的捷径吗?但学习丰田的TPS 管理不是靠我简单的说就学会的。
但只要我们树立学习的目标和决心,我坚信一定会对我们各企业的生产管理有很好的指导意义!6S管理是生产管理的全部一年多以前,我们专门邀请专业的顾问师到友发集团讲授精益生产和5S 管理。
我本人是想把5S管理作为是标准化管理的基础来做,通过在天津友发推行,我们看到了明显的效果,管理层次得到相应提高。
但此次我吃惊的发现丰田竟然把6S管理(5S加“安全”)看成是生产的全部!只要你把6S管理,即整理、整顿、清扫、清洁、素养、安全做好了,你的生产就做好了。
可见,丰田是把6S管理提到了何等重要的位置!5S管理源于日本,在全世界生产企业中都得到了广泛的认同和推行。