常用注塑件之缺陷及识别
注塑常见缺陷和原因分析
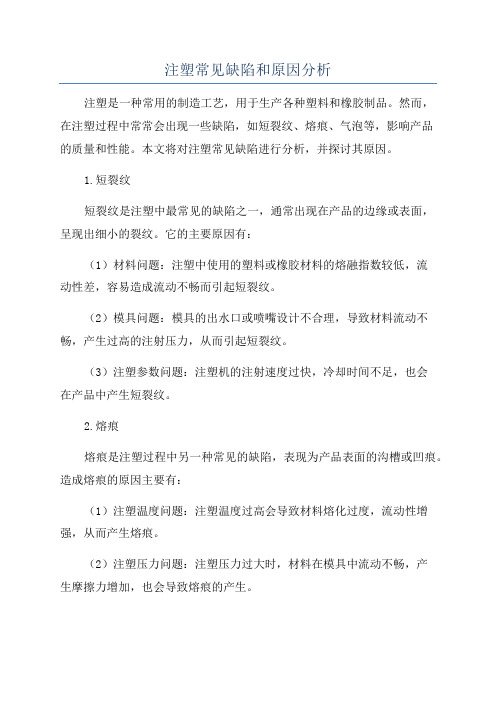
注塑常见缺陷和原因分析注塑是一种常用的制造工艺,用于生产各种塑料和橡胶制品。
然而,在注塑过程中常常会出现一些缺陷,如短裂纹、熔痕、气泡等,影响产品的质量和性能。
本文将对注塑常见缺陷进行分析,并探讨其原因。
1.短裂纹短裂纹是注塑中最常见的缺陷之一,通常出现在产品的边缘或表面,呈现出细小的裂纹。
它的主要原因有:(1)材料问题:注塑中使用的塑料或橡胶材料的熔融指数较低,流动性差,容易造成流动不畅而引起短裂纹。
(2)模具问题:模具的出水口或喷嘴设计不合理,导致材料流动不畅,产生过高的注射压力,从而引起短裂纹。
(3)注塑参数问题:注塑机的注射速度过快,冷却时间不足,也会在产品中产生短裂纹。
2.熔痕熔痕是注塑过程中另一种常见的缺陷,表现为产品表面的沟槽或凹痕。
造成熔痕的原因主要有:(1)注塑温度问题:注塑温度过高会导致材料熔化过度,流动性增强,从而产生熔痕。
(2)注塑压力问题:注塑压力过大时,材料在模具中流动不畅,产生摩擦力增加,也会导致熔痕的产生。
(3)模具设计问题:如果模具中的出水口或喷嘴设计不合理,也会在产品表面形成熔痕。
3.气泡气泡是注塑中常见的缺陷,表现为产品内部或表面的空腔。
气泡的形成原因有:(1)材料问题:注塑材料中含有过多的水分或挥发性物质,注塑过程中被加热蒸发,生成气泡。
(2)注塑温度过高:高温会导致材料熔化过度,容易产生气泡。
(3)注塑压力问题:过高的注塑压力会使材料在注塑过程中产生剧烈的振动,从而引起气泡。
(4)模具问题:模具中存在堵塞或不良的冷却系统,也会导致气泡的产生。
4.缩短问题缩短是指产品在冷却过程中出现尺寸缩小的现象。
产生缩短的主要原因有:(1)注塑温度过低:低温会使注塑材料的熔融程度不足,流动性降低,产生缩短。
(2)冷却时间不足:注塑材料冷却时间不足会导致产品未完全固化,容易产生缩短。
(3)注塑压力问题:过大的注塑压力会使产品产生内部的应力,引起尺寸缩小。
(4)模具问题:模具中存在过多的冷却系统,会导致材料过度冷却而使产品缩短。
注塑件常见缺陷及原因

注塑件常见缺陷及原因注塑件常见缺陷包括飞边、欠注、翘曲、黑点、气泡、起皮、焦痕、龟裂、色差、脆化、喷流纹等。
这些缺陷的形成原因有很多,具体如下:1.飞边:模具分型面或成型区域的设计尺寸不当,注塑压力过高,注射时间过早,注射位置离口模过远,注射位置离型腔面过远或浇口过大。
2.欠注:注塑机压力过低,注射时间过短,模具温度过低,熔体温度过高,模具浇注系统有堵塞现象。
3.翘曲:模具设计不当,冷却时间过短或过长,注塑温度或模具温度过高或过低,塑料材料的收缩率过大。
4.黑点:塑料材料中含有杂质,螺杆转速过高,螺杆温度过高,塑料受热时间过长。
5.气泡:塑料材料中含有水分或挥发物,料温过高或过低,注射压力过小,流道和浇口的尺寸过大。
6.起皮:塑料材料中水分和挥发物含量高,料温过高或过低,注射压力过小,模具温度过高或过低。
7.焦痕:塑料材料中水分和挥发物含量高,料温过高或过低,注射压力过大或过小,模具排气不良。
8.龟裂:塑料材料中水分和挥发物含量高,料温过低,注射压力过小,模具温度过低。
9.色差:塑料材料中水分和挥发物含量高,料温过高或过低,注射压力过小或过大,模具温度过高或过低。
10.脆化:塑料材料中水分和挥发物含量高,料温过高或过低,注射压力过小或过大。
11.喷流纹:塑料材料中水分和挥发物含量高,料温过高或过低,注射压力过小或过大。
此外,注塑件缺陷的形成原因还可能包括设备原因、模具设计问题、原料问题等。
解决注塑件缺陷的方法包括调整操作条件、检查设备及模具设计、更换原料等。
如何避免注塑件常见的缺陷产生,可以从以下几个方面进行改进:材料准备:设定适当的干燥条件,避免过长的干燥时间和过高的干燥温度,以免塑料内挥发物被驱离。
同时,根据产品需求选择适当的塑料材料,如高强度和热稳定性良好的塑料。
模具设计:改善模具排气系统,特别是在流动路径的末端和盲孔位置。
确保排气孔大小合适,结晶性塑料和非结晶性塑料的排气孔大小应有所区别。
注塑件常见缺陷的分析及解决办法

注塑常见缺陷分析及解决办法
C,增加注射压力或保压压力;
D,改善流道和型腔排气;
E,缩短成型周期;
F,制件采用退火方法处理。
B,熔料温度或模温偏低;
C,注塑压力或保压压力不够;
D,气体过多。
A,提高料筒温度特别是喷嘴温度,增加注射压力和速度;B,提高模温,加大流道浇口尺寸,注意抛光喷嘴孔及流道
B,控制料温,提高模温;
C,增加注射压力及熔胶背压。
A,对于投影面积大的扁平制件,要采用多点浇口,或扇形浇口及薄片浇口;
B,模具各部位冷却要均匀;
形(PE,PP,PA,POM等);
B,保压压力太高;
C,模温及冷却不均衡。
D,在允许的情况下,有些易变形胶件脱模后须用夹具定型或进行回火处理。
2尺寸:及相对位置的准确性;
3性能:与用途相关的机械性能,化学性能。
2调机问题:包括注射压力、温度和周期等;
3模具问题:包括模具设计,制造及磨损。
注塑常见外观缺陷及解决方法

注塑常见外观缺陷及解决方法一.注塑常见不良缺陷:缺胶、缩水、熔接线、射胶纹、光泽不一致、黑点、溢边、翘曲变形、料花,银纹、拉模,烧焦、冷料、气泡等以上缺陷成因:模具温度,冲孔刀、流道温度,注射速度、注射压力,保压力、保压时间,转换点,锁模力、冷却时间,炮筒温度、塑化时间、塑化速度,背压等二.解决方法:(一)熔接线(Weld line)熔接痕是由于来自不同方向的熔融树脂前端部分被冷却、在结合处未能完全融合而产生的。
熔合出现在树脂合流之处。
两股树脂流相遇时便会出现熔合。
此时,两者的温度越低,熔合就越明显。
由于熔合处的两股树脂流并不会相互混合(因为在喷流中一边半固化一边前进),因此如果温度偏低,表层就会变厚,纹路很明显,而且强度也会降低。
这是因为两者的粘合力变弱所致。
相反,如果两股树脂流的温度较高,粘合力便会增强,外观也就变得不很明显。
在熔合处,两种熔化了的树脂受到挤压,此处的粘合状况取决于施加在该处的压力。
保压越低,熔合就越明显,强度也就越低。
如果不仅要考虑保压的设定,而且要考虑实际施加在熔合处的压力会降低这一条件,则上述(i)~(iv)都几乎同样适用。
这是因为随着固化的进行,压力传递会变得更加困难。
此外,如果浇口尺寸变小,浇口位置变差的话,则熔合的外观和强度都会恶化。
熔合是树脂的合流点,同时也可能是流动末端。
此时,如果不在该位置很好地设置一个排气口来排出气体,则会使熔合的外观和强度恶化。
一般情况下,主要影响外观,对涂装、电镀产生影响。
严重时,对制品强度产生影响(特别是在纤维增强树脂时,尤为严重)。
可参考以下几项予以改善:l)调整成型条件,提高流动性。
如,提高树脂温度、提高模具温度、提高注射压力及速度等。
2)增设排气槽,在熔接痕的产生处设置推出杆也有利于排气。
3)尽量减少脱模剂的使用。
4)设置工艺溢料并作为熔接痕的产生处,成型后再予以切断去除。
5)若仅影响外观,则可改变烧四位置,以改变熔接痕的位置。
注塑产品常见缺陷

注塑产品常见缺陷注塑产品常见缺陷及其原因分析注塑产品在生产过程中可能会遇到各种缺陷,这些缺陷可能源于产品设计、模具制造、材料选择、注塑工艺等多个因素。
以下是一些常见的注塑产品缺陷及可能的原因分析:1.填充不足(缺料)这可能是由于注塑压力不足、注射时间过短、模具排气不良、浇口设计不合理等原因造成的。
解决这个问题的方法包括增加注塑压力、延长注射时间、优化模具排气设计、改进浇口位置等。
2.溢料(毛边)溢料通常是由于注射压力过高、浇口设计不当、模具磨损等原因造成的。
解决溢料问题的方法包括降低注塑压力、优化浇口设计、修复模具磨损等。
3.气泡(气孔)气泡可能是由于塑料在模具中未完全填满、气体未完全排出、注射速度过快等原因造成的。
解决气泡问题的方法包括降低注射速度、增加冷却时间、优化模具设计等。
4.变形变形可能是由于产品结构不合理、冷却不均匀、模具温度波动等原因造成的。
解决变形问题的方法包括优化产品结构设计、改善冷却条件、稳定模具温度等。
5.银纹(流纹)银纹可能是由于塑料流动不均匀、模具温度过低、注射速度过快等原因造成的。
解决银纹问题的方法包括优化注射条件、提高模具温度、降低注射速度等。
6.裂纹(龟裂)裂纹可能是由于产品结构设计不合理、材料韧性不足、注射压力过高等原因造成的。
解决裂纹问题的方法包括优化产品结构设计、更换韧性更好的材料、降低注射压力等。
7.翘曲(扭曲)翘曲可能是由于产品结构设计不合理、模具温度不均匀、注射压力过低等原因造成的。
解决翘曲问题的方法包括优化产品结构设计、改善冷却条件、提高注射压力等。
8.冷块(冷凝物)冷块可能是由于塑料在冷却过程中速度过快、模具温度过低等原因造成的。
解决冷块问题的方法包括降低冷却速度、提高模具温度等。
9.喷射痕迹(蛇形纹)喷射痕迹可能是由于注射速度过快、浇口设计不当等原因造成的。
解决喷射痕迹问题的方法包括降低注射速度、优化浇口设计等。
10.颜色分布不均(色差)颜色分布不均可能是由于材料混合不均匀、注塑条件不稳定等原因造成的。
7种常见的注塑产品缺陷及解决方法

7种常见的注塑产品缺陷及解决方法填充不满1.注塑件缺陷的特征注塑过程不完全,因为模腔没有填满塑料或注塑过程缺少某些细节。
2.可能出现问题的原因(1).注塑速度不足。
(2).塑料短缺。
(3).螺杆在行程结束处没留下螺杆垫料。
(4).运行时间变化。
(5).射料缸温度太低。
(6).注塑压力不足。
(7).射嘴部分被封。
(8).射嘴或射料缸外的加热器不能运作。
(9).注塑时间太短。
(10).塑料贴在料斗喉壁上。
(11).注塑机容量太小(即注射重量或塑化能力)。
(12).模温太低。
(13).没有清理干净模具的防锈油。
(14).止退环损坏,熔料有倒流现象。
3.补救方法(1).增加注塑速度。
(2).检查料斗内的塑料量。
(3).检查是否正确设定了注射行程,需要的话进行更改。
(4).检查止逆阀是否磨损或出现裂缝。
(5).检查运作是否稳定。
(6).增加熔胶温度。
(7).增加背压。
(8).增加注塑速度。
(9).检查射嘴孔有没有异物或未塑化塑料。
(10).检查所有的加热器外层用安培表检验能量输出是否正确。
(11).增加螺杆向前时间。
(12).增料斗喉区的冷却量,或降低射料缸后区温度。
(13).用较大的注塑机。
(14).适当升高模温。
(15).清理干净模具内的防锈剂。
(16).检查或更换止退环。
注塑件尺寸差异1.注塑件缺陷的特征注塑过程中重量尺寸的变化超过了模具、注塑机、塑料组合的生产能力。
2.可能出现问题的原因(1).输入射料缸内的塑料不均。
(2).射料缸温度或波动的范围太大。
(3).注塑机容量太小。
(4).注塑压力不稳定。
(5).螺杆复位不稳定。
(6).运作时间的变化、溶液黏度不一致。
(7).注射速度(流量控制)不稳定。
(8).使用了不适合模具的塑料品种。
(9).考虑模温、注射压力、速度、时间和保压等对产品的影响。
3.补救方法(1).检查有无充足的冷却水流经料斗喉以保持正确的温度。
(2).检查是否劣质或松脱的热电偶。
注塑产品常见的13种质量缺陷原因分析及解决办法
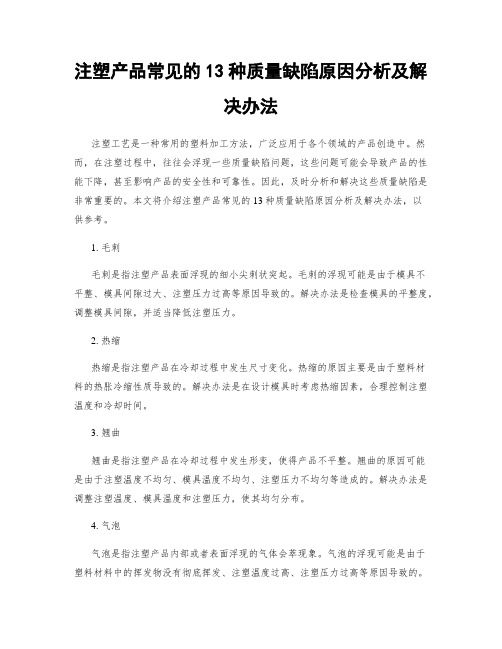
注塑产品常见的13种质量缺陷原因分析及解决办法注塑工艺是一种常用的塑料加工方法,广泛应用于各个领域的产品创造中。
然而,在注塑过程中,往往会浮现一些质量缺陷问题,这些问题可能会导致产品的性能下降,甚至影响产品的安全性和可靠性。
因此,及时分析和解决这些质量缺陷是非常重要的。
本文将介绍注塑产品常见的13种质量缺陷原因分析及解决办法,以供参考。
1. 毛刺毛刺是指注塑产品表面浮现的细小尖刺状突起。
毛刺的浮现可能是由于模具不平整、模具间隙过大、注塑压力过高等原因导致的。
解决办法是检查模具的平整度,调整模具间隙,并适当降低注塑压力。
2. 热缩热缩是指注塑产品在冷却过程中发生尺寸变化。
热缩的原因主要是由于塑料材料的热胀冷缩性质导致的。
解决办法是在设计模具时考虑热缩因素,合理控制注塑温度和冷却时间。
3. 翘曲翘曲是指注塑产品在冷却过程中发生形变,使得产品不平整。
翘曲的原因可能是由于注塑温度不均匀、模具温度不均匀、注塑压力不均匀等造成的。
解决办法是调整注塑温度、模具温度和注塑压力,使其均匀分布。
4. 气泡气泡是指注塑产品内部或者表面浮现的气体会萃现象。
气泡的浮现可能是由于塑料材料中的挥发物没有彻底挥发、注塑温度过高、注塑压力过高等原因导致的。
解决办法是控制注塑温度和压力,选择合适的塑料材料,并进行充分的挤出和干燥处理。
5. 缩孔缩孔是指注塑产品内部浮现的空洞状缺陷。
缩孔的原因可能是由于注塑温度过低、注塑压力不足、模具设计不合理等导致的。
解决办法是提高注塑温度、增加注塑压力,并优化模具设计。
6. 裂纹裂纹是指注塑产品表面或者内部浮现的裂纹状缺陷。
裂纹的浮现可能是由于注塑温度过高、注塑压力过大、冷却时间过短等原因导致的。
解决办法是降低注塑温度、减小注塑压力,并延长冷却时间。
7. 毛边毛边是指注塑产品边缘浮现的不平整现象。
毛边的原因可能是由于模具设计不合理、注塑压力过高、注塑速度过快等导致的。
解决办法是优化模具设计,降低注塑压力,并适当调整注塑速度。
常见注塑件缺陷及解决的方法
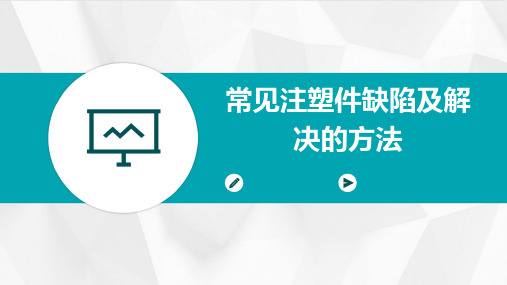
充填不足
01
总结词
充填不足是指注塑件在成型过程中未能完全填满 模具型腔,导致部分区域出现缺料或凹陷。
02
详细描述
充填不足通常是由于注射速度慢、注射压力不足、 模具温度过高或塑料流动性差等原因引起的。
缩痕
总结词
缩痕是指注塑件表面出现凹陷或收缩痕迹,影响 外观和尺寸精度。
详细描述
缩痕通常是由于塑料冷却过程中收缩率不均、模 具温度不均匀或注射压力不足等原因引起的。
常见注塑件缺陷及解 决的方法
目录
• 常见注塑件缺陷 • 注塑件缺陷原因分析 • 解决注塑件缺陷的方法 • 案例分析
01
常见注塑件缺陷
翘曲与扭曲
总结词
翘曲与扭曲是指注塑件形状发生扭曲或弯曲,不符合设 计要求。
详细描述
翘曲与扭曲通常是由于模具设计不合理、塑料收缩率差 异、注射温度和压力不适当等原因引起的。
环境条件的控制Байду номын сангаас
总结词
保持稳定的环境条件对注塑件的质量至关重 要,包括温度、湿度和清洁度等。
详细描述
确保注塑车间温度、湿度稳定,保持环境清 洁、无尘。定期对设备和环境进行清理和消 毒,防止污染和细菌滋生。同时,要关注天 气变化和季节性温差对注塑件质量的影响,
采取相应的措施进行调节。
04
案例分析
案例一:翘曲与扭曲缺陷的解决
材料选择与控制
总结词
选择合适的材料,控制材料质量是解决注塑件缺陷的重要步骤。
详细描述
根据产品使用要求和工艺特性,选择具有良好流动性和成型性的材料。同时, 要确保材料干燥、清洁,无杂质和污染。定期对材料进行质量检查,确保其性 能稳定。
模具优化与维护
常见注塑件缺陷及解决方法

解决方法: 1. 提高保压力,延长保压时间。 2. 加大流道和浇口的尺寸。 3. 提高模具温度,提高树脂温度。 4. 提高注射速度。
常见注塑件缺陷及解决方法
4.熔接线
产生的原因: 由于来自不同方向的熔融树脂前端部分被冷却、
在结合处未能完全融合而产生 的
常见注塑件缺陷及解决方法
2.流纹
产生的原因: 从浇口沿着流动方向,弯曲如蛇行一样的痕迹 它是由于树脂由浇口开始的注射速度过高所导致
解决方法: 1.调低注射速度 2.提高模具温度 ,提高保压力 3.扩大浇口断面尺寸 4. 改变浇口位置(缩短通过浇口后的直进距离) 5.增加排气槽
常见注塑件缺陷及解决方法
4.排气效果不好树脂容量不足。 5.型腔内加压不足。 6.树脂流动性不足。
7.排气效果不好
解决方法: 1.加长注射时间,防止由于成型周期过短,造成浇口 固化前树脂逆流而难于充满型腔。 2.提高注射速度。 3)提高模具温度。 4)提高树脂温度。 5)提高注射压力。 6)扩大浇口尺寸。一般浇口的高度应等于制品壁厚的1/2~l/3。 7)浇口设置在制品壁厚最大处。 8)设置排气槽(平均深度0.03mm、宽度3~smm)或排气杆。对于较小工件更为重要。 9)在螺杆与注射喷嘴之间留有一定的(约smm)缓冲距离。 10)选用低粘度等级的材料。 11)加入润滑剂。
2.模具的原因,主要是因为排气不良所致。这种烧伤一般发生在固 定的地方,容易与第 一种情况区别。这时应注意采取加排气槽反排气杆等措施。
3.在成型条件方面,背压在300MPa以上时,会使料筒部分过热,造 成烧伤。螺杆转速 过高时,也会产生过热,一般在40~90r/min范围内为好。在没设 排气槽或排气槽较小时,注射速度过高会引起过热气体烧伤。
注塑件不良情况图解大全

制件表面产生黑点、黑条或沿
缺陷释义 制件表面呈炭化现象,称为烧
伤
缺陷图片
模具类型
产生原因
1、料筒清洗不洁或有混杂物
2、模具排气不良或锁模力太大
3、熔料中或型腔表面有可燃性挥发物
塑料模
4、塑料受潮、水解变黑 5、染色不均,有深色物或颜料变质
6、塑料成分分解变质
7、熔料温度过高,造成熔料分解、炭化
8、熔料加热时间过长,造成熔料分解、炭化
缺陷图片
模具类型
产生原因
解决方法
1、熔料塑化不均匀
均匀塑化
2、模具温度太低
增加模温
塑料模
3、熔料内混入难熔的杂料 4、热嘴温度太低
使用干净原料 提高热嘴温度
5、无冷料穴或冷料穴尺寸不合理
增加冷料穴/更改冷料穴尺寸
6、注射速度过快或过慢
调整注射速度
缺陷名称 缺陷等级
表面光泽度不良、阴影
产品一级面:A类; 产品二级面:B类; 产品三级面:C类;
A
制件表面沿熔料流动方向产生
缺陷释义 的银白色纹理(针状条纹或片
状云母纹),称为银丝。
缺陷图片
模具类型
产生原因
解决方法
1、原料内含水分或挥发物过多
烘干原料
2、模具型腔内有水
清除模具型腔内水分
塑料模
3、模具型腔内润滑油、脱模剂用量使用过多
合理使用润滑剂及脱模剂
4、制件壁厚不均,融料从薄壁流入厚壁时膨胀、挥
4、注射压力过大
合理控制注射压力
5、浇口位置不当
更改浇口位置
缺陷名称 缺陷等级
熔接线
产品一级面:A类; 产品二级面:B类; 产品三级面:C类;
21种注塑缺陷及解决方法

1,雾气:淡淡的雾状长丝,沿熔体流动方向•雾气产生的原因,由于工模型面上产生有一些不能熔合的物质层分隔在塑件之间(可能是水份,气体),又或者是熔体在进入模腔内时遇到困难,使其不能完全依附在模腔原有型面上•解决方法:(1)塑料:检查塑料的MFI值,检查塑料配方,量度塑料的湿度,增加其干燥度。
(2)模具:冷却管道是否渗漏,模具型腔面抛光不良。
(3)注塑机条件:升高模温,除去过多的脱模剂。
解决方法:(1)塑料:更换较短的玻纤材料,换玻璃珠材料。
(2)模具:更改入闸口尺寸。
(3)注塑工艺:增加注射速度,考虑用多级注射,增加工模温度,增加熔体温度,增加保压时间与压力,检查射嘴温度是否足够,增加螺杆背压,减小螺杆转速,使用较长的料向,以缩短流程。
| 3,困气:大部分在入胶对面或狭窄深肋,呈现发白,发黄,焦黑,未完全填充。
困气产生的原因:模具内存在的空气排放不良,主要可能有A模具的设计不合理,B注塑材料选择不合理,C注塑条件不合理;模具内空气受高压,高温影响,熔体注射速度过快,高温熔体与模腔内空气产生化学作用、焦化。
解决方法:(1)模具:检查排气道是否通常,增加排气道,改变胶口位置。
(2)注塑工艺:减低注塑速度,采用多级注射(快一慢),减低锁模压力,降低注塑温度。
4,银丝纹:与雾气相似,但是更密集,更深刻。
银丝纹产生的原因:由于模具内或者料筒内的热熔体塑料有大量被气化的水份;由添加剂的化学反应导致的气/水份,在注塑过程中被一起注入型腔,并被压至放射形银丝纹形状。
解决方法:(1)塑料:塑料需要妥善存放。
(2)模具:检查冷却管道是否渗漏,避免过于尖角设计,减少雕刻深度。
(3)注塑工艺:增加干燥温度,干燥时间,背压力;减少倒索;减低注射速度,检查射嘴的密封程度(注塑机射嘴与模具射嘴是否配合密切);检查/更换颜料等添加剂。
5,结合线:在入水对面或碰穿位,象刮痕或小槽。
结合线产生的原因:注塑件由于在流入的过程中遇上不良的夹合,汇合流峰时产生仝10 C的温度降•结合线特别明显的情况:型芯大,长流道,浅口间;流体前锋相遇时的角度小•工艺调试不一定能消除结合线,但一定能降低明显程度或将其移到不明显或看不到的位置。
塑件常见缺陷及解决方案

注塑件常见成型缺陷及解决方案在注塑成型加式过程中,可能由于原材料处理不好、塑件或模具设计不合理、操作工没有掌握合适的工艺操作条件,或者因机械方面的原因,常常使塑件产品短射、凹痕、飞边、困气、开裂、翘曲变形等成型缺陷。
塑件在成型过程中出现的各种注塑缺陷,主要有:短射,困气,发脆,烧焦,飞边,分层起皮,喷流痕,流痕,雾斑(浇口晕),银纹(水花纹),凹痕,熔接痕,成型周期过长,翘曲变形,分析了问题产生的可能原因,从原材料、塑件或模具设计、成型工艺等各方面,提出解决方案。
一.短射短射是指模具型腔不能被完全充满的一种现象。
短射形成原因:1、模温、料温或注塑压力和速度过低2、原料塑化不均3、排气不良4、原料流动性不足5、制件太薄或浇口尺寸太小6、聚合物熔体由于结构设计不合理导致过早固化短射解决方案:材料:选用流动性更好的材料模具设计:1、填充薄壁之前先填充厚壁,避免出现滞留现象2、增加浇口数量和流道尺寸,减少流程比及流动阻力3、排气口的位置和尺寸设置适当,避免出现排气不良的现象注塑机:1、检查止逆阀和料筒内壁是否磨损严重2、检查加料口是否有料或是否架桥工艺条件:1、增大注塑压力和注塑速度,增强剪切热2、增大注塑量3、增大料筒温度和模具温度二.困气困气是指空气被困在型腔内而使制件产生气泡。
困气形成原因:它是由于两股熔体前锋交汇时气体无法从分型面、顶杆或排气孔中排出造成的。
困在型腔内气体不能被及时排出,易导致出现表面起泡,制件内部夹气,注塑不满等现象。
困气解决方案:结构设计:减少厚度的不一致,尽量保证壁厚均匀模具设计:1、在最后填充的地方增设排气口2、重新设计浇口和流道系统工艺条件:1、降低最后一级注塑速度.2、增加模温塑件发脆是指制件在某些部位出现容易开裂或折断。
发脆原因:1、干燥条件不适合;使用过多回收料2、注塑温度设置不对3、浇口和流道系统设置不恰当4、熔解痕强度不高发脆解决方案:材料:1、注塑前设置适当的干燥条件2、减少使用回收料,增加原生料的比例.3、选用高强度的塑胶.模具设计:增大主流道、分流道和浇口尺寸注塑机:选择设计良好的螺杆,使塑化时温度分配更加均匀工艺条件:1、降低料筒和喷嘴的温度2、降低背压、螺杆转速和注塑速度3、通过增加料温,加大注塑压力,提高熔解痕强度四.烧焦焦痕是指型腔内气体不能及时排走,导致在流动最末断产生烧黑现象。
注塑件常见品质缺陷分析及解决方法
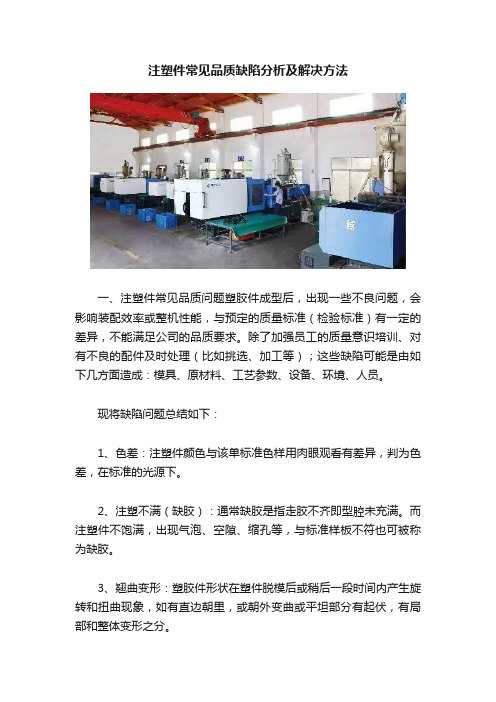
注塑件常见品质缺陷分析及解决方法一、注塑件常见品质问题塑胶件成型后,出现一些不良问题,会影响装配效率或整机性能,与预定的质量标准(检验标准)有一定的差异,不能满足公司的品质要求。
除了加强员工的质量意识培训、对有不良的配件及时处理(比如挑选、加工等);这些缺陷可能是由如下几方面造成:模具、原材料、工艺参数、设备、环境、人员。
现将缺陷问题总结如下:1、色差:注塑件颜色与该单标准色样用肉眼观看有差异,判为色差,在标准的光源下。
2、注塑不满(缺胶):通常缺胶是指走胶不齐即型腔未充满。
而注塑件不饱满,出现气泡、空隙、缩孔等,与标准样板不符也可被称为缺胶。
3、翘曲变形:塑胶件形状在塑件脱模后或稍后一段时间内产生旋转和扭曲现象,如有直边朝里,或朝外变曲或平坦部分有起伏,有局部和整体变形之分。
4、熔接痕(纹):在塑胶件表面的线状痕迹,由塑胶在模具内汇合在一起所形成,而熔体在其交汇处未完全熔合在一起,彼此不能熔为一体即产生熔接纹,多表现为一直线,由深向浅发展,此现象对外观和力学性能有一定影响。
如勾盘底部的熔接痕。
5、波纹:注塑件表面有螺旋状或云雾状的波形凹凸不平的表征现象,或透明产品的里面有波状纹,称为波纹。
6、溢边(飞边、披锋):在注塑件四周沿分型线的地方或模具密封面出现薄薄的(飞边)胶料,称为溢边。
7、银丝纹:注塑件表面的很长的、针状银白色如霜一般的细纹,开口方向沿着料流方向,在塑件未完全充满的地方,流体前端较粗糙,称为银丝纹(银纹)。
8、色泽不均(混色):注塑件表面的色泽不是均一的,有深浅和不同色相,称为混色。
9、光泽不良(暗色):注塑件表面为灰暗无光或光泽不均匀称为暗色或光泽不良。
10、脱模不良(脱模变形):与翘曲变形相似,注塑件成型后不能顺利的从模具中脱出,有变形、顶白、拉裂、拉伤等、称为脱模不良。
11、裂纹及破裂:塑胶件表面出现空隙的裂纹和由此形成的破损现象。
12、糊斑(烧焦):在塑件的表面或内部出现许多暗黑色的条纹或黑点,称为糊斑或烧焦。
常见注塑件缺陷

常见注塑件缺陷1.塑件不足:主要由于供料不足、融料填充流动不良,充气过多及排气不良等原因导致填充型腔不满,塑料外形残缺不完整或多型腔时个别型腔填充不满。
2、尺寸不稳定:主要由于模具强度不良,精度不良、注射机工作不稳定及形成条件不稳定等原因,使塑件尺寸变化不稳定。
3、气泡:由于融料内充气过多或排气不良而导致塑件内残留气体,并呈体积较小或成串的空穴(注意应与真空泡区别)。
4.塌坑(凹痕)或真空泡:由于保压补缩不良,塑件冷却不匀,壁厚不匀及塑料收缩率大。
5.飞边过大:由于合模不良,间隙过大,塑料流动性太好,加料过多使塑件沿边缘出现多余薄翅。
6.熔接不良:由于融料分流汇合时料温下降,树脂与附合物不相溶等原因,使融料分流汇合时,熔接不良,沿塑件表面或内部产生明显的细接缝线。
7.表面波纹:由于融料沿模具表面不是平滑流动填充型腔,而是成半固化波动状态沿型腔表面流动或融料有滞流现象。
8.银丝斑纹:由于料内水分或充气,及挥发物过多,融料受剪切作用过大,融料与模具表面密合不良,或急速冷却或混入异料或分解变质,而使塑件表面沿料流方向出现银白色光泽的针状条纹或云母片状斑纹(水迹痕)。
9.翘曲,变形:由于成形时残余应力、剪切应力、冷却应力及收缩不均等造成的内应力。
脱模不良,冷却不足,塑件强度不足、模具变形等原因,使塑件发生形状畸变,翘曲不平自型孔偏,壁厚不匀等现象。
10.裂纹:由于塑件内应力过大、脱模不良、冷却不匀,塑件性能不良或塑件设计不良及其他弊病(如变形)等原因,使塑件表面及进料口附加产生细裂纹,或开裂或在负荷和溶剂作用下发生开裂等现象。
11.黑点、黑条:由于塑件分解或料中可燃性挥发物,空气等在高温高压下分解燃烧,燃烧物随融料注入型腔,在塑件表面呈现黑点、黑条纹,或沿塑件表面呈炭状烧伤现象。
12.色泽不匀或变色:由于颜料或填料分布不良,塑料或颜料变色在塑件表面的色泽不匀。
色泽不匀随呈现的现象不同其原因也不同。
进料口附近主要是颜料分布不匀,如整个塑件色泽不匀时则为塑料热稳定不良所致,熔接部位色泽不匀时则与颜料性质有关。
注塑件常见缺陷及不良分析

不 光 泽
1、料筒内不干净 2、背压力不够
脱 模 困 难
2、光洁度不够 3、顶出方式不当 4、配合精度不够 5、进、排气不良 6、模板变形
1、顶出力不够 2、顶程不够
1、注射压力太高 2、保压时间太长 3、注射量太多 4、模具温度太高
缩 坑
1、流道太细小 2、浇口太小 3、排气不良
1、注射压力不够 2、喷孔堵有异物
厚薄不一致
熔 接 痕
1、浇口太小 2、排气不良 3、冷料穴太小 4、浇口位置不对 5、浇口数目不够 1、模芯无脱模斜 度或过小 2、模温太低 3、顶杆分布不均 或数量过少 4、表面光洁度差 1、浇口太小 2、多浇口时分布 不合理 1、流道口太小 2、浇口太小 3、排气不良 4、型腔面不光
注塑制品的缺陷及原因分析
原因 现象
模具方面 1、流道太小 2、浇口太小 3、浇口位置不合 理 4、排气不佳 5、冷料穴太小 6、型腔内有杂物 1、模板变形 2、型芯与型腔配 合有误差 3、模板组合不平 行 4、排气槽过 深
设备方面
工艺条件
原材料
制品设计
注 塑 不 满
1、注射压力太低 2、加料量不足 3、注塑量不够 4、喷嘴中有异物
注射压力过小
1、料温过低 2、模温过低 3、注射速度太慢 4、脱模剂过多
1、原料未预 干燥 2、原料流动 性差
壁厚过小
龟 裂
1、料温过低 2、料温太高或停 留时间太长 3、保压时间太长 4、脱模剂过多
1、牌号品级 不适用 2、后处理不 当
形状结构不够 合理,导致局 部应力集中
分 层
背压力不够
1、料温过低 1、不同料混 2、注射速度过快 入 2、混入 3、模具温度低 油污或异物 4、长 4、模具温度低 1、水分含量 高 2、助剂不 对 3、脱模 剂太多
注塑件内部缺陷判定标准

注塑件内部缺陷判定标准一、缺料/走料不齐定义:缺料是指注塑件内部出现不完整的塑料材料,导致外观和性能受到影响;走料不齐则指塑料材料在流动过程中出现不均匀的现象,使得部分区域注胶不足。
判别标准:外观检查:通过观察注塑件外观是否完整,是否存在塑料材料缺失或不均现象,手动触摸感知是否存在凹痕或阶梯状痕迹,以判定是否存在缺料或走料不齐现象。
尺寸测量:对于有明显缺料或走料不齐的注塑件,可采用测量工具进行尺寸测量,看是否存在明显的尺寸偏差,如局部区域胶位薄、厚度不均等。
二、缩水定义:缩水是指注塑件内部局部或整体收缩,导致尺寸和性能下降。
判别标准:外观观察:观察注塑件表面是否平整,有无局部凹陷、收缩现象,以及边缘部分是否有波浪形、碟形等不规则变化。
测量工具:使用测量工具对注塑件进行测量,看是否存在尺寸偏差,如局部缩小、整体短小等现象。
同时,可以采用卡尺、千分尺等工具进行精确测量。
手摸感觉:通过手摸来感知注塑件表面是否光滑,边缘部分是否存在毛刺等情况,以判定是否存在缩水现象。
三、披锋定义:披锋是指注塑件上出现不规则的凸起或凹痕,导致外观和性能受到影响。
判别标准:外观检查:观察注塑件外观是否平整,边缘部分是否存在多余的凸起或凹痕,以及表面是否光滑。
手动触摸注塑件表面,感知是否存在阶梯状痕迹、毛刺等情况。
位置判断:注意观察注塑件上披锋的位置和走向,看是否会影响到注塑件的性能和使用。
如果披锋出现在关键部位,如配合面、滑动面等,则可能会影响到注塑件的稳定性和可靠性。
成因分析:结合注塑件的生产过程和模具结构进行分析,了解披锋产生的原因。
通常,披锋可能是由于模具结构不合理、注胶速度过快、材料温度过高等因素所导致。
常用注塑件之缺陷及识别

常用注塑件之缺陷及识别常用注塑件之缺陷及识别1. 走料不齐:又名缺料,注塑件边缘光滑,形状不规则,有不整齐之感。
常发生在①离水口最边的地方;②又细又长的骨位。
2. 缩水:因部品收缩导致啤件表面有凹痕,不平整,对光看显示波浪状,常发生在①胶件厚度不均的地方;②胶厚部位;③柱位,骨位。
3. 披锋:注塑件边缘多出一块很薄的皮,常发生在①分模面;②模具活动芯位;③顶针位,柱位,孔位,扣位。
4. 气泡:注塑件表面有一与周围颜色不同的泡泡,一般分为①由未及时排出之气体、空气、水气形成的气泡;②热冷缩引起的真空泡。
透明部品要特别注意。
5. 夹纹:两股以上的料流融合时在注塑件表面形成一条很深之熔结痕。
一般发生在多股料汇合处。
6. 射纹:从入水口处开始有多条纹痕向外射,尤以透明件为明显。
7. 烧胶:表面不平,有深色或黑色焦痕,一般发生在难走胶、易困气的部位。
8. 黑点:有黑色之点状杂质在注塑件表面,一般由材料里混有杂料异引起的。
9. 哑色:注塑件表面不反光,不亮,朦胧,尤以透明件易发生。
10. 变色:与签办颜色不对。
透明件易变色,一般由色粉材料或调试比例不对,或模温不对引起。
11. 皱纹:注塑件表面有波浪纹,由于树脂向一边流动一边变更引起的。
12. 变形:注塑件扭曲,不平,不直,一股发生在柱位,骨位,细长胶件,盒状胶件。
PP料尤为常见。
13. 用错料:与规定用料不同,可以通过查包装标签,注塑件密度(放水中)及燃烧持续性,火焰和烟颜色进行识别。
14. 粘模:注塑件的局部残留模腔,致使注塑件注塑出后结构不完整(但不同于缺胶)或因设计模具顶出装置系统欠缺,致使注塑件难以从模腔中顶出,一般发生在薄壁,胶骨位,扣位,胶柱位上。
15. 拖伤:胶件在出模过程中与模腔表面磨擦使胶件表面出现擦花痕迹。
一般发生在多胶、柱高、柱底。
16. 多料:因模腔损伤致使胶件表面多出,一般发生在活动科、柱位,顶针位,分模面。
17. 混色:因料不干净或温度过高使胶件表面或内部形成与胶件不同的颜色点(混料不均匀以引起)。
注塑常见缺陷的分析与解决

15
解决方法
1.减小射胶压力、射胶时间,加快射胶速度,以降低制品内应力 2. 模具设计时要合理设计运水系统,确保模具型腔各部位模温 均匀。 3.加长冷却时间。 4.确认产品是否在台面堆积过多,或包装方法不当引起挤压变形 5.设计适当的夹具定型,使产品达到要求 6.在产品上增加加强筋
12.注射速度慢。
13.塑料流动性差。
14.模具温度未达到要求
9
3、色差 现象:在标准的光源下,注塑件颜色与标准色样
用肉眼观看有差异,判为色差。
10
产生的原因:
1)原材料方面因素:包括色粉更换、塑胶材料牌号 更改,定型剂更换等因数,造成产品色差。
2)原材料品种不同:如PP料与ABS料或PC料要求同 一种色,但因材料品种不同而有轻微色差,但允 许有一限度范围。
14
原因:
1)模具方面:主要是针对模具设计方面不合理原因造成。 2)成型操作方面:
A、注射压力过高,流体方向和垂直流向方向分子取向相差较大, 塑胶力图恢复原有的卷曲状态,所以流体流动方向上的收缩大于 垂直流动方向上的收缩; B、熔体温度过高; C、保压压力过高:保压压力高时,塑料中的内压力过高,在脱模 后内应力的释放使塑胶件产生翘曲变形; D、熔体流速太慢; E、回火温度过高或时间太长。
2) 原料方面: A、脱模剂用量太多,或使用不符合的脱模剂; B、熔体的流动性差,在成型时易产生熔接痕; C、原料中含水份较多或挥发物含量过高。
3) 成型操作方面: A、熔体温度过低,低温熔体的分流汇合性能较差,容易形成熔接纹; B、熔体注射压力过低,使得注射速度过慢,熔体在型腔中的温度不
相同,这时熔体在分流汇合时就易产生熔接纹。
- 1、下载文档前请自行甄别文档内容的完整性,平台不提供额外的编辑、内容补充、找答案等附加服务。
- 2、"仅部分预览"的文档,不可在线预览部分如存在完整性等问题,可反馈申请退款(可完整预览的文档不适用该条件!)。
- 3、如文档侵犯您的权益,请联系客服反馈,我们会尽快为您处理(人工客服工作时间:9:00-18:30)。
常用注塑件之缺陷及识别
1. 走料不齐:又名缺料,注塑件边缘光滑,形状不规则,有不整齐之感。
常发生在①离水口最边
的地方;②又细又长的骨位。
2. 缩水:因部品收缩导致啤件表面有凹痕,不平整,对光看显示波浪状,常发生在①胶件厚度不
均的地方;②胶厚部位;③柱位,骨位。
3. 披锋:注塑件边缘多出一块很薄的皮,常发生在①分模面;②模具活动芯位;③顶针位,柱位,
孔位,扣位。
4. 气泡:注塑件表面有一与周围颜色不同的泡泡,一般分为①由未及时排出之气体、空气、水气
形成的气泡;②热冷缩引起的真空泡。
透明部品要特别注意。
5. 夹纹:两股以上的料流融合时在注塑件表面形成一条很深之熔结痕。
一般发生在多股料汇合处。
6. 射纹:从入水口处开始有多条纹痕向外射,尤以透明件为明显。
7. 烧胶:表面不平,有深色或黑色焦痕,一般发生在难走胶、易困气的部位。
8. 黑点:有黑色之点状杂质在注塑件表面,一般由材料里混有杂料异引起的。
9. 哑色:注塑件表面不反光,不亮,朦胧,尤以透明件易发生。
10. 变色:与签办颜色不对。
透明件易变色,一般由色粉材料或调试比例不对,或模温不对引起。
11. 皱纹:注塑件表面有波浪纹,由于树脂向一边流动一边变更引起的。
12. 变形:注塑件扭曲,不平,不直,一股发生在柱位,骨位,细长胶件,盒状胶件。
PP料
尤为常见。
13. 用错料:与规定用料不同,可以通过查包装标签,注塑件密度(放水中)及燃烧持续性,火焰
和烟颜色进行识别。
14. 粘模:注塑件的局部残留模腔,致使注塑件注塑出后结构不完整(但不同于缺胶)或因设计模
具顶出装置系统欠缺,致使注塑件难以从模腔中顶出,一般发生在薄壁,胶骨位,扣位,胶柱位上。
15. 拖伤:胶件在出模过程中与模腔表面磨擦使胶件表面出现擦花痕迹。
一般发生在多胶、柱高、
柱底。
16. 多料:因模腔损伤致使胶件表面多出,一般发生在活动科、柱位,顶针位,分模面。
17. 混色:因料不干净或温度过高使胶件表面或内部形成与胶件不同的颜色点(混料不均匀以引
起)。
18. 混点:成型胶件表面所出现的杂点(如黑点)、焦点。
19. 顶白:顶针位因顶出速度太快的原因使胶件发白(白点)。
20. 爆裂:成型件出现破碎裂缝现象(如顶出速度或模温度低都可引起)。
21. 尺寸偏差:因模具金型不良或成型条件变化使部品尺寸在公差范围外。
22. 发白:因注塑件难出模而使胶件出现拉白(表面转角位出现白痕),一般发生在顶针位,骨位。
23. 顶裂:因顶出系统速度太快,以及注塑件不易出模或模温不够,使胶件顶出装置中冲击出裂痕。
24. 闭孔:因模具顶针、镶针,损坏、断,而导致胶件孔塞。
25. 模印:因模具型腔表面本身缺陷而形成模腔相对应的状况(如纹状、印痕、多胶等)。
26. 油污:成型件因模腔油污未清除干净或打油性脱模剥而使胶件表面出油性污染。
27. 料脆:因注塑参数不合要求而使胶件易断,抗冲击,拉伸强度减弱,一般发生在用错胶料、材
料配方错误、料温过高物料分解等。
28. 料花:因胶料未烘干或背压太小,而使胶件表面出现白色水纹状。
29. 困气:因模具设计缺陷或射胶速度太快,使模腔空气不易排而使胶
件内部出现空心或局部出现烧痕。