成品出货检查记录表
OQC出货检验程序(含表格)

OQC出货检验程序(含表格)OQC出货检验程序(ISO9001-2015)1.0⽬的:为确保⽣产线所⽣产的成品品质符合客户品质要求,对整个出货检验过程进⾏有效的管理,特制定本程序.2.0范围:适⽤于汕头市万晖实业有限公司所有产品出货品质检验作业.3.0职责:3.1OQC:出货品质检验、品质判定、状态标识、异常反馈与跟踪、检验结果记录。
3.2QE:制定或修订出货品质检验标准、异常原因分析、异常跟踪及作业指导。
3.3⽣产部:出货待检通知、不合格批的重⼯作业、不合格品处理.3.4仓库:成品⼊库管理、库存超保质期成品再检通知。
3.5业务部:成品特采申请、重⼯作业安排.4.0定义⽆5.0作业内容5.1⼊库成品待检通知⽣产部⼊库待检的成品必须是经FQC全检并判定合格(需贴合格标识)的产品,⼊库前需核对⼊库数量与检验数量是否相符,最后将待检之成品移⼊成品仓库指定的出货待检区域。
然后开⽴《出货待检通知单》通知OQC进⾏出货检验。
5.3出货品质检验作业5.3.1检验依据OQC检验时依据《成品检验规范》、《产品检验标准书》、⼯程样办等对产品进⾏品质检验和判定,抽样作业时按照MIL-STD-105E普通Ⅱ级抽样,合格质量允收⽔准(AQL):致命缺陷(CRI):0、主要缺陷(MAJ):0.65、次要缺陷(MIN):1.5,若客户有特别要求按照客户要求的允收⽔准进⾏抽样作业,具体参照《抽样检验计划》执⾏.5.3.2检验项⽬检验项⽬包括:外观/尺⼨/结构/特性/包装/标识等项⽬,具体检验项⽬参照《成品检验规范》中规定检验项⽬进⾏检验.5.3.3OQC出货检验作业时应按照抽样计划规定的抽检数量从待检批中的不同部位、不同箱号的箱⼦中抽取指定数量进⾏检验,尽量减少不量流⼊客户端.检验完成后需在《出货待检通知单》上进⾏品质判定,然后将《出货待检通知单》归还⽣产部.5.3.4正常情况出货检验需在6个⼯作⼩时内完成,急出货情形需在2个⼯作⼩时内完成检验.检验结果是否合格都需真实且详细的记录于《OQC成品检查报告》上,以便追溯和统计分析.5.3.5经OQC检验合格批次,由⽣产部门填写《成品⼊仓单》办理⼊库.5.4检验状态标识检验合格在标签上盖PASS印章,不合格贴红⾊REJECT标签,特采使⽤贴黄⾊特采使⽤标签.挑选或加⼯使⽤则贴挑选/加⼯使⽤标签.具体参考《产品标识与追溯性控制程序》.5.5品质异常反馈及处理经抽检判不合格批次,需在产品外箱上贴上红⾊的不合格(REJECT)标签,并将判定结果记录于《成品待检通知单》上并归还仓库,同时OQC开⽴《出货检验异常报告》给OQC组长确认/主管审核/经理核准,然后由业务/PMC/⽣产/品质/⼯程等相关单位会签评审.最终由(副)总经理批准,不合格批的处理⽅式按(副)总经理批准意见执⾏,会签完后将此单给责任单位进⾏原因分析和制定改善对策,⾄于检验发现之不合格品的处理⽅式参照《不合格品的控制程序》执⾏.5.6特采放⾏作业5.6.1经OQC检验不合格批产品,经公司(副)总经理批准决定特采使⽤的,由业务开⽴《特采申请单》并附上《出货检验异常报告》给品质部/⼯程部/⽣产部/PMC等相关单位会签评审,由公司(副)总经理批准执⾏,最后由OQC将不合格标签撕下,在标签上盖PASS印章,若是经客户同意特采使⽤需在外箱贴特采使⽤标识.5.7不合格批重⼯再检判重⼯的不合格批,OQC需对重⼯过程进⾏跟踪(包括重⼯项⽬是否与反馈之项⽬相符,重⼯之数量是否与判退的数量相符等内容),重⼯后⽣产部必须重新报验此批,并在《出货待检通知单》上注明”已重⼯”字样.重⼯再检OQC必须再次填写《OQC成品检查报告》,报告上需详细注明为”重⼯再检”字样,并详细记录《出货检验异常报告》编号和其他相关信息,以便于追溯.5.8库存成品再检所有库存成品超过保存期限,仓库必须重新提报给OQC重检和判定.重检后原标识需更换,若重检判不合格,需开⽴《出货检验异常报告》给相关单位会签评审,不合格批的处理参照5.5/5.6/5.7执⾏,不合格品参照《不合格品控制程序》执⾏.5.9控制计划的传递和执⾏5.9.1在新产品投产之前,由品质经理针对此项产品的特殊特性内容,对检查员进⾏培训,要求品管员严格按特殊特性的内容执⾏检查。
供应商审核各过程检查表

5,
6
检验员是否按工程图和检验规范执行,并实际记录检验结
果?
5,
7
进料检验状态及检验结果是否有清晰的标识,不合格品
有否被隔离?
5,
8
进料检验不合格时是否发出CAR书面通知供应商进行
对策回复及时效?
5,
9
是否制定进料检验品质目标?如何执行、统计分析?
5,
10
针对未达品质目标时如何处理?是否成立CIP专案小组
5,
6
危险品是否建立独立的仓库,并有文件支持?
5,
总分Total score
30'
签名:
8.环境系统(采购负责)
序号
内容
满分
供应
商
备注
1
供应商是否已经通过ISO14001的认证?最近的稽核
日期是哪一天由哪一家认证机构来稽核?
5,
2
近3年内企业是否发生过严重的环境事故、投诉或环保
部门的处罚?
5,
3
工业废水/废气/废物/噪声等排放是否取得环保部门的
130'
签名:
2.检验与测试仪器管理(SQE负责)
序号
内容
供应
商
备 注
1
是否有适当的程序支持仪校室管理?
5,
2
是否建立仪校室仪器清单,对使用仪器加以管制?(如购
进时间、保存地点、保管人员、校正周期等)
5,
3
是否制定实验仪器校正周期和保养计划?
5,
4
仪校室是否进行温湿度管制并做记录?
5,
5
是否建立仪校室紧急应变措施程序?
45,
签名:
出货检验控制程序(含表格)

出货检验控制程序(ISO9001-2015)1.0目的:确保交付给客户的产品符合客户品质要求。
2.0范围:凡本公司所销售之产品均属之。
3.0定义:无。
4.0权责:4.1品保部:产品出货前的检验工作。
4.2制造/仓储:出货产品的包装和搬运,交货工作。
4.3生管:制订出货计划和出货交付运输安排。
5.0作业内容:5.1生管课依据客户订单交期或排程做出生产出货计划表以E-MAIL或PAPER 档的形式通知到品保、仓储、制造等各相关单位。
5.2制程产品在入库前需经过OQC检验,仓储根据出货需求,把待出货之产品移置到“OQC待检区”。
5.3OQC依据《SIP》、承认样本及限度样品的要求对出货前的产品进行抽样检验,并把检验结果记录在《制程巡检/抽检品质记录表》及《出货检验报告单》中。
5.4抽检时OQC按每个栈板为一个批次或小件以不超过1000PCS为一个批次,按照《ISO2859抽样计划》正常单次抽样,AQL:MA为0.4,Mi为0.65。
出现客诉问题需重点检查,无客诉问题产品则以出货前的查核为主。
如有客户要求,则按客户要求标准进行。
5.5OQC检验判定合格:5.5.1OQC依据《检试验管理程序》的要求在《产品标识单》上盖“OQCPASS”章。
5.5.2制造依据《产品标示单》OQC的标识进行入库。
5.6OQC检验判定不合格:5.6.1OQC把不合格现象或不合格样品呈报上级主管后,确认为异常,则发出《品质异常联络单》给相关责任单位处理与改善,并要求相关责任单位在《品质异常联络单》背面会签。
具体依照《品质异常处理流程》执行。
不合格批,每一栈板朝外的最上层的左上角贴《不良品标示单》,注明相关不良现象等内容。
具体依照《检试验管理程序》执行。
5.6.2经OQC判定的不合格品依据《不合格管理程序》进行处理;相关单位评审是否采取纠正措施或预防措施,如需采取纠正措施或预防措施则依据《纠正与预防措施管理程序》执行。
如果不采取纠正措施,因出货紧急,在不影响功能的情况下,由生管或业务提出特采申请,具体依照《特采作业流程》执行。
出货检验SOP

编制审核批准
文件编号项目名称产品名称制定日期文件版本
工序名称
前工序
后工序
出货
设备/工具
型号数量/用量
卡尺
/1版本内容理由
更改人
针规
/
1
A00
检验作业
初版
表单编号:
SCS-EDS-07 V01
HSF要求:所有物料符合HSF要求生产
深圳市联华懿盛实业有限公司
出货检验作业指导书
1、室内温度:20-28摄氏度
2、亮度:800-1200LUX
对OQC检验人员的检验作业水平及流程进行归规范,提高OQC检验作业水平,控制出货不良不流到客户端,提高品质。
1、半成品检验
2、成品检验
1、出货检验对产品的包装外观、产品数量进行确认,确认无误后进行内部检查;
2、检验按批次检验,每批次检验如果是多套,产品至少要检验一整套/一整模;
3 、当产品有尺寸有 尺寸要求时按照SIP检验要求检验一整套。
日期
作业手法及步骤
检验范围
出货检验
使用设备/工具
作业环境
工程变更记录
SCS-EDS-07 V01
出货检验/目的要求
A00
检验
生产
生产
物料收料
品质检验
OK
出货
NG
品质工程复
判
OK
出货
NG
开据异常报告
生产部退货
特采
MRB 评
出货。
成品出货检验标准
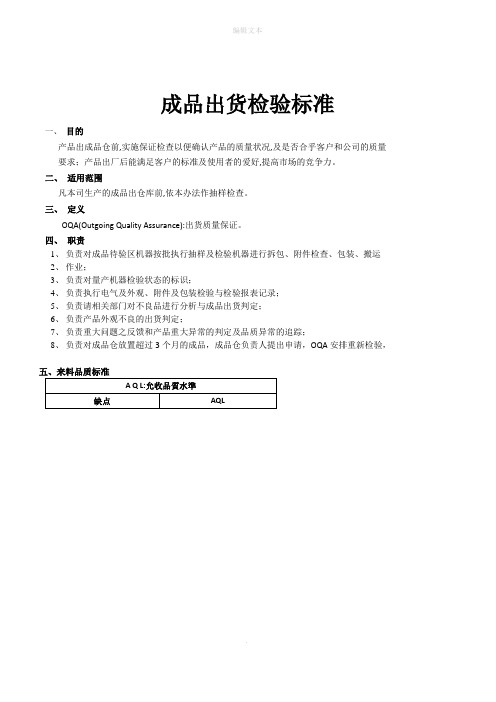
成品出货检验标准一、目的产品出成品仓前,实施保证检查以便确认产品的质量状况,及是否合乎客户和公司的质量要求;产品出厂后能满足客户的标准及使用者的爱好,提高市场的竞争力。
二、适用范围凡本司生产的成品出仓库前,依本办法作抽样检查。
三、定义OQA(Outgoing Quality Assurance):出货质量保证。
四、职责1、负责对成品待验区机器按批执行抽样及检验机器进行拆包、附件检查、包装、搬运2、作业;3、负责对量产机器检验状态的标识;4、负责执行电气及外观、附件及包装检验与检验报表记录;5、负责请相关部门对不良品进行分析与成品出货判定;6、负责产品外观不良的出货判定;7、负责重大问题之反馈和产品重大异常的判定及品质异常的追踪;8、负责对成品仓放置超过3个月的成品,成品仓负责人提出申请,OQA安排重新检验,(CRI)0(MAJ)0.4(MIN) 1.0六、缺点定义缺点(CRI):产品本身具备的功能失效及影响人身安全。
主要缺点(MAJ):外观结构或尺寸结构,部分功能失效或者附属功能失效。
品质不符合规格。
次要缺点(MIN):凡是没有安全上隐患,亦非尺寸不良,不影响产品功能。
外观面为次要不良,品质特性不符合规格及标准。
七、检验环境:在下列范围内的湿度、温度和气压的任意组合条件下进行测量。
环境温度:15℃~35℃;相对湿度:45%~75%;大气压力:86KPa~106Kpa;在上述测试条件下,被测设备应满足其性能规范,但在比上述测试条件更宽的范围内,设备仍能工作,但可不满足其所有的性能规范,并允许被测设备在更为极端的条件下储存。
12、检验要求和内容外观、结构质量检验图象、伴音质量检验功能质量检验安全、电磁兼容质量检验包装质量检验6.外观、结构质量检验要求6.1 检验内容与要求;Ⅰ产品外观必须具有如下标志,且标志正确、清晰可辨产品机壳或后盖贴纸上必须有产品商标、型号、名称、生产企业名称;产品后盖上应有电源性质、额定电压、最大电流、电源频率、功耗等;产品后盖必须具有警告用产品后盖上必须加贴产品序号条码,且与纸箱、保修卡号码一致;产品面壳上必须有正确的指示灯标志;Ⅱ产品外观、结构质量检验要求产品外观应整洁光滑,表面不应有凹凸变形、粗糙不平、划伤、脱漆、缩水、间隙、裂纹、毛刺、边缘棱角突出、霉斑、脏污、色差、金属斑点、黑点、纹理等任何缺陷;外观各类文字、图案及符号丝印应端正、清晰、牢固,标识功能应与实际产品特性相符;产品保护膜应粘贴良好,无破损、脏污等不良;产品铭牌、装饰件、紧固件及其它零部件应无锈蚀、变形、划伤、金属斑点、黑点等任何不良现象,且安装牢固、匹配良好,无缺损、脱落、松动、歪斜、间隙、台阶、螺孔错位等问题指示灯、接收头及其白镜或红镜安装应规范,不应漏装或歪斜;开关、按键、旋钮等应操作灵活可靠,无缺损、变形、划伤、歪斜等问题;各类音视频输入输出接口(含RF 接口、S 端子接口、YUV 接口、VGA 接口等)应安装牢固、端子颜色正确,拔插顺畅;显示屏应安装牢固,无偏斜,与机箱吻合,且无超标划伤、黑点、脏污、油渍等缺陷6.2 外观、结构质量检验方法;外观、结构质量检验方法采取目测和手感检查。
成品出货检验标准
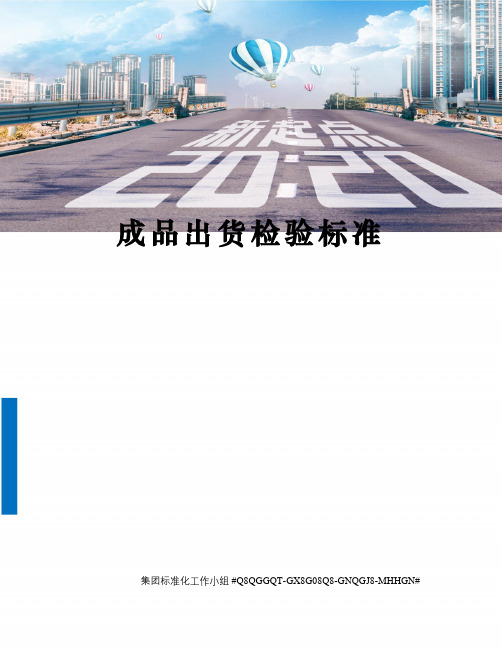
成品出货检验标准集团标准化工作小组 #Q8QGGQT-GX8G08Q8-GNQGJ8-MHHGN#成品出货检验标准一、目的产品出成品仓前,实施保证检查以便确认产品的质量状况,及是否合乎客户和公司的质量要求;产品出厂后能满足客户的标准及使用者的爱好,提高市场的竞争力。
二、适用范围凡本司生产的成品出仓库前,依本办法作抽样检查。
三、定义OQA(Outgoing Quality Assurance):出货质量保证。
四、职责1、负责对成品待验区机器按批执行抽样及检验机器进行拆包、附件检查、包装、搬运2、作业;3、负责对量产机器检验状态的标识;4、负责执行电气及外观、附件及包装检验与检验报表记录;5、负责请相关部门对不良品进行分析与成品出货判定;6、负责产品外观不良的出货判定;7、负责重大问题之反馈和产品重大异常的判定及品质异常的追踪;8、负责对成品仓放置超过3个月的成品,成品仓负责人提出申请,OQA安排重新检验,五、来料品质标准六、缺点定义缺点(CRI):产品本身具备的功能失效及影响人身安全。
主要缺点(MAJ):外观结构或尺寸结构,部分功能失效或者附属功能失效。
品质不符合规格。
次要缺点(MIN):凡是没有安全上隐患,亦非尺寸不良,不影响产品功能。
外观面为次要不良,品质特性不符合规格及标准。
七、检验环境:在下列范围内的湿度、温度和气压的任意组合条件下进行测量。
环境温度:15℃~35℃;相对湿度:45%~75%;大气压力:86KPa~106Kpa;在上述测试条件下,被测设备应满足其性能规范,但在比上述测试条件更宽的范围内,设备仍能工作,但可不满足其所有的性能规范,并允许被测设备在更为极端的条件下储存。
12、检验要求和内容外观、结构质量检验图象、伴音质量检验功能质量检验安全、电磁兼容质量检验包装质量检验6.外观、结构质量检验要求检验内容与要求;Ⅰ产品外观必须具有如下标志,且标志正确、清晰可辨产品机壳或后盖贴纸上必须有产品商标、型号、名称、生产企业名称;产品后盖必须具有警告用户安全使用的“警告标记”;产品后盖上应有电源性质、额定电压、最大电流、电源频率、功耗等;产品后盖上必须加贴产品序号条码,且与纸箱、保修卡号码一致;产品面壳上必须有正确的指示灯标志;Ⅱ产品外观、结构质量检验要求产品外观应整洁光滑,表面不应有凹凸变形、粗糙不平、划伤、脱漆、缩水、间隙、裂纹、毛刺、边缘棱角突出、霉斑、脏污、色差、金属斑点、黑点、纹理等任何缺陷;外观各类文字、图案及符号丝印应端正、清晰、牢固,标识功能应与实际产品特性相符;产品保护膜应粘贴良好,无破损、脏污等不良;产品铭牌、装饰件、紧固件及其它零部件应无锈蚀、变形、划伤、金属斑点、黑点等任何不良现象,且安装牢固、匹配良好,无缺损、脱落、松动、歪斜、间隙、台阶、螺孔错位等问题指示灯、接收头及其白镜或红镜安装应规范,不应漏装或歪斜;开关、按键、旋钮等应操作灵活可靠,无缺损、变形、划伤、歪斜等问题;各类音视频输入输出接口(含 RF 接口、S 端子接口、YUV 接口、VGA 接口等)应安装牢固、端子颜色正确,拔插顺畅;显示屏应安装牢固,无偏斜,与机箱吻合,且无超标划伤、黑点、脏污、油渍等缺陷外观、结构质量检验方法;外观、结构质量检验方法采取目测和手感检查。
成品出货检验工作标准流程
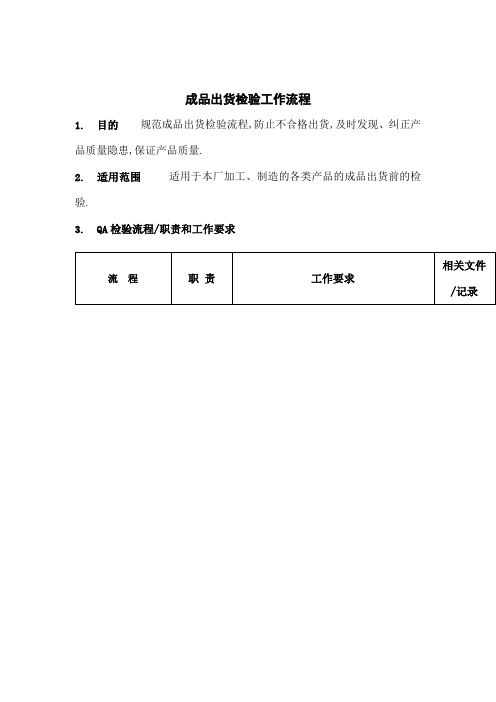
1. 目的规范成品出货检验流程,防止不合格出货,及时发现、纠正产品质量隐患,保证产品质量.
2. 适用范围适用于本厂加工、制造的各类产品的成品出货前的检验.
3.QA检验流程/职责和工作要求
流 程
职 责
工作要求
相关文件
/记录
首件检验
生产
生产
检验员
OQC组长
QE
PIE/OQC组长/PQC组长
OQC
PIE
生产部
OQC组长
检验员
OQC组长/PQC组长/PIE
OQC主管
检验员
PIE
每一订单生产的第一台机送OQC检验
按订单、样机、检验标准或规范、说明书、ECN、料表、设计文件作首件检验
填写首件检查表外观、功能
QE对首件及首件检查表确认,并签署合格与否意见
OQC、PQC和PIE对机确认,
不合格发出OQC检验报告,注明首件检查
客户、QE、PIE对机,
OQC转发客户验货报告
工程发出坏机分析报告和返工报告
计划安排返工,返工后再重新送检
客户验货合格,OQC检验员核对卡板数量在生产部产成品送检单上注明客户检验合格
生产线将合格产品入成品仓
送检单
客户验货报告
坏机分析报告
返工报告
需要更多的流程,请到
作业员
OQC组长/领班
QE/PIE
OQC
PIE
批量抽检合格பைடு நூலகம்组长在OQC检验报告签字确认
合格话机在生产部产成品送检单上盖蓝色QA PASS章,外箱贴绿色QA合格证贴纸,客户产品盖蓝色QA PASS章,
记录每一订单箱号范围、流水号范围、物流码范围
生产线封箱,OQC监督,外箱底部贴白色封箱签
出货检验作业流程
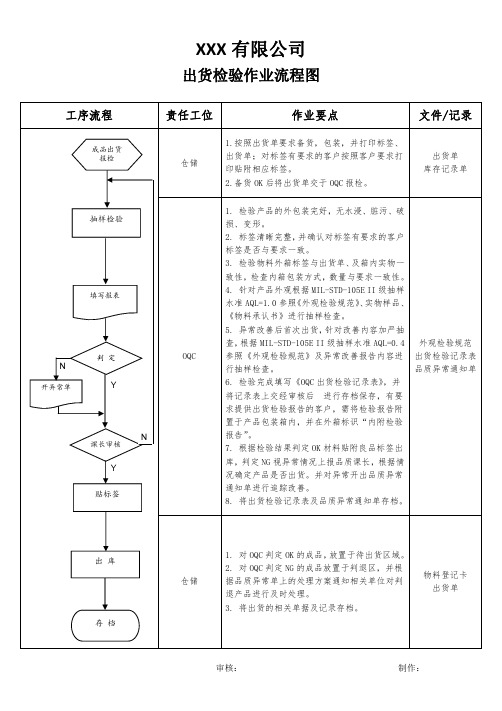
1. 检验产品的外包装完好,无水浸、脏晰完整,并确认对标签有要求的客户
标签是否与要求一致。
3. 检验物料外箱标签与出货单、及箱内实物一
致性,检查内箱包装方式,数量与要求一致性。
4. 针对产品外观根据 MIL-STD-105E II 级抽样
水准 AQL=1.0 参照《外观检验规范》、实物样品、
求提供出货检验报告的客户,需将检验报告附
置于产品包装箱内,并在外箱标识“内附检验
报告”。
7. 根据检验结果判定 OK 材料贴附良品标签出
库,判定 NG 视异常情况上报品质课长,根据情
况确定产品是否出货。并对异常开出品质异常
通知单进行追踪改善。
8. 将出货检验记录表及品质异常通知单存档。
出库 存档
仓储
XXX 有限公司
出货检验作业流程图
工序流程
责任工位
作业要点
文件/记录
成品出货 报检
仓储
1.按照出货单要求备货,包装,并打印标签、 出货单;对标签有要求的客户按照客户要求打 印贴附相应标签。 2.备货 OK 后将出货单交于 OQC 报检。
出货单 库存记录单
抽样检验
填写报表
N 开异常单
判定 Y
N 课长审核
1. 对 OQC 判定 OK 的成品,放置于待出货区域。 2. 对 OQC 判定 NG 的成品放置于判退区,并根 据品质异常单上的处理方案通知相关单位对判 退产品进行及时处理。 3. 将出货的相关单据及记录存档。
物料登记卡 出货单
审核:
制作:
《物料承认书》进行抽样检查。
5. 异常改善后首次出货,针对改善内容加严抽
查,根据 MIL-STD-105E II 级抽样水准 AQL=0.4 外观检验规范
仓库管理表格大全
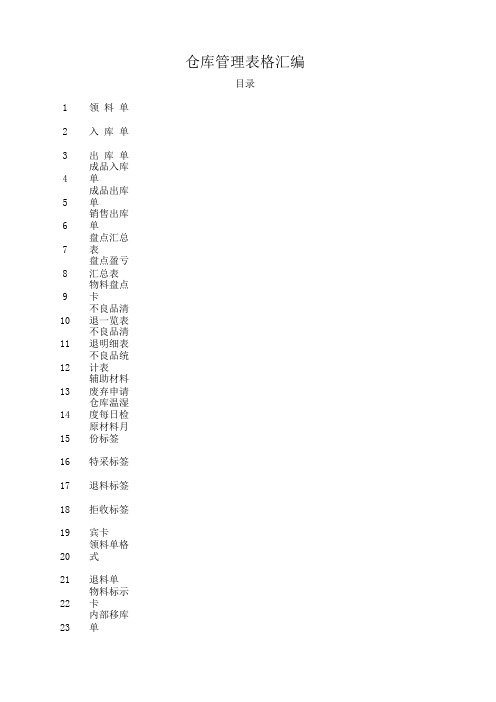
仓库管理表格汇编
目录
1领 料 单
2入 库 单
3出 库 单
4成品入库单
5成品出库单
6销售出库单
7盘点汇总表
8盘点盈亏汇总表
9物料盘点卡
10不良品清退一览表
11不良品清退明细表
12不良品统计表
13辅助材料废弃申请单
14仓库温湿度每日检查表
15原材料月份标签
16特采标签
17退料标签
18拒收标签
19宾卡
20领料单格式
21退料单
22物料标示卡
23内部移库单
24生产领料单
25物料复检周期表
26仓库温湿度记录曲线图
27仓库环境温湿度记录表
28请购单
29每日收货记录
30退火料仓库先进先出状态看板31成品丝仓库先进先出状态栏32原材料仓库管理看板
33退料单(2)
34成品出货检查确认单
35装货人员及装柜信息表
36成品装柜明细表单
37成品装柜明细图片
38成品出入库明细记录表
39外购月收货流水明细存根表40进料验收异常报告
41退货单
42车间退料及检查报告单
43报废单
44原物料库存表
45化学品仓库巡查记录表
46仓库定期检查记录表
47仓库定期巡回稽核表
48设备故障记录表
49设备日常点检表50设备故障报告单。
成品出货检验程序,成品包装、入库和出货前质量检验规定
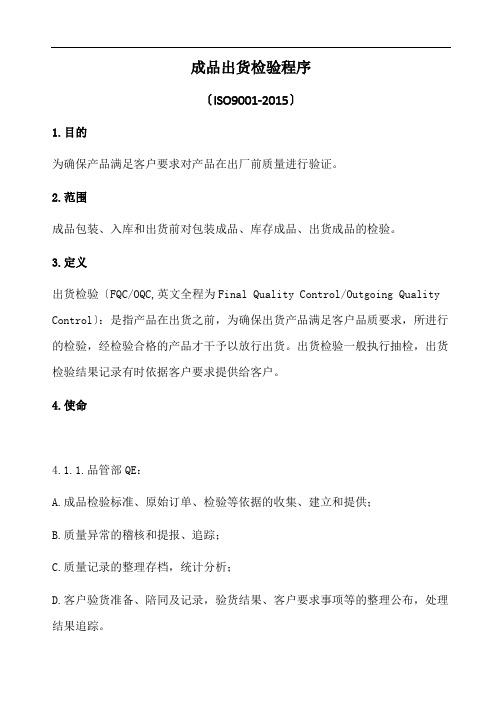
成品出货检验程序〔ISO9001-2015〕1.目的为确保产品满足客户要求对产品在出厂前质量进行验证。
2.范围成品包装、入库和出货前对包装成品、库存成品、出货成品的检验。
3.定义出货检验〔FQC/OQC,英文全程为Final Quality Control/Outgoing Quality Control〕:是指产品在出货之前,为确保出货产品满足客户品质要求,所进行的检验,经检验合格的产品才干予以放行出货。
出货检验一般执行抽检,出货检验结果记录有时依据客户要求提供给客户。
4.使命4.1.1.品管部QE:A.成品检验标准、原始订单、检验等依据的收集、建立和提供;B.质量异常的稽核和提报、追踪;C.质量记录的整理存档,统计分析;D.客户验货准备、陪同及记录,验货结果、客户要求事项等的整理公布,处理结果追踪。
4.1.2.品检PQC:A.包装成品〔含首件检验〕、库存成品的检验和判定。
B.成品检验记录的填写、质量记录的收集、汇总给品管部QE统计;C.质量问题的反馈、处理、追踪及改正预防措施的落实及跟踪;D.不良品的管制、标识。
4.1.3.品管部OQC:A.整理准备检验依据,并依照进行检验。
B.库存成品\出货成品检验的执行及异常的反馈、监督处理。
C.出货检验报告的填写、汇总。
4.2.资材仓库:成品包装、成品储存、成品装货。
4.3.制造单位:产品的自检、质量异常的改正预防措施的提出和处理。
4.4.技术部:技术资料、包装方式、装柜方式确实定和辅导。
5.作业内容5.1.包装成品首件确认5.1.1.批量成品包装前,由包装组依据《制造命令单》、《包装作业指导书》、有效的产品图纸,《产品检验规范》等文件,具体了解客户的包装要求〔如唛头、标签、条形码等〕,使用对应的包装材料和包装方法进行包装,必要时通知技术部进行辅导。
5.1.2.首件制作完成由品检人员进行首件确认,首件确认必需完成如下的检验项目:A.确认包装的正确性:包装材料的材质、规格、尺寸和包装方式、产品及所必需零配件数量。
成品外观检验规范

538系列旳料号不容许修补(含补金和补漆),需用AVI及板弯翘检查机100%检查。
4.2文字文字油墨颜色依客户指定或设计工程单位规定。
文字字体或图样需清晰且易辨识。
文字油墨因印刷过程偏移,则容许沾染大锡垫,但不可沾染S.M.D,金手指和零件孔内检查项目检查细项鉴定原则图示文字文字印刷印刷字体不得模糊导致无法辨识应清晰轻易辨识(L22)文字ONPAD文字印刷不得ON PAD(特殊设计者除外)文字印错/漏印文字印刷不得印错/漏印(对旳) (错误)4.3基板表面基板脱层在十倍放大镜下,不容许胶片与胶片间或是铜层与胶片间有脱层起泡。
粉红圈及白边现象在十倍放大镜下,不容许有脱层现象。
基板表面异物,不容许有目视可观测到不透明异物或导电性杂质。
4.4线径线径旳原则以客户所提供旳原稿底片为参照根据,来决定最大和最小旳允收条件。
线路缺口不容许超过原稿底片±20%。
线路上有针孔,凹陷或不规则形状时,不容许超过原稿底片±20%。
使用工具为50倍目镜。
4.5线路间距依客户所提供旳原稿底片,规定最小间距旳需求,无规定者依设计工程为主。
存在线路间距中旳金属残渣,不容许超过原稿底片±20%。
使用工具为50倍目镜。
4.6锡垫平环锡垫平环凹洞或变形不容许超过总面积旳30%。
锡垫平环残缺部份扔须维持最小锡垫2MIL 之规定。
导通孔平环残缺部份扔须维持最小锡垫1MIL 之规定。
检查 项目 检查细项鉴定原则 图示线路线路补线不可补线。
线路短/断路 不得短/断路线路不良1. 线边粗糙、线路缺口、裂痕、针孔、不可超过线路宽度20%2. 线路导体突出部凸出后,线路导体间隔不可不大于原间距之1/5线路变形 线路不得扭曲、翘起、剥离变形孔塞孔位置导通孔若正反两面阶位于防焊涂布区域内,必须用绿漆塞孔,且塞孔率必须高于95%以上(尤其指定之状况则不在此限内)孔与锡垫变形不得脱落、翘起、变形N-P孔有毛头不得影响组件及机构组装,突出尺寸不能超过机构图之tolerance ,且触碰后不可脱落之状况下可以允收,但折断边可不在此限制内,必要时以程度样本做为鉴定根据。
仓库成品出货单据流程
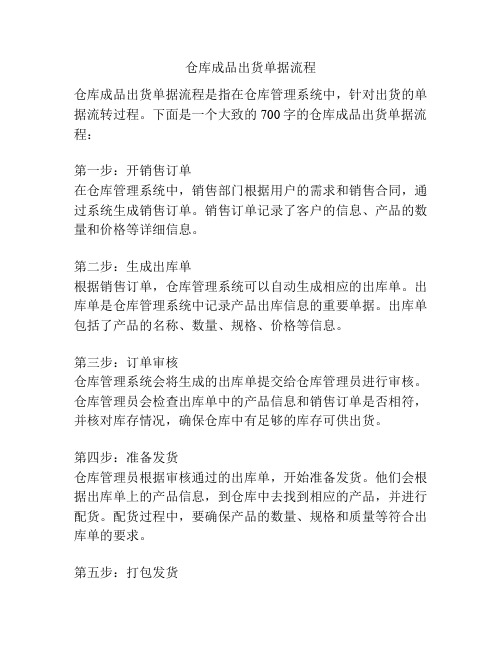
仓库成品出货单据流程仓库成品出货单据流程是指在仓库管理系统中,针对出货的单据流转过程。
下面是一个大致的700字的仓库成品出货单据流程:第一步:开销售订单在仓库管理系统中,销售部门根据用户的需求和销售合同,通过系统生成销售订单。
销售订单记录了客户的信息、产品的数量和价格等详细信息。
第二步:生成出库单根据销售订单,仓库管理系统可以自动生成相应的出库单。
出库单是仓库管理系统中记录产品出库信息的重要单据。
出库单包括了产品的名称、数量、规格、价格等信息。
第三步:订单审核仓库管理系统会将生成的出库单提交给仓库管理员进行审核。
仓库管理员会检查出库单中的产品信息和销售订单是否相符,并核对库存情况,确保仓库中有足够的库存可供出货。
第四步:准备发货仓库管理员根据审核通过的出库单,开始准备发货。
他们会根据出库单上的产品信息,到仓库中去找到相应的产品,并进行配货。
配货过程中,要确保产品的数量、规格和质量等符合出库单的要求。
第五步:打包发货准备发货后,仓库管理员会将产品进行包装,并进行标记,以便快递或物流公司可以方便进行运输。
包装的方式可能因不同产品而有所不同,但都要保证产品的安全和完整性。
第六步:生成发货单发货后,仓库管理员会根据发货情况,生成发货单。
发货单是一种记录产品出库和运输过程的单据,包括产品的名称、数量、运输方式、收货人信息等。
发货单会发送给销售部门和财务部门进行相应的处理。
第七步:发货确认销售部门在收到发货单后,会与物流或快递公司进行确认,确保产品按时送达客户,并记录相关的发货信息。
一旦确认发货无误,销售部门会通知客户,并进行相应的收款操作。
第八步:更新库存在完成出货后,仓库管理系统会自动更新库存数量。
出库的产品数量会从库存中扣除,以便进行后续的库存管理工作。
同时,系统也会生成相应的出库报表和库存报表,供仓库管理员和财务部门参考。
以上便是一个大致的仓库成品出货单据流程。
随着企业规模的扩大和仓储系统的升级,仓库管理流程也会有所变化和调整,以满足企业的需求和市场的变化。
产品抽样检验方案规范成品出货检验流程
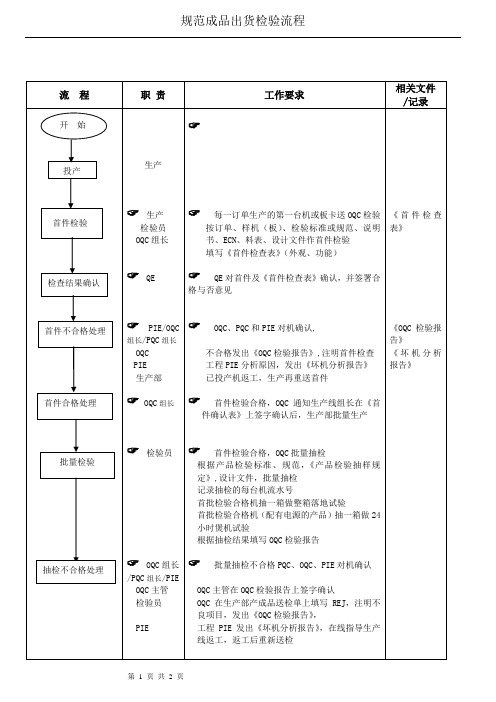
首件不合格处理 首件合格处理
PIE/OQC
组长/PQC 组长 OQC PIE 生产部
OQC、PQC 和 PIE 对机确认,
不合格发出《OQC 检验报告》,注明首件检查 工程 PIE 分析原因,发出《坏机分析报告》 已投产机返工,生产再重送首件
《OQC 检验报 告》 《坏机分析 报告》
OQC 组长 首件检验合格,OQC 通知生产线组长在《首
393812649工作要求相关文件记录首件检验生产生产检验员oqc组长qepieoqc长pqc组长oqcpie生产部oqc组长检验员oqc组长pqc组长pieoqc主管检验员pie每一订单生产的第一台机送oqc检验按订单样机检验标准或规范说明书ecn料表设计文件作首件检验填写首件检查表外观功能qe对首件及首件检查表确认并签署合格与否意见oqcpqc和pie对机确认不合格发出oqc检验报告注明首件检查工程pie分析原因发出坏机分析报告已投产机返工生产再重送首件首件检验合格oqc通知生产线组长在首件确认表上签字确认后生产部批量生产首件检验合格oqc批量抽检根据产品检验标准规范产品检验抽样规定设计文件批量抽检记录抽检的每台机流水号首批检验合格机抽一箱做整箱落地试验首批检验合格机配有电源的产品抽一箱做24小时煲机试验根据抽检结果填写oqc检验报告批量抽检不合格pqcoqcpie对机确认oqc主管在oqc检验报告上签字确认oqc在生产部产成品送检单上填写rej注明不良项目发出oqc检验报告工程pie发出坏机分析报告在线指导生产线返工返工后重新送检首件检查oqc检验报坏机分析报告投产检查结果确认首件不合格处理首件合格处理批量检验抽检不合格处理点亮网http
规范成品出货检验流程
流程
开始
投产
职责
生产
成品出货检验标准

成品出货检验标准一、目的产品出成品仓前,实施保证检查以便确认产品的质量状况,及是否合乎客户和公司的质量要求;产品出厂后能满足客户的标准及使用者的爱好,提高市场的竞争力。
二、适用范围凡本司生产的成品出仓库前,依本办法作抽样检查。
三、定义OQA(Outgoing Quality Assurance):出货质量保证。
四、职责1、负责对成品待验区机器按批执行抽样及检验机器进行拆包、附件检查、包装、搬运2、作业;3、负责对量产机器检验状态的标识;4、负责执行电气及外观、附件及包装检验与检验报表记录;5、负责请相关部门对不良品进行分析与成品出货判定;6、负责产品外观不良的出货判定;7、负责重大问题之反馈和产品重大异常的判定及品质异常的追踪;8、负责对成品仓放置超过3个月的成品,成品仓负责人提出申请,OQA安排重新检验,六、缺点定义缺点(CRI):产品本身具备的功能失效及影响人身安全。
主要缺点(MAJ):外观结构或尺寸结构,部分功能失效或者附属功能失效。
品质不符合规格。
次要缺点(MIN):凡是没有安全上隐患,亦非尺寸不良,不影响产品功能。
外观面为次要不良,品质特性不符合规格及标准。
七、检验环境:在下列范围内的湿度、温度和气压的任意组合条件下进行测量。
环境温度:15℃~35℃;相对湿度:45%~75%;大气压力:86KPa~106Kpa;在上述测试条件下,被测设备应满足其性能规范,但在比上述测试条件更宽的范围内,设备仍能工作,但可不满足其所有的性能规范,并允许被测设备在更为极端的条件下储存。
12、检验要求和内容外观、结构质量检验图象、伴音质量检验功能质量检验安全、电磁兼容质量检验包装质量检验6.外观、结构质量检验要求6.1 检验内容与要求;Ⅰ产品外观必须具有如下标志,且标志正确、清晰可辨产品机壳或后盖贴纸上必须有产品商标、型号、名称、生产企业名称;产品后盖必须具有警告用户安全使用的“警告标记”;产品后盖上应有电源性质、额定电压、最大电流、电源频率、功耗等;产品后盖上必须加贴产品序号条码,且与纸箱、保修卡号码一致;产品面壳上必须有正确的指示灯标志;Ⅱ产品外观、结构质量检验要求产品外观应整洁光滑,表面不应有凹凸变形、粗糙不平、划伤、脱漆、缩水、间隙、裂纹、毛刺、边缘棱角突出、霉斑、脏污、色差、金属斑点、黑点、纹理等任何缺陷;外观各类文字、图案及符号丝印应端正、清晰、牢固,标识功能应与实际产品特性相符;产品保护膜应粘贴良好,无破损、脏污等不良;产品铭牌、装饰件、紧固件及其它零部件应无锈蚀、变形、划伤、金属斑点、黑点等任何不良现象,且安装牢固、匹配良好,无缺损、脱落、松动、歪斜、间隙、台阶、螺孔错位等问题指示灯、接收头及其白镜或红镜安装应规范,不应漏装或歪斜;开关、按键、旋钮等应操作灵活可靠,无缺损、变形、划伤、歪斜等问题;各类音视频输入输出接口(含RF 接口、S 端子接口、YUV 接口、VGA 接口等)应安装牢固、端子颜色正确,拔插顺畅;显示屏应安装牢固,无偏斜,与机箱吻合,且无超标划伤、黑点、脏污、油渍等缺陷6.2 外观、结构质量检验方法;外观、结构质量检验方法采取目测和手感检查。
成品出货检验工作标准流程

OQC转发客户验货报告
工程发出坏机分析报告和返工报告
计划安排返工,返工后再重新送检
பைடு நூலகம்客户验货合格,OQC检验员核对卡板数量在生产部产成品送检单上注明客户检验合格
生产线将合格产品入成品仓
送检单
客户验货报告
坏机分析报告
返工报告
作业员
OQC组长/领班
QE/PIE
OQC
PIE
批量抽检合格,组长在OQC检验报告签字确认
合格话机在生产部产成品送检单上盖蓝色QA PASS章,外箱贴绿色QA合格证贴纸,客户产品盖蓝色QA PASS章,
记录每一订单箱号范围、流水号范围、物流码范围
生产线封箱,OQC监督,外箱底部贴白色封箱签
客户产品批量合格后,OQC填写送检单通知客户验货
OQC
PIE
生产部
OQC组长
检验员
OQC组长/PQC组长/PIE
OQC主管
检验员
PIE
每一订单生产的第一台机送OQC检验
按订单、样机、检验标准或规范、说明书、ECN、料表、设计文件作首件检验
填写首件检查表外观、功能
QE对首件及首件检查表确认,并签署合格与否意见
OQC、PQC和PIE对机确认,
不合格发出OQC检验报告,注明首件检查
根据抽检结果填写OQC检验报告
批量抽检不合格PQC、OQC、PIE对机确认
OQC主管在OQC检验报告上签字确认
OQC在生产部产成品送检单上填写 REJ,注明不良项目,发出OQC检验报告,
工程PIE发出坏机分析报告,在线指导生产线返工,返工后重新送检
首件检查表
OQC检验报告
坏机分析报告
OQC组长
OQC 成品出货检验标准 (参考模板)
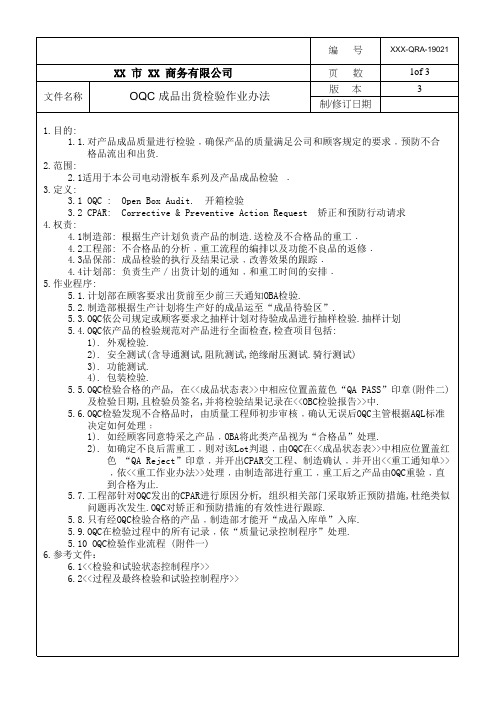
文件名称
XX 市 XX 商务有限公司 OQC 成品出货检验作业办法
6.3<<不合格品的控制程序>> 6.4<<质量记录控制程序>> 6.5<<重工作业办法>> 7.表单: 7.2. <<OQC Inspection Report>>
3.定义: 3.1 OQC : Open Box Audit. 开箱检验 3.2 CPAR: Corrective & Preventive Action Request 矫正和预防行动请求
4.权责: 4.1制造部: 根据生产计划负责产ห้องสมุดไป่ตู้的制造.送检及不合格品的重工﹒ 4.2工程部: 不合格品的分析﹐重工流程的编排以及功能不良品的返修﹒ 4.3品保部: 成品检验的执行及结果记录﹐改善效果的跟踪﹒ 4.4计划部: 负责生产/出货计划的通知﹐和重工时间的安排﹒
文件名称
XX 市 XX 商务有限公司 OQC 成品出货检验作业办法
编号
页数 版本 制/修订日期
XXX-QRA-19021
1of 3 3
1.目的: 1.1.对产品成品质量进行检验﹐确保产品的质量满足公司和顾客规定的要求﹐预防不合 格品流出和出货.
2.范围: 2.1适用于本公司电动滑板车系列及产品成品检验 ﹒
5.作业程序: 5.1.计划部在顾客要求出货前至少前三天通知OBA检验. 5.2.制造部根据生产计划将生产好的成品运至“成品待验区”. 5.3.OQC依公司规定或顾客要求之抽样计划对待验成品进行抽样检验.抽样计划 5.4.OQC依产品的检验规范对产品进行全面检查,检查项目包括: 1). 外观检验. 2). 安全测试(含导通测试,阻阬测试,绝缘耐压测试.骑行测试) 3). 功能测试. 4). 包装检验. 5.5.OQC检验合格的产品, 在<<成品状态表>>中相应位置盖蓝色“QA PASS”印章(附件二) 及检验日期,且检验员签名,并将检验结果记录在<<OBC检验报告>>中. 5.6.OQC检验发现不合格品时, 由质量工程师初步审核﹐确认无误后OQC主管根据AQL标准 决定如何处理﹕ 1). 如经顾客同意特采之产品﹐OBA将此类产品视为“合格品”处理. 2). 如确定不良后需重工﹐则对该Lot判退﹐由OQC在<<成品状态表>>中相应位置盖红 色 “QA Reject”印章﹐并开出CPAR交工程、制造确认﹐并开出<<重工通知单>> ﹐依<<重工作业办法>>处理﹐由制造部进行重工﹐重工后之产品由OQC重验﹐直 到合格为止. 5.7.工程部针对OQC发出的CPAR进行原因分析, 组织相关部门采取矫正预防措施,杜绝类似 问题再次发生.OQC对矫正和预防措施的有效性进行跟踪. 5.8.只有经OQC检验合格的产品﹐制造部才能开“成品入库单”入库. 5.9.OQC在检验过程中的所有记录﹐依“质量记录控制程序”处理. 5.10 OQC检验作业流程 (附件一)
成品出货检验标准
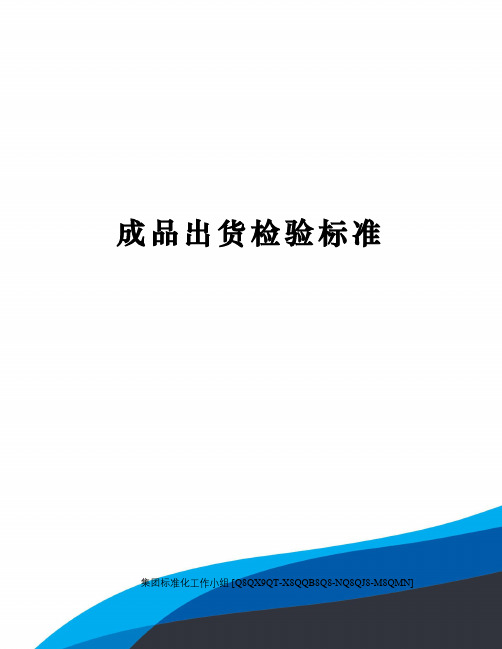
成品出货检验标准集团标准化工作小组 [Q8QX9QT-X8QQB8Q8-NQ8QJ8-M8QMN]成品出货检验标准一、目的产品出成品仓前,实施保证检查以便确认产品的质量状况,及是否合乎客户和公司的质量要求;产品出厂后能满足客户的标准及使用者的爱好,提高市场的竞争力。
二、适用范围凡本司生产的成品出仓库前,依本办法作抽样检查。
三、定义OQA(Outgoing Quality Assurance):出货质量保证。
四、职责1、负责对成品待验区机器按批执行抽样及检验机器进行拆包、附件检查、包装、搬运2、作业;3、负责对量产机器检验状态的标识;4、负责执行电气及外观、附件及包装检验与检验报表记录;5、负责请相关部门对不良品进行分析与成品出货判定;6、负责产品外观不良的出货判定;7、负责重大问题之反馈和产品重大异常的判定及品质异常的追踪;8、负责对成品仓放置超过3个月的成品,成品仓负责人提出申请,OQA安排重新检验,五、来料品质标准六、缺点定义缺点(CRI):产品本身具备的功能失效及影响人身安全。
主要缺点(MAJ):外观结构或尺寸结构,部分功能失效或者附属功能失效。
品质不符合规格。
次要缺点(MIN):凡是没有安全上隐患,亦非尺寸不良,不影响产品功能。
外观面为次要不良,品质特性不符合规格及标准。
七、检验环境:在下列范围内的湿度、温度和气压的任意组合条件下进行测量。
环境温度:15℃~35℃;相对湿度:45%~75%;大气压力:86KPa~106Kpa;在上述测试条件下,被测设备应满足其性能规范,但在比上述测试条件更宽的范围内,设备仍能工作,但可不满足其所有的性能规范,并允许被测设备在更为极端的条件下储存。
12、检验要求和内容外观、结构质量检验图象、伴音质量检验功能质量检验安全、电磁兼容质量检验包装质量检验6.外观、结构质量检验要求检验内容与要求;Ⅰ产品外观必须具有如下标志,且标志正确、清晰可辨产品机壳或后盖贴纸上必须有产品商标、型号、名称、生产企业名称;产品后盖必须具有警告用户安全使用的“警告标记”;产品后盖上应有电源性质、额定电压、最大电流、电源频率、功耗等;产品后盖上必须加贴产品序号条码,且与纸箱、保修卡号码一致;产品面壳上必须有正确的指示灯标志;Ⅱ产品外观、结构质量检验要求产品外观应整洁光滑,表面不应有凹凸变形、粗糙不平、划伤、脱漆、缩水、间隙、裂纹、毛刺、边缘棱角突出、霉斑、脏污、色差、金属斑点、黑点、纹理等任何缺陷;外观各类文字、图案及符号丝印应端正、清晰、牢固,标识功能应与实际产品特性相符;产品保护膜应粘贴良好,无破损、脏污等不良;产品铭牌、装饰件、紧固件及其它零部件应无锈蚀、变形、划伤、金属斑点、黑点等任何不良现象,且安装牢固、匹配良好,无缺损、脱落、松动、歪斜、间隙、台阶、螺孔错位等问题指示灯、接收头及其白镜或红镜安装应规范,不应漏装或歪斜;开关、按键、旋钮等应操作灵活可靠,无缺损、变形、划伤、歪斜等问题;各类音视频输入输出接口(含 RF 接口、S 端子接口、YUV 接口、VGA 接口等)应安装牢固、端子颜色正确,拔插顺畅;显示屏应安装牢固,无偏斜,与机箱吻合,且无超标划伤、黑点、脏污、油渍等缺陷外观、结构质量检验方法;外观、结构质量检验方法采取目测和手感检查。