微电子工业中清洗工艺的研究进展
清洗技术及其在微电子领域的应用

1 清 洗媒体
1 1 分 类
高。根据污垢微粒 的大 小, 将工业清洗 分为一 可
般工 业清洗 、 密工 业清 洗和超 精密 工业清 洗。 精
清洗媒体可分为液态清洗媒体和气态清洗媒
体。
其中, 一般工业清洗中要去除的污垢微粒直径, 通
常都大于 1 0一m(0 1 m) 清 洗 后 物 体 的 清 洁 程 度 , 通 常 用 肉 眼观 察 和 用 手 触 摸 即 可 判 断 。 精 密工 业 清洗 中要 洗 除 的微 粒 直 径 范 围 是 1 ~ 1 O~ 0~1, 1 1 这样 的 直径 范 围 至 少 用 光 学 显 微 镜 才能 观 察 到 。 超精 密 工 业 主 要 指 现 代 微 电子 工 业 , 在 半 导 体 如 工业 领域 要 求 去 除 的 污 垢 微 粒 直 径 小 到 1 ~ 0一
维普资讯
第{ 第 期 2 1 j 卷
( ) 清 洗 力 起 传 输 作 用 1对
娥 瞧隧g
物污垢。
2 1
如在超 声清洗 中必 须借助酒 精、 丙酮等 清洗 媒体, 才能将超声能作用在清洗对象 上, 使其上的
污 垢 得 以清 除 。 又 如 PI 处 理 必须 通 过 氮 气 这 ND
面附着的粗大砂土颗粒。
种清洗媒体 , 其冲刷 、 吹拭的力量才能作用在 电路
表 面 , 除 其 上 的 多 余 物 。 另 一 个 很 典 型 的 例 子 清
是用肥皂洗衣服。肥皂是一种具有很强清洗力的
物 质 , 我 们知 道 , 果 把 它 直 接 涂 在 沾 有污 垢 的 但 如 衣 物 上并 不 能 很 好 地 发 挥 它 的 清 洗 效 力 , 只 有 而
任何一个清洗过 程都必 然存在 三种物 质, 即 待清洗物体( 以下统称为清洗对象) 某种介质( 、 以
集成电路制造过程中的清洗技术

集成电路制造过程中的清洗技术嘿,朋友们!今天咱来聊聊集成电路制造过程中的清洗技术。
这可真是个了不起的环节啊!你想想看,集成电路就好比是一个极其复杂精细的迷你城市,里面有无数的“街道”和“建筑”。
而清洗技术呢,那就像是这个迷你城市的清洁工,要把那些不应该存在的脏东西都清理掉。
要是清洁工没做好工作,那这个城市不就乱套啦?同理,清洗技术要是不到位,集成电路可就没法好好工作咯!在制造集成电路的过程中,会有各种各样的污染物出现,就像我们生活中会有灰尘、垃圾一样。
这些污染物可能是微小的颗粒,也可能是一些化学物质。
它们要是留在集成电路上,那可就糟糕啦!就好像你走路的时候鞋子上沾了块口香糖,那多难受呀!那怎么进行清洗呢?这可就有很多门道啦!就像是我们打扫房间,得用合适的工具和方法。
有时候得用清水冲一冲,有时候得用专门的清洁剂擦一擦。
在集成电路制造中也是一样,有不同的清洗方法和试剂呢。
比如说有一种清洗方法叫湿法清洗,就好像给集成电路洗了个舒服的澡。
把它泡在合适的溶液里,那些污染物就被溶解啦,或者被冲刷掉啦。
还有干法清洗呢,就像是用一阵强风吹走灰尘一样,把污染物给弄走。
这清洗技术可不能马虎啊!要是没洗干净,集成电路可能会出各种问题。
就像你衣服没洗干净穿着就不舒服一样。
而且清洗的时候还得注意不能太用力啦,不然会把集成电路给弄坏的哦!这就好比你擦桌子不能太使劲把桌子擦坏了呀。
你说这清洗技术是不是很神奇?它虽然看起来不起眼,但是却对集成电路的质量有着至关重要的影响呢!它就像一个默默奉献的幕后英雄,没有它,集成电路可没法那么出色地工作。
所以啊,大家可别小看了集成电路制造过程中的清洗技术。
它就像我们生活中的那些看似平凡但却不可或缺的事情一样,虽然不显眼,但却无比重要。
我们应该好好重视它,让它为我们的科技发展发挥更大的作用呀!这就是我对集成电路制造过程中清洗技术的看法,你们觉得呢?。
半导体器件制造中的清洗技术研究

半导体器件制造中的清洗技术研究近年来,半导体器件制造技术的发展给人们的生活带来了巨大的变化。
从智能手机到笔记本电脑,从家用电器到工业自动化,嵌入式半导体器件的应用已经无处不在。
在这些半导体器件的制造过程中,清洗技术是一个非常关键的步骤。
本文将以半导体器件制造中的清洗技术研究为主题,对清洗技术的发展现状和未来趋势进行探讨。
第一部分:半导体器件的制造过程半导体器件的制造过程可以大致分为三个步骤:晶圆制备、芯片制作和封装封装。
其中,晶圆制备是制造过程中最为关键的一部分,需要对硅晶片进行加工,将其制成光刻图形的文件!,然后用掩模将光刻图形转移到晶圆上,形成芯片上的电路组件。
在以上两个步骤中,半导体芯片需要多次进行清洗,以去除杂质和处理涂覆的腐蚀剂。
这些清洗步骤的性能和效率直接影响到芯片的品质和制造成本。
第二部分:清洗技术的发展现状随着半导体制造过程的不断优化和升级,清洗技术也在不断发展和改进。
在过去的几十年中,清洗技术面临着许多挑战,如杂质的去除、电路的尺寸缩小、热处理和低压制造等问题,同时还需要考虑节能和减排的问题。
目前,在半导体器件制造中,一些常用的清洗技术包括化学和物理清洗。
化学清洗主要是利用酸碱反应将杂质和污垢分解和溶解,而物理清洗则是采用气体、水或高能量的激光束等物理方式将表面杂质去除。
如今,随着技术的发展,微型水射流、超声波和离子清洗等新型技术也开始被广泛应用到清洗半导体芯片的过程中。
除此之外,还有一些新兴的清洗技术开始出现。
例如等离子体清洗技术,它是通过等离子体在处理腐蚀剂时形成的氧化和还原的过程来进行清洗。
这种技术不仅不产生废水、废气和废液,而且能够降低废品率,提高效率。
第三部分:清洗技术的未来趋势清洗技术是半导体器件制造中最关键的一环,其技术的进步直接影响到半导体器件的成本和生产效率。
为了更好地适应未来市场需求,清洗技术也需要不断升级和改进。
一些专家预测,未来的清洗技术将更加趋向于绿色环保和智能化。
微电子工艺清洗技术的应用分析

微电子工艺清洗技术的应用分析作者:张爽来源:《科学与财富》2018年第10期摘要:当前的社会是一个高速发展的社会,其主要依赖的就是科技的进步。
而在当前的科技中,最为高端的就是微电子产业。
其承载的主要作用就是制作一些精密的电子仪器。
尤其是手机,电脑一类,但是在进行微电子产品制作的时候,却存在着很多的问题,其中主要是对于硅片的清洗工作。
因为微电子中使用的硅片一般体积较小,这就让清洗的工作变得非常的困难。
如果更好的进行硅片的清洗就成为了当前最为重要的一个课题。
本文就从当前的微电子清洗情况进行探究,来得出如何更好的在微电子工艺领域进行清洗技术的应用。
关键词:微电子行业;新型湿法清洗工艺;应用在当前来看,微电子工艺主要的用途就是将一些精密仪器变得更加的微型,更加的精密。
但是,在微电子工业的生产中,却常常存在着一个问题,那就是硅片的清洗较为困难。
这主要是因为硅片的清洗在微电子产品的生产中是非常重要的一个部分。
因此就需要强化硅片清洗的能力,才能够保证工厂正常的运行。
一、微电子工艺清洗的必要性众所周知,微电子工艺最核心的部分就是硅片的运用,这些硅片就是微电子核心最基础的组成部分,其主要承载的就是运行和储存的任务。
因此,在进行硅片处理的时候,是一定要小心的。
而且,许多的公司在得到硅片的时候,都是硅片的原始状态,这样原始状态的硅片其实是非常难以进行运用的。
因为其不仅质量参差不齐,更是有着许多的污渍。
这些污渍会严重的影响到硅片的使用,让一些硅片无法发挥作用。
因此就需要对硅片进行清洗,但是这种清洗却不是简单的清洗。
因为硅片是一种较为脆弱的电子元件,如果单纯的使用水流冲洗,那么就会对硅片造成致命的损伤。
所以,就需要采用特殊的办法去清理硅片上的污渍,这样才能够让硅片得以保存完好,并且付诸使用。
因此,如何清洗硅片一直是微电子公司最头疼的问题。
因为硅片上的污渍是分为很多的类型的,不可能都采用同一种方法进行清洗。
因此就需要采用特别多的方法进行清洗,这也极大的耽误了工作的效率。
微电子器件制造中晶片清洗技术研究

微电子器件制造中晶片清洗技术研究一、绪论自微电子器件问世以来,其已经成为现代信息科技、通讯、电子等领域最重要的组成部分。
而在微电子器件的制造中,晶片清洗技术也占据着至关重要的地位。
晶片清洗技术主要是对微电子器件加工过程中产生残留的污染物进行清除,以保证器件质量的稳定性和可靠性。
本文将围绕微电子器件制造中的晶片清洗技术展开深入探讨。
二、微电子器件制造中的晶片清洗技术1. 晶片清洗的原理晶片清洗是通过在纯水或其他含有清洗剂的浸泡液中对晶片进行清洗,使其表面的有害化学物质或杂质得以去除。
由于微电子器件晶片上的金属导线、绝缘层和结构尺寸都非常微小,故晶片清洗的要求也比较高。
在晶片清洗过程中,要保证清洗剂的品质和浓度,否则会对晶片产生细微的影响或短路等损坏。
此外,由于晶片上的零部件非常微小,清洗过程中的时间和温度控制也非常关键。
2. 晶片清洗的方法在微电子器件制造中,有许多清洗晶片的方法,例如机械清洗、超声波清洗、等离子体清洗、气体清洗和化学清洗等。
其中,化学清洗是目前最多被采用的一种方法。
化学清洗主要是采用化学溶解和化学反应的原理,通过浸泡或喷涂等方式,使有害化学物质得以清洗掉。
本方法具有高效、均匀、可重复性好等优点。
3. 晶片清洗后处理的方法晶片清洗后需要对其进行后处理,目的是去除残余的清洗剂和水分以及提高晶片表面的平整度和增强其吸附性。
后处理一般采用干燥、氧化和铝化等方法。
干燥是指将清洗后的晶片晾干或加热干燥,同时通过紫外线消毒和紫外线正离子发生器去除污染物。
氧化和铝化是一种添加氧化剂和铝剂的化学方法,可以使晶片表面变得更加平整,增强吸附性和附着力。
三、晶片清洗技术的发展趋势晶片清洗技术目前已经非常成熟,但随着微型芯片制造工艺的不断提升,对晶片清洗技术也提出了更高的要求。
未来的晶片清洗技术方向主要有三个:一是增强对微小污染物的清除能力;二是提高清洗过程对晶片的保护性能;三是快速清洗技术的发展。
在面对越来越严谨的环境要求下,晶片清洗技术的规范化和标准化将成为未来晶片清洗技术发展的重要趋势。
硅片清洗技术进展

硅片清洗技术进展一、序言半导体硅作为现代电子工业的基础材料己有半个世纪的历史,随着亚微米及深亚微米超大规模集成电路(ULSI)遵循着“摩尔定律”迅速发展,设计线宽急剧减小,基体表面的亚微米污物足以导致大量缺陷产生并对生产领域造成一系列影响,给硅片表面质量提出了越来越苛刻的要求。
硅片表面的颗粒、有机物、金属、吸附分子、微粗糙度、自然氧化层等严重影响器件性能,清洗不佳引起的器件失效已超过集成电路制造中总损失的一半。
因此,硅片清洗技术成为硅晶片加工和超大规模集成电路工艺研究的一大热点。
本文在分析硅片表面污染物基础上,对硅片目前流行的清洗工艺原理作概述,并介绍其最新进展[1] 。
二、硅片加工表面污染类型在硅片加工及器件制造过程中,所有与硅片接触的外部媒介都是硅片沾污的可能来源。
这主要包括以下几方面:硅片加工成型过程中的污染、环境污染、水造成的污染、试剂带来的污染、工业气体带来的污染、工艺本身带来的污染、人体造成的污染等。
其污染主要有以下几种类型[1] :(1)颗粒沾污;(2)有机物沾污;(3)金属离子沾污;(4)自然氧化层沾污。
三、硅片清洗的主要方法到目前为止,清洗方法可分为许多种,工业生产种使用较多的有:RCA青洗法、超声波清洗法、兆声波清洗法、机械刷片法等。
下面对以上几种方法作简要说明:(一)RCA清洗法RCA由Werner Kern 于1965 年在N.J.Princeton 的RCA实验室首创,并由此得名。
RCA清洗是一种典型湿式化学清洗,在各种清洗方法中仍占主导地位。
国内外已有多篇文章用不同的分析方法证实了RCA的有效性。
RCA清洗主要用于清除有机表面膜、粒子和金属沾污。
该清洗方法存在诸多弊端:如硅片表面清洗涉及到许多化学试剂;其处理均在高温过程中进行,要消耗大量的液体化学品和超纯水;同时要消耗大量空气来抑制化学品蒸发,使之不扩散到洁净室;由于化学试剂的作用,加大了硅片的粗糙度[2] 。
(二)机械刷片法刷片方法被认为是去除化学机械抛光液残余物的方法之一。
微电子行业新型湿法清洗工艺分析
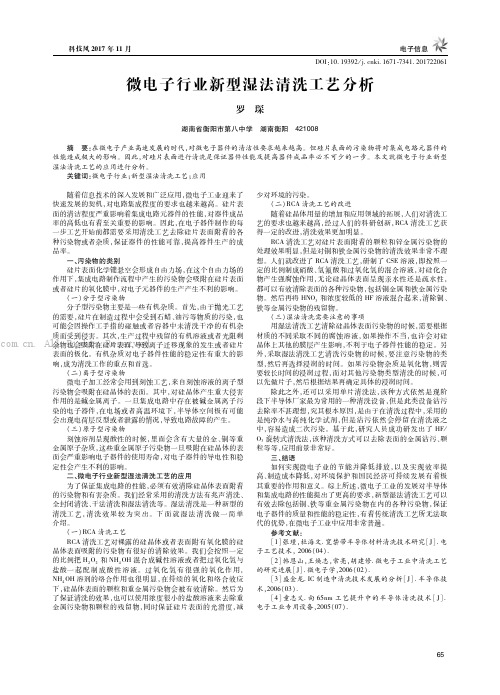
少对环境的污染 二 ^O;清洗工艺的改进 随着硅晶体用量的过人们的科研创新^O;清洗工艺获 得一定的改进清洗效果更加明显
^O;清洗工艺对硅片表面附着的颗粒和锌金属污染物的 处理效果明显但是对铜和铁金属污染物的清洗效果非常不理 想 人们就改进了 ^O;清洗工艺研制了 O<=溶液即按照一 定的比例制成硝酸氢氟酸和过氧化氢的混合溶液对硅化合 物产生强腐蚀作用无论硅晶体表面呈现亲水性还是疏水性 都可以有效清除表面的各种污染物包括铜金属和铁金属污染 物 然后再将 @A"( 和浓度较低的 @N溶液混合起来清除铜 铁等金属污染物的残留物
关键词微电子行业新型湿法清洗工艺应用
44随着信息技术的深入发展和广泛应用微电子工业迎来了 快速发展的契机对电路集成程度的要求也越来越高 硅片表 面的清洁程度严重影响着集成电路元器件的性能对器件成品 率的高低也有着至关重要的影响 因此在电子器件制作的每 一步工艺开始前都需要采用清洗工艺去除硅片表面附着的各 种污染物或者杂质保证器件的性能可靠提高器件生产的成 品率
一污染物的类别 硅片表面化学键悬空会形成自由力场在这个自由力场的 作用下集成电路制作流程中产生的污染物会吸附在硅片表面 或者硅片的氧化膜中对电子元器件的生产产生不利的影响 一 分子型污染物 分子型污染物主要是一些有机杂质 首先由于抛光工艺 的需要硅片在制造过程中会受到石蜡油污等物质的污染也 可能会因操作工手指的碰触或者容器中未清洗干净的有机杂 质而受到侵害 其次生产过程中残留的有机溶液或者光阻剩
三 湿法清洗需要注意的事项 用湿法清洗工艺清除硅晶体表面污染物的时候需要根据 材质的不同采取不同的腐蚀溶液如果操作不当也许会对硅 晶体上其他的膜层产生影响不利于电子器件性能的稳定 另 外采取湿法清洗工艺清洗污染物的时候要注意污染物的类 型然后再选择浸润的时间 如果污染物杂质是氧化物则需 要较长时间的浸润过程而对其他污染物类型清洗的时候可 以先做片子然后根据结果再确定具体的浸润时间 除此之外还可 以 采 用 单 片 清 洗 法 该 种 方 式 依 然 是 现 阶 段下半导体厂家最为常用的一种清洗设备但是此类设备沾污 去除率不甚理想究其根本原因是由于在清洗过程中采用的 是纯净水与高纯化学试剂但是沾污依然会停留在清洗液之 中容易造成二次污染 基于此研究人员成功研发出了 @N* "( 旋转式清洗法该种清洗方式可以去除表面的金属沾污颗 粒等等应用前景非常好 三结语 如何实现微 电 子 业 的 节 能 并 降 低 排 放 以 及 实 现 效 率 提 高制造成本降低对环境保护和国民经济可持续发展有着极 其重要的作用和意义 综上所述微电子工业的发展对半导体 和集成电路的性能提出了更高的要求新型湿法清洗工艺可以 有效去除包括铜铁等重金属污染物在内的各种污染物保证 电子器件的质量和性能的稳定性有着传统清洗工艺所无法取 代的优势在微电子工业中应用非常普遍 参考文献 $ 张瑾杜海文&宽禁带半导体材料清洗技术研究 5 &电 子工艺技术 )%%0%3 & ) 韩恩山王焕志常亮胡建修&微电子工业中清洗工艺 的研究进展 5 &微电子学)%%0%) & ( 盛金龙&#O制造中清洗技术发展的分析 5 &半导体技 术)%%0%( & 3 童志义&向 06-7工艺提升中的半导体清洗技术 5 & 电子工业专用设备)%%6%1 &
微波组件半水清洗工艺研究

微波组件半水清洗工艺研究目前,微波组件半水清洗工艺已经成为微波领域关键技术之一,它具有高效、易操作和对环境友好等优点。
针对微波组件半水清洗工艺,本文将从清洗原理、工艺流程和应用实例等方面进行探讨。
清洗原理是微波组件半水清洗工艺研究的重点之一、微波清洗技术是指利用微波对待清洗物体进行加热、振荡和湿润等效应,从而达到较好的清洗效果。
微波加热能量可以直接作用于待清洗物体内部,使其迅速升温,产生蒸汽压力,从而破坏待清洗物体表面的污垢结构。
微波振荡能够有效地激发待清洗物体中的分子振动,使其分解并与水分子形成络合物,进一步提高清洗效果。
微波湿润作用则是通过微波场作用下的介质极化现象,改变物体表面和内部的物理化学性质,使其更易于被清洗剂吸附和溶解。
工艺流程是微波组件半水清洗工艺研究的另一重要内容。
下面是一般微波组件半水清洗工艺的流程:1.待清洗微波组件的准备:包括微波组件的拆解、检查和清洗前处理。
2.清洗剂的选择:根据待清洗物体的特性和清洗要求选择合适的清洗剂。
一般情况下,清洗剂应具有良好的渗透性、去污性和稳定性。
3.清洗剂的配制:根据清洗剂的使用说明,按照一定的比例和方法将清洗剂稀释或激活。
4.清洗时间和温度的控制:根据待清洗物体的大小和污染程度,调整清洗时间和温度,确保清洗效果。
5.微波组件的清洗:将待清洗物体放入清洗设备,开启微波能源,进行清洗。
根据需要,可以采用连续清洗或间歇清洗方式。
6.清洗后处理:清洗完毕后,对微波组件进行水洗、干燥和质量检查等处理。
7.效果评估和记录:对清洗效果进行评估和记录,为后续的工艺改进提供依据。
微波组件半水清洗工艺在微波领域具有广泛的应用前景。
一方面,微波组件半水清洗工艺可以高效地清除微波组件表面和内部的污染物,提高微波器件的性能和可靠性。
另一方面,微波组件半水清洗工艺对环境友好,减少了传统清洗工艺中所需的有机溶剂和酸碱等化学物品的使用,降低了对环境的污染。
综上所述,微波组件半水清洗工艺是一种高效、易操作和环境友好的清洗技术。
IC制造中清洗技术发展的分析

IC制造中清洗技术发展的分析传统清洗技术的主要使用酸、碱、双氧水、甲苯、三氯乙烯、氟利昂等化学试剂,成本高,而且有毒,有腐蚀性,危害安全与健康并污染环境,特别是氟利昂等ODS物质研究破坏地球臭氧层,危及人类生态环境,是国际上限期禁止生产和使用的物质。
多年来,国内外科学家就致力于研究无毒、无腐蚀性的清洗工艺,但尚未取得突破。
随着芯片尺寸加大,工艺线宽减小,从90nm工艺开始,以往在清洗过程中使用的超声波清洗遇到一些问题,如造成半导体器件结构损伤,在65nm及以下工艺,其损伤程度可能会加剧,芯片中的深沟槽结构清洗时清洗液和漂洗去离子水很难进入结构内部,难以达到清洗目的,高堆叠式和深沟槽式结构清洗后的干燥过程也是很关键的技术问题,一般小于130nm工艺中,要求必须去除所有大于或等于100nm的颗粒,而由于表面边界层的限制,现行清洗技术,如液体或高压(液体)喷射清洗无法洗去100nm的颗粒,还有如何在后段有效地去除光刻胶,同时保证不腐蚀铜导线和不改变低k电介质的介电常数都是当前清洗技术面临的问题。
1 现代清洗技术中的关键要求在未来90-65nm节点技术工艺中,除了要考虑清洗后硅片表面的为粗糙度及自然氧化物清除率等技术指标外,也要考虑对环境的污染,清洗的率以及经济效益等。
硅片清洗技术评价的主要指标可以归纳为:微粗糙度(RMS)、自然氧化物清除率、金属沾污、表面颗粒度以及有机物沾污,其他指标还包括:芯片的破损率,清洗中的再沾污,对环境的污染,经济的可接受性(包括设备与运行成本、清洗效率)等。
金属沾污在硅片上是以范德华引力、共价键以及电子转移等3种表面形式存在的。
这种沾污会破坏薄氧化层的完整性,增加漏电流密度,影响MOS器件的稳定性,重金属离子会增加暗电流,情况为结构缺陷或雾状缺陷。
表面颗粒度会引起图形缺陷、外延前线、影响布线的完整性以及键合强度和表面质量。
颗粒的去除与静电排斥作用有关,所以硅片表面呈正电时,容易降低颗粒去除效率,甚至出现再沉淀。
微电子工艺中的清洗技术现状与展望论文

微电子工艺中的清洗技术现状与展望论文随着社会主义经济制度改革进程不断推进,我国市场经济程度越来越高,在这一时代背景下,微电子工艺的研究就被众多行业的企业家们提上了战略的日程。
但是,由于微电子技术的产物具有质量轻、体积小、与其他部件切合紧密等特征,从而致使对微电子的清洗工作越来越复杂。
微电子是科技产品的必备组成部分,其清洁度将直接影响到产品的散热功能、使用性能。
因此,对于微电子清洗技术的研究就变得愈发重要。
1微电子工艺清洗技术的理论研究在微电子元器件的制造过程当中,由于其体积小、制造过程复杂等众多客观原因存在,将会很有可能导致微电子元器件在其步骤繁琐的制造过程当中受到污染。
这些污染物质通常会物理吸附或者是化学吸附等多种方式在电子元器件生产过程当中吸附在其表面。
比如说,硅胶材质的硅片在其制造过程中污染物质通常会以离子或者是以粒子形式吸附在硅片的表面。
这些污染物质还有可能存在于硅片自身的氧化膜当中。
产生这一现象的原因并不奇怪,这是由于这些污染物质破坏掉了硅片表面的化学键,从而导致了在其表面形成了自然的力场,让众多污染物质轻松吸附或者直接进入到硅片的氧化膜当中。
在产生这种现象之后,要清洗硅片就非常困难了。
在清洗过程中,既要保持不能去破坏硅片的结构,又要保持能够对污染物质进行彻底的清洗,以便其对产品结构当中的其他元器件产生污染,这一问题就变得非常棘手,愈发困难了。
在当前微电子行业的大多企业或是研究所讲微电子的清洗技术两类:一种叫做湿法清洗;另一种叫做干法清洗。
这两种技术都能够保持比较高的清洗度,并且能够在不破坏电子元器件的化学键的基础上祛除电子元器件表面或是氧化膜内存在的污染物和杂质。
2微电子工艺清洗技术的现状研究由于我国行业的发展更重视对服务业的发展和我国微电子行业的起步和发展较晚,从而致使当前我国微电子工艺的清洗技术比较落后,并且存在诸多的问题。
2.1湿法清洗技术研究湿法清洗这一技术,是由上个世纪六十年代的一名美国科学家所研究发明出来的。
微电子工业中清洗工艺的研究进展
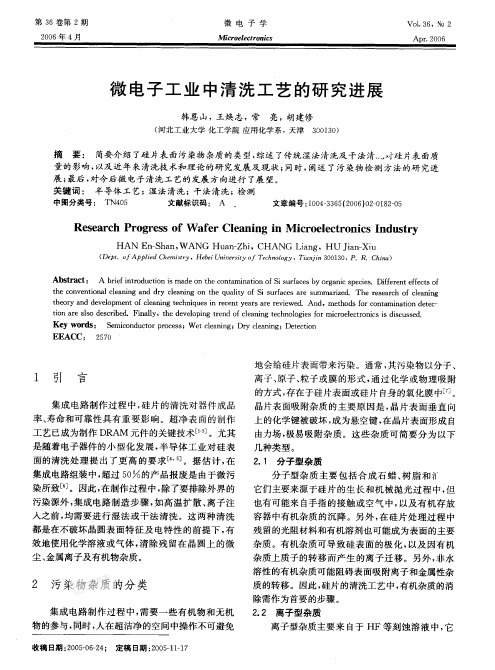
EEACC: 2 57 0
1引 言
集成 电 路 制作过程中,硅片的清洗对器件成品 率、寿命和可靠性具有重要影响。超净表面的制作 工艺已成为制作DRAM元件的关键技术〔1-3]。尤其 是随着电子器件的小型化发展,半导体工业对硅表
尘 、金属离子及有机物杂质 。
2 污染物杂质的分类
集成 电 路 制作过程中,需要一些有机物和无机 物的参与,同时,人在超洁净的空间中操作不可避免
地会给硅片表面带来污染 。通常,其污染物以分子、 离子 、原子、粒子或膜 的形式 ,通过化学或物理吸附 的方式,存在于硅片表面或硅片自身的氧化膜中川。 晶片表面吸附杂质的主要原因是 ,晶片表面垂直向 上的化学键被破坏,成为悬空键,在晶片表面形成 自 由力场 ,极易吸附杂质。这些杂质可简要分为以下 几种类型 。 2.1 分子型杂质
同时 , 在 制备 RCA清洗溶液时,若采用超纯水 代替一般溶剂,对沽污物的去除也会收到良好的效
果[13]。
3.1.2 RCA清洗的改进 随着 以 半 导体产品为特征的电子工业的飞速发
展 ,以计算机、通讯设备为代表的电子产品不断更新 换代 ,朝着高性能微型化方 向发展 ;同时,对沾污的 控制和更好的清洗工艺的研究也形成了一个非常活 跃的研究领域 ,并产生了大量的成果 。
199 ห้องสมุดไป่ตู้年 , 河北工业大学开发出控制吸附粒子在
晶片表面吸附状态 的技术 ,该技术很有推广应用价 值 。它主要是使表面吸附长期处于易清洗的物理吸 附状态,把抛光后的晶片置于 FA/0清洗液中,表 面活性剂分子在固液界面上吸附,形成一层易清洗 的保护膜 ;并利用活性剂的强渗透性 ,将表面吸附的 颗粒托起取而代之 ;这些脱附后 的颗粒又被表面活 性剂分子包围,形成胶束 ,防止脱附后的颗粒重新被
微电子封装中等离子体清洗及其应用2

封 装 测 试1 引言微电子工业中的清洗是一个很广的概念,包括任何与去除污染物有关的工艺。
通常是指在不破坏材料表面特性及电特性的前提下,有效地清除残留在材料上的微尘、金属离子及有机物杂质。
目前已广泛应用的物理化学清洗方法,大致可分为两类:湿法清洗和干法清洗。
湿法清洗在现阶段的微电子清洗工艺中还占据主导地位。
但是从对环境的影响、原材料的消耗及未来发展上看,干法清洗要明显优于湿法清洗。
干法清洗中发展较快、优势明显的是等离子体清洗,等离子体清洗已逐步在半导体制造、微电子封装、精密机械等行业开始普遍应用。
2 等离子体清洗2.1 等离子体清洗的机理等离子体是部分电离的气体,是物质常见的固体、液体、气态以外的第四态。
等离子体由电子、离子、自由基、光子以及其他中性粒子组成。
由于等离子体中的电子、离子和自由基等活聂磊 蔡坚 贾松良 王水弟微电子封装中等离子体清洗及其应用摘 要:随着微电子工艺的发展,湿法清洗越来越局限,而干法清洗能够避免湿法清洗带来的 环境污染,同时生产率也大大提高。
等离子体清洗在干法清洗中优势明显,本文主要 介绍了等离子体清洗的机理、类型、工艺特点以及在微电子封装工艺中的应用。
关键词:等离子体清洗;干法清洗;微电子封装性粒子的存在,其本身很容易与固体表面发生反应。
等离子体清洗的机理,主要是依靠等离子体中活性粒子的“活化作用”达到去除物体表面污渍的目的。
就反应机理来看,等离子体清洗通常包括以下过程:无机气体被激发为等离子态;气相物质被吸附在固体表面;被吸附基团与固体表面分子反应生成产物分子;产物分子解析形成气相;反应残余物脱离表面。
等离子体清洗技术的最大特点是不分处理对象的基材类型,均可进行处理,对金属、半导体、氧化物和大多数高分子材料,如聚丙烯、聚脂、聚酰亚胺、聚氯乙烷、环氧、甚至聚四氟乙烯等都能很好地处理,并可实现整体和局部以及复杂结构的清洗。
等离子体清洗还具有以下几个特点:容易采用数控技术,自动化程度高;具有高精度的控制装置,时间控制的精度很高;正确的等离子体清洗不会在表面产生损伤层,表面质量得到保证;由于是在真空中进行,不污染环境,保证清洗表面不被二次污染。
微电子工艺清洗技术的应用分析
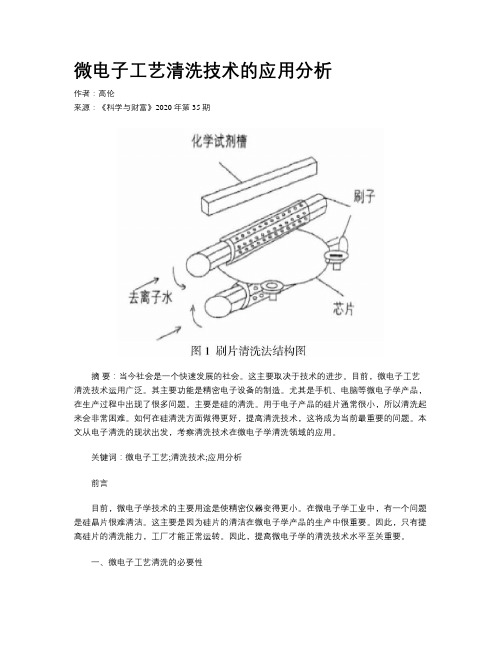
微电子工艺清洗技术的应用分析作者:高伦来源:《科学与财富》2020年第35期摘要:当今社会是一个快速发展的社会。
这主要取决于技术的进步。
目前,微电子工艺清洗技术运用广泛。
其主要功能是精密电子设备的制造。
尤其是手机、电脑等微电子学产品,在生产过程中出现了很多问题。
主要是硅的清洗。
用于电子产品的硅片通常很小,所以清洗起来会非常困难。
如何在硅清洗方面做得更好,提高清洗技术,这将成为当前最重要的问题。
本文从电子清洗的现状出发,考察清洗技术在微电子学清洗领域的应用。
关键词:微电子工艺;清洗技术;应用分析前言目前,微电子学技术的主要用途是使精密仪器变得更小。
在微电子学工业中,有一个问题是硅晶片很难清洁。
这主要是因为硅片的清洁在微电子学产品的生产中很重要。
因此,只有提高硅片的清洗能力,工厂才能正常运转。
因此,提高微电子学的清洗技术水平至关重要。
一、微电子工艺清洗的必要性微电子学技术的核心是硅芯片,而硅芯片是微电子学芯片的基本组成部分。
它的主要任务是执行任务和存储任务。
因此,在处理硅芯片时要非常细心。
更重要的是,许多公司收到的硅芯片都处于原始状态,这使得它们难以使用。
因为它不仅质量不均匀,而且有很多污点。
这些污垢严重影响了硅晶片的使用。
虽然硅片需要清洗,但这不是简单的用水清洗,需要复杂的清洗过程。
硅晶片是一种相对脆弱的电子元件,所以如果你简单地用水冲洗,它就有可能受到致命的伤害。
因此,需要一种特殊的方法来清除硅晶片上的污垢,这样硅晶片就可以被储存和使用。
如何清洁硅晶片一直是微电子学最棘手的问题。
硅晶片上有各种各样的污渍,所以我们不能用同样的方法来清洗。
因此,需要使用特殊的清洗方法。
二、污染物的类别1.分子型污染物分子污染物是硅表面最常见的污染物。
污染原因分为两部分,一部分原因是硅芯片需要被打磨和抛光,这样一来,一些有机物质就会留在芯片内部,还可能是硅芯片材料的一部分,一般来说,硅胶上存在污染物是不可避免的,在它被清除之前都会存在。
微电子工艺原理第讲清洗工艺

微电子工艺原理第讲清洗工艺清洗工艺是微电子制造过程中至关重要的一环,它对于器件性能和可靠性有着直接关系。
本文将从微电子工艺的角度介绍清洗工艺的原理、流程及影响因素。
清洗工艺的原理微电子器件的制造过程中,为了保证器件的品质,需要在每个制造步骤结束后进行清洗。
清洗的目的是除去沉积在表面的杂质、有机物及其他污染物,以便下一个制造步骤的顺利进行。
同时,清洗的质量还直接影响着器件性能和可靠性。
附着在表面的杂质可以降低器件的电学特性,影响其性能。
比如,杂质可能会影响制作金属电极的粘附性和导电性;有机物可以在高温和高压下分解并释放有害气体,导致器件失效。
通过对器件表面进行清洗,可以去除这些潜在的污染物,保证下一步的制造步骤可以在清洁的表面上进行,从而获得更好的器件性能。
清洗工艺的原理主要来源于化学和物理两方面。
化学清洗是通过合适的化学试剂去除表面的污染物,主要依靠化学反应来促进污染物的溶解和分离。
物理清洗则主要通过物理力学的方法,如振动、压缩和吸附等,去除表面的污染物。
清洗工艺的流程清洗工艺的流程主要包括前处理、主处理和后处理。
1.前处理在进行清洗之前,需要先将器件表面的半导体材料、金属材料或其他材料,进行表面预处理。
通常的处理方法包括:•去胶:使用某些有机物或者无机酸腐蚀去除器件表面的胶与封装材料,其中无机酸常见的有HF、KOH等。
•消毒:使用高温下的气体流去除器件表面的细菌以及器件内部的空气,以保证器件内外的干净。
•研磨:使用硅砂等磨料对器件表面进行研磨,以去除表面的氧化或锈蚀层。
在研磨过程中,还可以控制磨料的大小和硬度,以使磨料对表面不会产生附着物。
•水/氧化学气相清洗:使用去离子水或化学气相清洗器件表面,去除表面残留的杂质,以减少清洗过程中对器件的损伤。
2.主处理主处理是清洗工艺的核心步骤。
根据清洗方法的不同,主处理可以分为以下三个步骤:•预清洗:使用去离子水或去离子水混合有机溶剂对器件表面进行清洗,以去除表面的污染物,为下一步的清洗做准备。
MEMS_半导体和精密机械的超临界清洗技术
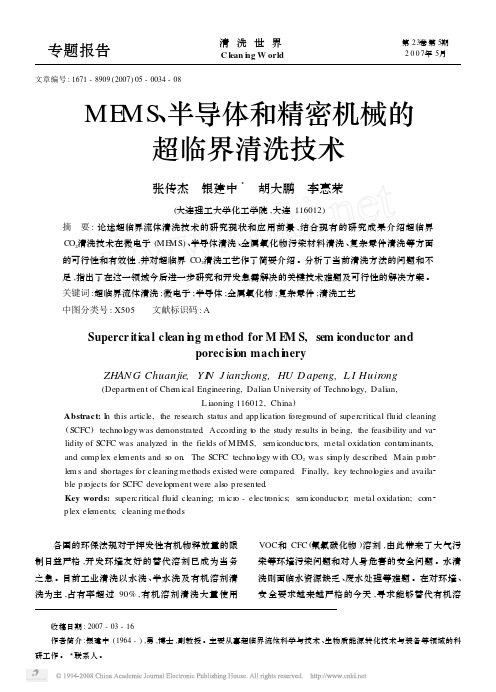
2. 3 环保问题 大量使用水和有机溶剂 ,造成了水资源的浪费
和环境的污染 。所以 ,在半导体清洗技术发展中 ,常
压下的传统商业湿式清洗法已面临发展的瓶颈 ;而 低压下干式电浆清洗法也遇到严峻的挑战 ;向高压 清洗发展是目前主要的方向之一 。超临界清洗技术 被视为最有潜力取代现有清洗方式的技术 。
2 超临界精密清洗在半导体行业中的 应用
随着半导体工业的进步 ,无论是集成电路还是
1 超临界 CO2清洗法简介
功效器件 ,都向着小尺寸方向发展 。以此来获取图 形密度的大幅度增加 ,尤其是随着超大规模集成电
早在 1977 年 , M affei[ 2 ] 就利用液态 CO2萃取的 方法清除衣物上的污迹 ;在 1991 年 , Jackson[ 3 ] 将超 临界 CO2清洗污物的方法称为“浓缩气体 ”清洗法和 干燥法 ,并且在清洗过程中使用了紫外线照射及超 声波振荡等辅助手段 ;到 1994年才真正出现超临界 流体清洗技术 ,而超临界精密清洗则是在大规模集 成电路等高新技术的发展基础上而发展起来的 。
图 2 超临界 CO2清洗光刻胶的过程
第 23卷
张传杰等 1M EM S、半导体和精密机械的超临界清洗技术
·37·
尽管超临界 CO2清洗技术已经运用到半导体清 洗业中 ,但是对于超临界 CO2去除光刻胶的机理尚 不是非常清楚 ,由于超临界 CO2为非极性且其本身 的低结合能量 ,对于构成光刻胶主要成分的高分子 的溶解度并不高 ,图 3 为 W illiam s[ 18 ]所推测的超临 界 CO2与高分子之间相互作用力图解 。
Abstract: In this article, the research status and app lication foreground of supercritical fluid cleaning ( SCFC) technology was demonstrated. According to the study results in being, the feasibility and va2 lidity of SCFC was analyzed in the fields of M EM S, sem iconductors, metal oxidation contam inants, and comp lex elem ents and so on. The SCFC techno logy w ith CO2 was simp ly described. M ain p rob2 lem s and shortages for cleaning m ethods existed were compared. Finally, key technologies and availa2 ble p rojects for SCFC development were also p resented. Key words: supercritical fluid cleaning; m icro - electronics; sem iconductor; metal oxidation; com2 p lex elements; cleaning m ethods
、清洗技术在IC制造的发展分析

1引言以集成电路为核心的电子信息产业已成为我国第一大产业,成为改造和拉动传统产业的强大引擎和技术基础。
当今世界经济竞争中,拥有自主知识产权的IC已成为经济发展的命脉、国际竞争的筹码和国家安全的保障。
集成电路制造过程中清洗硅片表面的污染和杂质是清洗的主要目的,在制造过程中,几乎每道工序都涉及到清洗,而且集成电路的集成度越高,制造工序越多,所需的清洗工序也越多[1]。
在诸多的清洗工序中,只要其中某一工序达不到要求,则将前功尽弃,导致整批芯片的报废,所以可以毫不夸张地说,没有有效的清洗技术,便没有集成电路和超大规模集成电路的今天。
传统清洗技术主要使用酸、碱、双氧水、甲苯、三氯乙烯、氟利昂等化学试剂,成本高,而且有毒,有腐蚀性,危害安全与健康并污染环境,特别是氟利昂等ODS物质研究破坏地球臭氧层,危及人类生态环境,是国际上限期禁止生产和使用的物质。
多年来,国内外科学家就致力于研究无毒,无腐蚀性的清洗工艺,但尚未取得突破。
随着芯片尺寸加大,工艺线宽减小,从90nm工艺开始,以往在清洗过程中使用的超声波清洗遇到一些问题,如造成半导体器件结构损伤,在65nm及以下工艺,其损伤程度可能会加剧。
芯片中的深沟槽结构清洗时清洗液和漂洗去离子水很难进入结构内部,难以达到清洗目的。
高堆叠式和深沟槽式结构清洗后的干燥过程也是很关键的技术问题。
一般小于130nm工艺中,要求必须去除所有大于或等于100nm的颗粒,而由于表面边界层的限制,现行清洗技术,如液体或高压(液体)喷射清洗已无法洗去100nm的颗粒。
还有如何在后段有效去除光刻胶,同时保证不腐蚀铜导线和不改变低k电介质的电介常数等都是当前清洗技术面临的问题。
2现代清洗技术中的关键要求在未来90~65nm节点技术工艺中,除了要考虑清洗后的硅片表面的微粗糙度及自然氧化物清除率等技术指标外,也要考虑对环境的污染以及清洗的效率其经济效益等。
硅片清洗技术评价的主要指标可以归纳为:(1)微粗糙度(RMS);(2)自然氧化物清除率;(3)金属沾污、表面颗粒度以及有机物沾污,其他指标还包括:(4)芯片的破损率;(5)清洗中的再沾污;(6)对环境的污染;(7)经济的可接受性(包括设备与运行成本、清洗效率)等。
微电子工艺清洗技术分析
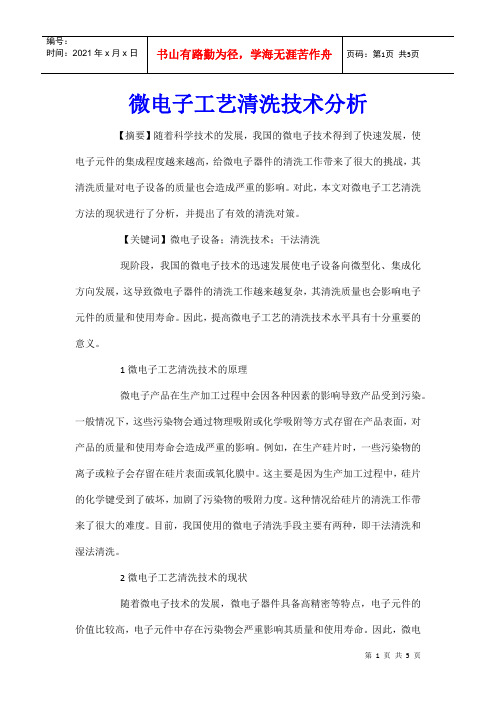
微电子工艺清洗技术分析【摘要】随着科学技术的发展,我国的微电子技术得到了快速发展,使电子元件的集成程度越来越高,给微电子器件的清洗工作带来了很大的挑战,其清洗质量对电子设备的质量也会造成严重的影响。
对此,本文对微电子工艺清洗方法的现状进行了分析,并提出了有效的清洗对策。
【关键词】微电子设备;清洗技术;干法清洗现阶段,我国的微电子技术的迅速发展使电子设备向微型化、集成化方向发展,这导致微电子器件的清洗工作越来越复杂,其清洗质量也会影响电子元件的质量和使用寿命。
因此,提高微电子工艺的清洗技术水平具有十分重要的意义。
1微电子工艺清洗技术的原理微电子产品在生产加工过程中会因各种因素的影响导致产品受到污染。
一般情况下,这些污染物会通过物理吸附或化学吸附等方式存留在产品表面,对产品的质量和使用寿命会造成严重的影响。
例如,在生产硅片时,一些污染物的离子或粒子会存留在硅片表面或氧化膜中。
这主要是因为生产加工过程中,硅片的化学键受到了破坏,加剧了污染物的吸附力度。
这种情况给硅片的清洗工作带来了很大的难度。
目前,我国使用的微电子清洗手段主要有两种,即干法清洗和湿法清洗。
2微电子工艺清洗技术的现状随着微电子技术的发展,微电子器件具备高精密等特点,电子元件的价值比较高,电子元件中存在污染物会严重影响其质量和使用寿命。
因此,微电子器件的清洗工作十分重要。
微电子工艺清洗法最早由美国发明并实施的,主要使用的是湿法,可利用有机溶剂或化学溶剂与污染物发生反应,并通过物理作用来达到清洗的目的,但部分化学溶剂会与电子元件发生反应,对电子元件造成损伤,因此,在清洗时要根据电子元件的材料来选择合适的溶剂。
另外,干法清洗方式与湿法清洗方式相对应,主要以等离子技术和气相技术为主,这种清洗方法不会对电子元件造成损伤,但清洗效果不如湿法清洗技术,一些金属氧化物无法清洗干净。
3微电子工艺清洗技术的应用3.1湿法清洗技术。
3.1.1化学溶剂清洗法。
微电子工艺中的清洗技术进展

108 集成电路应用 第 37 卷 第 6 期(总第 321 期)2020 年 6 月Applications创新应用 2 清洗工艺2.1 基本原理微电子元器件的制造工序是非常复杂的,过程中会受到污染,对产品质量会产生严重影响。
污染物一般会通过物理吸附或者化学吸附的方式在电子元件生产过程中吸附在表面。
以硅片制造为例,生产中污染物主要是以粒子或者离子的形式存在,吸附在硅片的表面。
通过研究发现,污染物还有可能存在于硅片自身的氧化膜当中,出现这种问题的原因是污染物质破坏了硅片表面的化学键,这样一来表面就会形成自然的力场,污染物质就很容易进入到硅片的氧化膜之中。
出现这种情况之后,清洗的难度就非常大,需要不断提升清洗技术,才能确保满足实际需求。
从现阶段情况来看,在微电子工艺行业中主要有两种清洗技术,实际应用效果比较好,可以有效清洗微电子产品中的污染物,保证产品的功能。
随着微电子产品的快速发展,对清洗技术会提出更高的要求,所以要不断加强研究,才能满足实际需求,为微电子工艺提供可靠的保障,不断提升产品质量。
相比较于西方发达国家,我国微电子行业起步比较晚,发展时间也比较短,所以微电子工艺清洗技术相对落后,在实际运用中存在一些问题,严重影响到使用效果。
0 引言随着社会快速发展,人们对微电子产品需求量持续增加,可以获得很好的体验。
微电子产品具有体积小、质量轻、集成度高的特点,所以清洗难度是比较大的,如果不进行有效清洗,肯定会影响到产品的正常使用。
所以要加强对清洗技术的研究,有效适应发展的需求,保证微电子产品的合格率。
1 微电子工艺中清洗技术在微电子工艺中,清洗技术一直是研究的重点,通过不断改进来满足发展的需求。
电子行业是追求精密的一个行业,小小的失误会对产品质量造成不利影响,所以要严格的去控制,才能确保达到生产标准。
微电子工艺中清洗技术的重要性主要体现在以下几个方面:(1)保证产品质量。
如果微电子产品中进入了污染物,肯定会影响到正常使用,所以要进行有效的清洗才可以,这是非常关键的。
半导体制造中清洗技术的研究新进展阐述

半导体制造中清洗技术的研究新进展阐述最近这几年来,电子技术得到了空前的发展。
随着市场经济中对于半导体器件与大量的集成电路的需求数量的不断增多,这也就要求了其性能性与可靠性的标准需要及时提升。
如何高效的将半导体器件表面清洁干净并达到相应的使用标准,已经成为了现阶段半导体制造过程中需要及时解决的问题。
在实际生产过程中我们可以清楚的发现,单单只是清洁了设备表面的污垢,并不能达到所要求的清洁标准。
为此,作者在文中主要对半导体制造中清洗技术的研究新进展进行阐述。
标签:半导体;清洗技术;进展长时间以来,人们都惯性使用多槽浸渍式RCA进行清洁半导体,随着清洁技术的不断创新变革,其多槽浸渍式清洁模式逐渐向单片式清洁进行转变,同时也衍生出了诸多可以取代多槽浸渍式RCA清洁方法的新技术。
为此,文章中将对现阶段半导体制造过程中所需的清洁技术进行深入探讨,并有效論述其清洁技术的未来发展方向等内容。
1 半导体清洗技术的发展史由于实际生产的需要,首部较为完备、且具备实用含义的硅表面清洁技术被人们正式提出。
在实际半导体制造过程中,通过对清洗技术的有效优化与相关设备的更新,集合诸多实验经验,逐渐构建一个相对比较完备且科学的清洗工艺。
这一技术对于提升产量、推动半导体良性发展具有不可取代的现实意义。
现有半导体制造过程中的清洗技术,随着不同发展时期对半导体性能要求的不同,不断进行更新换代。
早年间由于衬底晶圆中缺少密度支撑而进一步引发的微粒与金属物质间的污染问题,出现此问题的主要原因并不仅仅是因为其设备表面不清洁导致的。
随着清洗技术的不断革新,设备表面的微粒和金属污染也越来越少。
为此,人们在实际经济生产过程中,需要对现存的微粒和金属污染等问题及时予以重视[1]。
在实际清洗过程中,一般情况下,会采用简单便捷的清洗方法进行清洁设备表面上的污染物。
需要注意的是溶解在水与空气中的部分臭氧,在某种程度上会引发污染问题。
工作人员在进行实际清洁过程中,需要注意自我的清洁手法,并一边观察一边检验清洗质量,充分考虑到污染多样性的问题。
- 1、下载文档前请自行甄别文档内容的完整性,平台不提供额外的编辑、内容补充、找答案等附加服务。
- 2、"仅部分预览"的文档,不可在线预览部分如存在完整性等问题,可反馈申请退款(可完整预览的文档不适用该条件!)。
- 3、如文档侵犯您的权益,请联系客服反馈,我们会尽快为您处理(人工客服工作时间:9:00-18:30)。
微电子工业中清洗工艺的研究进展韩恩山,王焕志,常 亮,胡建修(河北工业大学化工学院应用化学系,天津 300130)摘 要: 简要介绍了硅片表面污染物杂质的类型,综述了传统湿法清洗及干法清洗对硅片表面质量的影响,以及近年来清洗技术和理论的研究发展及现状;同时,阐述了污染物检测方法的研究进展;最后,对今后微电子清洗工艺的发展方向进行了展望。
关键词: 半导体工艺;湿法清洗;干法清洗;检测中图分类号: TN405 文献标识码: A 文章编号:100423365(2006)022*******R esearch Progress of W afer Cleaning in Microelectronics IndustryHAN En2Shan,WAN G Huan2Zhi,C HAN G Liang,HU Jian2Xiu(Dept.of A p plied Chemist ry,Hebei Universit y of Technology,Tianj in300130,P.R.Chi na) Abstract: A brief introduction is made on the contamination of Si surfaces by organic species.Different effects of the conventional cleaning and dry cleaning on the quality of Si surfaces are summarized.The research of cleaning theory and development of cleaning techniques in recent years are reviewed.And,methods for contamination detec2 tion are also described.Finally,the developing trend of cleaning technologies for microelectronics is discussed.K ey w ords: Semiconductor process;Wet cleaning;Dry cleaning;DetectionEEACC: 25701 引 言集成电路制作过程中,硅片的清洗对器件成品率、寿命和可靠性具有重要影响。
超净表面的制作工艺已成为制作DRAM元件的关键技术[123]。
尤其是随着电子器件的小型化发展,半导体工业对硅表面的清洗处理提出了更高的要求[4,5]。
据估计,在集成电路组装中,超过50%的产品报废是由于微污染所致[6]。
因此,在制作过程中,除了要排除外界的污染源外,集成电路制造步骤,如高温扩散、离子注入之前,均需要进行湿法或干法清洗。
这两种清洗都是在不破坏晶圆表面特征及电特性的前提下,有效地使用化学溶液或气体,清除残留在晶圆上的微尘、金属离子及有机物杂质。
2 污染物杂质的分类集成电路制作过程中,需要一些有机物和无机物的参与,同时,人在超洁净的空间中操作不可避免地会给硅片表面带来污染。
通常,其污染物以分子、离子、原子、粒子或膜的形式,通过化学或物理吸附的方式,存在于硅片表面或硅片自身的氧化膜中[7]。
晶片表面吸附杂质的主要原因是,晶片表面垂直向上的化学键被破坏,成为悬空键,在晶片表面形成自由力场,极易吸附杂质。
这些杂质可简要分为以下几种类型。
2.1 分子型杂质分子型杂质主要包括合成石蜡、树脂和油污。
它们主要来源于硅片的生长和机械抛光过程中,但也有可能来自手指的接触或空气中,以及有机存放容器中有机杂质的沉降。
另外,在硅片处理过程中残留的光阻材料和有机溶剂也可能成为表面的主要杂质。
有机杂质可导致硅表面的极化,以及因有机杂质上质子的转移而产生的离子迁移。
另外,非水溶性的有机杂质可能阻碍表面吸附离子和金属性杂质的转移。
因此,硅片的清洗工艺中,有机杂质的消除需作为首要的步骤。
2.2 离子型杂质离子型杂质主要来自于HF等刻蚀溶液中,它第36卷第2期2006年4月微电子学Microelect ronicsVol136,№2Apr12006收稿日期:2005206224; 定稿日期:2005211217们甚至可能来自于去离子水的清洗过程中。
离子型杂质以化学或物理吸附的方式沉积在硅片上。
在所有的离子型杂质中,碱金属离子的害处最大。
它们可能在电场或温度升高的过程中移动,并可能导致半导体空间电荷层的反型、表面的泄漏,以及在器件的运行中移动。
2.3 原子型杂质原子型杂质主要指重金属原子(如金、银、铜等),它们主要来自硅的酸性刻蚀剂中。
原子型杂质主要影响器件中少子的寿命、表面导电性以及其它影响器件稳定性的参数。
去除原子型杂质的溶剂要求能溶解金属,或者能和金属络合,并防止金属的二次沉降。
3 目前清洗工艺的现状及发展趋势在集成电路工艺中,有多达30%的步骤为晶片清洗工序[8]。
不同的工艺技术所要求的硅片最终表面状态不同,其使用的清洗方法也不相同。
1970年代后期,对兆声清洗进行了讨论;1980年代后期,采用了全封闭清洗和干法清洗技术。
到了1990年代,对各种清洗方法进行改进,并将各种清洗方法综合使用,化学试剂和气体的纯度大大改善,为化学清洗新技术提供了可能。
到目前为止,清洗已经不再是一个单一的步骤,而是一个系统工程。
3.1 湿法清洗3.1.1 RCA清洗1970年,由Kern和Puotinen[9]首创的RCA工艺目前仍是对裸露或附有氧化膜的硅表面清洗工艺的基础[10,11]。
原始的RCA清洗工艺在清洗过程中会蚀去3.0~4.0nm的硅基体。
它主要基于两种以过氧化氢为主溶液,即与N H4O H混合的碱性混合液,和后来发展的与盐酸混合的酸性混合液。
第一种处理液是由体积比为(1∶1∶1.5)~(1∶2∶7)的N H4O H(27%)、H2O2(30%)和H2O组成的热溶液。
这就是众所周知的SC21清洗液。
SC21溶液的目的是通过N H4O H的溶剂化作用和过氧化物的氧化作用,去除有机沾污物。
由于H2O2的氧化作用,硅表面会形成氧化物,这种氧化物在溶液中会缓慢溶解。
当颗粒下面发生持续的氧化和氧化物的侵蚀时,对颗粒的去除非常有效。
诸如金、银、铜、镍、镉、锌、钴和铬等表面金属沾污物,也可以通过H2O2的氧化和N H4O H的络合效应溶解来去除。
比如,铜可以形成Cu(N H3)42+络合物。
若SC21清洗后再用很稀的酸(HCl∶H2O为1∶104)处理,则在去除金属杂质和颗粒上会收到良好的效果[12]。
在SC21溶液中清洗后,也可以用稀释的H F溶液短时间浸渍,以去除在SC21形成的水合氧化物膜。
最后,这一清洗溶液常常用只有原始溶液浓度1/10的稀释溶液,以避免表面粗糙,降低产品成本,以及减少对环境的影响。
第二种处理步骤则是将淋洗后的晶片置入SC2 2溶液中。
这种溶液是由体积比为(1∶1∶6)~(2∶1∶8)的H2O2(30%)、HCl(37%)和水组成的热混合溶液。
这种清洗同样是用以去除碱性离子和那些在碱性溶液中会形成不溶于N H4O H的氢氧化物的阳离子,如Al3+、Fe3+、Mg2+等。
它还可以清除在SC21中没有完全去除的金属沾污物(比如金),还可以通过与离子作用,形成可溶性的络合物组织,与表面发生置换沉积。
对含有可见残渣的严重沾污的晶片,可用热H2SO42H2O(2∶1)混合物进行预清洗。
同时,在制备RCA清洗溶液时,若采用超纯水代替一般溶剂,对沾污物的去除也会收到良好的效果[13]。
3.1.2 RCA清洗的改进随着以半导体产品为特征的电子工业的飞速发展,以计算机、通讯设备为代表的电子产品不断更新换代,朝着高性能微型化方向发展;同时,对沾污的控制和更好的清洗工艺的研究也形成了一个非常活跃的研究领域,并产生了大量的成果。
1995年,Park,T.H.等人[14]研制的CSE (HNO32HF2H2O2)溶液与SE(HNO32H F2H2O)相比,工艺过程更容易控制,且无论对亲水性或疏水性表面,去除金属沾污Fe、Cu的效果都较好。
实验结果表明,经RCA清洗后,硅晶片表面的颗粒和锌浓度急剧减少,而铜和铁的浓度仍基本不变[13]。
用SC21溶液很难将表面重金属(比如铁)减小到低于1011/cm2。
而调整后的溶液则可将Fe、Cu、Ni的浓度降低到1010/cm2[15]以下。
稀释HNO32F2H2O2在去除表面金属,如Zn、Ca、Ni和Al时,比RCA更有效。
经RCA清洗后,再用HNO3和稀释H F的混合液处理,可显著降低Fe、Ca、Mg的表面浓度,其间大约浸蚀去30nm的硅[16]。
1996年,Cady和Vardarajan[17]提出了采用四甲基氢氧化氨[N(C H3)4O H]与羧酸盐缓冲剂配置的碱性水溶液喷雾清洗法。
结果表明,温度是影响其清洗效果的主要因素,其中,温度/时间和温度/流速之间的比值是最为重要的。
1997年,J eon和Raghavan[18,19]提出了利用兆声波激发臭氧水对硅片进行清洗。
兆声使含有O3的水分解产生O H-、O3和H2O2,随着时间的变化, H2O2很快就分解了,而O3含量随兆声开始时直线下降,到0.5pp m时保持恒定15min,从而可持续产生O H-和H+,以有效地去除硅片表面的有机物。
同时,有报道称,表面用臭氧化水和过氧化物清洗去除颗粒和金属时,可得到清洁的表面,表面Cu 的浓度可低于108/cm2[2]。
1998年,Bakker[20]等人提出了用水和水/CO2混合溶液在高温、高压下的清洗。
通过XPS,检测到此种方法可将污染物碳氢化合物与聚合物薄膜同时除去,可与RCA方法媲美。
2001年,洛斯阿拉莫斯国家实验室(Lo s Ala2 mo s Natio nal Laboratory)一项新型光阻材料去除工艺的研究员Craig Taylor等人,开发了一种超临界二氧化碳光阻材料去除工艺(SCORR,Supercriti2 cal CO2Resist Remover)技术。
在该技术中,引入了一种亲环境工艺,利用超临界二氧化碳和少量相对无害的助溶剂混合(通常5%或更少),以去除光阻材料及其它残留物质。
1995年,山东大学光电材料与器件研究所研制成功含表面活性剂的新型半导体清洗剂和与之配套的新型DZ系列清洗工艺[21]。
2002年,在DZ系列清洗剂的基础上,又推出了含表面活性剂和螯合剂的新型电子清洗剂D GQ21和D GQ22。
它符合超大规模集成电路的清洗要求,在去除有机物和金属杂质离子方面,相当于标准RAC清洗工艺[22]。
1999年,河北工业大学开发出控制吸附粒子在晶片表面吸附状态的技术,该技术很有推广应用价值。