热冲成型技术
浅谈热冲压成形技术
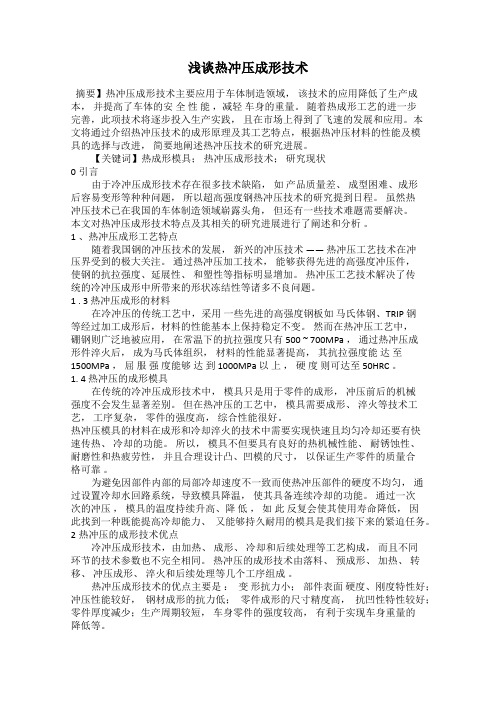
浅谈热冲压成形技术摘要】热冲压成形技术主要应用于车体制造领域,该技术的应用降低了生产成本,并提高了车体的安全性能,减轻车身的重量。
随着热成形工艺的进一步完善,此项技术将逐步投入生产实践,且在市场上得到了飞速的发展和应用。
本文将通过介绍热冲压技术的成形原理及其工艺特点,根据热冲压材料的性能及模具的选择与改进,简要地阐述热冲压技术的研究进展。
【关键词】热成形模具;热冲压成形技术;研究现状0引言由于冷冲压成形技术存在很多技术缺陷,如产品质量差、成型困难、成形后容易变形等种种问题,所以超高强度钢热冲压技术的研究提到日程。
虽然热冲压技术已在我国的车体制造领域崭露头角,但还有一些技术难题需要解决。
本文对热冲压成形技术特点及其相关的研究进展进行了阐述和分析。
1 、热冲压成形工艺特点随着我国钢的冲压技术的发展,新兴的冲压技术——热冲压工艺技术在冲压界受到的极大关注。
通过热冲压加工技术,能够获得先进的高强度冲压件,使钢的抗拉强度、延展性、和塑性等指标明显增加。
热冲压工艺技术解决了传统的冷冲压成形中所带来的形状冻结性等诸多不良问题。
1 . 3 热冲压成形的材料在冷冲压的传统工艺中,采用一些先进的高强度钢板如马氏体钢、TRIP 钢等经过加工成形后,材料的性能基本上保持稳定不变。
然而在热冲压工艺中,硼钢则广泛地被应用,在常温下的抗拉强度只有 500 ~ 700MPa ,通过热冲压成形件淬火后,成为马氏体组织,材料的性能显著提高,其抗拉强度能达至1500MPa ,屈服强度能够达到 1000MPa 以上,硬度则可达至 50HRC 。
1. 4 热冲压的成形模具在传统的冷冲压成形技术中,模具只是用于零件的成形,冲压前后的机械强度不会发生显著差别。
但在热冲压的工艺中,模具需要成形、淬火等技术工艺,工序复杂,零件的强度高,综合性能很好。
热冲压模具的材料在成形和冷却淬火的技术中需要实现快速且均匀冷却还要有快速传热、冷却的功能。
所以,模具不但要具有良好的热机械性能、耐锈蚀性、耐磨性和热疲劳性,并且合理设计凸、凹模的尺寸,以保证生产零件的质量合格可靠。
热冲压成形技术
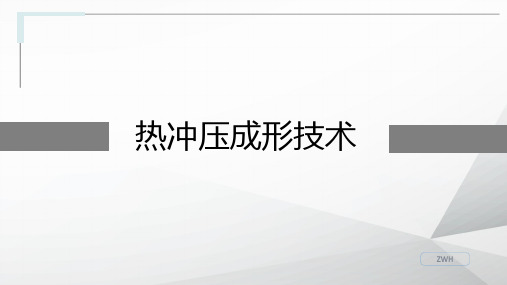
热冲压成型工艺
有镀层钢板
坯料被加热后,直接送至闭式模具内进行冲压成形和淬火,然后进行冷却、切边冲孔(或激 光切割)、表面清理等后续工艺
热冲压成型设备和模具
主要包括开卷机、冲裁压力机(激光下料机)、板料送进装置、加热炉、上料装置、压力机、 模具、下料装置、激光切边器和喷沙装置等。其中关键设备主要包括液压机、加热炉及热冲压 模具等。
硬度: HV10/HV30须在400~520之间。
金相组织: 板条状马氏体,总脱碳层深度不得超过0.1mm。
尺寸精度: 满足汽车厂规定的切边精度和装配精度要求。
碰撞试验: 不允许产生碰撞开裂。
车路试: 满足规定的疲劳强度。
可提供热成形钢的公司
宝钢可供规格
热冲压成形的优势有哪些
实现车身轻量化的有效途径
有效提高零件的表面硬度及其耐 磨性 增加高强板使用率,提高车型的 碰撞性能
车身加强板数量减少,车身开发 设计难度降低。
改善高强板的零件成形性,降低 压机吨位要求
降低车身开发成本
热冲压成形零件分布
热成型工艺
热冲压的关键工艺过程是加热、冲压、保压和冷却。加热过程直接影响到高强度钢板的冲压性 能,冲压过程中伴随的淬火则对零件强度的硬化起到决定性的作用。
加热炉பைடு நூலகம்
多层箱式炉 这类炉子灵活、节能、使用方便、占地面积小,但对炉门的开 闭机构和工件传输的自动化水平要求较高,适合于多品种、小 批量生产。对某些零件,在工艺和设备调试稳定的条件下,也 可以大批量生产。
辊道式炉子 这类炉子投资大,占地面积大,如生产铝硅镀层板,高温状态下 辊子粘附镀层的可能性较大,影响辊子的寿命,工件的粘附会导 致工件在炉子中跑偏。炉子适合于裸板大批量生产,是否适合于 镀锌板也有待试验。工件在这类炉子上传输比较简单,自动化部 分投资小,工件出炉到压机的传输时间短,冲压成形温度容易控 制。
热冲压成型工艺流程 预热处理 冲压成形

热冲压成型工艺流程预热处理冲压成形
热冲压成型工艺流程主要包括以下步骤:
1. 预热处理:首先,将需要加工的钢板进行预热处理。
预热温度通常控制在800℃\~950℃之间,以保证钢板的均匀加热和塑性变形。
同时,为了防止钢板在加热过程中氧化,需要采用保护气体或真空加热方式。
2. 冲压成形:将预热的钢板放入冲压模具中,通过冲压机施加压力进行成型。
冲压过程中需控制好压力、速度和时间等参数,以保证钢板的塑性变形和模具的完好无损。
同时,为了确保成品的精度和质量,需要对冲压过程中的压力、速度和时间等参数进行实时监控和调整。
在热冲压成形过程中,钢板在加热和冷却的过程中会发生相变硬化,从而提高其强度和韧性。
这种技术也被称为“冲压硬化”技术。
经过热冲压成形后的钢板,其强度可以大幅提高,例如从初始的500\~600MPa提高到1500MPa,同时零件的硬度也可以达到50HRC。
但需要注意的是,热冲压成形后的钢板伸长率会有所下降。
此外,完成冲压加工后,还需要对板材进行回火处理,以消除加工过程中的残余应力,并提高板材的韧性和可塑性。
最后,还需要对成型件进行后处理,包括去毛刺、打磨、修整等操作,以及可能的涂装或喷涂处理,以确保成品的表面质量和尺寸精度符合要求。
总的来说,热冲压成型工艺流程是一个复杂而精细的过程,需要严格控制各个环节的参数和操作,以保证最终产品的质量和性能。
热冲压原理

热冲压原理热冲压是一种利用热变形原理进行成形的工艺方法,它是将金属材料加热到一定温度后进行成形的过程。
在这个过程中,金属材料会发生热变形,从而达到所需的成形效果。
下面将详细介绍热冲压的原理。
一、热冲压的基本原理1.1 热变形原理热变形是指在高温下,材料因受到应力而发生塑性变形的现象。
在高温下,金属材料的晶粒会发生较大的位错活动和扩散现象,从而使其塑性增强。
这种增强效应可以使金属材料在受到应力时更容易发生塑性变形。
1.2 热冲压工艺流程热冲压工艺流程包括:原材料切割、预加工、加热、成形和后处理等环节。
其中,加热环节是整个过程中最为关键的环节之一。
通过加热可以使金属材料达到足够高的温度,从而使其发生塑性变形。
二、热冲压的主要特点2.1 成形精度高由于热冲压工艺采用的是加热后成形的方式,因此可以使金属材料发生较大的塑性变形,从而达到较高的成形精度。
2.2 成形效率高相比于传统的冷冲压工艺,热冲压工艺具有更高的成形效率。
这是因为在加热后,金属材料更容易发生塑性变形,从而可以在较短的时间内完成成形过程。
2.3 适用范围广热冲压工艺适用于各种不同类型的金属材料。
例如铝、镁、钛等轻合金材料以及不锈钢、铜、铁等常规金属材料都可以采用热冲压工艺进行成形。
三、热冲压的应用领域3.1 汽车制造业汽车制造业是热冲压应用最广泛的领域之一。
在汽车制造中,许多零部件都需要采用热冲压工艺进行成形。
例如车身件、底盘件、发动机件等。
3.2 电子制造业在电子制造业中,热冲压工艺也得到了广泛的应用。
例如手机、电视、电脑等电子产品中的金属外壳、散热片等部件都可以采用热冲压工艺进行成形。
3.3 航空航天制造业在航空航天制造业中,热冲压工艺也是一种重要的成形方法。
例如飞机发动机叶片、涡轮盘等部件都需要采用热冲压工艺进行成形。
四、总结综上所述,热冲压是一种利用热变形原理进行成形的工艺方法。
它具有成形精度高、成形效率高和适用范围广等优点,在汽车制造、电子制造和航空航天制造等领域都得到了广泛应用。
热冲压成形的高强度钢—硼钢技术应用发展
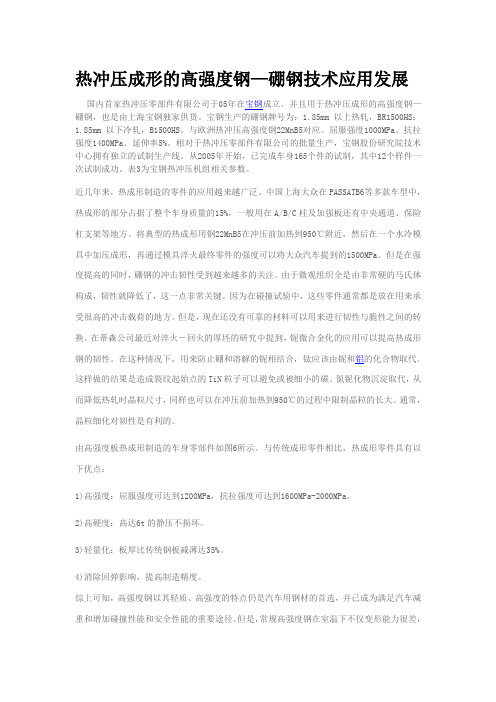
热冲压成形的高强度钢—硼钢技术应用发展国内首家热冲压零部件有限公司于05年在宝钢成立。
并且用于热冲压成形的高强度钢—硼钢,也是由上海宝钢独家供货。
宝钢生产的硼钢牌号为:1.85mm以上热轧,BR1500HS;1.85mm以下冷轧,B1500HS。
与欧洲热冲压高强度钢22MnB5对应。
屈服强度1000MPa、抗拉强度1400MPa、延伸率5%。
相对于热冲压零部件有限公司的批量生产,宝钢股份研究院技术中心拥有独立的试制生产线。
从2005年开始,已完成车身165个件的试制,其中12个样件一次试制成功。
表3为宝钢热冲压机组相关参数。
近几年来,热成形制造的零件的应用越来越广泛。
中国上海大众在PASSATB6等多款车型中,热成形的部分占据了整个车身质量的15%,一般用在A/B/C柱及加强板还有中央通道、保险杠支架等地方。
将典型的热成形用钢22MnB5在冲压前加热到950℃附近,然后在一个水冷模具中加压成形,再通过模具淬火最终零件的强度可以将大众汽车提到的1500MPa。
但是在强度提高的同时,硼钢的冲击韧性受到越来越多的关注。
由于微观组织全是由非常硬的马氏体构成,韧性就降低了,这一点非常关键。
因为在碰撞试验中,这些零件通常都是放在用来承受很高的冲击载荷的地方。
但是,现在还没有可靠的材料可以用来进行韧性与脆性之间的转换。
在蒂森公司最近对淬火-回火的厚坯的研究中提到,铌微合金化的应用可以提高热成形钢的韧性。
在这种情况下,用来防止硼和溶解的铌相结合,钛应该由铌和铝的化合物取代。
这样做的结果是造成裂纹起始点的TiN粒子可以避免或被细小的碳、氮铌化物沉淀取代,从而降低热轧时晶粒尺寸,同样也可以在冲压前加热到950℃的过程中限制晶粒的长大。
通常,晶粒细化对韧性是有利的。
由高强度板热成形制造的车身零部件如图6所示。
与传统成形零件相比,热成形零件具有以下优点:1)高强度:屈服强度可达到1200MPa,抗拉强度可达到1600MPa-2000MPa。
热冲压成形技术

发展前景
作为一种有效的经济的能源措施,轻巧的汽车发展方 向,已成为汽车行业最重要的研究课题之一。实现汽车 轻量化的主要途径有三个:一、优化汽车框架和结构, 使车辆的车身或者车架的结构更加轻便;二、新的替代 材料,降低整车质量(高和超高强度钢,可作为替代材 料,因为它的厚度更薄,);三、汽车轻量化,如厚度 梯度高强度钢(HSS)或金属系化合物板通过连续冲压 或热冲压成形技术改变性能。HSS已经应用在国内一些 高档车,关键生产技术一直占主导地位的外国公司,如 Acelor公司,从而显着提高了产品成本。由国内自行设 计的热压成型技术和水冷却模具,汽车HSS可以生产替 代国外汽车零部件。
实验验证:
1、实验装置
2、结果与讨论 3、结论
1、实验装置:
为了在高温下形成高速钢,以避免裂纹和 回弹,样品需要快速加热和完全变换成稳 定的奥氏体组织。然后,样品被压在自制 的水冷却模具中冷却,对于得到的HSS样本, 其形状冻结字符或没有回弹缺陷是一个明 显的优点,并且大部分样品中的显微组织 为马氏体。样品的厚度是1.6毫米,在HSS 这个实验中的主要元素,示于表1。
在一般情况下,随着钢质坯件的机械强度的增强,其可 塑性急剧恶化。这使很难适用于传统的冷冲压技术进入该 领域取代HSS,同时填补了马氏体钢应用空白。而热冲压 技术作为一项新技术,它结合了金属热塑性成型法和水冷 却模具淬火原则,在形成硼钢空白和水冷却模具骤冷的过 程期间同时烫印。相对于原汽车珠光体钢,汽车HSS通过 先进的热压成形技术可以减少车辆的总质量的30%左右, 实现复杂的几何形状,高安全性和机械强度。其原因是最 佳的塑性和延展性的奥氏体显微组织可以通过高温下热压 成形方式获得,同时形成后骤冷的条件将得到具有优异机 械性能、重量轻的HSS 。为实现车辆的重量轻,热成型 更薄的HSS板的应用将成为一个重要的措施。
汽车板热冲压成形生产线的相关设计

汽车板热冲压成形生产线的相关设计热冲压成形技术是实现汽车轻量化的关键技术之一,其相关设计是汽车板加工的重要环节。
本文主要介绍其技术原理、主要工艺流程、设备和工艺的选择以及工厂设计的要求。
标签:汽车板;热冲压成形;工厂设计随着人们对环保意识的加强,节能减排成为了工业企业转型升级的重要任务,而汽车轻量化则在汽车行业中担负起了节能减排的重任,也是当前汽车发展的主要潮流。
针对汽车轻量化,目前采用的先进生产技术主要有硼合金钢板的研发和生产、开卷落料、激光拼焊、热冲压成形、激光切割等。
其中,作为关键技术之一的热冲压成形生产线的设计是汽车板加工的重要环节。
1 热冲压成形简述1.1 热冲压成形技术原理热冲压成形的主要技术原理是将高强度钢板加热到奥氏体温度范围,在完成组织转变后将其快速移动到压机模具中进行热冲压,并通过模具中的冷却回路对其进行一定速度的淬火冷却以实现超高强度(抗拉强度可達1500MPa甚至更高)的冲压零件。
1.2 主要工艺流程主要工艺步骤如下:(1)上料。
用机械手将原料料片从原料料垛运送到加热炉中。
(2)加热。
在加热炉中将料片加热到AC3以上温度,对钢材进行充分的奥氏体化。
该温度根据材料的成分、相变过程、板料厚度和最终零件的形状来确定,加热温度一般控制在900~930℃之间。
(3)料片定位。
在将料片放入模具之前,需要合理的定位,以保证机械手上料后准确送到模具给定位置。
(4)装载。
用特殊的夹具将料片装载到模具预定位置。
(5)成形。
压机合模,将料片冲压成形。
(6)淬火。
模具合模之后,立即开始淬火过程,以大于30~40℃/s的冷却速度将零件均匀冷却到150~200℃。
准确的冷却速度由钢在机械变形下淬火时的临界冷却速度决定。
(7)卸料。
用机械手将成形后已冷却到给定温度的零件从模具中取出,并送到堆垛筐进行堆垛。
2 热冲压成形工艺选择2.1 主要技术选择热冲压成形的核心技术包括原材料、涂层技术、热冲压模具、工艺总控制及优化设计等。
热冲压成形工艺解析

热冲压成形工艺解析热冲压成形工艺解析随着汽车轻量化的发展,钢板热冲压技术应运而生,其将高强度钢板在温度场内由奥氏体转变为马氏体,提高了板料的强度,降低了板料的重量。
本文对热冲压成形板料和设备应用进行了总结,并预测了热冲压技术的未来发展趋势...安全、节能和环保是消费者最关心的汽车性能指标。
目前,降低汽车燃料消耗、减少CO2和废气排放是社会的主要需求。
车身轻量化对于减轻整车自身重量、降低油耗和促进节能环保至关重要。
为了适应轻量化的发展趋势,热成形工艺和应用技术应运而生。
热成形压力机简称热冲压,是相对于常见的冷冲压成形而言。
为了帮助减轻汽车自身重量并提高汽车的安全性,钢铁业开发出许多种类的高强度钢板。
为了克服高强度钢板冷成形的困难,热冲压需要通过将钢板加热,使其板料上产生一个不断变化的温度场。
在温度场的影响下,板料的基体组织和力学性能发生变化,导致板料的应力场也发生变化,同板料的应力场变化又反作用于温度场。
热成形工艺过程为:首先将常温下强度为500~600MPa的硼合金钢板加热到约940℃,全奥氏体后,将材料从加热炉转移到热成形的压力机中,该过程在空气中进行,必须尽快完成,如果成形前材料温度降到750℃以下,就可能形成铁素体从而恶化零件的机械性能。
送入内部具有冷却系统的模具内,压力机进行冲压、成形。
板料在模具内快速冷却(水冷),将奥氏体转变为马氏体(200℃以下),冷却速度一般为-40~100℃/s以保证零件的淬透性,使冲压件得到硬化,大幅度提高强度(1500MPa)。
所以热成形工艺就是板料内部温度场与应力场共存且相互耦合的变化过程。
热冲压成形的生产流程为拆垛装置、加热炉、上料装置、成形冷却、激光切割和喷丸涂油,如图1所示。
图1 热冲压成形的工艺流程热成形板料选择目前,热成形用钢均选用硼钢,因微量的硼可有效提高钢的淬透性,使零件在模具中以适当的冷却速度获得所需要的马氏体组织,从而保证零件的高强度。
热成形冲压板材主要分为镀层与无镀层板材。
高强钢热冲压成型工艺流程 预热处理 冲压成形 淬火
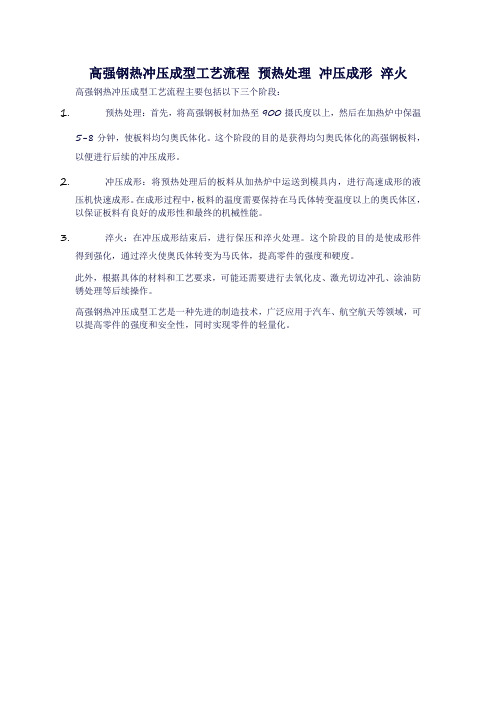
高强钢热冲压成型工艺流程预热处理冲压成形淬火高强钢热冲压成型工艺流程主要包括以下三个阶段:
1.预热处理:首先,将高强钢板材加热至900摄氏度以上,然后在加热炉中保温
5-8分钟,使板料均匀奥氏体化。
这个阶段的目的是获得均匀奥氏体化的高强钢板料,以便进行后续的冲压成形。
2.冲压成形:将预热处理后的板料从加热炉中运送到模具内,进行高速成形的液
压机快速成形。
在成形过程中,板料的温度需要保持在马氏体转变温度以上的奥氏体区,以保证板料有良好的成形性和最终的机械性能。
3.淬火:在冲压成形结束后,进行保压和淬火处理。
这个阶段的目的是使成形件
得到强化,通过淬火使奥氏体转变为马氏体,提高零件的强度和硬度。
此外,根据具体的材料和工艺要求,可能还需要进行去氧化皮、激光切边冲孔、涂油防锈处理等后续操作。
高强钢热冲压成型工艺是一种先进的制造技术,广泛应用于汽车、航空航天等领域,可以提高零件的强度和安全性,同时实现零件的轻量化。
热冲压的 现状和趋势
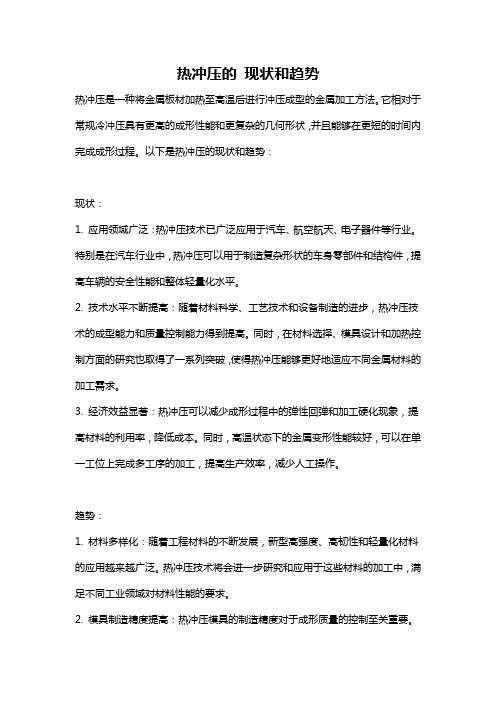
热冲压的现状和趋势热冲压是一种将金属板材加热至高温后进行冲压成型的金属加工方法。
它相对于常规冷冲压具有更高的成形性能和更复杂的几何形状,并且能够在更短的时间内完成成形过程。
以下是热冲压的现状和趋势:现状:1. 应用领域广泛:热冲压技术已广泛应用于汽车、航空航天、电子器件等行业。
特别是在汽车行业中,热冲压可以用于制造复杂形状的车身零部件和结构件,提高车辆的安全性能和整体轻量化水平。
2. 技术水平不断提高:随着材料科学、工艺技术和设备制造的进步,热冲压技术的成型能力和质量控制能力得到提高。
同时,在材料选择、模具设计和加热控制方面的研究也取得了一系列突破,使得热冲压能够更好地适应不同金属材料的加工需求。
3. 经济效益显著:热冲压可以减少成形过程中的弹性回弹和加工硬化现象,提高材料的利用率,降低成本。
同时,高温状态下的金属变形性能较好,可以在单一工位上完成多工序的加工,提高生产效率,减少人工操作。
趋势:1. 材料多样化:随着工程材料的不断发展,新型高强度、高韧性和轻量化材料的应用越来越广泛。
热冲压技术将会进一步研究和应用于这些材料的加工中,满足不同工业领域对材料性能的要求。
2. 模具制造精度提高:热冲压模具的制造精度对于成形质量的控制至关重要。
模具制造工艺和加工设备将进一步改进,以提高模具的加工精度和表面质量,提高成形产品的几何形状和尺寸一致性。
3. 数字化和自动化生产:热冲压过程中的温度、压力、成形力等参数对于产品质量具有重要影响。
通过引入数字化和自动化控制技术,可以实时监测和控制这些加工参数,提高生产过程的稳定性和一致性。
总的来说,热冲压技术在金属板材成形领域具有广阔的发展前景,将会继续在工业生产中得到广泛应用,并不断推动行业的发展和进步。
热成型关键技术-全工艺讲解

3、热冲压装备技术
上料夹持器(Grippers)
③ 上料自动化设备
3、热冲压装备技术
上料夹持器(Grippers)
③ 上料自动化设备
配置气刀以在冲压之前清除模具上的氧化皮!
3、热冲压装备技术
④ 压机
3、热冲压装备技术
④ 压机
技术要求及其特点:
1 快速合模、成形; 2 保压淬火; 3 备有过程监控(特别是温度); 4 自润滑材料; 5 高速液压机(兼顾一般液压机和机械压力机的优点)。 6 吨位相对较小,常用吨位800吨-1200吨。
3、热冲压装备技术
④ 压机
3、热冲压装备技术
④ 压机
采用蓄力器来提高冲压速度
3、热冲压装备技术
④ 压机
3、热冲压装备技术
④ 压机
温度检测
3、热冲压装备技术
• Minimum of leakage • Efficient oil cleaning and
cooling system • Hydraulic unit away from
目前业内更多地是采用减薄率 分析热冲压成形性!
HOT FORMING
1、热冲压零件/小总成协同设计
热冲压零件协同设计-关键要素
关键技术参数输入 不同温度、不同应变速度下的应变曲线
HOT FORMING 1、热冲压零件/小总成协同设计
热冲压零件协同设计-关键要素
CAE仿真分析、成形性评估和外形改进
优化碰撞建技术 采用更好的假人模型 系统研究热冲压零件的合理选用及其相关零件的高强化方案 达到最佳的整车性能
HOT FORMING
1、热冲压零件/小总成协同设计
宝钢每年要承担数个车型数十个热冲压零件的CAE分析,涵盖了所有典 型热冲压零件,至今已经完成200多个零件的热冲压CAE分析。具备较强 的热冲压零件/小总成的协同设计能力。
DEFORM 热冲压成形工艺数值模拟技术应用

DEFORM热冲压成形工艺数值模拟技术应用安世亚太公司工艺产品部1 前言热冲压成形工艺可使超高强度钢具有极好的可塑性、良好的成形性能及热加工性能,钣金热冲压成形技术作为钣金件冲压强化的有效途径,已在汽车等领域得到了越来越广泛的应用。
热冲压件可应用于汽车A柱、B柱、边梁、保险杠、顶盖纵梁、门梁、侧栏等重要结构件。
DEFORM金属热冲压成形模拟技术可实现高强度钣金热冲压成形过程的分析,预测冲压缺陷及热冲过程淬火现象,优化热冲工艺参数及热冲模设计。
2 热冲压成形工艺技术及特点热冲压成形是一项专门用来成形超高强度钢板冲压件的新型工艺和技术,是获得超高强度冲压件的有效途径。
热冲压成形部件的抗拉强度可达1500MPa以上,抗疲劳极限可达800MPa,因此硼钢等超高强度钢以其高强度特性已成为汽车重要保护部件用钢的最佳选择。
热冲压成形具有很多优点,如可得到超高强度的车身覆盖件;在保证汽车安全性能得条件下,优化设计以减薄车身零部件,可减轻车身重量,提高车身安全性、舒适性;改善冲压成形性,降低钣金出现易拉伸失稳性,克服传统工艺回弹严重、成形困难容易开裂等诸多难题。
热冲工艺成形技术是将钢板(如硼钢)加热至奥氏体状态,然后进行冲压并同时以20-30摄氏度/秒的冷却速度进行淬火处理,通过一定时间的保压以获得具有均匀马氏体组织的高强度钢钣金件的成形方式。
热冲压工艺包括直接成形(图1)和间接成形(图2),间接成形工艺因增加了设备成本,故现在的热冲压主要以直接热冲压工艺为主。
图1 直接热冲压成形工艺图2 间接热冲压成形工艺3 DEFORM热冲压成形工艺方案的工业应用热冲压成形技术虽具有很多优点,但因较普通冷冲压成形存在热成形及淬火冷却热处理的诸多因素影响,使得如何进行热冲压工艺参数优化及模具冷却结构设计成为需要解决的问题。
影响热冲成形的因素包括板料拉伸性能参数、冲压温度、冲压速度、润滑方案、保压时间、冷却速度及模具冷却水管的结构分布设计等,因此如何在工艺及模具设计阶段优化工艺设计参数,是提高热冲成形效率,降低研发成本的重点。
热冲压成形中的先进加热技术及设备

热冲压成形中的先进加热技术及设备摘要:热冲压成形技术是汽车工业中常用的零部件加工技术,通过热冲压制造的成形件具有强度高、质量轻等特点。
由此可见,热冲压成形技术可以很好的满足新时期汽车工业对材料轻量化、高强度的技术要求,具有非常广阔的应用前景。
关键词:热冲压成形;加热技术;设备前言热冲压成形技术是一种常见的零件加工方式,尤其在汽车工业中应用最为普遍。
将材料先加热至奥氏体化状态,该状态下钢板材料的塑性较好,强度低,并且具有一定的韧性,然后使用冲压机在模具中进行冲压并淬火,获得相应形状的高强度金属零件。
通过热冲压成形技术获取高强度的冲压件来代替传统的厚钢板,不但可以有效降低零部件自身的重量,而且能大幅度地提升抗拉强度。
1热冲压技术原理热冲压技术是一种将钢板材料加热至奥氏体形态下,快速进行冲压成形,并且通过模具对零件进行淬火冷却,获得强度为1500MPa左右的马氏体成形件。
可以说热冲压技术是将钢板材料由奥氏体向马氏体转化的过程。
奥氏体(Austenite)是钢铁的一种层片状的显微组织,该状态下的钢板材料ɣ-Fe中固溶少量碳的无磁性固溶体,因此也称为沃斯田铁或者ɣ-Fe。
马氏体(Martensite)是黑色金属材料的一种组织名称,是碳在α-Fe中的过饱和固溶体。
马氏体和奥氏体的不同在于,马氏体是体心正方结构,奥氏体是面心立方结构。
奥氏体向马氏体转变仅需很少的能量,因为这种转变是无扩散位移型的,仅仅是迅速和微小的原子重排。
马氏体的密度低于奥氏体,所以转变后体积会膨胀。
相对于转变带来的体积改变,这种变化引起的切应力、拉应力更需要重视。
热冲压成形技术可以分直接冲压和间接冲压两种形式,其中直接冲压是将钢板材料加热至奥氏体后,直接传送至模具上冲压,模具表面有冷却通道,可以在钢板材料冲压的过程中进行淬火冷却,获得马氏体成形件。
间接冲压则是钢板材料先进行冷冲压,然后再加热成奥氏体进行淬火和校准,确保成形材料强度达到1500MPa的马氏体。
热冲压成形、铝合金热冲压工艺特点-热成型_热冲压_热成形在车身轻量化上的运用

一,热成形工艺特点及原理
一,热成形工艺特点及原理
一,热成形工艺特点及原理
二,热成形零件在轻量化车身上的运用
三,热成形零件生产控制以及检测
四,热成形的新技术
五,铝合金热成型技术
六,钢板热冲压、铝板热冲压基本原理的异同相同点:本质上说,不论钢还是铝,热冲压都利用了以下3个共同的特点:
1.合金元素在高温下的溶解度远大于室温溶解度(钢的过冷奥氏体、铝的过饱和固溶体)
2.高温下面的材料的优良成形性能
3.成形后急速冷却并保压过程,优良的形状冻结能力
不同点:两者的强化机理完全不同,导致工艺过程不一样
1.钢的热冲压,利用的铁本身在不同温度下晶格的变化-同素异构特性,
2.铝的热冲压,则主要靠不同合金元素的溶解分布以及析出强化,铝合金热冲压需要时效处理。
如果你觉得太难于理解的话,可以简单的如下考虑:
钢的热冲压过程类似于做油脂雪糕过程,铝的热冲压过程类似于铺沥青马路的过程
一家之言,欢迎沟通与交流,热冲压李工给你任何你需要的;东西看完了,给大家打个广告吧,需要热冲压零件和模具的联系我天津百事泰汽车科技有限公司,是天津地区一家专业的热冲压零部件生产企业,可生产热冲压裸板、铝硅涂层板的热冲压,
有京津冀地区最好的抛丸涂油生产线
主要服务客户:天津、北京、河北、山东、河南、辽宁、江苏、上海等;
业务联系邮箱:
***************.cn ******************.cn ***************************@ 想讨论热冲压技术的也可以扫二维码加我微信。
高强钢热冲压成型工艺流程 预热处理 冲压成形
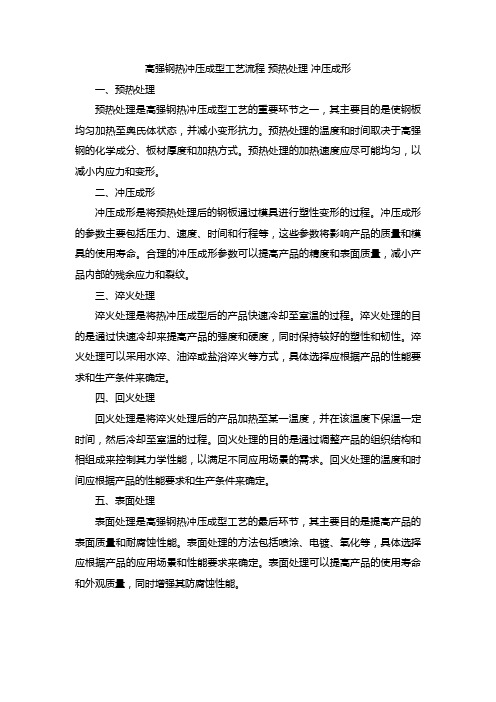
高强钢热冲压成型工艺流程预热处理冲压成形一、预热处理预热处理是高强钢热冲压成型工艺的重要环节之一,其主要目的是使钢板均匀加热至奥氏体状态,并减小变形抗力。
预热处理的温度和时间取决于高强钢的化学成分、板材厚度和加热方式。
预热处理的加热速度应尽可能均匀,以减小内应力和变形。
二、冲压成形冲压成形是将预热处理后的钢板通过模具进行塑性变形的过程。
冲压成形的参数主要包括压力、速度、时间和行程等,这些参数将影响产品的质量和模具的使用寿命。
合理的冲压成形参数可以提高产品的精度和表面质量,减小产品内部的残余应力和裂纹。
三、淬火处理淬火处理是将热冲压成型后的产品快速冷却至室温的过程。
淬火处理的目的是通过快速冷却来提高产品的强度和硬度,同时保持较好的塑性和韧性。
淬火处理可以采用水淬、油淬或盐浴淬火等方式,具体选择应根据产品的性能要求和生产条件来确定。
四、回火处理回火处理是将淬火处理后的产品加热至某一温度,并在该温度下保温一定时间,然后冷却至室温的过程。
回火处理的目的是通过调整产品的组织结构和相组成来控制其力学性能,以满足不同应用场景的需求。
回火处理的温度和时间应根据产品的性能要求和生产条件来确定。
五、表面处理表面处理是高强钢热冲压成型工艺的最后环节,其主要目的是提高产品的表面质量和耐腐蚀性能。
表面处理的方法包括喷涂、电镀、氧化等,具体选择应根据产品的应用场景和性能要求来确定。
表面处理可以提高产品的使用寿命和外观质量,同时增强其防腐蚀性能。
通过以上五个方面的介绍,可以看出高强钢热冲压成型工艺的流程涉及多个环节。
在生产过程中,要保证每个环节的质量和稳定性,以获得高性能的高强钢制品。
热冲压的发展史

热冲压的发展史
热冲压技术,也称为热成形或冲压淬火,是一种新型的制造技术,它将传统的冷冲压技术及热处理工艺相结合。
该技术起源于欧洲,由瑞典的Plannja公司开发并于1977年申请专利,主要用于生产割草机的刀片和锯条。
随后,瑞典的Saab汽车公司于1984年首先采用热冲压技术生产汽车零部件,并将生产的热冲压零部件用在车型Saab9000上。
法国Renault汽车公司在1999年的Laguna车型上首次采用了热冲压技术生产的防撞梁。
随着全球气候变暖问题日益严重,各国政府积极应对,制定各种法规促进节能减排。
汽车作为重要的排放源,对节能减排有重大影响。
例如,1975年美国国会通过了能源整车和保护议案,要求汽车制造商生产和销售符合油经济性指标的车辆。
1997年的京都议定书限制二氧化碳排放,再次促进轻量化。
热冲压技术正是为了解决汽车工业发展面临的三大问题——安全、节能和环保而产生的。
在节能方面,汽车必须降低排放和更好的气经济性,需要降低汽车自重,汽车每减重10%,油耗减少8%,排放降低5-6%。
而热冲压技术能够使成形之后
的零件具有超高的强度及硬度,满足安全碰撞法规,同时实现轻量化,符合节能和环保的要求。
以上内容仅供参考,如需更多信息,建议查阅相关文献或咨询材料学专家。
基于ABAQUS软件的热冲压成形接触问题分析

基于ABAQUS软件的热冲压成形接触问题分析热冲压成形是一种重要的金属加工技术,广泛应用于航空航天、汽车制造等领域。
在热冲压成形过程中,金属材料在高温和高压条件下进行塑性变形,因此需要对接触问题进行深入分析,以确保产品质量和生产效率。
本文将基于ABAQUS软件,对热冲压成形接触问题进行分析,并探讨其在实际工程中的应用。
1. 热冲压成形的基本原理热冲压成形是一种通过热加工和冷却加工相结合的金属成形工艺。
在热冲压成形过程中,首先将金属材料加热至一定温度,然后在高温下进行塑性变形,最后通过冷却加工使其保持所需的形状。
这种成形工艺不仅能够提高金属材料的延展性和塑性,还可以减少成形过程中的应力和变形,从而获得更高质量的成形件。
在热冲压成形过程中,由于金属材料在高温和高压条件下进行塑性变形,因此在接触区域会出现较大的接触压力和摩擦力。
这些接触问题不仅会影响成形过程的稳定性和精度,还会对成形件的表面质量和尺寸精度产生较大影响。
对热冲压成形接触问题进行深入分析是十分必要的。
ABAQUS是一种常用的有限元分析软件,具有强大的模拟和分析功能,广泛应用于工程领域。
在热冲压成形接触问题分析中,ABAQUS软件可以通过建立合适的有限元模型,对接触区域的接触压力、摩擦力等参数进行模拟和分析,从而为实际生产提供有效的参考和指导。
3. 热冲压成形接触问题分析的工程应用热冲压成形接触问题分析在工程领域具有重要的应用价值。
通过对接触问题进行深入分析,可以为优化成形工艺提供重要参考。
通过建立合理的有限元模型,对不同工艺参数进行模拟和分析,可以获得最佳的成形工艺参数,提高产品质量和生产效率。
热冲压成形接触问题分析还可以为成形模具的设计和优化提供重要指导。
通过模拟和分析不同模具结构和参数对成形过程的影响,可以设计出更加合理的模具结构,减少接触问题对模具的损耗,延长模具的使用寿命。
热冲压成形接触问题分析还可以为产品表面质量的提高提供重要依据。
热冲压定义
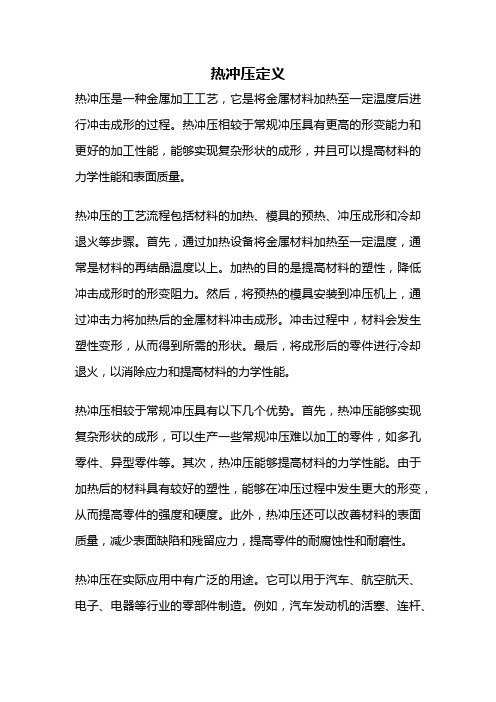
热冲压定义热冲压是一种金属加工工艺,它是将金属材料加热至一定温度后进行冲击成形的过程。
热冲压相较于常规冲压具有更高的形变能力和更好的加工性能,能够实现复杂形状的成形,并且可以提高材料的力学性能和表面质量。
热冲压的工艺流程包括材料的加热、模具的预热、冲压成形和冷却退火等步骤。
首先,通过加热设备将金属材料加热至一定温度,通常是材料的再结晶温度以上。
加热的目的是提高材料的塑性,降低冲击成形时的形变阻力。
然后,将预热的模具安装到冲压机上,通过冲击力将加热后的金属材料冲击成形。
冲击过程中,材料会发生塑性变形,从而得到所需的形状。
最后,将成形后的零件进行冷却退火,以消除应力和提高材料的力学性能。
热冲压相较于常规冲压具有以下几个优势。
首先,热冲压能够实现复杂形状的成形,可以生产一些常规冲压难以加工的零件,如多孔零件、异型零件等。
其次,热冲压能够提高材料的力学性能。
由于加热后的材料具有较好的塑性,能够在冲压过程中发生更大的形变,从而提高零件的强度和硬度。
此外,热冲压还可以改善材料的表面质量,减少表面缺陷和残留应力,提高零件的耐腐蚀性和耐磨性。
热冲压在实际应用中有广泛的用途。
它可以用于汽车、航空航天、电子、电器等行业的零部件制造。
例如,汽车发动机的活塞、连杆、气门等零件常常采用热冲压工艺进行加工,以提高零件的强度和耐久性。
此外,热冲压还可以用于制造锻件、粉末冶金件、高强度螺栓等特殊零件。
尽管热冲压具有许多优势,但也存在一些限制和挑战。
首先,热冲压需要相对较高的设备和能源投资,加热和冷却退火设备的成本较高。
其次,热冲压对模具的要求较高,模具的设计和制造难度较大。
此外,热冲压过程中材料易受氧化和变色的影响,需要采取一些措施来保护材料的表面质量。
热冲压是一种高效、精密的金属加工工艺,能够实现复杂形状的成形,并提高材料的力学性能和表面质量。
它在汽车、航空航天、电子等行业有广泛的应用前景。
随着科技的不断进步和工艺的不断改进,热冲压将继续发展壮大,为各行各业提供更高质量的零部件。
- 1、下载文档前请自行甄别文档内容的完整性,平台不提供额外的编辑、内容补充、找答案等附加服务。
- 2、"仅部分预览"的文档,不可在线预览部分如存在完整性等问题,可反馈申请退款(可完整预览的文档不适用该条件!)。
- 3、如文档侵犯您的权益,请联系客服反馈,我们会尽快为您处理(人工客服工作时间:9:00-18:30)。
SIMWON
Total Design Service
修正案 强制规制 2015 年 2020 年
目
140 g/km 轿车 欧洲-15个国家
175 g/km 商务车 欧洲-27个国家
160 g/km 商务车
95 g/km 轿车
目标车辆 目标国家
• 逐渐缩减燃料中碳素成分, 增大生物燃料的使用 其 他 • 汽车尾气排气制度待议 (2013年以前未实施)
58% 有 效 功 率
The Best Autobody Maker
15
7.加 热 炉
▶ 加热曲线
1000 930 900 800 700
SIMWON
Total Design Service
温 度 (℃)
600 500 400 300 200 100 0 0 60 120 180 200
常规使用 辊底炉 混合电炉
- 保险杠后梁 : 奔驰C级,菲亚特500,福特福克斯、蒙迪欧、高速公路,宝马3系列, - 顶盖侧板 : 福特蒙迪欧,奔驰C级
- A柱 : 奥迪 A3、A5、TT、Q7,日产 Altima
The Best Autobody Maker
10
5.热冲压流程
▶制造方法
白钢板 涂层钢板 冲裁 (冲孔) 预处理 钢板冷冲预成形 预成形部件
The Best Autobody Maker
20
9.模具设计和分析
▶模具设计
SIMWON
Total Design Service
• 优秀的冷却效率 • 高效的生产速度
CP 0 0 200 600 1000 MS
淬火 BS 1500
0
抗 拉 强 度 ( MPa )
时间
The Best Autobody Maker
9
4.应 用 部 件
-中 柱 : 大众帕萨特、路波,奥迪A3、A5、TT、Q7,奔驰 S-Class、C-Class, 沃尔沃XC70、XC90、S80,菲亚特500,福特蒙迪欧,雷诺Laguna3, 日产风雅、雅阁,丰田普锐斯、路虎揽胜
The Best Autobody Maker
7
2.为什么选择热冲压成形 ?
适用效果
①车体轻: 减轻10% (1,500 MPa 以上的最高超高强度钢) ② 尺寸精确度提高(确保质量) : 回弹力减少90% 以上
SIMWON
Total Design Service
回弹力 +43 残留应力
③ 提高加工性: 900℃ 以上的高温成型(延伸率= 70% 水平)
延伸率(%)
延伸率(%) 强度(MPa) 温度(℃)
The Best Autobody Maker
8
3.硼 钢
化学成分
材料牌号
20MnB5
SIMWON
Total Design Service
单 位 : wt % C min-max
0.17-0.23
Si max
0.40
Mn min-max
1.10-1.40
SIMWON
Total Design Service
The Best Autobody Maker
19
8.切 割 方 案
▶激光切割 ▶压力切割
SIMWON
Total Design Service
部件表面不同的切割状况
• 典型切割方法
• 每条生产线4台激光设备
• 通过高强度刀口快速切割 • 每条生产线1台切割模具
26% effective power
混合炉
58% effective power
The Best Autobody Maker
16
6.冲 压 机
▶冲压机要求
• 快速闭合和成形
SIMWON
Total Design Service
• 保持冲压和淬火 高速液压机
或 伺服压力机
600 550 500 450 400 350 300 250 200 150 100 50 0 0.0 0.5 1.0 1.5 2.0 2.5 3.0 3.5 4.0 4.55.0 5.5 6.0 6.5 7.0 7.5 8.0 8.5 9.0 9.5 10.0
SIMWON
Total Design Service
热冲压成形技术
2011. 04. 07
目录
1. 概 述 2. 为什么选择热冲压成形 ? 3. 硼 钢 4. 应 用 部 件 5. 热 冲 压 成 形 程 序 6. 冲 压 机 7. 加 热 炉 8. 切 割 方 案 9. 模 具 设 计 和 分 析 10. 特 征 和 效 率 11. 参 考 数 据 12. 业 务 情 况 13. 总 结
The Best Autobody Maker
13
7.加 热 炉
▶ 辊底炉 (普遍使用)
SIMWON
Total Design Service
26% 有 效 功 率
14
The Best Autobody Maker
7.加 热 炉
▶ 混合加热炉 (高频感应加热设备 + 电炉加热)
SIMWON
Total Design Service
14.5 6★条件
※ 4★ 以下 : 基准一样
The Best Autobody Maker
4
2.为什么选择热冲压成形 ?
▶欧洲 缩减 CO2 修正案
区分 规制形式 时 间 标 目前规则 自发规制 2009 年 2012 年 130 g/km (总体上更缩小 10 g/km, 最终达成 120 g/km ) 轿车
尺寸精度 :长系列的制造中具有很好的重复性。尺寸精度可媲美低碳钢的惯用成形加工(无回弹)。 接 :由于碳含量低,具有很好的焊接性能。点焊和惰性气体焊接都可以进行。 工 :加工的材料具有优良的热加工性能。非常复杂的形状可以一次冲压完成。
抗疲劳强度:细晶钢(如硼钢)结合热冲压工艺将使抗疲劳极限高达800兆帕 。
▶制造程序
钢卷
堆垛机
机器人1
加热炉
机器人2
冲压机
机器人3
成品
The Best Autobody Maker
3
2.为什么选择热冲压成形 ?
▶ 强化碰撞/安全法律 (欧洲新车安全评鉴协会Euro-NCAP )
SIMWON
Total Design Service
5 ★ 碰撞测试
确保辨别力
6 ★ 碰撞测试
Stroke (毫米)
Time (秒)
The Best Autobody Maker
17
6.冲 压 机
▶ 冲压机说明 (伺服压力机)
直接驱动伺服压力机(偏心齿轮式) 高速冲程 冲程运动控制 模具转换设备 /换模保持装置 公称力 滑块行程 闭模高度 工作台尺寸 变量 SPM 产 能 8,000 kN 600 mm 750 ~ 1,350 mm 3,000 x 2,000 mm x mm 30 SPM (最大) 约 5 ~ 8 (件/分)
SIMWON
Total Design Service
• 制造公司和政府之间到 2012年为止, 改善 15 % 以上燃料消费率, 签订自由的合约 (2005年 12月)
单位 : km/l (mpg) 区分 现行 强化方案
1600cc 以下 基准强化 (2012 年) 1600cc 超过
12.4 (29.2)
11
5.热冲压流程
1) 热冲压成形制作流程 (样车部分)
SIMWON
Total Design Service
钢板
加热 (930℃)
成型及速动
移动
产品
激光加工
完成品
12
The Best Autobody Maker
5.热冲压流程
2) 热冲压成形制作流程 (量产部分)
SIMWON
Total Design Service
SIMWON
Total Design Service
冷冲压成形 压力 切边
热 冲 压
钢板或者预成形部件在辊底炉中加热到950 °C 惰性气体保护 惰性气体保护 在水冷却模具中的热冲压和淬火 惰性气体保护
后期处理
喷砂或表面处理 激光切割或者压力切割
喷砂或表面处理
The Best Autobody Maker
• CO2 税金特惠, 通过贴燃料标签, 可以选择燃料更好的车型的制度.
• 针对提高燃料率的广告和宣传 (2007年中旬与汽车公司协商)
The Best Autobody Maker
5
2.为什么选择热冲压成形 ?
▶ 强化公司平均燃油经济性标准 (CAFE)
• 美国等国外国家, 为了提高平均燃料消费率, 加强政策
15.0 (35.3) (21%↑)
9.6 (22.6)
12.0 (28.2) (25%↑)
长期目标设定 (2020年) 基准单一化 扩大目标车辆
1600cc 基准由 2个郡 (以下, 超过)区分 对象 : 轿车 (小型车/ LPG燃料 以外)
15.8 (37.2) 单一基准设定 (排气量区分删除) 对象 : 轿车 (包括小型车, LPG燃料 以外)
(适用 : 2008. 下半年)
5★ 碰撞
未实施 -
6★碰撞
32.5
2 1 2
要 求
39.5
6
保护颈部 (8) SBR 侧面 梁 (3) (2)
32.5
选 择 要 求
3 2 14.5
12.5
12.5
Off-Set 碰撞 (16) 侧面碰撞 (16) ( ) : 最大分数
12.5 5★条件
12.5 5★条件
40