10 第二篇 板带材生产2015
国家标准《锂离子电池用压延铜箔》编制说明

国家标准GB /T XXXX-XX《锂离子电池用压延铜箔》(讨论稿)编制说明《锂离子电池用压延铜箔》标准起草小组二○一六年五月国家标准《锂离子电池用压延铜箔》(讨论稿)编制说明一、工作简况1、任务来源锂离子电池是最新发展起来的绿色能源,也是我国能源领域重点支持的高新技术产业。
压延铜箔是作为锂离子电池负极集流体的主要材料,其生产技术的发展和性能参数将直接影响锂离子电池的制作工艺、性能和生产成本。
目前国外压延铜箔的生产企业主要有:日本日矿金属(Nippon mining)、日本福田金属箔粉公司(Fukuda)、日立电线公司(Hitachi cable)、美国奥林黄铜(Olin Brass)等。
国内菏泽广源铜带有限公司、山东天和压延铜箔有限公司、中色奥博特铜铝业有限公司等逐渐开展锂离子电池用压延铜箔的研发与生产,形成规模化、行业化,且市场需求强劲。
国内主要生产锂离子电池企业有深圳比亚迪、天津捷威动力、天津力神、中航锂电、国联动力、深圳比克电池等百余家,对压延铜箔的使用及工艺性能具备深入的了解和掌握。
在生产企业和使用企业建立稳定供需关系的基础上,可共同对压延铜箔行业标准的技术内容和指标进行确定。
本标准制订的目的主要是规范锂离子电池用压延铜箔的生产与供货,为锂离子电池专用压延铜箔生产企业提供质量控制依据,而且为锂离子电池生产企业采购专用压延铜箔提供参考依据。
根据国标委综合〔2015〕59号和有色标委[2015]29号《关于转发2015年第二批有色金属国家、行业标准制(修)订项目计划的通知》,其中序号59(项目编号“20152292-T-610”)《压延铜箔》国家标准由菏泽广源集团山东天和压延铜箔有限公司、安徽鑫科新材料股份有限公司、中色奥博特铜铝业有限公司、绍兴市力博电气有限公司等负责起草,完成年限为2018年9月。
2、承担单位简况菏泽广源铜带有限公司及山东天和压延铜箔有限公司为菏泽广源集团核心企业。
依托集团公司近30年铜带箔技术积累、人才积累和生产研发平台技术创新能力,引进了世界先进水平的高精电子压延铜箔生产设备和尖端实验检测仪器,建成了国内首条高精电子压延铜箔生产线,主要生产厚度0.006mm以上、宽度650mm以内的高精电子压延铜箔,年生产能力5000吨,是集高精电子压延铜箔产品生产、研发、销售、服务为一体的专业化生产企业。
铝合金板带材生产车间设计的毕业设计论文
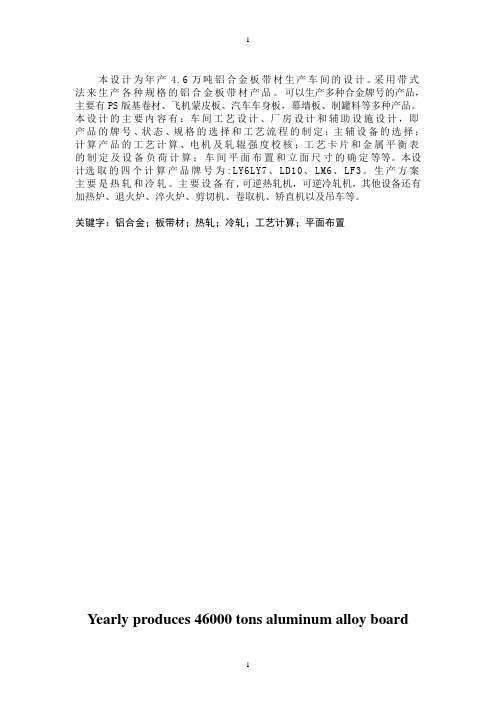
本设计为年产4.6万吨铝合金板带材生产车间的设计。
采用带式法来生产各种规格的铝合金板带材产品。
可以生产多种合金牌号的产品,主要有PS版基卷材、飞机蒙皮板、汽车车身板,幕墙板、制罐料等多种产品。
本设计的主要内容有:车间工艺设计、厂房设计和辅助设施设计,即产品的牌号、状态、规格的选择和工艺流程的制定;主辅设备的选择;计算产品的工艺计算、电机及轧辊强度校核;工艺卡片和金属平衡表的制定及设备负荷计算;车间平面布置和立面尺寸的确定等等。
本设计选取的四个计算产品牌号为:LY6LY7、LD10、LM6、LF3。
生产方案主要是热轧和冷轧。
主要设备有,可逆热轧机,可逆冷轧机,其他设备还有加热炉、退火炉、淬火炉、剪切机、卷取机、矫直机以及吊车等。
关键字:铝合金;板带材;热轧;冷轧;工艺计算;平面布置Yearly produces 46000 tons aluminum alloy boardstrip Production workshop designhis design is about to yearly produce46000 tons aluminum alloy board strip Production workshop design. Uses the belt law to produce each kind of specificationthe aluminum alloy board strip product. Many kinds of alloy trademarks the productcan be producted in workshop desingn, the PS version base volume material, theairplane Mongolia fur plates, the car body panels,just as the curtain wall plate, thesystem pot material and so on .This design's primary coverage includes: Workshop technological design, workshop design and ancillary facilities design, namely product trademark, condition, specification choice and technical process formulation; Advocates the auxiliary equipment's choice; Counting yield process design, electrical machinery and roll strength examination; Process chart and metal balance formulationand machine utilization computation; The workshop plane layout and sets up thesurface size the determination and so on.This design annual output is 46000 tons, the selection four counting yield trademark is: LY6LY7, LD10, LM6, LF3. The production decision is mainly hot rolling and the cold rolling. The major installationhas reversible hot-rolling mill, reversible cold-rolling mill,other equipment alsohave the heating furnace, the annealing furnace, the alligator shears, the crimping machine, the straightening machine as well as the crane and so on.Key words: aluminum alloy;Sheet;Strip;Hot rolling;Cold rolling;Process calculation ;layou t目录1 车间设计总论 (6)1.1车间设计的基本内容 (6)1.2车间设计的依据 (6)1.3车间设计的基本程序 (6)2 产品方案与生产方案制定 (8)2.1产品方案的编制 (8)2.2生产方案的选择 (8)3 生产工艺流程 (10)3.1生产工艺流程 (10)3.2计算产品的生产工艺流程 (10)3.3锭坯的选择 (12)4 热轧 (14)4.1热轧工艺 (14)4.2热轧设备的选择 (15)4.3热轧工艺计算 (18)5 冷轧 (24)5.1冷轧工艺 (24)5.2冷轧设备选择 (26)5.3冷轧工艺计算 (29)6 生产工艺流程定额卡与金属平衡 (34)6.1生产工艺流程定额卡的编制 (34)6.2编制金属平衡表 (34)7 设备负荷计算 (36)7.1工作制度和年工作台时确定 (36)7.2设备负荷能力的计算 (36)8 车间平面布置 (38)8.1车间布置应遵循的原则 (38)8.2金属流程线的确定 (38)8.3设备布置 (38)8.4确定仓库面积的原则 (39)8.5其它设施的布置 (39)8.6车间工艺平面布置图 (41)9 车间劳动组织和经济指标 (42)9.1车间劳动组织 (42)9.2投资概算 (44)9.3流动资金定额的概算 (46)9.4能源及动力 (46)9.5产品成本概算 (52)9.6 投资回收期估算 (53)9.7技术经济效果评论 (53)参考文献致谢附录A外文翻译——原文部分附录B外文翻译——译文部分附录C附表及附图附表1 产品方案表与计算产品表附表2 压力加工车间锭坯用量表附表3 热轧工艺规程计算表附表4 冷轧工艺规程计算表附表5 工艺流程定额卡附表6 金属平衡表附表7 设备负荷计算表附表8 设备明细表附表9 车间劳动定员表附图车间工艺平面布置图1 车间设计总论1.1 车间设计的基本内容车间设计的目的是为了建立一个年产 4.6万吨铝及铝合金板、带材生产车间。
钢铁行业规范条件(2015年修订)
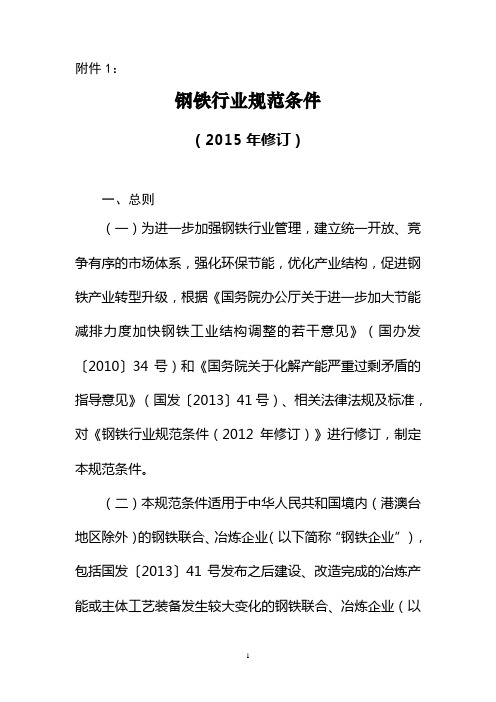
附件1:钢铁行业规范条件(2015年修订)一、总则(一)为进一步加强钢铁行业管理,建立统一开放、竞争有序的市场体系,强化环保节能,优化产业结构,促进钢铁产业转型升级,根据《国务院办公厅关于进一步加大节能减排力度加快钢铁工业结构调整的若干意见》(国办发〔2010〕34号)和《国务院关于化解产能严重过剩矛盾的指导意见》(国发〔2013〕41号)、相关法律法规及标准,对《钢铁行业规范条件(2012年修订)》进行修订,制定本规范条件。
(二)本规范条件适用于中华人民共和国境内(港澳台地区除外)的钢铁联合、冶炼企业(以下简称“钢铁企业”),包括国发〔2013〕41号发布之后建设、改造完成的冶炼产能或主体工艺装备发生较大变化的钢铁联合、冶炼企业(以下简称“新建、改造钢铁企业”)。
(三)本规范条件强化了环保节能约束,对新建、改造钢铁企业提出了要求,强化了对钢铁企业的事中事后监管,是钢铁企业的基本条件。
(四)符合本规范条件的企业,作为相关政策支持的基础性依据,不符合规范条件的企业应按照规范条件要求进行整改。
经整改仍不能达到规范条件要求的企业,各地要综合运用法律法规、经济和市场手段,推动其退出或转型发展。
二、规范条件(一)产品质量1.钢铁企业须建立完备的产品生产全过程质量保证制度和质量控制指标体系,具有产品质量保障机构和检化验设施,保持良好的产品质量信用记录,近两年内未发生重大产品质量问题。
2.钢铁企业产品须符合国家、行业、地方标准。
严禁生产Ⅱ级以下螺纹钢筋(直径14毫米及以下的Ⅱ级螺纹钢除外)、热轧硅钢片等《部分工业行业淘汰落后生产工艺装备号)中需淘汰的钢材产品。
3.严禁伪造他人厂名、厂址和商标,以次充好以及伪造、不开发票销售钢材等扰乱市场秩序的行为。
(二)工艺与装备1.严格控制新增钢铁生产能力。
新建、改造钢铁企业须按照国发〔2013〕41号和《工业和信息化部关于印发部分产能严重过剩行业产能置换实施办法的通知》(工信部产业〔2015〕127号)要求,制定产能置换方案,实施等量或减量置换,在京津冀、长三角、珠三角等环境敏感区域,实施减量置换。
钛及钛合金板带材生产学习资料
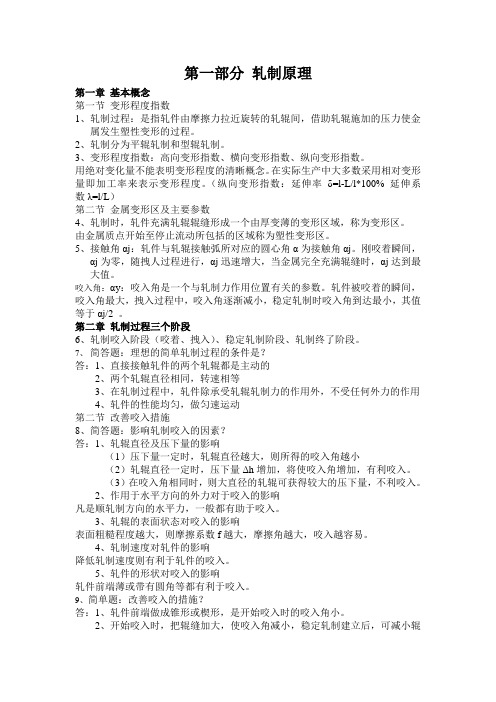
第一部分轧制原理第一章基本概念第一节变形程度指数1、轧制过程:是指轧件由摩擦力拉近旋转的轧辊间,借助轧辊施加的压力使金属发生塑性变形的过程。
2、轧制分为平辊轧制和型辊轧制。
3、变形程度指数:高向变形指数、横向变形指数、纵向变形指数。
用绝对变化量不能表明变形程度的清晰概念。
在实际生产中大多数采用相对变形量即加工率来表示变形程度。
(纵向变形指数:延伸率δ=l-L/l*100% 延伸系数λ=l/L)第二节金属变形区及主要参数4、轧制时,轧件充满轧辊辊缝形成一个由厚变薄的变形区域,称为变形区。
由金属质点开始至停止流动所包括的区域称为塑性变形区。
5、接触角αj:轧件与轧辊接触弧所对应的圆心角α为接触角αj。
刚咬着瞬间,αj为零,随拽人过程进行,αj迅速增大,当金属完全充满辊缝时,αj达到最大值。
咬入角:αy:咬入角是一个与轧制力作用位置有关的参数。
轧件被咬着的瞬间,咬入角最大,拽入过程中,咬入角逐渐减小,稳定轧制时咬入角到达最小,其值等于αj/2 。
第二章轧制过程三个阶段6、轧制咬入阶段(咬着、拽入)、稳定轧制阶段、轧制终了阶段。
7、简答题:理想的简单轧制过程的条件是?答:1、直接接触轧件的两个轧辊都是主动的2、两个轧辊直径相同,转速相等3、在轧制过程中,轧件除承受轧辊轧制力的作用外,不受任何外力的作用4、轧件的性能均匀,做匀速运动第二节改善咬入措施8、简答题:影响轧制咬入的因素?答:1、轧辊直径及压下量的影响(1)压下量一定时,轧辊直径越大,则所得的咬入角越小(2)轧辊直径一定时,压下量Δh增加,将使咬入角增加,有利咬入。
(3)在咬入角相同时,则大直径的轧辊可获得较大的压下量,不利咬入。
2、作用于水平方向的外力对于咬入的影响凡是顺轧制方向的水平力,一般都有助于咬入。
3、轧辊的表面状态对咬入的影响表面粗糙程度越大,则摩擦系数f越大,摩擦角越大,咬入越容易。
4、轧制速度对轧件的影响降低轧制速度则有利于轧件的咬入。
2015版XXXXXXXX制品有限公司质量手册

XXXXXXXXXX制品有限公司编号:Q/XXXX·SC-2016质量手册Quality Manual版次:A/0编制:XXXX审核:XXXX批准:XXXX2016年04月01日发布2016年04月01日实施XXXXXXXXXXXXXX Co.,Ltd.修订履历目录1.0 前言1.1 手册说明1.2 质量手册颁布令1.3 公司简介2.0 规范性引用文件3.0 术语和定义4. 组织环境4.1 理解组织及其环境4.2 理解相关方的需求和期望4.3 确定质量管理体系的范围4.4.质量管理体系及其过程5 领导作用5.1 领导作用和承诺5.1.1总则5.1.2以顾客为关注焦点5.2 质量方针5.2.1制定质量方针5.2.2沟通质量方针5.3 组织的角色、职责和权限6策划6.1 应对风险和机遇的措施6.2 质量目标及其实现的策划6.3变更的策划7支持7.1 资源7.1.1 总则7.1.2 人员7.1.3 基础设施7.1.4 过程运行环境7.1.5监视和测量资源7.1.6组织知识7.2 能力7.3意识7.4 沟通7.5 形成文件的信息7.5.1总则7.5.2编制和更新7.5.3文件化信息的控制8运行8.1 运行策划和控制8.2 产品和服务的要求8.2.1顾客沟通8.2.2与产品和服务有关要求的确定8.2.3 与产品和服务有关要求的评审8.2.4 产品和服务要求的变更8.3产品和服务的设计和开发8.3.1总则8.3.2设计和开发的策划8.3.3设计和开发的输入8.3.4设计和开发的控制8.3.5设计和开发的输出8.3.6设计和开发的更改8.4外部提供过程、产品和服务的控制8.4.1总则8.4.2 控制类型与程度8.4.3 外部供方信息8.5生产和服务提供8.5.1生产和服务提供的控制8.5.2标识和可追溯性8.5.3顾客或外供方的财产8.5.4防护8.5.5交付后活动8.5.6变更的控制8.6产品和服务的放行8.7不合格输出的控制9绩效评价9.1监视、测量、分析和评价9.1.1总则9.1.2顾客满意9.1.3 分析与评价9.2内部审核9.3管理评审10改进10.1总则10.2不合格与纠正措施10.3持续改进附件1 组织结构图附件2 质量管理体系职能分配表附件3 生产工艺流程图1前言1.1手册说明本手册按照ISO9001:2015标准要求编写,适用于本公司生产及服务在质量管理中的应用。
板带钢生产教学课件

contents
目录
• 板带钢生产概述 • 原料准备与加热 • 轧制工艺与设备 • 精整工艺与设备 • 质量检测与控制 • 安全与环保
01
板带钢生产概述
板带钢的定义与分类
总结词
板带钢是一种宽厚比相对较小、长度较长、形状扁平的钢材,广泛应用于建筑 、机械、汽车、船舶等领域。
详细描述
01
02
03
04
温度控制
控制轧制过程中的温度,确保 板带钢的力学性能和表面质量
。
厚度控制
通过调整轧辊间距或调节轧制 力等方式,控制板带钢的厚度
。
宽度控制
通过调整轧机两侧的宽度调整 装置,控制板带钢的宽度。
速度控制
根据生产需要,调节轧机的轧 制速度,以实现高效生产。
轧制过程中的缺陷与预防措施
裂纹
可能是由于轧制温度过高或过低 、轧制速度过快或过慢等原因造 成。应控制好轧制温度和速度, 确保板带钢的质量。
THANK YOU
质量检测的方法与设备
化学分析法
通过化学实验手段对板带钢的化学成 分进行检测,常用的设备包括光谱仪 、质谱仪等。
无损检测法
在不损伤板带钢的情况下对其内部和 表面缺陷进行检测,如超声波检测、 X射线检测等,常用的设备包括超声 波探伤仪、X射线探伤机等。
物理性能测试法
利用物理实验手段对板带钢的物理性 能进行检测,如硬度、韧性、塑性等 ,常用的设备包括硬度计、冲击试验 机等。
精整过程中的缺陷与预防措施
表面缺陷
如划痕、裂纹、麻点等,需针对缺陷产生的 原因采取相应措施,如调整工艺参数、更换 轧辊或加强设备维护等。
尺寸偏差
通过调整设备和工艺参数,确保产品尺寸精度符合 要求。
冷轧板带材生产PPT课件

RAL
张力的选择
主要指平均单位张力q ,从理论上讲,不应超过带材
的屈服极限。大小视延伸不均匀情况、材质与加工硬化
程度以及板边情况。
根据经验,
z (0.1~0.6)s
一般在中间道次上,可取 (0.2~0.4)。s
为防止退火粘结,卷取张力可小一些,开卷张力则更
小,几乎可忽略。
q = Q/bh ; Q —— 总张力
(3)推拉式(卷间不焊接)——又称为半连 续酸洗机组,带钢通过酸洗机组时是不连续的。 一卷带钢通过酸洗机组处理完毕后,再处理另 一个钢卷。
轧制理论与工艺
RAL
推拉式酸洗工艺流程简图
上料
切头
轧制理论与工艺
RAL
①酸洗
酸洗目的:清除氧化铁皮,保证带钢表面质量 酸洗方式:~1960年前,硫酸酸洗,难回收
~1960年后,盐酸酸洗,可再生利用 (深槽酸洗-浅槽酸洗-推式酸洗) ~1990年后,湍流酸洗
湍流酸洗要点:浅槽,带钢在窄缝中运行,酸液运动方向与 带钢相反 , 形成湍流 . 效率高,酸洗时间短、质量好,省电, 事故处理容易
当加工硬化超过一定程度后,就不能再继续轧制, 需经软化热处理使之恢复塑性。每两次软化热处理 之间所完成的冷轧工作,通常称之为一个“轧程”。
n lnhln H
ln(1)
n-轧程数,取整; h-成品厚度; H-原料厚度; ε-允许的最大变形程度。
轧制理论与工艺
RAL
二. 采用工艺冷却和润滑 三. 冷却的目的:
RAL
11 冷轧板、带材生产
冷轧产品特点:
冷轧——在再结晶温度以下且产生加工硬化的轧制。 优点——尺寸精确、板形好、表面光滑、性能高。
汽车用钢需求趋势分析
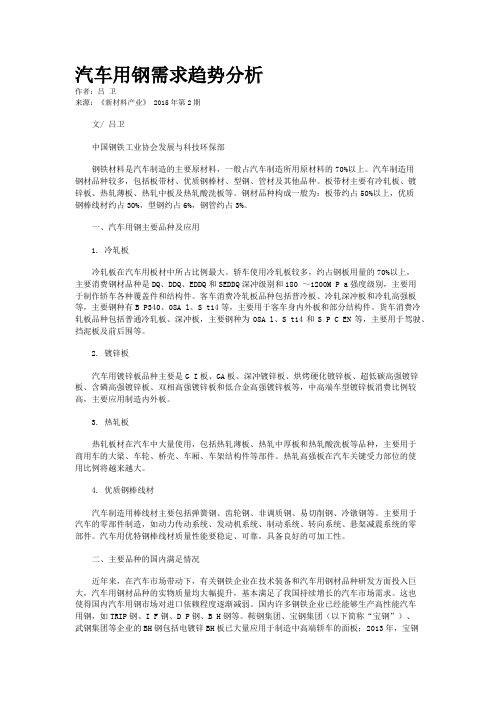
汽车用钢需求趋势分析作者:吕卫来源:《新材料产业》 2015年第2期文/ 吕卫中国钢铁工业协会发展与科技环保部钢铁材料是汽车制造的主要原材料,一般占汽车制造所用原材料的70%以上。
汽车制造用钢材品种较多,包括板带材、优质钢棒材、型钢、管材及其他品种。
板带材主要有冷轧板、镀锌板、热轧薄板、热轧中板及热轧酸洗板等。
钢材品种构成一般为:板带约占50%以上,优质钢棒线材约占30%,型钢约占6%,钢管约占3%。
一、汽车用钢主要品种及应用1. 冷轧板冷轧板在汽车用板材中所占比例最大。
轿车使用冷轧板较多,约占钢板用量的70%以上,主要消费钢材品种是DQ、DDQ、EDDQ和SEDDQ深冲级别和180 ~1200M P a强度级别,主要用于制作轿车各种覆盖件和结构件。
客车消费冷轧板品种包括普冷板、冷轧深冲板和冷轧高强板等,主要钢种有B P340、08A l、S t14等,主要用于客车身内外板和部分结构件。
货车消费冷轧板品种包括普通冷轧板、深冲板,主要钢种为08A l、S t14和S P C EN等,主要用于驾驶、挡泥板及前后围等。
2. 镀锌板汽车用镀锌板品种主要是G I板、GA板、深冲镀锌板、烘烤硬化镀锌板、超低碳高强镀锌板、含磷高强镀锌板、双相高强镀锌板和低合金高强镀锌板等,中高端车型镀锌板消费比例较高,主要应用制造内外板。
3. 热轧板热轧板材在汽车中大量使用,包括热轧薄板、热轧中厚板和热轧酸洗板等品种,主要用于商用车的大梁、车轮、桥壳、车厢、车架结构件等部件。
热轧高强板在汽车关键受力部位的使用比例将越来越大。
4. 优质钢棒线材汽车制造用棒线材主要包括弹簧钢、齿轮钢、非调质钢、易切削钢、冷镦钢等。
主要用于汽车的零部件制造,如动力传动系统、发动机系统、制动系统、转向系统、悬架减震系统的零部件。
汽车用优特钢棒线材质量性能要稳定、可靠,具备良好的可加工性。
二、主要品种的国内满足情况近年来,在汽车市场带动下,有关钢铁企业在技术装备和汽车用钢材品种研发方面投入巨大,汽车用钢材品种的实物质量均大幅提升,基本满足了我国持续增长的汽车市场需求。
2015年钢铁行业运行情况报告

2015年钢铁行业运行情况报告2015年,我国宏观经济下行,经济发展遇到了很多困难和挑战。
随着经济发展进入新常态,钢铁行业发展阶段也出现了新的变化,由原来的增量发展阶段向减量发展阶段过渡,由原来的规模扩张阶段向集约高效发展阶段过渡。
在严峻的市场形势下,国内钢材市场需求显著下降,钢铁行业产能过剩、市场供大于求矛盾突出,钢铁行业总体运行态势严峻。
一、2015年钢铁工业运行分析(一)钢铁行业运行基本情况1、我国粗钢产量34年来首次负增长据国家统计局统计,2015年全国生产粗钢8.0亿吨,同比下降2.3%。
从历史统计数据看,2015年粗钢年产量是自1982年以来的首次负增长。
2、全年生铁、粗钢、钢材产量情况据国家统计局统计,2015年全国生产生铁6.9亿吨,同比下降3.5%,生产粗钢8.0亿吨,同比下降2.3%,生产钢材11.2全国历年生铁、粗钢、钢材产量单位:亿吨(数据来源:国家统计局)亿吨,同比增长0.6%;平均日产粗钢220.2万吨。
2015年粗钢、生铁产量增幅由正转负,钢材产量增幅回落3.9个百分点。
3、从区域产量增减分析,多数省份减产,江苏增产超千万吨2015年全国六大区域粗钢产量仅华东小幅增产,西北、西南大幅减产;分省市看,统计的30个省市中仍然是江苏增产量最多,达到1037万吨。
山西、新疆、辽宁、云南、福建等11个省份减产超过100万吨;11个省市减幅超过10%。
产钢大省河北增产1.3%、辽宁减产6.7%、山东减产1.3%。
2015年,民营企业为增产主力,减产以国有企业为主。
4、从钢材品种结构分析,铁道用材、长材产量明显下降,但板带材、管材产量仍保持增长2015年,全国铁道用材、长材产量明显下降,但板带材、管材产量仍保持增长。
其中铁道用材中重轨、轻轨均大幅下降,长材中棒线材减幅较大;板材中冷轧薄板、特厚板增幅较大,管材中焊接钢管增幅较大。
5、粗钢产量占全球比重上升钢材分品种产量2015年,世界66个主要产钢国家和地区共生产粗钢16亿吨,同比下降2.9%;扣除中国内地后的世界粗钢产量约8亿吨,同比下降3.4%。
钢企智能工厂建设实施路径与商业模式思考
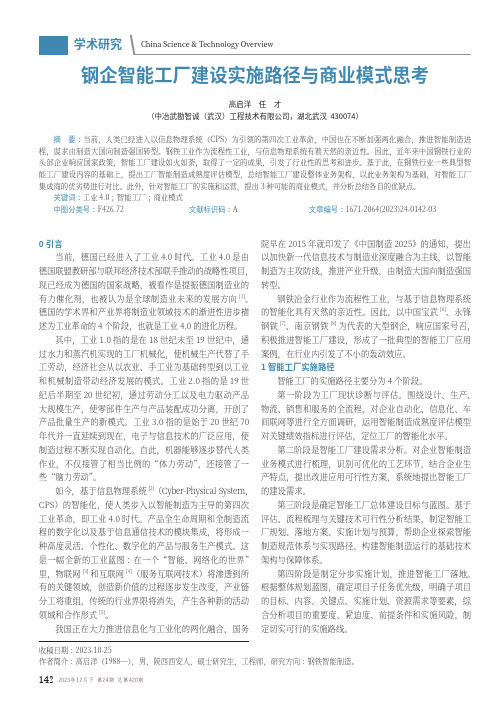
1422023年12月下 第24期 总第420期学术研究China Science & Technology Overview0引言当前,德国已经进入了工业4.0时代。
工业4.0是由德国联盟教研部与联邦经济技术部联手推动的战略性项目,现已经成为德国的国家战略,被看作是提振德国制造业的有力催化剂,也被认为是全球制造业未来的发展方向[1]。
德国的学术界和产业界将制造业领域技术的渐进性进步描述为工业革命的4个阶段,也就是工业4.0的进化历程。
其中,工业1.0指的是在18世纪末至19世纪中,通过水力和蒸汽机实现的工厂机械化,使机械生产代替了手工劳动,经济社会从以农业、手工业为基础转型到以工业和机械制造带动经济发展的模式。
工业2.0指的是19世纪后半期至20世纪初,通过劳动分工以及电力驱动产品大规模生产,使零部件生产与产品装配成功分离,开创了产品批量生产的新模式。
工业3.0指的是始于20世纪70年代并一直延续到现在,电子与信息技术的广泛应用,使制造过程不断实现自动化。
自此,机器能够逐步替代人类作业,不仅接管了相当比例的“体力劳动”,还接管了一些“脑力劳动”。
如今,基于信息物理系统[2](Cyber-Physical System,CPS)的智能化,使人类步入以智能制造为主导的第四次工业革命,即工业4.0时代。
产品全生命周期和全制造流程的数字化以及基于信息通信技术的模块集成,将形成一种高度灵活、个性化、数字化的产品与服务生产模式。
这是一幅全新的工业蓝图:在一个“智能、网络化的世界”里,物联网[3]和互联网[4](服务互联网技术)将渗透到所有的关键领域,创造新价值的过程逐步发生改变,产业链分工将重组,传统的行业界限将消失,产生各种新的活动领域和合作形式[5]。
我国正在大力推进信息化与工业化的两化融合,国务院早在2015年就印发了《中国制造2025》的通知,提出以加快新一代信息技术与制造业深度融合为主线,以智能制造为主攻防线,推进产业升级,由制造大国向制造强国转型。
十大工程主要内容

附件3:“十大工程”主要内容一、高强轻型合金材料专项工程工程目标:到2015年,关键新合金品种开发取得重大突破,形成高端铝合金材30万吨、高端钛合金材2万吨、高强镁合金压铸及型材和板材15万吨的生产能力,基本满足大飞机、轨道交通、节能与新能源汽车等需求。
主要内容:组织开发汽车用6000系铝合金板材,实现厚度0.7-2.0mm、宽幅1600-2300mm汽车铝合金板的产业化;加快完善高速列车用宽度大于800mm、直径大于250mm、长度大于30m的大型铝型材工艺技术,促进液化天然气储运用铝合金板材等重点产品产业化;积极开发航空航天用2000系、7000系、6000系、铝锂合金等超高强80-200mm铝合金中厚板及型材制品,复杂锻件及模锻件。
开发高强高韧、耐蚀新型钛合金和冷床炉熔炼、型材挤压技术,推进高性能Φ300mm以上钛合金大规格棒材,厚度4-100mm、宽度2500mm热轧钛合金中厚板,厚度0.4-1.0mm、宽幅1500mm冷轧钛薄板,大卷重(单重3吨以上)钛带等产品产业化。
推进低成本AZ、AM系列镁合金压铸,低成本AZ系列镁合金挤压型材和板材产业化,开展镁合金轮毂、大截面型材、宽幅1500mm以上板材、高性能铸锻件等应用示范。
二、高性能钢铁材料专项工程工程目标:到2015年,形成年产高品质钢800万吨的生产能力,基本满足核电、高速铁路等国家重点工程以及船舶及海洋工程、汽车、电力等行业对高性能钢材的需要。
主要内容:组织开发具有高强、耐蚀、延寿等综合性能好的高品质钢材。
重点推进核电压力容器大锻件508-3系列、蒸汽发生器690传热管、AP1000整体锻造主管道316LN等关键钢种的研发生产,实现核电钢成套供应能力。
提升超超临界锅炉大口径厚壁无缝管生产水平,形成年产50万吨生产能力。
加快开发船用特种耐蚀钢和耐蚀钢管,分别形成年产100万吨和10万吨生产能力。
开发高速铁路车轮、车轴、轴承等关键钢材,形成年产5万套生产能力。
第二代ABS铝合金及其生产工艺
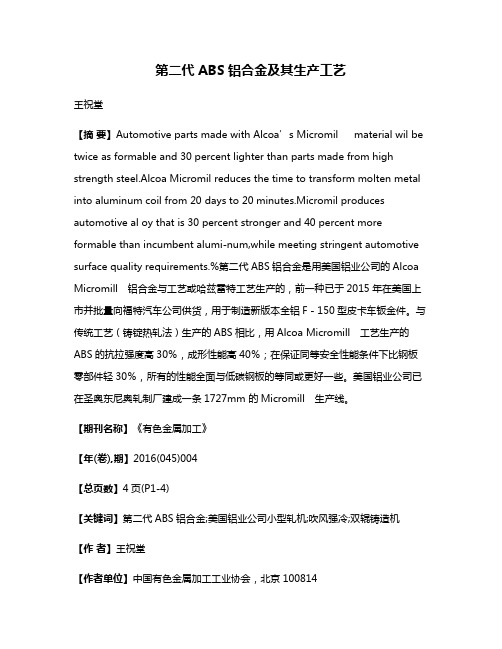
第二代ABS铝合金及其生产工艺王祝堂【摘要】Automotive parts made with Alcoa’s Micromil material wil be twice as formable and 30 percent lighter than parts made from high strength steel.Alcoa Micromil reduces the time to transform molten metal into aluminum coil from 20 days to 20 minutes.Micromil produces automotive al oy that is 30 percent stronger and 40 percent more formable than incumbent alumi-num,while meeting stringent automotive surface quality requirements.%第二代ABS铝合金是用美国铝业公司的Alcoa Micromill铝合金与工艺或哈兹雷特工艺生产的,前一种已于2015年在美国上市并批量向福特汽车公司供货,用于制造新版本全铝F-150型皮卡车钣金件。
与传统工艺(铸锭热轧法)生产的ABS相比,用Alcoa Micromill工艺生产的ABS的抗拉强度高30%,成形性能高40%;在保证同等安全性能条件下比钢板零部件轻30%,所有的性能全面与低碳钢板的等同或更好一些。
美国铝业公司已在圣奥东尼奥轧制厂建成一条1727mm 的Micromill生产线。
【期刊名称】《有色金属加工》【年(卷),期】2016(045)004【总页数】4页(P1-4)【关键词】第二代ABS铝合金;美国铝业公司小型轧机;吹风强冷;双辊铸造机【作者】王祝堂【作者单位】中国有色金属加工工业协会,北京100814【正文语种】中文【中图分类】TG339在全球都在呼吁节能减排的大背景下,汽车轻量化已成为各国的重点关注对象。
《板、带》精品资料

《板、带》精品资料1、板带材技术要求:尺寸精确板形好,表面光洁性能高。
2、试着从围绕降低外阻的角度分析板带轧机的演变和发展:通常降低外阻的主要技术措施就是减小工作辊直径,采取优质轧制润滑和采取张力轧制以及减小应力状态影响系数。
其中最主要最活跃的是减小工作辊直径,由此而出现了从二辊到多辊的各种形式的板、带轧机。
板带生产最初都是采用的二辊轧机,为了能以较少的道次轧制更薄更宽的钢板,必须加大轧辊的直径,才能有足够的强度和刚度去承受更大的压力,但这样使轧制压力急剧增大,从而使轧机弹性变形增大。
为了解决这个矛盾就出现了三辊劳特轧机和四辊轧机,它采用了小直径的工作辊以降低压力和增加延伸,采取大直径的支承辊以提高轧机的刚度和强度。
但是四辊轧机的工作辊不能太小,因为当直径小到一定程度时,其水平方向的刚度不足,轧辊会产生水平弯曲,使板形和尺寸精度变坏,甚至使轧制工程无法进行,为了更进一步的减小工作辊直径,随后又出现了12,20辊的轧机。
在轧制技术上出现了不对称轧机和异步轧机。
热轧润滑的发展降低了外摩擦的影响3、平面形状控制轧法(MAS轧制法、狗骨头轧制DBR):根据每种尺寸的钢板,在终轧后桶形平面形状的变化量,计算出粗轧阶段坯料厚度的变化量,以求最终轧出的钢板的平面形状矩形化。
4、整形MAS轧制法:轧制过程中为了控制切边损失,在整形轧制的最后一道中通过抬、压水平辊沿轧制方向给予预定的厚度变化,然后转钢横轧,利用宽展不均匀延伸,减少横轧时的平面桶形,最终纵轧时便可以使平面板型矩形化,得到侧面平整的矩形。
5、宽展MAS轧制法:轧制过程中为了控制头尾切损,在展宽轧制(横轧)的最后道次上沿轧制方向对未来的延伸面给予预定的厚度变化,旋转90度后进行延伸轧制,就可以控制头尾切损。
6、热装:将连铸坯或初轧坯在热状态下装入加热炉,热装温度越高,则节能越多。
热装对板坯的温度要求不如直接轧制严格。
直接轧制:板坯在连铸或初轧之后,不再入加热炉加热而只略经边部补偿加热,即直接进行的轧制。
板带钢生产教学ppt课件

张力的作用 防止带钢在轧制过程中跑偏(即保证正确对中轧制); 使所轧带钢坚持平直(轧后板形良好); 降低轧件的变形抗力,便于轧制更薄的产品 起适当调整冷轧机主电机负荷的作用; 自动调理带钢的延伸,使之均匀化。
4.4.3全延续冷轧机布置
4.4.4宝钢2030冷轧引见
• 2030冷轧概略 • 工艺流程 • 酸洗 • 五机架冷连轧 • 罩式退火 • 延续退火 • 涂层 • 镀锌 • 精整
4〕轧机刚度的影响
5〕轧制速度的影响
6〕光滑条件的影响
7〕轧辊偏心的影响
• 轧辊由于磨削不当或运用时磨损出现偏 心或成椭圆状时,轧后轧件出现纵向厚 度不均,厚度的动摇呈周期性。
厚度自动控制原理图
4.6板型控制技术
4.6.1垂直面轧辊弯曲系统
4.6.2程度面轧辊弯曲系统
• FFc轧机可以显著地降低边部减薄
• 轧机架为6个,废品热轧卷厚度为1.2-2.0mm, 消费才干为200万t/a。
• 消费线的平面布置设计见以下图
包钢csp车间平面图
ISP工艺(Inline strip Production)在线 热带消费工艺
• 该技术已于1992年1月在意大利阿维迪钢厂建 成投产,设计才干为50万t/a。
• ISP技术第一个实现了在线厚度紧缩,并有一 整套设备能保证铸坯温度均匀以及铸坯终轧前 的在线再加热。
4.1.4板带轧机及布置
轧辊在轧机机架中的陈列方式
带偏心辊轧机机架类型
行星轧制
轧机按轧辊轴线的方向分类
中厚板消费布置
薄板连铸连轧
4.1.5 关于板带钢轧制中的最小可轧厚度问题
钢铁行业规范条件(2015年修订)

附件1:钢铁行业规范条件(2015年修订)一、总则(一)为进一步加强钢铁行业管理,建立统一开放、竞争有序的市场体系,强化环保节能,优化产业结构,促进钢铁产业转型升级,根据《国务院办公厅关于进一步加大节能减排力度加快钢铁工业结构调整的若干意见》(国办发〔2010〕34号)和《国务院关于化解产能严重过剩矛盾的指导意见》(国发〔2013〕41号)、相关法律法规及标准,对《钢铁行业规范条件(2012年修订)》进行修订,制定本规范条件。
(二)本规范条件适用于中华人民共和国境内(港澳台地区除外)的钢铁联合、冶炼企业(以下简称“钢铁企业”),包括国发〔2013〕41号发布之后建设、改造完成的冶炼产能或主体工艺装备发生较大变化的钢铁联合、冶炼企业(以下简称“新建、改造钢铁企业”)。
(三)本规范条件强化了环保节能约束,对新建、改造钢铁企业提出了要求,强化了对钢铁企业的事中事后监管,是钢铁企业的基本条件。
(四)符合本规范条件的企业,作为相关政策支持的基础性依据,不符合规范条件的企业应按照规范条件要求进行整改。
经整改仍不能达到规范条件要求的企业,各地要综合运用法律法规、经济和市场手段,推动其退出或转型发展。
二、规范条件(一)产品质量1.钢铁企业须建立完备的产品生产全过程质量保证制度和质量控制指标体系,具有产品质量保障机构和检化验设施,保持良好的产品质量信用记录,近两年内未发生重大产品质量问题。
2.钢铁企业产品须符合国家、行业、地方标准。
严禁生产Ⅱ级以下螺纹钢筋(直径14毫米及以下的Ⅱ级螺纹钢除外)、热轧硅钢片等《部分工业行业淘汰落后生产工艺装备和产品指导目录(2010年本)》(工产业〔2010〕第122号)中需淘汰的钢材产品。
3.严禁伪造他人厂名、厂址和商标,以次充好以及伪造、不开发票销售钢材等扰乱市场秩序的行为。
(二)工艺与装备1.严格控制新增钢铁生产能力。
新建、改造钢铁企业须按照国发〔2013〕41号和《工业和信息化部关于印发部分产能严重过剩行业产能置换实施办法的通知》(工信部产业〔2015〕127号)要求,制定产能置换方案,实施等量或减量置换,在京津冀、长三角、珠三角等环境敏感区域,实施减量置换。
板带材工艺废品种类及产生原因

单机架平整机来料和平整时产生的主要缺陷及其消除的方法。
1.扁卷产生原因:前工序卷曲张力过小,或者是吊车在放置时过猛而形成。
消除方法:发现此类钢卷不宜时间过长,否则会越来越严重,必须尽快平整,平整是加倍小心,低速平整,增加开卷张力。
2.边部裂开或边部损伤产生原因:来料边裂或吊车夹钳损伤钢卷边部造成,进入机架容易压伤辊子。
消除方法:发现此类缺陷,钢卷必须慢速平整,并将边部损伤部位剪掉,或改轧制的规格生产,使边部多切边。
3.溢出边粘结:产生原因::前到工序卷曲时因棍子倾斜或跑偏装置失灵出现带钢跑偏而形成溢出边,在罩式炉退火时压折而形成粘结,另外对流板变形或为倒角也会将钢卷边部压粘,在平整时易撕裂断带。
消除方法:在粘结部位用粉笔做好记号,开卷时低速平稳。
4.中部面粘结和条状粘结:产生原因:钢卷在罩式退火时温度过高,局部卷层平面压力过大,会造成卷层层间彼此粘结,轧钢卷曲张力过大,层间压的过紧,加热时板面容易粘结,轧辊(轧钢)的粗糙度过小,板面容易形成粘结,轧钢喷嘴堵塞导致局部膨胀,使钢带变形不均,退火后生产条状粘结,以上这些现象在开卷时,发出撕裂的响声,严重时会撕裂断带。
消除方法:低速平稳,适当增加开卷张力,遇到边部撕裂,可剪:月牙弯再平整。
5.压痕:产生原因:在机架的一些辊上粘有铁屑片等杂物,压入带钢表面形成的。
它周期性出现在钢带表面上,量其距离可断,断是在哪个棍子造成的。
消除方法:找出那个辊子产生的然后用砂纸或手动砂轮摩掉,并用汽油清洗个辊子表面,钢卷两边有赃物也要清洗掉。
6.边浪:产生原因:在轧辊两端压力过大或辊面有油造成延伸大,轧辊两端磨损厉害,错误使用弯辊。
消除方法:随时检查是否支撑辊漏油,不断清洗轧辊及时换辊,调好合适的压力,采用正弯辊操作。
7.中间浪:产生原因:工作辊凸度太大,错误使用弯辊方式,压力过小。
消除方法:严格控制来料温度,采用负弯辊操作,加大轧制压力,以经出现的中间浪可通过再次平整消除。
- 1、下载文档前请自行甄别文档内容的完整性,平台不提供额外的编辑、内容补充、找答案等附加服务。
- 2、"仅部分预览"的文档,不可在线预览部分如存在完整性等问题,可反馈申请退款(可完整预览的文档不适用该条件!)。
- 3、如文档侵犯您的权益,请联系客服反馈,我们会尽快为您处理(人工客服工作时间:9:00-18:30)。
轧辊辊身、辊颈及接轴叉头等的强度条件—三个危险 断面
3
1)二辊、三辊轧机:最大轧制压力取决于轧辊辊身强度。
0.4 D Rb Pyx L l 0.5B
式中:D、L、l——轧辊辊身直径、长度、辊颈长度。 Rb——轧辊许用弯曲应力 B——轧辊宽度,取 Bmin
轧制工艺
2)四辊轧机:
由于支撑辊辊身强度很大,最大允许轧制压力取决于 支撑辊辊颈强度和轴承寿命
轧制工艺
二、 在保证操作稳定的条件下提高质量
当辊身为圆柱形,凸度为零时,若 钢板由轧制中心线偏移a的距离,
钢板轧制定心条件
则轧辊两端轴承上所受的力就不再
相等,两边牌坊及零件的弹性变形 也不再相等,使轧辊轴线不再平行, 使轧辊产生了倾斜。通过计算可求 出由于钢板偏移a的距离而引起的
钢板两侧厚度差Δ1为:
10 板带材轧制制度的确定
板带材轧制制度主要包括:压下制度、速度制度、温度 制度、张力制度及辊型制度等, 其中主要是压下制度(它必然涉及速度、温度和张力制 度)和辊型制度,它们决
总的来说——安全、高产、优质、低耗 具体的说:在保证设备安全的条件下,尽量提高产量。 在操作稳便的条件下,提高质量。
按支撑辊辊颈强度
0.4 Rb d Pyx l
3
式中:
d、l —— 支撑辊辊颈直径、长度
轧制工艺
3) 计算最大允许轧制力矩
除取决于电机额定力矩外,从机械设备的角度则通 常取决于传动辊的辊颈强度及万向接轴的扁头和叉头强 度。按传动辊辊颈许用扭转应力计算允许轧制压力:
0.4dc 3[ ] Pyx Rh
轧制工艺
(3)压下规程的制定步骤
a.在满足△hmax ≤D(1-cos)条件(咬入条件)下按经 验分配△hi和 i。 b.制定速度制度、计算轧制时间及轧制节奏。 c.确定轧制温度。 d.计算Pi、Mi。 e.校核轧辊强度及电机能力。 f.按“原则要求”进行修正和改进。
轧制工艺
10.2.2 中厚板轧机压下规程设计
若轧件不产生偏移,辊缝应呈凸透镜形状,即钢板的形状呈
凸透镜形状,凸度越大,操作越稳定,此时钢板横向厚差增 大,所以要寻找最小凸度值。 假定两辊的凹度并到一个辊上,另一轧辊呈圆柱形。钢板移 动a的距离,将使偏移侧的压下率增加,该作用正好与前面偏 移的作用相反。显然只有二者影响互相抵消,或前者比后者 大时,才能起到自动定心作用。
轧制工艺
10.1 制定板带轧制制度的原则和要求
一、在设备能力允许的条件下尽量提高产量
a.提高产量的途径
轧机的小时产量 式中:G——坯重 , A=3600GbK1/T b——成材率 ,
K1 ——轧机利用系数, K1=A实/A理 , T——轧制节奏时间(s),
T (t zhi t ji )
轧制工艺
注意:1)必须同时满足过载和发热条件。
2)当过载不能满足时,可重新分配△hi使Mmax↓
但发热不能满足时,必须增加轧制道次使Mi ↓,并使 T↑。 (4)板形控制条件的限制
影响板形的主因——轧辊的弹性变形、热凸度、磨损。 为了保证板形良好,在热轧的精轧阶段和冷轧时,必须使 轧制压力逐道减少而使压下率逐道减少。
轧制工艺
(2)压下规程制定的指导思想 1)根据压下规程的制定原则和要求,制定出一 个原则指导性的初步压下规程; 2)在实际操作中,灵活调整,修正。
轧制工艺
(3) 压下规程的制定方法
1)理论方法:从制定压下规程的原则要求出发,按予设条件 通过理论(数学模型)计算或图表以求最佳规程。 由于变化因素太多且难测、难控、往往与实际不符,在 人工操作情况下难以实现,随着检测技术和计算机技术的发 展、计算机优化设计已势在必行。 2)经验方法:参照现有类似轧机的压下规程制定,即根据经验 资料进行压下分配及校核计算。该方法稳妥、可靠、但不是最 佳。 常用的经验法:压下量或压下率( △hi 或i )分配法、 能耗负荷分配法等。
则最大允许轧制力矩
M yx Pyx Rh =0.4d [ ]
3
式中: dc——传动辊辊颈直径、通常为工作辊辊颈; []——许用扭转应力[]=(0.5—0.6) Rb
轧制工艺
(3)电机能力的限制——过载能力、发热能力
1)过载校核 Mmax≤K Mer (Nmax ≤KNer) 式中: Mer 、 Ner——主电机额定力矩、额定功率。 K——过载系数, 直流电机 2.0~2.5 ,交流电机 2.5~3.0
PB 2 H KA2
结论:(1 )中厚量与轧制压力及钢板宽度成正比,而与机架的刚 度及压下螺丝中心线间的距离的平方成反比。 (2)为提高钢板厚度精度(↓)而又使操作稳便,必须提 高轧机刚度k或降低轧制压力P (或↓△h )。
注意:a.中厚法操作仅适用于无张、无导板夹持的自由轧制情况。
轧制工艺
先立辊减边,由宽度1600,减至1550, 然后轧制,
25 ↗ 90°25 20 90 65 12 10 7 4 2.5 1.5 115 45 33 23 16 12 9.5 8
注意
(1)除立辊轧边外,单机布置必须为奇数道次出轧机
(2) △hi ≤ △hmax =D(1-cos允)
(3)为了保证板形良好,精轧道次 i应逐渐减少,为了 便于人工操作,除成品或成品前道次△hi应取整。
B 2 a 2 y yt W 1 B
2
令a→0,即偏移的距离极小时,则有
PB2 y yt W 2 KA
轧制工艺
为使轧件能自动定心所必须的最小原始辊型值为:
或者说,当原始辊型W一定时,所必须的轧辊弯曲最小挠度值为:
轧制工艺
假定两辊的凹度并到一个辊上,另一轧辊呈圆柱形。 由图△2与△1方向相反,只要△1+△2=0 或△2>△1 轧件可 自动定心。 ∵ 求出△2既可求得轧件自动定心条件
轧制工艺
设轧辊为凹辊型,其辊型曲线为 抛物线,则在轧件宽度上中心处 的辊型凹度t为:
t y yt W
式中,y、yt、W分别为工作辊在轧件
i 1
n
Tzh,tji,n——纯轧时间、间隙时间、轧制道次 。 年产量 A年=AT年 ……… T
年——轧机年工作小时
轧制工艺
途径:要提高年产量A年,就要提高G 、b 、k1 、 T年 、 减少T。 (1)提高G 当G ↑ 高。 A↑ n↑—T↑—A ↓ G 不能无限提高,要合理提
(2)提高b:降低金属消耗——烧损、切损、轧废、酸 损等。提高产品的合格率——尺寸、板形、表面、性能
4 PaB 1 2 KA
式中 P——轧制压力,kN;B、a——钢板宽度及钢板由轧制中心线偏移的距离, mm; A—— 两压下螺丝轴线之间的距离,mm;K—— 轧机刚度(不包括轧辊),kN/mm。
轧制工艺
在轧制过程中一旦形成偏移,只能扩大,不能消除,压下不 等势必引起两侧出辊速度产生差异,结果造成镰刀弯。
轧制工艺
(3)提高K1:操作技术、管理水平、机械化、自动化 程度,现代化轧机取1 。 (4)提高T年:减少计划和非计划停工时间。 (5)降低T: 1) 降低Tzh——↑v——轧制制度。 减少tji :主辅机速度、操作技术、工艺要求。 ↑ —— ≤ P↑—— P ≤ Pyx
2)减少n :↑△h
PB 2 W y yt KA 2
PB 2 y yt W 2 KA
由最小挠度值便可求出为产生此挠度所必须的最小轧制压力,进而确定出 为使轧件能自动定心所必须的最小压下量。这就是所谓的“中厚法”或 “中高法”。由上式可以推知,这个最小中厚量,即板凸度至少应该为:
PB 2 H y y t W KA 2
10.2 压下规程或轧制规程设计(设定)
10.2.1 压下规程内容、制定方法、步骤
(1)压下规程中心内容:变形制度——即确定轧制方法、轧 制道次及道次压下量,最终确定各道次辊缝值。 各道次的轧制速度、轧制温度及前后张力制度的 确定及原料尺寸的合理选择都是以压下制度为核心展开
的,反过来它们也影响压下制度。
8.9.10道n1 =60r/min 、 8.9道n2=20r/min 10道 n2 = n1 =60r/min e. 确定每道次轧制延续时间tz: 计算 tz(T), 确定轧制温度t ℃
tz=tzh + t0
tzh =t1+t2 t1 =(l-l2)/v1 v1 =Dn1/60 减速段长度 l2 =v2 t2
M↑—— M ≤ KMer ; Mjum ≤ Mer 板形↓——板形条件 可逆式轧机:提高压下量以缩减道次 连轧机:合理分配压下并提高轧制速度
轧制工艺
b.从设备能力着眼,限制压下量和速度提高的 主要因素: (1)咬入条件限制; (2)轧辊强度条件的限制:轧辊辊身、辊颈及 接轴叉头等的强度条件 ; (3)电机能力的限制。 (4)板形控制条件的限制
轧制工艺
解:a.轧制方法 (1)因为是初轧坯、纵向性能优于横向,因此采 用横轧法保证纵横性能均匀 (2)但坯长2200mm小于成品宽度2900mm故需 纵轧到成品宽度后转钢90°横轧到底。
故本规程采用除鳞、立辊侧压一道、纵轧一 道使板坯长度等于钢板宽度,然后转钢90 ° 、 横轧到底。
轧制工艺
b.按经验分配△hi
中厚板轧机多为四辊可逆式轧机,对于可逆式轧
机采用的压下规程设计方法也适于热连轧的粗轧机组。
根据中厚板轧制的特点,粗轧阶段的前几道次主
要应校核咬入能力及最大扭转力矩的限制条件,而精 轧阶段则主要应考虑板形尺寸及性能质量的限制,应 使轧制力逐道减小。
轧制工艺
1)经验法,(见教材p309) 例:在930~980/ 1660~1800×4200mm 单机 架四辊可逆式轧机上轧制8×2900×17500mm Q235 钢板、坯料规格为115×1600×2200mm 初轧坯。设有立辊、高压水除鳞装置; t开=1200℃横轧,t横开=1120℃、 Pyx=4200×104N 、Myx=2×224×104N .m 主电机功率NH=2×4600kw;V=0~2~4m/s. 锻钢轧辊、油膜轴承。试制定其压下规程(从横 轧开始)。