CMP后的晶圆的测量和评估方法研究
CMP后的晶圆清洗过程研究

作 者 简 介 : 伟 锋(9 5)男 , 张 17 一, 陕西 武 功 人 , 程 师 , 丰 要 从 事 、 体 设备 研 发 工 作 。 工 现 导
维普资讯
-
电 子 工 业 毫 用 设 备
・
CM P 与 清 洗 ・
剂
陷, 另一 部分 缺 陷包 括 化学 玷 污 , 离子 玷 污 , 晶片表
面金 属 的腐蚀 。
晶片 表 面 的 玷 污 主 要 有 两 种 , 微 粒 玷 污 和 金
属杂 质 。微 粒 玷 污 主 要 来 源 于 抛 光 垫 磨 损 所 牛 成 的残 留微 粒 , 是抛 光 液 中 的悬 浮 微 粒 。 属 杂 质 或 金 主 要 与 金 属 化 学 反应 和 电化 学 以及 抛 光 机 操 作 环
存 在 , C (h mi l c a i l lnr ain S 在 MP c e c h nc a ai t )l a me ap z o  ̄
艺中, 必然 会 引入 表 面缺 陷和玷 污 。在 晶片表 面 全
局 平 坦化 以后 , 必须 进 行 有 效 的清洗 来 实 现 C MP 工 艺 的优 点 。 了确 保得 到进 一步 金 属化所 需 要 的 为 无 缺 陷 无 玷 污 晶片 表 面 , MP后 清 洗 工 艺 是 必 需 C
Ab t a t Th o tCM P t c n l g s r c : ep s— e h o o y i i o tn swh s P p o e s S e e o i g Th a e o u s mp ra t o eCM r c s ’ v l p n . ep p r c s a d f
S u y o s-CM P Cla r c s t d n Po t e n P o es
半导体光刻中晶圆缺陷问题的研究

半导体光刻中晶圆缺陷问题的研究在半导体制造过程中,光刻技术被广泛应用于芯片的制造。
光刻是通过使用光源、掩模和投影透镜等工具,在晶圆表面上定义形状和位置的一种方法。
然而,光刻过程中晶圆缺陷问题是一项非常重要的研究课题。
晶圆缺陷问题对芯片制造质量以及设备可靠性等方面都有着重要影响。
晶圆缺陷指的是晶圆表面或内部存在的缺陷,例如微裂纹、气泡、颗粒和缺陷等。
这些缺陷可能导致芯片器件性能不稳定,甚至失效。
因此,研究晶圆缺陷问题对于提高芯片制造质量和设备可靠性至关重要。
首先,光刻过程中晶圆缺陷的形成机理是研究的重点之一。
晶圆缺陷的形成与光刻过程中的物理和化学反应有关。
例如,光刻胶在曝光和显影等过程中会释放出化学物质,这些化学物质会对晶圆表面产生腐蚀和侵蚀作用,从而引起缺陷的形成。
此外,光刻过程中的光能量和热能也会对晶圆材料产生应力,导致晶圆表面产生应变,从而引发缺陷的生成。
因此,研究晶圆缺陷的形成机理,可以帮助我们更好地理解光刻过程中的缺陷生成机制,从而采取相应的措施来减少晶圆的缺陷。
其次,研究晶圆缺陷问题还包括缺陷检测和监控。
在光刻过程中,及时发现和识别晶圆上的缺陷非常重要。
因此,需要开发出高分辨率的缺陷检测设备和技术,能够实现对晶圆表面和内部的缺陷进行快速、准确的检测。
传统的缺陷检测技术包括光学检测、扫描电子显微镜(SEM)和原子力显微镜(AFM)等。
但是,由于晶圆上的缺陷数量和尺寸在不断减小,传统的检测技术已经很难满足需求。
因此,研究如何开发出更高分辨率、更灵敏的缺陷检测设备和技术,成为一个重要的课题。
最后,研究晶圆缺陷问题还需要探索缺陷修复和缺陷防治的方法。
一旦在晶圆上发现了缺陷,那么将如何进行修复是一个非常重要的问题。
目前,常见的缺陷修复方法包括化学机械抛光(CMP)、激光修复和等离子修复等。
这些方法可以将晶圆上的缺陷进行修复,从而提高芯片的制造质量。
此外,研究如何预防晶圆缺陷的生成也是非常重要的。
cmp模组工艺技术
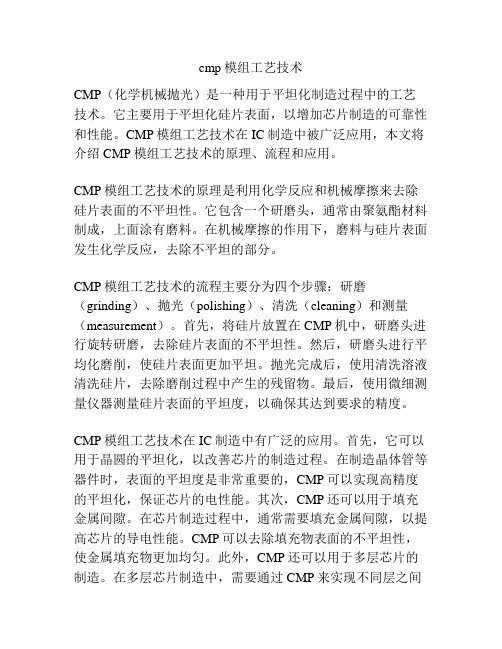
cmp模组工艺技术CMP(化学机械抛光)是一种用于平坦化制造过程中的工艺技术。
它主要用于平坦化硅片表面,以增加芯片制造的可靠性和性能。
CMP模组工艺技术在IC制造中被广泛应用,本文将介绍CMP模组工艺技术的原理、流程和应用。
CMP模组工艺技术的原理是利用化学反应和机械摩擦来去除硅片表面的不平坦性。
它包含一个研磨头,通常由聚氨酯材料制成,上面涂有磨料。
在机械摩擦的作用下,磨料与硅片表面发生化学反应,去除不平坦的部分。
CMP模组工艺技术的流程主要分为四个步骤:研磨(grinding)、抛光(polishing)、清洗(cleaning)和测量(measurement)。
首先,将硅片放置在CMP机中,研磨头进行旋转研磨,去除硅片表面的不平坦性。
然后,研磨头进行平均化磨削,使硅片表面更加平坦。
抛光完成后,使用清洗溶液清洗硅片,去除磨削过程中产生的残留物。
最后,使用微细测量仪器测量硅片表面的平坦度,以确保其达到要求的精度。
CMP模组工艺技术在IC制造中有广泛的应用。
首先,它可以用于晶圆的平坦化,以改善芯片的制造过程。
在制造晶体管等器件时,表面的平坦度是非常重要的,CMP可以实现高精度的平坦化,保证芯片的电性能。
其次,CMP还可以用于填充金属间隙。
在芯片制造过程中,通常需要填充金属间隙,以提高芯片的导电性能。
CMP可以去除填充物表面的不平坦性,使金属填充物更加均匀。
此外,CMP还可以用于多层芯片的制造。
在多层芯片制造中,需要通过CMP来实现不同层之间的平坦化。
总之,CMP模组工艺技术是一种在IC制造中广泛应用的工艺技术。
它利用化学反应和机械摩擦来实现硅片表面的平坦化,以提高芯片的可靠性和性能。
通过研磨、抛光、清洗和测量等步骤的组合,CMP可以实现高精度的平坦化,并在硅片制造中发挥着重要的作用。
CMP中抛光垫和晶圆接触状态的研究

CMP中抛光垫和晶圆接触状态的研究化学机械抛光(Chemical mechanical polishing,CMP)是芯片制造过程中最重要的工序之一,是目前保证亚微米集成电路芯片同时保持整体和局部平坦化的唯一手段。
随着集成电路特征尺寸的减小和结构层数的增加,对CMP全局平坦化效果的要求也越来越高。
但是,目前对CMP机理的认识还不够充分,特别是对CMP中抛光垫和晶圆不同接触状态下晶圆-磨粒-抛光垫之间相互作用的细节、各接触状态的存在条件及材料去除差异缺乏较为深入的理解。
因此,本文对此展开研究,为CMP的机理研究提供基础的理论指导。
首先,通过实验探究了抛光工艺参数对CMP性能的影响。
详细叙述了 CMP的实验步骤和实验中用到的仪器。
分别研究了抛光压力、抛光速度以及抛光时间对抛后晶圆表面质量和抛光过程中晶圆表面材料去除率(Material removal rate,MRR)的影响。
结果表明:本实验中MRR对压力、速度的依赖关系与Preston提出的线性关系以及Tseng等人提出的比例关系之间均存在较大偏离。
其次,建立了抛光垫与晶圆之间的接触模型。
分析求得微凸体弹塑性变形阶段的接触面积和接触压力。
结果表明:两者均实现了在临界点处光滑、连续的变化特征,尤其是本文建立的接触压力模型在弹塑性阶段单调递增,更为符合实际情况。
在此基础上,综合考虑抛光垫表面微凸体的完全弹性变形、弹塑性变形以及完全塑性变形,建立晶圆与抛光垫之间的接触模型,求得接触界面处的真实接触面积和平均接触压力。
然后,研究了晶圆和抛光垫不同接触状态下晶圆-磨粒-抛光垫的相互作用规律。
根据各接触状态下晶圆-磨粒-抛光垫的接触特征、几何特征以及力学平衡等关系,计算出晶圆和抛光垫不同变形状态下磨粒压入晶圆和抛光垫的深度、磨粒与晶圆和抛光垫接触圆的半径以及单个磨粒上的力等变量;分析了接触界面处磨粒和抛光垫与晶圆接触的面积、载荷分配;探讨了磨粒变形对CMP的影响:通过计算磨粒的变形量,给出了修正因子,从而更加精确地计算出磨粒压入晶圆表面的深度。
cmp 粗糙度
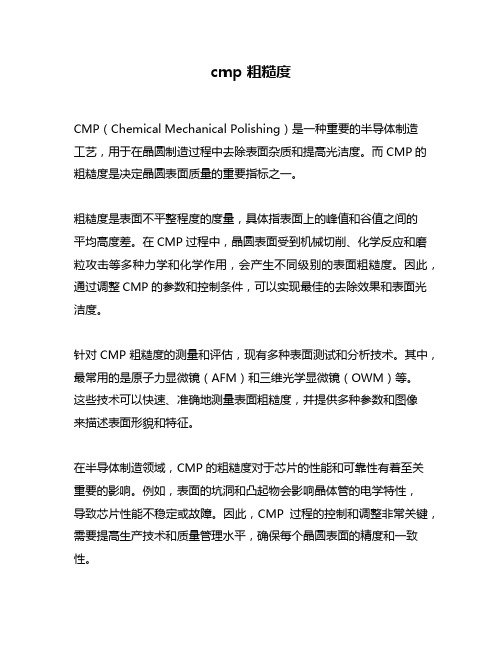
cmp 粗糙度
CMP(Chemical Mechanical Polishing)是一种重要的半导体制造
工艺,用于在晶圆制造过程中去除表面杂质和提高光洁度。
而CMP的粗糙度是决定晶圆表面质量的重要指标之一。
粗糙度是表面不平整程度的度量,具体指表面上的峰值和谷值之间的
平均高度差。
在CMP过程中,晶圆表面受到机械切削、化学反应和磨粒攻击等多种力学和化学作用,会产生不同级别的表面粗糙度。
因此,通过调整CMP的参数和控制条件,可以实现最佳的去除效果和表面光洁度。
针对CMP粗糙度的测量和评估,现有多种表面测试和分析技术。
其中,最常用的是原子力显微镜(AFM)和三维光学显微镜(OWM)等。
这些技术可以快速、准确地测量表面粗糙度,并提供多种参数和图像
来描述表面形貌和特征。
在半导体制造领域,CMP的粗糙度对于芯片的性能和可靠性有着至关重要的影响。
例如,表面的坑洞和凸起物会影响晶体管的电学特性,
导致芯片性能不稳定或故障。
因此,CMP过程的控制和调整非常关键,需要提高生产技术和质量管理水平,确保每个晶圆表面的精度和一致性。
总的来说,CMP的粗糙度是半导体制造过程中一个非常重要的指标,它直接关系到芯片性能和可靠性。
通过采用合理的测量和控制技术,可以有效提高CMP的效率和质量,促进半导体产业的快速发展。
电脑芯片制造中的晶圆质量分析与提升技术

电脑芯片制造中的晶圆质量分析与提升技术在电脑芯片的制造过程中,晶圆质量是影响芯片性能和可靠性的一个重要因素。
晶圆质量的提升是电脑芯片制造过程中的关键问题之一。
本文将介绍晶圆质量分析与提升技术的相关内容,探讨如何优化晶圆质量以提高芯片的性能和可靠性。
一、晶圆质量分析技术1. 光学检测技术光学检测技术是一种常用于晶圆质量分析的非接触式方法。
通过使用光学设备,如显微镜和光栅仪,可以观察和分析晶圆表面的缺陷、杂质等问题。
这些缺陷和杂质可能会对芯片的性能和可靠性产生负面影响。
2. 微观结构分析技术微观结构分析技术可以通过对晶圆的截面进行观察和分析来评估晶圆的质量。
常见的技术包括扫描电子显微镜(SEM)和透射电子显微镜(TEM)。
这些技术可以提供更加详细的晶圆内部结构和缺陷信息,帮助分析和改善晶圆质量。
3. X射线衍射分析技术X射线衍射分析技术可以通过照射晶圆并测量衍射图案来研究晶圆的晶体结构。
这项技术可以评估晶圆的晶格参数、晶体缺陷以及杂质含量等信息。
通过分析X射线衍射图案,可以及时发现晶圆中的结构问题,并采取相应的措施进行改善。
二、晶圆质量提升技术1. 晶圆清洁技术晶圆清洁是保证晶圆表面质量的重要措施。
采用合适的清洗剂和清洗工艺,可以有效去除晶圆表面的杂质和污染物,提高表面质量。
常见的晶圆清洁技术包括化学机械抛光(CMP)和去离子水清洗等。
2. 晶圆热处理技术晶圆热处理技术是一种通过加热和冷却过程对晶圆进行处理以改善其质量的方法。
常见的热处理技术包括退火和淬火等。
这些技术可以降低晶圆内部的残余应力、改善晶圆的结晶形态,提高晶圆的质量和可靠性。
3. 晶圆质量监控技术晶圆质量监控技术可以对制造过程中的各个环节进行实时监测和控制,及时发现和解决可能影响晶圆质量的问题。
常用的监控技术包括晶圆尺寸测量、表面缺陷检测和晶圆薄度均匀性测量等。
这些技术的应用可以帮助制造商及时发现问题并采取措施改进生产工艺,提高晶圆的质量。
基于多电脑的晶圆像质量评估算法在检测中的优势研究

基于多电脑的晶圆像质量评估算法在检测中的优势研究随着科技的不断发展,半导体行业的需求也在不断增加。
随着这种需求的增加,晶圆制造商也不断地寻求更加高效且安全的生产方式。
因此,现在越来越多的制造商正在转向使用基于多电脑的晶圆像质量评估算法来检测晶圆的质量。
在这篇文章中,我们将探讨这种算法是如何改变并优化晶圆制造业的。
首先,我们需要了解什么是晶圆像质量评估算法。
这种算法是一种先进的技术,利用电算力和大规模计算技术来检测晶圆的质量。
这种技术是基于多电脑的,因此可以高效地处理大量的数据。
使用这种技术,制造商可以快速发现晶圆中存在的任何缺陷。
使用基于多电脑的晶圆像质量评估算法的好处之一是,它可以检测出在人类无法察觉的微小缺陷。
这些缺陷可能会在制造过程中被忽略掉。
然而,这种技术可以捕捉这些缺陷,因此,可以确保制造商生产出的晶圆是优质的且符合行业标准的。
在传统的评估方法中,这些微小缺陷常常被忽略掉,从而导致质量下降和生产成本升高。
此外,使用基于多电脑的晶圆像质量评估算法,制造商可以更快地确定晶圆的缺陷,并采取相应的应对措施。
在制造业中,时间是非常重要的。
过长的生产周期会导致低效率,并可能使制造商丧失市场竞争力。
因此,使用基于多电脑的晶圆像质量评估算法可以显著提高制造商的生产速度,减少生产周期,从而提高整个生产线的效率。
最后,使用基于多电脑的晶圆像质量评估算法可以显著降低生产成本。
在传统的评估方法中,检测过程需要耗费大量的时间和人力资源,因此成本显著增加。
使用基于多电脑的晶圆像质量评估算法,可以在短时间内处理大量的数据,并减少了人力成本。
综上所述,基于多电脑的晶圆像质量评估算法是一种非常优秀的技术,可以显著提高晶圆制造业的质量和效率,并显著降低生产成本。
通过使用这种技术,制造商可以发现并解决缺陷问题,进一步提高晶圆制造业的标准。
因此,我们强烈建议在生产中使用这种技术,并相信它将为您的公司带来丰厚的回报。
晶圆像质量评估的多电脑协同处理算法及性能优化研究

晶圆像质量评估的多电脑协同处理算法及性能优化研究随着半导体工业的不断发展,晶圆像质量评估成为了一项关键工作。
在晶圆制造的过程中,通过对晶圆表面形貌的分析,可以评估晶圆的质量,并及时发现潜在问题,以保证最终的产品质量和稳定性。
然而,由于晶圆表面形貌数据量庞大,单机处理效率低下,因此需要使用多电脑协同处理算法来进行晶圆像质量评估,并进一步优化性能。
一、晶圆像质量评估的多电脑协同处理算法晶圆像质量评估需要对晶圆表面形貌进行处理和分析。
在传统的单机处理方式下,由于数据量大、算法复杂,处理时间长、效率低下,这就要求使用多电脑协同处理算法。
多电脑协同处理算法主要包含三个步骤:1. 数据分割:将待处理的晶圆图像分割成多个小部分,以便同时在多台计算机上并行处理。
2. 并行处理:将分割后的小部分晶圆图像同时进行计算和分析,分别在多个计算机上执行,并将计算结果合并。
3. 结果合并:将多个计算机处理后的结果进行合并,最终得到整个晶圆的表面形貌数据和质量评估结果。
基于多电脑协同处理算法,可以快速准确地评估晶圆的表面形貌质量,便于快速检查晶圆制造过程中的质量问题。
二、性能优化的研究多电脑协同处理算法虽然可以很好地解决单机处理效率低下的问题,但其性能仍需进一步优化。
针对多电脑协同处理算法中存在的瓶颈问题,本文提出了以下性能优化措施:1. 任务分配算法优化:通过智能化的任务分配算法,将晶圆表面形貌数据平均分配给每个计算机,以提高系统的负载均衡性和处理效率。
2. 数据传输方式优化:对数据传输进行优化,使用更快的传输方式,减少数据传输时间,提高数据传输效率。
3. 算法优化:在多电脑协同处理算法中应用优化算法,如并行算法、分布式算法、压缩算法等,提高算法的效率和精度。
通过上述性能优化措施的实施,能够进一步提高多电脑协同处理算法的效率和处理精度,以满足晶圆像质量评估的要求。
三、总结随着半导体工业的不断发展,晶圆像质量评估成为了一项重要工作。
晶圆像质量评估的多电脑协同处理算法研究

晶圆像质量评估的多电脑协同处理算法研究近年来,随着晶圆像在半导体生产中的广泛应用,其质量评估成为了一个热门的研究方向。
然而,由于晶圆像数据量大,数据处理速度慢的问题,传统的单机处理算法已经无法满足研究的需要。
因此,本文研究了基于多电脑协同处理技术的晶圆像质量评估算法,旨在提高数据处理速度和评估精度。
一、晶圆像数据处理的挑战晶圆像数据的处理过程中,需要从大量的像素点中提取出有效的信息。
数据的处理效率和准确性直接影响到后续质量评估的可靠性,以及生产效率的提升。
然而,由于晶圆像数据量大,存在以下挑战:1. 数据量大。
晶圆像数据容易导致数据量爆炸,无法快速处理和传输。
2. 数据质量差。
晶圆像数据中常常存在噪声和干扰,这会导致数据处理不准确,影响评估结果。
3. 处理速度慢。
传统的单机处理算法难以满足晶圆像数据快速处理的需求,这给生产线的调试和优化带来了很大的挑战。
二、基于多电脑协同处理的算法设计基于上述挑战,我们提出了一种基于多电脑协同处理的晶圆像质量评估算法。
该算法采用分布式处理技术,将晶圆像数据分配到多台计算机上进行处理,具有以下特点:1. 分布式并行处理。
将晶圆像数据分解为多个子任务,分配到不同的计算机进行处理,减少处理时间。
2. 多电脑协同。
多台计算机之间通过网络进行通信和协同完成任务,提高并行处理的效率。
3. 数据交互和共享。
每台计算机之间需要交互和共享数据,通过共享传输加快算法处理的速度。
三、实验结果分析为了验证算法的有效性,我们基于实际生产的晶圆像数据进行了实验。
在同等规模的数据量下,分别使用传统的单机处理算法和我们提出的多电脑协同算法进行处理。
实验结果表明,我们提出的算法具有明显的优势。
在保持与传统算法相同的评估准确率的情况下,我们的算法能够节省约80%的处理时间。
这充分表明了多电脑协同处理算法在晶圆像数据分析中的应用前景。
四、总结与展望本文研究了基于多电脑协同处理技术的晶圆像质量评估算法,并对其进行了实验。
晶圆像质量评估的多电脑协同处理算法及优化研究

晶圆像质量评估的多电脑协同处理算法及优化研究随着电子技术的不断发展,尤其是人工智能技术的不断进步,对于半导体行业来说,如何提高晶圆像质量评估已成为一个迫切需要解决的问题。
传统的晶圆像质量评估方法存在计算量大、处理时间长等缺点,难以满足实时性要求。
因此,本文研究了基于多电脑协同处理的晶圆像质量评估算法以及其优化方法。
首先介绍晶圆像质量评估的相关理论。
晶圆像主要包括光电信息获取和数字图像处理两个环节,而数字图像处理又包括预处理、分割、特征提取等部分。
常用的晶圆像质量评估指标主要包括均方误差、峰值信噪比、结构相似性等。
为了提高评估精度,针对这些指标进行了深入研究。
接着介绍了多电脑协同处理的优势。
传统的晶圆像质量评估方法通常采用单机计算,但处理速度慢。
而多电脑协同处理可以将一台计算机无法完成的任务分配给多台计算机进行计算,从而提高计算速度。
此外,多电脑协同处理还能够使计算机资源得到充分利用,加快计算速度,提高了晶圆像质量评估的效率。
然后介绍了基于多电脑协同处理的晶圆像质量评估算法。
首先,将大规模的晶圆像数据分割成若干块,再将每块数据分配给不同的计算机进行处理。
各个计算机处理完数据后,将结果汇总,再进行统一的评估得出最终结果。
这种算法具有高效性和可扩展性,可以满足晶圆像质量评估实时性的要求。
最后提出了针对多电脑协同处理算法的优化方法。
首先,采用局部排序技术对晶圆像进行预处理,减少数据处理的时间。
其次,采用GPU进行并行计算,提高计算速度。
最后,采用新的分块策略,能够更好地利用各个计算机的计算能力,并提高整体的评估精度。
总之,本文针对晶圆像质量评估的多电脑协同处理算法和优化进行了深入研究,提出了一种高效、可扩展的算法和优化方法,为晶圆像质量评估领域的研究提供了新的思路和方向。
CMP后的晶圆的测量和评估方法研究
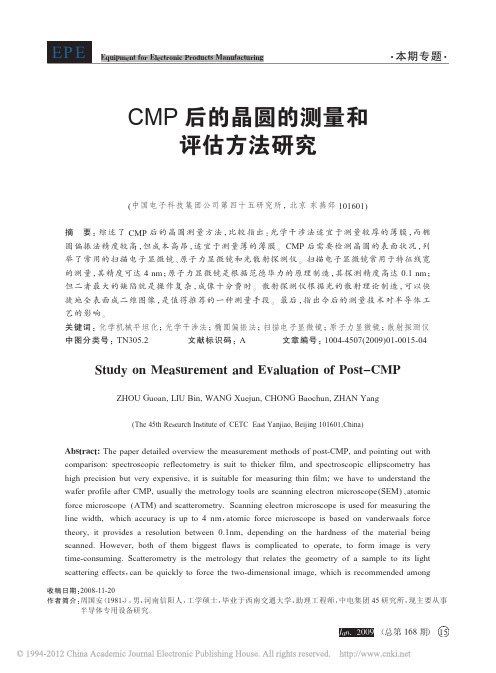
电子柬
灯丝 (电子发射器)
电子萃取器 阳极 聚光透镜
y 扫描
y 扫描讯号
x 扫描讯号 待测物 试片座
扫描磁镜 x 扫描 z 轴讯号
检测器
阴极射线管
图 4 扫描电子显微镜结构图
其原理是:电子束与样品发生作用后产生多种 信号,其中包括二次电子、背散射电子、X 射线、吸 收电子、俄歇(Auger)电子等。在上述信号中,最主要 的是二次电子,它是被入射电子所激发出来的样品 原子中的外层电子,产生于样品表面以下几纳米至 几十纳米的区域,其产生率主要取决于样品的形貌 和成分。通常所说的扫描电镜像指的就是二次电子 像,它是研究样品表面形貌的最有用的电子信号。 检测二次电子的检测器的探头是一个闪烁体,当电 子打到闪烁体上时,就会产生光,这种光被光导管 传送到光电倍增管,光信号即被转变成电流信号, 再经前置放大及视频放大,电流信号转变成电压信 号,最后被送到显像管的栅极经转换成像。
改进,已从手动进入到全自动、变入射角、变波长和
实时监测,极大地促进了纳米技术的发展。椭偏法
的测量精度很高(比一般的干涉法高一至两个数量
级),测量灵敏度也很高 (可测量 0.1 nm 的厚度变
化)[3]。
椭偏法通常情况下建立的数学公式异常繁琐,
但是在实际应用中可以采用多种有效方法,以特殊
值甚至特殊角度的方法来获得实际应用。
Abstract: The paper detailed overview the measurement methods of post-CMP, and pointing out with comparison: spectroscopic reflectometry is suit to thicker film, and spectroscopic ellipscometry has high precision but very expensive, it is suitable for measuring thin film; we have to understand the wafer profile after CMP, usually the metrology tools are scanning electron microscope (SEM)、atomic force microscope (ATM) and scatterometry. Scanning electron microscope is used for measuring the line width, which accuracy is up to 4 nm,atomic force microscope is based on vanderwaals force theory, it provides a resolution between 0.1nm, depending on the hardness of the material being scanned. However, both of them biggest flaws is complicated to operate, to form image is very time-consuming. Scatterometry is the metrology that relates the geometry of a sample to its light scattering effects,can be quickly to force the two-dimensional image, which is recommended among
晶圆关键尺寸测量算法

晶圆关键尺寸测量算法晶圆关键尺寸测量算法是半导体制造过程中的重要一环,通常涉及到晶圆直径、平坦度、表面粗糙度等关键参数的测量。
在半导体工业中,晶圆的关键尺寸测量对于保证产品质量和性能至关重要。
下面将介绍一种晶圆关键尺寸测量算法。
首先,我们需要选择适当的测量工具和仪器。
目前晶圆尺寸测量通常使用光学显微镜、扫描电子显微镜(SEM)和原子力显微镜(AFM)等仪器。
不同的测量目标和需求可能需要不同的仪器。
其次,我们需要准备一个合适的晶圆样品,并将其放置在测量仪器中。
样品的选择要符合测量需求,并且在测量前需要进行清洁处理,以确保测量结果的准确性。
然后,我们需要针对不同的关键尺寸进行相应的测量算法和程序编写。
以晶圆直径为例,可以使用光学显微镜进行测量。
首先,在显微镜下将需要测量的晶圆放置在合适的位置。
然后,通过调整显微镜的放大倍数,找到晶圆的中心位置,并使用测量标尺或图像分析软件测量晶圆直径。
为了提高测量精度,通常需要取多个测量值的平均值。
对于平坦度测量,可以使用扫描电子显微镜(SEM)或原子力显微镜(AFM)。
对于SEM测量,首先将样品放置在显微镜台上,并调整显微镜的工作参数。
然后通过扫描样品表面并记录表面高度变化,从而得到平坦度的测量结果。
对于AFM测量,首先将样品放置在显微镜台上,并使用探针扫描样品表面。
通过测量探针和样品之间的相互作用力,可以得到平坦度的测量结果。
最后,需要对测量结果进行分析和评估。
通常需要比较测量结果与设定标准或先前测量结果之间的差异,并评估其对产品质量和性能的影响。
如果发现了尺寸偏差或其他问题,需要进行相应的调整和控制措施。
本文介绍了一种晶圆关键尺寸测量算法,主要是针对晶圆直径和平坦度的测量。
实际应用中,还可以根据具体需求选择合适的测量方法和仪器。
同时,需要注意测量过程中的操作技巧和设备要求,以确保测量结果的准确性和可靠性。
在半导体制造过程中,关键尺寸的准确测量对于产品质量控制和工艺改进至关重要,因此需要不断改进测量算法和设备,提高测量精度和效率。
- 1、下载文档前请自行甄别文档内容的完整性,平台不提供额外的编辑、内容补充、找答案等附加服务。
- 2、"仅部分预览"的文档,不可在线预览部分如存在完整性等问题,可反馈申请退款(可完整预览的文档不适用该条件!)。
- 3、如文档侵犯您的权益,请联系客服反馈,我们会尽快为您处理(人工客服工作时间:9:00-18:30)。
Jan. 2009 (总第 168 期) 17
·本期专题·
电 子 工 业 专 用 设备
Equipment for Electronic Products Manufacturing
EPE
2.2 原子力显微镜 原子力显微镜(AFM)提供 0.1~5 nm 的表面
形态分布,它依据于被扫描区域的硬度大小。通常 用于测量图形结构的线宽、侧壁的倾斜等。由于它 的扫描速度十分慢,并且测量的可靠性和精准度 严重依赖于针头的形状及其运动的稳定性。因此, 在实时或者在线测量时该种测量手段并不适宜, 但其高精度的表面测量是其亮点之一。其结构如 图 5 所示:
文献标识码: A
文章编号: 1004-4507(2009)01-0015-04
Study on Measurement and Evaluation of Post-CMP
ZHOU Guoan, LIU Bin, WANG Xuejun, CHONG Baochun, ZHAN Yang
(The 45th Research Institute of CETC,East Yanjiao, Beijing 101601,China)
θ(t)= 2π λ0
2n2d(t)
(2)
I1 对应为直接反射的光强,而 I2 为进入介质再
折射空气后的光强,λ0 为选择的入射光的波长,d(t)
为平坦化后介质的厚度,2n 为透明层的折射率,两
反射光之间的相差为 θ(t),由公式(1)和(2)可以计算
出薄膜的厚度。
这种方法测量薄膜厚度分辨率较好的能够达
EPE 电 子 工 业 专 用 设备 Equipment for Electronic Products Manufacturing
·本期专题·
CMP 后的晶圆的测量和 评估方法研究
周国安,柳滨,王学军,种宝春,詹阳
(中国电子科技集团公司第四十五研究所, 北京 东燕郊 101601)
摘 要: 综 述 了 CMP 后 的 晶 圆 测 量 方 法 ,比 较 指 出 :光 学 干 涉 法 适 宜 于 测 量 较 厚 的 薄 膜 ,而 椭
改进,已从手动进入到全自动、变入射角、变波长和
实时监测,极大地促进了纳米技术的发展。椭偏法
的测量精度很高(比一般的干涉法高一至两个数量
级),测量灵敏度也很高 (可测量 0.1 nm 的厚度变
化)[3]。
椭偏法通常情况下建立的数学公式异常繁琐,
但是在实际应用中可以采用多种有效方法,以特殊
值甚至特殊角度的方法来获得实际应用。
EPE
the metrologies. At the end, the better metrology in the future will play a big promotion role in semiconductor technology. Keywords: CMP, Spectroscopic reflectometry; Spectroscopic ellipscometry; Scanning electron microscope; Atomic force microscope; Scatterometry
θθ
空气
氧化层
t
硅
θ1
θ1
图 1 分光光学干涉法测量
其计算公式如下[1]:
I(t)=I1+I2+2 姨I1I2 cos[θ(t)]
(1)
其中:
1.2 椭圆偏振法
椭圆偏振法简称椭偏法,是一种先进的测量薄
膜纳米级厚度的方法。椭偏法的基本原理由于数字
处理上的困难,直到 21 世纪 40 年代计算机出现以
后才发展起来[2]。椭偏法的测量经过几十年的不断
偏斜感应器 悬臂梁
悬臂偏角
y 压电驱动单元
x z
表面原子
雷射
图 5 原子力显微镜工作方式
其工作原理为:将一个对微弱力极敏感的微悬 臂一端固定,另一端有一微小的针尖,针头与样品 表面轻微接触,由于针尖尖端与样品表面原子间存 在着微弱的力(范德华力,根据原子间距离而存在 排斥力和引力),通过扫描控制这种力的恒定,带有 针尖的微悬臂将对应于针尖与样品表面原子间作 用力的等位面而在垂直于样品的表面方向起伏运 动。利用光学检测或隧道电流检测法,可测得微悬 臂对应于扫描点的位置变化,从而可以获得样品表 面形貌的信息。
电子柬
灯丝 (电子发射器)
电子萃取器 阳极 聚光透镜
y 扫描
y 扫描讯号
x 扫描讯号 待测物 试片座
扫描磁镜 x 扫描 z 轴讯号
检测器
阴极射线管
图 4 扫描电子显微镜结构图
其原理是:电子束与样品发生作用后产生多种 信号,其中包括二次电子、背散射电子、X 射线、吸 收电子、俄歇(Auger)电子等。在上述信号中,最主要 的是二次电子,它是被入射电子所激发出来的样品 原子中的外层电子,产生于样品表面以下几纳米至 几十纳米的区域,其产生率主要取决于样品的形貌 和成分。通常所说的扫描电镜像指的就是二次电子 像,它是研究样品表面形貌的最有用的电子信号。 检测二次电子的检测器的探头是一个闪烁体,当电 子打到闪烁体上时,就会产生光,这种光被光导管 传送到光电倍增管,光信号即被转变成电流信号, 再经前置放大及视频放大,电流信号转变成电压信 号,最后被送到显像管的栅极经转换成像。
2 晶圆表面的评估方法
CMP 后,我们有必要了解晶圆的表面状况,以 此来评估抛光的质量。通常的表面测量手段有扫描 电子显微镜、原子力扫描显微镜及光散射探测仪。
2.1 扫描电子显微镜 关键尺寸测量的一个重要原因是要达到对产品
所有线宽的准确控制。关键尺寸的变化通常显示半导 体制造工艺中一些关键部分的不稳定,为了获得对这
Abstract: The paper detailed overview the measurement methods of post-CMP, and pointing out with comparison: spectroscopic reflectometry is suit to thicker film, and spectroscopic ellipscometry has high precision but very expensive, it is suitable for measuring thin film; we have to understand the wafer profile after CMP, usually the metrology tools are scanning electron microscope (SEM)、atomic force microscope (ATM) and scatterometry. Scanning electron microscope is used for measuring the line width, which accuracy is up to 4 nm,atomic force microscope is based on vanderwaals force theory, it provides a resolution between 0.1nm, depending on the hardness of the material being scanned. However, both of them biggest flaws is complicated to operate, to form image is very time-consuming. Scatterometry is the metrology that relates the geometry of a sample to its light scattering effects,can be quickly to force the two-dimensional image, which is recommended among
在推导的公式中最有实际价值的是[4]:
tgψ= Erp/Ers
(3)
Eip/Eis
e =e iΔ i[(βrp-βrs)-(βip-βis)]
(4)
其中:Erp 和 Ers 代表反射光波电矢量的 P 分量和 s 分 量,Eip 和 Eis 代表入射光波电矢量的 P 分量和 s 分 量。而 β 代表对应各分光的相位。其中 ψ 和 Δ 为典型
化 学 机 械 平 坦 (CMP) 是 半 导 体 制 作 过 程 中 十 分关键的步骤,针对层间介质平坦化、浅沟道隔离、 铜大马士革等都具有直接的推动意义,它是实现六 层板以上金属互连的必备手段,是可靠迈向 65 nm、 45 nm 节点及 300 mm、450 mm 大直径晶圆的可靠 保证。
在化学机械平坦化后,必须进行晶圆的测量和 评估,以此来检查产品的合格率及不断优化工艺参 数。因此,检测方法的选择将具有十分重要的意义, 它关系着试验数据的准确性,是判断工艺操作合理 与否的直接根据。
但二者最大的缺陷就是操作复杂,成像十分费时。 散射探测仪根据光的散射理论制造,可以快
捷地全表面成二维图像,是值得推荐的一种测量手段。 最后,指出今后的测量技术对半导体工
艺的影响。
关键词: 化学机械平坦化; 光学干涉法; 椭圆偏振法; 扫描电子显微镜; 原子力显微镜; 散射探测仪
中图分类号 之内,操作简单,价格较为
低廉,较厚的膜测量无疑是最佳选择,但是,对于日
益精密的工艺要求,我们测量精度依然需要极大地
提高。
1 膜厚测量
在实际应用中,膜厚的测量,主要有光学干涉 法及分光椭圆偏振法。
1.1 分光光学干涉法 分光光学干涉是利用光在介质上下表面反射
的路程差形成干涉,测量干涉后的光强即可计算出 薄膜厚度,如图 1 所示。
收 稿 日 期 :2008-11-20 作者简介:周国安(1981-),男,河南信阳人,工学硕士,毕业于西南交通大学,助理工程师,中电集团 45 研究所,现主要从事