注射成型及模具设计实用技术知识点总结
关于注塑的知识点总结

关于注塑的知识点总结一、注塑工艺流程1.设计模具:根据产品设计要求,设计和制造塑料注射成型所需的模具。
2.原料筛选:根据产品要求和加工特点,选择合适的塑料原料,并进行配料、干燥等处理。
3.塑料熔化:将塑料颗粒加热至熔化状态,形成流动状态的熔体。
4.模具注射:将熔化的塑料通过高压注射进入模具腔内,充填整个模具腔,成型出所需的塑料制品。
5.冷却固化:待塑料充填完成后,进行冷却固化,使塑料制品在模具中形成稳定的形状。
6.模具打开:冷却固化完成后,打开模具,取出成型的塑料制品。
7.脱模整理:将成型的塑料制品进行去除模具余料、修整、表面处理等工序,得到符合要求的塑料制品。
二、注塑设备1.注塑机:是进行塑料注射成型的核心设备,根据产品要求和生产规模选择合适型号的注塑机。
2.模具:塑料注塑成型所需的模具,根据产品设计要求和注塑工艺特点进行设计和制造。
3.辅助设备:如塑料干燥机、颜料添加机、冷却水机、除湿机、输送设备等,用于对塑料原料和成品进行辅助处理。
三、注塑工艺参数1.注射压力:即注塑机对塑料进行注射时的压力大小,决定了塑料充填模具的速度和充填度。
2.注射速度:注射机对塑料进行注射的速度,影响着塑料注射的充填时间和充填性能。
3.冷却时间:成型后的塑料制品需要在模具内进行冷却固化,冷却时间的长短影响着产品的成型质量和产能。
4.模具温度:模具温度的设置影响着塑料的冷却固化速度和塑料制品的表面质量。
5.料斗温度:对塑料进行熔化处理前,通常需要进行干燥,料斗温度要根据塑料的种类和湿度进行合理设置。
四、注塑材料1.常见的注塑材料有聚丙烯(PP)、聚乙烯(PE)、聚苯乙烯(PS)、聚氯乙烯(PVC)、工程塑料如聚酰胺(NYLON)、聚碳酸酯(PC)、聚苯醚(PEEK)等。
不同种类的塑料具有不同的物理性能、耐热性、耐化学性、机械性能等特点,因此在选择注塑材料时需要根据产品功能和性能要求进行合理的选择。
2.在注塑过程中,需要对塑料原料进行干燥处理,以保证塑料中的水分含量在合理的范围内,避免在注塑过程中出现气泡、状况等缺陷。
模具注塑知识点归纳总结
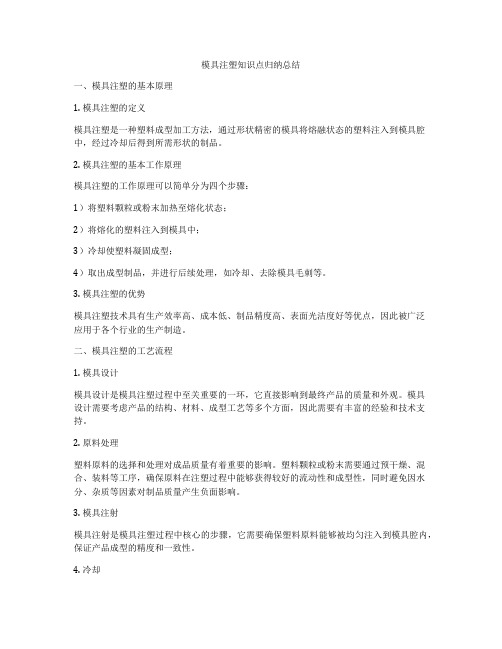
模具注塑知识点归纳总结一、模具注塑的基本原理1. 模具注塑的定义模具注塑是一种塑料成型加工方法,通过形状精密的模具将熔融状态的塑料注入到模具腔中,经过冷却后得到所需形状的制品。
2. 模具注塑的基本工作原理模具注塑的工作原理可以简单分为四个步骤:1)将塑料颗粒或粉末加热至熔化状态;2)将熔化的塑料注入到模具中;3)冷却使塑料凝固成型;4)取出成型制品,并进行后续处理,如冷却、去除模具毛刺等。
3. 模具注塑的优势模具注塑技术具有生产效率高、成本低、制品精度高、表面光洁度好等优点,因此被广泛应用于各个行业的生产制造。
二、模具注塑的工艺流程1. 模具设计模具设计是模具注塑过程中至关重要的一环,它直接影响到最终产品的质量和外观。
模具设计需要考虑产品的结构、材料、成型工艺等多个方面,因此需要有丰富的经验和技术支持。
2. 原料处理塑料原料的选择和处理对成品质量有着重要的影响。
塑料颗粒或粉末需要通过预干燥、混合、装料等工序,确保原料在注塑过程中能够获得较好的流动性和成型性,同时避免因水分、杂质等因素对制品质量产生负面影响。
3. 模具注射模具注射是模具注塑过程中核心的步骤,它需要确保塑料原料能够被均匀注入到模具腔内,保证产品成型的精度和一致性。
4. 冷却在模具注塑过程中,塑料充填后需要进行冷却,使其快速固化成型。
冷却的速度和均匀性会直接影响到产品的收缩率和内部应力分布,因此冷却系统的设计和控制非常重要。
5. 取模冷却后的成型制品将从模具中取出,这一步骤需要谨慎操作,避免对产品造成损伤或变形。
6. 后处理成型后的制品可能需要进行去除毛刺、修整、喷漆等后处理工序,以使其符合最终产品的要求。
三、模具注塑的材料选择1. 塑料原料的选择不同的塑料原料拥有不同的物理性能和化学性质,在模具注塑过程中需要根据产品的要求选择合适的塑料,如ABS、PC、PP、PE等。
2. 添加剂一些特殊的塑料制品可能需要添加颜色、增强剂、阻燃剂等添加剂,以满足产品的特殊需求。
注射成型工艺基础知识

注塑成型工艺基础知识
螺杆 喷嘴 螺杆传动装 置 注射成型座 移动油缸
料筒
注射油缸
料斗
注射 系统
计量装置
注塑成型工艺基础知识
模板 拉杆 安全门 制品顶 出装置
合模机 构
合模 系统
调模装 置
注塑成型工艺基础知识 动力油 泵
管路 各种阀 门
其他附 属装置 各种电 器仪表
液压与电 气系统
注塑成型工艺基础知识
注塑成型工艺基础知识
(三)时间 完成一次注射模塑过程所需要的时间称成型周期。成型周期包括以下几 个部分。
注射时 间
充模时间 保压时间
成型周期
模内冷 却时间
其他时 间
开模、脱模、 闭模时间等
注塑成型工艺基础知识
五、几种公司常见的材料注射成型工艺
(一)聚酰胺(尼龙,PA) 公司常用的PA类塑料有PA6、PA66。它们有明显的熔点,PA为215℃, PA66为250-260℃。 1、原材料的准备 由于PA类塑料具有较高的吸湿性,所以在加工前一定要对物料进行干燥, 常采用真空干燥。 2、成型工艺 1)注射温度 由于PA热稳定性差,故加工温度不宜太高,一般高于熔点1030℃即可。 2)模具温度 模具温度一般控制在40-90℃。 3)注射压力 一般为68-100MPa
注塑成型工艺基础知识
4、油温 正常的油温应保持在30-50℃。 (二)压力 1、塑化压力或背压 螺杆头部熔料在螺杆转动后退时所受到的压力称塑化压力或背压,其大 小可通过液压系统中的溢流阀来调节。塑化压力的大小与塑化质量、驱动 功率、反流和漏流以及塑化能力等有关。 2、注射压力 3、保压压力 保压是指在模腔充满后对模内熔体进行压实、补缩的过程。实际生产中, 保压压力的设定,可与注射压力相等,一般稍低于注射压力。
注射模具设计基础5

巩固
1、什么是模架?其作用是什么? 模架是模具的骨架。 其作用有二:一是将模具的各部分连接在一起 二是保证了凸凹模在开合模时能正确对准。 2、注射成型模架由哪四部分组成? 模架由动模、定模、固定、导向四部分组成。 3、注射成型模架需要设计的有哪些? 注射成型模架需要设计有:模架的长宽高;A、B板的高; 模脚的高
作业:
抄画模架,并写上相应的名称。
第二、三课时
复习 1、注射成型模架作用是什么? 2、注射成型模架由哪四部分组成? 3、注射成型模架哪些部分需要设计?哪些部 分不需要设计?
4、注射成型模架中有哪套导柱导套安装 位置不同?其作用是什么?
注射成型标准模架分类
目的和要求: 1、了解注射成型标准模架的种类
3)材料:SUJ2、GCr15、20钢、T8、T10等;硬度 为HRC60±2。
4)相关尺寸 :
5)在模具中的位置 :
导柱 剥料板 导套A 导套B 母模板 导套A
导柱
公模板
顶出板导柱深入模板里面10-15mm
顶出板导套(ejector guide bushing) 模脚
上顶出板
下顶出板
顶出板导柱(ejector guide pin)
3)细水口模架中英名称结构图
区分:DA型有垫板、无推板;DB型有垫板、有推板;DC型 无垫板、无推板;DD型无垫板、有推板;均有水口推板。 EA型有垫板、无推板;EB型有垫板、有推板;EC型无垫板、 无推板;ED型无垫板、有推板;均无水口推板。
2、模架的区别
(1)大水口与简化细 水口的区别
③ 简细化水口标准 模架没有推板。
注射成型及模具设计实用技术知识点总结

1、塑料是一种以树脂为主要成分,以添加剂(增塑剂、稳定剂、填充剂、增强剂、着色剂、润滑剂、特殊助剂、其他主要助剂)为辅助成分的高分子化合物。
增塑剂:为了改善聚合物成型时的流动性能和增进之间的柔顺性。
稳定剂:制止或者抑制聚合物因受外界因素影响所引起破坏作用。
填充剂:为了降低成本改善之间的某些使用性能,赋予材料新特性。
增强剂:使塑件力学性能得到补强。
着色剂:赋予塑料以色彩或特殊的光学性能。
润滑剂:改善塑料熔体的流动性能,减少、避免对成型设备的摩擦、磨损和粘附,改进制品表面粗糙度。
2、塑料的特性:相对分子质量大;在一定的温度和压力作用下有可塑性。
3、聚合物(树脂)通常有天然和合成两大类型。
对聚合物的选择主要是从分子量大小及分布、颗粒大小、结构以及与增塑剂、溶剂等相互作用的难易程度等诸方面考虑。
4、聚合物的作用:胶粘其他成分材料;赋予材料可塑性。
5、塑料的分类:根据来源:天然树脂、合成树脂。
根据制造树脂的化学反应类型:加聚型塑料、缩聚型塑料。
根据聚合物链之间在凝固后的结构形态:非结晶型、半结晶型、结晶型。
根据应用角度:通用塑料、工程塑料 根据化学结构及基本行为:热固性、热塑性塑料。
6、塑料的实用性能:轻巧美观、电气绝缘、热物理性能、力学性能、减震消音、防腐耐蚀。
7、塑料的技术指标:密度、比容、吸水率、拉伸强度、冲击强度、弯曲强度、弹性模量、马丁耐热、热变形温度等。
8、线性非结晶型聚合物在不同温度下所处的力学状态:g T T <聚合物处于玻璃态;处于高弹态f g T T T <<;f T T <粘流态。
9、玻璃态聚合物力学行为特点:内聚能大,弹性模量高,在外力作用下只能通过高分子主链键长、键角微笑改变发生变形。
10、高弹态聚合物力学行为特点:弹性模量与玻璃态相比显著降低,在外力作用下分子链段可发生运动11、黏流态聚合物力学行为特点:整个分子链的运动变为可能,在外力作用下,材料科发生持续性变形,变形主要是不可逆的黏流变形。
注塑模总结知识点

注塑模总结知识点第一篇:注塑模总结知识点1、注射成型原理是什么注射成型工艺过程有哪些?简述各部分作用?注射成形的原理:将颗粒状态或粉状塑料从注射机的料斗送进加热的料筒中,经过加热熔融塑化成为黏流态熔体,在注射机柱塞或螺杆的高压推动下,以很高的流速通过喷嘴,注入模具型腔,经一定时间的保压冷却定型后可保持模具型腔所赋予的形状,然后开模分型获得成形塑件。
注射成型工艺过程:1.成型前准备为了保证塑料制品质量,在成型前应作一些工艺准备工作2.注射工艺工艺1)加料由于注射成型是一个间歇过程,因而需要定量(定容)加料,以保证操作稳定,塑料塑化均匀,最终获得良好的塑件。
2)塑化由固体颗粒转换成粘流态并且具有良好的可塑性3)注射:①充模塑化好大的熔体填满型腔,型腔内熔体压力迅速上升,达到最大。
②保压继续保持施压状态的柱塞或螺杆迫使浇口附近的熔料不断补充进入模具中,使型腔中的塑料能成型出形状完整且致密的塑件。
③倒流使塑件产生收缩、变形及质地疏松等缺陷。
④浇口冻结后的冷却对模具进一步冷却。
⑤脱模在推出机构的作用下将塑料制件推出模外。
3.塑件的后处理改善和提高制品的性能和尺寸稳定性。
2、分别简述热塑性塑料和热固性塑料在注射成型过程中的特点?两者间的区别是什么?热塑性塑料特点:受热变软进而成为可流动的粘稠液体,具有可塑性,可塑制成一定形状塑件,并可经冷却定型;再加热可重新变软可塑,在受热过程中只发生物理变化。
热固性塑料特点:初次加热之初,分子呈线型结构,加热时可软化具有可塑性,继续加热,线型结构分子相互交联成体型网状结构,使形状固定下来,如再加热不再软化,不再具有可塑性。
受热过程中既有物理变化又有化学变化,其变化过程不可逆。
区别:热塑性塑料的合成树脂分子结构:线型或带有支链线型,在受热过程中只发生物理变化,可反复加热塑化成型。
而热固性塑料的合成树脂分子结构:体型网状结构,受热过程中既有物理变化又有化学变化,其变化过程不可逆。
模具设计知识之常用塑料主要性能及注射成型工艺要点
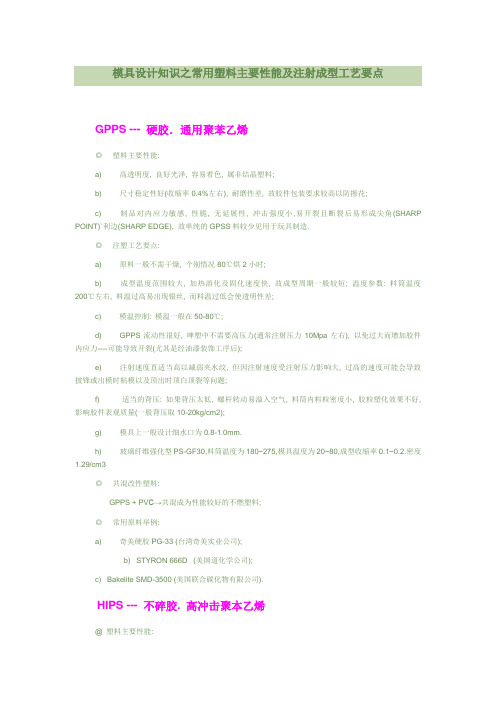
模具设计知识之常用塑料主要性能及注射成型工艺要点GPPS --- 硬胶.通用聚苯乙烯◎塑料主要性能:a) 高透明度, 良好光泽, 容易着色, 属非结晶塑料;b) 尺寸稳定性好(收缩率0.4%左右), 耐磨性差, 故胶件包装要求较高以防擦花;c) 制品对内应力敏感, 性脆, 无延展性, 冲击强度小,易开裂且断裂后易形成尖角(SHARP POINT)`利边(SHARP EDGE), 故单纯的GPSS料较少见用于玩具制造.◎注塑工艺要点:a) 原料一般不需干燥, 个别情况80℃烘2小时;b) 成型温度范围较大, 加热溶化及固化速度快, 故成型周期一般较短; 温度参数: 料筒温度200℃左右, 料温过高易出现银丝, 而料温过低会使透明性差;c) 模温控制: 模温一般在50-80℃;d) GPPS流动性很好, 啤塑中不需要高压力(通常注射压力10Mpa左右), 以免过大而增加胶件内应力----可能导致开裂(尤其是经油漆装饰工序后);e) 注射速度直适当高以减弱夹水纹, 但因注射速度受注射压力影响大, 过高的速度可能会导致披锋或出模时粘模以及顶出时顶白顶裂等问题;f) 适当的背压: 如果背压太低, 螺杆转动易溢入空气, 料筒内料粒密度小, 胶粒塑化效果不好, 影响胶件表观质量(一般背压取10-20kg/cm2);g) 模具上一般设计细水口为0.8-1.0mm.h) 玻璃纤维强化型PS-GF30,料筒温度为180~275,模具温度为20~80,成型收缩率0.1~0.2.密度1.29/cm3◎共混改性塑料:GPPS + P VC→共混成为性能较好的不燃塑料;◎常用原料举例:a) 奇美硬胶PG-33 (台湾奇美实业公司);b) STYRON 666D (美国道化学公司);c) Bakelite SMD-3500 (美国联合碳化物有限公司).HIPS --- 不碎胶. 高冲击聚本乙烯@ 塑料主要性能:a) 着色性好;b) 与GPPS比较是加入了5-20%的丁二(一般用顺丁橡胶或丁苯橡胶), 成份, 故抗冲击性大大提高.注塑工艺要点:a) 流动性小于GPPS, 故成型温度` 压力都稍高;b) 冷却速度较GPPS慢, 故需要足够的保压力和保压时间以及充分的冷却条件以减少局部收缩及冷却变形.共混改性塑料:HIPS + GPPS→混和啤塑, 调整比例使塑料具有足够强度及良好表观质量.常用原料举例:a) HIPS STYRON 470,475U (DOW Chemical Co., Ltd)b) Dolyrex PH-66 (台湾奇美实业公司)c) HIPS HI-425 (NIWON Co., Ltd 。
塑料注射模具知识点总结

概述塑料注射模具是用于制造塑料制品的一种装置,由模具基板、模具芯、注射系统、冷却系统、脱模系统等部分组成。
塑料注射模具制造是一项相对复杂的工艺,需要对材料、工艺、设计、加工等方面具有深入的了解和掌握。
本文将从材料、设计、加工、维护等方面综合介绍塑料注射模具的知识点。
一、塑料注射模具的材料1.1 模具基板材料模具基板是塑料注射模具的主要承载部分,需要具有高强度、耐磨损、耐腐蚀等特性。
常见的模具基板材料有P20、718、2738等。
P20材料具有良好的硬度和耐磨损性能,适合制作中小型模具;718材料具有高强度和硬度,适合制作大型模具;2738材料具有高镍合金特性,适合制作高精度模具。
1.2 模具芯材料模具芯是用于塑料制品内部结构的部分,需要具有高硬度、高精度、耐磨损等特性。
常见的模具芯材料有SKD61、S136等。
SKD61材料具有良好的热稳定性和硬度,适合制作高品质的模具芯;S136材料具有良好的耐腐蚀性和耐磨损性,适合制作高精度的模具芯。
1.3 注射系统材料注射系统是用于将熔融塑料材料注入模具腔内的部分,需要具有耐高温、耐腐蚀、高流动性等特性。
常见的注射系统材料有H13、H13W等。
H13材料具有良好的耐热性和抗氧化性,适合制作注射系统组件;H13W材料具有更高的硬度和耐磨损性,适合制作高性能的注射系统组件。
1.4 冷却系统材料冷却系统是用于控制模具温度的部分,需要具有良好的传热性能、耐腐蚀、高耐压等特性。
常见的冷却系统材料有铜合金、铝合金、不锈钢等。
铜合金具有良好的导热性和抗腐蚀性,适合制作冷却系统管道;铝合金具有较轻的重量和较高的导热性,适合制作冷却系统散热器;不锈钢具有较高的耐腐蚀性和耐压性,适合制作高性能的冷却系统组件。
1.5 脱模系统材料脱模系统是用于将成型塑料制品从模具中脱离的部分,需要具有良好的脱模性能、耐磨损、易维护等特性。
常见的脱模系统材料有冷作钢、硬质合金等。
冷作钢具有良好的硬度和耐磨损性,适合制作脱模系统零部件;硬质合金具有更高的硬度和耐磨损性,适合制作高性能的脱模系统零部件。
注射模具总结

注射模具总结引言注塑模具是注塑成型过程中的关键工具之一,其质量直接影响到产品的成型质量和生产效率。
本文将对注射模具进行总结,包括模具的定义、分类、制造工艺等方面,以帮助读者更好地了解注射模具。
何为注射模具注射模具是用于塑料注塑成型的专用模具,也称为注塑模具。
它由模具座(支架)、模具芯(浇注孔)、模具腔(成形孔)等部件组成。
注塑模具能够将熔化的塑料通过注射机注入到模具腔中,经过冷却固化后,得到所需形状的产品。
注射模具的分类根据注塑模具的结构和应用领域,可以将其分为以下几类:1.直线副模具:该类模具结构简单,适用于生产平面形状的产品。
2.斜线副模具:模具芯、模具腔的结构为斜面,多用于生产壁厚不均匀的产品。
3.寄生副模具:模具芯出现在模具腔的内部,通过模具座插入模具腔内注射成型,适用于细长形状的产品。
4.双色模具:该类模具可实现一次注塑成型,生产出颜色不同的产品。
5.复合模具:模具腔形状较复杂,需要多个注射机同时工作,用于生产多组件结构的产品。
6.热流道模具:通过热嘴将熔融塑料永远保持在熔融状态,可用于生产高要求的产品,如透明产品。
注射模具的制造工艺注射模具的制造工艺主要包括以下几个步骤:1.设计:根据产品的要求,设计注射模具的结构、尺寸和形状。
2.制作模具芯和模具腔:根据设计图纸,选用适当的材料,并通过数控机床进行切削加工,制作出模具芯和模具腔。
3.组装与调试:将模具芯和模具腔进行组装,并进行必要的调试工作,以保证模具正常使用。
4.热处理:对模具进行热处理,提高其硬度和耐磨性,以延长模具的使用寿命。
5.表面处理:对模具表面进行精细加工,以提高产品的光洁度和精度。
6.模具试模:在注射机上进行试模,调整模具腔和模具芯的位置和尺寸,以达到产品质量标准。
7.修整和保养:对模具进行定期的修整和保养工作,以保证模具的使用效果和寿命。
注射模具的优势和挑战注射模具作为一种关键工具,在塑料加工行业具有以下优势:•生产效率高:注射模具可以实现高速连续生产,提高生产效率。
注塑成型基础知识学习
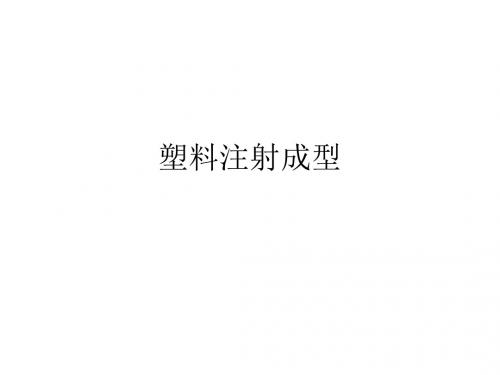
4.塑化能力: • 1h内所能塑化物料的千克数(以PS计)
• 应与注射机的成型周期相配合,若塑化能力高而 机器的空循环时间太长,则不能发挥塑化装置的 能力,反之会使塑料制品的成型周期延长
5.锁模力(合模力): • 注射机合模装置对模具所能施加的最大夹紧力
• 锁模力足够大,才能锁住模具,使制品顺利成型, 不产生溢料等不正常现象
PA1010: 210~225℃ • 换料时:料筒喷嘴调至210℃,然后用PS进行降
温清洗。换料后调至195℃
• 例3:以PC换POM: • 欲换料(PC)温度高黏度大, • 料筒内的料(POM)为热敏性料 • 成型温度:PC:270~330℃ • POM :190~200℃ • 换料时:195℃以LDPE或PS换POM • 270℃用PC换LDPE或PS • 换料后:调至300℃生产
• 保压(压实)阶段:指熔体充满模腔起至柱塞或螺 杆撤回时为止
作用:补缩、防止倒流
温度:不断下降
压力:压力下降(柱塞或螺杆停止不动) 或压力不变(柱塞或螺杆向前移动)
压实时间越长、分子取向程度越大
• 倒流阶段:从柱塞或螺杆后退开始到浇口凝封时 止
柱塞或螺杆后退,模腔压力比流道高、模内熔体 向流道倒流,模腔压力↓,倒流至浇口冻结为止
• ①直通式喷嘴(开式 喷嘴)
• ②自锁式喷嘴(关式 喷嘴)
• ③特殊用途喷嘴
• PVC:宜选用流道阻力小,剪切作用比较小的大 口径直通式喷嘴
• PA:为防止“流涎”现象,则宜选用带有加热装 置的弹簧针阀式或杠杆针阀式的喷嘴
• 形状复杂的薄壁制品:选用小孔径、射程远的喷 嘴
• 厚壁制品:选用大孔径、补缩作用大的喷嘴
保压时间短(浇口未冻结):倒流大、残余压力小
注射成型知识讲解

注射成型知识讲解塑料在注塑机加热料筒中塑化后,由柱塞或往复螺杆注射到闭合模具的模腔中形成制品的塑料加工方法。
此法能加工外形复杂、尺寸精确或带嵌件的制品,生产效率高。
大多数热塑性塑料和某些热固性塑料(如酚醛塑料)均可用此法进行加工。
用于注塑的物料须有良好流动性,才能充满模腔以得到制品。
主要装置注塑机由注射装置、合模装置和注塑模具三部分组成。
注塑机的规格有两种表示法:一种是每次最大注射体积或重量,另一种是最大合模力。
注塑机其他主要参数为塑化能力、注塑速率和注射压力。
注射装置注塑机的主要部分。
将塑料加热塑化成流动状态,加压注射入模具。
注射方式有柱塞式、预塑化式和往复螺杆式。
后者(图1)具有塑化均匀、注射压力损失小、结构紧凑等优点,应用较广泛。
合模装置用以闭合模具的定模和动模,并实现模具开闭动作及顶出成品。
注塑模具简称注模。
它由浇注系统、成型零件和结构零件所组成。
①浇注系统是指自注射机喷嘴到型腔的塑料流动通道;②成型零件是指构成模具型腔的零件,由阴模、阳膜组成;③结构零件,包括导向、脱膜、抽芯、分型等各种零件。
模具分为定模和动模两大部分,分别固定于合模装置之定板和动板上,动模随动板移动而完成开闭动作。
模具根据需要可加热或冷却。
因加工物料而异。
热塑性塑料的注射成型包括加料、塑化、注射、保压、冷却、脱模等过程。
热固性塑料和橡胶的成型也包括同样过程,但料筒温度较热塑性塑料的低,注射压力却较高,模具是加热的,物料注射完毕在模具中需经固化或硫化过程,然后趁热脱膜。
注射成型是指有一定形状的模型,通过压力将融溶状态的胶体注入摸腔而成型,工艺原理是:将固态的塑胶按照一定的熔点融化,通过注射机器的压力,用一定的速度注入模具内,模具通过水道冷却将塑胶固化而得到与设计模腔一样的产品。
注塑成型的七个步骤1、关门2、锁模3、注射保压4、冷却5、开模6、打开安全门7、取出产品。
重复执行这种作业流程,就可连续生产产品。
1、关门半自动需开关安全门,全自动安全门设置在关的状态。
模具设计知识点总结

模具设计知识点总结第一篇:模具设计知识点总结什么是冲压?它与其他加工方法相比的特点在常温下利用冲模和冲压设备对材料施加压力,使其产生塑性变形或分离,从而获得一定形状、尺寸和性能的工件。
它的生产效率非常高,且操作简便,便于实现机械化与自动化。
2冲压工序可分为哪两大类?它们的主要区别和特点是什么?冲压工序大致可分为分离工序和成型工序两大类。
分离工序是使冲压件与板料沿一定的轮廓线相互分离的工序。
成型工序是指材料在不破裂条件下产生塑性变形的工序。
3板料冲裁时,其切断面具有什么特征?这些特征是如何形成的?1圆角带:其大小与材料塑性和模具间隙有关。
板料在弹性变形时产生,塑性变形时定性。
2光亮带:光亮且垂直端面,在整个断面上所占的比例小于1/3。
塑性变形 3断裂带:粗糙且有锥度。
断裂分离4毛刺:成竖直环状,是模具拉齐的结果。
裂纹汇合结束4什么是冲裁间隙?它对冲载件的断面质量、冲载工序力、模具寿命有什么影响?实际生产中如何选择合理的冲裁间隙?冲裁间隙是指冲裁的凸模与凹模刃口部分的尺寸之差。
1对冲载件质量的影响。
一般来说,间隙小,冲载件的断面质量就高(光亮带增加);间隙大,则断面塌角大,光亮带减小,毛刺大。
但是,间隙过小,则断面易产生”二次剪切”现象,有潜伏裂纹。
2对冲载力的影响。
间隙小,所需的冲载力大(材料不容易分离):间隙大,材料容易分离,所需的冲载力就小。
3对冲载模具寿命的影响。
间隙大,有利于减小模具磨损,避免凹模刃口胀裂,可以提高冲载模具的寿命。
为保证冲载模有一定的使用寿命,设计时的初始间隙就必须选用适中间隙范围内的最小冲载间隙。
5什么是排样?冲载件在条料、带料或板料上的布置方式。
6求冲载模的压力中心位置有哪几种方法?用解析法如何求冲载模的压力中心位置?求冲载模压力中心位置有什么用处?方法:直接求解法和解析法按比例画出冲载件的冲载轮廓;建立坐标;将冲载件轮廓分成若干直线段;计算基本线段的长度及压力的中心坐标;根据力矩平衡原理计算压力中心坐标用处:保证压力机和模具正常工作7什么是弯曲件的回弹?影响弯曲回弹的因素有哪些?生产中减小回弹的方法有哪些?材料在弯曲过程中,伴随塑性变形总存在着弹性变形,弯曲力消失后,塑性变形部分保留下来,而弹性变形部分要恢复,从而使弯曲件与弯曲模的形状并不完全一致,这种现象称为弯曲件的回弹。
注塑模学习笔记

1-4
注射成型工艺条件
《俗子笔记 之 模具篇》 -1-
一、温度:主要指料筒温度和模具温度。 如果可能发生,就会发生。__默非
1、不同塑料的料温都不尽相同。 2、料温太低不利于塑化,料温太高,易导致塑件出飞边,严重时将导致塑 料发生降解。 3、喷嘴的温度通常低于料筒的前段温度,以避免“流涎”现象。 二、压力:包括注射压力,塑化压力(即背压) 、保压力和锁模压力。 1、塑件的尺寸越大,形状越复杂,壁厚越薄,要求注射压力越大。 2、流动性好的塑料及形状简单的塑件,注射压力较小;玻璃化温度及黏度 都较大的塑料,应用较高的注射压力。 3、模具或熔胶温度较低时,宜用较大的注射压力。 4、对于同一副模具,注射压力越大,注射速度也越快。 三、成型周期: 完成一次注射成型工艺过程所需的时间,包括合模时间,注射时间,保压 时间, 冷却时间, 开模时间, 顶出时间及其它时间 (如放嵌件, 喷脱模剂等) 。 其中保压时间和冷却时间占的比例最大,有时可达 80%。
底 板
方铁
托 B 板 板
A 板
面 板
唧 嘴
H1
胶 件
2、细水口模开模行程=H1+H2+A+C+ (5~10)
如果可能发生,就会发生。__默非定理 《俗子笔记 之 模具篇》 -4-
底 板
方 铁
托 B 板 板
A 板
水 口 板
面 板
唧 嘴 水 口
H1
注:H1—制品需要推出的最小距离; H2—制品及水口的高度; A—细水口水口高度+30mm; C—6 至 8mm。 2-4-2 模具的安装尺寸: 1、码模螺孔:加工在模具的底板和面板上(图示),作用:将模具固定在注 射机上。
状。 骨位在开模时要打 火花,增加加工难度, 不利于模具制造。 当然 这是产品设计上的问 题, 模具工程师可以对 此提出个人见解。 排位设计内模镶 件时, 必须要考虑到的 因素是: 上螺丝, 走运 水, 胶位。 保证设计内 模镶件的大小可以装 配这些结构。 原生模指的是:直 接在 A、 B 板上做型腔 或型芯。 并且在定模胚 时一定要注明 A、 B板 的材料。
模具设计重点知识(华航)
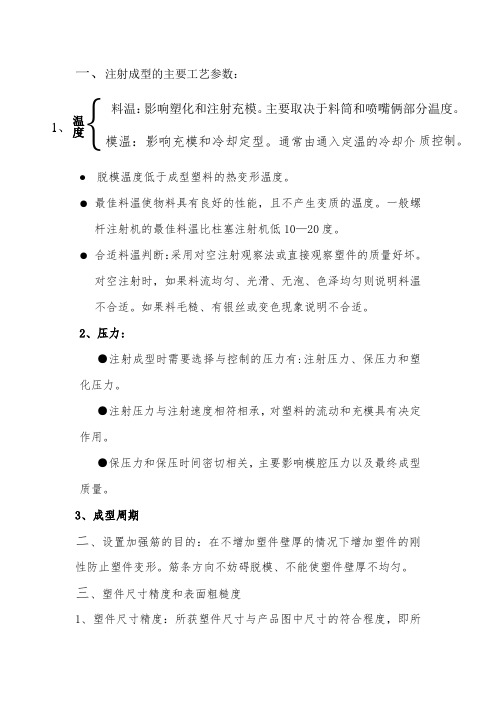
一、注射成型的主要工艺参数:{模温:影响充模和冷却定型。
通常由通入定温的冷却介 脱模温度低于成型塑料的热变形温度。
● 最佳料温使物料具有良好的性能,且不产生变质的温度。
一般螺杆注射机的最佳料温比柱塞注射机低10—20度。
● 合适料温判断:采用对空注射观察法或直接观察塑件的质量好坏。
对空注射时,如果料流均匀、光滑、无泡、色泽均匀则说明料温不合适。
如果料毛糙、有银丝或变色现象说明不合适。
2、压力:●注射成型时需要选择与控制的压力有:注射压力、保压力和塑化压力。
●注射压力与注射速度相符相承,对塑料的流动和充模具有决定作用。
●保压力和保压时间密切相关,主要影响模腔压力以及最终成型质量。
3、成型周期二、设置加强筋的目的:在不增加塑件壁厚的情况下增加塑件的刚性防止塑件变形。
筋条方向不妨碍脱模、不能使塑件壁厚不均匀。
三、塑件尺寸精度和表面粗糙度1、塑件尺寸精度:所获塑件尺寸与产品图中尺寸的符合程度,即所料温:影响塑化和注射充模。
主要取决于料筒和喷嘴俩部分温度。
质控制。
温度 1、得塑件的准确度。
{2、塑件比哦啊面粗糙度:塑件的外观要求越高,粗糙度越低。
成型时尽可能的从工艺上避免冷疤、云纹等缺陷产生除此之外主要取决于与型腔的粗糙度。
磨具比塑件精度高1-2级。
四、注射膜结构①成型零部件:是指动、定模部分中组成模腔零件。
(凸模或型芯、凹模、镶件等组成)决定塑件的尺寸形状。
②、浇注系统:熔融塑料从注射机喷嘴进入模腔所流经的通道。
(主/分流道、浇口、冷料穴)③、导向机构:分为动膜与定膜之间的导向机构和顶出的导向机构俩大类。
④、脱模机构:常见得有推杆、推板、推管脱模机构。
⑤侧面分型与抽芯机构:在塑件侧面有凹凸形状的孔或凸台时就要侧分型。
⑥加热和冷却系统 ⑦排气系统 ⑧支撑零部件●开模行程:是指动模固定板能够移动的最大行程。
模具是依靠动模固定板的移动实现合拢或打开,确定开模行程的需要量时,应以保证打开后顺利取出为度。
●影响因素:①磨具制造精度和磨损程度 ②塑料收缩率的波动以及成型时工艺参数的变化、塑件成型后时效变化和模具结构形状等。
注塑模具设计基本知识
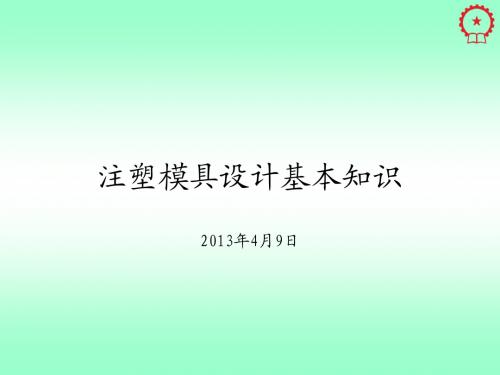
Hale Waihona Puke 注塑模具设计基本知识2012年7月12日
一、单分型面注射模
1.单分型面注射模结构
单分型面注射模又称为两板式模。它是注射模中最简单的一 种结构形式。这种模具只有一个分型面,其典型结构如图3.1单 分型面注射模结构所示。单分型面注射模具根据需要,既可以设 计承单型腔注射模,也可以设计成多型腔注射模,应用十分广泛。
二、UG注塑模具基本知识
3.UG手工分模步骤
(1)打开零件,进入建模环境,确定模具坐标系; (2)设置收缩率(使用“比例体”命令,或使用“变换”命 令中“比例”命令); (3)使用“拉伸”命令制作工件; (4)作分型面(使用建模环境中各种命令,如曲面命令、投 影曲线、抽取几何体、有界平面、修剪片体、缝合等); (5)使用“求差”命令对工件与零件求差(注意保留工具 体),再使用“分割体”命令分出型芯与型腔; (6)使用“变换”命令中“平移”命令创建模具分解视图; (7)制作侧抽芯机构(使用拉伸、求交、求差等命令); (8)添加模架与标准件。
二、UG注塑模具基本知识
2.UG模具设计步骤
(1)准备好零件图,制作或装载零件。 (2)多模腔设计。 (3)确定模具坐标系。 (4)确定收缩率。 (5)设计工件。 (6)分型(或叫分模)。 (7)添加模架与标准件。 (8)制作电极。 (9)剪裁标准件与腔体。 (10)给出材料清单。 (11)产生零件图与装配图。
2.单分型面注射模的组成
按机构组成,单分型面注射模可由成形零部件、浇注系 统、导向系统、推出装置、温度调节系统和结构零部件组成。 单分型面注射模零件
一、单分型面注射模
3.单分型面注射模的工作过程
单分型面注射模的一般工作过程为:模具闭合—模具紧锁—注射— 保压—补塑—冷却—开模—推出塑件。下面以图3.1为例介绍单分型面 注射模的工作过程。 在导柱8和导套9的导向定位下,动模和定模闭合。型腔零件由定模 板2与动模板1和型芯7组成,并由注射机合模系统提供的锁模力锁紧; 然后注射机开始注射,塑料熔体经定模上的浇注系统进入型腔;待熔 体充满型腔并经过保压、补塑和冷却定型后开模,开模时,合模注射 机系统带动动模后退,模具从动模和定模分型面分开,塑件包在型芯7 上随动模一起后退,同时,拉料杆15将浇注系统的主流道凝料从浇口 套中拉出。当动模移动一定距离后,注射机的顶杆21接触推板13,推 出机构开始动作,使推杆18和拉料杆15分别将塑件及浇注系统凝料从 型芯7和冷料穴中推出,塑料与浇注系统凝料从模具中落下,至此完成 一次注射过程。合模时,推出机构靠复位拉杆复位,并准备下一次注 射。
- 1、下载文档前请自行甄别文档内容的完整性,平台不提供额外的编辑、内容补充、找答案等附加服务。
- 2、"仅部分预览"的文档,不可在线预览部分如存在完整性等问题,可反馈申请退款(可完整预览的文档不适用该条件!)。
- 3、如文档侵犯您的权益,请联系客服反馈,我们会尽快为您处理(人工客服工作时间:9:00-18:30)。
1、塑料是一种以树脂为主要成分,以添加剂(增塑剂、稳定剂、填充剂、增强剂、着色剂、润滑剂、特殊助剂、其他主要助剂)为辅助成分的高分子化合物。
增塑剂:为了改善聚合物成型时的流动性能和增进之间的柔顺性。
稳定剂:制止或者抑制聚合物因受外界因素影响所引起破坏作用。
填充剂:为了降低成本改善之间的某些使用性能,赋予材料新特性。
增强剂:使塑件力学性能得到补强。
着色剂:赋予塑料以色彩或特殊的光学性能。
润滑剂:改善塑料熔体的流动性能,减少、避免对成型设备的摩擦、磨损和粘附,改进制品表面粗糙度。
2、塑料的特性:相对分子质量大;在一定的温度和压力作用下有可塑性。
3、聚合物(树脂)通常有天然和合成两大类型。
对聚合物的选择主要是从分子量大小及分布、颗粒大小、结构以及与增塑剂、溶剂等相互作用的难易程度等诸方面考虑。
4、聚合物的作用:胶粘其他成分材料;赋予材料可塑性。
5、塑料的分类:根据来源:天然树脂、合成树脂。
根据制造树脂的化学反应类型:加聚型塑料、缩聚型塑料。
根据聚合物链之间在凝固后的结构形态:非结晶型、半结晶型、结晶型。
根据应用角度:通用塑料、工程塑料根据化学结构及基本行为:热固性、热塑性塑料。
6、塑料的实用性能:轻巧美观、电气绝缘、热物理性能、力学性能、减震消音、防腐耐蚀。
7、塑料的技术指标:密度、比容、吸水率、拉伸强度、冲击强度、弯曲强度、弹性模量、马丁耐热、热变形温度等。
8、线性非结晶型聚合物在不同温度下所处的力学状态:g T T 聚合物处于玻璃态;处于高弹态f g T T T <<;f T T <粘流态。
9、玻璃态聚合物力学行为特点:内聚能大,弹性模量高,在外力作用下只能通过高分子主链键长、键角微笑改变发生变形。
10、高弹态聚合物力学行为特点:弹性模量与玻璃态相比显著降低,在外力作用下分子链段可发生运动 11、黏流态聚合物力学行为特点:整个分子链的运动变为可能,在外力作用下,材料科发生持续性变形,变形主要是不可逆的黏流变形。
12、成型加工的主要参数:收缩率、比体积和压缩率、流动性、吸湿性热敏性、结晶性、应力开裂及熔体破裂、定型速度。
13、成型收缩主要表现在:塑件的线尺寸收缩、收缩方向性、后收缩、后处理收缩。
14、影响收缩率变化的因素:塑料品种、塑件结构、模具结构、成型工艺。
15、防止塑料分解的措施:添加稳定剂;合理选择设备;正确控制成型温度和成型周期;及时清理设备中分解物。
合理设计模具浇注系统等。
16、减少或消除塑件内应力措施:合理选择成型条件,正确设计塑件结构,增加脱模斜度,合理选择浇口及顶出形式,适当调节料温、模温、注射压力及冷却时间,对塑件进行后处理,防止塑件与溶剂接触。
17、硬化速度:通常是以塑料式样硬化1mm 厚度所需的时间来表示s/mm18、注射成型是将热塑性塑料加工成型的主要方法。
19、研究注塑的目的:在循环时间和废品率最小的前提下保证制品有预定的性能。
20、常规注射成型加工系统是指热塑性材料通过注射成型系统,包括被加工的塑料原料和成型好的塑件,以及用来成型加工的注射机、注塑模等。
21、注射成型的优点:生产效率高、劳动强度低、制品无需休整或少量休整、可以成型复杂制品、设计灵活、废料损耗低、可以得到小的公差。
缺点:投入要求高;缺乏专门的技术和良好的保养,可能会造成高启动费和运作费;产品质量难以时刻保证;设计的技术和交叉学科的知识多、难于掌握;制品的结构有时不适合高效成型。
22、完整的注射成型工艺过程包括:成型前准备(外观检验、染色造粒、干燥)、注塑机上成型和成型所得制品的热处理和调湿处理。
23、注射机由合模机构、塑化装置、注塑装置和控制系统构成。
24、塑化:指塑料在料筒内经过加热达到流动状态,并具有良好的可塑性的过程。
25、成型周期可分为成型时间和辅助操作时间。
26、注射成型塑料所经过的三个阶段:塑料未进入料筒前的颗粒状态(颗粒流);塑料在料筒中的塑化运动而达到熔融状态(稳定流懂);通过注塑模浇注系统的充模流动及冷却定型(充模流动)。
27、熔体在型腔内的流动类型:湍流和层流流动充模。
28、流动距离比是衡量熔融树脂流动性能的一个重要参数。
29、注塑模中保压的作用:使熔体紧密贴合型腔壁,精确取得型腔的型样;使不同时间、不同流向的熔体相互熔合;使成型物料的密度增加。
30、模具出现变形的结果:使平制品的厚度大于型腔厚度;增大了厚度的不均匀性。
31、树脂固化过程中发生的主要现象是收缩。
32、型腔内塑料冷却过程是其内部的熔体先将其热量传导给外面的凝固层,凝固层再将热量传给型腔壁,最后由模具向外散发。
33、注射成型的工艺的三要素(条件):温度(料筒、喷嘴、模具、油温度)、压力(塑化、注射、保压、合模、顶出)、时间。
34、料筒温度和模具温度主要影响塑料的塑化与流动;模具温度对塑料的流动与冷却定型起决定性作用。
35、喷嘴和浇口的作用是为了加速熔体的流速、把势能转变为动能,并有调整熔体温度和均匀化温度的左右。
36、一般注射成型前都会通过“对空注射法”和“直观分析法”来调整成形工艺,以确定合适的料筒温度和喷嘴温度。
37、控制模具温度的方法有:自然散热、水冷却、电热丝、电热棒加热。
38、模具温度的控制方法:通入定温的冷却介质来控制;考熔体注入模具自然散热达到平衡;用电加热使模具保持定温。
39、注射压力的主要作用:克服塑料熔体从料筒向型腔的流动阻力;给予熔体一定的充模速率。
40、在各项条件都相同的情况下,柱塞式注射压力比螺杆的要大,是因为柱塞式注塑机料筒内压力损失大。
41、成型质量要素一般包括:外观性的、尺寸精度性的、功能性等内容42、塑件生产四要素:材料选择(成功前提)、产品设计、模具设计(成功关键)、成型工艺(成功保证)。
43、塑料注射成型所用的模具为注塑模;注塑模特点是模具先由注塑机合模机构紧密闭合,然后由注塑机的注射装置将高温高压的塑料熔体注入模腔,经冷却或固化定型后,开模取出塑件。
44、注塑成型的特点:注射是在封闭的模腔中进行;过程受多种工艺参数影响;成型过程有热交换作用并伴随着相变和聚集态变化。
45、注塑模的八大部件:成型零部件、浇注系统、导向部件、脱模机构、分型抽芯机构、调温系统、排气系统、其他零部件。
46、注塑机技术规范包括:最大注射量、最大注射压力、最大锁模力、模具安装尺寸及开模行程。
47、最大注射量有:注射容量、注射重量两种表示方法。
最大注射容量:指注塑机对空注射时,螺杆一次最大行程所射出的塑料体积,以cm3表示。
最大注射重量:指注塑机对空注射时,螺杆做一次最大注射行程所能射出聚苯乙烯塑料重量。
48、注塑机油路系统提供最大压力下所获得的注射压力称为最大注射压力。
49、工艺参数的校核:最大注射量、注射压力;安装尺寸的校核:喷嘴尺寸、定位圈尺寸、模具外形尺寸、模具厚度。
50、浇注系统的组成由:主流道、分流道、冷料井和浇口组成51、浇注系统的作用:是塑料熔体平稳有序地充满型腔,并在填充和凝固过程中吧注塑压力充分传递到各个部分,以获得组织紧密的塑件。
52、浇注系统的设计原则:重点考虑型腔布局、热量及压力损失小、均衡进料、塑料耗量少、消除冷料、排气良好、防止塑件出现缺陷、塑件外观美观、生产效率高、塑料熔体流动性好。
53、主流道的作用:将注塑机喷出的塑料熔体导入分流道或型腔中。
分流道的作用:使塑料熔体的流向得到平稳的转化并尽快的充满型腔。
冷料井的作用:贮存冷料,拉出凝料。
54、分流道的设计要点:流动阻力竟可能小;转折处以圆角过渡;各型腔要保持均衡进料;表面粗糙度以0.8为佳;分流道过长时设置冷料井。
55、分流道的截面形状有:圆形、梯形、U形、六角形;其不知道形式有平衡式(人工平衡、自然平衡)和非平衡式。
56、浇口的作用:型腔充满后,绒料在浇口处首先凝结防止倒流;易于切除浇口尾料;对于多型腔模具,用以控制熔接缝的位置。
(浇口:点浇口、潜伏式浇口、侧交口、重叠式浇口、扇形浇口、平缝式浇口、盘形浇口、圆环形浇口、轮辐式浇口与爪形浇口、护耳浇口)57、浇口位置选择原则:避免制件上产生喷射等缺陷;浇口应开设在塑件界面最厚处;有利于塑料熔体流动;有利于型腔排气;考虑塑件使用时的载荷状况;通过减少或避免塑件的熔接痕来增强牢度;考虑分子取向对塑件性能的影响;考虑浇口位置和数目对塑件尺寸的影响;校核流动距离比;防止将型芯或者嵌件挤歪变形。
58、为使大小不同的型腔能够同时充满需采用的措施:加长到较小模腔的流道长度;减小到较小模腔流道的截面尺寸、改变进入模腔的浇口尺寸(即人工平衡)。
59、在注塑模中,成型零部件有:凹模、凸模、成型杆、成型环。
60、型腔数目的确定方法:根据经济性确定型腔数目;根据注塑机的额定锁模力确定;根据制品精度确定;根据注塑机最大注射量确定。
61、分型面:是动定模具的分界面,即打开模具取出模具塑件或浇注系统、凝料的面。
62、分型面的选择原则:保证塑件质量、便于制品脱模和简化模具结构。
主要表现在:分型面的位置设在塑件截面尺寸最大位置处;有利于保证塑件尺寸精度;有利于保证塑件外观质量;考虑满足塑件的使用要求;考虑注塑机的技术规格;考虑锁模力,尽量减小塑件在分型面的投影面积;尽可能将塑件留在动模一侧;考虑侧向抽拔距;尽量方便浇注系统布置;便于排气;模具易于加工。
63、排气系统的作用是把模具型腔内的空气、塑料所产生的气体排放到模具之外,保证熔体在充模过程中的正常流动。
排气不良的危害:充填不足;影响表面质量;产生高温;形成流动痕和熔合痕;降低充模速度。
64、凹模的结构类型:整体式、整体嵌入式、局部镶嵌式、大面积镶嵌式、四壁镶嵌式。
凸模的结构类型:整体式、组合式、成型杆组合式、异形型芯结构式。
65、螺纹型芯:圆柱配合面固定螺纹型芯、弹性连接固定螺纹型芯。
螺纹型环:整体螺纹型环、组合式螺纹型环。
66、成型零件工作尺寸的计算方法:平均收缩率法和公差带法。