工业催化剂的制备浸渍法
综合化学实验报告浸渍法教学
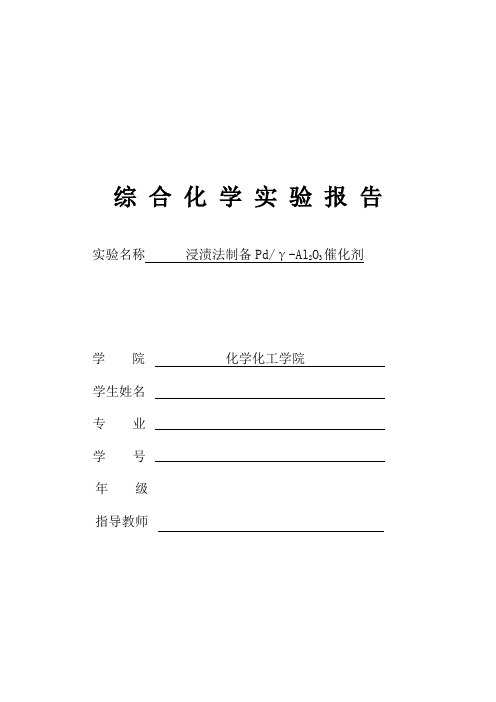
综合化学实验报告实验名称浸渍法制备Pd/γ-Al2O3催化剂学院化学化工学院学生姓名专业学号年级指导教师浸渍法制备Pd/γ-Al2O3催化剂摘要:浸渍法是将载体浸泡在含有活性组分(主,助催化剂组分)的可溶性化合物溶液中,接触一定的时间后除去过剩的溶液,再经干燥,焙烧和活化,即可制得催化剂。
本实验采用等体积浸渍法制备负载型Pd/γ-Al2O3催化剂。
实验中首先测出γ-Al2O3的饱和吸附量,进而计算出采用等体积浸渍法时所需的含有活性组分Pb2+的PbCl2溶液和水的量,然后将载体γ-Al2O3浸泡在适量的含有活性组分Pb2+的PbCl2溶液与适量的水的混合液中,接触一定的时间后,再经干燥,焙烧和活化,即可制得催化剂。
关键字:等体积浸渍法催化剂Pd/γ-Al2O30 引言:固体催化剂的制备方法很多,工业上使用的固体催化剂的制备方法有:沉淀法,浸渍法,机械混合法,离子交换法,熔融等[1]。
由于制备方法的不同,尽管原料和用量完全一样,但所制得的催化剂的性能仍可能有很大的差异。
浸渍法是将载体浸泡在含有在活性组分(主,助催化剂组分)的可溶性化合物溶液中,接触一定的时间后除去过剩的溶液,再经干燥,焙烧和活化,即可制得催化剂[2]。
由于浸渍法比较经济,且催化剂形状、表面积、孔隙率等主要取决于载体,容易选取。
等体积浸渍法是预先测定载体吸入溶液的能力,然后加入正好使载体完全浸渍所需的溶液量,这种方法称为等体积浸渍法。
应用这种方法可以省去过滤多余的浸渍溶液的步骤,而且便于控制催化剂中活性组分的含量。
因此,本实验采用等体积浸渍法[3][4]制备负载型Pd/γ- Al2O3催化剂。
实验中首先测出γ- Al2O3的饱和吸附量,进而计算出采用等体积浸渍法时所需的含有活性组分Pb2+的PbCl2溶液和水的量,然后将载体γ- Al2O3浸泡在适量的含有活性组分Pb2+的PbCl2溶液与适量的水的混合液中,接触一定的时间后,再经干燥,焙烧和活化,即可制得催化剂。
催化剂浸渍法

催化剂浸渍法
浸渍法,是催化剂工业生产中应用的方法,是以浸渍为关键和特殊步骤制造催化剂的方法。
浸渍法是目的催化剂工业生产中广泛应用的一种方法。
浸渍法是基于活性组分(含助催化剂),以盐溶液形态浸渍列多孔载体上并渗透列内表面,而形成高效催化剂的原理。
通常将含有活性物质的液体去浸各类载体,当浸渍平衡后,去掉剩余液体,再进行与沉淀法相同的干燥、焙烧、活化等工序后处理。
经干燥,将水分蒸发逸出,可使活性组分的盐类遗留在载体的内表面上,这些金属和金属氧化物的盐类均匀分布在载体的细孔中,经加热分解及活化后,即得高度分散的载体催化剂。
活性溶液必须浸在载体上,常用的多孔性载体有氧化铝、氧化硅、活性炭、硅酸铝、硅藻土、浮石、石棉、陶土、氧化镁、活性白土等,可以用粉状的,也可以用成型后的颗粒状的。
氧化铝和氧化硅这些氧化物载体,就像表面具有吸附性能的大多数活性炭一样,很容易被水溶液浸湿。
另外,毛细管作用力可确保液体被吸人到整个多孔结构中,甚至一端封闭的毛细管也将被填满,而气体在液体中的溶解则有助于过程的进行。
但也有些载体难于浸湿,例如高度石墨化或没有化学吸附氧的碳就是这样,可用有机溶利或将载体在抽空下浸渍。
综合化学实验报告 浸渍法
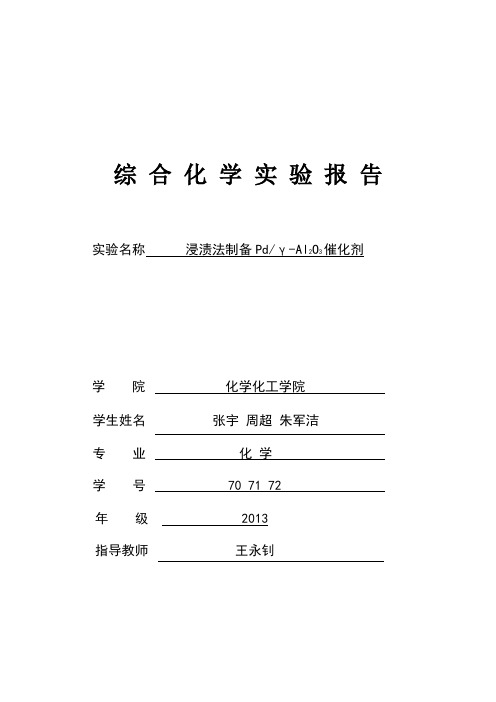
综合化学实验报告实验名称浸渍法制备Pd/γ-Al2O3催化剂学院化学化工学院学生姓名张宇周超朱军洁专业化学学号 70 71 72年级 2013 指导教师王永钊浸渍法制备Pd/γ-Al2O3催化剂张宇周超朱军洁(山西大学化学化工学院,山西太原 030006)摘要:浸渍法是将载体浸泡在含有活性组分(主,助催化剂组分)的可溶性化合物溶液中,接触一定的时间后除去过剩的溶液,再经干燥,焙烧和活化,即可制得催化剂。
本实验采用等体积浸渍法制备负载型Pd/γ-Al2O3催化剂。
实验中首先测出γ-Al2O3的饱和吸附量,进而计算出采用等体积浸渍法时所需的含有活性组分Pb2+的PbCl2溶液和水的量,然后将载体γ-Al2O3浸泡在适量的含有活性组分Pb2+的PbCl2溶液与适量的水的混合液中,接触一定的时间后,再经干燥,焙烧和活化,即可制得催化剂。
关键字:等体积浸渍法催化剂Pd/γ-Al2O30 引言:固体催化剂的制备方法很多,工业上使用的固体催化剂的制备方法有:沉淀法,浸渍法,机械混合法,离子交换法,熔融等[1]。
由于制备方法的不同,尽管原料和用量完全一样,但所制得的催化剂的性能仍可能有很大的差异。
浸渍法是将载体浸泡在含有在活性组分(主,助催化剂组分)的可溶性化合物溶液中,接触一定的时间后除去过剩的溶液,再经干燥,焙烧和活化,即可制得催化剂[2]。
由于浸渍法比较经济,且催化剂形状、表面积、孔隙率等主要取决于载体,容易选取。
等体积浸渍法是预先测定载体吸入溶液的能力,然后加入正好使载体完全浸渍所需的溶液量,这种方法称为等体积浸渍法。
应用这种方法可以省去过滤多余的浸渍溶液的步骤,而且便于控制催化剂中活性组分的含量。
因此,本实验采用等体积浸渍法[3][4]制备负载型Pd/γ- Al2O3催化剂。
实验中首先测出γ- Al2O3的饱和吸附量,进而计算出采用等体积浸渍法时所需的含有活性组分Pb2+的PbCl2溶液和水的量,然后将载体γ- Al2O3浸泡在适量的含有活性组分Pb2+的PbCl2溶液与适量的水的混合液中,接触一定的时间后,再经干燥,焙烧和活化,即可制得催化剂。
化学催化剂的制备方法

化学催化剂的制备方法化学催化剂在各个领域中都扮演着重要的角色,例如在工业化生产、环境保护和能源转化等方面。
制备高效的催化剂对于提高反应效率和产品选择性至关重要。
本文将介绍几种常见的化学催化剂制备方法。
一、沉积法沉积法是制备催化剂常用的方法之一。
通过在载体上制备沉积层,可以增加催化剂的活性和选择性。
常用的沉积法包括浸渍法和气相沉积法。
浸渍法是将载体浸泡在催化剂溶液中,使催化剂沉积于载体表面。
这种方法具有操作简单、适用范围广的优点。
气相沉积法则是利用气体反应生成沉积物,常见的气相沉积方法有化学气相沉积和物理气相沉积。
二、共沉淀法共沉淀法是通过共沉淀过程制备催化剂。
通常将两个或多个金属盐溶液混合,在适当的条件下发生沉淀反应,生成催化剂。
这种方法可以调控催化剂的成分以及晶体结构,从而影响催化剂的性能。
三、溶胶-凝胶法溶胶-凝胶法是利用溶胶和凝胶的特性,在溶胶阶段形成固体凝胶,并通过热处理生成催化剂。
这种制备方法具有成本低、适用范围广的特点。
四、微乳液法微乳液法是一种在溶胶和凝胶形成前,通过适当的界面活性剂和助剂形成的稳定微乳液中制备催化剂。
这种方法能够控制催化剂的形貌和粒径,从而影响催化剂的活性和选择性。
五、溶胶自组装法溶胶自组装法是一种制备催化剂的较新方法。
通过选择具有亲疏水性的功能分子,在溶液中自组装形成乳液,进而生成催化剂。
这种制备方法能够调控催化剂的孔径和分散度,提高催化剂的性能。
六、共沉淀-还原法共沉淀-还原法是一种通过先共沉淀生成前驱体,再进行还原处理制备催化剂的方法。
这种方法能够调控催化剂的成分和晶体结构,从而影响催化剂的活性和选择性。
在使用以上制备方法时,还可以通过调控反应条件、添加助剂等手段进一步改善催化剂的性能。
此外,还可以采用纳米材料制备方法来制备纳米尺度的催化剂,提高效率和选择性。
总之,化学催化剂的制备方法多种多样,每种方法都有其适用范围和特点。
通过合理选择制备方法和优化制备条件,可以制备出高效、高选择性的催化剂,促进各领域的化学反应。
制备工业催化剂的方法

制备工业催化剂的方法工业催化剂是指用于促进或加速化学反应的物质,广泛应用于许多生产过程中,如炼油、化工、能源等。
制备工业催化剂的方法有很多种,下面将介绍几种常见的制备方法。
一、沉淀法沉淀法是制备工业催化剂的常用方法之一、该方法通过在溶液中加入还原剂使金属离子还原成金属颗粒,然后沉淀得到催化剂。
该方法简单易行,适用于大规模生产。
二、浸渍法浸渍法是指将载体浸入金属溶液中,使金属离子被载体吸附,并通过热处理将金属还原成金属颗粒。
浸渍法可使金属颗粒分散均匀,催化剂活性较高。
三、沉积法沉积法是将金属源溶于溶剂中,然后将溶液喷洒在载体表面,通过烘干和热处理将金属还原成金属颗粒,从而制备催化剂。
该方法适用于制备高活性催化剂。
四、共沉淀法共沉淀法是将金属源和载体溶解在同一溶剂中,通过调节条件使金属沉淀到载体表面,再进行热处理得到催化剂。
共沉淀法制备的催化剂具有高分散性和高活性。
五、焙烧法焙烧法是将金属前驱体或金属盐溶于溶剂中,通过热处理使金属变得稳定且易于使用,然后得到催化剂。
焙烧法制备的催化剂适用于高温条件下的反应。
六、溶胶-凝胶法溶胶-凝胶法是将金属前驱体溶于溶剂中,通过加热使其形成溶胶,然后通过凝胶化得到凝胶,在热处理过程中形成催化剂。
该方法制备的催化剂具有高度分散性和活性。
七、离子交换法离子交换法是将金属离子与载体接触,通过离子交换反应将金属离子固定在载体上,形成催化剂。
离子交换法制备的催化剂具有高度分散性和稳定性。
综上所述,制备工业催化剂的方法有很多种,选择适当的制备方法取决于催化剂的要求和实际应用。
通过不断研究和创新,制备高效、高分散性和高稳定性的工业催化剂对促进化工和工业生产的发展具有重要作用。
催化剂制备方法
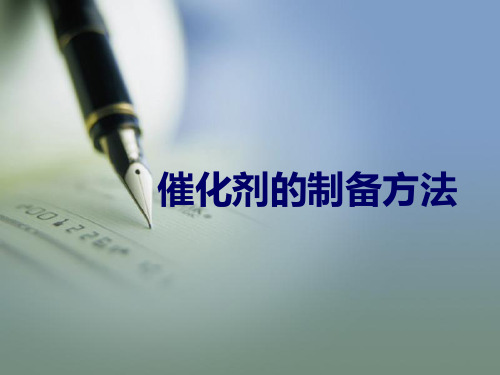
关于浸渍时间的几种情况:
1)活性组分在孔壁的吸附速率快于扩散速率,导致活 性组分吸附在孔口(时间或活性组分浓度不够);
2)浸渍后过滤,静臵,吸附的活性成分重新解吸,通
过再分配实现均匀分布(不立刻干燥); 3)浸渍后不过滤,载体外活性成分不断扩散至孔道内, 实现均匀分布(增加浸渍时间)。
3)浸渍前载体的状态 载体状态不同使组分在载体内部 的分布不均匀,且当浸渍液浓度愈 大,不均匀性愈显著。在同样浓度 的浸渍液条件下,干燥载体内浸渍 组分的分布比湿载体时均匀。
匀 pH稳定 多组分同时 沉淀 沉淀均 匀
(5)pH值 沉淀法中常用碱性物质作沉淀剂,沉 淀物的生成在相当大的程度上受溶液的 pH值得影响
沉淀方法的分离 1)单组分沉淀法 单组份沉淀法是通过沉淀剂与一种特 殊组分溶液作用以制备单一组分沉淀物 的方法。 例:氧化铝的制备 碱法:Al3+ + OH- Al2O3· nH2O 酸法:AlO2- + H3O+ Al2O3· nH2O
浸渍法的影响因素: 1)盐浓度盐、铵盐、有 机酸盐(乙酸盐、乳酸盐)
浸渍液浓度:
催化剂中活性组分含量(以氧化物计)
a
VpC 1 VpC
100%
浸渍液浓度(以氧化物计),g/ml
载体比孔容,ml/g
2)浸渍时间: t=2η/δx x2/r 渗透时间与粘度系数、表面张力、孔径 和粒度有关 在氧化铝上浸渍含Ni化合物
2.分子筛的制备 制备分子筛主要通过混合液成胶、晶化、洗 涤、成型及活化等步骤。以下介绍影响分子筛 制备的几个因素。 (1)硅铝比。不同型号的分子筛有其固定的硅铝 比,如A型为2.0左右。 (2)基数。基数是指反应物料中氧化铝的摩尔浓 度。A型为0.2-0.3mol/L. (3)碱度。指晶化过程中,反应液中所含碱的浓 度,一般以Na2O的摩尔度表示。 (4)晶化温度和晶化时间。一般规律是,高温晶 化需时短,低温晶化需时长。 (5)成胶温度。一般情况下,温度越高越易成胶。
工业催化--第八章 工业催化剂制备原理

– 待沉淀析出后,加入较大量热水稀释,以减少杂 质在溶液中的浓度,同时使一部分被吸附的杂质 转入溶液。
加入热水后,一般不宜放置,而应立即过滤,以防沉 淀进一 步凝聚,并避免表面吸附的杂质包裹在沉淀内 部不易洗净。
洗涤操作的主要目的是除去沉淀中的杂质。
均匀沉淀法常用的类似沉淀母体见下表:
4、浸渍沉淀法
浸渍沉淀法是在普通浸渍法的基础上辅以沉淀 法发展起来的一种新方法。
– 待盐溶液浸渍操作完成之后,再加沉淀剂,而使待 沉淀组分沉积在载体上。
5、导晶沉淀法
借助晶化导向剂(晶种)引导非晶型沉淀转化为 晶型沉淀的快速而有效的方法。
– 普遍用来制备以水玻璃为原料的高硅钠型分子筛, 包括丝光沸石,Y型与X型合成分子筛。
对沉淀剂选择有以下要求:
(1) 尽可能使用易分解并含易挥发成分的沉淀剂
– 常用的沉淀剂有:
碱类(NH4OH、NaOH、KOH); 碳酸盐[(NH4)2CO4、Na2CO4、CO2]; 有机酸(乙酸、草酸)等。 最处理常时用容的易是除NH去4O,H一和般(N不H会4)2遗CO留4,在因催为化铵剂盐中在,洗使涤催和化热剂
如此反复溶解、沉积的结果,消除了细晶体,获得了颗 粒大小均匀的粗晶体。
此时孔隙结构和表面积也发生了相应的变化。
–粗晶体表面积较小,吸附杂质少,吸留在细晶粒之 中的杂质也随溶解过程转入溶液。
– 老化的时间、温度及母液pH值等为老化应考虑的 几项影响因素。
在晶形催化剂制备过程中,老化对催化剂性 能的影响显著。
凝胶法特别适用于主要成分是氧化铝或二氧化 硅的催化剂或载体。
凝胶过程大致可分为缩合与凝结二个阶段。
催化剂 浸渍法
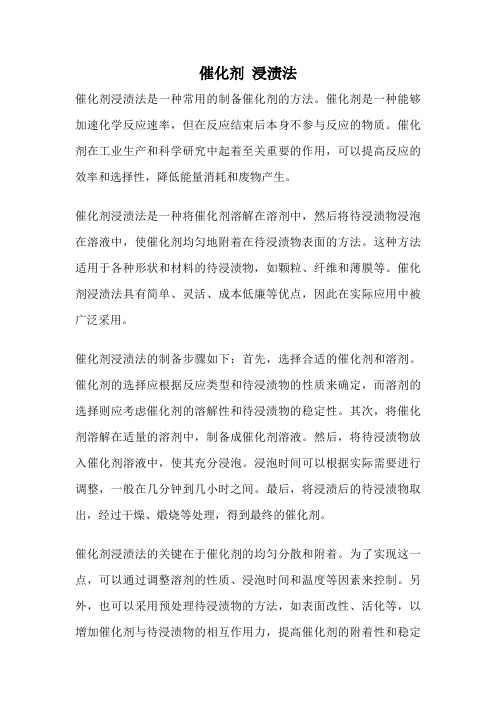
催化剂浸渍法催化剂浸渍法是一种常用的制备催化剂的方法。
催化剂是一种能够加速化学反应速率,但在反应结束后本身不参与反应的物质。
催化剂在工业生产和科学研究中起着至关重要的作用,可以提高反应的效率和选择性,降低能量消耗和废物产生。
催化剂浸渍法是一种将催化剂溶解在溶剂中,然后将待浸渍物浸泡在溶液中,使催化剂均匀地附着在待浸渍物表面的方法。
这种方法适用于各种形状和材料的待浸渍物,如颗粒、纤维和薄膜等。
催化剂浸渍法具有简单、灵活、成本低廉等优点,因此在实际应用中被广泛采用。
催化剂浸渍法的制备步骤如下:首先,选择合适的催化剂和溶剂。
催化剂的选择应根据反应类型和待浸渍物的性质来确定,而溶剂的选择则应考虑催化剂的溶解性和待浸渍物的稳定性。
其次,将催化剂溶解在适量的溶剂中,制备成催化剂溶液。
然后,将待浸渍物放入催化剂溶液中,使其充分浸泡。
浸泡时间可以根据实际需要进行调整,一般在几分钟到几小时之间。
最后,将浸渍后的待浸渍物取出,经过干燥、煅烧等处理,得到最终的催化剂。
催化剂浸渍法的关键在于催化剂的均匀分散和附着。
为了实现这一点,可以通过调整溶剂的性质、浸泡时间和温度等因素来控制。
另外,也可以采用预处理待浸渍物的方法,如表面改性、活化等,以增加催化剂与待浸渍物的相互作用力,提高催化剂的附着性和稳定性。
催化剂浸渍法在许多领域都有应用。
例如,在环境保护领域,可以将催化剂浸渍在吸附剂上,用于废气处理和水处理等。
在化工生产中,可以将催化剂浸渍在载体上,用于合成有机化合物或合成高分子材料。
在能源领域,可以将催化剂浸渍在电极上,用于燃料电池和光催化反应等。
此外,催化剂浸渍法还可以用于制备催化剂的载体材料,如氧化铝、硅胶等。
催化剂浸渍法是一种简单、灵活、成本低廉的制备催化剂的方法。
它可以将催化剂均匀地分散和附着在待浸渍物表面,提高反应的效率和选择性。
催化剂浸渍法在各个领域都有广泛应用,为工业生产和科学研究提供了重要的支持。
随着科学技术的不断进步,催化剂浸渍法的制备方法也在不断改进和创新,为催化剂的研究和应用带来了更多的可能性。
催化剂制备方法

浸渍法的影响因素: 1)盐浓度:
➢ 活性组分金属的易溶盐 —— 硝酸盐、铵盐、有机 酸盐(乙酸盐、乳酸盐)
➢ 浸渍液浓度:
催化剂中活性组分含量(以氧化物计)
a VpC 100% 1 VpC
载体比孔容,ml/g 浸渍液浓度(以氧化物计),g/ml
2)浸渍时间: t=2η/δx x2/r
渗透时间与粘度系数、表面张力、孔径 和粒度有关
Al2O3·nH2O
(2)共沉淀法
共沉淀法是将催化剂所需的两个或两 个以上组分同时沉淀的一个方法。
注意:
各金属盐、沉淀剂浓度、介质pH值、 加料方式等条件件必须满足各个组分同 时沉淀的要求
共沉淀时是否可形成复合碳酸盐的金属
金属
Al
Mg
Ca
Zn
Cu
是
否
否
是
Fe
是
是
否
否
Ni
是
是
否
否
Zn
是
否
否
×
Mg
二、沉淀法制备催化剂举例
1.Al2O3的制备(单组分沉淀剂)
多数情况下都是先制备氧化铝的水合物, 然后将其转化为Al2O3。水合氧化铝一 般有四种:α-Al2O3.3H2O-水氧铝αAl2O3.H2O-水软铝石、βAl2O3.3H2O-拜尔石、βAl2O3.H2O-水硬铝石。
A、α-Al2O3.H2O的制备
在交换过程中,根据交换离子的种类和 交换度的不同,需要注意交换温度、交 换浓度等因素。
分子筛上的离子交换过程:
分子筛的化学组成:
Mn+·[(Al2O3)p·(SiO2)q]·wH2O M 是n价碱金属、碱土金属阳离子,特 别是钠离子。p, q, w分别是氧化硅、氧 化铝、结晶水的分子数。通过改变这些 变数和分子筛晶胞内四面体的排列组合 (链状、层状、多面体等)可以衍生各 种类型分子筛。
催化剂浸渍法原理

zhangwengui330(金币+2,VIP+0):谢谢分享!8-25 15:10概述以浸渍为关键和特殊步骤制造催化剂的方法称浸渍法,也是目前催化剂工业生产中广泛应用的一种方法。
浸渍法是基于活性组分(含助催化剂)以盐溶液形态浸渍到多孔载体上并渗透到内表面,而形成高效催化剂的原理。
通常将含有活性物质的液体去浸各类载体,当浸渍平衡后,去掉剩余液体,再进行与沉淀法相同的干燥、焙烧、活化等工序后处理。
经干燥,将水分蒸发逸出,可使活性组分的盐类遗留在载体的内表面上,这些金属和金属氧化物的盐类均匀分布在载体的细孔中,经加热分解及活化后,即得高度分散的载体催化剂。
活性溶液必须浸在载体上,常用的多孔性载体有氧化铝、氧化硅、活性炭、硅酸铝、硅藻土、浮石、石棉、陶土、氧化镁、活性白土等,可以用粉状的,也可以用成型后的颗粒状的。
氧化铝和氧化硅这些氧化物载体,就像表面具有吸附性能的大多数活性炭一样,很容易被水溶液浸湿。
另外,毛细管作用力可确保液体被吸人到整个多孔结构中,甚至一端封闭的毛细管也将被填满,而气体在液体中的溶解则有助于过程的进行,但也有些载体难于浸湿,例如高度石墨化或没有化学吸附氧的碳就是这样,可用有机溶剂或将载体在抽空下浸渍。
浸渍法有以下优点:第一,附载组分多数情况下仅仅分布在载体表面上,利用率高、用量少、成本低,这对铂、铑、钯、铱等贵金属型负载催化剂特别有意义,可节省大量贵金属;第二,可以用市售的、已成形的、规格化的载体材料,省去催化剂成型步骤。
第三,可通过选择适当的载体,为催化剂提供所需物理结构特性,如比表面、孔半径、机械强度、热导率等。
可见浸渍法是一种简单易行而且经济的方法。
广泛用于制备负载型催化剂,尤其是低含量的贵金属附载型催化剂。
其缺点是其焙烧热分解工序常产生废气污染。
浸渍法工艺浸渍法可分为粉状载体浸渍法和粒状载体浸渍法两种工艺,其特点可由流程图看出。
粒状载体浸渍法工艺如图6—2所示。
粒状载体浸渍前通常先做成一定形状,抽空载体后用溶液接触载体,并加入适量的竞争吸附剂。
2009-12-21催化作用导论--浸渍法

八、浸渍法分类
将载体浸渍在过量溶液中, 过量浸渍法:将载体浸渍在过量溶液中,溶 液体积大于载体可吸附的液体体积, 液体积大于载体可吸附的液体体积,一段时 大于载体可吸附的液体体积 间后除去过剩的液体,干燥、焙烧、 间后除去过剩的液体,干燥、焙烧、活化后 得催化剂成品。 得催化剂成品。
等体积浸渍法:预先测定载体吸入溶液的能
浸渍沉淀法:使载体先浸渍在含有活性组
分的溶液中一段时间后, 分的溶液中一段时间后,然后加入沉淀剂使 活性组分沉淀于载体的内孔和表面 使用场合: 使用场合:制备贵金属催化剂
H2PtCl6盐酸溶液 先 浸 渍 吸附 载体 再加入 NaOH 沉淀
易还原 粒子细
氢氧化铂 沉淀
载体
借助浸渍化合物的挥发性, 蒸气浸渍法:借助浸渍化合物的挥发性,以 蒸气相的形式将其负载于载体上。 蒸气相的形式将其负载于载体上。
120oC 干燥 590oC活化焙烧分解 高温活化还原 负载型重整 重整催化剂 重整
• 镍/氧化铝-----重整催化剂 将甲烷或石脑 氧化铝-----重整催化剂— -----重整催化剂
油重整制合成气
Al2O3+铝酸钙水泥+石墨+水 成型φ16*16*6mm
预处理:120oC干燥、 1400oC焙烧,得载体
四、浸渍法的基本原理
Solution flow into pores
adsorption
1、固体孔隙与液体接触时, 固体孔隙与液体接触时, 由于表面张力的作用而产生 毛细管压力, 毛细管压力,使液体渗透到 毛细管内部。 毛细管内部。 2、活性组分在载体表面的 吸附。 吸附。
Adsorption/ desorption diffusion +
简述催化剂成型的常用方法

催化剂成型的常用方法催化剂成型的重要性催化剂是促进化学反应的物质,它们在化学工业中起着至关重要的作用。
催化剂的性能与其成型方法密切相关,良好的成型方法能够提高催化剂的活性、选择性和稳定性,从而提高反应的效率和产物纯度。
催化剂成型的常用方法催化剂成型涉及多种方法,下面将介绍其中常见的几种方法。
1. 浸渍法浸渍法是最常见的催化剂成型方法之一。
该方法通过将催化剂的载体浸渍于含有所需金属或化合物的溶液中,使其吸附或沉积在载体上。
然后,通过烘干和煅烧等处理,使金属或化合物转化为活性催化剂。
浸渍法的优点是操作简便,适用于各种载体和催化剂的制备。
同时,该方法能够控制催化剂的负载量和分散度,从而调控催化剂的性能。
2. 共沉淀法共沉淀法是一种将催化剂活性成分以沉淀形式沉淀到载体上的方法。
通常,将金属盐和沉淀剂在一定条件下共沉淀,得到催化剂的前驱体。
然后,通过热处理等方法,将前驱体转化为活性催化剂。
共沉淀法能够制备高度分散和均匀负载的催化剂,且对载体的要求较低。
然而,该方法对操作条件和前驱体的选择较为敏感,需要进行精确控制。
3. 模板法模板法是一种利用模板的形状和孔道结构来制备催化剂的方法。
常见的模板包括胶体微球、纳米颗粒和多孔材料。
模板法通过将催化剂活性成分沉积到模板上,并进行热处理,使得模板燃烧或溶解,最终得到具有特定结构和孔道的催化剂。
模板法能够制备高度有序和可控结构的催化剂,可用于合成纳米材料和高效催化剂。
然而,该方法的模板选择和模板去除过程需要一定的技术和设备支持。
催化剂成型的关键因素催化剂成型过程中,需要考虑的关键因素包括催化剂活性成分的选择、载体的选择、成型方法的控制和后续处理等。
1. 催化剂活性成分的选择催化剂活性成分的选择是催化剂成型的关键一步。
活性成分的选择应基于所需反应的特性和机理。
常见的活性成分包括过渡金属、贵金属和酸碱等。
2. 载体的选择载体作为催化剂的基底,对催化剂的性能起着重要影响。
常用的载体材料包括活性炭、氧化物、介孔材料等。
浸渍法
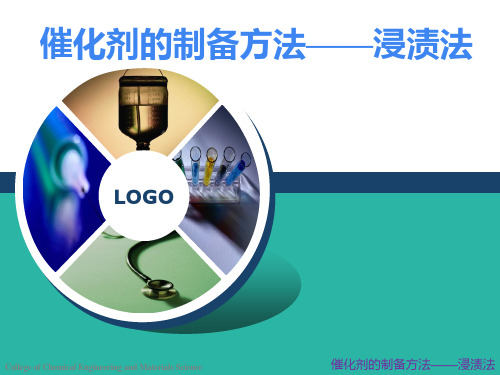
催化剂的制备方法——浸渍法
H+A-
- - + + + - + + + - + + - + + - + - + + + + - - - + + - + + - -- + + + + + +
B+OH-
在酸性介质中,S-OH+H+A-↔S-OH2+ +A-,按双电层理论,粒子带正 电,其周围为带负电的反离子扩散层; 在碱性介质中,S-OH+B+OH-↔S-O-B++H2O,按双电层理论,粒子带 负电,其周围为带正电的反离子扩散层; pH值为某一特定值下,粒子带正负电荷相等,即不带电,或称带零点 电荷(ZPC),此状态称为等电点状态;
载体的抽真空处理
提高载体的吸附容量,保证金属负载量
载体的化学改性处理
例如活性炭载体表面经不同氧化处理后,可产生大量具有 亲水性的基团,提高了对活性组分的锚定作用,使其分散 度提高
预处理条件 未处理 20%HNO370oC 处理 2h 40%HNO370oC 处理 2h 10%HNO340oC 处理 2h 表面酸量 (mmol/g 活性炭) 0.216 0.886 1.621 1.295 活性表面 (m2/g Pd-Pt) 51 87 125 103
催化剂的制备方法——浸渍法
4.1.1 金属盐类
当使用同种活性组分的不同类型金属盐类水溶液时,由于金属盐类中
的配合物与载体浸渍时所产生的配位基置换反应机理不同,所制备的催化
催化剂的制备方法--浸渍法概述
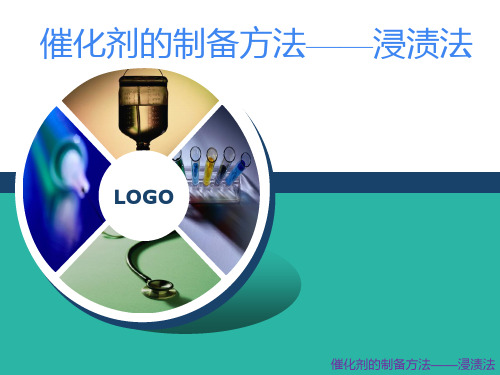
4.2.2 载体的吸附性质
氧化物对金属络离子的吸附决定于以下参数:
氧化物的等电点 浸渍液的pH值 金属络离子的性质
催化剂的制备方法——浸渍法
4.2.3 载体的孔结构
孔容 孔半径
扩散
催化剂
比表面积
活性组分
催化剂的制备方法——浸渍法
4.3 载体预处理的影响
载体的预处理
焙烧 处理 水泡 处理 抽真空 处理
影响 因素
浸渍 条件
载体 预处理 浸渍后 热处理 催化剂
催化剂的制备方法——浸渍法
4.1 浸渍液性质的影响
浸渍液的配制
活性组分金属的易溶盐 —— 硝酸盐、铵盐、有机酸盐(乙酸盐等); 浸渍液浓度(取决于所要求的活性组分负载量):
催化剂中活性组分含量(以氧化物计)
a
VpC 1 VpC
100%
催化剂的制备方法——浸渍法
LOGO
催化剂的制备方法——浸渍法
Content
1 2 3 4 5 6
浸渍法概述
浸渍法基本原理
活性组分的不均匀分布
制备催化剂的影响因素 浸渍法主要工艺 浸渍法制备催化剂示例
催化剂的制备方法——浸渍法
一、浸渍法概述
载体(如Al2O3)的沉淀 载体的成型 载体的预处理 用活性组份溶液浸渍 干燥 焙烧分解 活化(还原) 负载型金属催化剂
—— 广泛用于制备负载型催化剂 (尤其负载型金属催化剂)
催化剂的制备方法——浸渍法
浸渍法( impregnation )是将载体放进含有活性物质的 液体或气体中浸渍,活性物质逐渐吸附于载体的表面,当浸 渍平衡后,将剩下的液体除去,再进行干燥、焙烧、活化等 即可制得催化剂。 浸渍法通常包括载体预处理、浸渍液配制、浸渍、除去 过量液体、干燥和焙烧、活化等过程;
催化剂制备的主要七种工艺
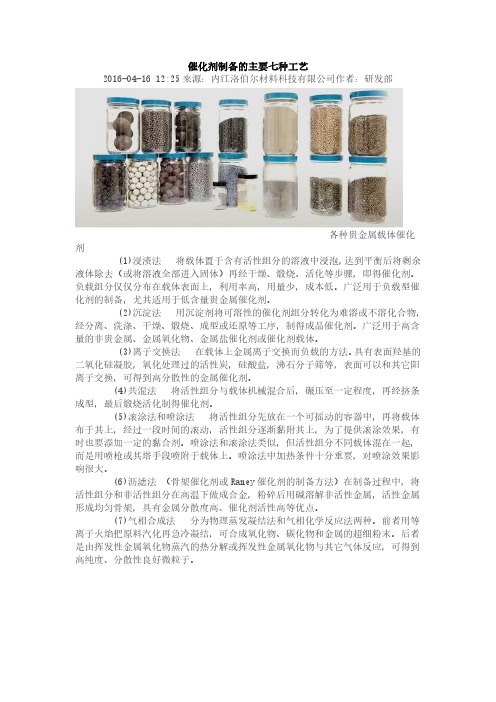
催化剂制备的主要七种工艺2016-04-16 12:25来源:内江洛伯尔材料科技有限公司作者:研发部各种贵金属载体催化剂(1)浸渍法将载体置于含有活性组分的溶液中浸泡,达到平衡后将剩余液体除去(或将溶液全部进入固体)再经干燥、煅烧、活化等步骤,即得催化剂。
负载组分仅仅分布在载体表面上,利用率高,用量少,成本低。
广泛用于负载型催化剂的制备,尤其适用于低含量贵金属催化剂。
(2)沉淀法用沉淀剂将可溶性的催化剂组分转化为难溶或不溶化合物,经分离、洗涤、干燥、煅烧、成型或还原等工序,制得成品催化剂。
广泛用于高含量的非贵金属、金属氧化物、金属盐催化剂或催化剂载体。
(3)离子交换法在载体上金属离子交换而负载的方法。
具有表面羟基的二氧化硅凝胶,氧化处理过的活性炭,硅酸盐,沸石分子筛等,表面可以和其它阳离子交换,可得到高分散性的金属催化剂。
(4)共混法将活性组分与载体机械混合后,碾压至一定程度,再经挤条成型,最后煅烧活化制得催化剂。
(5)滚涂法和喷涂法将活性组分先放在一个可摇动的容器中,再将载体布于其上,经过一段时间的滚动,活性组分逐渐黏附其上,为了提供滚涂效果,有时也要添加一定的黏合剂。
喷涂法和滚涂法类似,但活性组分不同载体混在一起,而是用喷枪或其塔手段喷附于载体上。
喷涂法中加热条件十分重要,对喷涂效果影响很大。
(6)沥滤法(骨架催化剂或Raney催化剂的制备方法)在制备过程中,将活性组分和非活性组分在高温下做成合金,粉碎后用碱溶解非活性金属,活性金属形成均匀骨架,具有金属分散度高、催化剂活性高等优点。
(7)气相合成法分为物理蒸发凝结法和气相化学反应法两种。
前者用等离子火焰把原料汽化再急冷凝结,可合成氧化物、碳化物和金属的超细粉末。
后者是由挥发性金属氧化物蒸汽的热分解或挥发性金属氧化物与其它气体反应,可得到高纯度、分散性良好微粒子。
浸渍法介绍分析

浸渍法概述以浸渍为关键和特殊步骤制造催化剂的方法称浸渍法,也是目前催化剂工业生产中广泛应用的一种方法。
浸渍法是基于活性组分(含助催化剂)以盐溶液形态浸渍到多孔载体上并渗透到内表面,而形成高效催化剂的原理。
通常将含有活性物质的液体去浸各类载体,当浸渍平衡后,去掉剩余液体,再进行与沉淀法相同的干燥、焙烧、活化等工序后处理。
经干燥,将水分蒸发逸出,可使活性组分的盐类遗留在载体的内表面上,这些金属和金属氧化物的盐类均匀分布在载体的细孔中,经加热分解及活化后,即得高度分散的载体催化剂。
活性溶液必须浸在载体上,常用的多孔性载体有氧化铝、氧化硅、活性炭、硅酸铝、硅藻土、浮石、石棉、陶土、氧化镁、活性白土等,可以用粉状的,也可以用成型后的颗粒状的。
氧化铝和氧化硅这些氧化物载体,就像表面具有吸附性能的大多数活性炭一样,很容易被水溶液浸湿。
另外,毛细管作用力可确保液体被吸人到整个多孔结构中,甚至一端封闭的毛细管也将被填满,而气体在液体中的溶解则有助于过程的进行,但也有些载体难于浸湿,例如高度石墨化或没有化学吸附氧的碳就是这样,可用有机溶剂或将载体在抽空下浸渍。
浸渍法有以下优点:第一,附载组分多数情况下仅仅分布在载体表面上,利用率高、用量少、成本低,这对铂、铑、钯、铱等贵金属型负载催化剂特别有意义,可节省大量贵金属;第二,可以用市售的、已成形的、规格化的载体材料,省去催化剂成型步骤。
第三,可通过选择适当的载体,为催化剂提供所需物理结构特性,如比表面、孔半径、机械强度、热导率等。
可见浸渍法是一种简单易行而且经济的方法。
广泛用于制备负载型催化剂,尤其是低含量的贵金属附载型催化剂。
其缺点是其焙烧热分解工序常产生废气污染。
浸渍法工艺浸渍法可分为粉状载体浸渍法和粒状载体浸渍法两种工艺,其特点可由流程图看出。
粒状载体浸渍法工艺如图6—2所示。
粒状载体浸渍前通常先做成一定形状,抽空载体后用溶液接触载体,并加入适量的竞争吸附剂。
也可将活性组分溶液喷射到转动的容器中翻滚到载体上,然后可用过滤、倾析及离心等方法除去过剩溶液。
催化剂的制备方法--浸渍法
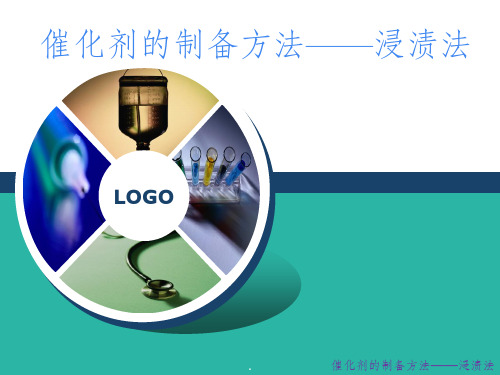
活性炭 硅藻土
浮石 活性白土 炭纤维
催化剂的制备方法——浸渍. 法
4.2.1 载体的选择与预处理
载体的选择因反应不同而异: 如,乙烯精制去除少量乙炔(加氢): Pd / -Al2O3 对载体的要求: Ø 低比表面积、大孔径
(使乙炔加氢产物乙烯尽快脱离催化剂表面)
Ø 无酸性(防止烯、炔的聚合反应,延长催化剂寿命)
缺点
Ø焙烧产生污染气体; Ø干 燥 过 程 会 导 致 活 性 组分迁移;
催化剂的制备方法——浸渍. 法
二、浸渍法基本原理
Ø 固体孔隙与液体接触时,
Solution flow into pores
adsorption
由于表面张力的作用而
产生毛细管压力,使液
Adsorption/desorption + diffusion
催化剂的制备方法——浸渍法
LOGO
.
催化剂的制备方法——浸渍法
Content
1
浸渍法概述
2
浸渍法基本原理
3
活性组分的不均匀分布
4
制备催化剂的影响因素
5
浸渍法主要工艺
6
浸渍法制备催化剂示例
催化剂的制备方法——浸渍. 法
一、浸渍法概述
载体(如Al2O3)的沉淀 载体的成型
—— 广泛用于制备负载型催化剂
浸渍液溶剂多采用去离子水,但当载体成分容易在水溶液中洗提出来时, 或者是要负载的活性组分难溶于水时,就需使用醇类或烃类等溶剂。
由于不同载体的亲疏水性不同,不同溶剂的极性也不同,所以当使用不同 类型的溶剂时,所制备的催化剂上活性组分的分布就不同。
溶剂 水
丙酮
表4-1 溶剂对活性组分在载体上分布的影响
催化剂的制备方法--浸渍法
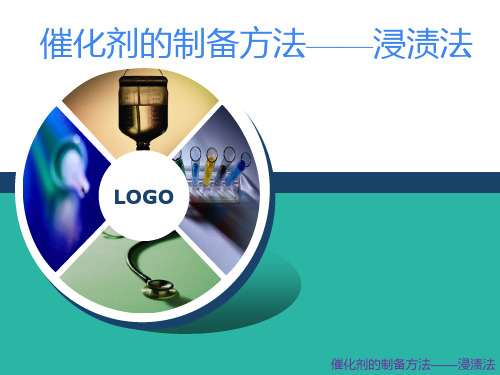
Drying
evaporation
在载体表面吸附;
催化剂的制备方法——浸渍法
三、活性组分的不均匀分布
活性组分分布类型的选择(取决于催化反应宏观动力学) : 均匀型 Uniform 蛋壳型 Egg-shell 蛋白型 Egg-white 蛋黄型 Egg-Yolk
Active phase/Support
冷却、浸渍活性组分前驱体溶液(70%)
干燥、500℃焙烧 冷却、浸渍活性组分前驱体溶液(30%) 干燥、480℃焙烧 高温活化还原、钝化
还原态Ni基 加氢催化剂
催化剂的制备方法——浸渍法
六、浸渍法制备催化剂示例
粉料的捏合
实验室
催化剂的制备方法——浸渍法
六、浸渍法制备催化剂示例
挤条成型
实验室 工业生产
不同类型的溶剂时,所制备的催化剂上活性组分的分布就不同。
表4-1 溶剂对活性组分在载体上分布的影响
溶剂
水 丙酮
H2PtCl6/γ-Al2O3
均匀分布 “蛋壳”型分布
H2PtCl6/活性炭
“蛋壳”型分布 均匀分布
催化剂的制备方法——浸渍法
4.1.3 浸渍液浓度
浓度过高,活性组分在孔内分布不均匀,易得到较粗的金属颗粒 且粒径分布不均匀; 浓度过低,一次浸渍达不到要求,必须多次浸渍,费时费力; 当要求负载量低于饱和吸附量,应采用稀浓度浸渍液浸渍,并延 长浸渍时间或使用竞争吸附剂,使吸附的活性组分均匀分布;
催化剂的制备方法——浸渍法
载体的抽真空处理
提高载体的吸附容量,保证金属负载量
载体的化学改性处理
例如活性炭载体表面经不同氧化处理后,可产生大量具有 亲水性的基团,提高了对活性组分的锚定作用,使其分散 度提高
浸渍法介绍

浸渍法概述以浸渍为关键和特殊步骤制造催化剂的方法称浸渍法,也是目前催化剂工业生产中广泛应用的一种方法。
浸渍法是基于活性组分(含助催化剂)以盐溶液形态浸渍到多孔载体上并渗透到内表面,而形成高效催化剂的原理。
通常将含有活性物质的液体去浸各类载体,当浸渍平衡后,去掉剩余液体,再进行与沉淀法相同的干燥、焙烧、活化等工序后处理。
经干燥,将水分蒸发逸出,可使活性组分的盐类遗留在载体的内表面上,这些金属和金属氧化物的盐类均匀分布在载体的细孔中,经加热分解及活化后,即得高度分散的载体催化剂。
活性溶液必须浸在载体上,常用的多孔性载体有氧化铝、氧化硅、活性炭、硅酸铝、硅藻土、浮石、石棉、陶土、氧化镁、活性白土等,可以用粉状的,也可以用成型后的颗粒状的。
氧化铝和氧化硅这些氧化物载体,就像表面具有吸附性能的大多数活性炭一样,很容易被水溶液浸湿。
另外,毛细管作用力可确保液体被吸人到整个多孔结构中,甚至一端封闭的毛细管也将被填满,而气体在液体中的溶解则有助于过程的进行,但也有些载体难于浸湿,例如高度石墨化或没有化学吸附氧的碳就是这样,可用有机溶剂或将载体在抽空下浸渍。
浸渍法有以下优点:第一,附载组分多数情况下仅仅分布在载体表面上,利用率高、用量少、成本低,这对铂、铑、钯、铱等贵金属型负载催化剂特别有意义,可节省大量贵金属;第二,可以用市售的、已成形的、规格化的载体材料,省去催化剂成型步骤。
第三,可通过选择适当的载体,为催化剂提供所需物理结构特性,如比表面、孔半径、机械强度、热导率等。
可见浸渍法是一种简单易行而且经济的方法。
广泛用于制备负载型催化剂,尤其是低含量的贵金属附载型催化剂。
其缺点是其焙烧热分解工序常产生废气污染。
浸渍法工艺浸渍法可分为粉状载体浸渍法和粒状载体浸渍法两种工艺,其特点可由流程图看出。
粒状载体浸渍法工艺如图6—2所示。
粒状载体浸渍前通常先做成一定形状,抽空载体后用溶液接触载体,并加入适量的竞争吸附剂。
也可将活性组分溶液喷射到转动的容器中翻滚到载体上,然后可用过滤、倾析及离心等方法除去过剩溶液。
- 1、下载文档前请自行甄别文档内容的完整性,平台不提供额外的编辑、内容补充、找答案等附加服务。
- 2、"仅部分预览"的文档,不可在线预览部分如存在完整性等问题,可反馈申请退款(可完整预览的文档不适用该条件!)。
- 3、如文档侵犯您的权益,请联系客服反馈,我们会尽快为您处理(人工客服工作时间:9:00-18:30)。
载体的选择
1.物理因素
适宜的形状、大小、比表面、孔结构 机械强度、耐热性能好 2.化学因素 表面酸碱性和足够的吸水性
不含使催化剂中毒和导致副反应发生的物质
原料易得,制备简单,无污染
通常采用硝酸盐、 氯化物、有机酸盐、 浸渍液的配制 铵盐的浸渍液
蒸气相浸渍法
除了溶液浸渍之外,亦可借助浸渍化合物的挥发 性,以蒸气相的形式将它附载到载体上。这种方 法首先应用正丁烷异构化过程中的催化剂,催化 剂为A1C13/铁钒土。在反应器内先装入铁钒土载 体,然后以热的正丁烷气流将活性组分A1C13气温 升,而有足够的AICl3沉淀在载体铁矾土上后气化, 并使A1C13微粒与丁烷一起通过铁矾土载体的反应 器,当附载量足够时,便转入异构化反应。用此 法制备的催化剂,在使用过程中活性组分也容易 流失。为了维持催化性稳定,必须连续补加浸渍 组分。适用于蒸气相浸渍法的活性组分沸点通常 比较低。
例如,加氢脱硫CO2O3-MoO3/A12()3催化剂的制 备,可将氧化铝先用钴盐溶液浸渍,干燥、焙烧 后再用钼盐溶液按上述步骤处理。必须注意每次 浸渍时附载量的提高情况。随着浸渍次数的增加, 每次附载增量将减少。 多次浸渍法工艺过程复杂,劳动效率低,生产成 本高,除非上述特殊情况,应尽量少采用。
多次浸渍法
本法即浸渍、干燥、焙烧反复进行数次。采用 这种方法的原因有两点。 第一,浸渍化合物的溶解度小,一次浸渍不能得 到足够大的附载量,需要重复浸渍多次; 第二, 为避免多组分浸渍化合物各组分间的竞争 吸附,应将各别组分按秩序先后浸渍。每次浸渍 后,必须进行干燥和焙烧,使之转化为不溶性的 物质,这样可以防止上次浸 载在载体的化合物在 下一次浸渍时又溶解到溶液中,也可以活性组分的分布
均匀型 (uniform type)
蛋壳型 (egg-shell type)
蛋白型 (egg-white type)
蛋黄型 (egg- yolk type)
浸渍颗粒的热处理过程
干燥过程中活性组分的迁移
负载型催化剂的焙烧与活化 互溶与固相反应
各种浸渍法及评价
竞争吸附原理及模型
吸附速度和扩散速度不同,活性组分分布往往不 均匀
在浸渍溶液中,除含有活性组分外,再加入适量 第二组分(一般为酸类),该组分也吸附在载体 上,加入的第二组分称为竞争吸附剂 采用竞争吸附剂提高活性组分的分布均匀性
竞争吸附模型示意图
浸渍前
单纯氯铂酸浸渍
有竞争吸附剂
过量浸渍法
本法系将载体泡人过量的浸渍溶液中,即浸渍溶 液体积超过载体可吸收体积,待吸附平衡后,滤 去过剩溶液,干燥、活化后便得催化剂成品。
等体积浸渍法
将载体浸入到过量溶液中,整釜溶液的成分将 随着载体的浸渍而被改变,释放到溶液中的碎物 可形成淤泥,使浸渍难于完全使用操作溶液。因 而工业上使用等体积浸渍法(吸干浸渍法), 即将 载体浸到初湿程度,计算好溶液的体积,做到更 准确地控制浸渍工艺。 工业上,可以用喷雾使载体与适当浓度的溶液接 触,溶液的量相当于已知的总孔体积,这 样做可 以准确控制即将掺入催化剂中的活性组织的量。 各个颗粒都可达到良好的重复性,但在一次浸渍 中所能达到最大负载量,要受溶剂溶解度的限制。
工业催化剂的制备
浸渍法
将载体放到含有活性物质、助剂成分的液体或气
体中浸渍,依靠毛细管压力进入使组分进入载体
内部,同时组分还会在载体表面上吸附。使活性
组分在载体表面吸附直到平衡,除去剩余液体,
进行干燥、焙烧、活化(还原)等后处理
优点
使用已经制成的各种形状尺寸的催化剂载体;
可以选择具有合适比表面、孔径、强度、导热率 性能的载体;
根据活性组分在载体上分布形式的要求,选择适
宜的盐溶液 浸渍液的浓度
注意事项:
浓度过高,活性组分在孔内分布不均匀,易得到 较粗的金属颗粒且粒径分布不均匀 浓度过低,一次浸渍达不到要求,必须多次浸渍, 费时费力
活性组分在载体上的分布与控制
浸渍时溶解在溶剂中含活性组分的盐类(溶质) 在载体表面的分布,与载体对溶质和溶剂的吸附 性能有很大的关系 一般认为活性组分在一个孔内吸附动态平衡,其 模型可能有以下四种情况:1.快速吸附2.静置、 吸附、溶解平衡3.过量活性组分4.活性组分不足
在任何情况 下,制成的催化剂通常都要经过干燥 与焙烧。在少数情况下,为使得有效组分更均匀 地分散,可将浸渍过的催化剂浸入到一种试剂中, 以使发生沉淀,从而可使活性 组分固定在催化剂 内部。 本法将载体与它可吸收体积的浸渍溶液相混合, 由于浸渍溶液的体积与载体的微孔体积相当,只 要充分混合,浸渍溶液恰好浸透载体颗粒而无过 剩,可省略废液的过滤 与回收。但是必须注意, 浸渍溶液体积是浸渍化合物性质和浸渍溶液黏度 的函数。确定浸渍溶液体积,应预先进行试验测 定。等体积浸渍可以连续或间断进行,设备 投资 少,生产能力大,能精确调节附载量,所以工业 上广泛采用。