第二节 机械加工精度
机械加工精度控制
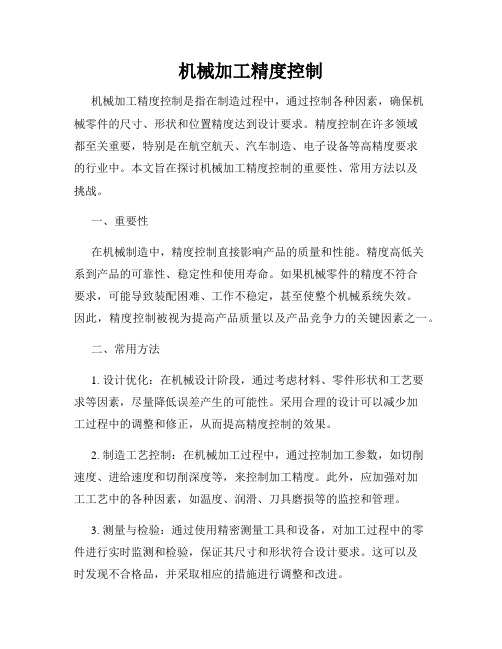
机械加工精度控制机械加工精度控制是指在制造过程中,通过控制各种因素,确保机械零件的尺寸、形状和位置精度达到设计要求。
精度控制在许多领域都至关重要,特别是在航空航天、汽车制造、电子设备等高精度要求的行业中。
本文旨在探讨机械加工精度控制的重要性、常用方法以及挑战。
一、重要性在机械制造中,精度控制直接影响产品的质量和性能。
精度高低关系到产品的可靠性、稳定性和使用寿命。
如果机械零件的精度不符合要求,可能导致装配困难、工作不稳定,甚至使整个机械系统失效。
因此,精度控制被视为提高产品质量以及产品竞争力的关键因素之一。
二、常用方法1. 设计优化:在机械设计阶段,通过考虑材料、零件形状和工艺要求等因素,尽量降低误差产生的可能性。
采用合理的设计可以减少加工过程中的调整和修正,从而提高精度控制的效果。
2. 制造工艺控制:在机械加工过程中,通过控制加工参数,如切削速度、进给速度和切削深度等,来控制加工精度。
此外,应加强对加工工艺中的各种因素,如温度、润滑、刀具磨损等的监控和管理。
3. 测量与检验:通过使用精密测量工具和设备,对加工过程中的零件进行实时监测和检验,保证其尺寸和形状符合设计要求。
这可以及时发现不合格品,并采取相应的措施进行调整和改进。
4. 质量管理系统:建立完善的质量管理体系,包括质量控制标准、工艺规范和检验要求等。
通过建立有效的质量保证措施,全面提高机械加工精度控制水平。
三、挑战机械加工精度控制面临许多挑战。
首先是技术难题,如高速加工、复杂形状零件等对机械加工精度提出了更高要求。
其次是装备条件限制,如设备刚性不足、磨损、热变形等会影响精度控制的效果。
此外,人为因素也是一个不可忽视的挑战,操作员的技能水平和经验对精度控制的结果有着重要影响。
为了应对这些挑战,需要不断加强技术研发,提高机械设备的精度和稳定性。
同时,加强人员培训和管理,提高操作人员的技能水平和质量意识。
此外,还应加强与供应商的合作,共同解决技术和设备问题,提高机械加工精度控制的整体水平。
机械制造工艺课件第三章机械加工精度
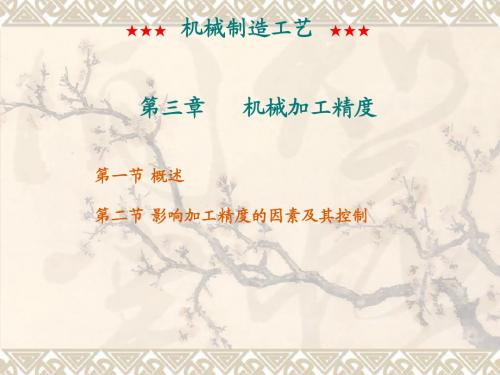
★★★
机械制造工艺
★★★
三、影响加工精度的原始误差
机械加工时,机床、刀具、夹具和工件等组成了一个工艺系统, 工艺系统的各个部分在加工过程中,应该保持严格的相对位臵关系。 由于受到许多因素的影响,系统的各个环节难免会产生一定的偏移, 使工件和刀具间相对位臵的准确性受到影响,从而引起加工误差。 原始误差即导致工艺系统各环节产生偏移的这些因素的总称。原始 误差中,有的取决于工艺系统的初始状态,有的与切削过程有关。 当原始误差的方向发生在加工表面法线方向时,引起的加工误 差最大;当原始误差的方向发生在加工表面的切线方向时,引起的 加工误差最小,一般可以忽略不计。为了便于分析原始误差对加工 精度的影响程度,我们把对加工精度影响最大的那个方向(即通过 切削刃的加工表面的法向)称为误差的敏感方向。而把对加工精度 影响最小的那个方向(即通过切削刃的加工表面的切向)则称为误 差的不敏感方向。
★★★
机械制造工艺
★★★
一、加工原理误差
原理误差即是在加工中由于采用近似的加 工运动、近似的刀具轮廓和近似的加工方法而 产生的原始误差。 完全符合理论要求的加工方法,有时很难实 现,甚至是不可能的。这种情况下,只要能满 足零件的精度要求,就可以采用近似的方法进 行加工。这样能够使加工难度大为降低有利于 提高生产效率降低成本。
★★★
机械制造工艺
ห้องสมุดไป่ตู้
★★★
3)定尺寸刀具法:是直接利用刀具的相应尺寸来 保证加工尺寸的方法。如用钻头钻孔,铰刀铰孔,用拉 刀、铣刀加工键槽等。加工尺寸精度的高低主要与刀具 的制造精度,安装精度和磨损及机床运动精度等因素有 关。这种加工方法加工精度稳定,生产率也高。 4)自动获得尺寸法:是利用测量装臵、调整装臵 和控制系统等组成的自动化加工系统,在加工过程中能 自动测量、补偿调整,当工件达到尺寸要求时,能自动 退回停止加工的方法。
机械加工质量培训课件PPT(共 104张)

2.1 机械加工精度
i工 机件 (蜗 床杆 丝) 杆 PP螺 1螺 ZZ距 距 21ZZ34
例1. 在公制车床上车模数为2mm蜗杆时,挂轮计算式为 :
z1 z2
z3 z4
P(P机 (1 床 蜗丝 杆杆 螺螺 距距 )) ,若P=6mm,
Z 1 1,1 Z 2 0 7,Z 0 3 8,Z 0 4 1,2 求加0 工后蜗杆螺距
误差是多少?
i
P1=2
P=6
解: i工 机件 (蜗 床杆 丝) 杆 PP螺 1螺 ZZ距 距 21ZZ34 P ห้องสมุดไป่ตู้iP Z Z2 1Z Z3 4P1 71 0 2 800 066.2857
1)主轴回转误差。 纯径向跳动误差 轴向窜动误差 纯角度摆动误差
①主轴纯径向跳动误差对加精度的影响。 产生的主要原因:主轴支承轴颈的圆度误差、轴承工作表面的
圆度误差等。 a. 切削力F的作用方向不变(见图2-5 车外圆的情形)
2
R
1
3
R3
R1 △R
o o′
理论位置
实际位置
R
4
车外圆时它使加工面产生圆度和圆柱度误差。
@加工质量与设备、工艺方法、工艺措施有关。
2.1 机械加工精度
2.1.1 概述 1、机械加工精度(简称加工精度):是指零件在机械加工后
的几何参数(尺寸、几何形状和表面间相互位置)的实际值和理 论值相符合的程度。
2、加工误差:实际参数与理论参数的差值
2.1 机械加工精度
2.1.2 影响加工精度的因素及其分析 在机械加工中,零件的尺寸、几何形状和表面间相互位置的
机械加工精度的概念
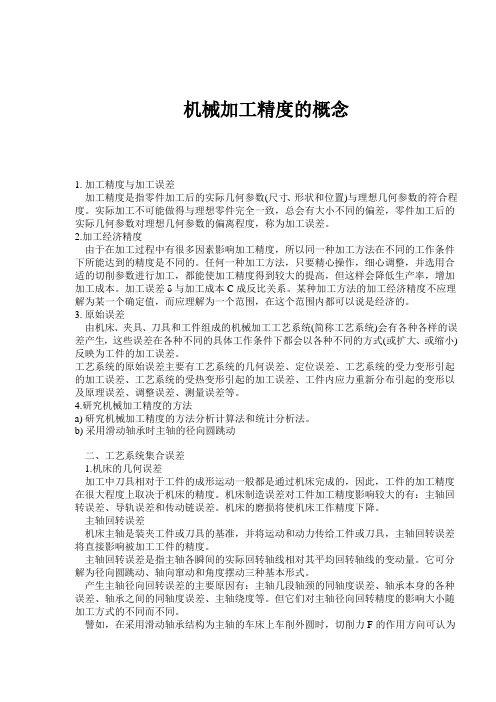
机械加工精度的概念1. 加工精度与加工误差加工精度是指零件加工后的实际几何参数(尺寸、形状和位置)与理想几何参数的符合程度。
实际加工不可能做得与理想零件完全一致,总会有大小不同的偏差,零件加工后的实际几何参数对理想几何参数的偏离程度,称为加工误差。
2.加工经济精度由于在加工过程中有很多因素影响加工精度,所以同一种加工方法在不同的工作条件下所能达到的精度是不同的。
任何一种加工方法,只要精心操作,细心调整,并选用合适的切削参数进行加工,都能使加工精度得到较大的提高,但这样会降低生产率,增加加工成本。
加工误差δ与加工成本C成反比关系。
某种加工方法的加工经济精度不应理解为某一个确定值,而应理解为一个范围,在这个范围内都可以说是经济的。
3. 原始误差由机床、夹具、刀具和工件组成的机械加工工艺系统(简称工艺系统)会有各种各样的误差产生,这些误差在各种不同的具体工作条件下都会以各种不同的方式(或扩大、或缩小)反映为工件的加工误差。
工艺系统的原始误差主要有工艺系统的几何误差、定位误差、工艺系统的受力变形引起的加工误差、工艺系统的受热变形引起的加工误差、工件内应力重新分布引起的变形以及原理误差、调整误差、测量误差等。
4.研究机械加工精度的方法a) 研究机械加工精度的方法分析计算法和统计分析法。
b) 采用滑动轴承时主轴的径向圆跳动二、工艺系统集合误差1.机床的几何误差加工中刀具相对于工件的成形运动一般都是通过机床完成的,因此,工件的加工精度在很大程度上取决于机床的精度。
机床制造误差对工件加工精度影响较大的有:主轴回转误差、导轨误差和传动链误差。
机床的磨损将使机床工作精度下降。
主轴回转误差机床主轴是装夹工件或刀具的基准,并将运动和动力传给工件或刀具,主轴回转误差将直接影响被加工工件的精度。
主轴回转误差是指主轴各瞬间的实际回转轴线相对其平均回转轴线的变动量。
它可分解为径向圆跳动、轴向窜动和角度摆动三种基本形式。
产生主轴径向回转误差的主要原因有:主轴几段轴颈的同轴度误差、轴承本身的各种误差、轴承之间的同轴度误差、主轴绕度等。
机械加工质量及其控制概述ppt68页课件

二、机械加工表面质量
(一)表面质量的概念
粗糙度太大、太小都不耐磨
适度冷硬能提高耐磨性
对疲劳强度的影响
对耐腐蚀性能的影响
对工作精度的影响
粗糙度越大,疲劳强度越差
适度冷硬、残余压应力能提高疲劳强度
粗糙度越大、工作精度降低
残余应力越大,工作精度降低
粗糙度越大,耐腐蚀性越差
压应力提高耐腐蚀性,拉应力反之则降低耐腐蚀性
本章提要
机械产品质量取决于零件的加工质量和产品的装配质量,机器零件的加工质量是整台机器质量的基础。 机器零件的加工质量一般用机械加工精度和加工表面质量两个重要指标表示,它的高低将直接影响整台机器的使用性能和寿命。 机械产品加工的首要任务,就是保证零件的机械加工质量要求。 本章重点讨论影响机械加工精度和表面质量的因素及其控制方法。
(1)主轴回转误差
第二节 机械加工精度的影响因素及控制
一、工艺系统几何误差对加工精度的影响
(一)机床的几何误差
(1)主轴回转误差
第二节 机械加工精度的影响因素及控制
一、工艺系统几何误差对加工精度的影响
(一)机床的几何误差
主轴回转误差的基本形式
车床上车削
镗床上镗削
内、外圆
端面
螺纹
孔
端面
纯径向跳动
机械加工中,采用近似的成形运动或近似的刀刃形状进行加工,虽然会由此产生一定的原理误差,但却可以简化机床结构和减少刀具数,只要加工误差能够控制在允许的制造公差范围内,就可采用近似加工方法。
原始误差
工艺系统动误差
工艺系统受力变形
刀具磨损
残余应力引起变形
测量误差
工艺系统热变形
第二节 机械加工精度的影响因素及控制
机械制造工艺与机床夹具 第2版 教学课件 吴年美 吴拓 第二章 机械加工精度
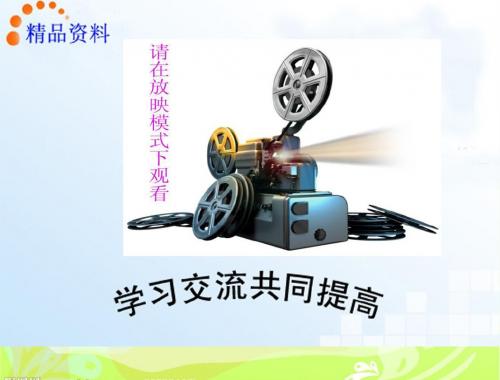
而且毛坯结构越复杂、壁厚越不均,散热的条件差别越大,毛坯内
部产生的残余应力也越大。
第二节 影响加工精度的因素及其分析
(2)冷校直带来的残余应力 直工艺进行校直。 某些刚度低的零件,如细长轴、曲轴和
丝杠等,由于机加工产生弯曲变形不能满足精度要求,常采用冷校
第二节 影响加工精度的因素及其分析
图2-12 冷校直引起的残余应力 a)冷校直方法 b)加载时残余应力的分布 c)卸载后残余应力的分布
教材其余课件及动画素材请查阅在线教务辅导网 在线教务辅导网:
QQ:349134187 或者直接输入下面地址:
第二章
机械加工精度
第二章 机械加工精度 第一节 概 述
第二节 影响加工精度的因素及其分析 第三节 加工误差的综合分析 第四节 保证和提高加工精度的主要途径
证工件位置精度的安装方法。
第二节 影响加工精度的因素及其分析
图2-1 原始误差
一、加工原理误差
第二节 影响加工精度的因素及其分析
加工原理误差是指采用了近似的成形运动或近似的切削刃轮廓进行 加工而产生的误差。 二、工艺系统的几何误差 1.机床几何误差 (1)机床主轴误差。 1)主轴回转误差。
图2-2 主轴回转轴线的运动误差
一、加工误差的性质 根据一批工件加工误差出现的规律,可将影响加工精度的误差因素 按其性质分为两类: (1)系统误差 (2)随机误差 在顺序加工的一批工件中,若加工误差的大小和方向 在顺序加工的一批工件中,其加工误差的大小和方向 都保持不变或按一定规律变化,这类误差统称为系统误差。 的变化是无规律的,称为随机误差,例如,毛坯误差的复映、残余 应力引起的变形误差和定位、夹紧误差等都属于随机误差。 二、加工误差的数理统计方法
机械加工精度
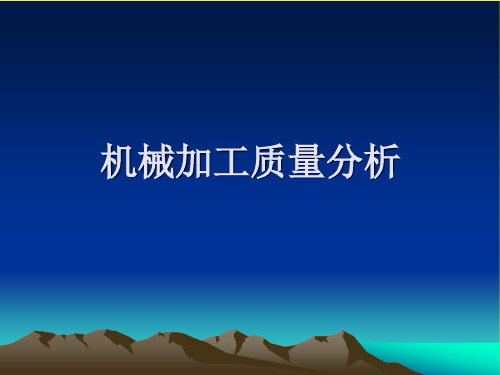
机械加工精度
1. 获得尺寸精度的方法
(1) (2) (3) (4) 试切法 调整法 定尺寸法 自动控制法
机械加工精度
2. 获得形状精度的方法 (1)轨迹法 (2)成形法 (3)展成法 3. 获得位置精度的方法 (1)根据工件加工过的表面进行找正的 方法; (2)工件的位置精度由夹具来保证。
机械加工精度
机械加工表面质量
四、 影响表面层物理机械性能的因素 1.影响表面层冷作硬化的因素
(1)切削用量 ①切削速度: 随着切削速度的增大,被加工金属塑性变形减小,同时由于 切削温度上升使回复作用加强,因此冷硬程度下降。 ②进给量: 进给量增大使切削厚度增大,切削力增大,工件表面层金属的 塑性变化增大,故冷硬程度增加。 (2)刀具 ①刀具刃口圆弧半径 增大,表面层金属的塑性变形加剧,冷硬程度增大。 ②刀具后刀面磨损宽度VB 增大,刀具后刀面与工作表面摩擦加剧,塑性变 形增大,导致表面层冷硬程度增大。 ③前角增大,可减小加工表面的变形,故冷硬程度减小。刀具后角、主偏角、 副偏角及刀尖圆角半径等对表面层冷硬程度影响不大。 (3)工件材料 工件材料的塑性越大,加工表面层的冷硬程度越严重,碳钢中含碳量越高, 强度越高,其冷硬程度越小。
机械加工精度
4)刀具热变形及对加工精度的影响 (1)刀具连续工作时 (2)刀具间歇工作 ξ(μm)
ξmax
连续切削升温曲线
间断切削升温曲线 冷却曲线
图中 ξ—— 热伸长量; ξmax —— 达到热平衡热伸长量; τ—— 切削时间; τc —— 时间常数(热伸长量为热平 衡热伸长量约63%的时间,常取3~4分钟 )。
机械加工表面质量
二、 表面质量对零件使用性能的影响 1.表面质量对零件耐磨性的影响
机械加工精度

夹具安装法是指通过夹具保证工件加工表面与定 位基准面之间位置精度的安装方法。这种方法定位迅 速方便,定位精度高且稳定,但专用夹具的制造周期 长,费用高,因此主要用于成批、大量生产。
(3)机床控制法
机床控制法是指利用机床本身所设置的保证相对 位置精度的机构来保证工件位置精度的方法,例如坐 标镗床和数控机床等。
自动控制法生产率高,加工精度稳定,加工柔 性好,能适应多品种生产,是目前机械制造的发展 方向和计算机辅助制造(CAM)的基础。
2.形状精度的获得方法
(1)成形运动法
成形运动法是指使刀具相对于工件作有规律的 切削成形运动,从而获得所要求形状精度的方法, 如2.1节中所介绍的轨迹法、成形法、展成法和相切 法等。成形运动法主要用于加工圆柱面、圆锥面、 平面、球面、回转曲面、螺旋面和齿形面等。
(2)非成形运动法
非成形运动法是指通过对加工表面形状的检测, 由工人对其进行相应的修整加工,以获得所要求形状 精度的方法。非成形运动法生产率较低,但当零件形 状精度要求很高或表面形状比较复杂时,常采用此方 法。
3.位置精度的获得方法
(1)找正安装法
找正是指用工具或仪表根据工件上的有关基准, 找出工件在加工或装配时正确位置的过程。用找正 法安装工件称为找正安装。找正安装可分为划线找 正安装和直接找正安装两种。
试切法的生产率较低,对操作者的技术水平要求 较高,主要用于单件、小批量生产。
(2)调整法
调整法是指预先调整好刀具相对于工件加工 表面的位置,并在加工过程中保持这一位置不产率较高,对操作工的要求不高,但 对调整工的要求较高,主要用于成批、大量生产。
(3)定尺寸刀具法
一、尺寸、形状和位置精度
工件的加工精度包括尺寸精度、形状精度和位 置精度三部分内容。
机械加工精度获得方法
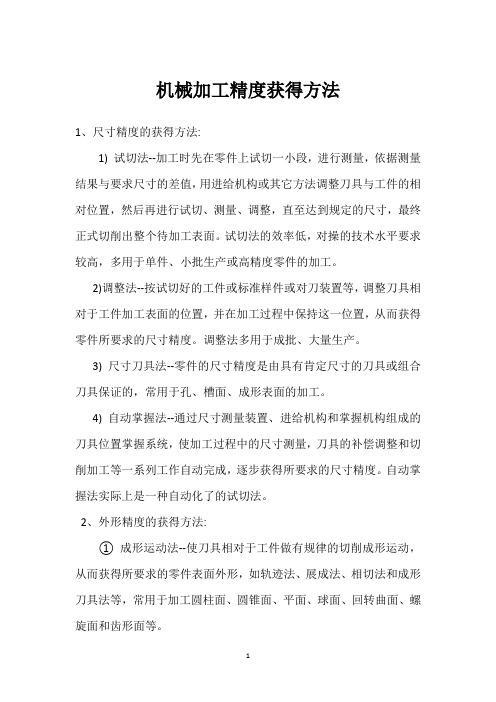
机械加工精度获得方法1、尺寸精度的获得方法:1) 试切法--加工时先在零件上试切一小段,进行测量,依据测量结果与要求尺寸的差值,用进给机构或其它方法调整刀具与工件的相对位置,然后再进行试切、测量、调整,直至达到规定的尺寸,最终正式切削出整个待加工表面。
试切法的效率低,对操的技术水平要求较高,多用于单件、小批生产或高精度零件的加工。
2)调整法--按试切好的工件或标准样件或对刀装置等,调整刀具相对于工件加工表面的位置,并在加工过程中保持这一位置,从而获得零件所要求的尺寸精度。
调整法多用于成批、大量生产。
3) 尺寸刀具法--零件的尺寸精度是由具有肯定尺寸的刀具或组合刀具保证的,常用于孔、槽面、成形表面的加工。
4) 自动掌握法--通过尺寸测量装置、进给机构和掌握机构组成的刀具位置掌握系统,使加工过程中的尺寸测量,刀具的补偿调整和切削加工等一系列工作自动完成,逐步获得所要求的尺寸精度。
自动掌握法实际上是一种自动化了的试切法。
2、外形精度的获得方法:① 成形运动法--使刀具相对于工件做有规律的切削成形运动,从而获得所要求的零件表面外形,如轨迹法、展成法、相切法和成形刀具法等,常用于加工圆柱面、圆锥面、平面、球面、回转曲面、螺旋面和齿形面等。
② 非成形运动法--通过对加工表面外形的检测,由工人对其进行相应的修整加工,以获得所要求的外形精度。
尽管非成形运动法是获得零件表面外形精度的最原始方法,效率相对比较低,但当零件外形精度要求很高(超过现有机床设备所能供应的成形运动精度)时,常采纳此方法。
例如,0级平板的加工,就是通过三块平板配刮方法来保证其平面度要求的。
3、位置精度的获得方法:① 一次装夹获得法--零件表面的位置精度在一次安装中,由刀具相对于工件的成形运动位置关系保证。
② 多次装夹获得法--通过刀具相对工件的成形运动与工件定位基准面之间的位置关系来保证零件表面的位置精度。
③ 非成形运动法--利用人工,而不是依靠机床精度,对工件的相关表面进行反复的检测和加工,使之达到零件的位置精度要求。
机械加工精度(完整版)
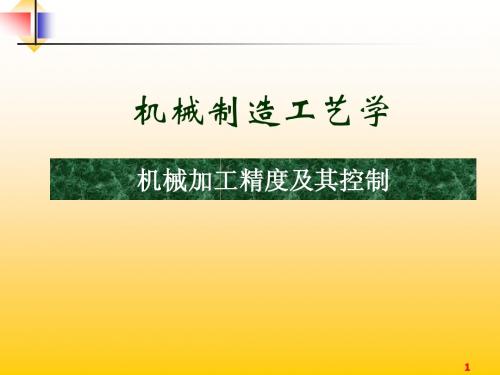
零件的机械加工质量包括零件的机械加工精度
和加工表面质量两方面
3
一、机械加工精度
• 机械加工精度:零件加工后的实际几何
参数(尺寸、形状和表面间的相互位置)
•机械加工误差:加工后零件的实际几何
参数(尺寸、形状和表面间的相互位置) 与理想几何参数的偏离程度。
与理想几何参数的符合程度。
9
2.2 工艺系统的几何精度对加工精度的影响
10
一、加工原理误差
加工原理误差:是指采用了近似的成形运动或近似 的刀刃轮廓代替理论的成形运动或刀刃形状进行 加工而产生的误差。 数控加工原理误差:直线或圆弧插补(功能强、 精度高的机床配B样条插补)近似的成形运动。 展成刀具加工成形表面误差: (1)采用阿基米德蜗杆或法向直廓蜗杆代替渐开 线基本蜗杆而产生的刀刃齿廓形误差 ; (2)由于滚刀刀齿有限,实际上加工出的齿形是 一条由微小折线段组成的曲线,和理论上的光滑 渐开线有差异,从而产生加工原理误差。
41
铰刀的类型
(a)直柄机用铰刀(b)锥柄机用铰刀c)硬质合金锥柄机用铰刀 (d)手用铰刀(e)可调节手用铰刀(f)套式机用铰刀(g)直柄 莫式圆锥铰刀(h)手用1:50锥度铰刀 42
加工槽类铣刀
43
拉刀的类型
44
图3-27 车刀磨损过程
45
11
二、调整误差
工艺系统两种调整方法:试切法和调整法 (1) 试切法 测量误差 机床(微量)进给机构的位移误差(精度) 切削层厚度的影响(试切与正式切削的切削厚 度不同),对精加工影响尤甚 (2) 调整法加工 定程机构的误差 样件或样板的误差 测量有限试件造成的误差(调整尺寸的误差)
14
机械加工精度
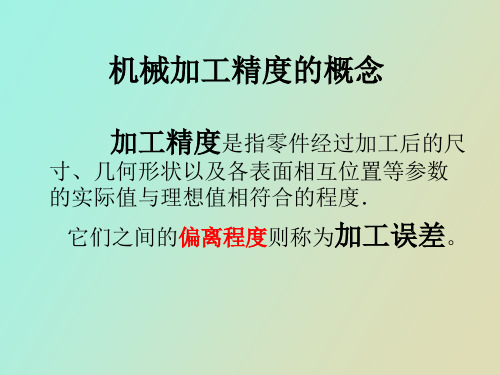
正反加卸载变形曲线
• 先在正方向加载,得加载变形曲线,然后 卸载,得到卸载变形曲线。可见两条曲线 不重合,产生类似“磁滞”现象,
• 这主要是由于接触面上的塑性变形,零件 位移时的摩擦力消耗以及间隙的影响。
• 同理在反方向加载和卸载,又可得到加载 变形曲线和卸载变形曲线.两者也不重合。
①变形曲线是非线性的,有凸形和凹形两种。 可根据曲线求瞬时刚度和平均刚度。
②加载变形曲线与卸载变形曲线不重合,且 不回到起始点。
③多次重复加卸载变形曲线不重合,随着重 复次数的增加,变形曲线逐渐接近。
④单件零件的变形曲线与一个机器或部件的 变形曲线相差很大。
影响工艺系统刚度的因素
(1)接触面的表面质量 接触面间的变形与零件的表面粗糙度、
2)几何形状精度 限制加工表面宏观几何形状 误差,如圆度、圆柱度、平面度、直线度 等;
3)相互位置精度 限制加工表面与其基准面的 相互位置误差,如平行度、垂直度、同轴 度、位置度等。
几何形状精度和尺寸精度有关系吗?
零件公差必须大于形状位置误差
注:如果没有特殊要求,圆度、圆柱度等不 需要特别标注
接触刚度
机床是由多个零件组成的。一台机床或 部件的受力变形,除了零件本身的变形以 外,还有零件之间接触面的变形。
加载变形曲线
刚度曲线
(1)接触变形影响 (2)刚度很差零件存在
• 这种变形曲线又可以分为两类,
1 是凹形曲线 2 是凸形曲线
• 凹形曲线的特点是开始变形很大,逐渐刚 度变好;
• 而凸形曲线的特点是开始刚度较好,随着 载荷的加大,刚度愈来愈差。
转子受热膨胀,对转子间隙的影响 压差可以计算,转子受力变形可以知道 刀具的变化磨损,热伸长都是变值误差
机械加工精度的相关概念
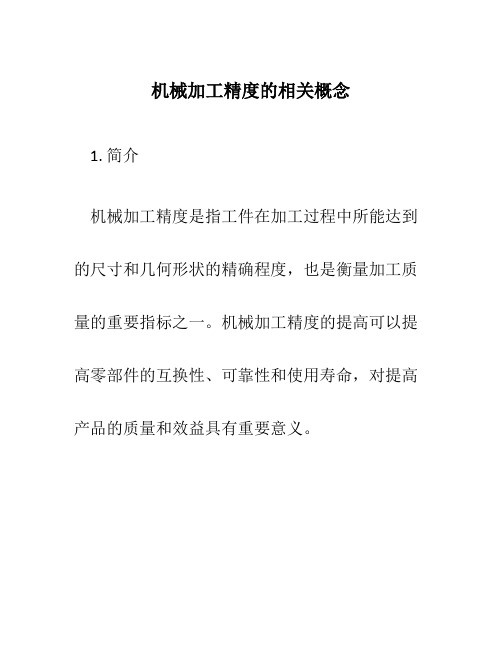
机械加工精度的相关概念1. 简介机械加工精度是指工件在加工过程中所能达到的尺寸和几何形状的精确程度,也是衡量加工质量的重要指标之一。
机械加工精度的提高可以提高零部件的互换性、可靠性和使用寿命,对提高产品的质量和效益具有重要意义。
2. 加工精度的分类根据加工对象的不同,机械加工精度可以分为整体精度和局部精度两种。
2.1 整体精度整体精度是指整个工件所具备的尺寸和几何形状的精确程度。
在机械加工中,常用的整体精度指标有:•尺寸精度:即工件加工后尺寸与设计尺寸之间的偏差。
常见的尺寸精度表示方法有公差、偏差、界限尺寸等。
•形状精度:描述工件的几何形状特征,如直线度、平面度、圆度、平行度、垂直度等。
•位置精度:描述工件间的位置关系,如平行度、垂直度、同轴度等。
2.2 局部精度局部精度是指工件上某一局部区域的尺寸和形状精度。
在机械加工中,常用的局部精度指标有:•表面粗糙度:描述工件表面的光洁程度,常用的表面粗糙度参数有Ra、Rz等。
•轮廓误差:描述工件轮廓与理论轮廓之间的偏差,常用的轮廓误差参数有最大偏差、最小偏差等。
•合拢误差:描述工件套合尺寸与设计尺寸之间的偏差,常用的合拢误差参数有最大间隙、最小间隙等。
3. 加工精度的影响因素机械加工精度受多种因素的影响,主要包括以下几个方面:3.1 设备精度设备精度是指加工设备本身的精确程度。
设备数控系统的精度、主轴精度、传动系统精度以及位置测量系统的精度等都会影响到加工精度。
3.2 工艺参数工艺参数对加工精度具有重要影响。
如切削速度、进给速度、切削深度等参数的选择会直接影响到工件的精度。
3.3 刀具刃磨刀具刃磨的质量对加工精度影响很大。
刃磨时要注意刃磨角度的控制,刃磨后的刃口应具备良好的切割能力,避免加工出现毛刺、切屑、划痕等问题。
3.4 工件材料工件材料的性能和物理特性也会对加工精度产生影响。
不同材料的切削特性不同,对切削工具的磨损、切削力等都会产生影响。
4. 加工精度的控制方法为了提高机械加工精度,可以采取以下控制方法:4.1 设备检修与校准定期对加工设备进行检修和校准,确保设备处于最佳工作状态。
机械加工精度习题答案
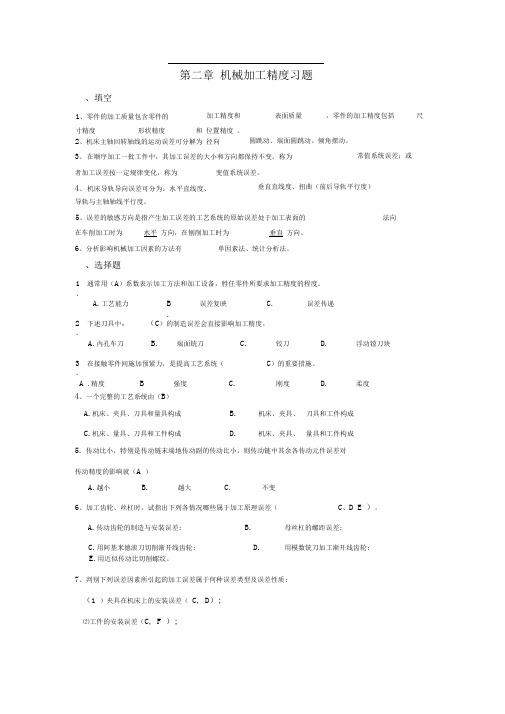
第二章 机械加工精度习题2、机床主轴回转轴线的运动误差可分解为 径向圆跳动、端面圆跳动、倾角摆动。
4、一个完整的工艺系统由(B )5. 传动比小,特别是传动链末端地传动副的传动比小,则传动链中其余各传动元件误差对传动精度的影响就(A )E.用近似传动比切削螺纹。
7、判别下列误差因素所引起的加工误差属于何种误差类型及误差性质: (1 )夹具在机床上的安装误差( C, D );⑵工件的安装误差(C, F );、填空 1、零件的加工质量包含零件的 加工精度和 表面质量 ,零件的加工精度包括 尺寸精度形状精度和 位置精度 。
3、 在顺序加工一批工件中,其加工误差的大小和方向都保持不变,称为 者加工误差按一定规律变化,称为 变值系统误差。
4、 机床导轨导向误差可分为:水平直线度、 常值系统误差;或垂直直线度、扭曲(前后导轨平行度) 导轨与主轴轴线平行度。
5、误差的敏感方向是指产生加工误差的工艺系统的原始误差处于加工表面的法向 在车削加工时为 水平 方向,在刨削加工时为 垂直 方向。
6、分析影响机械加工因素的方法有 单因素法、统计分析法。
、选择题 1、 通常用(A )系数表示加工方法和加工设备,胜任零件所要求加工精度的程度。
A.工艺能力 B . 误差复映 C. 误差传递 2、 下述刀具中, (C )的制造误差会直接影响加工精度。
3、 A.内孔车刀B. 端面铳刀C. 铰刀D. 浮动镗刀块在接触零件间施加预紧力,是提高工艺系统( C )的重要措施。
A .精度 B . 强度C.刚度D.柔度A.机床、夹具、刀具和量具构成B. 机床、夹具、 刀具和工件构成C.机床、量具、刀具和工件构成D.机床、夹具、 量具和工件构成A.越小B.越大C.不变6、加工齿轮、丝杠时,试指出下列各情况哪些属于加工原理误差( C 、D E )。
A.传动齿轮的制造与安装误差;B. 母丝杠的螺距误差;C.用阿基米德滚刀切削渐开线齿轮;D.用模数铳刀加工渐开线齿轮;8、测定机床部件静刚度的实验曲线说明(C )三、简答与计算1、在车床上加工细长轴,一端用三爪卡盘装夹,另一端用固定顶尖,工件出现弯曲变形的原因是什么可采取什么措施克服 答:原因是 1、细长工件刚度较差,在切削力作用下产生弯曲;2、由于采用死顶尖,工件在切削热作用下的热。
机械加工精度与加工误差

机械加工精度与加工误差机械加工是制造业中的重要工艺之一,主要涉及到钣金加工,车削加工,铣削加工等不同类型的加工工艺。
在加工过程中,精度和误差是非常重要的概念,精度指的是加工零件尺寸与设计图纸所规定尺寸之间的偏差,而加工误差则是指加工零件实际尺寸与设计要求尺寸之间的差异。
本文就从这两个方面来介绍机械加工中精度和误差的相关知识。
一、机械加工精度机械加工的精度主要包括工件尺寸精度和几何精度两个方面。
1. 工件尺寸精度工件尺寸精度指的是加工出的工件的各个尺寸参数的精度程度,这种精度关系到一个零部件是否能够与其他零部件匹配,从而保证整个装配的精度。
在机械加工过程中,尺寸精度主要由机床本身的精度、刀具和夹具等的精度、加工材料的性质以及机工操作的技术水平等多种因素综合作用所决定。
在机械加工中需要控制的工件尺寸精度可以根据精度要求的不同,分为以下几类:(1)高精度:±0.001mm以内(2)中等精度:±0.01mm 以内(3)一般精度:±0.1mm以内2. 几何精度几何精度是指加工出的零件与其要求的几何形状要求之间的误差。
几何精度包括以下几个方面:直线度、平面度、圆度、圆柱度、倾斜度、同轴度、互相垂直度、翻转度和角度误差等。
在机械加工过程中需要控制的几何精度同样可以根据不同的要求进行分类:(1)高精度:直线度、平面度、圆度、圆柱度都要求在0.005mm以内。
(2)中等精度:直线度、平面度、圆度、圆柱度不超过0.01mm,而其他几个精度值需达到中等精度要求即可。
(3)一般精度:直线度、平面度、圆度、圆柱度需达到一般精度要求(0.1mm以内),而其他几个精度值可以稍高一些。
二、机械加工误差机械加工误差是由于加工过程中所产生的无法避免的错误,包括各个零部件之间的误差、机床刚性等因素带来的误差及非机械因素带来的误差等。
1. 设备误差设备误差是指加工设备本身的误差造成的误差,包括机床热变形、运动误差、加工速度误差、机床导轨偏差等因素。
机械加工精度及其控制

ISO9001、ISO9002、ISO9003之间的关系
12
机械制造工艺学
第2章 机械加工精度及其控制
Analysis and Control of Machining Precision
2.2 工艺系统几何精度对 加工精度的影响
Geometric Precisions of Technological System and its influence to machining Precision
2
2.1.1 机械加工精度
加工质量
尺寸精度
加工精度
形状精度 位置精度
(通常形状误差限制在位置公差内,位 置公差限制在尺寸公差内)
表面粗糙度 波度 表面几何形状精度
纹理方向
伤痕(划痕、裂纹、砂眼等)
表面质量
表面缺陷层
表层加工硬化 表层金相组织变化 表层残余应力 加工质量包含的内容
3
2.1.1 机械加工精度
ISO9001(20项) ISO9002(18项) ISO9003(12项)
内 设 合 采 部 计 同 购 产 品
管 理 职 责
质 标 检 量 文 记 测 系 件 跟 试 统 踪 验
检 验 装 置
检 验 记 录
不 合 格 品
处 理 交 货
质 过 量 培 统 程 记 训 计 控 录 制
改 进 活 动
内 部 服 控 务 制
Y 2 RY 2 R0
RX X
O
O
ΔR
ΔY X
a)
Y
X ΔR =ΔX
显然:
RX RY
b)
Y
误差敏感方向
8
2.1.4 研究加工质量的方法
物理方法
机械加工精度的影响因素及提高措施

机械加工精度的影响因素及提高措施
机械加工精度是指在加工过程中所达到的尺寸公差范围内的误差大小。
影响机械加工
精度的因素有很多,主要有以下几点:
一、机床本身的精度
机床本身的精度是决定加工精度的重要因素之一。
机床本身的精度包括机床主轴的同
轴度、导轨的平直度、滚珠丝杆的回转精度等等。
如果机床本身精度不够高,将会严重影
响加工件的精度。
二、工件的材质与形状
工件的材质与形状也会影响机械加工精度。
对于硬度较高的金属材料,加工难度较大,同时也容易引起刀具的磨损,影响加工精度。
而且工件的形状也会对加工精度产生影响。
例如,与平面铣削相比,曲面铣削所需的加工参数更加复杂,因此,曲面工件的加工精度
要求更高。
三、切削参数的选择
选择合适的切削参数是确保机械加工精度的一个重要手段,包括切削刃数、进给量、
转速等。
如果选择不当,将导致加工表面粗糙、毛刺、刀具磨损等问题,并降低加工精
度。
一、提高机床本身的精度
要提高机械加工精度,首先就要提高机床本身的精度。
可以通过更换合适的机床,在
生产制造过程中减小误差,提高加工精度。
三、改善工件形状
对于形状复杂的工件,可以采用其他加工方式(如电火花加工、激光加工等),来改
善其加工精度。
四、提高工艺技术水平
提高工艺技术水平也是提高机械加工精度的重要手段,可以通过改进研究新技术、新
加工工艺,逐步提高机械加工精度。
总之,提高机械加工精度需要考虑多种因素,只有全面加以考虑,并结合实际生产情况,完善加工工艺、提高技术水平,才能真正的提高机械加工精度。
机械加工精度
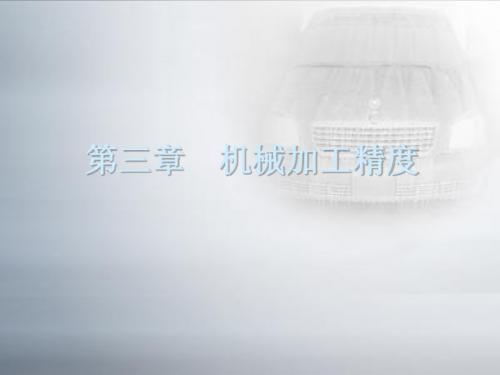
二、加工精度 1.加工精度:零件加工后,其实际尺寸、几何形状、相互位置 与理想零件的符合程度。 2.加工误差:零件加工后,其实际尺寸、几何形状、相互位 置与理想零件的不符合程度。 在生产中,一般都是通过控制加工误差来保证加工精度。 3.加工精度的指标 零件的加工精度,一般由以下三个指标来衡量: (1)尺寸精度:零件的直径、长度和表面间距等尺寸的实际 值与理想值的符合程度; (2)几何形状精度:零件的直线度、平面度、圆度、圆柱度、 线轮廓度和面轮廓度的实际值与理想值的符合程度; (3).相互位置精度:零件平行度、垂直度、同轴度、对称度、 位置度、圆跳动和全跳动的实际值与理想值的符合程度。
从式(3—6)及ε的定义域可以得出:只要毛坯有误差 (Δm≠0),工件加工后必定有误差(Δg≠0)。由于工件误 差与毛坯误差是相对应的,因此可以把工件误差看成是毛坯 误差的“复映”。同时,由于ε<1,所以工件误差值必定小于 毛坯误差值。以上就是毛坯误差的复映规律。 要减少工件的复映误差,可以增加工艺系统的刚度,减 小径向切削分力。此外,增加走刀次数也可以大大减少工件 的复映误差。 设ε1、ε2、ε3……分别为第一、第二、第三次……走刀时 的误差复映系数,则 Δg1=ε1Δm Δg2=ε2Δg1=ε1ε2Δm Δ g3=ε 3Δ g2=ε 1ε 2ε 3Δ m
kxt=Fy/yxt
(3—1)
2.工艺系统受力变形对加工精度的影响 设刀具变形量为零,即yd=0。 (1)机床的变形 如图3—5(1)所示,在车床的两顶尖间车一根光轴。设切 削过程中切削力保持不变,机床各部件所发生的变形如图3— 5(2)所示。图中: yct ——车头部件的变形量,ywz ——尾座部件的变形量, ydj ——刀架部件的变形量; Rct、Rwz————车头、尾座所受到的支反力。 刀具在任意点x处时,有受力及力矩平衡式: Rct+Rwz=Fy Rct(L-x)=Rwz×x
机械加工精度的基本概念

机械加工精度的基本概念机械加工精度,这个词一听就有点高大上,但其实它跟我们生活中的很多东西都有关系。
想象一下,你要做个精致的手工艺品,结果发现每一刀都歪歪扭扭,那可真是让人抓狂呀。
就像我们平常做菜,一刀切下去要是菜不齐整,那吃起来的感觉都不对劲。
所以,机械加工精度其实就是讲究一个“准”字,能不能把每个零件加工得刚刚好。
就像师傅的手艺,能把刀刃磨得恰到好处,既不多也不少。
说到机械加工,很多朋友可能想到的是那些嘈杂的工厂和忙碌的机器。
没错,机械加工就是在这些车间里进行的。
机器一开动,声音就像打雷一样,震耳欲聋。
可就是在这样的环境里,师傅们用他们的智慧和技巧,把一块冰冷的金属变成你想要的形状。
就像魔术师变戏法,几下功夫,一个复杂的零件就诞生了。
你说这多神奇啊,真是让人忍不住想鼓掌!在机械加工的世界里,精度可以说是王道。
它就像是万里长征的第一步,只有迈好了,后面的路才能顺畅。
如果一个零件的精度不过关,那可就像穿错鞋,走路都觉得别扭。
你想啊,汽车的发动机、飞机的翅膀,哪个不是靠精度来确保它们的安全和性能的?如果发动机的零件稍微差点,那发动机就可能“罢工”,结果你可就麻烦了。
安全第一,大家都懂这个道理。
什么是精度呢?简单来说,精度就是指加工后零件的实际尺寸和理想尺寸之间的差距。
理想的尺寸就像我们的目标,大家都想追求完美,但在实际加工中,难免会有一些误差。
这个误差有时候就像你做数学题时的“失误”,看似不大,可是凑到一起就显得很关键了。
人们常说“千里之行,始于足下”,在机械加工中,这句话同样适用。
每一个小细节都得注意,才能达到想要的结果。
在实际操作中,影响加工精度的因素有很多。
机器的精度、刀具的磨损、操作工的经验,都对最终的效果有很大的影响。
就像开车,车的性能、路况、司机的技术都得配合得当,才能开得又快又稳。
为了提高加工精度,很多工厂会使用先进的设备,比如数控机床。
这些高科技的玩意儿,能帮你在精度上省下不少力气。
机械加工精度

机械加工精度一、基本概念机械加工精度:指零件加工后的实际几何参数(尺寸、形状和表面间的互相位置)与理想几何参数的符合程度。
加工误差:指加工后零件的实际几何参数(尺寸、形状和表面间的互相位置)对理想几何参数的偏离程度。
加工原理误差:指采用了近似的成形运动或近似的刀刃轮廓进行加工而产生的误差。
系统误差:在顺序加工一批工件中,其加工误差的大小和方向都保持不变,或者按一定规律变化,统称为系统误差。
随机误差:在顺序加工一批工件中,其加工误差的大小和方向的变化是属于随机性的,称为随机误差。
调整误差:在机械加工的每一个工序中,总是要对工艺系统进行这样或那样的调整工作。
由于调整不可能绝对地准确,因而产生调整误差。
机床误差:A)导轨的导向误差:指机床导轨副的运动件实际运动方向与理想方向的偏差。
B)主轴的回转误差:指主轴实际回转轴线对其理想回转轴线的漂移。
C)传动链的传动误差:指内联系的传动链中首末两端传动元件之间,相对运动的误差。
工艺系统刚度:指工件加工表面在切削力法向分力Fy的作用下,刀具相对工件在该方向上位移y的比值。
误差的敏感方向:对加工精度影响最大的那个方向(即通过刀刃的加工表面的法向)。
二、影响机械加工精度的因素1. 影响机械加工精度的工艺系统几何因素(1)加工原理误差(2)调整误差(3)机床误差(4)夹具的制造误差与磨损(5)刀具的制造误差与磨损2.工艺系统的受力变形(1)工艺系统的刚度(2)机床部件刚度减小工艺系统的受力变形影响的措施:(1)提高工艺系统的刚度:a.合理的结构设计b.提高连接表面的接触刚度c.采用合理的装夹和加工方式(2)减小载荷及其变化3.工艺系统的热变形(1)工件热变形(2)刀具热变形(3)机床热变形减小工艺系统的热变形影响措施:(1)减小热源的发热和隔离热源(2)均衡温度场(3)采用合理的机床部件结构及装配基准(4)加速达到热平衡状态(5)控制环境温度三、保证和提高加工精度的途径1.误差预防(1)合理采用先进工艺与设备(2)直接减少原始误差法(3)转移原始误差发(4)均分原始误差(5)均化原始误差(6)就地加工法2.误差补偿法(1)在线检测(2)偶件自动配磨(3)积极控制起决定作用的误差因素。
- 1、下载文档前请自行甄别文档内容的完整性,平台不提供额外的编辑、内容补充、找答案等附加服务。
- 2、"仅部分预览"的文档,不可在线预览部分如存在完整性等问题,可反馈申请退款(可完整预览的文档不适用该条件!)。
- 3、如文档侵犯您的权益,请联系客服反馈,我们会尽快为您处理(人工客服工作时间:9:00-18:30)。
车外圆的敏感方向
影响主轴回转精度的因素:
滑动轴承轴颈或滚动轴承滚道圆度误差 滚动轴承内环的壁厚误差 滑动轴承轴颈、轴承套或滚动轴承滚道的 波度 滚动轴承滚子的圆度误差和尺寸偏差 轴承间隙以及切削中的受力变形 轴承定位端面与轴心线垂直度误差 轴承端面之间的平行度误差 锁紧螺母端面的跳动等
三、加工误差的综合分析 1.加工误差的性质
误差分为两类
系统性误差
当连续加工一批零件时,误差的大小和 方向或是保持不变,或是按一定规律变 化。前者称为常值系统性误差,后者称 为变值系统性误差
常值系统性误差有:
原理误差;
刀具、夹具、量具、机床的制造误差;
调整误差;
系统受力变形。
变值系统性误差有:
导轨误差对加工精度的影响:如车削
时导轨在水平面内弯曲,向前凸出,则 出现鼓形误差;向后凸出,则出现鞍形 误差
传动链误差
传动链误差产生的原因
传动元件的制造误差、传动元件的装配误 差、使用过程中的磨损
减少传动链误差对加工精度的影响, 可采取如下措施:
缩短传动链 采用降速传动 提高传动链的制造精度和装配精度 设法消除传动链的间隙 采用误差校正机构提高传动精度
刀具的制造误差与磨损 刀具的制造误差
刀具的制造误差对加工精度的影响,根 据刀具的种类不同而不同。定尺寸刀具 以刀具尺寸误差为主;成形刀具以刀具 形状误差为主
刀具的磨损:分为三个阶段:初始磨
损、正常磨损、急剧磨损
减少刀具制造误差对加工精度的影 响的措施:
提高制造精度 合理选择刀具材料 合理选择切削用量 合理选择刀具几何参数 合理选择冷却润滑 准确刃磨,减少磨损
导轨误差
导轨是确定主要部件相对位置的基准, 也是运动基准,各项误差 直接影响被加 工工件的精度 对导轨的精度要求主要有:
在水平面内的直线度 在垂直面内的直线度 前后导轨的平行度(扭曲)
机床导轨 在水平面 内的直线度 对加工精 度的影响
机床导轨 在垂直面 内的直线度 对加工精 度的影响
机床导轨 扭曲对 工件形状 的影响
只要能保证加工精度和零件的使用性能, 一定的原理误差是允许的。这种误差不 应超过相应公差的10~15%。
近似的刀具轮廓带来的误差
例如用模数铣刀铣齿轮,由于:铣刀的成 形面不是纯粹的渐开线;模数相同而齿数 不同的渐开线齿轮齿形是不同的,一把铣 刀铣一组齿数的齿轮,故存在原理误差 再如,用齿轮滚刀加工齿轮时,滚刀也是 采用阿基米德基本蜗杆或法向直廓蜗杆代 替渐开线蜗杆
由于机械加工中的种种原因,不可能把 零件做得绝对精确,总会产生偏差。这 种偏差即加工误差。
一、获得零件加工精度的方法
1.获得尺寸精度的方法
试切法:通过试切—测量—调整—再
试切,反复进行到工件尺寸达到规定要 求为止
调整法:先调整好刀具和工件在机床
上的相对位置,并在一批零件的加工过 程中保持这个位置不变,以保证工件被 加工尺寸
夹具的制造误差与磨损
主要是指定位元件、夹紧元件、导向元 件、分度元件、夹具体等的制造误差 除制造误差外,还有夹具安装、工件装 夹等误差对加工精度也会带来很大影响 夹具的磨损主要是定位元件和导向元件 的磨损 为减少夹具误差对加工精度的影响,夹 具的制造误差必须小于工件的公差;及 时更换易损件
工艺措施 环境恒温,避免光照 保持工艺系统热平衡,如加工前机床空转 一段时间(精密加工中途不停车) 装夹时考虑加工热变形方向 注意选材 提高切削速度和走刀量 保持刀具锋利(降低切削热) 粗、精加工分开 切削区施加充分的冷却液
5.工件内应力对加工精度的影响
内应力——当外载荷去除后,仍残留在
工艺系统的刚度对加工精度的影响
归纳起来为下列常见形式: 由于受力点位置的变化而产生的工件形状 误差 误差复映 毛坯材料硬度不均匀使切削力产生变化, 工艺系统受力变形随之变化而产生加工误 差 工艺系统中其它作用力使工艺系统中某些 环节受力变形而产生加工误差
误差复映规律
误差复映——由毛坯加工余量和材料硬度
件放在夹具中定位
机床控制法:利用机床的相对位置精度
保证位置精度
二、影响加工精度的因素及其分析
工艺系统——由机床、夹具、刀具和工
件构成的一个完整系统
原始误差——工艺系统中的误差
来自两个方面:
加工前就存在的工艺系统本身的误差 加工过程中因工艺系统受力变形等引
起的误差
1.加工原理误差(理论误差)
内部热源:
切削热,摩擦热,电气等
外部热源:
环境温度变化,取暖设备,热幅射等
减少和控制工艺系统热变形的主要途径
结构措施
采用热对称结构 使关键件的热变形在无害于加工精度的方向 移动 合理安排支承位置,使产生热变形位移的有 效部分缩短 发热量大的热源采取足够的冷却措施,采用 热补偿方法减少热变形 均衡关键件的温升,避免弯曲 隔离热源
度量误差、调整误差以及安装误差 度量误差
引起测量误差的原因: 量具本身的误差 测量方法引起 测量力引起 温度引起 减少或消除度量误差的措施 提高量具精度,合理选择量具 注意操作方法 注意测量条件
调整误差
工艺系统的调整问题有:机床的调整、 夹具的调整、刀具的调整 不同的调整方式,有不同的误差来源
解得 n=3
减少工艺系统受力变形的措施
提高表面配合质量,以提高接触刚度
或者预加载荷,以提高接触刚度
或者锁紧暂不需移动的部件,以提高 接触刚度 设置辅助支承,提高部件刚度
缩短切削力作用点和支承点的距离,提 高工件刚度 选择合理的零件结构和断面形状
提高刀具刚度;改善材料性能
合理装夹工件,减少夹紧变形
车细 长轴 时的 变形
传动力所引起的加工误差
离心力 所引起 的加工 误差
夹紧力不 当所引起 的误差
工艺系统的刚度
刚度——工艺系统受外力作用后抵抗变
形的能力
在上述力的作用下,工艺系统受力变形, 刀具和工件相对退让。设刀具相对工件在 切削接触点法线方向的相对位移量为y, 则工艺系统的刚度是:
工艺系统热变形;
刀具、夹具、量具、机床磨损。
随机性误差
加工一批零件时,其误差的大小和方向 无规律地变化,这类误差叫随机性误差 随机性误差有: 复映误差; 定位误差; 夹紧误差; 多次调整引起的误差; 内应力引起的误差。
2.加工误差的数理统计方法 实际分布曲线(直方图)
将零件按尺寸大小以一定的间隔范围分 成若干组,同一尺寸间隔内的零件数称 为频数mi,零件总数n;频率为mi/n。 以频数或频率为纵坐标,以零件尺寸为 横坐标,画出直方图,进而画成一条折 线,即为实际分布曲线
4.工艺系统热变形及对加工精度的影响 工艺系统热变形的现象
系统受热升温而使工件、刀具及机床的许 多部分会因温度升高而产生复杂变形 改变工件、刀具、机床间的相互位置 破坏刀具与工件间相互运动的正确性 改变已调整好的加工尺寸 引起切削深度和切削力改变 破坏传动链的精度
引起热变形的热源
试切法调整
度量误差:试切调整过程中由于度量失 误或不准而引起误差 加工余量影响:最小切屑厚度太小,以 致刀刃打滑,不起切削作用 微量进给误差:最后一刀容易出现爬行
各机构调整
机构的制造精度
机构的灵敏度
调整的准确性
样件或样板调整
大批量,多刀加工时采用
样板本身的误差(制造和安装误差)
J 系统
Fy y
( N / m m)
工艺系统的刚度特性
力和变形不是直线关系,即不符合虎克 定律
加载和卸载曲线不重合
卸载后,变形不能恢复到起点
部件刚度比我们想象的小源自 影响部件刚度的因素
接触变形(接触点的变形) 薄弱零件本身的变形 间隙的影响 摩擦的影响 施力方向的影响
机械加工精度——零件在加工后几何参
• 机械加工精度包括:
三者有联系,也有区别
数(尺寸、几何形状、表面间的相互位置) 的实际值与理论值相符合的程度
尺寸精度、形状精度、位置精度——
所谓理想零件,即对表面形状而言,就 是绝对正确的圆柱面、平面、锥面等; 对表面位置而言,就是绝对的平行、垂 直、同轴和一定的角度等;对尺寸而言, 就是零件尺寸的公差带中心
对刀误差
安装误差 定位误差
基准不重合引起 定位元件和定位面制造误差 元件配合间隙引起
夹紧误差
夹紧机构的夹紧力不当引起 夹紧方式不当引起 夹紧状态不良引起
3.工艺系统受力变形及对加工精度的影响 工艺系统受力变形的现象
加工过程中的力:切削力、传动力、夹紧力、 重力、控制力、惯性力、干扰力等
的变化引起切削力和工艺系统受力变形的变 化,因而产生工件的尺寸、形状误差的现象
毛坯形状 误差的复映
误差复映规律
误差复映系数ε:定量反映毛坯误差经过 加工后减少的程度
i 工 0.75 = C p f J 系统 坯
当加工过程有多次走刀时,每次走刀的复 映系数为ε1、ε2、ε3…,则总复映系数ε总 =ε1ε2ε3…
定尺寸刀具法:通过刀具的相应尺寸
保证加工表面的尺寸精度
自动控制法:将测量、进给装置和控
制系统组成一个自动加工系统,通过自 动测量和数字控制装置,在达到尺寸精 度后自动停止加工
主动测量法:边加工边测量加工尺寸
2.获得形状精度的方法
刀尖轨迹法: 通过刀尖运动的轨迹来
获得形状精度的方法