载重汽车焊接车轮断裂失效原因分析
焊接缺陷引起汽车轮辋断裂的失效分析

位置 。检 查时 , 口已经锈 蚀 , 断 根据 锈 蚀 程 度判 定 较 早
开裂区为紧靠圆周焊缝的焊缝边缘及热影 响区位 置 ,
见图 2 。
维普资讯
・
6 2・
焊接
20 ( ) 0 6 4
1 2 母 材化 学成 分分 析 .
母材 及焊 缝金 相 分析 照片 见 图 6及 图 7, 图 中可 从 见 断 口处轮 辋 母 材 非 金 属 夹 杂 严 重 , 缝 的 柱 状 晶 区 焊 与 母材 的等 轴 晶 区明显 未熔合 。 14 扫 描 电镜 断 口分 析 .
材料 H 8 n SA, 丝 直 径 412mm, 接 电流 20~ 0 M 2i 焊 ). 焊 0 2 0 A,电 弧 电 压 2 ~2 V, 接 速 度 0 2 ~ 2 6 8 焊 .4
0 2 / i, .6m mn 焊丝 伸 出长度 1 2 5~ 0mm, 气体 流 量 2 O~ 2 / i, 接 层 如 图 2所 示 。第 1层 参 数 相 对 调 小 5L mn 焊 些 , 2层 参 数相对 调 大 些 。焊 接 时焊 枪 作 适 当摆 动 , 第 以保 证焊 缝充 分焊 透并 有一 定 宽度 。
维普资讯
焊接
20 ( ) 0 6 4
・ 61・
订 。具 体焊 接 时 由两人 在 平衡 臂 两 侧 以相 同工 艺 同时 对称 施焊 , 并且 要 一次 全 部 焊完 避 免 中途停 顿 , 以减 小 整体 的扭 曲变 形 。
而热影 响 大 。现 采用 C 气 体 保 护 焊 焊 接 两 层 , 丝 O 焊
缝的热影响 区扩展延伸。其 主要 原因是 : ①该位 置晶 粒粗大 、 强度低 ; ②该位置过热 区组织不均匀 。
车轮轮辋深裂纹故障分析与探讨

技术与应用1 问题提出车轮是轮对的重要组成部分,承担着车辆的自质量和载质量,车轮轮辋直接与钢轨接触,其质量的好坏直接关系车辆的运行安全。
随着铁路重载、提速工作的不断推进,列车运行速度不断提高,车轮的使用条件更加恶劣,故障也在不断增多,全路曾发生过多起由车轮故障引发的行车事故。
因此,在车辆厂修、段修时,施修单位对车轮故障均高度重视。
神华铁路货车公司肃宁车辆维修分公司在车辆段修中进行轮对旋修作业时,发现一起严重威胁行车安全的车轮典型质量缺陷,该车轮在旋修前外观无异状,旋修时第一次吃刀量选择3 mm时旋后发现有裂纹迹象,第二次旋修吃刀量选择4 mm,裂纹呈扩大趋势,再次吃刀4 mm进行旋修缺陷完全暴露,轮辋大片掉块,面积为140×50 mm2,且裂纹仍有85 mm延伸(见图1)。
2 原因分析通过对故障车轮进行分析,认为该故障属轮辋深裂纹造成的大片掉块,一般轮辋质量占车轮质量较大比例,即轮辋质量在很大程度上决定车轮质量,该类故障如不能及时发现,极易引发车轮崩裂,造成严重行车事故。
2.1 轮辋深裂纹形成原因此故障车轮为辗钢车轮。
辗钢车轮生产工艺过程包括:炼钢、热成型、热处理、机加工及检测。
炼钢工艺包括炼钢、炉外精炼、浇注3部分;热成型工艺主车轮轮辋深裂纹故障分析与探讨果小军:北京铁路安全监管办机辆验收室驻肃宁验收室,工程师,河北 肃宁,062350范文明:神华铁路货车公司肃宁车辆维修分公司,高级工程师,河北 肃宁,062350摘 要:货车提速重载对车轮运行安全提出严峻挑战,从轮对检修过程中发现的车轮轮辋掉块故障入手进行分析,找出故障原因,同时指出该类车轮故障缺陷的危害,分析故障形成的原因、演变的3个主要阶段,提出防范措施,并阐述车轮技术的发展方向。
关键词:车轮;轮辋;深裂纹中图分类号:U260.331+.1 文献标识码:A文章编号:1001-683X(2015)12-0059-04图1 旋后车轮缺陷图车轮轮辋深裂纹故障分析与探讨 果小军 等要包括预成型、成型、轧制和冲孔压弯几个工步;热处理工艺主要是轮辋淬火+回火;机加工工序主要采用专用或通用立式车床进行车轮加工,一般有单机式、单机组合式及生产线等几种;检测工序须全数对加工到最终尺寸的车轮进行检测,主要内容涉及静平衡检测、硬度、外观肉眼检查、超声波探伤、磁粉探伤、关键尺寸检查等。
汽车车轮轮辋电阻对焊开裂原因分析

万方数据.生产碘场±严搬琢(a)轮辋中间开裂形貌(b)轮辋端缘开裂形貌图1焊缝开裂宏观形貌图5高温氧化物微观形貌图2温度不均的焊缝形貌图3对焊后轮辋端缘搭焊错边形貌裂处断面形貌见图4。
高温氧化物微观形貌见图5。
夹杂物评级:A0.B0,CO。
DO.5;AO,BO.5。
C0,D0.5。
母材金相组织见图6。
焊缝处组织见图7。
晶粒度10—11级。
检验结果表明,材料组织、夹杂物、晶粒度均未见异常。
3.焊接工艺、设备情况分析(1)从随机取样情况看,在焊接过程中,发现焊件沿焊缝方向冷热状态时的颜色均存在不一样的现象,说明加热温度不均匀。
电镜检验发现存在高温氧化物,说明未将氧化物挤出。
存在轮辋厚度方向的错边,特别是存在边部翘曲,电极压力无法对悬空状态的错边和翘曲压平,导致焊接时电流分布不均。
图4开裂处断面形貌(2)从开裂情况看,焊后去毛刺时发现轮辋端部有小裂口,占总量的比例为3.9%。
焊接接头未经过扩口等工序的塑性变形就出现开裂.表明导致轮辋焊缝开裂的原因主要是与设备调试及焊接工艺有关。
4.材料因素分析(1)合理选材。
钢的强度影响电阻焊的卷圆难度及焊接时的电极压平程度。
因此.在设备能力有限的条件下,在保证疲劳寿命的同时.尽可能选择强度级别低的牌号。
《2)硫化物的影响。
在电阻对焊过程中,若S含量过高,则将在焊缝区出现裂纹,为了防止裂纹产生,需控制Mn/S比。
另外,钢中的Mn,Si比值对电阻对焊也有重要影响,当Mn,Si在4—40之间时,焊接时形成的氧化物熔点比钢低.在电阻对焊顶锻时容易被挤出,有利于焊接质量提高。
总之.钢中的S越低越好,钢的强度越低对卷圆、焊接越有利。
从实际统计及检验的情况看,硫含量控制~般在0.010%左右,未发现硫含量与开裂率间存在对应关系,Mn,Si比的控制范围也在要求范围内。
措施及效果在原因分析的基础上.用户对相关设备进行了检测及调试,通过采取及时更换磨损严重的夹具,使加热温度均匀.并控制好错边量等措施.杜绝图6基体组织(400×图7焊缝组织(200×)假焊、搭焊,轮辋焊缝开裂率明显下降.取得了较好的效果。
汽车车轮轮辋电阻对焊开裂原因分析

滚 型 l一 滚 型 …一扩 涨 定 径 一 冲气 裂的炉次化 学成分在标准 及内控要求 决 。 l
门孔 一合成压 装一 四工 位C O 合成焊 范 围内 .其C、S、Mn Si 含量 、Al
差 ;焊 接接头错边 量的控 制。
高 。2 0 0 3年 该 用 户 三 次 出现 轮 辋 焊 缝 开 裂 质量 问题 .为 找 出开 裂 原
轮辋焊缝开裂原 因分析
1获得优质接头的基本条件及焊 .
s
材 料 方 面 :选 材 问题 ;钢 中的
n/ i S bo E
:
Hale Waihona Puke 2取样检 验分析 .图2 温 度不均 的焊缝 形貌
表 明导 致轮 辋焊 缝 开 裂 的 原 因 主要 是 与设备调试 及焊接 工艺有关 。 4材料 因素 分析 .
( )合理 选材 。钢 的强 度影响 电 1
图6 基 体组织 (0 x 4o)
阻焊 的卷 圆 难 度及 焊 接 时 的 电极 压 平程 度 。 因此 .在设 备 能 力 有 限 的 条 件 下 .在 保 证 疲 劳寿 命 的同 时 ,
区 出现 裂 纹 ,为了 防 止 裂纹 产 生 .
图7 焊缝 组织 ( 0 x 2o)
DO5 .。母 材金 相组 织见 图6。焊缝 处 需控制MnS:。另外 ,钢 中的Mns /l E /i
组 织见 图7。晶粒 度 1 - 1 。检 验 比值 对 电阻 对 焊也 有 重 要 影 响 , 当 假焊 、搭 焊 ,轮 辋 焊 缝 开 裂率 明显 0 1级
重型汽车制动轮毂疲劳断裂失效分析

1 、情况介绍
QT 4 5 0 . 1 0 ,采 用铸 态工 艺 。为 了减 少经 济损 失 ,避 免此类 事件 再 次发 生 ,本文 对制 动轮 毂进 行 了断裂 成 因分 析 。
2 、理 化 检 验
2 . 1 宏观检 查
断裂 制动 轮毂 零件 沿 轮胎连 接 螺栓 处呈 环状 断 裂 ,断 裂零件 外 观形貌 见 图 1 ,环 状 断裂部 分外 观
Li Li n l i n. Ba i Pe i q i a n
( S h a n x i A u t o mo b i l e G r o u p C o . , L t d . Q u a l i t y Ma n a g e me n t D e p a a me n t , S h a a n x i X i ’ n a 7 1 0 2 0 0 )
的重 要部件 ,它还 承受 着转 弯 时 的横 向载 荷 、驱 动
开始 , 向四周推 进呈 弧形 ,它 垂直 于疲 劳裂 纹扩 展 方 向。 由断 口宏 观形 貌可 知 ,两处 疲 劳源均 位 于螺 栓 孔 处 附近 的圆 弧过 渡 处 附近 ( 如 图 4 箭 头所 示
作者简介 : 李琳 琳 , 就职 于陕西汽车集 团有限责任公 司 , 主 处) , 疲 劳扩展 区域较 大 , 最后 瞬断 区域面 积则 较小 。 要从事金相分析和失效分析方面研究工作。
汽 午 实 用 技 术 ] 二 艺 ・设 备 ・材 料
AUTMOBILE APPLI ED TECHNOLOGY
2 0 1 3 q: 第9 期
201 3 N0.9
重型汽 车制动轮毂疲劳断裂失效分析
李琳琳 ,白培谦
( 陕西 汽车 集 团有 限责任 公司质 量管 理部 , 陕西 西 安 7 1 0 2 0 0 ) 摘 要 :重 型汽 车制 动轮 毂 在使 用过 程 中发 生疲 劳断裂 事 故 。对 断裂零 件 失效形 貌 、断 口分 析 、 理 化指 标测试 ,发现 是 因制动轮 毂零 件外 端轴 承与 相对 的轴承 孔之 间无法 保持 过盈配 合 ,引起 轴
车轮断裂原因分析

3 化 学成 分检测 化 学成 分检测结 果如表 1所 示 , 符合 GB / - r 6 9 9 — 1 9 9 9
( 上接第 3 1 2页 )
6 金 相检测 6 . 1 取样
发, 技术人 员是主 要的影 Ⅱ 向因素。 要求 进行整定 计算 的专业 前 形 势 下 , 要尽 快 研 究 与 制定 检 修 策 略 , 来 指 导 当前 的继
表 2 力学- 眭能 检 测 结 果 与技 术 条 件 比对 表
力 学 性 能
指 标
( N / mm ) ( N / m m ) 9 9 0 5 7 5
R
R ∞2
A( %)
Z ( %)
A K U ( J )
检 测 结 果
1 0 5
1 2 . O
检 样 品进 行 了超 声 波检 测 , 检 测结 果 为 : 在 样 品 中 间部 位 电镜 对断 裂源 区微观 形貌 进行 了检 测 ,结 果如 图 3~7所 见 图 3~7 ) , 是 锻造 ( 车 轮壁厚 , bl l 位置 ) 深约 4 5—7 0 mm 之 间发 现最 大 当量 示。宏观 小 亮面位 置 未显 示断面 特征 (
技 术人员 必须拥 有较高 的责任 心与 技术 ,计 算 时必须 全面 电保 护检 修 工作 , 结 合 微机 保 护 自检 与通 信 能 力 , 提 高 继 考 虑到 网络 整体进 行认 真分析 ,; 隹确 整定 各级保 护装 置 的 电装置 的可 靠性 与安 全性 。 进 一步开 展 二次 线的在 线监 测 计算, 进一步确 保 系统 上下 级的保护 整定值 匹配合理 性。 技术, 研 究 不停 电检修 的整体 继 电保 护 系统 。
重载车轮辋崩断原因分析

r a r e f a c t i o n,b i a s we l d i n g,a n d we l d j u n c t i o n c r a z e ,e t c .wh i c h g i v i n g r i s e t o f a t i g u e s o u r c e a t c e n t r a l i z e d
断裂 的结 果 。它表 示 裂 纹 快 速 断 裂 的特 征 , 断 口形 貌 凸 凹程 度 较 大 。这 个 区 域 有 时 称 之 为 瞬 时 断 裂 区, 简 称 为“ 瞬断区” 。疲 劳 断 口的 瞬 断 区是 由纤 维 状, 剪 切唇 及放 射 状 三 个 部分 所 组 成 的。 瞬 断 区 的 大小 取决 于负 载 的大小 、 材料 的优 劣 、 环境介 质 等 因
3 2
武汉 工 程 职 业 技 术 学 院 学 报
呈 现 同心 圆标 记 , 如图 1 5 ( b ) 所 示 。本 文 分 析 中 的 轮 辋疲 劳属 于后 者 。
车轮总成焊接缺陷分析及措施

缺陷原因
1、焊丝或工件有丝或有油、锈和水
2、气体不纯
3、喷嘴被焊接飞溅堵塞
4、输气管路堵塞
5、有风
1、焊丝表面或工件表面不洁净
2、焊缝中含有C、S量高而Mn量低
3、熔深过大
1、焊丝干伸过长
2、焊丝的校正机构调整不良
3、导电嘴磨损严重
1、电压太高
2、导电嘴磨损严重
3、送死不均匀
4、焊丝与工件清理不良
1、导电嘴内孔过大
2、导电嘴磨损
3、焊丝打结
4、送丝轮的构槽磨损太大引起送死不良
5、送丝轮压紧力不适合
6、焊机输出电压不稳定
7、送丝软管阻力大
气孔裂纹蛇形焊道飞溅电弧不稳
措施
1、除去锈、油、水
2、更换气体或脱水
3、仔细清除附着在内壁的飞溅物
4、检查气路有无堵塞和弯折处
5、采用挡风措施或更换场地
1、焊前仔细清理
2、检查工件和焊丝化学成分
3、调整焊接规范控制熔深
1、保持适合长度
2、仔细调整
3、更换新导电嘴
1、根据焊接电流调节电压
2、更换新导电嘴
3、检查送丝滚轮和送丝导管
4、仔细清理
1、使用与直径相适合的导电嘴
2、更换新导电嘴
3、仔细清理
4、更换送丝轮
5、调整
6、检查整流元件和焊接电流接头
7、校正弯曲处或清理弹簧软管。
汽车轮辋闪光对焊焊接开裂原因分析

pat s g 3 0 L v h l w els e o i n I n ad SelC . t. hog h m cl l i 8 C e i e h e t l fQ a a r n t o,Ld,tru h c e ia nun c e n o e
YI Na N ZHOU hi i Z we CUIYa g n LIFe ZHAO n i Li L ie g IRu h n
( h eerhIstt o eh ooy ( ina rnadSel o, t. T eR sa tue f cn lg ) Qa nI n te C . Ld ) c ni T o
A s a t Ai n tt e s r u r c h n me o ftu k rm u twed n n a d me t e l b t c mi g a h e i s c a k p e o n n o c r o r i bt l i g i o si wh e c
减 重 和节 能是 汽车行 业未 来 的发展 趋 势 。为
象 。这不仅造成材料和工时的浪费 ,也相应增加 了产品成本 。因此 ,对轮辋焊接开裂成因的研究
减轻车身重量 ,汽车行业逐步增加 了高强钢板 的 使用¨ 。车轮钢具有强度和硬度高、疲劳性能以 J 及冷弯性能好的特点 ,因此被广泛应用于制造载 重卡车 、客车的轮辐和轮辋。焊接是轮辐和轮辋 生产的关键工序之一。闪光对焊因其具有省 时、 省料和省能源等诸 多优点 ] 。 ,使其在汽车轮辋 生产 中得到广泛应用。闪光对焊后 ,轮辋还须经 受扩 口、滚压成形和扩张定径等多次大的变形工 序 ,因此对焊接接头质量要求非常高。然而 ,国 内某车轮厂在使用首钢迁钢公 司 ( 称迁钢公 简 司)30 L生产轮辋时 ,尤其在扩 口及扩张工序 8C 中,发生过焊接 接头强度低 导致 焊缝 开裂 的现
汽车轮毂轴承的断裂失效研究

汽车轮毂轴承的断裂失效研究摘要:汽车轮毂轴承是汽车的关键构件之一,可以将汽车方向盘操作力度精确地传送给车轮,便于司机及时控制行车方向,在保证变相以及变速灵敏度方面具有重要的作用。
汽车轮毂轴承断裂失效是较为常见的问题,分析其产生原因具有现实意义。
基于此,本文以某批次失效轮毂轴承为例,讨论其断裂失效情况,并从润滑不良以及游隙过大两个方面提出有效预防方案,以期能为汽车轮毂轴承断裂失效问题的解决提出参考。
关键词:汽车轮毂;轴承;失效引言轮毂轴承是汽车的重要零件之一,其核心作用是承载重量,并为控制轮毂的转动,这就需要其不仅能够承载轴向荷载,同时能够承受径向荷载[1]。
汽车车轮采用两套圆锥滚子轴承或是球轴承联合的方法,轴承安装、润滑、密封以及游隙调节都是在汽车生产线上完成安装。
如果车辆轮轴承受损,将导致轴承在车辆行驶过程中失效,进而威胁乘客的生命安全。
一般情况下,失效的主要表现形式包括异常磨损、振动明显等,失效的主要原因包括断裂、磨损、锈蚀等类型,其中又以断裂失效引发的后果最为严重。
因此,检修人员应分析车辆轮毂轴承断裂失效产生的原因,并通过有效的方式予以处理,保证汽车行驶的安全性。
一、轴承断裂情况及检测工作(一)轴承断裂情况某汽车制造商维修站存在一批轮毂轴承失效零构件,该批次轴承质量保证时长为3年或是20万公里的。
该批次失效轮毂主要用在某国产品牌汽车组装之中,构成零构件包括内圈、外圈以及滚球等多个部分。
通过对本批次内容进行分析总结等发现,该批次汽车轮毂轴承之中,40%已经断裂失效的轴承使用时长在0个月至5个月之间,40%的轴承使用时长在6个月至10个月之间,18%失效轴承使用时长在11个月至15个月之间,剩下的轴承使用时长在16个月至20个月之间。
检修人员拆卸部分典型的断裂失效轴承,并开展力学、成分等检验与分析,寻找导致轮毂轴承失效的根本原因。
(二)检测研究工作第一,宏观观察。
针对其中十分典型的三类轮毂轴承予以失效研究,编号分别设为1号、2号与3号。
后车轮螺栓断裂失效分析

摘要:载重车后车轮螺栓在安装轮胎螺母时断裂。为了分析断裂的原因,应用扫描电子显微镜、能谱仪、光学显微 镜、直读光谱分析仪对该螺栓进行了宏观、微观、化学成分等分析,同时还进行了硬度和拉伸试验。检测结果表明: 由于螺栓存在较严重的偏析、疏松缺陷,在安装预紧力作用下缺陷处产生裂纹并不断扩展,导致螺栓脆性断裂。 关键词:偏析;疏松;化学成分;预紧力;脆性断裂 中图分类号:TG115.2 文献标识码:A
某载重车后车轮螺栓在安装轮胎螺母时断裂, 取断裂螺栓残件和完好件各一件进行失效分析。对 其宏观形貌、金相组织、化学成分进行分析,并对其 力学性能进行试验,分析断裂原因。
1 理化检验 1.1 宏观分析
该批螺栓为高强度螺栓,表面电镀锌。螺栓材 质为 35CrMo,性能等级 10.9级。制造工艺为:材料 改拔→下料 → 车坯径 → 红锻 → 车头部 → 淬火 (调 质)→磨外圆及螺纹径→滚螺纹→镀锌(挂镀)。断 裂螺栓试样和完好试样如图 1所示。从图 1断裂螺 栓的宏观照片可见断裂位置为第四扣螺纹牙底。 1.2 断口分析
sectionSEM
d)D区 图 3 断面 A、B、C、D区微观形貌 Fig.3 Microscopicmorphologyoffracture
sectionA,B,C,D
发现因电镀而沉积的锌,说明螺栓在电镀前尚未形 成贯穿至表面的裂纹。
a)A区 b)B区
图 4 断面 E区微观形貌 Fig.4 MicroscopicmorphologyoffracturesectionE
Fracturts
XuanYixun1,YeChen1,MaWenqing1,ShenFei1,LuZhexiao1,LiJiajun1,LiZhengang2
汽车零部件断裂失效分析简述(岑举
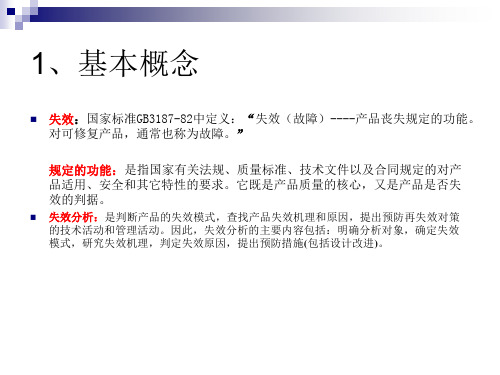
结构和配合的特性、载荷的性质和幅值、大多的内在质量缺陷、工作 和运行的状态、应力状态等等,都属于力学分析的范畴。他们不仅决 定了是否开裂,还总体上决定了以什么形式或在什么部位开裂。
设计的使用应力(各种指标)和强度(各种指标)技术条件;
关注实际的使用应力(工况)及制造质量分布的偏移和变化; 两者分布曲线相交则产生失效。 目前的失效分析和认知程度、评价主要还是在定性的水平上。
技术条件 设计应力
制造质量 使用应力、工况
2.5 断裂分析要素
从可靠性理论中断裂的应力模型得知,应力和强度是断裂分析的两大 要素,两个要素中哪一个贡献较大?最为活跃?如何地感知和评价是 断裂分析中的一个焦点;
关于灰色系统
是对内部结构可以部分了解或可以综合运用逻辑推理的方法进行 分析的系统。
从人类实践的绝对性来看,人类可以穷尽对机电失效规律及其预 防的认识,但从对失效分析的个别实践和认识来看,又总是在有 限的空间内进行的。因此,对失效特点和规律的认识又往往是有 限的和相对的,这就决定了失效分析的研究和发展总是处于一 个灰色系统内。 (失效分析的持续性、阶段性、可认知性和无止境性) (失效分析的病理学研究方法和流行病学研究方法)
式等原因引发局部产生微动磨损现 象,导致疲劳开裂。这类问题在轴 孔配合结构中最多体现。
疲劳断裂
案例20、某连杆销孔疲劳开裂 在挤压载荷作用下的疲劳开裂; 表现出了对油孔边缘处应力集中
的敏感性。
疲劳断裂
案例22、剪切应力疲劳开裂
半轴、钢板弹簧等零件,产生在高强韧性的零件中; 属于应变疲劳的性质,也称为高应力低周疲劳; 扭转的应力状态更有部件及断裂失效特性
焊接件断裂的原因及预防措施

开展焊接件断裂的实验研究和 案例分析,积累更多的实际经 验和数据,为预防措施的制定 和实施提供更加可靠的支撑。
加强焊接结构的安全性和可靠 性研究,推动焊接技术的不断 创新和发展,为工业生产和工 程建设提供更加可靠和高效的 技术支持。
THANKS
谢谢您的观看
止裂纹的产生。
结构设计改进
01
02
03
优化焊缝设计
合理布置焊缝位置、数量 和尺寸,避免焊缝集中、 受力不均等问题。
加强薄弱部位
对结构中的薄弱部位进行 加强设计,提高焊接件的 承载能力。
考虑焊接变形
在结构设计时充分考虑焊 接变形的影响,采取相应 的补偿措施。
03
工程实例分析
工程实例一:某大型桥梁的焊接断裂问题
总结词
材料缺陷、结构设计不合理
详细描述
该大型桥梁在焊接过程中,由于材料存在缺陷或焊接工艺不当,导致焊接部位出 现微裂纹。在长期承受载荷的作用下,裂纹逐渐扩展,最终导致桥梁断裂。
工程实例二:某压力容器的焊接开裂问题
总结词
焊接工艺不当、使用环境恶劣
详细描述
该压力容器在焊接过程中,由于焊接工艺参数设置不当或焊接后热处理不足,导致焊接部位存在残余应力。在长 期承受压力和腐蚀介质的作用下,焊接部位出现开裂。
焊接件断裂的原因及预防措 施
汇报人: 20 • 焊接件断裂的预防措施 • 工程实例分析 • 结论与展望
01
焊接件断裂的原因
材料因素
母材缺陷
母材中存在的夹渣、气孔、裂纹 等缺陷会导致焊接接头强度下降 ,增加断裂的风险。
焊缝金属组织不均
焊缝金属组织中存在大量脆性相 或夹杂物,导致焊缝金属的韧性 下降,容易发生脆性断裂。
汽修毕业论文 交通事故车辆轮毂断裂原因分析

汽修毕业论文交通事故车辆轮毂断裂原因分析交通事故是时常发生的事件,其中车辆的轮毂断裂是造成许多事故的主要原因之一。
本文将对车辆轮毂断裂的原因进行详细分析,以期提供有关部门和汽修专业人员在修理和预防轮毂断裂方面的参考。
一、背景介绍车辆轮毂承载车轮,并根据车辆的运动进行旋转。
当轮毂出现断裂时,车轮会失去稳定性,导致驾驶员失去控制,从而发生事故。
因此,准确分析车辆轮毂断裂原因,对于保障道路交通安全非常重要。
二、设计与制造问题车辆轮毂的设计和制造质量是造成断裂的主要原因之一。
首先,如果轮毂的设计不合理,不符合车辆的载荷要求,就容易发生断裂。
其次,如果轮毂的制造过程中出现质量问题,如材料选用不当、焊接工艺不合格等,也会导致断裂现象的出现。
三、材料问题轮毂的材料是影响其质量和强度的关键因素之一。
如果选用的材料质量不达标,或者材料有缺陷,如气孔、夹杂等,都会导致轮毂在使用过程中容易断裂。
此外,车辆在行驶过程中会受到各种外力的作用,如果材料的韧性和耐蚀性不强,也会增加轮毂断裂的风险。
四、使用与维护问题车辆使用和维护不当也会导致轮毂断裂。
比如,长期超载使用会使轮毂过度受力,超过其承载能力,使其易于断裂。
同时,使用不合格的轮胎,如磨损过度或胎压过高等,也会对轮毂产生过度载荷,加速其断裂的发生。
另外,缺乏定期维护、润滑和紧固,也会导致轮毂在使用过程中出现断裂。
五、环境与外界因素环境和外界因素也会对车辆轮毂的断裂产生影响。
例如,恶劣的道路条件(如凹凸不平、坑洼等)会使轮毂受到冲击和振动,加速其疲劳断裂。
另外,经常在潮湿或腐蚀性环境中行驶的车辆,轮毂易受到腐蚀和损坏,增加断裂的风险。
六、预防与修复为了预防车辆轮毂的断裂,有几个关键的措施需要采取。
首先,设计和制造轮毂时应符合相关标准和要求,确保质量和强度。
其次,材料选择必须严格按照技术要求,杜绝使用质量不过关的材料。
此外,定期对轮毂进行维护,包括检查螺丝的紧固程度、润滑轮毂轴承以及检查胎压等,可以减少轮毂断裂的风险。
车轮螺栓断裂分析
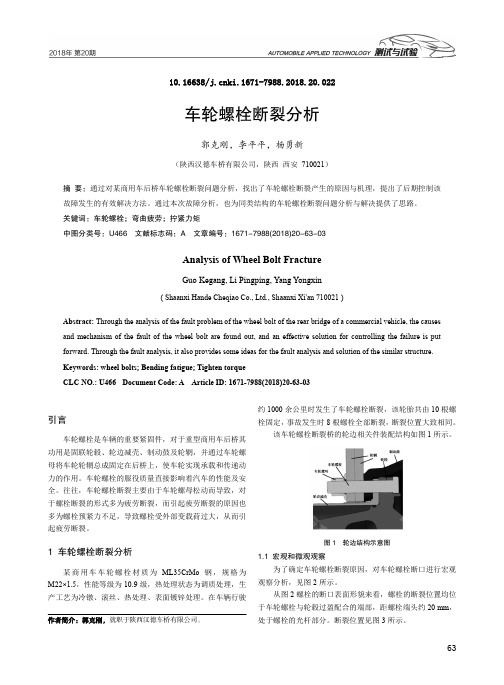
6310.16638/ki.1671-7988.2018.20.022车轮螺栓断裂分析郭克刚,李平平,杨勇新(陕西汉德车桥有限公司,陕西 西安 710021)摘 要:通过对某商用车后桥车轮螺栓断裂问题分析,找出了车轮螺栓断裂产生的原因与机理,提出了后期控制该故障发生的有效解决方法。
通过本次故障分析,也为同类结构的车轮螺栓断裂问题分析与解决提供了思路。
关键词:车轮螺栓;弯曲疲劳;拧紧力矩中图分类号:U466 文献标志码:A 文章编号:1671-7988(2018)20-63-03Analysis of Wheel Bolt FractureGuo Kegang, Li Pingping, Yang Yongxin( Shaanxi Hande Cheqiao Co., Ltd., Shaanxi Xi'an 710021 )Abstract: Through the analysis of the fault problem of the wheel bolt of the rear bridge of a commercial vehicle, the causes and mechanism of the fault of the wheel bolt are found out, and an effective solution for controlling the failure is put forward. Through the fault analysis, it also provides some ideas for the fault analysis and solution of the similar structure. Keywords: wheel bolts; Bending fatigue; Tighten torqueCLC NO.: U466 Document Code: A Article ID: 1671-7988(2018)20-63-03引言车轮螺栓是车辆的重要紧固件,对于重型商用车后桥其功用是固联轮毂、轮边减壳、制动鼓及轮辋,并通过车轮螺母将车轮轮辋总成固定在后桥上,使车轮实现承载和传递动力的作用。
车轮断裂原因分析

车轮断裂原因分析作者:王升李金全来源:《中小企业管理与科技·下旬刊》2014年第11期摘要:通过无损探伤检测、化学成分检测、扫描电镜和金相分析等方法对车轮断裂原因进行了失效分析. 结果表明,由于车轮存在内部气泡缺陷,且车轮材料韧性很差,当锻造或正火处理冷却速度过快时,在缺陷部位形成应力集中,产生开裂源。
关键词:车轮失效分析缺陷0 引言某钢厂生产的Φ600mm车轮在运输过程中发生开裂,该车轮材质为65#钢,制造工艺为锻造—正火—机加—车轮踏面喷水淬火。
为了寻找车轮开裂的原因,我们从宏观和微观断口形貌、材料金相组织及成分等方面对其失效原因进行了分析。
1 宏观检测开裂车轮断口样品宏观形貌如图1所示。
断裂沿车轮径向扩展,断裂部位无宏观塑性变形。
图中上表面均为断面。
■图12 无损探伤检测用PXUT-350B+超声波探伤仪,B4S-N 探头对送检样品进行了超声波检测,检测结果为:在样品中间部位(车轮壁厚心部位置)深约45~70mm之间发现最大当量为Φ4 左右的单个不连续缺陷。
3 化学成分检测化学成分检测结果如表1所示,符合GB/T 699-1999标准中65#钢的成分规定。
表1 化学成分分析结果■4 力学性能检测在非缺陷区截取了拉伸和冲击试样,所得力学性能检测结果如表2所示。
检测结果显示,车轮样品抗拉强度及延伸率符合技术条件要求;冲击吸收功(AKU)很低,说明材料韧性很差(冲击试验样品断口边缘无宏观塑性变形)。
踏板表面硬度平均值为36.3HRC,心部位置硬度平均值为37.7HRC,符合技术条件(HRC:33.1~41.8)要求。
表2 力学性能检测结果与技术条件比对表■5 断口检测断口宏观形貌如图2所示。
用日立S-3400N 型扫描电镜对断裂源区微观形貌进行了检测,结果如图3~7所示。
宏观小亮面位置未显示断面特征(见图3~7),是锻造变形后的气泡缺陷表面[1]。
6 金相检测6.1 取样低倍组织检测样品在缺陷区域截取,金相组织检测样品取自硬度检测样品。
汽车轮毂的断裂失效分析

汽车轮毂的断裂失效分析摘要:通过外观检查、成分测试、硬度测试、金相组织和扫描电镜观察等方法,对某品牌汽车3个轮毅轴承失效件进行分析,可以找出造成轮毅轴承最终断裂失效的原因。
结果表明,3种轮毅轴承的内圈和外圈的组织都符合JB/T1255-2001标准的要求;1#轮轴轴承失效的原因是由于化学成分不合格和轴承内圈滚道的表面硬度较低;2#轮毅轴承的化学成分、硬度和组织都满足要求,失效原因在于密封性较差,而使得外圈滚道中外界硬度相对较高的颗粒落入滚道,造成磨损加剧;3#轮毅轴承外圈碳含量较低,使得外圈滚道表面硬度偏低,且由于润滑条件不好引起了粘着磨损,加剧了轴承的磨损,并最终造成失效。
关键词:轮毅轴承;断裂失效;分析研究一、前言。
随着我国汽车产量不断增加,轮毅轴承的需求量也在日益增大。
轮毅轴承是汽车的重要基础件,其质量对汽车整车质量的影响非常大,对其性能要求也越来越高。
轮毅轴承的作用主要是作为承重件和为轮毅的传动提供精确引导,既承受径向载荷又承受轴向载荷。
常用的汽车轮毅轴是由两套圆锥滚子轴承或球轴承组合而成,其套圈一般采用热锻毛坯结合后续机加工进行生产。
轮毅轴承形状复杂,尺寸精度和形位公差要求高,锻造工艺性差。
目前,国内外各主要轴承企业主要采用开式模锻工艺进行生产,锻件成形质量较差,材料的利用率较低。
某汽车在行驶过程中,其后轮毅轴在安装轴承附近发生断裂,该车累计行驶里程为17km。
轮毅轴材料为65Mn弹簧钢,经毛坯一锻造一机械加工一调质处理一轴表面高频感应淬火(淬火层深度要求为1.5一3.Omm)后成形。
通过对失效轮毅轴进行外观检查,对其断口进行宏、微观观察和能谱分析,对其金相组织和硬度进行检查,确定了裂纹性质,最后分析了其断裂失效的原因,并给出了建议。
本研究对提高后轮毅轴的可靠性,防止同类事故的发生具有一定的工程应用价值。
二、检测分析。
(一)宏观分析。
对其中典型的3种轮毅轴承进行失效分析,编号为1#,2#和3#。
重载车轮辋崩断原因分析

The Analysis of Wheel Rim Breakdown of Heavy-
duty Truck
作者: 陈雪艳 张彦文 孙宜强
作者机构: 武汉钢铁(集团)公司研究院,湖北武汉430080
出版物刊名: 武汉工程职业技术学院学报
页码: 29-32页
年卷期: 2013年 第1期
主题词: 多源疲劳断裂 疏松缺陷
摘要:对重载车轮辋崩断后的断面进行了宏观观察,用扫描电镜和光学金相显微镜对轮辋组织结构进行了解剖分析。
结果表明,轮辋的断裂属多源疲劳断裂,轮辐与轮辋的内外侧焊缝中均存在气孔、疏松、偏焊、熔合线裂纹等缺陷,在轮辋结构张应力集中处产生疲劳源.它在车轮运转过程中不断扩展,最终导致轮辋崩断。
车轮断裂原因分析
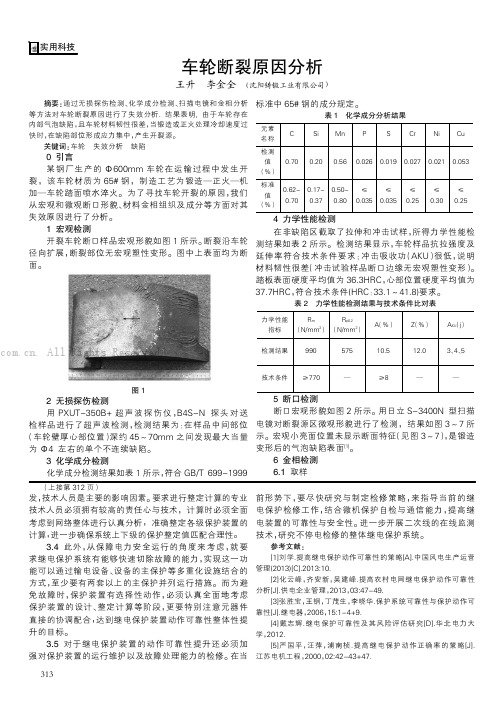
(上接第312页)摘要:通过无损探伤检测、化学成分检测、扫描电镜和金相分析等方法对车轮断裂原因进行了失效分析.结果表明,由于车轮存在内部气泡缺陷,且车轮材料韧性很差,当锻造或正火处理冷却速度过快时,在缺陷部位形成应力集中,产生开裂源。
关键词:车轮失效分析缺陷0引言某钢厂生产的Φ600mm 车轮在运输过程中发生开裂,该车轮材质为65#钢,制造工艺为锻造—正火—机加—车轮踏面喷水淬火。
为了寻找车轮开裂的原因,我们从宏观和微观断口形貌、材料金相组织及成分等方面对其失效原因进行了分析。
1宏观检测开裂车轮断口样品宏观形貌如图1所示。
断裂沿车轮径向扩展,断裂部位无宏观塑性变形。
图中上表面均为断面。
图12无损探伤检测用PXUT-350B+超声波探伤仪,B4S-N 探头对送检样品进行了超声波检测,检测结果为:在样品中间部位(车轮壁厚心部位置)深约45~70mm 之间发现最大当量为Φ4左右的单个不连续缺陷。
3化学成分检测化学成分检测结果如表1所示,符合GB/T 699-1999标准中65#钢的成分规定。
表1化学成分分析结果元素名称C Si Mn P S Cr Ni Cu检测值(%)0.700.200.560.0260.0190.0270.0210.053标准值(%)0.62-0.700.17-0.370.50-0.80≤0.035≤0.035≤0.25≤0.30≤0.254力学性能检测在非缺陷区截取了拉伸和冲击试样,所得力学性能检测结果如表2所示。
检测结果显示,车轮样品抗拉强度及延伸率符合技术条件要求;冲击吸收功(AKU )很低,说明材料韧性很差(冲击试验样品断口边缘无宏观塑性变形)。
踏板表面硬度平均值为36.3HRC,心部位置硬度平均值为37.7HRC,符合技术条件(HRC:33.1~41.8)要求。
表2力学性能检测结果与技术条件比对表力学性能指标R m(N/mm 2)R p0.2(N/mm 2)A (%)Z (%)A KU (j )检测结果99057510.512.03、4、5技术条件≥770—≥8——5断口检测断口宏观形貌如图2所示。
- 1、下载文档前请自行甄别文档内容的完整性,平台不提供额外的编辑、内容补充、找答案等附加服务。
- 2、"仅部分预览"的文档,不可在线预览部分如存在完整性等问题,可反馈申请退款(可完整预览的文档不适用该条件!)。
- 3、如文档侵犯您的权益,请联系客服反馈,我们会尽快为您处理(人工客服工作时间:9:00-18:30)。
不仅引起焊接结构尺寸形状发生变化 , 而且过 大的焊 接 应力 可使 焊接 结构 产 生裂 纹 , 至 断 裂 。 因此 , 甚 焊接
应 力 与变形 是影 响焊 接结 构质 量 的重要 因素 。
4 结束语
在拆 卸 以前 已经部 分开 裂 。 ( )冲压 折 弯处 组 织 已 发 生 塑性 流 变 , 表 明该 4 这 处 存 在冷变 形 硬 化 现 象 及 冷 加 工 应 力 , 轮 辋 的一 个 为 薄弱部 位 , 因此 在 内胎 爆 炸时 , 该 部位撕 裂 开 。 从 ( )焊 接 过 程 是 在 热 力 学 不 平 衡 的 条 件 下 进 行 5 的 , 金属 材料 的冶金 因素 、 受 焊接 件 的结 构 因素 以及焊
处所示。
而该 断 裂 的 车轮 焊 缝 咬 边 已深达 3~ 5mm, 远 超 过 远 了标 准 中对 咬边缺 陷 的要求 。 焊缝 与 轮辋 交 界 处 断 裂 的断 口为疲 劳 断 口, 纹 裂 源 位于 咬边 焊 接 缺 陷形 成 的 尖 角 应 力 集 中处 , 图 4 如 所 示 。轮辋 折弯 处 的断 口为一 次性撕 裂状 断 口。
均匀性加热和焊 接接 头的组织改变等原 因, 焊接结构 总 会 产生 不 同程度 的变形 和 大小 不 同的焊 接应 力 。这
理事 , 从事机械 工程材料和机械制造技 术 的教 学与
研究。
铜 合 金 螺 旋 桨 裂纹 补焊 修 复 工 艺
广州航海高等专科学校(175 50 2 ) 陈爱国
响区已延伸到钢板 的剩余部分 , 热影 响 区组织 如图 5 所示。冲压折弯处显 微组织 已发生 塑性流变 , 如图 6
所示
图 6 轮辋 冲压折弯处 的塑性流变组织 5 0× 0
3 分析讨 论
( )轮辋 的化 学 成 分 , 轮 与 轮 胎 型 号 匹 配 情 况 1 车 均符 合 国家标 准要 求 。
摘 要 采用锰黄铜或 铝青铜铸 造的大型海船 螺旋 桨在 海水 中工作 时容易产生 应力腐蚀裂 纹和腐蚀疲 劳裂纹 。 该裂纹 的修 复一般采 用氩 弧焊 , 在焊接前应进行裂纹 的探伤 , 出是 否可 以补焊的判 断 , 接时要 做好焊接 准备 、 做 焊 执行严格 的工艺操作 , 焊后应进行相应的处理 , 以确保 螺旋 桨的力学性 能和形状 。
( )从焊接 的外观质量看 , 2 车轮存在严重 的咬边
图 5 焊缝热影响 区的组织 10× 0
和气孔等焊接缺 陷。气孔缺陷的存在 , 减少了焊缝 有 效工作截面 , 降低 了焊接接 头强度 , 响焊缝 的致 密 影
( %硝酸酒精溶 液侵蚀 ) 4
维普资讯
( 稿 日期 收 2 0 0 0 ) 0 6 5 9
接接头具有的复杂几何形状 、 应力集 中程度 等综合 因
素所 影 响 , 因此 , 接 工 艺 与 其 它 工 艺 相 比 , 焊 是较 容 易 出现 缺 陷的 一 种 工 艺 。在 焊 接 过 程 中 , 于 焊件 的 不 由
作者简介 : 左传付 ,9 8年 出生 , 15 高级讲 师 , 壁市焊 接 学会 鹤
图 3 焊缝 中的咬边缺陷
图 4 焊缝 与轮辋 交界 熔 化 焊 接 头 的要 求 和 缺 陷 钢 分级 ) B T 26 -9 准 中可 知 , 接 零 件 中 的 Ⅲ级 ) / 149 -0标 G 焊 咬边 缺 陷深度 ≤0 06且 ≤0 5mm, .5 . 咬边 缺 陷 连 续 长
焊 缝处 严重 咬边 和气 孔 等焊 接 缺 陷 是造 成 车 轮断
裂 的主要 原 因 。 由于 焊 接 工 艺 的 特 殊 性 , 汽 车 车 轮 对
这类较 重 要 的零 件 , 接 操 作 者 必 须 经 专 业 培 训 后 持 焊 证上 岗 , 工序 应严格 执 行 工艺 规 程 , 各 同时须 按 标准 要 求检 验 , 其 是 探 伤 检 查更 应严 格 把 关 。焊 后 应 及 时 尤 进行 必要 的热处 理 , 改善 焊接 件 的 内部 组 织 , 除 内应 消 力 , 高其 力学 性能 和安 全可靠 性 。 提
度 ≤10 mm 且 焊 缝 两 侧 咬 边 总 长 ≤1 % 焊 缝 全 长 。 0 0
2 理化 检 验 2 1 化学 成分 .
车轮 化学 成分 见 表 1其 中 ,5 W 为 《 , 1L 汽车 车 轮轮 辋用 热轧 型钢 ) B 6 —8 准 中所 规定 的牌 号 。 ) 122 9标 G 1
维普资讯
维普资讯
・
4 ・ 8
焊接
20 ( ) 06 8
续 的 咬边缺 陷 , 咬边 深 度达 3~5mm, 使 8mm 厚 的 这 轮辋 钢板 的有 效 厚 度 变 成 为 3~ n , 图 3中箭 头 5it 如 o
对 于 汽 车 车 轮 这样 的零 件 是 不 应有 Ⅲ级 咬 边 缺 陷 的 ,
表 1 化学成分 ( 量分 数, ) 质 %
2 2 金 相组 织 .
轮 辋与 轮盘 的 组 织 为 铁 素 体 +少 量珠 光体 , 正 为 常的低 碳钢 热 轧 正 火 组 织 。在 焊 缝 咬 边处 , 接 热 影 焊
焊接
20 ( ) 0 6 8
・4 9・
性 。咬边 缺陷 会 大 大 减 少 基 体 金 属 的有 效 面 积 , 造 易 成应 力集 中 , 会 使 焊 接 接 头 强 度 降低 。轮 盘 和 轮 辋 也 的焊 接接 头 为 双 面 满 圈焊 , 必 造 成 焊 接 残 余 应 力 增 势 大 。最终 导致 车轮从 焊 缝处 产生疲 劳 开裂 。