FPC干制程不良图片
(整理)FPC制程中常见不良因素.
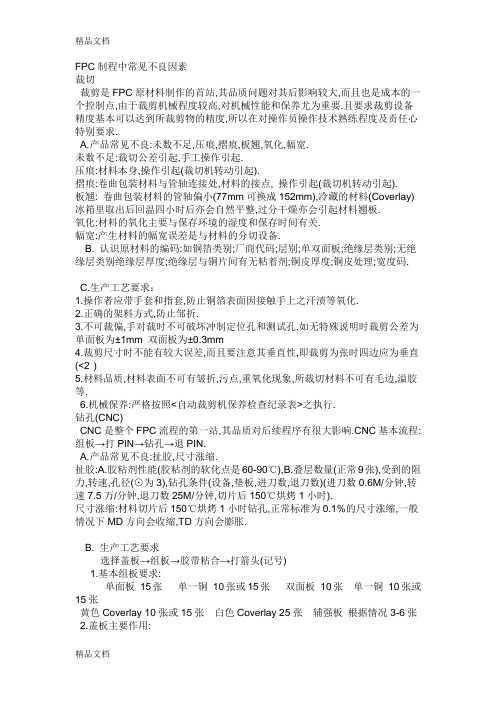
B.研磨种类:
1.待贴膜:双面板去氧化,拉伸(孔位偏移)单面板:去氧化
2.待假贴Coverlay:打磨,去红斑(剥膜后NaOH残留),去氧化
3.待假贴铺强:打磨,清洁
4.待电镀:打磨,清洁,增加附着力
5.电镀后:烘干,提高光泽度
4.预浸;防止对活化槽的污染.
5.活化;使钯胶体附着在孔壁.
6.速化;将Pd离子还原成Pd原子,使化学铜能锡镀上去。
7.化学铜:通过化学反应使铜沉积于孔壁和铜箔表面。
C.PTH生产中不良状况处理办法
1.孔无铜
a:活化钯吸附沉积不好。
b:速化槽:速化剂溶度不对。
c:化学铜:温度过低,使反应不能进行反应速度过慢;槽液成分不对。
否完全导通.
外观品质不可有翘铜,毛边之不良现象.
5.生产制程管控要点
产品确认
流程确认
组合确认
尺寸确认
位置确认
程序确认
刀具确认
坐标确认
方向确认.
6.生产中操作常见不良表现和原因
a.断针:①钻机操作不当,②钻头存有问题,③进刀太快等
b.毛边:①盖板,垫板不正确,②钻孔条件不对,③静电吸附等等
7.影响到钻孔品质的主要原因:
FPC制程中常见不良因素
裁切
裁剪是FPC原材料制作的首站,其品质问题对其后影响较大,而且也是成本的一个控制点,由于裁剪机械程度较高,对机械性能和保养尤为重要.且要求裁剪设备精度基本可以达到所裁剪物的精度,所以在对操作员操作技术熟练程度及责任心特别要求.
A.产品常见不良:未数不足,压痕,摺痕,板翘,氧化,幅宽.
6.机械保养:严格按照<自动裁剪机保养检查纪录表>之执行.
FPC曝光机设计技术手记(10) FPC曝光机作业常见不良分析

元器件可靠性不良 接线安装不良 信号干扰不良 对位识别效率低
对位位移迭代效率低 元器件选择不当 动作设计不合理
日积月累,铁杵成针!
2020-12-02
曝光作业线路开路不良
菲林异物污染
曝光作业线路开路不良
基材异物污染 机内环境异物污染
对位不良
过曝/过蚀不良
菲林表面损伤 菲林表面异物 基材表面异物污染 机内浮尘颗粒污染 对位破孔不良 菲林线路补偿设计 曝光/蚀刻工艺条件控制
曝光机设备运行及可靠性不良
电控不良
曝光机设备运行不良
对位效率不良
动作稳定性不良
曝光作业常见不良分析
曝光作业 常见不良现象
线路不良 运行不良
线路短路不良 线路开路不良 对位孔破孔不良 设备动作不稳定 对位次数过多
曝光作业线路短路不良分析
曝光解析度
曝光作业线路短路不良
菲林/铬版 曝光工艺调节裕度
干膜覆膜质量
Gap过大 是否抽真空 光源安装准直性 菲林制造精度 线路设计补偿 曝光能量调节 曝光时间调节裕度 干膜覆膜颗粒物
FPC曝光机设计技术手记(10)
—— FPC曝光机作业常见不良分析
曝光干膜覆膜时毛絮异物影响不良
分析: 左图中的不良主要可能是干膜覆合作业过程 中的毛絮污染物不良,主要原因是在干膜覆 合作业过程中,在基材与干膜之间存在毛絮 状异物,从而影响了干膜与基材的附着力, 并在后续蚀刻作业中造成失去干膜保护区域 的“过蚀”不良;其主要的不良判断特征为: 1、这类不良全部为过蚀或断路不良; 2、在显微镜下观察,不良部位存在明显的毛 絮状异物;
曝光干膜覆膜附着力不良,蚀刻中干膜飘起
分析: 这类情况主要原因可能是干膜覆合时 压膜条件和覆膜后老化时间不足,造 成蚀刻过程中干膜局部与基材气隙剥 离,而没有干膜保护的部分在蚀刻作 业过程中造成过蚀短路。其主要的不 良判断特征是: 1、全部为断路不良; 2、断路不良部分为连续弧曲线形状。
FPC常见不良

开料:裁剪是FPC原材料制作的首站,其品质问题对其后影响较大,而且也是成本的一个控制点,由于裁剪机械程度较高,对机械性能和保养尤为重要,且要求裁剪设备精度基本可以达到所裁剪的精度,所以在对操作员操作技术熟练程度及责任心特别要求。
1、开料前要注意检查:1>、取出来的材料型号是否与MI是否一致2>、确保材料在生产日期之内3>、检查材料对否因为存储环境导致变质2、产品常见不良及预防:未数不足、压痕、折痕、板翘、氧化、幅宽。
1>、未数不足:裁切公差引起,手工操作引起。
2>、压痕:材料本身,操作引起(裁切机转动引起)。
3>、折痕:卷曲包装材料与管轴连接处,材料的接点,操作引起(裁切机转动引起)。
4>、板翘:卷曲包装材料的管轴偏小(77mm可换成152mm),冷藏的材料(Coverlay)。
冰箱里取出后回温四小时后亦会自然平整,过分干燥亦会引起材料翘板。
5>、氧化:材料的氧化主要与保存环境的湿度和保存时间有关。
6>、幅宽:产生材料的幅宽误差是与材料的分切设备有关。
3、控制不良方法:上述大部分不良都与员工操作有关,即认为因素。
针对此,采取以下解决方法。
1>、操作者应带手套和指套,防止铜箔表面因接触手上的汗渍等氧化。
2>、正确的架料方式,防止邹折。
3>、不可裁偏,手对裁时不可破坏冲制定位孔和测试孔。
如无特殊说明时裁剪公差为单面板为±1mm ,双面板为±0.3mm。
4>、裁剪尺寸时不能有较大误差,而且要注意其垂直性,即裁剪为张时四边应为垂直(<2°)。
5>、材料品质,材料表面不可有皱折、污点、重氧化现象,所裁切材料不可有毛边、溢胶等。
6>、机械保养:严格按照<自动裁剪机保养检查纪录表>之执行。
钻孔:有时为了让一般的线路板符合客户的要求,常常要钻出不同用途的孔,例如,测试孔、定位孔、导通孔(双面板、多面板)、零件孔、识别孔等。
FPC制程中常见不良因素

FPC制程中常见不良因素在FPC(柔性印刷电路)制程中,常见的不良因素包括以下几个方面:1. 材料问题:材料是FPC制程的基础,而使用劣质或不合格的材料会直接影响到产品质量。
例如,基材的厚度不均匀、柔韧度不够或表面有缺陷等都会导致制程中的不良。
2. 印刷问题:印刷是FPC制程中的一个重要步骤,而不良的印刷会直接影响到导线的连接和绝缘层的性能。
常见的印刷问题包括图形失真、线宽不一致、线间距不符合要求等。
3. 焊接问题:焊接是FPC制程中连接电子元件的关键步骤,而不良的焊接会导致电子元件与FPC之间的连接不牢固,甚至出现接触不良或短路等问题。
常见的焊接问题有焊点不完整、焊接温度不稳定或焊盘设计不良等。
4. 切割问题:在FPC制程中,切割是将制成好的FPC板切割成需要的尺寸的步骤。
然而,不良的切割会导致切割边缘不平整、切割过深或切割过浅等问题,影响到产品的外观和实用性。
5. 测试问题:最后一个环节是对FPC产品进行测试,以确保其质量符合要求。
不良的测试会导致缺陷产品进入市场,给消费者带来损失。
常见的测试问题包括测试设备故障、测试程序不完善或测试指标不准确等。
综上所述,FPC制程中的不良因素主要包括材料问题、印刷问题、焊接问题、切割问题和测试问题。
在FPC制程中,为了确保产品质量和性能,必须对这些不良因素进行有效的预防和控制。
延续上述所说的FPC制程中常见不良因素,以下是关于每个因素的详细解释和有效控制措施:1. 材料问题:在FPC制程中,选择高质量的基材和覆盖层材料至关重要。
首先,基材的厚度应均匀,以确保整个FPC板的弯曲性和柔韧性一致。
其次,基材表面应无异物、凹凸或损伤,以防止材料在制程中的破裂或损坏。
另外,覆盖层材料的粘附性和耐磨性也必须符合要求,以确保FPC板的绝缘和保护功能。
要解决材料问题,厂商应严格选择和采购合格的材料,并确保供应商提供的材料符合相关标准和要求。
2. 印刷问题:在FPC制程中,印刷是将导线层印在基材表面的关键步骤。
产品制程不良率统计表

日期
12/1 12/1 12/1 12/1 12/1 12/1 12/1 12/1 12/1 12/1 12/2 12/2 12/2 12/2 12/2 12/2 12/1 12/2 12/3 12/4 12/5 12/6 12/7 12/8 12/9 0 1 2 3 4 5 6 7 8 9 0 1 2 3 4 5
生产总数
良品数
不良数
0
0
0
0
0
0
0
0
0
0
0
0
0
0
0
0
0
0
0
0
0
0
0
0
0
不良率
/
/
/
/
/
/
/
/
/
/
/
/
/
/
/
/
/
/
/
/
/
/
/
/
/
翹PIN
電測不良
端子變形
不 良
焊端錫子不 鉚良壓Fra bibliotek现 變形
象 PCB裝歪
來料不良
其它不良
注:
1:本表为产品生产的履历表;2:本表要求填写完后才可用第二张;3:日期不顺延,接到上次的生产日期;4:只在浅绿色的部份进行填写具体内容;5:黄色部份为 具体的不良现象.
产品生产履历表
产品生产履历表
產品名稱
产品型号
生产部门
不良率目标值
备注
100% 90% 80% 70% 60% 50% 40% 30% 20% 10% 0%
不良率统计图
0.0% 0.0% 0.0% 0.0% 0.0% 0.0% 0.0% 0.0% 0.0% 0.0% 0.0% 0.0% 0.0% 0.0% 0.0% 0.0% 0.0% 0.0% 0.0% 0.0% 0.0% 0.0% 0.0% 0.0% 0.0% 12/1 12/2 12/3 12/4 12/5 12/6 12/7 12/8 12/9 12/10 12/11 12/12 12/13 12/14 12/15 12/16 12/17 12/18 12/19 12/20 12/21 12/22 12/23 12/24 12/25
FPC不良因素及改善ppt课件

誠信、努力、熱忱
3
曝光不良
A.抽真空曝光時間 B.菲林刮傷或 調整曝光條件、修復或更
有贓物
新菲林
圖像轉移 顯影不潔或過度 藥液濃度或傳送速度失調
重新配制藥液或調整參數
壓膜氣泡
A.壓膜壓力太低 B。板面磨刷不 A.調整壓力
良
B.調整磨刷粗糙度
蝕刻
殘銅、缺口、斷 路
噴嘴堵塞蝕刻參數不當
A.清洗噴嘴B.重新校正蝕 刻參數
2
制程 工藝 設計
開料
鑽孔
沉銅+ 電鍍 銅
不良項目
發生原因
改進措施
1.菲林制作不良
貯存不當
重新制作菲林,改善菲林貯 存條件
2.MI資料編錯
人員疏忽
加強QA資料審核
1.板面皺折
A.違反操作規范,拿板和出貨動作不正確
提高人員品質意識,加強教 育訓練及操作熟練度
2.尺寸不正確
A.首件確認錯誤 B.機器誤差太大 C。操作時精力不集中。
不良
測試
機械加工
毛刺、偏移、 壓傷
膜具鈍化、模具設計出錯、模具裝 置不當、或模具老化
模具磨或重開膜 增加模 具清潔頻率重新裝置模具 或模具返磨
誠信、努力、熱忱
4
二、客戶對材料品質需求
平
平整性主要表現在外觀上,在FPC制程中,其一般不會造成成品性能
整 上的影響,但會給終端客戶造成元件安裝上的不便,但如翹曲過度也會
壓合
溢膠過大、氣泡、 層離、滲透、壓
傷、皺折
壓合參數不當,腹膜膠厚不均或超 過保存期,操作不規范
重新調整壓合參數,不要 使用過期覆膜
表面涂覆
錫(金)面粗糙 或不均
工作溶液失調或失效
fpc常见不良

1.作业 时要保持 底片和板 子的清 洁;
2.底片 与板子应 对准,正 确;
3.不可 有气泡, 杂质;放 片时要注 意将孔露 出。
4.双面 板作业时 应垫黑纸 以防止曝 光。
B.品质 确认:
底片的 规格,露 光机的曝 光能量, 底片与干 膜的紧贴 度都会影 响线路的 精密度。
1.准确 性
B.PTH 流程及各 步作用
整孔→ 水洗→微 蚀→水洗 →酸洗→ 水洗→水 洗→预浸 →活化→ 水洗→速 化→水洗 →水洗→ 化学铜→ 水洗. 1.整孔; 清洁板 面,将孔 壁的负电 荷极化为 政电荷, 已利与带 负电荷的 钯胶体粘 附.
2.微蚀; 清洁板 面;粗化 铜箔表 面,以增 加镀层的 附3.着酸性洗.; 清洁板 面;除去 氧化层, 杂4.质预.浸; 防止对活 化槽的污 染5..活化; 使钯胶体 附着在孔 壁6..速化; 将Pd离 子还原成 Pd原 子,使化 学铜能锡 镀上去。 7.化学 铜:通过 化学反应 使铜沉积 于孔壁和 铜箔表面 。
0.3mm
4.裁剪尺 寸时不能 有较大误 差,而且 要注意其 垂直性, 即裁剪为 张时四边 应为垂直
(5<.材2°料) 品 质,材料 表面不可 有皱折, 污点,重 氧化现 象,所裁 切材料不 可有毛 边,溢胶 6.机械保 养:严格 按照<自 动裁剪机 保养检查 纪录表> 之执行.
钻孔
(CNC) CNC是 整个FPC 流程的第 一站,其 品质对后 续程序有 很大影 响.CNC 基本流 程:组板 →打PIN →钻孔→ 退A.P产IN品. 常见不 良:扯胶, 尺寸涨 缩.
B. 认识 原材料的 编码:如 铜箔类 别;厂商 代码;层 别;单双 面板;绝 缘层类 别;无绝 缘层类别 绝缘层厚 度;绝缘 层与铜片 间有无粘 着剂;铜 皮厚度; 铜皮处
FPC 生产过程常见不良原因分析

FPC 生产过程常见不良原因分析2010-12-16 23:44:05| 分类:FPC 生产过程常见 | 标签:拉丝/拖尾 how to solve tail |字号大中小订阅1、拉丝/拖尾现象:拉丝/拖尾,点胶中常见缺陷生原因:胶嘴内径太小,点胶压力太高,胶嘴离PCB的间距太大,粘胶剂过期或品质不好,贴片胶黏度太高,从冰箱中取出后未能恢复到室温,点胶量太多等。
解决办法:改换内径较大的胶嘴,降低点胶压力,调节“止动”高度,换胶,选择适合黏度的胶种,从冰箱中取出后应恢复到室温(约4h),调整点胶量。
2、胶嘴堵塞现象:胶嘴出量偏少活没有胶点出来。
生原因:针孔内未完全清洗干净,贴片胶中混入杂质,有堵孔现象,不相容的胶水相混合。
解决办法:换清洁的针头,换质量较好的贴片胶,贴片胶牌号不应搞错。
3、孔打现象:只有点胶动作,无出现胶量。
产生原因:混入气泡,胶嘴堵塞解决方法:注射筒中的胶应进行脱气泡处理(特别是自己装的胶),按胶嘴堵塞方法处理。
4、元器件偏移象:固化元器件移位,严重时元器件引脚不在焊盘上。
产生原因:贴片胶出胶量不均匀(例如片式元件两点胶水一个多一个少),贴片时,元件移位,贴片胶黏力下降,点胶后PCB放置时间太长,胶水半固化。
解决办法:检查胶嘴是否有堵塞,排除出胶不均匀现象,调整贴片机工作状态,换胶水,点胶后PCB放置时间不应过长(小于4h)。
5、固化后,元器件黏结强度不够,波峰焊后会掉片现象:固化后,元器件黏结强度不够,低于规范值,有时用手触摸会出现掉片产生原因:固化后工艺参数不到位,特别是温度不够,元件尺寸过大,吸热量大,光固化灯老化,胶水不够,元件/pcb有污染。
解决办法:调整固化曲线,特别是提高固化温度,通常热固化胶的峰值固化温度很关键,达到峰值温度易引起掉片,对光固化胶来说,应观察光固化灯是否老化,灯管是否有发黑现象,胶水的数量,元件/pcb是否有污染。
6、固化后元件引脚上浮/移位现象:固化后元件引脚浮起来或移位,波峰焊后锡料会进入焊盘,严重时会出现短路和开路。
FPC常见不良

开料:裁剪是FPC原材料制作的首站,其品质问题对其后影响较大,而且也是成本的一个控制点,由于裁剪机械程度较高,对机械性能和保养尤为重要,且要求裁剪设备精度基本可以达到所裁剪的精度,所以在对操作员操作技术熟练程度及责任心特别要求。
1、开料前要注意检查:1>、取出来的材料型号是否与MI是否一致2>、确保材料在生产日期之内3>、检查材料对否因为存储环境导致变质2、产品常见不良及预防:未数不足、压痕、折痕、板翘、氧化、幅宽。
1>、未数不足:裁切公差引起,手工操作引起。
2>、压痕:材料本身,操作引起(裁切机转动引起)。
3>、折痕:卷曲包装材料与管轴连接处,材料的接点,操作引起(裁切机转动引起)。
4>、板翘:卷曲包装材料的管轴偏小(77mm可换成152mm),冷藏的材料(Coverlay)。
冰箱里取出后回温四小时后亦会自然平整,过分干燥亦会引起材料翘板。
5>、氧化:材料的氧化主要与保存环境的湿度和保存时间有关。
6>、幅宽:产生材料的幅宽误差是与材料的分切设备有关。
3、控制不良方法:上述大部分不良都与员工操作有关,即认为因素。
针对此,采取以下解决方法。
1>、操作者应带手套和指套,防止铜箔表面因接触手上的汗渍等氧化。
2>、正确的架料方式,防止邹折。
3>、不可裁偏,手对裁时不可破坏冲制定位孔和测试孔。
如无特殊说明时裁剪公差为单面板为±1mm ,双面板为±0.3mm。
4>、裁剪尺寸时不能有较大误差,而且要注意其垂直性,即裁剪为张时四边应为垂直(<2°)。
5>、材料品质,材料表面不可有皱折、污点、重氧化现象,所裁切材料不可有毛边、溢胶等。
6>、机械保养:严格按照<自动裁剪机保养检查纪录表>之执行。
钻孔:有时为了让一般的线路板符合客户的要求,常常要钻出不同用途的孔,例如,测试孔、定位孔、导通孔(双面板、多面板)、零件孔、识别孔等。
FPC常见不良及预防PPT文档31页

31、只有永远躺在泥坑里的人,才不会再掉进坑里。——黑格尔 32、希望的灯一旦熄灭,生活刹那间变成了一片黑暗。——普列姆昌德 33、希望是人生的乳母。——科策布 34、形成天才的决定因素应该是勤奋。——郭沫若 35、学到很多东西的诀窍,就是一下子不要学很多。——洛克
FPC常见不良及预防
16、自己选择的路、跪着也要把它走 完。 17、一般情况下)不想三年以后的事, 只想现 在的事 。现在 有成就 ,以后 才能更 辉煌。
18、敢于向黑暗宣战的人,心里必须 充满光 明。 19、学习的关键--重复。
20、懦弱的人只会裹足不前,莽撞的 人只能 引为烧 身,只 有真正
FPC各制程的不良原因分析及管制重点
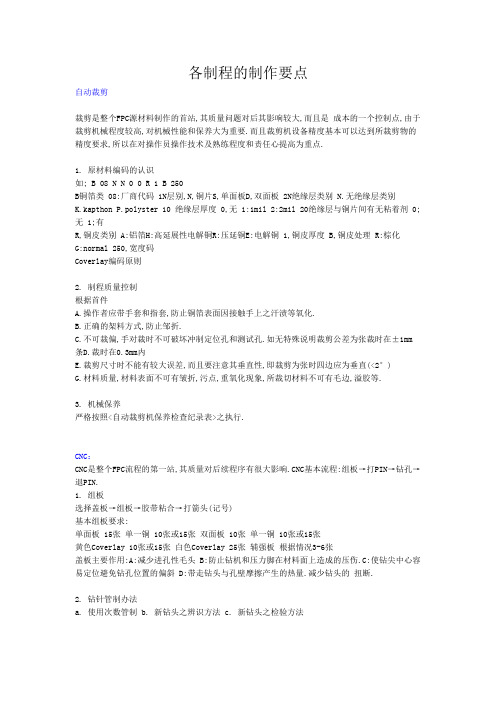
各制程的制作要点自动裁剪裁剪是整个FPC源材料制作的首站,其质量问题对后其影响较大,而且是成本的一个控制点,由于裁剪机械程度较高,对机械性能和保养大为重要.而且裁剪机设备精度基本可以达到所裁剪物的精度要求,所以在对操作员操作技术及熟练程度和责任心提高为重点.1. 原材料编码的认识如; B 08 N N 0 0 R 1 B 250B铜箔类 08:厂商代码 1N层别,N,铜片S,单面板D,双面板 2N绝缘层类别 N.无绝缘层类别K.kapthon P.polyster 10 绝缘层厚度 0,无 1:1mil 2:2mil 20绝缘层与铜片间有无粘着剂 0;无 1;有R,铜皮类别 A:铝箔H:高延展性电解铜R:压延铜E:电解铜 1,铜皮厚度 B,铜皮处理 R:棕化G:normal 250,宽度码Coverlay编码原则2. 制程质量控制根据首件A.操作者应带手套和指套,防止铜箔表面因接触手上之汗渍等氧化.B.正确的架料方式,防止邹折.C.不可裁偏,手对裁时不可破坏冲制定位孔和测试孔.如无特殊说明裁剪公差为张裁时在±1mm 条D.裁时在0.3mm内E.裁剪尺寸时不能有较大误差,而且要注意其垂直性,即裁剪为张时四边应为垂直(<2°)G.材料质量,材料表面不可有皱折,污点,重氧化现象,所裁切材料不可有毛边,溢胶等.3. 机械保养严格按照<自动裁剪机保养检查纪录表>之执行.CNC:CNC是整个FPC流程的第一站,其质量对后续程序有很大影响.CNC基本流程:组板→打PIN→钻孔→退PIN.1. 组板选择盖板→组板→胶带粘合→打箭头(记号)基本组板要求:单面板 15张单一铜 10张或15张双面板 10张单一铜 10张或15张黄色Coverlay 10张或15张白色Coverlay 25张辅强板根据情况3-6张盖板主要作用:A:减少进孔性毛头 B:防止钻机和压力脚在材料面上造成的压伤.C:使钻尖中心容易定位避免钻孔位置的偏斜 D:带走钻头与孔壁摩擦产生的热量.减少钻头的扭断.2. 钻针管制办法a. 使用次数管制b. 新钻头之辨识方法c. 新钻头之检验方法3. 品质管控点a. 正确性;依据对b. 钻片及钻孔数据确认产品孔位与c. 孔数的正确性,并check断针监视孔是否完全导通.d. 外观质量;不e. 可有翘铜,毛边之不f. 良现象.4. 制程管控a. 产品确认b.流程确认c. 组合确认d.尺寸确认e. 位置确认f. 程序确认g.刀具确认h.坐标确认i. 方向确认.5. 常见不良表现即原因断针 a.钻机操作不当 b.钻头存有问题c.进刀太快等毛边 a.盖板,垫板不正确 b. 钻孔条件不对 c. 静电吸附等等7. 良好的钻孔质量a. 操作人员;技术能力,责任心,熟练程度b. 钻针;材质,形状,钻数,钻尖c. 压板;垫板;材质,厚度,导热性d. 钻孔机;震动,位置精度,夹力,辅助性能e. 钻孔参数;分次/单次加工方法,转数,进刀退刀速.f. 加工环境;外力震h. 动,噪音,温度,湿度相关连接;我司28日,机种F5149-001-CO1 由于程序的使用误用,造成钻孔’’不良’’2700张,虽然两公司都有工作上的疏忽,但对于我司的质量要求,故也要对程序要有个相对完善的管理方案.P.T.H站1.PTH原理及作用PTH即在不外加电流的情况下,通过镀液的自催化(钯和铜原子作为催化剂)氧化还原反应,使铜离子析镀在经过活化处理的孔壁及铜箔表面上的过程,也称为化学镀铜或自催化镀铜,化学反应方程式:2.PHT流程及各步作用整孔→水洗→微蚀→水洗→酸洗→水洗→水洗→预浸→活化→水洗→速化→水洗→水洗→化学铜→水洗.a. 整孔;清洁板面,将孔壁的负电荷极化为政电荷,已利与带负电荷的钯胶体粘附.b. 微蚀;清洁板面;粗化铜箔表面,以增加镀层的附着性.c. 酸洗;清洁板面;除去氧化层,杂质.d. 预浸;防止对活化槽的污染.e. 活化;使钯胶体附着在孔壁.f. 速化;将Pd离子还原成Pd原子,使化学铜能锡镀上去。
FPC各制程的不良原因分析及管制重点

FPC各制程的不良原因分析及管制重点各制程的制作要点自动裁剪裁剪是整个FPC源材料制作的首站,其质量问题对后其影响较大,而且是成本的一个控制点,由于裁剪机械程度较高,对机械性能和保养大为重要.而且裁剪机设备精度基本可以达到所裁剪物的精度要求,所以在对操作员操作技术及熟练程度和责任心提高为重点.1. 原材料编码的认识如; B 08 N N 0 0 R 1 B 250B铜箔类 08:厂商代码 1N层别,N,铜片S,单面板D,双面板 2N绝缘层类别 N.无绝缘层类别K.kapthon P.polyster 10 绝缘层厚度 0,无 1:1mil 2:2mil 20绝缘层与铜片间有无粘着剂 0;无 1;有R,铜皮类别 A:铝箔H:高延展性电解铜R:压延铜E:电解铜 1,铜皮厚度 B,铜皮处理 R:棕化G:normal 250,宽度码Coverlay编码原则2. 制程质量控制根据首件A.操作者应带手套和指套,防止铜箔表面因接触手上之汗渍等氧化.B.正确的架料方式,防止邹折.C.不可裁偏,手对裁时不可破坏冲制定位孔和测试孔.如无特殊说明裁剪公差为张裁时在±1mm 条D.裁时在0.3mm内E.裁剪尺寸时不能有较大误差,而且要注意其垂直性,即裁剪为张时四边应为垂直(<2°)G.材料质量,材料表面不可有皱折,污点,重氧化现象,所裁切材料不可有毛边,溢胶等.3. 机械保养严格按照<自动裁剪机保养检查纪录表>之执行.CNC:CNC是整个FPC流程的第一站,其质量对后续程序有很大影响.CNC基本流程:组板→打PIN→钻孔→退PIN.1. 组板选择盖板→组板→胶带粘合→打箭头(记号)基本组板要求:单面板 15张单一铜 10张或15张双面板 10张单一铜 10张或15张黄色Coverlay 10张或15张白色Coverlay 25张辅强板根据情况3-6张盖板主要作用:A:减少进孔性毛头B:防止钻机和压力脚在材料面上造成的压伤.C:使钻尖中心容易定位避免钻孔位置的偏斜D:带走钻头与孔壁摩擦产生的热量.减少钻头的扭断.2. 钻针管制办法a. 使用次数管制b. 新钻头之辨识方法c. 新钻头之检验方法3. 品质管控点a. 正确性;依据对b. 钻片及钻孔数据确认产品孔位与c. 孔数的正确性,并check断针监视孔是否完全导通.d. 外观质量;不e. 可有翘铜,毛边之不f. 良现象.4. 制程管控a. 产品确认b.流程确认c. 组合确认d.尺寸确认e. 位置确认f. 程序确认g.刀具确认h.坐标确认i. 方向确认.5. 常见不良表现即原因断针 a.钻机操作不当 b.钻头存有问题c.进刀太快等毛边 a.盖板,垫板不正确 b. 钻孔条件不对 c. 静电吸附等等7. 良好的钻孔质量a. 操作人员;技术能力,责任心,熟练程度b. 钻针;材质,形状,钻数,钻尖c. 压板;垫板;材质,厚度,导热性d. 钻孔机;震动,位置精度,夹力,辅助性能e. 钻孔参数;分次/单次加工方法,转数,进刀退刀速.f. 加工环境;外力震h. 动,噪音,温度,湿度相关连接;我司28日,机种F5149-001-CO1 由于程序的使用误用,造成钻孔’’不良’’2700张,虽然两公司都有工作上的疏忽,但对于我司的质量要求,故也要对程序要有个相对完善的管理方案.P.T.H站1.PTH原理及作用PTH即在不外加电流的情况下,通过镀液的自催化(钯和铜原子作为催化剂)氧化还原反应,使铜离子析镀在经过活化处理的孔壁及铜箔表面上的过程,也称为化学镀铜或自催化镀铜,化学反应方程式:2.PHT流程及各步作用整孔→水洗→微蚀→水洗→酸洗→水洗→水洗→预浸→活化→水洗→速化→水洗→水洗→化学铜→水洗.a. 整孔;清洁板面,将孔壁的负电荷极化为政电荷,已利与带负电荷的钯胶体粘附.b. 微蚀;清洁板面;粗化铜箔表面,以增加镀层的附着性.c. 酸洗;清洁板面;除去氧化层,杂质.d. 预浸;防止对活化槽的污染.e. 活化;使钯胶体附着在孔壁.f. 速化;将Pd离子还原成Pd原子,使化学铜能锡镀上去。
FPC制程中常见不良因素
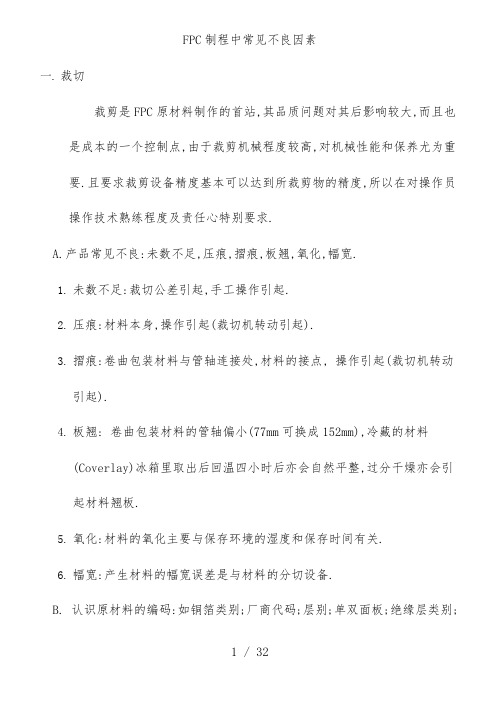
FPC制程中常见不良因素一. 裁切裁剪是FPC原材料制作的首站,其品质问题对其后影响较大,而且也是成本的一个控制点,由于裁剪机械程度较高,对机械性能和保养尤为重要.且要求裁剪设备精度基本可以达到所裁剪物的精度,所以在对操作员操作技术熟练程度及责任心特别要求.A.产品常见不良:未数不足,压痕,摺痕,板翘,氧化,幅宽.1.未数不足:裁切公差引起,手工操作引起.2.压痕:材料本身,操作引起(裁切机转动引起).3.摺痕:卷曲包装材料与管轴连接处,材料的接点, 操作引起(裁切机转动引起).4.板翘: 卷曲包装材料的管轴偏小(77mm可换成152mm),冷藏的材料(Coverlay)冰箱里取出后回温四小时后亦会自然平整,过分干燥亦会引起材料翘板.5.氧化:材料的氧化主要与保存环境的湿度和保存时间有关.6.幅宽:产生材料的幅宽误差是与材料的分切设备.B. 认识原材料的编码:如铜箔类别;厂商代码;层别;单双面板;绝缘层类别;无绝缘层类别绝缘层厚度;绝缘层与铜片间有无粘着剂;铜皮厚度;铜皮处理;宽度码.C.生产工艺要求:1.操作者应带手套和指套,防止铜箔表面因接触手上之汗渍等氧化.2.正确的架料方式,防止邹折.3.不可裁偏,手对裁时不可破坏冲制定位孔和测试孔.如无特殊说明时裁剪公差为单面板为±1mm 双面板为±0.3mm4.裁剪尺寸时不能有较大误差,而且要注意其垂直性,即裁剪为张时四边应为垂直(<2°)5.材料品质,材料表面不可有皱折,污点,重氧化现象,所裁切材料不可有毛边,溢胶等.6.机械保养:严格按照<自动裁剪机保养检查纪录表>之执行.二. 钻孔(CNC)CNC是整个FPC流程的第一站,其品质对后续程序有很大影响.CNC基本流程:组板→打PIN→钻孔→退PIN.A.产品常见不良:扯胶,尺寸涨缩.1.扯胶:A.胶粘剂性能(胶粘剂的软化点是60-90℃),B.叠层数量(正常9张),受到的阻力,转速,孔径(⊙为3),钻孔条件(设备,垫板,进刀数,退刀数)(进刀数0.6M/分钟,转速7.5万/分钟,退刀数25M/分钟,切片后150℃烘烤1小时).2.尺寸涨缩:材料切片后150℃烘烤1小时钻孔,正常标准为0.1%的尺寸涨缩,一般情况下MD方向会收缩,TD方向会膨胀.B. 生产工艺要求选择盖板→组板→胶带粘合→打箭头(记号)1.基本组板要求:单面板 15张单一铜 10张或15张双面板 10张单一铜 10张或15张黄色Coverlay 10张或15张白色Coverlay 25张辅强板根据情况3-6张2.盖板主要作用:a.减少进孔性毛头.b.防止钻机和压力脚在材料面上造成的压伤.c.使钻尖中心容易定位避免钻孔位置的偏斜.d.带走钻头与孔壁摩擦产生的热量,减少钻头的扭断.3.钻针管制办法a.使用次数管制.b.新钻头之辨识方法.c.新钻头之检验方法.4.品质管控要点a.依据钻片及钻孔资料确认产品孔位与孔数的正确性,并检查断针,验视钻孔是否完全导通.b.外观品质不可有翘铜,毛边之不良现象.5.生产制程管控要点a.产品确认b.流程确认c.组合确认d.尺寸确认e.位置确认f.程序确认g.刀具确认h.坐标确认i.方向确认.6. 生产中操作常见不良表现和原因a.断针 :①钻机操作不当,②钻头存有问题,③进刀太快等b.毛边 :①盖板,垫板不正确,②钻孔条件不对,③静电吸附等等7. 影响到钻孔品质的主要原因:a. 操作人员;技术能力,责任心,熟练程度b. 钻针;材质,形状,钻数,钻尖c. 压板;垫板;材质,厚度,导热性d. 钻孔机;震动,位置精度,夹力,辅助性能e. 钻孔参数;分次/单次加工方法,转数,进刀退刀速.f. 加工环境;外力震动,噪音,温度,湿度三. 磨刷研磨是FPC制程中可能被多次利用的一个辅助制程,作为其它制程的预处理或后处理工序,一般先对板子进行酸洗,微蚀或抗氧化处理,然后利用尼龙轮刷对板子的表面进行刷磨以除去板子表面的杂质,黑化层,残胶等。
制程不良品处理流程图

4、制程不良配Βιβλιοθήκη 扔到废料框、私自处理放到报废区域、未开报废单或报废单未经过品管经理签字就处理掉的,一经发现警告处分;
5、未祥之处参考公司不良品管理制度文件。
编订:核对:批准:
备注:
1、制程内部直接产生的不良品须须通过组长或调模工、物料员,经品管确认后放置不良品区,并按要求填写不良品登记表,私自放置:第一次口头警告,第二次申诫处分。
2、包装、中间仓退下不良品须填写不良品退货单,经品管确认,接收单位签字,许可放置指定区域,没有任何程序,私自放置:第一次口头警告,第二次申诫处分。
FPC制程品质缺陷样本录

本样本录包括工序介绍、检验流程、注意事项、缺陷原因、改善措施属 PQC 人员教育训练用。
审核
做成
工序不良样本解析
NO:
样本工序 缺陷名称
冲切 不完全冲切
样本料号 缺陷等级
H0202502 □CR ■MA □MI
3.重新验收模具
样本工序 缺陷名称 判定标准
缺陷产生现状描述: 模具刀口间缝隙偏大 缺陷样本:
缺陷图示:
冲切
样本料号
T0102142C-1
毛边
缺陷等级
□CR □MA ▓MI
导体毛边不可有;非导体毛边长须小于 0.3mm 宽小于 0.2mm,可接收
原因分析: 1. 模具刀口合模间隙偏大 2. 刀口太钝 3. 压力偏小
检验流程
确认模具编号→有无流程单或模版→了解流程单上的作业及检验事项→首件确认(OK 品留 样)→相关记录→按频率巡线检验→相关记录
检验注意事项
模具编号、是否有流程单、是否有模板、首件检验、巡线检验、作业者自检、按频率清洁
缺陷产生现状描述:
冲切外形时,作业者套错了孔,导致裁偏裁到了铜皮
缺陷样本:
原因分析:
确认模具编号→有无流程单或模版→了解流程单上的作业及检验事项→首件确认(OK 品留 样)→相关记录→按频率巡线检验→相关记录
检验注意事项
模具编号、是否有流程单、是否有模板、首件检验、巡线检验、作业者自检、按频率清洁
缺陷产生现状描述:
模具冲针太短且当时冲床压力大小
缺陷样本:
原因分析:
1. 模具冲针太短
本样本录包括工序介绍、检验流程、注意事项、缺陷原因、改善措施属 PQC 人员教育训练用。
- 1、下载文档前请自行甄别文档内容的完整性,平台不提供额外的编辑、内容补充、找答案等附加服务。
- 2、"仅部分预览"的文档,不可在线预览部分如存在完整性等问题,可反馈申请退款(可完整预览的文档不适用该条件!)。
- 3、如文档侵犯您的权益,请联系客服反馈,我们会尽快为您处理(人工客服工作时间:9:00-18:30)。
渗镀
1、压合保护膜后是否存在 气泡现象; 2、保护膜之接著剂未完全 熟化,不抗药液之攻击; 3、是否保护膜之接著剂与 药水不间融;
判 定:OK
判 定:NG
缺 陷
弧度
改善方向
1、板材是否涨缩; 2、冲孔定位孔是否偏差;
缺 陷
弧度
改善方向
1、板材是否涨缩; 2、冲孔定位孔是否偏差;
名 称
冲平
3、模具本身是否偏差; 4、黄光区线路对位是否偏 差; 5、钻孔是否偏差;
判 定:OK
判 定:NG
缺 陷
二钻 改善方向 1、二钻前是否进比例缩 放;
缺 陷
二钻 改善方向 1、二钻前是否进比例缩 放;
名 称
孔偏
2、主轴是否存在偏移; 3、程序是否本身偏移; 4、包板松紧度、固定方式 、坐标设置是否合理;
名 称
孔偏
2、主轴是否存在偏移; 3、程序是否本身偏移; 4、包板松紧度、固定方式 、坐标设置是否合理;
改善方向 缺
改善方向
陷
陷
1、冲孔定位孔是否偏移;
1、冲孔定位孔是否偏移;
名 称
到铜
2、模具是否本身偏差; 3、套孔方式是否正确;
名 称
到铜
2、模具是否本身偏差; 3、套孔方式是否正确;
判 定:NG
判 定:NG
缺
改善方向 缺
改善方向
陷 名 称
残胶
陷
1、擦胶重工后残胶是否清
洁干净;
名
称 2、PSA是否有指定重工区;
改善方向
陷
陷 1、模具刀口是否钝化;
2、模具合模时凹凸口边缘
1、模具刀口是否钝化; 2、模具合模时凹凸口边缘
名 称
毛边
是否间隙太大; 3、模具刀口是否存在缺
名
称 口;
4、是否采用多张叠加作业
毛边
是否间隙太大; 3、模具刀口是否存在缺 口; 4、是否采用多张叠加作业
判 定:OK
判 定:NG
裁切 裁切 缺
名 称
贴偏
1、操作者是否认真仔细; 2、DOME是否本身尺寸偏小
判 定:OK
判 定:NG
缺 陷
引线 改善方向 缺 陷 1、钻孔程序是否多增设了 孔;
引线 改善方向 1、钻孔程序是否多增设了 孔;
名 称
断裂
2、是否设计不合理,引线 太小易断裂; 3、取放板方式是否合理, 避免折断;
名 称
断裂
2、是否设计不合理,引线 太小易断裂; 3、取放板方式是否合理, 避免折断;
4、黄光区线路对位是否偏
差; 5、钻孔是否偏差;
称
冲开
3、模具本身是否偏差; 4、黄光区线路对位是否偏 差; 5、钻孔是否偏差;
判 定:OK
判 定:NG
缺
改善方向 缺
改善方向
陷 名
压痕
1、冲切时模具表面之废料 是否及时清洁; 2、板材表面是否附着废
陷 名
压痕
1、冲切时模具表面之废料 是否及时清洁; 2、板材表面是否附着废
换;
2、压力是否偏大或不稳 定;
名
称 3、是否多张叠加一冲;
4、刀口内是否存在填充物
PSA 缺损
改善方向
1、模具刀口是否往内变 形;
判 定:OK
判 定:NG
缺 陷
补强 改善方向 缺 陷 1、PET盖板是否长时间未更 换;
补强
改善方向
1、PET盖板是否长时间未更 换;
名 称
压痕
2、压力是否偏大或不稳 定; 3、是否多张叠加一冲; 4、刀口内是否存在填充物
缺
改善方向 缺
改善方向
陷 名
异物
1、产品是否清洗干净; 2、白光区贴合时是否自检 待贴板;
陷 名
异物
1、产品是否清洗干净; 2、白光区贴合时是否自检 待贴板;
称
3、白光区贴合时是否清洗 板面、台面;
称
3、白光区贴合时是否清洗 板面、台面;
判 定:NG
判 定:NG
缺
改善方向 缺
改善方向
陷 名
异物
1、产品是否清洗干净; 2、白光区贴合时是否自检 待贴板;
称
3、模具冲针是否断裂;
判 定:NG
判 定:NG
缺 陷 名 称
溢胶
改善方向
1、压合参数是否最佳; 2、接著剂本身是否有变 异; 3、是否选材厚度搭配不合 理;
保护膜 缺
改善方向
陷
1、操作者是否认真仔细;
2、保护膜开窗是否本身偏
名 称
贴偏
小; 4、保护膜开窗是否偏移; 5、板材是否存在涨缩;
判 定:OK
缺 陷
PSA
改善方向 缺 陷 1、操作者贴合时是否认真
PSA
改善方向
1、操作者贴合时是否认真
名 称
贴偏
仔细; 2、贴合好后赶压方式是否 合理;
名 称
贴偏
仔细; 2、贴合好后赶压方式是否 合理;
判 定:OK
判 定:NG
缺
改善方向 缺
改善方向
陷 名
冲偏
1、是否多张叠加冲切套孔 未套到底; 2、裁切机上模块快速移动 过程中是否就已按键;
名 称
压痕
2、压力是否偏大或不稳 定; 3、是否多张叠加一冲; 4、刀口内是否存在填充物
偏离标 记线
判 定:NG
判 定:NG
补强 PSA 缺
改善方向 缺
改善方向
陷
陷
名 称
1、操作者是否认真仔细;
贴偏 2、补强本身尺寸存在偏 差;
名 称
贴偏
1、操作者是否认真仔细; 2、PSA本身尺寸存在偏差;
判 定:NG
判 定:NG
补强 补强 缺
改善方向 缺
改善方向
陷
陷
名 称
毛刺
1、是否采用二次冲切; 2、压力是否调至最佳;
名 称
毛刺
1、是否采用二次冲切; 2、压力是否调至最佳;
判 定:NG
判 定:NG
缺 陷
冲孔 改善方向 1、冲头是否校准验证;
缺 陷
冲孔 改善方向 1、冲头是否校准验证;
名 称
偏移
2、机器是否存在故障; 3、操作者推、取方式是否 合理;
称
3、白光区贴合时是否清洗 板面、台面;
判 定:NG
保护膜 缺
改善方向 缺
陷
陷
名 称
贴偏
名 1、操作者是否认真仔细;
2、钻孔是否钻偏
称
判 定:NG
钻孔 改善方向
偏移
1、操作者是否认真仔细; 2、钻孔是否钻偏
判 定:NG
判 定:NG
判 定:NG
判 定:NG
缺 陷
元件 改善方向 1、模具避位形状是否全 理;
缺 陷
元件 改善方向 1、模具避位形状是否全 理;
名 称
压坏
2、模具避位的深浅、大小 是否合理; 3、凹槽内填充物是否合 理;
名 称
压坏
2、模具避位的深浅、大小 是否合理; 3、凹槽内填充物是否合 理;
判 定:OK
判 定:NG
称
理;
称
理;
判 定:OK
判 定:NG
缺
改善方向 缺
改善方向
陷 名
针痕
1、探针弹力是否最佳; 2、合模速度是否最佳;
陷 名
针痕
1、探针弹力是否最佳; 2、合模速度是否最佳;
称
3、治具设计是否合理;
称
3、治具设计是否合理;
判 定:OK
判 定:NG
缺
改善方向 缺
改善方向
陷 名
变色
1、板面是否清洗烘干; 2、清洗烘干后是否受潮或
判 定:OK
判 定:NG
缺
改善方向 缺
改善方向
陷 名
压痕
1、板材本身来料是否存 在; 2、堆放板材之台面是否不 干净;
陷 名
压痕
1、板材本身来料是否存 在; 2、堆放板材之台面是否不 干净;
称
称 3、板材与板材之间是否存
在异物;
3、板材与板材之间是否存 在异物;
判 定:OK
判 定:NG
保护膜 保护膜 缺
称
孔粗 糙
改善方向
1、钻针品质是否存在变 异; 2、叠板是否存在不紧; 3、主轴是否存在偏差; 4、钻孔参数是否最佳;
判 定:NG
判 定:NG
缺
改善方向 缺
改善方向
陷 名
孔堵
1、模具冲针是否没有; 2、模具冲针是否太短;
陷 名
孔堵
1、模具冲针是否没有; 2、模具冲针是否太短;
称
3、模具冲针是否断裂;
判 定:OK
判 定:NG
缺 陷
二钻 改善方向 1、二钻前是否进比例缩 放;
缺 陷
二钻 改善方向 1、二钻前是否进比例缩 放;
名 称
孔偏
2、主轴是否存在偏移; 3、程序是否本身偏移; 4、包板松紧度、固定方式 、坐标设置是否合理;
名 称
孔偏
2、主轴是否存在偏移; 3、程序是否本身偏移; 4、包板松紧度、固定方式 、坐标设置是否合理;
陷 名
毛边
1、模具刀口是否钝化; 2、模具合模时凹凸口边缘 是否间隙太大;
陷 名
毛边
1、模具刀口是否钝化; 2、模具合模时凹凸口边缘 是否间隙太大;
称
3、模具刀口是否存在缺 口;
称
3、模具刀口是否存在缺 口;
判 定:NG
判 定:NG
缺
改善方向 缺
改善方向
陷 名
气泡
1、压合参数是否最佳; 2、接著剂是否本身存在变 异;