航空发动机整体叶轮五轴数控加工机床运动学分析
航空发动机精锻叶片数字化数控加工技术
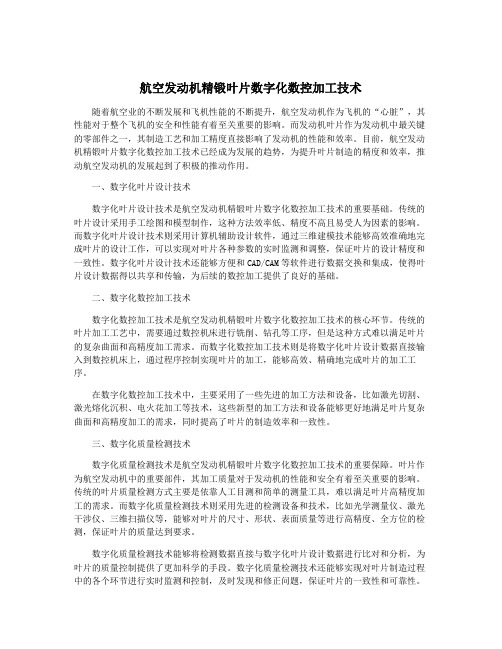
航空发动机精锻叶片数字化数控加工技术随着航空业的不断发展和飞机性能的不断提升,航空发动机作为飞机的“心脏”,其性能对于整个飞机的安全和性能有着至关重要的影响。
而发动机叶片作为发动机中最关键的零部件之一,其制造工艺和加工精度直接影响了发动机的性能和效率。
目前,航空发动机精锻叶片数字化数控加工技术已经成为发展的趋势,为提升叶片制造的精度和效率,推动航空发动机的发展起到了积极的推动作用。
一、数字化叶片设计技术数字化叶片设计技术是航空发动机精锻叶片数字化数控加工技术的重要基础。
传统的叶片设计采用手工绘图和模型制作,这种方法效率低、精度不高且易受人为因素的影响。
而数字化叶片设计技术则采用计算机辅助设计软件,通过三维建模技术能够高效准确地完成叶片的设计工作,可以实现对叶片各种参数的实时监测和调整,保证叶片的设计精度和一致性。
数字化叶片设计技术还能够方便和CAD/CAM等软件进行数据交换和集成,使得叶片设计数据得以共享和传输,为后续的数控加工提供了良好的基础。
二、数字化数控加工技术数字化数控加工技术是航空发动机精锻叶片数字化数控加工技术的核心环节。
传统的叶片加工工艺中,需要通过数控机床进行铣削、钻孔等工序,但是这种方式难以满足叶片的复杂曲面和高精度加工需求。
而数字化数控加工技术则是将数字化叶片设计数据直接输入到数控机床上,通过程序控制实现叶片的加工,能够高效、精确地完成叶片的加工工序。
在数字化数控加工技术中,主要采用了一些先进的加工方法和设备,比如激光切割、激光熔化沉积、电火花加工等技术,这些新型的加工方法和设备能够更好地满足叶片复杂曲面和高精度加工的需求,同时提高了叶片的制造效率和一致性。
三、数字化质量检测技术数字化质量检测技术是航空发动机精锻叶片数字化数控加工技术的重要保障。
叶片作为航空发动机中的重要部件,其加工质量对于发动机的性能和安全有着至关重要的影响。
传统的叶片质量检测方式主要是依靠人工目测和简单的测量工具,难以满足叶片高精度加工的需求。
基于POWERMILL的航空整体叶轮五轴数控加工研究

a Ce r t a i n I n t e g r a l Av i a t i o n I mp e l l e r
C AO Z h u - mi n g ,W ANG L i u - f e i ,Z HU Yu , J I We n — l o n g ( 1 . B e i j i n g P o l y t e c h n i c , B e i j i n g 1 0 0 1 7 6 , C h i n a ; 2 . B e i h a n g U n i v e r s i t y , B e i j i n g 1 0 0 0 8 3 , C h i n a )
第 8期 2 0 1 5年 8月
机 械 设 计 与 制 造
Ma c h i n e r y De s i g n & Ma n u f a c t u r e 2 5 3
基于P O WE R MI L L的航 空整 体 叶轮 五 轴数控 加 工研 究
曹著明, 王刘菲 , 朱 熵, 纪文龙
题 。
关键词 : 航空整体叶轮; 五轴加工 ; 关键技术 ; 研究 ; 刀位轨迹 ; 工艺工装
中图分类号 : T H1 6 ; T G 6 5 9 文献标识码 : A 文章编号 : 1 0 0 1 — 3 9 9 7 ( 2 0 1 5 ) 0 8 — 0 2 5 3 — 0 3
K e y T e c h n o l o g i e s Re s e a r c h o n t h e 5 - Ax i s Ma c h i n i n g o f
( 1 . 北京电子科技职业学院 , 北京 1 0 0 1 7 6 ; 2 . 北京航空航天大学 , 北京 1 0 0 0 8 3 )
整体叶轮五轴数控加工技术的研究

关 键词 : 叶轮
三 维建模
五轴 加 工 加 工仿真 后 置处 理 文献标 识码 : B
中图分 类号 : T G6 1 + 9
S t u d y o n t h e f i v e - a x i s NC ma c h i n i n g t e c h n o l o g y f o r i n t e g r a l i mp e l l e r
—
ห้องสมุดไป่ตู้
a x i s NC ma c h i n e .Wi t h t h e h e l p o f UG s o f t wa r e, a u t o ma t i c p r o g r a mmi n g a n d t o o l p a t h we r e c a r r i e d
工艺与检测 T e c h n 0 I o g v a n d T e s t
整体 叶轮 五轴 数 控 加 工技 术 的研 究
丁 刚强
( 柳 州五菱 汽车 工业有 限公 司制造 工程部 , 广西 柳州 5 4 5 0 0 7 )
摘 要: 整体 叶轮是 典型 的航 空航 天 复杂 零件 。为 了进行 整体 叶轮 的数 控 加 工 , 用P r o / E对 其进 行 了参 数 化建模 。在 深入 分析整 体 叶轮加 工工艺 的基础 上 , 确 定 了五轴数 控机 床加 工叶轮 的工艺流 程 。使用 U G 软件 实现 了 自动编程 , 生成 了刀 路轨迹 。通 过后置 处 理生 成 G 代 码 , 并在 实 际机 床上 进 行 了加
c e s s i n g
整体 叶轮是 燃气 发 动 机 中 的一 种 关键 零 件 , 其 作 用是 南外 界供 给的机 械功连 续不 断地将 气体 压缩并 传 输 出去 。气体 经进 气管 进 人 工作 轮 , 在 工 作 轮 中 因受 到 叶片 的作用力 而 压 力 升高 , 速 度 增 加 。因 此对 叶轮
整体叶轮五轴数控加工的研究
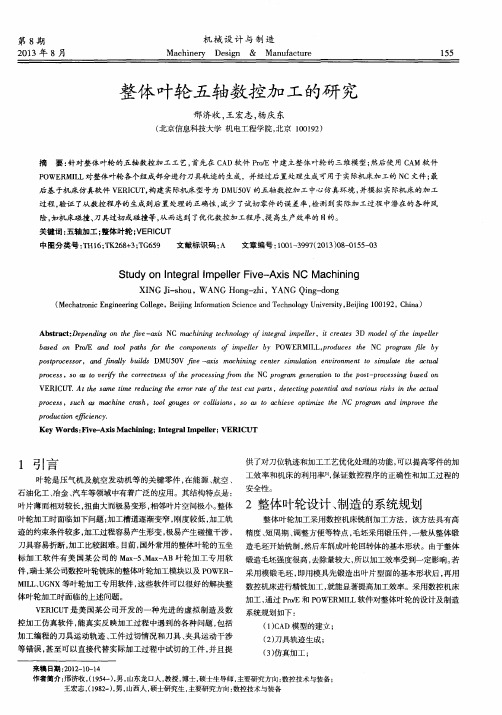
Ab s t r a c t : D e p e n d i n g o n t h e i f v e - a x i s N C ma c h i n i n g t e c h n o l o g y o f i n t e g r a l i m p e l l e r ,i t c r e a t e s 3 D m o d e l o f t h e i m p e l l e r b a s e d o n P r o / E a n d t o o l p t a h s f o r t h e c o m p o n e n t s o f i m p e l l e r b y P O WE R MI L L , p r o d u c e s t h e N C p r o ra g m il f e b y p o s t p r o c e s s o r ,a n d in f a l l y b u i l & D M U 5 0 V iv f e- xi a s ma ch i n i n g c e n t e r s i m u l a t i o n e n v i r o n m e n t t o s i mu l te a t h e ct a u l a p r o c e s s , S O s a t o v e r i f y t h e c o r r e c t n e s s o f t h e p r o c e s s i n g f r o m t h e N C p r o ra g m g e n e r a t i o n t o t h e p o s t - p r o c e s s i n g b a s e d o n
后基 于机床仿真软件 V E R I C U T , 构建 实际机床 型号为 D MU 5 0 V的五轴数控加工 中心仿真环境 , 并模拟 实际机床 的加 工 过程 , 验证 了从数控程序 的生成到后置处理 的正确性 , 减 少了试切 零件 的误 差率, 检 测到实际加 工过程 中潜在 的各种风 险, 如机床碰撞 、 刀具过切或碰撞等 , 从而达到 了优化数控加工程序、 提 高生产效率的 目的。 关键词 : 五轴J j  ̄ - r ; 整体叶轮 ; VE R I CU T
航空发动机精锻叶片数字化数控加工技术
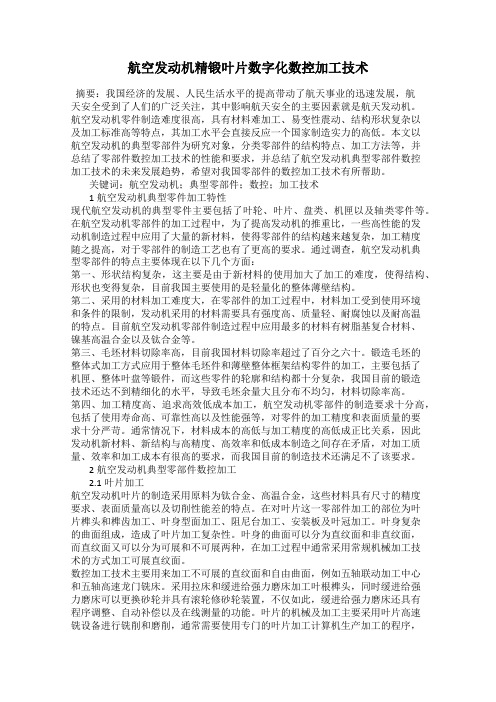
航空发动机精锻叶片数字化数控加工技术摘要:我国经济的发展、人民生活水平的提高带动了航天事业的迅速发展,航天安全受到了人们的广泛关注,其中影响航天安全的主要因素就是航天发动机。
航空发动机零件制造难度很高,具有材料难加工、易变性震动、结构形状复杂以及加工标准高等特点,其加工水平会直接反应一个国家制造实力的高低。
本文以航空发动机的典型零部件为研究对象,分类零部件的结构特点、加工方法等,并总结了零部件数控加工技术的性能和要求,并总结了航空发动机典型零部件数控加工技术的未来发展趋势,希望对我国零部件的数控加工技术有所帮助。
关键词:航空发动机;典型零部件;数控;加工技术1航空发动机典型零件加工特性现代航空发动机的典型零件主要包括了叶轮、叶片、盘类、机匣以及轴类零件等。
在航空发动机零部件的加工过程中,为了提高发动机的推重比,一些高性能的发动机制造过程中应用了大量的新材料,使得零部件的结构越来越复杂,加工精度随之提高,对于零部件的制造工艺也有了更高的要求。
通过调查,航空发动机典型零部件的特点主要体现在以下几个方面:第一、形状结构复杂,这主要是由于新材料的使用加大了加工的难度,使得结构、形状也变得复杂,目前我国主要使用的是轻量化的整体薄壁结构。
第二、采用的材料加工难度大,在零部件的加工过程中,材料加工受到使用环境和条件的限制,发动机采用的材料需要具有强度高、质量轻、耐腐蚀以及耐高温的特点。
目前航空发动机零部件制造过程中应用最多的材料有树脂基复合材料、镍基高温合金以及钛合金等。
第三、毛坯材料切除率高,目前我国材料切除率超过了百分之六十。
锻造毛坯的整体式加工方式应用于整体毛坯件和薄壁整体框架结构零件的加工,主要包括了机匣、整体叶盘等锻件,而这些零件的轮廓和结构都十分复杂,我国目前的锻造技术还达不到精细化的水平,导致毛坯余量大且分布不均匀,材料切除率高。
第四、加工精度高、追求高效低成本加工,航空发动机零部件的制造要求十分高,包括了使用寿命高、可靠性高以及性能强等,对零件的加工精度和表面质量的要求十分严苛。
数控机床在航空发动机加工中的应用

数控机床在航空发动机加工中的应用航空发动机作为飞行器的核心动力装置,对其性能和可靠性要求极高。
在航空发动机的制造过程中,数控机床扮演着至关重要的角色。
本文将探讨数控机床在航空发动机加工中的应用,并分析其优势和挑战。
一、航空发动机加工的需求航空发动机具有复杂的结构和高精度的加工要求。
其零部件通常由高强度合金材料制成,需要进行精确的切削和加工。
常见的航空发动机零部件包括涡轮盘、叶片、缸套等。
这些零部件的制造要求高精度、高效率、高可靠性。
二、数控机床在航空发动机加工中的优势1. 高精度加工:数控机床采用数字化的控制系统,可以实现高精度的切削和加工,保证零部件的准确尺寸和光洁度。
这对于航空发动机的性能和可靠性至关重要。
2. 复杂零部件加工:航空发动机的零部件通常具有复杂的形状和结构。
数控机床具有多轴控制和多功能加工的能力,可以制造出各种复杂的零部件,如曲线叶片和复杂腔体,满足航空发动机的设计要求。
3. 高效率生产:数控机床具有高速切削和快速移动的能力,可以大幅提高生产效率。
在航空发动机的大规模制造中,数控机床能够快速完成大批量的零部件加工,节约时间和成本。
4. 自动化加工:数控机床可通过预先编程实现自动化加工过程,减少人工操作和干预,提高生产的一致性和稳定性。
这对于航空发动机的质量控制和工艺稳定性非常重要。
三、数控机床在航空发动机加工中面临的挑战1. 加工工艺的优化:数控机床的应用需要与先进的加工工艺相结合,以提高加工效率和零部件质量。
需要深入研究航空发动机加工过程中的各种技术和方法,进行工艺的优化和改进。
2. 精确度和可靠性的要求:航空发动机零部件的加工需要达到极高的精确度和可靠性要求。
数控机床的性能和稳定性对加工质量有直接影响,需要不断改进和提高数控机床的精度和可靠性。
3. 人才培养和技术创新:数控机床的应用需要人才掌握相应的操作和编程技能。
航空发动机加工领域需要培养一批专业的数控机床操作人员和技术创新人才,推动技术的发展和创新。
航空发动机整体叶轮五轴数控加工机床运动学分析

A b s t r a c t : Ai mi n g p  ̄ n b ? e m s o fo v e r ll a b l i s k p o r t s y o r a i r c r ft o e n g i l l  ̄ e s 5 一 d f x i s C N C m a c h i n i n g . t h e k i n e m a t i c s s t r u c t u r e s o f5 -
机 械 设 计 与 制 造
1 4 8 Ma c h i n e r y De s i g n & Ma n u f a c t ur e
第 6期
2 0 1 3年 6月
航 空发动机整体 叶轮五轴数控加 工机床运动 学 中国轻 型燃气轮机开发中心 , 北京 1 0 0 0 2 8 ; 2 . 北京航空航天大学 机械工程及 自动化学院, 北京 1 0 0 1 9 1 ;
ma ch i n i n g p r e s e n t e d .
工整体叶轮的结构特点 ,对最适用五轴加工机床的选择 的思路 ,并就整体叶轮 构型与五轴加 工机床选择进行 了定性分
析。
关键词 : 整体叶轮 ; 五轴加工 ; 运动学模型
中图分类号 : T H1 6 ; V 2 6 3 ; T G 6 5 9 文献 标 识 码 : A 文章编号 : 1 0 0 1 — 3 9 9 7 ( 2 0 1 3 ) 0 6 — 0 1 4 8 — 0 4
a x i s C N C m ch a i n e t o o l s e e l ss a ! . i f e d . P r r z t i c a l " e — - n x C N C m a c h i n e t o o l s c a l l b e u s e d f o r t h e 5 - a x i s N C m a c h i n i n g o f b l i s k ma ch i n i n g , w h i c h d i v i d e d i n t o 5 - a x i s w i t h d u a l r o t a r y h e a d s t y p e fs o t r u c t u r e , 5 - a x i s w i t h d u a l r o t a r y t a b l e s t y p e f o
五轴加工中心的动力学分析

摘要数控铣床日益向高速度、高精度和高刚度的方向发展,其机构日趋复杂,对其工作性能的要求越来越高。
而发达国家在进出口技术含量高的五轴联动加工中心方面,对我国进行限制。
所以,我国就必须自主开发。
虚拟制造技术的发展应用,为开发研究高技术数控机床产品提供了技术手段。
本科题的主要任务是在设计阶段采用有限元法完成基础件(底座、工作台、滑枕、立柱)及整机的虚拟动力学分析。
其虚拟动力学研究包含两个方面:固有振动特性分析和响应特性分析。
对基础件(底座、工作台、滑枕、立柱)及整机进行了固有振动特性分析,得出了相应的固有频率和振型,通过振型的动画显示,形象而逼真地描述各模态的振动过程。
对滑枕进行了响应特性分析,得出了主轴在工作转速下的响应位移,并绘出了主轴在一系列频率下的响应位移对频率的曲线。
本课题的研究,为设计高性能的基础件(底座、工作台、滑枕、立柱)及整机提供了可靠的理论依据,缩短了产品的开发周期,降低了开发成本,其中的分析方法易于推广到其它各类机床的开发研究中,故本课题的研究方法及结论具有广泛的工程意义。
ABSTRACTThe milling machine is developing towards high speed, high precision and high rigidity, its organization is becoming more complex, the need of its work performance is becoming more. For the developed countries restrict our country in importing the NC machine with 5-axes linkage, we should do it by ourself. The development and appliance of the VMT provide the technical measurement in exploiting the NC machine tool of the high technology. The main task of this study is the accomplishment of the virtual dynamics of the basic parts including worktable、base、slider and the whole machine by means of the finite element analysis. The virtual dynamics research include two sides: the analysis ofthe inherent libration speciality and the analysis of the response speciality.The analysis of the inherent libration speciality of the worktable、base、slider and the whole machine oth the system is done to get the relevant inherent frequencies and the librating models. The moving show of the librating models describes the vibrating process of several modes.The analysis of the slider is done on the slider, the response displacement of the working speed is gotten. The curve of the response displacement and the frequency is drawn.The virtual dynamics research is done in this thesis, to shorten the exploiting period of the product, and to reduce the exploiting cost. The reliable theory is provided to design the worktable、base、slider and the whole machine performance. The way is easy to extend to the research of the other machine tools. So the way and the conclusion is of abroad engineer meaning.1.1 课题研究的来源和技术背景本课题的主要任务是对五轴加工中心的动力学分析(固有振动特性分析和响应特性分析)。
五轴加工中心原理

五轴加工中心原理
五轴加工中心是一种先进的数控机床,它的原理是通过同时控制五个方向的运动,即X轴、Y轴、Z轴和两个旋转轴(A轴
和C轴),来实现对复杂工件的加工。
在加工过程中,工件被夹持在工作台上,并通过刀具来切削和加工。
通过控制X、Y、Z轴的运动,可以实现工件在平面内
的移动和上下移动。
同时,通过控制A轴和C轴的旋转,可
以使工件在不同方向上进行旋转。
通过这五个方向的联合运动,五轴加工中心可以灵活地切削工件的任意曲面。
五轴加工中心利用数控系统来控制各个轴的运动。
数控系统根据预先编好的加工程序,通过计算机控制各个轴的步进电机或伺服电机的运动,从而实现对工件加工的控制。
同时,数控系统还可以通过传感器对加工过程中的刀具位置进行实时监测,确保加工的精度和质量。
五轴加工中心的运动精度和稳定性对加工质量有着重要影响。
为了保证五轴加工中心的高精度加工,机床结构和传动系统需要具备足够的刚性和稳定性。
同时,对于数控系统的控制算法和参数调节也需要精心设计,以确保刀具的轨迹和工件表面的加工精度。
总之,五轴加工中心通过同时控制五个方向的运动,可以实现对复杂曲面工件的高精度加工。
这种机床在航空航天、汽车制造、模具制造等领域有着广泛的应用前景,对提高加工效率和产品质量具有重要意义。
整体叶轮5轴数控加工工艺仿真技术研究

整体叶轮5轴数控加工工艺仿真技术研究*夏雨(浙江工商职业技术学院机电工程学院,浙江宁波315012)【摘要】分析了整体叶轮的造型轮廓和加工特点,依据叶轮的整体形状和加工工艺技术要求,确定了基于UG NX 软件的5轴加工策略,生成刀路轨迹,并完成整体叶轮零件的数控仿真的加工。
结果表明:经过加工工艺的优化,通过在5轴加工中心加工整体叶轮,零件的表面质量和加工效率得到全面提升,对叶轮类零件的加工有一定借鉴的意义。
关键词:整体叶轮;5轴加工;UG NX ;加工工艺;仿真技术中图分类号:TG659文献标识码:BDOI :10.12147/ki.1671-3508.2023.02.014Study on the Simulation Technology of5-Axis CNC Machining Process of Integral ImpellerXia Yu(College of Mechanical and Electrical Engineering,Zhejiang Bussiness and Technology Institute,Ningbo ,Zhejiang 315012,CHN )【Abstract 】The modeling contour and processing characteristics of the integral impeller are analyzed.Based on the overall shape of the impeller and the technical requirements of the machining process,the 5-axis machining strategy based on UG NX software is determined,the toolpath trajectory is generated,and the machining of the integral impeller part with CNC simulation is completed.The results show that after the optimization of the machining process,the surface quality and machining efficiency of the parts are comprehensively improved by machining the integral impeller in the 5-axis machining center,which has certain significance for the machining of impeller-type parts.Key words :integral impeller ;5-axis machining ;UG NX ;machining process ;simulationtechnology*基金项目:浙江省教育厅访问工程师项目:手机马达整盘治具数控加工技术研究(编号:FG2022085);浙江工商职业技术学院2021年学校科研年度项目“整体叶轮叶片多轴铣削加工技术研究”(编号:KYND202108)1引言整体叶轮零件在航空航天、汽车工业、冶金石油工业里有广泛的应用,作为机械结构零件的核心部件之一,其特点是结构复杂,加工困难和应用范围广,同时对整体叶轮的加工质量和加工精度要求较高,整体叶轮的曲面形状复杂,优化的加工工艺一直是制造业重要研究方向,因此,本文主要讨论经过优化的加工工艺能提升整体叶轮的加工质量,提高加工效率,并能广泛应用到各个场合[1]。
整体叶轮五轴数控技术的研究

整体叶轮五轴数控技术的研究整体叶轮是典型的航空航天复杂零件。
为了进行整体叶轮的数控加工,用Pro/E对其进行了参数化建模。
在深入分析整体叶轮加工工艺的基础上,确定了五轴数控机床加工叶轮的工艺流程。
使用UG软件实现了自动编程,生成了刀路轨迹。
通过后置处理生成G代码。
并在实际机床上进行了加工验证。
整体叶轮是燃气发动机中的一种关键零件,其作用是由外界供给的机械功连续不断地将气体压缩并传输出去。
气体经进气管进入工作轮,在工作轮中因受到叶片的作用力而压力升高,速度增加。
因此对叶轮的要求:一是气体流过叶轮的损失要小,即气体流经叶轮的效率要高;二是叶轮型式能使整机性能曲线的稳定工况区及高效区范围较宽。
好的外形构造是发挥叶轮性能的保证。
在设计过程巾,叶片的数量和外形轮廓需要经过多次的修改,配合发动机试车后的性能优化得以确定。
整体叶轮的加工一直是机加工中长期困扰我们的难题。
在叶片之间有大量的材料需要去除。
为了使叶轮满足气动性的要求,叶片常采用大扭角、根部变圆角的结构,这都给叶轮的加工提出了较高的要求。
普通的叶轮加工往往采用铸造成形,然后再机械加工成形;或者叶片单独加工,然后将叶片与轮毂焊接,再通过打磨、抛光使之外观平滑。
这些方法的技术含量低,做出来的叶轮曲面精度难以保证,表面的质量也差,严重影响了叶轮的使用性能。
近几年随着多轴联动数控技术的发展,使得加工整体叶轮类零件成为可能。
由于整体叶轮的结构造型的复杂性,其数控加工技术一直是制造业的难点,也是研究的热点。
为了解决该问题,本文从以下几个方面展开研究:用Pro/E对其进行了参数化建模;整体叶轮加工工艺的分析与设计,制定五轴数控机床加工叶轮的工艺流程;使用UG软件实现了自动编程,生成了刀路轨迹;通过后置处理生成G代码;通过实际机床加工进行验证。
1 叶轮的参数化建模叶轮是典型航空航天复杂零件,具有重大的应用意义。
由于叶片的曲线和曲面形状比较复杂,本文利用Pro/Engineer软件进行参数化建模,并完成其三维设计。
浅谈整体叶轮五轴数控加工技术 刘辉
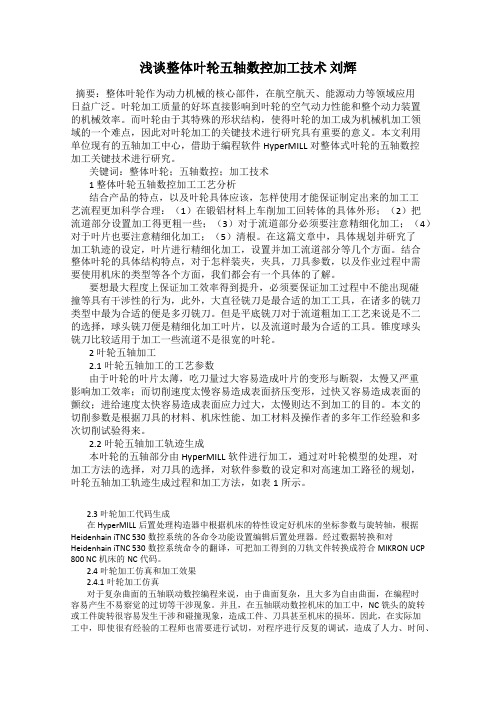
浅谈整体叶轮五轴数控加工技术刘辉摘要:整体叶轮作为动力机械的核心部件,在航空航天、能源动力等领域应用日益广泛。
叶轮加工质量的好坏直接影响到叶轮的空气动力性能和整个动力装置的机械效率。
而叶轮由于其特殊的形状结构,使得叶轮的加工成为机械机加工领域的一个难点,因此对叶轮加工的关键技术进行研究具有重要的意义。
本文利用单位现有的五轴加工中心,借助于编程软件HyperMILL对整体式叶轮的五轴数控加工关键技术进行研究。
关键词:整体叶轮;五轴数控;加工技术1 整体叶轮五轴数控加工工艺分析结合产品的特点,以及叶轮具体应该,怎样使用才能保证制定出来的加工工艺流程更加科学合理:(1)在锻铝材料上车削加工回转体的具体外形;(2)把流道部分设置加工得更粗一些;(3)对于流道部分必须要注意精细化加工;(4)对于叶片也要注意精细化加工;(5)清根。
在这篇文章中,具体规划并研究了加工轨迹的设定,叶片进行精细化加工,设置并加工流道部分等几个方面。
结合整体叶轮的具体结构特点,对于怎样装夹,夹具,刀具参数,以及作业过程中需要使用机床的类型等各个方面,我们都会有一个具体的了解。
要想最大程度上保证加工效率得到提升,必须要保证加工过程中不能出现碰撞等具有干涉性的行为,此外,大直径铣刀是最合适的加工工具,在诸多的铣刀类型中最为合适的便是多刃铣刀。
但是平底铣刀对于流道粗加工工艺来说是不二的选择,球头铣刀便是精细化加工叶片,以及流道时最为合适的工具。
锥度球头铣刀比较适用于加工一些流道不是很宽的叶轮。
2 叶轮五轴加工2.1叶轮五轴加工的工艺参数由于叶轮的叶片太薄,吃刀量过大容易造成叶片的变形与断裂,太慢又严重影响加工效率;而切削速度太慢容易造成表面挤压变形,过快又容易造成表面的颤纹;进给速度太快容易造成表面应力过大,太慢则达不到加工的目的。
本文的切削参数是根据刀具的材料、机床性能、加工材料及操作者的多年工作经验和多次切削试验得来。
2.2叶轮五轴加工轨迹生成本叶轮的五轴部分由HyperMILL软件进行加工,通过对叶轮模型的处理,对加工方法的选择,对刀具的选择,对软件参数的设定和对高速加工路径的规划,叶轮五轴加工轨迹生成过程和加工方法,如表1所示。
基于五轴联动加工技术的叶轮加工方法分析

DOI:10.19392/j.cnki.1671 7341.202019120基于五轴联动加工技术的叶轮加工方法分析钟国成桂林航天工业学院 广西桂林 541000摘 要:叶轮是动力机械中不可缺少的重要部件,已经被广泛应用于汽车制造、航空航天等多个领域。
由于叶轮本身的结构复杂性较强,应用传统加工技术困难性大,性价比不高。
五轴联动加工技术可有效避免刀具干涉,提升表面质量,增强加工精度,性价比高,目前已经逐渐取代传统加工技术。
本文主要讨论了基于五轴联动加工技术的叶轮加工思路与具体加工方法,以供参考。
关键词:五轴联动加工技术;叶轮加工;方法 所谓五轴联动加工技术,简单来说就是一种在CNC控制下五个坐标轴协调运动加工零件的加工技术,它以计算机网络技术作为主要的技术支撑。
随着加工技术的持续发展,虚拟仿真技术逐渐被应用于五轴联动加工中,给后者加工质量与精度的提升产生了重大的积极影响。
基于五轴联动加工技术加工叶轮,为避免刀具干涉、碰撞,先在仿真环境中构建叶轮模型,经多次试验后确定切削参数,并对其进行验证,再将参数录入五轴联动数控机床,叶轮一次成型。
这不仅能提升叶轮加工质量与精度,也能减少加工叶轮的必要时间,同时做到资源的有效节约。
那么,基于五轴联动加工技术的叶轮加工具体方法是什么样的呢?以下就是笔者对此的分析与论述。
一、基于五轴联动加工技术的叶轮加工思路(一)工艺流程叶轮加工主要是加工叶片与流道,由于叶片通常为扭曲状,而流道则很狭窄,所以加工中常有干涉、过切、碰刀现象。
为了实现对这些现象的有效规避,并保证加工精度,选择分阶段济钢。
第一阶段,叶片、流道粗加工,主要采用五轴曲线加工法,对于流道,先进行结构分割后再加工;第二阶段,叶片精加工与清根处理,主要采用五轴侧铣方式;第三阶段,流道精加工,主要采用五轴限制面加工法。
(二)五轴加工刀具路径规划(1)粗加工刀具。
第一阶段粗加工从流道深度延伸的方向进行分层加工,合理连接每层的刀具路径,使之构成整体加工路径。
三元整体叶轮五轴数控加工

1.5 目标及特色
目标: (1)完成整体叶轮刀具轨迹生成工艺分析 (2)完成基于 UGNX4.0 整体叶轮叶片的刀具路径生成 (3)完成整体叶轮叶片加工的刀具干涉与刀位修正 特色:利用UG软件对三元整体叶轮进行仿真设计,得到叶轮主要部分的NC程序, 并对其刀具轨迹进行规划。
4
2 自由曲面的五坐标数控加工研究
5
这种结构类型是指两个转动轴都作用于刀具上, 由刀具绕两个互相正交的轴 转动以使刀具能指向空间任意方向。由于运动是顺序传递的,因而在两个转动轴 中,有一个的轴线方向在运动过程中始终不变,成为定轴,而另一个的轴线方向 则是随着定轴的运动而变化,成为动轴(动轴紧靠刀具)。对于定、动轴的配置, 理论上存在A-B, A-C, B-C, B-A, C-A和C-B等六种组合情况。但由于在A-C, B-C 的情况下动轴轴线与刀具轴线平行而没有意义,因此定、动轴的运动配置主要是 A-B, B-A, C-A和C-B等四种,这类机床的主要特点是摆动机构结构较复杂,一般 刚性较差,但其运动灵活,机床使用操作(如装卡工件)较方便。 (2)工作台回转/摆动型 这种结构类型是指两个转动轴都作用于工件上,根据运动的相对性原理,它 与由刀具摆动产生的效果在本质上是一样的。这种结构也是定、动轴结构,只是 其动轴紧靠工件。对于其定、动轴的配置,理论上也有A,-B',A ,-C', B ’-C'、 B’-A',C’-A’和C’-B’等六种组合情况。但由于此时的定轴到刀具间只存在 平动,因而选C’轴作为定轴将不能改变刀具轴线的方向而失去意义,因此该类 型的定、动轴的运动配置分类是A’-B'、A,一C',B ’-C', B ’-A'等四种,而 且A,-B', A '-C', B ’-C', B ’-A’实质上也可看成是等效的结构(初始状态 不同)。 这类机床的主要特点是其旋转/摆动工作台刚性容易保证、 工艺范围较广, 而且容易实现。 但由于工件要随工作台在空间摆动,因此这种结构主要适合于中 小规格的机床用于加工体积不大的零件。 (3)刀具与工作台回转/摆动型 这种结构类型是指刀具与工件各具有一个转动运动。这种结构不是定、动轴 结构,两个回转轴在空间的方向都是固定的。对于其两个转动轴的配置情况,若 按先后工件后刀具的顺序,则理论上也有A,-B', A’-C', B’-C', B’-A' 、C’ -A,和C’-B’等六种组合情况。显然,刀具绕其转动的轴不能取为平行于C,否 则同样将因不能改变刀具轴线的方向而失去意义。 因此该类型机床中的两个转动 轴的配置情况是A’-B', B ’-A' 、C’-A,和C’-B’等四种。这类机床的特点 介于上述两类机床之间。 对于五坐标机床,不管是哪种类型,由于他们具有两个回转坐标,相对于静 止的工件来说,其运动合成可使刀具轴线的方向在一定的空间内(受机构结构限 制)任意控制,从而具有保持最佳切削状态及有效避免刀具干涉的能力,因此, 五坐标加工又可以获得比四坐标加工更广的工艺范围和更好的加工效果, 特别适
面向特征的整体叶轮五轴数控加工技术

面向特征的整体叶轮五轴数控加工技术彭芳瑜,邹孝明,丁继东,李 斌(华中科技大学国家数控系统工程技术研究中心,湖北武汉430074)摘要:基于特征制定整体叶轮数控加工工艺,同时兼顾叶轮的工作要求和加工刚度,利用U G NX3.0提供的Interpolate 方式规划流道特征的开粗加工和精加工轨迹,Sw arf 方式规划叶片特征的侧铣加工轨迹。
经过仿真验证加工轨迹的合理性,最后使用配有HNC-22M 数控系统的五轴加工中心VM C-1100成功加工了整体叶轮。
关键词:整体叶轮;五轴加工;加工轨迹规划;侧铣;UG NX中图分类号:TP391.7 文献标识码:A 文章编号:1672-1616(2007)01-0051-03 叶轮是涡轮式发动机、汽车增压器等动力机械的核心部件,其加工技术一直是研究的焦点。
整体叶轮的结构复杂,规划加工轨迹时约束条件多,加工时易产生碰撞干涉,采用传统的铸造成型后修光法、石蜡精密铸造法等较难保证叶片、流道以及叶片与轮毂倒角处的加工质量[1]。
五轴数控加工因具备有效避免干涉、可侧铣直纹面、切削状态良好等优点,从而成为提高整体叶轮加工效率和质量的首选。
目前,许多加工整体叶轮的企业多采用一些功能强大、界面良好、适用面广的通用型CAD/CAM 软件,如U G NX 、CAT IA 、Pro/Eng ineer 等。
本文基于整体叶轮的几何特征,利用大型通用CAD/CAM 软件UG NX3.0对其进行加工轨迹规划。
1 整体叶轮五轴数控加工工艺分析根据复杂型面零件的多轴数控加工特点,整体叶轮的五轴数控加工一般遵循如下的基本技术路线(如图1所示)。
图1 整体叶轮加工技术路线1.1 叶轮几何模型特征分析分析整体叶轮的叶片、流道等几何特征,确定叶片曲面、流道面和清根的特征参数,判断叶片曲面的类型,图2即为叶轮的基本几何特征。
整体叶轮的关键体素是叶片,叶片曲面可以分为直纹曲面和自由曲面(非直纹曲面),其中直纹面又可分为可展直纹面和非可展直纹面。
复杂曲面零件数控加工的关键问题——解读《复杂曲面零件五轴数控加工理论与技术》

1五轴数控加工简介复杂曲面零件作为数字化制造的主要研究对象之一,在航空、航天、能源和国防等领域中有着广泛的应用,其制造水平代表着一个国家制造业的核心竞争力。
复杂曲面零件往往具有形状和结构复杂、质量要求高等难点,是五轴数控加工的典型研究对象。
当前,复杂曲面零件主要包括轮盘类零件、航空结构件以及火箭贮箱壁板等,如图1所示。
轮盘类零件是发动机完成对气体的压缩和膨胀的关键部件,主要包括整体叶盘类零件和叶片类零件。
整体叶盘类零件的叶展长、叶片薄且扭曲度大,叶片间的通道深且窄,开敞性差,零件材料多为钛合金、高温合金等难加工材料,因此零件加工制造困难。
叶片是一种特殊的零件,数量多、形状复杂、要求高、加工难度大且故障多发,一图1复杂曲面零件直以来都是各发动机厂生产的关键。
航空整体结构件由整块大型毛坯直接加工而成,在刚度、抗疲劳强度以及各种失稳临界值等方面均比铆接结构胜出一筹,但由于其具有尺寸大、材料去除率大、结构复杂、刚性差等缺点,因此加工后会产生弯扭组合等加工变形。
随着新一代大型运载火箭设计要求的提高,为保证火箭的可靠性,并减轻结构质量,提高有效载荷,对火箭贮箱壁板网格壁厚精度和根部圆弧过渡尺寸都提出了更严格的要求。
五轴数控铣削加工具有高可达性、高效率和高精度等优势,是加工大型与异型复杂零件的重要手段。
五轴数控机床在3个平动轴的基础上增加了2个转动轴,不但可以使刀具相对于工件的位置任意可控,而且刀具轴线相对于工件的方向也在一定的范围内任意可控。
五轴数控加工的主要优势包括:①提高刀具可达性。
通过改变刀具方向可以提高刀具可达性,实现叶轮、叶片和螺旋桨等复杂曲面零件的数控加工。
②缩短刀具悬伸长度。
通过选择合理刀具方向可以在避开干涉的同时使用更短的刀具,提高铣削系统的刚度,改善数控加工中的动态特性,提高加工效率和加工质量。
③可用高效加工刀具。
通过调整刀轴方向能够更好地匹配刀具与工件曲面,增加有效切宽,实现零件的高效加工。
航空发动机中叶盘整体加工技术

整体叶盘加工中应用到的特种加工技术1.绪1论现代航空发动机的结构设计和制造技术是发动机研制、发展、使用中的一个重要环节,为满足以FII9、FI20、EJ200为标志的第4代战斗机用发动机以及未来高推重比新概念发动机的性能要求除采用先进技术、减少飞机机体结构、机载设备的重量外,关键是要求发动机的推重比达到I0这一级重点突破发动机部件的气动、结构设计、材料、工艺等方面的关键技术。
其中在发动机风扇、压气机、涡轮上采用整体叶盘(Biisk)结构(包括整体叶轮、整体叶环)是重要措施。
整2体叶盘结构的特点整体叶盘是航空发动机的一种新型结构部件,它与常规叶盘连接相比有以下特点:(1)不需叶片榫头和榫槽连接的自重和支撑这些重量的结构,减轻了发动机风扇、压气机、涡轮转子的重量。
(2)原轮缘的榫头变为鼓筒;盘变薄,其内孔直径变大;消除了盘与榫头的接触应力,同时也消除了由于榫头安装角引起的力矩产生的挤压应力;减轻了盘的重量提高了叶片的振动频率。
(3)整体叶盘可消除常规叶盘中气流在榫根与榫槽间缝隙中逸流造成的损失,使发动机工作效率增加,从而使整台发动机推重比显著提高。
(4)由于省去了安装边和螺栓、螺母、锁片等连接件,零件数量大大减少,避免了榫头、榫槽间的微动摩损、微观裂纹、锁片损坏等意外事故,使发动机工作寿命和安全可靠性大大提高。
(5)如整体叶盘叶片损坏,为避免拆换整个转子将整体叶盘与其他级用螺栓相连形成可分解的连接结构。
(6)由于高压压气机叶片短而薄叶片离心力较小,轮缘径向厚度小采用整体叶盘结构减重不显著。
航3空发动机整体叶盘结构在研究发展中存在的问题虽然,整体叶盘具有如此多的我优点,但是在整体叶盘的加工和使用过程中,我们也遇到了很多的问题,比如:(1)整体叶盘加工困难,只有制造技术发展到一定水平后,整体叶盘的应用才成为可能。
(2)发动机在使用过程中转子叶片常遇到外物打伤或因振动叶片出现裂纹,整体叶盘要更换叶片非常困难,也有可能因为一个叶片损坏而报废整个整体叶盘,因此风扇的第I\2级一般不用整体叶盘结构。
整体叶轮五轴数控粗加工刀位轨迹规划

整体叶轮五轴数控粗加工刀位轨迹规划曾巧芸;王宏涛;闫波【摘要】针对具有分流叶片的整体叶轮五轴数控粗加工,提出了一种刀位轨迹规划方法.采用偏置轮毂面分层加工方法对整体叶轮进行粗加工刀位轨迹规划,根据叶轮流道的儿何特征,将叶轮的1个粗加工区域分成5个加工单元.在每个加工区域内,选用直径最大的刀具,计算边界面的刀位轨迹,再由边界面的刀位轨迹插值计算得到整个加工区域的刀位轨迹.利用VERICUT软件进行加工仿真,结果表明所提出的刀位轨迹生成算法可行.【期刊名称】《应用科技》【年(卷),期】2012(039)004【总页数】5页(P42-46)【关键词】整体叶轮;粗加工;刀位轨迹;五轴数控加工【作者】曾巧芸;王宏涛;闫波【作者单位】南京航空航天大学机电学院,江苏南京,210016;南京航空航天大学机电学院,江苏南京,210016;南京航空航天大学机电学院,江苏南京,210016【正文语种】中文【中图分类】TP391.7整体叶轮被广泛使用在航空航天、海洋、能源和涡轮机械等行业,在国民经济和国防事业中发挥着巨大作用.整体叶轮按工作方式不同可分为轴流式和径流式[1].径流式整体叶轮的流道狭窄,叶片型面通常是扭曲的直纹面,采用五轴数控加工可以很好地解决叶轮加工中刀位干涉的问题.从毛坯到成品的加工过程中,叶轮粗加工的材料切除量最大,大量的加工时间被消耗在粗加工过程中;因此,合理设计粗加工方案,高效去除粗加工余量,对提高整体叶轮数控加工效率具有重要意义.对于径流式整体叶轮粗加工,曹利新等[2]先确定粗加工边界,采用之字形走刀和三角形走刀的刀具路径规划方法.Young等[3]先计算得到侧铣叶片的刀轴矢量,再将侧铣叶片的刀轴矢量绕叶轮中心轴旋转,由此得到叶轮粗加工刀具轨迹.Chuang等[4]通过等残留高度方法计算粗加工刀位点,插值侧铣叶片的刀轴矢量得到整个粗加工刀位轨迹.Heo等[5]根据整体叶轮叶片叶顶线与叶根线投影的交点数目将叶轮流道分为几个加工区域,预先设定机床的旋转角与摆动角,采用类似三轴数控加工方式进行叶轮的粗加工.文中针对叶片型面为直纹面具有分流叶片的径流式整体叶轮,根据整体叶轮流道的几何特征将叶轮流道划分为5个加工单元,采用偏置轮毂面分层加工的方法对整体叶轮进行粗加工刀位轨迹规划.对每个加工单元合理选择刀具参数,先计算边界面的刀位点和刀轴矢量,然后计算加工区域内的刀位点和刀轴矢量,从而得到整个流道的刀位轨迹.1 划分粗加工单元加工整体叶轮时,需要分析叶轮流道可加工性,包括叶片扭曲度、倾斜度、流道宽度和深度等,以确定刀具是否能够通过流道(可达性)、刀具直径等参数和加工方案.待加工整体叶轮各组成部分如图1所示,叶轮流道呈漏斗型,由于分流叶片的存在,最窄处在分流叶片进气口,主叶片进气口处和出气口处开敞性均比分流叶片进气口处要好.因此,粗加工时将叶轮流道分为5个加工单元.图1 整体叶轮各组成部分划分粗加工单元主要包括以下步骤:1)过分流叶片压力面叶根线起点作左边主叶片吸力面叶根线的垂线,根据叶根线参数方程求得垂足所在参数值,进而求得垂足所在的直母线ll.2)对分流叶片吸力面、右边主叶片压力面重复步骤1),得到直母线lr.3)作曲面通过ll、lr并垂直于分流叶片前缘,得到加工区域分界面.4)分流叶片压力面叶根线中点所在直母线为la,过分流叶片压力面叶根线中点作左主叶片吸力面叶根线垂线,重复步骤1),得到垂足所在直母线lb.5)作曲面 f通过 la、lb.6)对分流叶片吸力面、右主叶片压力面重复步骤 4)、5)得到直母线 lc、ld及曲面 g.划分好的5个粗加工单元如图2所示.图2 粗加工区域的划分2 加工区域刀具尺寸的确定粗加工的原则就是尽可能高效率地去除毛坯余量,因此尽量选择大尺寸的刀具;但刀具尺寸过大,可能导致刀具未能到达加工表面,也容易发生干涉.粗加工时一般根据流道最窄处的距离来选择刀具大小.对于每个加工区域,计算区域间最短的距离,由此选择刀具半径为式中:δ为叶片精加工余量,η为保障系数,1.2<η<1.5.3 粗加工刀具轨迹生成3.1 走刀步长和刀轨条数的计算在粗加工中,如果刀位点过于稀疏,则2个相邻刀位之间残余高度就会过大;刀位点稠密虽然能够得到较好的加工表面,但由于走刀次数过多,就体现不出粗加工快速去除余量的优势.因此,确定加工步长和行距是必要的.3.1.1 走刀步长的计算图3 走刀步长与直线逼近误差的关系图4 走刀步长的计算如图3所示,Δ为直线逼近控制误差,p0、p1为两相邻刀具路径的刀心点,则|p0p1|为走刀步长,记作L,有 KL2/8<Δ,即,K为走刀参数方向上最大法曲率[6].设曲线参数方向为u,取参数方向的增量Δu,如图4所示,计算出曲线C上的一系列点{M,N1,N2,…,Ni} 以及与这些点相对应的曲率{K0,K1,K2,…,Ki},计算起始点 M 到 Ni的距离|MNi|,令K max=max{K0,K1,K2,…,Ki},在曲线 C 上从点 M 到 Ni这段内,计算满足线性误差小于Δ的最大弦长Li=,判断不等式Li>|MNi|是否成立,若成立,令i=i+1;若不成立,记Ni-1为离散点,沿参数增加的方向,重复上述步骤,直到曲线上所有的轨迹点都计算完毕,最终得到曲线上所有加工所需的离散点.3.1.2 刀轨条数的计算在相邻2条刀位轨迹上,相邻的刀具路径距离比较小,近似认为两刀具路径间的加工面为平面,可大大简化行距的计算复杂度[7-9].设刀具直径为D,叶轮出气边处轮毂表面的残留高度的允许值为h,则行距为;再设出气边的弧长为s,则流道的刀轨条数为3.2 边界刀轴矢量的计算图5 粗加工边界刀轴矢量粗加工边界刀轴矢量计算[8]如图5所示,叶片为直纹面,设P1是叶顶线E上一点,P2是叶根线F上一点,点P1的单位法矢量为n1,点P2的单位法矢量为n2,点C1为n1所在直线上一点,点C2为n2所在直线上一点.令|P1P2|=l,|P1C1|=|P2C2|=d,d 为未知量.连接C1C2,以C1C2为刀具加工直母线P1P2时的刀轴方向.在确定轴线方向时,关键要计算出d的值.从上述分析可知,C1C2为刀轴方向,如图6所示,过P1作C1C2的垂线,垂足为O1,过P2作C1C2的垂线,垂足为O2.要使刀具在加工面P1点上切触,必须使|P1O1|=R+δ,R为刀具半径,δ为叶片精加工余量,类似地,|P2O2|=R+δ.由几何关系可知,∠C2C1P1=∠C1C2P2.图6 直母线与刀具轴线的关系图7 刀具轴线的求取在图7中,从点C1向过点P2且与P1P2垂直的平面作垂线,垂足为 C'1,则有C1C'1∥P1P2,且|C1C'1|=|P1P2|=l,令P2C2与P2C1的夹角为β,则β为法矢量n1、n2的夹角联立式(7)、(8),求解得到α 和 d.得到α 和 d 的解后,C1、C2点的位置就被确定,从而铣削该位置时的刀轴矢量就被确定了.3.3 流道粗加工刀位轨迹规划如图8所示,整体叶轮流道粗加工采用偏置轮毂面分层加工的方法,当完成一层的加工后,将刀具退刀,然后再将刀具移动到下一切削层的加工区域,继续加工.Qc、Qd为2条边界曲线,如图9所示,首先根据走刀步长计算方法,计算边界曲线Qc上所有刀位点Q c_i(i=0,1,2,…,n),过Q c_i做垂直于叶轮轴线的平面Wi,Wi交边界曲线于 Qd点 Qd_i,则Q d_i为Qd上的刀位点.根据边界刀轴矢量计算方法计算得到边界刀位点Q c_i、Q d_i的刀轴矢量分别为T c_i、T d_i.根据刀轨条数ns,采用线性插值的方法在叶片边界刀轴矢量之间进行插值,得到流道的刀轴矢量:式中j=0,1,2,…,ns.将刀轴矢量与轮毂偏置面求交,所得交点即为刀位点.每一层中将所有刀位点按之字形走刀路径规划,生成流道粗加工刀位轨迹.由于整体叶轮具有几何对称性,可以通过旋转和复制一个流道的刀位轨迹即可得出所有流道的刀位轨迹,从而规划出整体叶轮的粗加工刀位轨迹.图8 偏置轮毂面分层加工方法图9 粗加工刀位点的计算4 实例根据所提出的整体叶轮五轴粗加工刀位轨迹规划方法,采用UG/OPEN API函数开发出整体叶轮粗加工专用模块,并运用VERICUT软件对整体叶轮进行粗加工仿真.整体叶轮叶片数为14个,主叶片和分流叶片各7个,叶轮出气口出直径为108 mm,进气口出直径为22 mm.根据各加工单元叶片间的最小距离,选用半径分别为4、3、3、5、5 mm的球头铣刀进行粗加工,叶片精加工余量为1 mm,轮毂精加工余量为1 mm.运用VERICUT软件实现整体叶轮5个加工单元的粗加工仿真,仿真加工结果分别如图10~12所示.图10 叶轮第1加工单元粗加工仿真图11 叶轮第2、3加工单元粗加工仿真图12 叶轮第4、5加工单元粗加工仿真5 结束语对具有分流叶片的整体叶轮粗加工刀位轨迹规划进行了重点研究,根据整体叶轮几何特征,分析整体叶轮的可加工性,采用偏置轮毂面分层加工的方法,确定粗加工工艺方案.将叶轮流道分成5个加工单元,根据加工单元间的最小距离选取刀具半径,计算了边界刀位点和刀轴矢量,基于边界刀位轨迹计算整个加工区域的刀位轨迹.运用VERICUT软件对整体叶轮粗加工进行仿真,验证所提出的整体叶轮粗加工方案是可行的.参考文献:[1]姬俊锋.复杂整体叶轮数控加工关键技术研究[D].南京:南京航空航天大学,2009:37-41.[2]曹利新,马晓嘉.五坐标加工整体叶轮粗加工刀位规划[J].大连理工大学学报,2008,48(1):68-73.[3]YOUNG H T,CHUANG L C,GERSCHWILER K.A five-axis rough machining approach for a centrifugal impeller[J].International Journal of Advanced Manufacturing Technology,2004,23:233-239.[4]CHUANG L C,YOUNG H T.Integrated rough machining methodology for centrifugal impeller manufacturing[J].Internal Journal of Advanced Manufaturing Technology.2006,34(11/12):1062-1071.[5]HEO E Y,KIM D W,KIM B H.Efficient rough-cut plan for machining an impeller with a 5-axis NC machine[J].International Journal of Computer Intergrated Manufacturing,2008,21(8):971-983.[6]刘雄伟,张定华,王增强,等.数控加工理论与编程技术[M].北京:机械工业出版社,2007:29-33.[7]曹利新,苏云玲,金玉淑.三元叶轮几何造型与数控加工刀具路径规划[J].推进技术,2005,26(2):188-192.[8]蔡永林,席光,查建中.任意扭曲直纹面叶轮数控侧铣刀位计算与误差分析[J].西安交通大学学报,2004,38(5):517-520.[9]胡占齐,解亚飞,刘金超.超重型数控镗铣床精度可靠性研究[J].哈尔滨工程大学学报,2011,32(12):1599-1604.。
- 1、下载文档前请自行甄别文档内容的完整性,平台不提供额外的编辑、内容补充、找答案等附加服务。
- 2、"仅部分预览"的文档,不可在线预览部分如存在完整性等问题,可反馈申请退款(可完整预览的文档不适用该条件!)。
- 3、如文档侵犯您的权益,请联系客服反馈,我们会尽快为您处理(人工客服工作时间:9:00-18:30)。
1 引言
运动轴配置的不同,五轴数控机床的结构类型亦有多种,而通常
航空发动机是飞机的最重要的核心部件,为飞机提供动力, 对飞机性能起着决定因素。整体叶轮作为新型发动机的关键部 件,其制造加工工艺水平一直是发动机制造行业中的一个重要课
各学者考虑实际加工的通用性及五轴数控加工设备的可行性将 五轴设备划分为 A-B,B-A,A-C,B-C 四种类型[3],也有的对 CA,C-B 型结构类型的五轴数控机床进行了较为系统的分析[4]
(10)
(2)分别计算机床本体固联的参考坐标系 MCS 到摆动坐标
系 TTCS 的转转
坐标系 RTCS 的转换矩阵 M(RTCS←TTCS)。因为转动副 A 与转
动副 C 均在 TTCS 之内,因此 MCS 坐标系与 TTCS 坐标系之间不
存在旋转位姿关系,M(TTCS←MCS)只有两个坐标系原点的位置
Kinematic Analysis of Five-Axis CNC Machine Tools for Aircraft Engine Blisk Manufacturing
LI Tian1,CHEN Wu-yi2,LIU Zi-cheng3
(1.Gas-turbine Development Center of China,Beijing 100028,China;2.School of Mechanical Engineering & Automation, Beihang University,Beijing 100191,China;3.Gas Turbine Establishment of China,Sichuan Jiangyou 621703,China)
摘 要:针对航空发动机整体叶轮零件的五轴数控加工问题,对工程实用五轴数控加工机床的空间构型进行了系统划 分,将可以用于整体叶轮加工的五坐标数控加工机床划分为双摆头结构类型,双转台结构类型和摆头转(摆)台及单摆头 单摆台结构类型,并对各种构型的五轴数控加工机床的坐标变换后处理过程进行了详细的推导。最后,提出了根据待加 工整体叶轮的结构特点,对最适用五轴加工机床的选择的思路,并就整体叶轮构型与五轴加工机床选择进行了定性分 析。 关键词:整体叶轮;五轴加工;运动学模型 中图分类号:TH16;V263;TG659 文献标识码:A 文章编号:1001-3997(2013)06-0148-04
Machine Tool Kinematic Chain Cascade
设定机床两个回转轴线的交点为主轴支点 OR,在机床的初 始位置,机床的运动坐标[X′,Y,Z,A,C]为[0 0 0 0 0],在机床
模型中分别建立支点坐标系 RCS,其原点位于主轴支点 OR,与 Y 轴固联,不随 A、C 转动副的旋转而变化;建立与机床本体固联
图 1 多轴串联机床各级运动副示意图 Fig.1 Multi-Axis Series Machine Tool Schematic Diagram
of Motion Pair at All Levels
3 五轴加工机床构型分类及运动学分析
3.1 双摆头五轴数控机床
对于刀具旋转摆动的五轴结构通常在大型加工设备中使用
差值,因此等于机床 X 轴与 Z 轴的平动转换矩阵 T (TTCS←
No.6
150
机械设计与制造
June.2013
RCS)。
(3)计算旋转坐标系 RTCS 到工件坐标系 WCS 坐标系的刀
具位姿变换矩阵 M(WCS←RTCS)。一般设定 C 轴回转中心为编
程零点,则 M(WCS←RTCS)其中的平移分量为一单位阵。
做工作的基础上从五轴数控加工系统的结构运动学普遍性着手 现代五坐标数控加工技术的广泛应用和发展,各种特定设备的多
进行分类和几何分析,使得五轴数控加工机床后置处理结构运动 个运动轴之间的相对运动变化已经使得很多商用 CAM 软件的通
学分析的工程化处理更易于实现。
用后置处理程序的功能受到很大程度上的制约。因此需要在原理
一般五轴数控机床由三个平动轴和二个回转轴构成。根据 位置关系示意,如图1 所示。
来稿日期:2012-08-10 作者简介:李 湉,(1983-),男,北京人,博士,工程师,主要研究方向:航空发动机先进加工技术;
陈五一,(1951-),男,山西太原人,教授,博士生导师,主要研究方向:先进加工及机电一体化、加工机理、并联机构及切削数据库
旋转的 B 轴和与工作台级联的绕空间向量[1 0 -1]旋转的 A 旋
转轴。其运动链级联关系,如图 4 所示。其运动链级联顺序为 B→
X→Z→Y→A。
RCS
X轴 Z轴
OR B轴
刀具 TCS OT
WCS
OW 工作台
RICS ORT
A轴
Y轴
MCS OM
机床本体
图 4 摆头转台五轴数控机床运动链级联关系 Fig.4 Oscillating Turntable 5-Axis NC Machine
量 CM 和刀具轴线方向矢量 IM 分别为: CM =M(MCS←RCS)CR
=M(MCS←RCS)R AC,θC AR AA,θA AC
IM =M(MCS←RCS)IR
=M(MCS←RCS)R AC,θC AR AA,θA AI
(5) (6)
式中:M(MCS←RCS)—支点坐标系 RCS 到机床本体固联的参考
的转动台实现,因此,A 轴为 C 轴的基轴,C 轴为 A 轴的依赖轴。
其运动链级联关系,如图 3 所示。其运动链级联顺序为 Y→Z→
X→A→C。
WCS
OW 工作台
RTCS
ORI C轴
OTT A轴
TTCS Y轴
Z轴
Y轴
刀具 TCS
OT
MCS OM
机床本体
图 3 双转台五轴数控机床运动链级联关系 Fig.3 Double Turntable 5-Axis NC Machine Kinematic Chain Cascade
(12)
3.3 摆头转台机床及其他
工程实际所使用的五轴数控机床除了刀具旋转摆动的五轴
构型与工作台旋转摆动的五轴构型,还有较为常用的单摆头单转
台五轴构型数控机床。而且某些特定机床为了用于特殊零件加工
用途,其转动轴围绕倾斜矢量旋转,某型五轴数控加工中心机构
模型(图略)。机床亦具有两组转动副级:与主轴级联的为绕 Y 轴
(1)
T
I=[0 0 1 0]
(2)
式中:L—刀心位置距离主轴支点 OR 的摆长。
(1)支点坐标系 RCS 坐标系中刀具刀位点位置矢量 CR 和刀
具轴线方向矢量 IR 分别可求得:
CR =R AC,θC AR AA,θA AC IR =R AC,θC AR AA,θA AI
(3) (4)
(2)机床本体固联的参考坐标系 MCS 中刀具刀位点位置矢
(1)由于机床本体固联的参考坐标系 MCS 与刀具坐标系 TCS
之间相对位置变换关系简单,只有 Y 轴平动关系,因此可以对
MCS 坐标系中的刀具位姿参数直接求得机床本体固联的参考坐
标系 MCS 中刀具刀位点位置矢量 CM 和刀具轴线方向矢量 IW:
T
CM =[0 Y 0 1 ]
(9)
T
IM =[0 0 1 0]
3.2 双转台五轴数控机床
双转台五轴数控机床(图略)。通常情况下,X、Y 方向的平动
由工作台实现,Z 方向平动由主轴带动刀具上下移动实现,也有
X、Z 方向的平动由工作台平移和升降实现,Y 方向平动由主轴的
前后伸缩移动实现。但两种情况中刀轴方向矢量在机床坐标系
MCS 中始终保持不变。绕 X 方向的旋转由下方摆动台带动 C 轴
较多,某型双摆头五轴数控机床。其运动链级联关系,如图 2 所
示。其运动链级联顺序为 A→C→Y→Z→X。
RCS
A轴
Y轴 Z轴
OR C轴
WCS
OW 工作台
TCS 刀具
OT
X轴
MCS OM
机床本体
图 2 双摆头五轴数控机床运动链级联关系 Fig.2 Double Pendulum Head Five Axis NC
第6期
李 湉等:航空发动机整体叶轮五轴数控加工机床运动学分析
149
1 O(2 1CS) 副1 动副 滑动 转
主轴 刀具
O(t TCS)
O(2 2CS)
工件 OW(WCS) 工作台
转滑动动副副22
副 N-1N-1 滑动动副
转
ON-(1 N-1CS) O(3 3CS)
滑动副 N 转动副 N
O(N NCS)
(4)WCS 坐标系下刀具刀位点位置矢量 CW 和刀具轴线方向
矢量 IW 分别为:
CM =M(WCS←MCS)CM =M(WCS←RTCS)
gM(RTCS←TTCS)M(TTCS←RCS)CM
(11)
IM =M(WCS←MCS)IM =M(WCS←RTCS)
gM(RTCS←TTCS)M(TTCS←RCS)IM
坐标系 MCS 转换矩阵。
(3) 加工坐标系 WCS 坐标系下刀具刀位点位置矢量 CW 和 刀具轴线方向矢量 IW 分别为:
CM =M(MCS←MCS)CM
=M(WCS←MCS)M(WCS←PCS)R AC,θC AR AA,θA AC(7)
IM =M(WCS←MCS)IM
=M(WCS←MCS)M(WCS←RCS)R AC,θC AR AA,θA AI (8)
(注:A、B、C 分别为绕机床 X、Y、Z 轴的旋转向量),并分别对其运 题。航空发动机整体叶轮零件目前通常使用五轴数控铣削设备予以
动变换关系进行研究,通过对前置刀位轨迹变换将其分解到机床 加工完成[1-3]。五轴数控铣削设备的后置处理算法已经相对成熟[4-7],