切槽的加工过程
槽的数控车削加工

(四)切槽切削用量选择
切削速度: 通常取外圆切削速度的60%-70%。
进给量:
一般取0.05-0.3mm/r。
相关理论
1、G01指令
G00 X35. Z-26.; 绝对坐标方式: G01 X18. F50 ; 增量坐标方式: G01 U-17. F50 ;
2、径向切槽循环G75
2)指令说明G75循环轨迹如图所示。
项目七:槽的数控车削加工
学习内容
1、车沟槽的走刀路线设计 2、切槽刀的选用 3、G75指令
零件工艺分析
1、结构分析 2、尺寸分析 3、表面粗糙度分析
轴类零件数控加工工艺的设计方法
(一)切槽、切断刀
(二)切槽、切断的走刀路线设计(三)切槽加工方法1、一般要求切槽刀刀尖与工件轴线等高,而且 刀头与工件轴线垂直。 2、精度要求较高的沟槽,一般采用二次进给车 成。 3、车较宽的沟槽,可以采用多次直进法切割。 4、较大的梯形槽,通常先车直槽,然后用梯形 刀直进法或左右切削法完成。
3)编程示例
G75用于切削较宽的径向槽(刀宽为3mm) 程序如下: O1010 M03S500T0101 G00X100Z100 G00X52Z-18(起刀点) G75R1 G75X30Z-55P3000Q3000R0F0.1 G00X100Z100 M30
注意: 程序段中的△I、 △k值,在FANUC系统中,不能输入 小数点,而直接输入最小编程单位。
如:P1500表示径向每次切深量为1.5mm.
●△i、 △k、 △d的单位为最小编程单位。 ●△i、 △k、 △d为不带符号的值表示。 ●当G75指令中Z(W)省略不写,刀具仅作X向进给而不作Z向偏移。 ●e值大于每次切深量△i,报警。 ●F值应略小。
数控车床编程切槽加工

指令代码
指令代码是数控车床编程的基础, 包括准备功能指令(G指令)、 辅助功能指令(M指令)等。
坐标系设定与原点选择
01
02
03
坐标系设定
数控车床采用右手直角坐 标系,分别设定X、Y、Z 三个坐标轴。
原点选择
原点选择是建立工件坐标 系的关键步骤,通常选择 工件的某一固定点为原点, 建立工件坐标系。
需的槽深度和宽度。
圆弧槽编程方法
选择合适的切削刀具
与直线槽类似,根据圆弧槽的半径和深度选择合适的切削刀具。
编写圆弧插补程序
使用G02或G03指令编写圆弧插补程序,指定圆弧的起点、终点 和中心点坐标,以及切削速度和进给量等参数。
添加切削循环
同样使用切削循环指令实现多次切削,直到达到所需的圆弧槽深 度和宽度。
补偿原理
刀具补偿原理主要包括长度补偿和半径补偿两种。长度补偿通过测量刀具长度并输入数控 系统,实现刀具长度的自动调整;半径补偿则根据刀具半径和工件轮廓计算出刀具中心轨 迹,实现工件的精确加工。
02
切槽加工原理及工艺参数
切槽加工原理简介
切槽加工定义
切槽加工是数控车床上的一种常见加 工方式,通过切削工具在工件表面切 除一定深度和宽度的材料,形成所需 的槽形结构。
04
常见问题及解决方案
切削振动问题分析及处理措施
切削振动原因分析
切削振动可能由刀具刚性不足、 切削参数不合理、工件装夹不稳 等因素引起。
处理措施
提高刀具刚性,优化切削参数, 确பைடு நூலகம்工件装夹稳定,采用减振装 置等措施。
刀具磨损过快原因及优化策略
刀具磨损过快原因
刀具材料选择不当、切削用量过大、冷却不充分等。
槽加工
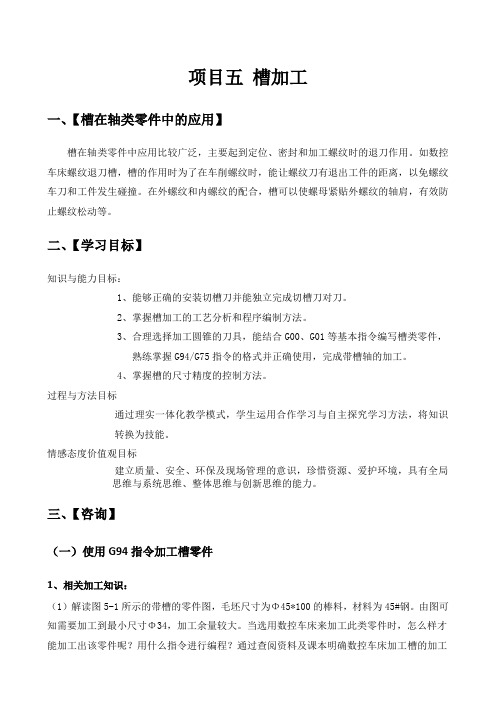
项目五槽加工一、【槽在轴类零件中的应用】槽在轴类零件中应用比较广泛,主要起到定位、密封和加工螺纹时的退刀作用。
如数控车床螺纹退刀槽,槽的作用时为了在车削螺纹时,能让螺纹刀有退出工件的距离,以免螺纹车刀和工件发生碰撞。
在外螺纹和内螺纹的配合,槽可以使螺母紧贴外螺纹的轴肩,有效防止螺纹松动等。
二、【学习目标】知识与能力目标:1、能够正确的安装切槽刀并能独立完成切槽刀对刀。
2、掌握槽加工的工艺分析和程序编制方法。
3、合理选择加工圆锥的刀具,能结合G00、G01等基本指令编写槽类零件,熟练掌握G94/G75指令的格式并正确使用,完成带槽轴的加工。
4、掌握槽的尺寸精度的控制方法。
过程与方法目标通过理实一体化教学模式,学生运用合作学习与自主探究学习方法,将知识转换为技能。
情感态度价值观目标建立质量、安全、环保及现场管理的意识,珍惜资源、爱护环境,具有全局思维与系统思维、整体思维与创新思维的能力。
三、【咨询】(一)使用G94指令加工槽零件1、相关加工知识:(1)解读图5-1所示的带槽的零件图,毛坯尺寸为Φ45*100的棒料,材料为45#钢。
由图可知需要加工到最小尺寸Φ34,加工余量较大。
当选用数控车床来加工此类零件时,怎么样才能加工出该零件呢?用什么指令进行编程?通过查阅资料及课本明确数控车床加工槽的加工方法及指令的应用;叙述数控车床加工槽工件的全过程。
(2)任务分析解读图5-1所示的槽零件,所用的毛坯为棒料,加工余量大,要得到图纸标注尺寸,需要一层层切削。
如果使用G00、G01等指令分层切削编程,编程将会很繁琐,采用外圆粗车循环 G71指令及精车循环G70指令以及G94端面切削循环指令编程则可简化编程。
本任务为带槽圆柱轴的车削,在编程与加工之前,应先了解槽零件的工艺分析方法及车削加工路线等相关知识。
图5-1槽加工零件图(3)刀具卡(见表5-1)表5-1 槽加工刀具卡(4)检测方法(见表5-2)2、制定加工工艺:(1)加工路线:粗车所有外圆尺寸,精车所有外圆尺寸,切槽。
端面切槽加工工艺
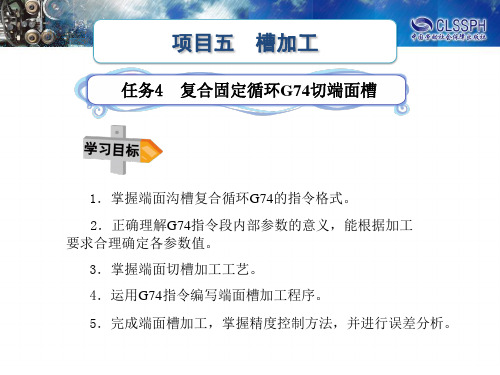
O0002;
T0202;
切槽刀,刃宽为4mm
G00 X60.0 Z2.0 S300 M03; 定位至循环起点
G74 R0.5;
退刀量0.5mm
端面均布槽加工件
G74 X100.0 Z-3.0 P10000 Q2000 F0.1;
G00 X100.0 Z100.0; M05; M30;
终点坐标(100.0,-3.0),Z向每次切 入量2mm,X向偏移量10mm,进给量
0.1mm/r
项目五 槽加工
一、分析零件图样
本任务中,端面槽槽宽5mm、槽深6mm,端面槽两侧圆弧直径分别
为φ34、φ44,有一定的尺寸精度要求,表面粗糙度要求为Ra3.2μm。 二、分析加工工艺
1.编程原点的确定(工件右端面的中心处) 2.制定加工方案及加工路线
本任务中选用刃宽为3mm的端面切槽刀,循环起点坐标(35.0, 1.0),终点坐标(39.0,-6.0)。
任务要求:如下图所示工件,外形轮廓加工已完成, 试编写工件上端面槽的数控车削加工程序并进行加工。
端面槽加工实例
项目五 槽加工
任务分析:本任务工件中的端面槽和外沟槽一样,如果采用 G01指令来编程则程序冗长。因此,引入了端面沟槽复合固定循 环指令进行编程,以达到简化编程的目的。另一方面,端面槽刀 的几何参数、装刀及对刀操作,端面切槽加工中切削用量的合理 选择等加工工艺知识也是本任务的重点。
(2)指令说明 G74循环轨迹与G75循环轨迹相类似,刀具从循环起点A出
发,先轴向切深,再径向平移,依次循环直至完成全部动作。
项目五 槽加工
端面切槽循环轨迹图
端面切槽循环轨迹图
项目五 槽加工
端面啄式深孔钻削
当G75指令用于端面啄式深孔钻削循环 指令时,装夹在刀架(尾座无效)上的刀具 一定要精确定位到工件的旋转中心。
数控车削中几种切槽加工方法及其应用

数控车削中几种切槽加工方法及其应用
数控车削是一种高效、精度高的加工方法,广泛应用于各种机械零件的加工中。
在数控车削中,切槽加工是一种常见的加工方式,可以用于加工各种形状的槽口,如直槽、斜槽、圆弧槽等。
本文将介绍几种常见的切槽加工方法及其应用。
1. 直线切槽加工
直线切槽加工是最常见的切槽加工方式之一,它可以用于加工各种形状的直槽。
在数控车床上,直线切槽加工通常采用直线插补方式,通过控制刀具的进给速度和切削深度来实现加工。
直线切槽加工适用于加工各种形状的直槽,如方槽、矩形槽、三角形槽等。
2. 圆弧切槽加工
圆弧切槽加工是一种常用的切槽加工方式,它可以用于加工各种形状的圆弧槽。
在数控车床上,圆弧切槽加工通常采用圆弧插补方式,通过控制刀具的进给速度和切削深度来实现加工。
圆弧切槽加工适用于加工各种形状的圆弧槽,如圆弧形槽、椭圆形槽等。
3. 斜线切槽加工
斜线切槽加工是一种常用的切槽加工方式,它可以用于加工各种形状的斜槽。
在数控车床上,斜线切槽加工通常采用斜线插补方式,通过控制刀具的进给速度和切削深度来实现加工。
斜线切槽加工适
用于加工各种形状的斜槽,如斜槽、斜面槽等。
以上是数控车削中几种常见的切槽加工方式及其应用。
在实际加工中,根据不同的加工要求和零件形状,可以选择不同的切槽加工方式。
同时,在进行切槽加工时,还需要注意刀具的选择、进给速度、切削深度等参数的控制,以确保加工质量和效率。
槽的加工

三、编程知识:
进给暂停指令(G04) : 含义:该指令可以使刀具作短时间(几秒钟) 无进给光整加工,主要用于车削沟槽、不通孔 以及自动加工螺纹等场合。 格式 : G04 X_或P_; 说明:该指令控制系统指令时间暂时停止执行 后续程序段。暂停时间结束则继续执行。该指 令为非模态指令,只在本程序段有效。X、P均 为暂停时间,单位分别为秒和毫秒。暂停指令 应用于下列情况:
3.加工注意事项:
1.车槽刀主刀刃和轴心线是否平行,车成 的沟槽槽底一侧直径大,另一侧直径小成 竹节 2.槽壁与轴心线不垂直,出现内槽狭窄外 口大的喇叭形,造成这种情况的主要原因: 刀刃磨钝让刀;车刀装夹不垂直。 3.槽壁与槽底产生小台阶,主要原因是车 刀装夹不垂直所造成。 4.要正确使用游标卡尺测量沟槽。 5.合理选择转速和进给量;正确使用冷却 液。
2.加工步骤:
开机 对刀 程序调试、执行 关机 回原点 刀具选择、安装
编辑输入程序 加工 检验:检验尺寸是否合格
填写本项目工序卡和编程卡
四、项目训练:
毛坯:∮45×65 选用工具量具:90度外圆车刀、切断刀、游标卡尺、
外径千分尺
1.参考程序:
G40G97G99M03S600T0202; G00X42.Z-14.; G01X18.F0.05; X42.; G01Z-23.F0.1; G01X18.F0.05; X42.; Z2.F1.0; G00X100.Z100.; M30;
项目四: 槽的加工
一、项目目标:
知 识 目 标
掌握轴类零件槽的加工工艺与编程方法
掌握切槽刀的选择、安装方法
技 能 目 标
能熟练使用手动方式进行切槽
数控车精品课程-切槽加工

02
切槽加工的技术要点
切槽刀具的选择
切槽刀具的材料
切槽刀具的规格
选择具有高硬度、高耐磨性和高耐热 性的刀具材料,如硬质合金和陶瓷等。
根据切槽的宽度和深度选择合适的切 槽刀具,以确保切削过程中的刚性和 安全性。
数控车精品课程-切槽加工
目录 Contents
• 切槽加工的基本概念 • 切槽加工的技术要点 • 切槽加工的工艺流程 • 切槽加工的常见问题及解决方案 • 切槽加工的案例分析
01
切槽加工的基本概念
切槽加工的定义
切槽加工是指在金属切削加工过程中 ,利用数控车床的切削刀具对工件上 的槽进行切削,以达到预设的槽宽、 槽深和槽型的过程。
切削振动问题
总结词
切削振动会降低切槽加工的表面质量和加工精度,同时可能加剧刀具磨损。
详细描述
切削振动的原因可能是机床刚性不足、刀具设计不合理或切削参数设置不合适。 为了解决这个问题,可以提高机床的刚性和稳定性,优化刀具设计,选择合适的 切削参数。同时,加强切削液的供给和使用也可以有效减小切削振动。
05
切槽加工的案例分析
案例一:不锈钢切槽加工
总结词
难度适中,刀具选择要求高
详细描述
不锈钢切槽加工对刀具的硬度和耐磨性要求较高,同时需要合理选择切削参数, 以避免刀具过快磨损和工件表面质量下降。在加工过程中,还需注意控制切削 温度,防止刀具和工件产生热变形。
案例二:铝合金切槽加工
总结词
加工效率高,切削参数范围广
切槽加工后的检测与修正
切槽尺寸检测
使用测量工具对切槽尺 寸进行检测,确保符合
内孔槽刀切槽的正确方法

内孔槽刀切槽的正确方法内孔槽刀切槽的正确方法应注意以下几点:一、内孔槽刀的组成结构内孔槽刀主要由刀体、刀杆、内孔槽刀头三部分组成。
刀体为刀的主体部分;刀杆用来固定刀体,并带动刀体运动;内孔槽刀头是最关键的切削部件,它的几何形状决定了切削效果。
二、准备工作1. 根据图纸选用合适规格的内孔槽刀头。
内孔槽刀头有直槽刀头、斜槽刀头等多种类型,要根据加工需求选择。
2. 将内孔槽刀头安装固定在刀杆上,刀体装入刀柄中。
确保刀杆和刀体连接牢固、转动灵活。
3. 将工件安装固定在机床工作台上,控制工件的刚性,必要时使用定位装置。
4. 根据切槽图纸布置好切削路径,设置切削参数,如主轴转速、进给速度等。
三、切槽过程1. 开启内孔槽刀和冷却液,开始切削过程。
内孔槽刀旋转切入工件表面,按设定路径和进给速度由浅入深切出槽型。
2. 在切削过程中,注意刀体和工件的相对位置,手动或自动调整XYZ 方向的进给,确保刀头始终处在最佳切削位置。
3. 采用螺旋interpolation移動路径,将刀头缓慢螺旋进入孔内,可获得更好的切削效果。
4. 根据加工材料选择合适的主轴转速、进给速度等参数,保证切削顺畅。
5. 内孔槽面切削完成后,可进行后续的抛光、去毛刺等处理,提升表面质量。
四、结束加工1. 关闭主轴电源,内孔槽刀停止旋转,退出孔内。
2. 关闭冷却液阀门,将工件取出检视槽型效果。
3. 将刀体和工件上的切屑、冷却液清理干净,做好清洁。
4. 检查内孔槽刀刀头是否需要更换,记录刀具使用时间。
5. 将各项机床参数复位,做好定期维护保养工作。
综上所述,这就是内孔槽刀切槽的基本方法流程,需要熟练掌握刀具选择、切削参数设定和机床操作,才能提高加工质量和工作效率。
槽的加工(切槽固定循环指令)
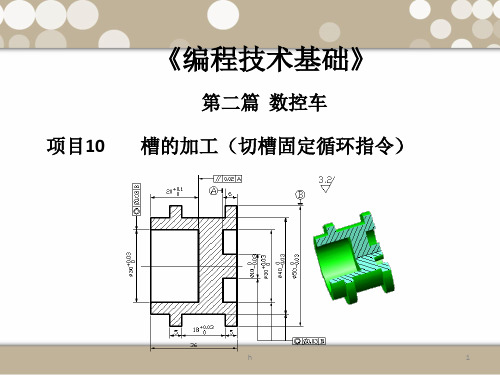
G74 X10 Z-6 P2500 Q3000 F60;
G28 U0 W0;
退刀
M30;
程序结束
h
12
h
4
G75的循环轨迹如图所示,刀具从循环起点A点开始,沿径向进刀Δi并到达C点, 然后退刀e(断屑)到D点,再继续按循环递进切削至径向终点的X坐标处,然后 快速退刀到径向起刀点,完成一次切削循环;接着沿轴向偏移Δk至F点,进行第 二次切削循环;依次循环直至刀具切削至程序终点坐标处(B点),径向退刀至 起刀点(G点),再轴向退刀至起刀点(A点),完成整个切槽循环动作。
其中, e为退刀量,其值为模态值; X(U)_Z(W)_为切槽终点处坐标; Δi为X方向的每次切深量,用不带符号的半径量表示,单位:μm; Δk为刀具完成一次径向切削后,在Z方向的偏移量,用不带符号的值表 示,单位:μm; Δd为刀具在切削底部的Z向退刀量,无要求时可省略; F为径向切削时的进给速度。 最后一次切深量和最后一次Z向偏移量均由系统自行计算。
(2)由于Δi和Δk为无符号值,所以刀具切深完成后的偏移方向由系 统根据刀具起刀点及切槽终点的坐标自动判断。
(3)切槽过程中,刀具或工件受较大的单方向切削力,容易在切削 过程中产生振动,因此,切槽过程中进给速度F的取值应略小,特别是 在端面切削时,通常取50~100mm/min。
h
11
【本项目参考程序】
h
6
例题:按如图所示尺寸切断零件。
解:
T0101;
M03 S600;
G00 X45 Z-40;
G75 R1;
G75 X-1 P5000 F50;
M05;
M30;
h
7
2、端面切槽循环指令G74
切槽加工工艺流程详细介绍

切槽加工工艺流程详细介绍下载温馨提示:该文档是我店铺精心编制而成,希望大家下载以后,能够帮助大家解决实际的问题。
文档下载后可定制随意修改,请根据实际需要进行相应的调整和使用,谢谢!并且,本店铺为大家提供各种各样类型的实用资料,如教育随笔、日记赏析、句子摘抄、古诗大全、经典美文、话题作文、工作总结、词语解析、文案摘录、其他资料等等,如想了解不同资料格式和写法,敬请关注!Download tips: This document is carefully compiled by theeditor. I hope that after you download them,they can help yousolve practical problems. The document can be customized andmodified after downloading,please adjust and use it according toactual needs, thank you!In addition, our shop provides you with various types ofpractical materials,such as educational essays, diaryappreciation,sentence excerpts,ancient poems,classic articles,topic composition,work summary,word parsing,copy excerpts,other materials and so on,want to know different data formats andwriting methods,please pay attention!1. 设计与规划。
确定切槽的位置、形状、尺寸和深度等要求。
切槽销轴加工工艺流程
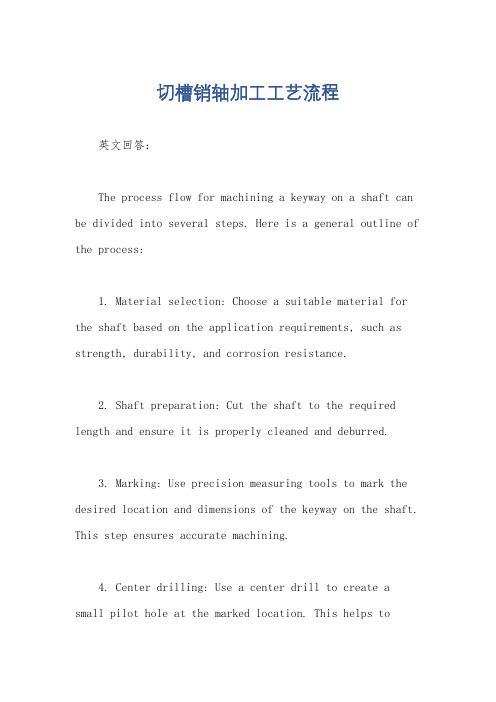
切槽销轴加工工艺流程英文回答:The process flow for machining a keyway on a shaft can be divided into several steps. Here is a general outline of the process:1. Material selection: Choose a suitable material for the shaft based on the application requirements, such as strength, durability, and corrosion resistance.2. Shaft preparation: Cut the shaft to the required length and ensure it is properly cleaned and deburred.3. Marking: Use precision measuring tools to mark the desired location and dimensions of the keyway on the shaft. This step ensures accurate machining.4. Center drilling: Use a center drill to create a small pilot hole at the marked location. This helps toguide the subsequent drilling and milling operations.5. Drilling: Use a drill bit with the appropriate size to create a hole that matches the width of the keyway. The depth of the hole should be slightly shallower than the final desired depth of the keyway.6. Milling: Use a milling cutter or broach to remove material from the sides of the hole, creating the keyway. The milling operation can be done using a milling machine or a CNC machine for more precise and automated control.7. Finishing: After the keyway is machined, use deburring tools to remove any burrs or sharp edges. This step ensures a smooth and safe surface finish.8. Inspection: Measure the dimensions of the keyway using precision measuring tools to ensure it meets the required tolerances and specifications.9. Surface treatment: Depending on the application requirements, the shaft may undergo additional surfacetreatments such as heat treatment, plating, or coating to enhance its properties.10. Final inspection and assembly: Perform a final inspection to ensure the keyway meets all the required specifications. The shaft can then be assembled into the final product, such as a machine or equipment.中文回答:切槽销轴的加工工艺流程可以分为几个步骤。
数控车课程切槽加工

谢谢 大 家
Thank you
第21页/共22页
感谢您的观看!
第22页/共22页
…
第12页/共22页
切槽加工实例
已知1号刀为切槽刀,刀宽4mm,试编写图示工件切 槽部分的加工程序。
… T0101 M03S400F0.08 G00X30.0Z-14.0 G94X18.0Z-14.0 G00X100.0Z100.0
…
第13页/共22页
切槽加工实例
已知1号刀为切槽刀,刀宽2mm,试编写图示工件切 槽部分的加工程序。
第6页/共22页
外圆车刀
第7页/共22页
切槽刀
第8页/共22页
刀位点
刀位点:刀具的定位基准点。
刀宽
第9页/共22页
切削过程
第10页/共22页
切削轨迹
②G01
③G01 ①G00
④G00
第11页/共22页
切槽加工实例
已知1号刀为切槽刀,刀宽4mm,试编写图示工件切 槽部分的加工程序。
… T0101 M03S400F0.08 G00X30.0Z-14.0 G01X18.0 X30.0 G00X100.0Z100.0
T0101
M03S400F0.08
G00X32.0Z-12.0
G01X20.0
X32.0
G00Z-20.0
G01X20.0
X32.0
Z
G00Z-32.0
பைடு நூலகம்
G01X20.0
X32.0
G00Z-40.0
G01X20.0
X32.0 G00X100.0Z100.0
X
…
第14页/共22页
切槽加工实例
如何使用手工锯进行切槽与掏空处理

如何使用手工锯进行切槽与掏空处理手工锯是一种常见的木工工具,用于进行切割、掏空和切槽等木材加工任务。
在木工工作中,手工锯是一种简单有效的工具,特别适用于小型工作和局部修剪。
本文将介绍如何正确地使用手工锯进行切槽和掏空处理。
首先,为了确保安全,使用手工锯之前应该戴上适当的防护手套和护目镜。
这样可以防止木屑和碎片进入眼睛,同时保护手部免受切割伤害。
接下来,准备好需要处理的木材。
确保木材稳定地放置在工作台上,并用夹钳或其他夹紧装置固定。
这能提供更好的稳定性和控制性,使操作更加安全和准确。
在使用手工锯切割木材之前,首先确定所需的切槽或掏空部分的位置和大小。
使用一把铅笔或细尺寸的标记工具,在木料上做好标记。
确保标记清晰明确,这将帮助您按照预定的要求进行切割。
选择合适的手工锯。
手工锯通常分为两种类型:十字锯和背锯。
十字锯一般用于切割粗糙木材,而背锯适用于更精细的切割任务。
根据您的需要选择正确类型的锯以确保最佳效果。
开始切割之前,您可以在标记的位置上钻孔。
这将有助于锯子更容易进入并开始切割。
使用适当直径的钻头进行钻孔,并确保孔的深度足够以满足所需的切槽或掏空要求。
现在,您可以开始使用手工锯进行切割。
将锯子的齿部放在标记的位置上,用锯子的沿直线运动来切割材料。
特别注意保持稳定的手臂和手腕姿势,这将有助于实现更准确和平稳的切割。
切割时,不要用过多的力量,使用适当的力量来保持稳定和控制。
在切割或掏空木材时,一定要定期检查切削进展。
这将帮助您确保木材以正确的形式进行切割,避免过度掏空或切割过多。
根据需要,可以使用木工锉或砂纸进行进一步的修整和整理。
切割完成后,务必检查切割区域周围的木材是否平整和光滑。
如果出现木屑或其他不平整的地方,可以使用砂纸进行打磨和修整,以获得最终理想的效果。
最后,一定要将使用的手工锯保持良好的状态。
在使用后,清理锯子上的木屑和尘土,然后将其放置在干燥和安全的位置。
对刃部进行保护,可以使用锯切锋利或刃部保护套,以防止刃口变钝和损坏。
端面切槽加工指南

GFVS-AA
(P.298) GFVT-AA
(P.298)
端面切槽加工
(小口径内圆切槽加工) (2 刀头使用)
端面切槽直径 ø8~
深度 : 2.2mm 宽度 : 1.0, 2.0, 3.0mm
深度 : 2.0mm 宽度 : 1.0, 2.0, 3.0mm
GFV
(P.300) GFVS
(P.302) GFVT
前斜角、侧斜角和前凸起的 组合使肩切槽加工时切屑控 制良好
切屑很容易排出
后凸起使即使是粘性材 料的加工也可以很好地 控制切屑
GBA-MY 3 刀头 . 三座标断屑槽
侧斜角和前凸起产生的窄切屑排 出会产生很好的切槽侧壁表面精 加工效果
安装在刀把后的14° -15°త 前角使切削阻力减小
247
切 槽 加 工
产 品 一 览 表
切槽加工指南
■ 用瓷金刀片切槽加工的指南 ( 一般钢 )
1. 把进刀量设定在 0.12mm/rev 以下(通常为 0.05~0.10mm/ 刃) 2. 推荐用湿式 3. 切削速度设定为 150~220m/min 4. 设定刀把伸长量越短越好。
■ 如何加工出很好光洁度的表面
(P.308)
多功能刀具
(切槽加工)
端面切槽直径 深度 : 13.0~32.0mm
见每页
宽度 : 2.0~6.0mm
深度 : 25.0mm 宽度 : 8.0mm
深度 : 2.2~8.1mm 宽度 : 2.0)
深度 : 25.0~38.0mm 宽度 : 4.0, 5.0mm
■ 端面切槽加工
VNFG
端面切槽加工
(小口径内圆切槽加工) (整体型)
(P.297) PSFG-S
- 1、下载文档前请自行甄别文档内容的完整性,平台不提供额外的编辑、内容补充、找答案等附加服务。
- 2、"仅部分预览"的文档,不可在线预览部分如存在完整性等问题,可反馈申请退款(可完整预览的文档不适用该条件!)。
- 3、如文档侵犯您的权益,请联系客服反馈,我们会尽快为您处理(人工客服工作时间:9:00-18:30)。
切槽的加工过程
对刀 • 启动车床,使工件回转。左手摇动大滑板手柄,右手摇动中滑板手 柄,使车刀刀尖趋近将要加工槽的表面并轻轻接触工件,以此作为 确定背吃刀量的零点位置,然后记住中滑板的刻度。
切槽的加工过程
试车削 • 对刀后,横向进给切削工件1㎜左右时,横向快速退出车刀,停车测 量;根据测量结果计算中滑板应进给的刻度。
切槽的加工过程
使用中、小滑板刻度盘时应注意以下两点: • 由于丝杠和螺母之间有间隙存在,因此在使用刻度盘时会产生空行 程(即刻度盘转动,而刀架并未移动)。根据加工需要慢慢地把刻 度盘转到所需位置,如果不慎多转过几格,不能简单地直接退回多 转的格数,必须向相反方向退回全部空行程,再将刻度盘转到正确 的位置。 • 由于工件在加工时是旋转的,在使用中滑板刻度时,车刀横向进给 后的切除量正好是背吃刀量ap的两倍。因此,当工件外圆余量确定 后,中滑板刻度盘控制的背吃刀量是外圆量的二分之一。而小滑 板的刻度值,则直接表示工件长度方向的切除量。
切槽的加工过程
正常车削 • 切槽加工一般都采用手动横向进给(只有槽深较深,槽宽较宽时候 为了省力采用机动进给)。当车削到所要求的部位时,横向退出车 刀,停车测量。多次进给,直到被加工表面达到图样要求为止。
切槽的加工过程
刻度盘的原理和应用
切槽时,背吃刀量可利用中滑板的刻度盘来控制。 • 中滑板刻度盘安装在中滑板丝杠上。当中滑板的摇动手柄带动刻度 盘转一周时,中滑板丝杠也转一周。这时固定在中滑板上与丝杠配 合的螺母沿丝杠轴线方向移动了一个螺距,因此安装在中滑板上的 刀架也移动了一个螺距。如果中滑板丝杠螺距为5㎜,当手柄转一周
时,刀架就移动了5㎜。若把刻度盘圆周等分100格,当刻度盘转过 一格时,中滑板则移动了5㎜/100=0.05㎜。所以,中滑板刻度盘转
过一格,车刀横向移动的距离可按下式计算:
kP n
式中:P——中滑板丝杠的螺距㎜; n ——刻度盘圆周上等分格数。
切槽的加工过程
小滑板刻度盘用来控制车刀短距离的纵向和斜向移动,其刻度的工作原 理与中滑板相同。