压铸件结构设计及压铸工艺
压铸件结构设计 ppt课件
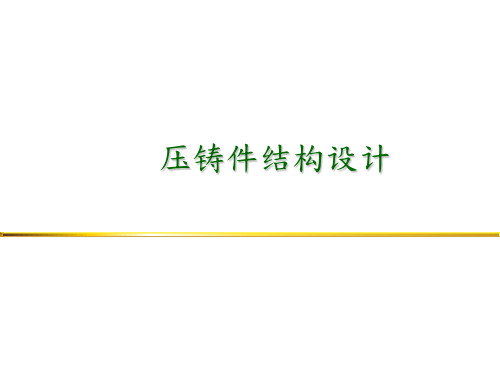
好的案例
说明
深入模穴尽量位置于 制品之同一方向。
型模固定侧之心型形 状﹐应避免因收缩而
固着。
压铸件结构设计
不好的案例
好的案例
说明
切面肉厚较厚处所﹐ 增强肋之厚度应与肉 厚均一。
肉厚需有均一之厚度 。
压铸件结构设计
不好的案例
好的案例
说明
为使深入之增强肋脱 模容易﹐尽量使用最 大之退缩倾斜﹒
阶级部角隅应尽量放 大R来连接。
压铸件结构设计
不好的案例
好的案例
说明
T形切面之接合面将 产生凹陷﹐在心型侧 边缘设置锲入改善之 。
由于型模构造更改﹐ 避免"A"部肉厚过薄 。
压铸件结构设计
压铸件结构设计
压铸件结构设计
同一产品内壁厚应尽量保持一致,且应 平滑过渡,不然容易产生卷气影响产品 强度,壁厚突然过度还会导致厚的地 方产生收缩,粘模,影响外观。
压铸件结构设计
铜合金
D
铝合金
L
锌合金 镁合金
脱模斜度查询表
压铸件结构设计
压铸件结构设计
压铸件结构设计
压铸件结构设计
压铸件结构设计
一般来说,除外模具分型面处外,产品上两壁相连处不管是钝角还是锐角 ,都需要做倒圆角处理。适当圆角不但有利于产品的成型,防止产品 开裂,还能有效的延长模具的寿命。当铸件的内角必须为清角时,应按 以下图片所示做产品结构。
压铸件结构设计
压铸件结构设计
压铸件结构设计
压铸件结构设计
压铸件结构设计
压铸件结构设计
内容大纲
产品的壁厚(模具成型的基础) 产品的拔模(模具脱模的保障) 产品的圆角(模具寿命的关键) 加强筋的设计(结构优化的手段)
压铸件结构设计工艺
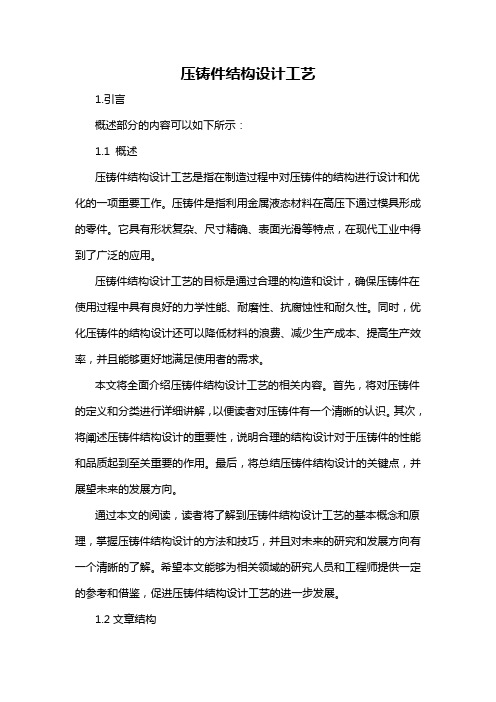
压铸件结构设计工艺1.引言概述部分的内容可以如下所示:1.1 概述压铸件结构设计工艺是指在制造过程中对压铸件的结构进行设计和优化的一项重要工作。
压铸件是指利用金属液态材料在高压下通过模具形成的零件。
它具有形状复杂、尺寸精确、表面光滑等特点,在现代工业中得到了广泛的应用。
压铸件结构设计工艺的目标是通过合理的构造和设计,确保压铸件在使用过程中具有良好的力学性能、耐磨性、抗腐蚀性和耐久性。
同时,优化压铸件的结构设计还可以降低材料的浪费、减少生产成本、提高生产效率,并且能够更好地满足使用者的需求。
本文将全面介绍压铸件结构设计工艺的相关内容。
首先,将对压铸件的定义和分类进行详细讲解,以便读者对压铸件有一个清晰的认识。
其次,将阐述压铸件结构设计的重要性,说明合理的结构设计对于压铸件的性能和品质起到至关重要的作用。
最后,将总结压铸件结构设计的关键点,并展望未来的发展方向。
通过本文的阅读,读者将了解到压铸件结构设计工艺的基本概念和原理,掌握压铸件结构设计的方法和技巧,并且对未来的研究和发展方向有一个清晰的了解。
希望本文能够为相关领域的研究人员和工程师提供一定的参考和借鉴,促进压铸件结构设计工艺的进一步发展。
1.2文章结构文章结构部分的内容如下:1.2 文章结构本文将按照以下几个部分来进行介绍和分析压铸件结构设计工艺。
首先,在引言部分,将对整篇文章进行概述,介绍文章的目的和结构。
接着,正文部分将分为两个主要章节,分别是压铸件的定义和分类以及压铸件结构设计的重要性。
在第一章节中,将详细解释压铸件的定义,并对其进行分类,以便读者更好地理解和掌握压铸件结构设计的工艺。
在第二章节中,将重点探讨压铸件结构设计的重要性,包括其在产品设计中的作用,以及对产品质量、成本和生产效率的影响。
最后,结论部分将总结本文所介绍的压铸件结构设计的关键点,同时对未来的发展方向进行展望。
通过对以上不同章节的详细讲解和分析,读者将能够全面了解压铸件结构设计工艺的相关知识,并能够应用于实际生产中。
压铸件结构工艺设计分解

5、螺纹与齿轮
锌、铝、镁合金的铸件可以直接压铸出螺纹。熔 点高的合金(如铜合金),则因其对模具的螺纹 型腔和型芯的热损坏十分剧烈,螺牙峰谷热裂、 崩损过早,故一般不压铸出螺纹。
压铸螺纹的成型方法
外螺纹的压铸常采用两种方式。
由可分开的两半螺纹型腔构成,是最常见且较
经济的压铸方式。 采用螺纹型环来压铸。但压铸生产时,效率很 低 压铸内螺纹只是在十分必要的情况下才加以采用。
螺纹不宜过长,牙形应是圆头或平头。
压铸齿轮的成型方法
压铸齿轮的最小模数
项 目
铅锡合金 锌合金 铝合金
镁合金
铜合金
模 数
0.3
0.3
0.5
0.5
1.5
精 度
3
33ຫໍສະໝຸດ 33斜 度
在宽度小于20mm时,每面至少有0.05~0.2mm, 而铜合金应为0.1~0.2mm
6、嵌件
嵌铸也称镶铸,它是把金属或非金属的零件(嵌件)先 嵌放在压铸模内,再与压铸件铸合在一起。这样既可充 分利用各种材料的性能(如强度、硬度、抗蚀性、耐磨 性、导磁性、导电性等)以满足不同条件下使用的要求, 又可弥补因铸件结构工艺性差而带来的缺点以解决具有 特殊技术要求零件的压铸问题。
铸件的同轴度和对称度公差 名义 尺寸
~18 >18~50 >50~12 0
同一半型 内的公差
0.10 0.15 0.25
两个半型 内的公差
0.20 0.25 0.35
名义 尺寸
>120~2 60 >260~5 00
同一半型 内的公差
0.35 0.65
两个半型 内的公差
0.50 0.80
4、铸件的表面要求
压铸件结构设计

h2≥0.8mm
a≤3°
压铸件加强筋的运用
3,作为散热加强;
4,作为装饰作用。
2,引导料流流向;
1,加强结构强度;
压铸件结构工艺性分析一
不好的案例
好的案例
说明
于型模中加工凹入文字较之加工凸出文字为困难﹒且模具寿命难以保证,使用后续刻加工﹐则与此相反。
1.5
0.014~0.020
6
0.056~0.084
2
0.018~0.026
7
0.066~0.100
2.5
0.022~0.032
8
0.076~0.116
3
0.028~0.040
9
0.088~0.138
3.5
0.034~0.050
10
0.100~0.160
4
0.040~0.060
合金浇注温度高时,填充时间可选长些。 模具温度高时,填充时间可选长些。 铸件厚壁部分离内浇口远时,填充时间可选长些。 熔化潜热和比热高的合金,填充时间可选长些。
好的案例
说明
陈学民
2021
2023
内容大纲
O1
产品的壁厚(模具成型的基础)
O2
产品的拔模(模具脱模的保障)
O3
产品的圆角(模具寿命的关键)
O4
加强筋的设计(结构优化的手段)
压铸件壁厚的设计
3.5
2.5
3.5
2.5
2.5
2.0
>500
3.0
1.8
3.0
1.8
2.2
1.5
>100~500
2.5
压铸件结构设计
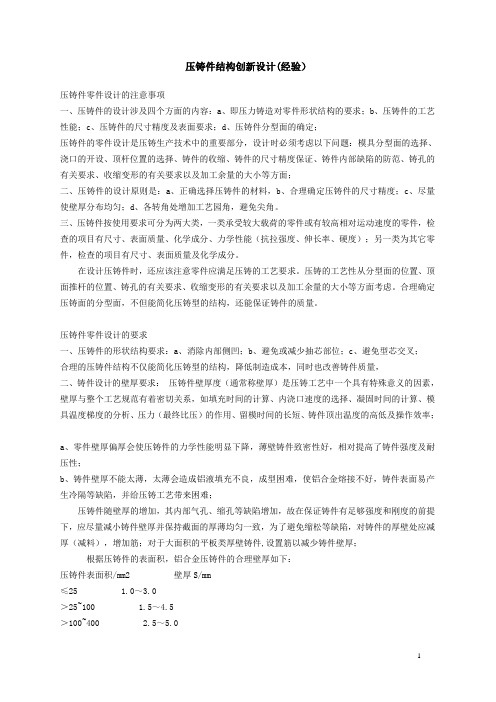
压铸件结构创新设计(经验)压铸件零件设计的注意事项一、压铸件的设计涉及四个方面的内容:a、即压力铸造对零件形状结构的要求;b、压铸件的工艺性能;c、压铸件的尺寸精度及表面要求;d、压铸件分型面的确定;压铸件的零件设计是压铸生产技术中的重要部分,设计时必须考虑以下问题:模具分型面的选择、浇口的开设、顶杆位置的选择、铸件的收缩、铸件的尺寸精度保证、铸件内部缺陷的防范、铸孔的有关要求、收缩变形的有关要求以及加工余量的大小等方面;二、压铸件的设计原则是:a、正确选择压铸件的材料,b、合理确定压铸件的尺寸精度;c、尽量使壁厚分布均匀;d、各转角处增加工艺园角,避免尖角。
三、压铸件按使用要求可分为两大类,一类承受较大载荷的零件或有较高相对运动速度的零件,检查的项目有尺寸、表面质量、化学成分、力学性能(抗拉强度、伸长率、硬度);另一类为其它零件,检查的项目有尺寸、表面质量及化学成分。
在设计压铸件时,还应该注意零件应满足压铸的工艺要求。
压铸的工艺性从分型面的位置、顶面推杆的位置、铸孔的有关要求、收缩变形的有关要求以及加工余量的大小等方面考虑。
合理确定压铸面的分型面,不但能简化压铸型的结构,还能保证铸件的质量。
压铸件零件设计的要求一、压铸件的形状结构要求:a、消除内部侧凹;b、避免或减少抽芯部位;c、避免型芯交叉;合理的压铸件结构不仅能简化压铸型的结构,降低制造成本,同时也改善铸件质量,二、铸件设计的壁厚要求:压铸件壁厚度(通常称壁厚)是压铸工艺中一个具有特殊意义的因素,壁厚与整个工艺规范有着密切关系,如填充时间的计算、内浇口速度的选择、凝固时间的计算、模具温度梯度的分析、压力(最终比压)的作用、留模时间的长短、铸件顶出温度的高低及操作效率;a、零件壁厚偏厚会使压铸件的力学性能明显下降,薄壁铸件致密性好,相对提高了铸件强度及耐压性;b、铸件壁厚不能太薄,太薄会造成铝液填充不良,成型困难,使铝合金熔接不好,铸件表面易产生冷隔等缺陷,并给压铸工艺带来困难;压铸件随壁厚的增加,其内部气孔、缩孔等缺陷增加,故在保证铸件有足够强度和刚度的前提下,应尽量减小铸件壁厚并保持截面的厚薄均匀一致,为了避免缩松等缺陷,对铸件的厚壁处应减厚(减料),增加筋;对于大面积的平板类厚壁铸件,设置筋以减少铸件壁厚;根据压铸件的表面积,铝合金压铸件的合理壁厚如下:压铸件表面积/mm2 壁厚S/mm≤25 1.0~3.0>25~100 1.5~4.5>100~400 2.5~5.0>400 3.5~6.0三、铸件设计筋的要求:筋的作用是壁厚改薄后,用以提高零件的强度和刚性,防止减少铸件收缩变形,以及避免工件从模具内顶出时发生变形,填充时用以作用辅助回路(金属流动的通路),压铸件筋的厚度应小于所在壁的厚度,一般取该处的厚度的2/3~3/4;四、铸件设计的圆角要求:压铸件上凡是壁与壁的连接,不论直角、锐角或钝角、盲孔和凹槽的根部,都应设计成圆角,只有当预计确定为分型面的部位上,才不采用圆角连接,其余部位一般必须为圆角,圆角不宜过大或过小,过小压铸件易产生裂纹,过大易产生疏松缩孔,压铸件圆角一般取:1/2壁厚≤R≤壁厚;圆角的作用是有助于金属的流动,减少涡流或湍流;避免零件上因有圆角的存在而产生应力集中而导致开裂;当零件要进行电镀或涂覆时,圆角可获得均匀镀层,防止尖角处沉积;可以延长压铸模的使用寿命,不致因模具型腔尖角的存在而导致崩角或开裂;五、压铸件设计的铸造斜度要求:斜度作用是减少铸件与模具型腔的摩擦,容易取出铸件;保证铸件表面不拉伤;延长压铸模使用寿命,铝合金压铸件一般最小铸造斜度如下:铝合金压铸件最小的铸造斜度外表面内表面型芯孔(单边)1°1°30′2°铸件的结构工艺性铸件中的基础件都是箱体形结构,并增设了很多加强筋,致使铸件结构形状较为复杂。
压铸产品结构设计的工艺要求

压铸类产品结构设计的工艺要求
压力铸造是将熔融状态或者(半)熔融状态合金浇入压铸机的压室,以极高的速度在高压的作用下充填在压铸模的型腔内,使熔融合金在高压下冷却凝固成型的方法。
常见的压铸材料包括:铝合金、锌合金、镁合金、铜合金等,铝合金又分为铝镁合金、铝铜合金、铝锌合金、铝硅合金等。
压铸类产品在结构设计时的工艺要求注意的几个方面。
①压铸件的厚度
压铸件产品的厚度一般指料厚,料的厚薄直接影响压铸的难易,一般情况下,压铸产品的料厚≥0.8mm,具体料厚根据产品设计。
压铸产品不会因为局部料厚产生缩水的现象,相反,在一些尖钢薄钢处要加料填充,避免模具强度低而损坏。
压铸产品的外观面局部最小料厚≥0.7mm,非外观面局部最小料厚度建议≥0.4mm,太薄会导致填充不良、无法成型,薄的区域面积也不能太大,否则无法成型。
②压铸件的拔模角
压铸件与塑胶件一样,内外表面都需要拔模角,压铸件外表面的
拔模角一般在1°~3°,内表面拔模角比外表面拔模角大一点,方便产品出模。
③压铸件的后续加工
压铸件有时达不到设计的要求,需要后续加工。
其中螺丝柱中的螺纹就是后续加工的,在设计产品时只需留出底孔就可以。
压铸件有深孔时,压铸件需要做出孔位置,再通过后续机械钻孔加工完成。
压铸件有些表面要求较高的精度,一般也需要后续加工,在设计时可在需要后续加工的地方留出加工余量,加工余量一般在0.5mm 左右。
④压铸件产品不能变形,一般是螺丝连接,在做扣位连接,连接的对应产品必须能变形,如塑胶产品等。
⑤压铸件产品加强筋不能太多,对于薄壁类零件,需适当设计加强筋,以增加产品的抗弯强度,防止产品变形损坏。
压铸件的工艺流程
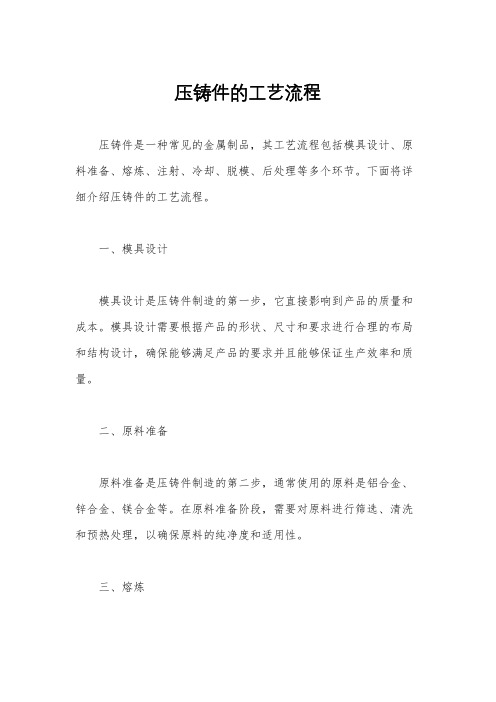
压铸件的工艺流程压铸件是一种常见的金属制品,其工艺流程包括模具设计、原料准备、熔炼、注射、冷却、脱模、后处理等多个环节。
下面将详细介绍压铸件的工艺流程。
一、模具设计模具设计是压铸件制造的第一步,它直接影响到产品的质量和成本。
模具设计需要根据产品的形状、尺寸和要求进行合理的布局和结构设计,确保能够满足产品的要求并且能够保证生产效率和质量。
二、原料准备原料准备是压铸件制造的第二步,通常使用的原料是铝合金、锌合金、镁合金等。
在原料准备阶段,需要对原料进行筛选、清洗和预热处理,以确保原料的纯净度和适用性。
三、熔炼熔炼是将原料加热至熔化状态的过程,通常使用电炉或燃气炉进行熔炼。
在熔炼过程中,需要控制炉温和炉内气氛,确保原料能够完全熔化并且保持一定的温度。
四、注射注射是将熔化的金属液注入模具腔体的过程,通常使用压铸机进行注射。
在注射过程中,需要控制注射速度和压力,确保金属液能够充分填充模具腔体并且形成完整的产品形状。
五、冷却冷却是将注射后的模具进行冷却的过程,通常使用冷却水或风冷设备进行冷却。
在冷却过程中,需要控制冷却速度和温度,确保产品能够快速冷却并且保持一定的结构和硬度。
六、脱模脱模是将冷却后的产品从模具中取出的过程,通常使用振动或冲击的方式进行脱模。
在脱模过程中,需要注意保护产品表面,避免产生划痕或变形。
七、后处理后处理是对脱模后的产品进行去除余料、修磨、喷漆等加工的过程。
在后处理过程中,需要根据产品的要求进行相应的处理,以确保产品的表面光滑、尺寸精度和表面质量。
总结压铸件的工艺流程包括模具设计、原料准备、熔炼、注射、冷却、脱模、后处理等多个环节,每个环节都需要严格控制和操作,以确保产品的质量和成本。
压铸件制造是一个复杂的工艺过程,需要生产厂家具备一定的设备和技术实力,以满足客户的需求。
压力铸造工艺

压力铸造工艺一、压铸及特点1. 压铸定义及特点压力铸造(简称压铸)是在压铸机的压室内,浇入液态或半液态的金属或合金,使它在高压和高速下充填型腔,并且在高压下成型和结晶而获得铸件的一种铸造方法。
由于金属液受到很高比压的作用,因而流速很高,充型时间极短。
高压力和高速度是压铸时液体金属充填成型过程的两大特点,也是压铸与其他铸造方法最根本区别之所在。
比如压射比压在几兆帕至几十兆帕范围内,甚至高达500MPa;充填速度为0.5—120m/s,充型时间很短,一般为0.01-0.2s,最短只有干分之几秒。
2. 压铸的优缺点优点:1) 产品质量好。
由于压铸型导热快,金属冷却迅速,同时在压力下结晶,铸件具有细的晶粒组织,表面坚实,提高了铸件的强度和硬度,此外铸件尺寸稳定,互换性好,可生产出薄壁复杂零件;2) 生产率高,压铸模使用次数多;3) 经济效益良好。
压铸件的加工余量小,一般只需精加工和铰孔便可使用,从而节省了大量的原材料、加工设备及工时。
缺点:1) 压铸型结构复杂,制造费用高,准备周期长,所以,只适用于定型产品的大量生产;2) 压铸速度高,型腔中的气体很难完全排出,加之金属型在型中凝固快,实际上不可能补缩,致使铸件容易产生细小的气孔和缩松,铸件壁越厚,这种缺陷越严重,因此,压铸一般只适合于壁厚在6mm以下的铸件;3) 压铸件的塑性低,不宜在冲击载荷及有震动的情况下工作;4) 另外,高熔点合金压铸时,铸型寿命低,影响压铸生产的扩大应用。
综上所述,压力铸造适用于有色合金,小型、薄壁、复杂铸件的生产,考虑到压铸其它技术上的优点,铸件需要量为2000-3000件时,即可考虑采用压铸。
3.压铸的应用范围压铸是近代金属加工工艺中发展较快的一种高效率、少无切削的金属成型精密铸造方法,是一种“好、快、省”高经济双效益的铸造方法。
压铸零件的形状大体可以分为六类:1)圆盘类——号盘座等;2)圆盖类——表盖、机盖、底盘等;3)圆环类——接插件、轴承保持器、方向盘等;4)筒体类——凸缘外套、导管、壳体形状的罩壳盖、上盖、仪表盖、探控仪表罩、照像机壳与化油器等;5)多孔缸体、壳体类——汽缸体、汽缸盖及油泵体等多腔的结构较为复杂的壳体(这类零件对机械性能和气密性均有较高的要求,材料一般为铝合金)。
压铸件设计

挤压铸造工艺是1937 年由前苏联发明的, 它在二次大战期间为军品有
色金属件的紧急生产曾发挥重要作用, 并已形成较大产业规模。在20 世 纪五六十年代, 先后传入 压铸型设计
压铸型是实现压铸的主要工艺装备,它的设计质量 和制造质量与铸件的形状精度、表面质量和内部质量以 及生产操作的顺利程度有直接的关系,更为重要的是, 压铸型制造好以后,在修改的可能性已不大了,其价格 很高,制造周期长,所以在压铸型设计时必须细致分析 铸件的结构和工作性能的要求,充分考虑生产现场的操 作过程和工艺参数可实施的程度,才能设计出结构合理、 切合实际并能满足生产要求的压铸型。
型架部分 成形部分
4.4.1 压铸型的总体结构
浇注系统
抽芯机构——是阻碍铸件冲压铸型内取出的
成型部分,都必须作成活动的型芯或型块,在
开型前或开型后自铸件中取出.抽出活动型芯
的机构称为抽芯机构
顶出铸件机构——顶出
机构的作用是开型过程
中将铸件顶出铸型,以便
取出铸件
排溢系统
导向零件——包括导柱和
导套,在其闭合后构成型
以Al2Si 状态图为例,随压力升高, 纯铝熔点升高;Al2Si 共晶点向高温 和富硅的方向移动,硅在铝中的 固溶体即α相区扩大,也向高温富硅 方向移动。这将对初晶硅的形成, α相的强化产生一定的影响。
影响合金的宏观晶粒度,细化其显微组织
压力对合金结晶的宏观晶粒度的影响是复杂的,要视其他工艺条件而 定。由于压力结晶会改善合金与铸型壁的热交换条件,使生长中的枝晶破 碎,以形成新晶核,因此,在工艺选配得当的情况下,压力结晶是可以使合金 宏观晶粒细化的。但是工艺不当时,在某些条件下,压力会促进发达柱状 晶的形成。由于合金的显微组织(即枝晶间距或胞晶尺寸) 与其合金成分 及凝固速度有关,因此绝大多数情况下,压力会细化合金的显微组织,对改 善合金力学性能是有利的。
压铸件结构设计和压铸工艺
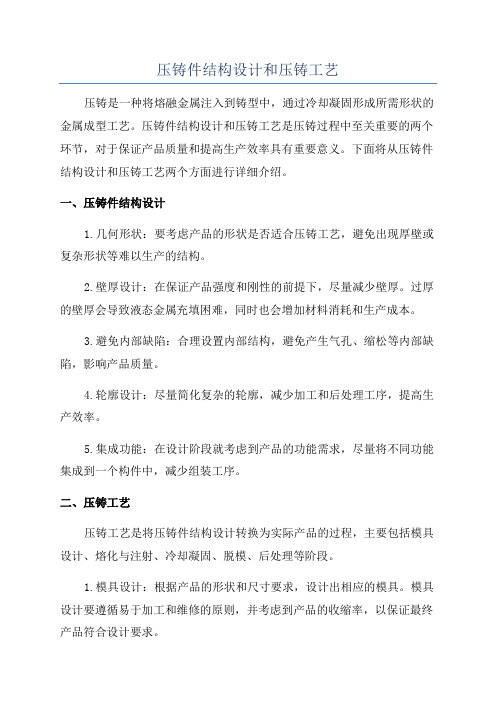
压铸件结构设计和压铸工艺压铸是一种将熔融金属注入到铸型中,通过冷却凝固形成所需形状的金属成型工艺。
压铸件结构设计和压铸工艺是压铸过程中至关重要的两个环节,对于保证产品质量和提高生产效率具有重要意义。
下面将从压铸件结构设计和压铸工艺两个方面进行详细介绍。
一、压铸件结构设计1.几何形状:要考虑产品的形状是否适合压铸工艺,避免出现厚壁或复杂形状等难以生产的结构。
2.壁厚设计:在保证产品强度和刚性的前提下,尽量减少壁厚。
过厚的壁厚会导致液态金属充填困难,同时也会增加材料消耗和生产成本。
3.避免内部缺陷:合理设置内部结构,避免产生气孔、缩松等内部缺陷,影响产品质量。
4.轮廓设计:尽量简化复杂的轮廓,减少加工和后处理工序,提高生产效率。
5.集成功能:在设计阶段就考虑到产品的功能需求,尽量将不同功能集成到一个构件中,减少组装工序。
二、压铸工艺压铸工艺是将压铸件结构设计转换为实际产品的过程,主要包括模具设计、熔化与注射、冷却凝固、脱模、后处理等阶段。
1.模具设计:根据产品的形状和尺寸要求,设计出相应的模具。
模具设计要遵循易于加工和维修的原则,并考虑到产品的收缩率,以保证最终产品符合设计要求。
2.熔化与注射:将所需的金属材料加热至液态,然后通过注射机将熔融金属注入到模具中。
注射过程需要控制注射速度和压力,保证金属充填完整且无气泡。
3.冷却凝固:在模具中进行冷却凝固,使注入的金属逐渐凝固。
冷却过程需要控制温度和时间,以保证产品的结晶组织均匀性和性能稳定性。
4.脱模:凝固后的产品从模具中取出,包括冷却水冲洗和振动脱模等工序。
脱模过程需要注意避免产品的变形和损坏。
5.后处理:包括修磨、去毛刺、清洗、表面处理等工序。
后处理旨在提高产品表面质量和机械性能,并满足特定的外观要求。
总结:压铸件结构设计和压铸工艺是相互关联的,一个合理的结构设计可以提高生产效率和产品质量,而一个良好的压铸工艺可以保证结构设计的实施效果。
因此,在进行压铸件结构设计和压铸工艺选择时,需要综合考虑产品的功能要求、材料特性、生产成本等因素,以达到最佳的工艺效果。
(完整版)压铸件结构设计
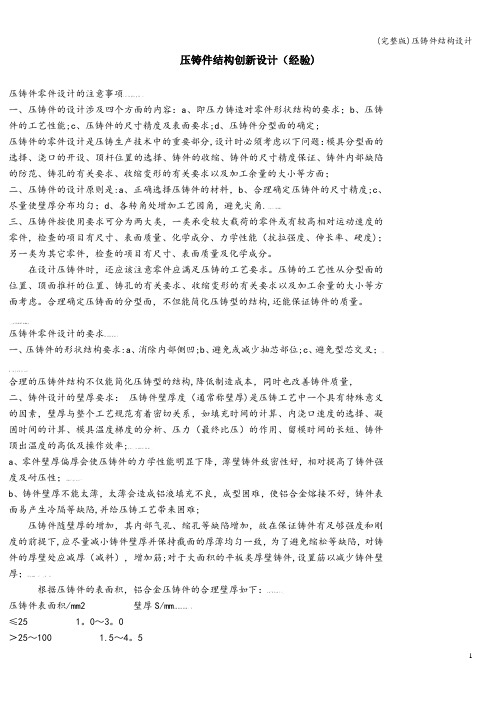
压铸件结构创新设计(经验)压铸件零件设计的注意事项) t) C+ g7 n; g. D!~一、压铸件的设计涉及四个方面的内容:a、即压力铸造对零件形状结构的要求;b、压铸件的工艺性能;c、压铸件的尺寸精度及表面要求;d、压铸件分型面的确定;压铸件的零件设计是压铸生产技术中的重要部分,设计时必须考虑以下问题:模具分型面的选择、浇口的开设、顶杆位置的选择、铸件的收缩、铸件的尺寸精度保证、铸件内部缺陷的防范、铸孔的有关要求、收缩变形的有关要求以及加工余量的大小等方面;二、压铸件的设计原则是:a、正确选择压铸件的材料,b、合理确定压铸件的尺寸精度;c、尽量使壁厚分布均匀;d、各转角处增加工艺园角,避免尖角.( w: i; h5 @8 L三、压铸件按使用要求可分为两大类,一类承受较大载荷的零件或有较高相对运动速度的零件,检查的项目有尺寸、表面质量、化学成分、力学性能(抗拉强度、伸长率、硬度);另一类为其它零件,检查的项目有尺寸、表面质量及化学成分。
在设计压铸件时,还应该注意零件应满足压铸的工艺要求。
压铸的工艺性从分型面的位置、顶面推杆的位置、铸孔的有关要求、收缩变形的有关要求以及加工余量的大小等方面考虑。
合理确定压铸面的分型面,不但能简化压铸型的结构,还能保证铸件的质量。
" _; q( }3 Q0 D7 x0 W6 q压铸件零件设计的要求% l5 X1 A" K; ?一、压铸件的形状结构要求:a、消除内部侧凹;b、避免或减少抽芯部位;c、避免型芯交叉;’ ]1E9 {*]* ~2 |) a. F合理的压铸件结构不仅能简化压铸型的结构,降低制造成本,同时也改善铸件质量,二、铸件设计的壁厚要求:压铸件壁厚度(通常称壁厚)是压铸工艺中一个具有特殊意义的因素,壁厚与整个工艺规范有着密切关系,如填充时间的计算、内浇口速度的选择、凝固时间的计算、模具温度梯度的分析、压力(最终比压)的作用、留模时间的长短、铸件顶出温度的高低及操作效率;* n— _' e. e% J! C* b) _a、零件壁厚偏厚会使压铸件的力学性能明显下降,薄壁铸件致密性好,相对提高了铸件强度及耐压性;1 P# i" q( z/ x" ^b、铸件壁厚不能太薄,太薄会造成铝液填充不良,成型困难,使铝合金熔接不好,铸件表面易产生冷隔等缺陷,并给压铸工艺带来困难;压铸件随壁厚的增加,其内部气孔、缩孔等缺陷增加,故在保证铸件有足够强度和刚度的前提下,应尽量减小铸件壁厚并保持截面的厚薄均匀一致,为了避免缩松等缺陷,对铸件的厚壁处应减厚(减料),增加筋;对于大面积的平板类厚壁铸件,设置筋以减少铸件壁厚;5 \+ v# J f _; V O根据压铸件的表面积,铝合金压铸件的合理壁厚如下:* d" ~0 Z; d! ?( _压铸件表面积/mm2 壁厚S/mm2 Q5 Y8 f6 X2 X$ |' Z≤251。
压铸件结构设计及压铸工艺

压铸件结构设计及压铸工艺压铸件结构设计是指在满足产品功能和使用要求的前提下,通过合理地设计压铸件的结构,使得其具有较好的可靠性、经济性和工艺性。
压铸工艺是将熔化的金属经过高压注入模具中,经冷却固化后得到所需形状和尺寸的工艺过程。
1.功能需求:首先需要明确产品的功能需求,包括产品所需的力学性能、流体性能、电气性能等。
根据功能需求来确定结构形状和尺寸。
2.材料选择:根据产品使用环境和功能需求,选择合适的材料。
材料的选择会影响到压铸件的结构设计。
3.结构强度:压铸件在使用过程中需要承受一定的载荷,因此要考虑结构的强度和刚度问题。
通过合理的布局和加强设计,保证产品在正常使用情况下不会发生失效。
4.成本控制:在结构设计中要考虑到成本因素,通过优化设计和合理选择材料等方式,尽量降低制造成本。
5.工艺性:结构设计需要考虑到压铸工艺的要求。
例如,制造过程中是否需要加工孔、缝隙等,模具是否能够顺利铸造等。
要尽量避免设计上的复杂性,方便生产制造。
压铸工艺是将熔化的金属通过高压注入模具中,并在固化后得到所需形状和尺寸的工艺过程。
压铸工艺一般包括以下几个步骤:1.模具设计:根据压铸件的结构和尺寸要求,设计合适的模具。
模具需要具备良好的冷却性能和顺畅的金属流动性。
2.材料准备:根据产品要求选择合适的金属材料,并进行熔化和调质处理。
熔化后的金属要满足一定的温度和流动性要求。
3.注入模具:将熔化的金属注入到模具中,通过高压力使金属充填模具腔体,保证细节部位的填充。
4.冷却固化:金属在模具中冷却并固化,使其具备一定的力学性能和稳定性。
5.取出铸件:打开模具,将固化好的压铸件取出,并清理剩余的模具材料。
6.补充工艺:根据产品需求,可能需要进行后续的加工和处理工艺,比如热处理、表面处理、组装等。
压铸工艺的选择和优化对产品的质量和成本具有重要影响。
在工艺中需要考虑的因素有:1.注射参数:包括注射速度、注射压力、注射温度等。
这些参数会影响到铸件的成形和凝固过程。
纯铝压铸工艺及压铸模技术要点总结
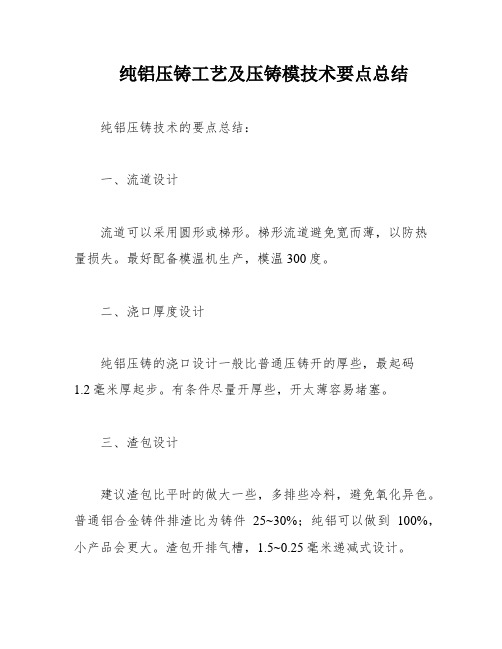
纯铝压铸工艺及压铸模技术要点总结
纯铝压铸技术的要点总结:
一、流道设计
流道可以采用圆形或梯形。
梯形流道避免宽而薄,以防热量损失。
最好配备模温机生产,模温300度。
二、浇口厚度设计
纯铝压铸的浇口设计一般比普通压铸开的厚些,最起码
1.2毫米厚起步。
有条件尽量开厚些,开太薄容易堵塞。
三、渣包设计
建议渣包比平时的做大一些,多排些冷料,避免氧化异色。
普通铝合金铸件排渣比为铸件25~30%;纯铝可以做到100%,小产品会更大。
渣包开排气槽,1.5~0.25毫米递减式设计。
四、顶针孔间隙设计
间隙比普通铝压铸模放大1.5~2.0倍,不会跑料。
五、钢材及热处理
可选用国产8418.热处理:48~50HRC比较合理。
模芯大的更低些,镶针镶件硬度可以高些,易断的部件降低点热处理硬度。
六、铝液温度
保持铝液的稳定性,一般生产在700~730度,也可以高于730度,最高不高于750度,最低不低于700.
七、根据压铸件氧化的颜色需求选择合适的铝含量成份
氧化黑色,建议用铝含量低的铝锭,可以用ADC10.氧化灰色,比如铁灰色,建议铝含量在95~97%的铝锭。
压铸模设计—第五章 压铸件结构设计及压铸工艺
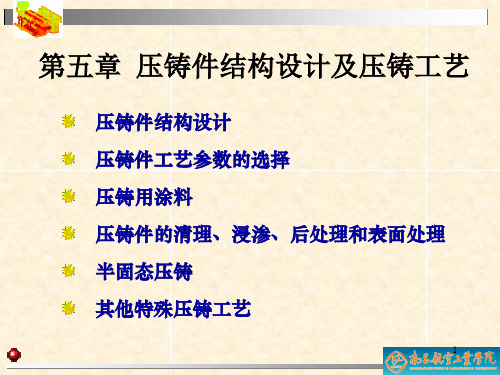
53
二、对涂料的要求
在高温状态下具有良好的润滑性; 挥发点低,在100~150℃,稀释剂能很快挥发; 涂敷性好; 对压铸模和压铸件无腐蚀作用; 性能稳定,在空气中稀释剂不应挥发过快而变稠, 存放期长; 高温时不分解出有害气体,并不会在压铸模型腔 表面产生积垢; 配制工艺简单,来源丰富,价格便宜。
32
表5-14 压铸件平行度、垂直度和倾斜度公差
表5-15 压铸件同轴度和对称度公差
33
(三)表面粗糙度
在填充条件良好的情况下,压铸件表面粗糙度
一般比模具成型表面的粗糙度低两级。
若是新模具,压铸件上可衡量的表面粗糙度应
达到相当于国标GB13l—1989的Ra2.5~6.3mm,也
可能达到Ra0.32mm。
48
表5-21 生产中常用的持压时间
49
2、留模时间
留模时间是指持压时间终了到开模推出压铸 件的时间,以推出压铸件不变形、不开裂的最短 时间为宜。 停留时间过短,由于铸件强度尚低,可能在铸件 顶出和自压铸模落下时引起变形,对强度差的合 金还可能因为内部气孔的膨胀而产生表面气泡。
停留时间太长,则铸件温度过低,收缩大,对抽 芯和顶出铸件的阻力亦大:对热脆性合金还能引 起铸件开裂,同时也会降低压铸机的效率。
表5-7 压铸件基本尺寸公差等级 合金 锌合金 铝(镁 )合金 铜合金 公差等级CT 4-6 5-7 6-8
26
压铸件受分型面或压铸模活动部分影响的尺寸、
应按表5-8规定在基本尺寸公差上再加附加公差。
表5-8 线性尺寸受分型面和压铸模活动部分影响附加的公差
27
2、壁厚、肋厚、法兰或凸缘厚度等尺寸
11
压铸件适宜的壁厚:铝合金为1~6mm,锌合金
压铸件结构设计和压铸工艺

〔一从简化模具结构、延长模具使用寿命考虑
• 避免内侧凹 • 针对要求采取的措施有: • 1>外形不加大,内部形状凸出至底部〔见下图a>. •
2>局部加厚,内形加至底部,外形加至分型面处,从而消除侧 凹〔见下图b> .
3>原凸台形状不改变,在零件底部开出通孔,模型成型镶件 可以从通孔处插入形成台阶〔见下图c>.
8.压铸嵌件 镶铸件的作用有如下几个方面:
1、加强压铸件某些部位的强度、耐磨性、导电性、成绝缘 性等.如:铝中铸人钢件提高强度,铸入蓝宝石提高耐磨 性,铸入绝缘材料降低成本及提高绝缘性,铸入铁心赋予 导磁性等;
2、清除压铸件过于复杂的型腔以及内侧凹形无法压铸的型 腔;
3、消除热节,避免疏松;
4、利用低熔点金属压铸代替贵金属,如用高硅铝代替青铜;
〔四加工余量
压铸件能达到较高的精度,故多数的表面和部件都 不必进行机械加工,便可直接装配使用.同时还有 以下两个原因也不希望对压铸件进行机械加工:
1>压铸件表层坚实耐磨,加工会失去这层好的表皮;
2>压铸件有时有内部气孔存在,分散而细小的气孔 通常是不影响使用的,但机械加工后却成为外露 气孔,反而可能影响使用.
• 压铸件壁厚的极限范围: • 压铸件壁厚的极限范围很难加以限制.通常可按铸件
各个壁厚表面积的总和来选择适宜的壁厚.在零件的工艺 性能好以及压铸生产中又具备良好的工艺条件时,还可以 压铸出更薄的壁. • 这时,锌合金铸件最小壁厚度为0.5mm,铝合金铸件最小 厚度为0.7mm,镁合金铸件最小厚度为0.8mm,铜合金铸件 最小厚度为1mm.
〔±,但其偏差值为CT6级公差的1/2.
3、非配合尺寸,根据铸件结构而定.
压铸产品的结构设计

随着越来越多的产品追求更好看的外观,更高的工艺水平。
压铸在产品中应用的越来越多,比如手机,监视器,灯,甚至特斯拉汽车外壳,随着这些工艺的发展,越来越多的产品会使用到压铸件,因此本文就介绍一下压铸产品的结构设计。
一,了解一下压铸的工艺压铸是一种金属铸造工艺,其特点是利用模具腔对融化的金属施加高压。
根据压铸类型的不同,需要使用冷室压铸机或者热室压铸机。
铸造设备和模具的造价高昂,因此压铸工艺普通只会用于批量创造大量产品。
压铸特殊适合创造大量的中小型铸件,因此压铸是各种铸造工艺中使用最广泛的一种。
同其他铸造技术相比,压铸的表面更为平整,拥有更高的尺寸一致性。
压铸分为热室压铸与冷室压铸。
热室压铸,有时也被称作鹅颈压铸,它的金属池内是熔融状态的液态、半液态金属,这些金属在压力作用下填充模具。
当压铸无法用于热室压铸工艺的金属时可以采用冷室压铸,包括铝、镁、铜以及含铝量较高的锌合金。
压铸模的使用寿命普通是 3 万-8 万次。
压铸模的精度要求越低,合用寿命越长。
二,合用于压铸的材料以及材料的相关特点锌最容易压铸的金属,创造小型部件时很经济,容易镀膜,抗压强度、塑性高,铸造寿命长。
如家具配件、建造装饰、浴室配件、灯饰零件、玩具、领带夹、皮带扣、各种金属饰扣等铝质量轻、创造复杂和薄壁铸件时尺寸稳定性高,耐腐蚀性强,机械性能好,高导热以及导电性,高温下强度依然很高。
铝合金压铸类产品主要用于交通信号灯外壳、拉手、渔轮配件、户外锁、电器产品、通信器材、厨具配件、摩托车散热器及喇叭罩、 LED 灯外壳、照像机器材、散热片、汽车配件、电子通讯器材、电子游戏机外壳等行业,一些高性能、高精度、高韧性的优质铝合金产品也被用于大型飞机、船舶等要求比较高的行业中。
镁易于进行机械加工,强度分量比高,常用压铸金属中最轻。
镁合金有优良的压铸工艺性能:镁合金液粘度低,流动性好,易于充满复杂型腔。
用镁合金可以很容易地生产壁厚 1.0mm~2.0mm 的压铸件,现在最小壁厚可达 0.6mm。
压铸件工艺
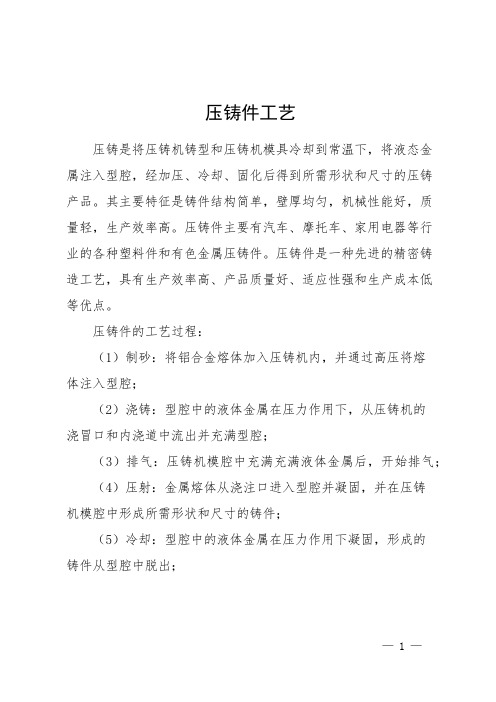
压铸件工艺
压铸是将压铸机铸型和压铸机模具冷却到常温下,将液态金属注入型腔,经加压、冷却、固化后得到所需形状和尺寸的压铸产品。
其主要特征是铸件结构简单,壁厚均匀,机械性能好,质量轻,生产效率高。
压铸件主要有汽车、摩托车、家用电器等行业的各种塑料件和有色金属压铸件。
压铸件是一种先进的精密铸造工艺,具有生产效率高、产品质量好、适应性强和生产成本低等优点。
压铸件的工艺过程:
(1)制砂:将铝合金熔体加入压铸机内,并通过高压将熔
体注入型腔;
(2)浇铸:型腔中的液体金属在压力作用下,从压铸机的
浇冒口和内浇道中流出并充满型腔;
(3)排气:压铸机模腔中充满充满液体金属后,开始排气;
(4)压射:金属熔体从浇注口进入型腔并凝固,并在压铸
机模腔中形成所需形状和尺寸的铸件;
(5)冷却:型腔中的液体金属在压力作用下凝固,形成的
铸件从型腔中脱出;
— 1 —
(6)固化:压铸件经过冷却和固化后,得到所需形状和尺寸的压铸产品。
— 2 —。
压铸工艺及压铸新技术

求要本基定测
GI测定应遵守相关伦理要求。 测定机构设施与条件应符合附录B的要求。
• 开展GI测定的机构应具备食物检验资质和/或临床检验资质。 • 测定机构应能提供安静、舒适、可供受试者静坐及小范围活动的场地。 • 测定机构设有独立的食物准备区、抽血区、血液分离及血糖测定分区等。 • 测定场所应配备抢救或急救基本设施,防止发生应急事件。 • 测试机构应配备从事医学、预防医学、营养学工作的专业人员负责方案
肠-胰岛轴
blood glucos e re s pons e
血糖
胰岛素 胰高血糖素
组织
The re fe re nce food (glucos e or bre ad) has a GI of 100
Plas m a glucos e
100%
40%
Tim e
Tim e
背景
低GI膳食有益于糖尿病等慢性病的预防和控制, 膳食GI成为预防和控制慢性病的一个新概念。
对任何合金系列而言,都是以共晶合金或者结晶温度范围小 的合金具有最好的流动性,而结晶温度范围大的合金压铸性 能差。熔点高的合金都难于压铸。
压铸工艺及模具设计
3.1.2 常用压铸合金及其主要特性 压铸用合金的分类见表3-1。
表3-1 压铸用合金分类
压铸用合金种类
说
明
压铸铁合金
铸铁 铸钢
压铸非铁合 金
NSP
纤维、半纤维,果 胶
] ] ]
全薯碳谷类物 、根茎类 豆水类
] 蔬化菜
] 水合果
] 脱物脂奶
] 糖来作物
] 含源糖饮料
DF高 粗加工 天然
添加
可利用碳水化合物
• 包括糖、淀粉(抗性淀粉除外)和部分具有生血糖作用的 糖醇。
- 1、下载文档前请自行甄别文档内容的完整性,平台不提供额外的编辑、内容补充、找答案等附加服务。
- 2、"仅部分预览"的文档,不可在线预览部分如存在完整性等问题,可反馈申请退款(可完整预览的文档不适用该条件!)。
- 3、如文档侵犯您的权益,请联系客服反馈,我们会尽快为您处理(人工客服工作时间:9:00-18:30)。
27
2、壁厚、肋厚、法兰或凸缘厚度等尺寸
壁厚、肋厚、法兰或凸缘厚度等尺寸公差按表5-9选取。 表5-9 厚度尺寸公差
28
3、圆角半径尺寸
圆角半径尺寸公差按表5-10选取。
表5-10 园角半径尺寸公差
29
4、角度和锥度尺寸
自由角度和自由锥度尺寸公差按表5-11选取。 表5-11 自由角度和自由锥度公差
持压时间应长些, • 对熔点低、结晶温度范围小的薄壁压铸件、持
压时间可以短些。
48
表5-21 生产中常用的持压时间
49
2、留模时间
留模时间是指持压时间终了到开模推出压铸 件的时间,以推出压铸件不变形、不开裂的最短 时间为宜。
停留时间过短,由于铸件强度尚低,可能在铸件 顶出和自压铸模落下时引起变形,对强度差的合 金还可能因为内部气孔的膨胀而产生表面气泡。 停留时间太长,则铸件温度过低,收缩大,对抽 芯和顶出铸件的阻力亦大:对热脆性合金还能引 起铸件开裂,同时也会降低压铸机的效率。
53
二、对涂料的要求
在高温状态下具有良好的润滑性; 挥发点低,在100~150℃,稀释剂能很快挥发; 涂敷性好; 对压铸模和压铸件无腐蚀作用; 性能稳定,在空气中稀释剂不应挥发过快而变稠 ,存放期长; 高温时不分解出有害气体,并不会在压铸模型腔 表面产生积垢; 配制工艺简单,来源丰富,价格便宜。
54
30
5、孔中心距尺寸
孔中心距尺寸公差按表5-12选取。若受模具分 型面和活动部分影响,在基本尺寸公差上也应加附 加公差。
表5-12 孔中心距尺寸公差
31
(二)表面形状和位置
对于压铸件来说,变形是一个不可忽视的问题 ,其公差值应控制在一定的范围内,整形前和整形 后的平面度和直线度公差,平行度、垂直度和倾斜 度公差,同轴度和对称度公差分别按表5-13,表 5-14和表5-15选取。
52
一、压铸涂料的作用
✓ 为压铸合金和模具之间提供有效的隔离保护层,避免金
属液直接冲刷型腔和型芯表面,改善模具的工作条件; ✓ 降低模具热导率,保持金属液的流动性,提高金属的成
型性;
✓ 高温时保持良好的润滑性能,减少压铸件与模具成型部
分尤其是型芯之间的摩擦,便于推出,延长模具寿命, 提高压铸件的表面质量; ✓ 预防粘模(对铝、锌合金而言)。
充填速度过小会使铸件的轮廓不清,甚至 不能成形。 充填速度选择过大,会引起铸件粘型并使 铸件内部气孔率增加,使力学性能下降。
38
充填速度的选择,一般应遵循的原则:
对于厚壁或内部质量要求较高的铸件,应选择 较低的充填速度和高的增压比压; 对于薄壁或表面质量要求高的铸件以及复杂的 铸件,应选择较高的比压和高的充填速度; 合金的浇注温度较低、合金和模具材料的导热 性能好、内浇道厚度较大时,也要选择较高的 充填速度。
39
表5-18 常用的充填速度
40
三、温度参数的选择
(一)合金浇注温度
合金浇注温度是指金属液从压室进入型腔的平 均温度,通常用保温炉内的温度表示,一般高于合 金液相线20~30℃。
浇注温度过高,合金收缩大,使铸件容易产生
裂纹,铸件晶粒粗大,还能造成脆性;
浇注温度过低,易产生冷隔、表面流纹和浇不
足等缺陷;
当压铸件体积确定后,填充时间与内浇口速度 和内浇口截面积之乘积成反比。
46
表5-20 铸件的平均壁厚与充填时间的推荐值
47
(二)持压时间和留模时间
1、持压时间
• 从液态金属充填型腔到内浇道完全凝固时,继 续在压射冲头下的持续时间称为持压时间。
• 持压时间长短取决于压铸件的材料和壁厚。 • 对于熔点高、结晶温度范围大的厚壁压铸件,
压铸件结构设计及压铸工艺
1
第一节 压铸件结构设计
一、压铸工艺对压铸件结构的要求
压铸件结构的合理性和工艺适应性决定了 后序工作能否顺利进行。
分型面的选择 浇道的设计 推出机构的布置 收缩规律的掌握、精度的保证 缺陷的种类及其程度
2
(一)简化模具,延长模具使用寿命
压铸件的分型面上,应尽量避免带有圆角
表5-13 压铸件平面度和直线度公差
32
表5-14 压铸件平行度、垂直度和倾斜度公差 表5-15 压铸件同轴度和对称度公差
33
(三)表面粗糙度
在填充条件良好的情况下,压铸件表面粗糙度 一般比模具成型表面的粗糙度低两级。
若是新模具,压铸件上可衡量的表面粗糙度应 达到相当于国标GB13l—1989的Ra2.5~6.3mm,也 可能达到Ra0.32mm。
50
综上所述,压铸工艺参数中压力、速度、温度 及时间的选择应遵循以下原则:
结构复杂的厚壁压铸件压射力要大; 结构复杂的薄壁压铸件压射速度要快,浇注 温度和模具温度要高; 形状一般的厚壁压铸件持压时间和留模时间 要长。
51
第三节 压铸用涂料
压铸过程中对模具型腔、型芯表面、 滑块、推出元件、压铸机的冲头和压室等 所喷涂的润滑材料和稀释剂的混合物,通 称为压铸涂料。
表5-2 压铸件脱模斜度
18
4、压铸孔和槽
压铸法的特点之一是能够铸出小而深的圆孔、长 方形孔和槽。
表5-3 铸孔最小孔径以及孔径与深度的关系
19
表5-4 压铸长方形孔和槽的深度
20
5、压铸镶嵌件
压铸的另一个特点是可以方便地采用嵌件。
图5-13 镶嵌件上凹槽的尺寸 图5-14 镶嵌螺纹件的尺寸
21
图5-5 压铸件支承部位形状与抽芯
7
图5-6 孔的结构与抽芯
8
(三)方便压铸件脱模和抽芯
图5-7 压铸件形状与抽芯
9
(四)防止变形
图5-8 压铸件结构与变形
10
二、压铸件基本结构的设计
1、壁厚与肋
压铸件壁厚增加,内部气孔、缩孔等缺陷也随之增加, 故在保证铸件有足够强度和刚度的前提下应尽量减少厚 度并保持各截面的厚薄均匀一致。 对铸件的厚壁处,为了避免缩松等缺陷,应通过减薄厚 度并增设加强肋来解决。 设计肋来增加零件的强度和刚性,同时也改善了压铸的 工艺,使金属的流路顺畅,消除单纯依靠加大壁厚而引 起的气孔和收缩缺陷。
43
表5-19 不同压铸合金的压铸模预热温度及工作温度
44
图5-15 压铸件力学性能与压铸模工作温度的关系 1-ZL105 2-ZM5
45
四、充填、持压和开模时间
(一)充填时间
金属液自开始进入型腔到填满所需的时间称为 填充时间。
充填时间长短取决于铸件的体积、壁厚的大小 及铸件形状的复杂程度。 对大而简单的铸件,充填时间要相对长些;对 复杂和薄壁铸件充填时间要短些。
压射比压的选择应根据压铸件的形状、 尺寸、复杂程度、壁厚、合金的特性、温度 及排溢系统等确定,一般在保证压铸件成形
和使用要求的前提下选用较低的比压。
36
表5-17 选择压射比压要考虑的主要因素
37
二、压铸速度的选择
充填速度也是压铸工艺主要参数之一,
充填速度的高低直接影响压铸件的内部和外 观质量。
三、涂料的使用
使用涂料时应特别注意用量,不论是涂刷还是喷涂, 要避免厚薄不均或者太厚; 当采用喷涂时,涂料浓度要加以控制。用毛刷涂刷时 ,在刷后应用压缩空气吹匀; 喷涂或涂刷后,应待涂料中的稀释剂挥发后才能合模 浇注; 喷涂涂料后,应特别注意压铸模排气道的清理、避免 因被涂料堵塞而起不到排气作用。对于转折、凹角部位应 避免涂料沉积,以免造成压铸件的轮廓不清晰。
2、常用的方法
真空加压法。
57
真空加压法的处理工艺
压铸件洗净、烘干,装入浸渗罐,用真 空泵抽真空,使罐内真空度高于80kPa,然 后吸入预热到50~70℃的浸渗剂液体,待完 全覆盖压铸件后,关闭阀门并加0.5~1.0MPa 气压,保持10~15min后除去浸渗液,取出铸 件洗净,经8~24h干燥即成。
两壁丁字形连接
S1/S2<1.75时,R=0.25(S1+S2);
S1/S2>1.75时,加强部位在一壁,
,
加强部位在两壁,h = 0.5(S1+S2)。
图5-11 两壁丁字形连接
16
交叉连接的壁(壁厚不相等时,选最薄的壁厚代入公式) 当
当 当
图5-12 交叉连接时的园角
17
3、铸造斜度
铸造斜度又称脱模斜度。为了便于从压铸模内取 出压铸件和从压铸件内抽出型芯,压铸件应具有足够 的和尽可能大的铸造斜度。
图5-1 避免在分型面上有圆角
3
避免模具局部过薄
图5-2 改进铸件结构保证镶块足够的厚度
4
避免在压铸件上设计互相交叉的盲孔
图5-3 压铸件应避免有互相交叉的盲孔
5
避免内侧凹
图5-4 内侧凹结构及消除
6
(二)改进模具结构、减少抽芯部位
减少不与分型面垂直的抽芯部位,对降低模具的 复杂程度和保证压铸件的精度是有好处的。
随着模具使用次数的增加,通常压铸件的表面 粗糙度值会逐渐变大。
34
(四)加工余量
当压铸件的尺寸精度与形位公差达不到设计要求而需机
械加工时,应优先考虑精整加工,以便保留其强度较高的致
密层。机械加工余量应选用较小值,见表5-16。 表5-16 机械加工余量
35
第二节 压铸工艺参数的选择
一、压铸压力的选择
58
三、压铸件的后处理、表面处理
1、压铸件的后处理
11Leabharlann 压铸件适宜的壁厚:铝合金为1~6mm,锌合金 为l~4mm,镁合金为1.5~5mm,铜合金为2~5mm。
表5-1 压铸件最小和正常壁厚
12
2、铸造圆角
铸造圆角有助于金属液的流动,减少涡流,气体容易 排出,有利于成形; 可避免尖角处产生应力集中而开裂。 对需要进行电镀和涂覆的压铸件更为重要,圆角是获 得均匀镀层和防止尖角处镀层沉积不可缺少的条件。 对于模具来讲,铸造圆角能延长模具的使用时间。没 有铸造圆角会产生应力集中,模具容易崩角,这一现 象对熔点高的合金(如铜合金)尤其显著。