薄壁零件切削参数优化系统研究
薄壁类零件数控加工工艺改进分析研究
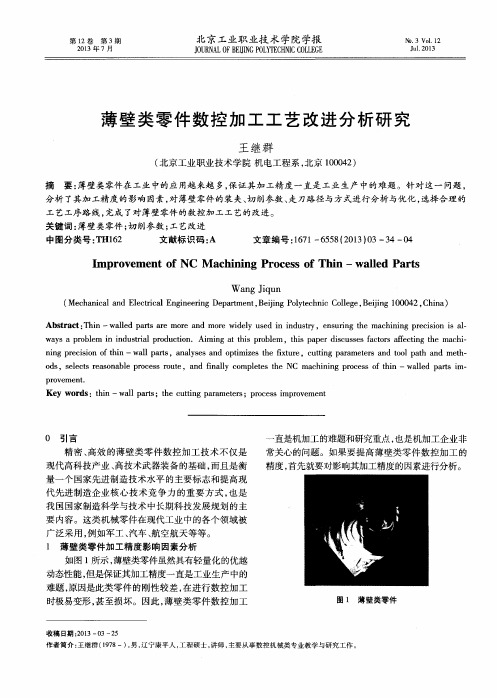
( Me c h a n i c a l a n d E l e c t i r c a l E n g i n e e r i n g D e p a r t m e n t , B e i j i n g P o l y t e c h n i c C o l l e g e , B e i j i n g 1 0 0 0 4 2 , C h i n a )
代先 进制 造企业 核 心 技 术竞 争 力 的重 要 方 式 , 也 是
我 国 国家 制造科 学 与技术 中长期科 技发 展规 划 的主
要 内容 。这类 机械零 件在 现代 工业 中的各个 领域 被 广 泛采用 , 例 如军 工 、 汽车、 航 空航 天等 等 。
1 薄壁 类零 件加 工精 度影 响 因素 分析
作者简介 : 王继群( 1 9 7 8一) , 男, 辽宁康平人 , 工程硕士 , 讲师 , 主要从事数控 机械类专业教学与研究工作 。
第3 期
王继群 : 薄壁类零件数控加 工工艺改进分析研 究
3 5
加 工精 度 是 指 加 工 后 零 件 表 面 的实 际尺 寸 、 形
状、 位 置 的几 何参数 与 图纸 要求 的理想 几何 参数 的符
pr o v e me n t .
Ke y wor ds :t h i n —wa l l pa ts r ;t h e c u t t i n g p a r a me t e r s ;pr o c e s s i mpr o v e me n t
0 引 言
一
直是 机加工 的难题 和研究重点 , 也 是机 加工企 业非
工艺工序路线, 完成 了对薄壁零件的数控加工工艺的改进 。 关 键词 : 薄壁 类零 件 ; 切 削参数 ; 工 艺改进
薄壁零件数控加工工艺质量改进方法

薄壁零件数控加工工艺质量改进方法
薄壁零件在数控加工过程中往往面临一系列质量问题,如变形、振动、表面粗糙度等。
为了有效解决这些问题,我们可以采取以下改进方法来提高薄壁零件的加工质量。
首先,选用适当的加工参数是至关重要的。
合理的加工参数能够控制零件变形和振动的发生。
我们应该根据零件材料的特性、加工设备的性能及工件的尺寸来合理选择切削速度、进给速度和切削深度等参数,确保零件在加工过程中能够保持稳定的状态。
其次,合理设计夹具和刀具也是提高薄壁零件加工质量的重要手段。
薄壁零件因其材料薄弱而容易发生变形和振动,因此我们需要设计稳定而牢固的夹具,以确保零件在加工过程中能够始终保持稳定的位置和形状。
同时,选择合适的刀具也能够减少振动和提高表面光洁度。
此外,采用适当的加工策略也能够改善薄壁零件的加工质量。
在进行高速切削时,可以考虑采用多道次深浅切削的方法,避免一次性过深切削造成零件变形。
同时,在切削过程中要注意冷却润滑和切屑处理,以避免因摩擦产生的热量影响零件的加工质量。
最后,进行必要的表面处理也能够改善薄壁零件的加工质量。
通过进行抛光、打磨和喷砂等表面处理,可以增加零件的表面光洁度和光泽度,提高零件的整体美观度。
总而言之,薄壁零件数控加工工艺质量的改进方法包括选用适当的加工参数、合理设计夹具和刀具、采用适当的加工策略以及进行必要的表面处理。
通过综合运用这些方法,我们可以有效地提高薄壁零件的加工质量,满足客户的需求。
薄壁零件数控加工工艺质量改进措施分析

薄壁零件数控加工工艺质量改进措施分析随着薄壁零件数控加工工艺的不断发展,在现代化高科技产业当中,已经得到了十分广泛的应用,并且成为了衡量制造技术和水平的重要指标。
在航空航天、军事等重要领域当中,薄壁零件都得到了极大的应用。
而在加工工程中,计算机技术和仿真技术更是发挥了不可替代的重要作用。
在现代加工业中应用高精密机床,结合高仿真系统的分析,在薄壁零件的整个加工过程中都起到了十分良好的作用。
一、薄壁零件数控加工工艺质量影响因素(一)零件装夹对加工精度的影响在零件加工过程中,影响加工精度的一个主要原因就是零件自身的刚度。
对此,可以适当的利用装卡夹紧的方法,对加工工艺进行改进,从而使数控工艺的加工精度得到提高。
在数控加工薄壁零件的时候,应当对零件位置、夹紧装置进行细致的分析,详细的分析引起形变的应力部位、作用方向等方面的数据。
可以采用账套、施工圈、辅助支承等专用夹具当作夹紧装置。
利用轴向装卡替代径向装卡,对薄壁环形零件进行处理。
通过以上的方式和手段,能够有效的解决和预防薄壁零件的形变问题。
另一方面,可以对薄壁零件的刚度进行加强,可以临时对薄壁零件的壁厚进行增加,具体方式可以利用浇灌松香、石蜡等方式,浇灌在数控零件的空心处。
在完成薄壁零件的数控加工过程之后,再将这些辅助材料去除即可。
(二)切削角度对切削质量的影响通过具体实践可以看出,如果确定了刀具几何参数、机床结构系统等因素,那么主要影响切削力的原因包括切削宽度、背吃刀量、进给速度、切削速度等。
对于切削质量来说,刀具的角度对其能够产生十分巨大的影响。
将刀具的前、后角适当增大,能够将切削过程中的摩擦和形变情况有效降低,从而使切削力得以降低,减少薄壁零件的形变程度。
另一方面,加工的主、副偏角,也能够对加工精度产生很大的影响。
在加工的过程中,主偏角决定了加工过程中轴向和径向的切削力。
对于一些刚性较差的薄壁零件来说,应当将主偏角尽量趋近于90°,通过以上的方式,能够使零件数控加工的强度得到加强,从而使加工精度得以提高。
薄壁零件数控加工工艺质量的改进方法

薄壁零件数控加工工艺质量的改进方法薄壁零件数控加工工艺质量的改进方法引言:薄壁零件数控加工是现代制造业中常见的加工方式之一,它具有高效、精度高等优点,广泛应用于航空航天、汽车、电子等行业。
然而,由于薄壁零件的特殊性,其加工工艺存在一定的难度和挑战。
本文旨在探讨薄壁零件数控加工工艺质量的改进方法,以提高加工的精度和可靠性。
一、了解薄壁零件的特点与难点1. 薄壁零件的特点薄壁零件是指壁厚相对较薄的零件,通常在0.5mm以下。
其特点包括结构复杂、易变形、加工难度大等。
对于薄壁零件的加工,需要充分理解其特点,以便制定相应的加工工艺。
2. 薄壁零件加工的难点薄壁零件加工存在以下难点:一是加工过程中易引起变形,导致尺寸不准确;二是薄壁零件的剧烈变形会对零件的功能性能和使用寿命产生影响;三是由于加工剩余应力的积累,薄壁零件易发生开裂等问题。
为了克服这些难点,我们需要采取相应的改进方法。
二、改进方法1. 合理选用材料薄壁零件的材料选择直接关系到加工的难易程度和成本。
在选材时,应考虑材料的力学性能、热膨胀系数等因素,并选择具有良好切削性能和抗变形能力的材料。
2. 优化刀具和切削参数刀具的选择和切削参数的确定对薄壁零件的加工至关重要。
合理选择刀具的材料、几何形状和刃口角度,以提高切削效率和切削质量。
通过调整切削速度、进给速度和切削深度等切削参数,可以有效控制加工过程中的变形和表面质量。
3. 改进夹持方式薄壁零件在加工过程中的夹持方式直接影响零件的加工精度和变形情况。
可以采用多点夹持、对称夹持等方式,以提高零件的稳定性和刚度。
合理设计夹具,避免对零件表面产生明显的应力集中,也是重要的改进措施。
4. 控制加工温度和冷却方式薄壁零件的加工过程中,应注意控制加工温度,避免过热造成变形和材料软化。
合理选择冷却方式,可以有效降低加工温度,并提高加工质量。
5. 优化加工路径和策略在数控加工过程中,优化加工路径和策略是提高加工质量和效率的重要手段。
薄壁类零件的车削工艺分析

薄壁类零件的车削工艺分析段立波一.引言薄壁类零件指的是零件壁厚与它的径向、轴向尺寸相比较, 相差悬殊, 一般为几十倍甚至上百倍的金属材料的零件,具有节省材料、结构简单等特点。
薄壁类零件已广泛地应用于各类石油机械部件。
但是薄壁类零件的车削加工是比较棘手的,具体的原因是因为薄壁类零件自身刚性差、强度弱,在车削加工中极容易变形,很难保证零件的加工质量。
如何提高薄壁类零件的加工精度是机械加工行业关心的话题。
二.薄壁类零件车削过程中常出现的问题、原因及解决办法我们在车削加工过程中,经常会碰到一些薄壁零件的加工。
如轴套薄壁件(图1),环类薄壁件(图2),盘类薄壁件(图3)。
本文详细分析了薄壁类零件的加工特点、防止变形的装夹方法、车刀材料、切削参数的选择及车刀几何角度。
进行了大量的实验,为以后更好地加工薄壁类零件,保证加工质量,提供了理论依据。
图1轴套薄壁件图2环类薄壁件图3盘类薄壁件1.薄壁类零件的加工特点1.1因零件壁薄,在使用通用夹具装夹时,在夹压力的作用下极易产生变形,而夹紧力不够零件又容易松动,从而影响零件的尺寸精度和形状精度。
如图4所示,当采用三爪卡盘夹紧零件时,在夹紧力的作用下,零件会微微变成三角形,车削后得到的是一个圆柱体。
但松开卡爪,取下零件后,由于零件弹性,又恢复成弧形三角形。
这时若用千分尺测量时,各个方向直径相同,但零件已变形不是圆柱体了,这种变形现象我们称之为等直径变形。
图4三爪卡盘装夹1.2因零件较薄,加工时的切削发热会引起零件变形,从而使零件尺寸难以控制。
对于膨胀系数较大的金属薄壁零件,如在一次安装中连续完成半精车和精车,由切削热引起零件的热变形,会对其尺寸精度产生极大影响,有时甚至会使零件卡死在芯轴类的夹具上。
1.3薄壁类零件加工内孔中,一般采用单刃镗刀加工,此时,当零件较长时,如果刀具参数及切削用量处理不当,将造成排屑困难,影响加工质量,损伤刀具。
1.4由于切削力和夹紧力的影响,零件会产生变形或振动,尺寸精度和表面粗糙度不易控制。
薄壁类零件车削加工的优化设计
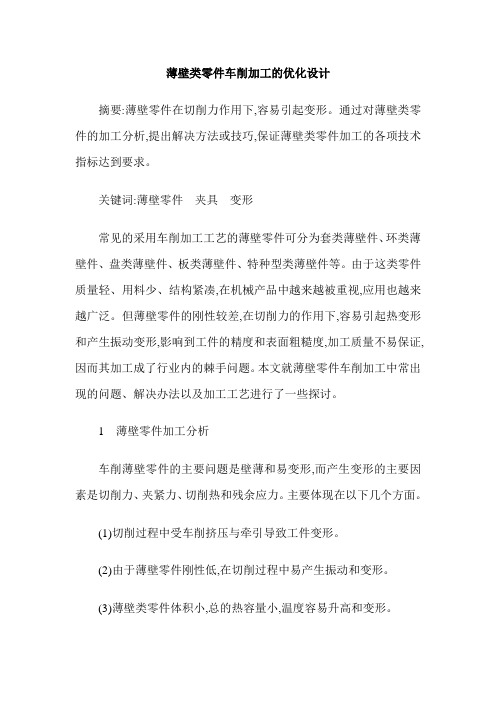
薄壁类零件车削加工的优化设计摘要:薄壁零件在切削力作用下,容易引起变形。
通过对薄壁类零件的加工分析,提出解决方法或技巧,保证薄壁类零件加工的各项技术指标达到要求。
关键词:薄壁零件夹具变形常见的采用车削加工工艺的薄壁零件可分为套类薄壁件、环类薄壁件、盘类薄壁件、板类薄壁件、特种型类薄壁件等。
由于这类零件质量轻、用料少、结构紧凑,在机械产品中越来越被重视,应用也越来越广泛。
但薄壁零件的刚性较差,在切削力的作用下,容易引起热变形和产生振动变形,影响到工件的精度和表面粗糙度,加工质量不易保证,因而其加工成了行业内的棘手问题。
本文就薄壁零件车削加工中常出现的问题、解决办法以及加工工艺进行了一些探讨。
1 薄壁零件加工分析车削薄壁零件的主要问题是壁薄和易变形,而产生变形的主要因素是切削力、夹紧力、切削热和残余应力。
主要体现在以下几个方面。
(1)切削过程中受车削挤压与牵引导致工件变形。
(2)由于薄壁零件刚性低,在切削过程中易产生振动和变形。
(3)薄壁类零件体积小,总的热容量小,温度容易升高和变形。
(4)当每切除一层金属层时,由于应力释放,而引起变形。
(5)装夹时由于径向夹紧力的作用,从而引起变形。
(6)相对位置调整不准,产生壁厚不均,引起工件几何形状变化或变形。
(7)刀具选用不当影响零件的精度和表面粗糙度,造成零件变形。
(8)其他因素引起变形,如机床振动等。
2 解决方法或技巧薄壁零件在车削加工过程中,主要是受到切削力、夹紧力、切削热和残余应力等因素影响而极易产生变形,所以其难点就是如何防止和减小工件的变形,可以通过以下几种方法有效改善加工变形。
2.1 优化装夹方案薄壁工件在装夹中的位置受夹紧力的影响会使工件相对于刀具的位置发生改变。
如用普通三爪自定心卡盘装夹时,由于夹紧力的作用零件会发生变形(变成三角形),导致内孔加工余量出现不均匀;当内孔加工完成后,松开卡盘,零件由于弹性恢复,恢复为圆柱形,而已加工的圆形内孔会变成弧形或三角形,从而产生很大的变形而无法保证加工精度。
基于加工误差综合分析的薄壁件工艺顺序及参数优化方法(精)
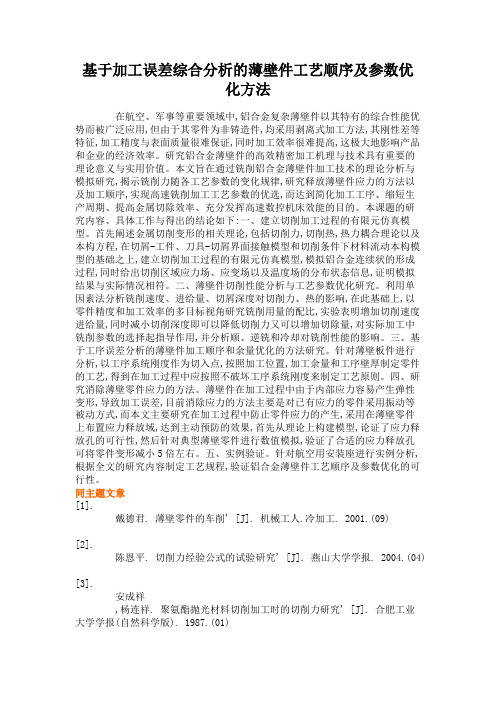
基于加工误差综合分析的薄壁件工艺顺序及参数优化方法在航空、军事等重要领域中,铝合金复杂薄壁件以其特有的综合性能优势而被广泛应用,但由于其零件为非铸造件,均采用剥离式加工方法,其刚性差等特征,加工精度与表面质量很难保证,同时加工效率很难提高,这极大地影响产品和企业的经济效率。
研究铝合金薄壁件的高效精密加工机理与技术具有重要的理论意义与实用价值。
本文旨在通过铣削铝合金薄壁件加工技术的理论分析与模拟研究,揭示铣削力随各工艺参数的变化规律,研究释放薄壁件应力的方法以及加工顺序,实现高速铣削加工工艺参数的优选,而达到简化加工工序、缩短生产周期、提高金属切除效率、充分发挥高速数控机床效能的目的。
本课题的研究内容、具体工作与得出的结论如下:一、建立切削加工过程的有限元仿真模型。
首先阐述金属切削变形的相关理论,包括切削力,切削热,热力耦合理论以及本构方程,在切屑-工件、刀具-切屑界面接触模型和切削条件下材料流动本构模型的基础之上,建立切削加工过程的有限元仿真模型,模拟铝合金连续状的形成过程,同时给出切削区域应力场、应变场以及温度场的分布状态信息,证明模拟结果与实际情况相符。
二、薄壁件切削性能分析与工艺参数优化研究。
利用单因素法分析铣削速度、进给量、切屑深度对切削力、热的影响,在此基础上,以零件精度和加工效率的多目标视角研究铣削用量的配比,实验表明增加切削速度进给量,同时减小切削深度即可以降低切削力又可以增加切除量,对实际加工中铣削参数的选择起指导作用,并分析顺、逆铣和冷却对铣削性能的影响。
三、基于工序误差分析的薄壁件加工顺序和余量优化的方法研究。
针对薄壁板件进行分析,以工序系统刚度作为切入点,按照加工位置,加工余量和工序壁厚制定零件的工艺,得到在加工过程中应按照不破坏工序系统刚度来制定工艺原则。
四、研究消除薄壁零件应力的方法。
薄壁件在加工过程中由于内部应力容易产生弹性变形,导致加工误差,目前消除应力的方法主要是对已有应力的零件采用振动等被动方式,而本文主要研究在加工过程中防止零件应力的产生,采用在薄壁零件上布置应力释放域,达到主动预防的效果,首先从理论上构建模型,论证了应力释放孔的可行性,然后针对典型薄壁零件进行数值模拟,验证了合适的应力释放孔可将零件变形减小5倍左右。
薄片类零件平面磨削工艺参数优化研究

Do : . 9 9 . is . 0 9 0 . 0 1 1 ( ) 4 i1 3 6 / . n 1 0 - 14 2 1 .0 下 .6 0 Js 3
宋 崇金 ’ ,宋 崇寨 ,魏 强 峰 ,张琳琳
S G h n -n , ONG Ch n .h i W E a g fn Z ANG Ln1 ON C o gj 。S i o gz a , I n — g, H Qi e i i n
(. 1 同济大学 机械工程学 院 ,上 海 2 1 0 ;2 郑州煤炭 工业 集团 ,郑 州 4 4 0 ) 084 . 5 0 0 摘 要 :针对 薄片零件 平面磨削过 程中理论 计算温度 与实 际温 度偏差较 大的问题 ,根据移 动热源的 实 际传 递规律并结 合 目前 的两种温度 场理论计 算方法 ,建立 了混合 热传导模 型 ,根据此 模型用 数 学的方法解决 了工 艺优 化问 题。 关键词 : 薄 片零件 ;平面磨削 ;参数优化
ห้องสมุดไป่ตู้0 引言
磨 削 加 工 是 现 代 机 械 制 造 业 中进 行 精 密 加 工
和超精 密加 工的重 要工艺 技术。在 磨削加工 中, 所消耗 的能量 大部分 转化 为热能传 入被磨工 件 ,
1 薄 片零 件 平 面 磨 削 表 面 温 度 场 的 计算理论研 究
传 入 工 件 的 热 量 主 要 集 中 在很 薄 的 表 面 层 里 ,形 成 局 部 高 温 ,这 种 现 象 对 工 件 表 面 质 量 和 工 件 的 使 用 性 能 影 响很 大 。 国 内外 大 量 专 家 学 者 对 磨 削 加 工 中 的 热 效 应 问题 进 行 了研 究 。 14 9 2年 ,J C. . Je e… 首 先 提 出 了 移 动 热 源 理 论 ,O t tr a gr uwa 和 e
数控加工薄壁零件的优化方案

数控加工薄壁零件的优化方案数控加工薄壁零件的优化方案在数控加工薄壁零件的过程中,为了确保零件的质量和加工效率,我们可以采取一系列的优化方案。
下面将逐步介绍这些方案。
第一步:设计优化在进行数控加工之前,优化零件的设计是至关重要的。
首先,我们应该选择适合数控加工的材料,如铝合金或钛合金,这些材料具有良好的可加工性和轻量化的特点。
其次,我们应该尽量避免复杂的形状和尺寸,以减少加工难度。
此外,在设计过程中还应该考虑到零件的结构强度和稳定性,以确保加工后的零件能够满足使用要求。
第二步:工艺优化在进行数控加工之前,我们需要进行工艺优化。
首先,我们应该选择合适的切削工具,如高硬度的硬质合金刀具,以满足加工薄壁零件的高精度要求。
其次,我们应该选择合适的切削参数,如切削速度、进给速度和切削深度,以在确保质量的同时提高加工效率。
此外,我们还应该对加工过程进行充分的冷却和润滑,以避免加工过程中产生过多的热量和切削力,从而减少零件变形的风险。
第三步:夹紧优化在进行数控加工之前,我们需要对零件的夹紧方式进行优化。
首先,我们应该选择合适的夹具,如弹性夹具或真空吸附夹具,以确保零件的位置和稳定性。
其次,我们应该对夹具进行适当的调整和校准,以确保夹具与零件的匹配度和夹紧力的均匀性。
此外,我们还应该避免夹紧力过大或过小,以避免零件的变形和损坏。
第四步:加工优化在进行数控加工之前,我们需要对加工过程进行优化。
首先,我们应该选择适合薄壁零件加工的数控机床和刀具,如高速铣床和高精度刀具,以确保加工的精度和表面质量。
其次,我们应该合理安排加工顺序,尽量避免在薄壁区域进行多次切削,以减少变形的风险。
此外,我们还应该控制加工参数,如加工速度、切削深度和冷却液的使用量,以确保加工的稳定性和一致性。
第五步:后处理优化在完成数控加工之后,我们需要对零件进行后处理。
首先,我们应该对零件进行清洁和除锈,以去除加工过程中产生的污垢和氧化物。
其次,我们应该对零件进行热处理或表面处理,以提高零件的性能和耐腐蚀性。
基于加工误差综合分析的薄壁件工艺顺序及参数优化方法研究的开题报告

基于加工误差综合分析的薄壁件工艺顺序及参数优化方法研究的开题报告一、研究背景及意义薄壁件因其轻、刚、美、便于加工等优点,在汽车、飞机、船舶等重要领域得到广泛应用。
在制造过程中,薄壁件加工误差的控制是实现其优秀性能的关键。
因此,对于薄壁件的加工工艺顺序及参数进行优化,对于提高薄壁件的精度和质量具有重要意义。
二、研究目标和内容该研究旨在通过加工误差综合分析,探究薄壁件加工工艺顺序及参数的优化方法,以提高薄壁件的加工精度和质量。
具体内容包括:1.分析薄壁件的结构特点和加工难点,探讨薄壁件加工误差的来源。
2.基于加工误差综合分析,确定薄壁件加工误差的主要因素,建立薄壁件加工误差的数学模型。
3.探究薄壁件加工工艺顺序的影响因素,通过对比分析不同工艺顺序的加工效果,确定最优工艺顺序。
4.研究薄壁件加工参数的影响因素,探索最佳加工参数组合,实现薄壁件加工过程的优化。
5.设计实验验证理论研究结论的可行性和可靠性。
三、研究方法和技术路线该研究采用实验方法和理论分析相结合的方式进行。
具体技术路线如下:1.收集薄壁件加工相关数据和文献资料,分析薄壁件加工特点。
2.通过数学模型分析探究薄壁件加工误差来源及关键因素。
3.采用正交实验方法研究薄壁件加工工艺顺序对加工误差的影响,确定最优工艺顺序。
4.采用响应面法研究薄壁件加工参数对加工误差的影响,确定最佳加工参数组合。
5.设计实验验证理论研究结论的可行性和可靠性。
四、预期研究成果通过本研究,预计能够获得以下成果:1.系统分析薄壁件加工误差的来源及关键因素,建立加工误差数学模型,提高薄壁件加工精度和质量。
2.探索薄壁件加工工艺顺序和参数的优化方法,实现薄壁件加工过程的优化。
3.设计验证实验,验证理论研究结论的可行性和可靠性。
五、研究难点本研究的难点在于:1.薄壁件加工误差的来源多样化,需要综合考虑各种因素。
2.薄壁件加工工艺顺序和参数的优化方法需要进行多次探索和尝试,确定最佳组合方案。
薄壁零件数控加工工艺质量的改进方法

薄壁零件数控加工工艺质量的改进方法在制造业中,薄壁零件的数控加工一直是一个具有挑战性的工艺。
由于薄壁零件的特殊性,数控加工在保证质量的同时也面临着许多困难。
为了有效地改进薄壁零件数控加工工艺的质量,我们需要综合考虑材料选择、工艺参数优化、加工设备条件等多方面因素。
一、材料选择薄壁零件的加工质量首先取决于材料的选择。
常见的薄壁零件材料包括铝合金、镁合金、不锈钢等。
在选择材料时,需要考虑材料的强度、塑性、热导率等因素,以保证加工过程中材料不易变形、断裂或产生其他质量问题。
材料的表面性能也需要考虑,如氧化膜、油污等对加工过程的影响。
二、工艺参数优化对于薄壁零件的数控加工,工艺参数的优化至关重要。
首先是刀具的选择和刀具路径的设计,需要考虑切削力、切削温度等因素,以减小切削过程中的振动和变形。
其次是切削速度、进给速度和切削深度的合理设置,以保证加工过程中不产生毛刺、毛刺和刀痕等质量问题。
针对不同材料和形状的薄壁零件,还需要采用不同的切削方式和切削策略。
三、加工设备条件薄壁零件的数控加工质量还受到加工设备条件的影响。
在选择数控加工设备时,需要考虑设备的稳定性、精度、刚性等因素,以保证加工过程中稳定、精确地实现设计要求。
加工设备的维护和保养也是关键,定期检查设备的润滑、传动系统、冷却系统等,以保证设备处于良好的工作状态。
个人观点和理解薄壁零件数控加工工艺质量的改进方法是一个综合性的问题,需要在材料、工艺、设备等多个方面进行考虑和优化。
在实际生产中,我们还需要根据具体的零件形式和要求,结合实际情况进行针对性的改进和优化。
随着科学技术的不断发展,新材料、新工艺、新设备的应用也会为薄壁零件的数控加工提供更多的可能性。
总结回顾通过对薄壁零件数控加工工艺质量的改进方法的深入探讨,我们了解到薄壁零件的数控加工质量受到材料选择、工艺参数优化、加工设备条件等多方面因素的影响。
在实际工作中,我们需要综合考虑这些因素,做好准备工作,才能够更好地保证薄壁零件数控加工的质量。
基于切削实验的薄壁件切削用量优化选择

的影 响 。所 以在 加工薄壁件时 , 提高切 削速 度是 很有必要 的。
收 稿 日期 :0 0 0 — 7 2 1- 5 1 作者简介 : 何永强 ( 9 l ) 男 , 1 8 一 , 助教 , 士研究生 , 硕 主要从事先进 制造技术理论及应 用研究 。
E up n Ma u a t n e h o o y N . 2 1 q i me t n f cr gT c n l g o 8, 0 0 i
00 0 . 0
增大 , 因此其加 工变形也随着增大。
l ∞ l O 5 2o o 25 0 3 oU
进给速度( m/ l) m m n
34 铣削变形 随轴 向切深 变化的规律 .
中 图 分 类 号 : G5 12 T 0 . 文献标识码 : A 文 章 编 号 :6 2 5 5 2 1 )8 0 - 3 1 7 — 4 X( 0 0 - 01 0 0 5
随着 铝合金薄壁 件的广泛应 用 , 其应用 价值越 来越 明显 。 而 如何 选择合理 的加工切 削参数 , 就显得非 常重要。以薄壁件
弘
. .
主 3 0
2 6
1 实验 方 案
20 00 20 5o 30 00 30 50 40 00
主轴转速(/ i) r n m
根 据 已有 的铣 削力 数学 模型 【 在 明确 了实验方 案 、 验 l 】 , 实
设 备 、 具 、 件 材 料 、 工 工 艺 前 提 下 , 对 不 同 的 铣 削 用 刀 工 加 针
詈z :
2 O l 8
径向切深( m m )
图 5 铣削 力与径 向切深 n 关 系 E
l 6
l 4 l 2 l 0o l 0 5 20 0 25 0 3 00
薄壁零件加工技术研究

介绍一种所有要素均为薄壁的小型零件加工方法,从工步顺序、刀具选择和工装制作几方面入手,通过制定合适的切冷屏作为超薄壁壳体结构,外形尺寸φ20m m×14m m,壁厚0.2m m左右,零件由多个台阶圆、2个很深的内环槽、锥面和2个凸台组成,内环槽中间的隔板也仅厚0.25mm,结构非常复杂,同时精度要求高,加工难度极大,经过反复分析,找到了独特的解决方法。
1.零件分析零件材料为N C u30-4-2-1蒙乃尔棒,是一种以金属镍为基体添加铜、硅、铁、锰等其他元素而成的合金,其中硅含量高达4%以上,使得此合金比普通蒙乃尔和。
)主要技术难点。
①零件为超薄壁壳体结构,最薄壁厚仅左右,刚性差,最后精加扫码了解更多助理工程师、主管工艺师 高 歌图1 冷屏零件模型冷加工具或者普通磨制刀具使用常规方法无法加工。
④φ6+0.10+0.02mm的通孔12.7mm、深0.3mm孔位于切断面,在首道工序中无法完成,必须分工序加工,而此时零件已工成形,壁厚仅有,刚性差,不仅无合适装夹面,而且易装夹变形,因此,合适的装夹设计十分关键。
⑤材料难切削。
材料为镍基合金,强度高、韧性好,这种金属切削加刀具磨损快,切削振动大,不易切削。
工艺设计件结构复杂,加工余量大,且零件精度高,正常加工时通常选择粗加工、时效去应力再精加工的流程。
但该零件壁薄不易装夹,综合考虑后采用工序尽量集中、减少工序数量、优化刀具几何角度及切削参数以减小零件变形的原则来设计工艺流程。
加工工艺路线为:0下料→5 10数车→15线切割→20检验→25喷砂→30发黑。
5工序数车一道工序中尽可能加工多的结构要素,除切断面上φ12.7mm、深0.3mm孔台阶及大端面上两处凸台外,其余全部在本工序保证,加工完后从毛坯棒上切下。
10工序调头平切断面,加工该面上的φ12.7m m、深0.3m m孔台阶,并且由于刀具悬伸过长,故而安排在本工序镗φ6+0.10+0.02mm孔。
探究铝合金薄壁零件机械加工工艺的优化
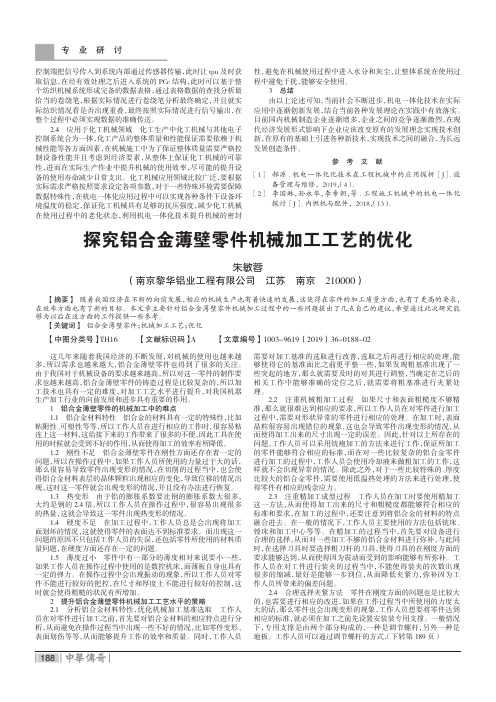
专 业 研 讨控制端把信号传入到系统内部通过传感器传输,此时让tpu及时获取信息,在经有效处理之后进入系统的PCc结构,此时可以基于整个纺织机械系统形成完备的数据表格,通过表格数据的查找分析最恰当的卷绕笔,根据实际情况进行卷绕笔分析最终确定,并且就实际纺织情况看是否出现重叠,最终按照实际情况进行信号输出,在整个过程中必须实现数据的准确传送。
2.4 应用于化工机械领域 化工生产中化工机械与其他电子控制系统合为一体,化工产品的整体质量和性能保证需要依赖于机械性能等各方面因素,在机械施工中为了保证整体质量需要严格控制设备性能并且考虑到经济要素,从整体上保证化工机械的可靠性,进而在实际生产作业中提升机械的使用效率,尽可能的提升设备的使用寿命减少日常支出。
化工机械应用领域比较广泛,要根据实际需求严格按照要求设定各项参数,对于一些特殊环境需要保障数据特殊性,在机电一体化应用过程中可以实现各种条件下设备环境温度的稳定,保证化工机械具有足够的抗压强度,减少化工机械在使用过程中的老化状态,利用机电一体化技术提升机械的密封性,避免在机械使用过程中进入水分和灰尘,让整体系统在使用过程中避免干扰,能够安全使用。
3 总结由以上论述可知,当前社会不断进步,机电一体化技术在实际应用中逐渐创新发展,结合当前各种发展理论在实践中有效落实。
目前国内机械制造企业逐渐增多,企业之间的竞争逐渐激烈,在现代经济发展形式影响下企业应该改变原有的发展理念实现技术创新,在原有的基础上引进各种新技术,实现技术之间的融合,为长远发展创造条件。
参 考 文 献[1] 郝源.机电一体化化技术在工程机械中的应用探析[J].设备管理与维修,2019,(4).[2] 李国琳,孙永华,李希朝,等.工程施工机械中的机电一体化探讨[J].内燃机与配件,2018,(13).探究铝合金薄壁零件机械加工工艺的优化朱敏蓉(南京黎华铝业工程有限公司 江苏 南京 210000)【摘要】 随着我国经济在不断的向前发展,相应的机械生产也有着快速的发展,这使得在零件的加工质量方面,也有了更高的要求,在效率方面也有了新的目标。
薄壁零件数控加工工艺质量改进方法探究
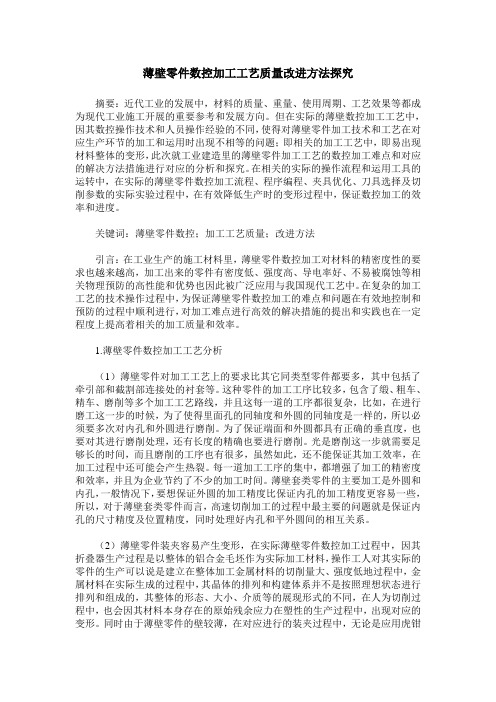
薄壁零件数控加工工艺质量改进方法探究摘要:近代工业的发展中,材料的质量、重量、使用周期、工艺效果等都成为现代工业施工开展的重要参考和发展方向。
但在实际的薄壁数控加工工艺中,因其数控操作技术和人员操作经验的不同,使得对薄壁零件加工技术和工艺在对应生产环节的加工和运用时出现不相等的问题;即相关的加工工艺中,即易出现材料整体的变形,此次就工业建造里的薄壁零件加工工艺的数控加工难点和对应的解决方法措施进行对应的分析和探究。
在相关的实际的操作流程和运用工具的运转中,在实际的薄壁零件数控加工流程、程序编程、夹具优化、刀具选择及切削参数的实际实验过程中,在有效降低生产时的变形过程中,保证数控加工的效率和进度。
关键词:薄壁零件数控;加工工艺质量;改进方法引言:在工业生产的施工材料里,薄壁零件数控加工对材料的精密度性的要求也越来越高,加工出来的零件有密度低、强度高、导电率好、不易被腐蚀等相关物理预防的高性能和优势也因此被广泛应用与我国现代工艺中。
在复杂的加工工艺的技术操作过程中,为保证薄壁零件数控加工的难点和问题在有效地控制和预防的过程中顺利进行,对加工难点进行高效的解决措施的提出和实践也在一定程度上提高着相关的加工质量和效率。
1.薄壁零件数控加工工艺分析(1)薄壁零件对加工工艺上的要求比其它同类型零件都要多,其中包括了牵引部和截割部连接处的衬套等。
这种零件的加工工序比较多,包含了缎、粗车、精车、磨削等多个加工工艺路线,并且这每一道的工序都很复杂,比如,在进行磨工这一步的时候,为了使得里面孔的同轴度和外圆的同轴度是一样的,所以必须要多次对内孔和外圆进行磨削。
为了保证端面和外圆都具有正确的垂直度,也要对其进行磨削处理,还有长度的精确也要进行磨削。
光是磨削这一步就需要足够长的时间,而且磨削的工序也有很多,虽然如此,还不能保证其加工效率,在加工过程中还可能会产生热裂。
每一道加工工序的集中,都增强了加工的精密度和效率,并且为企业节约了不少的加工时间。
薄壁零件加工的切削力模型分析与试验研究

南京航空航天大学硕士学位论文
Key words: Thin-walled structure, cutting force model, regressing-orthogonal experiment, machining deformation, finite element analysis
III
南京航空航天大学硕士学位论文
图清单
图 1.1 原始误差......................................................................................................3 图 2.1 刀具切削运动示意图..................................................................................9 图 2.2 单刃硬质合金刀切削参数示意图............................................................10 图 2.3 车削时的合力与分力................................................................................ 11 图 2.4 切削力计算原理图....................................................................................13 图 2.5 铣削加工时切削层面积示意图...............................................................16 图 2.6 镗削切削力分布平面示意图....................................................................18 图 2.7 镗削切削层分布示意图............................................................................18 图 2.8 镗削力示意图............................................................................................20 图 3.1 切削力随切削深度变化趋势图................................................................24 图 3.2 切削力随切削宽度变化趋势图................................................................24 图 3.3 切削力随进给速度变化趋势图................................................................25 图 3.4 切削力随主轴转速变化趋势图................................................................25 图 3.5 切削力测量及采集系统(右为 Kistler 测力仪) ...................................27 图 3.6 试验加工测量现场(右为铣削平面示意图)........................................28 图 3.7 DynoWare 采集系统参数设置 .................................................................28 图 3.8 试验数据波形图(F-t) ...........................................................................29 图 4.1 铣削台阶面切削层面积示意图................................................................38 图 4.2 切削层面积示意图 (f<r,ae>r) ..................................................................43 图 4.3 切削层面积示意图(f<r,ae<r) ...............................................................44 图 4.4 切削层面积示意图 (f>r,ae>r) ..................................................................44 图 4.5 切削层面积示意图 (f>r,ae<r) ..................................................................45 图 5.1 薄壁零件的加工现场及刀位轨迹平面示意图........................................49 图 5.2 切削力随时间变化波形图........................................................................50 图 5.3 Fz 方向力波形图 .......................................................................................50 图 5.4 Fx 随时间变化波形图 ...............................................................................51 图 5.5 Fx 的 Matlab 仿真曲线图 ..........................................................................51 图 5.6 圆环切削时切入面积变化图....................................................................51 图 5.7 Fy 方向力的实测曲线图 ...........................................................................52 图 5.8 Fy 方向力的仿真曲线图 ...........................................................................52 图 5.9 有限元分析步骤示意图............................................................................53 图 5.10 薄壁零件..................................................................................................54 图 5.11 C3D8R 单元示意图 ................................................................................55
薄壁件加工工艺优化技术研究
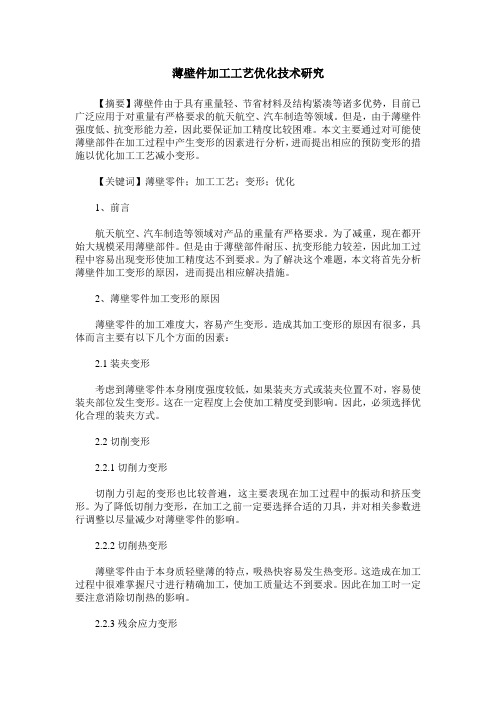
薄壁件加工工艺优化技术研究【摘要】薄壁件由于具有重量轻、节省材料及结构紧凑等诸多优势,目前已广泛应用于对重量有严格要求的航天航空、汽车制造等领域。
但是,由于薄壁件强度低、抗变形能力差,因此要保证加工精度比较困难。
本文主要通过对可能使薄壁部件在加工过程中产生变形的因素进行分析,进而提出相应的预防变形的措施以优化加工工艺减小变形。
【关键词】薄壁零件;加工工艺;变形;优化1、前言航天航空、汽车制造等领域对产品的重量有严格要求。
为了减重,现在都开始大规模采用薄壁部件。
但是由于薄壁部件耐压、抗变形能力较差,因此加工过程中容易出现变形使加工精度达不到要求。
为了解决这个难题,本文将首先分析薄壁件加工变形的原因,进而提出相应解决措施。
2、薄壁零件加工变形的原因薄壁零件的加工难度大,容易产生变形。
造成其加工变形的原因有很多,具体而言主要有以下几个方面的因素:2.1装夹变形考虑到薄壁零件本身刚度强度较低,如果装夹方式或装夹位置不对,容易使装夹部位发生变形。
这在一定程度上会使加工精度受到影响。
因此,必须选择优化合理的装夹方式。
2.2切削变形2.2.1切削力变形切削力引起的变形也比较普遍,这主要表现在加工过程中的振动和挤压变形。
为了降低切削力变形,在加工之前一定要选择合适的刀具,并对相关参数进行调整以尽量减少对薄壁零件的影响。
2.2.2切削热变形薄壁零件由于本身质轻壁薄的特点,吸热快容易发生热变形。
这造成在加工过程中很难掌握尺寸进行精确加工,使加工质量达不到要求。
因此在加工时一定要注意消除切削热的影响。
2.2.3残余应力变形零件在加工过程中受热变形,冷却后就容易产生内应力。
内应力会造成成型零件的变形,考虑到薄壁零件的强度较低,这种变形情况更加严重。
为了尽量消除内应力的影响,需要对成型薄壁零件进行回火热处理,以降低残余应力变形。
3、薄壁零件加工变形的控制通过以上对引起薄壁零件变形的原因进行分析,我们发现可以从以下几个方面来控制薄壁零件加工过程中的变形情况:3.1控制装夹变形的方法3.1.1扇形软爪应用为了减小装夹变形,可以从增大装夹接触面积着手进行优化。
薄壁零件高速铣削工艺与仿真研究的开题报告

薄壁零件高速铣削工艺与仿真研究的开题报告一、研究背景薄壁零件广泛应用于汽车、航空、航天、电子等各个工业领域,对用料节约、重量降低、结构复杂性增强、制造过程提高效率等方面都有着非常显著的作用。
薄壁结构的复杂性和脆弱性使得其在加工过程中容易出现割裂、变形等质量问题,而高速铣削作为一种高效的加工技术,能够有效地解决这些问题,提高加工质量和工艺效率。
因此,对于薄壁零件的高速铣削技术的研究和优化有着非常重要的意义。
二、研究内容和目的本研究旨在对薄壁零件高速铣削工艺进行深入的研究和优化,并通过仿真分析来验证优化效果。
具体研究内容如下:1. 基于薄壁零件的特点,对高速铣削过程中的刀具路径进行设计和优化,以降低零件变形和表面质量。
2. 采用数值仿真的方法,对不同刀具路径的加工过程进行模拟和优化,以验证各种加工策略的优劣。
3. 通过实验验证仿真结果的准确性和可靠性,优化高速铣削工艺参数,提高加工效率和加工质量。
通过以上研究,旨在构建一个完整的薄壁零件高速铣削工艺流程和优化模型,为薄壁零件的高效加工提供有效的技术支撑和理论指导。
三、研究方法和步骤1. 针对薄壁零件的特点,设计合适的高速铣削刀具路径,以降低零件表面质量和变形。
2. 建立高速铣削工艺数值模拟模型,通过仿真分析不同刀具路径的加工过程,验证优化效果。
3. 对模拟结果进行实验验证,比较模拟结果与实验结果的偏差情况,根据实验数据优化模拟模型,确保模拟结果的准确性和可靠性。
4. 通过实验和仿真,结合实际加工情况,优化高速铣削工艺参数。
5. 对优化后的高速铣削工艺进行评价和验证,比较不同工艺参数的加工效率和加工质量。
四、预期成果1. 建立薄壁零件高速铣削工艺优化模型,提供工艺调整和优化依据。
2. 建立薄壁零件高速铣削仿真模型,为优化工艺提供可靠的理论支持。
3. 优化高速铣削工艺参数,提高薄壁零件的加工效率和加工质量,降低生产成本,提高经济效益。
五、研究的创新点1. 针对薄壁零件特点,设计适合的高速铣削刀具路径,提高加工质量和效率。
- 1、下载文档前请自行甄别文档内容的完整性,平台不提供额外的编辑、内容补充、找答案等附加服务。
- 2、"仅部分预览"的文档,不可在线预览部分如存在完整性等问题,可反馈申请退款(可完整预览的文档不适用该条件!)。
- 3、如文档侵犯您的权益,请联系客服反馈,我们会尽快为您处理(人工客服工作时间:9:00-18:30)。
Ab ta t sr c :A i e tt o e o m d a he pr blm f Thi w ald pa t lw te t n a y e o m a in i o e sn , n— l rs o s rngh a d e s d f r to n pr c s i g e
S o,i c n a hive t e t n- a l d pa t i ih pr c s o hih- pe d,e fc e t pr c s i g t a c e h hi w l r s w t h g e ii n, g s e e h f i in o e s n . K e o ds:c tn r m e e s hi - al d w o k c ;c t i g f r e yw r uti g pa a t r ;t n w l e r p i e u tn o c e
摘 要 : 对 薄壁零 件 自身强度低 、 工 易变 形 的 问题 , 过 优化 调 整切 削参数 的 大 小 , 而 调 整 动 态 针 加 通 进 切 削 力大 小和控 制切 削状 态 , 因切 削 力影 响 造 成 薄壁 零 件 的加 工 变形 量 能 满足 公 差要 求 , 使 且使 加 3 状 态始终 处 于稳 定 , - . 降低 切 削震 动造 成 的变形 , 而 实现 薄壁零件 的高精 、 从 高速 、 高效加 工 。
M AO n hu ,ZHANG Xi — a Hu —i g i ln
( . n n Isi t o ce c n e h oo y 1 He a n tue fS in e a d T c n lg ,Xixa g He a 5 0 3,C ia;2 Xixa g Vo ain l t n in n n 4 3 0 hn . n in c t a o
关键 词 : 削参数 ; 壁零件 ; 削力 切 薄 切
中 图 分 类 号 : H1 T 5 T 6; G6 文 献标 识码 : A
Re e r h o ti r m e e s a c n Cu tng Pa a t r Optm i a i n S s e fTh n- le o kp e e i z to y t m o i wa l d W r i c
b p i zn h u t gp rmeest du ti ie a d t e du td n mi c tigf rea d c n rl yo t miigt ec ti aa tr o aj s t sz , n h n aj s y a c u t oc n o to n s n
第 1期
2 1 年 1 月 01
组 合 机 床 与 自 动 化 加 工 技 术
M od a a hi ul r M c ne Too l& Aut m a e acurng Te hn qu
N0. 1
J an.2 11 0
c ti g s a e I c n m a e d f r a in o hn- l d Pat , a e u t g f r e u tn tt . t a k e o m to ft i wal rs c us d by c ti o c ,m e tt lr n e r q ie e n e o e a c e ur - m e t ,a o e sn t t l a en tbl,a e u e t e o m a in c us d by u tn b ai n. n s nd pr c s i g s ae aw ys b i g sa e nd r d c he d f r to a e c ti g vir to
O 引 言 切 削参 数 是 影 响加 工 过 程 的主 要 因 素 , 于 切 关
削参 数优 化 , 目前 大 多 数 的 研 究 主 要 是 基 于 生 产 效 率 和 生 产 成 本 为 目 标 函 数 进 行 优 化 , 变 形 控 制 为 以 目标 函 数 的 研 究 较 少 。 但 是 对 于 薄 壁 零 件 切 削 而 言 , 于 薄 壁 零 件 结 构 复 杂 , 对 刚 度 较 低 , 切 削 由 相 在 加 工 中 极 易 发 生 加 工 变 形 , 成 壁 厚 上 厚 、 薄 尺 寸 造 下 超 差 等问题 。 在 装 夹 情 况 、 具 情 况 、 件 情 况 等 相 同 的 前 提 刀 工
文 章 编 号 :0 1—2 6 2 1 ) 1—0 9 10 2 5( 0 1 0 0 9—0 2
薄 壁 零 件切 削 参 数 优 化 系统 研 究
毛 新 华 , 慧 玲 张
( . 南科 技学 院 , 南 新 乡 1河 河 4 3 0 2 新 乡职 业 技 术 学 院 , 南 新 乡 5 0 3; . 河 4 30 ) 5 0 3
下 , 壁 零 件 变 形 主 要 是 受 动 态 切 削 力 和 切 削 时 是 薄
几 何精度 、 刀具 震 动 、 具 磨 损 、 件 内应 力 、 件 受 力 刀 工 工 变 形 、 件 装 夹 影 响 等 。 对 于 薄 壁 零 件 而 言 , 为 其 刚 工 因 度 小 , 加 工 过 程 中受 残 余 应 力 、 夹 力 、 削 力 、 削 在 装 切 切 热 等 因 素 影 响极 易 发 生 加 工 变 形 和 切 削 振 动 , 致 加 导