油箱焊接机器人工作站20120414
焊接机器人工作站
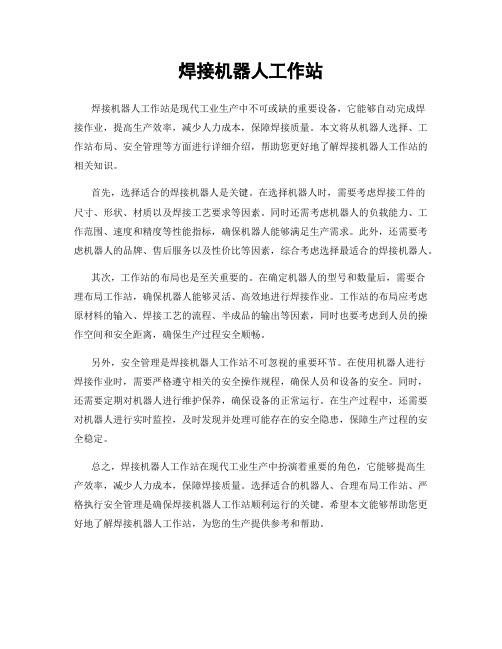
焊接机器人工作站
焊接机器人工作站是现代工业生产中不可或缺的重要设备,它能够自动完成焊
接作业,提高生产效率,减少人力成本,保障焊接质量。
本文将从机器人选择、工作站布局、安全管理等方面进行详细介绍,帮助您更好地了解焊接机器人工作站的相关知识。
首先,选择适合的焊接机器人是关键。
在选择机器人时,需要考虑焊接工件的
尺寸、形状、材质以及焊接工艺要求等因素。
同时还需考虑机器人的负载能力、工作范围、速度和精度等性能指标,确保机器人能够满足生产需求。
此外,还需要考虑机器人的品牌、售后服务以及性价比等因素,综合考虑选择最适合的焊接机器人。
其次,工作站的布局也是至关重要的。
在确定机器人的型号和数量后,需要合
理布局工作站,确保机器人能够灵活、高效地进行焊接作业。
工作站的布局应考虑原材料的输入、焊接工艺的流程、半成品的输出等因素,同时也要考虑到人员的操作空间和安全距离,确保生产过程安全顺畅。
另外,安全管理是焊接机器人工作站不可忽视的重要环节。
在使用机器人进行
焊接作业时,需要严格遵守相关的安全操作规程,确保人员和设备的安全。
同时,还需要定期对机器人进行维护保养,确保设备的正常运行。
在生产过程中,还需要对机器人进行实时监控,及时发现并处理可能存在的安全隐患,保障生产过程的安全稳定。
总之,焊接机器人工作站在现代工业生产中扮演着重要的角色,它能够提高生
产效率,减少人力成本,保障焊接质量。
选择适合的机器人、合理布局工作站、严格执行安全管理是确保焊接机器人工作站顺利运行的关键。
希望本文能够帮助您更好地了解焊接机器人工作站,为您的生产提供参考和帮助。
油箱焊接机器人工作站20120414
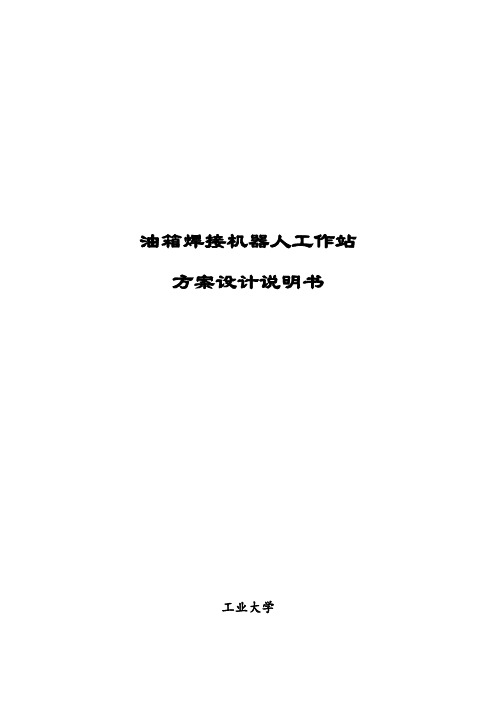
油箱焊接机器人工作站方案设计说明书工业大学2012年4月油箱焊接机器人工作站方案设计说明书一、项目容➢设备名称:油箱焊接机器人工作站➢设备数量:一个工作站,包括一套机器人和两个焊接工位➢设备用途:本工作站用于各规格油箱的焊接二、工件技术规格➢工件材料:低碳钢(16Mn)➢焊缝规格:指接焊缝➢工件厚度:2mm➢工件尺寸:700×700×2000mm(最大规格)➢工件重量:约为500Kg左右➢焊前工艺:手工点固。
三、油箱焊接机器人工作站总体方案说明3.1焊接工艺油箱为方形结构,焊缝形式为指接形式,焊缝宽度为2+2共4mm。
若采用CO2/MAG 焊接方式,那么由于焊缝宽度有限,只能采取小电流来进行焊接,而由于工件属于结构件,焊缝缝隙会有较大变化,这时若加大送丝填充缝隙,会带来焊接电流的增加,易发生咬边烧蚀等焊接问题。
TIG焊接方法有电弧稳定,能量集中的优点,相比较CO2/MAG,更容易控制焊接稳定性。
通过填丝的方式满足焊缝的工艺要求,而且在焊缝缝隙较大的位置可以提高送丝速度来填充金属,而不会影响焊接参数。
由于工件产量不高而且为高质量要求的工件,因此该方案选用TIG焊接方法进行工件焊接。
3.2机器人机器人柔性度高,只需要编制相对应机器人程序,即可满足于多种规格型号工件的焊接需要。
此外,为了减少工件变形,需要在焊接时按照一定的焊接顺序和焊接方向进行焊接,机器人完全可以满足这样的焊接要求。
目前,机器人主要制造商集中在欧洲和日本。
日本机器人虽然在使用寿命,机械刚度,扩展功能相对于欧洲机器人略逊一筹,但是物美价廉。
不过日本机器人存在对军工企业的限制问题。
本方案采用日本安川公司的MOTOMAN MH6机器人,MOTOMAN机器人全世界销量第一,而且在国较早成立中日合资公司,主要销售、技术、售后服务均是中国技术人员,限制较少。
3.3焊接工位由于焊缝分布在工件6个面上,因此需要变位机对工件进行翻转变位才能使机器人焊接到所有焊缝。
焊接机器人工作站方案

焊接机器人工作站方案一、引言在现代工业生产中,焊接是一项常见而重要的工艺。
而随着科技的发展和机器人技术的成熟,焊接机器人在工业生产领域中发挥着越来越重要的作用。
焊接机器人工作站方案,就是为了有效地实现焊接作业的自动化和智能化,提高生产效率和质量水平。
本文将从软硬件设计、工作流程和优势等方面论述焊接机器人工作站方案的相关内容。
二、软硬件设计焊接机器人工作站方案的一项核心任务就是设计出符合工业生产需求的软硬件系统。
首先,软件方面需要开发出适配焊接机器人的程序,包括控制算法、路径规划、任务调度等。
这些程序需要能够实现焊接作业的自动化,并且能够根据工件的不同形状和尺寸进行灵活调整。
同时,还需要具备数据采集和分析的功能,以便进行工艺参数的优化和质量控制。
硬件方面,则需要设计出适应焊接机器人工作站的工作环境和工作需求的硬件设备。
这包括焊接机器人本身,焊接工装、夹具等。
焊接机器人需要具备高精度、高稳定性和强大的负载能力,以确保焊接作业的质量和效率。
而焊接工装和夹具的设计需要结合具体的工件形状和尺寸,以确保焊接过程中工件的稳定性和精度。
三、工作流程焊接机器人工作站的工作流程主要包括工件上料、焊接作业和工件下料。
在工件上料环节,焊接机器人需要通过视觉系统或其他传感器来感知和定位工件的位置和朝向,并且将其准确地摆放在焊接工装上。
在焊接作业环节,焊接机器人根据程序的指令,沿着预定的路径进行焊接作业。
同时,在焊接过程中还需要实时监测焊接参数和质量,以便及时调整和纠正。
最后,在工件下料环节,焊接机器人将焊接完成的工件从焊接工装上取下并放置到指定位置。
四、优势焊接机器人工作站方案相较于传统人工焊接具有诸多优势。
首先,焊接机器人可以连续、高速、精确地进行焊接作业,从而提高生产效率。
其次,焊接机器人不受工作环境的限制,可以在狭小或有害的空间中进行操作,减少了对工作人员的健康和安全的影响。
此外,焊接机器人还可以通过数据采集和分析,进行生产质量的监控和优化,提高产品的一致性和稳定性。
汽车油箱托架机器人焊接工装的制作方法
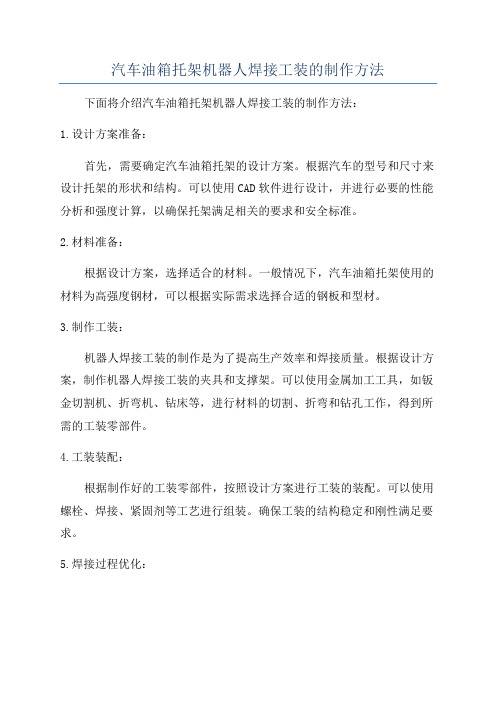
汽车油箱托架机器人焊接工装的制作方法下面将介绍汽车油箱托架机器人焊接工装的制作方法:1.设计方案准备:首先,需要确定汽车油箱托架的设计方案。
根据汽车的型号和尺寸来设计托架的形状和结构。
可以使用CAD软件进行设计,并进行必要的性能分析和强度计算,以确保托架满足相关的要求和安全标准。
2.材料准备:根据设计方案,选择适合的材料。
一般情况下,汽车油箱托架使用的材料为高强度钢材,可以根据实际需求选择合适的钢板和型材。
3.制作工装:机器人焊接工装的制作是为了提高生产效率和焊接质量。
根据设计方案,制作机器人焊接工装的夹具和支撑架。
可以使用金属加工工具,如钣金切割机、折弯机、钻床等,进行材料的切割、折弯和钻孔工作,得到所需的工装零部件。
4.工装装配:根据制作好的工装零部件,按照设计方案进行工装的装配。
可以使用螺栓、焊接、紧固剂等工艺进行组装。
确保工装的结构稳定和刚性满足要求。
5.焊接过程优化:在进行实际焊接之前,可以使用仿真软件对焊接过程进行模拟和优化。
确定焊接路径和参数,以提高焊接质量和生产效率。
可以考虑使用机器人焊接系统来实现焊接过程的自动化,减少人力成本和提高工艺稳定性。
6.焊接和质检:根据焊接工艺中所需的焊接方法和参数进行实际焊接。
在焊接完成后,需要进行质检,检查焊缝的质量和焊接工艺的一致性。
如有问题,需要进行修补和调整。
7.表面处理和喷涂:完成焊接和质检后,对汽车油箱托架进行表面处理,如除锈、打磨等。
然后进行喷涂处理,使用合适的防腐漆和喷涂设备,保护托架表面,延长其使用寿命。
总之,汽车油箱托架机器人焊接工装的制作方法包括设计方案准备、材料准备、制作工装、工装装配、焊接过程优化、焊接和质检、表面处理和喷涂等步骤。
通过科学的制作方法和工艺流程,可以制作出质量优良的汽车油箱托架,提高生产效率和产品质量。
基于视觉跟踪的货车油箱焊接机器人工作站设计

机器人技术44 ROBOT TECHNOLOGY前言重型货车的油箱一般采用铝合金制成,油箱的截面为带圆角的方形,箱体部件为两个端盖和筒体,分别冲压和焊接成形,主要焊缝包括直缝和两端的环缝。
建造焊接机器人工作站,进行自动化焊接生产,可以大幅提高焊接质量和生产效率[1]-[3]。
由于铝合金材料的厚度,表面氧化膜和电弧特性,采用传统的接触寻位和电弧跟踪容易出现焊偏,烧穿及撞枪等问题,造成产品的报废,因此,需采用目前最先进和最具发展前景的激光焊缝跟踪技术。
1基于视觉传感器的焊接机器人工作站整体设计铝合金油箱机器人焊接系统由两台Fronius 焊接机器人、头尾式焊接变位机、MIG 双脉冲焊接电源、激光跟踪系统、机器人控制柜等组成,如图1所示,为提高效率,系统采用双机器人双工位结构,焊缝激光跟踪技术实现了机器人自动焊缝寻位,激光束扫描焊缝位置,随焊缝变化调整焊枪位置及高度,取代了人工对焊枪的调整,真正实现无人值守自动焊接,Touch Sensor 通过触头确定工件位置,系统从而计算出焊缝的位置,实现了对油箱加油口、放油口等装配误差较大的工件的自动焊接。
图1 油箱焊接机器人工作站整体模拟图2工作站关键组成部分设计 2.1双Fronius 焊机为尽可能提高生产效率,系统采用双Fronius 机器人同时焊接两端环缝的方案,旋转变位机旋转一周,两条环缝同步进行焊接,整个工作站设置两个工位,一个工位进行焊接时,另一个工位用于装卸工件,两个机器人侧挂方式安装在带有1轴导轨的固定龙门架上,可以左右移动在两个工位上焊接。
Fronius 焊机大部份功能由软件控制,减少了40%的电子元件数量,外置送丝机重量为15Kg ,移动方便,同加长中间连线配合,可焊接30米范围内的工件。
焊机逆变频率高达100KHz 远高于同类逆变焊机,输出规范平稳,电弧稳定,并且其可以调节电弧推力大小,进行全方位的焊接工作,焊机内存80组焊接专家系统,基于视觉跟踪的货车油箱焊接机器人工作站设计基于视觉跟踪的货车油箱焊接机器人工作站设计武汉理工大学 能动学院 王鹏洁武汉理工大学 工程训练中心 郑卫刚摘 要:针对货车油箱的焊接特点与Fronius 焊接机器人的焊接特性,采用MIG 焊方法,设计了一种新型的油箱焊接机器人工作站,重点对焊接机器人工作站结构进行了新型设计,采用双焊接机器人双工位焊接结构,并配置最先进的激光焊缝跟踪系统,大大提高了生产效率。
焊接机器人工作站方案设计

焊接机器人工作站方案设计一、设计要求:1.提高生产效率:通过自动化的焊接过程,减少人工干预,提高焊接效率,提高生产线产能。
2.提高焊接质量:机器人焊接能够保持稳定的焊接参数,消除人为因素对焊接质量的影响,提高焊接工艺的稳定性和一致性。
3.减少人员劳动强度:将繁重、危险的焊接工作交给机器人完成,减少人员的劳动强度,提高工作安全性。
4.提高工作环境:减少焊接过程中产生的噪音、烟尘和废气等有害物质对工作环境和员工健康的影响,提高工作环境的舒适度。
二、机器人选择:根据焊接工艺的需要,可以选择适合的焊接机器人类型,如MIG/MAG焊接机器人、TIG焊接机器人等。
选择时要考虑机器人的焊接能力、灵活性、质量稳定性和维护成本等因素,并与具体的工作站设计需求相匹配。
三、工作站布局:1.工作台设计:根据工件的大小和形状,设计工作台的尺寸和结构,以便机器人可以方便地对焊接位置进行定位和操作。
2.焊接设备布置:安装焊接机器人和辅助设备,如焊枪、焊接电源等,合理利用空间,确保设备之间有足够的间距和通道,方便维护和操作。
3.安全设施设置:设置安全围栏、安全门、光栅等安全设施,确保机器人工作时的安全性,防止人员误入危险区域。
四、安全性:1.安全保护装置:在机器人周围设置安全保护装置,如防护罩、安全围栏和光栅等,防止机器人误伤人员或受到外部干扰。
2.紧急停止按钮:设置紧急停止按钮,以便在紧急情况下能够迅速停止机器人运动,保护人员和设备的安全。
3.安全教育培训:对相关人员进行安全教育培训,使其熟悉机器人操作规程、事故预防和紧急情况处理,提高安全意识。
综上所述,焊接机器人工作站的方案设计应综合考虑工作站的需求和机器人的选择,合理布局工作站,确保安全性。
随着科技的不断发展,焊接机器人工作站在工业生产中的应用将会越来越广泛,为提高生产效率、质量和安全性做出更大的贡献。
机器人工作站

油箱焊接机器人工作站技术方案●焊接对象:油箱端盖点定●需方公司:●供方公司:编制日期:2011月09月20日油箱焊接机器人工作站方案书1、焊接对象:熔化极CO2混合气体保护焊●工件名称:微型车油箱●工件品种:以用户提供图纸为准●工件材料:碳钢●工件焊前状态:未点定焊接●工件外形图:2、焊接工艺:●焊缝形式:对接焊缝、角焊缝;●焊接工艺:接工艺(MAG);机器人焊接工艺;焊丝采用Φ0.8mm盘式焊丝;焊接机器人选用日本MOTOMAN公司生产的专用同轴式弧焊机器人SSA-2000;焊接电源选用日本MOTOMAN公司生产的机器人专用MOTOWELD-SR350逆变焊接电源;焊枪选用日本MOTOMAN公司生产的机器人专用空冷MAG焊枪;●上下料方式:人工上下料方式;3、设备概述:油箱焊接机器人工作站主要用于完成对微型车油箱通气管、加油管类工件环缝的自动焊接,固定坐式机器人工位及焊接变位机工位采用H型双工位平行布局方式;其中焊接工位分别由一套夹具固定平台和焊接工装夹具组成。
即油箱焊接机器人工作站采用壹套固定座式焊接机器人+两套焊接夹具平台+两套焊接夹具(通气管和加油管各壹套)的组合方式。
当机器人作为双工位焊接时,两个工位能进行预约焊接,一个工位焊接的同时另一工位进行工件的装卸,有效提高机器人使用率和生产效率。
为方便进行多种规格工件焊接及参数设置,控制系统采用三菱PLC+工业触摸屏方式进行控制和操作。
⏹设备布局方式:H型双工位平行工位布局;两套焊接夹具平台对称布置,坐式机器人安装在两套变位机的中间,工作站设置全封闭式安全围栏。
⏹机器人周边系统:设置清枪、剪丝及喷硅油装置,程序设定焊枪进行清枪、剪丝或喷硅油,避免焊枪堵死,造成焊接缺陷;设置全封闭式安全围栏,防止无关人员在工作时间进入焊接区域。
⏹工作站控制系统:采用三菱PLC+工业触摸屏主控方式,系统的启动、停止以及暂停、急件等均可通过操作盘进行;系统的运行状态及系统报警可在操作盘上显示。
150314s02-油箱焊接机器人工作站.doc

职业教育机电一体化专业教学资源库企业解决方案名称:《油箱焊接机器人工作站》编制人:邮箱:电话:编制时间:编制单位:XXXXXXX《油箱焊接机器人工作站》解决方案该工作站由弧焊机器人ARCMAN-MP、焊接电源UC500、1轴变位机组成,机器人控制轴数为7轴, 能够方便实现油箱高效、可靠的自动焊接。该系统结构紧凑,生产效率高,手动夹具设计,操作工序简便。
目录系统概要 (01)系统构成和规格 (01)操作方法和流程 (17)制造、安装、运转分工范围 (18)系统概要◎油箱焊接机器人工作站技术特点专门针对中厚板焊接领域开发优化的神钢机器人系统,具有完善的中厚板焊接解决方案及非常成熟的实践经验;夹具为手动柔性结构,最优化设计,适用标书要求各规格工件。
使用快捷、可靠;该系统为设备本身及人员提供了充分的安全保障和良好的工作环境。
◎适用工件(1)工件名称: 油箱(2)工件规格:最大质量500kg (含有夹紧夹具质量)(3)组对情况:有。
点焊点位置基本固定,焊点焊角高小于3mm。
组对间隙应小于2mm,当间隙大于2mm时应该手工补焊,补焊焊缝均匀。
(4)焊缝坡口形式:按图纸要求。
◎焊接条件焊接方法: 气体保护电弧焊接Ar(80%)+CO2 (20%)焊接姿势: 水平焊接焊丝: φ1.2mm,实芯焊丝焊丝伸出长度: Φ1.2mm-22mm系统构成和规格◎系统构成(表中数量为1套系统所属数量)◎各部的规格和构成◆焊接机器人ARCMAN-MP技术规格:机器人本体6自由度・多关节型机器人、220kg◆ARCMAN的标准功能◆接触传感功能焊丝接触传感功能是开始点传感、3方向传感、焊接长传感、圆弧传感、根隙传感、多点传感等的集合。
机器人通过焊丝端部传感电压,检测焊接工件偏差、坡口尺度,记忆工件或焊缝位置,利用这些功能,可以使焊接过程不受由于工件的加工、组对拼焊和焊接装夹定位带来的误差的影响,自动寻找焊缝并识别焊接情况,保证能够顺利地焊接。
机器人焊接工作站

机器人焊接工作站机器人焊接工作站是一种自动化焊接设备,它通过预先编程的程序,能够完成各种焊接任务。
它具有高效、精准、稳定的特点,广泛应用于汽车制造、航空航天、电子电器等行业。
下面我们将详细介绍机器人焊接工作站的组成、工作原理以及应用领域。
首先,机器人焊接工作站由机器人、焊接设备、控制系统和安全系统组成。
机器人是整个工作站的核心,它能够根据预先设定的程序,进行精准的动作控制。
焊接设备包括焊枪、焊丝等,用于实际的焊接操作。
控制系统则负责指挥机器人和焊接设备的工作,保证整个焊接过程的稳定性和精准度。
安全系统则是为了保障操作人员和设备的安全,包括防护罩、安全传感器等。
其次,机器人焊接工作站的工作原理是通过预先编程的程序,控制机器人和焊接设备的动作,实现焊接操作。
首先,操作人员需要设定焊接工艺参数和焊接路径,并将其输入到控制系统中。
然后,机器人根据这些参数和路径进行动作控制,完成焊接操作。
在整个焊接过程中,控制系统会实时监测焊接质量和设备状态,确保焊接质量和工作安全。
最后,机器人焊接工作站在汽车制造、航空航天、电子电器等行业有着广泛的应用。
在汽车制造领域,机器人焊接工作站能够实现车身焊接、零部件焊接等工艺,提高生产效率和焊接质量。
在航空航天领域,机器人焊接工作站能够完成航空器构件的精密焊接,确保航空器的安全性和可靠性。
在电子电器领域,机器人焊接工作站能够完成电子零部件的精细焊接,提高产品的稳定性和可靠性。
综上所述,机器人焊接工作站是一种高效、精准、稳定的自动化焊接设备,具有广泛的应用前景。
随着工业自动化水平的不断提高,机器人焊接工作站将在更多领域发挥重要作用,推动工业生产的发展。
焊接机器人工作站系统的构成
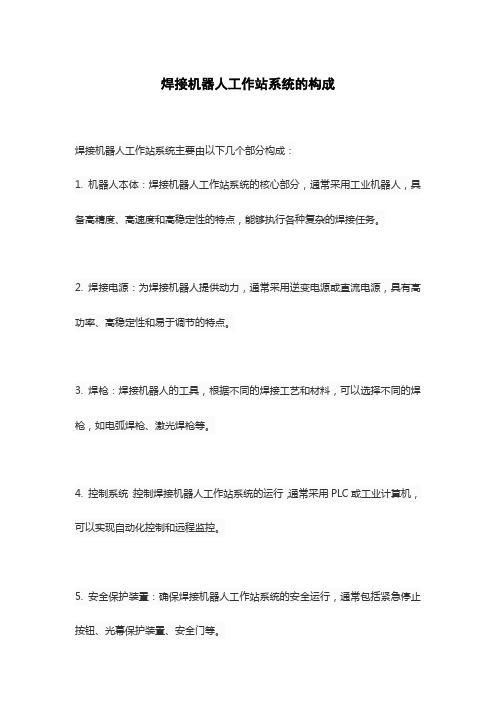
焊接机器人工作站系统的构成
焊接机器人工作站系统主要由以下几个部分构成:
1. 机器人本体:焊接机器人工作站系统的核心部分,通常采用工业机器人,具备高精度、高速度和高稳定性的特点,能够执行各种复杂的焊接任务。
2. 焊接电源:为焊接机器人提供动力,通常采用逆变电源或直流电源,具有高功率、高稳定性和易于调节的特点。
3. 焊枪:焊接机器人的工具,根据不同的焊接工艺和材料,可以选择不同的焊枪,如电弧焊枪、激光焊枪等。
4. 控制系统:控制焊接机器人工作站系统的运行,通常采用PLC或工业计算机,可以实现自动化控制和远程监控。
5. 安全保护装置:确保焊接机器人工作站系统的安全运行,通常包括紧急停止按钮、光幕保护装置、安全门等。
6. 焊接夹具:固定待焊接工件,保证焊接质量和精度,通常由定位器、夹紧机构和支撑结构组成。
7. 输送装置:将待焊接工件输送到焊接位置,通常采用输送带、搬运机械手等装置。
8. 通风系统:排除焊接过程中产生的烟尘和废气,保证工作环境清洁和工人健康。
9. 冷却系统:对机器人本体和焊接电源进行冷却,保证设备的正常运行和使用寿命。
10. 视觉系统:辅助机器人进行定位和跟踪,提高焊接精度和自动化程度,通常包括激光扫描仪、摄像头等装置。
以上是焊接机器人工作站系统的主要构成部分,各部分协同工作,共同完成焊接任务。
在实际应用中,根据不同的需求和场景,还可以进行定制化配置,以满足不同的生产需求。
【FJ0904000】油箱机器人焊接系统方案说明书
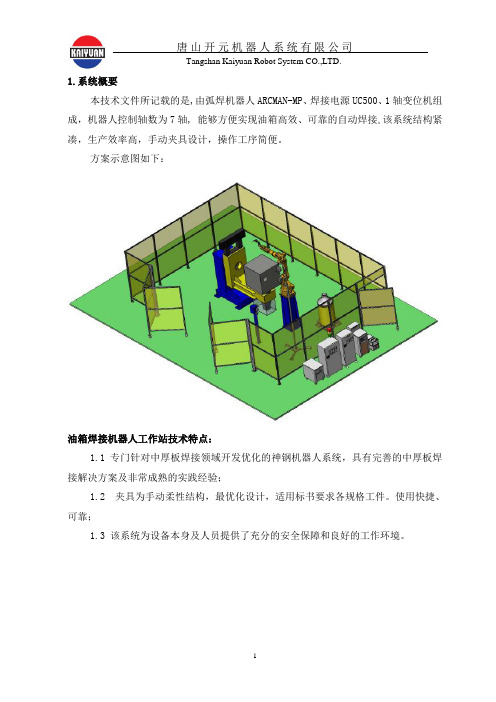
1.系统概要本技术文件所记载的是,由弧焊机器人ARCMAN-MP、焊接电源UC500、1轴变位机组成,机器人控制轴数为7轴, 能够方便实现油箱高效、可靠的自动焊接。该系统结构紧凑,生产效率高,手动夹具设计,操作工序简便。
方案示意图如下:油箱焊接机器人工作站技术特点:1.1 专门针对中厚板焊接领域开发优化的神钢机器人系统,具有完善的中厚板焊接解决方案及非常成熟的实践经验;1.2 夹具为手动柔性结构,最优化设计,适用标书要求各规格工件。
使用快捷、可靠;1.3 该系统为设备本身及人员提供了充分的安全保障和良好的工作环境。
2.适用工件(1)工件名称: 油箱(2)工件规格:最大质量500kg (含有夹紧夹具质量)(3)组对情况:有。
点焊点位置基本固定,焊点焊角高小于3mm。
组对间隙应小于2mm,当间隙大于2mm时应该手工补焊,补焊焊缝均匀。
(4)焊缝坡口形式:按图纸要求。
3.焊接条件(20%)焊接方法 : 气体保护电弧焊接 Ar(80%)+CO2焊接姿势 : 水平焊接焊丝 : φ1.2mm,实芯焊丝焊丝伸出长度: Φ1.2mm-22mm4.系统构成和规格4.1. 系统构成(表中数量为1套系统所属数量)4.2.各部的规格和构成4.2.1焊接机器人ARCMAN-MP技术规格: 1套※1 接触传感功能焊丝接触传感功能是开始点传感、3方向传感、焊接长传感、圆弧传感、根隙传感、多点传感等的集合。
机器人通过焊丝端部传感电压,检测焊接工件偏差、坡口尺度,记忆工件或焊缝位置,利用这些功能,可以使焊接过程不受由于工件的加工、组对拼焊和焊接装夹定位带来的误差的影响,自动寻找焊缝并识别焊接情况,保证能够顺利地焊接。
其优势在于焊枪不需要外加其他设备,以施焊焊丝为检测传感器,精度高,可达性好。
<1> 开始点传感功能开始点传感功能是,在焊接中预先检测焊接线的中央位置,其与示教时工件的偏移量作为纠正量,纠正以后的焊接线的位置偏移的功能。
原创技术方案10:油箱焊接机器人工作站技术方案
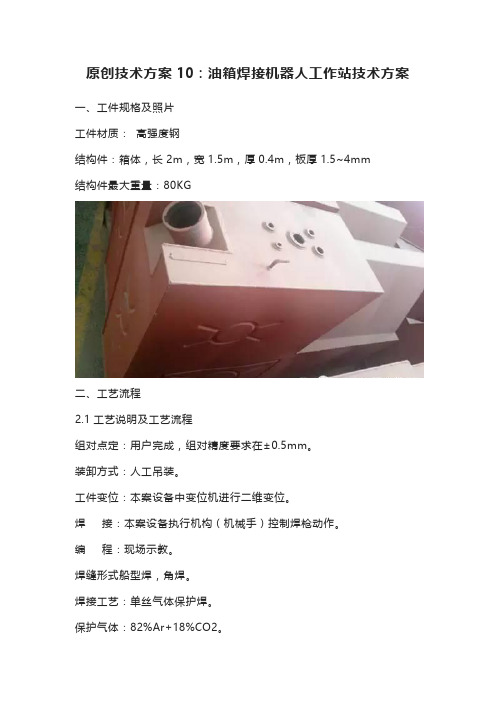
原创技术方案10:油箱焊接机器人工作站技术方案一、工件规格及照片工件材质:高强度钢结构件:箱体,长2m,宽1.5m,厚0.4m,板厚1.5~4mm结构件最大重量:80KG二、工艺流程2.1工艺说明及工艺流程组对点定:用户完成,组对精度要求在±0.5mm。
装卸方式:人工吊装。
工件变位:本案设备中变位机进行二维变位。
焊接:本案设备执行机构(机械手)控制焊枪动作。
编程:现场示教。
焊缝形式船型焊,角焊。
焊接工艺:单丝气体保护焊。
保护气体:82%Ar+18%CO2。
焊接可达率:90%人工组对点焊后吊装至工作位置,机器人进行焊接。
特别说明:为了便于夹持定位,厂家需在油箱的一侧压两个定位坑。
2.2工件模型及装夹形式组对工装组对状态组对工装无工件状态三、设备简介3.1设备简述本案提供的设备用于以上所提到的工件的自动化焊接。
设备主要由弧焊机器人、焊接电源、焊接变位机、清枪剪丝站、控制系统等组成。
采用一套单机器人双工位焊接工作站,满足24小时三班连续作业工作能力。
操作人员只需将组对点固好的工件放到变位机上,利用圆锥定位,然后另一端直接顶紧,调用相关程序即可完成的自动化焊接。
具有高效、快捷、稳定可靠等特点。
工作站基础采用混凝土地基结构。
机器人动作协调采用6+2+2+1模式,即六轴机器人、双工位二维变位机,回转立柱,全部协调控制。
对于焊缝偏差,采用接触传感寻位和激光跟踪解决。
3.2工作站参考布局图平面布置图(占地面积:6*6米)三维效果图3.3设备配置清单序号名称型号及配置生产厂家数量备注弧焊机器人1 弧焊机型号:KUKA Robot KR5-倒挂德国1含10 防碰撞传感器KS-1德国TBI1套11 激光跟踪仪加拿大赛融1套12 清枪剪丝站1套13 备品备件1套14 随机工具1套15 配套资料设备整机说明书\机器人操作说明书(中文)\操作手册(中文)\编程手册(中文)\维修手册(中文)各1本四、主要非标设计件4.1焊接工装4.4.2机器人支承立柱4.3C型两轴变位机参数:1)承重:单工位500KG2)可装工件:2000 mm *1500 mm *500mm 3)旋转角度:360度。
焊接机器人工作站系统的构成

焊接机器人工作站系统的构成焊接机器人工作站系统是一个集成了自动化、智能化和精密化技术的先进设备,其构成主要包括焊接机器人、工作台、控制系统、安全系统和配套设备等几个方面。
下面我将详细介绍这几个方面的构成。
一、焊接机器人焊接机器人是焊接工作站系统的核心部件,通常包括机器人臂、焊枪、传感器和控制系统等。
焊接机器人通常采用多轴关节型机器人,如六轴机器人,其关节灵活可调,适用于多种焊接工艺和位置。
焊接机器人的臂部采用轻量化材料,结构设计紧凑,可以灵活移动和操作,适应不同焊接角度和位置的需求。
焊接机器人的焊枪通常采用自动送丝和气体保护系统,能够实现高效、精密的焊接操作。
焊接机器人还配备各种传感器,如视觉传感器、力传感器等,以实现精确的焊接控制和质量检测。
二、工作台焊接机器人工作台是焊接作业的基础设施,通常包括工作平台、夹具、定位装置和辅助设备等。
工作平台是焊接机器人的操作平台,通常采用平整、耐高温的工作面板,方便焊接机器人进行移动和定位操作。
夹具是用于固定焊接工件的装置,通常采用可调节、可定位的结构设计,以适应不同形状和尺寸的工件夹持需求。
定位装置则是用于确保焊接工件的准确定位,通常采用机械、气动或液压传动装置,能够实现精确定位和夹持。
辅助设备如焊接辅助工具、夹具换装装置等也是工作台的重要构成部分,能够提高焊接作业的效率和质量。
三、控制系统焊接机器人工作站的控制系统是系统的大脑,负责对焊接机器人和配套设备进行精确的控制和协调。
控制系统通常由上位机和下位机组成,上位机用于焊接程序的编制、仿真和监控,下位机则负责对机器人和设备的实时控制和数据反馈。
控制系统还包括相关的传感器、执行器和通讯设备,以实现对焊接机器人和工作站的全面控制和监控。
现代焊接机器人工作站的控制系统通常采用PLC(可编程序逻辑控制器)或CNC(计算机数控)技术,能够实现高精度、高效率的焊接操作。
四、安全系统安全系统是保证焊接机器人工作站安全运行的重要保障,包括防护装置、急停装置、安全监控设备和安全培训等方面。
- 1、下载文档前请自行甄别文档内容的完整性,平台不提供额外的编辑、内容补充、找答案等附加服务。
- 2、"仅部分预览"的文档,不可在线预览部分如存在完整性等问题,可反馈申请退款(可完整预览的文档不适用该条件!)。
- 3、如文档侵犯您的权益,请联系客服反馈,我们会尽快为您处理(人工客服工作时间:9:00-18:30)。
油箱焊接机器人工作站方案设计说明书工业大学2012年4月油箱焊接机器人工作站方案设计说明书一、项目容➢设备名称:油箱焊接机器人工作站➢设备数量:一个工作站,包括一套机器人和两个焊接工位➢设备用途:本工作站用于各规格油箱的焊接二、工件技术规格➢工件材料:低碳钢(16Mn)➢焊缝规格:指接焊缝➢工件厚度:2mm➢工件尺寸:700×700×2000mm(最大规格)➢工件重量:约为500Kg左右➢焊前工艺:手工点固。
三、油箱焊接机器人工作站总体方案说明3.1焊接工艺油箱为方形结构,焊缝形式为指接形式,焊缝宽度为2+2共4mm。
若采用CO2/MAG 焊接方式,那么由于焊缝宽度有限,只能采取小电流来进行焊接,而由于工件属于结构件,焊缝缝隙会有较大变化,这时若加大送丝填充缝隙,会带来焊接电流的增加,易发生咬边烧蚀等焊接问题。
TIG焊接方法有电弧稳定,能量集中的优点,相比较CO2/MAG,更容易控制焊接稳定性。
通过填丝的方式满足焊缝的工艺要求,而且在焊缝缝隙较大的位置可以提高送丝速度来填充金属,而不会影响焊接参数。
由于工件产量不高而且为高质量要求的工件,因此该方案选用TIG焊接方法进行工件焊接。
3.2机器人机器人柔性度高,只需要编制相对应机器人程序,即可满足于多种规格型号工件的焊接需要。
此外,为了减少工件变形,需要在焊接时按照一定的焊接顺序和焊接方向进行焊接,机器人完全可以满足这样的焊接要求。
目前,机器人主要制造商集中在欧洲和日本。
日本机器人虽然在使用寿命,机械刚度,扩展功能相对于欧洲机器人略逊一筹,但是物美价廉。
不过日本机器人存在对军工企业的限制问题。
本方案采用日本安川公司的MOTOMAN MH6机器人,MOTOMAN机器人全世界销量第一,而且在国较早成立中日合资公司,主要销售、技术、售后服务均是中国技术人员,限制较少。
3.3焊接工位由于焊缝分布在工件6个面上,因此需要变位机对工件进行翻转变位才能使机器人焊接到所有焊缝。
变位机采用头尾架形式,旋转轴与地面水平。
为了适应不同长度的工件装夹,尾架可前后移动。
为了提高生产效率,在机器人两侧分别布置一套变位机,一套变位机进行焊接,另一套进行工件装夹。
3.4机器人运动滑轨MH6机器人最大运动围可达2844mm,但最大围是指机器人手臂伸直时的运动围,而这个姿态的机器人不可避免的与工件发生干涉;同时若工件靠近机器人,机器人受其自身结构限制,是无法到达的。
因此,必须增加机器人有效的运动围,即提高机器人可达性。
本方案采用高精度机器人运动滑轨来提高机器人可达性。
机器人安装在机器人运动滑轨上,不仅可以扩展机器人运动围,而且在焊接靠近机器人的焊缝时,改善机器人姿态。
良好的机器人姿态会提高了送丝稳定性,保证焊接质量。
3.5跟踪系统由于工件为结构件,焊缝位置会有较大偏差,焊缝间隙不一致等问题,需要通过焊缝跟踪的方法来实时校正机器人焊接位置轨迹,使其能够按照实际焊缝轨迹行走。
而指接形式焊缝为平面焊缝,目前只有激光视觉跟踪可以满足这种焊缝形式的跟踪要求。
本方案采用英国META公司的SLS-050激光视觉焊缝跟踪系统来实时校正机器人轨迹偏差,同时根据其输出的焊缝间隙信息,实时调节送丝速度,具有一定的自适应能力。
3.6工装夹具工装夹具安装在焊接工位的变位机上,工件的工装夹具不采用标准的横梁结构,横梁结构会遮挡焊缝,使机器人难以一次装件完成所有焊缝的焊接。
为此采用顶紧的方式来固定工件,这样只需要变位机翻转,即可焊接所有焊缝。
四、工作站设备介绍4.1焊接机器人系统4.1.1机器人本体MOTOMAN MH6型机器人为一6轴关节式机器人,采用的新型交流伺服电机具有结构紧凑、高输出、响应快、高可靠性等特点,从而使机器人本体紧凑灵活,具有较大的运动空间、更好的稳定性和较高的重复定位精度,尤其适合于三维曲线焊缝的焊接。
技术数据如下:4.1.2机器人控制系统DX100机器人控制柜的控制是基于Intel公司的处理器开发的,采用Windows CE技术的智能运动控制系统。
全数字伺服模块给机器人的6个关节的交流伺服电机提供驱动电源,有能力提供多达54个伺服电机轴同步协调控制,完成直线插补和圆弧插补。
采用友好和简易的编程界面,图标式按键,使操作人员更加易学和舒适。
分布式硬件结构和精简指令集软件能保证严格的时序和任务的执行。
记忆容量达到160000步,外部I/O点可达32点。
开放式结构,可以与Ethernet、Device-net等网络进行连接。
另外,带有过滤网的自循环通风系统可以保证在5℃-45℃围正常工作。
机器人控制柜的控制系统具有如下的软件功能●再引弧功能:可以在第一次引弧失败后,自动再次引燃电弧。
●再起弧功能:在焊接过程中意外断弧后,能够自动再次起弧。
●防粘丝功能:防止在熄弧时焊丝与工件的粘连。
●焊接参数存储与调用功能:经过优化的焊接参数,可存储于数据库的焊接文件中,通过简单调用程序,即可编入后续编制的同类型焊缝的焊接程序中。
●摆焊功能:多种焊枪摆动方式供编程时调用,摆动两侧停留时间可按需要设定。
●故障自诊断显示功能。
技术规格:4.1.3示教编程器机器人系统配有大屏幕彩色LCD触摸编程器,操作与编程简单明了,具有在线焊接参数修改和故障自诊断显示功能。
可转换中/英文显示方式,方便操作者。
并且安装有dead-man开关,其一步保证安全。
●可以进行摆动模式,摆动波形的编辑●可以进行焊接参数和焊接电流、电压波形的实时显示和参数修改。
●可以进行多窗口显示。
(例如,可以进行程序、焊接参数、输入、输出的同时显示)●可以进行部PLC的梯形图编程,不同其他机器人的语句表编程。
使编程更加直观,更加易于掌握。
●可以显示电机速度变化波形,利于维护人员进行维修和服务技术规格:4.1.4焊接设备系统MW5000焊接电源是Fronius公司生产的全数字式逆变直流脉冲TIG焊接电源。
在焊机部装有数字信号处理器DSP芯片,实现焊接参数、控制程序、填丝速度的全数字化控制,并带有焊接参数的专家系统。
该芯片可以精确控制电弧,快速进行反馈和补偿,即使网路电压波动大,同样能保证输出平稳。
由于逆变频率越高,输出电流越平稳,MW5000最小电流3A,5A电流就可稳弧,更有利于薄板的精确焊接。
脉冲频率从0.2-2000Hz可调,满足于薄板焊接热输入量精确控制的需要。
焊机具有接触引弧和数字高频引弧方式,高频强度可调,同普通焊机的电火花高频引弧比具有更高的可靠性。
高频引弧可选择转极性引弧,使引弧过程更加迅速。
焊接电源部存储了多套经过优化的标准焊接规参数,操作人员可以根据焊丝直径、材料、保护气体、焊接位置来调用焊接参数,使焊接参数的选择更方便可靠。
该焊接电源具有JOB工作方式,每一焊道的焊接参数可以根据接头形式和位置调用焊机部相应的JOB焊接工作程序。
焊接工作程序包括焊接电流、送丝速度、脉冲频率、峰值及基值电流等焊接参数。
数字显示焊接电流、脉冲参数、弧长、送丝速度、焊接工作程序号等参数。
可以通过焊机提供的RS485、RS232计算机接口对焊接过程和参数进行实时监控。
技术规格4.1.5 TTW 4500水冷TIG焊枪TTW4500焊枪是为TIG焊机器人设计的,其特有的17度倾角设计非常适合焊接生产对焊枪姿态的要求。
强水冷设计,保证了在长时间焊接时焊枪不会发生损坏。
一体化焊枪电缆便于安装和机器人运行。
可以配备直径1.0-4.0mm的钨极。
技术规格:4.1.6 KD1500-11送丝机KD1500-11送丝机是Fronius公司专门为自动焊接设计的。
该送丝机可以适应输送1.0、1.2、1.6mm的焊丝要求;采用数字化控制系统及在送丝电机上安装转速控制装置,以保证恒定的送丝速度,最大送丝速度可达到11m/min;无级调速;四滚轮送丝装置,保证了送丝的可靠性。
可以调节送丝轮的压力满足各种焊丝对送丝压力的要求。
4.1.7焊缝跟踪传感系统激光视觉实时跟踪系统采用英国META公司生产的SLS050激光视觉视觉焊缝跟踪系统。
该系统包括SLS050激光视觉视觉跟踪头,控制柜以及相应的跟踪识别软件。
激光视觉非接触式焊缝自动跟踪系统,负责纠正工件的装配误差及焊接过程中的热变形引起的焊缝偏差。
技术规格:4.2机器人所需外部设备4.2.1机器人滑轨滑轨铺设在地面上,采用双直线导轨,齿轮齿条结构。
在直线导轨上有滑台,机器人安装在滑台上,滑台的移动驱动同样采用可由机器人控制柜进行协调控制的交流伺服电机。
减速机构采用高精度的RV减速机。
技术规格:4.2.2头尾架翻转变位机头尾架单轴翻转变位机采用头架驱动,尾架随动的方式。
变位机额定负载1t,尾架可移动,最大工件长度≤2m。
翻转的驱动采用可与机器人进行协调控制的交流伺服电机,减速机采用大减速比、高精度的RV减速机,保证重复定位精度为±0.2mm(距旋转中心500mm处)。
技术规格:五、设备安装要求及调试、验收和人员培训油箱焊接机器人工作站安装环境要求1、电源要求:3相380V±10%,50Hz 40kVA2、压缩空气:气体压力大于0.5Mpa (经过油、水过滤)3、环境要求:环境温度:5-45°C湿度:20~80%RH(不能结露)震动:0.5G以下设备调试、验收工作站整套设备的安装、调试和验收采用一贯的交钥匙工程的方式,即整套工作站设计完成后,由贵公司派人双方进行前期设计审核;审核后,进行拆图和设备加工。
机器人系统到货及外围设备加工完毕后,进行系统的总装与联调,检测调整各项技术参数,并进行模拟件的焊接实验。
全部完成后,由贵公司再次派人来进行整个系统的出厂前检验;检验满意后,设备发送到贵公司。
我校工程技术人员在设备到贵公司指定的安装地点后的一周到达现场,进行设备的安装调试,设备的安装调试完成后进行工件的试焊接。
焊件检测合格后,进行正式焊接生产。
在完成焊接一定数量的产品后,贵公司进行设备最后的验收,双方签署设备验收报告,设备正式交付贵公司使用。
人员培训培训由我公司为贵公司培训三名机器人工作站的编程、操作和维护工程技术人员,第一次培训在整个设备出厂验收之前在我公司进行;第二次培训在设备在贵公司安装后进行。
六、工程进度及付款方式整套生产线的工程工期为合同生效后6个月。
支付条件如下:a)合同生效后,贵公司首付30%合同款,我公司在收到预付款后2个月完成整个系统的设计,并开始采购机器人系统。
b)贵公司完成设计审核认可后,贵公司支付35%合同款(即全部付款数达到合同总额的65%)。
同时我公司在3个月完成整套设备的制造及机器人系统的引进,并进行整个系统的联调。
c)贵公司在完成出厂前的检验后,设备拆装发送到贵公司。
我公司的技术人员在设备到厂后的一周到达现场,进行整套设备的安装调试,人员培训,预生产及设备验收。