大直径预应力钢筋混凝土筒仓滑模施工要点..
大直径预应力筒仓滑模施工技术

大直径预应力筒仓滑模施工技术大直径预应力筒仓在现代建筑中应用越来越广泛,其建造需要使用滑模施工技术。
滑模施工技术是一种高效、节能、节省钢模板和节省人力的施工技术,能够大大缩短筒仓建设周期和降低成本。
下面是大直径预应力筒仓滑模施工技术的详细介绍。
1.滑模施工原理滑模施工原理是通过在钢丝绳、钢管或钢板的支承下,使用涂了高强混凝土浆料的钢丝网,将混凝土浆料均匀地涂覆在支承体上并精密振捣,以形成一层普通混凝土、预应力混凝土或复合钢混凝土结构。
由于其具有施工便捷和施工周期短的特点,在大跨度桥梁、高层建筑和大直径预应力筒仓等重要工程中得到了广泛应用。
一般滑模施工流程包括准备现场、制作钢模板、地基处理及构造验收、安装支承、浇注钢筋混凝土、封端与拆卸钢型、反复横贯性验收等多个环节。
其中,支承的制作是滑模施工的重要步骤之一。
支承是指在施工过程中支撑并保持钢模板刚度的材料,主要包括钢丝绳、钢管或钢板。
制作支承时,要根据构造要求进行尺寸、悬挑长度、施工高度、滑板厚度和未来荷载的计算,制作支承可以采用加固杆和丝束,以提高支承的稳固性。
3.混凝土的质量保证滑模施工中混凝土的质量保证是十分关键的。
为了确保混凝土质量,必须注意以下几个方面:首先,在混凝土浆料中加入水泥固化剂,以提高水泥砂浆的强度;其次,混凝土浆料必须在规定的时间内施工,在施工前应进行调配和检测;再次,混凝土浆料的成分比例必须严格控制,以确保混凝土的均匀性和固化质量;最后,混凝土浆料中添加一定的适应性改善剂,以改善和控制混凝土的流动性、坍落度和黏度。
4.施工现场的安全措施因为滑模施工需要在高处进行,所以需要在施工现场设置严格的安全措施。
这些措施包括:在进行滑模施工前,对施工场地和工作区进行全面检查,确定是否存在安全隐患;在施工上方设置安全网或保护罩,防止物品掉落或砖块飞出伤人;在施工区域设置安全警示标志,以明确施工区域范围,以及指导工人注意安全;在作业期间,必须有专人负责监控安全状况,及时发现并解决问题。
大直径预应力筒仓滑模施工技术
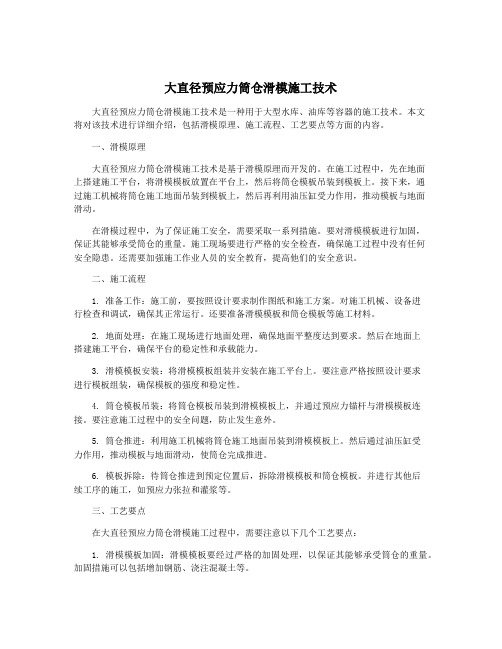
大直径预应力筒仓滑模施工技术大直径预应力筒仓滑模施工技术是一种用于大型水库、油库等容器的施工技术。
本文将对该技术进行详细介绍,包括滑模原理、施工流程、工艺要点等方面的内容。
一、滑模原理大直径预应力筒仓滑模施工技术是基于滑模原理而开发的。
在施工过程中,先在地面上搭建施工平台,将滑模模板放置在平台上,然后将筒仓模板吊装到模板上。
接下来,通过施工机械将筒仓施工地面吊装到模板上,然后再利用油压缸受力作用,推动模板与地面滑动。
在滑模过程中,为了保证施工安全,需要采取一系列措施。
要对滑模模板进行加固,保证其能够承受筒仓的重量。
施工现场要进行严格的安全检查,确保施工过程中没有任何安全隐患。
还需要加强施工作业人员的安全教育,提高他们的安全意识。
二、施工流程1. 准备工作:施工前,要按照设计要求制作图纸和施工方案。
对施工机械、设备进行检查和调试,确保其正常运行。
还要准备滑模模板和筒仓模板等施工材料。
2. 地面处理:在施工现场进行地面处理,确保地面平整度达到要求。
然后在地面上搭建施工平台,确保平台的稳定性和承载能力。
3. 滑模模板安装:将滑模模板组装并安装在施工平台上。
要注意严格按照设计要求进行模板组装,确保模板的强度和稳定性。
4. 筒仓模板吊装:将筒仓模板吊装到滑模模板上,并通过预应力锚杆与滑模模板连接。
要注意施工过程中的安全问题,防止发生意外。
5. 筒仓推进:利用施工机械将筒仓施工地面吊装到滑模模板上。
然后通过油压缸受力作用,推动模板与地面滑动,使筒仓完成推进。
6. 模板拆除:待筒仓推进到预定位置后,拆除滑模模板和筒仓模板。
并进行其他后续工序的施工,如预应力张拉和灌浆等。
三、工艺要点在大直径预应力筒仓滑模施工过程中,需要注意以下几个工艺要点:1. 滑模模板加固:滑模模板要经过严格的加固处理,以保证其能够承受筒仓的重量。
加固措施可以包括增加钢筋、浇注混凝土等。
2. 安全检查:施工现场要进行严格的安全检查,确保施工过程中没有任何安全隐患。
大直径预应力筒仓滑模施工技术

大直径预应力筒仓滑模施工技术大直径预应力筒仓是一种常见的混凝土结构,主要用于储存粮食、水泥等物料。
为了提高大直径预应力筒仓的承载能力和安全性能,采用滑模施工技术进行施工是一种有效的方法。
滑模施工技术是一种通过移动施工模板来完成结构部件施工的方法。
在大直径预应力筒仓的施工中,滑模施工技术可以用于筒仓壁体、底板和顶板的施工。
下面将详细介绍大直径预应力筒仓滑模施工技术的步骤和注意事项。
一、滑模施工技术的步骤1. 准备工作:确定施工计划和施工顺序,制定滑模施工方案,并组织施工人员进行安全培训。
2. 制作滑模:根据设计要求,制作筒仓壁体、底板和顶板的滑模。
滑模的制作需要考虑模板的强度、可移动性和成本等因素。
3. 准备施工材料:准备好混凝土、预应力钢筋和其他施工材料,并进行质量检查。
4. 安装滑模:按照滑模施工方案,将滑模安装在筒仓基础上,并进行调整和固定。
5. 浇筑混凝土:根据滑模施工方案,将混凝土通过泵送或其他方式送至模板内,进行浇筑。
6. 预应力施工:在混凝土刚性化前,对预应力钢筋进行张拉和锚固,以增加结构的承载能力。
7. 脱模和拆模:待混凝土强度达到要求后,进行脱模和拆模。
脱模过程中需要注意保护混凝土表面,避免损坏。
8. 连续施工:当第一段滑模施工完成后,根据施工顺序进行连续施工。
重复上述步骤,直至整个筒仓结构完成。
1. 滑模的制作要符合设计和施工要求,模板的强度要能够承受混凝土的浇筑压力。
在制作过程中,要注意检查模板的质量和尺寸,确保滑模的准确性和稳定性。
2. 在滑模的安装过程中,要按照施工方案进行调整和固定。
要及时检查滑模的水平度和垂直度,并进行必要的调整。
3. 在浇筑混凝土时,要控制混凝土的流动性和浇注速度,以避免混凝土流失或产生空隙。
要按照混凝土的浇注顺序进行施工,避免出现结构不稳定的情况。
4. 在预应力施工过程中,要控制好钢筋的张拉力度和锚固位置,以确保钢筋的承载能力和连接性能。
6. 连续施工过程中,要做好施工记录和交接工作,保证施工的连贯性和安全性。
大直径预应力筒仓滑模施工技术

大直径预应力筒仓滑模施工技术随着我国经济的不断发展,建筑行业也在迅速壮大,各种新型建筑结构和施工工艺层出不穷。
大直径预应力筒仓滑模施工技术就是其中之一,它在大型建筑工程中得到了广泛应用。
本文将介绍大直径预应力筒仓滑模施工技术的相关知识和施工过程。
一、大直径预应力筒仓滑模概述大直径预应力筒仓是指直径大于10m的圆筒形建筑结构,它通常用于存储散装物料,如水泥、煤炭、粮食等。
由于筒仓的特殊性,需要具备良好的耐久性和承载能力。
预应力技术是一种提高筒仓承载能力和抗震性能的重要方法,而滑模施工技术则是一种提高筒仓施工效率和质量的重要手段。
大直径预应力筒仓滑模施工技术是在滑模工程基础上,结合预应力技术,通过预埋筋筋带和张拉设备,实现圆筒形结构的预应力施工,从而提高筒仓的整体性能和使用寿命。
1.施工周期短:大直径预应力筒仓滑模施工技术采用模板滑动施工,相对于传统的筒仓施工方法,施工周期大大缩短,节约了人力和物力,提高了施工效率。
2.施工质量高:预应力技术能够有效改善筒仓的承载能力和抗震性能,滑模施工能够保证结构的整体性和平整度,因此大直径预应力筒仓滑模施工技术能够保证筒仓的施工质量。
3.成本低:大直径预应力筒仓滑模施工技术采用的材料和设备相对较少,成本相对较低,而且施工周期短也能够减少人力和物力的浪费,因此整体成本较低。
4.灵活性强:大直径预应力筒仓滑模施工技术适用于直径较大的筒仓,而且模板可根据筒仓的尺寸进行调整,因此具有较强的适用性。
5.经济效益好:由于施工周期短、质量高、成本低,大直径预应力筒仓滑模施工技术能够带来较好的经济效益。
1.准备工作:确定筒仓的设计尺寸和结构形式,根据设计图纸准备模板和支撑系统,同时确认预应力筒仓的预埋筋筋带位置,并做好防腐处理。
2.模板安装:根据设计要求,在筒仓的内外侧安装滑模模板,同时设置合理的支撑系统确保模板的稳固和平整。
3.混凝土浇筑:根据设计要求,通过混凝土搅拌车将混凝土浇入模板内,同时通过振捣器进行振捣,保证混凝土的密实度和均匀性。
大直径预应力筒仓滑模施工技术

大直径预应力筒仓滑模施工技术随着经济、技术的不断更新发展,煤炭行业大直径预应力筒仓设计及施工技术越来越引起行业人员的高度重视,大直径预应力筒仓滑模施工面临更多挑战和施工难题,本文通过分析大直径预应力筒仓滑模技术在施工中存在的难题和技术改进措施,希望可以起到一定借鉴意义。
标签:预应力;筒仓;滑模;施工一般筒仓滑模施工工艺分为柔性滑模施工工艺与刚性滑模施工工艺,前者工艺相对简单,操作方便、快捷,但后期锥壳施工时因自身刚度较差,需要借助仓内脚手架施工锥壳,造成工期长,投入人力、物力较大;而后者刚性好,平台稳定,安全性能好,能够加快后期锥壳施工,节约工期与成本。
由于受限于滑模平台自身荷载过大,不适用于25m直径以上的大直径筒仓滑模,大直径筒仓滑模工艺较多采用柔性滑模施工工艺配套中心脚手架支撑系统工艺。
1、大直径预应力筒仓滑模施工技术分析1.1柔性滑模方案控制措施通常滑模结构设计需要科学合理,为之后施工中滑模结构的运用提供可能。
施工单位在进行滑模施工时需要完善相关滑模施工体系,全面提升施工效率与质量。
需要完善柔性滑模方案控制措施,从多个角度全方位控制滑模施工,提升滑模质量。
在柔性滑模控制方案措施制定中要注重全面,从模板系统、液压控制系统、操作平台系统设计、配电系统设计等方面全面控制滑模质量,另外再从中心脚手架支撑系统完善方面,全面提升大直径筒仓滑模质量。
1.2完善模板系统滑模模板系统包括提升架、模板、围圈、开字架、吊架。
操作平台系统与模板系统用钢桁架连接,并用螺栓与开字架连接。
相关滑模设计人员与施工人员要注重完善模板系统。
施工单位在滑模模板质量控制方面需要从围圈与模板两方面入手,全面完善模板系统。
首先,施工单位需要完善围圈。
施工中关注围圈间距控制,一般控制在451—751mm比较合适,且要关注测压、荷载等参数,为围圈设计提供可靠依据,有效提升围圈科学性。
其次,关注模板科学性。
施工人员从模板、吊架结构出发提升模板质量,为滑模施工质量提升提供一定条件。
大直径预应力筒仓滑模施工技术

大直径预应力筒仓滑模施工技术大直径预应力筒仓滑模施工技术是指利用滑模模板技术进行大直径预应力筒仓的施工,通过先进的工艺和设备,实现高效、高质量、安全的工程建设。
本文将从技术原理、施工工艺及关键技术等方面详细介绍大直径预应力筒仓滑模施工技术。
技术原理大直径预应力筒仓滑模施工技术的核心原理是利用滑模模板进行筒仓壁的连续浇筑,同时在筒仓壁内部预置预应力钢筋,利用预应力钢筋的受拉能力来增强筒仓的承载能力。
通过先进的设备和工艺,将混凝土从顶部一次性浇筑至底部,形成整体连续的筒仓壁体,增强筒仓的整体强度和稳定性。
施工工艺大直径预应力筒仓滑模施工技术的工艺流程包括筒仓模板制作、预应力钢筋预置、混凝土搅拌浇筑等多个环节。
首先是筒仓模板的制作,采用优质的木材或钢材制作成模板,确保模板的平整度和稳定性。
然后在模板内部进行预应力钢筋的预置,按照设计要求将预应力钢筋布置在筒仓壁的内侧,以增加筒仓的承载能力。
接下来是混凝土的搅拌和浇注,选择高质量的混凝土原材料,并使用先进的搅拌设备进行搅拌,保证混凝土的均匀性和稳定性。
然后将混凝土通过泵车等设备从顶部一次性浇注至底部,形成整体连续的筒仓壁体。
在浇筑完成后,进行养护和维护工作,确保混凝土的完全硬化和强度达到设计要求。
最后进行模板拆除和清理工作,完成整个滑模施工的工艺流程。
首先是筒仓模板的制作,筒仓模板的平整度和稳定性对于施工的成功至关重要。
采用先进的数控设备进行模板的制作,确保模板的尺寸精准和表面光滑,以保证滑模施工的顺利进行。
其次是预应力钢筋的预置,预应力钢筋的布置需要按照设计要求进行,确保预应力钢筋在浇筑混凝土时能够正确发挥作用,增强筒仓的整体承载能力。
最后是结构的养护和维护,尤其是对于筒仓壁的养护和维护工作,需要按照设计要求进行,确保混凝土的完全硬化和强度达到设计要求。
应用前景大直径预应力筒仓滑模施工技术在工程领域具有广阔的应用前景。
可以满足大直径预应力筒仓的快速建设需求,提高工程建设的效率和质量。
大直径预应力筒仓滑模施工技术
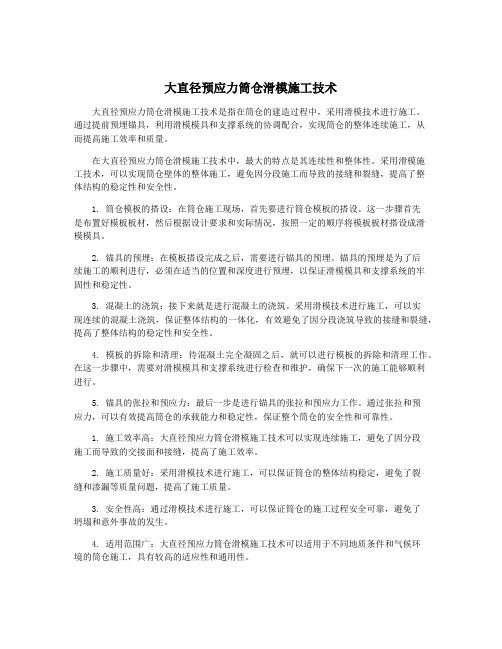
大直径预应力筒仓滑模施工技术大直径预应力筒仓滑模施工技术是指在筒仓的建造过程中,采用滑模技术进行施工。
通过提前预埋锚具,利用滑模模具和支撑系统的协调配合,实现筒仓的整体连续施工,从而提高施工效率和质量。
在大直径预应力筒仓滑模施工技术中,最大的特点是其连续性和整体性。
采用滑模施工技术,可以实现筒仓壁体的整体施工,避免因分段施工而导致的接缝和裂缝,提高了整体结构的稳定性和安全性。
1. 筒仓模板的搭设:在筒仓施工现场,首先要进行筒仓模板的搭设。
这一步骤首先是布置好模板板材,然后根据设计要求和实际情况,按照一定的顺序将模板板材搭设成滑模模具。
2. 锚具的预埋:在模板搭设完成之后,需要进行锚具的预埋。
锚具的预埋是为了后续施工的顺利进行,必须在适当的位置和深度进行预埋,以保证滑模模具和支撑系统的牢固性和稳定性。
3. 混凝土的浇筑:接下来就是进行混凝土的浇筑。
采用滑模技术进行施工,可以实现连续的混凝土浇筑,保证整体结构的一体化,有效避免了因分段浇筑导致的接缝和裂缝,提高了整体结构的稳定性和安全性。
4. 模板的拆除和清理:待混凝土完全凝固之后,就可以进行模板的拆除和清理工作。
在这一步骤中,需要对滑模模具和支撑系统进行检查和维护,确保下一次的施工能够顺利进行。
5. 锚具的张拉和预应力:最后一步是进行锚具的张拉和预应力工作。
通过张拉和预应力,可以有效提高筒仓的承载能力和稳定性,保证整个筒仓的安全性和可靠性。
1. 施工效率高:大直径预应力筒仓滑模施工技术可以实现连续施工,避免了因分段施工而导致的交接面和接缝,提高了施工效率。
2. 施工质量好:采用滑模技术进行施工,可以保证筒仓的整体结构稳定,避免了裂缝和渗漏等质量问题,提高了施工质量。
3. 安全性高:通过滑模技术进行施工,可以保证筒仓的施工过程安全可靠,避免了坍塌和意外事故的发生。
4. 适用范围广:大直径预应力筒仓滑模施工技术可以适用于不同地质条件和气候环境的筒仓施工,具有较高的适应性和通用性。
大直径预应力筒仓滑模施工技术

大直径预应力筒仓滑模施工技术【摘要】大直径预应力筒仓滑模施工技术是一种先进的施工方式,旨在提高仓库建设的效率和质量。
本文首先对该技术进行了概述,介绍了其基本原理。
随后详细阐述了大直径预应力筒仓滑模施工技术的工艺流程、所需设备和材料,以及施工步骤和质量控制措施。
通过对这些内容的分析,读者可以全面了解该技术的操作要点和注意事项。
在结论中,文章指出了大直径预应力筒仓滑模施工技术的优势,如节约成本、缩短工期等,同时也展望了其未来的发展趋势,为读者深入了解和应用该技术提供了参考。
本文系统性地介绍了大直径预应力筒仓滑模施工技术,为仓库建设领域的相关工作者提供了有益的信息和指导。
【关键词】大直径预应力筒仓、滑模施工技术、原理、工艺流程、设备、材料、施工步骤、质量控制、优势、发展趋势1. 引言1.1 大直径预应力筒仓滑模施工技术概述大直径预应力筒仓滑模施工技术是一种先进的施工方法,适用于大直径预应力筒仓的建设。
它采用预应力技术和滑模模板技术相结合,能够有效提高施工效率和施工质量。
本文将着重介绍大直径预应力筒仓滑模施工技术的原理、工艺流程、设备和材料、施工步骤以及质量控制等方面。
大直径预应力筒仓滑模施工技术利用滑模模板来进行施工,通过预应力技术对筒仓进行支撑和加固,使其具有更好的承载能力和抗震能力。
在施工过程中,需要精确控制施工步骤和参数,确保筒仓的稳定性和安全性。
大直径预应力筒仓滑模施工技术还能够减少对环境的影响,降低施工成本,提高工程的可持续性。
大直径预应力筒仓滑模施工技术是一种较为成熟和先进的施工方法,具有很好的技术优势和发展前景。
通过本文的介绍,读者将能够更加深入地了解这一技术,并掌握其施工要点和注意事项,为今后在大直径预应力筒仓工程中的应用提供参考和指导。
2. 正文2.1 大直径预应力筒仓滑模施工技术原理大直径预应力筒仓滑模施工技术是一种先进的施工方法,主要应用于大直径预应力筒仓的施工过程中。
其原理是通过模板滑移技术,将施工现场的模板系统逐步移动,实现筒仓壁体的连续浇筑,从而达到预应力筒仓的施工要求。
大直径预应力筒仓滑模施工技术

大直径预应力筒仓滑模施工技术一、引言大直径预应力筒仓滑模施工技术是一种将筒仓组块预制、按段安装、逐节顺序滑动推进,并通过预应力将各组块紧密连接成整体的施工方法。
该方法具有施工周期短、质量可控、适应性强等优点,被广泛应用于大直径储仓、大直径冷藏库等工程。
二、滑模施工流程1. 筒仓设计根据工程的要求,确定筒仓的高度、直径、厚度等参数,并进行结构计算和施工方案设计。
2. 筒仓模块制造将筒仓按照设计要求划分为若干个组块,每个组块由若干个相同尺寸的筒仓片拼接而成。
筒仓片的制造可以采用钢模预制、混凝土浇筑、现浇钢模等方法。
3. 基础施工首先根据设计要求在地基上建立基础平台,再在基础平台上进行基础的浇筑,以保证筒仓的稳固性和承载能力。
4. 推进台架制作制作滑模施工所需的台架,台架要具备良好的承重能力和稳定性,并按照设计要求设置滑模导轨和滑模移动装置。
5. 推进台架安装将制作好的推进台架安装在已建立的基础上,并进行校正和调整,确保台架的水平度和垂直度。
6. 滑模装配将筒仓片按照设计顺序逐个装配到滑模导轨上,每个筒仓片与前一个筒仓片之间设置预应力钢筋和连接钢筋,通过预应力将各筒仓片牢固连接。
7. 滑模推进利用滑模移动装置,将滑模上的筒仓片逐渐向上推进,以完成筒仓的施工。
8. 浇筑混凝土待滑模推进到一定高度后,利用施工吊机将混凝土输送到滑模上,由上至下逐层浇筑,形成筒仓的壁体。
9. 混凝土养护混凝土浇筑完成后,对筒仓进行适当的养护,以保证混凝土的强度和耐久性。
10. 外部附件安装对筒仓进行外部附件的安装,如进出料口、通风口、检修门等,以满足筒仓的使用要求。
三、滑模施工注意事项1. 设计合理滑模施工前,必须进行结构设计和施工方案设计,并确保设计合理,满足工程要求。
2. 安全可靠滑模施工过程中,必须保证施工人员的安全,所有设备和材料都要经过检查和验收,确保安全可靠。
3. 现场管理滑模施工现场要进行严格的管理,确保施工人员的作业秩序和质量控制。
大直径预应力筒仓滑模施工技术

大直径预应力筒仓滑模施工技术大直径预应力筒仓是现代化仓储设施的重要组成部分,它具有体积大、载荷能力强、使用寿命长等优点。
为了保证大直径预应力筒仓的施工质量和工期进度,滑模施工技术被广泛应用于大直径预应力筒仓的施工中。
本文将对大直径预应力筒仓滑模施工技术进行详细介绍。
一、滑模施工技术概述滑模施工技术是指在土方开挖完毕后,通过滑模机将钢模板组装并连续滑动到预定位置,然后进行钢筋绑扎和混凝土浇筑的一种施工方法。
该方法具有施工速度快、工序简化、施工质量高等优点。
二、滑模机的选择大直径预应力筒仓的滑模施工需要选用适合的滑模机。
滑模机的选择要考虑以下几个因素:1. 承载能力:滑模机的承载能力必须能够满足预应力筒仓的重量要求,同时还要考虑到混凝土浇筑时的额外荷载。
2. 滑动速度:滑模机的滑动速度要适中,既要满足施工进度要求,又不能过快导致混凝土浇筑不均匀。
3. 精度控制:滑模机的控制系统要能够精确控制滑模的滑动速度和位置,以确保筒仓的几何形状和尺寸的精度。
4. 操作便捷性:滑模机的操作要便捷,能够满足施工人员的需要。
根据以上要求,目前市场上常见的滑模机有液压滑模机和电动滑模机两种。
液压滑模机承载能力大,滑动速度可调,精度高,但操作和维护相对复杂。
电动滑模机承载能力相对较小,滑动速度相对较慢,但操作和维护相对简单。
三、滑模施工过程滑模施工过程包括以下几个基本步骤:1. 构造筒仓基础:首先需要按照设计要求施工筒仓基础,包括地基处理、基础平整、基础支撑等。
2. 滑模模板组装:将滑模机带来的钢模板组装成一个圆筒形,确保模板的平整度和尺寸精度。
3. 初次滑模:将组装好的滑模模板通过滑模机滑动到初次浇筑混凝土的位置,进行初次浇筑。
5. 钢筋绑扎:每次浇筑完混凝土后,需要进行钢筋的绑扎工作,以增加筒仓的强度和稳定性。
6. 混凝土浇筑:每次滑模后,需要进行混凝土的浇筑,一般采用泵送方式进行。
7. 滑模机退模:当所有浇筑工作完成后,滑模机将滑模模板缓慢滑动至筒仓的顶部,待混凝土达到预设强度后,滑模机退离现场。
大直径预应力筒仓滑模施工技术

大直径预应力筒仓滑模施工技术大直径预应力筒仓滑模施工技术是一种适用于建造大直径预应力筒仓的施工技术。
预应力筒仓是一种用于储存粮食、饲料、化肥等物品的大型仓库结构。
在传统的预应力筒仓施工中,常常需要使用大量的模板和支架来搭建施工平台,既费时又费力。
而大直径预应力筒仓滑模施工技术则能够解决这一问题,大大提高施工效率。
大直径预应力筒仓滑模施工技术的基本原理是通过使用滑模板来实现仓壁的连续施工。
具体的施工步骤如下:第一步,根据设计要求,确定预应力筒仓的直径和高度,并进行预应力筒仓的初步设计。
第二步,按照初步设计的要求,制作滑模板,并进行现场安装和调整。
滑模板通常由多段组成,每段的长度大约为3-5米,可以根据需要进行调整。
第三步,开始滑模施工。
将一段滑模板与下一段滑模板端部相连接,并用螺栓进行固定。
然后,使用涂油机对滑模板进行涂油,以降低摩擦力。
第四步,将混凝土倒入滑模板内。
由于滑模板的倾斜设计,混凝土会自动流动,填满滑模板内的空间。
在滑模板倾斜的过程中,要注意混凝土的流动速度,以防止空隙和气泡的产生。
第五步,待混凝土凝固之后,将滑模板向上移动一段距离,并进行下一段滑模板的连接和固定。
重复以上步骤,直至完成预应力筒仓的施工。
大直径预应力筒仓滑模施工技术的优点是施工速度快、效率高。
相比于传统的滑模施工技术,大直径预应力筒仓滑模施工技术无需搭建大量的模板和支架,减少了施工时间和成本。
滑模板的倾斜设计也能够保证仓壁的光滑度和强度。
大直径预应力筒仓滑模施工技术也存在一些挑战。
需要对滑模板进行准确的定位和调整,以保证仓壁的垂直度和强度。
滑模板的设计和制作也需要考虑混凝土的流动性和凝固时间,以防止出现空隙和气泡。
大直径预应力筒仓滑模施工技术是一种高效的施工技术,能够显著提高大直径预应力筒仓的施工效率。
在实际施工中仍需要精确的操作和细致的调整,以确保施工质量和安全性。
浅析大直径预应力矿井筒仓滑模施工技术

建材发展导向2018年第03期2561 工程简介文章选取山西省大同煤矿集团有限责任公司旗下的同忻矿井煤仓为研究对象,其煤仓是当前我国直径最大,高度最高的筒仓之一。
采用了筒中筒结构的设计形式,简体为漏斗以下三层,而漏斗以上的部分为单筒。
单仓内径达到34米,内壁厚4.5米,储煤量达3.5万吨。
2 施工工艺简介2.1 柔性滑膜施工工艺通常,大直径筒仓仓顶采用的是钢结构,筒仓仓壁施工时选择柔性平台进行滑膜工艺,仓顶钢结构在地面进行拼装后直接采用大吨位的起重机吊装到筒仓顶部安置即可。
但是文本涉及的工程其筒仓仓顶采取的是钢筋混凝土结构,因其自身重力较大,不能采取吊装方案。
因此,在滑膜施工后,需要搭建满堂筒脚手架对锥壳进行支撑,才能完成仓顶的施工工作。
但是采用该种工艺施工周期长,进度慢,周转材料投入增加,大大加剧了其生产成本,同时施工期间的安全性得不到有效的保证。
2.2 刚性滑膜—内外筒同时升滑工艺内外筒同时升滑采用钢桁架平台,利用钢材质的承重柱,搭建中心筒脚手架进行支撑作用是刚性滑膜工艺的核心技术内容。
通过对这种结构进行科学化的分析,发现此方案具有较强的实用性,简单便捷,且安全可靠。
能够有效解决后期施工过程中筒仓仓顶结构的支撑问题。
而且该种工艺施工周期短,进度快。
中心筒脚手架的采用对于降低滑膜平台挠度有很好的促进作用,同时也能够减少施工过程中单榀桁架的跨度。
即便筒仓仓顶平台封闭,筒仓内漏斗也可以与锥壳进行有效地配合,交叉作业。
2.3 大直径筒仓滑膜施工方法煤矿行业在开展大直径筒仓滑膜施工过程中,一般采取的工艺方法有两种:其一,筒仓筒璧部分采取定型组合钢模板,然后搭建中心筒脚手架进行滑膜施工,当筒璧施工完毕后,就在筒仓内搭建满堂脚手架、操作平台,在平台上对筒仓仓顶钢结构部分进行施工。
其二,筒仓筒璧部分采取液压滑动模板进行施工,与此同时,在地面进行仓顶钢结构的组装工作,然后采用大吨位的起重机吊装到筒仓顶部进行安装。
超大直径预应力矿井筒仓滑模施工技术
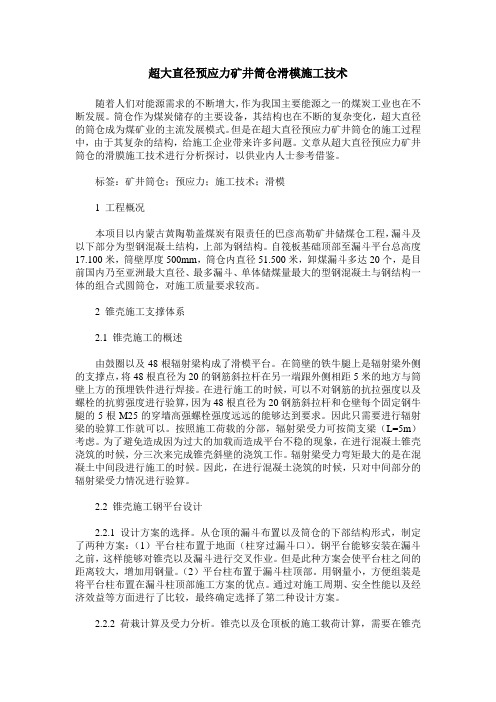
超大直径预应力矿井筒仓滑模施工技术随着人们对能源需求的不断增大,作为我国主要能源之一的煤炭工业也在不断发展。
筒仓作为煤炭储存的主要设备,其结构也在不断的复杂变化,超大直径的筒仓成为煤矿业的主流发展模式。
但是在超大直径预应力矿井筒仓的施工过程中,由于其复杂的结构,给施工企业带来许多问题。
文章从超大直径预应力矿井筒仓的滑膜施工技术进行分析探讨,以供业内人士参考借鉴。
标签:矿井筒仓;预应力;施工技术;滑模1 工程概况本项目以内蒙古黄陶勒盖煤炭有限责任的巴彦高勒矿井储煤仓工程,漏斗及以下部分为型钢混凝土结构,上部为钢结构。
自筏板基础顶部至漏斗平台总高度17.100米,筒壁厚度500mm,筒仓内直径51.500米,卸煤漏斗多达20个,是目前国内乃至亚洲最大直径、最多漏斗、单体储煤量最大的型钢混凝土与钢结构一体的组合式圆筒仓,对施工质量要求较高。
2 锥壳施工支撑体系2.1 锥壳施工的概述由鼓圈以及48根辐射梁构成了滑模平台。
在筒壁的铁牛腿上是辐射梁外侧的支撑点,将48根直径为20的钢筋斜拉杆在另一端跟外侧相距5米的地方与筒壁上方的预埋铁件进行焊接。
在进行施工的时候,可以不对钢筋的抗拉强度以及螺栓的抗剪强度进行验算,因为48根直径为20钢筋斜拉杆和仓壁每个固定钢牛腿的5根M25的穿墙高强螺栓强度远远的能够达到要求。
因此只需要进行辐射梁的验算工作就可以。
按照施工荷载的分部,辐射梁受力可按简支梁(L=5m)考虑。
为了避免造成因为过大的加载而造成平台不稳的现象,在进行混凝土锥壳浇筑的时候,分三次来完成锥壳斜壁的浇筑工作。
辐射梁受力弯矩最大的是在混凝土中间段进行施工的时候。
因此,在进行混凝土浇筑的时候,只对中间部分的辐射梁受力情况进行验算。
2.2 锥壳施工钢平台设计2.2.1 设计方案的选择。
从仓顶的漏斗布置以及筒仓的下部结构形式,制定了两种方案:(1)平台柱布置于地面(柱穿过漏斗口)。
钢平台能够安装在漏斗之前,这样能够对锥壳以及漏斗进行交叉作业。
大直径预应力筒仓滑模施工技术
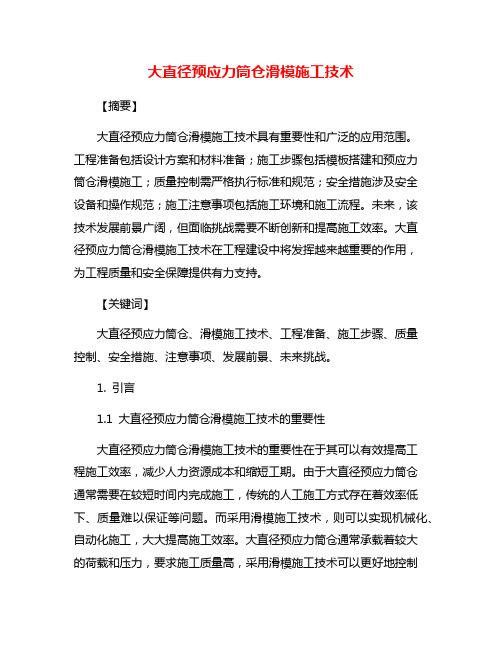
大直径预应力筒仓滑模施工技术【摘要】大直径预应力筒仓滑模施工技术具有重要性和广泛的应用范围。
工程准备包括设计方案和材料准备;施工步骤包括模板搭建和预应力筒仓滑模施工;质量控制需严格执行标准和规范;安全措施涉及安全设备和操作规范;施工注意事项包括施工环境和施工流程。
未来,该技术发展前景广阔,但面临挑战需要不断创新和提高施工效率。
大直径预应力筒仓滑模施工技术在工程建设中将发挥越来越重要的作用,为工程质量和安全保障提供有力支持。
【关键词】大直径预应力筒仓、滑模施工技术、工程准备、施工步骤、质量控制、安全措施、注意事项、发展前景、未来挑战。
1. 引言1.1 大直径预应力筒仓滑模施工技术的重要性大直径预应力筒仓滑模施工技术的重要性在于其可以有效提高工程施工效率,减少人力资源成本和缩短工期。
由于大直径预应力筒仓通常需要在较短时间内完成施工,传统的人工施工方式存在着效率低下、质量难以保证等问题。
而采用滑模施工技术,则可以实现机械化、自动化施工,大大提高施工效率。
大直径预应力筒仓通常承载着较大的荷载和压力,要求施工质量高,采用滑模施工技术可以更好地控制施工质量,确保工程安全可靠。
大直径预应力筒仓滑模施工技术的重要性在于提高施工效率、保证施工质量、确保工程安全,对于大直径预应力筒仓工程的顺利进行具有重要意义。
1.2 大直径预应力筒仓滑模施工技术的应用范围1. 桥梁建设:大直径预应力筒仓滑模施工技术在桥梁建设中有着重要的应用。
通过该技术可以实现桥墩、桥墩横梁等大型结构件的预应力施工,提高结构的承载能力和耐久性。
2. 隧道工程:在隧道工程中,大直径预应力筒仓滑模施工技术被广泛应用于隧道衬砌、隧道拱顶等结构件的预应力处理,保证了隧道的稳定性和安全性。
2. 正文2.1 大直径预应力筒仓滑模施工技术的工程准备大直径预应力筒仓滑模施工技术的工程准备是保证整个施工过程顺利进行的基础。
在进行大直径预应力筒仓滑模施工技术之前,必须进行详细的工程准备工作,包括但不限于以下几个方面:1. 现场勘测:在开始施工之前,需要对施工现场进行详细的勘测,确定地形、地质情况,以及周围环境的影响因素。
大直径预应力筒仓滑模施工技术
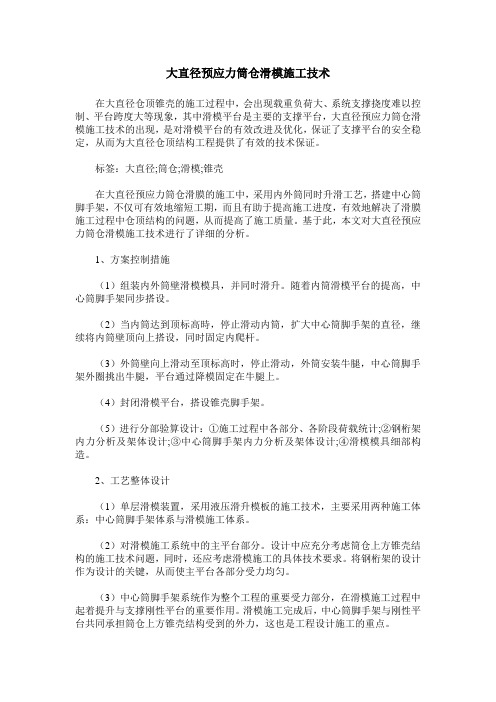
大直径预应力筒仓滑模施工技术在大直径仓顶锥壳的施工过程中,会出现载重负荷大、系统支撑挠度难以控制、平台跨度大等现象,其中滑模平台是主要的支撑平台,大直径预应力筒仓滑模施工技术的出现,是对滑模平台的有效改进及优化,保证了支撑平台的安全稳定,从而为大直径仓顶结构工程提供了有效的技术保证。
标签:大直径;筒仓;滑模;锥壳在大直径预应力筒仓滑膜的施工中,采用内外筒同时升滑工艺,搭建中心筒脚手架,不仅可有效地缩短工期,而且有助于提高施工进度,有效地解决了滑膜施工过程中仓顶结构的问题,从而提高了施工质量。
基于此,本文对大直径预应力筒仓滑模施工技术进行了详细的分析。
1、方案控制措施(1)组装内外筒壁滑模模具,并同时滑升。
随着内筒滑模平台的提高,中心筒脚手架同步搭设。
(2)当内筒达到顶标高時,停止滑动内筒,扩大中心筒脚手架的直径,继续将内筒壁顶向上搭设,同时固定内爬杆。
(3)外筒壁向上滑动至顶标高时,停止滑动,外筒安装牛腿,中心筒脚手架外圈挑出牛腿,平台通过降模固定在牛腿上。
(4)封闭滑模平台,搭设锥壳脚手架。
(5)进行分部验算设计:①施工过程中各部分、各阶段荷载统计;②钢桁架内力分析及架体设计;③中心筒脚手架内力分析及架体设计;④滑模模具细部构造。
2、工艺整体设计(1)单层滑模装置,采用液压滑升模板的施工技术,主要采用两种施工体系:中心筒脚手架体系与滑模施工体系。
(2)对滑模施工系统中的主平台部分。
设计中应充分考虑筒仓上方锥壳结构的施工技术问题,同时,还应考虑滑模施工的具体技术要求。
将钢桁架的设计作为设计的关键,从而使主平台各部分受力均匀。
(3)中心筒脚手架系统作为整个工程的重要受力部分,在滑模施工过程中起着提升与支撑刚性平台的重要作用。
滑模施工完成后,中心筒脚手架与刚性平台共同承担筒仓上方锥壳结构受到的外力,这也是工程设计施工的重点。
(4)筒仓上面框架结构与锥壳结构施工技术。
该技术主要借助刚性支撑平台,在施工过程中搭设钢筋、模板与脚手架。
大直径预应力筒仓滑模施工技术
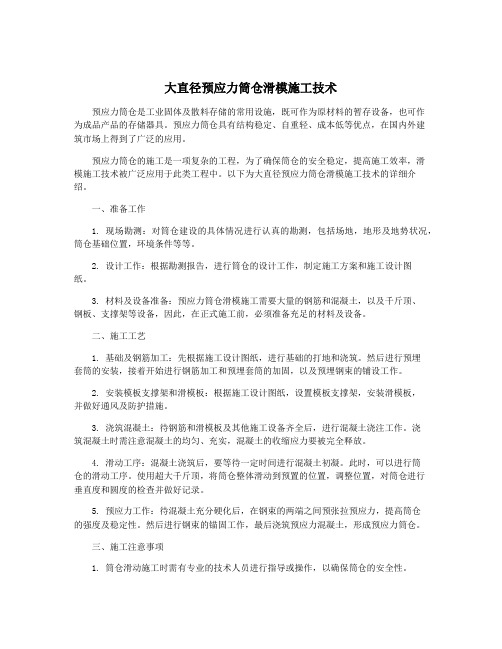
大直径预应力筒仓滑模施工技术预应力筒仓是工业固体及散料存储的常用设施,既可作为原材料的暂存设备,也可作为成品产品的存储器具。
预应力筒仓具有结构稳定、自重轻、成本低等优点,在国内外建筑市场上得到了广泛的应用。
预应力筒仓的施工是一项复杂的工程,为了确保筒仓的安全稳定,提高施工效率,滑模施工技术被广泛应用于此类工程中。
以下为大直径预应力筒仓滑模施工技术的详细介绍。
一、准备工作1. 现场勘测:对筒仓建设的具体情况进行认真的勘测,包括场地,地形及地势状况,筒仓基础位置,环境条件等等。
2. 设计工作:根据勘测报告,进行筒仓的设计工作,制定施工方案和施工设计图纸。
3. 材料及设备准备:预应力筒仓滑模施工需要大量的钢筋和混凝土,以及千斤顶、钢板、支撑架等设备,因此,在正式施工前,必须准备充足的材料及设备。
二、施工工艺1. 基础及钢筋加工:先根据施工设计图纸,进行基础的打地和浇筑。
然后进行预埋套筒的安装,接着开始进行钢筋加工和预埋套筒的加固,以及预埋钢束的铺设工作。
2. 安装模板支撑架和滑模板:根据施工设计图纸,设置模板支撑架,安装滑模板,并做好通风及防护措施。
3. 浇筑混凝土:待钢筋和滑模板及其他施工设备齐全后,进行混凝土浇注工作。
浇筑混凝土时需注意混凝土的均匀、充实,混凝土的收缩应力要被完全释放。
4. 滑动工序:混凝土浇筑后,要等待一定时间进行混凝土初凝。
此时,可以进行筒仓的滑动工序。
使用超大千斤顶,将筒仓整体滑动到预置的位置,调整位置,对筒仓进行垂直度和圆度的检查并做好记录。
5. 预应力工作:待混凝土充分硬化后,在钢束的两端之间预张拉预应力,提高筒仓的强度及稳定性。
然后进行钢束的锚固工作,最后浇筑预应力混凝土,形成预应力筒仓。
三、施工注意事项1. 筒仓滑动施工时需有专业的技术人员进行指导或操作,以确保筒仓的安全性。
2. 对钢筋、混凝土的选择要加以严格的检查,以确保质量合格。
3. 严格掌握施工工期及速度,避免过快或过慢对质量的影响。
大直径预应力筒仓滑模施工技术
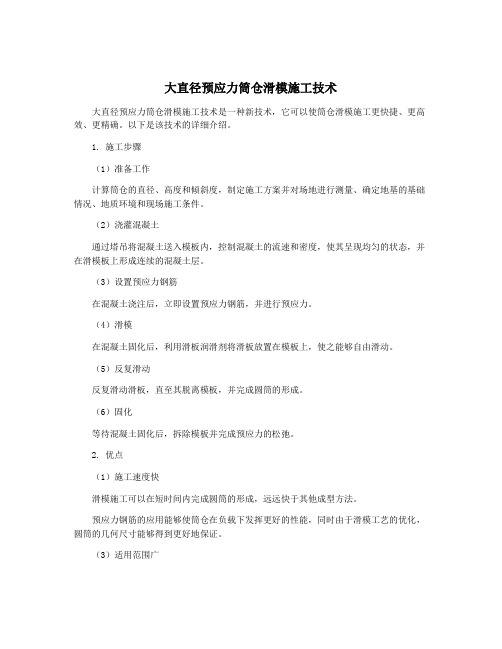
大直径预应力筒仓滑模施工技术大直径预应力筒仓滑模施工技术是一种新技术,它可以使筒仓滑模施工更快捷、更高效、更精确。
以下是该技术的详细介绍。
1. 施工步骤(1)准备工作计算筒仓的直径、高度和倾斜度,制定施工方案并对场地进行测量、确定地基的基础情况、地质环境和现场施工条件。
(2)浇灌混凝土通过塔吊将混凝土送入模板内,控制混凝土的流速和密度,使其呈现均匀的状态,并在滑模板上形成连续的混凝土层。
(3)设置预应力钢筋在混凝土浇注后,立即设置预应力钢筋,并进行预应力。
(4)滑模在混凝土固化后,利用滑板润滑剂将滑板放置在模板上,使之能够自由滑动。
(5)反复滑动反复滑动滑板,直至其脱离模板,并完成圆筒的形成。
(6)固化等待混凝土固化后,拆除模板并完成预应力的松弛。
2. 优点(1)施工速度快滑模施工可以在短时间内完成圆筒的形成,远远快于其他成型方法。
预应力钢筋的应用能够使筒仓在负载下发挥更好的性能,同时由于滑模工艺的优化,圆筒的几何尺寸能够得到更好地保证。
(3)适用范围广大直径预应力筒仓滑模施工技术适用于各种类型的筒仓,特别是大直径、高度较大、不规则形状或倾斜度较小的筒仓。
3. 注意事项(1)施工现场必须具备一定的平整度和坚实度,以确保滑模板的平稳滑动。
(2)混凝土的抗裂性能必须得到保证,以避免混凝土裂缝对筒仓性能产生不良影响。
(3)预应力钢筋的放置和张紧都需要严格按照工艺要求来进行,以确保筒仓的承载能力。
总之,大直径预应力筒仓滑模施工技术是一种高效、高精度的成型方法,其应用为圆筒的制作注入了新的活力,为工程建设提供更加稳定、可靠的支撑。
浅谈钢筋混凝土筒仓滑模施工质量控制要点
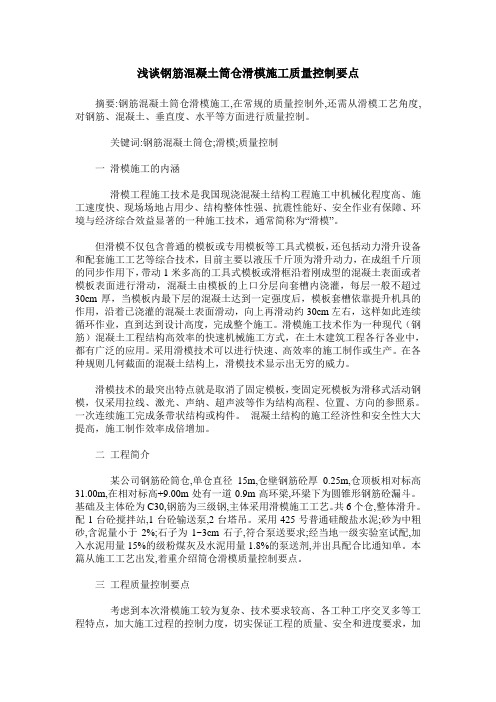
浅谈钢筋混凝土筒仓滑模施工质量控制要点摘要:钢筋混凝土筒仓滑模施工,在常规的质量控制外,还需从滑模工艺角度,对钢筋、混凝土、垂直度、水平等方面进行质量控制。
关键词:钢筋混凝土筒仓;滑模;质量控制一滑模施工的内涵滑模工程施工技术是我国现浇混凝土结构工程施工中机械化程度高、施工速度快、现场场地占用少、结构整体性强、抗震性能好、安全作业有保障、环境与经济综合效益显著的一种施工技术,通常简称为“滑模”。
但滑模不仅包含普通的模板或专用模板等工具式模板,还包括动力滑升设备和配套施工工艺等综合技术,目前主要以液压千斤顶为滑升动力,在成组千斤顶的同步作用下,带动1米多高的工具式模板或滑框沿着刚成型的混凝土表面或者模板表面进行滑动,混凝土由模板的上口分层向套槽内浇灌,每层一般不超过30cm厚,当模板内最下层的混凝土达到一定强度后,模板套槽依靠提升机具的作用,沿着已浇灌的混凝土表面滑动,向上再滑动约30cm左右,这样如此连续循环作业,直到达到设计高度,完成整个施工。
滑模施工技术作为一种现代(钢筋)混凝土工程结构高效率的快速机械施工方式,在土木建筑工程各行各业中,都有广泛的应用。
采用滑模技术可以进行快速、高效率的施工制作或生产。
在各种规则几何截面的混凝土结构上,滑模技术显示出无穷的威力。
滑模技术的最突出特点就是取消了固定模板,变固定死模板为滑移式活动钢模,仅采用拉线、激光、声纳、超声波等作为结构高程、位置、方向的参照系。
一次连续施工完成条带状结构或构件。
混凝土结构的施工经济性和安全性大大提高,施工制作效率成倍增加。
二工程简介某公司钢筋砼筒仓,单仓直径15m,仓壁钢筋砼厚0.25m,仓顶板相对标高31.00m,在相对标高+9.00m处有一道0.9m高环梁,环梁下为圆锥形钢筋砼漏斗。
基础及主体砼为C30,钢筋为三级钢,主体采用滑模施工工艺。
共6个仓,整体滑升。
配1台砼搅拌站,1台砼输送泵,2台塔吊。
采用425号普通硅酸盐水泥;砂为中粗砂,含泥量小于2%;石子为1~3cm石子,符合泵送要求;经当地一级实验室试配,加入水泥用量15%的级粉煤灰及水泥用量1.8%的泵送剂,并出具配合比通知单。
- 1、下载文档前请自行甄别文档内容的完整性,平台不提供额外的编辑、内容补充、找答案等附加服务。
- 2、"仅部分预览"的文档,不可在线预览部分如存在完整性等问题,可反馈申请退款(可完整预览的文档不适用该条件!)。
- 3、如文档侵犯您的权益,请联系客服反馈,我们会尽快为您处理(人工客服工作时间:9:00-18:30)。
滑升模板在大直径预应力钢筋混凝土筒仓滑模施工中的应用钢筋混凝土圆型筒仓用途广泛,坚固耐用,防水性能好,随着我国的国民经济飞速发展和科技水平的提高,预应力技术用于钢筋混凝土筒仓越来越普遍,筒仓的单仓设计容量越来越大,随之而来的是筒仓的直径大,高度高,目前在使用温度不超过60O C情况下设计多数采用无粘结预应力钢绞线作预应力钢筋。
由于混凝土筒仓直径大,高度高,所以仓壁采用滑模施工既节省施工成本,又有施工速度快的优点,但由于预应力钢绞线施工的介入,也给滑模施工提出了新的要求,近年来我公司与江苏新筑预应力工程有限公司合作施工的有粮食储仓,煤仓,水泥筒仓,污泥消化池等,获得较好的施工质量和经济效益,其中不少被评为省优、市优工程。
其中的关键技术主要有以下几点:一、执行标准1、《钢筋混凝土工程施工质量验收规范》(GB50204---2005)2、《滑动模板工程技术规范》(GB 50113-2005)3、《钢绞线钢丝无粘结预应力筋规范》(JG3006-93)二、无粘结预应力钢筋混凝土仓壁滑模施工工艺流程三、滑升装置设计1、滑升装置组成滑模装置包括模板系统、液压系统、操作平台系统。
1.1模板系统1.1.1围圈围圈采用Φ48×3.5mm钢管抛圆制作,共六种规格,其中模板围圈两种,提升架围圈四种规格,要求弧度准确,抛圆后在同一平面上,洞口边围圈根据图纸尺寸单独制作。
1.1.2提升架提升架横梁采用[10槽钢制作,立柱用Φ48×3.5mm钢管焊接制作,规格2400×200,沿圆周每隔1.3米~1.4米一只均匀布置。
1.13模板内外模板均采用,1200×300,1200×200,1200×150,1200×100的普通定型钢模板,回旋卡拼接(每条拼缝不少于4个)。
在模板上端第二孔、下端第一孔分别设双钢管围圈,以管卡勾头螺栓拉结模板(每条拼缝不少于2个),围圈以调节钢管与提升架立柱连接。
按照以上设置模板及围圈满足滑升强度和刚度要求。
安装好的模板单面倾斜度为模板高度的小于0.2%,按规范要求模板高2/3处净距为结构截面尺寸。
1.2液压提升系统液压系统千斤顶使用QYD60滚珠式千斤顶,每榀提升架设置一台QYD60滚珠式千斤顶,一次行程为25mm,额定顶推力60KN,施工设计时取额定顶推力50%计算为30KN。
主油管使用Φ16,支油管使用Φ8钢丝编织高压软管与各种分油器组成并联平行分支-式液压油路系统,额定压力≥15Mpa布管时尽可能使油路长短相近。
液压动力使用YHJ-80型控制台分区联动,油压机试验压力为15Mpa施工中油压控制在8Mpa正常压力升高滑动模板。
有千斤顶和油泵机技术参数和合格证。
提升架立柱为尺寸2400×200mm,用Φ48×3.5mm普通钢管焊接成的格构式构件,上横梁为单根10号槽钢,下横梁为双拼10号槽钢,立柱与横梁螺栓连接。
提升架规格根据仓壁厚度选用2400×1200,2400×1500扶壁处选用2400×1800(双千斤顶)2400×2100(双千斤顶)不等。
1.3滑模操作平台筒仓内外操作平台使用钢管桁架作为支承结构,桁架用Φ48×3.5mm普通建筑钢管和扣件搭设成型。
桁架支承在平台围圈上,平台围圈支承于提升架上,形成一空间网架承力系统,桁架高H=900,桁架上铺50×100木方,间距500,用铁丝与桁架扎牢,上铺18厚胶合板,外平台净宽1700,内平台铺满平台板宽度1000mm,高架平台距平台面约4000mm高,宽为4200mm,高架平台输送混凝土,堆放钢筋和接长支承杆之用;从外平台浇筑混凝土,内平台作为绑扎钢筋,高架平台上对称设两只混凝土集料斗,商品混凝土有输送泵进入料斗,再从料斗中人工放料用小推车布设到各浇筑点。
筒仓滑模滑升平台采用环形柔性平台,平台中心设置一圆形铁板Φ1000δ10,铁板与提升架之间用拉杆Φ16Q235将拉结形成整体,环形平台内侧加设折线形桁架予以加固。
开字架详图千斤顶布置详图2、滑升原理2.1支承杆为主要承压构件,下端浇筑在混凝土中为嵌固端,上端连结千斤顶为铰接端。
2.2千斤顶通过钢板与提升架下横梁连结,当油泵供油并加压时,千斤顶钢珠压紧支承杆带动提升架向上爬升而提升架腿上的四根钢管又通过模板围圈带动模板向上爬升,当模板爬升到预定高度时油泵关闭,千斤顶回油停止爬升,再绑扎钢筋浇筑混凝土,再开启油泵继续爬升。
如此循环一直滑升到仓顶。
3、滑升计算1.支承杆的允许承载力和千斤顶用量按GB 50113-2005规定以下式计算d)×(99.6 - 0.22L)(GB50113-2005)P O=(kP O支撑杆允许承载力L取千斤顶下卡头到模板下口第一个横向支撑扣件节点的距离d工作条件系数取0.7~1.0(视操作水平,滑模平台结构情况,刚性整体平台取0.7,柔性取0.8)k安全系数不小于2.0.2.千斤顶提升能力计算Nn=Pn千斤顶用量1取30KN)P千斤顶设计提升力值(额定提升力的2N竖向荷载总值包括平台自重、设备重、模板与混凝土的摩阻力、施工荷载。
4、提升部件计算4.1模板围圈抗力校核(1)浇筑工状模板围圈在浇筑工状主要承受新浇混凝土的侧压力和振捣荷载,根据《滑动模板工程技术规范》(GB50113-2005)附录A,1200高的模板侧压力取其最大值6KN/M,根据《混凝土结构工程施工及验收规范》(GB50204),振捣对垂直模板产生的荷载为4KN/M2,本工程模板高1.2M下围圈承受的荷载取4KN/M×0.6M=2.4 KN/Mq1=6 KN/Mq2=2.4 KN/M围圈的支点即提升架的距离按三跨连续梁计算,其计算简图如下:Q=q 1.4(q1+q2)=11.76 KN/MMmax=QL2/10=11.76×1.352/10=1.59 KN/M每道围圈由两根Φ48×3.5钢管组成:A=4.89CM2×2=9.78 CM2I=12.19CM4W=5.08 CM3×2=10.16i=1.58 CM钢管围圈在最大侧压力和振捣荷载作用下产生的内力为。
M=1.59 KN/M×103/10.16=156.5<[205]强度σ=W挠度校核f max=(0.667q l 4)/100EI=0.667×(6+2.4) ×103×13504/206000×121900×100=18.6/25=0.744<[ f ]允许挠度[ f ]为1/400=3.4MM(按清水模板)(2)提升工状:提升阶段围圈主要承受提升架竖向提升传给围圈的垂直荷载,按设计每榀提升架的额定提升力为30KN,由四根调节钢管承担每处的支反力为30KN/4=7.5KN计算简图:按三跨连续梁计算,最大弯矩M maxM=0.175PL=0.175×7.5×103×1350=1771875 N ·MMσ=W M =1771875/10.16×103=174 N/MM 24.2提升架主要部件内力校核:4.2.1调节钢管校核当提升机爬升时带动模板爬升的连结件为四根可调节钢管,主要克服模板向上滑升时的摩阻力和模板及围圈的自重,根据GB50113-2005条文说明1200高模板混凝土出模时间约4小时左右,摩阻力取2.5KN/M 2为宜,模板加围圈重0.58 KN/M 2每计算单元为1.2M ×1.35M=1.62 M 2计算单元内模板及围圈自重1.62 M 2×0.58 KN/M 2=0.94 KN可调钢管,计算简图:P==⨯+⨯294.02.15.24.1263.4KN 2.32KN (两根调节钢管,所以除以2) RA=P(1+λ) λ=M/L=150/200=0.75RA=2.32×1.75=4.05RB= -P λ= -2.32×0.75= -1.74MA= -2.32×0.15=0.348K N ·M =348000N ·MMσ=348000/5080=68.5 KN/MM 2f =EIL PM 32(1+λ)= 121900206000310)2.015.072.1(122⨯⨯⨯⨯M M KN =33.756.51=0.68MM <1/200<[0.75mm]4.2.2提升架下横梁强度和刚度计算提升架下横梁由千斤顶带动在提升工状下像一根扁担挑起平台上的全部荷载和模板与混凝土的摩阻力,在设计千斤顶的提升力限制为30KN ,因此计算简图如下:下横梁为双拼10号槽钢组成,其力学特征如下:Wx=79.32CM 3,Ix=396.6CM 4,γ=3.94CM ,E=2.06×105 Mmax=PL/4=45.130⨯=11.25K N ·M σ=W M =361032.791025.11⨯⨯142N/MM 2<[205 N/MM 2] f =EI PL 483=453106.3961006.248150030000⨯⨯⨯⨯⨯ 2.58mm <1/400<[3.75 mm ] 4.2.3拼装螺栓抗剪校核,[τ]= [190 N/MM 2],A=201 MM 2,提升架每根立柱和下横梁由两根螺栓连结,共四根。
P=30/4=7.5KNτ=P/A=7500/201=37.3N/MM2<[190 N/MM2]4.2.4千斤顶与提升架连结螺栓:主要承受提升时垂直向上的拉力,由四根Φ16螺栓连结。
P=30/4=7.5Φ16螺栓B级, [σ]= [205 N/MM2],螺纹处面积As=157 MM2P/A=7500/157=47.8 N/MM2<[205 N/MM2]4.2.5 环型平台挑三角架计算平台荷载30KN,减一侧摩阻力2.5×1.2×1.35=4.05KN30-4.05=10.95KN2q=10.95KN,通过三角架上弦上的檩条传三角架,三角架的杆件强度和稳定复核如下:P1=10.95×0.4 P2=10.95×0.45θ1=28°θ2=25°L1=800MM L2=900MMγ=15.8MM A=489MM I=12.19CM 4Rba=2(P1+P2)=18.615N Rah=-Rbh=h L 2 (P1+P2)+ hL P1=9.3075+8.2733=17.5808N S1=S2=P1×ctg θ1=10.95×0.4×ctg28°=8.238NS3= -P1×csc θ1=-10.95×0.4×csc28°= -9.33NS4=Rbh ×sec θ1= -17.5808×sec28°=-19.911 NS5= -(P1+P2) ×sec α= -18.615×sec45°=-26.326S7= S4×sin θ1=Rbh ×tg θ1= -19.911×sin28°= -17.5808×tg28°=-9.348N S6=2sin 27θP Rba S -+=︒⨯-+-25sin 45.095.10615.18348.9=10.268N 稳定性验算:(1)拉杆验算: S1=S2=A S =4898238=16.849N <[205] S6=A S =48910268=20.998 N <[205] (2)压杆验算:σ=AS ϕ,min i Lo =ϕ S 3:min i Lo =ϕ=8.15905=57.278 查表得:ϕ=0.829 S4: min i Lo =ϕ=8.151018=64.43 查表得:ϕ=0.802 S5:min i Lo =ϕ=8.151273=80.57 查表得:ϕ=0.716 S7:min i Lo =ϕ=8.15900=56.962 查表得:ϕ=0.829 S3:σ=AS ϕ=489829.09330⨯=23.015<[205]S4:σ=A S ϕ=489802.019911⨯=50.77<[205] S5:σ=A S ϕ=489716.026326⨯=75.191<[205] S7:σ=A S ϕ=489829.09348⨯=23.06<[205] 4.2.6提升架立柱强度计算:提升架立柱主要承受上向提升架时平台荷载对立柱形成的垂直拉力。