世界工厂精益生产制造 资料共126页
精益生产PPT

1990
精益制造Biblioteka 第2次管理革命1955
丰田生产方式
大批量生产方式
第1次管理革命
手工作坊生产 1776 1908
1950
1908 1913 1920
1990
1996
4
精益生产工具
精益生产中常用工具
New Material New Life
衍生自 丰田生产方式 的一种管理哲学
n 精 :即少而精,不投入多余的生产要素 n 益 :即所有经营活动都要有益有效,具有经济效益
3
精益生产发展史
New Material New Life
手工单件生产—— 大规模大批量——
精益生产——
1993 大规模定制敏捷制造
5
精益生产效用
New Material New Life
精益生产三大KPI (Q丨C丨D)
动作改善 作业流程改善 物流改善 品质改善等 八大浪费等
动作标准化 作业流程标准化 操作流程标准化等 整理 整顿 清扫 清洁 素养
6
精益生产推荐资料
书籍
微信公众号
1.《精益思想》 2.《改变世界的机器》
Lean Production
讲师: 2020年07月13日
New Material New Life
目录
CONTENTS
New Material New Life
2
何谓“精益”
JING
YI
New Material New Life
THE END
7
1. 精益智能工厂
-詹姆斯·P·沃麦克 2. 精益生产促进中心
3.《丰田生产方式》
精益生产_培训资料

精益生产
单元 1
5
注塑
6
4
7 装配
8 检查
9 包装
3 清洁
2
1
单元l 2
5
注塑 6
7 装配
8 检查
9 包装
4
3 清洁
2
1
单元3ቤተ መጻሕፍቲ ባይዱ
5
注塑 6
7 装配
8 检查
9 包装
4
3 清洁
2
1
在这里,物料的流动是单向的,没有返回,没有运输的浪费, 非常简洁 的行程安排。
郭辉
04:01 20
2、精益生产体系
为股东创造利润 向社会提供好的产品 企业和员工共同发展
郭辉
04:01 3
2、精益生产的的诞生
精益生产
企业经营的目的是制造利润 在不同的历史阶段,企业获得的方法是不同的.
售价=成本+利润(计划经济时) 售价-成本=利润(市场经济时) 售价-利润=成本(精益生产)
郭辉
04:01 4
2、精益生产的的诞生
--丰田章男
在亚洲金融危机中的做法:
紧缩产量,减少成本,培训员工,提高竞争
力!
04:01 7
精益生产
投资回报率和生产运作的关系
总资产收益率
销售回报率
X
总资产周转率
营业利润 / 销售净收入 销售净收入 / 资产总额
销售净 收入
-
直接 成本
-
管理间 接费用
毛利率 - 管理费用率
流动资 产
+
非流动 资产
1、如果库存在现场容纳不下,就要修建多余的仓库; 2、雇佣搬运工将库存运到仓库(搬运的浪费); 3、给每位搬运工购买一台叉车; 4、为了防止产品在库房中锈蚀和管理库存,就必须增加人员; 5、为了随时掌握库存的数量,管理部门需要相当数量的工时; 6、需要用计算机管理库存的人员。
精选精益生产资料

精益生产
4.按计划得实施 -选定的部门 -培训 -材料的准备 -生产线的设计、评审 -实施、评审
精益生产
5.对由影响作业人员的培训 -精益生产的基本思想 -实施的要求 -视觉指导书 -看板的管理
精益生产
• 塔克特
– 为了达到用户的需求所需要得产品制造平均 周转时间。
精益生产
员工和机器设计计算法
某一个过程所需要得员工、工序、单位置机
器、多位置机器的数量的计算方法。 -把每一个过程的标准操作表的标准时间除塔克特。
标准时间/塔克特
精益生产
员工和机器在多产品情况
-为了决定所需要的员工、机器数量:
把标准加权平均时间/塔克特
标准时间
产品规格 需求 机器 人员
A
10 36 36
塔克特=840/70=12
B
5 36 36
C
20 40 40
机器=41.6/12=3.5
D
35 45 45
需求
70
每天工作时间 840 840
人员=41.6/12=3.5
塔克特
12 12
加权平均时间 41.6 41.6
机器/人员 3.5 3.5
精益生产
所计算得数目有何意义
-机器数目要圆整 -人员数目要保留分数
精益生产
看板公式
∑[(需求)×( 数量)]×时间 需求-用户的要求
提议:
数量-使用的数量 时间-递送的时间
可对库存的物资作分级管理
A ≤ 一天
B = 二天
C ≥ 三天
精益生产
计算每天需求和计划
• 可用资源:生产线设计、人员、班次、送货时 间、移动时间等
精益生产(完美版)(PPT109页)
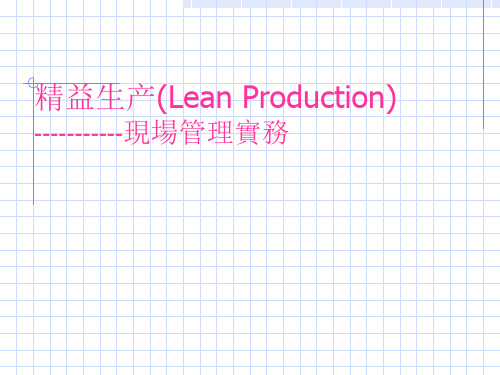
(3)消除浪费——管理的重要目的之一
Management
创造性的管理活动 提高产品和服务的附加价值
+1 增加价值
0
-1
消除浪费
最大限度地减少不增值劳动 封闭性的管理活动
精益思维(Lean Thinking)的5个基本原则
No.1 从顾客的角度而不是从某个公司、部门或机构 的角度确定价值;
No.2 确定设计、采购和生产产品的整个价值流中的 步骤,找出不增加价例 能力需求:100件/H
项目 能力 达成率 奖金 效率
工序1 100件/H
100% 标准产量奖金 个别效率合格
工序2 125件/H
125% 125%奖金 个别效率高
工序3 80件/H
80% 0
个别效率低
工序4 100件/H
80% 0
个别效率低
≠ 个别效率
整体效率
专业化作业有利于提高个别效率,不少企 业因此实行计件工资。
精益生产(Lean Production)
-----------現場管理實務
第一部分 精益生产簡介
很多精益技术源于日本企业的生产管理方法, 如看 板管理、全面质量管理(TQM)、快速换模等技术 都是 在丰田等日本公司的生产管理(NPS)中产生的。美国 的丹尼尔·琼斯教授等人通过大量细致的研究,并与 当 时欧美大量生产方式相比较后得出结论,正是这 些生 产管理方式使得日本企业(如丰田汽车公司)迅速成为 世界级的公司。这些管理思想和原则就是精益生产。
· 三不主义
77个个““零””目目标标 不良
保证
不良率高企, 批量事故多发, 忙于“救火”
· 零缺陷运动 · 工作质量 · 全员质量改善活动 · 自主研究活动 · 质量改善工具运用
精益生产制造

.标准成本系统无法实现两个主要的管理目标是: 标准成本系统无法实现两个主要的管理目标是: 标准成本系统无法实现两个主要的管理目标是A.降低成本和有效的反馈B.评估和降低成本C.评估和有效的反馈D.降低浪费和有效的反馈 2.丰田看到的浪费不包括: 丰田看到的浪费不包括: 丰田看到的浪费不包括A.次品的浪费B.过量生产的浪费C.等待的浪费D.搬运的浪费 3.杜绝浪费的三个步骤是: 杜绝浪费的三个步骤是: 杜绝浪费的三个步骤是 回答:正确A. 标准作业、标准流程、标准作业工序B. 标准流程、标准作业图、标准作业工序C. 标准作业、标准作业图、标准操作D. 标准作业、标准作业图、标准作业工序 4.国内制造业企业目前普遍采用的成本计算方法是: 国内制造业企业目前普遍采用的成本计算方法是: 国内制造业企业目前普遍采用的成本计算方法是 回答:正确A. 制造成本计算法B. 弹性边际成本法C. 成本归集法D. 成本分配方法 5.绩效管理系统的第一步是: 绩效管理系统的第一步是: 绩效管理系统的第一步是A. 绩效管理制度的建立B. KPI 的分析C. 企业战略分析D. 绩效目标设定第一讲 高成本的历史从战略的高度认识成本控制和成本管理, 从成本控制和成本管理的角度去认识战略, 低 成本战略是关键的支撑因素,或者叫支撑元素,它已被证明是有效的成本控制和成本方法。
高成本的历史在人类历史上,制造业发生了几次革命: 泰勒制 美国人泰勒研究了工人作业动作所费的时间, 发展出了一种新的体系, 叫做标准成本体 系。
福特生产方式 福特生产的模式特点包括: 规模经济 流水线 科学管理 通过流水线作业的大批量生产的方式,被称之为自动化方式。
比如由 A 车间、B 车间构 成一个工作小组,要把部件送到车间里进行装配,先到 A 车间,再到 B 车间,进行装配后, 再送到 C 车间,再进行装配。
流水线模式与“一个流” 图 1-1 流水线模式与“一个流”模式因为流水线的产生,规模经济即大规模的制造变成了可能。
生产管理精益生产资料汇编(doc 64页).doc

精益生产及其产生精益生产(Lean Production,LP),又称精良生产,其中“精”表示精良、精确、精美;“益”表示利益、效益等等。
精益生产就是及时制造,消灭故障,消除一切浪费,向零缺陷、零库存进军。
它是美国麻省理工学院在一项名为“国际汽车计划”的研究项目中提出来的。
它们在做了大量的调查和对比后,认为日本丰田汽车公司的生产方式是最适用于现代制造企业的一种生产组织管理方式,称之为精益生产,以针对美国大量生产方式过干臃肿的弊病。
精益生产综合了大量生产与单件生产方式的优点,力求在大量生产中实现多品种和高质量产品的低成本生产。
一、精益生产的产生与推广20世纪初,从美国福特汽车公司创立第一条汽车生产流水线以来,大规模的生产流水线一直是现代工业生产的主要特征。
大规模生产方式是以标准化、大批量生产来降低生产成本,提高生产效率的。
这种方式适应了美国当时的国情,汽车生产流水线的产生,一举把汽车从少数富翁的奢侈品变成了大众化的交通工具,美国汽车工业也由此迅速成长为美国的一大支往产业,并带动和促进了包括钢铁、玻璃、橡胶、机电以至交通服务业等在内的一大批产业的发展。
大规模流水生产在生产技术以及生产管理史上具有极为重要的意义。
但是第二次世界大依以后,社会进入了一个市场需求向多样化发展的新阶段,相应地要求工业生产向多品种、小批量的方向发展,单品种、大批量的流水生产方式的弱点就日渐明显了。
为了顺应这样的时代要求,由日本丰田汽车公司首创的精益生产,作为多品种、小批量混合生产条件下的高质量、低消耗进行生产的方式在实践中摸索、创造出来了。
1950年,日本的丰田英二考察了美国底持律的福特公司的轿车厂。
当时这个厂每天能生产7000辆轿车,比日本丰田公司一年的产量还要多。
但丰田在他的考察报告中却写道:“那里的生产体制还有改进的可能”。
战后的日本经济萧条,缺少资金和外汇。
怎样建立日本的汽车工业?照搬美国的大量生产方式,还是按照日本的国情,另谋出路,丰田选择了后者。
精益生产培训资料全

部品配置方法变更 只需移动手
原则2 动作要最短距离 皮带拉
制品要到作业者手的近处
原则4 取送材料利用重力和机械力
作业台
滑台
部品 B0X
自动滑入 包装箱内
4.2.4 动作要方便
原则1 动作利用重力和其他力量 利用孔 的大小
大
中
小
原则3 动作的方向和其变换要圆滑
动作的急变时不合适的
二、现场七大浪费
浪费
1. 过量生产 2. 库存 3. 搬运 4. 作业本身 5. 等待 6. 多余动作 7. 不良
2.1 过量生产
?生产多于下游客户所需 Making More Than Needed ?生产快于下游客户所求 Making Faster Than Needed
2.2 在库的浪费
1.2 大量生产方式
20世纪初,美国福特公司创建了世界上第一条汽车 生产流水线:以流水线形式生产大批量、少品种的产品, 以规模效应带动成本降低,并由此带来价格上的竞争力 特点是:
单一化:连续19年只生产黑色T型车 标准化:设备、零件、工装模具、工具 节拍化:按节拍组织生产 专一化:分解为7600工序,每个工人只承担
任何超过加工必 须的物料供应
2.3 搬运的浪费
不符合精 益生产的 一切物料 搬运活动
2.4 作业本身
对最终产品或服务 不增加价值的过程
2.5 作业本身
任何不增加产品或服务价值的 人员 和 设备的动作
2.6 等待的浪费
当两个关联要素间 未能完全同步时 所产生的空闲时间
7、不良的浪费
为了满足顾客的 要求而对产品或服 务进行返工!
4.2 动作分析改善
为了消除动作中的浪费,以如下 4个观点为基准,研究改善方法,做出好的方案。
精益生产WorldClassManufacturing世界级制造精益生产-PPT精品.ppt

Lean Thinking and Lean Manufacturing System 精益思维和精益生产系统
Starting with Toyota in the late 50’s and
catching on in the mid – 80’s in the reminder of the industrial world, Lean Manufacturing has become a key strategy for manufacturers
F.W. Taylor Frank F.W. Harris H. Dodge
IBM Toyota
Goldratt ASQC/ISO M. Hammer SAP, Oracle
现代生产管理的特征
r 以用户为中心 r 产品品种多样 r 柔性生产体系 r 制造技术先进 r 追求国际标准 r 运用智能设备
Henry Ford • Assembly line mass production • Produce in high volume with low variety • Single skill
福特首创的装配线是大规模低品种生产方式的代表, 工人被当成工作的机器
Toyota Production System (TPS) • Just-In-Time Production (produce only what is needed) • Pull System • High variety to meet customers wants
Output
Quality Assurance Customer satisfaction Sales/Marketing Customer service/support etc...
《精益生产》PPT课件

编辑ppt
持续改善
持续改善方法指逐渐、连续地增加改善。是日本持续改进之父今井正明在 《改善—日本企业成功的关键》一书中提出的,Kaizen意味着改进,涉及 每一个人、每一环节的连续不断的改进:从最高的管理部门、管理 人员到工人。持续改善的策略是日本管理部门中最重要的理念,是日本人 竞争成功的关键
自我反省和现地现物16改善原则取消合并重排简化17制造业经常面临的问题产能不够无法满足市场需求不能按时按量交货人员效率低下库存太高积压资金质量无法满足客户要求生产成本太高问题重复发生每日忙于救火研发能力不够量产时浮现大量问题供应商无法准时保质保量交货以上这些问题的解决之道精益生产
编辑ppt
1
主讲人:朱宝
15
编辑ppt
十二原则
1:消除八大浪费:过量生产、等待时间、运输、库存、过程(工序)、动 作、产品缺陷以及忽视员工创造力。 2:关注流程,提高总体效益 3:建立无间断流程以快速应变 4:降低库存 5:全过程的高质量,一次做对 6:基于顾客需求的拉动生产 7:标准化与工作创新 8:尊重员工,给员工授权 9:团队工作 10:满足顾客需要 11:精益供应链 12:"自我反省"和"现地现物”
16
改善原则
取消
编辑ppt
简化
合并
重排
17
编辑ppt
制造业经常面临的问题
➢产能不够无法满足市场需求 ➢不能按时按量交货 ➢人员效率低下 ➢库存太高,积压资金 ➢质量无法满足客户要求 ➢生产成本太高 ➢问题重复发生,每日忙于救火 ➢研发能力不够,量产时浮现大量问题 ➢供应商无法准时保质保量交货 以上这些问题的解决之道——精益生产:
4
质量、低消耗进行生产的方式在实践中摸索、创造出来了。
精益生产PPT模板

四、从价格谈与我们的的关系
旧模式: 成本+ 效益 = 价格 [固定] [固定] [获得] 新模式: 价格 –效益 =成本 [固定] [固定] [获得]
旧模式: .公司预期利润是通过价格设定而得.
新模式:价格由市场而定,利润由股东而定,這意味必须达至最高成本,而节省成本便成为公司的必要措施.
*
丰田式生产管理 丰田式生产管理(Toyota Management),或称丰田生产体系(Toyota Production System,TPS)由日本丰田汽车公司的副社长大野耐一创建,它包括: 经营思路、生产组织、物流控制、质量管理、成本控制、库存管理、现场管理、现场改善等在内的较为完整的生产管理技术与方法体系。 丰田喜一郎、大野耐一,丰田生产模式创始人…
5. 库存浪費
存货过多 -- 过多的原材料 • 交货周期过长? • 错误的订货量? -- 过多的成品 • 是因为生产过剩? • 是因为生产排期错误?
*
动作太大 单手空闲 转身动作过大 操作动作不流畅 重复/不必要的动作 不必要的弯腰动作
标准作业的直接目的
*
标准作业 以人的动作为中心,把工序集中起来,以没有MUDA的操作顺序有效的进行生产的方法。 标准工时(T.T) 生产一件产品应该使用的时间值。 循环时间(C.T) 作业者一个人进行标准作业时,毫不困难的、最快的、一个循环的实际作业时间(包括步行时间),但不包括空手等待时间。 标准中间在库(标准手持) 按照标准作业规定的作业顺序进行操作时,为了能够反以相同的循序、动作操作生产而在工序内持有的最少限度的待加工品。(入料口和成品货店的在库不属于标准手持)
2S
3S
5S
4S
*
B15
C16
精益生产资料

精益生产(LP)二战以后,丰田汽车公司的丰田和大野考察了福特汽车公司轿车厂。
当时,这个厂日产7000辆轿车,比丰田公司一年的产量还多。
但丰田却没有想到仅简单地照搬福特的生产模式,他认为“那里的生产体制还有些改进的可能”。
回到日本后,丰田和大野进行了一系列的探索和实验,根据日本国情(社会和文化背景、严格的上下级关系、团队工作精神),建立了一整套新的生产管理体制,采用精益生产方式组织生产和管理,使丰田汽车的质量、产量和效益都跃上一个新台阶,变成世界汽车之王。
与此同时,其他的汽车公司和别的行业也纷纷采用这种组织管理方式,使日本经济得到飞速发展。
与技艺性生产和大批量生产不同,精益生产组合了前两者的优点,避免了技艺性生产的高费用和大批量生产的高刚性。
为此目的,精益生产采用的是由多能工人组成的工作小组和柔性很高的自动化设备。
与大批量生产不同,精益生产的一切都是“精简”的:与大批大量生产相比,只需要一半的劳动强度、一半的制造空间、一半的工具投资、一半的产品开发时间、库存的大量减少、废品大量的减少和品种大量的增加。
两者的最大区别在于它们的最终目标上:大量生产强调“足够”好的质量,因此总是存在着缺陷;而精益生产则追求完美性(不断降低价格、零缺陷、零库存和无限多的品种)。
一、丰田公司的精益生产1. 精益生产的出现由丰田和大野创造的精益生产技术可以通过一个实例来说明。
在大批大量生产方式下,制造汽车覆盖件的冲压模的更换是个很大的问题。
由于精度要求极高,模具的更换即昂贵且费时,需要极高技术的工人来完成。
为了解决这个问题,西方汽车制造商采用一组冲压机来生产同一种零件,于是,他们可以实现几个月甚至几年不更换模具。
对于50年代的丰田公司,这种办法却行不通,他们没有足够的资金来购买好几百台冲压机用于汽车覆盖件的生产,他们必须用少数的几条生产线生产所有汽车的冲压件。
于是,大野发明了一种快速更换模具新技术(SMED法──Single Minute of Dies),这种技术使更换一副模具的时间从1天减少到3分钟,也不需要专门的模具更换工。
从精益生产到世界级制造资料PPT文档94页

16、人民应该为法律而战斗,就像为 了城墙 而战斗 一样。 ——赫 拉克利 特 17、人类对于不公正的行为加以指责 ,并非 因为他 们愿意 做出这 种行为 ,而是 惟恐自 己会成 为这种 行为的 牺牲者 。—— 柏拉图 18、制定法律法令,就是为了不让强 者做什 么事都 横行霸 道。— —奥维 德 19、法律是社会的习惯和思想的结晶 。—— 托·伍·威尔逊 20、人们嘴上挂着的法律,其真实含 义是财 富。— —爱献 生
46、我们若已接受最坏的,就再没有什么损失。——卡耐基 47、书到用时方恨少、事非经过不知难。——陆游 48、书籍把我们引入最美好的社会,使我们认识各个时代的伟大智者。——史美尔斯 49、熟读唐诗三百首,不会作诗也会吟。——孙洙 50、谁和我一样用功,谁就会和我一样成功。——莫扎特
ห้องสมุดไป่ตู้
精益生产的相关知识讲述(ppt 102页)

供應商 發展團隊
Honda 部門員工
27
BP tea27m
BP的範圍及成效
❖BP team 主要在少數特定工作範圍的改善,初期 避免大量資本投資或額外人力。 ▪ 技術、工作組織、二階供應商及員工的問題, 例:積極度、教育訓練、報酬、保障福利。
❖ 對於BP團隊關注的生產線,執行改善的成效:
28
28
BP的精神
❖Capitol Plastics 介紹 ❖前期:BP團隊支援Capitol的原因 ❖中期:BP輔導的過程與成效 ❖後期:BP專案在Capitol的結果 ❖本個案小結
38
Capitol Plastics 介紹
❖Capitol 原本是美國三巨頭的供應商,隨著 三巨頭生意衰退,開始接觸新客戶,便開 始與Honda接觸。
26
26
“BP” at Honda
❖BP :Best Practice, Best Process, and Best Performance.
❖ 美國Honda成立”供應商發展團隊”,主要為監 督BP及其他供應商改善行為。
❖BP team:由供應商發展團隊選出少數成員與其 他Honda各部門員工組成。被BP選中的供應商 BP team將進駐供應商工廠與供應商的員工一起 工作數週。
7
7
精實生產概念
❖ 及時化生產(Just In Time, JIT) ❖ 徹底消除浪費 ❖ 拉式生產系統 ❖ 平準化生產 ❖ 看板管理(kanban) ❖ 持續改善(Kaizen) ❖ 現場現地現物主義
8
8
背景脈絡
❖1980年代汽車產業,日商開始在海外投資 製造廠,在北美建立新裝配廠,一開始以 日本的零組件為主。
25
25
精益化生产资料整理

精益化生产培训资料整理一、何谓精益化生产方式?精益生产(Lean Production,简称LP)是美国麻省理工学院数位国际汽车计划组织(IMVP)的专家对日本丰田准时化生产JIT(Just In Time)生产方式的赞誉称呼。
精,即少而精,不投入多余的生产要素,只是在适当的时间生产必要数量的市场急需产品(或下道工序急需的产品);益,即所有经营活动都要有益有效,具有经济效益。
二、效率、效能、效果1、效率Efficiency--产出/投入比例值效率就是做事要快,且快而不乱。
贯穿精益生产始终的一个观念是生产不需要快、不需要忙,而是要注意减少浪费、降低消耗【案例1】甲、乙两个大学生在一次考试中,甲得了81分、乙考了78分,从得分情况上看,甲比乙好。
但是,甲每天要用12个小时读书,不参加运动、不参加社交活动,是个标准的书呆子。
而乙不仅参加了学校里的多项运动,还参加了社团活动、辩论比赛,且每天花在学习上的时间只有2个小时,因此从效率看,乙更高一些。
【案例2】一家企业的生产线有很多步骤, A步骤需要5个小时,B步骤需要3个小时,C步骤需要2个小时。
A单位要花5小时,B单位要花3小时,C单位要花2小时,如果这三个单位同时出发,就是一个浪费。
在这家企业中,A单位的5小时叫做核心流程,只要抓住这个核心步骤,让A单位立刻出发,过2个小时候B单位再出发,过3个小时后C单位再出发,最后同时会合。
同时会合比同时出发重要。
2、效能Effective--组织/分工/授权/OEM【案例】一次篮球明星乔丹所在的球队和另一个球队比赛,乔丹队得了99分,乔丹一个人就得了51分。
参加比赛的另一个球队,核心球员打得不怎么样,得了20分,但是他的助攻能力强,全队得了100分。
点评:乔丹打得好,是效率高,但球队输了,是效能不高,所以工作中一定要分工。
效能就是不要所有的东西都自己做,这就是精简、效益的观念--不只求快,还要懂得合作。
3、效果Effect--对策办法+调配布局【案例】1950年,26岁的田口先生是日本一个企业里的小小助理工程师。