垂直化学沉锡线槽液除铜过滤方法的改进
锡火法精炼铜浮渣处理的新方法
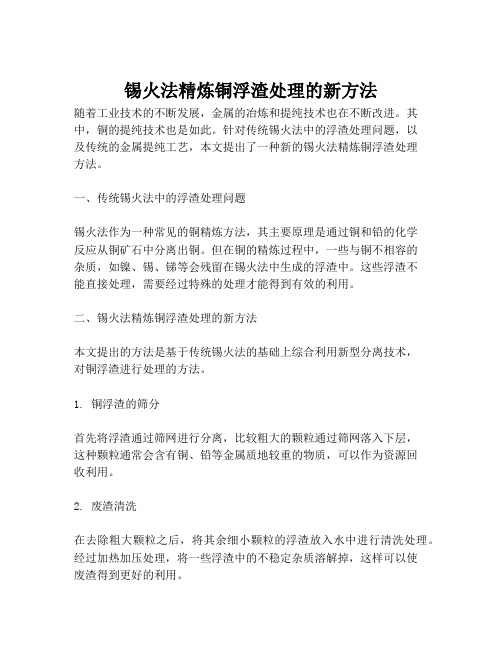
锡火法精炼铜浮渣处理的新方法随着工业技术的不断发展,金属的冶炼和提纯技术也在不断改进。
其中,铜的提纯技术也是如此。
针对传统锡火法中的浮渣处理问题,以及传统的金属提纯工艺,本文提出了一种新的锡火法精炼铜浮渣处理方法。
一、传统锡火法中的浮渣处理问题锡火法作为一种常见的铜精炼方法,其主要原理是通过铜和铅的化学反应从铜矿石中分离出铜。
但在铜的精炼过程中,一些与铜不相容的杂质,如镍、锡、锑等会残留在锡火法中生成的浮渣中。
这些浮渣不能直接处理,需要经过特殊的处理才能得到有效的利用。
二、锡火法精炼铜浮渣处理的新方法本文提出的方法是基于传统锡火法的基础上综合利用新型分离技术,对铜浮渣进行处理的方法。
1. 铜浮渣的筛分首先将浮渣通过筛网进行分离,比较粗大的颗粒通过筛网落入下层,这种颗粒通常会含有铜、铅等金属质地较重的物质,可以作为资源回收利用。
2. 废渣清洗在去除粗大颗粒之后,将其余细小颗粒的浮渣放入水中进行清洗处理。
经过加热加压处理,将一些浮渣中的不稳定杂质溶解掉,这样可以使废渣得到更好的利用。
3. 新型化学活性分离技术通过经过清洗处理的废渣,使用新型化学活性分离技术,进一步将其中的金属离子分离出来。
其中,离子交换、膜过滤、离子选择性沉淀等都可以作为化学活性分离技术的手段。
这样分离的金属离子可以更加纯度地提取,并达到有效的回收及再利用。
三、新方法的优点及局限性1. 新方法相对于传统锡火法中浮渣处理方法更加先进,其效率更高,经济效益更加显著。
2. 新方法可以进一步提高铜提纯产品的质量,达到更好的质量控制。
3. 新方法的局限性在于其需要更加高超的技术和设备作为支持,在实际应用中需要耗费较高的人力和物力成本。
综上所述,锡火法精炼铜浮渣处理的新方法是一种先进的铜浮渣处理方法。
该方法在传统的锡火法基础上采用了化学活性分离技术的手段,对浮渣进行了综合利用,可以更好地使废渣得到回收和再利用。
虽然该方法有些需要耗费较高的人力和物力成本,但作为一种先进的技术手段,其效益显著,并将有望在今后的工业生产中得到更广泛的应用。
含铜废水处理工艺分析
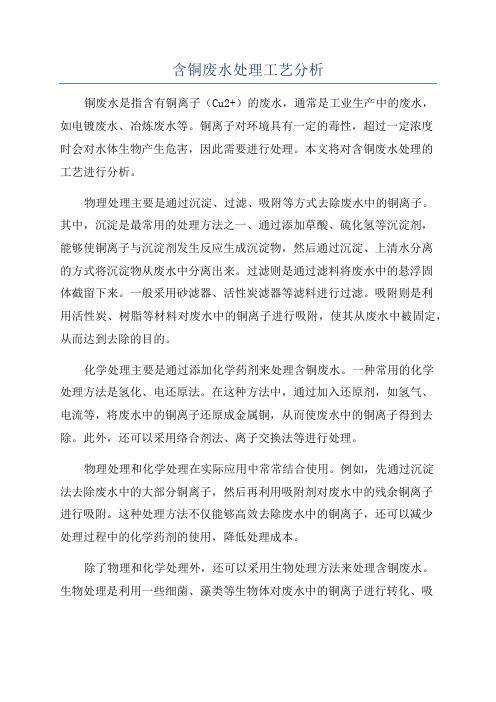
含铜废水处理工艺分析铜废水是指含有铜离子(Cu2+)的废水,通常是工业生产中的废水,如电镀废水、冶炼废水等。
铜离子对环境具有一定的毒性,超过一定浓度时会对水体生物产生危害,因此需要进行处理。
本文将对含铜废水处理的工艺进行分析。
物理处理主要是通过沉淀、过滤、吸附等方式去除废水中的铜离子。
其中,沉淀是最常用的处理方法之一、通过添加草酸、硫化氢等沉淀剂,能够使铜离子与沉淀剂发生反应生成沉淀物,然后通过沉淀、上清水分离的方式将沉淀物从废水中分离出来。
过滤则是通过滤料将废水中的悬浮固体截留下来。
一般采用砂滤器、活性炭滤器等滤料进行过滤。
吸附则是利用活性炭、树脂等材料对废水中的铜离子进行吸附,使其从废水中被固定,从而达到去除的目的。
化学处理主要是通过添加化学药剂来处理含铜废水。
一种常用的化学处理方法是氢化、电还原法。
在这种方法中,通过加入还原剂,如氢气、电流等,将废水中的铜离子还原成金属铜,从而使废水中的铜离子得到去除。
此外,还可以采用络合剂法、离子交换法等进行处理。
物理处理和化学处理在实际应用中常常结合使用。
例如,先通过沉淀法去除废水中的大部分铜离子,然后再利用吸附剂对废水中的残余铜离子进行吸附。
这种处理方法不仅能够高效去除废水中的铜离子,还可以减少处理过程中的化学药剂的使用,降低处理成本。
除了物理和化学处理外,还可以采用生物处理方法来处理含铜废水。
生物处理是利用一些细菌、藻类等生物体对废水中的铜离子进行转化、吸附等方式达到去除的目的。
这种方法具有良好的环境友好性,但操作难度较大,且处理效果受环境因素影响较大。
综上所述,含铜废水处理可以通过物理处理、化学处理和生物处理等方式进行。
根据实际情况选择合适的工艺组合进行处理,能够高效去除废水中的铜离子,保护环境安全。
电路板沉铜工作总结怎么写

电路板沉铜工作总结怎么写
电路板沉铜工作总结。
电路板沉铜工作是电子制造过程中非常重要的一环,它直接影响着电路板的质
量和性能。
在这篇文章中,我们将总结电路板沉铜工作的关键步骤和注意事项,希望能为电子制造行业的从业人员提供一些帮助和启发。
首先,电路板沉铜工作的第一步是表面处理。
在这一阶段,我们需要对电路板
的表面进行清洁和去除氧化处理,以确保沉铜过程能够顺利进行。
这一步骤的关键在于选择合适的清洁剂和去氧化剂,以及控制清洁和处理的时间和温度。
接下来,我们需要进行化学沉铜。
在这一步骤中,我们将电路板浸入含有铜离
子的化学溶液中,利用化学反应在电路板表面沉积一层均匀的铜膜。
这一步骤的关键在于控制化学溶液的成分和浓度,以及控制沉铜的时间和温度。
最后,我们需要进行电镀处理。
在这一步骤中,我们将电路板浸入含有铜离子
的电镀液中,利用电化学反应在电路板表面沉积一层均匀的铜膜。
这一步骤的关键在于控制电镀液的成分和浓度,以及控制电镀的时间和电流密度。
总的来说,电路板沉铜工作是一个复杂而又精细的工艺过程,需要严格控制各
个环节的参数和条件,才能确保沉铜的质量和均匀性。
希望本文能够为电子制造行业的从业人员提供一些参考和帮助,让他们在电路板沉铜工作中能够更加得心应手。
关于PCB化学沉锡常见技术问题的分析研究与改善

关于PCB化学沉锡常见技术问题的分析研究与改善作者:赵金亮来源:《中国新通信》2016年第24期【摘要】 PCB沉锡工艺是为有利于SMT与芯片封装而特别设计的在铜面上以化学方式沉积锡金属镀层,是取代Pb-Sn合金镀层制程的一种绿色环保新工艺,已广泛应用于电子产品、五金件、装饰品等。
印刷线路板有两个较为常用的工艺:喷锡和沉锡。
喷锡,主要是将PCB 板直接侵入到熔融状态的锡浆里面,在经过热风整平后,在PCB铜面会形成一层致密的锡层,厚度一般为1um-40um。
沉锡,主要是利用置换反应在PCB板面形成一层极薄的锡层,锡层厚度大约在在0.8um-1.2um之间,沉锡工艺更普遍应用在线路板表面处理工艺当中。
本文就PCB化学沉锡导致的可焊性不良的问题进行详尽的分析与研究,希望能给业界同仁一点启发。
【关键词】化学沉锡喷锡可焊性不良一、前言作为电子产业高速发展的基础工程,印制电路板(PCB)已是现代电子设备不可缺少的配件,无论上天下海之高端电子设备,还是家用电器和电子玩具都少不了负载电子元器件和电信号的PCB,PCB是随着整个电子信息产业的发展而发展的。
沉锡工艺是较为常见的一种线路板表面处理技术,主要目的是为了保证电子元器件和线路板之间连接的牢固、可靠,使电信号的传输更加稳定,由此可见,沉锡技术在线路板制造工艺中的应用还是十分重要的。
在实际生产过程中,化学沉锡也是有很多技术难题,沉锡不良、表面变色、厚度不均、厚度超差等等,这些问题了一直困扰着技术人员,本人根据这么多年的工作经验,结合自己扎实的理论基础,就化沉锡不良问题进行简要的剖析,具体如下。
二、化学沉锡常见技术问题分析化学沉锡是PCB沉锡工艺的一种,应用较为普遍,其工作原理是通过改变铜离子的化学电位使镀液中的亚锡离子发生化学置换反应,其实质是电化学反应。
被还原的锡金属沉积在铜基材的表面上形成锡镀层,且其浸锡镀层上吸附的金属络合物对锡离子还原为金属锡起催化作用,以使锡离子继续还原成锡,其化学反应方程式为2Cu+4TU+Sn2→2Cu+(TU)2+Sn。
杂铜电解系统净液脱铜的技术改造
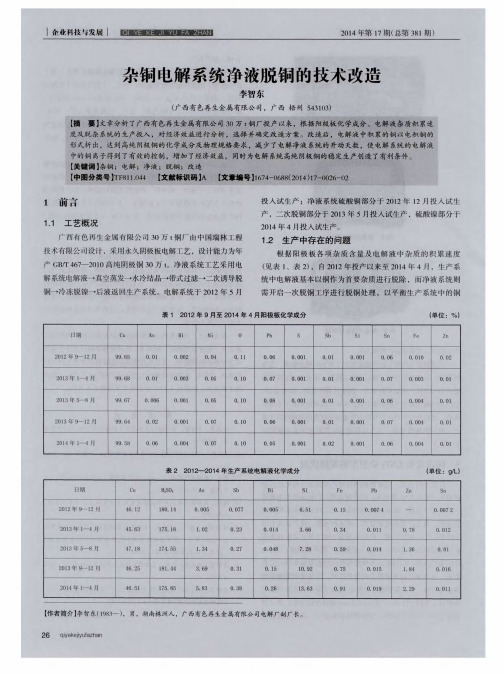
槽给液方式 为上 进下 出且单槽进 出 ,每槽设计 2 4块铅 阳极及 2 3块永久 不锈钢 阴极 ,在生产 过程 中漂浮 阳极泥 被出液挡 板
阻挡 ,不易排 除槽 外 ,而且 电解液上 、下层浓度差较大 ,造 成 生产的电极铜 化学成分 只能达到 1 级铜的标准 ,无法得到高纯 阴极铜 ,经济效益低 。
图 1 一次脱铜 电解槽 电解液流 向图
电极脱铜槽开设在生产 系统 内 ,缩短 了脱铜 的工 艺流程 , 电解 液中铜离子浓度及系统各方面的控制水平 、稳定性有了较
由于净液系统无阴极板 剥片设备 ,生产 出来 的电极铜采用 人工剥离方式 ,劳动强度较 大 ,且在剥铜过程 中易对不锈钢阴 极板板面造成损 坏 ,从 而增加 了维护成本 。
大的提升 ;同时 ,减少 了一道生产 工序 ,降低 了设备 使用率 , 延长 了设备使用寿命,精简了劳动岗位 ,降低了劳动强度。
2 0 1 3 年共产出阴极铜 1 1 3 8 5 4 . 9 t ,其 中电积铜 1 2 3 5 . 4t ,硫
2 改造 方案
针对上述 问题进行分析后发现 ,如果能将一次脱铜 槽开至 生产系统 内 ,就能解决 以上 问题 。根据生产系统阳极板的投 入
3 改造 后的效 果
改造于 2 0 1 2年 1 0月初 步实施完成 ,并 于 2 0 1 3年 1月正 式投入生 产 ,投产 至今 已运行 1 年 多 。生 产实践证 明 ,改 造 后的系统工 艺稳定 、效 果 明显 。2 0 1 3年全年净 液开动 天数 为 9 0 d ,主要 生产硫酸铜 ,大大减少了净液系统的开动天数 。
2 0 1 4年第 1 7 期( 总第 3 8 1 期)
企业科技与发展
浓度 。而在 实际生产 过程 中 ,由于阳极板 供应计 划差 、设 备 故 障率较 高 、电解生产 系统 扩液 等因素 ,所 以电解及净 液 2 个 系统 匹配生产 易 出现体积控 制难度 大 的问题 ,直接危及 阴 极铜产 品的质量 。 净液一次脱铜槽 电解液 流向图如 图 1 所示 。净液一次脱铜
一种再生锡除铜方法

一种再生锡除铜方法引言锡和铜是常见的金属材料,广泛应用于制造业。
然而,在使用过程中,锡和铜表面容易积聚氧化物、煤尘、油污等杂质,影响其再利用和性能。
因此,有必要研究一种高效的再生锡除铜方法,以提高再生金属材料的质量和利用率。
传统方法存在的问题传统的再生锡除铜方法主要有熔炼法、酸洗法和电解法。
然而,这些方法存在一些问题:1. 熔炼法:该方法需要高温条件,对环境有一定的污染,并且会造成能源浪费。
2. 酸洗法:使用酸溶液进行清洗会造成对环境的污染,并且酸洗过程复杂,操作繁琐。
3. 电解法:电解法需要大量的电能消耗,并且操作复杂,需要经验丰富的操作人员。
因此,需要研究一种高效、环保、简便的再生锡除铜方法。
一种新型再生锡除铜方法的研究近年来,学者们提出了一种基于化学溶液的再生锡除铜方法,该方法在环保和高效方面取得了显著的进展。
该方法主要包括以下几个关键步骤:1. 金属材料的预处理将待处理的再生锡材料进行彻底的清洁,去除外层油污和杂质,以提高后续步骤的效果。
2. 铜离子溶解使用一种特定的化学溶液对含有铜离子的再生锡材料进行溶解。
该溶液可以有效地将铜离子从锡材料中分离出来,而不影响锡的再利用。
3. 溶液处理将溶解得到的含有铜离子的溶液进行后续处理。
可以采用化学还原、电解或其他适合的技术将铜离子转化为固态或液态的纯铜,以便进一步提取和利用。
4. 锡材料回收对溶液处理后得到的纯铜进行进一步的处理,以提取出纯铜作为再生材料,用于生产其他铜制品。
优点和前景相比传统的再生锡除铜方法,这种基于化学溶液的新型方法具有以下优点:1. 环保性:该方法无需高温和酸洗,减少了对环境的污染,符合绿色环保的理念。
2. 高效性:该方法操作简单,能够高效地分离锡和铜,提高再生金属材料的质量和利用率。
3. 经济性:该方法使用的化学溶液一般易得且价格较低,能够降低生产成本。
该方法在再生锡除铜领域具有广阔的应用前景。
未来,研究人员可以进一步改进溶液处理过程,提高分离效率和纯度,以满足不同领域的需求。
金属制品厂废水处理工艺改进与优化

金属制品厂废水处理工艺改进与优化随着金属制品行业的快速发展,金属制品厂的废水处理问题日益凸显。
废水中含有大量重金属离子、有机物和悬浮物等有害物质,对环境造成了严重污染。
因此,金属制品厂废水处理工艺的改进与优化至关重要。
本文将探讨金属制品厂废水处理工艺的现状及存在的问题,并提出相应的解决方案。
一、金属制品厂废水处理工艺现状金属制品厂通常采用常规的废水处理工艺,包括预处理、沉淀、过滤、氧化和吸附等步骤。
然而,现有工艺在处理高浓度污染物和有机物方面存在一定的局限性。
例如,传统的沉淀法对于重金属离子去除效果不佳,滤液处理过程中容易出现堵塞等问题。
此外,未能充分回收和利用废水中的资源也是一个亟待解决的问题。
二、金属制品厂废水处理工艺改进方案为了解决金属制品厂废水处理工艺存在的问题,可以采取以下几个方面的改进措施:1. 高效沉淀剂的应用:传统的沉淀法存在对重金属离子去除效果低的问题。
可以考虑引入高效沉淀剂,如聚合物沉淀剂、太阳能辐照法等,以提高沉淀效果。
2. 活性炭吸附:利用活性炭对废水中的有机物进行吸附可以有效提高废水处理效果。
通过调整活性炭的孔径和表面性质,可提高有机物吸附量和去除率。
3. 膜技术的应用:膜技术包括微滤、超滤、纳滤和反渗透等,可以有效去除废水中的悬浮物、胶体物质和微量有机物。
此外,膜技术还可以实现废水的分离和浓缩,便于后续处理和资源回收。
4. 多级处理系统的建立:针对金属制品厂废水中含有多种有害物质的特点,建立多级处理系统可以提高废水处理效率。
将不同的工艺组合在一起,可以有效去除废水中的各类污染物。
5. 资源化利用:金属制品厂废水中含有大量的有价值金属和有机物。
通过合理的分离和回收,可以实现废水资源化利用,实现废物减量化和资源循环利用。
三、金属制品厂废水处理工艺优化方案除了改进工艺,金属制品厂还可以针对废水处理工艺进行优化,以提高处理效果和降低成本。
以下是一些建议的优化方案:1. 定期检测和监控:建立废水处理系统的实时监测系统,定期检测废水处理效果和出水水质,及时发现问题并进行调整和优化。
垂直化学沉锡线槽液除铜过滤方法的改进

垂直化学沉锡线槽液除铜过滤方法的改进阐述了一种化学沉锡线的沉锡槽液除铜工艺方法,对传统的过滤工艺进行改进,包括以下工艺步骤:吸取槽液→冷凝分离→压滤装置挤压过滤→槽液回用→废渣排出,本方法采用压轮挤压式过滤的方式,可最大限度的回收利用沉锡槽液,过滤效率从20%提高到70%,极大的节省了制造成本;本方法采用的压轮挤压过滤装置设计结构简单,占地面积小,便于操作和维护保养;过滤后的污泥废渣含有极少量的沉锡槽液,降低了废弃物处理的成本。
标签:沉锡槽液;除铜;压滤装置1 前言化学沉锡表面涂覆作为一种安全、稳定的表面处理工艺,广泛应用与印制线路板的制造当中。
化学沉锡线设备一般分为垂直式和水平式生产线两种,但不论哪一种设备,都存在这沉锡槽液的除铜问题:在沉锡槽液对印制线路板进行化学反应的过程中,线路板导电线路上的铜被不断地置换进沉锡槽中形成离子,而金属锡则在导电线路表面不断沉积,形成焊接媒介层;当沉锡槽液中的铜离子含量达到一定程度,槽内的化学反应平衡会遭到破坏,严重时甚至会停止反应,而且过高的铜离子含量会导致沉锡层的稳定性变差,影响产品品质。
因此,化学沉锡线都会在沉锡槽配置沉锡槽液的除铜过滤装置,用于除去沉锡槽液中不断生成的铜离子。
传统的设备一般采用“重力垂流”的过滤方式,依靠槽液的自重进行过滤,不但效率低下,而且槽液过滤不净,浪费严重。
新式设备采用了“板式压滤”的过滤方式,效率有明显提高,但机械结构复杂,维护保养不便。
2 过滤方法的改进(1)锡槽中温度为69±2℃的沉锡槽液通过出液泵泵入槽液冷凝分离器,出液泵由电磁阀控制,每次泵出固定体积的沉锡槽液。
(2)泵入冷凝分离器的沉锡槽液使用5±2℃的冷水冷却并进行搅拌,当槽液温度降低达到11℃时,槽液中富集的铜离子就会开始析出,形成絮状凝结物;冷水进管和冷水出管的供给量由电磁阀通过温度探头控制,使冷凝分离器中的槽液温度维持在7±2℃。
用不同分离方法从废液中去除铜

用不同分离方法从废液中去除铜
张丽霞
【期刊名称】《湿法冶金》
【年(卷),期】2004(023)003
【总页数】1页(P143)
【作者】张丽霞
【作者单位】无
【正文语种】中文
【中图分类】TD923
【相关文献】
1.让学生真正投入到科学探究中去--《分离盐与水的方法》教学实录和反思 [J], 俞国兴
2.用三烷基氧膦(TRPO)从强放废液中去除铜系元素:TRPO对mei和某些镧... [J], 宋崇立
3.二甲基乙酰胺废液的分离方法 [J], 董冰;张宝龙
4.从含四氯化钛有机废液中分离有机物的方法研究 [J], 段庆春;姚红;刘汉新
5.从钼精矿中去除铜的新方法 [J], 李有观
因版权原因,仅展示原文概要,查看原文内容请购买。
基于控制周期计算的锌液净化除铜过程优化控制

基于控制周期计算的锌液净化除铜过程优化控制张凤雪;阳春华;周晓君;桂卫华【摘要】The copper removal process is the first step in zinc solution purification of direct leaching of zinc hydromet-allurgy, and its result has a significant impact on the follow-up process and the quality of the final product. In the copper removal process, the undetermined control period and addition amount of zinc-powder always lead to the fluctuation of outlet copper concentration and the waste of zinc powder. In order to solve this problem, an optimal control strategy based on control period calculation for copper removal process is proposed. First, the sequential relationship between oxidation-reduction-potential (ORP) and zinc powder is analyzed to calculate the response time of copper removal process, and then the control period is obtained by analyzing the statistical characteristic of response time. Next, the optimal control problem is transformed into a nonlinear mathematical programming problem by the fixed-node control parameterization method. Furthermore, the state transition algorithm is applied to solve the nonlinear mathematical programming problem. And the simulation results demonstrate the effectiveness of the proposed control strategy.%净化除铜过程是锌直接浸出冶炼工艺中硫酸锌溶液净化的第1个步骤,其效果直接影响着后续工序的正常进行以及最终锌产品的质量.本文针对除铜过程中控制周期与锌粉添加量不确定性,造成出口铜离子浓度波动大及锌粉浪费等问题,研究基于控制周期的除铜过程锌粉添加优化控制方法.首先通过分析反应器中氧化还原电位(oxidation-reduction-potential,ORP)与锌粉的时序变化关系计算除铜过程反应响应时间,然后分析响应时间的统计特性,从而确定锌粉控制周期.在确定控制周期的基础上,采用基于控制周期的固定节点控制参数化方法,从而将最优控制求解问题转化为非线性规划问题.最后,采用状态转移算法对该非线性规划问题进行求解.采集工业现场数据进行实验证明了该优化控制方法的有效性,为类似的净化过程的优化控制提供了新思路.【期刊名称】《控制理论与应用》【年(卷),期】2017(034)010【总页数】8页(P1388-1395)【关键词】除铜过程;优化控制;控制周期;控制参数化;状态转移算法【作者】张凤雪;阳春华;周晓君;桂卫华【作者单位】中南大学信息科学与工程学院,湖南长沙410083;中南大学信息科学与工程学院,湖南长沙410083;中南大学信息科学与工程学院,湖南长沙410083;中南大学信息科学与工程学院,湖南长沙410083【正文语种】中文【中图分类】TP2731 引言(Introduction)锌直接浸出冶炼工艺由磨矿、直接浸出、净化、电积、熔铸5部分构成[1].净化过程通过添加锌粉除去浸出后的硫酸锌溶液中有害的杂质离子,为电积过程提供合格的新液.锌粉添加量决定了除铜生产稳定性与产品质量,锌粉添加量过多,出口铜离子浓度过低,后续除杂活化剂不足;锌粉添加量过低,出口铜离子浓度过高,易降低电积效率.实际生产中,矿源变化与工况波动,以及除铜反应机理的复杂性,造成操作员难以及时准确控制锌粉添加量.由于锌粉控制周期和锌粉添加量往往由人工经验决定,使得出口铜离子波动较大,产品质量难以稳定.因此在工业生产过程中采用优化控制思想:在工业过程处在最佳工况环境下,优化调整过程控制量,使生产条件达到最优的状态,以满足生产要求.针对复杂工业生产过程的反应影响因素、反应过程建模、优化控制等问题国内外研究人员进行了大量的研究[2–10].Sun等[11]针对湿法炼锌除钴镍过程建立了一种基于氧化还原电位的钴离子浓度预测模型,并将数据驱动补偿法与该动态模型相结合以解决精确度问题.Xie等[12]将沉铁过程的机理模型与误差补偿模型相结合,建立了一种基于参数辨识的亚铁离子浓度预测的动态模型,并采用在线更新策略来预测硫酸锌溶液中亚铁离子浓度.Ma等[13]针对铝土矿连续磨矿过程球磨机节能降耗问题以及铝土矿来源复杂、品位差异大等特点,建立了状态空间浓度预测模型和粒级质量平衡加权多模型细度预测模型,提出了球磨机多目标多模型预测控制方法.Chai等[14]提出了一种针对复杂工业过程优化运行的混合智能控制方法,该方法由控制回路与设定模型、前馈补偿与反馈补偿器、工艺指标预报模型、故障工况诊断和容错控制器组成.Yang等[15]针对铝冶炼工业过程提出了一种基于综合模型和分层理论的优化设定模型,采用机理知识分析和智能技术提高了生料浆的品质.针对湿法炼锌净化除铜过程,Laatikainen等[16]研究了温度对湿法炼锌净化除铜过程反应进行的影响,并通过大量的实验分析得到了除铜过程最适宜的反应温度.Zhang等[17]详细研究了除铜过程两个主反应的反应动力学模型,得到了基于竞争反应关系的动力学模型,并进行了动态模型的参数辨识.而现阶段针对除铜过程的优化控制方法的研究还比较少,但一些控制方法在其它类似的工业过程中已有应用,Li等[18]针对湿法炼锌净化过程,建立了交互CSTR模型,并采用控制参数化方法进行模型的优化求解.Loxton等[19]提出了一种基于改进控制参数化的计算方法来解决控制信号不断变化的优化问题,并将此计算方法成功应用到了捕鱼技术、列车控制以及化学工程中.现本文将控制参数化方法引入到除铜过程中,从而进行锌粉的优化控制.在采用优化控制思想解决复杂工业的问题中,控制周期的设置尤为重要,直接影响了整体的控制效果.控制周期时间过短时,不利于观察控制效果;频繁的调节易造成过程扰动,不利于长流程生产稳定;同时控制周期过短,会使锌粉来不及完全反应造成浪费.控制时间周期过长,难以及时满足反应器内铜离子浓度变化所需锌粉添加量,出口铜离子浓度极易超标,不利于除铜过程稳定运行.因此,本文的新颖性体现在以下3个方面:首先在湿法炼锌净化除铜过程的一些已经完成的研究基础上,建立除铜过程的优化控制模型,将其转换成锌粉添加量的优化问题;然后提出了基于控制周期的固定节点控制参数化方法,该方法不同于常规控制参数化方法的随意确定控制周期,而是先对实际生产数据进行了大量的统计学分析,然后计算锌粉添加的控制周期,使得控制周期的确定不再具有盲目性;最后本文采用新型的全局最优状态转移算法[20]在满足出口铜离子浓度达标的基础上求解最优的锌粉添加量,既节约了锌粉的添加量又稳定了出口铜离子浓度.2 除铜过程机理模型(Mechanism model of copper removal process)2.1 除铜过程工艺(Copper removal process)锌直接冶炼的浸出过程中存在未能除去的杂质离子如铜、镉、钴、镍及少量砷、锑、锗等,这些杂质对电积过程有很大的危害.因此必须在电积过程之前通过净化过程将其降低到足够低的范围内.净化过程一般采用3段净化方案,其基本流程如图1所示. 图1 净化过程示意图Fig.1 The technical process of puri cation净化过程首先进行的是除铜过程,这是因为铜离子是所有杂质中含量最高的,而且在溶液中铜离子标准电势较大,会首先和锌粉进行反应[21].除铜过程的详细工艺流程如图2所示,浸出后的硫酸锌溶液流入两个串联的反应器,通过在反应釜中持续添加锌粉,使得溶液中的铜离子形成以单质铜和氧化亚铜为主的沉淀分离除去.除铜后液经过浓密机固液分离后,液体部分将溢流至除钴镍工段,产生的铜渣进行回收利用,还有小部分含固底流将作为晶种重新加入到第1个反应器,从而促进氧化亚铜的形成,达到节约锌粉的目的.除铜过程最终要完成的目标是将出口铜离子稳定在200~400 mg/L的范围内.这主要是因为在后续的除钴镍过程中,需要少量铜离子作为活化剂,实验证明200~400 mg/L的范围有利于加快除钴镍过程进行的速度;然后,在此基础上尽量减小铜离子浓度的波动也是十分必要的,只有保证稳定才能更好的调控后续除钴镍工段砷盐和锌粉的添加量.图2 除铜流程示意图Fig.2 The technical process of copper removal2.2 除铜过程动态模型(Kinetic model of copper removal process)除铜过程发生的主要化学反应如式(1)–(2)所示:反应器中铜离子浓度的变化主要受上述两个化学反应的影响,在实际工业中,每一个反应器都可以被视作一个CSTR系统,且两个反应器中铜离子变化规律可用以下动态方程来表示[18]:其中:分别是第i个反应器中铜离子浓度变化速率;分别是第i个反应器中入口的铜离子浓度;CCu2+,i分别是第i个反应器中铜离子浓度;V是反应器的体积;Q和q分别为入口溶液的流量和返回底流溶液的流量;rCu2+,i分别为第i个反应器内铜离子的反应速率(i=1,2).根据冶金过程化学反应动力学和除铜过程的竞争反应,该反应的反应速率为[16]其中:k1,k2,k3为待辨识参数;CCu2+,i分别是第i个反应器中铜离子浓度;GZn,i为第i个反应器中所需锌粉的重量.由于从第1个反应器流出口的铜离子浓度应为第2个反应器入口的铜离子浓度,则将式(4)–(5)代入式(3)中,则两个反应器的动态模型可以转换为由上述分析可知,除铜过程的控制量为锌粉添加量,设状态变量为x=[CCu2+,1,CCu2+,2],初始状态变量为控制量u=[GZn,1,GZn,2],则可得除铜过程的状态模型为3 控制周期的计算(The calculation of control period)在湿法炼锌净化除铜过程中,对锌粉的添加量进行优化时,控制周期的设置尤为重要且直接影响了整体的控制效果.控制周期时间过短时,不利于观察控制效果;频繁的调节易造成过程扰动,不利于长流程生产稳定;同时控制周期过短,会使锌粉来不及完全反应造成浪费.控制时间周期过长,难以及时满足反应器内铜离子浓度变化所需锌粉添加量,出口铜离子浓度极易超标,不利于除铜过程稳定运行.因此,控制周期的设置需满足能够在溶液内铜离子浓度达标时进行及时调节.在工业运行中,ORP值与溶液中的铜离子浓度有着一一对应的关系,ORP值的变化可以反应溶液中铜离子浓度的变化.在稳定的入口离子浓度下,某一时间添加锌粉后,经过一段时间反应器中的铜离子浓度会达到极小值,同样ORP值的变化曲线也会出现极小值,则这一段时间间隔称为响应时间T.图3为反应器中锌粉和ORP的变化曲线以及响应时间的示意图,采用统计学方法多组反应过程响应时间进行分布统计,获得响应时间的样本分布,进而确定控制周期. 基于统计学方法的控制周期计算步骤如下:步骤1 基于工业运行现场采集的数据,建立反应釜中ORP及锌粉含量随时间变化的曲线,确定锌粉含量的极大值与ORP的极小值的对应关系,即两条曲线中波峰和波谷之间的对应关系.步骤2 基于上述获得的曲线,采用式(8)计算从锌粉添加到反应完全的时间(即响应时间T):其中:Tt(Zn)是反应釜中锌粉含量变化曲线的波峰值对应的时间,Tc(ORP)是ORP变化曲线上后出现的第一个波谷值对应的时间.步骤3 对获得的多组响应时间数据进行概率纸检验,从而判断数据分布的正态性. 步骤4 若数据服从正态分布,则建立数据的正态分布曲线;若数据不服从正态分布,则先采用数据转换的方法将数据正态化,然后再建立正态分布曲线.步骤5 根据正态分布曲线得到各响应时间样本的分布律,然后计算置信水平为α的响应时间置信区间[Ta,Tb].步骤6 计算分布于置信区间[Ta,Tb]内的响应时间均值,以此均值作为锌粉添加的控制周期T∗.图3 锌粉与ORP变化曲线Fig.3 The changing curves of Zn and ORP4 除铜过程锌粉添加优化控制(Optimal control of copper removal process) 4.1 除铜过程锌粉添加优化控制模型(Optimal control model of copper removal process)1)除铜过程优化控制目标函数.湿法炼锌净化除铜过程不仅要保证反应器出口的铜离子质量浓度在200~400 mg/L之间,而且还要合理的控制锌粉的添加量.如果锌粉添加量太低,则会使得反应器出口铜离子浓度超标,影响整个流程的净化效果;如果锌粉添加量太高,则会造成后续工段所需的铜离子浓度不足,且造成了锌粉的浪费.综合考虑,在反应过程中尽量使得反应器出口铜离子浓度达标的情况下锌粉的添加量最小.结合式(7),除铜过程锌粉添加优化控制的目标函数为其中:tf为硫酸锌溶液在反应器中的平均停留时间;J为锌粉添加优化控制目标函数. 值得注意的是,实际除铜工业运行中,tf的值一般通过tf=V/Q计算获得.此外本文的锌粉添加优化控制模型以离子浓度某一化验时刻作为起始时间0,计算时间跨度tf 内反应器中最优锌粉添加量,再以下一化验时刻为起始时间0,求解下一个时间跨度内的最优锌粉添加量,如此反复实现长流程的优化控制.2)除铜过程状态方程.除铜过程的动力学模型描述的是反应过程中铜离子的变化规律,其状态方程可由式(7)得其中:3)终端条件约束.除铜过程实际工业运行要求2号反应器出口的铜离子浓度在200~400 mg/L之间.设该范围为[CCu2+,min,CCu2+,max],则终端约束条件为因此,除铜过程锌粉添加优化控制是:寻找最优的控制量u∗(t),使得目标函数J最小,且满足终端约束条件.该最优控制问题可描述为问题1 求解式(12)所描述的锌粉添加优化控制模型的最优锌粉添加量.4.2 基于控制周期的控制参数化方法(Control parameterization method based on control period)除铜过程的控制问题具有很强的非线性并带有连续状态不等式约束,控制量与状态量之间存在很强的耦合,传统方法难以实现求解,控制参数化方法的思想正是为解决这一问题而提出[21–22].控制参数化方法利用非线性问题分段化的思想将时间区间[0,tf]划分为一系列连续的子区间,控制量根据区间划分来分段,并且用适当的样条函数逼近,从而将相应的优化问题转换为求解一系列最优控制参数的非线性规划.而子区间的划分直接关系到这种方法对控制量的近似程度,因此本文基于第3章的控制周期的计算,提出了一种基于控制周期的控制参数化方法,使得划分的每一个子区间长度等于控制周期T∗,进而将问题1转换为易于求解的非线性规划问题.为采用控制参数化方法将最优控制问题转换为近似问题,把优化模型求解时间区间[0,tf]分成N个子区间[tn−1,tn](n=1,2,...,N),如下所示其中T∗=tn−tn−1,即由于优化计算模型的控制量为2维向量,定义一系列常数向量κn ∈ R2,n=1,2,...,N,则其中:为第n段时间内第1个反应器中锌粉添加量;为第n段时间内第2个反应器中锌粉添加量.将问题1的控制量设计为与常数向量κn有关的分段常函数,则其中:tn(n=0,1,...,N −1)是控制量的切换时间点;函数θ[tn−1,tn)(t)定义如下:当t=tf时,控制量为将分段常函数控制量式(15)代入系统动态方程,有优化计算模型(27)的终端不等式约束变为则最优控制问题1转换成了易于求解的非线性规划问题2:问题2 优化选择参数向量κn,使得如下目标函数值最小且满足约束条件(19)问题2是非线性规划问题,可以用许多优化算法进行求解.本文采用的是近年来刚提出的一种全局优化算法––状态转移算法(state transition algorithm,STA)[20]进行求解,且其在求解实际工程优化问题上的有效性和优越性已被大量证实[23–32]. 4.3 状态转移算法(State transition algorithm)状态转移算法借鉴状态及状态转移的概念,将待优化问题的解理解为状态,优化算法的思想理解为状态转移,求解待优化问题的过程便是一个状态转移过程.该状态转移过程具有如下形式:其中:xk∈Rn表示一个状态,对应待优化问题的一个解;Ak,Bk为状态转移矩阵,可理解为优化算法的算子;uk为状态xk及历史状态的函数;f为目标函数.状态转移算法的算子主要包括以下4个核心操作算子:1)旋转变换算子其中α为旋转因子;Rr∈Rn×n是一个随机矩阵,且元素的取值在[−1,1]范围内;‖ .‖2为向量的2范数.2)平移变换算子其中β为平移因子;Rt∈R为一随机变量,取值在[0,1]范围内.3)伸缩变换算子其中γ为伸缩因子;Re∈Rn×n为一元素服从高斯分布的随机对角矩阵.4)坐标变换算子其中δ为坐标因子;Ra∈Rn×n为一元素服从高斯分布且仅有一个随机位置为非零值的随机对角矩阵.采用状态转移算法求解优化问题的步骤为步骤1 随机产生一个初始解Bestk=Best,设置算法参数α=αmax=1,αmin=1e−4,β=1,γ=1,δ=1,fc=2,k=0[20];步骤2 基于当前最好解Bestk,利用伸缩变换操作产生SE个样本,并利用更新策略更新当前最好解,如果当前最好解有变动,执行平移变换操作并以同样的机制更新当前最好解Bestk;步骤3 基于当前最好解Bestk,利用旋转变换操作产生SE个样本,并利用更新策略更新当前最好解,如果当前最好解有变动,执行平移变换操作并以同样的机制更新当前最好解Bestk;步骤4 基于当前最好解Bestk,利用坐标搜索操作产生SE个样本,并利用更新策略更新当前最好解,如果当前最好解有变动,执行平移变换操作并以同样的机制更新当前最好解Bestk;步骤5 置k=k+1,若α<αmin,置α=αmax,否则置然后重返步骤2直到终止条件满足.5 数值仿真及结果分析(The analysis of simulation results)以某湿法炼锌企业除铜过程2个反应器为实验仿真对象,流程生产数据采集于2014年.首先从工业现场采集的数据中选取700组ORP和锌粉数据,根据第3章提出的控制周期计算步骤确定控制周期.从图4可以看出,计算得到的响应时间数据分布在一条直线上,通过概率纸检验,确定所选取的数据服从正态分布.该数据的正态分布曲线和直方图如图5所示.其均值和置信区间等结果的统计如表1所示,根据表中统计结果可知计算得到的控制周期为18.12 min,即每调整1次控制量要求持续18.12分钟.表1 数据统计结果Table 1 Result of data statistics置信水平/% 置信区间/min 均值/min 控制周期/min 95 [17.71,18.53] 18.12 18.12由于除铜过程现场实行的是8小时倒班工作制,所以采用本文所提的优化控制方法对2014年某天的一班8小时进行数值仿真实验.图4 数据的正态概率纸检验Fig.4 Normal probability plot of data图5 数据的正态分布曲线和直方图Fig.5 The normal distribution curve and histogram of data由于状态转移算法具有随机性,所以本文采用随机生成的初始值进行了100次问题求解,并采用了遗传算法(genetic algorithm,GA)和粒子群优化算法(particle swarm optimization,PSO)与状态转移算法进行了对比,3种算法的最大迭代次数和种群大小是相同的,分别为20和30.另外,在粒子群算法中,c1=c2=1,w从0.9至0.4进行线性递减.对于遗传算法,本文调用的MATLAB遗传算法工具箱v1.2进行问题的求解.最后采用显著性水平为0.05的秩和检验方法对两种对比算法的结果分别与状态转移算法的结果进行显著性分析.其统计结果如表2所示.表2 3种算法求解结果统计Table 2 Comparison of three different algorithmMean Value±Std Dev Rate/%状态转移算法(STA) 8.35E-5±1.68E-5 97遗传算法(GA) 6.97E-4±1.00E-4(−) 91粒子群优化算法(PSO) 9.41E-4±7.90E-5(−) 94表2中采用了2种性能指标比较3种优化算法,其中Mean Value±Std Dev表示所求解的目标函数J1样本的平均值与标准偏差,(−)表示采用秩和检验进行显著性分析后两种对比算法的结果样本与状态转移算法的结果样本服从不同分布,这种性能指标可以用来评价3种算法的求解精度;Rate表示100次运行中求得的目标函数值小于10−3所占的比例,可以用来评价3种算法求解问题的成功率.从中可以看出状态转移算法的求解精度和成功率都要优于遗传算法和粒子群优化算法.选取状态转移算法求解的结果与人工经验操作进行对比,其仿真实验结果如图6–8所示.图6和图7分别表示2个除铜反应器优化控制计算所得的锌粉添加量和人工经验操作的锌粉添加量对比结果.图8为优化控制和人工经验操作相应的2#反应器出口的铜离子浓度.表3统计了仿真时间8小时内优化控制和人工经验操作的锌粉总添加量以及相应的2#反应器出口铜离子浓度的标准差.图6 1#反应器锌粉添加量对比Fig.6 Comparison of zinc addition between optimal control and arti cial manipulation in 1#reactor图7 2#反应器锌粉添加加量对比Fig.7 Comparison of zinc addition between optimal control and arti cial manipulation in 2#reactor图8 2#反应器出口铜离子浓度对比Fig.8 Comparison of outlet copper ion between optimal control and arti cial manipulation in 2#reactor由图6–8和表3可知,实际除铜工业过程中工作人员往往凭经验添加过量的锌粉,从而确保2#反应器出口的铜离子浓度在工艺要求的范围之内,从而造成了锌粉浪费,增加了生产成本.而且,由于人工经验操作的不及时和盲目性,使得2#反应器出口的铜离子浓度波动大,不利于后续流程的稳定生产.而本文所提出的优化控制方法所计算的锌粉添加量要低于人工操作使用的锌粉,同时减小了2#反应器出口的铜离子浓度的波动性.表3 优化控制和人工操作统计结果对比Table 3 Statistical comparison results of optimal control and arti cial manipulation优化控制人工操作1#反应器锌粉添加量/kg 1002 1176 2#反应器锌粉添加量/kg 274 398 2#反应器出口Cu2+浓度标准差 0.02 0.136 结论(Conclusions)锌湿法冶炼除铜过程反应机理复杂、矿源多变、锌粉添加的控制周期不确定性及控制量准确度低,使得出口铜离子浓度波动大,产品质量不稳定.针对该问题,本文提出了基于控制周期计算的除铜过程优化控制方法.该方法分析了反应器中ORP与锌粉的时序关系,采用统计学方法确定最优控制周期.在控制周期确定的基础上,根据除铜过程竞争反应动态模型,采用基于控制周期的固定节点控制参数化方法将无穷维动态优化问题转化为有穷维的非线性规划问题,并采用状态转移算法求解锌粉的优化添加量.仿真结果表明,论文提出的优化控制方法能够有效降低除铜过程的锌粉添加量,与人工经验添加相比一工作班可节约近298 kg锌粉.除此之外,出口铜离子浓度的标准差结果表明该方法还可以减小反应器出口的铜离子浓度波动情况,为实际生产过程提供了相应的操作指导.参考文献(References):【相关文献】[1]SUN Dekun.The progress of the zinc smelting technology at home and abroad[J].China Nonferrous Metallurgy,2004,6(3):1–5.(孙德堃.国内外锌冶炼技术的新进展[J].中国有色冶金,2004,6(3):1–5.)[2]FILIPPOU D.Innovative hydrometallurgical processes for the primaryprocessingofzinc[J].MineralProcessing&ExtractiveMetallurgyReview,2004,25(3):205–252.[3]AHMED I M,EL Y A.Cementation of copper from spent copperpickle sulfate solution by zinc ash[J].Hydrometallurgy,2011,110(1/2/3/4):62–66.[4]YAHIAOUII.Experimentaldesignforcoppercementationprocessin xed bed reactor using two-level factorial design[J].Arabian Journal of Chemistry,2010,3(3):187–190.[5]JIN Yanghua,WU Shixue.The dynamics of copper replacement on the surface of iron powder[J].Materials Review,2007,21(S1):226–229.(金洋华,吴世学.铁粉表面置换镀铜的动力学[J].材料导报,2007,21(S1):226–229.)[6]GUI Weihua,YANG Chunhua,LI Yonggang,et al.Data-driven operational-patternoptimizationforcopperぼashsmeltingprocess[J].Acta AutomaticaSinica,2009,35(6):717–724.(桂卫华,阳春华,李勇刚,等.基于数据驱动的铜闪速熔炼过程操作模式优化及应用[J].自动化学报,2009,35(6):717–724.)[7]YE J X,XU H L,FENG E M,et al.Optimization of a fed-batch bioreactor for 1,3-propanediol production using hybrid nonlinear optimal control[J].Journal of Process Control,2014,24(10):1556–1569.[8]SUN B,GUI W H,WANG Y L,et al.Intelligent optimal setting control of a cobalt removal process[J].Journal of Process Control,2014,24(5):586–599.[9]CHAI T Y,DING J L,WU F H.Hybrid intelligent control for optimal operation of shaft furnace roasting process[J].Control Engineering Practice,2011,19(3):264–275.[10]ZHOU Xiaojun,YANG Chunhua,GUI Weihua.Modeling and control of nonferrous metallurgical processes on the perspective of global optimization[J].ControlTheory&Applications,2015,32(9):1158–1169.(周晓君,阳春华,桂卫华.全局优化视角下的有色冶金过程建模与控制[J].控制理论与应用,2015,32(9):1158–1169.)[11]SUN B,GUI W H,WU T B.An integrated prediction model of cobalt ion concentration based on oxidation-reduction potential[J].Hydrometallurgy,2013,140(11):102–110. [12]XIE Y F,XIE S W,CHEN X F,et al,An integrated predictive model with an online updating strategy for iron precipitation in zinc hydrometallurgy[J].Hydrometallurgy,2015,151(1):62–72.[13]MA Tianyu,GUI Weihua.Optimal control for continuous bauxite grinding process in ball-mill[J].Control Theory&Applications,2012,29(10):1339–1347.(马天雨,桂卫华.铝土矿连续磨矿过程球磨机优化控制[J].控制理论与应用,2012,29(10):1339–1347.)[14]CHAI Tianyou,DING Jinliang,WANG Hong,et al.Hybrid intelligent optimal control method for operation of complex industrial processes[J].Acta AutomaticaSinica,2008,34(5):505–515.(柴天佑,丁进良,王宏,等.复杂工业过程运行的混合智能优化控制方法[J].自动化学报,2008,34(5):505–515.)[15]YANG C H,GUI W H,KONG L S,et al.Modeling and optimalsetting control of blending process in a metallurgical industry[J].Computers&Chemical Engineering,2009,33(7):1289–1297.[16]LAATIKAINEN K,LAHTINEN M,LAATIKAINEN M.Copper removal by chelating adsorption in solution puri cation of hydrometallurgical zincproduction[J].Hydrometallurgy,2010,104(1):14–19.[17]ZHANG B,YANG C H,ZHU H Q.Kinetic modeling and parameter estimation for。
沉铜常见问题及对策

1.检查钻孔条件,钻头质量和研磨质量。
2.加强去毛刺高压水洗。
各槽清洗不足,有污染物积聚,在孔里或表面残留
定期进行槽清洁保养。
水洗不充分,使各槽位的药水相互污染
检查水洗能力,水量/水洗时间。
加速处理液失调或失效
调整或更换工作液。
电镀后孔壁无铜
化学镀铜太薄被氧化
增加化学镀铜厚度。
电镀前微蚀处理过度
活化剂性能恶化,在铜箔表面发生置换反应
检查活化处理工艺浓度/温度/宋体; mso-hansi-font-family: 'Times New Roman'; mso-ascii-font-family: 'Times New Roman'">时间以副产物含量。必要时应更换槽液。
活化处理过度,铜表面吸附过剩的Pd/Sn,在其后不能被除去
加设摇摆、震动等。
化学镀铜液的活性差
检查NaOH、HCHO、Cu2+的浓度以及溶液温度等。
反应过程中产生气体无法及时逸出
加强移动、振动和空气搅拌等。以及降低温度表面张力。
化学镀铜层分层或起泡
层压板在层压时铜箔表面粘附树脂层
加强环境管理和规范叠层操作。
来自钻孔时主轴的油,用常规除油清洁剂无法除去
定期进行主轴保养。
活化液浓度偏低影响pd吸附检查活化处理工艺补充活化剂加速处理过度在去除sn的同时pd也被除掉检查加速处理工艺条件温度us时间浓度如降低加速剂浓度或浸板时间水洗不充分使各槽位的药水相互污染检查水洗能力水量水洗时间
【沉铜常见问题及对策】
故障现象
可能原因
措施对策
化学镀铜存在空洞
钻孔粉尘孔化后脱落
1.检查吸尘器,调整钻头的钻孔参数。
线路板厂含铜废水处理化学沉淀法

线路板厂含铜废水处理化学沉淀法近年来,我国电子技术的发展,使印刷线路板成为一种被广泛应用的电子产品,由于电子产品的更新换代速度不断加快,这也使传统的线路板被逐渐淘汰。
与此同时,由于在制造印刷线路板时会产生大量的含铜废水,这些含铜废水如果不加以处理就进行直接排放,势必会给自然环境造成严重污染,甚至还会危害到人体健康。
一直以来,人们在回收线路板的含铜废液时,需要通过中和、出料及废水,采用离子交换方法来对废水进行处理,然后进行再蒸发和再渗透,以此进行再离子交换,通过对处理后的废水进行铜离子含量检测,合格后方可排放,但在处理后的废水中却含有较高的氨氮。
为了解决该问题,本文采用化学沉淀法来对线路板厂的含铜废水进行处理,并借助于正交实验来对最佳的工艺条件进行确定,以期能够为线路板厂在改进废水处理工艺中提供参考和借鉴。
1、实验部分1.1实验原理在应用化学沉淀法来对线路板厂的含铜废水进行处理时,首先需要确定化学沉淀法中的沉淀剂成分,本文将硫化钠与硫酸亚铁作为沉淀剂中的主要成分。
化学沉淀法的去铜原理主要是利用硫酸亚铁法来实现,也就是在暴气条件下对pH为2~3的硫酸亚铁内的二价铁离子进行氧化,使其成为三价铁离子,然后将三价铁离子投加至含铜废水中,使三价铁离子能够与EDTA进行结合,从而实现对Cu2+的置换,从而使含铜废水中的铜离子从原有的络合态向着游离态进行转变,然后提高含铜废水的pH值,由此便可使Fe(OH)3、Fe(OH)2与Cu(OH)2得以沉淀,进而有效去除了废水中的铜离子和铁离子,此外,因Fe(OH)3在沉淀过程中发挥混凝作用,这能够提高含铜废液的沉淀速度,进而提高含铜废水的处理效率。
通过对硫化钠中的Cu2+与S2-在碱性环境中进行操作,可使废液中产生大量的CuS沉淀,然后将絮凝剂与混凝剂加入到含铜废水中,可确保细小CuS的快速沉淀,进而实现对含铜废水中铜离子的有效去除。
1.2实验方法为了对含铜废水的水质进行分析,本文通过二乙基二硫代氨基甲酸钠来对处理前与处理后的含铜废水的铜离子含量进行分别测定,测定方法采用分光光度法,测定结果表明,处理前的含铜废水中所含的铜离子含量高达15.7mg/L,而通过化学沉淀法的应用,处理后的含铜废水中,其铜离子含量的浓度只有1mg/L。
一种铜电解液沉淀脱杂及沉淀剂氯化再生的方法与流程

一种铜电解液沉淀脱杂及沉淀剂氯化再生的方法与流程铜电解液在铜电解过程中,容易受到杂质的干扰,影响铜的纯度和生产效率。
铜电解液需要进行脱杂处理,以提高铜的纯度和防止生产过程中的故障和损失。
本文将介绍一种铜电解液沉淀脱杂及沉淀剂氯化再生的方法与流程。
一、铜电解液沉淀脱杂的方法及流程:1.准备工作:准备好沉淀剂、搅拌设备、升温设备、滤液设备等工具和设备,并对设备进行消毒和清洁。
2.调整pH值:将铜电解液调整至适当的pH值,一般在3-5之间较为合适。
可以使用氢氧化钠、硫酸等化学试剂对铜电解液进行调节。
3.加入沉淀剂:将沉淀剂逐渐加入铜电解液中,并边加入边搅拌,直到沉淀剂完全溶解。
这个过程通常需要30分钟以上。
常用的沉淀剂有氢氧化钠、氧化铁等。
4.沉淀:在调整好pH值和加入沉淀剂后,放置电解液静置。
沉淀剂会汇集并沉淀下来,将杂质一同排除。
5.过滤:将沉淀后的电解液使用滤纸进行过滤,去除掉沉淀物。
6.处理滤渣:将滤渣进行处理,以防止再次对铜电解产生影响和污染。
可以使用化学方法或物理方法对滤渣进行处理。
二、氯化再生沉淀剂的方法及流程:1.准备工作:准备好氯化剂、搅拌设备和加热设备等工具和设备,并对设备进行消毒和清洁。
2.溶解沉淀物:将沉淀物与适量氢氧化钠混合,加热至65°C左右,搅拌使其充分溶解。
然后加入适量的氯化钠溶液,继续搅拌,使溶液保持在约70°C下10分钟以上。
3.沉淀:停止加热和搅拌,使溶液自然降温,沉淀物逐渐沉淀到底部。
4.分离:将沉淀物与液体分离,将离心分离或者使用过滤纸进行过滤。
5.处理氯化废液:将氯化废液进行处理,以回收有用元素和避免对环境的污染。
可以采取环保化学方法或物理方法进行处理。
综合以上,铜电解液沉淀脱杂及沉淀剂氯化再生的方法及流程大约需要4-5个小时左右,主要取决于电解液的含杂质程度和杂质类型。
在整个过程中,需要仔细控制温度、pH值和加工时间,以确保产品的纯度和品质。
提高铜回收率的措施

锌浸出厂锌I系统提高铜回收率初步方案一、锌I系统矿粉系统提高铜回收率措施。
1、将浸出中性浓密槽出口PH降低0.5即由现在5.2-5.4降到4.7-5.0,并逐步降到4.5-5.0,减少铜在中性浸出过程的沉淀。
需要在5#中性浸出过程增加一套PH检测(带自动清洗,并在浸出楼及浓缩槽两地显示)。
2、预除铜是利用原来的洗水槽临时做试验用,由于是普通材质,由于铜离子腐蚀,无法正常运行,故障率很高,不能满足生产要求,要求重新做一个耐腐蚀的槽体,材质采用不锈钢(316L)。
3、由于铜镉渣浓密机能力偏小,锌I系统产能不断扩大,导致溢流约一半未经压滤直接返系统,不仅铜镉渣的铜被损失,而且铜镉渣的锌使溶液中的铜被置换造成第二次损失,造成铜在浸出渣中大量损失。
第一步:在铜镉渣浓密机旁增加一个贮槽(利用原双氧水贮槽)和一台泵(要求在溢流压滤贮槽及新增贮槽增加液位计),将压不完的溢流,进一次管式过滤器残液罐,增浓返回。
(进维修实施)每二步:在原铜镉渣压滤厂房内增加一台150m3的压滤机(必须更换上下楼梯及吊车),溢流全部经压滤再返系统。
渣浆化后泵入浸出槽(要求增加浆化槽、泵和液位计)。
4、2#、3#沸腾槽上部已经腐蚀多处穿孔,无法维持正常生产,存在严重安全隐患,必须紧急安排逐台计划部分更换原为普通钢改为不锈钢。
(进维修实施)5、沸腾槽下清理的铜镉渣现送挥发窑,造成铜在窑渣中损失。
必须制作6个渣盆,定期将沸腾槽下清理的铜镉渣转运镉II集中处理。
(进维修实施)6、净液工段一次净化机械搅拌槽锌粉加入将绞笼改为计量皮带,需要增加一台电葫芦和三台计量皮带。
二、锌I系统氧化锌系统提高铜回收率措施。
由于4#、5#挥发窑处理直浸铁渣,大量的铁渣在挥发窑干燥段以粉尘的形态被风机抽入氧化锌中,造成氧化锌中铁和铜含量成倍增加,并造成富集渣量大,品位低。
为降低富集渣量,提高品位。
通过试验:将部分高酸上清返回氧化锌中性浸出,分离部分铁和铜,已取得很好的效果。
- 1、下载文档前请自行甄别文档内容的完整性,平台不提供额外的编辑、内容补充、找答案等附加服务。
- 2、"仅部分预览"的文档,不可在线预览部分如存在完整性等问题,可反馈申请退款(可完整预览的文档不适用该条件!)。
- 3、如文档侵犯您的权益,请联系客服反馈,我们会尽快为您处理(人工客服工作时间:9:00-18:30)。
垂直化学沉锡线槽液除铜过滤方法的改进
摘要:阐述了一种化学沉锡线的沉锡槽液除铜工艺方法,对传统的过滤工艺进行改进,包括以下工艺步骤:吸取槽液→冷凝分离→压滤装置挤压过滤→槽液回用→废渣排出,本方法采用压轮挤压式过滤的方式,可最大限度的回收利用沉锡槽液,过滤效率从20%提高到70%,极大的节省了制造成本;本方法采用的压轮挤压过滤装置设计结构简单,占地面积小,便于操作和维护保养;过滤后的污泥废渣含有极少量的沉锡槽液,降低了废弃物处理的成本。
关键词:沉锡槽液;除铜;压滤装置
1 前言
化学沉锡表面涂覆作为一种安全、稳定的表面处理工艺,广泛应用与印制线路板的制造当中。
化学沉锡线设备一般分为垂直式和水平式生产线两种,但不论哪一种设备,都存在这沉锡槽液的除铜问题:在沉锡槽液对印制线路板进行化学反应的过程中,线路板导电线路上的铜被不断地置换进沉锡槽中形成离子,而金属锡则在导电线路表面不断沉积,形成焊接媒介层;当沉锡槽液中的铜离子含量达到一定程度,槽内的化学反应平衡会遭到破坏,严重时甚至会停止反应,而且过高的铜离子含量会导致沉锡层的稳定性变差,影响产品品质。
因此,化学沉锡线都会在沉锡槽配置沉锡槽液的除铜过滤装置,用于除去沉锡槽液中不断生成的铜离子。
传统的设备一般采用“重力垂流”的过滤方式,依靠槽液的自重进行过滤,不但效率低下,而且槽液过滤不净,浪费严重。
新式设备采用了“板式压
滤”的过滤方式,效率有明显提高,但机械结构复杂,维护保养不便。
2 过滤方法的改进
(1)锡槽中温度为69±2℃的沉锡槽液通过出液泵泵入槽液冷凝分离器,出液泵由电磁阀控制,每次泵出固定体积的沉锡槽液。
(2)泵入冷凝分离器的沉锡槽液使用5±2℃的冷水冷却并进行搅拌,当槽液温度降低达到11℃时,槽液中富集的铜离子就会开始析出,形成絮状凝结物;冷水进管和冷水出管的供给量由电磁阀通过温度探头控制,使冷凝分离器中的槽液温度维持在7±2℃。
(3)打开冷凝分离器底部的计时电磁阀,将冷却后的槽液混合物定量排出,至压轮挤压过滤装置的过滤袋中。
(5)过滤袋中残留的过滤废渣手工倾倒清理。
3 沉锡槽液除铜压滤装置
所述的压滤装置如图2所示,包括箱体、主动压轮、被动压轮、箱体和传动齿条;主动压轮通过主动压轮固定轴固定在箱体的框架上,并能够绕主动压轮固定轴的轴心自由旋转;主动压轮固定轴上还设有主动压轮齿轮;被动压轮通过被动压轮固定轴和支架连接在被动压轮气缸上,被动压轮固定轴设置在框架上的被动压轮滑道内,并能够在被动压轮气缸的推拉作用下沿被动压轮滑道滑动,同时被动压轮能够绕被动压轮固定轴的轴心自由旋转;传动齿条通过设置在箱体上的齿条限位卡槽予以固定,并通过传动齿轮实现与主动压轮齿轮的动力连接;传动齿条上端连接有齿条气缸,并能够在
齿条气缸的推拉作用下沿齿条限位卡槽上下滑动;传动齿条的侧面设置有过滤袋支撑杆,其上设置四个过滤袋固定柱,用于安装并固定过滤袋;过滤袋支撑杆位于主动压轮和被动压轮中间挤压区域的上方,确保固定的过滤袋位于主动压轮和被动压轮中间挤压区域;箱体的底部设置一个排放管路。
主动压轮和被动压轮的表面刻有沟槽。
排放管路还可以用于压轮挤压过滤装置清洗废液的排放。
4 结束语
同现有技术相比,本方法的优点是显而易见的,具体如下:
4.1 本装置设计结构简单,占地面积小,便于操作和维护保养。
4.2 采用挤压式过滤,可最大限度的回收利用沉锡槽液,过滤效率从20%提高到70%,极大的节省了制造成本。
4.3 过滤后的污泥废渣含有极少量的沉锡槽液,降低了废弃物处理的成本。
参考文献
[1]刘彬云.电路板绿色制造技术探讨(1)[j].印制电路信息,2010(6).
[2]李伏.你了解沉锡吗?[j].印制电路信息,2012(4).。