IT CCIE RS K5+2月7号
CCIE RS5.0 红头发讲解

文:CCIE#15101(红头发@微奥)
2012.9.26 夜
PS:有兴趣的朋友可以回帖加以讨论,能提前做好准备当然最好。最近风传日本登陆的K5,加大了IPv6的考察力度,这不得不说是一个信号。
本主题由 红头发 于 前天 08:28 解除置顶
CCIE R&S认证,所用到的实验设备,从早期的CISCO 2500/2600/3600系列,到如今ISR 2800/3800系列路由器,交换机从早期的CAT3550到如今的CAT3560系列。为何不采用CISCO 7200/GSR系列,交换机不采用CAT4500/6500系列?原因:CCIE R&S认证对应的是企业网客户。对于企业网来说,从厂商角度来说,能够说服客户的,从技术环节来讲,肯定是“标准”以及“特性”(Features)这两个角度,这也正是为什么CCIE R&S Lab考试里,对路由(IGP或者BGP)的考察,实际上是很弱化的,特别是BGP,没有什么难度;如果参加了微奥CCIE SP V3的远程培训,你会发现,无论是从课程内容,还是CCIE SP Lab考试,更多关注的是选路策略(routing policy)。这也难怪,一个被服务,需要的是更多新奇的功能与特性;一个是提供服务,需要的是稳定性、可用性以及策略控制流量管制等等。因此,实际上在CCIE R&S V4的考察环节里,更多的,应该是:
所以,CCIE R&S V4的考察重点,不再是路由交换,而应该是上述四大块。不知道有多少人从根本上去思考过这个问题。
二、CCIE R&S V5的课程与考试会有个什么变化?
也许有考生说,看,CCIE#15101又吹牛了,大纲都还没出来,就宣称自己做V5的课程设计了。通常情况下,我不会对一个只具有二元思维的人和他做过多辩解甚至辩论。那么在这里我阐述下我的观点,今后各位可以验证下我又预见了多少。
CORONA 2.4GHz Spread Spectrum (FASST COMPATIBLE) R

CORONA 2.4GHz Spread Spectrum (FASST COMPATIBLE)Receiver Instruction Manual for R4FA‐SB and R6FA‐SB Compatibility:The CORONA 2.4GHz Spread Spectrum FASST Compatible Receiver is designed for use with FUTABA’s FASST 2.4GHz transmitters; including the 3PM,3PKS,3VCS,3GR,4PK(S),TM7, TM8, TM10, TM14 and the T6EX‐2.4G, 7C‐2.4G, 8FG, 10CG, 12FG. The R4FA‐SB and R6FA‐SB receivers supply a more useful mode for users. Both the R4FA‐SB and R6FA‐SB support FUTABA’s FASST air system and surface system. The R4FA‐SB supports 7‐channel with continuous PPM (positive and negative) output ,RSSI output and S.BUS output, R6FA‐SB supports 6 channel high speed PPM(HS) mode to optimize helicopter response control and S.BUS output.Under S.BUS output mode, both R4FA‐SB and R6FA‐SB supply 12 proportional channels and 2 DG channels. Therefore, the R4FA‐SB or R6FA‐SB becomes 14‐channel receivers when using S.BUS output.Specifications:Operating Current: 50mA maxOperating Voltage: 3.6 ~10VLatency: R4FA‐SB’s description14mS for independent 4 channel output and S.BUS output @ FASST multi‐channel mode21mS for Continuous PPM output and RSSI output@ FASST multi‐channel mode16mS for independent 4 channel output and S.BUS output @ FASST 7ch mode24mS for Continuous PPM output and RSSI output@ FASST 7ch mode14mS for independent 3 channel output@ FASST surface system C1 CODE modeR6FA‐SB’s description7mS for independent 6 channel (HS) output@ FASST multi‐channel mode14mS for independent 7 channel (LS) output and S.BUS output @ FASST multi‐channel mode 8ms for independent 6 channel (HS) output@ FASST 7ch mode16mS for independent 7 channel (LS) output and S.BUS output @ FASST 7ch mode14ms for independent 3 channel output@ FASST surface system C1 CODE modeSensitivity: about ‐100dBmOperation temperature:‐10~80 deg CSetup:Bind procedure:∙Turn on the FASST transmitter∙Connect the battery to the receiver while pressing the receiver’s F/S button.∙The Dual‐color LED’s will continuously cycle through the following:o Red LED light (searching radio signal)o Green LED light (acquired the radio signal)o Red LED off (bind ok)o Green LED flashes 10 times (ID stored in memory)o Green LED lights solid (normal operation)Note: FASST surface systems take a bit more time to complete the bind procedure.Fail‐safe setting:There are two ways to set the Failsafe setting on the CORONA 2.4GHz Spread Spectrum FASST Compatible Receiver;1.TX‐failsafe feature: This method sets the failsafe on the FASST transmitter and has priority (works onchannel 3 only under FASST 7ch mode or on multiple‐channels under FASST multi‐channel mode) while the receiver is on, just like FUTABA receivers (only available on FASST air system).2.RX‐failsafe feature: Turn on the FASST transmitter and then turn on the CORONA 2.4GHz Spread SpectrumReceiver, put all the sticks and switches to control inputs you want if the receiver looses signal and Press the F/S button down for about 5 ‐ 6 seconds while the Green LED lights solid (Rx in normal operation), then release the button. You will see the Red LED will flash for about 4 ‐ 5 seconds. (Note: The Red LED will FLASH high speed to indicate the RX‐failsafe is turned on OR FLASH low speed to indicate the RX‐failsafe is turned off). If you press the F/S button a second time while the Red LED is flashing, the receiver will change its RX‐failsafe status (on / off), then the LED will return to Green solid again. If you not press the F/S button, nothing will be changed and the LED will return to solid Green. If you want to cancel the RX‐failsafe feature (not just turn it off), you can do so by binding the receiver again. After binding operation the receiver will be back to factory settings without any failsafe feature.Note: If you do not set a failsafe setting, the receiver will hold all controls at the position of the last command received before signal was lost. When RX‐failsafe is turned on, the receiver will initiate the RX‐failsafe settings after loosing signal for over 1 second and the receiver will hold the last received positions until the failsafe takes over. When the RX‐failsafe and TX‐failsafe feature are both turned on, the receiver will use the TX‐failsafe command.We highly recommend you set failsafe feature before flying your models. An example of a minimal useful, failsafe setting would be to shut down the model’s throttle, so that it does not fly or drive away uncontrolled.Output mode setting (only available on FASST air system):Turn off the transmitter, connect the battery to the receiver, you will see the Red LED light flashing. The RED LED flashes at high speed to indicate the receiver is in the special output mode OR a Low speed indicates the receiver is under (LS) low speed PPM normal output mode, press the F/S button for 5‐6 seconds while the Green LED is off (Rx in signal searching status), then release the button. You will see the Green LED flash for about 4 ‐ 5 seconds. (Note: The Green LED will FLASH high speed under special mode OR FLASH low speed under normal output mode). If you press the F/S button a second time while the Green LED is flashing, the receiver will change its output mode status (special/normal), if you do not press the F/S button the output mode will not be changed and the Red LED will flash at its original speed.Note: Output mode function is described in the form below,R4FA‐SB R6FA‐SBnormal Ch1~CH4 independent PPM output normal Ch1~CH7 independent PPM outputCH1 Neg CPPM out(FUTABA trainer FUNC)^1 CH2 Pos CPPM out for special user^2 CH1~CH6 independent high speed(HS)PPM out for helicopter fast response controlCH3 RSSI PWM out for FPV()^3 specialCH4 S.BUS output for compact system specialCH7 S.BUS output for compact systemNote: ^1 refer the signal description picture below^2 refer the signal description picture below^3 refer the signal description picture belowRSSI PWM out define: Pulse width from about 900uS~ 2100uS to indicate RSSI strength from ‐100dBm~‐40dBm.Important Note: If you are using analog servos in your model you must keep your receiver under the factory settings (normal output mode) or your analog servo will get hot and possibly burn out. As well you cannot use a non S.BUS servo on a channel while S.BUS signal output present.LED status indicated under normal working status:RED LED GREEN LED Statusflash off No signal searchedoff solid Signal is very goodSometime flash solid Signal is not very goodflash flash Signal is weak。
CCIE R&S Troubleshooting-排错实例

Are you ready to find prefixes that go bump in the night? Here is the sample Trouble Ticket we will attack, and the appropriate portion of the Cisco diagram. You will want to have some scratch paper handy (just like in the actual exam). Diagramming can prove to be more important here then in any exam section. You should practice a diagram now based on the show output that follows.Trouble Ticket 1Vampires located in VLAN 666 (behind Amityville) are unable to access any resources located behind Transylvania. Correct this issue without static routing, additional routing protocols, or redistribution of any kind.The first order of business is to “expand” upon t heir diagram and determine what protocols are in use and where. A quick show ip protocols on each of the devices in the transit path should do the trick.Transylvania#show ip protocolsRouting Protocol is "eigrp 100"Outgoing update filter list for all interfaces is not setIncoming update filter list for all interfaces is not setDefault networks flagged in outgoing updatesDefault networks accepted from incoming updatesEIGRP metric weight K1=1, K2=0, K3=1, K4=0, K5=0EIGRP maximum hopcount 100EIGRP maximum metric variance 1Redistributing: eigrp 100EIGRP NSF-aware route hold timer is 240sAutomatic network summarization is not in effectMaximum path: 4Routing for Networks:53.234.10.23/32Routing Information Sources:Gateway Distance Last UpdateDistance: internal 90 external 170Routing Protocol is "bgp 65001"Outgoing update filter list for all interfaces is not setIncoming update filter list for all interfaces is not setIGP synchronization is disabledAutomatic route summarization is disabledUnicast Aggregate Generation:10.10.0.0/16 summary-onlyNeighbor(s):Address FiltIn FiltOut DistIn DistOut Weight RouteMap 53.234.10.44Maximum path: 1Routing Information Sources:Gateway Distance Last UpdateDistance: external 20 internal 200 local 200HalloweenTown#show ip protocolsRouting Protocol is "eigrp 100"Outgoing update filter list for all interfaces is not setIncoming update filter list for all interfaces is not setDefault networks flagged in outgoing updatesDefault networks accepted from incoming updatesEIGRP metric weight K1=1, K2=0, K3=1, K4=0, K5=0EIGRP maximum hopcount 100EIGRP maximum metric variance 1Redistributing: eigrp 100EIGRP NSF-aware route hold timer is 240sAutomatic network summarization is not in effectMaximum path: 4Routing for Networks:53.234.10.44/32Routing Information Sources:Gateway Distance Last UpdateDistance: internal 90 external 170Routing Protocol is "bgp 65001"Incoming update filter list for all interfaces is not setIGP synchronization is disabledAutomatic route summarization is disabledNeighbor(s):Address FiltIn FiltOut DistIn DistOut Weight RouteMap 23.10.24.19053.234.10.23Maximum path: 1Routing Information Sources:Gateway Distance Last UpdateDistance: external 20 internal 200 local 200Salem#show ip protocolsRouting Protocol is "ospf 1"Outgoing update filter list for all interfaces is not setIncoming update filter list for all interfaces is not setRouter ID 66.150.201.12Number of areas in this router is 1. 1 normal 0 stub 0 nssaMaximum path: 4Routing for Networks:Routing on Interfaces Configured Explicitly (Area 0):FastEthernet0/0Reference bandwidth unit is 100 mbpsRouting Information Sources:Gateway Distance Last Update102.34.102.12 110 00:30:55Distance: (default is 110)Routing Protocol is "bgp 65000"Outgoing update filter list for all interfaces is not setIncoming update filter list for all interfaces is not setIGP synchronization is disabledAutomatic route summarization is disabledNeighbor(s):Address FiltIn FiltOut DistIn DistOut Weight RouteMap 23.10.24.200Maximum path: 1Routing Information Sources:Gateway Distance Last UpdateDistance: external 20 internal 200 local 200CrystalLake#show ip protocolsRouting Protocol is "ospf 1"Incoming update filter list for all interfaces is not setRouter ID 102.34.102.1Number of areas in this router is 1. 1 normal 0 stub 0 nssaMaximum path: 4Routing for Networks:Routing on Interfaces Configured Explicitly (Area 0):FastEthernet0/1FastEthernet0/0Reference bandwidth unit is 100 mbpsRouting Information Sources:Gateway Distance Last UpdateDistance: (default is 110)Routing Protocol is "bgp 65000"Outgoing update filter list for all interfaces is not setIncoming update filter list for all interfaces is not setIGP synchronization is disabledAutomatic route summarization is disabledNeighbor(s):Address FiltIn FiltOut DistIn DistOut Weight RouteMap 66.150.201.12Address FiltIn FiltOut DistIn DistOut Weight RouteMap 102.34.102.12Maximum path: 1Routing Information Sources:Gateway Distance Last UpdateDistance: external 20 internal 200 local 200Amityville#show ip protocolsRouting Protocol is "ospf 1"Outgoing update filter list for all interfaces is not setIncoming update filter list for all interfaces is not setRouter ID 102.34.102.12Number of areas in this router is 1. 1 normal 0 stub 0 nssaMaximum path: 4Routing for Networks:Routing on Interfaces Configured Explicitly (Area 0):FastEthernet0/0Reference bandwidth unit is 100 mbpsRouting Information Sources:Gateway Distance Last Update102.34.102.1 110 00:33:23Distance: (default is 110)Routing Protocol is "bgp 65000"Outgoing update filter list for all interfaces is not setIncoming update filter list for all interfaces is not setIGP synchronization is disabledAutomatic route summarization is disabledNeighbor(s):Address FiltIn FiltOut DistIn DistOut Weight RouteMap102.34.102.1Maximum path: 1Routing Information Sources:Gateway Distance Last UpdateDistance: external 20 internal 200 local 200As I parse the results, I create a more detailed diagram to provide a better picture of what is going on. Looking at the diagram, I immediately contemplate some design issues th at could come into play. The iBGP split-horizon rule, next-hop reachability, and synchronization all could come into play here given the protocol configuration.I decide to start as close the destination as possible and examine the relevant configurations.Transylvania#show run | section bgprouter bgp 65001no synchronizationbgp log-neighbor-changesnetwork 10.0.0.0aggregate-address 10.10.0.0 255.255.0.0 summary-onlyneighbor 53.234.10.44 remote-as 65001no auto-summaryIt appears the intent is to advertise prefixes (the Loopback interfaces) beyond Transylvania using BGP prefix aggregation. Let me ensure that configuration is done correctly.Sure enough, here is our first BGP configuration issue. We need to advertise a component prefix of the aggregate. The little gremlin that attempted this configuration tried to accomplish this with the network statement, but they got it wrong. Subnetting is being done here of the 10.x.x.x space, so you need to reconfigure the network statement as follows:Transylvania#show ip int briefInterface IP-Address OK? MethodStatus ProtocolFastEthernet0/0 53.234.10.23 YES manualup upFastEthernet0/1 unassigned YESunset administratively down downLoopback1 10.10.10.1 YES manualup upLoopback2 10.10.11.1 YES manualup upLoopback3 10.10.12.1 YES manualup upTransylvania#configure terminalEnter configuration commands, one per line. End with CNTL/Z. Transylvania(config)#router bgp 65001Transylvania(config-router)#network 10.10.10.0 mask 255.255.255.0After making this change, I check Salem to see if it is receiving the aggregate from Transylvania and we have reachability:Salem#show ip bgpBGP table version is 2, local router ID is 66.150.201.12Status codes: s suppressed, d damped, h history, * valid, > best, i - internal,r RIB-failure, S StaleOrigin codes: i - IGP, e - EGP, ? - incompleteNetwork Next Hop Metric LocPrf Weight Path*> 10.10.0.0/16 23.10.24.200 0 65001 i Salem#show ip route bgp10.0.0.0/16 is subnetted, 1 subnetsB 10.10.0.0 [20/0] via 23.10.24.200, 00:06:26Salem#ping 10.10.10.1Type escape sequence to abort.Sending 5, 100-byte ICMP Echos to 10.10.10.1, timeout is 2 seconds: !!!!!Success rate is 100 percent (5/5), round-trip min/avg/max = 28/33/40 msWe are on our wa y to solving this Trouble Ticket…we hope you will follow this blog and continue this (and more) troubleshooting scenarios!。
北师大版高中英语必修二《Information Technology》(第5课时)

Focus on Language
Compound words
A compound word is two words that joined together to create a new meaning.
butter + fly = butterfly
Focus on Language
Complete the compound words with a word from
speed railwa,ywill make our country stronger.
like high-
Focus on Language
Adjectives
What do adjectives (adj.) do? Adjectives describe nouns.
Focus on Language
the circles.
1. friend 2. any 3. per 4. web
site ship cent thing
5. on 6. self7. real8. smart
phone line
centred life
Focus on Language
Complete the compound words with a word from
Some people believe that the Internet has many negative aspects. Talking to people online or having a friendship with someone you only talk to on the Internet isn’t a replacement for real-life communication. While it can connect you with other people …
Recom RAC AC DC Converter 产品说明说明书

RAC AC/DC ConverterFeaturesRegulated Converter• Wide input range 85-305VAC• Standby mode optimized (eco design Lot 6)• High efficiency over the entire load range • Operating temperature range: -40°C to +90°C • Overvoltage and overcurrent protected• EMC compliant without external components • Encapsulated module with pins or wiredDescriptionThe RAC05-K/277 series are multipurpose 5 watt AC/DC power supplies for enhanced mains input conditions from 90VAC up to 305VAC with an extra wide operating temperature range from -40°C to +90°C. These modules are designed to supply worldwide applications in automation, Industry 4.0, IoT, household and smart buildings. For worldwide use they come with international safety certifications for industrial, domestic and ITE as well as household standards. With both PCB-mount and wired packages, fully protected outputs, and EMC class B emissions compliance without any external components, these are the easiest to use modular power solutions in the industry.E224736RAC05-__ SK/277/WModel NumberingOrdering Examples:RAC05-05SK/277 5 Watt 5Vout Single Output THT version RAC05-24SK/277 5 Watt 24Vout Single Output THT version RAC05-05SK/277/W 5 Watt 5Vout Single Output Wired version RAC05-12SK/277/W5 Watt 12Vout Single Output Wired versionS inglenom. Output PowerOutput Voltage5 Watt Single OutputRAC05-K/277Selection GuidePart Input Output Output Efficiency Max. CapacitiveNumber Voltage Range Voltage Current typ (1) Load (2)[VAC] [VDC] [mA] [%] [µF]RAC05-3.3SK/277 85-305 3.3 1510 77 10000RAC05-05SK/277 85-305 5 1000 80 8000RAC05-12SK/277 85-305 12 416 83 1500RAC05-15SK/277 85-305 15 330 83 1000RAC05-24SK/277 85-305 24 210 84 330Notes:Note1: Efficiency is tested at nominal input and full load at +25°C ambient Note2: Max Cap Load is tested at nominal input and full resistive loadW ired Notes:Note3: add suffix …W“ for wired versionwithout suffix, standard THT versionUL62368-1 certified EN62368-1 certified IEC/EN60335-1 certified EN62233 certifiedIEC/EN61558-1 certified IEC/EN61558-2-16 certified EN55032 compliantEN55014-1(-2) compliant CB ReportSpecifications(measured @ Ta= 25°C, nom. Vin, full load and after warm-up unless otherwise stated)Specifications (measured @ Ta= 25°C, nom. Vin, full load and after warm-up unless otherwise stated)REGULATIONSParameterConditionValueOutput Accuracy ±1.0% typ.Line Regulation low line to high line, full load±0.5% typ. Load Regulation (7)10% to 100% load 1.0% typ.Transient Response25% load step change4.0% max.recovery time500µs typ.PROTECTIONSParameterTypeValueInput Fuse (8)internal T1A, slow blowShort Circuit Protection (SCP)below 100m Whiccup, automatic restart Over Voltage Protection (OVP)125% - 195%, latch of modeOver Voltage Category OVC IIOver Current Protection (OCP)125% - 195%, hiccup modeClass of EquipmentClass IIIsolation Voltage (safety certified) (9)I/P to O/P1 minute4.2kVACIsolation Resistance Isolation Voltage 500VDC 1G W min.Isolation Capacitance 100pF max.Insulation Grade reinforced Leakage Current0.25mA max.continued on next pageDeviation vs. Load(at 115VAC, 230VAC, 277VAC)10.50-0.5-1D e v i a t i o n [%]102030405060708090100Output Load [%]10.5-0.5-1D e v i a t i o n [%]0102030405060708090100Output Load [%]RAC05-05SK/277RAC05-12SK/277Notes:Note8: Refer to local safety regulations if input over-current protection is also required Note9: For repeat Hi-Pot testing, reduce the time and/or the test voltageNotes:Note7: Operation below 10% load will not harm the converter, but specifications may not be metSpecifications(measured @ Ta= 25°C, nom. Vin, full load and after warm-up unless otherwise stated)Specifications(measured @ Ta= 25°C, nom. Vin, full load and after warm-up unless otherwise stated)SAFETY AND CERTIFICATIONSCertificate Type (Safety)Report / File Number StandardAudio/Video, information and communication technology equipment - Part 1: Safety requirements E491408-A6004-ULUL62368-1, 2nd Edition, 2014-12-01CAN/CSA-C22.2 No. 62368-1-14, 2nd Edt., 2014-12Audio/Video, information and communication technology equipment -Part 1: Safety requirements (CB Scheme)E491408-A6007-CB-1IEC62368-1:2014 2nd EditionAudio/Video, information and communication technology equipment -Part 1: Safety requirements (LVD)EN62368-1:2014 + A11:2017Household and similar electrical appliances - Safety -Part 1: General requirementsLCS190308001CS IEC60335-1:2010 + A2:2016 + C1:2016, 5th Edt.EN60335-1:2012 + A13:2017Measurement methods for electromagnetic fields of household appliances and similarapparatus with regard to human exposureEN62233:2008Safety of power transformers, power supplies, reactors and similar products for sup-ply voltages up to 1100 V (CB Scheme)50230493 001IEC61558-1:2005 2nd Edition + A1:2009Safety of power transformers, power supplies, reactors and similar products for sup-ply voltages up to 1100 V Part 2: Particular requirements (CB Scheme)IEC61558-2-16:2009 1st Edition + A1:2013 Safety of power transformers, power supplies, reactors and similar products for sup-ply voltages up to 1100 VEN61558-1:2005 + A1:2009 Safety of power transformers, power supplies, reactors and similar products for sup-ply voltages up to 1100 V Part 2: Particular requirementsEN61558-2-16:2009 + A1:2013 RoHS2RoHS-2011/65/EU + AM-2015/863 EMC Compliance Conditions Standard / Criterion Low-voltage power supplies DC output - Part 3: Electromagnetic compatibility EN61204-3: 2018, Class B Electromagnetic compatibility of multimedia equipment - Emission requirements (11)EN55032:2015, Class B Electromagnetic compatibility - Requirements for household appliances, electric toolsand similar apparatus - Part 1: EmissionEN55014-1:2006 + A2:2011 I nformation technology equipment - Immunity characteristics - Limits and methods of measurement EN55024:2010 + A1:2015 Electromagnetic compatibility - Requirements for household appliances, electric toolsand similar apparatus - Part 2: ImmunityEN55014-2:2015ESD Electrostatic discharge immunity testAir: ±2, 4, 8kVContact: ±2, 4kVEN61000-4-2: 2009, Criteria BRadiated, radio-frequency, electromagnetic field immunity test 10V/m, 80MHz-1GHz3V/m, 1.4GHz-2GHz1V/m, 2GHz-2.7GHzEN61000-4-3: 2006 + A1, 2009, Criteria AFast Transient and Burst Immunity AC and DC Port: ±2kV EN61000-4-4: 2012, Criteria BSurge Immunity AC In Port (L-N): ±1kVDC Output Port: ±0.5kVEN61000-4-5: 2014 +A1:2017, Criteria BImmunity to conducted disturbances, induced by radio-frequency fields AC and DC Port: 10V EN61000-4-6: 2014, Criteria A Power Magnetic Field Immunity50Hz, 30A/m EN61000-4-8: 2010, Criteria AVoltage Dips and InterruptionsVoltage Dips: 30%Voltage Dips: 60%Voltage Dips: 100%Interruptions: >95%EN61000-4-11:2004 + A1:2017, Criteria CEN61000-4-11:2004 + A1:2017, Criteria CEN61000-4-11:2014 + A1:2017, Criteria BEN61000-4-11: 2014 + A1:2017,Criteria CVoltage Fluctuations and Flicker in Public Low-Voltage Systems <=16A per phase EN61000-3-3: 2013 Limitations on the amount of electromagnetic interference allowed from digital and electronic devices FCC 47 CFR Part 15 Supbart B, Class B Methods of Measurement of Radio-Noise Emissions from Low-Voltage Electrical andElectronic Equipment in the Range of 9 kHz to 40 GHzANSI C63.4-2014, Class BNotes:Note11: If output is connected to GND, please contact RECOM tech support for adviceSpecifications(measured @ Ta= 25°C, nom. Vin, full load and after warm-up unless otherwise stated)Specifications (measured @ Ta= 25°C, nom. Vin, full load and after warm-up unless otherwise stated)The product information and specifications may be subject to changes even without prior written notice.The product has been designed for various applications; its suitability lies in the responsibility of each customer. The products are not authorized for use in safety-critical applications without RECOM’s explicit written consent. A safety-critical application is an application where a failure may reasonably be expected to endanger or cause loss of life, inflict bodily harm or damage property. The applicant shall indemnify and hold harmless RECOM, its affiliated companies and its representatives against any damage claims in connection with the unauthorizeduse of RECOM products in such safety-critical applications.PACKAGING INFORMATIONParameterTypeValuePackaging Dimension (LxWxH)THT wiredtube tray466.0 x 30.4 x 29.3mm 468.0 x 198.0 x 46.0mmPackaging Quantity THT wired12pcs 24pcsStorage Temperature Range -40°C to +85°C Storage Humiditynon-condensing 20% to 90% RH max.。
LabWindows CVI实时模块入门指南说明书

Getting Started with the LabWindows/CVI Real-Time™™ModuleThis document provides an introduction to the LabWindows™/CVI™ Real-Time Module. Refer to this document for installation and configuration instructions and information about creating a real-time (RT) project.Installing the Real-Time Module Software on a Host ComputerYou must first install the Real-Time Module software on a host computer. Then you can configure and install software on the RT target.To install and use the Real-Time Module software, you must have the following:•Free Disk Space—In addition to the minimum system requirements for LabWindows/CVI, you must have at least 250 MB of free disk space for the Real-Time Module software. Refer to the LabWindows/CVI Release Notes for minimum system requirements.•RT Target—The LabWindows/CVI Real-Time Module supports NI RT Series PXI controllers, NI Real-Time Industrial Controllers, stand-alone NI CompactDAQ systems, and desktop PCs converted to RT targets.•Refer to the Using Desktop PCs as RT Targets with the Real-Time Module document for more information about converting a desktop computer to an RT target.Refer to the LabWindows/CVI Real-Time Module Readme for a step-by-step guide to installing the LabWindows/CVI Real-Time Module. You can access the LabWindows/CVI Real-Time Module Readme by selecting Start»All Programs»National Instruments»LabWindows/CVI version»LabWindows/CVI Real-Time Module Readme.Configuring the RT T argetAfter you install LabWindows/CVI and the RT module, you must use Measurement & Automation Explorer (MAX) to configure the RT target and to install software and drivers on the RT target. MAX provides access to NI devices and systems and can communicate with networked RT targets, also known as remote systems.Complete the following steps to configure the RT target. The following sections describe these steps in more detail.1.Boot the RT target into LabVIEW RT.2.Configure network settings.2| |Getting Started with the LabWindows/CVI Real-Time Module3.Install software on the RT target.4.Configure I/O.5.Configure system settings.6.Configure time settings.Refer to the Measurement & Automation Explorer Help for a complete tutorial aboutconfiguring the RT target. Select Help»MAX Help to access this help file, and then refer to the MAX Remote Systems Help section.Tip The Measurement & Automation Explorer Help refers to the LabVIEWReal-Time Module. However, you can apply the same concepts when you use theLabWindows/CVI Real-Time Module.Booting the RT Target into LabVIEW RTBefore you begin configuration, make sure your remote system is booted into LabVIEWReal-Time. If your RT target came with only LabVIEW Real-Time preinstalled on its hard drive, the system is already set up to boot into LabVIEW Real-Time. Many NI RT targets have DIP switches or BIOS settings for booting into LabVIEW Real-Time. For more information, refer to the Booting Into the LabVIEW Real-Time Module topic in the Measurement & Automation Explorer Help .You can permanently format the hard drive and configure it to boot directly into RT using the Tools»Desktop PC Utility USB Drive command in MAX.Configuring Network SettingsNoteFor the initial configuration, you must connect networked RT targets to thesame network subnet as the host computer from which you launch MAX.1.Connect the RT target to the network and power on the target.2.Launch MAX and expand the Remote Systems item in the MAX configuration tree.3.Select the RT target from the Remote Systems list. Some RT targets will be listed with an automatically configured name or IP address while other targets will be listed as 0.0.0.0.4.Specify a name for the RT target in the System Settings tab.5.Configure the IP address settings in the Network Settings tab using one of the followingoptions:•Select the DHCP or Link Local item from the Configure IPv4 Address option to obtain an IP address automatically.•Select the Static item from the Configure IPv4 Address option and specify anIP address.6.Click Save to commit the changes.7.Click Yesto reboot the RT target when prompted.Getting Started with the LabWindows/CVI Real-Time Module |© National Instruments |3Installing Software on the RT TargetUse the LabVIEW Real-Time Software Wizard in MAX to install the software and drivers from the host computer on the RT target. With the LabVIEW Real-Time Software Wizard, you can view and change the software that is installed on the target. Click Help in the wizard for more information about installing and uninstalling software on the RT target.Complete the following steps to launch the LabVIEW Real-Time Software Wizard:1.Launch MAX.2.Find and expand your RT target under the Remote Systems item in the MAX configurationtree, right-click Software , and select Add/Remove Software .When you select Add/Remove Software , MAX launches the LabVIEW Real-TimeSoftware Wizard. This displays all the National Instruments software and drivers installed on the host computer that you can install on a selected RT target.3.Select the software you want to install on the RT target, click the icon next to the software,and select Install the feature .Some components are automatically included as dependencies of other components. For more information about the features listed in the wizard, select the feature to view a description.The following list describes components you might commonly install.NoteIf you have multiple versions of a component installed on the host computer,the most recent version is selected by default. You can choose to install anotherversion.•Ethernet Drivers —MAX automatically selects the appropriate Ethernet driver(s) forthe RT target when you install the LabWindows/CVI Run-Time Engine for RTcomponent.•LabVIEW Real Time —MAX selects this item automatically when you install the LabWindows/CVI Run-Time Engine for RT component.–NI RT Extensions for SMP (MultiCore Support)—Install this item to takeadvantage of parallel processing on a multiple-CPU system.NoteSingle-CPU systems perform best without the NI RT Extensions for SMP .Also, some applications, such as those that consist mainly of single-point I/O, canachieve lower latency on a multicore system by using a single CPU without the NI RT Extensions for SMP .–Microsoft Visual Studio 2008 Runtime Support —Install this item if your application requires additional DLLs built with Visual Studio 2008.•LabWindows/CVI Network Streams for RT —Install this item if your application uses functions from the Network Streams Library. •LabWindows/CVI Network Variable for RT —Install this item if your applicationuses functions from the Network Variable Library.•LabWindows/CVI Run-Time Engine for RT—Install this item to add support for LabWindows/CVI RT applications on the RT target. This component is required forall LabWindows/CVI RT applications.•Language Support for LabVIEW RT—Install this item if you are using strings in your RT application containing ASCII characters above 127 or multibyte characters.After installing this item on the RT target, you can configure the locale in MAX byselecting the target in the Remote Systems item in the MAX configuration tree,selecting the System Settings tab, and modifying the Locale option.•NI Hardware Drivers—Install the appropriate drivers for any other hardware libraries that you use in your application. For example, install the NI-DAQmxcomponent if your application uses functions from the NI-DAQmx Library.•Network Variable Engine—MAX automatically selects this item when you install the LabWindows/CVI Network Variable for RT component.•NI Web-Based Configuration and Monitoring—Install this item to use a Web browser to monitor and configure an RT target.•State System Publisher—Install this item to monitor CPU and memory usage for an RT target from the NI Distributed System Manager.•USB Support—Install this item to enable support for accessing USB thumbdrives.•Variable Client Support for LabVIEW RT—MAX automatically selects this item when you install the LabWindows/CVI Network Variable for RT component. 4.When you finish selecting the software you want to install, click Next and continuefollowing the instructions on the screen.Configuring I/OYou must configure any National Instruments I/O devices before you can use them from a LabWindows/CVI RT application. For information about how to correctly configure I/O devices, refer to the documentation for that hardware.Configuring System Settings1.Select the System Settings tab to configure system-level settings for the RT target.2.Configure the Locale option to match the language you use for strings in your RTapplication. This option is available only when you install the Language Support for LabVIEW RT component on the RT target. This option determines the code page that LabWindows/CVI uses when processing strings containing ASCII characters above 127 or multibyte characters.Configuring Time Settings1.Select the Time Settings tab to configure date and time settings for the RT target.e the Time Zone option to configure the time zone for the RT target. You can use thissetting with time and date functions to provide accurate time information relative to the time zone setting.4||Getting Started with the LabWindows/CVI Real-Time ModuleUsing NI Web-Based Monitoring and ConfigurationIf you install NI Web-Based Monitoring and Configuration, you can use a Web browser to monitor and configure the RT target.Configuration. If you have not installed Microsoft Silverlight, NI Web-BasedMonitoring and Configuration prompts you to do so.1.In a Web browser, enter the URL http://[IP address of the RT target] toaccess Web-based monitoring and configuration for the remote system.2.Click the Login button in the top-right corner of the page.3.Enter Admin in the User name field.4.Leave the Password field blank.5.Click the OK button.6.When you log in, you can view and change system, network, security, and time settings;view console output remotely; access the file system remotely; and so on.For more information about NI Web-Based Monitoring and Configuration, refer to the LabWindows/CVI Real-Time Module Help.Configuring an RT ProjectAfter you configure the RT target, you can create an RT application on the host computer and then run the application on an RT target. The applications that you create with the LabWindows/CVI Real-Time Module are DLLs.Complete the following steps to create a DLL and specify an RT target directly from LabWindows/CVI.1.Create a project in LabWindows/CVI using RTmain instead of main as the entry pointfunction for the program. Select Edit»Insert Construct»RTmain to insert the RTmain code into the program source.2.Select Build»Configuration»Debug or Build»Configuration»Release to specify theactive configuration for the project.3.Select Build»Target Type»Dynamic Link Library to configure the project to generate aDLL.4.Select Build»Target Settings to open the Target Settings dialog box. Select Real-timeonly in the Run-time support option. If you specify this option, LabWindows/CVI does not link to the entire set of LabWindows/CVI libraries but instead links to only thoselibraries supported on an RT system.5.Click OK to exit the dialog box.6.Select Build»Build to create the DLL.You also can use a project template to create an RT DLL. The project template includes basicsettings for RT projects described in the preceding section. To select a project template,Getting Started with the LabWindows/CVI Real-Time Module|© National Instruments|5select File»New»Project from Template. In the New Project from Template dialog box, select Real-Time Target Application.Specifying an RT TargetComplete the following steps to select the RT target on which to run your RT application.1.Select Run»Select Execution Target for Debugging to view a list of previouslyconfigured RT targets. Select the RT target you want to use from the list, if it is available.2.To configure a new RT target, select Run»Select Execution Target for Debugging»NewExecution Target.3.In the New Real-Time Execution Target dialog box, enter the computer name or IP addressof the RT target in the Hostname/IP Address option and click OK to exit the dialog box. Running an RT ApplicationSelect Run»Debug Project to run your RT application.warning message. Click Continue to download and run the release DLL on the RTtarget.LabWindows/CVI automatically builds the DLL and downloads the DLL and any DLLs that are statically linked to it onto the specified RT target. LabWindows/CVI places the files that it automatically downloads in the NI-RT\CVI\temp folder. LabWindows/CVI empties the folder when you reset the RT device.While you run your RT application, LabWindows/CVI displays a <<Running on target>> menu in the upper left corner of the LabWindows/CVI environment. The menu contains the following options, which you can use for debugging and for shutting down the RT application:•Toggle Breakpoint—Turn on or turn off a breakpoint on the selected line when a Source window is active.•Break Execution—Suspend execution of the program.•Simulate RT Shutting Down—End program execution. This option causes the RTIsShuttingDown function to return 1, giving the RT application an opportunity to run any necessary cleanup code and exit. The RT target does not reboot.•Abort Execution and Reboot Target—End program execution and reboot the RT target.The application cleanup code is not guaranteed to finish running before the RT target reboots.•Disconnect from RT target—Disconnect LabWindows/CVI from the RT target while theRT application continues running on the target. Once you disconnect from the RT target,you cannot reconnect LabWindows/CVI to the RT application that is running.6||Getting Started with the LabWindows/CVI Real-Time ModuleDebugging an RT ApplicationIf you select Build»Configuration»Debug, you can debug the DLL from the LabWindows/CVI environment as you would debug any other application. For example, you can set breakpoints and watch expressions, step through code, view and edit variable values, and so on. For more information about debugging in LabWindows/CVI, refer to the Using LabWindows/CVI»Debugging Tools section of the LabWindows/CVI Help.Using the Real-Time Execution T race ToolkitThe LabWindows/CVI Real-Time Module includes a limited time full-featured evaluation of the Real-Time Execution Trace Toolkit.Use the Real-Time Execution Trace Toolkit to analyze the timing and execution of an RT application. Use the Execution Trace functions in the Real-Time Utility Library to capture the timing and execution data of functions and threads in an application running on an RT target. The Real-Time Execution Trace Tool displays the timing and event data, or trace session, on the host computer.In LabWindows/CVI, select Tools»Real-Time Execution Trace Tool to launch the Real-Time Execution Trace Tool. Refer to the LabWindows/CVI Help for more information about using the Real-Time Execution Trace Toolkit to analyze RT applications.Deploying an RT ApplicationWhen you finish developing your RT application, you can deploy it to an RT target. After you deploy the RT application, the RT application runs automatically every time the RT target reboots.Select Run»Install Program to Real-Time Execution Target to deploy your RT application. This option performs the following actions:•Checks that the release configuration of the DLL has been built; if not, LabWindows/CVI prompts you to build the DLL or cancel.•Deploys the release DLL and any statically linked DLLs to the NI-RT\CVI folder on the RT target.•Sets the release DLL as a startup DLL.•Displays a dialog box indicating that the DLL was copied and prompting you to reboot the RT target.If you have additional support files that you need to deploy, complete the following steps:1.Select Run»Manage Files on Real-Time Execution Target to launch theLabWindows/CVI Real-Time File Copy Utility.2.Click Add Files and browse to any support files that your application requires. The utilityimmediately copies the files to the NI-RT\CVI folder on the RT target.3.Click Done when you finish adding support files.Getting Started with the LabWindows/CVI Real-Time Module|© National Instruments|7Where to Go from HereRefer to the following resources for more information about the LabWindows/CVI Real-Time Module:•The LabWindows/CVI Real-Time Module Help section of the LabWindows/CVI Help includes conceptual information about real-time programming techniques, application architectures, and Real-Time Module software features you can use to create real-time applications. Select Help»Contents in LabWindows/CVI to access the LabWindows/CVI Help.•Use the NI Example Finder, available by selecting Help»Find Examples in LabWindows/CVI, to browse or search for example programs. You also can access the example programs from the samples\CVI samples\realtime directory.Refer to the NI Trademarks and Logo Guidelines at /trademarks for more information on National Instruments trademarks. Other product and company names mentioned herein are trademarks or trade names of their respective companies. For patents covering National Instruments products/technology, refer to the appropriate location: Help»Patents in your software, the patents.txt file on your media, or the National Instruments Patents Notice at /patents. You can find information about end-user license agreements (EULAs) and third-party legal notices in the readme file for your NI product. Refer to the Export Compliance Information at /legal/export-compliance for the National Instruments global trade compliance policy and how to obtain relevant HTS codes, ECCNs, and other import/export data.© 2007–2013 National Instruments. All rights reserved.374686E-01Aug13。
DrayTek Vigor2865 35b Security Firewall Quick Star
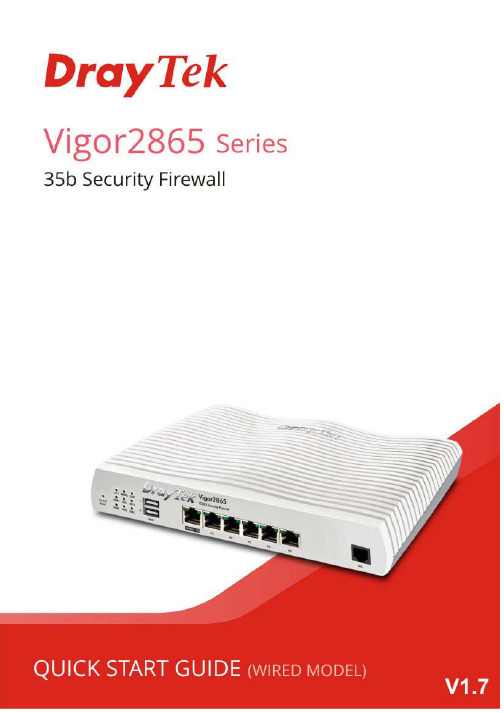
Vigor286535b Security Firewall Quick Start Guide (for Wired Model)Version: 1.7Firmware Version: V4.4.2(For future update, please visit DrayTek web site)Date: June 27, 2023Intellectual Property Rights (IPR) InformationCopyrights © All rights reserved. This publication contains information that is protected by copyright. No part may be reproduced, transmitted, transcribed, stored ina retrieval system, or translated into any language without written permissionfrom the copyright holders.Trademarks The following trademarks are used in this document:●Microsoft is a registered trademark of Microsoft Corp.●Windows 8,10, 11 and Explorer are trademarks of Microsoft Corp.●Apple and Mac OS are registered trademarks of Apple Inc.●Other products may be trademarks or registered trademarks of theirrespective manufacturers.Safety Instructions and ApprovalSafety Instructions ●Read the installation guide thoroughly before you set up the router.●The router is a complicated electronic unit that may be repaired only beauthorized and qualified personnel. Do not try to open or repair therouter yourself.●Do not place the router in a damp or humid place, e.g. a bathroom.●Do not stack the routers.●The router should be used in a sheltered area, within a temperaturerange of +5 to +40 Celsius.●Do not expose the router to direct sunlight or other heat sources. Thehousing and electronic components may be damaged by direct sunlight or heat sources.●Do not deploy the cable for LAN connection outdoor to prevent electronicshock hazards.●Do not power off the router when saving configurations or firmwareupgrades. It may damage the data in a flash. Please disconnect theInternet connection on the router before powering it off when a TR069/ ACS server manages the router.●Keep the package out of reach of children.●When you want to dispose of the router, please follow local regulations onconservation of the environment.Warranty We warrant to the original end user (purchaser) that the router will be free from any defects in workmanship or materials for a period of two (2) yearsfrom the date of purchase from the dealer. Please keep your purchase receiptin a safe place as it serves as proof of date of purchase. During the warrantyperiod, and upon proof of purchase, should the product have indications offailure due to faulty workmanship and/or materials, we will, at our discretion,repair or replace the defective products or components, without charge foreither parts or labor, to whatever extent we deem necessary tore-store theproduct to proper operating condition. Any replacement will consist of a newor re-manufactured functionally equivalent product of equal value, and willbe offered solely at our discretion. This warranty will not apply if the productis modified, misused, tampered with, damaged by an act of God, or subjectedto abnormal working conditions. The warranty does not cover the bundled orlicensed software of other vendors. Defects which do not significantly affectthe usability of the product will not be covered by the warranty. We reservethe right to revise the manual and online documentation and to make changesfrom time to time in the contents hereof without obligation to notify anyperson of such revision or changes.EU Declaration of ConformityWe DrayTek Corp. , office at No.26, Fushing Rd., Hukou, Hsinchu Industrial Park, Hsinchu 303, Taiwan, declare under our soleresponsibility that the product●Product name: VDSL2 Security Firewall●Model number: Vigor2865●Manufacturer: DrayTek Corp.●Address: No.26, Fushing Rd., Hukou, Hsinchu Industrial Park, Hsinchu 303, Taiwan.is in conformity with the relevant Union harmonisation legislation:EMC Directive 2014/30/EU , Low Voltage Directive 2014/35/EU , ErP 2009/125/EC and RoHS2011/65/EU with reference to the following standardsStandard Version / Issue dateEN 550322012+AC:2013 class BEN 61000-3-22014 Class AEN 61000-3-32013EN 550352017+A11:2020EN 62368-12014+A11:2017EC No. 1275/2008 2008Hsinchu2nd September, 2019Calvin Ma / President .Signature)(place) (date)(LegalDeclaration of ConformityWe DrayTek Corp. , office at No.26, Fushing Rd., Hukou, Hsinchu Industrial Park, Hsinchu 303, Taiwan, declare under our soleresponsibility that the product●Product name: VDSL2 Security Firewall●Model number: Vigor2865●Manufacturer: DrayTek Corp.●Address: No.26, Fushing Rd., Hukou, Hsinchu Industrial Park, Hsinchu 303, Taiwan●Importer: CMS Distribution Ltd: Bohola Road, Kiltimagh, Co Mayo, Irelandis in conformity with the relevant UK Statutory Instruments:The Electromagnetic Compatibility Regulations 2016 (SI 2016 No.1091), The Electrical Equipment (Safety) Regulations 2016 (SI2016 No.1101), The Ecodesign for Energy-Related Products and Energy Information (Amendment) (EU Exit) Regulations 2019 (SI2019 No.539) and The Restriction of the Use of Certain Hazardous Substances in Electrical and Electronic Equipment Regulations2012 (SI 2012 No. 3032) with reference to the following standards:Standard Version / Issue dateEN 550322012+AC:2013 class BEN 61000-3-22014 Class AEN 61000-3-32013EN 550352017+A11:2020EN 62368-12014+A11:2017EC No. 1275/2008 2008Hsinchu2nd September, 2019Calvin Ma / President .Signature)(Legal (place) (date)Regulatory InformationFederal Communication Commission Interference StatementThis equipment has been tested and found to comply with the limits for a Class B digital device, pursuant to Part 15 of the FCC Rules. These limits are designed to provide reasonable protection against harmful interference in a residential installation. This equipment generates, uses and can radiate radio frequency energy and, if not installed and used in accordance with the instructions, may cause harmful interference to radio communications. However, there is no guarantee that interference will not occur in a particular installation. If this equipment does cause harmfulinterference to radio or television reception, which can be determined by turning the equipment off and on, the user is encouraged to try to correct the interference by one of the following measures:● Reorient or relocate the receiving antenna.● Increase the separation between the equipment and receiver.● Connect the equipment into an outlet on a circuit different from that to which the receiver is connected.●Consult the dealer or an experienced radio/TV technician for help.This device complies with Part 15 of the FCC Rules. Operation is subject to the following two conditions:(1) This device may not cause harmful interference, and(2) This device may accept any interference received, including interference that may cause undesired operation.Company nameABP International Inc.Address 13988 Diplomat Drive Suite 180 Dallas TX 75234 ZIP Code 75234 E-mail*******************USA Local RepresentativeContact PersonMr. Henry N CastilloTel. (972)831-1600 140Caution:Any changes or modifications not expressly approved by the grantee of this device could void the user's authority to operate the equipment.Any changes or modifications not expressly approved by the party responsible for compliance could void the user's authority to operate this equipment.This transmitter must not be co-located or operating in conjunction with any other antenna or transmitter.Radiation Exposure Statement: This equipment complies with FCC radiation exposure limits set forth for an uncontrolled environment. This equipment should be installed and operated with minimum distance 20cm between the radiator & your body.More update, please visit .*The external power supply used for each product will be model dependent.1 2 3 4 5 6 7 8 9 AManufacturer CWT CWT CWT CWT CWT APD APD APD APDB Address No. 222, Sec.2, Nankan Rd.,LujhuTownship,TaoyuanCounty 338,TaiwanNo. 222, Sec.2, Nankan Rd.,LujhuTownship,TaoyuanCounty 338,TaiwanNo. 222, Sec.2, Nankan Rd.,LujhuTownship,TaoyuanCounty 338,TaiwanNo. 222, Sec.2, Nankan Rd.,LujhuTownship,TaoyuanCounty 338,TaiwanNo. 222, Sec.2, Nankan Rd.,LujhuTownship,TaoyuanCounty 338,TaiwanNo.5, Lane 83,Lung-Sou St.,Taoyuan City330, TaiwanNo.5, Lane 83,Lung-Sou St.,Taoyuan City330, TaiwanNo.5, Lane 83,Lung-Sou St.,Taoyuan City330, TaiwanNo.5, Lane 83,Lung-Sou St.,Taoyuan City330, Taiwan2ABB012F UK 2ABB018F UK 2ABL024F UK 2ABL030F UK 2ABN036F UK WA-12M12FG WB-18D12FG WA-24Q12FG WA-36A12FGC Model identifier2ABB012F EU 2ABB018F EU 2ABL024F EU 2ABL030F EU 2ABN036F EU WA-12M12FK WB-18D12FK WA-24Q12FK WA-36A12FKDInputvoltage 100~240V 100~240V 100~240V 100~240V 100~240V 100~240V 100~240V 100~240V 100~240V InputACfrequency 50/60Hz 50/60Hz 50/60Hz 50/60Hz 50/60Hz 50/60Hz 50/60Hz 50/60Hz 50/60Hz EOutputvoltageDC 12.0V 12.0V 12.0V 12.0V 12.0V 12.0V 12.0V 12.0V 12.0V F Outputcurrent 1.0A 1.5A 2.0A 2.5A 3.0A 1.0A 1.5A 2.0A 3.0A GOutputpower 12.0W 18.0W 24.0W 30.0W 36.0W 12.0W 18.0W 24.0W 36.0W H Average activeefficiency84.9% 86.2% 87.6% 87.8% 89.8% 83.7% 85.4% 88.6% 88.2%I Efficiency at low load10%73.6% 78.0% 81.3% 83.3% 83.7% 74.5% 80.5% 86.4% 85.4% J No-loadpowerconsumption0.07W 0.07W 0.07W 0.07W 0.07W 0.07W 0.10W 0.07W 0.10W External power supply (Power Adapter) information. For more update, please visit .T a b l e o f C o n t e n t s1. Package Content (1)2. Panel Explanation (2)3. Hardware Installation (4)3.1 Network Connection (4)3.2 Wall-Mounted Installation (5)4. Software Configuration (6)4.1 Quick Start Wizard for Network Connection (6)5. Customer Service (12)Be a Registered Owner (12)Firmware & Tools Updates (12)1.P a c k a g e C o n t e n tTake a look at the package content. If there is anything missed or damaged, please contact DrayTek or dealer immediately.Vigor router Quick Start GuideRJ-45 Cable (Ethernet)RJ-11 to RJ-45 Cable (Annex B)RJ-11 to RJ-11 Cable (Annex A) The type of the power adapter depends on the country that the router will be installed. * The maximum power consumption is 22 Watts.UK-type Power Adapter EU-type Power AdapterUSA/Taiwan-type Power Adapter AU/NZ-type Power Adapter2. P a n e l E x p l a n a t i o nLED Status ExplanationOff The router is powered off.ACTBlinking The router is powered on and running normally.On Internet connection is ready. OffInternet connection is not ready. WAN2Blinking The data is transmitting. On The QoS function is active. QoS Off The QoS function is inactive.On USB device is connected and ready for use. OffNo USB device is connected. USB1~2Blinking The data is transmitting.On The router is ready to access Internet through DSL link.DSLBlinkingSlowly: The DSL connection is ready. Quickly: The connection is training. OnThe Web Content Filter is active. (It is enabled from Firewall >> General Setup ). WCFOffWCF is disabled.OnThe VPN tunnel is active. OffVPN services are disabledVPN BlinkingTraffic is passing through VPN tunnel. OnThe DMZ function is enabled. OffThe DMZ function is disabled. DMZ BlinkingThe data is transmitting.LED on ConnectorOnThe port is connected. Off The port is disconnected. Left LED BlinkingThe data is transmitting.On The port is connected with 1000Mbps. WAN2 / P6Right LED Off The port is connected with 10/100Mbps. OnThe port is connected. Off The port is disconnected. Left LED BlinkingThe data is transmitting.On The port is connected with 1000Mbps. LAN P1~P5Right LED OffThe port is connected with 10/100MbpsThe port “WAN2 / P6” is switchable. It can be used for LAN connection or WAN connection according to the settings configured in WUI.Switch on Rear SideInterface DescriptionFactory Reset Restore the default settings. Usage: Turn on the router(ACT LED is blinking). Press the hole and keep for more than5 seconds. When you see the ACT LED begins to blinkrapidly than usual, release the button. Then the router willrestart with the factory default configuration.USB1~2 Connecter for a USB device (for 3G/4G USB Modem orprinter or thermometer).WAN2 / P6 Connecter for local network devices or modem foraccessing Internet.LAN P1-P5 Connecters for local network devices.DSL Connecter for accessing the Internet.PWR Connecter for a power adapter.Switch.ON/OFF Power3.H a r d w a r e I n s t a l l a t i o nThis section will guide you to install the router through hardware connection and configure the router’s settings through web browser.Before starting to configure the router, you have to connect your devicescorrectly.3.1N e t w o r k C o n n e c t i o n1.Connect the DSL interface to the land line jack with a DSL line cable, orConnect the cable Modem/DSL Modem/Media Converter to the WAN port ofrouter with Ethernet cable (RJ-45).2.Connect one end of an Ethernet cable (RJ-45) to one of the LAN ports of therouter and the other end of the cable (RJ-45) into the Ethernet port on yourcomputer.3.Connect one end of the power adapter to the router’s power port on therear panel, and the other side into a wall outlet.4.Power on the device by pressing down the power switch on the rear panel.5.The system starts to initiate. After completing the system test, the ACT LEDwill light up and start blinking. (For the detailed information of LED status,please refer to section 2. Panel Explanation)3.2 W a l l -M o u n t e d I n s t a l l a t i o nVigor router has keyhole type mounting slots on the underside.1. Drill two holes on the wall. The distance between the holes shall be 168mm.2.Fit screws into the wall using the appropriate type of wall plug.NoteThe recommended drill diameter shall be 6.5mm (1/4”).3. When you finished about procedure, the router has been mounted on thewall firmly.4.S o f t w a r e C o n f i g u r a t i o nTo access Internet, please finish basic configuration after completing thehardware installation.4.1Q u i c k S t a r t W i z a r d f o r N e t w o r k C o n n e c t i o nThe Quick Start Wizard is designed for you to easily set up your router forInternet access. You can directly access the Quick Start Wizard via WebConfigurator. Make sure your PC connects to the router correctly.Note You may either simply set up your computer to get IP dynamically from the router or set up the IP address of the computer to be thesame subnet as the default IP address of Vigor router192.168.1.1. For the detailed information, please refer to -Trouble Shooting of the user’s guide.Open a web browser on your PC and type http://192.168.1.1. A pop-up window will open to ask for username and password. Please type “admin/admin” as the.Username/Password and click LoginNote If you fail to access to the web configuration, please go to“Trouble Shooting” on User’s Guide for detecting and solvingyour problem.Now, the Main Screen will pop up. Click Wizards>>Quick Start Wizard.If your router can be under an environment with high speed NAT, the configuration provide here can help you to deploy and use the router quickly. The first screen of Quick Start Wizard is entering login password. After typing the password, please click Next.On the next page as shown below, please select the WAN interface that you use. If DSL interface is used, please choose WAN1; if Ethernet interface is used, please choose WAN2; if 3G USB modem is used, please choose WAN5 or WAN6. Then click Next for next step. WAN1, WAN2, WAN5 and WAN6 will bring up different configuration page. Here, we take WAN1 (ADSL/VDSL2) as an example.Click Next to go to the following page. You have to select the appropriate Internet access type according to the information from your ISP. For example, you should select PPPoE mode if the ISP provides you PPPoE interface. In addition, the field of For ADSL Only will be available only when ADSL is detected. Then click Next for next step.P P P o E/P P P o A1.Choose WAN1 as WAN Interface and click the Next button; you will get thefollowing page.2.After finished the above settings, simply click Next.3.Please manually enter the Username/Password provided by your ISP. Thenclick Next for viewing summary of such connection.4.Click Finish. A page of Quick Start Wizard Setup OK will appear.Then,the system status of this protocol will be shown.5.Now, you can enjoy surfing on the Internet.M P o A/S t a t i c o r D y n a m i c I P1.Choose WAN1 as WAN Interface and click the Next button; you will get thefollowing page.2.Please type in the IP address/mask/gateway information originally providedby your ISP. Then click Next for viewing summary of such connection.3.Click Finish. A page of Quick Start Wizard Setup OK will appear.Then,the system status of this protocol will be shown.4.Now, you can enjoy surfing on the Internet.5.C u s t o m e r S e r v i c eIf the router cannot work correctly after trying many efforts, please contact your dealer for further help right away. For any questions, please feel free to send ***************************.B e a R e g i s t e r e d O w n e rWeb registration is preferred. You can register your Vigor router viahttps://.F i r m w a r e&T o o l s U p d a t e sDue to the continuous evolution of DrayTek technology, all routers will beregularly upgraded. Please consult the DrayTek web site for more information on newest firmware, tools and documents.https://。
苏州思朋CCIE K5_v1版本完整解法

BDPU Filter configured on all uplinks in one of the switches ( Remove the bpdufilter on those uplink ports - no spanning-tree bpdufilter enable ) 苏州 CCIE
新R-LINK 2软件升级安装指南说明书

New R-LINK 2S oftware upgrade installation guideThis upgrade is only compatible with Renault vehicles equipped with R-LINK 2 multimedia systems where the VIN number has been verified on the multimedia website. Use the software only on this specific Renault. Do not install it on another car.Before you start: Get your VIN number readyYou can find your VIN number in your car or on your V5 car registration document. This information is mandatory to check if the software upgrade is available for your Renault vehicle. Please check the number. It must begin with VF and include 17 digits without any letters "i" nor "o".Before you start: Find a USB stick in FAT 32 format (8GB-32 GB)To check if your USB stick is in FAT 32 format access its properties (example: right click on PC/ properties).Make sure that your internet connection is active during the whole process.Please do not interrupt the download whilst it is in progress.Step 1: Download the softwareExample screen. The version’s number is indicated at the time of the download.Step 2: Unzip the fileUnzip and “Extract” the file you have downloaded. You can use 7-zip (/) to do this. Then copy the R-LINK folder onto the USB key at the root. Keep the R-LINK folder exactly as it is. Do not rename the folder nor install the software in another location on the USB stick.Step 3: View the downloaded file on your USB stickThe folder may contain several files. You can open the folder to check the software has been correctly copied.Step 4: Install the software on your R-LINK 2 1/2Switch on the engine and your R-LINK 2 system. Plug in your USB stick. The software on your USB stick will be automatically detected after 3 minutes. Please keep the engine running while the software installs. It can take up to 10 minutes.R-LINK 2 will automaticallycheck the file integrity. Thenthe following screens will bedisplayed. Choose “Yes”for all screens to begin theinstallation process.The screen will be black for afew minutes during theinstallation process.The R-LINK 2 system mayrestart several times duringthe procedure. Rear cameraand parking aid sensor willneither be available. Do notunplug the USB. Amessage on the R-LINK 2will confirm that theinstallation is successful.Step 4: Install the software on your R-LINK 2 2/2You can now remove the USB stick.Note that the installation of the new R-LINK 2 software will reset your navigationfavorites and navigation history.Final CheckYou can double check if the software hasInstalled correctly Menu->System->SystemInformation. Example screen. The version’s numberis indicated at the time of the downloadDo not forget to check if your R-LINK 2 system has the connectivity activated for LIVE Info TrafficPlease go to main menu on your R-LINK 2 and check if the connect button isshowing. If connect button showing, follow the instructions below.Press the “Connect” button. Accept thedifferent conditions to allow connectivity(you can also fill in your email address(optional).The activation may take up to 72 hours.。
Quake II RTX Getting Started说明书

QUAKE II RTX Getting Started tQUAKE II RTX - Getting StartedIntroductionThis guide provides further information about the real-time ray tracing enhancements, and other advanced features, that NVIDIA has implemented to create Q uake II RTX. Most noticeably, we have introduced high-fidelity, real-time path-traced reflections, ambient occlusion, lighting, and shadows, which is a world’s first for any game. For an explanation, c heck out this video:https:///watch?v=p7RniXWvYhYQuake II RTX includes the first 3 levels of the game with our full suite of enhancements. P urchase the full game to get access to all the levels, as well as multiplayer with path-tracing.System RecommendationThe following system configuration, or better, is recommended:●GPU:NVIDIA GeForce RTX 2060 or higher●OS:Windows 10 64 bit or Ubuntu 18.04 LTS 64-bit●CPU:Intel Core i3-3220, or AMD equivalent●RAM:8 GB RAMGetting Started1.)Ensure you have the recommended system specifications2.)Have the latest G ame Ready Driver installed.3.)Install Q uake II RTX.a.)Please see installer instructions below4.)Launch Q uake II RTX via desktop shortcut.5.)Set Recommended Settingsa.)Go to Video -> Set desired Global Illumination Setting (R ecommended: Medium)b.)Set desired resolution (R ecommended: 1080p)c.)Go back and click Game -> Choose desired difficulty.Installer Instructions1.)Windows (Demo)a.)Launch the Q uake II RTX installer executable, or download and run from S teamb.)Make sure that "Quake II Shareware Demo" and "Desktop Shortcut" are both selectedc.)The Installer will install the RTX Demo and leave a shortcut on your desktop.2.)Linux (Demo - Debian / Ubuntu Package)a.)Install the Quake II RTX.deb packageb.)The Installer will install the RTX Demo and leave an icon in your applications menu.3.)Linux (Demo - Steam)a.)Download and run Quake II RTX from SteamEnable Ray Tracing for the Full Game1)Purchase the full game2)Launch the Q uake II RTX installer executable, or download and run from S team3)The installer will detect the Quake II executable location.4)The installer will implement RTX with the full game and leave a shortcut on your desktop.Playing the DemoQuake II RTX is a remaster of the classic game.Quake II R TX i s fully ray-traced (using path tracing), delivering highly realistic lighting, shadows, reflections, global illumination and more.●Start game○Game > Easy●Movement & Weapons○Left Mouse Button = Fire/Attack/Action○W = Forward○ A = Strafe Left○S = Backward○ D = Strafe Right○SPACE = Jump○CTRL = (Holding) = Crouch○SHIFT = Walk (default is run)○ F = Flare gun○G = Grenades●Give weapons and ammo○Press ~ (tilda) button to open the console○/give all = All weapons, ammo, items, keys○/dmflags 8192 = Unlimited Ammo●Show RTX ON/OFF○Show RTX OFF■RTX OFF: V ideo > Renderer > OpenGL■RTX ON: Video > Renderer > rtxMultiplayer SupportQuake II RTX comes with multiplayer support.There are multiple options to play this game in multiplayer mode:1.Join an existing public or private Quake II server online.2.Start a server directly from the game.3.Start a dedicated server and join it.Joining a serverThere are two ways to join an existing server:through the server catalog on ,and manually. The catalog is available through the Multiplayer menu:To join an unlisted server, open the console and type “connect <address>”.If the server is password protected,open the console and type“password<password>”before joining the server.Note that when playing on non-Q2RTX servers, you may observe some compatibility issues: -Rockets and other items may disappear in certain pools of water,which were opaque in the original Quake II;-Flare gun will not be available;-Gameplay mods or custom maps may be incompatible with Q2RTX.Starting a server from the gameIn the multiplayer menu, select “start server”. The following dialog will appear:Starting a dedicated serverQuake II RTX ships with a separate dedicated server executable, “q2rtxded.exe” (on Windows). This is a lightweight version of the game that can only act as a server, but doesn’t allow you to play it directly and doesn’t have any graphics.Simply launching the dedicated server will make it start a deathmatch session on the first available map, which is “base1”. You can change the map and other game settings using the server console, or you can put those commands into a config file and execute that file on server startup using the command line. For example, you can put something like this in a file called “server.cfg” in the baseq2 directory:set password <password>set rcon_password <another_password>set deathmatch 1set coop 0set sv_maplist q2dm1 q2dm2 q2dm3 q2dm4set timelimit 20set fraglimit 20map q2dm1Then start the server using command line:q2rtxded.exe +exec server.cfgServer configurationMany of the console variables useful for dedicated server administration are documented in the Q2PRO server manual- since Quake II RTX is derived from Q2PRO, these variables still apply. We have added some more variables to control RTX specific features:sv_flaregun: controls whether players spawn with the flare gun and ammo for it. 0 means no flare gun, 1 means spawn with the flare gun but no ammo, 2 means spawn with the flare gun and 5 grenades (because the flare gun uses grenades).sv_restrict_rtx: if set to 1, makes the server available only to clients playing Quake II RTX; other clients like the regular Quake II or Q2PRO will be rejected.sv_savedir: path to the directory w ithin baseq2where the server will save game state in cooperative play mode. If multiple dedicated cooperative servers are started from the same installation directory, they should use different directories to save game state.The s v_flaregun and s v_restrict_rtx settings have been added mostly for compatibility reasons. Quake II RTX uses the regular Quake II network protocol (version 36 from Q2PRO), but the flare gun is an extension to the protocol. If both Q2RTX and other clients participate in a multiplayer game, and theQ2RTX user fires a flare gun, other clients that see the flare will disconnect because they do not understand what that means. So it is advised to either disable the flare gun on MP servers, or to make the servers only available to Q2RTX players.© 1997 id Software LLC, a ZeniMax Media company. QUAKE, id, id Software, id Tech and related logos are registered trademarks or trademarks of id Software LLC in the U.S. and/or other countries. Bethesda, Bethesda Softworks, ZeniMax and related logos are registered trademarks or trademarks of ZeniMax Media Inc. in the U.S. and/or other countries. All Rights Reserved.This product is based on or incorporates materials from the sources listed below (third party IP). Such licenses and notices are provided for informational purposes only.Quake II: Copyright (C) 1997-2001 Id Software, Inc. Licensed under the terms of the GPLv2.Q2VKPT: Copyright © 2018 Christoph Schied. Licensed under the terms of the GPLv2.Quake2MaX "A Modscape Production":TexturesfromQuake2MaxusedinQuake2XP.Copyright©*******************************************.SubjecttoCreative Commons license version 1.0. Roughness and specular channels were adjusted in texture maps to work with the Q uake II RTX engine.Q2XP Mod Pack: Used with permission from Arthur Galaktionov.Q2Pro: Copyright © 2003-2011 Andrey Nazarov. Licensed under the terms of the GPLv2.。
PmodBT2 蓝牙接口模块说明书

1300 Henley Court Pullman, WA 99163 509.334.6306PmodBT2™ Reference ManualRevised November 18, 2019This manual applies to the PmodBT2 rev. AOverviewThe PmodBT2 is a powerful peripheral module employing the Roving Networks® RN-42 to create a fully integrated Bluetooth interface.1 Functional DescriptionThe PmodBT2 uses a standard 12-pin port and communicates via UART. There is a secondary SPI header on the board for updating the RN-42 firmware if needed.1.1 Jumper SettingsThe PmodBT2 has several modes available to the user via jumper settings. JP1 through JP4 provide various modes of operation as indicated in Table 1 below. Each jumper is active when shorted. JP1 restores the device to factor default settings after three transitions of the jumper setting (short-to-open or open-to-short). After the third transition, the device returns to factor default except for the Bluetooth name. The other three jumpers, JP2-JP4, only sample in the first 500 ms of operation to allow the pins that they tie to on the RN-42 module to serve a separate purpose later in the modules operation. JP2 enables pairing with a special device class defined by the user in software. This may be used so that the PmodBT2 operates as a substitute for an RS232 cable. JP3 enables auto connect to a stored address defined by the user. Finally, JP4 chooses whether to operate at the stored baudThe PmodBT2. • Bluetooth 2.1/2.0/1.2/1.0 compatible • Add wireless capability with this low power, Class 2 Bluetooth radio • Supports HID profile for making accessories such as pointing devices, etc. • Secure communications, 128-bit encryption • Supports Bluetooth data link to iPhone/iPad/iPod Touch • Six different modes • Small PCB size for flexible designs 1.5“ × 0.8” (3.8 cm × 2.0 cm) • 12-pin Pmod port with UART interfaceFeatures include:rate (115.2kbps default) or a baud rate of 9600 regardless of the software selected rate when shorted. For more detailed information on jumper settings and functionality, refer to the RN-42 user manual.Jumper DescriptionJP1 (PIO4) Factory DefaultJP2 (PIO3) Auto Discovery/PairingJP3 (PIO6) Auto ConnectJP4 (PIO7) Baud Rate Setting (9600)Table 1. Set jumper description.Figure 1. PmodBT2 block diagram.1.2 UART InterfaceBy default, the UART interface uses a baud rate of 115.2 kbps, 8 data bits, no parity, and a single stop bit. The startup baud rate may be customized to predefined rates or set to a specific user customized baud rate. Predefined baud rates range from 1200 to 921k.The reset pin (RST) on J1 is active low. If the RST pin is toggled, the device will undergo a hard reset. This hard reset performs similarly to a power cycling of the device. The second interface besides the standard UART signals is the STATUS pin also on J1The STATUS pin directly reflects the connection status of the device. STATUS is driven high by the device when connected and is driven low otherwise.For more information on the devices UART interface and RST and STATUS pins refer to the RN-42 user manual on the Roving Networks website.1.3 Command ModeIn order to enter the command mode, the PmodBT2 must receive "$$$" to which it will respond "CMD". When in command mode, the module will respond to a large number of commands allowing the user to customizing the module for specific applications. In order to exit command mode, send "---<cr>" (three minus signs in a row and where <cr> stands for the carriage return character) to which the device will respond "END". Remote configuration, or configuration over a Bluetooth connection, is possible through the command mode but has several restrictions. The configure time, which defaults to 60 sec, defines the time window in which the PmodBT2 may be configured remotely. Outside of this time, the PmodBT2 will not respond to any remote commands. It is important to note that any of the "set" commands available for the PmodBT2 must be followed by a power cycle to take effect in any design.Connector J1 – UART CommunicationsPin Signal Description1 RTS Ready to Send2 RX Receive3 TX Transmit4 CTS Clear to Send5 GND Power Supply Ground6 VCC Power Supply (3.3V)7 STATUS Connection Status8 ~RST Reset9 NC Not Connected10 NC Not Connected11 GND Power Supply Ground12 VCC Power Supply (3.3V)Connector J2 – SPI Connector (Firmware Update Only)1 MISO Master in/ Slave out2 MOSI Master out/ Slave in3 SCK Serial Clock4 ~CS Chip Select5 VCC Power Supply (3.3V)6 GND Power Supply GroundTable 2. Connector descriptions.The various modes of operation are accessed by using the "SM,<5,4,3,2,1,0>" command while in command mode. The PmodBT2 can be put into one of six available modes of operation. The modes in order, 0 to 5, are: slave, master, trigger master, auto-connect, auto-connect DTR, and auto-connect ANY. For more detailed information onthe different modes of operation, refer to the RN-42 user manual. For the full list of device commands, how to use remote configuration, and more detailed information on the different modes of operation, see the RN-42 data.。
NVIDIA Spectrum SN4000系列交换机数据手册说明书

NVIDIA® Spectrum™ SN4000 series switches are the 4th generation of Spectrumswitches, purpose-built for leaf/spine/super-spine datacenter applications. Allowing maximum flexibility, SN4000 series provides port speeds spanning from 1GbE to 400GbE, with a port density that enables full rack connectivity to any server at any speed. In addition, the uplink ports allow a variety of blocking ratios to suit any application requirement.The SN4000 series is ideal for building wire-speed and cloud-scale layer-2 and layer-3 networks. The SN4000 platforms deliver high performance, consistent low latency along with support for advanced software defined networking features, making it the ideal choice for web scale IT, cloud, hyperconverged storage and data analytics applications. Network Disaggregation: NVIDIA Open EthernetOpen Ethernet breaks the paradigm of traditional switch systems, eliminating vendor lock-in. Instead of forcing network operators to use the specific software that is provided by the switch vendor, Open Ethernet offers the flexibility to use a choiceof operating systems on top of Ethernet switches, thereby re-gaining control of the network, and optimizing utilization, efficiency and overall return on investment. Open Ethernet adopts the same principles as standard open solutions for servers and storage, and applies them to the world of networking infrastructure. It encourages an ecosystem of open source, standard network solutions.These solutions can then be easily deployed into the modern data center across network equipment that eases management and ensures full interoperability. With a range of system form factors, and a rich software ecosystem, NVIDIA SN4000 series allows you to pick and choose the right components for your data center.NVIDIA SN4000 SeriesSN4000 series platforms are based on the high-performance Spectrum-3 ASIC with a bidirectional switching capacity of 12.8Tbps. SN4000 platforms are available in a range of configurations, each delivering high performance combined with feature-rich layer2 and layer3 forwarding, ideally suited for both top-of-rack leaf and fixed configuration spines. SN4000 series provides full wire speed, cut through-mode latency, on-chip fully-shared 64MB packet buffering, and flexible port use in addition to advanced capabilities. Combining a wide range of innovations in the area of programmability, telemetry, and tunneling with industry leading performance, NVIDIA SN4000 series is capable of addressing today’s data center’s complex networking requirements.VISIBILITY>What Just Happened?® (WJH) telemetry dramatically reduces mean time to issue resolution by providing answers to: When, What, Who, Where and Why>Hardware-accelerated histograms track and summarize queue depthsat sub-microsecond granularity>Inband network telemetry(INT)-ready hardware>Streaming Telemetry>512K on-chip flow counters PERFORMANCE>Fully shared packet buffer provides a fair, predictable and high bandwidth data path >Consistent and low cut-through latency >Intelligent hardware-accelerated data movement, congestion management and load balancing for RoCE and Machine learning applications that leverage GPUDirect®>Best-in-class VXLAN scale-10X more tunnels and tunnel endpoints>512K shared forwarding entriesflexibly shared across ACL, LPM routes, host routes, MAC, ECMPand tunnel applications>Up to 1M IPv4 route entriesAGILITY>Comprehensive Layer-2, Layer-3and RoCE>Advanced network virtualization with high performance single pass VXLAN routing and IPv6 segment routing>Cloud Scale NAT – 100K+ sessions>Programmable pipeline that can programmatically parse, processand edit packets>Deep Packet Inspection – 512B deepNVIDIA SpECTRUMSN4000 SERIES SWITCHES for accelerated data centers DATASHEETSN4700The SN4700 spine/super-spine offers 32 ports of 400GbE in a compact 1U form factor . It enables connectivity to endpoints at varying speeds and carries a throughput of 12.8 Tb/s, with a landmark 8.4Bpps processing capacity. As an ideal spine solution, the SN4700 allows maximum flexibility, with port speeds spanning from 1 to 400GbE per port.SN4600SN4600 is a 2U 64-port 200GbE spine that can also be used as a high density leaf, fully splittable to up to 128X 10/25/50GbE ports when used with splitter cables. SN4600 allows for maximum flexibility, with ports spanning from 1 to 200GbE and port density that enables full rack connectivity to any server at any speed, and a variety of blocking ratios.SN4600CSN4600C is a 64-port 100GbE switch system that is ideal for spine/super-spine applications. With a landmark 8.4Bpps processing capacity and 6.4Tb/s throughput in a dense 2U form factor, SN4600C offers diverse connectivity in combinations of 10/25/40/50/100GbE. The SN4600C is well-suited to answer the challenging needs of large virtualized data centers and cloud environments.SN4410SN4410 is a 48-port 100GbE (24x QSFP28-DD) + 8x 400GbE (8x QSFP56-DD) leaf/spine switch system. The SN4410 is ideal for interconnecting 100GbE servers and networks to 400GbE infrastructure. With a landmark 8.4Bpps processing capacity and 8.0Tb/s throughput in a dense 1U form factor, SN4410 offers diverse connectivity in combinations of 10/25/40/50/100/200/400GbE.SN4800SN4800 is a modular switch platform ideally-suited for large virtualized data centers and cloud environments, allowing flexibility and customization with up to 8 line cards and a single management card. Demonstrating a landmark 8.4B pps processing capacity and up to 12.8Tb/s throughput in a versatile 4U form factor . The SN4800 offers 10/25/40/50/100GbE connectivity with a 16 x 100GbE (QSFP28) line card.Linux Switch†††††* Future Optionplatform Software OptionsSN4000 series platforms are available out of the factory in three different flavors:>Pre-installed with NVIDIA Cumulus Linux, a revolutionary operating system, taking the Linux user experience from servers to switches and providing a rich routing functionality for large scale applications.>Pre-installed with NVIDIA Onyx™, a home-grown operating system utilizingcommon networking user experiences and an industry standard CLI.>Bare metal including ONIE image, installable with any ONIE-mounted OS.ONIE-based platforms utilize the advantages of Open Networking and theSpectrum-3 ASIC capabilities.High AvailabilitySN4000 series switches are designed with the following software and hardware features for high availability:>1+1 hot-swappable power supplies and N+1 hot-swappable fans>Color-coded PSUs and fans>Up to 128X 100/50/25/10/1GbE, 64X 200GbE or 32X 400GbE>Multi-chassis LAG for active/active L2 multipathing>128-way ECMP routing for load balancing and redundancySN4000 Series: A Rich Software EcosystemNVIDIA Cumulus-LinuxNVIDIA Cumulus Linux is a powerful open network operating system enabling advanced automation, customization and scalability using web-scale principles like the world’s largest data centers. It accelerates networking functions and provides choice from an extensive list of supported switch models including Spectrum based switches. Cumulus Linux was built for automation, scalability and flexibility, allowing you to build data center and campus networks that ideally suits your business needs. Cumulus Linux is the only open network OS that allows you to build affordable and efficient network operations like the world’s largest data center operators, unlocking web-scale networking for businesses of all sizes.SONiCSONiC was designed for cloud networking scenarios, where simplicity and managing at scale are the highest priority. NVIDIA fully supports the Pure Open Source SONiC from the SONiC community site on all of the SN4000 series switch platforms. With advanced monitoring and diagnostic capabilities, SONiC is a perfect fit for the NVIDIA SN4000 series. Among other innovations, SONiC on SN4000 series enables fine-grained failure recovery and in-service upgrades (ISSU), with zero downtime.Linux Switch and DentLinux Switch enables users to natively install and use any standard Linux distributionas the switch operating system, such as DENT, a Linux-based networking OS stackthat is suitable for campus and remote networking. Linux Switch is based on a Linux kernel driver model for Ethernet switches (Switchdev). It breaks the dependency of using vendor-specific, closed-source software development kits. The open-source Linux driver is developed and maintained in the Linux kernel, replacing proprietary APIs with standard Linux kernel interfaces to control the switch hardware. This allows off-the-shelf Linux-based networking applications to operate on Spectrum-based switches for L2 switching and L3 routing, including open source routing protocol stacks, such as FRR (Quagga), Bird and XORP, OpenFlow applications, or user-specific implementations.NVIDIA OnyxOnyx is a high performance switch operating system, with a classic CLI interface. Whether building a robust storage fabric, cloud, financial or media and entertainment fabric, customers can leverage the flexibility of Onyx to tailor their network platform to their environment. With built-in workflow automation, monitoring and visibility tools, enhanced high availability mechanisms, and more, Onyx simplifies network processes and workflows, increasing efficiencies and reducing operating expenses and time-to-service. Onyx leverages capabilities of the SN4000 series to provide greater magnitudes of scale, state-of-the-art telemetry, enhanced QoS, exceptional programmability that enables a flexible pipeline supporting both new and legacy protocols, a larger fully-shared buffer, and more**.NVIDIA NetQNVIDIA NetQ is a highly-scalable, modern, network operations tool set that provides visibility, troubleshooting and lifecycle management of your open networks inreal time. NetQ delivers actionable insights and operational intelligence about the health of your data center and campus networks — from the container or host, all the way to the switch and port, enabling a NetDevOps approach. NetQ is the leading network operations tool that utilizes telemetry for deep troubleshooting, visibility and automated workflows from a single GUI interface, reducing maintenance and network downtimes. With the addition of full lifecycle management functionality, NetQ now combines the ability to easily upgrade, configure and deploy network elements with a full suite of operations capabilities, such as visibility, troubleshooting, validation, trace and comparative look-back functionality.ONIEThe open network install environment (ONIE) is an open compute project open source initiative driven by a community to define an open “install environment” for bare metal network switches, such as the NVIDIA SN4000 series. ONIE enables a bare metal network switch ecosystem where end users have a choice of different network operating systems.Docker ContainersNVIDIA fully supports the running of third party containerized applications on the switch system itself. The third party application has complete access to the bare-metal switch via its direct access to the SDK. The switch has tight controls over the amount of memory and CPU cycles each container is allowed to use, along with fine grained monitoring of those resources.Docker Containers SupportNVIDIA Spectrum-3: Build your cloud without compromise Groundbreaking PerformancePacket buffer architecture has a major impact on overall switch performance.The Spectrum-3 packet buffer is monolithic and fully shared across all ports, supporting cut-through line rate traffic from all ports, without compromising scale or features. With its fast packet buffer, Spectrum-3 is able to provide a high-performance fair and bottleneck-free data path for mission-critical applications.Pervasive VisibilitySpectrum-3 provides deep and contextual network visibility, which enables network operators to proactively manage issues and reduce mean time to recovery/innocence. The WJH feature leverages the underlying silicon and software capability to provide granular and event-triggered information about infrastructure issues. In addition, the rich telemetry information from Spectrum-3 is readily available via open APIs that are integratable with third party software tools and workflow engines. Unprecedented AgilityFor modern data center infrastructure to be software defined and agile, both its compute and network building blocks need to be agile. Spectrum-3 features a unique feature rich and efficient packet processing pipeline that offers rich data center network virtualization features without compromising on performance or scale. Spectrum-3 has a programmable pipeline and a deep packet parser/editor that can process payloads up to the first 512B. Spectrum-3 supports single pass VXLAN routing as well as bridging. Additionally, Spectrum-3 supports advanced virtualization features such as IPv6 segment routing, and Network Address Translation (NAT). Massive ScaleThe number of endpoints in the data center is increasing exponentially. With the current shift from virtual machine-based architectures to container-based architectures, the high-scale forwarding tables required by modern data centers and mega-clouds increase by up to an order of magnitude or more. To answer these needs for scalability and flexibility, Spectrum-3 uses intelligent algorithms and efficient resource sharing, and supports unprecedented forwarding table, counters and policy scale.>Fine-grained resource allocation to fit all specific needs, allowing up to 512Kentries to be dynamically shared across MAC, ARP, IPv4/IPv6 routes, ACLs,ECMP, and Tunnels.>An innovative algorithmic TCAM optimized for data centers and cloudenvironments, which can scale the number of rules to up to half a million rules.End-to-End SolutionThe SN4000 series is part of the NVIDIA complete end-to-end solution which provides 1GbE through 400GbE interconnectivity within the data center. Other devices in this solution include ConnectX®-based network interface cards and LinkX® copper or fiber cabling.specificationsSupported Transceivers and CablesOrdering informationComplianceAccessories and Replacement partsNVIDIA SN4000 series switches come with a one-year limited hardware return-and-repair warranty, with a 14 business day turnaround after the unit is received. For more information, please visit the NVIDIA Technical Support User Guide .Additional InformationSupport services including next business day and 4-hour technician dispatch are available. For more information, please visit the NVIDIA Technical Support User Guide . NVIDIA offers installation, configuration, troubleshooting and monitoring services, available on-site or remotely delivered. For more information, please visit the NVIDIA Global Services website .Ordering InformationFor ordering information, please contact *************。
DS-K1T805系列访问控制终端快速启动指南说明书
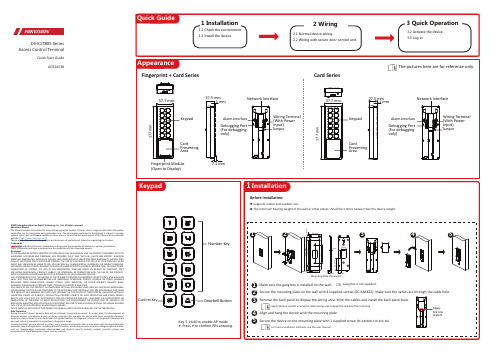
DS-K1T805SeriesAccess Control TerminalQuick Start GuideUD32453B©2023Hangzhou Hikvision Digital Technology Co.,Ltd.All rights reserved.About this ManualThe Manual includes instruc�ons for using and managing the Product.Pictures,charts,images and all other informa�on hereina�er are for descrip�on and explana�on only.The informa�on contained in the Manual is subject to change, without no�ce,due to firmware updates or other reasons.Please find the latest version of this Manual at the Hikvision website(h�ps:///).Please use this Manual with the guidance and assistance of professionals trained in suppor�ng the Product. Trademarksand other Hikvision’s trademarks and logos are the proper�es of Hikvision in various jurisdic�ons.Other trademarks and logos men�oned are the proper�es of their respec�ve owners.DisclaimerTO THE MAXIMUM EXTENT PERMITTED BY APPLICABLE LAW,THIS MANUAL AND THE PRODUCT DESCRIBED,WITH ITS HARDWARE,SOFTWARE AND FIRMWARE,ARE PROVIDED“AS IS”AND“WITH ALL FAULTS AND ERRORS”.HIKVISION MAKES NO WARRANTIES,EXPRESS OR IMPLIED,INCLUDING WITHOUT LIMITATION,MERCHANTABILITY,SATISFACTORY QUALITY,OR FITNESS FOR A PARTICULAR PURPOSE.THE USE OF THE PRODUCT BY YOU IS AT YOUR OWN RISK.IN NO EVENT WILL HIKVISION BE LIABLE TO YOU FOR ANY SPECIAL,CONSEQUENTIAL,INCIDENTAL,OR INDIRECT DAMAGES, INCLUDING,AMONG OTHERS,DAMAGES FOR LOSS OF BUSINESS PROFITS,BUSINESS INTERRUPTION,OR LOSS OF DATA, CORRUPTION OF SYSTEMS,OR LOSS OF DOCUMENTATION,WHETHER BASED ON BREACH OF CONTRACT,TORT (INCLUDING NEGLIGENCE),PRODUCT LIABILITY,OR OTHERWISE,IN CONNECTION WITH THE USE OF THE PRODUCT, EVEN IF HIKVISION HAS BEEN ADVISED OF THE POSSIBILITY OF SUCH DAMAGES OR LOSS.YOU ACKNOWLEDGE THAT THE NATURE OF THE INTERNET PROVIDES FOR INHERENT SECURITY RISKS,AND HIKVISION SHALL NOT TAKE ANY RESPONSIBILITIES FOR ABNORMAL OPERATION,PRIVACY LEAKAGE OR OTHER DAMAGES RESULTING FROM CYBER-ATTACK,HACKER ATTACK,VIRUS INFECTION,OR OTHER INTERNET SECURITY RISKS; HOWEVER,HIKVISION WILL PROVIDE TIMELY TECHNICAL SUPPORT IF REQUIRED.YOU AGREE TO USE THIS PRODUCT IN COMPLIANCE WITH ALL APPLICABLE LAWS,AND YOU ARE SOLELY RESPONSIBLE FOR ENSURING THAT YOUR USE CONFORMS TO THE APPLICABLE LAW.ESPECIALLY,YOU ARE RESPONSIBLE,FOR USING THIS PRODUCT IN A MANNER THAT DOES NOT INFRINGE ON THE RIGHTS OF THIRD PARTIES,INCLUDING WITHOUT LIMITATION,RIGHTS OF PUBLICITY,INTELLECTUAL PROPERTY RIGHTS,OR DATA PROTECTION AND OTHER PRIVACY RIGHTS.YOU SHALL NOT USE THIS PRODUCT FOR ANY PROHIBITED END-USES,INCLUDING THE DEVELOPMENT OR PRODUCTION OF WEAPONS OF MASS DESTRUCTION,THE DEVELOPMENT OR PRODUCTION OF CHEMICAL OR BIOLOGICAL WEAPONS,ANY ACTIVITIES IN THE CONTEXT RELATED TO ANY NUCLEAR EXPLOSIVE OR UNSAFE NUCLEAR FUEL-CYCLE,OR IN SUPPORT OF HUMAN RIGHTS ABUSES.IN THE EVENT OF ANY CONFLICTS BETWEEN THIS MANUAL AND THE APPLICABLE LAW,THE LATTER PREVAILS.Data Protec�onDuring the use of device,personal data will be collected,stored and processed.To protect data,the development of Hikvision devices incorporates privacy by design principles.For example,for device with facial recogni�on features, biometrics data is stored in your device with encryp�on method;for fingerprint device,only fingerprint template will be saved,which is impossible to reconstruct a fingerprint image.As data controller,you are advised to collect,store,process and transfer data in accordance with the applicable data protec�on laws and regula�ons,including without limita�on,conduc�ng security controls to safeguard personal data, such as,implemen�ng reasonable administra�ve and physical security controls,conduct periodic reviews and assessments of the effec�veness of your security controls.Align andsupplied2006/66/EC This with standards 2014/30/EU,WarningIn the use of regulationsdirect The If enter The If Make Create Click Click If you should Click 1.Connect Make sure 2.Open address 3.Enter Make sure 2.Enter 3.Click Authentication Card:Present authentication LoginWhen ground。
赛米控丹佛斯电子 Board_93_GB_SKYPER_42_R 数据表

®Adaptor boardIGBT Driver CoreBoard 93 GB SKYPER 42 R Preliminary Data Features•Two output channels •Gold nickel finish •Failure managementTypical Applications*•Adaptor board for SKYPER 42 IGBT drivers in bridge circuits for industrial applications •PCB with gold plating •DC bus up to 1200VFootnotesIsolation test voltage with external high voltage diodeThe isolation test is not performed as a series test at SEMIKRONThe driver power can be expanded to 50µC with external boost capacitorsIsolation coordination in compliance with EN50178 PD2Operating temperature is real ambient temperature around the driver core Degree of protection: IP00This is an electrostatic discharge sensitive device (ESDS), international standard IEC 60747-1, Chapter IX* The specifications of our components may not be considered as an assurance of component characteristics. Components have to be tested for the respective application. Adjustments may be necessary. The use of SEMIKRON products in life support appliances and systems is subject to prior specification and written approval by SEMIKRON. We therefore strongly recommend prior consultation of our staff.Absolute Maximum Ratings SymbolConditionsValuesUnitV s Supply voltage primary 16V Iout PEAK Output peak current 30A Iout AVmax Output average current 150mA f max Max. switching frequency100kHz V CECollector emitter voltage sense across the IGBT1700V V isol IO Isolation test voltage input - output (AC, rms, 2s)4000V V isolPD Partial discharge extinction voltage, rms, Q PD ≤ 10pC1500V V isol12Isolation test voltage output 1 - output 2 (AC, rms, 2s)1500V R Gon min Minimum rating for external R Gon 0.8ΩR Goff min Minimum rating for external R Goff 0.8ΩT op Operating temperature -40...85°C T stgStorage temperature-40 (85)°CCharacteristics SymbolConditionsmin.typ.max.UnitV s Supply voltage primary side 14.41515.6V V i Input signal voltage on / off 15 / 0V V IT+Input treshold voltage HIGH 12.3V V IT-Input threshold voltage (LOW) 4.6V V G(on)Turn on output voltage 15V V G(off)Turn off output voltage-8V t d(on)IO Input-output turn-on propagation time 1.1µs t d(off)IOInput-output turn-on propagation time1.1µsAdaptor Board 93 SKYPER® 42 RTechnical ExplanationsRevision 04------------------------------------------------------------------------------------------------------------------------------------------------------------------------------------------ This Technical Explanation is valid for the following parts:Related documents:Prepared by: Johannes Krapp------------------------------------------------------------------------------------------------------------------------------------------------------------------------------------------ ContentApplication and Handling Instructions (2)Further application support (2)General Description (2)Dimensions (3)PIN Array (3)Setting Dynamic Short Circuit Protection (4)Collector Series Resistance (4)Adaptation Gate Resistors (5)Boost Capacitors (6)Environmental conditions (6)Mounting Notes (6)Please note:All values in this technical explanation are typical values. Typical values are the average values expected in large quantities and are provided for information purposes only. These values can and do vary in different applications. All operating parameters should be validated by user’s technical experts for each application.Application and Handling Instructions▪Please provide for static discharge protection during handling. As long as the hybrid driver is not completely assembled, the input terminals have to be short-circuited. Persons working with devices have to wear a grounded bracelet. Any synthetic floor coverings must not be statically chargeable. Even during transportation the input terminals have to be short-circuited using, for example, conductive rubber. Worktables have to be grounded. The same safety requirements apply to MOSFET- and IGBT-modules.▪Any parasitic inductances within the DC-link have to be minimised. Over-voltages may be absorbed by C- or RCD-snubber networks between main terminals for PLUS and MINUS of the power module.▪When first operating a newly developed circuit, SEMIKRON recommends to apply low collector voltage and load current in the beginning and to increase these values gradually, observing the turn-off behaviour of the free-wheeling diode and the turn-off voltage spikes generated across the IGBT. An oscillographic control will be necessary. Additionally, the case temperature of the module has to be monitored. When the circuit works correctly under rated operation conditions, short-circuit testing may be done, starting again with low collector voltage.▪It is important to feed any errors back to the control circuit and to switch off the device immediately in failure events.Repeated turn-on of the IGBT into a short circuit with a high frequency may destroy the device.▪The inputs of the hybrid driver are sensitive to over-voltage. Voltages higher than V S +0,3V or below -0,3V may destroy these inputs. Therefore, control signal over-voltages exceeding the above values have to be avoided.▪The connecting leads between hybrid driver and the power module should be as short as possible (max. 20cm), the driver leads should be twisted.Further application supportLatest information is available at . For design support please read the SEMIKRON Application Manual Power Modules available at .General DescriptionThe Board 93 GB SKYPER® 42 is an adaptor board for the IGBT module SKiM® 93 (spring contact). The board is paralleling three channels so the SKiM module can be used in half bridge configuration. The board can be customized allowing adaptation and optimization to the used IGBT module.The switching characteristic of the IGBT can be influenced through user settings, e.g. changing turn-on and turn-off speed by variation of R Gon and R Goff. Furthermore, it is possible to adjust the monitoring level and blanking time for the DSCP (see Technical Explanations SKYPER® 42 R).Please note:This technical explanation is based on the Technical Explanations for SKYPER®42 R. Please read the Technical Explanations SKYPER® 42 R before using the Adaptor Board.Dimensions116 PIN ArraySetting Dynamic Short Circuit ProtectionThe Vce formula for the Vce monitoring is described in the technical explanation of SKYPER 42 R. Collector Series ResistanceDesignation Shape SettingR105 MiniMELF (SMD) R VCE*Factory setting: not equippedTOPR205 MiniMELF (SMD) R VCE *Factory setting: not equippedBOTAdaptation Gate ResistorsBoost CapacitorsEnvironmental conditionsPlease refer to the technical explanation of SKYPER 42 R for the environmental conditions.Mounting NotesDISCLAIMERSEMIKRON reserves the right to make changes withoutfurnished in this document is believed to be accurate and reliable. However, no representation or warranty is given and no liability is assumed with respect to the accuracy or use of such information. SEMIKRON does not assume any liability arising out of the application or use of any product or circuit described herein. Furthermore,。
CalMaster2 快速入门指南说明书

Field and Software ToolsCalMaster2Quick Start GuideIM/VCM2/QRG Issue 21IntroductionCalMaster IRIS and CheckMaster are stand-alone verification andvalidation tools within the CalMaster2 Verification Suite.There are two options of CalMaster2 available:!CalMaster IRISEnables the printing of service reports and certification towithin 1% of factory calibration (fingerprinted flow meters) or2% (non-fingerprinted flow meters). Predictive diagnostics arealso provided to provide early warning of a possible systemfailure, enabling maintenance engineers to anticipateproblems and take planned remedial action in advance.CalMaster2 comprises:–CalMaster IRIS Verification Tool–Enhanced IRIS Software!CheckMasterEnables the validation of flow meters and the printing of aservice report.CheckMaster comprises:–CheckMaster Validation Tool–IRIS Software2UnpackingUnpack and visually inspect the CheckMaster.Also packed with the CheckMaster are:!CalMaster2 IRIS software CD.!Instruction manual.!Mains-operated battery charger & in-car adaptor! 5 MagMaster adaptors kits (Part no. WADX0089):!CheckMaster Leads:AquaMaster Communications Leads(Red and yellow numeric sleeves)AquaMaster Explorer Leads(Red numeric sleeves)MagMaster Leads(Yellow numeric sleeves)AquaMaster MIL Connector Leads(Green numeric sleeves)SensorCablePlugMagMasterVKEAdaptorConnection Lead 1WEBC0221WEBC2000 for RS232 SerialCommunications WEBC2000AquaMaster TransmitterConnection Lead 2WEBC0222AquaMaster TransmitterConnection Lead 3WEBC0223AquaMaster MILSensor CableWEBC0233AquaMaster 19-wayOutput CableWEBC235AquaMaster 7-way Output CableWEBC0234AquaMaster 7-way Output CableWEBC0232MagMaster Connection Lead 2WEBC0212MagMaster Connection Lead 3WEB0C213AquaMaster Transmitter Connection Lead 2WEBC2113Charge the CheckMasterCharge the CheckMaster for a minimum of four hours before first use.ab Plug the CalMaster2 mains adaptor into the power socket.c Recharge for at least four hours.4Install the CalMaster2 IRIS softwareInsert the CD into the computer; the install program should start automatically. If it does not, from the Windows Start menu, select Run… and type D:\Setup.exe (where D is the drive letter of the CD) and click OK or press Enter.Follow the on-screen instructions to install.To run the software, select Start | Programs | ABB | CalMaster2. Refer to the instruction manual (IM/VMC2) for complete details of the CalMaster2 IRIS software.5Register CalMaster2From the CalMaster software, selectHelp | RegisterCalMaster2… A registration screen appears:1.Type the User name, Company name and Customeridentification number.2.Select to either create a PDF of the registration or send thedetails by email:–To create a pdf, select the Create a pdf file forprinting or faxing check box.–To send an email, leave the Create a pdf file forprinting or faxing check box unselected.3.Click Next. Either an e-mail is sent to****************.com automatically or a PDF is created:–If an e-mail was sent, a response is received within 24hours. A confirmation message that the e-mail hasbeen sent appears.–If a PDF was created, print the PDF and either send itto:ABB LimitedCalMaster HelplineOldends Lane, StonehouseGloucestershireGL10 3TAUKor Fax it to: +44 (0)1453 8296714.Click Close to exit CalMaster2.6Connect the CheckMaster to the ComputerWith the CalMaster2 software running:a Slide the cover down to reveal the serial port.b Connect the RS232 cable to the CalMaster2c Connect the RS232 cable tothe computer.From the CalMaster2 IRIS software, click thebutton. Thesoftware checks that the CalMaster2 is connected.7Verify a Flow MeterFollow the detailed instructions in the manual (IM/VCM2) toconnect to a flow meter.Note.The 'Customer identification number' is printed on thelabel of the CD.Note.As this is the first time that the CheckMaster has beenused, no flow meters are listed.The Company’s policy is one of continuous product improvement and the right is reserved to modify the information contained herein without notice.Printed in UK (09.06)© ABB 2006ABB LimitedOldends Lane, Stonehouse GloucestershireGL10 3TAUKTel:+44 (0)1453 826661 Fax:+44 (0)1453 829671ABB Inc.125 E. County Line RoadWarminsterPA 18974USATel:+1 215 674 6000Fax:+1 215 674 7183IM/VCM2/QRG Issue 2。
多渠道声音处理器CP850与基于Christie IMB的Christie高清投影仪连接指南说明书

Connect a Dolby Atmos Cinema Processor CP850 to a Christie IMB Instruction SheetThis document provides procedures and information for connecting a Dolby® Atmos™ Cinema Processor CP850 to a Christie IMB.Prerequisites•One Christie Solaria Series 2 projector with Solaria firmware 3.0.0(1) or later installed•One Christie IMB with Christie IMB-S2 Main Software v1.4.0 or later installed. See the Christie Integrated Media Block User Guide on the Christie web site for installationinstructions.•One NAS or DAS device with the hard drives installed and properly configured.•One Dolby Atmos Cinema Processor CP850•Two Ethernet cables•One 25-pin AES audio cable2 Connect a Dolby Atmos Cinema Processor CP850 to a Christie IMB Instruction SheetConnect a Dolby Atmos Cinema Processor CP850 to a Christie IMB Instruction SheetSample Network TopologyItem Description AControl computer B10/100 switch CTheatre Management System (TMS) or Library Management System (LMS)DProjector intelligence board (PIB)EChristie IMB FDolby Atmos Cinema processor CP850GNetwork attached storage (NAS)H GigE switch for content networkCommand and control network (10/100)Content network (GigE)Home run connections (GigE)AES connectionConnect a Dolby Atmos Cinema Processor CP850 to a Christie IMB Instruction SheetIP and Subnet ConsiderationsYou must configure your network settings correctly for the Christie IMB to operate. Incorrect subnet settings can cause communication issues between the Christie IMB, the NAS device, and external automation devices. To reduce the risk of communication issues:•Assign the projector intelligence board (PIB) and the Christie IMB NAS1 and NAS2 ports to nonconflicting subnets. For example:•Configure the NAS1 and NAS2 ports on the Christie IMB faceplate to use DHCP when they are not in use. When you set DHCP on a NAS port and nothing is connected to the port, the Christie IMB does not mount the port and there is no risk of an IP address conflict.•Use static IP addresses on the NAS1 and NAS2 ports. If you need to use DHCP:•Verify the NAS device can be configured as a DHCP server . See the documentation provided by the manufacturer of your NAS device.•Verify that the DHCP service is enabled on the NAS device. See the documentation provided by the manufacturer of your NAS device.•Verify the address range provided by the NAS device does not conflict with the other NASport or the PIB port. See the documentation provided by the manufacturer of your NASdevice.Connect the Dolby Atmos Cinema Processor1.Connect one end of an AES cable to the AES Input (A) port on the rear panel of the DolbyAtmos Cinema Processor CP850.2.Connect the other end of the AES cable to the AES3 port on the Christie IMB.For multi-projector installations, connect the other end of the AES cable to the AES3 port on the Christie IMB of the master projector .3.Connect one end of an Ethernet cable to the Dolby Atmos Input port on the rear panel of theDolby Atmos Cinema Processor CP850.4.Connect the other end of the Ethernet cable to an Ethernet port on the GigE switch on thecontent network.If you do not have a content network, connect the Ethernet cable to the NAS port on the Christie mask255.255.255.0PIB192.168.1.100NAS1192.168.2.1NAS2192.168.3.14 Connect a Dolby Atmos Cinema Processor CP850 to a Christie IMB Instruction SheetConnect a Dolby Atmos Cinema Processor CP850 to a Christie IMB Instruction Sheet5.Connect a second Ethernet cable to the Dolby Atmos Command port on the rear panel of theDolby Atmos Cinema Processor CP850.6.Connect the other end of the Ethernet cable to an Ethernet port on the 10/100 switch on thecommand and control network.Enable Dolby Atmos1.On the projector touch panel controller (TPC), tap Menu > Christie IMB > System > DolbyAtmos .2.Tap Enabled .3.Enter the IP address for the Dolby Atmos Cinema Processor CP850 in the Control IP Addressfield.The IP addresses of all devices connected to the command and control network must use the same subnet. Use a different subnet from the content network. Configure the netmask settings so they do not conflict with the content network.4.Enter the IP address for the Dolby Digital Cinema Sound Processor CP750 n the Input IPAddress field.The IP addresses of all devices connected to the content network must use the same subnet. Use a different subnet from the command and control network. Configure the netmask settings so they do not conflict with the command and control network.5.Tap Test Connections to test the connections.6.Tap Save .Set the Global Audio DelayTo synchronize the audio track with playback you must set the global audio delay to -250milliseconds (ms).1.On the projector TPC, tap Menu > Christie IMB > System > Audio .2.Tap the Speaker Mappingtab.3.Tap the ellipsis button () to the right of Delay (ms) in the Global Settings area.4.Enter -250.5.Tap Enter .6.Tap Save .。
JUMO 温度传感器说明书

Page 1/11Data Sheet 702040Blocks tructureFeature sk S tructured operating and programming layout k S elf-optimi s ation k Ramp functionk Timer functionk Digital input filter withprogrammable filter time con s tant k 1 limit comparator k limit s witchJUMO iTRON 04/08/16/32Compact microproce ss or controller sHou s ing for flu s h-panel mounting to DIN IEC 61554Brief de s criptionThe JUMO iTRON controller s erie s compri s e s univer s al and freely programmable com-pact in s trument s for a variety of control ta sks . It con s i s t s of five model s , with the bezel s ize s 96mm x 96mm, 96mm x 48mm in portrait and land s cape format, 48mm x 48mm and 48mm x 24mm.The controller s feature a clearly readable 7-s egment di s play which, depending on the ver-s ion, i s 10 or 20 mm high, for proce ss value and s etpoint indication or for dialog s . Only three k ey s are needed for configuration. Parameter s etting i s arranged dynamically, and after two operation-free s econd s the value i s accepted automatically. S elf-optimi s ation,which i s provided a s s tandard, e s tabli s he s the optimum controller parameter s by a k ey s tro k e. The ba s ic ver s ion al s o include s a ramp function with adju s table gradient s . A timer function ha s been integrated a s an extra.All controller s can be employed a s s ingle-s etpoint controller s with a limit comparator, or as double-s etpoint controller s . The lineari s ation s of the u s ual tran s ducer s are stored. Pro-tection i s IP66 at the front and IP20 at the bac k . The electrical connection i s by a plug-in connector with s crew terminal s .The input s and output s are s hown in the bloc k s tructure below.JUMO iTRON 08Type 702042JUMO iTRON 04Type 702044JUMO iTRON 08Type 702043JUMO iTRON 32Type 702040JUMO iTRON 16Type 702041Approval s /approval mark s (s ee "Technical data")Data Sheet 702040Page 2/11Technical dataThermocouple inputRe s i s tance thermometer inputStandard s ignal inputMea s urement circuit monitoring 1De s ignation Range 1Mea s urement accuracy Ambienttemperature error Fe-Con L Fe-Con J EN 60584Cu-Con U Cu-Con T EN 60584NiCr-Ni K EN 60584NiCr S i-Ni S i N EN 60584Pt10Rh-Pt S EN 60584Pt13Rh-Pt R EN 60584Pt30Rh-Pt6Rh BEN 60584-200to +900°C -200to +1200°C -200to +600°C -200to +400°C -200to +1372°C -100to +1300°C0— 1768°C 0—1768°C +300— 1820°C≤0.4%≤0.4%≤0.4%≤0.4%≤0.4%≤0.4%≤0.4%≤0.4%≤0.4%100 ppm/°C 100 ppm/°C 100 ppm/°C 100 ppm/°C 100 ppm/°C 100 ppm/°C 100 ppm/°C 100 ppm/°C 100 ppm/°CCold junctionPt 100 internal1. The s e range s refer to the ambient temperature of 20°CDe s ignation Connection type RangeMea s urement accuracy Ambienttemperature error Pt 100 EN 607512-/3-wire -200to +850°C ≤0.1%50 ppm/°C Pt 1000 EN 607512-/3-wire -200to +850°C ≤0.1%50 ppm/°C K TY11-62-wire-50to +150°C≤1.0%50 ppm/°CS en s or lead re s i s tance 20Ω max. per lead for 2- and 3-wire circuitMea s urement current 250µALead compen s ationNot required for 3-wire circuit. For 2-wire circuit, lead compen s ation can be implemented in s oftware through proce ss value correction.De s ignation RangeMea s urement accuracy Ambienttemperature error Voltage0—10V , input re s i s tance R E > 100k Ω2—10V , input re s i s tance R E > 100k Ω0—1V , input re s i s tance R E > 10M Ω10,2—1V , input re s i s tance R E > 10M Ω1≤0.1%≤0.1%≤0.1%≤0.1%100 ppm/°C 100 ppm/°C 100 ppm/°C 100 ppm/°C Current4—20mA, voltage drop 3V max.0—20mA, voltage drop 3V max.≤0.1%≤0.1%100 ppm/°C 100 ppm/°C1. for Type 702040/41 with 2 relay output s (option)Tran s ducer Overrange/underrangeProbe /lead s hort-circuit 1Probe/lead breakThermocouple•-•Re s i s tance thermometer •••Voltage 2—10V / 0.2—1V0—10V/ 0—1V •••-•-Current4—20mA 0—20mA•••-•-1. In the event of a fault, the output s move to a defined s tatu s (configurable).= factory s etting •recogni s ed-not recogni s edData Sheet 702040Page 3/11Output sControllerTimerElectrical dataHou s ingA ss ignment Type 702040/41Type 702042/43/44Output 1relayrelay Output 2logic 0/5V or logic input logic 0/5V Output 2 (option)logic 0/12V or logic input logic 0/12V Output 2 (option)relay not po ss ible Output 3not availablerelayTechnical data Relay ratingcontact life n.o. (ma k e) contact 3A at 250VAC re s i s tive load 150 000 operation s at rated loadLogiccurrent limiting load re s i s tance 0/5V 20mAR load 250Ω min .Logiccurrent limiting load re s i s tance 0/12V 20mAR load 600Ω min.= factory s ettingController types ingle-s etpoint controller with limit comparator, double-s etpoint controllerController s tructure s P/PD/PI/PIDA/D converter re s olution better than 15 bitS ampling time210m s ec/250m s ec with activated timer functionAccuracy0.7% ± 10ppm/°CS upply (s witch-mode power s upply)110—240V -15/+10%AC 48—63Hz, or 20—30V AC/DC 48—63Hz, or10—18V DC (Connection to S ELV or PELV)Te s t voltage s (type te s t)to EN 61010, Part 1, March 1994,overvoltage category II, pollution degree 2, for Type 702040/41overvoltage category III, pollution degree 2, for Type 702042/43/44Power con s umption max. 7VA Data bac k upEEPROMElectrical connectionat the rear, via plug-in s crew terminal s ,conductor cro ss -s ection up to 1.5mm 2 (1.0mm 2 for Type 702040/41) or2x 1.5mm 2 (1.0mm 2 for Type 702040/41) with ferrule sElectromagnetic compatibility interference emi ss ion interference immunity EN 61 326Cla ss Bto indu s trial requirement sS afety regulationto EN 61010-1In s tallation height maximum 2000 m above s ea levelCa s e typePla s tic ca s e for panel mounting acc to. IEC 61554 (indoor u s e)Dimen s ion s in mm (for Type)702040702041702042702043702044Bezel s ize48x 2448x 4848x 96(portrait)96x 48(land s cape)96x 96Depth behind panel100100707070Panel cut-out45+0.6x 22.2+0.345+0.6x 45+0.645+0.6x 92+0.892+0.8x 45+0.692+0.8x 92+0.8Ambient/s torage temperature range 0—55°C /-40 to +70°CData Sheet 702040Page 4/11Approval s /approval mark sDi s play and control sSelf-optimi s ation (SO)The s tandard s elf-optimi s ation facility produce s an automatic adju s tment of the controller to the proce ss .S elf-optimi s ation determine s the controller parameter s for PI and PID controller s (proportional band, re s et time, derivative time), a s well a s the cycle time and the filter time con s tant of the digital input filter.Ramp functionClimatic condition s not exceeding 75% rel. humidity, no conden s ationOperating po s ition unre s tricted Protection to EN 60529,IP66 at the front, IP20 at the bac kWeight75g approx.95g approx.145g approx.160g approx.200g approx.Approval mark Te s ting agencyCertificate/certification numberIn s pection ba s i sValid forUL Underwriter Laboratorie s E201387UL 61010-1all device s C S A C S A-Approval232831CAN/C S A-C22.2No. 61010.1-04all device sData Sheet 702040Page 5/11Limit comparatorLimit s witch (extra code)If the limit comparator function i s active, then the s witched s tate will have to be re s et by hand.Precondition: the condition that cau s ed the alarm i s no longer pre s ent (for l k 8: proce ss value < AL). The di s play s how s the alarm s tatu s .The alarm s tatu s will be retained after a power failure.Timer function (extra code)U s ing the timer function, the control action can be influenced by mean s of the adju s table time t i 0. After the timer ha s been s tarted by power ON, by pre ss ing the k ey or via the logic input, the timer s tart value t i 0 i s counted down to 0, either in s tantly or after the proce ss value ha s gone above or below a programmable tolerance limit. When the timer ha s run down, s everal event s are triggered, s uch a s control s witch-off (output 0%) and s etpoint s witching. Furthermore, it i s po ss ible to implement timer s ignalling during or after the timer count, via an output.The timer function can be u s ed in conjunction with the ramp function and s etpoint s witching.Table: Timer function s (u s ing the example of a rever s ed s ingle-s etpoint controller)Data Sheet 702040Page 6/11Tolerance limitThe po s ition of the tolerance limit depend s on the controller type:- S ingle-s etpoint controller (rever s ed, heating): Tolerance limit i s below the s etpoint - S ingle-s etpoint controller (direct, cooling): Tolerance limit i s above the s etpoint - Double-s etpoint controller: Tolerance limit i s below the s etpointIf, during the control proce ss , the proce ss value goe s above/below the tolerance limit, then the timer will be s topped for the duration of the infringement.Di s play and operationThe timer value i s di s played at the operating level and remain s s o permanently (no time-out).Operation i s from the k eypad, when the timer value i s vi s ible in the di s play, or via the logic input. The operating option s compri s e s tart,s top, continue and cancel timer function, and are s hown differently in the di s play.The current timer value and the timer s tart value are acce ss ible and adju s table at any time at a s eparate timer level.Data Sheet 702040Page 7/11Parameter and configurationOperating levelParameter levelConfiguration levelDe s ignation Di s play Factory s ettingValue range S etpointSP /SP1/SP20S PL—S PH Ramp s etpointSPr 0S PL—S PH Timer value/timer s tart valuet i /t i 00 —999.9hDe s ignation Di s play Factory s ettingValue range S etpoint 1SP 10S PL—S PH S etpoint 2SP 20S PL—S PH Limit value for limit comparator AL 0-1999to +9999digit Proportional band 1Pb:100—9999digit Proportional band 2Pb:200—9999digit Derivative time dt 80s ec 0—9999s ec Re s et time rt 350s ec 0—9999s ec Cycle time 1CY 120.0s ec 1.0—999.9s ec Cycle time 2CY 220.0s ec1.0—999.9s ec Contact s pacingdb 00—1000digit Differential (hy s tere s i s ) 1HYS.110—9999digit Differential (hy s tere s i s ) 2HYS.210—9999digit Wor k ing point Y:00%-100to +100%Maximum output Y:1100%0to 100%Minimum output Y:2-100%-100to +100%Filter time con s tant dF 0.6s ec 0.0—100.0s ec Ramp s loperASd—999digitDe s ignation Di s play Factory s etting Value range/s electionTran s ducerC111Pt100Pt100, Pt1000, K TY11-6, T, J, U, L, K , S ,R, B, N, 0 (4)—20mA, 0 (2)—10VDecimal place/unitC112none/°C none, one, two/°C, FController type/output s C113s ee table on next pageLimit comparator function C114no function no function, l k 1—8Ramp functionC115no function no function, °C/min, °C/h Output s ignal on overrange/ underrange C1160% output limit comparator off 0%, 100%, -100% limit comparator on/offLogic inputC117no function k ey / level inhibit,ramp s top, s etpoint s witchingOutput s 1, 2 and 3(only Type 702042/43/44)C118function s a s defined under C113freely configurable(s ee table on next page)Timer functionC120no function s ee de s cription “Timer function”S tart condition for timerC121from k eypad/logic input - power ON - k eypad/logic input- tolerance limitTimer s ignalling C122no function - timer s tart to timer run-down- after run-down for 10s ec - after run-down for 1 min.- after run-down until ac k nowledgementUnit of time (timer)C123mm.ss - mm.ss- hh.mm - hhh.hS tart value of value range SCL0-1999 to +9999 digitData Sheet 702040Page 8/11Controller type/output s (C 113)Expanded configuration option s for the output s on Type 702043/44 (C118)End value of value range SCH 100-1999 to +9999 digit Lower s etpoint limit SPL -200-1999 to +9999 digit Upper s epoint limitSPH 850-1999 to +9999 digit Proce ss value correction OFFS 0-1999 to +9999 digit Differential (hy s tere s i s )HySt 1 0—9999 digitController typeOutput 1Output 2 + 3S ingle s etpoint rever s ed controller limit comparator/timer s ignalling S ingle s etpoint direct controllerlimit comparator/timer s ignallingDouble s etpointcontroller rever s edcontroller direct S ingle s etpoint rever s ed limit comparator/timer s ignalling controller S ingle s etpoint direct limit comparator/timer s ignallingcontrollerDouble s etpoint controller directcontroller rever s ed= factory s ettingOutput 1: Relay (K1)Output 2: Logic (K2)Output 3: Relay 1-s e t p o i n t c o n t r o l l e rFunction s of the output s a s defined under C 113controller output limit comparator timer s ignalling controller output timer s ignalling limit comparator limit comparator controller output timer s ignalling limit comparator timer s ignalling controller output timer s ignalling controller output limit comparator timer s ignalling limit comparator controller output 2-s e t p t .c o n t r o l l e rcontroller output 1controller output 2limit comparator/timer controller output 1limit comparator/timer controller output 2controller output 2controller output 1limit comparator/timer controller output 2limit comparator/timer controller output 1limit comparator/timer controller output 1controller output 2limit comparator/timercontroller output 2controller output 1Data Sheet 702040Page 9/11Dimen s ion sType 702040 / …Type 702043/...Type 702041 / …Type 702044/...Type 702042 / …Typehorizontal vertical 70.2040/418mm min.8mm min.70.2042/43/4410mm min.10mm min.Edge-to-edge mounting(minimum s pacing s of the panel cut-out s)Data Sheet 702040Page 10/11Connection diagram sJUMO iTRON 32, Type 702040, 48mm x 24mm format JUMO iTRON 16, Type 702041, 48mm x 48mm formatJUMO iTRON 08, Type 702042, 48mm x 96mm format (portrait)JUMO iTRON 08, Type 702043. 96mm x 48mm format (land s cape)JUMO iTRON 04, Type 702044, 96mm x 96mm formatStandard ver s ion / Ver s ion with 12V logic outputVer s ion with 2 relay outputs2014-09-01/00357838Data Sheet 702040Page 11/11Order detail sExtra order code s for cu s tomized configuration(2)Ba s ic type exten s ion(3)Input s(1)(2)(3)(4)(5)(6)Type de s ignation 7020../..-...-...-../...,...** Li s t extra code s in s equence, s eparated by comma s(1)Ba s ic type(bezel s ize in mm)40=48x 24, 41 = 48x 48, 42 = 48x 96 (portrait), 43 = 96x 48 (land s cape), 44 = 96x 96(2)Ba s ic typeexten s ion 8899==controller type configurable 1controller type configured to cu s tomer s pecification 2(3)Input s 888999==input s configurable 1input s configured to cu s tomer s pecification 2(4)Output s000=S tandardType 702040/41Type 702042/43/44Output 1relay (n.o. ma k e)relay (n.o. ma k e)Output 2logic 0/5V , optionally configurable a s logic input logic 0/5V Output 3not available relay (n.o. ma k e)Option sType 702040/41Type 702042/43/44113=Output 2(output s 1+3 a s for S tandard)logic 0/12V , optionally configurable a s logic input logic 0/12V 101=Output 2(output 1 a s for S tandard)relay (n.o. ma k e)(logic input i s alway s available)not po ss ible(5)Supply162523===10—18V DC20—30V AC/DC 48—63Hz110—240V AC -15/+10% 48—63Hz (6)Extra code069=UL and C S A approval 210=Timer function220=Timer function + limit s witch 3Delivery package ex-factory for Type 702040/41Type 702042/43/441 mounting frame2 mounting brac k et s1 s eal, 1 Operating In s truction s 70.20401. s ingle-s etpoint with limit comparator, s ee factory s etting s under configuration and parameter level2. s ee extra order code s (below) or factory s etting s under configuration and parameter level3. The linearization s for K TY11-6 and thermocouple B have been deletedController typeOutput 1Output 2 and 310=s ingle s etpoint rever s ed 1controller limit comparator/timer s ignalling 11=s ingle s etpoint direct 2controllerlimit comparator/timer s ignalling 30=double s etpoint controller rever s edcontroller direct 20=s ingle s etpoint rever s ed 1limit comparator/timer s ignalling controller 21=s ingle s etpoint direct 2limit comparator/timer s ignalling controller33=double s etpointcontroller directcontroller rever s ed1. controller output i s active when proce ss value i s below s etpoint, e. g. heating2. controller output i s active when proce ss value i s above s etpoint, e. g. cooling001=Pt1003-wire 040=Fe-Con J 045=Pt13 Rh-Pt R 063=0—10V 003=Pt1002-wire041=Cu-Con U 046=Pt30 Rh-PtRh B 071=2—10V 005=Pt1000 2-wire 042=Fe-Con L 048=NiCr S i-Ni S i N601=K TY11-6 (PTC)006=Pt1000 3-wire 043=NiCr-Ni K 052=0—20mA 039=Cu-Con T044=Pt10Rh-PtS053=4—20mA= factory-s et。
- 1、下载文档前请自行甄别文档内容的完整性,平台不提供额外的编辑、内容补充、找答案等附加服务。
- 2、"仅部分预览"的文档,不可在线预览部分如存在完整性等问题,可反馈申请退款(可完整预览的文档不适用该条件!)。
- 3、如文档侵犯您的权益,请联系客服反馈,我们会尽快为您处理(人工客服工作时间:9:00-18:30)。
1.3 STPConfigure Multiple Spanning-Tree(MST)on all four switches as per the following requirements∙Set the region name as CCIE∙Assign all active odd VLANs to instance 1∙Assign all active even VLANs to instance 2∙Explicitly assign all unused VLANs to instance 3∙Ensure that SW1 is the primary root bridge for odd VLANs and for CIST∙Ensure that SW1 is the secondary root for even VLANs∙Ensure that SW2 is the primary root bridge for even VLANsEnsure that SW2 is the secondary root for odd VLANs and for CIST解法:SW1-SW4Spanning-tree mode mstSpanning-tree mst configurationName CCIEInstance 3 vlan 1-4094Instance 1 vlan 1,45,69,89,999Instance 2 vlan 16,18,28,36,68,100,200,300,500SW1:Spanning-tree mst 0,1 root priSpanning-tree mst 2 root secSW2:Spanning-tree mst 0,1 root secSpanning-tree mst 2 root pri1.4 Switching Trunking and EtherChannelRefer to “Diagram 5: Trunk Ports” and configure your network as per the fellowing requirements:•All inter-switch links must use encapsulation 802.1Q.•Disable DTP on all trunks.•Ensure that the native VLAN (VLAN1) is always tagged.•On the each switch, configure three 200Mb/s fault-tolerant links relying on the cisco proprietary(思科私有)•Traffic forward through these fault-tolerant links must be load-balanced based on the source and destination ip addresses.1.6·SW4的F0/1-5口,属于VLAN500·SW4的F0/1-5口,开启快速过渡到转发状态的特性(portfast)·使用一条命令,确保这5个端口的任意一个收到BPDU,需要过渡到err-disable状态·err-disable状态的端口,在15min后,自己恢复解法:Interface range f0/1-5Sw mo acSw ac vlan 500Spanning-tree portfastSpnning-tree portfast bpduguard defaulterrdisable recovery cause bpduguarderrdisable recovery interval 9002.9(IPv6 ospfv3)OSPFv2 和OSPFv3 必须拓扑吻合(就是在IPv4的OSPFv2中运OSPFv3)Loopback0 的IPv4 address要配置成OSPFv3的ROUTER-ID Area 0位于SW1-SW3之间AREA1必须被配置成stub,但是允许注入外部路由(NSSA)解法:SW1Ipv6 router ospf 1Router-id 129.6.6.6Area 1 nssaInterface loopback0Ipv6 ospf 1 area 0Interf vlan 68Ipv6 ospf 1 area 0Interface range vlan 36,vlan 16Ipv6 ospf 1 area 1SW3:Ipv6 router ospf 1Router-id 129.8.8.8Interface loopback0Ipv6 ospf 1 area 0Interf vlan 68Ipv6 ospf 1 area 0R3Ipv6 router ospf 1Router-id 129.3.3.3Area 1 nssaInterfa lo0,f0/0,s0/0/0Ipv6 ospf 1 a 1R5Ipv6 router ospf 1Router-id 129.5.5.5Area 1 nssaInterface lo0,s0/1/0,s0/0/0.100 Ipv6 ospf 1 a 12.10 IPv6 Routing·configure a 6to4 tunnel between R4 and R5 in oder to transport IPv6 traffic from R4 to the OSPFv3 domain via the Fa0/1 interface of R4.·Configure the interface Fa0/0 on R4 and R5 using the 6to4 prefix.·You may use any IPv6 prefix for the tunnel address.·You may use two static routes on R4 and one static route on R5.·Ensure that R4 is able to reach Loopback0 of SW3 as show below.6to4技术,动态的tunnel技术注意点:1,tunnel 不可能出现destination(只有tunnel source)配置步骤1,改造网络根据需求的tunnel source ipv4 address 来进行改造(source 一般使用loopback0),改主要是把R4/R5的F0/0接口地址改对。
2,配置tunnelR4:interface tunnel 45tunnel source loo0tunnel mode ipv6ip 6to4ipv6 enableR5:interface tunnel 45tunnel source loo0tunnel mode ipv6ip 6to4ipv6 enable3,起路由(6to4不支持协议,题意给出R4两条静态,R5一条静态)R4:ipv6 route 2002::/16 tunnel 45ipv6 route 2001:YY:YY:8::8/128 tunnel 45 (R5的F0/0)4,OSPF区域的回包路由(R5去重分发静态)R5:ipv6 route 2002::/16 tunnel 45ipv6 router ospf 1redistribute static3.2 Advanced Multicast feature·Ensure that both RPs process Join requests for group 232.1.1.1 only·Ensure that only the authorized sources (hosts located in VLAN_68 and the VLAN_36 SVI of SW1) are allowed to register to the RPs.·Ensure that sources from VLAN 68 can not register to R2 , and that any other sources can register to R2.·Do not use any route-map or named access-list to achieve this task.4.2 L2 Security·A server (with the MAC address 1e.1234) connected to the interface Fa0/18 of SW1 must be able to talk to all devices on VLAN 500 as well as to the rest of the network.·Ensure that if anyone unplugs that server from SW1 and connects a laptop , the port will shut itself down for ten minutes , at which point it will accept another attempt.·Two ports on SW1 (Fa0/16 and Fa0/17) are connected to hosts on VLAN 500 and are known to be heavy abusers of the network. Ensure that they cannot talk to one another or to any other users located in VLAN 500 , These two hosts can talk to the server connected to Fa0/18 of SW1 as well as to the rest of the network. ·Use VLAN 2000 if you need to create a new VLAN to accomplish this task.解法:规划PVLAN需要创建的VLAN,就是2000SW1-SW4Spanning-tree mst configurationInstance 2 vlan 2000SW1vlan 2000name ISOprivate-vlan isolatedvlan 500name USERSprivate-vlan primaryprivate-vlan association 2000default interface range f0/16-18interface range f0/16-17switchport private-vlan host-association 500 2000 switchport mode private-vlan hostno shutdowninterface FastEthernet0/18switchport private-vlan mapping 500 2000 switchport mode private-vlan promiscuousswitchport port-securityswitchport port-security mac-address 1e.1234errdisable recovery cause psecure-violationerrdisable recovery interval 600no shutdown4.5 First Hop RedundancyFor your information , a DHCP server (which is not in service yet) will issue two different gateways to clients located in VLAN 45.·For client with the host portion of their IP address lower than 128 , the default gateway will be 10.YY.45.1·For client with the host portion of their IP address higher or equal to 128 , the default gateway will be 10.YY.45.254Configure both R4 and R5 as per the following requirements.·Both R4 and R5 must provide automatic default gateway backup for hosts located on VLAN 45.·Ensure that DHCP client request sourced from users connected to VLAN 45 and sent to the DHCP server with IP address 10.YY.99.99·for 10.YY.45.1>R4 must be the preferred gateway.>R5 must be assume ownership if R4 fails.>R4 must advertise VRRP packet every 300 milliseconds for this gateway only.·For 10.YY.45.254>R5 must be the preferred gateway.>R4 must be assume ownership if R5 fails.>Ensure that if , at a later date , a non-Cisco device (which is also running VRRP) is introduced to VLAN 45 , it must take over the VRRP master role in the event R5 was powered off , with R4 as a tertiary backup gateway . (Assume this non-Cisco device will advertise a default priority)解法:R4-R5Interface f0/1Ip helper-address 10.YY.99.99For 10.YY.45.1R4Interface fastethernet0/1Vrrp 1 ip 10.YY.45.1Vrrp 1 priority 101Vrrp 1 timers advertise msc 300 R5Interface fastethernet0/1Vrrp 1 ip 10.YY.45.1FOR 10.YY.45.254R4Interface fastethernet0/1Vrrp 2 ip 10.YY.45.254VRRP 2 priority 99R5Interface fastethernet0/1Vrrp 2 ip 10.YY.45.254VRRP 2 PRIORITY 101。