SolidWorks模具设计案例
SolidWorks模具设计教程

SolidWorks 模具设计1。
拔模分析为了创建可以实现注塑的模具, 塑料产品必须被设计和拔模正确才能从围绕在周围的模具中顶出。
要对模型产品进行拔模分析,使用拔模分析命令有助于发现拔模和设计的错误。
对前视面进行向上拔模分析。
来看看各分析面的含义: 跨立面:是横跨分型线的面。
用户必须把跨立面分割成两块以分开模具的表面。
跨立面可以通过跨立面命令手工处理或者通过单击分型线命令中的分割面选项自动完成。
正陡面:这些表面中包含部分拔模量不够的区域。
如果整个面的拔模量都不够,它将被归类为【需要拔模】。
这些面能在模具中的正侧找到. 负陡面:这些表面包含部分拔模量不够的区域.这些面能在模具中的负侧找到.2. 调整收缩率模具上产品型腔部分的加工要略微比从模具中生产出来的塑料件大些。
这样做是为了补偿高温的被顶出的塑料件冷却后的收缩率。
在通过塑料产品创建模具之前,模具设计者需要放大塑料产品来解决收缩率.不同的材料,收缩率也是不同的,SolidWorks 用比例缩放命令在解决这个问题.这个零件我们以ABS 材料来做,5%的收缩率。
3. 确定分型线分型线是注塑类塑料产品中型腔与型心曲面中相互接触的边界.分型线是那些用来分割型心和型腔曲面的边界。
它们也构成了分型面的内部边界。
型腔面(正拔模)是绿色的,型心面(负拔模)是红色的。
任何一条被红色和绿色面共用的边都是分型线边界。
当拔模分析完成后,所有的被绿色和红色边共用的边被自动选中并被添加到分型线列表中。
单击确定。
手动添加分型线:在这个例子中,当分型线命令运行时,分型线边被自动的选中。
因为这是一个简单的分型线边界,这些边界被自动添加到位于分型线PropertyManager 的边线列表中。
有时分型线可能会更复杂以致于软件无法自动搜索到分型线。
当这种情况发生时,使用位于边线列表框下方的边线选择按钮去选择分型线。
4. 关闭孔和开口在分型线建立后,下一步是决定塑料产品上哪些开放的成型区域需要关闭曲面. 一个开放的成型区域或者是一个孔或者是一个开口,在注塑产品上就是模具型心型腔完全吻合形成的孔。
Solidworks经典实例-80例

1图1 图2图1提示:①拉伸圆柱→倒内外角→拉伸切槽;。
②拉伸带槽柱体→倒内外角;。
③旋转带倒角圆套→切伸切槽。
图2提示:①拉伸带孔的六边形→倒内角→倒外角;。
②拉伸圆柱套→倒内角→倒外角→拉伸切六边;。
③旋转带倒角圆柱套→拉伸切六边。
图3 图4图3提示:①拉伸带孔的六边形→倒内角→倒外角→拉伸切顶槽;②拉伸圆柱套→倒内角→倒外角→拉伸切六边形→拉伸切顶槽;③旋转带倒角的圆柱套→拉伸切六边→拉伸切顶槽。
图4提示:①拉伸圆锥套→拉伸侧耳→切除多余部分→圆角;②旋转圆锥套→拉伸侧耳→切除多余部分→圆角。
图5 图6图5提示:旋转生成主体→拉伸切横槽→阵列横槽。
图6提示:①拉伸圆柱→倒角→拉伸切除圆柱孔;②旋转带倒角圆柱→拉伸切除圆柱孔。
图7 图8图7提示:旋转法。
图8示:①旋转阶梯轴(带大端孔)→拉伸切内六角→拉伸切外六角→切小端圆孔;②拉伸阶梯轴→拉伸切圆柱孔→拉伸切内六角→拉伸切外六角→切小端圆孔。
图9 图10图9提示:①旋转带球阶梯轴→拉伸切中孔→拉伸切横孔→拉伸切球部槽。
图10提示:①旋转法。
图11 图12图11示:旋转生成轮主体→拉伸切轮幅→拉伸切键槽。
图12提示:旋转主体→切除拉伸孔→切除拉伸槽。
23图13 图14图13提示:①旋转。
图14提示:①旋转生成带皮带槽的轮主体→拉伸切轮幅→拉伸切键槽。
图15 图16图15提示:①画一个方块→切除拉伸内侧面→拉伸两个柱→切除拉伸外侧面→切除拉伸孔。
图16提示:①旋转生成齿轮主体→切除拉伸键槽→画一个齿的曲线→扫描生成一个齿→阵列其它齿。
②从库中提取→保存零件。
图17 图18图17提示:旋转主体→切除拉伸孔。
图18提示:旋转主体→切除拉伸孔。
图19 图20图19提示:旋转主体→拉伸切除六边形。
图20提示:旋转主体→拉伸切除六边形。
图21 图22图21提示:旋转主体1→旋转主体2→圆角→拉伸中间方块→切除方块中孔。
图22提示:旋转主体1→旋转主体2→圆角→拉伸中间方块→切除方块中孔。
SolidWorks模具设计,很简单
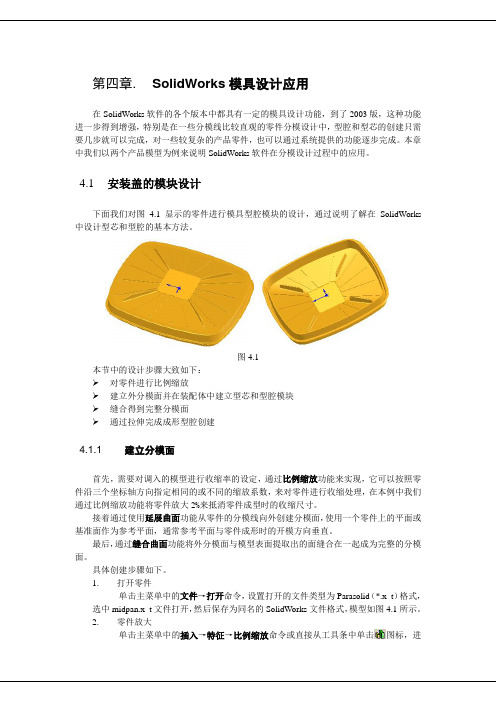
第四章.SolidWorks模具设计应用在SolidWorks软件的各个版本中都具有一定的模具设计功能,到了2003版,这种功能进一步得到增强,特别是在一些分模线比较直观的零件分模设计中,型腔和型芯的创建只需要几步就可以完成,对一些较复杂的产品零件,也可以通过系统提供的功能逐步完成。
本章中我们以两个产品模型为例来说明SolidWorks软件在分模设计过程中的应用。
4.1安装盖的模块设计下面我们对图 4.1显示的零件进行模具型腔模块的设计,通过说明了解在SolidWorks 中设计型芯和型腔的基本方法。
图4.1本节中的设计步骤大致如下:➢对零件进行比例缩放➢建立外分模面并在装配体中建立型芯和型腔模块➢缝合得到完整分模面➢通过拉伸完成成形型腔创建4.1.1 建立分模面首先,需要对调入的模型进行收缩率的设定,通过比例缩放功能来实现,它可以按照零件沿三个坐标轴方向指定相同的或不同的缩放系数,来对零件进行收缩处理,在本例中我们通过比例缩放功能将零件放大2%来抵消零件成型时的收缩尺寸。
接着通过使用延展曲面功能从零件的分模线向外创建分模面,使用一个零件上的平面或基准面作为参考平面,通常参考平面与零件成形时的开模方向垂直。
最后,通过缝合曲面功能将外分模面与模型表面提取出的面缝合在一起成为完整的分模面。
具体创建步骤如下。
1.打开零件单击主菜单中的文件→打开命令,设置打开的文件类型为Parasolid(*.x_t)格式,选中midpan.x_t文件打开,然后保存为同名的SolidWorks文件格式,模型如图4.1所示。
2.零件放大单击主菜单中的插入→特征→比例缩放命令或直接从工具条中单击图标,进入缩放设置界面,在其中选中统一比例缩放选项,输入缩放比例为1.02%,设定比例缩放点为重心或原点,如图4.2所示,单击确定按钮。
图4.23.建立延展曲面单击工具条中的图标,弹出延展曲面的设置界面,从特征树中选择前视图基准面作为参考平面,然后在要延展的边线列表中单击,选中零件分模线上的一条边,再勾选沿切面延伸选项,在延展距离中将默认的10mm改为30mm,如图4.3所示。
solidworks曲面建模案例
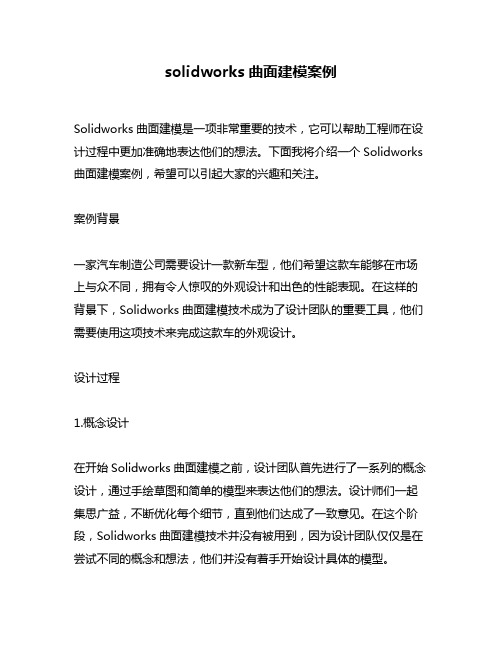
solidworks曲面建模案例Solidworks曲面建模是一项非常重要的技术,它可以帮助工程师在设计过程中更加准确地表达他们的想法。
下面我将介绍一个Solidworks 曲面建模案例,希望可以引起大家的兴趣和关注。
案例背景一家汽车制造公司需要设计一款新车型,他们希望这款车能够在市场上与众不同,拥有令人惊叹的外观设计和出色的性能表现。
在这样的背景下,Solidworks曲面建模技术成为了设计团队的重要工具,他们需要使用这项技术来完成这款车的外观设计。
设计过程1.概念设计在开始Solidworks曲面建模之前,设计团队首先进行了一系列的概念设计,通过手绘草图和简单的模型来表达他们的想法。
设计师们一起集思广益,不断优化每个细节,直到他们达成了一致意见。
在这个阶段,Solidworks曲面建模技术并没有被用到,因为设计团队仅仅是在尝试不同的概念和想法,他们并没有着手开始设计具体的模型。
2.建立基础几何形状在经过了概念设计之后,设计团队使用Solidworks构建了基础几何形状,这包括车的车身、车顶和整个底盘。
基础几何形状通常由简单的几何体组成,例如立方体和球体。
借助这些基础几何形状,设计师们可以更加容易地调整整个模型的形状和大小。
3.创建曲面特征在建立了基础几何形状之后,设计团队开始使用Solidworks曲面建模技术来创建车身的各种曲面特征。
这些特征通常包括车头、车尾、车侧面和车顶。
在这个阶段,设计师们需要花费大量的时间来调整每个特征,以确保它们能够完美地结合在一起。
4.完善细节在完成了车身的曲面建模之后,设计团队进入了最后一个阶段,他们需要添加一些细节来使车的外观更为完美。
这些细节通常包括车灯、车轮和车窗等。
借助Solidworks曲面建模技术,设计师们可以快速地创建这些细节,并将它们精确地融合到整个模型中。
总结在这个案例中,Solidworks曲面建模技术帮助设计团队成功地完成了一款新车型的外观设计。
solidworks曲面仿形案例

一、概述SolidWorks是一款领先的三维设计软件,它提供了丰富的功能和工具,可以帮助工程师和设计师轻松地进行曲面仿形。
曲面仿形是指通过对已有曲面进行变形和调整,生成新的曲面形状,这在产品设计和工程领域中具有重要的应用价值。
在本文中,我们将介绍使用SolidWorks 进行曲面仿形的案例,帮助读者了解这一技术的应用和实践。
二、案例背景我们需要设计一个汽车车顶的曲面,要求曲面光滑、连续,并且能够适配整个车身结构。
在这个案例中,我们将使用SolidWorks进行曲面仿形,以实现车顶曲面的设计和优化。
三、案例步骤1. 创建基础曲面:我们需要在SolidWorks中创建基础曲面,作为车顶曲面的起始点。
可以使用工具栏中的“曲面”功能,在平面上绘制基础曲线,并使用曲线来创建基础曲面。
2. 曲面修正:在创建基础曲面后,我们需要对其进行修正和调整,使得曲面能够更好地适配整个车顶结构。
可以使用SolidWorks提供的曲面修正工具,通过拉伸、旋转、偏移等操作来调整曲面形状。
3. 曲面连接:接下来,我们需要将基础曲面和修正后的曲面进行连接和融合,以实现曲面的连续和光滑。
SolidWorks提供了丰富的曲面连接工具,可以帮助我们对曲面进行连接和融合,以满足设计要求。
4. 曲面优化:我们需要对整个曲面进行优化和调整,确保曲面的形状和结构能够满足汽车车顶的设计需求。
可以使用SolidWorks提供的曲面优化工具,对曲面进行微调和优化,以实现最终的设计效果。
四、案例成果通过上述步骤,我们成功地使用SolidWorks进行了汽车车顶曲面的设计和仿形。
最终的曲面形状光滑、连续,并且能够完美地适配整个车身结构,达到了设计要求。
这个案例充分展示了SolidWorks曲面仿形技术在产品设计和工程领域的应用和实践,为读者提供了宝贵的经验和启示。
五、结论曲面仿形是SolidWorks中一个重要的设计技术,它在产品设计和工程领域中具有广泛的应用价值。
solidworks参数化设计案例

SolidWorks 是一种功能强大的三维计算机辅助设计(CAD)软件,广泛应用于工程领域。
它的参数化设计功能可以帮助工程师快速建模和调整模型,极大地提高了设计效率和精度。
本文将通过一个实际案例来介绍 SolidWorks 的参数化设计功能及其应用。
案例背景:某公司生产一种特定型号的汽车零部件,由于市场需求的变化,公司需要对该零部件进行改进,以提高其性能和降低成本。
在这种情况下,利用 SolidWorks 的参数化设计功能会极大地简化设计过程,并且可以方便地应对后续的变更需求。
1. 参数化设计的基本原理参数化设计是一种基于参数的设计方法,即通过定义和调整设计模型的参数来实现快速建模和修改。
在 SolidWorks 中,可以通过数学表达式或者限制条件来定义模型的参数,然后通过改变参数的数值来调整模型的尺寸、形状和特征等。
2. 设计过程工程师需要打开 SolidWorks 软件并创建一个新的零部件文件。
根据原零部件的几何形状和结构,建立一个初始的三维模型。
接下来,通过参数化设计功能,为模型中的关键尺寸和特征添加参数,并定义它们之间的关系。
可以定义零部件的长度、宽度、高度、孔的直径等参数,并设置它们之间的数学表达式或者约束条件。
3. 参数调整与优化一旦模型的参数化设计完成,工程师就可以方便地调整模型的各个参数,来实现对零部件的尺寸和结构的快速优化。
通过改变零部件的长度和宽度参数,来实现不同尺寸的模型的快速切换。
又或者通过调整孔的直径参数,来实现不同规格的零部件的快速修改。
这种快速调整和优化的能力,大大提高了设计效率和灵活性。
4. 参数化设计的优势通过参数化设计,工程师可以快速构建复杂的模型,并且可以方便地应对后续的变更需求。
另外,通过参数化设计,可以轻松地生成不同规格的零部件模型,并且可以准确地预测不同参数取值下的零部件性能和成本。
这种能力对于快速响应市场需求和提高产品竞争力具有重要意义。
5. 参数化设计在实际应用中的注意事项在实际应用中,需要注意以下几点:- 合理选择参数:需要根据零部件的实际特性和设计需求,选择合适的参数进行设计。
solidworks的拔模实例
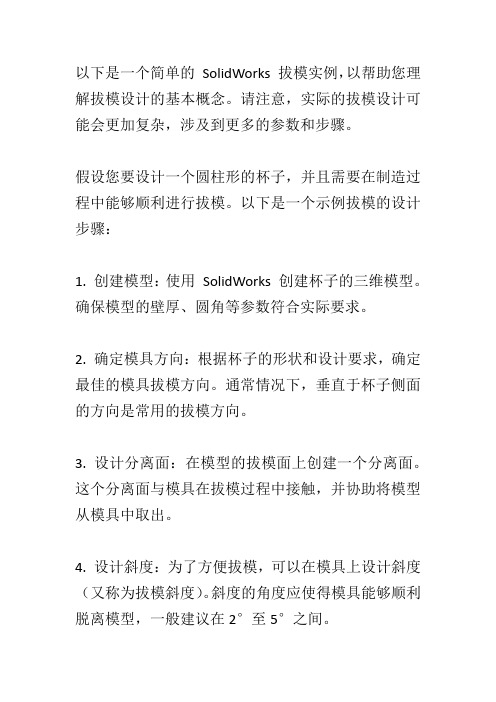
以下是一个简单的SolidWorks 拔模实例,以帮助您理解拔模设计的基本概念。
请注意,实际的拔模设计可能会更加复杂,涉及到更多的参数和步骤。
假设您要设计一个圆柱形的杯子,并且需要在制造过程中能够顺利进行拔模。
以下是一个示例拔模的设计步骤:1. 创建模型:使用SolidWorks 创建杯子的三维模型。
确保模型的壁厚、圆角等参数符合实际要求。
2. 确定模具方向:根据杯子的形状和设计要求,确定最佳的模具拔模方向。
通常情况下,垂直于杯子侧面的方向是常用的拔模方向。
3. 设计分离面:在模型的拔模面上创建一个分离面。
这个分离面与模具在拔模过程中接触,并协助将模型从模具中取出。
4. 设计斜度:为了方便拔模,可以在模具上设计斜度(又称为拔模斜度)。
斜度的角度应使得模具能够顺利脱离模型,一般建议在2°至5°之间。
5. 添加剥离角:在模型底部或需要添加剥离角的位置,添加一个斜面以帮助模具脱离。
剥离角度的大小取决于材料和表面要求。
6. 模具设计:基于以上设计参数,使用SolidWorks 创建包含拔模方向、分离面、斜度和剥离角的模具结构。
7. 检查干涉:进行干涉检查,确保在拔模过程中没有任何零件之间的干涉。
8. 制造模具:根据设计好的模具结构进行制造,并进行试模验证。
9. 进行拔模测试:使用制造好的模具进行拔模测试。
确保模具能够正常脱离杯子模型,并且不会损坏模型和模具。
需要注意的是,拔模设计是一个复杂的过程,涉及到材料特性、模具制造技术和实际工艺等因素。
上述步骤仅为一个简单示例,实际应用中可能需要更复杂的设计和优化。
建议在实际设计中,结合相关资料和经验,并进行多次测试和调整,以确保拔模顺利进行。
]基于SolidWorks的锥齿轮精锻模具设计
![]基于SolidWorks的锥齿轮精锻模具设计](https://img.taocdn.com/s3/m/0263ac84a0116c175f0e48c7.png)
基于SolidWorks的锥齿轮精锻模具设计锥齿轮精锻工艺是指模锻齿轮时轮齿直接被锻出,齿面不再进行切削加工的精密模锻工艺。
锥齿轮广泛应用于汽车、拖拉机、摩托车、坦克等的差速器中,应用面广,需求量大。
用传统机械切削方式生产锥齿轮,速度慢、效率低、精度差。
锥齿轮的热精锻成形技术已基本成熟,但在冷锻闭式成形技术方面,还有待进一步地改进和提高,采用冷精锻方法成形零件,可节约原材料,提高零件的力学性能,并能获得理想尺寸精度和表面粗糙度的制件,是一种高产、优质、低消耗的工艺技术,其经济效益十分可观?。
但也存在变形抗力大,对模具和设备要求较高等问题。
因此对锥齿轮冷精锻工艺及模具进行设计和分析十分必要的。
三维CAD系统有较好的造型工具,能实现"自顶向底"和"自底向顶"等设计方法,实现装配等复杂设计过程,使设计更加符合实际设计过程;三维造型系统能方便地与CAE系统相连,进行仿真分析;能提供数控加工所需的信息,实现CAD/CAE/CAPP /CAM的集成。
基于三维CAD系统这些优点,本文利用SolidWorks三维设计软件来完成锥齿轮及其模具的设计。
l 锥齿轮精锻成形工艺冷精锻是随着汽车工业而迅速发展起来的一种净成形工艺。
精锻锥齿轮有连续的沿齿廓合理分布的金属流线和致密的组织,轮齿的强度、齿面的耐磨能力、热处理变形量和啮合噪声等都比切削齿轮的加工优越。
齿轮材料为中高强度合金钢20Cr,其供应状态强度高、变形抗力大、塑性较差,存在加工硬化现象,难以进行大变形量的冷模锻成形。
但若对毛坯进行充分软化退火处理,就可降低变形抗力和提高材料塑性指标。
精锻锥齿轮的强度和抗弯疲劳寿命提高,热处理变形减少,生产成本降低。
综上分析,决定采用冷锻成形工艺。
其工艺过程为:下料一退火叶冷锻一精加工一检验一入库。
冷锻成形前,要对坯料进行软化处理,在各道工序之间要进行退火处理,在冷锻前进行磷化处理。
2 模具设计2.1 锻件根据锥齿轮零件图及冷模锻工艺的基本要求,设计了齿轮锻件。
solidworks案例例题

solidworks案例例题
以下是一个SolidWorks设计案例的例题:
设计一个简单的工具箱,包括两个引出把手的抽屉和一个可抬起的顶盖。
工具箱尺寸为300mm(长)x 200mm(宽)x
150mm(高)。
抽屉内部尺寸为250mm(长)x 180mm(宽)x 100mm(高),抽屉前部有一个12mm宽的拉手孔。
请使用SolidWorks设计软件进行如下操作:
1. 创建一个新的零件文件。
2. 绘制一个300mm x 200mm的矩形,作为工具箱的底部。
3. 创建一个300mm x 150mm的矩形,作为工具箱的顶盖。
4. 绘制两个250mm x 180mm的矩形,分别作为两个抽屉的底部。
5. 在每个抽屉底部上创建一个12mm x 50mm的矩形拉手孔。
6. 创建一个150mm x 200mm的矩形,作为一个抽屉的前面板。
7. 将前面板与抽屉底部合并为一个零件。
8. 将前面板复制一份并旋转90度,得到另一个抽屉。
9. 将工具箱底部与两个抽屉合并为一个零件。
10. 使用“凸起”功能将顶盖零件添加到工具箱。
11. 对工具箱进行细节设计,例如添加圆滑边和倒角。
12. 导出工具箱的三维模型文件。
请根据以上要求完成SolidWorks设计,并在最后导出一个三
维模型文件。
用Solidworks建模的冲压模具设计(含图片预览

1. 零件工艺性分析 (2)2. 冲压工艺方案的确定 (2)3. 排样方式及材料利用率 (2)4. 模具结构形式合理性分析 (3)5. 模具主要零件形式、材料的选择、公差配合、技术要求的说明 (5)6. 凸、凹模工作部分尺寸与公差 (9)7. 压力中心计算、弹性元件的选用及计算 (13)8. 冲裁力计算、设备类型及吨位的确定 (14)9. 小结 (16)10. 参考文献 (16)1. 零件工艺性分析:该零件为连接片,材料较薄,主要用于零件之间的连接作用。
零件外 形轴对称,有圆弧段,系典型的板料冲裁件,材料为15钢,板厚1mm冲裁件孔与孔、或孔与边缘的间距 b 、bl ,符合b>1.5t ,b1>t 。
根据 设计图纸可知,采用典型的冲孔模和落料模工艺,来达到一定的精度要求。
根据要求,采用冲裁落料复合模的正装形式。
2. 冲压工艺方案的确定冲压性质:冲孔落料工序组合方式:采用冲孔落料模3.排样方式及材料利用率(2)复合模矩形薄凹模典型组合 :3]图1 — 79材料利用率为n = (d/A )x 100%=(8860.63/11386.32 ) X 100% =77.82 %4. 模具结构形式合理性分析(1)滑动导向模架结构型式[3]图2-73 a中间导柱的模架规格:单位:表1 — 286复合模矩形薄凹模典型组合尺寸:单位:mm 表1 — 304凹模周界L200件5 卸料板厚度1 16 B2006固定板厚度122 凸凹模长度 61号7 垫板厚度1 8配用模架闭 最小 2008螺钉6M12X 65合高度 H最大240和9 圆柱销件2 12 X 70S16410卸料螺钉612 X 55孔距S190名12螺钉6M12X 90S216413数2 12 X 90S390称14圆柱销212 X 601垫板厚度1 82固定板厚度1203空心垫板厚度件 数1 184凹模厚度118s I* •井——-k …曲• ©(3)合理性分析各板厚之和=8+20+18+18+16+22+8= 110各板厚之和+hl +h 2 +1 = 110+45+50+1= 206H MA= 240 H M IN= 200/. H MAX>206> H M IN即合理5. 模具主要零件形式、材料的选择、公差配合、技术要求的说明(1) 导柱和导套导柱和导套都加工方便,容易装配,是模具行业应用最广的导向装置。
solidworls模具设计案例

solidworls模具设计方法
以照相机壳为例:
先插入模具设计工具栏,方便模具设计使用.点击视图/工具栏/模具工具。
1.将零件导入Solidworks中进行拔模分析.
拔模分析
2.然后对肋板进行拔模;
对肋板进行拔模
3.进行比例缩放,缩放倍数为1.05。
比例缩放4.建立分型线。
建立分型线5.对有孔的地方进行“关闭曲面”设置.
关闭曲面6.建立分型面.
分型面7.在分型面上画草图,根据上下模的整体形状来画。
在分型面上画草图
8.退出草图,并同时选中特征栏里的分型面和草图,点击“切削分割”,完成磨具设计.
进行切削分割
9.完成模具设计,在“实体"栏里有“切削分割实体",右击可进行“孤立"和“插入新零件"操作,看或者生产上下模实体.
完成模具设计。
solidworks汽车壳体曲面建模实例教程

本节详细讲了solidworks曲面建模实例汽车壳体的绘制过程以及注意事项等内容。
在SolidWorks中利用三视图进行汽车建模的一般方法是:首先将汽车视图分别导入到相应基准面作为草绘的参考,然后找到各视图中对应的轮廓线,进行投影形成空间曲线,最后进行放样等操作。
限于篇幅,本文将以audi R8为例介绍汽车壳体建模的大致过程。
一、建模前的图片准备首先利用图片处理软件(如PhotoShop)对图片进行必要的裁剪,将图片以主视图、左视图及俯视图的形式进行裁剪,并分别保存为单独的图片文件,以便后续的操作。
二、汽车壳体建模1.打开SolidWorks软件单击“开始”→“所有程序”→“SolidWorks 2009”→“SolidWorks 2009 x64 Edition SP3.0”→“SolidWorks 2009 x64 Edition SP3.0”,打开软件或双击桌面快捷图标打开软件。
1)单击“新建”按钮,如下图所示:2)在弹出的“新建Solidworks文件”对话框中单击“零件”按钮,然后单击“确定”按钮,如下图所示:2.导入汽车图片1)在上视基准面新建草图,然后单击“工具”→“草图工具”→“草图图片”,在弹出的对话框中选中“俯视图”图片,单击“打开”按钮,如下图所示,图片将显示在上视基准面中。
2)拖动鼠标,将图片移动到中心位置,并调整合适的大小,单击“确定”按钮完成图片调整.为了定位准确,可以在上视基准面参考图片大小,绘制一个矩形,标注合适的尺寸,完成汽车图片的导入。
可能需要反复调整图片的大小及矩形的大小,最终达到类似于图4的效果,单击右方角的按钮退出草图。
(在调整过程中,可随时双击图片,激活它以调整大小和位置。
)同理,分别在前视基准面和右视基准面插入主视图和左视图,调整到合适的大小及位置。
插入图片的效果如下图所示。
3.车壳建模1)在前视基准面上新建草图,用"样条曲线"命令沿汽车轮廓绘制曲线,如下图所示:2)单击曲面工具栏中的“拉伸曲面”按钮,拉伸长度为10mm的曲面,如下图所示。
solidworks仿真simulation实例.

一、范例名:(Lifter升降机构)1 设计要求:(1)输入转速1500rpm。
(2)额定提升载荷2000N。
2 分析零件该升降装置中,蜗杆、蜗轮是传动装置,本体零件是主要的承载部分。
因此,这里对本体零件进行静力分析。
3 分析目的验证本体零件在给定的载荷下静强度是否满足要求。
4 分析结果按书中尺寸建立模型,零件体积为68.7cm3。
材料选用可锻铸铁,极限应力275.7MPa。
根据零件的工作情况,对该零件进行静力分析,结果如图1-9 所示。
模型的最大von Mises 为62.1MPa,零件的安全系数约为4.4。
图1-9 本体零件应力云图5 零件改进由零件的应力云图可以看出,零件上的最大应力为62.1MPa,零件上应力小的部分比较多,同时考虑零件的结构,如钻螺纹孔,可以对这些部位减小尺寸,从而减轻零件的质量。
除了减小了零件的厚度外,还更改了模型上加强筋结构的尺寸和结构。
改进后零件的体积为60cm3对改进后的模型运行静力分析,结果如图1-10 所示:最大von Mises 为120.5MPa,安全系数约2.3。
图1-10 改进模型应力云图6 成本节约模型原来的体积为68.7cm3,改进后的模型的体积为60cm3,体积减少了8.7cm3,每件减少的重量为63.5g,如果生产10000 件,那么总共可节省材料635kg,以当前可锻铸铁的市场价格为10000 元/吨,那么可以节省6350 元。
二、范例名:(Gas Valve气压阀)1 设计要求:(1)输入转速1500rpm。
(2)额定输出压力5Mpa,最大压力10Mpa。
2 分析零件该气压泵装置中,推杆活塞、凸轮轴和箱体三个零件是主要的受力零件,因此对这三个零件进行结构分析。
3 分析目的(1)验证零件在给定的载荷下静强度是否满足要求。
(2)分析凸轮轴零件和推杆活塞零件的模态,在工作过程中避开共振频率。
(3)计算凸轮轴零件的工作寿命。
4 分析结果1.。
推杆活塞零件材料:普通碳钢。
solidworks注塑件实例

solidworks注塑件实例我们需要创建一个新的SolidWorks零件文件。
在打开SolidWorks 后,选择“新建零件”选项,然后选择适当的单位和尺寸。
接下来,我们可以开始设计注塑件的外形。
在SolidWorks中,我们可以使用多种建模工具来创建注塑件的几何形状。
例如,我们可以使用绘图工具创建草图,并通过拉伸、旋转和剪切等操作将草图转换为三维模型。
我们还可以使用曲面建模工具来创建复杂的曲面形状。
在设计注塑件时,需要考虑到材料的流动性、收缩率和模具的脱模性。
为了更好地模拟注塑过程,SolidWorks提供了注塑模拟功能。
通过设置注塑模拟参数,我们可以预测材料在注塑过程中的流动情况、气泡的形成和注塑件的变形情况。
这可以帮助我们在设计阶段发现潜在的问题并进行优化。
除了外形设计和注塑模拟,SolidWorks还提供了许多其他功能来辅助注塑件的设计。
例如,我们可以使用装配功能将多个注塑件组装在一起,并检查它们之间的间隙和配合情况。
我们还可以使用绘图功能创建注塑件的工程图纸,并标注尺寸和注塑件的特征。
在SolidWorks中,我们还可以通过添加材料和应用材料属性来模拟注塑件的物理性能。
通过选择合适的材料,我们可以评估注塑件在不同负载条件下的强度、刚度和耐热性能。
这有助于我们选择最合适的材料并优化注塑件的设计。
在完成注塑件的设计后,我们可以使用SolidWorks生成三维打印文件或导出STL文件,以便进行快速原型制造或与其他软件进行兼容。
此外,SolidWorks还支持与其他CAD软件和CAE软件的集成,使设计团队能够更好地进行协作和数据交换。
总结起来,SolidWorks是一种功能强大的CAD软件,广泛应用于注塑件的设计。
通过SolidWorks,我们可以进行注塑件的外形设计、注塑模拟、装配和工程图纸制作等工作。
它提供了丰富的功能和工具,帮助设计师更好地进行注塑件的设计和优化。
使用SolidWorks 进行注塑件设计,不仅可以提高设计效率,还可以减少设计错误和成本。
Solidworks数控加工实例

Solidworks数控加工实例1、由于考虑铸模制造中产品存在收缩率的问题,运用【比例缩放】工具进行缩放模型,缩放比例为1.05。
2、运用【分割线】工具,以右视面为基准将面分为两部分,一部分作为公模参照,一部分作为母模参照。
3.3、运用【分型线】工具,以右基准面为基准,以第二步分割线构造成面设置分型面4、运用【分型面】工具,设置分型面,并设置扩展距离为250mm。
5、运用【切削分割】工具,创建模具并设置公模、母模高度均为250mm。
6、由于Solidworks无数控加工模块,故挑选母模进行数控加工仿真,其中公模类似加工。
将母模导入Pro/E中进行数控仿真,并保存母模模型文件为mumo.prt。
7、在ProE中选择【新建】来新建NC制造文件,文件名为:mumonc,并使用mmns_mfg_nc模板。
8、点击【装配参照模型】,并选择mumo.prt从而载入制造单元,并运用缺省操作将制造单元固定。
9、点击【自动工件】,创建矩形工件并设置矩形工件尺寸。
10、选择【步骤】-【操作】进行机床设定。
机床使用默认的三轴联动机床,机床类型为铣削;机床零点设置为矩形工件的一角并调整X、Y、Z坐标方向;退刀面设置在离工件表面上10mm处。
11、选择【端面铣削】进行工件上表面铣削,使此次加工至母模上表面。
刀具参数:刀具号1、名称T0001、类型为端铣削、材料为HSS、单位为毫米、凹槽编号为4,直径为25mm、长度为100mm;切削进给为200,跨度为5,安全距离5,主轴转速600。
得到刀具轨迹如下图:12、选择【轮廓铣削】进行工件外形轮廓的加工,加工至母模外侧面。
类似于上述设定,刀具参数:刀具号2、名称T0002、类型为端铣削、材料为HSS、单位为毫米、凹槽编号为4,直径为30mm、长度为300mm;切削进给为60,步长深度为3,安全距离5,主轴转速800。
得到刀具轨迹如下图:13、选择【体积块粗加工】加工母模内凹面。
SolidWorks模具设计案例

拔模分析
相关定义
正拔模:指面的角度相对于拔模角度大 于参考角度。
负拔模:指面的角度相对于拔模方向小 于负参考角度。
需要拔模。显示需要校正的任何面。这 些为成一角度的面。此角度大于负参考 角度但小于正参考角度。
跨立面。显示同时包含正拔模和负拔模 的任何面。通常,这些为需要您生成分 割线的面。
添加拔模
重新进行拔模分析
缩放比例
生成分型线
关闭曲面
生成两个无任何通孔的完整曲面(一型心曲面和一型腔 曲面),将模具分割成上摸和下模。关闭曲面关闭通孔。
Hale Waihona Puke 闭曲面生成分型面分型面:拉伸自分型线,用于将模具型腔从型心分离开来。
制作基准面
切削分割
观看结果
- 1、下载文档前请自行甄别文档内容的完整性,平台不提供额外的编辑、内容补充、找答案等附加服务。
- 2、"仅部分预览"的文档,不可在线预览部分如存在完整性等问题,可反馈申请退款(可完整预览的文档不适用该条件!)。
- 3、如文档侵犯您的权益,请联系客服反馈,我们会尽快为您处理(人工客服工作时间:9:00-18:30)。
SolidWorks模具设计案例SolidWorks的模具工具已存在许久,但因为默认值的关系,想必有多数使用者可能还不知道SolidWorks本身就有模具的工具吧。
而本章节除了是要让读者们能知知道有这样的工具之外,同时也为模具工具做了一些说明,希望这一篇能为各位带来显著的学习效果。
单纯只讲模具的话,这所牵扯的围有些广泛,因此笔者将围与应用的部分缩小至塑料模具的部分。
会特别这样说明是因为SolidWorks的模具工具还可应用在铸造模具上,如果跳脱模具工具这四个字而将其他工具一并纳入,那么又可以涵盖到冲压模或是连续冲压模具。
图1 模具设计当我们呼叫出模具工具时,可以看到几个主要的功能,像是缩放(缩水率)、分模线、模具分割…等,除此之外还可以看到几个曲面的工具在这其中(图2)。
曲面工聚会放置在模具工具中有一个主要的因素,SolidWorks中的模具功能会使用到大量的曲面功能,也就是说,当我们使用模具的功能时,会有部分的指令其实是在执行产生曲面的相关动作,因此,为了面对各种不同的产品、模具需求,因此会需要使用到曲面的工具来辅助。
图2 模具工具接下来将会以一个例来为读者们介绍模具工具中的主要功能,曲面相关的工具则不在此篇探讨的围之,而主要的工具有『拔模分析』、『底切分析』、『分模线分析』、『拔模』、『缩放』、『插入模具文件夹』、『封闭曲面』、『分模曲面』、『模具分割』、『侧滑块』,工具栏中除了刚刚所提到的曲面工具之外,还可以看一个名为「分割线」的工具,尽管这一个工具并不列在这次的介绍中,但读者们可要好好记得与学习这一个工具,因为他能给你所想要的分模线位置。
拔模分析,此功能主要在于帮助我们了解模具在脱模的时候,是否会有倒勾的状况发生,或是帮我们了解哪些地方的拔模角度是不够的,底下就用比较简单且夸一些的角度来说明一下,上下个为公模具,而中间则为产品;图3的情况则是最佳的状况,脱模的时候就自然与产品有间隙并顺利脱模。
图4则是需要改善的状况,一般来说,模具的设计都会尽量给予角度,而此状况则是不足所需求的脱模角度。
图5则是最糟情况,这样的状况可是会让产品无法顺利从模具中脱模。
图3 拔模角度情况最佳状况图4 拔模角度需要改善图5 拔模角度最糟情况透过刚刚三图片,这便是拔模分析所要提供给我们检查的功能,让设计者在一开始就能知道那些地方是需要在修改的。
拔模分析使用起来相当简易,且对于模具设计的人来说是一个非常重要而不可或缺的工具,大多数的情况之下,只要使用一般的检查就可以(图6),检视上很简单,模具是公、母模仁两个主要构成,而图面中的绿色与红色代表的就是个别的模仁,这里我并不会特别去说明公、母模是哪个颜色,因为这可以对调,只要了解模仁所搭配的颜色中,没有其他颜色在围里面即可,如果有,那就得视情况来决定是要修改模型,还是制作侧滑块、斜销。
图7的功能则是帮我们将复杂的产品,直接透过隐藏与显示的方式来抓出哪些地方是会倒钩还是不足拔模角度,。
图8则是透过手动的方式来检视;由于前两个设定只能针对单一的脱模方向来检查,而这个设定可以动态调整并且实时显示,如此一来我们就可以清楚的知道要以哪个方向作为我们的脱模方向了。
图6 拔模分析一般检查图7 复杂产品检查图8 手动检查底切分析,这个功能主要就是协助我们将公母模仁无法直接成形的位置抓取出来,像这样的地方一般来说就是要制作侧滑块或是斜销了。
由图9来看,同样设定上基准面来做为脱模方向,这时模型所显示的外观会与刚刚的拔模分析不太一样,而这边我们主要要注意的地方就是有出现红色的位置,这些地方就是我们要制作滑块的位置了。
图9 底切分析分模线分析,这个功能有些特别,主要运用于造型曲面且不好抓取分模线的产品,可以直接透过这一个功能将虚拟的分模线显示出来,图10中的紫色线条就是虚拟的分模线。
透过这样的方式,我们就可以直接以这一条线段为参考,然后在将实际的分模线位置透过其他工具分割后取得。
图10 分模线分析拔模,这个工具主要是将不足所需求的拔模角度直接进行修正(图11),图片中是两个边长50mm的正方形,经过拔模功能修正之后,会依照设定的角度与拔模方向给予变化,因此在使用上必须要特别注意,而通常指定为中立面的位置,最后是不会因为拔模面的关系而影响到既有的面积围,建议还未了解此功能所造成的影响之前,先透过简单的几何来进行练习,如图中的正方形,就是一个很容易理解的方式。
图11 拔模缩放,此功能若是直接翻译成缩水率,想必大家应该都能马上理解这一个功能,但因为缩放不只能应用在模具上,所以就以较能通用的名词来使用。
无论是铸造或是塑料射出,基本成形原理都是将原料热熔之后再注入模穴中来冷固成形,而根据物质「热胀冷缩」的原理,成品在冷固成形之后的尺寸会因此而缩小,因此我们在整个模具的设计开端就必须要先给予一个比例来放大,这样最后在冷固成形时才会把尺寸缩小回来到正确的尺寸。
依照材料、产品大小与复杂程度不同,所需要给予的比例不尽相同,而此例中所给予的1.06所代表的是百分之6,也就是放大6/100,不过常见的比例并非是百分比,而是千分比,只是SolidWorks 会自动地将小数值末的0值自动删除,因此就已百分比来做表示。
产品如果因外型关系而造成收缩不等比例,那么便可以取消一致缩放来个别为不同的轴向予不同的缩水率。
(图12)(图13)图12 缩放设置图13 轴向缩放分模线,模具工具最重要的一个功能,也就是抓出公母模区分的一条线段,当然,前提是不需要补破孔;一般来说,分模线是一条封闭的循环,而绝大多数都是直接以模型的边界作为分模线,如果复杂度不高,通常都能很快的自动完成分模线的工作(图14、15),假如模型外观上没有需要的边线可作为分模线的选取,那么就必须要透过分割线的功能将需要的边界自行切割出来(图16),这样的话我们就可以透过手动选取的方式来完成分模线的工作。
分模线还有另一个小功能可以尝试一下,那就是勾选「分模面」的选项,透过这一个功能,我们可以将模型要制作分模线的位置上自动给予分割的指令,然后就可以直接点选分割出来的边线作为分模线。
(图17)图14 分模线功能图15 分模线图16 分割线自行切割分模线图17 「分模面」封闭曲面,当面临到产品有贯穿孔、排气孔之类的孔洞,这时如果要顺利使用SolidWorks 来完成模具的话,那就必须要使用到封闭曲面这样的功能。
在封闭的过程中,对于封闭、填补的类型可以依照产品外型另外调整,以图18为例的缺口状况,我们可以选择相切或是接触的填补类型(图19);选择接触的话,缺口的地方会直接不考虑任何状况填补起来(图20),而设定相切的话,缺口则是会依照边界相邻的面来进行相切的填补(图21)。
封闭曲面还有一个功能是大家比较少再使用的,那就是无填补;无填补的功用主要在于将选取的边界直接切断,透过这样的方式,我们就可以自由的建立需要的填补外型,而不受限于既有的模型外观(图22)。
图18 缺口模型图19 填补类型设置图20 直接添补图21 相切填补图22 无填补分模曲面,这一个功能在使用之前,一定要确定分模线的功能是否有完成,而且还得确定是否有错误的惊叹号,如果有的话,则代表的是该分模线并非是一个完整的封闭循环,那就必须要重新编辑来检查。
分模曲面在使用时最怕遇到的就是像图23的边线,这样的边线很容易让产生的曲面错乱,即便是没有严重的错乱,产生的曲面基本上也会呈现不太规则的样子,这会让后端的加工花上不少时间来处理这一小部分。
分模曲面会错乱的问题一直都存在,但是在SolidWorks2013开始有了不一样的变化,透过简单的设定,就能让这样的问题严重性降低,甚至是没有(图24),当我们从上视图来检视的时候,可以发现节点的变化几乎是沿着单一方向前进,这让原本错乱的问题大幅的改善(图25)。
分模曲面有针对起模方向的设定(图25),绝大多数我们是以第三个的垂直于起模方向为主要设定,除非考虑到分模曲面与产品的外观所连接的位置是否会影响到最后成品,不然大多还是以垂直余起模方向为主。
图23 边线图24 没有曲面错乱图25 起模方向的设定模具分割与插入模具文件夹,当我们把前面的几项流程都完成之后,我们就可以将模仁的草图绘制上去,然后再使用模具分割来将公母模仁各自拆出。
在绘制草图时,必须要以刚刚的分模曲面为参考,参考他的边界围来绘制需要的草图围,从这边也可以发现的是,在产生分模曲面的时候,尽量让产生的曲面围扩大,好让现在所要绘制的草图能够在这围之(图26),这样的考虑是因为分模具分割的功能主要是藉由曲面的与分割的功能来搭配进行,因此草图的围有任何一个地方小过于曲面的边界,那么模具分割就一定会失败。
图26 模具分割完成了草图的绘制并执行模具分割的功能之后,我们便可在属性管理员中看到几项重要的项目,分别是模块尺寸、公模、母模、分模曲面(图27)。
模块尺寸建议配合3D视图来进行调整(图28),好让我们可以不至于浪费过多的料。
而另外三个,公模、母模、分模曲面,这主要是告诉我们模具分割的功能有抓取到我们刚刚在前置作业中所产生的公、母模曲面与分模曲面,这三个曲面本体;会因为我们再产生分模线的时候就出现公母模曲面,需要填补孔的话,则是在完成填补孔的时候才会出现公母模曲面,而分模曲面就是分模曲面功能完成之后才会有的。
图27 属性管理员图28 3D视图从图29中我们可以看到曲面本体文件夹中,还有另外三个文件夹,分别是公母模、与分模曲面文件夹,这些文件夹大多是经由模具工具而产生的,而当我们面临需要自行制作模具分割所需要的相关曲面时,这时我们就可以执行插入模具文件夹的功能来产生这三个文件夹,届时完成曲面的建立之后再直接拖曳到该文件夹中即可完成(图30)。
另外要注意的就是,尽管完成了三个模具分割需要的曲面,但只要后续有针对其中一个曲面进行其他特征的编辑,那么该曲面就会脱离模具文件夹,这时就只要重新拖曳曲面到所属文件夹即可。
图29 曲面本体文件夹图30 模具分割侧滑块,首先可以经由底切分析工具来了解产品中有那些地方是需要制作侧滑块,而侧滑块的功用就如一开始在底切分析中所说明的,只要是无法透过公母模仁完成的位置,我们就是要制作侧滑块的时候了。
以图31为例,产品的的底端有一些排气孔,而这些地方是无法直接透过公母模来完成,所以得制作一个侧滑块让我们能往公母模脱模的方向之外来抽离。
图31 侧滑块先将模具还原到尚未完成侧滑块的样子来检视一下(图32),很明显可以看到底端的位置因为排气孔的设计关系,这里有几个像是肋条的外型,这个地方就是我们要制作侧滑块的位置。
由于模仁外部的面几乎都是平坦面,因此我们直接将草图建构于此就可以了,至于草图该绘制甚么样轮廓,这个就得依照实际需求来改变,但一个重点就是,不要再草图上绘制圆角,最好是在完成侧滑块之后再直接给予圆角特征,这样才回不造成圆角的变形(图33)。