{最新文档}炼焦工序能耗
关于炼焦工序能耗标准的建议

炼焦生产物料平衡图
炼焦主要产品产率图(重量百分比%)
煤焦油 3.5% 焦炉煤气 17%
焦碳 焦炉煤气 煤焦油 粗轻苯 氨 化合水 其他
粗轻苯 1.1%
氨 0.3%
化合水 1.6%
其他 1%
焦碳 75%
4-2能量守恒
4-2.1炼焦热平衡
4.2.2焦炉炼焦热平衡表
收入 序 号 1 2 3 4 5 6 符 号 Q1 Q2 Q3 Q4 Q5 Q6 项目 加热煤气燃烧热 加热煤气显热 泄露荒煤气燃烧热 空气显热 干煤显热 配煤水分显热 数值 kJ/t % 1 2 3 4 5 6 7 8 9 10 Q ’1 Q ’2 Q ’3 Q ’4 Q ’5 Q ’6 Q ’7 Q ’8 Q ’9 Q’10 焦炭显热 煤焦油潜热和显热 粗苯潜热和显热 氨显热 净煤气显热 水气潜热和显热 废气显热 不完全燃烧热 炉体表面散热 误差 序号 符号 支出 项目 数值 kJ/t %
二.炼焦生产能耗计算必须遵守的原则
炼焦生产是十分典型的能源再加工过程 和热能的再回收利用过程,既生产重要的能 源产品(焦炭、炼焦煤气),又生产多种煤 化工产品(焦化苯类、煤焦油)等含热能较 高的重要化工资源。 ----必须遵照《物质守恒、能量守恒》的原则
2-1物质守恒—重量转化差
以2006年协会对部分会员单位的有关情 况统计看:
能源消耗总量包括以下各项: ①从投料到制成 产 品的整个生 产过 程,直接用于 该产 品的原料、燃料、 动 力和工 艺 用的 一 次能源 和二次能源; ②分摊在该产品的辅助生产系 统和附属生产系统消 耗的一次能源和二次能源; ③分摊在该产品的企业内部的亏损能源; ④次品和废品所消耗的一次能源和二次能源。 不包括下列各项: ①非工业生产用能源,如基本建设、生活用能源; ②各种余热、余气的回收利用及工业废渣的利用。
3能耗指标体系的分类计算

能耗指标体系的分类钢铁企业能耗指标主要有吨钢综合能耗、吨钢可比能耗、主要产品的工序能耗、主要产品的实物单耗(如炼铁焦比、炼焦煤耗等)以及产值能耗、增加值能耗等等。
能源分析评价指标中,包括企业内部能源加工转换指标和企业损失指标。
按钢铁企业能耗经济技术指标体系可分为:(1)企业级能源技术经济指标:如吨钢综合能耗、万元产值能耗、吨钢耗新水、吨钢电耗、损失率等。
(2)工序级能源技术经济指标:如炼钢工序能耗、炼铁工序能耗等。
(3)耗能设备级能源技术经济指标:加热炉燃耗、高炉焦比、制氧机电耗等。
按钢铁企业能效对标指南中能耗指标体系可分为:(1)综合性指标:如企业级能源消耗总量、工序级能源消耗总量、各类能源介质消耗总量、企业能源亏损量等指标。
(2)单耗性指标:如吨钢综合能耗、企业吨钢可比能耗、工序单位产品能耗。
(3)经济性指标:万元产值能耗、万元增加值能耗等。
2.能耗指标的范围及计算钢铁制造流程是由多个不同的生产工序组成的,前一道工序的产品为下一道工序的原料,这是钢铁工业的特点,由于其复杂性,因此,统计范围和指标定义必须规范,以便于对标,找出节能潜力,提升企业效益。
(1)吨钢综合能耗范围及计算综合能耗是规定的耗能体系在一段时间内实际消耗的各种能源实物量按规定的计算方法和单位分别折算为标准煤后的总和。
吨钢综合能耗(comprehensive energy consumption ):吨钢综合能耗是企业生产每吨粗钢所综合消耗的各种能源自耗总量;也就是每生产一吨钢,企业消耗的净能源量。
其计算公式为:吨钢综合能耗=企业钢产量企业自耗能源量(吨标准煤/吨钢,千克标准煤/吨;tce/t ,kgce/t )式中,企业自耗能源量即报告期内企业自耗的全部能源量。
统计上报按企业全部耗能量。
企业自耗能源量= 企业购入能源量 ± 库存能源增减量 - 外销能源量= 企业各部位耗能量之和 + 企业能源亏损量作为行业对标,吨钢综合能耗的统计范围可按照企业生产流程的主体生产工序(包括原料储存、焦化、烧结、球团、炼铁、炼钢、连铸、轧钢、自备电厂、制氧等动力厂)、厂内运输、燃料加工及输送、企业亏损等消耗能源总量,不包括矿石的采、选工序,也不包含炭素、耐火材料、机修、石灰、精制及铁合金等非钢生产工序的能源消耗量。
炼焦工序

炼焦工序能耗的计算方法目前,我国焦化工序能耗出现较大差异,钢铁行业要用科学发展观来对其进行分析,对于焦化工序能耗所表现出的先进值和落后值,应当科学分析其背后隐藏的原因,并严格按照2004年中国钢铁工业协会公布的《中国钢铁工业生产统计指标体系指标解释》中关于“洗煤、炼焦、焦炉煤气处理及煤化工生产主要技术经济指标解释”来进行计算。
否则,焦化厂之间的能耗对比,以及与国外同行之间的对标活动就难以进行,不利于我国焦化工业节能降耗工作的开展和促进行业整体能耗的降低。
正确掌握能耗的科学计算方法焦化工序能耗是指生产1吨焦炭(干基)所消耗的能量,具体包括炼焦工序生产系统的备煤车间(不包括洗煤)和厂内原料煤的损耗,炼焦车间、回收车间(冷凝鼓风、氨回收、粗苯、脱硫脱氢、黄血盐)辅助生产系统的机修、化验、计量、环保等,以及直接为生产服务的附属生产系统的食堂、浴池、保健站、休息室、生产管理和调度指挥所消耗的各种能源实物量,扣除回收利用和外供的余热余能和二次能源,并将所有能源折成标煤。
在统计期内,将炼焦所用的原煤量(含生产过程中的亏损量)折算为千克标煤,称为E1;将炼焦过程中生产的焦炭(要包括焦粉、焦末)、焦炉煤气、粗焦油、粗苯等化学产品折算为千克标煤,可称为E2;将炼焦过程中所消耗的能量,包括所用的高炉煤气、焦炉煤气、水、电、蒸汽、压缩空气、氮气等物质,均按国家和行业统一的单位折标系数将上述各种能耗折算为千克标煤,并将这些数加在一起,可称之为E3;将炼焦过程中的余热回收,如干熄焦、焦炉煤气余热回收等折算为千克标煤,作为E4。
要注意,炼焦厂的焦炭产量(包括焦粉、焦末)要与使用部门核对,保持数据一致,这是因为厂际之间会有亏损量。
将焦炭总产量用K表示,它是指全部焦炭合格产出量(干基),则焦化工序能耗的定义可用下列公式表示:焦化工序能耗=(E1-E2 E3-E4)/K。
合理应对能耗指标可比性的影响因素2007年,我国重点钢铁企业炼焦平均煤耗为1388千克/吨焦,先进值为1267千克/吨焦,落后值为1472千克/吨焦。
工信部钢铁能耗标准
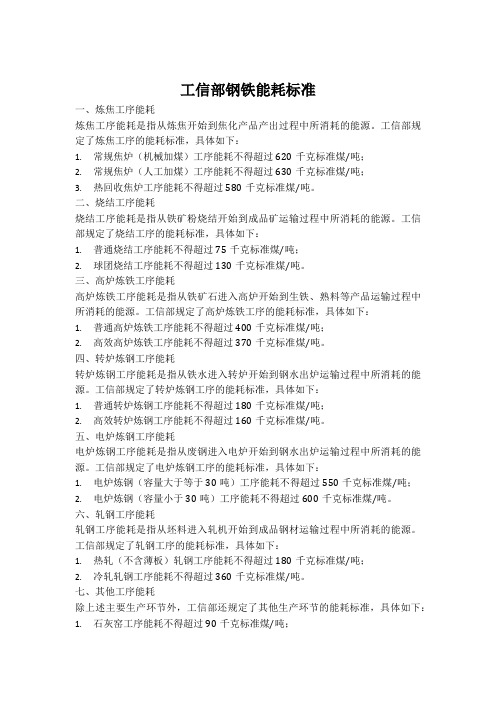
工信部钢铁能耗标准一、炼焦工序能耗炼焦工序能耗是指从炼焦开始到焦化产品产出过程中所消耗的能源。
工信部规定了炼焦工序的能耗标准,具体如下:1.常规焦炉(机械加煤)工序能耗不得超过620千克标准煤/吨;2.常规焦炉(人工加煤)工序能耗不得超过630千克标准煤/吨;3.热回收焦炉工序能耗不得超过580千克标准煤/吨。
二、烧结工序能耗烧结工序能耗是指从铁矿粉烧结开始到成品矿运输过程中所消耗的能源。
工信部规定了烧结工序的能耗标准,具体如下:1.普通烧结工序能耗不得超过75千克标准煤/吨;2.球团烧结工序能耗不得超过130千克标准煤/吨。
三、高炉炼铁工序能耗高炉炼铁工序能耗是指从铁矿石进入高炉开始到生铁、熟料等产品运输过程中所消耗的能源。
工信部规定了高炉炼铁工序的能耗标准,具体如下:1.普通高炉炼铁工序能耗不得超过400千克标准煤/吨;2.高效高炉炼铁工序能耗不得超过370千克标准煤/吨。
四、转炉炼钢工序能耗转炉炼钢工序能耗是指从铁水进入转炉开始到钢水出炉运输过程中所消耗的能源。
工信部规定了转炉炼钢工序的能耗标准,具体如下:1.普通转炉炼钢工序能耗不得超过180千克标准煤/吨;2.高效转炉炼钢工序能耗不得超过160千克标准煤/吨。
五、电炉炼钢工序能耗电炉炼钢工序能耗是指从废钢进入电炉开始到钢水出炉运输过程中所消耗的能源。
工信部规定了电炉炼钢工序的能耗标准,具体如下:1.电炉炼钢(容量大于等于30吨)工序能耗不得超过550千克标准煤/吨;2.电炉炼钢(容量小于30吨)工序能耗不得超过600千克标准煤/吨。
六、轧钢工序能耗轧钢工序能耗是指从坯料进入轧机开始到成品钢材运输过程中所消耗的能源。
工信部规定了轧钢工序的能耗标准,具体如下:1.热轧(不含薄板)轧钢工序能耗不得超过180千克标准煤/吨;2.冷轧轧钢工序能耗不得超过360千克标准煤/吨。
七、其他工序能耗除上述主要生产环节外,工信部还规定了其他生产环节的能耗标准,具体如下:1.石灰窑工序能耗不得超过90千克标准煤/吨;2.耐火材料及制品生产工序能耗不得超过450千克标准煤/吨;3.铁合金生产(包括硅系、锰系等)工序能耗不得超过580千克标准煤/吨。
加强炼焦管理降低工序能耗

年同期 比下降 1. 9 egt 由原来 第三 名跃居 全 国 4 7 ck/ , 同类型企 业的前列 ( 见图 1 。 )
1 7 40 2 13 9 78
l
_ 1 l
20 年 04
i 圈
圈
; .
2 0 年 06
厂, 焦化厂的工 序能耗 指 标是衡 量企 业 能源综 合利
3 降低 工 序能 耗 的途径
3 1 完 善 能源 管理 机制 , . 推行 目标 管理 模式
厂部健全与 完 善能源 管理 网络 , 全厂 的能 源 对 实施统一管 理。每 月制定 能 源计划 、 目标及 管理 考
类能耗指标都 有显 著 降低 , 年工 序能 耗指 标与 去 今
维普资讯
处 于受 控 状 态 。
减少 人煤水分 的波 动 , 好雨 季到 来前 的原 料储 备 做
工作 , 免潮料 或 杂料 直接 进料 仓 。由于各 矿点 煤 避 的结焦性能不 同, 分 、 分 的差 异 , 灰 硫 因此按 品种 合 理堆放 , 按贯标要 求 , 牌 一致 。取煤采 用 “ 点煤 物 定 堆, 回转 取煤 ” 行均 匀化 作业 。根据 不 同矿点 、 进 煤
3 2 精 细化 管 理 , 绝能 源浪 费 . 杜
3 2 1 保证进厂煤 的质量 .. 进厂煤 的灰份 、 、 硫 水分是 直接影 响购人 能源质 量 的重要指标 , 要保证进 厂煤 的数 、 质量 做法是 : 在质量上 , 场严 格按 公 司进 厂原 料验 收 规定 煤
种, 充分 发挥 4 k 焦 炉实 验 的作 用 , 确 定最 佳 0 g小 来
配 比方 案 , 在保 证焦炭质量 的前 提下 , 配用低价 格 的
13焦煤 、 / 瘦煤替代其他高价格煤种 , 降低原料成本 。
洗煤、炼焦及化学产品主要技术经济指标计算方法

洗煤、炼焦及化学产品主要技术经济指标计算方法一、洗煤(一)洗精煤灰分洗精煤灰分是指洗精煤所含灰分在洗精煤中所占重量的百分比。
其计算公式为:洗精煤灰分(%)= 洗精煤含灰分总量(吨)×100%洗精煤产量(干基)(吨)计算说明:洗精煤灰分由发货批料取样化验而得。
汇总时,各批料应按加权算术平均计算。
(二)洗精煤硫分洗精煤硫分是指洗精煤所含硫分在洗精煤中所占重量的百分比。
其计算公式为:洗精煤硫分(%)= 洗精煤含硫分总量(吨)×100%洗精煤产量(干基)(吨)计算说明:洗精煤硫分指标的计算可参照洗精煤灰分指标的计算说明。
(三)洗精煤回收率洗精煤回收率是指洗选后的精煤占入洗原煤总量的百分比。
其计算公式为:洗精煤回收率(%)= 洗精煤产量(含计价水)(吨)×100%入洗原煤总量(含计价水)(吨)(四)洗精煤耗原煤量洗精煤耗原煤量是反映每生产一吨洗精煤所耗用的原煤数量的指标。
其计算公式为:洗精煤耗原煤量(吨/吨)= 原煤耗用量(含计价水)(吨)洗精煤产量(含计价水)(吨)计算说明:原煤耗用量包括途耗、库耗等损耗在内。
(五〕洗精煤水分洗精煤水分是指洗精煤所含水分占洗精煤总量的百分比。
其计算公式为:洗精煤水分(%)= 洗精煤含水分总量(吨)×100%洗精煤量(实物量)(吨)计算说明:参照洗精煤灰分指标的计算说明。
(六〕浮选精煤耗药剂量浮选精煤耗药剂量是指每浮选1吨精煤所消耗的药剂数量。
其计算公式为:浮选精煤耗药剂量(千克/吨)= 药剂消耗总量(千克)浮选洗精煤总产量(含计价水)(吨)二、配煤(一)配煤比配煤比是指在报告期内所消耗各种煤量占配合煤总量的百分比。
其计算公式为:焦煤比(%)= 焦煤配入量(含计价水)(吨)×100%配合煤总量(含计价水)(吨)肥煤比(%)= 肥煤配入量(含计价水)(吨)×100%配合煤总量(含计价水)(吨)瘦煤比(%)= 瘦煤配入量(含计价水)(吨)×100%配合煤总量(含计价水)(吨)气肥煤比(%)=气肥煤配入量(含计价水)(吨)×100%配合煤总量(含计价水)(吨)1/3焦煤比(%)=1/3焦煤配入量(含计价水)(吨)×100%配合煤总量(含计价水(吨)其它煤比(%)= 其它煤配入量(含计价水)(吨)×100%配合煤总量(含计价水)(吨)(二)配合煤灰分配合煤灰分是指配合煤中所含灰分在配合煤总量中所占的百分比。
浅谈煤化工企业炼焦环节中的节能降耗

浅谈煤化工企业炼焦环节中的节能降耗云南曲靖麒麟煤化工曹国祥摘要:焦化产业既是高能耗、高污染产业,也是为下游行业提供二次能源和生产高价值化工产品原料的产业,同时肩负着节能减排的重要使命。
生产中应通过强化管理和优化工艺技术,进一步减少炼焦过程的能量转换损失、降低生产动力消耗和加强余热利用,从而达到降低炼焦工序能耗的目的。
关键词:炼焦工序;节能降耗;炼焦耗热量;余热利用;污水零排放引言随着《焦化行业准入条件》以及国家一系列宏观调控政策措施的深入贯彻落实,节能减排在焦化行业中得到高度重视,节能已经成为企业生存发展的重中之重。
尤其是在新的《中华人民共和国节约能源法》颁布和焦化行业执行《焦炭单位产品能源消耗限额》的标准以来,对该行业在能源管理和能耗水平上有了更高的要求。
本文从减少炼焦过程能源转换损失,降低炼焦耗热量,减少电力、蒸汽、水的消耗以及加强余热回收利用等方面探讨了炼焦工序的节能降耗。
一、减少炼焦过程中的能源转换损失1、加强物流环节的管理炼焦过程是能源转换过程,因此企业应该首先从精煤采购、运输、贮存及焦炭分筛、销售等物流环节加强管理,减少能源的损耗。
例如,精煤入厂质量要严格把关,满足企业工艺和配煤的要求;加强煤场管理,做到顺序用煤,防止煤料存放过久,氧化变质;贮煤场设置室内煤库或对露天贮煤场设置喷洒水设施,带式输送机输送采用密闭输煤通廊,减少途损。
2、减少炼焦煤消耗炼焦煤的消耗主要取决于配煤的结构和性质。
企业可以通过进行配煤成焦率实验,掌握真实的炼焦耗煤量,用以指导生产。
另外,通过严格计量、化验等环节,尽可能减少炼焦煤的损耗。
3、提高化产品产率焦炉煤气发生量和煤焦油、粗苯等化产品产率虽然主要取决于配煤的性质,但受生产操作及管理的影响也比较大。
在生产中应该严格执行各项煤气管理制度和规程,杜绝煤气泄漏及不合理放散;焦炉集气管压力采用先进的控制技术,通过鼓风机吸力的合理控制与调节,消除焦炉冒烟现象,最大限度地增加煤气发生量。
工业企业单位产品能源消耗指标计算方法

工业企业单位产品能源消耗指标计算方法(按统计局的统计口径计算)【选煤电力单耗】(千瓦时/吨)=100×选煤生产过程耗电量(万千瓦时)/入选原煤量(吨)分子项:选煤生产过程耗电量按电业部门结算的电量计算,不包括选煤厂向外转供电量,以及与选煤生产无直接关系的各种用电量(如居民生活用电、基建工程用电、文化福利设施用电等)。
分母项:入选原煤量指从入厂毛煤中拣出的不计原煤产量的大块(一般指50毫米以上)矸石后进入选煤过程,进行加工处理的原煤量。
无机碱制造(2612)【单位烧碱生产综合能耗】(千克标准煤/吨)=1000×液体烧碱综合能源消耗量(吨标准煤)/液体烧碱产量(折100%)(吨)分子项:烧碱综合能源消耗量是指用于烧碱生产的各种能源折标准煤后的总和。
包括烧碱生产工艺系统耗能量和为烧碱生产服务的辅助系统和附属生产系统耗能量。
烧碱生产系统耗能量的统计范围,从原料投入开始,包括盐水制备、整流、电解、蒸发、蒸煮至成品烧碱包装入库为止的所有工艺用的电解用交流电、动力用电、蒸汽、油、煤等实际消耗量。
烧碱生产的辅助和附属系统耗能量的统计范围包括:电槽修理、阳极组装、石棉绒回收、炭极加工、以及车间检修、车间分析、车间办公室、休息室、更衣室等各种耗能量。
分母项:烧碱产量折成100%计算。
氢氧化钠(烧碱)(折100%)包括由盐水电解法或由纯碱(或天然碱)苛化法生产的液体氢氧化钠。
也包括氢气干燥和本企业其他产品自用的合格烧碱。
不同方法生产的各种烧碱,经检验符合国家标准(GB209-93),方可统计产量。
产量中不包括在使用烧碱过程中回收的烧碱和生产烧碱过程中自用的电解碱液、浓缩碱液、回收盐液中的含碱量。
企业填报烧碱产量,应将不同的生产方法(水银法、隔膜法、离子膜法、苛化法)生产的液碱折成100%计算产量。
【单位烧碱生产耗交流电】(千瓦小时/吨)=100×交流电消耗量(万千瓦时)/液体烧碱(100%)产量(吨)分子项:交流电消耗量以电业局安装的直流耗交流电度表为准。
工业企业单位产品能源消耗指标计算方法
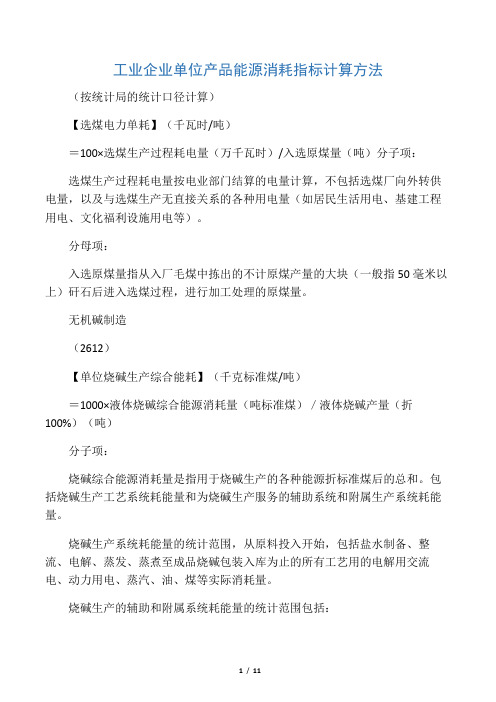
工业企业单位产品能源消耗指标计算方法(按统计局的统计口径计算)【选煤电力单耗】(千瓦时/吨)=100×选煤生产过程耗电量(万千瓦时)/入选原煤量(吨)分子项:选煤生产过程耗电量按电业部门结算的电量计算,不包括选煤厂向外转供电量,以及与选煤生产无直接关系的各种用电量(如居民生活用电、基建工程用电、文化福利设施用电等)。
分母项:入选原煤量指从入厂毛煤中拣出的不计原煤产量的大块(一般指50毫米以上)矸石后进入选煤过程,进行加工处理的原煤量。
无机碱制造(2612)【单位烧碱生产综合能耗】(千克标准煤/吨)=1000×液体烧碱综合能源消耗量(吨标准煤)/液体烧碱产量(折100%)(吨)分子项:烧碱综合能源消耗量是指用于烧碱生产的各种能源折标准煤后的总和。
包括烧碱生产工艺系统耗能量和为烧碱生产服务的辅助系统和附属生产系统耗能量。
烧碱生产系统耗能量的统计范围,从原料投入开始,包括盐水制备、整流、电解、蒸发、蒸煮至成品烧碱包装入库为止的所有工艺用的电解用交流电、动力用电、蒸汽、油、煤等实际消耗量。
烧碱生产的辅助和附属系统耗能量的统计范围包括:电槽修理、阳极组装、石棉绒回收、炭极加工、以及车间检修、车间分析、车间办公室、休息室、更衣室等各种耗能量。
分母项:烧碱产量折成100%计算。
氢氧化钠(烧碱)(折100%)包括由盐水电解法或由纯碱(或天然碱)苛化法生产的液体氢氧化钠。
也包括氢气干燥和本企业其他产品自用的合格烧碱。
不同方法生产的各种烧碱,经检验符合国家标准(GB209-93),方可统计产量。
产量中不包括在使用烧碱过程中回收的烧碱和生产烧碱过程中自用的电解碱液、浓缩碱液、回收盐液中的含碱量。
企业填报烧碱产量,应将不同的生产方法(水银法、隔膜法、离子膜法、苛化法)生产的液碱折成100%计算产量。
【单位烧碱生产耗交流电】(千瓦小时/吨)=100×交流电消耗量(万千瓦时)/液体烧碱(100%)产量(吨)分子项:交流电消耗量以电业局安装的直流耗交流电度表为准。
关于炼焦工序能耗标准的建议资料

0.225m3 17.5m3
3.7 m3~4.7m3 60 m3~65m3
4.2m3 62.5m3
760 m3~800 m3
780m3
折标准煤 0.50~0.70 6.75~7.50 7.57~8.33
0.29 12.93~14.14
24.8~31 0.54~0.72 0.19~0.24
36~39
平均值 折标煤 占总共能比
0.6
0.5
7.125
7.95
0.29
14.99
13.54
14
炼焦工序煤气消耗应在120~130kgce/t
动力消耗
新水 循环水 制冷水 除盐水 电 蒸汽 压缩空气
氮气 焦炉煤气
高炉煤气
2-2.4其他能源消耗图
折标系数 0.2t/103m3 0.15t/103m3 0.757t/103m3 0.5 t/103m3 0.404t/103kwh
0.124t/t 0.036 t/103m3
炼焦生产是十分典型的能源再加工过程 和热能的再回收利用过程,既生产重要的能 源产品(焦炭、炼焦煤气),又生产多种煤 化工产品(焦化苯类、煤焦油)等含热能较 高的重要化工资源。 ----必须遵照《物质守恒、能量守恒》的原则
2-1物质守恒—重量转化差
以2006年协会对部分会员单位的有关情 况统计看:
投入
炼焦:将各种经过洗选的炼焦煤按一定比例 配合后,在炼焦炉内进行高温干馏,可 以得到焦炭和荒煤气。将荒煤气进行加 工(净化)处理,可以得到多种煤化工
产品和焦炉煤气。焦炭是炼铁的燃料和 还原剂,它能将氧化铁(铁矿)还原为 生铁。焦炉煤气发热值高,是钢铁厂及
民用的优质燃料,又因其含氢量多,也 是制取氢气用于合成氨、合成甲醇等的 原料。(请见典型的焦化厂生产流程图)
焦化厂炼焦工序的节能降耗

引 言
随着 《 焦化 行业准 入条件》 以及 国家一系列 宏观 调控政策措 施 的深 入贯 彻 落 实 , 能 减排 在焦 化 行 节
业 中得到高 度重 视 , 能 已经 成 为企业 生 存发 展 的 节
1 2 减 少炼焦煤 消耗 .
炼 焦煤 的消耗 主要 取决 于 配煤 的结构 和性 质 。
企业 可 以通过进 行 配煤 成 焦率 实验 , 掌握 真 实 的炼
焦耗 煤量 , 以指 导 生产 。另外 , 用 通过 严格计 量 、 化
验 等环节 , 尽可 能减少炼 焦煤 的损耗 。
1 3 提 高化 产品产 率 .
重 中之重 。尤其 是在 新 的 《 中华人 民共 和 国节 约 能 源法》 布和焦 化行业 执行《 炭单位产 品能源 消耗 颁 焦 限额》 的标 准 以来 , 对该 行业在 能源管理 和能耗水平 上有 了更高 的要 求 。 本 文从 减少 炼 焦过 程 能源 转换 损失 , 降低 炼焦 耗 热量 , 减少 电力 、 蒸汽 、 的消耗 以及加 强余 热 回 水
焦 炉煤 气发 生 量和 煤焦 油 、 苯 等化产 品产 率 粗 虽然 主要 取决于 配煤 的性质 , 受生 产操 作及 管 理 但
的影 响也 比较 大 。
在 生产 中应 该严格执 行各项煤气 管理制度 和规 程, 杜绝 煤气泄 漏及不合 理放散 ; 焦炉集 气管压 力采 用先 进 的控制技 术 , 通过 鼓 风机 吸力 的合 理 控制 与 调 节 , 除焦炉 冒烟现象 , 消 最大 限度地增 加煤气 发生 量 。通 过合理操 作 与调 节 , 改善 焦油氨水分离效 果 ,
收利用等方面探讨了炼焦工序的节能降耗。
1 减少炼焦过程中的能源转换损失
控制炼焦工序能耗 降低生产运行成本

这 几座 焦 炉 也有所体 现。上述 因素不 仅影响焦 炉正 常 生产 ,同时还使焦 炉能耗剧 增 ,生产运行 成本 大幅增 加 .严 重影 响 了企业 的经济 效益 :因 此 ,对 炼 焦生产 过程 中的能耗情 况 ,特 别是能源 浪费情 况进 行总 结并加 以整改就 成为 车间节能 降
该 车间细致 分析 了炼焦生 产工艺 中的重点 能 耗 浪 费 环 节 ,主 要 从下 面几 个 方 面 人 手 进 行 整
改 ,取得 了明显 效果 一
( ) 从原料煤 人手 ,避免热 能浪 费 1
该 车间 的加 煤塔位 于两座焦 炉之 间 ,与熄 焦
本 钢焦 化 厂 焦 一 车 间现 有 炉 龄 二 十余 年 的 43 . m焦 炉两座 ,年设计 能 力为 8 0万 吨。 由于 车 间在 多年生产 过程 中积 累了大量 的安全生 产经验
度长 时 间低 于 10 ℃ 时 ,会 导 致 炉 头焦 炭 成 熟 10
缓慢及 装煤后 炭化 室头 部大 幅度降温 ,出现 炉砖 大面积损 坏 的情况 ,最终 导致耗 热量增 加 。
( ) 加强 炉体维 护 ,避免煤气 窜漏 4 炉体 状态 好坏对 炼焦 耗热量 有直接 影响 。该 车间焦 炉均 为高龄炉 ,由于长期 使用 ,炉体 承受 高温 、机械力 等 ,墙 面 剥 蚀 ,炉 墙 或顶 砖 裂 缝 ,
维普资讯
冶
1 0
金
能
源
Vo . 6 No 5 12 .
S p. 0 e t 2 07
ENERGY OR F METALL URຫໍສະໝຸດ I CAL I NDUS TRY
控 制 炼 焦 工 序 能 耗 降 低 生 产 运 行 成 本
谢 东
炼焦工序的能效标杆水平

炼焦工序的能效标杆水平
炼焦工序的能效标杆水平通常是指工业界中在该工序中能够达到的最高能效水平。
能效标杆水平可以通过各种方式来衡量,如单位产品消耗的能源量、产量与消耗能源的比例等。
一种常见的能效标杆指标是煤焦比,即单位焦炭产量所需的原煤消耗量。
在国际上,目前炼焦工序的能效标杆一般为1.35吨/吨焦炭。
这意味着,每生产一吨焦炭所需的原煤消耗量为1.35吨。
然而,实际的能效水平可能因地域、技术、设备等因素而有所差异。
一些先进的炼焦工艺和设备可以实现更高的能效水平,如采用先进的炼焦炉和余热回收技术,能够将煤焦比降低到1.2吨/吨焦炭以下。
为了提高能效,炼焦工业可以采取一系列的措施,如优化炼焦炉操作、提高煤质和焦炭质量、加强能耗监控与管理等。
同时,合理利用余热、压缩能耗、减少能源浪费等都是提高炼焦工序能效的有效途径。
尽管炼焦工序的能效标杆水平已经相对较高,但在实际生产中仍存在改进的空间。
通过不断推进新技术和改进现有工艺,炼焦工业可以继续提升能效水平,实现更加可持续和环保的生产。
炼焦工序单位能耗

炼焦工序单位能耗:指报告期内炼焦工序中生产每吨焦炭的能源净消耗量。
计算公式:炼焦工序单位能耗(千克标准煤/吨 )=炼焦工序净耗能量(吨标准煤)/全部焦炭合格产出量(干基)(吨)×1000计算说明:1.炼焦工序净耗能量是指炼焦工艺生产系统的备煤车间(不包括洗煤) 、厂内部原料煤的损耗、炼焦车间、回收车间(冷凝鼓风、氨回收、粗苯、脱硫脱氰、黄血盐)、辅助生产系统的机修、化验、计量、环保等,以及直接为生产服务的附属生产系统的食堂、浴池、保健站、休息室、生产管理和调度指挥系统等所消耗的各种能源,扣除回收利用并外供的余热、二次能源、余能量。
计量单位为吨标准煤。
计算公式如下:炼焦工序净耗能量=原料煤折标准煤+动力折标准煤—焦化产品外供量折标准煤—余热回收外供量折标准煤—回收二次能源外供量折标准煤-利用余能外供量折标准煤2.原料煤为装入焦炉的干洗精煤量;焦化产品外供量是指供外厂(车间)的焦炭、焦炉煤气、煤焦油、粗苯等数量;动力是指各类加热煤气(高炉煤气、发生炉煤气、焦炉煤气等)、电、蒸汽、氮气、压缩空气、生产用水及各类燃料等;余热回收外供量,如供应外工厂(车间)的蒸汽数量及干熄焦工序外供的电量等。
炼铁工序单位能耗:指报告期内炼铁工序中生产每吨生铁的能源净消耗量。
计算公式:炼铁工序单位能耗(千克标准煤/吨)=炼铁工序净耗能量(吨标准煤)/生铁合格产出量(吨)×1000【2501】【炼焦工序单位能耗】(千克标准煤/吨)=1000×炼焦工序净耗能量(吨标准煤)/全部焦炭合格产出量(干基)(吨)分子项:炼焦工序净耗能量是指炼焦工艺生产系统的备煤车间(不包括洗煤)、厂内部原料煤的损耗、炼焦车间、回收车间(冷凝鼓风、氨回收、粗苯、脱硫脱氰、黄血盐)、辅助生产系统的机修、化验、计量、环保等,以及直接为生产服务的附属生产系统的食堂、浴池、保健站、休息室、生产管理和调度指挥系统等所消耗的各种能源,扣除回收利用并外供的能源量。
炼焦工序能耗

一、炼焦工序单位能耗炼焦工序单位能耗是指生产 1 吨焦炭(干基)所耗用的能量。
其计算公式为:炼焦工序单位能耗(千克标准煤/吨) =炼焦工序净耗能量(千克标准煤)/全部焦炭合格产出量(吨)计算说明:1、子项炼焦工序净耗能量是指炼焦工艺生产系统的备煤车间(不包括洗煤)、厂内部原料煤的损耗、炼焦车间、回收车间(冷凝古风、氨回收、粗苯、脱硫脱氰、黄血盐)辅助生产系统的机修、化验、计量、环保等,以及直接为生产服务的附属生产系统的食堂、浴池、保健站、休息室、生产管理和调度指挥系统等所消耗的各种能源的实物量,扣除回收利用并外供的余热、二次能源、余热量,并折成标准煤。
即子项 =原料煤折标准煤(千克) +动力折标准煤(千克) -焦化产品外供量折标准煤(千克) -余热回收外供量折标准煤(千克) -回收二次能源外供量折标准煤(千克) -利用余热外供量折标准煤(千克);2、原料煤为装入焦炉的干洗精煤量;3、焦化产品外供量是指供外厂(车间)的焦炭、焦炉煤气、煤焦油、粗苯等数量;4、动力是指高炉煤气、水、电、蒸汽、压缩空气等;5、余热回收外供量,如供应外工厂(车间)的蒸汽数量及熄焦工序外供的电量等。
二、焦炭主要能源实物消耗焦炭主要能源实物消耗是指每生产 1 吨焦炭所消耗的某种能源实物量。
其计算公式为:焦炭某种能源实物消耗(该能源计量单位 / 吨) =焦炭某种能源耗用量(该能源计量单位) /全部焦炭合格产出量(干基)(吨)计算说明:1、应按所消耗的电力、水、煤气等能源品种分别计算。
2、某种能源耗用量是指全厂的耗用量,包括从配煤到煤气净化工序结束止,但不包括化工产品精制产品所用的物料消耗。
3、煤气消耗的单位也可用米3/吨焦;蒸汽消耗单位也可用吨/吨焦。
4、在计算车间消耗指标时,除炼焦车间按焦炭量计算外,其他车间则按产品分别进行计算,即子项为生产该产品的水、电、煤气等能源实物消耗量,母项为该产品合格产出量。
三、焦炭单位产品综合能耗1、统计范围备煤(不包括洗煤)、炼焦和煤气净化工段的能耗和扣除自身回收利用和外供的能源量,不包括精制。
焦化厂节能降耗
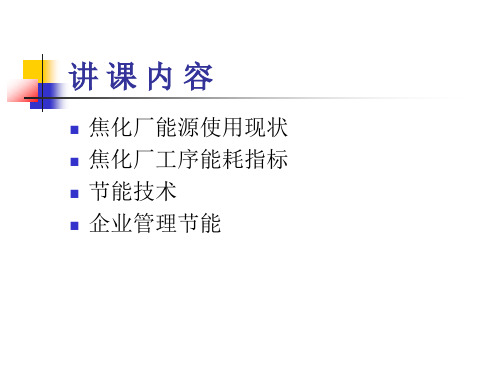
循环风机
旋风分离气
干熄焦能源消耗与回收
能耗:
N2:消耗量为71.26m3/ min 蒸汽:2×0.64t/h (低压) 压缩空气:生产用压缩空气消耗量为6.82m3/min,除尘用干燥压缩 空气量为16.8m3/ min,仪表用干燥空气量为4.84m3/ min 除盐水:消耗量为30m3/h
焦炉煤气:烘炉用,每年一次,2000m3/h
循环水:
主要用途:污水处理消泡、消防用水
电:
我厂吨焦耗电量明显高于指标要求,主要是设备多、功率大。
皮带通廊照明用电、空转设备(如皮带起动、停止)、不合理的运行方 式(设计存在的缺陷)、长明灯等
蒸汽:
我厂的蒸汽使用主要是化产作业区,目前低压蒸汽分为两趟管线,一趟 供制冷机(每台用量6t/h,现按开三备一方式运行)、蒸氨塔( 5.5~6t/h)、脱苯塔(3~3.5t/h)、焦炉 一趟低压蒸汽经减温装置(减温至150~160℃)后专供脱硫脱氰工序。 冬季皮带取暖、保温仍采用蒸汽方式 我厂操作间取暖仍存在低压蒸汽方式,尤其是乍暖还寒时采取的开窗户 取暖,导致蒸汽消耗量的增加
节约用水:我厂用水种类较多,主 要的耗水是工业新水和循环水。目 前工业新的消耗量增大主要原因是 炼焦熄焦塔用水和干熄焦的循环水 收集能力不够。 清水槽 分析:1、熄焦塔
满 流 管 满 流 管
2、干熄焦
回水收 集槽
43t/h
(4)我厂的节能潜力:
(1)通过作业区、厂级的小改造提高水、蒸汽的二次利用率,如 化产对排污水的改造 (2)通过管理、技术等手段节约能源,技术:如煤备对除尘与粉 碎机进行联锁,减少8秒/次的延时,进行节电;采用节能灯节 电;增加变频器节电 管理:杜绝长明灯节电、根据天气情况改变取暖用汽量 (3)每个员工都是节能单元,身边有许多节能机会,如普通空气 吹扫的杜绝。 (4)余热利用:冬季对初冷器高温段进行利用,用于采暖;下一 步公司增加对中温段的余热利用,目前正在作方案。 (5)对能源的回收:蒸汽凝结水,公司统一回收后进行处理,代 替软水用于发电
焦化工序计算公式

焦化工序计算公式焦化工序计算公式(一)冶金焦抗碎强度(M40转鼓指数)冶金焦抗碎强度是反映焦炭的抗碎性能的指标,以百分比表示。
其计算公式为:逐日(月)(试验后块度大于40毫米所占的冶金焦抗碎强度(M40)(%)=百分比(%)×冶金焦产量(吨))之和×100%冶金焦总产量(吨)计算说明:按规定水分(水量)计算。
采用国外转鼓试验的,按实际情况计算,并加以说明。
(二)冶金焦抗碎强度(M25转鼓指数)冶金焦抗碎强度是反映焦炭的抗碎性能的指标,以百分比表示。
其计算公式为:冶逐日(月)(试验后块度大于25毫米所占金焦抗碎强度(M25)(%)=的百分比(%)×冶金焦产量(吨)之和×100%冶金焦总产量(吨)(三)冶金焦耐磨强度(M10转鼓指数)冶金焦耐磨强度是反映焦炭的耐磨性能的指标,以百分比表示,其计算公式为:逐日(月)(试验后块度小于10毫米所占的冶金焦耐磨强度(M10)(%)=百分比(%)×冶金焦产量(吨))之和×100%冶金焦总产量(吨)计算说明:按规定水分(水量)计算,采用国外转鼓试验的,按实际情况计算,并加以说明,该指标实质上是磨损率,指标值越小越好。
(四)冶金焦灰分冶金焦灰分是指冶金焦炭中含灰量所占的百分比。
其计算公式为:冶金焦灰分(%)=冶金焦中所含灰分总量(吨)×100%冶金焦总产量(干基)(吨)(五)冶金焦硫分冶金焦硫分是指冶金焦中含硫量所占的百分比。
其计算公式为:冶金焦硫分(%)=冶金焦中所含硫分总量(吨)×100%冶金焦总产量(干基)(吨)(六)冶金焦合格率冶金焦合格率是指检验合格的冶金焦占冶金焦检验总量的百分比。
冶金焦各种质量指标中,只要有一项不符合国家规定标准的,即视为不合格品。
冶金焦合格率的计算公式为:冶金焦合格率(%)=冶金焦检验合格量(吨)×100%冶金焦检验总量(吨)(七)全焦率全焦率(成焦率)是指入炉煤干馏后所获得的焦炭数量占入炉煤量的百分比。
炼焦工序能效标杆水平

炼焦工序能效标杆水平
炼焦工序的能效标杆水平取决于多个因素,包括采用的技术、设备、操作方式等。
然而,以下是一些常见的炼焦工序能效标准:
1. 煤气利用率:衡量炼焦工序中煤气的利用效率。
通常用于发电或热能回收等用途。
高效的炼焦工序应该能够最大限度地利用煤气。
2. 焦炭收率:炼焦工序中产生的焦炭数量与原料煤数量的比例。
高效的工序应该能够最大限度地将原料转化为焦炭,以提高焦炭收率。
3. 能耗:炼焦工序中消耗的能源总量。
高效的工序应该能够尽量减少能源的消耗,例如优化供热系统、改善燃烧方式等。
4. 废水和废气处理:炼焦工序中产生的废水和废气的处理效率。
高效的工序应该能够有效处理废水和废气,以减少对环境的负面影响。
需要注意的是,能效标杆水平可能因地区和工艺的不同而有所差异。
因此,在具体应用中,应根据实际情况来确定具体的能效标杆水平。
- 1、下载文档前请自行甄别文档内容的完整性,平台不提供额外的编辑、内容补充、找答案等附加服务。
- 2、"仅部分预览"的文档,不可在线预览部分如存在完整性等问题,可反馈申请退款(可完整预览的文档不适用该条件!)。
- 3、如文档侵犯您的权益,请联系客服反馈,我们会尽快为您处理(人工客服工作时间:9:00-18:30)。
一、炼焦工序单位能耗
炼焦工序单位能耗是指生产1吨焦炭(干基)所耗用的能量。
其计算公式为:
炼焦工序单位能耗(千克标准煤/吨)=炼焦工序净耗能量(千克标准煤)/全部焦炭合格产出量(吨)计算说明:
1、子项炼焦工序净耗能量是指炼焦工艺生产系统的备煤车间(不包括洗煤)、厂内部原料煤的损耗、炼焦车间、回收车间(冷凝古风、氨回收、粗
苯、脱硫脱氰、黄血盐)辅助生产系统的机修、化验、计量、环保等,以及直
接为生产服务的附属生产系统的食堂、浴池、保健站、休息室、生产管理和调
度指挥系统等所消耗的各种能源的实物量,扣除回收利用并外供的余热、二次
能源、余热量,并折成标准煤。
即子项=原料煤折标准煤(千克)+动力折标准煤(千克)-焦化产品外供量折标准煤(千克)-余热回收外供量折标准煤(千克)-回收二次能源外供量折标准煤(千克)-利用余热外供量折标准煤(千克);
2、"原料煤为装入焦炉的干洗精煤量;
3、焦化产品外供量是指供外厂(车间)的焦炭、焦炉煤气、煤焦油、粗苯
等数量;
4、"动力是指高炉煤气、水、电、蒸汽、压缩空气等;
5、余热回收外供量,如供应外工厂(车间)的蒸汽数量及熄焦工序外供的
电量等。
二、焦炭主要能源实物消耗
焦炭主要能源实物消耗是指每生产1吨焦炭所消耗的某种能源实物量。
其
计算公式为:
焦炭某种能源实物消耗(该能源计量单位/吨)=焦炭某种能源耗用量(该能源计量单位)/全部焦炭合格产出量(干基)(吨)计算说明:
1、应按所消耗的电力、水、煤气等能源品种分别计算。
2、某种能源耗用量是指全厂的耗用量,包括从配煤到煤气净化工序结束止,但不包括化工产品精制产品所用的物料消耗。
3、煤气消耗的单位也可用米 3
/吨焦;蒸汽消耗单位也可用吨/吨焦。
4、在计算车间消耗指标时,除炼焦车间按焦炭量计算外,其他车间则按产品分别进行计算,即子项为生产该产品的水、电、煤气等能源实物消耗量,母项为该产品合格产出量。
三、焦炭单位产品综合能耗
1、统计范围
备煤(不包括洗煤)、炼焦和煤气净化工段的能耗和扣除自身回收利用和外供的能源量,不包括精制。
备煤工段包括贮煤、粉碎、配煤及系统除尘;炼焦工段包括炼焦、熄焦、筛运焦、装煤除尘、出焦除尘和筛运焦除尘;煤气净化工段内容包括冷凝鼓风、脱硫、脱氰、脱氨、脱苯、脱萘等工序和酚氰污水处理;干熄焦产出只计算蒸汽,不含发电。
2、计算方法
焦炭单位产品综合能耗应按以下公式计算:
EJT=(e
yl+e
jg-e
cp-e
yr)/p
JT
式中:
EJT------焦炭单位产品综合能耗,单位为千克标准煤每吨(kgce/t);e
yl------原料煤量,单位为千克标准煤(kgce);ejg------加工能耗量,是指炼焦生产所用焦炉煤气、高炉煤气、水、电、蒸汽、压缩空气等能源,单位为千
克标准煤(kgce);e
cp------焦化产品外供量,是指供外厂(车间)的焦炭、焦炉煤气、粗焦油、粗苯等的数量,单位为千克标准煤每吨(kgce/t);e
yr-----余热回收量,如干熄焦工序回收的蒸汽数量等,单位为千克标准煤每
吨(kgce/t);p
JT------------焦炭产量,单位为吨(t)。
资源能源利用指标
指标一级二级三级
工序能耗,kg标煤/t焦≤150≤170≤180
吨焦耗新鲜水量,m
3/t焦≤
2."5≤
3."5
吨焦耗蒸汽量,t/t焦≤
0."20≤
0."25≤
0."40
吨焦耗电量,kW·h/t焦≤30≤35≤40
炼焦耗热量(7%H
2O)kJ/kg标煤
焦炉煤气≤2150≤2250≤2350
高炉煤气≤2450≤2550≤2650
焦炉煤气利用率,% 100≥95≥80水循环利用率,%≥95≥85≥75。