制粉工艺与设备 研磨 LN
粉磨工艺及设备
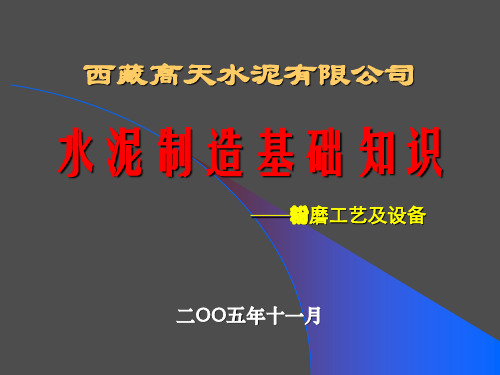
功率3000~7000KW的磨机
无齿轮传动
一般用在传动功率>7000KW的磨机
磨机的工作原理
物料在磨机中的磨碎主要是靠研磨体落下 的冲击能量,其次是靠研磨体的滚动和滑动的 研磨作用。
当磨机回转时,研磨体由于离心力的作用 贴在磨机内壁上,并与磨机一起回转,并被带 到一定的高度,由于重力的关系,便脱离内壁 下落以冲击物料,将物料粉碎。在磨机研磨仓 内的研磨体以滚动或滑动(即泻落式运动状态) 为主,此时即对物料产生研磨作用。如此反复 进行,使块状物料逐渐变成细粉。
水泥制造基础知识
——粉磨工艺及设备
二OO五年十一月
一、物料粉碎的过程
粗碎
破 碎
中碎
粉
细碎
将物料粉碎到100mm左右 将物料破碎到30mm左右 将物料破碎到3mm左右
碎
粗磨
将物料粉磨到0.1mm左右
粉 细磨
将物料粉磨到60μm左右
磨 超细磨
将物料粉磨到5μm或更小
二、生料粉磨的细度要求
一般生料细度控制在0.08mm方孔筛筛余 10%左右,0.2mm方孔筛筛余<1.5%。
磨机尾部出现很大颗粒的原因
在磨机产量、质量正常时,磨尾有少量颗 粒排出是正常的,但如果出现很多颗粒碎锻, 则可能是由于一仓填充系数比二仓大得太多 (两仓磨),或隔仓板有破洞、隔仓板与隔仓 板之间安装的缝隙太大,一仓较大颗粒的物料 跑到二仓,而二仓由于研磨体较小无法破碎, 从而从磨尾排出。
如何处理磨机尾部出现很大颗粒
一般水泥细度要控制在0.08mm方孔筛筛余 和比表面积两个指标。普通32.5水泥0.08mm方孔 筛筛余5~8%, 比表面积为2600 ~ 3000cm2/g。 42.5水泥3000 ~ 3400cm2/g。
制粉工艺与设备课件
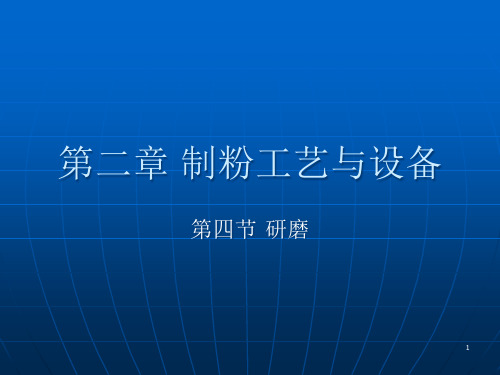
意义
产品代号
意义
B
皮磨系统
F
小麦粉
S
渣磨系统
Br
M
心磨系统
G
麸皮 麦胚
T
尾磨系统
P
清粉
设备代号 BrF BrB D
意义 打麸机 刷麸机 重筛
注;1.各系统先后顺序用阿拉伯数字1、2、3……表示。如1B、2M。
2.各道磨分粗细时,分别在系统代号右下角用小写的c、f表示。如2BC、1MF。 3.不同品种小麦粉,在代号前用阿拉伯数字区别。如1F、2F。
第二章 制粉工艺与设备
第四节 研磨
1
本章主要内容
4.1 制粉的基本规律 4.2 研磨效果的评价 4.3 磨粉机
2
4.1 制粉的基本规律
1、在制品
小麦经过1B研磨后,即成为 许多粒度、品质不同的混合 物料,这些物料必须按粒度、 品质分类,再经过多道磨筛 工作单元逐步地进行研磨筛 分,才能够从原料中提取质 量、数量均符合要求的面粉。 因此,由各工作单元提取、 分类的物料,基本上都是制 粉工艺过程中的中间产品, 即在制品。
21
5.3 喂料机构
作用: 将小麦均匀喂入研磨区磨辊全长上,并进入二辊间隙 处,流量可调。 对喂料辊的要求:
(1)保证连续而均匀的送料,沿着磨辊整个长度送下的物 料,其流层应厚薄一致;
(2)有高度的灵敏度,能准确地调整流量,当流量变化不 大时,还具有自动适应的能力;
(3)喂料机构与磨辊的相对位置应保证物料能正确地送入 磨辊的间距内,并具有一定的速度,以提高产量;
若产品为高等级面粉,粉筛采用较密的筛网,检验时筛 理时间应适当延长。测同一工艺流程中各道磨粉机取粉率时, 检验筛理时间应一致。
制粉工艺与设备第五节筛理和清粉 LN

2020/6Leabharlann 1427(3)清粉系统
在皮磨系统获得的麦渣、麦心和粗粉, 它们是纯粉粒(胚乳)、连麸粉粒和麸屑的 混合物。利用清粉机的筛选和风选系统,将 纯粉粒、连麸粉粒和麸屑分开,再送往相应 的研磨系统处理。
2020/6/14
28
(4)心磨系统
是将皮磨、渣磨、清粉系统取得的麦心和 粗粉研磨成具有一定细度的面粉,并提出麸屑 , 心磨系统一般有5~9道,称1心、2心等 。
将麦粒剥开,从麸皮上刮下麦渣、麦心 和粗粉,并保持麸片不过分破碎,以便使得 胚乳与麦皮最大限度地分离。皮磨一般设3~ 5道,称为1皮、2皮、3皮等。
2020/6/14
26
(2) 渣磨系统
处理皮磨及其他系统分离出的带有表皮 的粉粒,使表皮与胚乳分开,从中提出品质 较好的麦心和粗粉,送入心磨系统磨制成粉 。渣磨一般为1~2道,称为1渣、2渣。
2020/6/14
13
2020/6/14
14
第六节 清粉
1 清粉目的
在皮磨系统获得的麦渣、麦心和粗粉, 它们是纯粉粒(胚乳)、连麸粉粒和麸屑的 混合物。利用清粉机的筛选和风选作用,将 纯粉粒、连麸粉粒和麸屑分开,再送往相应 的研磨系统处理。
制特精粉时采用,标准粉生产不用。
2020/6/14
15
清粉实际上是一种筛理,将上述 麦心(粉粒)分离后进入心磨进一步研 磨处理,筛下物称特制粉,筛上物基本 上全为麸皮。到此制粉工艺全部结束。
2020/6/14
10
3 刷麸机
工作原理 利用旋转的刷帚或打板,把粘附在麸
皮上的粉粒分离下来,并使其穿过筛孔而 成为筛出物,而麸皮则留在筛内。
2020/6/14
11
2020/6/14
磨粉工艺技术

磨粉工艺技术磨粉工艺技术是粉体加工工艺的一种重要环节。
磨粉是将物料从初级颗粒逐渐细化至所需粒度的过程,可以使物料更好地与其他材料混合、溶解、吸附等。
下面我将通过对磨粉工艺技术的介绍,来探讨磨粉工艺技术的原理、设备和应用。
磨粉工艺技术的主要原理是通过相互碰撞、摩擦、切割等作用,使物料逐步破碎、细化。
首先,物料经过上料装置进入磨矿机的研磨腔,磨矿机通过旋转装置对物料进行研磨。
在磨矿机的内腔中,物料与研磨体之间发生碰撞和摩擦,研磨体起到了破碎和细化物料的作用。
其次,通过分级机构,将粗粉从细粉中分离出来,形成所需的粉末。
磨粉工艺技术的设备包括磨矿机和分级机。
磨矿机是磨粉过程中的关键设备,常用的有球磨机、砂磨机、搅拌磨机等。
球磨机是一种传统的磨矿机,其研磨体为钢球,通过转动装置将物料和钢球一起进行研磨。
砂磨机是一种新型磨矿机,其研磨体为砂石,通过砂石的摩擦磨擦物料完成磨粉过程。
搅拌磨机则是通过搅拌装置将物料与研磨体进行强烈的混合,并通过摩擦实现研磨的效果。
分级机是将研磨后的粉末按照粒度分级的设备,常见的有风力分级机和离心分级机。
磨粉工艺技术在许多领域中有着广泛的应用。
首先,在制药工业中,磨粉工艺技术能够将药物原料研磨成粉末,以提高药物的可溶性和吸收率。
其次,在陶瓷工业中,磨粉工艺技术能够细化陶瓷原料,并使得陶瓷材料的致密性和强度得到提高。
再者,在化工工业中,磨粉工艺技术能够将化工原料研磨成细粉,以提高反应速率和转化率。
此外,磨粉工艺技术还广泛应用于金属矿山、建材、食品等行业。
总而言之,磨粉工艺技术是一种关键的粉体加工工艺,通过相互碰撞、摩擦、切割等作用将物料逐步细化至所需粒度。
磨粉工艺技术的设备包括磨矿机和分级机,常见的有球磨机、砂磨机、搅拌磨机等。
磨粉工艺技术在制药、陶瓷、化工等领域具有广泛应用。
通过磨粉工艺技术,可以提高物料的可溶性、吸附性,提高产品的强度和致密性,提高反应速率和转化率,满足各个领域对粉末产品的需求。
高压磨粉机设备工艺原理
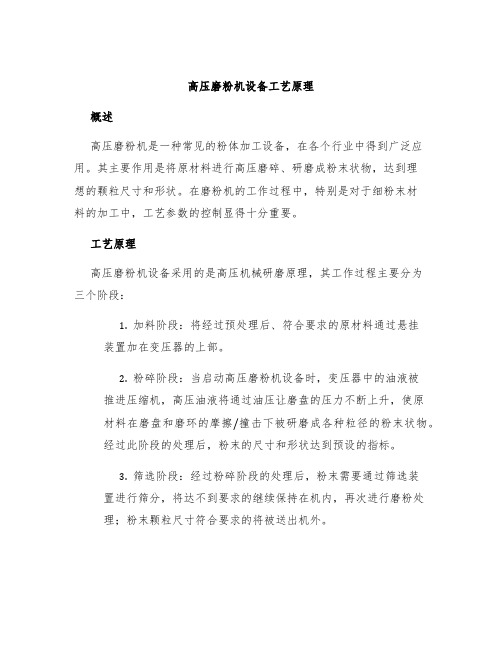
高压磨粉机设备工艺原理概述高压磨粉机是一种常见的粉体加工设备,在各个行业中得到广泛应用。
其主要作用是将原材料进行高压磨碎、研磨成粉末状物,达到理想的颗粒尺寸和形状。
在磨粉机的工作过程中,特别是对于细粉末材料的加工中,工艺参数的控制显得十分重要。
工艺原理高压磨粉机设备采用的是高压机械研磨原理,其工作过程主要分为三个阶段:1.加料阶段:将经过预处理后、符合要求的原材料通过悬挂装置加在变压器的上部。
2.粉碎阶段:当启动高压磨粉机设备时,变压器中的油液被推进压缩机,高压油液将通过油压让磨盘的压力不断上升,使原材料在磨盘和磨环的摩擦/撞击下被研磨成各种粒径的粉末状物。
经过此阶段的处理后,粉末的尺寸和形状达到预设的指标。
3.筛选阶段:经过粉碎阶段的处理后,粉末需要通过筛选装置进行筛分,将达不到要求的继续保持在机内,再次进行磨粉处理;粉末颗粒尺寸符合要求的将被送出机外。
设备特点高压磨粉机设备的一大特点是,其工作过程中的粉碎过程比较充分,粉末的颗粒尺寸和形状均匀,磨粉机处理出来的粉末不但细度高,且颗粒具有各种形状,具有非常广泛的应用前景。
此外,高压磨粉机还具有以下特点:1.磨盘和磨环的耐用性强,经久耐用,长时间运行下磨损小,寿命长。
2.高压磨粉机设备的噪音和振动都比较小,其工作过程比较平稳。
3.可以根据不同颗粒尺寸的要求进行调整,精度较高,稳定性强。
4.具有自动控制的功能,可以对料量、压力等指标进行精准的控制,操作简便。
应用范围高压磨粉机设备广泛应用于矿山、化工、冶金、建材、环保等领域,主要用于将硬质物质(例如:石灰石、白垩石、矽、石英等)和粘性物质(例如:粉煤灰、水泥熟料、陶土、烧结土等)进行精细粉碎加工。
而且,因为高压磨粉机设备的磨盘和磨环采用合金材质等高强度材料的制作,其处理过程可以大大减少粉末的金属污染和因物料摩擦磨损所产生的杂质,从而获得高质量的粉末状物。
总结高压磨粉机设备的工艺原理非常简单,但是其应用范围非常广泛,具有多种形状颗粒和精度较高的处理特点。
制粉工艺与设备
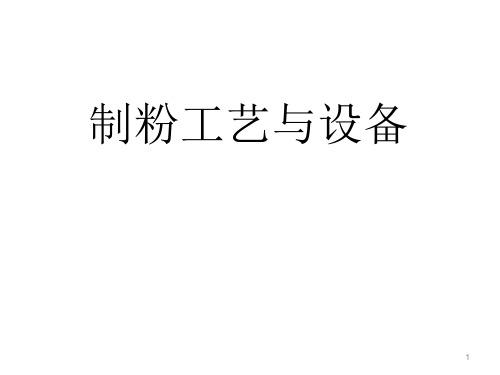
2、千粒重 3、悬浮速度
1千粒小麦的重量
4、自动分级性 5、散落性 6、麦粒的结构力学性质
6
4、小麦粉的种类
特制一等粉(精粉)
按加工精度
特制二等粉(精粉) 标准粉 普通粉 面包粉 馒头粉 面条粉 专用粉 饺子粉 饼干粉
小麦粉
按用途分
蛋糕粉 通用粉:没有明确专门用途的小麦粉,主要满 足家庭和手工作坊不同面制食品的制作要求。
及无食用价值的生芽、病斑、变质麦粒等。
18
第二节
小麦清理的意义与工艺
2.2杂质分类与特点
2、按物理性质分 ①按颗粒大小分: 大杂质:留存在直径4.5mm圆孔筛上的杂质;并肩杂质: 通过4.5mm圆形筛孔、留存在直径1.5~2.0mm圆形筛孔上 的杂质。 小杂质:通过直径1.5~2.0mm圆形筛孔的杂质。 ②按比重(或密度)的大小分: 重杂质:指比重大于小麦的杂质; 轻杂质:指比重小于小麦的杂质。
16
2.1 小麦清理的意义
综上所述,小麦清理的意义主要有以下两点 • (1)保护生产的正常运行 • (2)保证产品的纯度与质量
17
第二节
小麦清理的意义与工艺
• 2.2杂质分类与特点
1、按化学成份分 无机杂质(尘芥杂质):泥土、沙石、煤渣、砖瓦、 玻璃碎块、金属物及其它矿物质。 有机杂质(粮食杂质):混杂在小麦中的根、茎、叶、 颖壳,野生植物种子,异小麦清理的意义与工艺
利用刷擦作用清理小麦表面的工艺方法称为刷麦。刷麦可清理附着在麦粒表 面及腹沟内的泥、麦杂等杂质,处理一次灰分可降低0.03%。
34
思考与练习
• • • 小麦清理的目的是什么?小麦除杂的原理与方法有哪些? FDMW型打麦机工作于轻打或重打状态时,设备的工作 参数有何区别? 打麦机的工作间隙调小以后,对物料的打击效果将如何 变化? FDMW型打麦机的设计工作速度范围为400-600r/min。 该设备装置的麦路中什么位置时应轻打?相应的工作转 速是多少? 对于卧式打麦机而言,出机物料中的小杂含量大于进机 物料,这是否正常?为什么? 卧式打麦机的实际工作流量大于其设计产量,这对设备 的工作效果有什么影响?说明理由。 碾麦机的主要工作原理与作用是什么?
制粉工艺流程
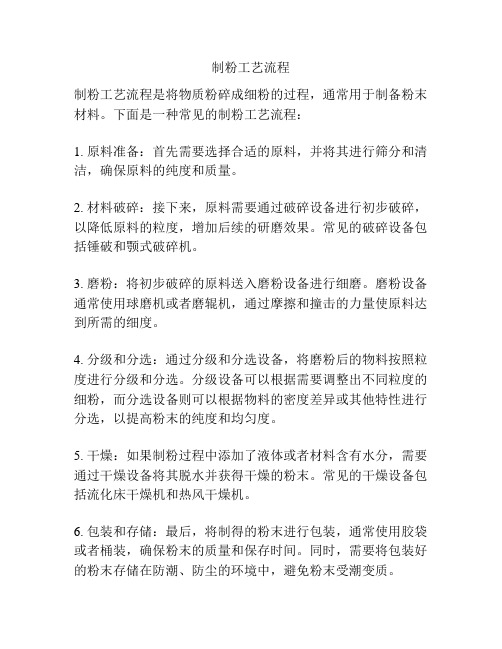
制粉工艺流程
制粉工艺流程是将物质粉碎成细粉的过程,通常用于制备粉末材料。
下面是一种常见的制粉工艺流程:
1. 原料准备:首先需要选择合适的原料,并将其进行筛分和清洁,确保原料的纯度和质量。
2. 材料破碎:接下来,原料需要通过破碎设备进行初步破碎,以降低原料的粒度,增加后续的研磨效果。
常见的破碎设备包括锤破和颚式破碎机。
3. 磨粉:将初步破碎的原料送入磨粉设备进行细磨。
磨粉设备通常使用球磨机或者磨辊机,通过摩擦和撞击的力量使原料达到所需的细度。
4. 分级和分选:通过分级和分选设备,将磨粉后的物料按照粒度进行分级和分选。
分级设备可以根据需要调整出不同粒度的细粉,而分选设备则可以根据物料的密度差异或其他特性进行分选,以提高粉末的纯度和均匀度。
5. 干燥:如果制粉过程中添加了液体或者材料含有水分,需要通过干燥设备将其脱水并获得干燥的粉末。
常见的干燥设备包括流化床干燥机和热风干燥机。
6. 包装和存储:最后,将制得的粉末进行包装,通常使用胶袋或者桶装,确保粉末的质量和保存时间。
同时,需要将包装好的粉末存储在防潮、防尘的环境中,避免粉末受潮变质。
以上是一种常见的制粉工艺流程,不同的物料和要求可能会有所不同。
在制粉过程中需要注意物料的纯度和质量,设备的选择和操作也对制粉效果有着重要的影响。
此外,在制粉过程中还需要遵守相关的安全规范和操作规程,确保工作环境的安全和人员的健康。
水泥生产粉磨工艺及设备
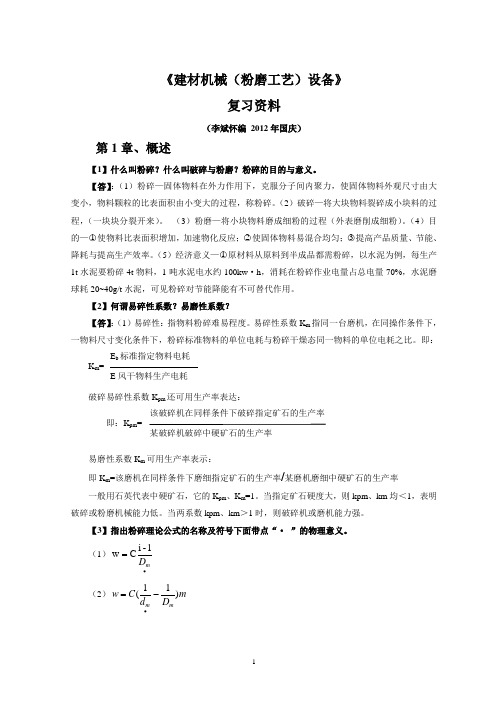
《建材机械(粉磨工艺)设备》复习资料(李斌怀编 2012年国庆)第1章、概述【1】什么叫粉碎?什么叫破碎与粉磨?粉碎的目的与意义。
【答】:(1)粉碎—固体物料在外力作用下,克服分子间内聚力,使固体物料外观尺寸由大变小,物料颗粒的比表面积由小变大的过程,称粉碎。
(2)破碎—将大块物料裂碎成小块料的过程,(一块块分裂开来)。
(3)粉磨—将小块物料磨成细粉的过程(外表磨削成细粉)。
(4)目的—○1使物料比表面积增加,加速物化反应;○2使固体物料易混合均匀;○3提高产品质量、节能、降耗与提高生产效率。
(5)经济意义—○1原材料从原料到半成品都需粉碎,以水泥为例,每生产1t 水泥要粉碎4t 物料,1吨水泥电水约100kw ·h ,消耗在粉碎作业电量占总电量70%,水泥磨球耗20~40g/t 水泥,可见粉碎对节能降能有不可替代作用。
【2】何谓易碎性系数?易磨性系数?【答】:(1)易碎性:指物料粉碎难易程度。
易碎性系数K m 指同一台磨机,在同操作条件下,一物料尺寸变化条件下,粉碎标准物料的单位电耗与粉碎干燥态同一物料的单位电耗之比。
即:E b 标准指定物料电耗K m =E 风干物料生产电耗破碎易碎性系数K pm 还可用生产率表达:该破碎机在同样条件下破碎指定矿石的生产率即:K pm =某破碎机破碎中硬矿石的生产率易磨性系数K m 可用生产率表示:即K m =该磨机在同样条件下磨细指定矿石的生产率/某磨机磨细中硬矿石的生产率一般用石英代表中硬矿石,它的K pm 、K m =1。
当指定矿石硬度大,则kpm 、km 均<1,表明破碎或粉磨机械能力低。
当两系数kpm 、km >1时,则破碎机或磨机能力强。
【3】指出粉碎理论公式的名称及符号下面带点“· ”的物理意义。
(1)∙=m D 1-i C w (2)m D d C w m m )11(-=∙(3))(1mm d D g K w ∙= (4)m i m i D w d w w 100100-=∙][h kw ⋅ 【答】:(1)(2)公式为粉碎表面积假说推导出的单位产品消耗的粉碎功J/kg 。
建筑材料生产工艺与设备第2章 粉磨概述
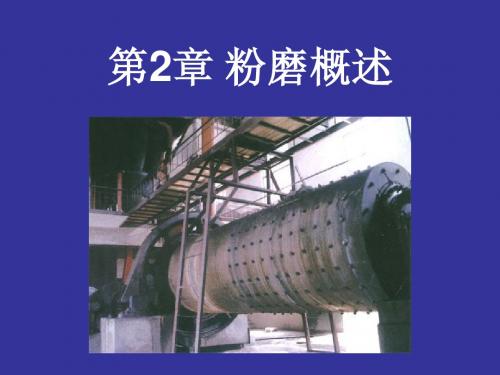
三、应用
颚式破碎机广泛用于冶金、建材、化工、煤炭等工业 部门,该机适用于莫氏硬度7级以下的各种物料的粗、中、 细碎,当用于细碎时,宜选用细碎颚式破碎机。颚式破碎机 适用的物料有硫铁矿石、磷矿石、重晶石、天青石、电石、 焦炭、石灰石等,不宜用于片矿石的破碎。
3.2圆锥破碎机
圆锥破碎机是近年来随着 矿山机械的不断进步而研 发出来的传统破碎机的绝 佳替代品,圆锥破碎机较 先前的破碎机最突出的特 点就是使用寿命长,技术 含量高,在最大限度的节 约能源。
简单摆动颚式破碎机结构简单,可制成大型设备,是该破碎机 的优点,但活动颚板有空载行程,使颚板受负荷不均,生产效 率低,破碎比小。
复杂摆动颚式破碎机动颚板的上下运动有促进排料的作用,而且其
上部的水平行程大于下部,易于破碎大块物料,故其破碎效率高于 简单摆动颚式破碎机。它的缺点是颚板磨损较快和物料因有过粉碎 现象而使能耗增高。
供选矿、化学、水泥、建筑材料等工业部门中碎 和细碎各种中等硬度以下的矿石和岩石之用。是煤炭、 电力、化工、建材、地质勘探和医药、教学、科研等行 业和部门破碎煤炭、矿石、岩石或其他中等硬度的非金 属物质。
3.4 锤式破碎机
锤式破碎机是破碎机设备之一,主要用于破碎石膏、砖 瓦、石灰石等物料。
一、工作原理
破碎机械是指排料中粒度大于三毫米的含量占总排料量50 %以上的粉碎机械。破碎作业常按给料和排料粒度的大小分为 粗碎、中碎和细碎。
常使用的破碎机械有颚式破碎机、圆锥破碎机、辊式破碎
机、锤式破碎机和反击式破碎机等几种。
3.1颚式破碎机
颚式破碎机是利用两颚板对物料的挤
压和弯曲作用粗碎或中碎各种硬度物料的 破碎机械。破碎机构由固定颚板和可动颚
旋摆运动。破碎锥时而靠近又时而 离开固定锥,完成破碎和排料。
微粉加工工艺及设备
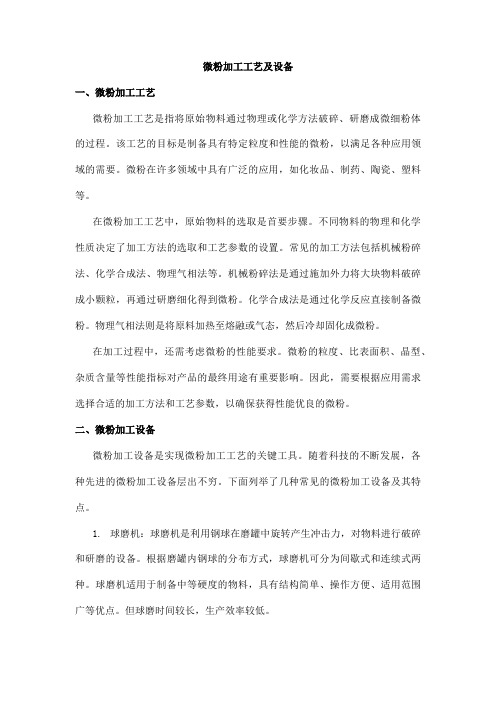
微粉加工工艺及设备一、微粉加工工艺微粉加工工艺是指将原始物料通过物理或化学方法破碎、研磨成微细粉体的过程。
该工艺的目标是制备具有特定粒度和性能的微粉,以满足各种应用领域的需要。
微粉在许多领域中具有广泛的应用,如化妆品、制药、陶瓷、塑料等。
在微粉加工工艺中,原始物料的选取是首要步骤。
不同物料的物理和化学性质决定了加工方法的选取和工艺参数的设置。
常见的加工方法包括机械粉碎法、化学合成法、物理气相法等。
机械粉碎法是通过施加外力将大块物料破碎成小颗粒,再通过研磨细化得到微粉。
化学合成法是通过化学反应直接制备微粉。
物理气相法则是将原料加热至熔融或气态,然后冷却固化成微粉。
在加工过程中,还需考虑微粉的性能要求。
微粉的粒度、比表面积、晶型、杂质含量等性能指标对产品的最终用途有重要影响。
因此,需要根据应用需求选择合适的加工方法和工艺参数,以确保获得性能优良的微粉。
二、微粉加工设备微粉加工设备是实现微粉加工工艺的关键工具。
随着科技的不断发展,各种先进的微粉加工设备层出不穷。
下面列举了几种常见的微粉加工设备及其特点。
1.球磨机:球磨机是利用钢球在磨罐中旋转产生冲击力,对物料进行破碎和研磨的设备。
根据磨罐内钢球的分布方式,球磨机可分为间歇式和连续式两种。
球磨机适用于制备中等硬度的物料,具有结构简单、操作方便、适用范围广等优点。
但球磨时间较长,生产效率较低。
2.振动磨:振动磨是一种利用高频振动将物料破碎成微粉的设备。
它由磨筒、振动电机和弹簧支撑架等部分组成。
在振动过程中,物料在磨筒内受到反复的冲击和摩擦作用,从而达到破碎和研磨的效果。
振动磨具有破碎能力强、粒度可调范围广、生产效率高等优点,但结构复杂、噪音较大。
3.气流磨:气流磨利用高速气流将物料吹向撞击板或研磨介质,通过冲击和摩擦作用将物料破碎成微粉。
气流磨可分为扁平式、流化床式和旋风式等类型。
气流磨具有粒度细、产量高、操作简便等优点,但能耗较大,适用于脆性物料的加工。
粉磨工艺流程
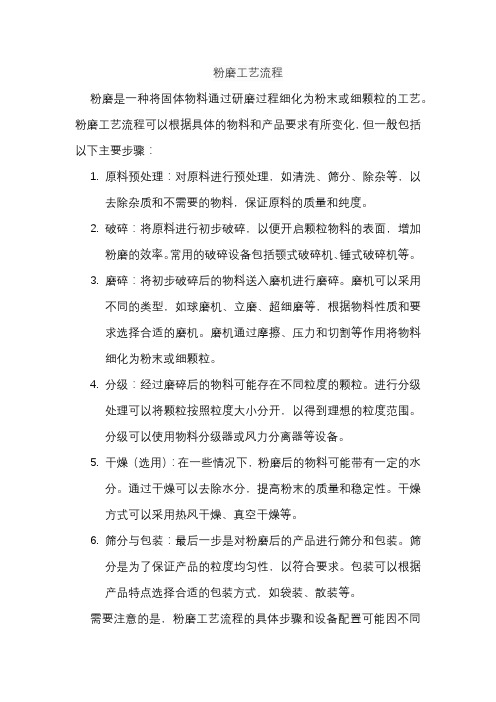
粉磨工艺流程
粉磨是一种将固体物料通过研磨过程细化为粉末或细颗粒的工艺。
粉磨工艺流程可以根据具体的物料和产品要求有所变化,但一般包括以下主要步骤:
1.原料预处理:对原料进行预处理,如清洗、筛分、除杂等,以
去除杂质和不需要的物料,保证原料的质量和纯度。
2.破碎:将原料进行初步破碎,以便开启颗粒物料的表面,增加
粉磨的效率。
常用的破碎设备包括颚式破碎机、锤式破碎机等。
3.磨碎:将初步破碎后的物料送入磨机进行磨碎。
磨机可以采用
不同的类型,如球磨机、立磨、超细磨等,根据物料性质和要
求选择合适的磨机。
磨机通过摩擦、压力和切割等作用将物料
细化为粉末或细颗粒。
4.分级:经过磨碎后的物料可能存在不同粒度的颗粒。
进行分级
处理可以将颗粒按照粒度大小分开,以得到理想的粒度范围。
分级可以使用物料分级器或风力分离器等设备。
5.干燥(选用):在一些情况下,粉磨后的物料可能带有一定的水
分。
通过干燥可以去除水分,提高粉末的质量和稳定性。
干燥
方式可以采用热风干燥、真空干燥等。
6.筛分与包装:最后一步是对粉磨后的产品进行筛分和包装。
筛
分是为了保证产品的粒度均匀性,以符合要求。
包装可以根据
产品特点选择合适的包装方式,如袋装、散装等。
需要注意的是,粉磨工艺流程的具体步骤和设备配置可能因不同
的物料和产品要求而有所差异,此处提供的是一般性的流程概述。
在实际应用中,需要根据具体情况进行调整和优化。
水泥粉磨工艺及设备

水泥粉磨工艺及设备水泥制造过程中,粉磨是其中一个关键环节,也是实现水泥产品高质量的关键。
粉磨过程通过将水泥熟料破碎细化,使其达到规定的细度要求,进而提高水泥的强度、稳定性、可操作性,为后续工序提供优质原料。
本文将介绍水泥粉磨工艺及设备的相关内容。
1、进料系统熟料在生产过程中出炉后,需要经过冷却和储存放置。
进料系统的作用即是将熟料送入到粉磨机的进料口。
2、粉磨机粉磨机是水泥粉磨过程中最重要的机器设备。
通常使用的粉磨机有球磨机、风扫式球磨机(如水泥制造中的辊压机)、立磨机等。
在粉磨过程中,经过一定粗细磨损,熟料会变得越来越细,以致于可以达到GGBS、矿渣微粉等较高的细度。
3、扬料机扬料机是用于将粉磨机中的水泥粉末输送到储存设备或炉内用于成品水泥制备的工序中的输送机械。
常见的扬料机有斗式扬料机和鼓式扬料机等。
4、分选系统分选系统是将粉磨机中的颗粒分选。
通过分选,可以分出符合规格要求的水泥粉末,以供后续使用,也可以将不符合规格要求的颗粒进行回磨,再次变成可用的原料。
5、储存装置粉磨后的水泥粉末需要存放在储存装置中,以便在需要用到时随时取出使用。
储存装置有多种形式,最常见的是水泥仓或散装水泥仓,以及袋装水泥储存堆库等。
二、水泥粉磨设备分类和特点:1、球磨机球磨机是目前使用最为广泛的水泥粉磨机种之一,其主要包括球磨机本身、配套的传动设备和磨介。
使用球磨机粉磨水泥熟料具有结构简单、便于操作、适于生产流程的特点。
但是由于球体受力不均、制粉效率低等因素,其在细粉生产方面的应用受到较大局限。
2、滚压机滚压机器(辊压机)属于较新型的粉磨机器,该机采用滚轮块状圆柱体,在相对转动的情况下将物料分层挤压碾磨,而获得细小颗粒的技术,也被称为压路机、压板机等。
较新型的滚压机一般采用上辊磨制粉的方式,能有效提高效率。
其优点是生产效率高,磨粉细度优良,但成本较高。
3、立磨机立磨机的主要特点是结构紧凑,小占地面积,但生产效率比球磨机和滚压机要低。
制粉工艺与设备第四节研磨
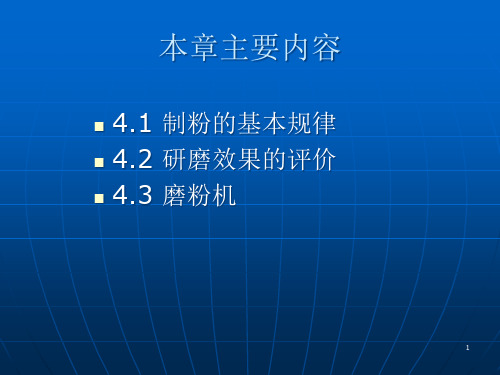
剥刮率一般由截取磨下物 来进行测定。
磨粉机对物料的破碎作用越强,其 剥刮率就越高,相应平筛粗筛的筛 上物数量越少,而渣、心、粉的数 量就越多。
剥刮率(%)
b料样重 a料样重 b料样重
100%
8
4.2 研磨效果的评价
2、取粉率
取粉率的测定及计算方法类似剥刮率,不同的是检验筛 面需采用对应平筛的粉筛筛面,其筛下物b为粉,筛上物a为 其他制品,测出的数据位磨下物中粉的含量,即取粉率。
20
5.3 喂料机构
作用: 将小麦均匀喂入研磨区磨辊全长上,并进入二辊间隙 处,流量可调。 对喂料辊的要求:
(1)保证连续而均匀的送料,沿着磨辊整个长度送下的物 料,其流层应厚薄一致;
(2)有高度的灵敏度,能准确地调整流量,当流量变化不 大时,还具有自动适应的能力;
(3)喂料机构与磨辊的相对位置应保证物料能正确地送入 磨辊的间距内,并具有一定的速度,以提高产量;
锥形磨:锥形母线磨辊, 磨小麦,杂粮。 对辊式磨粉机:广泛用于小麦,葡萄破碎,
啤酒麦芽轧碎等。 现以辊式用的最多,重点介绍。
11
4.3 磨粉机
研磨工作原理包括磨辊研磨过程及磨辊工作面的状 态对研磨的影响等内容,是研究磨粉机的基础。
2、磨辊的工作状态
工作时两辊相向转动,转速不同。其中转 速较快地磨辊称为快辊,转速慢的为慢辊。 物料由两辊间通过而受到研磨,两辊之间 形成较规则的研磨区。 轧距:两辊间最小的距离称为轧距。 速比:快辊和慢辊的转速之比称为速比。
②工艺过程中各设备间的联系和各种在制品、产品的流 动方向。
③小麦粉或副产品的分类与收集方法,配粉方式与设备。
3
小麦加工
2.绘制粉路图的要求 ①设备及其技术参数必须采用统一的图形或符号。 ②在图形符号的—侧要注明系统名称、设备的规格 数量和主要示,并在箭头处用文字 或代号注明去向。 ④各系统中各道设备的工艺符号,按制粉过程中的 大致顺序,在图中自左向右,自上而下进行绘制。
制粉工艺与设备
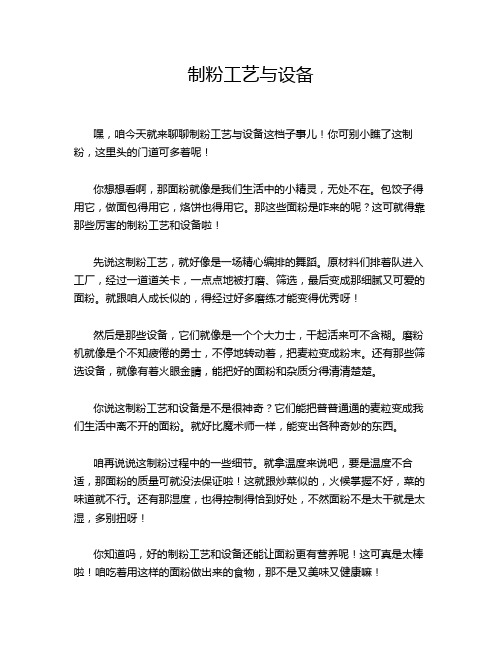
制粉工艺与设备嘿,咱今天就来聊聊制粉工艺与设备这档子事儿!你可别小瞧了这制粉,这里头的门道可多着呢!你想想看啊,那面粉就像是我们生活中的小精灵,无处不在。
包饺子得用它,做面包得用它,烙饼也得用它。
那这些面粉是咋来的呢?这可就得靠那些厉害的制粉工艺和设备啦!先说这制粉工艺,就好像是一场精心编排的舞蹈。
原材料们排着队进入工厂,经过一道道关卡,一点点地被打磨、筛选,最后变成那细腻又可爱的面粉。
就跟咱人成长似的,得经过好多磨练才能变得优秀呀!然后是那些设备,它们就像是一个个大力士,干起活来可不含糊。
磨粉机就像是个不知疲倦的勇士,不停地转动着,把麦粒变成粉末。
还有那些筛选设备,就像有着火眼金睛,能把好的面粉和杂质分得清清楚楚。
你说这制粉工艺和设备是不是很神奇?它们能把普普通通的麦粒变成我们生活中离不开的面粉。
就好比魔术师一样,能变出各种奇妙的东西。
咱再说说这制粉过程中的一些细节。
就拿温度来说吧,要是温度不合适,那面粉的质量可就没法保证啦!这就跟炒菜似的,火候掌握不好,菜的味道就不行。
还有那湿度,也得控制得恰到好处,不然面粉不是太干就是太湿,多别扭呀!你知道吗,好的制粉工艺和设备还能让面粉更有营养呢!这可真是太棒啦!咱吃着用这样的面粉做出来的食物,那不是又美味又健康嘛!哎呀,说了这么多,我就是想让你知道,制粉工艺与设备真的超级重要!它们就像是幕后的英雄,默默地为我们的美食生活贡献着。
没有它们,咱哪能吃到那么多好吃的面食呀!所以呀,咱可得好好珍惜这些来之不易的面粉,可别浪费哦!总之呢,制粉工艺与设备是个非常有意思也非常重要的领域。
咱得好好了解了解,这样才能更好地享受美食带来的快乐呀!你说是不是呢?原创不易,请尊重原创,谢谢!。
粉磨工艺和设备

粉磨工艺及设备第一章原料预均化第二章粉磨机械第三章粉磨过程及影响磨机产量的因素第四章粉磨系统的技术标定第五章收尘设备第六章其它输送设备第一章原料的预均化一.原料预均化的原理在堆放物料时,尽可能地以最高的相互平行和上下重叠的同厚度的料层构成料堆。
而在取料时,则在垂直料层方向,尽可能同时切取所有的料层,依次切取,直到取完为止。
这样取出的物料成分就比取放时要均匀得多,这就是所谓的平铺直取。
二、原料预均化的意义1、有利于稳定水泥窑正常的热工操作制度,提高产品质量,维持长期安全运转。
2、采用预均化技术,可以充分利用低品位矿石,有效利用资源,对发展国民经济具有重要意义。
三、原料预均化堆场评价方法1、标准偏差:衡量物料成分的波动情况式中,i x i ---物料中某成分的各次测量值x’---各次测量值的算术平均值n---测量次数2、均化效果:衡量均化设施的均化情况H=式中,H—均化效果S进—进入均化堆场前物料中某成分的标准偏差S入—出均化堆场后物料中某成分的标准偏差。
四、原料、燃料预均化的选用条件1、石灰石中CaCO3标准偏差大于3%时,应考虑预均化。
2、粘土(SiO2,Al2O3),当粘土中SiO2标准偏差大于56%时,应考虑预均化。
3、原煤灰分标准偏差大于5%时,应考虑预均化。
五、预均化堆场的布置形式1、矩形预均化堆场一般都有两个料堆,一个堆料,一个取料,互相交替。
2、圆形堆场作业方法一般采用3×120°的方法即1/3正在堆料,1/3正在取料,1/3已经堆料完成,整个堆场中,堆料、取料和储备都是轮流进行的。
六、堆料和取料方法1、堆料方法⑴人字形堆料法。
一般矿山在料的万分都不均匀,因为波动频率大时,各层原最佳以有可能铺上极高或极低万分的原料。
所以即使⑵波浪形堆料法⑶水平层堆料法⑷横向倾斜层堆料法⑸纵向倾斜层堆料法2、取料方法⑴端面取料⑵侧面取料⑶底部取料七、影响预均化效果的因素1、原料成分波动的影响2、物料离析作用的影响3、堆料布料不均的影响4、料堆总层数的影响八、对生料均化库的要求均化用压缩空气少,单位电耗低,库内空气装置简单,库的土建结构合理,造价低,操作维护简便,故障少,安全可靠,均化效果好。
粉磨工艺流程

粉磨工艺流程
《粉磨工艺流程》
粉磨工艺是一种非常重要的制粉方法,广泛应用于化工、食品加工、制药等行业。
通过粉磨工艺,原料可以经过特定的机械作用,被分解成微小的颗粒或粉末,从而增加其表面积,改善其流动性和溶解性。
下面将介绍一般粉磨工艺的流程:
1. 原料准备:首先,需要准备好待粉磨的原料。
原料应该符合相关的技术要求,例如粒度、含水量等。
2. 预处理:有些原料在粉磨前需要进行一些预处理步骤,例如破碎、干燥等。
这些预处理步骤可以帮助提高粉磨的效果。
3. 粉磨:将原料送入粉磨设备进行加工。
粉磨设备可以采用不同的方法,例如冲击破碎、摩擦研磨、切割磨碎等。
这些方法能够将原料破碎成所需颗粒大小的粉末。
4. 分级:粉磨后的颗粒可能会有不同的大小,需要进行分级处理,将符合规格的颗粒分离出来。
5. 包装:最后,经过粉磨和分级处理的颗粒需要被包装。
包装通常会根据颗粒的性质和用途进行选择,例如纸箱、袋装等。
以上就是一般的粉磨工艺流程。
通过粉磨,原料可以得到理想的粉末形态,从而满足不同行业的生产需要。
因此,粉磨工艺在工业生产中有着重要的地位。
粉磨工艺及设备
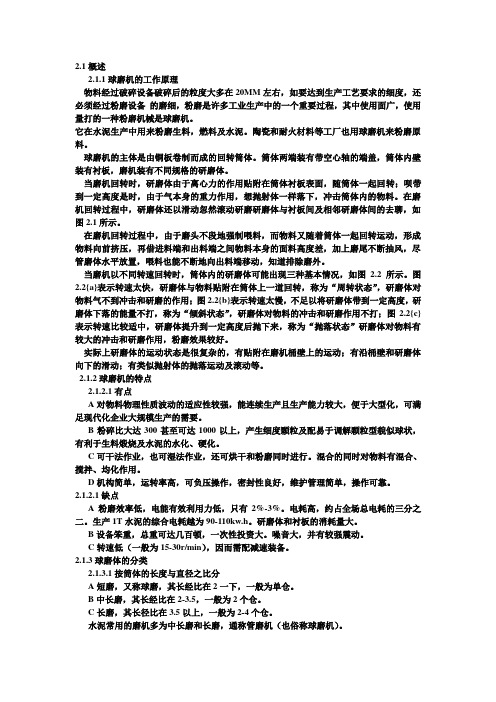
2.1概述2.1.1球磨机的工作原理物料经过破碎设备破碎后的粒度大多在20MM左右,如要达到生产工艺要求的细度,还必须经过粉磨设备的磨细,粉磨是许多工业生产中的一个重要过程,其中使用面广,使用量打的一种粉磨机械是球磨机。
它在水泥生产中用来粉磨生料,燃料及水泥。
陶瓷和耐火材料等工厂也用球磨机来粉磨原料。
球磨机的主体是由铜板卷制而成的回转筒体。
筒体两端装有带空心轴的端盖,筒体内壁装有衬板,磨机装有不同规格的研磨体。
当磨机回转时,研磨体由于离心力的作用贴附在筒体衬板表面,随筒体一起回转;呗带到一定高度是时,由于气本身的重力作用,想抛射体一样落下,冲击筒体内的物料。
在磨机回转过程中,研磨体还以滑动忽然滚动研磨研磨体与衬板间及相邻研磨体间的去聊,如图2.1所示。
在磨机回转过程中,由于磨头不段地强制喂料,而物料又随着筒体一起回转运动,形成物料向前挤压,再借进料端和出料端之间物料本身的面料高度差,加上磨尾不断抽风,尽管磨体水平放置,喂料也能不断地向出料端移动,知道排除磨外。
当磨机以不同转速回转时,筒体内的研磨体可能出现三种基本情况,如图2.2所示。
图2.2{a}表示转速太快,研磨体与物料贴附在筒体上一道回转,称为“周转状态”,研磨体对物料气不到冲击和研磨的作用;图2.2{b}表示转速太慢,不足以将研磨体带到一定高度,研磨体下落的能量不打,称为“倾斜状态”,研磨体对物料的冲击和研磨作用不打;图2.2{c}表示转速比较适中,研磨体提升到一定高度后抛下来,称为“抛落状态”研磨体对物料有较大的冲击和研磨作用,粉磨效果较好。
实际上研磨体的运动状态是很复杂的,有贴附在磨机桶壁上的运动;有沿桶壁和研磨体向下的滑动;有类似抛射体的抛落运动及滚动等。
2.1.2球磨机的特点2.1.2.1有点A对物料物理性质波动的适应性较强,能连续生产且生产能力较大,便于大型化,可满足现代化企业大规模生产的需要。
B粉碎比大达300甚至可达1000以上,产生细度颗粒及配易于调解颗粒型貌似球状,有利于生料煅烧及水泥的水化、硬化。
粉磨工艺流程
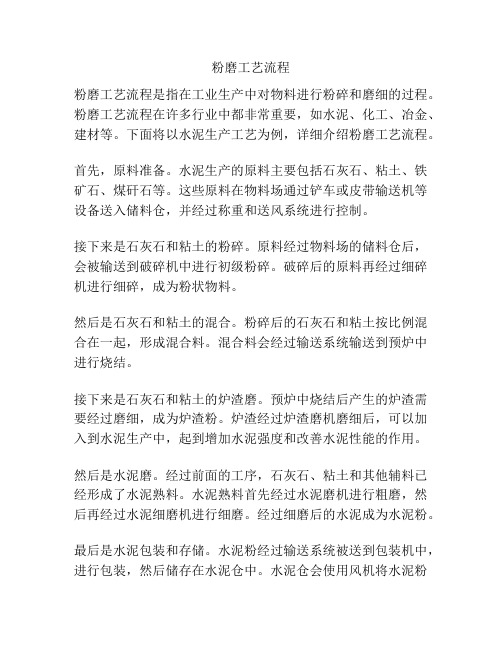
粉磨工艺流程粉磨工艺流程是指在工业生产中对物料进行粉碎和磨细的过程。
粉磨工艺流程在许多行业中都非常重要,如水泥、化工、冶金、建材等。
下面将以水泥生产工艺为例,详细介绍粉磨工艺流程。
首先,原料准备。
水泥生产的原料主要包括石灰石、粘土、铁矿石、煤矸石等。
这些原料在物料场通过铲车或皮带输送机等设备送入储料仓,并经过称重和送风系统进行控制。
接下来是石灰石和粘土的粉碎。
原料经过物料场的储料仓后,会被输送到破碎机中进行初级粉碎。
破碎后的原料再经过细碎机进行细碎,成为粉状物料。
然后是石灰石和粘土的混合。
粉碎后的石灰石和粘土按比例混合在一起,形成混合料。
混合料会经过输送系统输送到预炉中进行烧结。
接下来是石灰石和粘土的炉渣磨。
预炉中烧结后产生的炉渣需要经过磨细,成为炉渣粉。
炉渣经过炉渣磨机磨细后,可以加入到水泥生产中,起到增加水泥强度和改善水泥性能的作用。
然后是水泥磨。
经过前面的工序,石灰石、粘土和其他辅料已经形成了水泥熟料。
水泥熟料首先经过水泥磨机进行粗磨,然后再经过水泥细磨机进行细磨。
经过细磨后的水泥成为水泥粉。
最后是水泥包装和存储。
水泥粉经过输送系统被送到包装机中,进行包装,然后储存在水泥仓中。
水泥仓会使用风机将水泥粉送入卸料管道,最后通过卡车等运输工具运出。
总结起来,粉磨工艺流程主要包括原料准备、原料粉碎、原料混合、炉渣磨和水泥磨、水泥包装和存储。
这些工序紧密配合,形成了完整的粉磨工艺流程。
通过粉磨工艺,原料可以被粉碎、磨细,提高物料的利用率和水泥的性能,对于工业生产有着重要的意义。
制粉工艺技术方法
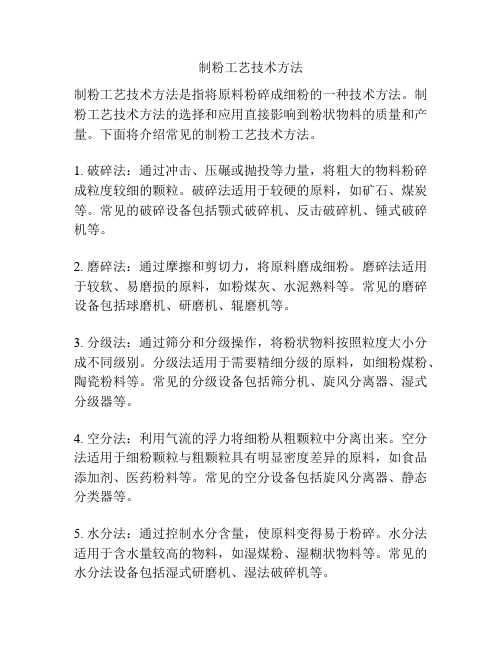
制粉工艺技术方法制粉工艺技术方法是指将原料粉碎成细粉的一种技术方法。
制粉工艺技术方法的选择和应用直接影响到粉状物料的质量和产量。
下面将介绍常见的制粉工艺技术方法。
1. 破碎法:通过冲击、压碾或抛投等力量,将粗大的物料粉碎成粒度较细的颗粒。
破碎法适用于较硬的原料,如矿石、煤炭等。
常见的破碎设备包括颚式破碎机、反击破碎机、锤式破碎机等。
2. 磨碎法:通过摩擦和剪切力,将原料磨成细粉。
磨碎法适用于较软、易磨损的原料,如粉煤灰、水泥熟料等。
常见的磨碎设备包括球磨机、研磨机、辊磨机等。
3. 分级法:通过筛分和分级操作,将粉状物料按照粒度大小分成不同级别。
分级法适用于需要精细分级的原料,如细粉煤粉、陶瓷粉料等。
常见的分级设备包括筛分机、旋风分离器、湿式分级器等。
4. 空分法:利用气流的浮力将细粉从粗颗粒中分离出来。
空分法适用于细粉颗粒与粗颗粒具有明显密度差异的原料,如食品添加剂、医药粉料等。
常见的空分设备包括旋风分离器、静态分类器等。
5. 水分法:通过控制水分含量,使原料变得易于粉碎。
水分法适用于含水量较高的物料,如湿煤粉、湿糊状物料等。
常见的水分法设备包括湿式研磨机、湿法破碎机等。
6. 压缩法:利用高压力将原料压缩成颗粒,然后再进行细碎和分级。
压缩法适用于需要高度均匀颗粒的原料,如冶金焦粉、造纸用材料等。
常见的压缩设备包括压缩机、压力辊机等。
以上是常见的制粉工艺技术方法,不同的原料和粉末要求适用不同的方法。
在实际应用中,常常会综合利用多种方法,通过多级粉碎和分级操作来获得所需的粉末。
此外,还需要根据原料的特性和生产要求,在制粉的过程中进行适当的控制和调整,以确保产品的质量和产量。
- 1、下载文档前请自行甄别文档内容的完整性,平台不提供额外的编辑、内容补充、找答案等附加服务。
- 2、"仅部分预览"的文档,不可在线预览部分如存在完整性等问题,可反馈申请退款(可完整预览的文档不适用该条件!)。
- 3、如文档侵犯您的权益,请联系客服反馈,我们会尽快为您处理(人工客服工作时间:9:00-18:30)。
6
小麦加工
系统代号
表4-9 粉路中常用代号
意义产品代号Fra bibliotek意义B
皮磨系统
F
小麦粉
S
渣磨系统
Br
M
心磨系统
G
麸皮 麦胚
T
尾磨系统
P
清粉
设备代号 BrF BrB D
意义 打麸机 刷麸机 重筛
注;1.各系统先后顺序用阿拉伯数字1、2、3……表示。如1B、2M。 2.各道磨分粗细时,分别在系统代号右下角用小写的c、f表示。如2BC、1MF。 3.不同品种小麦粉,在代号前用阿拉伯数字区别。如1F、2F。 4.设备顺序,在相应代号前用阿拉伯数字区别。如1Br、2D。
2、磨辊的工作状态
工作时两辊相向转动,转速不同。其中转 速较快地磨辊称为快辊,转速慢的为慢辊。 物料由两辊间通过而受到研磨,两辊之间 形成较规则的研磨区。 轧距:两辊间最小的距离称为轧距。 速比:快辊和慢辊的转速之比称为速比。
2020/6/14
13
4.3 磨粉机
3、 制粉对磨粉机的要求
① 能耗小,物料流量要大(生产率高); ② 研磨效果好,不伤麸皮,胚乳刮净、能出粉、出
2020/6/14
18
2020/6/14
19
5.1 机身
机座用铸铁制造,机壳上部有玻璃门, 以便观察机内情况,揭开此门,即可调节 喂料。在下部有磨膛门,可开启检查研磨 后的物料。
2020/6/14
20
5.2 研磨机构-----磨辊
分快、慢辊和 “齿辊” 、 “光辊”两种, 起研 磨作用。
齿辊是在圆柱面上用拉丝刀切削成磨齿,用于 破碎谷物,剥刮麸片上的胚乳。
磨粉机对物料的破碎作用越强,其 剥刮率就越高,相应平筛粗筛的筛 上物数量越少,而渣、心、粉的数 量就越多。
剥 刮 率 ( %) a料 样 b 重 料 样 b 重 料 样 重 100%
2020/6/14
9
4.2 研磨效果的评价
2、取粉率
取粉率的测定及计算方法类似剥刮率,不同的是检验筛 面需采用对应平筛的粉筛筛面,其筛下物b为粉,筛上物a为 其他制品,测出的数据位磨下物中粉的含量,即取粉率。
②工艺过程中各设备间的联系和各种在制品、产品的流 动方向。
③小麦粉或副产品的分类与收集方法,配粉方式与设备。
2020/6/14
4
小麦加工
2.绘制粉路图的要求 ①设备及其技术参数必须采用统一的图形或符号。 ②在图形符号的—侧要注明系统名称、设备的规格 数量和主要技术参数。磨辊技术特性亦可单独列表说明。 ③各种物料的流向用箭头表示,并在箭头处用文字 或代号注明去向。 ④各系统中各道设备的工艺符号,按制粉过程中的 大致顺序,在图中自左向右,自上而下进行绘制。
2020/6/14
5
小麦加工
3.粉路图中的图形符号及代号 粉路图中的图形符号应能简单明确地反映设备的 特点。一般用该设备最具代表性的剖面或一个投影面 的示意图来表示。GB/T12529.3-90规定了粉路图中 通常使用的图形符号,(附录二)。 在该标准中还规定了有关代号,见表4-9。
2020/6/14
2020/6/14
7
4.2 研磨效果的评价
处于不同工作位置的磨粉机,对其破碎效果的 要求也将不同。对于皮磨,将主要控制其破碎、 剥刮物料的能力,通常用剥刮率作为衡量的指 标;对于心磨,一般采用取粉率来衡量其研磨 物料提取面粉的能力。
2020/6/14
8
4.2 研磨效果的评价
1、剥刮率
剥刮率一般由截取磨下物 来进行测定。
光辊则经磨光后采用喷砂处理,得到绒状的微 粗糙表面,用于磨制高等级面粉的心磨系统,将 胚乳颗粒磨细成粉和处理细小的连粒麸屑。
2020/6/14
21
5.3 喂料机构
作用: 将小麦均匀喂入研磨区磨辊全长上,并进入二辊间隙 处,流量可调。
2020/6/14
15
4.3磨粉机
5、磨粉机的基本结构与工作过程
2020/6/14
16
工作过程
4.3磨粉机
2020/6/14
17
4.3 磨粉机
磨粉机主要有机身、研磨机构、喂料机构、磨 辊轧距调节机构、液压自动控制机构、传动机构 及清理装置七个主要部分组成。
大型磨粉机上筛理装置是独立的。 小型磨粉机上磨粉和筛理装置是一体的。
若产品为高等级面粉,粉筛采用较密的筛网,检验时筛 理时间应适当延长。测同一工艺流程中各道磨粉机取粉率时, 检验筛理时间应一致。
在以生产高等级粉为主的制粉工艺中,前路心磨得取粉 率一般为30%-40%,而后路心磨得取粉率将低于这个数值。
2020/6/14
10
2020/6/14
11
4.3 磨粉机
1、磨粉原理
2020/6/14
3
小麦加工
2、粉路图
制粉流程是将制粉工序组合起来,对入磨净麦按一定的 精度等级标准进行加工的生产工艺流程,简称粉路。
粉路图是表达整个制粉工艺过程的工程图。通常用图形 及符号表示各种工艺设备,用箭头、文字或代号表示物料的流 动方向。
1.粉路图的内容 粉路图主要包括以下内容:
①各类工艺设备的规格、数量、主要技术参数。
渣、出面、麦心; ③ 温升不能太高,便于贮存,养分损失少; ④ 调节维修方便。
2020/6/14
14
4.3 磨粉机
4、辊式磨粉机的特点
它是一对以不同速度相向旋转的圆柱形磨辊, 物料通过两辊之间,依靠磨辊的相对运动和磨齿 的挤压、剪切作用而粉碎。辊式磨粉机是现代面 粉厂广泛使用的研磨设备,有各种调节机构,能 适应制粉工艺过程中各种要求,故具有生产效率 高,工艺效果好等优点。
片磨:石磨、钢磨、砂磨、陶瓷磨. 两圆盘挤压、摩擦,磨米粉、豆浆。
锥形磨:锥形母线磨辊, 磨小麦,杂粮。 对辊式磨粉机:广泛用于小麦,葡萄破碎,
啤酒麦芽轧碎等。 现以辊式用的最多,重点介绍。
2020/6/14
12
4.3 磨粉机
• 研磨工作原理包括磨辊研磨过程及磨辊工作面的状 态对研磨的影响等内容,是研究磨粉机的基础。
制粉工艺与设备第四节研磨
本章主要内容
• 4.1 制粉的基本规律 • 4.2 研磨效果的评价 • 4.3 磨粉机
2020/6/14
2
4.1 制粉的基本规律
• 1、在制品
小麦经过1B研磨后,即成为 许多粒度、品质不同的混合 物料,这些物料必须按粒度、 品质分类,再经过多道磨筛 工作单元逐步地进行研磨筛 分,才能够从原料中提取质 量、数量均符合要求的面粉。 因此,由各工作单元提取、 分类的物料,基本上都是制 粉工艺过程中的中间产品, 即在制品。