锣带制作标准
锣带制作培训文件1

2021/7/10
12
2.对输入文件的处理
1:利用入图中的命令将输 入的文件移动到原点。
2:也可以利用move将资 料移动到绝对原点。
2021/7/10
13
3.将文件资料对齐
1:用如图所示的命令将各 层分别对齐。
2:也可以利用move命令将 各个层移动到相同的TAB
R2mm
2021/7/10
单元
43
8.4.2 : TAB边 上要加工具孔和光点
光点DIA2.0mm,绿油开窗: DIA3.0mm,无铜皮时要加保 护圈,两面
DIA4.0mm或2.0mm (3X)
2021/7/10
44
8.4.3 :加退刀槽 退刀槽
2021/7/10
45
8.4.4 :内角
2021/7/10
9
• G33X#Y#A#
机锣指令
逆时针锣圆
指令后面提供了X和 或Y表示圆心的坐标。A#表示运 动轨迹的半径(圆)。
2021/7/10
10
• M15 表示下刀指令其通常在G00指令
后面。
• M16 表示收刀指令,自成一行。
• M25 表示需要重复的图形,与M01与
M02的指令粘合行动.
5. 新添一层,对要求作锣带的outline作描线处理, 其具体操作如下:
2021/7/10
15
6.:将描线层生成锣带
将描线层生成锣带
要求在nc editor的界面中选择 gerber to mill
2021/7/10
16
7. 生成锣带时的具体操作:
在此界面中根据实际
需要来定义要用到的 刀径.
4:将处理好的程式再导入文件重新检查。 (主要是针对其排版,间距,是否有变 形来检查)
用genesis2000做锣带教程

選定 層別
G07-Rout 28
排版輸出
步驟六. 程式輸出 ( Output) 細部參數
座標單位 MM ; INCH 座標模式 Abs; Inc 是否輸出小數 省零模式 整數與小數位數 是否省略相同座標 刀具單位
G07-Rout
29
G07-Rout10Fra bibliotekG07-Rout
11
步驟四. 確認及標示尺寸 ( Dimension )
可量測, 標示或調 整尺寸, 並可做圖形自 製.
G07-Rout
12
量測與標示 尺寸模式
確認及標示尺寸 ( Dimension )
指定起點
指定終點
量測值,可直接 輸入新值修改
G07-Rout 13
確認及標示尺寸 ( Dimension )
成型程式編輯 Genesis2000
Rout Editing
G07-Rout
1
成型程式編輯
Rout Editing
步驟一. 取得 (自製) 外型線 步驟二. 整理外型線 ( Design to Rout ; Connection)
步驟三. 層別特性轉換 ( Matrix -> Rout )
步驟四. 確認及標示尺寸 ( Dimension ) 步驟五. 刀具及切割路線設定 ( Chain ) 步驟六. 程式輸出 ( Output ; ARM )
21
步驟五. 刀具及切割路線設定 ( Chain )
變更已設定之參數
G07-Rout
22
步驟五. 刀具及切割路線設定 ( Chain )
刪除 Chain 設定
需點選欲刪除之 chain ( 亦可再選層中個 別線段做局部刪除)
PCB锣机操作规程及工艺技术要求
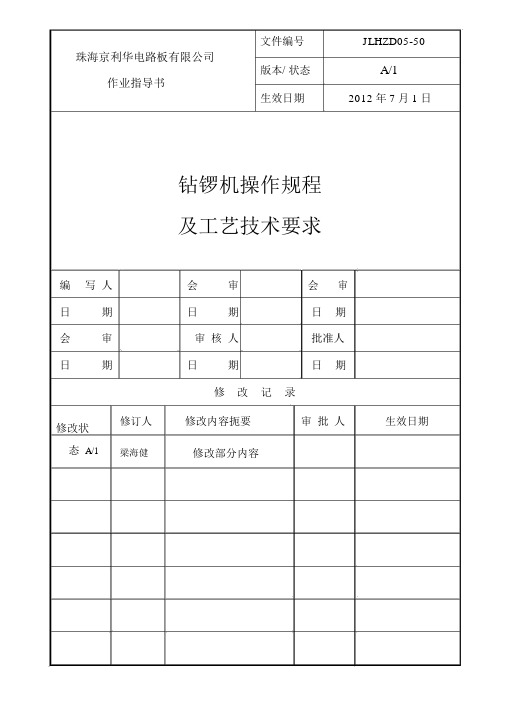
文件编号JLHZD05-50 珠海京利华电路板有限公司版本/ 状态A/1 作业指导书2012年7月1日生效日期钻锣机操作规程及工艺技术要求编写人会审会审日期日期日期会审审核人批准人日期日期日期修改状态A/1 修订人梁海健修改记录修改内容扼要修改部分内容审批人生效日期作业指导书版本A/1标题:BST系列 PCB钻锣机操作规程及工艺技术要求页码第 1 页共 3 页工人工序内容及要求设备种数及工具一、工作流程吸尘器钻 1 接收板→对照 PCB 板编号调钻锣带资料→试钻锣一块自检→合格→交与抽水孔QA 首检→合格→批量生产→样板不用V 刻的就直接过后工序→样板泵人需要 V 刻的就要给移交 V 刻小组 V 刻→生产板钻锣好移交给后工序并做好移交记录。
(一)操作规程1)操作前准备;2)清洁机台及周围卫生特别是感应器;3)检查机器是否运行正常,抽水泵的水管的水是否循环,吸尘器是否可以吸尘;4)打开电脑主机,在网上邻居菲林完成上查找 PCB 板编号,将查找到资料拷贝到我的电脑桌面下调入钻锣带,检查资料是否有重孔和有没有补偿对不对,确认资料无误后,将钻锣带优化,然后调出钻锣带,打开钻锣机电源开关;双击桌面“ BSTCN。
EXE”软件,然后双击右上角“更多”出现一个界面有配置参数单位:选公制;省零方式:选后省零;数据方式:选整数位 3,小数位 3;数据方式:绝对,然后确定。
再出现一个小窗口 Z 轴参数:抬钻高度一般 3~4(mm);板材厚度根据所放几块板的厚度相加再加一个 1 mm 即可;下止点;对刀时的高度再加上 0.5 mm。
填写完毕关闭后,又出现一个窗口,一般只填写以下参数:填写基准抬刀高度和基准进刀速度和 XY 空移速度,填写完后,然后点击参考工艺,然后关闭。
按“ F9”返回原点,移动 X 与 Y 轴到有垫板地方,用手动装上钻头,然后再按“ F9”返回原点,按“ F5”加工。
5)加工好一块做首检,准备好工作中所需要的工具测量。
锣带的制作规范
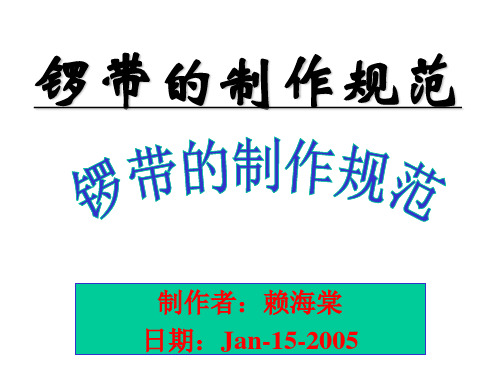
公 差 在 3 或 以 下
注 意 要 拉 边 料
MIL
3、若是要求比较大的锣坑或锣孔,则必 须先在坑里面拉直线(用G40指令)或者 钻孔,将锣坑或锣孔分成若干部分,然 后再正常锣成型(注意下刀位距单元内 板边的距离),以防止板边有凹凸位或 因边料未拉断而撞断锣刀(边料应拉小 至5MM以下)。 若是边料有35MM或以 上的锣坑或锣孔则不用拉直线而直接锣 成型,但必须要注意下刀位尽量保持与 锣坑的其中一个角大约成45度,可避免 伤到锣坑边或造成单元板边凹凸不平 。
1ST锣带的位置按MI要求做,特别 注意要锣入单元内2MIL,并检查锣 后是否会伤到单元内或Breakout位。 可用CAM350软件将锣带资料转换成 有补偿的图形与原装外围对拍检查。 2ND锣带若对应位置有钻披峰的孔, 则在离板边电镀区10MIL处下刀和收 刀(以防止铜皮被扯掉),无钻披峰 的孔则在板边电镀区处下刀和收刀。
七、特殊板的做法(综合内容):
1、内存条板的特殊做法:先用1.70至 1.90mm的大锣刀在锣手指位时预留4mil 的余料(另外要先锣非金手指边,再锣 金手指边),再用1.50mm的指定锣刀锣 手指位并加3mil补偿将外围成型(前后 共有7mil的相差),以减少披峰的产生。 另外内存条的KEY SLOT位必须在锣完 1.50mm锣刀后接着用锣金手指板的KEY SLOT的方法锣出来,特别注意两边同时 让刀的外围只加2mil的补偿(内存条的 两边,类似的也只加2mil的让刀补偿)。
走三 个点
不变
四 、 板 边 有 凹 凸 位 的 制 作 方 法 (特别是有金手指的板): 1、若单元间距是3.80MM或以上的 板,可用2.00或2.40MM的锣刀正常 锣出外围(如果单元间距是锣刀直 径的1.75倍或以上的板,则不用在 板边预拉直线而直接锣成型)。 2、尽量通过修改锣板顺序(即 重复程序),可减少预拉直线和 避免造成板边凹凸不平的情况。
京剧大锣尺寸标准

京剧大锣尺寸标准一、简介京剧大锣是京剧伴奏乐器之一,也是京剧表演中不可或缺的重要元素。
它在演出中发挥着承上启下的作用,旋律高亢激昂,与演员的动作相互呼应,营造出磅礴壮丽的视听效果。
本文将探讨京剧大锣的尺寸标准,包括其大小、重量、制作材料以及演奏技巧等方面的内容。
二、大锣的大小标准2.1 尺寸要求京剧大锣的大小要根据其不同的用途来定。
一般来说,主要有两种尺寸标准:大锣和小锣。
大锣通常用于重大场合和大型剧目的演出,而小锣则多用于轻松愉悦的剧目中。
2.2 大锣的直径和高度一般情况下,大锣的直径在30-40厘米之间,高度为4-6厘米。
这个尺寸的选择是为了使得大锣在演奏时能够发出响亮而富有穿透力的声音,给观众带来视听上的震撼。
三、重量标准3.1 重量要求京剧大锣的重量也是非常重要的一项标准。
大锣的重量通常在5-8千克之间,要根据演奏者的体力来确定合适的重量。
过重则会给演奏者带来困扰,过轻则会影响到演奏时的稳定性。
3.2 选材和制作大锣的选材一般采用高品质的铜制材料,经过多道工序的锻造、冷却和打磨等处理,以保证大锣的质地和音质。
制作大锣的工艺需要经验丰富的匠人进行,他们会根据锣的大小和重量要求来选择合适的材料和制作方法,保证大锣的质量达到标准。
四、演奏技巧4.1 持锣方式演奏京剧大锣时,演奏者一般使用两根木杆来持锣。
锣通过绳索或者皮带固定在木杆上,演奏者通过摆动木杆来敲击锣面。
演奏者的姿势和动作需要稳定而灵活,以确保锣面与锣杆的间距和角度适当。
4.2 敲击技巧和节奏演奏京剧大锣时,需要注意敲击的力度和节奏。
大锣的音色丰满而独特,演奏者需要通过掌握合适的敲击力度来打出清晰而饱满的音响。
同时,演奏者还需要与其他乐器和演员的表演动作相配合,确保节奏的准确和统一。
4.3 表达情感京剧大锣在演出中有着举足轻重的地位,不仅能够引领气氛,还能够表达角色的情感。
演奏者需要通过掌握好节奏和力度,将角色的情感和剧情发挥到极致,给观众带来视听上的享受和共鸣。
CAM350锣带

锣带制作培训
锣带制作注意事项: 1.检查所有的外形数据是否和MI标示一致。 2.当有不对称公差时要调整外形至合理范围 才能制作锣带 3.选定位孔时以较大的NP孔为优先,并且应 注意孔的分布,以尽量靠近板边和四角为最 佳
锣带制作培训
4.同一条锣带须补偿的地方只能用一种补偿, 〈如G42右补偿〉 5.内槽锣刀和外形锣刀必须分刀,以利于生产 控制 6.能走单刀时应尽量走单刀,不能走循环方 式,以节约成本 7.内槽和外形的走刀方向不能一致
锣带制作培训
四:增加刀具表
锣带制作培训
2. 刀具表设置
锣带制作培训
五:制作锣带
1.添加钻孔
锣带制作培训
2. 画锣带
锣带制作培训
3.排版
锣带制作培训
六:输出锣带
锣带制作培训
七:小结 CAM350是制作锣带的有力武器,只要运 用得当,应可使工作得心应手。但同时也存 在一些弊端,(如容易产生飞刀现象,捕捉 不够精准等)所以在运用的时候应多注意检 查,以避免一些不必要的问题发生。
点此处调入GDG
锣带制作培训
二:测量定位孔的孔 径、确认外形数据 1. 测量孔径:点Q 键,然后在需测的孔上 点左键,则会显示相关 信息,如图:
锣带制作培训
2.测量外形:
锣带制作培训
三:新增锣带层、进入 NC编辑器
点Y键新增锣带层
锣带制作培训
进入NC 编辑器
只有在NC编辑的状态下 才能够制作锣带
2008-8-的 1: 规范锣带的制作 2:为后续的锣带制作提供参考 二:培训对象 相关锣带制作人员 三:培训人 黄运芬
锣带制作培训
因本厂锣机的限制,需要制作二种格式的锣 带: 有补偿的锣带和没补偿的锣带 通常情况下只须制作有补偿的锣带,没补偿 的锣带只在锣房通知的情况下才制作 有补偿的锣带采用G42右补偿,利用 CAM350软件制作,没补偿的锣带利用GCCAM制作
锣带的制作规范
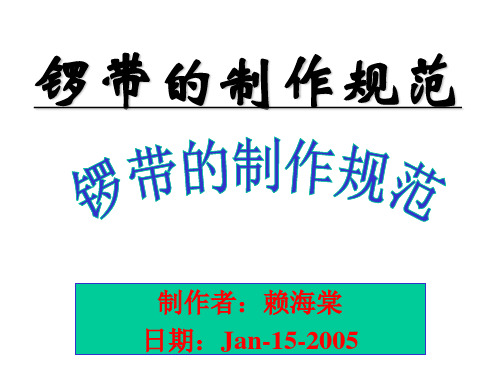
下刀位
下刀位
5、若有与圆弧相交的直线段不足半个锣 刀时,即不够退刀位置(如下图所示), 可考虑分两部分锣出,先锣直线段并在A 示处起刀,然后在B示处下刀并锣至圆弧 与直线的交点,接着就可锣圆弧然后再 到C点,或者将这部分改用走中间补偿来 锣板(其它部分仍用G42补偿锣板)。
若R1圆弧与直线F可以相交,则在制作 锣带时改为在E点下刀,接着锣直线至直 线F与R1圆弧的交点,然后锣圆弧至R1 圆弧与直线G的交点D(注意此段圆弧必 须一次性锣出来,不能走2段圆弧,否则 将因退刀位不够而锣到单元内,切记), 最后再锣至C点。。。。。。
退 刀 位
或 再者 用先 小用 锣大 刀锣 锣刀 内锣 角一 处次 。,
2、若是有≥15.0MM的锣孔,则选用 2.00MM或2.40MM的锣刀一次性锣出, 并且将锣孔半径加大1MIL。若是外围公 差要求为≤±3MIL或15MM以下的锣孔, 则采用两次锣出的方法锣成型。 即第一次锣出比锣孔半径小15MIL的孔, 第二次锣时将半径加大3MIL(因有留让 刀),可避免因锣孔不圆而严重超公差。 另外不管是一次性锣出还是两次锣出的 锣孔都选用2.0MM或2.4MM的锣刀锣出 来(除板边有绿油窗选用2.0MM的锣刀 以外,其它的用2.40MM的锣刀锣出)。
G41
G42
3、板长超过27in或板宽超过20in的外围, 要分开两条锣带才能锣板(MI上可能会 只要求制作一条锣带,可不用理会), 并且将锣带的零点大概定在板的中间。
三、锣SLOT槽的制作方法:
1、金手指板的KEY SLOT位用相应的锣 刀来回两刀锣出(用G40指令),并且将 其深度加深1 MIL,KEY SLOT位下刀 点出板边20~25 MIL,可避免单元边爆 板严重或压伤到另一个单元边。 2、小于1.60MM并且长度小于35MM的 SLOT槽和大于或等于1.60MM但长度小 于5MM的SLOT槽(例如1.80X3.80)用 与其宽度相同的锣刀来回两刀锣出(用 G40指令)——其作用主要为了除粉尘。
锣带设计要求 (2)

啤板后修锣的板,直接成型时预锣必须逆时针打偏移,打偏移前需改小刀径(参考TG130℃的标准),修锣正常使用G42打补偿方式。
21
工艺边较窄、长、没有固定孔或连接位时,内槽需先锣靠近工艺边的一端,走刀方向使用逆时针锣一遍。(详见SOP:5.4.8)
22
锣圆时,为改善圆小问题,预锣使用G33锣一遍(逆时针相当于G41补偿),修锣时使用G32锣两遍(顺时针相当于G42补偿),注意预锣、修锣顺序错误会报废!
31
蚀刻前一锣半孔时,下刀会锣破半孔时需增加小刀锣下刀点(详见附件1第七项)
32
锣PTH的锣带必须有补偿。下刀点必须在工程预钻孔内。
5
防反、防漏锣孔必须单独另建一把刀,不能和其他刀合并。
6
锣
带
设
计
要
求
直线路径到圆弧路径要相切。
7
夹角中的直线长度小于等于锣刀直径则锣带不用画此段直线。
8
圆弧半径等于小于锣刀半径,则不用画此圆弧。
9
下刀后先走直线才能走弧线,防止变形。
10
内槽的锣刀路径不得在外直角处相交。
11
不可在外直角处下刀。
12
板材TG值≤130℃的,为改善板灰,内槽预锣必须逆时针打偏移,偏移需改小刀径,0.8-1.0刀改小0.04mm,1.1-1.3刀改小0.05mm,1.4-1.5刀改小0.08mm,1.8-2.0刀改小1.0mm。修锣正常使用G42打补偿方式。
1
定位孔要求
小于1.6mm的定位孔增加外围孔定位。每SET使用6-8个孔定位。小于1.0的孔要>10个
2
有一锣(蚀刻前半孔、PTH槽,沉金前锣槽)的,必须有外围孔
3
定位孔到锣刀路径最近的距离不得小于0.5mm。
genesis2000制作锣带教程

Genesis2000制作锣带教程
Genesis2000的功能非常强大,由于操作界面友好,所以一直备受线路板从业人士的推崇。
Genesis2000不仅可以用来制作各种生产菲林、钻孔文件,而且可以制作飞针资料、AOI、锣带等工程资料。
今天我们酒来跟大家分享,如何利用genesis2000制作锣带?
操作步骤如下:
第1步 导入资料
以下举例,随便导入一款线路板资料
第2步 处理轮廓
这里需要注意的是,有的资料已经有处理好的轮廓,直接网络选中就可以,然后将轮廓拷贝到一个新的层。
如果是第一次处理客户资
料,大多数时候需要我们进行基本处理,例如轮廓不完整连接在一起,中间被打断了,那么就需要我们手工连接起来;又如,轮廓的线粗不一致,需要我们把线粗设置成一样,这样做的目的是,为了防止过程中出错。
第3步 定义层属性
我们用out层制作锣带,那么层的属性需要定义为rout层,同时板子的属性定义为board,因为锣带程序将来是需要作用到产品上。
第4步 生成锣带
①选择Rout→chains
②输入相关参数
只需要输入两个基本参数就可以,第一个是Tool size,这是刀具的直径;第二个是Compensation,这是走刀方向,即朝内侧锣还是朝外侧锣,这两个参数的设定是根据公司的常规工艺来确定的,还有板子的实际情况,需要制作人员提前考虑周全。
③点击apply→OK即可生成锣带
当然,这只是初步生成,还需要工程人员仔细检查走刀方向,以及过渡的地方设计是否不合理,如果发现不合理的地方,那么还需要手工调整。
CAM350锣带制作步骤

CAM350锣带制作步骤
1:导入钻孔文件及外形GERBER 2:对照MI测量成品外围
3:进入NC编状态----建立新的空钻孔表
4:建立新的NC层(锣带层)-----把刚建的空钻孔表赋于该层
5:选生产钻带中一个成品内的管位孔(GH1,2,3)COPY至锣带层(注意 先要确定下刀位及用来拼版的成品)
6:打开钻孔表把管位孔径改成与MI一致,并增加锣刀刀径或钻下刀位刀径
<注意刀排序>
7:板边钻防错孔及定位孔及下:锣板(一般先锣内槽再锣外形框)(选择锣刀描外形线,注意行刀方向, 可通过右补偿后线中心在板外来判断)
9:改变补偿(用右补偿)
编锣带时的一些常用指令
10:输出锣带并在写字板中拼版
11:导入CAM350检查有没变形或拼版错误,无误后填写参数表格
锣带制作标准

锣带制作标准作者: 日期:铣带制作标准1.程式指令介绍和结构说明:1.1程式基本指令介绍本公司使用C NC成型机常用指令如下:M48 -------- 程式头的开始% ――程式头的结束(即程序的开始)G 00 ——机器移至某点(下刀位置)G O 1 ——直线锣至某点(两点距离)G O 2 ——顺时针锣圆弧(逆时针用G03 举例:GO 2/G O 3X..Y. . A..(半径用A表示G32―― 顺时针锣圆孔(逆时针用G3 3)举例:G 32/ G33X..Y..A..(半径用A 表示)M15 ―― 下刀指令M17 ―― 直接提刀指令(间接用M16)G40 ――中间补偿(不作补偿)G4 1——前进方向左补偿G42 前进方向右补偿M25 ―― 重复起点M0 1 ——重复图形开始MO 2X# Y# ――重复图形偏移R#M02X#Y#——重复块M08——重复结束M30——程序结束M8 0M90 ——图形旋转1 80度M70M 90——图形旋转90度M97/M9 8 ——钻字麦(M97横向/M98竖向)G85 ——钻si o t G84 ——钻扩孔1. 2成型程式结构说明:M4 8 HEADE开头T01C1. 400 T02C1. 60 2C P ,1,1.360 CP,2,1 .562 % H EA D ERT0 1M2 5第1支锣刀直径1 .4mm第2支锣刀直径1.60 2 mm尾数2表示最后一把刀第1支锣刀补偿为1.3 6 0mm第2支锣刀补偿为1. 5 6 2mm结束,程式开始选择刀具重复起点G00X192.2873Y34.446 8 机台移至X 192 .287 3 Y 34.4 46 8G4 0M15F16. 0G01Y186 .4455 M17M01刀具不做补偿卜刀进刀速直线铣切提刀重复图形开始R5M02X36. 002依X每相隔36 . 0 0 2距离排版5次M0 1重复图形开始R 2 M02X191 .0359依X 每相隔1 9 1.03 5 9距离排版2次M08重复结束 T02 选择刀具M2 5 重复起点3G 0 0 X12.2 877Y 2 0. 4 489 机台移至 X 1 2. 2 8 7 7Y 20.4 4 8 9G42 刀具做右补偿Ml 5 下刀F18. 0 进刀速G01 X 2 01.2883 Y 200. 4 485 直线铣切 X 1 3.2877 Y20.4489M17提刀 M01重复图形开始 R2M02X 91.03 5 9 依X 每相隔1 91. 03 5 9距离排版2次M08重复结束 M30 程序结束 1.3 钻孔程式结构说明:M 48 HEA D E R 开头T O 1C3.1 7 5T 02C0.4 0 0 T 14C0 .4 0 0 % HE ADER T 01 X - 2 24. 5 89Y28 9.078 钻孔坐标X -25 0.310 Y 2 6 6 .532X-249.73 6 Y-15 9 .3 7 6T 0 2 选择第2把刀X -224.5 89Y289. 078 钻孔坐标X-250.3 1 0Y 26 6 .532X -24 9 .736 Y -159. 3 76T1 4 选择第14把刀M97,4 80323 0 2 6B0 X+1Y + 2 * &S 钻字麦(附带系数和活动机台代码) X-213. 667Y 2 88.8 24 字麦坐标M30 程序结束2、锣板程式处理规范对PC5外卜形进行整理,去除外形中的 叠线、叠点、断线刀具序号 刀具序号刀具序号结束,程式开始钻孔开始(选择第1把刀)常用铣刀规格:为0.8MM ;为1.0MM ;为1.2MM ;为1.5 MM;为1.8MM;为2.0MM;为 2.4M M。
锣带制作标准[详]
![锣带制作标准[详]](https://img.taocdn.com/s3/m/c837508550e2524de5187e8c.png)
铣带制作标准1.程式指令介绍和结构说明:1.1程式基本指令介绍本公司使用CNC成型机常用指令如下:M48 ——程式头的开始% ——程式头的结束(即程序的开始)G00 ——机器移至某点(下刀位置)G01 ——直线锣至某点(两点距离)G02 ——顺时针锣圆弧(逆时针用G03)举例:G02/G03X..Y..A..(半径用A 表示)G32 ——顺时针锣圆孔(逆时针用G33)举例:G32/G33X..Y..A..(半径用A 表示)M15 ——下刀指令M17 ——直接提刀指令(间接用M16)G40 ——中间补偿(不作补偿)G41 ——前进方向左补偿G42 ——前进方向右补偿M25 ——重复起点M01 ——重复图形开始M02X#Y# ——重复图形偏移R#M02X#Y# ——重复块M08 ——重复结束M30 ——程序结束M80M90 ——图形旋转180度M70M90 ——图形旋转90度M97/M98 ——钻字麦(M97横向/M98竖向)G85 ——钻slot G84 ——钻扩孔1.2 成型程式结构说明: M48 HEADER开头T01C1.400 第1支锣刀直径1.4mmT02C1.602 第2支锣刀直径1.602mm,尾数2表示最后一把刀CP,1,1.360 第1支锣刀补偿为1.360mmCP,2,1.562 第2支锣刀补偿为1.562mm% HEADER 结束,程式开始T01 选择刀具M25 重复起点G00X192.2873Y34.4468 机台移至X192.2873Y34.4468G40 刀具不做补偿M15 下刀F16.0 进刀速G01Y186.4455 直线铣切M17 提刀M01 重复图形开始R5M02X36.002 依X每相隔36.002距离排版5次M01 重复图形开始R2M02X191.0359 依X每相隔191.0359距离排版2次M08 重复结束T02 选择刀具M25 重复起点3G00X12.2877Y20.4489 机台移至X12.2877Y20.4489G42 刀具做右补偿M15 下刀F18.0 进刀速G01X201.2883 Y200.4485 直线铣切 X13.2877 Y20.4489M17 提刀M01 重复图形开始R2M02X191.0359 依X每相隔191.0359距离排版2次M08 重复结束M30 程序结束1.3 钻孔程式结构说明:M48 HEADER开头T01C3.175 刀具序号T02C0.400 刀具序号T14C0.400 刀具序号% HEADER 结束,程式开始T01 钻孔开始(选择第1把刀)X-224.589Y289.078 钻孔坐标X-250.310Y266.532X-249.736Y-159.376T02 选择第2把刀X-224.589Y289.078 钻孔坐标X-250.310Y266.532X-249.736Y-159.376T14 选择第14把刀M97,480323026B0 X+1Y+2 *&S 钻字麦(附带系数和活动机台代码)X-213.667Y288.824 字麦坐标M30 程序结束2、锣板程式处理规对PCS外形进行整理,去除外形中的叠线、叠点、断线常用铣刀规格:∮0.8MM;∮1.0MM;∮1.2MM;∮1.5MM;∮1.8MM;∮2.0MM;∮2.4MM。
CAM350锣带锣带文档教程

6.添加定位孔,进入钻孔层复制方向孔及一个SET的管位孔到锣带层。
7.添加铣路径.在锣带层以外形图,钻孔层为影响层,点击菜单增加铣路径,先添加铣废料,以Z字形或全部铣掉的方式铣好废料,铣废料不得超过外形中心线,铣废料为大刀不补偿模式,小于10MM大于50MM废料可不用画铣废料,大于50MM废料在记事本粗捞内槽刀具后添加M47暂停指令,拿出即可,设置粗捞进刀方向和精锣相反,按粗捞顺时针方向,精锣逆时针方向,添加铣路径,添加铣路径时大圆或长弧分几个连接点画出,异形槽拐角处,角度不够的地方,用不连接的方式画出,粗捞排尘用路径偏移命令偏移至离外形线中心0.1或0.2处,闭合路径粗捞可和精锣用相同的刀径,单槽必须小精锣0.1或0.2,精锣成型除单槽不补偿模式外,都用右补偿模式.用以上方法画好一个SET的锣带
程式锣带文本档,如有不懂处请与店家掌柜联系。如有不好处请指出后续修改。谢谢
汝易知技术
3.改单位,公制,1/100.进入350.点击NC编辑器,用菜单测量命令测量外形图尺寸是否和MI相符,确定无误后,查看内槽,SET,间距。
4.建立钻锣一体刀具表,第一把刀方向孔第二把,定位孔,方便生产操作,第三把刀,铣废料,一般用最大刀,第四把,内槽粗捞排尘刀,第五把,内槽精锣成型刀,第六把,外形粗捞排尘刀,第七把,外形精锣成型刀。注:单槽粗捞刀具比精锣刀具小0.1或0.2 ,闭合槽刀具可以一样,粗捞都为不补偿,锣至离外形线中心0.1或0.2,精锣锣至成型线中心。刀具建立好,点OK。
8.铣路径排序,点击菜单铣路径排序,点击OK,命令自动排好序。
9.导出锣带,点击菜单导出锣带,设置导出路径,命好锣带名,更改至公制33后导零,绝对坐标,应用狂点几下,OK.
(新)锣带资料作业规程

1.0目的
作出正确的锣带资料,以满足本公司的生产需求。
2.0适用范围
适用于本公司的锣带制作。
3.0定义(略)
4.0职责
光绘部锣带作业员负责作业,由检查TEMP人员提供正确的分孔菲林及MI机械图,指出相关信息。
5.0作业程序
5.1在PARCAM中输出分孔(包括客户的设计图文件)及钻带资料。见《PARCAM》作业指导书。
Mill Data Enport选择锣带输出到的文件夹在锣带层输入锣带型号
Enpdly中画勾通选择输出的单位,一般为Metric点击Apdly OK.
7、输出锣带的文件夹中找到锣带文件,并以记事本的形式打工,加入定位孔坐标及排队版数据,后存盘就OK。
为了更准确的制作锣带,可将此资料再次输入到之中检查一次。(File lnport
Mill DATA找出锣带所在文件夹OpenOK Yes打开分孔层检查资料是否正确。
自检合格后,把锣带文件通过网络传送到锣板房推选首件,经QA审核确认是否合格。
不合格锣带,重返作业员检查重做。
注意:锣带文本格式为Excellon格式如下:
%T0Βιβλιοθήκη CM25X……Y……钻定位孔
………
………
………
M01
R‥M02X
5.5锣带制作:
1、先添加一个新层(Edit Layers addlayers)点击OK。
2、显示新层:用光标点击新层的名称,不用关闭分孔层。
3、在新建立的一层中,将分孔资料的外形重新描绘一次,线的操作来Add Line,圆弧为Add Arc 3-Porints(一般选择三点画孤)。
特别注意:一定要将线与线,线与弧连接起来,不能有错及断开的现象。
5.2读入CAM350:
CAM锣带设计及优化
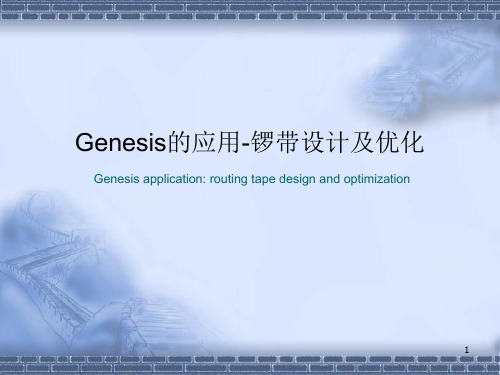
定义层别属性
必须于Matrix 中 將该层特性改为 Rout
25
Genesis的应用-锣带设计及优化
Genesis application: routing tape design and optimization
三、rout的制作
确认尺寸 量测是否rout中尺寸与图纸中标注是否一致,不一致按客户要求修改。 注:图纸中标注的尺寸必须全部量测。
选择顺序
选择起始set
一般选择此 顺序
点此 生成 程序
36
Genesis的应用-锣带设计及优化
Genesis application: routing tape design and optimization
三、rout的制作
生成程序
点右键,出现两个按 钮,open file(打开 检查程序)和export file(输出程序)
Genesis application: routing tape design and optimization
三、rout的制作
Rout 顺序 残条-内槽-外围
备注:如有修铜皮或修内角,则放在内槽前。
34
Genesis的应用-锣带设计及优化
Genesis application: routing tape design and optimization
四、锣带的优化
残条的优化 方法一
39
Genesis的应用-锣带设计及优化
Genesis application: routing tape design and optimization
四、锣带的优化
残条的优化 方法二
40
Genesis的应用-锣带设计及优化
- 1、下载文档前请自行甄别文档内容的完整性,平台不提供额外的编辑、内容补充、找答案等附加服务。
- 2、"仅部分预览"的文档,不可在线预览部分如存在完整性等问题,可反馈申请退款(可完整预览的文档不适用该条件!)。
- 3、如文档侵犯您的权益,请联系客服反馈,我们会尽快为您处理(人工客服工作时间:9:00-18:30)。
铣带制作标准
1.程式指令介绍和结构说明:
1.1程式基本指令介绍本公司使用CNC成型机常用指令如下:
M48 ——程式头的开始
% ——程式头的结束(即程序的开始)
G00 ——机器移至某点(下刀位置)
G01 ——直线锣至某点(两点距离)
G02 ——顺时针锣圆弧(逆时针用G03)举例:G02/G03X..Y..A..(半径用A 表示)
G32 ——顺时针锣圆孔(逆时针用G33)举例:G32/G33X..Y..A..(半径用A 表示)
M15 ——下刀指令
M17 ——直接提刀指令(间接用M16)
G40 ——中间补偿(不作补偿)
G41 ——前进方向左补偿
G42 ——前进方向右补偿
M25 ——重复起点
M01 ——重复图形开始
M02X#Y# ——重复图形偏移
R#M02X#Y# ——重复块
M08 ——重复结束
M30 ——程序结束
M80M90 ——图形旋转180度
M70M90 ——图形旋转90度
M97/M98 ——钻字麦(M97横向/M98竖向)
G85 ——钻slot G84 ——钻扩孔
1.2 成型程式结构说明: M48 HEADER开头
T01C1.400 第1支锣刀直径1.4mm
T02C1.602 第2支锣刀直径1.602mm,尾数2表示最后一把刀
CP,1,1.360 第1支锣刀补偿为1.360mm
CP,2,1.562 第2支锣刀补偿为1.562mm
% HEADER 结束,程式开始
T01 选择刀具
M25 重复起点
G00X192.2873Y34.4468 机台移至X192.2873Y34.4468
G40 刀具不做补偿
M15 下刀
F16.0 进刀速
G01Y186.4455 直线铣切
M17 提刀
M01 重复图形开始
R5M02X36.002 依X每相隔36.002距离排版5次
M01 重复图形开始
R2M02X191.0359 依X每相隔191.0359距离排版2次
M08 重复结束
T02 选择刀具
M25 重复起点
3G00X12.2877Y20.4489 机台移至X12.2877Y20.4489
G42 刀具做右补偿
M15 下刀
F18.0 进刀速
G01X201.2883 Y200.4485 直线铣切 X13.2877 Y20.4489
M17 提刀
M01 重复图形开始
R2M02X191.0359 依X每相隔191.0359距离排版2次
M08 重复结束
M30 程序结束
1.3 钻孔程式结构说明:
M48 HEADER开头
T01C3.175 刀具序号
T02C0.400 刀具序号
T14C0.400 刀具序号
% HEADER 结束,程式开始
T01 钻孔开始(选择第1把刀)
X-224.589Y289.078 钻孔坐标
X-250.310Y266.532
X-249.736Y-159.376
T02 选择第2把刀
X-224.589Y289.078 钻孔坐标
X-250.310Y266.532
X-249.736Y-159.376
T14 选择第14把刀
M97,480323026B0 X+1Y+2 *&S 钻字麦(附带系数和活动机台代码)X-213.667Y288.824 字麦坐标
M30 程序结束
2、锣板程式处理规范
对PCS外形进行整理,去除外形中的叠线、叠点、断线
常用铣刀规格:∮0.8MM;∮1.0MM;∮1.2MM;∮1.5MM;∮1.8MM;∮2.0MM;∮2.4MM。
管位钉最小为1.95mm,最大为5.0mm。
2.1管位孔选择原则:管位孔尽量选择非金属化、内管位、需要满足对角分部的
基本原则,管位孔不能为小于2.05的孔。
2.2板件单元尺寸≥300mm时,需要至少3个管位钉。
2.3一个锣带里,一般情况下只允许出现一把刀。
2.4在选择锣刀时,尽量用大刀;在无法使用大刀的情况下,可以使用两把刀。
锣刀选得越大,锣板效率越高,尽量考虑用1.50MM或以上的锣刀来锣板。
2.5外形锣机的走刀方向按逆时针,向右补偿制作,但下刀点须在板外下刀,板
四角倒按0.8mm的圆角,防止板件擦花,如下图,特殊客户要求除外。
2.5.1外形锣机内槽的走刀方向按顺时针,如下图:
2.6需要在长槽的下刀点及收刀点加与锣刀直径相同的引导孔,防止板面板粉残
留。
2.7在锣带走刀时,尽量减少抬刀次数。
2.8 在走刀时,要按先内锣在外锣的顺序;一个一个单元的锣。
2.9 当槽孔位于V -CUT 线相切时,须向V -CUT 线内多铣0.2mm ,以避免V -CUT
偏时产生毛刺。
在把下刀点定在开V 槽的方向。
3.0最小工作槽宽大于或等于0.8mm ,槽宽<0.8mm 以钻孔方式制作。
3.1当槽孔有圆角且圆角ø≥铣刀ø时,从圆弧处下刀,如下图
3.2当槽孔无圆角或有圆角且圆角ø≤铣刀ø时则在直角处下刀,下刀点为直角处铣刀则设计为不封闭的,连续性的回形锣带形式;下刀点和收刀点不连接,需断开。
如下图
3.3在锣圆时,下到点可为多处,不可只为一处下刀点,防止飞刀。
如下图
3.4如下图同心圆铣法:内圆是顺时针走刀①,外圆逆时针走刀②,此两个方向不能为同一位置下刀点;注意在下刀位加下刀孔
①
下刀孔
外形边
3.5内锣边料打碎,防止擦花板件
3.5.1采用一次性锣,不抬刀的原则制作;从中间开始走,进行螺旋形走刀,中间不要留有节点。
如下图
3.5.2在不规则的图形下,我们用连线的方式,不补偿走刀,锣内锣;最后在正常走刀,锣内锣外形。
如下图
3.5.3 在锣带是有内外锣时,刀径相同时需做一个锣带分成两把刀来做,刀径不相同时需分成两个锣带来制作。
3.5.4在需打碎或多锣一次时,在内外锣时需要不同补偿值,需设内锣为两把刀(依次类推) 如下图
3.6当程式中出现细长条时,须特别注意其受力影响,一般情况下只铣一趟,与外形连接时须先铣外形后铣出细长条。
如下图
3.7当槽孔距其他槽可成型线较近时,须先铣出受力影响较大的方槽,后铣受力
影响较小的长槽。
如下图
3.8大足锣机进给速度太快,无法手动调节,需删除进给速度。
方槽距长槽较近, 须铣方槽后铣长槽。
(F100为锣机进给速度)
3.9在倒角孔与锣带交界处,倒角处以打断的方式走刀,使锣刀尽量进孔内,不会产生凸台。
4.0 和锣带相同大小的长槽孔,不允许走一刀过做法,还是要走循环锣,防止槽内有板粉。
4.1槽宽小于等于2.4mm长槽,把下刀点定为圆弧的中点处,防止有凸台产生。
4.2在整排方形槽的情况下,槽宽小于2.0mm刀径2倍时,使用小刀进行铣锣。
4.3在做锣带时,必须把多把刀合成一把刀。
修改后:
4.4。