压力钢管的防腐技术
压力钢管防腐施工方案

压力钢管防腐施工方案
1. 引言
压力钢管是在工业领域中广泛使用的一种管道材料,它承受着高压力和高温的工作环境。然而,由于其长期暴露在恶劣的外部环境中,容易受到腐蚀和损坏。为了延长钢管的使用寿命并确保安全运行,对压力钢管进行防腐处理就变得尤为重要。
本文档将介绍一种常用的压力钢管防腐施工方案,包括准备工作、防腐涂料选择、施工技术等内容,帮助施工人员更好地进行防腐工作。
2. 准备工作
在进行压力钢管防腐施工之前,需要进行一些准备工作,以确保施工顺利进行。以下是准备工作的主要内容:
2.1 清洁表面
在施工之前,必须确保钢管表面干净,无油污、锈蚀等物质。可以使用钢丝刷、喷砂机等工具对表面进行清洁处理,将附着物彻底清除。
2.2 检查钢管
在施工之前,需要对钢管进行全面的检查,确保没有任何裂纹、破损或其他缺陷。如有必要,可以进行修复或更换。
2.3 建立安全措施
在进行防腐施工时,必须建立相应的安全措施。施工现场应设立警示标志,施工人员必须佩戴个人防护装备,如手套、面具等,以防止对健康产生不良影响。
3. 防腐涂料选择
对于压力钢管的防腐施工,正确选择合适的防腐涂料非常重要。以下是一些常用的防腐涂料类型:
3.1 热镀锌涂层
热镀锌涂层是一种常用的防腐涂层,在高温下将锌与钢管表面进行反应,形成一层坚硬的保护层。它具有良好的耐腐蚀性能,适用于一般工业环境。
3.2 煤焦沥青涂层
煤焦沥青涂层是一种能够有效抵抗大气腐蚀的防腐涂层。它具有优异的耐热性和耐化学品腐蚀性能,适用于高温和腐蚀性较强的工业环境。
3.3 环氧涂层
环氧涂层是一种常用且性能优良的防腐涂层。它具有良好的耐腐蚀性、耐磨损性和耐高温性能,适用于多种工业环境,尤其是化工领域。
压力钢管安装后整体防腐施工工法(2)
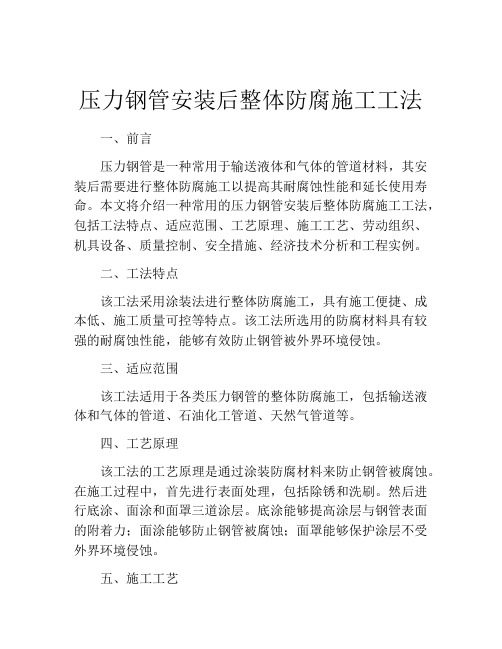
压力钢管安装后整体防腐施工工法
一、前言
压力钢管是一种常用于输送液体和气体的管道材料,其安装后需要进行整体防腐施工以提高其耐腐蚀性能和延长使用寿命。本文将介绍一种常用的压力钢管安装后整体防腐施工工法,包括工法特点、适应范围、工艺原理、施工工艺、劳动组织、机具设备、质量控制、安全措施、经济技术分析和工程实例。
二、工法特点
该工法采用涂装法进行整体防腐施工,具有施工便捷、成本低、施工质量可控等特点。该工法所选用的防腐材料具有较强的耐腐蚀性能,能够有效防止钢管被外界环境侵蚀。
三、适应范围
该工法适用于各类压力钢管的整体防腐施工,包括输送液体和气体的管道、石油化工管道、天然气管道等。
四、工艺原理
该工法的工艺原理是通过涂装防腐材料来防止钢管被腐蚀。在施工过程中,首先进行表面处理,包括除锈和洗刷。然后进行底涂、面涂和面罩三道涂层。底涂能够提高涂层与钢管表面的附着力;面涂能够防止钢管被腐蚀;面罩能够保护涂层不受外界环境侵蚀。
五、施工工艺
施工工艺包括表面处理、底涂施工、面涂施工和面罩施工四个阶段。表面处理阶段主要完成钢管的除锈和洗刷工作。底涂施工阶段先进行底涂涂布,然后进行固化处理。面涂施工阶段进行面涂涂布,然后进行固化处理。面罩施工阶段将面罩固定在钢管外壁。
六、劳动组织
在施工过程中,需要组织专业施工人员进行作业,包括表面处理人员、涂装人员、面罩安装人员等。
七、机具设备
该工法所需的机具设备包括除锈机、洗刷机、喷涂机、固化设备等,这些机具设备能够提高施工效率和精度。
八、质量控制
为确保施工质量达到设计要求,需要进行严格的质量控制。包括对涂层厚度、涂布质量和固化效果的检测和控制,以及施工过程中的质量记录和追踪等。
管道防腐的处理方法
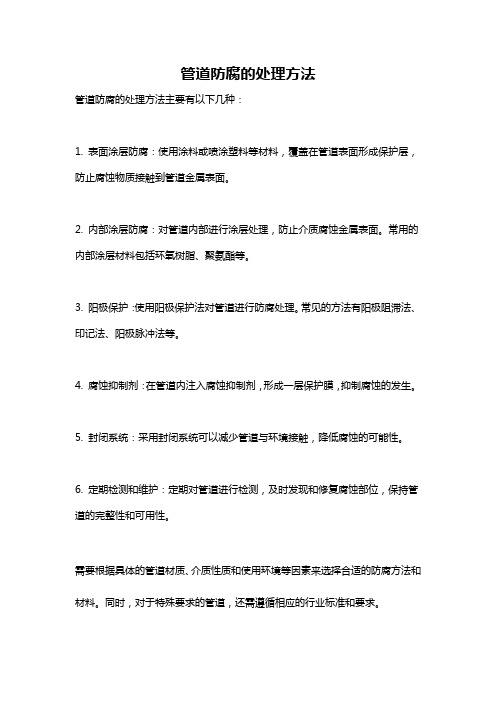
管道防腐的处理方法
管道防腐的处理方法主要有以下几种:
1. 表面涂层防腐:使用涂料或喷涂塑料等材料,覆盖在管道表面形成保护层,防止腐蚀物质接触到管道金属表面。
2. 内部涂层防腐:对管道内部进行涂层处理,防止介质腐蚀金属表面。常用的内部涂层材料包括环氧树脂、聚氨酯等。
3. 阳极保护:使用阳极保护法对管道进行防腐处理。常见的方法有阳极阻滞法、印记法、阳极脉冲法等。
4. 腐蚀抑制剂:在管道内注入腐蚀抑制剂,形成一层保护膜,抑制腐蚀的发生。
5. 封闭系统:采用封闭系统可以减少管道与环境接触,降低腐蚀的可能性。
6. 定期检测和维护:定期对管道进行检测,及时发现和修复腐蚀部位,保持管道的完整性和可用性。
需要根据具体的管道材质、介质性质和使用环境等因素来选择合适的防腐方法和材料。同时,对于特殊要求的管道,还需遵循相应的行业标准和要求。
压力钢管防腐施工方案
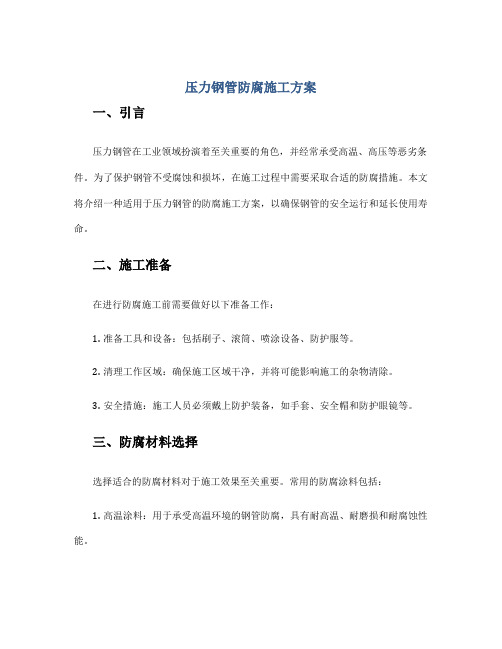
压力钢管防腐施工方案
一、引言
压力钢管在工业领域扮演着至关重要的角色,并经常承受高温、高压等恶劣条件。为了保护钢管不受腐蚀和损坏,在施工过程中需要采取合适的防腐措施。本文将介绍一种适用于压力钢管的防腐施工方案,以确保钢管的安全运行和延长使用寿命。
二、施工准备
在进行防腐施工前需要做好以下准备工作:
1.准备工具和设备:包括刷子、滚筒、喷涂设备、防护服等。
2.清理工作区域:确保施工区域干净,并将可能影响施工的杂物清除。
3.安全措施:施工人员必须戴上防护装备,如手套、安全帽和防护眼镜等。
三、防腐材料选择
选择适合的防腐材料对于施工效果至关重要。常用的防腐涂料包括:
1.高温涂料:用于承受高温环境的钢管防腐,具有耐高温、耐磨损和耐腐蚀性能。
2.酚醛涂料:适用于高酸、高碱环境下的防腐,具有耐久性强和较高的耐腐蚀性能。
3.环氧涂料:常用于海洋或潮湿环境下的防腐,具有优异的耐腐蚀性和附着力。
根据钢管的使用环境和要求,选择合适的防腐涂料进行施工。
四、施工步骤
以下是压力钢管防腐施工的基本步骤:
1.钢管表面处理:使用砂轮机或喷砂机对钢管进行打磨,去除锈蚀和污垢以保证涂料的附着力。
2.底漆涂覆:选择适合的底漆涂料,刷涂或喷涂在钢管表面,形成一层保护层,并增强涂层的附着力。
3.中间涂覆:根据需要,涂刷一到两层中间涂料,以增加涂层的厚度和保护性能。
4.上光涂覆:使用光滑涂料进行最后一层涂覆,以提供最佳的防腐保护和外观。
5.干燥和硬化:根据涂料的要求,使涂层完全干燥和硬化,通常需要等待数小时或数天。
6.检查和维护:在施工完成后,对涂层进行检查,确保涂层质量,并及时维护和修复。
钢管防腐工艺流程
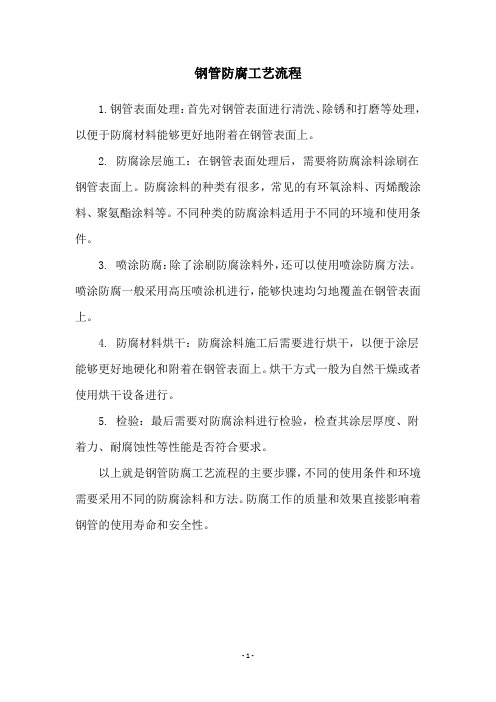
钢管防腐工艺流程
1.钢管表面处理:首先对钢管表面进行清洗、除锈和打磨等处理,以便于防腐材料能够更好地附着在钢管表面上。
2. 防腐涂层施工:在钢管表面处理后,需要将防腐涂料涂刷在钢管表面上。防腐涂料的种类有很多,常见的有环氧涂料、丙烯酸涂料、聚氨酯涂料等。不同种类的防腐涂料适用于不同的环境和使用条件。
3. 喷涂防腐:除了涂刷防腐涂料外,还可以使用喷涂防腐方法。喷涂防腐一般采用高压喷涂机进行,能够快速均匀地覆盖在钢管表面上。
4. 防腐材料烘干:防腐涂料施工后需要进行烘干,以便于涂层能够更好地硬化和附着在钢管表面上。烘干方式一般为自然干燥或者使用烘干设备进行。
5. 检验:最后需要对防腐涂料进行检验,检查其涂层厚度、附着力、耐腐蚀性等性能是否符合要求。
以上就是钢管防腐工艺流程的主要步骤,不同的使用条件和环境需要采用不同的防腐涂料和方法。防腐工作的质量和效果直接影响着钢管的使用寿命和安全性。
- 1 -
水电站压力钢管防腐施工方案
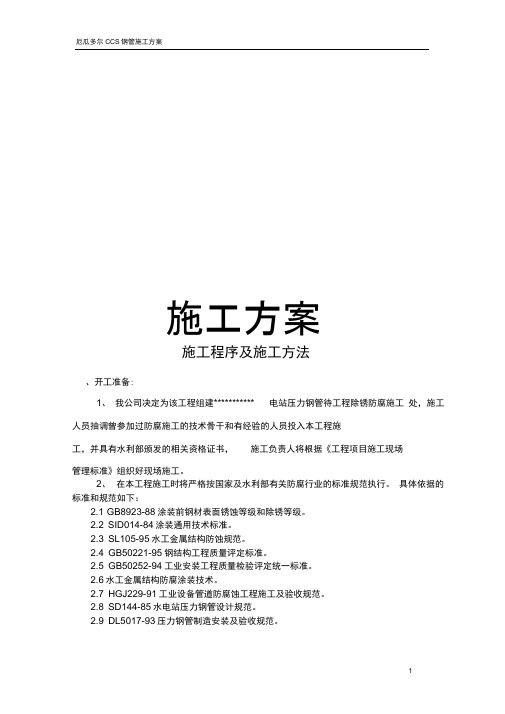
施工方案
施工程序及施工方法
、开工准备:
1、我公司决定为该工程组建*********** 电站压力钢管待工程除锈防腐施工处,施工人员抽调曾参加过防腐施工的技术骨干和有经验的人员投入本工程施
工,并具有水利部颁发的相关资格证书,施工负责人将根据《工程项目施工现场
管理标准》组织好现场施工。
2、在本工程施工时将严格按国家及水利部有关防腐行业的标准规范执行。具体依据的标准和规范如下:
2.1 GB8923-88涂装前钢材表面锈蚀等级和除锈等级。
2.2 SID014-84涂装通用技术标准。
2.3 SL105-95水工金属结构防蚀规范。
2.4 GB50221-95钢结构工程质量评定标准。
2.5 GB50252-94工业安装工程质量检验评定统一标准。
2.6水工金属结构防腐涂装技术。
2.7 HGJ229-91工业设备管道防腐蚀工程施工及验收规范。
2.8 SD144-85水电站压力钢管设计规范。
2.9 DL5017-93压力钢管制造安装及验收规范。
、材料准备
主要材料表
注:、各种主要材料、辅助材料、消耗材料的储备量,应满足施工进度的要求,
材料应有防潮和防雨水浇淋措施。
2、氯化橡胶面漆具有很好的耐候性、耐水性能,长期暴晒漆膜稳定,水工建筑物的防
腐,常采用此类材料。
1、材料的检验控制
材料使用前,应会同质检人员,对材料按下列要求核对验收,合格签字后,方可使用,严禁使用伪劣、过期、不合格产品。
1.1材料出厂合作证或产品质量证书的各项技术指标,应符合设计文件或其
它质量指标的规定。
1.2根据订货合同核对品种、型号、规格、数量及有效使用期等。
钢管防腐工艺流程

钢管防腐工艺流程
《钢管防腐工艺流程》
钢管在使用过程中容易受到腐蚀的侵害,为了延长其使用寿命,常常需要进行防腐处理。下面是钢管防腐工艺的流程:
1. 表面清洁:首先需要对钢管进行表面清洁,去除表面的油污、锈蚀和其他杂质。通常采用喷砂、喷丸或者清洗等方法来清洁表面,确保表面干净光滑。
2. 预处理:在表面清洁完成后,需要进行预处理以提高钢管表面的附着力和防腐效果。这一步通常包括化学处理、磷化处理等,以形成均匀致密的表面。
3. 底漆涂装:在预处理完成后,需要涂刷底漆来加强防腐效果。底漆的选择应根据钢管所处的环境条件和使用要求来确定,以确保底漆与钢管的兼容性和耐腐蚀性。
4. 中间涂层:在底漆涂装完成后,通常需要进行中间涂层的处理以增加防腐效果。中间涂层的选择应根据具体需要来确定,可以是聚合物涂层、环氧涂层等。
5. 面漆涂装:最后一步是进行面漆涂装,以增加防腐效果和美观度。面漆的选择要考虑到抗腐蚀性能和颜色要求,确保其与底漆和中间涂层的兼容性。
通过以上流程的处理,钢管就能得到有效的防腐保护,延长其
使用寿命,确保安全可靠地运行。钢管防腐工艺的流程是一个系统的过程,需要严格按照要求进行操作,以确保防腐效果和使用寿命的达到预期的效果。
压力钢管的防腐技术
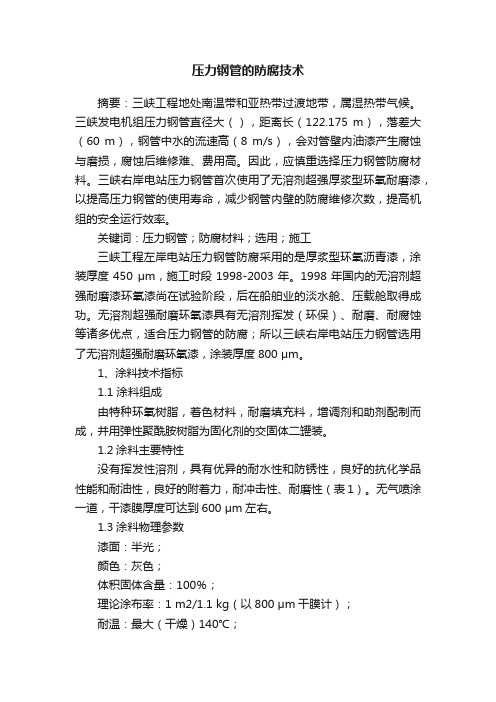
压力钢管的防腐技术
摘要:三峡工程地处南温带和亚热带过渡地带,属湿热带气候。三峡发电机组压力钢管直径大(),距离长(122.175 m),落差大(60 m),钢管中水的流速高(8 m/s),会对管壁内油漆产生腐蚀与磨损,腐蚀后维修难、费用高。因此,应慎重选择压力钢管防腐材料。三峡右岸电站压力钢管首次使用了无溶剂超强厚浆型环氧耐磨漆,以提高压力钢管的使用寿命,减少钢管内壁的防腐维修次数,提高机组的安全运行效率。
关键词:压力钢管;防腐材料;选用;施工
三峡工程左岸电站压力钢管防腐采用的是厚浆型环氧沥青漆,涂装厚度450 μm,施工时段1998-2003年。1998年国内的无溶剂超强耐磨漆环氧漆尚在试验阶段,后在船舶业的淡水舱、压载舱取得成功。无溶剂超强耐磨环氧漆具有无溶剂挥发(环保)、耐磨、耐腐蚀等诸多优点,适合压力钢管的防腐;所以三峡右岸电站压力钢管选用了无溶剂超强耐磨环氧漆,涂装厚度800 μm。
1、涂料技术指标
1.1 涂料组成
由特种环氧树脂,着色材料,耐磨填充料,增调剂和助剂配制而成,并用弹性聚酰胺树脂为固化剂的交固体二罐装。
1.2涂料主要特性
没有挥发性溶剂,具有优异的耐水性和防锈性,良好的抗化学品性能和耐油性,良好的附着力,耐冲击性、耐磨性(表1)。无气喷涂一道,干漆膜厚度可达到600 μm左右。
1.3涂料物理参数
漆面:半光;
颜色:灰色;
体积固体含量:100%;
理论涂布率:1 m2/1.1 kg(以800 μm干膜计);
耐温:最大(干燥)140℃;
闪点:>100℃;
比重:1.3 kg/L;
钢质管道内外防腐技术要求
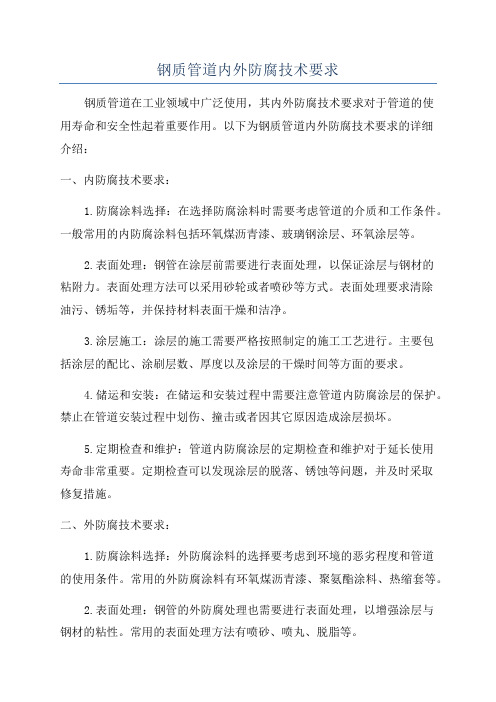
钢质管道内外防腐技术要求
钢质管道在工业领域中广泛使用,其内外防腐技术要求对于管道的使
用寿命和安全性起着重要作用。以下为钢质管道内外防腐技术要求的详细
介绍:
一、内防腐技术要求:
1.防腐涂料选择:在选择防腐涂料时需要考虑管道的介质和工作条件。一般常用的内防腐涂料包括环氧煤沥青漆、玻璃钢涂层、环氧涂层等。
2.表面处理:钢管在涂层前需要进行表面处理,以保证涂层与钢材的
粘附力。表面处理方法可以采用砂轮或者喷砂等方式。表面处理要求清除
油污、锈垢等,并保持材料表面干燥和洁净。
3.涂层施工:涂层的施工需要严格按照制定的施工工艺进行。主要包
括涂层的配比、涂刷层数、厚度以及涂层的干燥时间等方面的要求。
4.储运和安装:在储运和安装过程中需要注意管道内防腐涂层的保护。禁止在管道安装过程中划伤、撞击或者因其它原因造成涂层损坏。
5.定期检查和维护:管道内防腐涂层的定期检查和维护对于延长使用
寿命非常重要。定期检查可以发现涂层的脱落、锈蚀等问题,并及时采取
修复措施。
二、外防腐技术要求:
1.防腐涂料选择:外防腐涂料的选择要考虑到环境的恶劣程度和管道
的使用条件。常用的外防腐涂料有环氧煤沥青漆、聚氨酯涂料、热缩套等。
2.表面处理:钢管的外防腐处理也需要进行表面处理,以增强涂层与
钢材的粘性。常用的表面处理方法有喷砂、喷丸、脱脂等。
3.涂层施工:涂层施工时需要遵循规定的工艺流程,涂刷面积、厚度和干燥时间等都需要符合要求。如采用热喷涂工艺,需要注意控制喷涂温度和喷涂速度。
4.储运和安装:在储运和安装过程中,需要保护好外防腐涂层以防止损坏。可以采用塑料薄膜或者其他保护措施来保障涂层的完整性。
钢管防腐施工方法
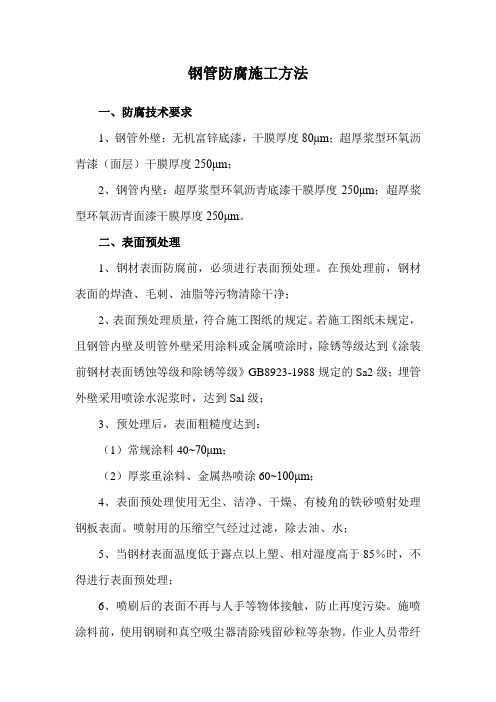
钢管防腐施工方法
一、防腐技术要求
1、钢管外壁:无机富锌底漆,干膜厚度80μm;超厚浆型环氧沥青漆(面层)干膜厚度250μm;
2、钢管内壁:超厚浆型环氧沥青底漆干膜厚度250μm;超厚浆型环氧沥青面漆干膜厚度250μm。
二、表面预处理
1、钢材表面防腐前,必须进行表面预处理。在预处理前,钢材表面的焊渣、毛刺、油脂等污物清除干净;
2、表面预处理质量,符合施工图纸的规定。若施工图纸未规定,且钢管内壁及明管外壁采用涂料或金属喷涂时,除锈等级达到《涂装前钢材表面锈蚀等级和除锈等级》GB8923-1988规定的Sa2级;埋管外壁采用喷涂水泥浆时,达到Sal级;
3、预处理后,表面粗糙度达到:
(1)常规涂料40~70μm;
(2)厚浆重涂料、金属热喷涂60~100μm;
4、表面预处理使用无尘、洁净、干燥、有棱角的铁砂喷射处理钢板表面。喷射用的压缩空气经过过滤,除去油、水;
5、当钢材表面温度低于露点以上塑、相对湿度高于85%时,不得进行表面预处理;
6、喷刷后的表面不再与人手等物体接触,防止再度污染。施喷涂料前,使用钢刷和真空吸尘器清除残留砂粒等杂物。作业人员带纤
维手套。若不慎用手触及己清理好的表面,立即用溶剂清洗钢管表面。
三、防腐施工方法
1、一般要求
(1)施涂前,根据施工图纸要求和涂料生产厂的规定进行工艺试验。试验过程中有涂料生产制造厂的人员负责指导。试验成果提交监理人;
(2)组焊后的管节、岔管及附件(除安装焊缝外),在车间内完成防腐;现场安装焊缝及表面防腐损坏部位在现场进行防腐;
(3)清理后的钢材表面在潮湿气候条件下,涂料在4h内防腐完成,金属喷涂在2h内完成;在晴天和正常大气条件下,涂料防腐时间最长不超过12h,金属喷涂时间不超过8h;
压力管道的管道防腐技术及其要求

压力管道的管道防腐技术及其要求压力管道是从事石化、化工、能源等行业生产的关键设备,管
道防腐技术在其中起着至关重要的作用。本篇文章就围绕着压力
管道的管道防腐技术及其要求展开。
一、压力管道的基本概念
压力管道是一种用于输送流体介质的管道,一般工作压力大于
或等于0.1 MPa的管道均属于压力管道。压力管道多用于石化、
化工、冶金、电力等行业,由于输送的介质特性、操作条件及环
境等因素的影响,使得管道材料会发生各种腐蚀、磨损、老化等
现象,严重影响其使用寿命和安全性能。其中,管道腐蚀是威胁
管道生命安全的一个主要问题。
二、压力管道的管道防腐技术
1. 内壁涂层防腐技术
内壁涂层防腐技术是将一定性能的涂料涂在管道内壁,与管道
材料形成一层整体的防腐层。内壁涂层防腐技术不仅可以抵御腐蚀,同时还可以起到防止热能、电能、化学能等在管道内部的热、
电、化学反应的作用。内壁涂层一般分为有机涂层和无机涂层两类。其中,有机涂层是指使用有机涂料制作的防腐层,而无机涂层是指使用无机涂料制作的防腐层。
2. 外壁防腐技术
外壁防腐技术是在压力管道外壁涂上具有一定性能的涂料,从而形成一层完整的防腐层。与内壁涂层技术相比,外壁防腐技术有着更高的技术难度和复杂性。外壁涂层防腐材料主要分为热喷涂、机械喷涂和涂刷三种。其中,热喷涂技术是将具有防腐性能的材料熔融喷射在管道表面,使其形成密实坚固的防腐层,具有使用寿命长、耐腐蚀性能强等特点。
3. 阴极保护技术
阴极保护技术是一种常用的管道防腐技术,其工作原理是利用外部电位(电正极),通过导体、阳极保护系统和被保护金属构成电池电路,从而在金属表面形成一层保护膜,从而达到防腐的目的。阴极保护技术主要分为直流阴极保护法、电泳均匀阴极保护法、保护电流源阴极保护法、铁素体交流阴极保护法等几个方法。阴极保护技术具有操作简单,使用寿命长,效果稳定等诸多优点,是广泛应用的一种管道防腐技术。
压力管道的腐蚀与防腐
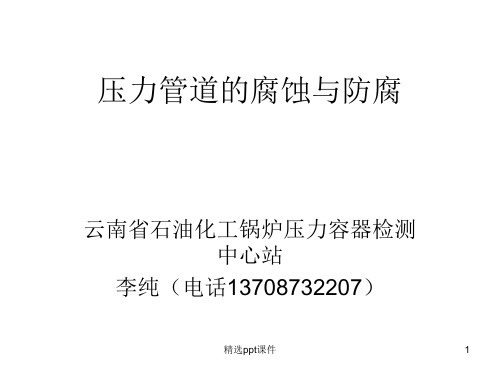
精选ppt课件
15
奥氏体不锈钢焊接过程中,热影响区温度 较容易处于敏化温度范围,故热影响区常出 现晶间腐蚀。
3)刀口腐蚀:沿焊缝金属熔合线发生象刀切 一样的腐蚀,称为刀状腐蚀。刀状腐蚀实质 上是晶间腐蚀的一种特例。
精选ppt课件
16
晶粒
• 2).预先腐蚀然后再疲劳虽然强度下降,但 其作用要比介质和应力同时作用弱得多并 保持疲劳极限。
精选ppt课件
33
• 疲劳裂纹一般为穿晶,往往有很多条,但 无分支。
• 压力管道疲劳源主要有:机械振动、流体 工况、自然因素等。
精选ppt课件
34
• 4.2.5氢损伤
• 氢渗透进入金属内部而造成金属性能劣化 称为氢损伤。氢损伤可分为:
精选ppt课件
1
4.1 概述
压力管道的腐蚀是由于受到内部输送物 料及外部环境介质的化学和电化学作用以及 机械等因素的共同作用而发生的破坏。
腐蚀造成管道失效带来经济损失,对于 压力管道更主要的危害是腐蚀破坏可能导致 物料泄漏,发生火灾、中毒、爆炸等安全事 故,带来生命财产的重大损失。故必须采取 科学有效的方法防止或减缓压力管道的腐蚀, 以保证压力管道的安全使用。
13
• 3)焊接接头的腐蚀
• 通常发生于不锈钢管道焊缝,有三种腐 蚀形式:
压力钢管安全鉴定防腐蚀措施与效果评估
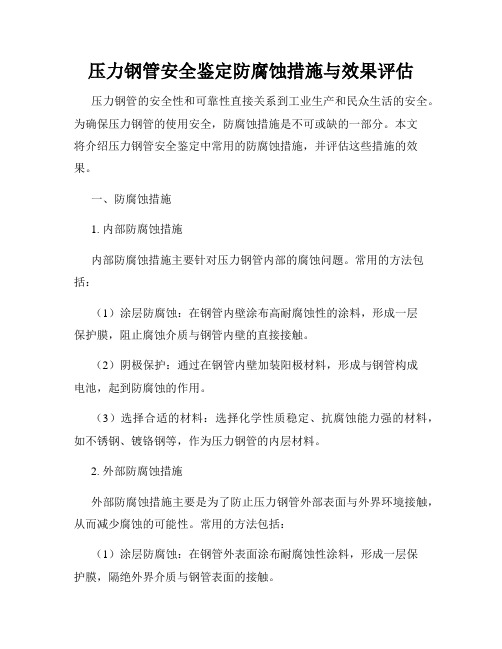
压力钢管安全鉴定防腐蚀措施与效果评估
压力钢管的安全性和可靠性直接关系到工业生产和民众生活的安全。为确保压力钢管的使用安全,防腐蚀措施是不可或缺的一部分。本文
将介绍压力钢管安全鉴定中常用的防腐蚀措施,并评估这些措施的效果。
一、防腐蚀措施
1. 内部防腐蚀措施
内部防腐蚀措施主要针对压力钢管内部的腐蚀问题。常用的方法包括:
(1)涂层防腐蚀:在钢管内壁涂布高耐腐蚀性的涂料,形成一层
保护膜,阻止腐蚀介质与钢管内壁的直接接触。
(2)阴极保护:通过在钢管内壁加装阳极材料,形成与钢管构成
电池,起到防腐蚀的作用。
(3)选择合适的材料:选择化学性质稳定、抗腐蚀能力强的材料,如不锈钢、镀铬钢等,作为压力钢管的内层材料。
2. 外部防腐蚀措施
外部防腐蚀措施主要是为了防止压力钢管外部表面与外界环境接触,从而减少腐蚀的可能性。常用的方法包括:
(1)涂层防腐蚀:在钢管外表面涂布耐腐蚀性涂料,形成一层保
护膜,隔绝外界介质与钢管表面的接触。
(2)金属防腐蚀:通过对钢管进行镀锌、镀锡等处理,使钢管表
面形成一层具有抗腐蚀能力的金属层。
(3)绝缘防腐蚀:使用绝缘材料覆盖压力钢管,防止钢管与外界
环境接触,减少腐蚀风险。
二、效果评估
对于压力钢管安全鉴定中的防腐蚀措施,需要进行有效的效果评估,以确保其可靠性。
1. 检测方法
(1)物理检测:采用物理方法对压力钢管进行检测,如外观检查、厚度测量等,判断涂层是否完好,并评估外观腐蚀情况。
(2)化学分析:对压力钢管内、外涂层进行化学成分分析,确定
涂层防腐蚀材料的质量,并评估其防腐蚀性能。
2. 评估标准
压力管道涂漆防腐工艺标准导则
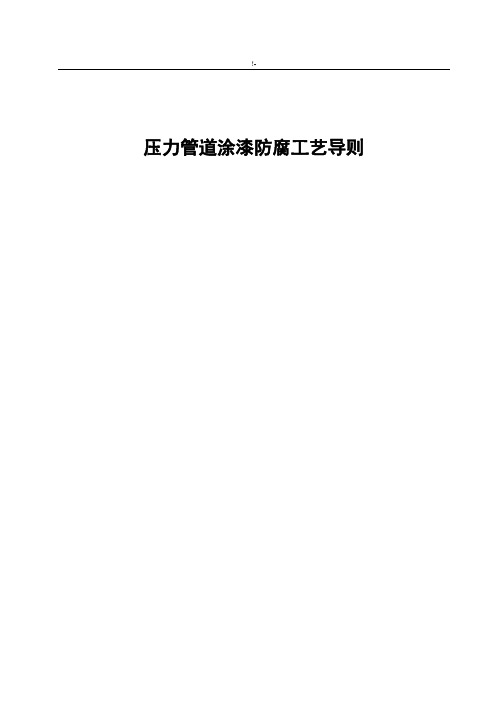
防腐层的绝缘性能在管子下沟回填土前,应用电火花检验器检测。检测时用的电压:正常防腐层为12kV,加强防腐层为24kv,特加强防腐层为36kv。
沥青绝缘防腐层施工工序间的检查及最后全面检查,都应做详细记录,做为隐蔽工程资料。其中内容应包括:管长、管径、坐标,防腐层结构类型,净管方法与质量,所用材料的配比、性能及种类,每层厚度及质量,工程质量的总鉴定等。
机械喷涂
采用的工具为喷枪,以压缩空气为动力。喷射的漆流应和喷漆面垂直。喷漆面为平面时,喷嘴与喷漆面应相距250一350mm;喷漆面如为圆弧面,喷嘴与喷漆面的距离应为400mm左右。
喷涂时,喷嘴的移动应均匀,速度宜保持在10—18m/min。喷漆使用的压缩空气压力0.2—0.4MPa。
涂漆施工程序如下:
绿
白
氮气管
棕
热力网送出水管
绿
黄
抽管
橙黄
热力网返回水管
绿
褐
排水管
绿
蓝
疏水管
绿
黑
排气管
红
黑
高热值煤气管
黄
软化(补给)水管
绿
白
低热值煤气管
黄
褐
生水管
绿
黄
液化石油气管
黄
绿
热水管
绿
蓝
压缩空气管
浅蓝
盐水管
浅黄
钢管防腐技术要求
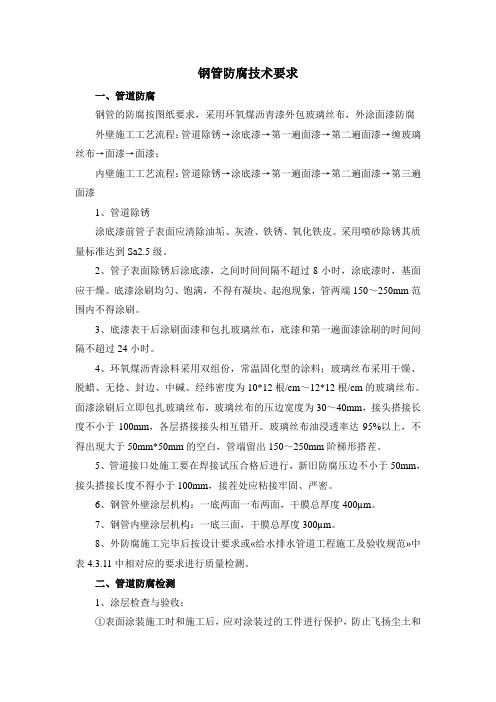
钢管防腐技术要求
一、管道防腐
钢管的防腐按图纸要求,采用环氧煤沥青漆外包玻璃丝布,外涂面漆防腐外壁施工工艺流程:管道除锈→涂底漆→第一遍面漆→第二遍面漆→缠玻璃丝布→面漆→面漆;
内壁施工工艺流程:管道除锈→涂底漆→第一遍面漆→第二遍面漆→第三遍面漆
1、管道除锈
涂底漆前管子表面应清除油垢、灰渣、铁锈、氧化铁皮。采用喷砂除锈其质量标准达到Sa2.5级。
2、管子表面除锈后涂底漆,之间时间间隔不超过8小时,涂底漆时,基面应干燥。底漆涂刷均匀、饱满,不得有凝块、起泡现象,管两端150~250mm范围内不得涂刷。
3、底漆表干后涂刷面漆和包扎玻璃丝布,底漆和第一遍面漆涂刷的时间间隔不超过24小时。
4、环氧煤沥青涂料采用双组份,常温固化型的涂料;玻璃丝布采用干燥、脱蜡、无捻、封边、中碱、经纬密度为10*12根/cm~12*12根/cm的玻璃丝布。面漆涂刷后立即包扎玻璃丝布,玻璃丝布的压边宽度为30~40mm,接头搭接长度不小于100mm,各层搭接接头相互错开。玻璃丝布油浸透率达95%以上,不得出现大于50mm*50mm的空白,管端留出150~250mm阶梯形搭茬。
5、管道接口处施工要在焊接试压合格后进行,新旧防腐压边不小于50mm,接头搭接长度不得小于100mm,接茬处应粘接牢固、严密。
6、钢管外壁涂层机构:一底两面一布两面,干膜总厚度400µm。
7、钢管内壁涂层机构:一底三面,干膜总厚度300µm。
8、外防腐施工完毕后按设计要求或«给水排水管道工程施工及验收规范»中表4.3.11中相对应的要求进行质量检测。
钢管内外防腐技术要求
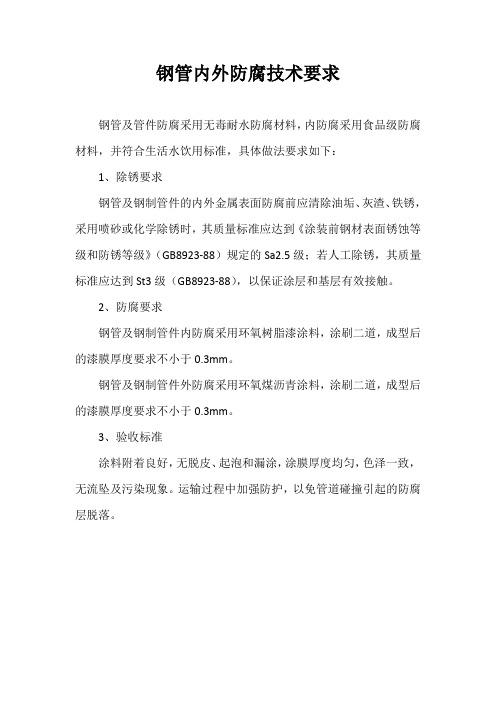
钢管内外防腐技术要求
钢管及管件防腐采用无毒耐水防腐材料,内防腐采用食品级防腐材料,并符合生活水饮用标准,具体做法要求如下:
1、除锈要求
钢管及钢制管件的内外金属表面防腐前应清除油垢、灰渣、铁锈,采用喷砂或化学除锈时,其质量标准应达到《涂装前钢材表面锈蚀等级和防锈等级》(GB8923-88)规定的Sa2.5级;若人工除锈,其质量标准应达到St3级(GB8923-88),以保证涂层和基层有效接触。
2、防腐要求
钢管及钢制管件内防腐采用环氧树脂漆涂料,涂刷二道,成型后的漆膜厚度要求不小于0.3mm。
钢管及钢制管件外防腐采用环氧煤沥青涂料,涂刷二道,成型后的漆膜厚度要求不小于0.3mm。
3、验收标准
涂料附着良好,无脱皮、起泡和漏涂,涂膜厚度均匀,色泽一致,无流坠及污染现象。运输过程中加强防护,以免管道碰撞引起的防腐层脱落。
- 1、下载文档前请自行甄别文档内容的完整性,平台不提供额外的编辑、内容补充、找答案等附加服务。
- 2、"仅部分预览"的文档,不可在线预览部分如存在完整性等问题,可反馈申请退款(可完整预览的文档不适用该条件!)。
- 3、如文档侵犯您的权益,请联系客服反馈,我们会尽快为您处理(人工客服工作时间:9:00-18:30)。
摘要:三峡工程地处南温带和亚热带过渡地带,属湿热带气候。三峡发电机组压力钢管直径大(),距离长(122.175 m),落差大(60 m),钢管中水的流速高(8 m/s),会对管壁内油漆产生腐蚀与磨损,腐蚀后维修难、费用高。因此,应慎重选择压力钢管防腐材料。三峡右岸电站压力钢管首次使用了无溶剂超强厚浆型环氧耐磨漆,以提高压力钢管的使用寿命,减少钢管内壁的防腐维修次数,提高机组的安全运行效率。
关键词:压力钢管;防腐材料;选用;施工
三峡工程左岸电站压力钢管防腐采用的是厚浆型环氧沥青漆,涂装厚度450 μm,施工时段1998-2003年。1998年国内的无溶剂超强耐磨漆环氧漆尚在试验阶段,后在船舶业的淡水舱、压载舱取得成功。无溶剂超强耐磨环氧漆具有无溶剂挥发(环保)、耐磨、耐腐蚀等诸多优点,适合压力钢管的防腐;所以三峡右岸电站压力钢管选用了无溶剂超强耐磨环氧漆,涂装厚度800 μm。
1、涂料技术指标
1.1 涂料组成
由特种环氧树脂,着色材料,耐磨填充料,增调剂和助剂配制而成,并用弹性聚酰胺树脂为固化剂的交固体二罐装。
1.2涂料主要特性
没有挥发性溶剂,具有优异的耐水性和防锈性,良好的抗化学品性能和耐油性,良好的附着力,耐冲击性、耐磨性(表1)。无气喷涂一道,干漆膜厚度可达到600 μm左右。
1.3涂料物理参数
漆面:半光;
颜色:灰色;
体积固体含量:100%;
理论涂布率:1 m2/1.1 kg(以800 μm干膜计);
耐温:最大(干燥)140℃;
闪点:>100℃;
比重:1.3 kg/L;
指触干:约24 h(环境温度20℃左右);
完全固化:7 d(环境温度20℃左右)。
2 、施工要求
2.1表面处理
表面处理采用喷丸除锈。压力钢管内壁表面清洁度达到Sa2.5级以上标准,表面粗糙度达到Ry40~70 μm。磨粒粒径0.5~1.5 mm。
2.2喷涂技术要求
(1)压力钢管内壁预处理后,应尽快实施喷涂施工,一般应在6 h内喷涂。
晴天和正常天气条件下,最长不得超过10 h,压力钢管内壁表面处理后不得用手触摸,不得污染。
(2)喷涂施工环境应高于5℃,压力钢管内壁表面高于露点3℃以上,相对湿度小于85%。
(3)无溶剂超强耐磨漆环氧漆使用要求:
① 混合比例:基料H542/固化剂G542=4/1(体积比);
② 稀释剂:不必稀释;
③ 混合使用时间:约1 h;
④漆膜厚度:湿膜600μm(第一道),湿膜450μm(第二道);
⑤重涂间隔:24 h(环境温度20℃左右)。
2.3喷涂设备选用
采用GPQ6C型无气喷涂机,喷嘴030B30型。主要技术参数如下:
①外形尺寸520mm×430mm×670mm;质量45 kg;压力比65∶1;涂料排量25 L/min;进气压力0.3~0.6 MPa;空气消耗量300~2500 L/min。
②030B30型喷嘴:流量3 L/min;喷嘴前30 cm处雾幅宽度30 cm。
3、喷涂施工
油漆开桶后要分别对基料H542和固化剂G542进行充分搅拌,使沉淀混合均匀。再按照4∶1的比例进行配比,充分搅拌,待油漆反应1 h后进行喷涂。
喷涂时应以手带动喷枪移动,做到“手到枪到、枪随手动”,最忌手不动,仅以喷枪的摆动进行喷涂,移动幅度以0.5~0.8 m为宜。喷涂距离0.3~0.5 m 为宜,若喷涂距离过小,涂层形成高温在降至常温时,涂层收缩应力增大,会引起涂层破裂,翘皮和脱落;喷距过大,所形成的喷涂层结构疏松(俗称桔子皮现象),表面大量针孔现象,钢管内壁油漆结合力下降、耐腐蚀能力下降。
喷涂时喷枪应与钢管内壁垂直,否则很难保证油漆涂层均匀(厚800 μm)。如果喷涂工操作不当,不仅会浪费大量油漆,而且局部厚度过厚将产生流挂现象,因此,要求喷涂工人必须具备熟练操作技术,同时须给喷涂工人创造好的操作条件。压力钢管一般高4 m,可先制作一高2.3 m左右的活动台车以备喷涂工人操作用。喷涂时采用从上到下,从左到右有次序方式进行喷涂,使油漆光滑平整、厚度均匀。
涂装过程中操作人员应随时用湿膜测厚仪测定湿膜厚度,以控制漆膜厚度及油漆厚度的均匀性。
4、油漆用量测算
根据大面积喷涂后对压力钢管油漆用量进行测算,1 m2油漆用量1.35 kg左右,基本同厂家油漆说明书吻合。计算结果如下:
理论用漆量 Q1=F(1 m2)×干漆膜厚(0.8 mm)×容重(1.3 kg/L)×1.07(干湿比)=1.11 kg
实际油漆用量Q2=Q1×1.2(损耗+不均匀涂布影响)=1.33 kg
5、涂装质量检验
无溶剂超强耐磨环氧漆完全固化后,须按规范SL105、GB9286对内部质量及外部质量进行检测,面漆颜色应符合BG51001漆膜颜色标准的要求。按上述要求编制、填写质量检测记录表。
内部质量:涂层厚度达到厚度要求的点数要大于或等于检测点数的85%(1 m2范围不少于3个点);未达到厚度的检测点,其厚度也要大于或等于
800μm×85%=680μm;附着力采用划夹角60°的两切割线,胶带粘撕无剥落;涂层内不允许有针孔。
外部质量:涂层不允许有漏涂、鼓泡、裂纹、皱纹、流挂等现象;油漆表面颜色要均匀。
压力钢管采用无溶剂超强耐磨环氧漆涂装施工过程中应加强控制压力钢管的表面处理质量和涂装工艺质量,使压力钢管涂装的无溶剂超强耐磨环氧漆在保护年限20年内不被损坏。
三峡工程的压力钢管防腐刚刚开始,是否能真正满足防腐设计要求所规定的年限以及涂装质量,只有通过工程实践和水下运行才能做结论