浅谈回转窑结圈
回转窑结圈的原因及处理方法

回转窑结圈的原因及处理方法1、结圈的危害回转窑“结圈”的部位一般在距窑口一定距离的固体燃料集中燃烧点附近的耐火窑衬上,厚度可达200-500 mm左右。
“结圈”对球团生产的危害有以下几方面:(1)降低产量,增加劳动强度窑圈一经形成,对燃料烧烧所产生的热气流势必起阻碍作用,如图-1所示。
热气流被部分阻挡在A区,影响了球团的焙烧效果。
同时,由于链篦机上生球的干燥、预热过程是利用窑尾废气进行的,故此,结圈也对生球的干燥、预热产生不良影响。
具体地说,就是透气性差,火焰不进,后部温度低,干燥时水分不易脱除,生球爆裂、粉化严重,成品率低,从而降低了劳动生产率。
另外,圈结形成后,如不及时处理,就会使圈的纵向长度、厚度增加,当圈掉下时,必然增加工人的劳动强度,有时甚至需停机处理,也影响了球团矿的产量。
(2) 增加了设备负荷如图-1所示,一定面积及厚度的结圈使物料流被阻于B区,此时,被阻的料量要高出正常时许多,加之圈本身的重量,必然增加了托轮、轴承的磨损,同时,增加了电机的负荷,甚至烧毁。
(3) 浪费能源在实际看火操作中,当出现“结圈”现象后,由于热气流被阻于A区,为保证链篦机的干燥和预热效果,看火工往往采用加大给煤量的方式,这无疑造成了能源浪费。
2、结圈的原因结圈的原因,在生产中主要可以归纳为操作不当。
具体地说,是由于上料量过大,干燥效果差,生球爆裂,粉化严重,致使透气性差,使得引风机抽动火焰的作用不明显,火焰只在窑内一定距离燃烧。
在大于1 200℃的高温下,未完全氧化的Fe3O4就与磁铁矿中一定数量的SiO2发生反应形成液相。
2Fe3O4+3SiO2+2CO=3Fe2SiO4+2CO22FeO+SiO2=Fe2SiO4另外,当给煤量较大时,在1 150℃条件下,Fe2O3也会部分分解为Fe3O4,与SiO2作用而生成2FeO·SiO2,形成渣相粘结。
这就使得物料在流经焙烧带时,所产生的液相、渣相极易粘附在窑衬的表面,同时粘结物料而产生结圈现象。
回转窑接圈原因分析

1 结圈的形成回转窑内形成结圈的因素很多,但液相的产生和固化是结圈的主要形成过程。
而物料温度、煤灰和原料组成又是决定液相的生成和固化的主要因素。
在煅烧过程中,料在1200℃左右出现液相,在1250℃左右液相粘度开始变小,液相量增加,由于料层覆盖温度突降,加之筒体表面散热,液相在窑壁上凝固下来,形成窑皮。
窑继续运转,窑皮又暴露在高温中而被熔掉下来,再次被物料覆盖,液相又凝固下来,如此周而复始。
如果粘挂上去的多,掉下来的小,窑皮就增厚,反之就变薄。
在正常情况下,窑皮可保持在200mm左右的厚度。
该温度条件及区域内若熔化和固化的过程达到平衡,窑皮就不会增厚。
当熔化的少固化的多,其厚度增长到一定程度,即形成圈。
当物料与液相的温差大时,在足够液相的条件下,圈体越结越厚。
1.1 前结圈的形成前结圈(又称窑口圈),是结在回转窑烧成带末端部位的圈。
在正常煅烧条件下,物料温度为1350~1450℃,液相量约为24%,其粘度较大。
当熟料离开烧成带时,液相开始冷却,进入冷却带的液相已基本固化。
在烧成带和冷却带的交界处存在着较大的温差,窑口物料温度高于窑皮温度。
当熟料进入冷却带时,带有液相的高温熟料覆盖在温度较低的末端窑皮上,就会很快粘结、越粘越厚,最后形成前结圈。
在煅烧过程中,当烧成带高温部分温度过于集中时,冷却带与烧成带交界处出现很大的温差,加之高温急烧液相量增多,粘度较小,熟料进入冷却带时,仍有大量液相迅速冷却在交界的附近,促进了前圈的增长。
1.2 熟料圈的形成熟料圈(又称二道圈),是结在窑内烧成带与放热反应带之间的圈,也是回转窑内危害最大的结圈。
在熟料煅烧过程中,当物料温度达到1280℃时,其液相粘度较大,熟料圈最易形成,冷却后比较坚固,不易除掉,在正常煅烧情况下,熟料圈体的内径部分,往往被烧熔而掉落,保持正常的圈体内径。
如果在1250~1280℃温度范围内出现的液相量偏多,往往形成妨碍生产的熟料圈。
熟料圈一般结在烧成带的边界或更远,开始是烧成带后边的窑皮逐渐增长,逐渐长厚,发展到一定程度即形成熟料圈。
煤基还原回转窑结圈
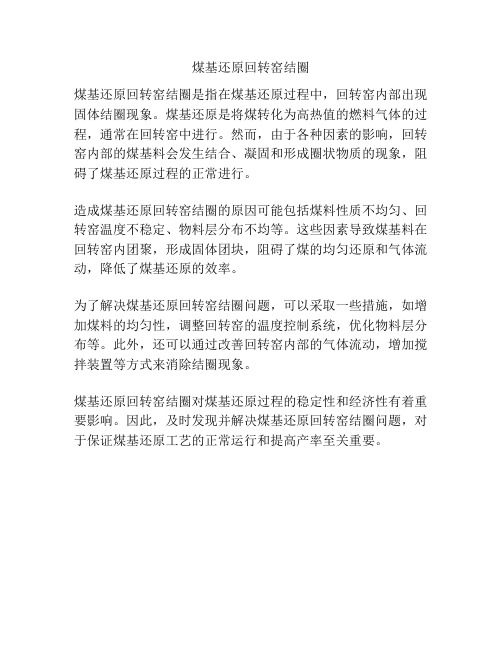
煤基还原回转窑结圈
煤基还原回转窑结圈是指在煤基还原过程中,回转窑内部出现固体结圈现象。
煤基还原是将煤转化为高热值的燃料气体的过程,通常在回转窑中进行。
然而,由于各种因素的影响,回转窑内部的煤基料会发生结合、凝固和形成圈状物质的现象,阻碍了煤基还原过程的正常进行。
造成煤基还原回转窑结圈的原因可能包括煤料性质不均匀、回转窑温度不稳定、物料层分布不均等。
这些因素导致煤基料在回转窑内团聚,形成固体团块,阻碍了煤的均匀还原和气体流动,降低了煤基还原的效率。
为了解决煤基还原回转窑结圈问题,可以采取一些措施,如增加煤料的均匀性,调整回转窑的温度控制系统,优化物料层分布等。
此外,还可以通过改善回转窑内部的气体流动,增加搅拌装置等方式来消除结圈现象。
煤基还原回转窑结圈对煤基还原过程的稳定性和经济性有着重要影响。
因此,及时发现并解决煤基还原回转窑结圈问题,对于保证煤基还原工艺的正常运行和提高产率至关重要。
回转窑窑后结圈原因分析及处理方法

回转窑窑后结圈原因分析及处理方法巩义市恒昌冶金建材设备厂生产的1000t/d熟料生产线是由天津水泥工业设计研究院有限公司设计的,主要包括TDF型分解炉、单系列五级旋风预热器、Φ3.2m×50m回转窑及TC-836篦式冷却机。
自2007年2月以来,窑后频繁发生结圈、结球的工艺事故,巩义市恒昌冶金建材设备厂技术人员现将原因分析及解决措施介绍如下,供同仁参考。
1、结圈情况2007年3月19日最为严重,窑前返火,窑尾有漏料现象,无法操作煅烧,迫使停窑处理。
从窑内看,主窑皮长达22m,副窑皮长到窑尾,35~37m处形成后结圈,结圈最小孔洞呈不规则状,直径约l.5m,进窑观察该圈明显分为两层,且层次明确、清晰,第一层厚约150mm,呈黄白色,第二层厚约460mm,呈黑色,圈体非常致密。
对圈体取样分析见表1。
表1 圈体取样分析结果从表l可以看出,第一层硫碱含量较高,是硫碱圈,第二层明显是煤粉圈,熟料液相出现过早、过多导致结圈。
2、原因分析(1)由于2006年煤价不断上涨,加之公路运输距离远,为了降低成本,采用当地劣质煤煅烧,煤质下降,灰分高,挥发分低,发热值低,煤工业分析如表2、3。
实际生产中,煤可燃性差,煤粉燃烧不完全,大量煤灰不均掺入生料中,液相在窑后面提前出现,而未燃尽的煤灰产生沉积及液相的提前出现结圈。
(2)2007年以来,由于机械原因,高温风机l号轴与密封圈强烈摩擦,产生局部高温,使轴侧曲,水平振动最高达6.4mm/s。
为了降低振动,不得不降低高温风机转速,由原来的1130r/min降至l060r/min,有时更低,严重影响了窑内通风,加上煤质又差,更多的窑头燃烧不完全的煤粉沉积在窑后燃烧,使窑内后部温度升高,液相量增加,加速了窑后结圈的形成。
(3)为了处理窑后结圈,我厂在迫不得已的情况下停窑烧后圈,由于煤质差,二、三次风温低,燃料不完全或未燃烧的煤粉落在圈上及圈后的积料上,不断燃烧,造成物料发粘,不但圈未烧掉,反而越结越厚,这也是第一层圈形成的主要原因。
回转窑后结圈的原因分析与解决措施

回转窑后结圈的原因分析与解决措施发布时间:2022-04-25T02:30:40.147Z 来源:《工程管理前沿》2022年1期作者:田硕[导读] 近年来,由于国家倡导节能减排的生产,从而加大了对一些浪费资源和污染比较大的企业改革田硕山东申丰水泥集团有限公司山东省枣庄市 277300引言:近年来,由于国家倡导节能减排的生产,从而加大了对一些浪费资源和污染比较大的企业改革,这就给了新型熟料回转窑一个重要的市场,让他们可以快速的发展起来。
熟料回转窑设备结构坚固、运转平稳、出窑产品质量高。
此外,在环保方面,利用熟料窑焚烧危险废物、垃圾,这不仅使废物减量化、无害化,而且将废物作为燃料利用,节省煤粉,做到废物的资源化。
关键词:回转窑后结圈解决措施摘要:熟料回转窑后结圈往往形成于烧成带和过渡带之间。
在熟料煅烧过程中,当窑内温度达到1280℃时,其液相粘度较大,此时,如果生料的KH、n率值较低,操作使窑内拉风较大,火焰太长,烧成带后边浮窑皮逐渐增长、增厚,发展到一定程度就形成了熟料回转窑的后结圈。
一、后结圈情况A企业配置一条5000t/d预分解熟料回转窑。
于2021年10月份在窑尾38米、43米处出现两道结圈,严重时窑尾出现漏料,窑投料量下降,熟料质量波动,窑况很不稳定。
二、原因分析2.1原煤内水偏高加剧了结圈的发生2021年煤价不断上涨,原煤库存为0吨,原煤随来随用,严重影响煤的均化效果。
煤粉内水偏高,窑头喷煤管燃烧速度慢、燃烧时间长,火焰的热力分散,燃烧时热力强度低,高温点后移,烧成带拉长,高温点不集中,熟料烧结不致密,二次风温偏低,恶性循环更加加剧了火焰燃烧速度。
物料预烧不好,容易产生不完全燃烧,没有燃尽的煤粉颗粒和CO不能在烧成带燃烧,部分聚集在窑尾燃烧,促使液相在过渡带提前出现,将未熔的物料黏结在一起,形成后结圈。
停窑后取结圈料化学分析结果发现:正常熟料烧失量为0.42%,结圈料为1.66%、2.06%也验证了这一点。
回转窑结圈的原因及处理方法
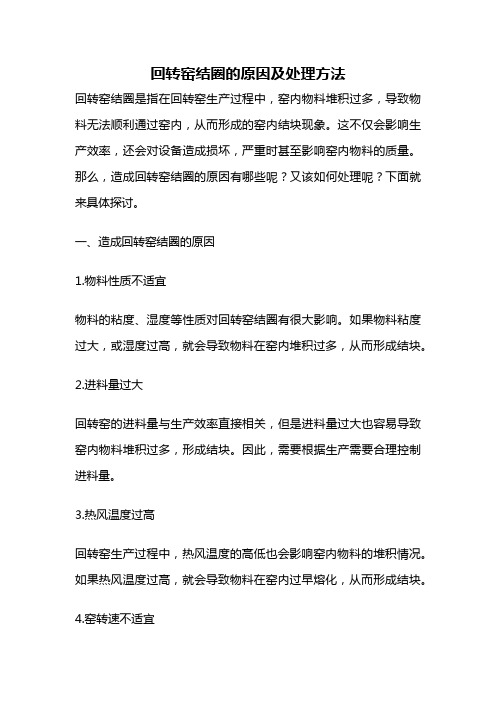
回转窑结圈的原因及处理方法回转窑结圈是指在回转窑生产过程中,窑内物料堆积过多,导致物料无法顺利通过窑内,从而形成的窑内结块现象。
这不仅会影响生产效率,还会对设备造成损坏,严重时甚至影响窑内物料的质量。
那么,造成回转窑结圈的原因有哪些呢?又该如何处理呢?下面就来具体探讨。
一、造成回转窑结圈的原因1.物料性质不适宜物料的粘度、湿度等性质对回转窑结圈有很大影响。
如果物料粘度过大,或湿度过高,就会导致物料在窑内堆积过多,从而形成结块。
2.进料量过大回转窑的进料量与生产效率直接相关,但是进料量过大也容易导致窑内物料堆积过多,形成结块。
因此,需要根据生产需要合理控制进料量。
3.热风温度过高回转窑生产过程中,热风温度的高低也会影响窑内物料的堆积情况。
如果热风温度过高,就会导致物料在窑内过早熔化,从而形成结块。
4.窑转速不适宜回转窑的转速也会影响窑内物料的堆积情况。
如果转速过快,就会导致物料在窑内无法均匀分布,从而形成结块。
二、回转窑结圈的处理方法1.减少进料量当回转窑结圈发生时,可以适当减少进料量,以缓解窑内物料堆积过多的情况。
2.调整热风温度如果回转窑结圈是由于热风温度过高导致的,可以适当降低热风温度,以减少窑内物料的过早熔化。
3.调整窑转速如果回转窑结圈是由于窑转速不适宜导致的,可以适当调整窑转速,以保证物料在窑内均匀分布。
4.清理窑内物料当回转窑结圈严重时,需要停窑清理窑内物料。
清理时需要注意安全,避免对设备造成损坏。
5.加入流化剂在窑内加入一定量的流化剂,可以有效地缓解回转窑结圈现象。
流化剂可以使物料在窑内均匀分布,减少结块的情况。
6.调整物料配比如果回转窑结圈是由于物料配比不合理导致的,可以适当调整物料配比,以保证物料在窑内均匀分布,减少结块的情况。
回转窑结圈是一种常见的生产问题,多种因素都可能导致其发生。
因此,在回转窑生产过程中,需要做好预防措施,保证物料在窑内均匀分布,避免结块的发生。
同时,一旦发生回转窑结圈,需要及时采取相应的处理措施,以保证生产效率和产品质量。
回转窑结圈的原因及处理方法

回转窑结圈的原因及处理方法回转窑是制造水泥的重要设备,而回转窑结圈是影响生产效率和质量的常见问题。
结圈的原因有很多,如窑内温度不均、烧成温度过低、原材料成分不合适等。
本文将从原因和处理方法两个方面详细介绍回转窑结圈问题。
一、结圈的原因1. 窑内温度不均:回转窑内部温度分布不均会导致部分区域的烧成程度不够,形成未熟料,容易粘在窑壁上,最终导致结圈。
2. 烧成温度过低:如果烧成温度过低,则无法将原材料完全反应,也容易导致未熟料粘附在窑壁上。
3. 原材料成分不合适:原材料中含有过多的游离SiO2、Al2O3等物质,会使得反应速率变慢,在高温下难以完全反应。
同时,如果含有过多的碱金属氧化物,则会使得产生大量液态相,增加了结圈的风险。
4. 进出料方式不当:进出料口位置设置不合理,或者进出料速度过快或过慢,都会导致窑内物料分布不均,从而增加结圈的风险。
二、处理方法1. 调整窑内温度:调整窑内温度是解决结圈问题的关键。
可以通过改变燃烧器位置、调整燃料供给量等方式来调整窑内温度分布,使得各个区域的温度均匀。
2. 提高烧成温度:提高烧成温度可以促进原材料反应,减少未熟料生成的可能性。
但是需要注意控制好温度,避免超出窑的承载能力。
3. 调整原材料成分:在生产过程中要严格控制原材料的成分,避免含有过多的游离SiO2、Al2O3等物质和碱金属氧化物。
如果发现原材料成分不合适,则需要及时停机清理,并重新投入符合要求的原材料。
4. 改善进出料方式:调整进出料口位置和速度可以改善窑内物料分布不均的问题。
可以采用多点进出料口、减缓进出料速度等方式来改善这一问题。
5. 定期清理窑壁:定期清理窑壁可以有效减少未熟料的积累,降低结圈的风险。
清理时需要注意安全,避免对设备造成损伤。
综上所述,回转窑结圈是影响水泥生产效率和质量的常见问题。
通过调整窑内温度、提高烧成温度、调整原材料成分、改善进出料方式和定期清理窑壁等方式可以有效解决这一问题。
回转窑结圈的影响

什么是结圈
• 结圈是指回转窑在正常生产中,由于原燃材料 的变化,或者操作和热工制度的影响,窑内因物料过 度粘结,在特定的区域形成一道阻碍物料运动的环 形、坚硬的圈。这种现象在回转窑内是一种不正常 的窑况,它破坏了正常的热工制度,影响窑内通风, 造成窑内来料波动很大,直接影响到回转窑的产量、 质量、消耗和长期安全运转。而且处理窑内结圈费 时费力,严重时需停窑停产,危害极其严重。
结圈的处理方法
无论是前结圈还是后结圈,处理 结圈时一般采用冷热交替法,尽量加 大其温差,使圈体受温度变化而垮落。
前结圈的处理方法
前结圈不高时,对煅烧操作的影响不大,尚 可增加烧成带料层厚度,延长物料在烧成带 的停留时间,使物料反应更完全并降低熟料 中的CaO含量,同时减少烧成带向窑前的辐 射散热。但当前结圈较高时,既影响看火操 作,又影响窑内通风及火焰形状,大块熟料 滚不出来,易损坏烧成带窑皮及衬料。这 时应及时调整风、煤或移动喷煤管进行处理。
后结圈的处理办法
从总体来讲,烧后圈不是一件容易的事, 有时圈体很牢固,若烧圈时间过长,容易 烧坏窑皮及衬料,或在过渡带结长厚窑皮 进而在圈体后产生第2道圈。所以,处理时 一定要小心。一定要在保护窑皮的前提下 进行,前后兼顾,精心操作,勿使火焰过 分集中,避免将窑皮及衬料烧坏,造成更 大的损失。
后结圈的处理办法
在处理后结圈时,要根据圈体的特点和远近,分 别采取不同的处理方法,才能达到较好的效果。 一般采用冷热交替法处理,烧远圈时以冷为主, 烧近圈时以热为主。 (1)当窑内窑皮长而厚或有轻度圈根时,将喷煤管 向外拉出,使烧成带位置前移,降低圈体的温 度,改变煤灰沉落位置,使厚长的窑皮逐渐垮 落。同时调整风煤配合,加速煤粉燃烧,使高 温带两端低温部分不拖长,防止圈根继续成长。
氧化锌回转窑结圈原因

氧化锌回转窑结圈原因
氧化锌回转窑结圈是指在氧化锌生产过程中,回转窑内部出现了石灰石或其他物质的结块现象。
这种现象可能会导致生产效率下降、产品质量下降等问题。
氧化锌回转窑结圈的原因主要有以下几个方面: 1. 原料成分不均匀:如果原料中含有过多的石灰石或其他物质,就会导致回转窑内部结圈。
2. 操作不当:回转窑操作时如果不当,例如进料速度过快或过慢、回转速度不均匀等,都可能导致结圈。
3. 窑内温度过低:回转窑内部温度过低也会导致结圈现象。
因此,在生产过程中需要保持合适的温度。
4. 窑内积存物质:如果回转窑内部有积存的物质,也会导致结
圈现象。
因此,在生产过程中需要及时清理。
为了避免氧化锌回转窑结圈现象的出现,需要在生产过程中严格执行操作规范,控制原料成分,保持合适的温度,并及时清理回转窑内部。
- 1 -。
浅谈回转窑结圈
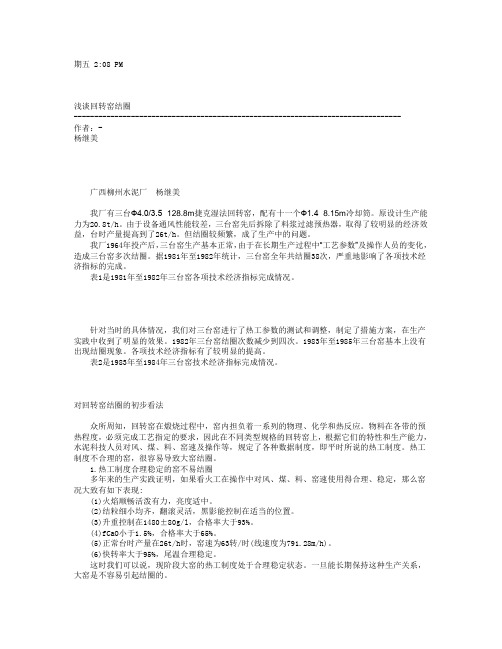
期五 2:08 PM浅谈回转窑结圈--------------------------------------------------------------------------------作者:-杨继美广西柳州水泥厂杨继美我厂有三台Ф4.0/3.5×128.8m捷克湿法回转窑,配有十一个Ф1.4×8.15m冷却筒。
原设计生产能力为20.8t/h。
由于设备通风性能较差,三台窑先后拆除了料浆过滤预热器,取得了较明显的经济效益,台时产量提高到了26t/h。
但结圈较频繁,成了生产中的问题。
我厂1964年投产后,三台窑生产基本正常,由于在长期生产过程中“工艺参数”及操作人员的变化,造成三台窑多次结圈。
据1981年至1982年统计,三台窑全年共结圈38次,严重地影响了各项技术经济指标的完成。
表1是1981年至1982年三台窑各项技术经济指标完成情况。
针对当时的具体情况,我们对三台窑进行了热工参数的测试和调整,制定了措施方案,在生产实践中收到了明显的效果。
1982年三台窑结圈次数减少到四次。
1983年至1985年三台窑基本上没有出现结圈现象。
各项技术经济指标有了较明显的提高。
表2是1983年至1984年三台窑技术经济指标完成情况。
对回转窑结圈的初步看法众所周知,回转窑在煅烧过程中,窑内担负着一系列的物理、化学和热反应。
物料在各带的预热程度,必须完成工艺指定的要求,因此在不同类型规格的回转窑上,根据它们的特性和生产能力,水泥科技人员对风、煤、料、窑速及操作等,规定了各种数据制度,即平时所说的热工制度。
热工制度不合理的窑,很容易导致大窑结圈。
1.热工制度合理稳定的窑不易结圈多年来的生产实践证明,如果看火工在操作中对风、煤、料、窑速使用得合理、稳定,那么窑况大致有如下表现:(1)火焰顺畅活泼有力,亮度适中。
(2)结粒细小均齐,翻滚灵活,黑影能控制在适当的位置。
(3)升重控制在1480±80g/l,合格率大于93%。
回转窑窑后结圈的原因和处理结果

回转窑窑后结圈的原因和处理结果一、回转窑窑后结圈的原因回转窑是一种常用于石灰生产和水泥生产的设备,但在使用过程中,有时会出现窑后结圈的情况。
结圈是指窑内物料在烧结过程中出现结块现象,导致窑内热量传递不畅,影响生产效率和产品质量。
而窑后结圈的原因主要有以下几个方面:1.原料成分不稳定:回转窑生产过程中,原料成分的不稳定性是导致结圈的主要原因之一。
原料成分中的各种氧化物、硅酸盐和铝酸盐等物质,对烧结过程中的矿物相转化和结构稳定性起着重要作用。
如果原料成分的变化超出了窑内控制范围,就容易引起结圈。
2.燃烧条件不理想:回转窑的燃烧条件对结圈问题也有一定影响。
燃料的选择、供氧方式、燃烧温度等因素都会影响窑内气氛的稳定性和热量分布情况。
如果燃烧条件不理想,窑内温度分布不均匀,就容易导致结圈的发生。
3.窑内温度过高:窑内温度是影响回转窑结圈的重要因素之一。
当窑内温度过高时,原料中的一些物质会发生过度烧结,形成块状物质,从而导致结圈。
窑内温度过高可能是由于燃烧条件不理想、窑内热量分布不均匀等原因引起的。
4.窑内物料层厚度不均匀:窑内物料层厚度的不均匀也容易导致结圈。
如果窑内物料层厚度不均匀,热量传递不均匀,就会导致部分物料温度过高,发生结圈。
二、回转窑窑后结圈的处理结果针对回转窑窑后结圈的问题,可以采取一系列措施进行处理,以保证生产的正常进行和产品质量的稳定。
1.优化原料配比和成分控制:通过对原料配比和成分的优化,可以减少原料成分的波动范围,降低结圈的发生概率。
同时,加强对原料成分的在线监测和调控,及时发现和处理原料成分异常,以避免结圈的发生。
2.改进窑内燃烧条件:优化燃料选择、供氧方式和燃烧温度等因素,改善窑内燃烧条件,提高窑内气氛的稳定性和热量分布的均匀性。
通过调整燃烧条件,可以有效预防和减少结圈的发生。
3.控制窑内温度:合理控制窑内温度,避免温度过高或过低,对窑内物料进行适当的保护和调控。
通过优化燃烧条件、改善窑内热量分布等措施,可以有效降低窑内温度的波动,减少结圈的发生。
回转窑结圈种类及其处理
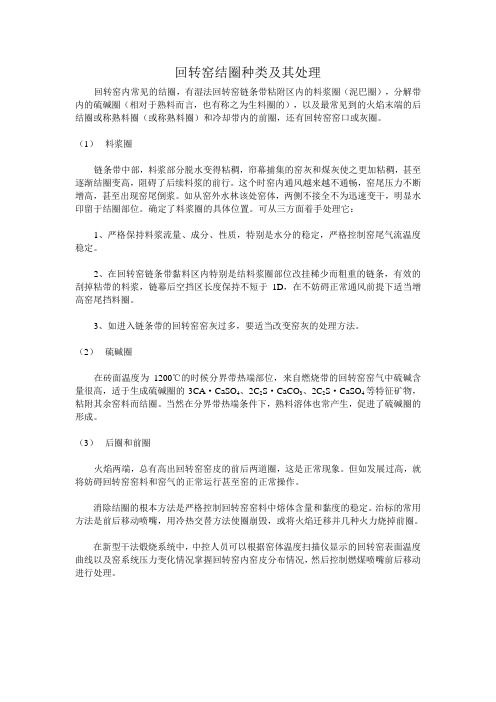
回转窑结圈种类及其处理回转窑内常见的结圈,有湿法回转窑链条带粘附区内的料浆圈(泥巴圈),分解带内的硫碱圈(相对于熟料而言,也有称之为生料圈的),以及最常见到的火焰末端的后结圈或称熟料圈(或称熟料圈)和冷却带内的前圈,还有回转窑窑口或灰圈。
(1)料浆圈链条带中部,料浆部分脱水变得粘稠,帘幕捕集的窑灰和煤灰使之更加粘稠,甚至逐渐结圈变高,阻碍了后续料浆的前行。
这个时窑内通风越来越不通畅,窑尾压力不断增高,甚至出现窑尾倒浆。
如从窑外水林该处窑体,两侧不接全不为迅速变干,明显水印留于结圈部位。
确定了料浆圈的具体位置。
可从三方面着手处理它:1、严格保持料浆流量、成分、性质,特别是水分的稳定,严格控制窑尾气流温度稳定。
2、在回转窑链条带黏料区内特别是结料浆圈部位改挂稀少而粗重的链条,有效的刮掉粘带的料浆,链幕后空挡区长度保持不短于1D,在不妨碍正常通风前提下适当增高窑尾挡料圈。
3、如进入链条带的回转窑窑灰过多,要适当改变窑灰的处理方法。
(2)硫碱圈在砖面温度为1200℃的时候分界带热端部位,来自燃烧带的回转窑窑气中硫碱含量很高,适于生成硫碱圈的3CA·CaSO4、2C2S·CaCO3、2C2S·CaSO4等特征矿物,粘附其余窑料而结圈。
当然在分界带热端条件下,熟料溶体也常产生,促进了硫碱圈的形成。
(3)后圈和前圈火焰两端,总有高出回转窑窑皮的前后两道圈,这是正常现象。
但如发展过高,就将妨碍回转窑窑料和窑气的正常运行甚至窑的正常操作。
消除结圈的根本方法是严格控制回转窑窑料中熔体含量和黏度的稳定。
治标的常用方法是前后移动喷嘴,用冷热交替方法使圈崩毁,或将火焰迁移并几种火力烧掉前圈。
在新型干法煅烧系统中,中控人员可以根据窑体温度扫描仪显示的回转窑表面温度曲线以及窑系统压力变化情况掌握回转窑内窑皮分布情况,然后控制燃煤喷嘴前后移动进行处理。
回转窑结圈的原因及处理方法

回转窑结圈的原因及处理方法回转窑是一种常用于水泥生产过程中的设备,它通过高温和旋转运动将原料进行煅烧,以产生水泥熟料。
然而,有时候在回转窑的运行过程中,会出现结圈现象,这会严重影响设备的正常运行和水泥生产的质量。
了解回转窑结圈的原因及处理方法是至关重要的。
一、回转窑结圈的原因1. 原料成分不理想:回转窑的结圈问题与原料中的成分有很大的关系。
如果原料的化学成分不理想,其中含有过多的硫酸钠、硫酸镁等物质,将会导致煅烧过程中产生黏性物质,从而引起结圈。
2. 烧成温度过低:回转窑烧成温度过低也是导致结圈的一个重要原因。
当烧成温度过低时,原料中的化学反应无法完全进行,会导致部分物质残留在窑内,形成结圈。
3. 运行时间过长:长时间的运行也是回转窑结圈的一个重要原因之一。
当回转窑的运行时间超过其设计要求时,窑内结构会变得粘性,给结圈问题的发生提供了条件。
二、回转窑结圈的处理方法1. 优化原料配比:通过调整原料的化学成分,合理设计原料的配比,可以减少结圈问题的发生。
降低硫酸钠和硫酸镁等物质的含量,增加硅酸盐等成分,从而降低结圈的风险。
2. 提高烧成温度:增加回转窑的烧成温度可以有效地解决结圈问题。
适当提高温度可以加速化学反应的进行,降低黏性物质的生成,从而减少结圈发生的可能性。
3. 控制运行时间:合理控制回转窑的运行时间,确保在规定的运行时间内对窑内进行清理和维护。
定期对窑内进行清扫,清除可能产生结圈的物质,可以预防结圈问题的发生。
4. 使用防结圈剂:可以考虑在回转窑的煅烧过程中添加一定量的防结圈剂。
这些防结圈剂可以改变物料表面的化学性质,降低物料的粘性,减少结圈的风险。
5. 加强设备维护:定期对回转窑进行维护保养,保持设备的正常运行状态。
清理窑内的积存物,检查窑体和内衬的磨损情况,修复和更换损坏的部件,可以有效地预防结圈问题的发生。
总结与回顾:回转窑结圈问题是水泥生产过程中的常见现象,它会严重影响生产效率和产品质量。
回转窑结圈原因分析

回转窑结圈原因分析
经过我国12年来的大型链篦机—回转窑工艺生产实践,大体上讲,引起回转窑结圈的原因主要有四方面:①回转窑内粉状物太多(回转窑中的粉末一部分是从链篦机中随球团一起带入,一部分是由于球团在回转窑中受到摩擦剥落而产生的,还有一部分为煤燃烧的残留物);②回转窑气氛控制不好;③回转窑温度控制不当;④原料中SiO2含量高(当窑内温度上升到1200℃左右时,低熔点物软化,窑内粉末在窑壁上固相扩散粘附和液相粘附不断积累形成)。
就这几方面而言,似乎回转窑结圈的原因很简单,而实际上造成球团结圈的因素是多种多样的,这些因素及其相互关系如图示。
因此,根据回转窑结圈的各种因素分析,在即将生产的链篦机—回转窑工艺中提前做好各项预防措施,以降低回转窑结圈对生产的影响。
从物理和化学方面详细阐述回转窑结圈现象的原因
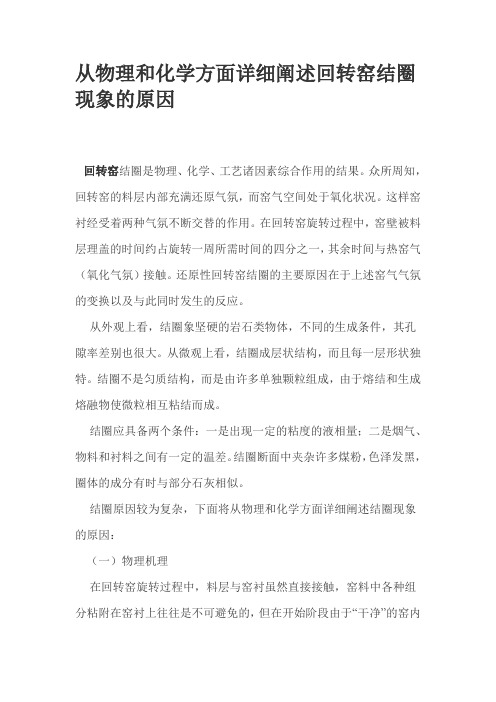
从物理和化学方面详细阐述回转窑结圈现象的原因回转窑结圈是物理、化学、工艺诸因素综合作用的结果。
众所周知,回转窑的料层内部充满还原气氛,而窑气空间处于氧化状况。
这样窑衬经受着两种气氛不断交替的作用。
在回转窑旋转过程中,窑壁被料层理盖的时间约占旋转一周所需时间的四分之一,其余时间与热窑气(氧化气氛)接触。
还原性回转窑结圈的主要原因在于上述窑气气氛的变换以及与此同时发生的反应。
从外观上看,结圈象坚硬的岩石类物体,不同的生成条件,其孔隙率差别也很大。
从微观上看,结圈成层状结构,而且每一层形状独特。
结圈不是匀质结构,而是由许多单独颗粒组成,由于熔结和生成熔融物使微粒相互粘结而成。
结圈应具备两个条件:一是出现一定的粘度的液相量;二是烟气、物料和衬料之间有一定的温差。
结圈断面中夹杂许多煤粉,色泽发黑,圈体的成分有时与部分石灰相似。
结圈原因较为复杂,下面将从物理和化学方面详细阐述结圈现象的原因:(一)物理机理在回转窑旋转过程中,料层与窑衬虽然直接接触,窑料中各种组分粘附在窑衬上往往是不可避免的,但在开始阶段由于“干净”的窑内壁表面缺乏附着基础,只有比重轻的细顺粒和烟气中的粉尘,首先附在窑壁的耐火衬上,这种极细颗粒的粘附主要是经过机械沉积,少量是经化学粘结桥而形成的。
粘附在窑壁上的这种颗粒,承受颗粒自重的机械分力、烟气流动的机械分力以及窑的轴向和切线负荷的机械分力,还有料层压紧力,当粘附强度不够时,较大的和较重的颗粒会从窑壁上自动脱落或被擦落。
因而窑料在窑衬的粘附只有在粘附严重的后期层中才包有较小的球团或破碎球团等较大颗粒,如果使用粉矿还原工艺,则窑壁结圈主要由细顺粒矿石组成,也夹有细煤颗粒。
总之,窑料与窑衬直接接触极细粒级的机械粘附及料层上部窑气气流中的粉尘沉积,都是窑衬结圈的主要物理演变过程。
(二)化学机理产生大粘附强度结圈更重要的原因是各种组分之间的化学反应和键组合。
当达到一定的温度条件时,该区存在的窑料在合适的条件下形成低熔点共晶物,特别是酸性煤灰或矿石中的脉石与FeO生成的铁橄榄石起很重要的作用,在还原性气氛下,FeO的存在使煤灰分熔点降低,产生液相,还原煤灰分熔点越低,产生的液相越多,粘附也越严重,粘附力也越大。
球团回转窑结圈诊断

球团回转窑结圈诊断球团回转窑是一种重要的水泥生产设备,广泛应用于水泥生产过程中。
然而,由于生产过程中的各种因素,球团回转窑的结圈问题经常发生,影响生产效率和产品质量。
因此,球团回转窑的结圈诊断显得尤为重要。
结圈是指在球团回转窑内墙面和转筒内壁上形成厚而坚固的结合层的现象,这可能会导致生产过程中的下列问题:1.增加能耗:由于结圈层的存在,火焰与物料之间的热交换效率降低,导致能耗的增加。
2.降低生产能力:结圈层会堵塞球团回转窑的内部空间,使物料无法自由流动,从而降低生产能力。
3.降低产品质量:结圈层的存在可能导致产生大量的灰渣,降低水泥产品的质量。
为了诊断球团回转窑的结圈问题,可以采取以下步骤:1.观察结圈形态:通过观察球团回转窑内壁上的结圈形态,可以初步判断结圈的原因。
例如,如果结圈形态较为均匀,可能是由于煤气流量不足或者煤粉燃烧不完全所造成的。
2.分析排放气体:通过分析球团回转窑排放的气体成分,可以了解燃烧过程中的变化。
例如,高CO和CO₂含量可能是煤粉燃烧不完全的表现,需要调整煤粉供给和燃烧风量。
3.检测内部温度:利用红外热像仪等设备,检测球团回转窑内部的温度变化。
高温区域可能是结圈问题的主要发生地点,因此需要对高温区域进行进一步的分析和处理。
4.样品分析:采集球团回转窑内物料和结圈层的样品进行分析。
通过分析物料中的成分和结圈层的组成,可以判断结圈层的形成机制。
例如,结圈层中含有较高的氧化铁或氧化钙,可能是由于煤粉中矿物质含量过高所导致的。
5.优化工艺参数:根据诊断结果,调整球团回转窑的工艺参数,以减少结圈问题的发生。
例如,可以调整煤粉供给量、燃烧风量和冷却风量等参数,以优化燃烧和冷却过程。
总结起来,球团回转窑的结圈诊断是一项复杂而重要的工作。
通过观察结圈形态、分析排放气体、检测内部温度和样品分析等方法,可以找出结圈问题的原因,并优化工艺参数,以减少结圈的发生。
这将有助于提高球团回转窑的生产效率和产品质量。
回转窑结圈原理

回转窑结圈原理
嘿,朋友们!今天咱就来好好聊聊回转窑结圈原理。
你们知道吗,回转窑就像是一个大胃王,不停地“吃”进各种原料,然后进行加工。
那结圈呢,就好像是这个大胃王闹肚子了!比如说哈,就像我们吃坏了东西会不舒服一样。
回转窑在工作的时候,温度那是相当高啊!高温会让物料产生一系列奇妙的变化。
就好比是魔法在施展,物料在窑内翻滚、融合。
但是呢,如果有些物料在某些地方聚集得太多了,哎呀,那麻烦可就来了!这不就像路上堵车了嘛,一下子就不顺畅了。
咱再举个例子,你想想,要是一条公路上有一堆石头堆在那儿,车还能顺利通过吗?这回转窑里的物料也是这样啊,聚在一起慢慢就形成了结圈。
“哎呀,那咋办呀?”别急呀,咱有办法!我们得时刻关注着回转窑的运转情况,就像我们照顾一个生病的小伙伴一样。
一旦发现有结圈的迹象,就赶紧采取措施。
你说这回转窑结圈是不是很让人头疼啊?但只要我们了解它的原理,找到应对的办法,也不用太害怕。
所以呀,我们得深入研究它,和它斗智斗勇,
可不能让它随便就“生病”了呀!总之,回转窑结圈原理虽然有点复杂,但只要我们用心去理解,就一定能搞定它!。
- 1、下载文档前请自行甄别文档内容的完整性,平台不提供额外的编辑、内容补充、找答案等附加服务。
- 2、"仅部分预览"的文档,不可在线预览部分如存在完整性等问题,可反馈申请退款(可完整预览的文档不适用该条件!)。
- 3、如文档侵犯您的权益,请联系客服反馈,我们会尽快为您处理(人工客服工作时间:9:00-18:30)。
浅谈回转窑结圈作者:-杨继美广西柳州水泥厂杨继美我厂有三台Ф4.0/3.5×128.8m捷克湿法回转窑,配有十一个Ф1.4×8.15m冷却筒。
原设计生产能力为20.8t/h。
由于设备通风性能较差,三台窑先后拆除了料浆过滤预热器,取得了较明显的经济效益,台时产量提高到了26t/h。
但结圈较频繁,成了生产中的问题。
我厂1964年投产后,三台窑生产基本正常,由于在长期生产过程中“工艺参数”及操作人员的变化,造成三台窑多次结圈。
据1981年至1982年统计,三台窑全年共结圈38次,严重地影响了各项技术经济指标的完成。
表1是1981年至1982年三台窑各项技术经济指标完成情况。
针对当时的具体情况,我们对三台窑进行了热工参数的测试和调整,制定了措施方案,在生产实践中收到了明显的效果。
1982年三台窑结圈次数减少到四次。
1983年至1985年三台窑基本上没有出现结圈现象。
各项技术经济指标有了较明显的提高。
表2是1983年至1984年三台窑技术经济指标完成情况。
对回转窑结圈的初步看法众所周知,回转窑在煅烧过程中,窑内担负着一系列的物理、化学和热反应。
物料在各带的预热程度,必须完成工艺指定的要求,因此在不同类型规格的回转窑上,根据它们的特性和生产能力,水泥科技人员对风、煤、料、窑速及操作等,规定了各种数据制度,即平时所说的热工制度。
热工制度不合理的窑,很容易导致大窑结圈。
1.热工制度合理稳定的窑不易结圈多年来的生产实践证明,如果看火工在操作中对风、煤、料、窑速使用得合理、稳定,那么窑况大致有如下表现:(1)火焰顺畅活泼有力,亮度适中。
(2)结粒细小均齐,翻滚灵活,黑影能控制在适当的位置。
(3)升重控制在1480±80g/l,合格率大于93%。
(4)fCaO小于1.5%,合格率大于65%。
(5)正常台时产量在26t/h时,窑速为63转/时(线速度为791.28m/h)。
(6)快转率大于95%,尾温合理稳定。
这时我们可以说,现阶段大窑的热工制度处于合理稳定状态。
一旦能长期保持这种生产关系,大窑是不容易引起结圈的。
2.热工参数对煅烧及结圈的影响风:一、二次风是回转窑重要的热工参数。
它关系到火焰的长短、物料的预烧、预热程度、质量的好坏、产量的高低及衬料寿命的长短。
若一、二次风配合不合理,仍会导致大窑的结圈。
(1)一次风过大一次风过大,在看火孔观察到火焰短粗发亮,烧成带混浊不清,起火快,高温过于集中。
这时尾温有下降的趋势,看火工稍有不慎,物料很容易起块发粘,造成大量退煤或止煤,导致后面物料预烧不足,而打大慢车。
如果处理得不恰当,还会造成周期性慢车,破坏热工制度的稳定,引起大窑结圈。
(2)一次风过小一次风过小时,火焰显瘦长无力,烧成带清亮但起火慢,尾温上升,料层稍厚时熟料升重低甚至出废品。
长时间的风小,促使烧成带的窑皮延伸长厚,引起大窑结圈。
(3)二次风过大在操作中,使用过大排风时,出现黑火头长,尾温偏高,火色发红,结粒较粗。
感觉到物料粘性差,fCaO 偏低,长时间的尾温高,促使窑口圈长得很快,而高温区的窑皮却不长。
烧成带窑皮明显延伸,几个班不掉,很容易引起结圈。
(4)二次风过小当二次风过小时,火焰被压缩,火色发亮,黑影近,尾温偏低,结粒粗细不均,快转率明显下降。
同时升重、fCaO也波动很大。
由于慢车多尾温不稳,破坏了热工制度,容易引起不完全燃烧,烧成带窑皮往后延长,造成大窑结圈。
一、二次风过大或过小,均会引起热工制度的紊乱而影响生产,甚至引起大窑结圈。
当大窑台时产量在26t/h时,一次风量应为16000Nm3/h,二次风量应为38000Nm3/h,才有利于煅烧。
煤:煤质的好坏都会严重地影响产、质量和热工制度的稳定,是促使大窑结圈的重要因素之一。
(1)煤质过好过好的媒质在经济上是一种浪费,对工艺来说却体现不出它的优越性。
由于它的挥发分和固定碳含量均较高,在高温下燃烧激烈,火色发白,高温集中,物料很容易起块发粘而损窑皮,又容易造成放“过头火”而打大慢车,冒黑烟,出黄料,破坏热工制度的稳定,造成大窑结圈。
(2)煤质过差煤质过差时窑内表现出黑火头长,燃烧速度慢,用煤量大而起火慢,容易造成不完全燃烧。
料层厚时常常造成大慢车或周期性慢车,严重地影响产质量和破坏热工制度的稳定,引起大窑结圈。
煤质过好或过差,对正常生产均不利,一般说,A 25~27%,V 28~29%,C 44~45%,HO<3%,对我厂回转2窑的煅烧是比较理想的。
料:为了能使回转窑达到优质、高产、低消耗及长期安全运转的目的,在配料中要下很大的气力,因为一旦配料不当,就会造成原料成分的波动而影响煅烧。
(1)原料成分中的KH过高KH过高,在煅烧时窑内反应出用煤量大,火色亮,不易结粒,升重偏上线,fCaO也偏高。
烧成范围窄,慢车频繁。
升重忽高忽低,热工制度很难稳定,如果所用原料KH高不及时纠正,则很容易导致大窑结圈。
(2)KH过低KH过低时的特点是物料发亮,结粒易粗易粘,升重偏低,fCaO也偏低,但熟料的强度并不高,由于熔媒矿物含量较高,导致液相出现过早,促使窑皮长得过长,也容易导致大窑结圈。
(3)SM过高根据公式SM=SiO2/(Al2O3+Fe2O3),SM过高,则说明熔媒矿物物含量相对少。
在煅烧中表现出火色亮而不易结粒,液相量少,物料翻滚过快,冷却带的物料发黑,似河砂状。
此料由于粘度小,影响CaO和C2S进一步地生成C3S的速度,而造成fCaO偏高。
遇到此情况,看火工往往拉大排风量,提高尾温以弥补预烧的不足,而造成窑皮往后伸延,引起大窑结圈。
(4)SM过低SM过低时,物料发亮不吃火,烧成范围窄,结粒易粗易粘。
这说明熔媒矿物过高,造成熔点低而易长厚窑皮,引起大窑结圈。
(5)IM过高当IM过高时,在煅烧中表现出物料发白,结粒易粗易“推车”,由于物料粘度大反应慢,fCaO不易吸收。
此料液相量多,而且出现过早,容易长厚窑皮导致大窑结圈。
(6)IM过低IM过低则说明KH过高,表现难烧,fCaO含量高,因CaO没有和C2S完全化合成C3S而影响质量。
提高烧成温度则容易损坏窑皮,对稳定热工制度很不利而容易造成大窑结圈。
引起大窑结圈的重要因素是原料成分不稳定。
我厂多年来生产实践说明,熟料中三个率值为:KH 0.915~0.945,SM 1.78~1.80,lM 1.17~1.20;熟料化学成分为:SiO220.5%,CaO 65%;Al2O36.3%,Fe2O35.2%,MgO<0.85%较为理想。
窑速:回转窑能达到优质、高产、低消耗及长期安全运转的目的,窑速起着重要作用。
由于我厂回转窑动力的缺陷,曾一度严重地影响着生产。
下面简单说明窑速对煅烧及结圈的影响。
(1)窑速过快当窑速过快时,窑内料层薄火色红,结粒细小而升重偏高,尾温不易提起。
由于物料翻滚过快,通过高温区的时间短而影响CS的形成,造成fCaO偏高。
遇到料层3偏厚或者垮落厚窑皮时,很难烧起来而引起快转率低,升重不稳,质量偏差,危害各种热工制度的稳定,导致大窑结圈。
(2)窑速过慢每当窑速过慢时,窑内表现出料层厚,火焰短粗发白“黑影”明显,物料结粒粗粉不均。
看火工稍有疏忽,很容易造成“窜料”而大打慢车。
如果慢车时间长或开快车稍迟,物料很容易起块,发粘“推车”。
造成大窑热工制度紊乱,引起结圈。
为了能达到优质、高产、低消耗及长期安全运转的目的,回转窑有合理的热工制度是很重要的。
一般经验认为,当台时产量在26t/h时,窑速应为63转/时(即线速度为791.28m/h)。
操作:水泥企业是否能发挥出最大的经济效益,对于回转窑的厂家来说,看火工素质的高低起着关键性的作用。
因此,要求看火工要不断地学习和总结看火经验,提高操作技术水平,以适应复杂的工艺要求。
下面就防止大窑结圈浅谈一些对看火工操作的技术要求。
(1)加强生产责任心,严格遵守交接班制度和各项操作规程。
(2)做到勤看火、勤操作、勤分析、勤联系、勤检查,确保大窑热工制度的稳定。
(3)在操作中,努力控制火焰顺畅活泼有力。
物料结粒细小均齐,翻滚灵活,黑影远近适中。
(4)不顶火逼烧,预打小慢车克服大变动,防止大窑热工制度的紊乱。
(5)不烧大火,不出次品废品。
升重一般控制在1420~1550g/l,合格率大于93%。
fCaO一般控制在0.40~1.50%,合格率大于65%。
这样有利于稳定热工制度。
(6)努力提高对煤、料变动的应变能力,采取相应的操作方法。
做到煤、料、操作三“对口”。
(7)努力稳定各项热工制度,采用合理的操作方法,使大窑快转率大于95%。
(8)勤活动风煤管,创造掉窑皮的条件。
在操作中,如发现负压升高,要及时减产,人为大幅度地波动尾温,活动风煤管等措施,促使厚窑皮垮落。
(9)每次活动风煤管后,要注意调整其左、右、高、低。
一般情况都稍偏料的右上方,以保持火焰的完整,活泼清亮,燃烧完全。
小结回转窑内结熟料圈问题,许多厂家都认为是棘手的难题。
一些国外资料认为:窑径小,煤灰大,KH、SM越低,越容易引起大窑的结圈。
国内生产实践证明并非完全如此。
有的窑直径大到4米,仍结圈频繁,窑径小到1米却能安全生产。
有些厂家饱和比高到0.93,仍然结圈,而另一些厂饱和比低到0.85,结圈并不严重。
我厂三台相同型号规格的回转窑,也不存在原料、燃料的区别,一号窑结圈频繁,二、三号窑仍能正常生产。
这些现象说明,单用一种因素来解释结圈原因是不全面的,各种因素往往是联系在一起的。
这就需要我们根据生产中的条件,在复杂的过程中找出主要矛盾加以解决。
比如1980年我厂1号窑大修时,在热端又增加了三排耐热钢花环斜挂链条,传热面积由原来的1458m2增加到1620m2。
根据通常经验,传热面积提高后,废气温度可压低10~15¡æ,但是在生产中却给我们带来了许多弊病,台时产量上不去,结圈也频繁了。
以往正常生产时,台时产量可达27t/h,可是当时台时产量只加到25t/h,看火工就觉得窑内表现极不正常,火焰缩短,黑影近而明显,物料结粒粗细不均,周期性慢车难以克服,fCaO、升重均波动很大,同时窑皮也很差。
由于快转率低,出链物料温度高达450~500¡æ。
十一个月之内,竟结圈19次。
这时有人提出两种不同的看法,第一种说法是:出链物料温度高,则说明排风量大,尾温高,造成窑皮伸延而引起结圈;另一种说法是:黑影明显、慢车多、用煤量大,是预烧不足引起热工制度紊乱,而导致结圈。
双方在理论上分析都是有道理的,但却是矛盾的。
一方主张再压低尾温,保持出链物料温度在350~400¡æ。
另一方面则要提高尾温,促使快转率的提高,恢复大窑正常生产。
通过生产实践证明,后一种看法是正确的。
尾温提高10¡æ后,快转率有了明显提高,产质量得到了保证,随之而来的煤耗、料耗都有所下降,大窑趋向于正常生产。