回转窑结圈
回转窑内结圈结球的原因及处理方法

各种类型的水泥回转窑都遇到过结圈问题。
结圈使窑该处的横断面积显著减少,严重影响窑内通风,阻碍物料运动,对回转窑的产量、质量、安全运转、煤耗、电耗均有一定影响。
尤其频繁结圈的回转窑,不仅破坏了窑内正常热工制度,而且损害操作人员的身体健康,给生产造成经济损失。
Eg2jexl 引起回转窑结圈的因素很多,它与原料性质、生料成分、燃料的灰分和细度、窑型、窑内还原气氛及热工制度等有关。
在实际生产过程中,煅烧硅酸率高的熟料时,对减少结圈有好处,但是烧硅酸率很高的白水泥熟料也结圈。
至于说煤灰的影响,但所有烧油的水泥回转窑同样也结圈。
所以结圈问题比较复杂。
现结合生产中的体会和认识,谈谈水泥回转窑结圈的预防和处理。
t%k`)p7O1 结圈的形成 LtKR15h,回转窑内形成结圈的因素很多,但液相的产生和固化是结圈的主要形成过程。
而衬料温度、物料温度、煤灰和生料组成又是决定液相的生成和固化的主要因素。
在熟料煅烧过程中,生料在1200℃左右出现液相,在1250℃左右液相粘度开始变小,液相量增加,由于料层覆盖温度突降,加之筒体表面散热,液相在窑壁上凝固下来,形成窑皮。
窑继续运转,窑皮又暴露在高温中而被熔掉下来,再次被物料覆盖,液相又凝固下来,如此周而复始。
如果粘挂上去的多,掉下来的小,窑皮就增厚,反之就变薄。
在正常情况下,窑皮可保持在200mm左右的厚度。
该温度条件及区域内若熔化和固化的过程达到平衡,窑皮就不会增厚。
当熔化的少固化的多,其厚度增长到一定程度,即形成圈。
当衬料与物料的温差大时,在足够液相的条件下,圈体越结越厚。
ma) + G!1.1 前结圈的形成 Gb"kl .j前结圈(又称窑口圈),是结在回转窑烧成带末端部位的圈。
在正常煅烧条件下,物料温度为1350~1450℃,液相量约为24%,其粘度较大。
当熟料离开烧成带时,液相开始冷却,进入冷却带的液相已基本固化。
在烧成带和冷却带的交界处存在着较大的温差,窑口物料温度高于窑皮温度。
回转窑结圈的原因及处理方法

回转窑结圈的原因及处理方法1、结圈的危害回转窑“结圈”的部位一般在距窑口一定距离的固体燃料集中燃烧点附近的耐火窑衬上,厚度可达200-500 mm左右。
“结圈”对球团生产的危害有以下几方面:(1)降低产量,增加劳动强度窑圈一经形成,对燃料烧烧所产生的热气流势必起阻碍作用,如图-1所示。
热气流被部分阻挡在A区,影响了球团的焙烧效果。
同时,由于链篦机上生球的干燥、预热过程是利用窑尾废气进行的,故此,结圈也对生球的干燥、预热产生不良影响。
具体地说,就是透气性差,火焰不进,后部温度低,干燥时水分不易脱除,生球爆裂、粉化严重,成品率低,从而降低了劳动生产率。
另外,圈结形成后,如不及时处理,就会使圈的纵向长度、厚度增加,当圈掉下时,必然增加工人的劳动强度,有时甚至需停机处理,也影响了球团矿的产量。
(2) 增加了设备负荷如图-1所示,一定面积及厚度的结圈使物料流被阻于B区,此时,被阻的料量要高出正常时许多,加之圈本身的重量,必然增加了托轮、轴承的磨损,同时,增加了电机的负荷,甚至烧毁。
(3) 浪费能源在实际看火操作中,当出现“结圈”现象后,由于热气流被阻于A区,为保证链篦机的干燥和预热效果,看火工往往采用加大给煤量的方式,这无疑造成了能源浪费。
2、结圈的原因结圈的原因,在生产中主要可以归纳为操作不当。
具体地说,是由于上料量过大,干燥效果差,生球爆裂,粉化严重,致使透气性差,使得引风机抽动火焰的作用不明显,火焰只在窑内一定距离燃烧。
在大于1 200℃的高温下,未完全氧化的Fe3O4就与磁铁矿中一定数量的SiO2发生反应形成液相。
2Fe3O4+3SiO2+2CO=3Fe2SiO4+2CO22FeO+SiO2=Fe2SiO4另外,当给煤量较大时,在1 150℃条件下,Fe2O3也会部分分解为Fe3O4,与SiO2作用而生成2FeO·SiO2,形成渣相粘结。
这就使得物料在流经焙烧带时,所产生的液相、渣相极易粘附在窑衬的表面,同时粘结物料而产生结圈现象。
回转窑结圈的影响因素及解决措施

回转窑结圈的影响因素及解决措施-----龙仕连我司从11月23日开始窑内断断续续出现少量漏料,并出现了三次大料球,严重影响到窑的正常运转,公司及部门领导高度重视。
经分析是窑23米处结后圈导致窑尾漏料和结料球。
于25日开始处理后圈:1、窑减产到350 t/h煅烧;2、窑头煤管每个班移动两次,-200~+100冷热交替处理;3、每班清理煤管头部积料结焦4次,以保证头煤燃烧好,火焰集中;4、控制煤粉细度及水分,以保证煤粉燃烧效果(煤磨出磨温度控制在63~65度,入磨温度<300度。
内部控制煤粉细度<6.0);5、适当提高熟料KH。
通过3天的处理,23料处后圈薄了很多,并有缺口,于28日窑恢复了365 t/h正常生产。
出现这样的工艺事故,我们必须深度反思。
特别是工艺管理人员和窑操作员一定要密切关注窑皮的变化趋势及原燃材料的变化,及时调整窑参数,保证窑正常运转。
下面让我们再次学习一下窑内结圈的成因、危害及解决措施:结圈是指回转窑在正常生产中,由于原燃材料的变化,或者操作和热工制度的影响,窑内因物料过度粘结,在特定的区域形成一道阻碍物料运动的环形、坚硬的圈。
这种现象在回转窑内是一种不正常的窑况,它破坏了正常的热工制度,影响窑内通风,造成窑内来料波动很大,直接影响到回转窑的产量、质量、消耗和长期安全运转。
而且处理窑内结圈费时费力,严重时需停窑停产,危害极其严重。
结圈的成因及危害:结圈的形成: 结圈实际上是在烧成带末端与放热反应带交界处形成的窑皮,是回转窑内危害最大的结圈。
在熟料煅烧过程中,当物料温度达到1280℃时,其液相黏度较大,最容易形成结圈,而且冷却后比较坚固,不易除掉。
在正常的煅烧情况下,后结圈体的内径部分往往被烧熔而掉落,保持正常的圈体内径。
如果在1 250~l 280℃温度范围内出现的液相量偏多,往往会形成妨碍生产的后结圈。
后结圈一般结在烧成带的边界或更远,开始是烧成带后边的窑皮逐渐增长、增厚,发展到一定程度即形成后结圈。
球团回转窑结圈诊断

球团回转窑结圈诊断1. 什么是球团回转窑结圈?球团回转窑是一种常用的矿石烧结设备,用于将粉末状物料(如铁矿石、焦炭等)在高温下进行结圈反应,制成球团。
然而,在使用过程中,由于各种因素的影响,常常会出现球团回转窑结圈问题。
球团回转窑结圈指的是物料在回转窑内部形成不可解开的块状物质,导致生产过程中停机维修、产量下降以及能源浪费等问题。
因此,对球团回转窑结圈进行诊断和解决具有重要意义。
2. 球团回转窑结圈诊断方法2.1 观察法通过观察球团回转窑内部情况,如物料流动状态、温度分布、气体排放等,可以初步判断是否存在结圈问题。
例如,如果发现物料流动不畅或者有大块物料积聚在某些区域,则可能存在结圈现象。
2.2 温度测量法利用红外测温仪等设备对回转窑内部进行温度测量,可以发现温度异常区域。
结圈通常会导致某些区域温度升高,或者出现局部温度过低的情况。
2.3 物料取样分析法通过在回转窑停机后,取出物料样品进行化学成分和物理性质的分析,可以确定结圈原因。
例如,如果发现物料中含有大量易熔成分或者粘结剂,则可能是由于成分不合理导致结圈。
2.4 球团形态观察法观察球团形态可以判断结圈程度和原因。
例如,如果球团形状不规则、表面粗糙,则可能是由于结圈导致球团形成不完整。
3. 球团回转窑结圈诊断结果分析根据以上诊断方法得到的结果,对球团回转窑结圈问题进行分析。
3.1 结圈原因分析根据物料取样分析结果,确定了结圈原因为成分不合理。
进一步观察球团形态,并参考温度测量结果,发现高温区域处的球团形状不规则、表面粗糙。
结合观察法得到的物料流动不畅的情况,可以推断结圈是由于粘结剂含量过高导致的。
3.2 结圈解决方案针对结圈原因,制定相应的解决方案。
首先,需要调整粘结剂配比,控制粘结剂含量在合理范围内。
其次,通过改变进料速度和角度等操作参数,改善物料流动性。
此外,还可以考虑增加通风设备、调整燃烧器位置等措施,以提高温度分布均匀性。
4. 结论球团回转窑结圈是生产过程中常见的问题,通过综合运用观察法、温度测量法、物料取样分析法和球团形态观察法等诊断方法,可以准确判断结圈原因,并制定相应解决方案。
回转窑结圈处理机

回转窑结圈处理机回转窑结圈处理机是一种用于处理回转窑结圈的设备,它在水泥生产过程中起到了重要的作用。
本文将从不同角度来描述回转窑结圈处理机,并探讨其在水泥生产中的作用。
一、回转窑结圈处理机的工作原理回转窑结圈处理机通过一系列的工作步骤来处理回转窑产生的结圈问题。
首先,它利用高温燃烧的方式将结圈烧解,并将其转化为可再利用的物料。
然后,通过机械装置将烧解后的物料输送到后续的处理工艺中,进一步进行处理和利用。
回转窑结圈处理机的工作原理简单而高效,能够有效解决回转窑结圈问题,提高水泥生产的效率。
1. 高效节能:回转窑结圈处理机能够将结圈物料烧解并转化为可再利用的物料,减少能源消耗和原材料浪费,实现节能环保的目标。
2. 自动化程度高:回转窑结圈处理机采用自动化控制系统,能够实现自动化操作和监控,减少人工干预,提高生产效率。
3. 适应性强:回转窑结圈处理机能够适应不同规模和工艺要求的水泥生产线,具有较强的适应性和灵活性。
4. 减少环境污染:回转窑结圈处理机能够有效减少水泥生产过程中的废气和废水排放,降低环境污染的程度。
三、回转窑结圈处理机的应用案例回转窑结圈处理机在水泥生产中得到了广泛的应用。
以某水泥厂为例,该厂引进了先进的回转窑结圈处理机,通过对回转窑结圈进行烧解和处理,成功解决了结圈问题,提高了水泥生产的效率和质量。
同时,该厂还充分利用回转窑结圈处理机产生的再利用物料,实现了资源的循环利用,进一步降低了生产成本和环境污染。
四、结语回转窑结圈处理机在水泥生产中发挥了重要的作用,通过高效烧解和处理回转窑结圈,实现了资源的循环利用和环境保护。
随着水泥产业的发展和技术的进步,回转窑结圈处理机将在未来得到更广泛的应用,并为水泥生产带来更大的效益和贡献。
煤基还原回转窑结圈
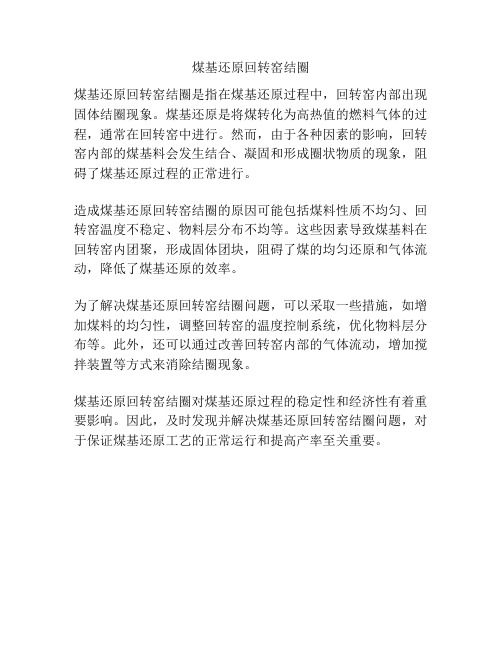
煤基还原回转窑结圈
煤基还原回转窑结圈是指在煤基还原过程中,回转窑内部出现固体结圈现象。
煤基还原是将煤转化为高热值的燃料气体的过程,通常在回转窑中进行。
然而,由于各种因素的影响,回转窑内部的煤基料会发生结合、凝固和形成圈状物质的现象,阻碍了煤基还原过程的正常进行。
造成煤基还原回转窑结圈的原因可能包括煤料性质不均匀、回转窑温度不稳定、物料层分布不均等。
这些因素导致煤基料在回转窑内团聚,形成固体团块,阻碍了煤的均匀还原和气体流动,降低了煤基还原的效率。
为了解决煤基还原回转窑结圈问题,可以采取一些措施,如增加煤料的均匀性,调整回转窑的温度控制系统,优化物料层分布等。
此外,还可以通过改善回转窑内部的气体流动,增加搅拌装置等方式来消除结圈现象。
煤基还原回转窑结圈对煤基还原过程的稳定性和经济性有着重要影响。
因此,及时发现并解决煤基还原回转窑结圈问题,对于保证煤基还原工艺的正常运行和提高产率至关重要。
回转窑窑后结圈原因分析及处理方法

回转窑窑后结圈原因分析及处理方法巩义市恒昌冶金建材设备厂生产的1000t/d熟料生产线是由天津水泥工业设计研究院有限公司设计的,主要包括TDF型分解炉、单系列五级旋风预热器、Φ3.2m×50m回转窑及TC-836篦式冷却机。
自2007年2月以来,窑后频繁发生结圈、结球的工艺事故,巩义市恒昌冶金建材设备厂技术人员现将原因分析及解决措施介绍如下,供同仁参考。
1、结圈情况2007年3月19日最为严重,窑前返火,窑尾有漏料现象,无法操作煅烧,迫使停窑处理。
从窑内看,主窑皮长达22m,副窑皮长到窑尾,35~37m处形成后结圈,结圈最小孔洞呈不规则状,直径约l.5m,进窑观察该圈明显分为两层,且层次明确、清晰,第一层厚约150mm,呈黄白色,第二层厚约460mm,呈黑色,圈体非常致密。
对圈体取样分析见表1。
表1 圈体取样分析结果从表l可以看出,第一层硫碱含量较高,是硫碱圈,第二层明显是煤粉圈,熟料液相出现过早、过多导致结圈。
2、原因分析(1)由于2006年煤价不断上涨,加之公路运输距离远,为了降低成本,采用当地劣质煤煅烧,煤质下降,灰分高,挥发分低,发热值低,煤工业分析如表2、3。
实际生产中,煤可燃性差,煤粉燃烧不完全,大量煤灰不均掺入生料中,液相在窑后面提前出现,而未燃尽的煤灰产生沉积及液相的提前出现结圈。
(2)2007年以来,由于机械原因,高温风机l号轴与密封圈强烈摩擦,产生局部高温,使轴侧曲,水平振动最高达6.4mm/s。
为了降低振动,不得不降低高温风机转速,由原来的1130r/min降至l060r/min,有时更低,严重影响了窑内通风,加上煤质又差,更多的窑头燃烧不完全的煤粉沉积在窑后燃烧,使窑内后部温度升高,液相量增加,加速了窑后结圈的形成。
(3)为了处理窑后结圈,我厂在迫不得已的情况下停窑烧后圈,由于煤质差,二、三次风温低,燃料不完全或未燃烧的煤粉落在圈上及圈后的积料上,不断燃烧,造成物料发粘,不但圈未烧掉,反而越结越厚,这也是第一层圈形成的主要原因。
回转窑结圈的原因及处理方法
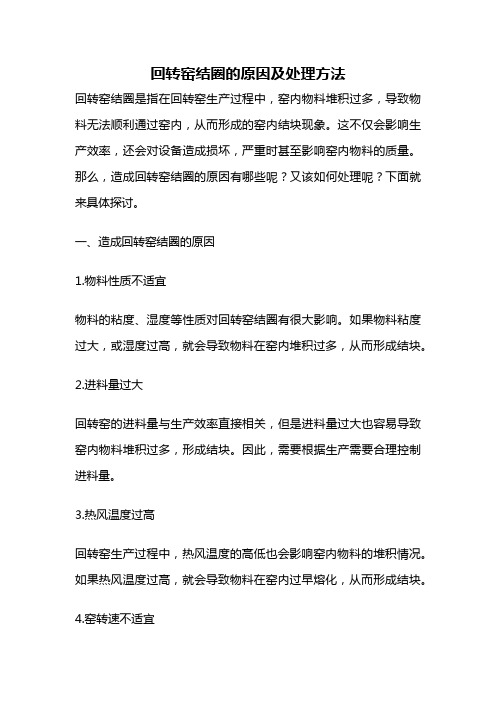
回转窑结圈的原因及处理方法回转窑结圈是指在回转窑生产过程中,窑内物料堆积过多,导致物料无法顺利通过窑内,从而形成的窑内结块现象。
这不仅会影响生产效率,还会对设备造成损坏,严重时甚至影响窑内物料的质量。
那么,造成回转窑结圈的原因有哪些呢?又该如何处理呢?下面就来具体探讨。
一、造成回转窑结圈的原因1.物料性质不适宜物料的粘度、湿度等性质对回转窑结圈有很大影响。
如果物料粘度过大,或湿度过高,就会导致物料在窑内堆积过多,从而形成结块。
2.进料量过大回转窑的进料量与生产效率直接相关,但是进料量过大也容易导致窑内物料堆积过多,形成结块。
因此,需要根据生产需要合理控制进料量。
3.热风温度过高回转窑生产过程中,热风温度的高低也会影响窑内物料的堆积情况。
如果热风温度过高,就会导致物料在窑内过早熔化,从而形成结块。
4.窑转速不适宜回转窑的转速也会影响窑内物料的堆积情况。
如果转速过快,就会导致物料在窑内无法均匀分布,从而形成结块。
二、回转窑结圈的处理方法1.减少进料量当回转窑结圈发生时,可以适当减少进料量,以缓解窑内物料堆积过多的情况。
2.调整热风温度如果回转窑结圈是由于热风温度过高导致的,可以适当降低热风温度,以减少窑内物料的过早熔化。
3.调整窑转速如果回转窑结圈是由于窑转速不适宜导致的,可以适当调整窑转速,以保证物料在窑内均匀分布。
4.清理窑内物料当回转窑结圈严重时,需要停窑清理窑内物料。
清理时需要注意安全,避免对设备造成损坏。
5.加入流化剂在窑内加入一定量的流化剂,可以有效地缓解回转窑结圈现象。
流化剂可以使物料在窑内均匀分布,减少结块的情况。
6.调整物料配比如果回转窑结圈是由于物料配比不合理导致的,可以适当调整物料配比,以保证物料在窑内均匀分布,减少结块的情况。
回转窑结圈是一种常见的生产问题,多种因素都可能导致其发生。
因此,在回转窑生产过程中,需要做好预防措施,保证物料在窑内均匀分布,避免结块的发生。
同时,一旦发生回转窑结圈,需要及时采取相应的处理措施,以保证生产效率和产品质量。
回转窑结圈的原因及处理方法

回转窑结圈的原因及处理方法回转窑是制造水泥的重要设备,而回转窑结圈是影响生产效率和质量的常见问题。
结圈的原因有很多,如窑内温度不均、烧成温度过低、原材料成分不合适等。
本文将从原因和处理方法两个方面详细介绍回转窑结圈问题。
一、结圈的原因1. 窑内温度不均:回转窑内部温度分布不均会导致部分区域的烧成程度不够,形成未熟料,容易粘在窑壁上,最终导致结圈。
2. 烧成温度过低:如果烧成温度过低,则无法将原材料完全反应,也容易导致未熟料粘附在窑壁上。
3. 原材料成分不合适:原材料中含有过多的游离SiO2、Al2O3等物质,会使得反应速率变慢,在高温下难以完全反应。
同时,如果含有过多的碱金属氧化物,则会使得产生大量液态相,增加了结圈的风险。
4. 进出料方式不当:进出料口位置设置不合理,或者进出料速度过快或过慢,都会导致窑内物料分布不均,从而增加结圈的风险。
二、处理方法1. 调整窑内温度:调整窑内温度是解决结圈问题的关键。
可以通过改变燃烧器位置、调整燃料供给量等方式来调整窑内温度分布,使得各个区域的温度均匀。
2. 提高烧成温度:提高烧成温度可以促进原材料反应,减少未熟料生成的可能性。
但是需要注意控制好温度,避免超出窑的承载能力。
3. 调整原材料成分:在生产过程中要严格控制原材料的成分,避免含有过多的游离SiO2、Al2O3等物质和碱金属氧化物。
如果发现原材料成分不合适,则需要及时停机清理,并重新投入符合要求的原材料。
4. 改善进出料方式:调整进出料口位置和速度可以改善窑内物料分布不均的问题。
可以采用多点进出料口、减缓进出料速度等方式来改善这一问题。
5. 定期清理窑壁:定期清理窑壁可以有效减少未熟料的积累,降低结圈的风险。
清理时需要注意安全,避免对设备造成损伤。
综上所述,回转窑结圈是影响水泥生产效率和质量的常见问题。
通过调整窑内温度、提高烧成温度、调整原材料成分、改善进出料方式和定期清理窑壁等方式可以有效解决这一问题。
回转窑结圈的影响

什么是结圈
• 结圈是指回转窑在正常生产中,由于原燃材料 的变化,或者操作和热工制度的影响,窑内因物料过 度粘结,在特定的区域形成一道阻碍物料运动的环 形、坚硬的圈。这种现象在回转窑内是一种不正常 的窑况,它破坏了正常的热工制度,影响窑内通风, 造成窑内来料波动很大,直接影响到回转窑的产量、 质量、消耗和长期安全运转。而且处理窑内结圈费 时费力,严重时需停窑停产,危害极其严重。
结圈的处理方法
无论是前结圈还是后结圈,处理 结圈时一般采用冷热交替法,尽量加 大其温差,使圈体受温度变化而垮落。
前结圈的处理方法
前结圈不高时,对煅烧操作的影响不大,尚 可增加烧成带料层厚度,延长物料在烧成带 的停留时间,使物料反应更完全并降低熟料 中的CaO含量,同时减少烧成带向窑前的辐 射散热。但当前结圈较高时,既影响看火操 作,又影响窑内通风及火焰形状,大块熟料 滚不出来,易损坏烧成带窑皮及衬料。这 时应及时调整风、煤或移动喷煤管进行处理。
后结圈的处理办法
从总体来讲,烧后圈不是一件容易的事, 有时圈体很牢固,若烧圈时间过长,容易 烧坏窑皮及衬料,或在过渡带结长厚窑皮 进而在圈体后产生第2道圈。所以,处理时 一定要小心。一定要在保护窑皮的前提下 进行,前后兼顾,精心操作,勿使火焰过 分集中,避免将窑皮及衬料烧坏,造成更 大的损失。
后结圈的处理办法
在处理后结圈时,要根据圈体的特点和远近,分 别采取不同的处理方法,才能达到较好的效果。 一般采用冷热交替法处理,烧远圈时以冷为主, 烧近圈时以热为主。 (1)当窑内窑皮长而厚或有轻度圈根时,将喷煤管 向外拉出,使烧成带位置前移,降低圈体的温 度,改变煤灰沉落位置,使厚长的窑皮逐渐垮 落。同时调整风煤配合,加速煤粉燃烧,使高 温带两端低温部分不拖长,防止圈根继续成长。
中南大学-回转窑结圈物的形成机理

Element Weight/ %
Fe 14.07
Al 12.74
Si 30.12
Ca 37.99
Mg 1.77
Ti 3.22
Element Weight/ %
Fe 50.59
Al 1.02
Si 20.50
Ca 24.67
Mg 3.21
图15 硅灰石能谱分析
图16 多组分化合物能谱分析
硅灰石中以CaO、SiO2为主,同时含有部分Al2O3、FeO、MgO、 TiO2等。这些杂质的存在进一步降低了硅灰石的熔点。
(2)粉尘的物料粘附 微细粒的铁精矿和煤灰,表面能大,附在窑壁上。 粘附细粒,承受机械力作用下,发生机械沉积而粘附 在窑壁上,当粘附强度不够时,会自动脱落或被擦落,并 反复进行粘附和脱落。
4 回转窑中部结圈物矿相分析及机理
4.1 回转窑中部结圈物矿相分析
Fe
多 CS FeO
图5 中部结圈物断面照片 图6 中部结圈物显 微结构(反光,50×)
10.03 0.054 8.87 0.043
表2 结圈物矿物组成/%
部位 后部结圈物 中部结圈物 前部结圈物 MFe 2.50 36.50 41.00 FeO 32.50 28.10 33.10 Fe3O4 40.20 3.20 ― 钙铁橄榄石 ― 16.40 15.60 多成分化合物 23.8 15.80 10.30
Element Fe
Weight/% 100.00
Element Weight/%
Si 18.05
Fe 52.89
Al 0.08
Mg 2.73
Ca 20.25
图3 Fe3O4或FeO相能谱分析
图4 多成分化合物能谱分析
氧化锌回转窑结圈原因

氧化锌回转窑结圈原因
氧化锌回转窑结圈是指在氧化锌生产过程中,回转窑内部出现了石灰石或其他物质的结块现象。
这种现象可能会导致生产效率下降、产品质量下降等问题。
氧化锌回转窑结圈的原因主要有以下几个方面: 1. 原料成分不均匀:如果原料中含有过多的石灰石或其他物质,就会导致回转窑内部结圈。
2. 操作不当:回转窑操作时如果不当,例如进料速度过快或过慢、回转速度不均匀等,都可能导致结圈。
3. 窑内温度过低:回转窑内部温度过低也会导致结圈现象。
因此,在生产过程中需要保持合适的温度。
4. 窑内积存物质:如果回转窑内部有积存的物质,也会导致结
圈现象。
因此,在生产过程中需要及时清理。
为了避免氧化锌回转窑结圈现象的出现,需要在生产过程中严格执行操作规范,控制原料成分,保持合适的温度,并及时清理回转窑内部。
- 1 -。
回转窑结圈的原因及处理方法

水泥回转窑结圈的形成机理与处理方法水泥回转窑结圈的形成机理与处理方法 ______________________________________ 1一、窑皮是如何形成 ____________________________________________________________________________ 1二、结圈的机理与成因__________________________________________________________________________ 2三、圈的种类____________________________________________________________________________________ 3四、避免结圈的方式和方法_____________________________________________________________________ 3五、窑皮窑圈的几个根本性问题 ________________________________________________________________ 4六、处理结圈的方式 ____________________________________________________________________________ 5水泥回转窑结圈的形成机理与处理方法不管现今悬浮预热窑外分解窑多么先进,出现非正常窑况——结圈,也是煅烧中的正常现象。
虽然经过多年水泥人努力及水泥专家的研究,对出现不正常窑况的问题基本上能够解决,并且已经形成了完整的理论。
但话又说回来一旦出现不正常现象,运用理论解决问题的时候,问题又不能很好的解决,这也是事实。
我们不能否认理论,但是也不能完全把希望寄托于原有的理论中,这就是矛盾的两面性。
如何才能够快速及时的解决问题其实是我们关注的主要问题,所以本文主要是从几个主要方面来探讨结圈的机理和处理结圈的措施,以及时帮助读者解决所面临的不正常窑况。
回转窑窑后结圈的原因和处理结果

回转窑窑后结圈的原因和处理结果一、回转窑窑后结圈的原因回转窑是一种常用于石灰生产和水泥生产的设备,但在使用过程中,有时会出现窑后结圈的情况。
结圈是指窑内物料在烧结过程中出现结块现象,导致窑内热量传递不畅,影响生产效率和产品质量。
而窑后结圈的原因主要有以下几个方面:1.原料成分不稳定:回转窑生产过程中,原料成分的不稳定性是导致结圈的主要原因之一。
原料成分中的各种氧化物、硅酸盐和铝酸盐等物质,对烧结过程中的矿物相转化和结构稳定性起着重要作用。
如果原料成分的变化超出了窑内控制范围,就容易引起结圈。
2.燃烧条件不理想:回转窑的燃烧条件对结圈问题也有一定影响。
燃料的选择、供氧方式、燃烧温度等因素都会影响窑内气氛的稳定性和热量分布情况。
如果燃烧条件不理想,窑内温度分布不均匀,就容易导致结圈的发生。
3.窑内温度过高:窑内温度是影响回转窑结圈的重要因素之一。
当窑内温度过高时,原料中的一些物质会发生过度烧结,形成块状物质,从而导致结圈。
窑内温度过高可能是由于燃烧条件不理想、窑内热量分布不均匀等原因引起的。
4.窑内物料层厚度不均匀:窑内物料层厚度的不均匀也容易导致结圈。
如果窑内物料层厚度不均匀,热量传递不均匀,就会导致部分物料温度过高,发生结圈。
二、回转窑窑后结圈的处理结果针对回转窑窑后结圈的问题,可以采取一系列措施进行处理,以保证生产的正常进行和产品质量的稳定。
1.优化原料配比和成分控制:通过对原料配比和成分的优化,可以减少原料成分的波动范围,降低结圈的发生概率。
同时,加强对原料成分的在线监测和调控,及时发现和处理原料成分异常,以避免结圈的发生。
2.改进窑内燃烧条件:优化燃料选择、供氧方式和燃烧温度等因素,改善窑内燃烧条件,提高窑内气氛的稳定性和热量分布的均匀性。
通过调整燃烧条件,可以有效预防和减少结圈的发生。
3.控制窑内温度:合理控制窑内温度,避免温度过高或过低,对窑内物料进行适当的保护和调控。
通过优化燃烧条件、改善窑内热量分布等措施,可以有效降低窑内温度的波动,减少结圈的发生。
回转窑结圈种类及其处理
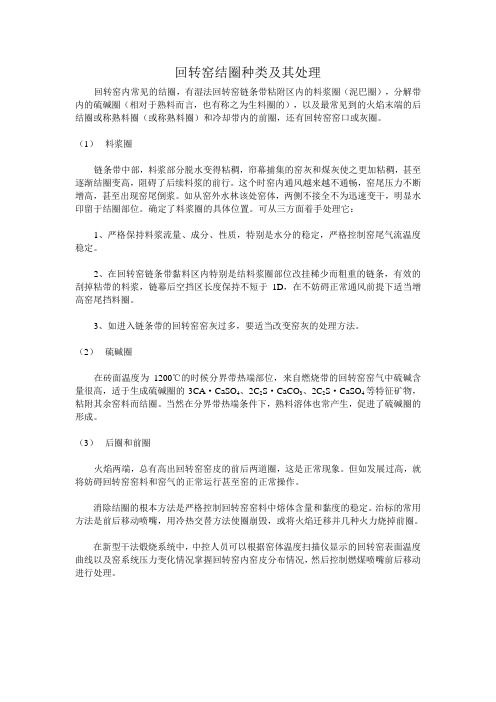
回转窑结圈种类及其处理回转窑内常见的结圈,有湿法回转窑链条带粘附区内的料浆圈(泥巴圈),分解带内的硫碱圈(相对于熟料而言,也有称之为生料圈的),以及最常见到的火焰末端的后结圈或称熟料圈(或称熟料圈)和冷却带内的前圈,还有回转窑窑口或灰圈。
(1)料浆圈链条带中部,料浆部分脱水变得粘稠,帘幕捕集的窑灰和煤灰使之更加粘稠,甚至逐渐结圈变高,阻碍了后续料浆的前行。
这个时窑内通风越来越不通畅,窑尾压力不断增高,甚至出现窑尾倒浆。
如从窑外水林该处窑体,两侧不接全不为迅速变干,明显水印留于结圈部位。
确定了料浆圈的具体位置。
可从三方面着手处理它:1、严格保持料浆流量、成分、性质,特别是水分的稳定,严格控制窑尾气流温度稳定。
2、在回转窑链条带黏料区内特别是结料浆圈部位改挂稀少而粗重的链条,有效的刮掉粘带的料浆,链幕后空挡区长度保持不短于1D,在不妨碍正常通风前提下适当增高窑尾挡料圈。
3、如进入链条带的回转窑窑灰过多,要适当改变窑灰的处理方法。
(2)硫碱圈在砖面温度为1200℃的时候分界带热端部位,来自燃烧带的回转窑窑气中硫碱含量很高,适于生成硫碱圈的3CA·CaSO4、2C2S·CaCO3、2C2S·CaSO4等特征矿物,粘附其余窑料而结圈。
当然在分界带热端条件下,熟料溶体也常产生,促进了硫碱圈的形成。
(3)后圈和前圈火焰两端,总有高出回转窑窑皮的前后两道圈,这是正常现象。
但如发展过高,就将妨碍回转窑窑料和窑气的正常运行甚至窑的正常操作。
消除结圈的根本方法是严格控制回转窑窑料中熔体含量和黏度的稳定。
治标的常用方法是前后移动喷嘴,用冷热交替方法使圈崩毁,或将火焰迁移并几种火力烧掉前圈。
在新型干法煅烧系统中,中控人员可以根据窑体温度扫描仪显示的回转窑表面温度曲线以及窑系统压力变化情况掌握回转窑内窑皮分布情况,然后控制燃煤喷嘴前后移动进行处理。
回转窑结圈原理

回转窑结圈原理
嘿,朋友们!今天咱就来好好聊聊回转窑结圈原理。
你们知道吗,回转窑就像是一个大胃王,不停地“吃”进各种原料,然后进行加工。
那结圈呢,就好像是这个大胃王闹肚子了!比如说哈,就像我们吃坏了东西会不舒服一样。
回转窑在工作的时候,温度那是相当高啊!高温会让物料产生一系列奇妙的变化。
就好比是魔法在施展,物料在窑内翻滚、融合。
但是呢,如果有些物料在某些地方聚集得太多了,哎呀,那麻烦可就来了!这不就像路上堵车了嘛,一下子就不顺畅了。
咱再举个例子,你想想,要是一条公路上有一堆石头堆在那儿,车还能顺利通过吗?这回转窑里的物料也是这样啊,聚在一起慢慢就形成了结圈。
“哎呀,那咋办呀?”别急呀,咱有办法!我们得时刻关注着回转窑的运转情况,就像我们照顾一个生病的小伙伴一样。
一旦发现有结圈的迹象,就赶紧采取措施。
你说这回转窑结圈是不是很让人头疼啊?但只要我们了解它的原理,找到应对的办法,也不用太害怕。
所以呀,我们得深入研究它,和它斗智斗勇,
可不能让它随便就“生病”了呀!总之,回转窑结圈原理虽然有点复杂,但只要我们用心去理解,就一定能搞定它!。
回转窑结圈的原因及处理方法

回转窑结圈的原因及处理方法回转窑是一种常用于水泥生产过程中的设备,它通过高温和旋转运动将原料进行煅烧,以产生水泥熟料。
然而,有时候在回转窑的运行过程中,会出现结圈现象,这会严重影响设备的正常运行和水泥生产的质量。
了解回转窑结圈的原因及处理方法是至关重要的。
一、回转窑结圈的原因1. 原料成分不理想:回转窑的结圈问题与原料中的成分有很大的关系。
如果原料的化学成分不理想,其中含有过多的硫酸钠、硫酸镁等物质,将会导致煅烧过程中产生黏性物质,从而引起结圈。
2. 烧成温度过低:回转窑烧成温度过低也是导致结圈的一个重要原因。
当烧成温度过低时,原料中的化学反应无法完全进行,会导致部分物质残留在窑内,形成结圈。
3. 运行时间过长:长时间的运行也是回转窑结圈的一个重要原因之一。
当回转窑的运行时间超过其设计要求时,窑内结构会变得粘性,给结圈问题的发生提供了条件。
二、回转窑结圈的处理方法1. 优化原料配比:通过调整原料的化学成分,合理设计原料的配比,可以减少结圈问题的发生。
降低硫酸钠和硫酸镁等物质的含量,增加硅酸盐等成分,从而降低结圈的风险。
2. 提高烧成温度:增加回转窑的烧成温度可以有效地解决结圈问题。
适当提高温度可以加速化学反应的进行,降低黏性物质的生成,从而减少结圈发生的可能性。
3. 控制运行时间:合理控制回转窑的运行时间,确保在规定的运行时间内对窑内进行清理和维护。
定期对窑内进行清扫,清除可能产生结圈的物质,可以预防结圈问题的发生。
4. 使用防结圈剂:可以考虑在回转窑的煅烧过程中添加一定量的防结圈剂。
这些防结圈剂可以改变物料表面的化学性质,降低物料的粘性,减少结圈的风险。
5. 加强设备维护:定期对回转窑进行维护保养,保持设备的正常运行状态。
清理窑内的积存物,检查窑体和内衬的磨损情况,修复和更换损坏的部件,可以有效地预防结圈问题的发生。
总结与回顾:回转窑结圈问题是水泥生产过程中的常见现象,它会严重影响生产效率和产品质量。
回转窑结圈原因分析

回转窑结圈原因分析
经过我国12年来的大型链篦机—回转窑工艺生产实践,大体上讲,引起回转窑结圈的原因主要有四方面:①回转窑内粉状物太多(回转窑中的粉末一部分是从链篦机中随球团一起带入,一部分是由于球团在回转窑中受到摩擦剥落而产生的,还有一部分为煤燃烧的残留物);②回转窑气氛控制不好;③回转窑温度控制不当;④原料中SiO2含量高(当窑内温度上升到1200℃左右时,低熔点物软化,窑内粉末在窑壁上固相扩散粘附和液相粘附不断积累形成)。
就这几方面而言,似乎回转窑结圈的原因很简单,而实际上造成球团结圈的因素是多种多样的,这些因素及其相互关系如图示。
因此,根据回转窑结圈的各种因素分析,在即将生产的链篦机—回转窑工艺中提前做好各项预防措施,以降低回转窑结圈对生产的影响。
- 1、下载文档前请自行甄别文档内容的完整性,平台不提供额外的编辑、内容补充、找答案等附加服务。
- 2、"仅部分预览"的文档,不可在线预览部分如存在完整性等问题,可反馈申请退款(可完整预览的文档不适用该条件!)。
- 3、如文档侵犯您的权益,请联系客服反馈,我们会尽快为您处理(人工客服工作时间:9:00-18:30)。
回转窑结圈
1、安全因素:
所有的设备安全防护装置完好。
确保巡检通道畅通、干净。
保证所有区域有足够的照明。
所有人员必须正确配戴PPE。
各个观察孔门关闭,各处无热气、灰尘冒出。
压缩空气无泄漏。
窑尾出现漏料时及时调整,制止漏料,并设置警戒线等明显标志,以防高温物料烫伤
2、环境因素:
需考虑以下环境因素:
1. 严格执行国家相关的环保政策和法律法规。
2. 当发现有灰尘泄漏时,需及时汇报。
3. 按照要求,定期的监控和记录所有排气点的排气情况。
4. 除去外部可能产生灰尘的料堆。
5. 若发现润滑油、液压油、水火干物料有任何泄漏或漏料的话,需要及时汇报。
3、资源
可供参考的文件:
回转窑中控操作说明书。
功能分析。
4、窑结圈形成判断
4.1筒体扫描仪观察,结圈处筒体温度降低至150℃以下
4.2窑内通风变差,烟室氧含量下降4%以下
4.3系统阻力增加,烟室负压升高至-500以下
4.4窑负荷增大到1000A左右,窑负荷平均值高和波动幅度较大,波动幅度达200A—300A
4.5窑尾烟室密封处漏料
4.6窑内出料变少或来料不均匀
5、窑结圈原因分析
5.1窑口圈
5.1.1煤粉细度变粗
5.1.2二次风温异常波动
5.1.3火焰不顺畅
5.2烧成带尾部结圈
5.2.1烧成带起点波动,料的成分变化,分解率波动
5.2.2筒体冷却风机使用不当
5.2.3火焰不顺畅
5.3硫碱圈
5.3.1煤粉中的S含量高,
5.3.2窑内还原气氛,有害成份内循环富集
5.3.3入窑生料成分波动,导致热工制度的不稳定
5.3.4烧成带温度过高
5.3.5火焰不顺畅
6、窑结圈的处理
6.1窑口圈的处理
6.1.1调整火焰,煤管退至零位
6.1.2确保煤粉细度合格率达到90%以上
6.2烧成带尾部结圈
6.2.1稳定入窑分解率,稳定篦冷机运转、窑头罩压力和燃料加入量,以便稳定火焰
6.2.2稳定生料率值,将入窑生料的硅率提高0.1,控制熟料的液相量
6.2.3减少三次风门的开度并增加引风量,控制烟室的氧含量不低于4.0% 6.2.4如结圈继续恶化不能控制,则停窑打圈,执行该SOP操作程序
6.3硫碱圈的处理
6.3.1稳定煤的成份,降低煤粉中的S含量。
6.3.2稳定煅烧,保证煤粉完全燃烧,禁止出现CO。
6.3.3优化生料率值,适当提高硅率0.1,控制熟料的液相量
6.3.4减少三次风门的开度并增加引风量,控制烟室的氧含量不低于4.0% 6.3.5改善入窑生料的易烧性,控制生料的细度,降低煅烧温度
6.3.6如果高温风机已达到极限,烟室的氧含量仍低于4.0%,适当减料保证窑内通风
6.3.5如结圈继续恶化不能控制,,则停窑打圈,执行该SOP操作程序。