2011.05.17滚镀-04 PFMEA(除氢)
PFMEA(汽车产品塑胶件分析案例)
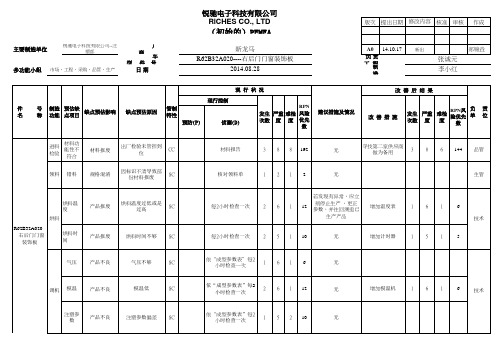
材料报废
出厂检验未管控到 位
CC
领料 错料
规格混淆
因标识不清导致部 份材料报废
SC
材料报告
3 8 8 192
核对领料单
1 21 2
无
寻找第二家供应商 做为备用
3
8
6 144
品管
无
生管
烘料温 度
烘料
R62B32A020---右后门门窗
装饰板
烘料时 间
产品报废
烘料温度过低或是 过高
SC
产品报废
烘料时间不够 SC
主要制造单位
锐驰电子科技有限公司--注 塑部
多功能小组 市场、工程、采购、品管、生产
厂 商车 型 件号 日期
锐驰电子科技有限公司 RiCHES CO., LTD
(初始的)PFMEA
新龙马 R62B32A020----右后门门窗装饰板
2014.08.28
版次 提出日期 修改内容 核准 审核 作成
A0 14.10.17 新出
发生
严重
难检
RPN风 险优先
负 单
责 位
次数 度 度 数
尺寸
报废
1.注塑工艺参数 (模温、压力、射 速)调试不当。
3
8
2
48
由专门人员进行调 试,必要时进行培训 。
由专职技术员调试 并记录到成型参数 表,首未件对比测
量
2
8
1
16
2.读数错误
SC
首未件检 测
依“成型参数表” 每2小时检查一次
2 8 5 80
3 7 4 84 由专门人员负责保养 第一个岗位人员需 2
7
3
42
要对每个产品外观
电镀的FMEA
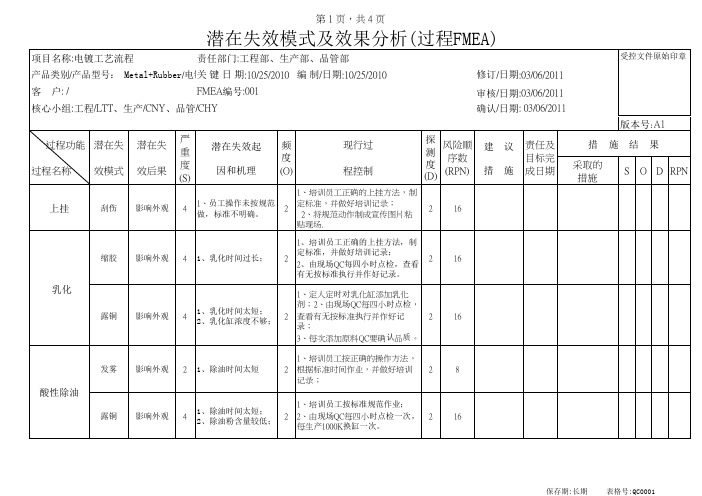
2
8
麻面
影响外观
2
防染盐时间过长
1
2
4
防染盐
脱镀层 影响功能 4 酸性活化时间太短 1
3
12
拉尾
影响外观
3
氯化镍缸内原料含量 比例失衡
2
2
12
氯化镍
重影
影响外观
3
镍缸里杂质过多
2
2
12
颜色不均
影响外观
3
镍缸里杂质过多 (含铜量)
1
2
6
保存期:长期
表格号:QC0001
第 3 页,共 4 页 过程功能 潜在失 过程名称 效模式 潜在失 效后果 严 重 度 (S)
频 度 (O)
现行过 程控制
1、培训员工正确的上挂方法,制 定标准,并做好培训记录; 2、将规范动作制成宣传图片粘 贴现场. 1、培训员工正确的上挂方法,制 定标准,并做好培训记录; 2、由现场QC每四小时点检,查看 有无按标准执行并作好记录。 1、定人定时对乳化缸添加乳化 剂;2、由现场QC每四小时点检, 查看有无按标准执行并作好记 录; 3、每次添加原料QC要确认品质。 1、培训员工按正确的操作方法, 根据标准时间作业,并做好培训 记录; 1、培训员工按标准规范作业; 2、由现场QC每四小时点检一次, 每生产1000K换缸一次。
3
潜在失效起 因和机理
频 度 (O)
现行过 程控制
1、培训员工按标准规范作业; 2、由现场QC每四小时点检一次; 检查时间是否在;2--3分钟内; 1、培训员工按标准规范作业; 2、由现场QC每四小时点检一次;
探 风险顺 测 序数 度 (RPN) (D)
2 18
建 措
议 施
PFMEA培训课件
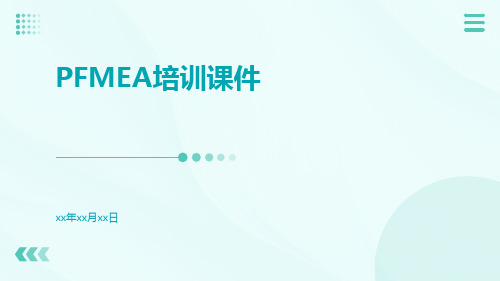
3
PFMEA在全球范围内得到了广泛应用,已成为 汽车、电子、航空航天、医疗器械等多个行业 的质量保证工具。
PFMEA的重要性
01
PFMEA有助于企业预防质量问题,降低生产成本,提高产品质量和可靠性。
02
PFMEA能够发现和解决潜在的设计、过程或设备失效模式,减少产品的缺陷和 故障,提高客户满意度和市场竞争力。
化工生产过程中存在大量的潜在风险因素,如高温、高压、腐蚀等。
PFMEA在该行业的应用可以帮助企业识别和控制这些风险因素,提高生产过程的安全性和稳定性。
PFMEA在化工生产中可以应用于各个阶段,包括原料选择、设备设计、生产流程制定、产品检验等。 通过分析潜在的失效模式和影响,制定相应的措施,提高生产效率和产品质量。
03
PFMEA是一种系统性的分析方法,有助于企业全面了解产品或过程的质量风险 ,为企业制定更加科学合理的质量控制计划提供依据。
02
PFMEA基础
PFMEA的原理
PFMEA的起源和定义
PFMEA(过程潜在失效模式与效应分析)是一种以过程为导向的分析方法, 用于识别、评估和排序潜在过程故障模式及其对产品、过程和客户的影响。
感谢观看
PFMEA培训课件
xx年xx月xx日
目录
• PFMEA概述 • PFMEA基础 • PFMEA应用案例 • PFMEA总结与展望
01
PFMEA概述
PFMEA定义与特点
PFMEA(潜在失效模式与效应分析)是一种预防性的质量工 具,用于识别、评估和解决潜在的设计、过程或设备失效模 式及其对系统性能的影响。
PFMEA的分析框架
PFMEA的分析框架包括产品分解、过程分解、故障模式识别、故障影响和故 障发生频率评估、风险优先级排序等步骤。
什么是PFMEA

什么是PFMEAPFMEA是过程失效模式及后果分析(ProcessFailureModeandEffectsAnalysis)的英文简称。
是由负责制造/装配的工程师/小组要紧采纳的一种分析技术,用以最大限度地保证各种潜在的失效模式及其相关的起因/机理已得到充分的考虑和论述。
失效:在条件下〔环境、操作、时刻〕,不能完成既定功能或产品参数值和不能维持在的上下限之间,以及在工作范围内导致零组件的破裂卡死等损坏现象。
严重度〔S〕:指一给定失效模式最严重的碍事后果的级不,是单一的FMEA范围内的相对定级结果。
严重度数值的落低只有通过设计更改或重新设计才能够实现。
频度〔O〕:指某一特定的起因/机理发生的可能发生,描述出现的可能性的级不数具有相对意义,但不是尽对的。
探测度〔D〕:指在零部件离开制造工序或装配之前,利用第二种现行过程操纵方法寻出失效起因/机理过程缺陷或后序发生的失效模式的可能性的评价指标;或者用第三种过程操纵方法寻出后序发生的失效模式的可能性的评价指标。
风险优先数〔RPN〕:指严重度数〔S〕和频度数〔O〕及不易探测度数〔D〕三项数字之乘积。
顾客:一般指“最终使用者〞,但也能够是随后或下游的制造或装配工序,维修工序或政府。
[编辑]PFMEA的分析原理PFMEA的分析原理如下表所示,它包括以下几个要害步骤:〔1〕确定与工艺生产或产品制造过程相关的潜在失效模式与起因;〔2〕评价失效对产品质量和顾客的潜在碍事;〔3〕寻出减少失效发生或失效条件的过程操纵变量,并制定纠正和预防措施;〔4〕编制潜在失效模式分级表,确保严重的失效模式得到优先操纵;〔5〕跟踪操纵措施的实施情况,更新失效模式分级表。
〔1〕“过程功能/要求〞:是指被分析的过程或工艺。
该过程或工艺能够是技术过程,如焊接、产品设计、软件代码编写等,也能够是治理过程,如方案编制、设计评审等。
尽可能简单地讲明该工艺过程或工序的目的,要是工艺过程包括许多具有不同失效模式的工序,那么能够把这些工序或要求作为独立过程列出;〔2〕“潜在的失效模式〞:是指过程可能发生的不满足过程要求或设计意图的形式或咨询题点,是对某具体工序不符合要求的描述。
PFMEA(福特)

Potential Failure Mode and Effects Analysis(Process FMEA)FMEA Number:C245Rev1.2Prepared By:Ozaki ShigeoItem: C245放大器Process Responsibility: 生产部FMEA Date (Orig.):2003年5月12日Model Year/Vehicle(s):Current/Various Program Key Date: 2003年6月1日FMEA Date (Rev.):2003年5月28日Core Team: 开发部----彭贤志、吴秀华; IQC----F.C.KO;品管部----李志斌;生产部----廖剑雄;技术部----OZAKI、薛明Action Results Requirements不合格品、待验品混淆功能降低5未放入待验区2无1. 放后自检2. 仓库收货员确认550无包装箱摔坏降低功能5堆放层数过高3卡通箱最高层底部不超1.6m 控制堆放层数,堆后自检345无卡通箱受潮降低功能5直接放在地面上2无卡通箱堆放底部离地面≥10cm。
345无没检不合格物料上线,难以进行装配加工影响产品品质7检验人员将已检标签错贴到未检物料批,1人事部对IQC检验人员上岗前进行能力培训与考核检验情况记录于检验日报表214无检验人员取样数量错误2定期对检验人员培训取样规则每天进行工艺纪律检查,以确保检验员是否按作业指导书进 行检验342无记数错误2人事部对IQC检验人员上岗前进行能力考核检验情况记录于检验日报表342无检验人员注意力不集中,漏检物料1人事部对IQC检验人员进行职业道德培训,并进行能力考核每天进行工艺纪律检查,以确保检验员是否按作业指导书进行检验428无检验人员能力不够,误读数3每月由人事部组织IQC检验人员进行技能培训每半年由人事部进行能力考核363无检验使用的仪器出现故障,2每年对检验仪器进行校正检验生产制程中由IPQC进行抽检确认物料合格情况456无测量所使用的方法与要求不符2人事部对IQC检验人员上岗前进行检验方法的培训。
PFMEA分析范例
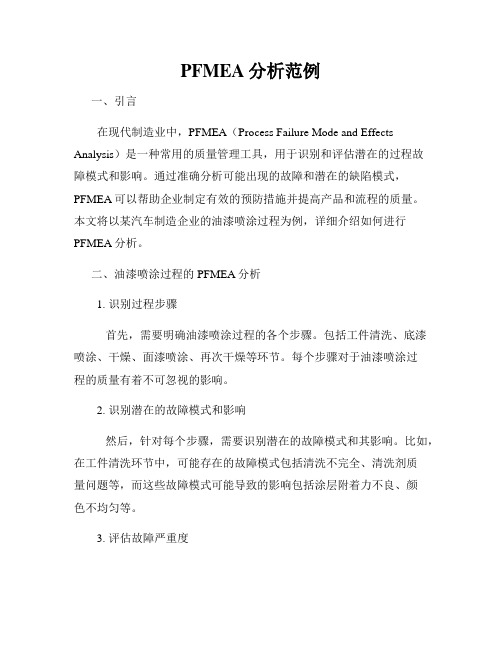
PFMEA分析范例一、引言在现代制造业中,PFMEA(Process Failure Mode and Effects Analysis)是一种常用的质量管理工具,用于识别和评估潜在的过程故障模式和影响。
通过准确分析可能出现的故障和潜在的缺陷模式,PFMEA可以帮助企业制定有效的预防措施并提高产品和流程的质量。
本文将以某汽车制造企业的油漆喷涂过程为例,详细介绍如何进行PFMEA分析。
二、油漆喷涂过程的PFMEA分析1. 识别过程步骤首先,需要明确油漆喷涂过程的各个步骤。
包括工件清洗、底漆喷涂、干燥、面漆喷涂、再次干燥等环节。
每个步骤对于油漆喷涂过程的质量有着不可忽视的影响。
2. 识别潜在的故障模式和影响然后,针对每个步骤,需要识别潜在的故障模式和其影响。
比如,在工件清洗环节中,可能存在的故障模式包括清洗不完全、清洗剂质量问题等,而这些故障模式可能导致的影响包括涂层附着力不良、颜色不均匀等。
3. 评估故障严重度对于识别出的潜在故障模式和影响,需要进行评估其严重度。
可以使用一定的评分标准,按照质量、成本、安全和客户满意度等指标进行评估,将故障的严重度进行量化。
4. 确定故障原因对于每个潜在的故障模式,需要进一步确定其引发故障的根本原因。
可能的原因包括工艺参数不稳定、操作工人培训不足、设备老化等。
通过深入调查和分析,可以找到导致故障的真正原因。
5. 确定现有控制措施在识别故障原因之后,需要评估当前已有的控制措施对于防止或减轻故障影响的效果。
这些控制措施可以包括工艺设备的保养维护、操作规程的制定、员工培训等。
对于有效的控制措施,需要进行确认和评估。
6. 提出改进措施最后,根据之前的分析结果,提出具体的改进措施。
这些措施应该针对潜在的故障原因,包括在工艺设计阶段进行优化、提升操作工人技能水平、更新设备以及改进工序等。
改进措施应该层层递进,以提高整个油漆喷涂过程的稳定性和可控性。
三、总结通过对某汽车制造企业油漆喷涂过程的PFMEA分析,可以深入理解每个步骤可能出现的故障模式和其对质量的影响。
电镀工序FMEA
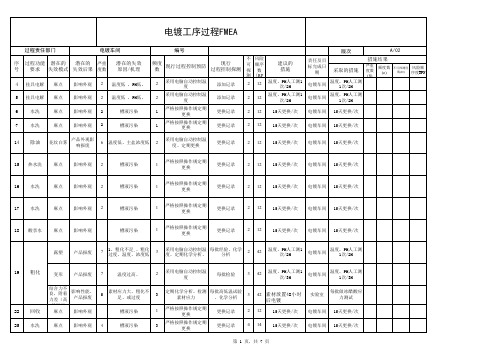
槽液污染 槽液污染 槽液污染
编号
频度 数
现行过程控制预防
现行 过程控制探测
3
严格按照操作规定期 更换
更换记录
不 风险 可 顺序 探数 测 (RP
4 14
3
严格按照操作规定期 更换
更换记录
4 14
3
严格按照操作规定期 更换
更换记录
4 14
建议的 措施
15天更换/次 15天更换/次 15天更换/次
责任及目 标完成日
6 温度低、主盐浓度低
2
采用电脑自动控制温 度、定期更换
更换记录
2 12 15天更换/次 电镀车间 15天更换/次
15 热水洗
麻点 影响外观 2
槽液污染
严格按照操作规定期
1
更换
更换记录
2 12 15天更换/次 电镀车间 15天更换/次
16 水洗
麻点 影响外观 2
槽液污染
1
严格按照操作规定期 更换
更换记录
1、粗化不足,、粗化 过度,温度、浓度低
3
采用电脑自动控制温 每批经验、化学
度、定期化学分析、
分析
2
42
温度,PH人工测1 次/2H
电镀车间
温度,PH人工测 1次/2H
19 粗化
变形 产品报废 7
温度过高、
采用电脑自动控制温
2
度
每批检验
3
42
温度,PH人工测1 次/3H
电镀车间
温度,PH人工测 1次/3H
38 水洗
麻点 影响外观 1
槽液污染
2
严格按照操作规定期 更换
更换记录
2 12 15天更换/次 电镀车间 7天更换/次
PFMEA分析范例

PFMEA分析范例1. 引言PFMEA(Process Failure Mode and Effects Analysis)是一种常用的质量管理工具,用于识别和评估制造过程中存在的潜在故障模式及其对产品质量的影响。
本文将通过一个实例来展示PFMEA分析的过程和方法。
2. 实例描述假设我们正在开发一种新型电动汽车电池组装工艺,并希望通过PFMEA分析来发现潜在的故障模式并采取相应的措施预防。
3. PFMEA步骤3.1 选择分析范围首先,我们需要确定要分析的工艺范围。
在本例中,我们选择了电动汽车电池组装工艺中的关键步骤:电池包装、电池连接和充电检测。
3.2 收集工艺信息接下来,我们收集与每个工艺步骤相关的信息,包括工艺流程、设备、材料和人员等。
针对电池包装步骤,我们列出了以下信息: - 工艺流程:电芯装载、包装封装- 设备:电芯装载机、包装机- 材料:电芯、包装材料- 人员:操作工、质检员3.3 识别故障模式在此步骤中,我们识别潜在的故障模式,即制造过程中可能发生的问题。
针对电池包装步骤,我们列出了以下故障模式: - 电芯装载不准确- 包装封装不牢固3.4 评估故障影响在此步骤中,我们评估每个故障模式对产品质量的影响程度。
针对电芯装载不准确这一故障模式,我们评估了以下影响: - 电池运行时间缩短- 电池性能下降3.5 评估故障原因在此步骤中,我们分析导致每个故障模式出现的可能原因。
针对电芯装载不准确这一故障模式,可能的原因包括:- 操作工技能不熟练- 设备故障3.6 识别和实施控制措施在此步骤中,我们确定并实施控制措施以防止故障模式的发生。
针对电芯装载不准确这一故障模式,可能的控制措施包括: - 培训操作工,提高技能水平- 定期维护设备,确保其正常运行3.7 重新评估和更新PFMEA最后,我们重新评估已实施的控制措施并更新PFMEA表格。
如果控制措施有效,我们将确认问题得到了解决。
如果问题仍存在,我们需要重新评估并采取进一步的纠正措施。
PFMEA(氢气检漏)

编制 : 阮伟 __第 1 页 共 1 页零件或设备名称及代号频度数严重度不易探风险顺1、未按指定压力进行气密试验,达不到气密试验目的。
2、气密完成后未及时进行排空1)操作者未看流转卡,违规操作。
2)压力表失效或指针不准。
安全事故、影响产品质量1、编制气密试验流转卡2、 压力表定期送计量室计量标定。
15151、加强员工培训 及考核。
2、把气密试验过程纳入工艺纪律检查3、无无无无////无4、启动程序时,按钮按错。
员工操作失误控制装置不运行启动按钮设置误操作保护及防呆措施1111对员工进行设备操作培训5、抽真空未达到要求抽真空参数设置错误影响检漏可靠性和产品质量参数由专人设置,不允许员工随意修改。
1224参数由专人设置,不允许员工随意修改。
1、机组未进行抽空直接进行充气员工违规操作未对机组进行抽真空直接把充气管接入机组机组小管路及复杂型腔内角落处氢氮混合气不能迅速充入,影响检漏质量加强对员工设备操作培训1212加强对员工设备操作培训2、 充气压力未达到要求充气压力参数设置错误影响检漏精度和产品质量参数由专人设置,不允许员工随意修改。
1212参数由专人设置,不允许员工随意修改。
3、无无无无////无1、检漏误报警1、报警值设定过高2、违规操作或操作失误影响检漏精度和漏点判断参数由专人设置,不允许员工随意修改。
并对员工进行操作培训。
3139参数由专人设置,不允许员工随意修改。
并对员工进行操作培训。
2、对部分焊接点或密封面漏检员工操作失误、责任心不强影响检漏精度和漏点判断并对员工进行操作培训。
3139并对员工进行操作培训。
3、无无无无////无机组未内混合气体未进行排空直接流入下道工序员工违规操作机组内由一定压力的气体,存在较大的安全隐患。
加强对员工的安全操作培训。
25110加强对员工的安全操作培训。
排空后机组内还参与一定量(一个大气压下内容积量)的混合气气体物理性质决定残留混合气为安全气体,泄漏到大气中会被迅速稀释,也是安全的。
PFMEA(第四版)
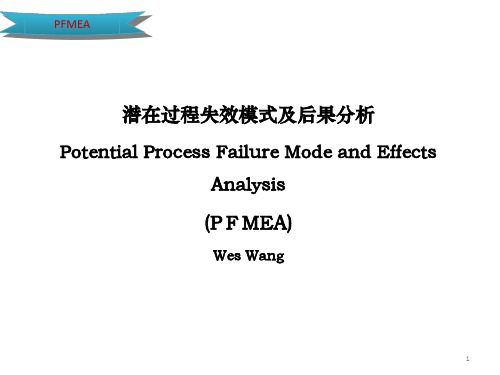
• 关键日期(E):输入初次FMEA应完成的日期,不能超过计划 的生产开始日期,如果是供应商,则此日期不能超过顾客要求 的生产件批准程序(PPAP)提交日期。
21
第四章:PFMEA
过程FMEA表头
• FMEA日期(F):输入原始FMEA的完成日期,以及最近的 修订日期。
• 核心小组(G):输入负责开发PFMEA的小组成员联系方式。
螺钉拧入其他孔洞里
制造和装配:难以安装 剩余的螺钉
螺钉没有完全拧入 螺钉扭矩太高 螺钉扭矩太低
最终顾客:座垫松动, 有噪音。 制造和装配:由于受影响 的部分,因而进行额外挑 选和返工。
最终顾客:由于螺钉断裂 导致座垫松动,有噪音。 制造和装配:由于受影响 的部分,因而进行额外挑 选和返工。
➢ 例二:一个箱体与箱盖装配后被拒收的潜在原因是: “不密封”、“漏装零件”、“未注润滑剂”,等。
对于试验、检验过程两种可能的失效模式: ➢ 接受不合格的零件; ➢ 拒收合格的零件。
27
第四章:PFMEA
如何做PFMEA
过程步骤/功能
操作20: 使用扭矩枪把坐垫安 装 在座椅轨道上
要求 四个螺钉 规定的螺钉
过程功能(a2):输入与每个受分析的过程步骤/操作相应的过程功能。过 程功能描述的是操作的目的。
要求(a3):列出每个受分析的过程步骤/操作的过程功能的要求。要求是指
对规定过程的输入,以期达到设计目的和其他顾客要求。
23
潜在失效模ห้องสมุดไป่ตู้及后果分析
(过程FMEA) FMEA编号 FM01-12
共 1 页,第 3 页
装配顺序:首先在右前孔拧 螺钉
螺钉被完全拧入
按照动态扭矩规格来扭转 螺钉
电镀制程PFMEA

镀层厚 度不足
零件寿命降低
7
△
镀锌
在原材表面通 过电化学反应 形成规定厚度 镀层起 的均匀镀层 泡/脱皮 镀层外 观发黑 镀层外 观太亮 镀层外 观亮度 差或发 雾
镀层厚 度超标
零件寿命降低 7 结合力不良 △
△ 7 不符合客户外 观要求 6 △
△
光亮剂过少 有机杂质 电流设置偏 低
镀锌后水 洗去药水残液 洗 及保湿
包裝
按客户要求
数量错 误 零件外 观被污 染 外观不 良
客诉
5
△
作业注意力 不集中,漏 检物料 包装材料不 干净
2
每天进行工艺 纪律检查,以 确保作业员是 否按作业指导 书进行检验 巡查 每天进行工艺 纪律检查,以 确保检验员是 否按作业指导 书进行检验 首检确认
6
60
无
客诉
5
△
2
6
60
无
无外观不良, 镀层厚度符合 客户要求,并 及时提供检测 FQC抽验 报告 耐盐雾达到客 户要求
残留碱 液
影响后面水洗
2
○
移动水洗
洗去药水残液 及保湿
残留碱 液
影响后面水洗
2
○
水洗
洗去药水残液 及保湿
残留碱 液
出光浓度降低
5
△
水流量不 足,水呈碱 性 水洗时间不 够 水流量不 足,水呈碱 性 水洗时间不 够 水流量不 足,水呈碱 性 水洗时间不 够
3 3 3 3 3 3
现行过程 控制预防 发生率
上料
装载正确数量 的原材
初段预电 清除原材表面 解除油 大部分油垢
残留大 部分油 垢
影响下工序电 解除油效果
pfmea分类

pfmea分类PFMEA(Process Failure Mode and Effects Analysis)是一种用于识别和评估制程中潜在故障模式及其对产品和过程性能的影响的方法。
它是以预防为主导的质量管理工具,旨在通过在设计阶段识别和消除潜在故障模式,以确保产品的质量和可靠性。
本文将以PFMEA分类为标题,介绍其基本概念、应用步骤和实施过程。
一、PFMEA的基本概念PFMEA是一种系统性的方法,用于识别和分析制程中潜在的故障模式及其对产品和过程性能的影响。
它主要包括三个关键要素:故障模式(Failure Mode)、故障影响(Effects)和故障严重性(Severity)。
故障模式指的是制程中可能发生的故障,故障影响指的是故障对产品和过程性能可能造成的影响,故障严重性则是对故障影响的评估。
二、PFMEA的应用步骤1. 确定要分析的制程:首先需要明确要分析的制程或过程,这可以是产品的设计、制造、装配、测试等各个环节。
2. 确定参与者:确定参与分析的团队成员,包括制程工程师、质量工程师、设计工程师等相关人员。
3. 制程流程图绘制:绘制制程的流程图,以便全面了解制程中的各个环节和流程。
4. 识别潜在故障模式:通过分析制程流程,识别可能发生的故障模式,即在每个环节中可能出现的故障。
5. 评估故障影响:对于每个故障模式,评估其对产品和过程性能的影响,包括安全性、可靠性、质量等方面。
6. 评估故障严重性:对故障影响进行评估,确定故障的严重性,以确定哪些故障需要重点关注和处理。
7. 制定改进措施:针对识别出的故障模式和严重性,制定相应的改进措施,以降低故障风险和提高产品质量。
8. 实施改进措施:实施制定的改进措施,并跟踪和监控改进效果,确保改进措施的有效性和可持续性。
三、PFMEA的实施过程1. 收集制程信息:收集与制程相关的信息,包括制程流程图、产品设计规范、制程参数等。
2. 制定分析计划:制定PFMEA的分析计划,包括确定分析的范围、参与者、时间计划等。
PFMEA分析范例
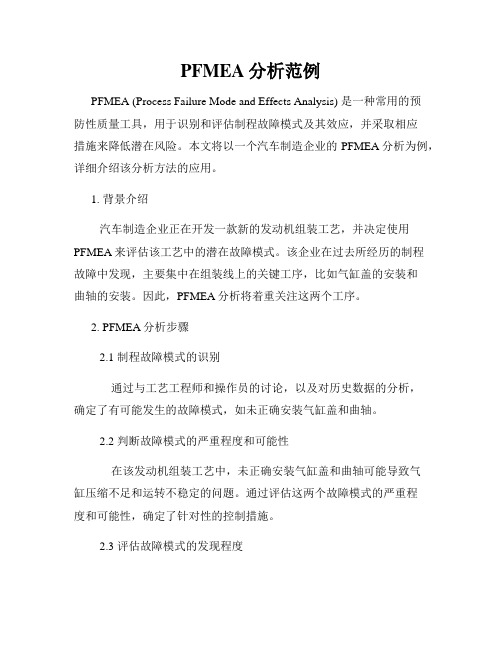
PFMEA分析范例PFMEA (Process Failure Mode and Effects Analysis) 是一种常用的预防性质量工具,用于识别和评估制程故障模式及其效应,并采取相应措施来降低潜在风险。
本文将以一个汽车制造企业的PFMEA分析为例,详细介绍该分析方法的应用。
1. 背景介绍汽车制造企业正在开发一款新的发动机组装工艺,并决定使用PFMEA来评估该工艺中的潜在故障模式。
该企业在过去所经历的制程故障中发现,主要集中在组装线上的关键工序,比如气缸盖的安装和曲轴的安装。
因此,PFMEA分析将着重关注这两个工序。
2. PFMEA分析步骤2.1 制程故障模式的识别通过与工艺工程师和操作员的讨论,以及对历史数据的分析,确定了有可能发生的故障模式,如未正确安装气缸盖和曲轴。
2.2 判断故障模式的严重程度和可能性在该发动机组装工艺中,未正确安装气缸盖和曲轴可能导致气缸压缩不足和运转不稳定的问题。
通过评估这两个故障模式的严重程度和可能性,确定了针对性的控制措施。
2.3 评估故障模式的发现程度考虑到设备和操作员的现有检测手段,确定了对未正确安装气缸盖和曲轴的发现程度。
如采用视觉检测和质量控制人员的检验。
2.4 计算RPN值通过将故障模式的严重程度、可能性和发现程度相乘,得到Risk Priority Number (RPN) 值,用于确定哪些故障模式需要优先处理。
2.5 制定预防和改善措施针对具有较高RPN值的故障模式,制定预防和改善措施,如提供培训、改进工艺规程、增加检测设备等。
2.6 实施和验证措施的有效性实施制定的措施,并通过监控和验证来确保其有效性。
比如设立关键工序的抽样检验,并对不合格品进行追踪分析。
3. 结果与总结通过PFMEA分析,汽车制造企业识别出了发动机组装工艺中的关键故障模式,并相应制定了有效的控制措施。
这些措施将有助于降低潜在的质量风险,提高发动机组装的可靠性和稳定性。
4. 心得体会通过本次PFMEA分析,我们深刻认识到了预防性质量工具的重要性。
PFMEA开发教程
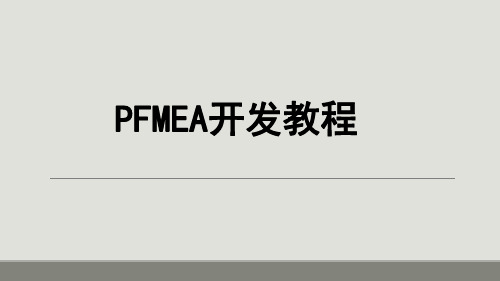
PFMEA开发教程目录•什么是PFMEA1•为什么要做PFMEA2•什么时候做PFMEA3•由谁来做PFEMA4•如何做PFMEA5•PFMEA和APQP的关联6PFMEA 中英文全称:过程失效模式和后果分析-> Process Failure Mode & Effect Analysis失效模式:指制造过程无法达到预定或规定的要求所表现出的现象;如:不合格品、不良设备状况后果:指失效模式在内部、车厂及顾客处(包括后续工序)所造成的不良影响PFMEA定义及其含义:PFMEA是一种分析工具,用于识别出产品或过程的潜在失效,从而可以采取相应的纠正措施FMEA的发展历史:●1949年由美国军方创建用于国防工业●上世纪50年代被航空航天工业采纳●上世纪70年代,汽车工业将FMEA作为在对其零件设计和生产制造的评审项目的重要部分-Ford公司首次应用于汽车工业●上世纪80年代,产品事故责任的费用突升和不断的法庭起诉事件发生,使FMEA成为降低事故的不可缺少的重要工具●1993年美国汽车工业行动集团(AIAG)首次发行了FMEA标准,定义了对OEM和供应商最基本的FMEA要求●2008年AIAG发布FMEA (第四版)FMEA的主要类型:●DFMEA: 在产品正式设计发布之前分析潜在失效—专注于产品由于设计造成的和功能相关的潜在失效●PFMEA: 用于分析制造和装配过程—专注于过程由于设计和操作造成的和功能相关的潜在失效模式0246810类别1类别2类别3110100设计开发过程开发售后阶段010080602040成本($)减少变更成本风险1:10:100设计改起来很麻烦,这个风险等以后有问题再改吧?FMEA评估和减小风险做PFMEA 之后,我们产品不良率能降低多少PPM 呢?M2M3.1M3.2M3.3M3PPAP发布初版u p d a t eu p d a t eu p d a t eu p d a t ePFMEA制作IQC SQEMEDSMT PQOQA评审PMMPPFMEA 是团队的成果过程步骤/功能要求潜在失效模式潜在失效影响潜在失效原因严重度频度控制预防控制探测探测度RPN5、DIETZ的PFMEA分析理论举个例子目前公司内所有的PCB板都会镭雕二维码以及相关信息,小小的二维码在追溯以及防错等方面发挥着重大作用。
PFMEA培训课件
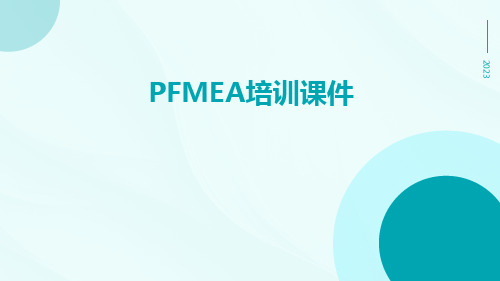
PFMEA的历史与发展
1
PFMEA起源于20世纪70年代的美国宇航局( NASA),最初用于分析太空任务EA逐渐在汽车、电子 、医疗和机械制造等领域得到广泛应用。
2023
PFMEA培训课件
目录
• PFMEA概述 • PFMEA基础 • PFMEA核心概念 • PFMEA应用案例 • PFMEA总结与展望
01
PFMEA概述
PFMEA定义与特点
PFMEA(潜在失效模式与效应分析)是一种预防性的质量工 具,用于识别、评估和解决潜在的设计、过程或设备失效模 式及其对系统性能的影响。
01
严重度(Severity)
指失效模式或故障模式对产品或过程 的影响程度。
02
发生频率( Occurrence)
指失效模式或故障模式在生产过程中 出现的概率。
03
可探测性( Detectabili…
指在生产过程中能够发现和识别人员 、机器、材料、测量、环境和工艺方 面的故障模式的难易程度。
PFMEA的分析策略和技巧
制定PFMEA改进措施
根据PFMEA分析结果,制定改进措 施并进行实施。
PFMEA的工具与技术
PFMEA表格
FTA(故障树分析)
PFMEA表格是PFMEA分析的基础工具,用 于记录潜在失效模式、失效影响等信息。
FTA是一种用于分析复杂系统故障的工具, 可以帮助PFMEA团队更好地分析潜在失效 模式。
02
PFMEA通过对产品设计、制造、装配和维修等过程进行深入分析,能够帮助企 业提前发现潜在问题,采取预防措施,降低产品开发成本和缩短产品上市时间 。
钢铁零件铬前除应力与铬后除氢的重要性
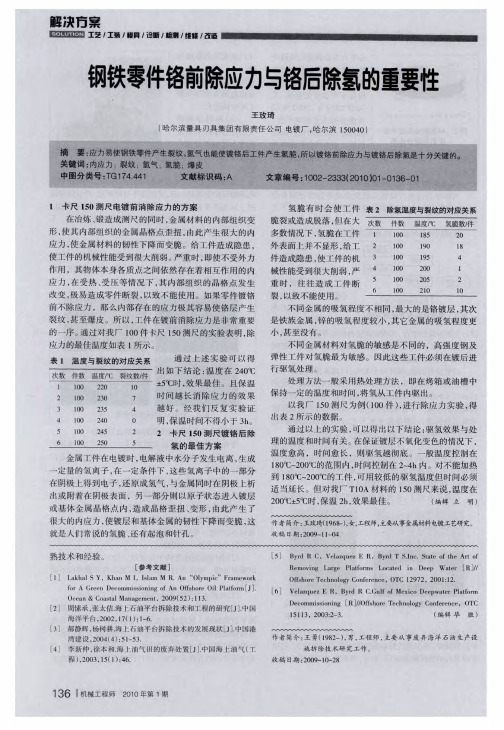
关键 词 :内应 力 ; 裂纹 ; 氢气 ; 氢脆 ; 爆皮
j
中图分 类号
:T G
l
7
4
4
。
4
1
文 献标 识 码 :A
文 章 编 号 :1 0 0 2 - 2 3 3 3 ( 2 0 1 0 )0 1 — 0 1 3 6 一 o l
。
…
…
1 卡尺 1 5 0 测 尺 电镀 前 消 除应 力的方案
在冶炼 、 锻造成测 尺 的 同时 , 金 属 材料 的 内部组 织 变 形 , 使 其 内部 组 织 的金 属 晶格 点 歪 扭 , 由此 产 生 很 大 的 内 应 力 , 使金 属 材 料 的韧 性 下 降而 变 脆 。 给 _T 件造 成 隐患 , 使工 件的机械性能受到很大削弱 。 严重时 , 即使不 受外力 作用 , 其物体本身各质点之 间依然存在着相互 作用 的 内
氢脆 有 时 会 使 工 件 表 2 除氢温度与裂纹的对应关 系
脆裂或造成脱落 ,但在大
多数情况下 ,氢脆在工 件
外表面上并不 显 形 ,给工
件造成 隐患 , 使工 件 的机
械性能受到很 大削弱 ,严
重时 , 往往造成工 件断
裂 , 以致 不 能使用 。
不 同金 属 的 吸 氢程 度 不 相 同 最 , 大 的是 铬镀 层 其 , 次
180 ℃~ 2 0 0 0C 的范 围内 , 时间控制在 2 ~ 4 h 内。 对 不 能加热
到 l 8 0 ℃ ~ 2 0 0 0C 的工 件 , 可用较低 的驱 氢温 度但 时间必 须
适 当延 长 。 但对 我 厂 T 10 A 材料 的 15 0 测 尺 来说 , 温度在
2 0 0 0C ±5 0 C 时 , 保 温 2 h , 效果 最 佳 。
PFMEA---DELL(格式)
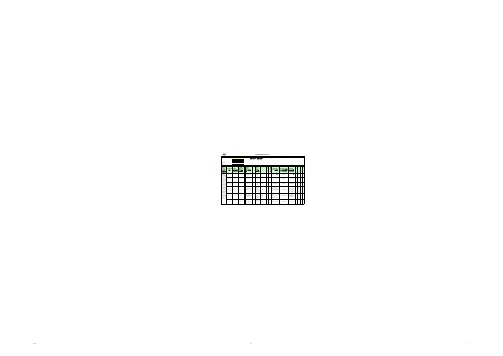
Recommended resource for using PFMEA effectively: AIAG FMEA Manual or similarFMEA Orig. Date FMEA Rev. DateSeverity - Occurrence - Detection Rankings Scale - See RPN Rankings sheet tab Characteristic<XX>Feature &Tolerance (if applicable)典型特征&公差(如果适用)Process Flow 流程Potential Failure Mode 潜在失效模式Potential Effect(s) of Failure 潜在失效效果S e v 严重性Potential Cause(s) of Failure 潜在失效原因O c c u r 发生性Current Process Controls 现行制程管控De t e c 侦测R P N(S *O *D )重要分级P r io r i t yR a n k i n gRecommended Actions 推荐措施Responsibility & Target Completion Date 责任单位&目标完成日期Comments/ Actions Taken 备注/采取的措施Se v 严重性O c c u r 发生性D e t e c 侦测R P N染色 化抛流纹外观不良4染色槽浓度过高,PH 值偏低2降低浓度,升高PH值5403降低浓度,升高PH值阳极(1/14)降低浓度,升高PH值42432水洗 片碱脏污外观不良3水洗槽不干净2及时更换水洗槽6363及时更换水洗槽阳极(1/14)及时更换水洗槽32318染色前水洗 染色白点外观不良2过滤机压力过大3两天清洗滤芯一次,一周必须更换滤芯5303两天清洗滤芯一次,一周必须更换滤芯阳极(1/14)两天清洗滤芯一次,一周必须更换滤芯23212前处理 上下挂碰划伤外观不良41.隔板过于粗糙2.操作时,产品会碰到槽体四周21.隔板表面加一层棉布2.要求并督导员工轻拿轻放 ,产线水槽曝气减小,减少产品在生产过程中的晃动64831.隔板表面加一层棉布2.要求并督导员工轻拿轻放 ,产线水槽曝气减小,减少产品在生产过程中的晃动阳极(1/14)1.隔板表面加一层棉布2.要求并督导员工轻拿轻放 ,产线水槽曝气减小,减少产品在生产过程中的晃动42432染 色色差外观不良51.人员操作疏失。
PFMEA评价准则第四版
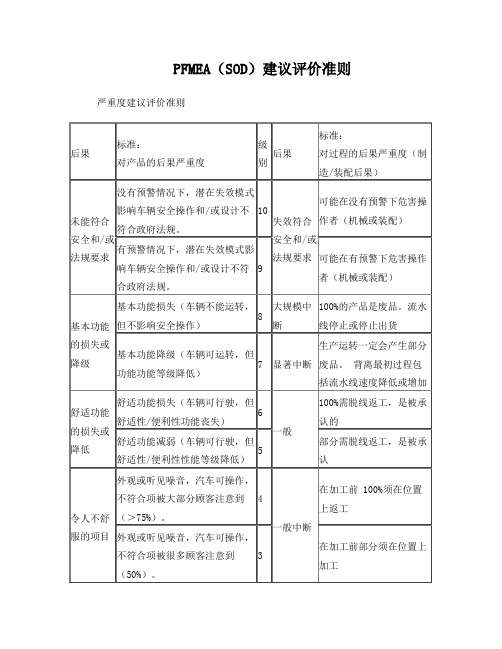
严重度建议评价准则
后果
标准:
对产品的后果严重度
级别
后果
标准:
对过程的后果严重度(制造/装配后果)
未能符合安全和/或法规要求
没有预警情况下,潜在失效模式影响车辆安全操作和/或设计不符合政府法规。
10
失效符合安全和/或法规要求
可能在没有预警下危害操作者(机械或装配)
有预警情况下,潜在失效模式影响车辆安全操作和/或设计不符合政府法规。
(RPN) (S)X(O)X(D)=RPN
2、优先关注风险
S=8,9,10
SO>35
RP陷状况
措施
O
S
D
1
1
1
理想状况
不必采取
1
1
10
可靠控制
不必采取
1
10
1
缺陷未到用户处
不必采取
1
10
10
缺陷会到用户处
必须采取
10
1
1
缺陷频率高, 能保证发现,但要投资
必须采取
6
低
开始时问题探测
操作者在位置上使用变量测量或通过位置上的自动控制探测差异零件和通知操作者(光、杂音等)。在设置上或首件检验时执行测量(仅对于设置要因)。
5
一般
加工后问题探测
由自动控制探测变异零件并锁住零件预防进一步加工的事后失效模式探测。
4
一般高
开始时问题探测
由自动控制在位置上探测变异零件并在位置上自动锁住零件预防进一步加工的失效模式探测。
3
在加工前部分须在位置上加工
外观或听见噪音,汽车可操作,不符合项被有辨别能力的顾客注意到(< 25%)。
PFMEA在汽车整车生产中的优势与建议
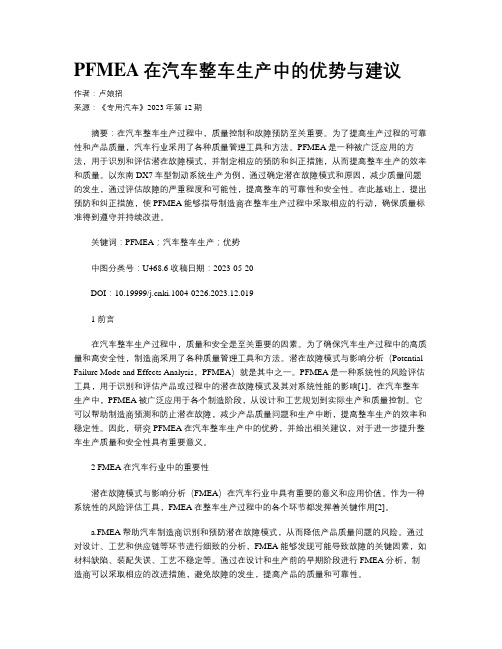
PFMEA在汽车整车生产中的优势与建议作者:卢娘招来源:《专用汽车》2023年第12期摘要:在汽车整车生产过程中,质量控制和故障预防至关重要。
为了提高生产过程的可靠性和产品质量,汽车行业采用了各种质量管理工具和方法。
PFMEA是一种被广泛应用的方法,用于识别和评估潜在故障模式,并制定相应的预防和纠正措施,从而提高整车生产的效率和质量。
以东南DX7车型制动系统生产为例,通过确定潜在故障模式和原因,减少质量问题的发生,通过评估故障的严重程度和可能性,提高整车的可靠性和安全性。
在此基础上,提出预防和纠正措施,使PFMEA能够指导制造商在整车生产过程中采取相应的行动,确保质量标准得到遵守并持续改进。
关键词:PFMEA;汽车整车生产;优势中图分类号:U468.6 收稿日期:2023-05-20DOI:10.19999/ki.1004-0226.2023.12.0191 前言在汽车整车生产过程中,质量和安全是至关重要的因素。
为了确保汽车生产过程中的高质量和高安全性,制造商采用了各种质量管理工具和方法。
潜在故障模式与影响分析(Potential Failure Mode and Effects Analysis,PFMEA)就是其中之一。
PFMEA是一种系统性的风险评估工具,用于识别和评估产品或过程中的潜在故障模式及其对系统性能的影响[1]。
在汽车整车生产中,PFMEA被广泛应用于各个制造阶段,从设计和工艺规划到实际生产和质量控制。
它可以帮助制造商预测和防止潜在故障,减少产品质量问题和生产中断,提高整车生产的效率和稳定性。
因此,研究PFMEA在汽车整车生产中的优势,并给出相关建议,对于进一步提升整车生产质量和安全性具有重要意义。
2 FMEA在汽车行业中的重要性潜在故障模式与影响分析(FMEA)在汽车行业中具有重要的意义和应用价值。
作为一种系统性的风险评估工具,FMEA在整车生产过程中的各个环节都发挥着关键作用[2]。
- 1、下载文档前请自行甄别文档内容的完整性,平台不提供额外的编辑、内容补充、找答案等附加服务。
- 2、"仅部分预览"的文档,不可在线预览部分如存在完整性等问题,可反馈申请退款(可完整预览的文档不适用该条件!)。
- 3、如文档侵犯您的权益,请联系客服反馈,我们会尽快为您处理(人工客服工作时间:9:00-18:30)。
温度及时间确认记 温度及时间确认 3 录表 记录表 秒表确认
3
36
解
4 1.使用时间过长
自动线溶液定期跟 自动线溶液定期 3 换计划及实绩记录 跟换计划及实绩 表 记录表
5
60
1.整流机故障, 5 2.槽液浓度不够 3.投入量不足
3 始业点检基准书
始业点检成绩表
3
45
4
1.水中杂质多 2.溢流水小
自动线溶液定期跟 自动线溶液定期 3 换计划及实绩记录 跟换计划及实绩 表 记录表
1.浓度过高,产品处理 过头,影响产品外观及 性能; 1.槽液浓度不在标 2.浓度过低,产品处理 准范围内 不彻底,影响后工序, 且会造成产品品质不合 格 1.温度过高,产品处理 过头,影响产品外观及 性能; 2.温度不在标准范 2.温度过低,产品处理 围内 不彻底,,影响后工 序,且会造成产品品质 不合格 1.时间过长,产品处理 过头,影响产品外观及 性能; 3.时间不是设定时 2.时间过短,产品处理 间 不彻底,油脂未除尽, 影响后工序,且会造成 产品品质不合格 1.产品处理不彻底,影 4.杂质过多槽液失 响后工序,且会造成产 效 品品质不合格 1.电压过高,产品处理 过头,影响产品外观及 性能; 5.电压不在范围值 2.电压过低,产品处理 不彻底,,影响后工 序,且会造成产品品质 不合格 水 洗 水洗不净 产品水洗不净,带出量 大,污染下道工序
3
36
保存期限:产品停产后外加一年
4/12
制程功能 严 重 度 S 探 频 目前制程控制方 测 度 目前制程控制方式 度 式 ( 预防) ( 检测) O D
潜在失效模式 要求
潜在失效的后果
潜在失效的起因/机 理
风 险 度 R P N
建议措施
负责部门、人 员及完成日期
采取措施
改善后结果 风 严 探 险 频 重 测 度 度 度 度 - R O S D P N
温度及时间确认记 温度及时间确认 3 录表 记录表 秒表确认
3
36
3 始业点检基准书
始业点检成绩表
3
36 2/12
制程功能 严 重 度 S 探 频 目前制程控制方 测 度 目前制程控制方式 度 式 ( 预防) ( 检测) O D
潜在失效模式 要求
潜在失效的后果
潜在失效的起因/机 理
风 险 度 R P N
上料滚筒残留品确 4 认作业指导书 上料作业记录表 上料作业指导书
7
严格按照作 业指导书操 作,确认残 留品及粘滞 112 品,品质检 查员巡检时 应更严格, 更仔细。
制造课/ 2011.05.18
严格按照作 业指导书操 作,确认残 留品及粘滞 4 3 7 84 品,品质检 查员巡检时 应更严格, 更仔细。
潜在失效模式 要求
潜在失效的后果
潜在失效的起因/机 理
建议措施
负责部门、人 员及完成日期
采取措施
1.部品与番号不一 1.产品无法正常受入, 致 无法进入后续工序
1.客户提供的部品与 番号不一致 2 2.接收时部品与流程 票混乱 1.客户来料时,来料 容器内有异品混入; 5 2.在运输装卸过程 中,来料容器倾覆, 导致异品混入 3 1.客户来料的部品螺 纹精度不对 1.客户来料实际重量 与发货单不一致; 2.运输装卸时产品遗 失 1.客户来料产品外观 不合格; 2.在运输装卸过程中 的意外情况导致产品 外观不合格 1.客户发货单上的批 号与流程票上的批号 不一致 2.接收时部品与流程 票混乱 1.客户未放置流程 票;2.运输装卸过程 中流程票遗失;3.接 收时将流程票遗失
5
60
1.液位过高,槽液易溢 出,流于地面 ,会造 成溶液体积变大,浓度 降低; 5.液位不在设定水 2.液位过低,部分产品 位线 处理不彻底,影响后工 序,且会造成产品品质 不合格且会造成溶液体 积变小,浓度升高
1.水位开关故障 2.手动加水或手动排 4 水开关忘记开关或故 障
3 始业点检基准书
始业点检成绩表
上
1.导致产品品质不良, 1.部品投入量错误 需要申请报废
1.备料时,按错误重 量进行称量准备 6 2.电子称精度不够, 称量不准 2
投入量一览表 上料作业指导书 标准重量点检 外部标准校正
上料作业记录表 电子秤日常点检 记录 校准证书 2 24
2.有异品混入
1.产品混料,流入下一 工序,影响下一工序操 作
1.浓度过高,产品处理 过头,影响产品外观及 性能; 1.槽液浓度不在标 2.浓度过低,产品处理 准范围内 不彻底,影响后工序, 且会造成产品品质不合 格 1.温度过高,产品处理 过头,影响产品外观及 性能; 2.温度不在标准范 2.温度过低,产品处理 围内 不彻底,影响后工序, 且会造成产品品质不合 格 1.时间过长,产品处理 过头,影响产品外观及 性能; 3.时间不是设定时 2.时间过短,产品处理 间 不彻底,影响后工序, 且会造成产品品质不合 格 洗 4.槽液失效
建议措施
负责部门、人 员及完成日期
采取措施
改善后结果 风 严 探 险 频 重 测 度 度 度 度 - R O S D P N
1.浓度过高,产品处理 过头,影响产品外观及 性能; 1.槽液浓度不在标 2.浓度过低,产品处理 准范围内 不彻底,油脂未除尽, 影响后工序,且会造成 产品品质不合格 1.温度过高,产品处理 过头,影响产品外观及 性能; 2.温度不在标准范 2.温度过低,产品处理 围内 不彻底,油脂未除尽, 影响后工序,且会造成 产品品质不合格 脱 脂 2 1.时间过长,产品处理 过头,影响产品外观及 性能; 3.时间不是设定时 2.时间过短,产品处理 间 不彻底,油脂未除尽, 影响后工序,且会造成 产品品质不合格 1.液位过高,槽液易溢 出,流于地面 ,会造 成溶液体积变大,浓度 降低; 5.液位不在设定水 2.液位过低,部分产品 位线 处理不彻底,影响后工 序,且会造成产品品质 不合格且会造成溶液体 积变小,浓度升高 水 洗 产品水洗不净,带出量 大,污染下道工序
4
1.温控设备故障 2.加热设备故障
2
自动显示 温度计校正
始业点检成绩表 温度及时间确认 记录表
3
24
酸
4 1.程序故障
温度及时间确认记 温度及时间确认 3 录表 记录表 秒表确认
3
36
1.产品处理不彻底,影 响后工序,且会造成产 品品质不合格
4 1.使用时间过长
自动线溶液定期跟 自动线溶液定期 3 换计划及实绩记录 跟换计划及实绩 表 记录表
3/12
制程功能 严 重 ( 检测) O D
潜在失效模式 要求
潜在失效的后果
潜在失效的起因/机 理
风 险 度 R P N
建议措施
负责部门、人 员及完成日期
采取措施
改善后结果 风 严 探 险 频 重 测 度 度 度 度 - R O S D P N
温度及时间确认记 温度及时间确认 3 录表 记录表 秒表确认
3
36
1.水位开关故障 2.手动加水或手动排 4 水开关忘记开关或故 障
3 始业点检基准书
始业点检成绩表
3
36
水洗不净
4
1.水中杂质多 2.溢流水小
自动线溶液定期跟 自动线溶液定期 3 换计划及实绩记录 跟换计划及实绩 表 记录表
3
36
保存期限:产品停产后外加一年
广州市新旭金属表面处理有限公司
潜在失效模式和后果分析--(过程FMEA-PFMEA)
T-06-004-V.1 种类: 零件编号: 规格/型号: 跨功能小組: 制程功能 滚镀 螺丝类除氢产品 / 陈传雷、张华飞、卢宜维、唐宇坤、吕勇勇 严 重 度 S 探 频 目前制程控制方 测 度 目前制程控制方式 度 式 ( 预防) ( 检测) O D 风 险 度 R P N 改善后结果 风 严 探 险 频 重 测 度 度 度 度 - R O S D P N 制程责任: 张华飞/唐四军 关键日期:2011.05.17 FMEA编号:FMEA-03-V.7 FMEA日期(原版):2010.08.01
2
受入检查基准及作 受入检查成绩表 业手顺书 受入检查基准及作 发货单 业手顺书 受入检查成绩表
2
12
4.部品来料实际重 1.产品无法正常受入, 量与客户发货单注 无法进入后续工序 明重量不一致
2
3
1
6
5.外观检查不合格
1.产品无法正常受入, 无法进入后续工序
4
2
受入检查基准及作 业手顺书 受入检查成绩表
1.药液分析失误 2.药品添加过多或过 6 少 3.水量添加过少或过 多
药水分析及添加 记录表 滴定分析作业指导 浓度管理图表 3 书 化工原材料领料 始业点检基准书 单 始业点检成绩表
3
54
酸
4
1.温控设备故障 2.加热设备故障
3
自动显示 温度计校正
始业点检成绩表 温度及时间确认 记录表
3
36
电
4 1.程序故障
3
上料作业指导 书
上料作业记录表
3
63
药水分析及添加 滴定分析作业指导 记录表 浓度管理图表 3 书 化工原材料领料 始业点检基准书 单 始业点检成绩表 始业点检成绩表 温度及时间确认 记录表
3
54
4
1.温控设备故障 2.加热设备故障
3
自动显示 温度计校正
3
36
4 1.程序故障 1.水位开关故障 2.手动加水或手动排 4 水开关忘记开关或故 障
1.药液分析失误 2.药品添加过多或过 6 少 3.水量添加过少或过 多
药水分析及添加 记录表 滴定分析作业指导 浓度管理图表 3 书 化工原材料领料 始业点检基准书 单 始业点检成绩表
3
54
4