改善连铸板坯表面质量的措施
连铸坯质量控制

连铸坯质量控制连铸坯质量控制引言连铸坯质量是决定钢铁产品质量的重要因素之一。
在连铸过程中,通过控制连铸坯的凝固结晶形貌、尺寸尺寸以及内部缺陷等,可以保证最终钢铁产品的质量稳定性。
本文将介绍连铸坯质量控制的基本原则和常用技术手段。
1. 连铸坯凝固结晶形貌控制1.1 凝固路径设计连铸坯的凝固路径设计是影响凝固结晶形貌的关键因素。
凝固路径包括主要凝固温度区间、凝固速度以及凝固过程中应有的温度梯度等要点。
通过科学合理地设计凝固路径,可以控制连铸坯的凝固结晶形貌,提高产品的均匀性和致密性。
1.2 凝固浸没深度控制凝固浸没深度是指连铸坯在铸机中浸没的深度。
凝固浸没深度的调整可以通过调整浇注速度、浇注高度和结晶器深度等因素来实现。
恰当地控制凝固浸没深度可以优化凝固结构,减少坯壳厚度和缩孔等缺陷的发生。
2. 连铸坯尺寸控制2.1 坯型设计连铸坯的尺寸控制需要科学合理地设计坯型。
坯型设计要考虑连铸机的性能和工艺条件,以及产品需要达到的尺寸要求。
有效的坯型设计可以保证连铸坯尺寸的精确控制,减少修磨损失并提高铸坯产量。
2.2 坯型换边控制连铸坯在连铸过程中,由于挤压力和引拉力的作用,容易发生坯型换边的情况。
坯型换边会导致铸轧过程中尺寸控制困难,甚至导致产品尺寸不合格。
通过控制连铸机的工艺参数和优化设备结构,可以有效地控制坯型换边,提高铸坯质量。
3. 连铸坯内部缺陷控制3.1 结晶器设计结晶器是连铸过程中控制坯内部缺陷的关键设备。
结晶器的设计应考虑到坯内部的流动状态,并通过合理的传热和传质方式,控制连铸坯内的气体和夹杂物等缺陷。
合理的结晶器设计可以有效减少坯内部夹杂物和气体等缺陷的产生。
3.2 液相线保护措施液相线是连铸过程中凝固结构变化的关键位置。
液相线的形成过早或过晚都会导致内部缺陷的产生。
通过合理的冷却水设定和轧制工艺,可以保证液相线的稳定形成,有效控制坯内部缺陷。
结论连铸坯质量控制是保证钢铁产品质量稳定的关键环节。
提高连铸坯内部质量的方法
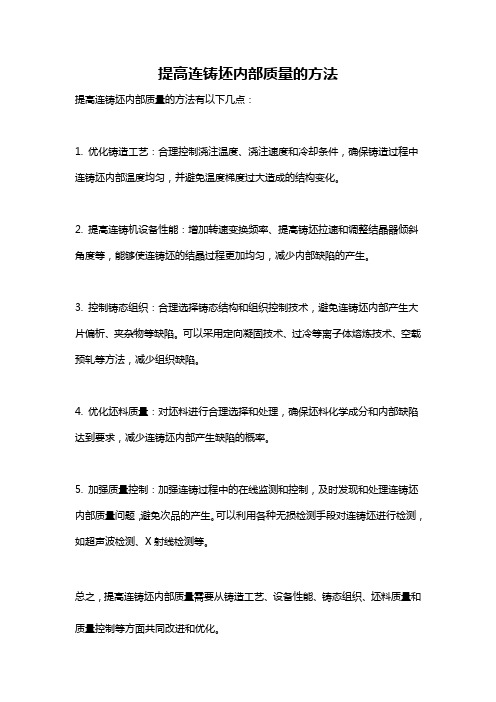
提高连铸坯内部质量的方法
提高连铸坯内部质量的方法有以下几点:
1. 优化铸造工艺:合理控制浇注温度、浇注速度和冷却条件,确保铸造过程中连铸坯内部温度均匀,并避免温度梯度过大造成的结构变化。
2. 提高连铸机设备性能:增加转速变换频率、提高铸坯拉速和调整结晶器倾斜角度等,能够使连铸坯的结晶过程更加均匀,减少内部缺陷的产生。
3. 控制铸态组织:合理选择铸态结构和组织控制技术,避免连铸坯内部产生大片偏析、夹杂物等缺陷。
可以采用定向凝固技术、过冷等离子体熔炼技术、空载预轧等方法,减少组织缺陷。
4. 优化坯料质量:对坯料进行合理选择和处理,确保坯料化学成分和内部缺陷达到要求,减少连铸坯内部产生缺陷的概率。
5. 加强质量控制:加强连铸过程中的在线监测和控制,及时发现和处理连铸坯内部质量问题,避免次品的产生。
可以利用各种无损检测手段对连铸坯进行检测,如超声波检测、X射线检测等。
总之,提高连铸坯内部质量需要从铸造工艺、设备性能、铸态组织、坯料质量和质量控制等方面共同改进和优化。
连铸板坯质量提升措施
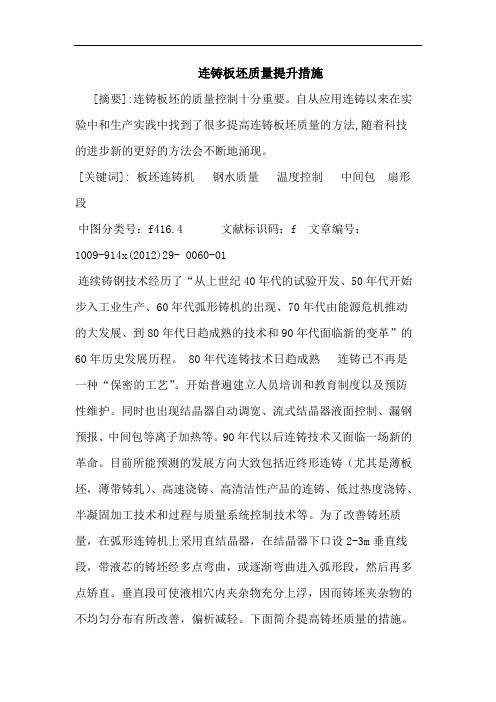
连铸板坯质量提升措施[摘要]:连铸板坯的质量控制十分重要。
自从应用连铸以来在实验中和生产实践中找到了很多提高连铸板坯质量的方法,随着科技的进步新的更好的方法会不断地涌现。
[关键词]: 板坯连铸机钢水质量温度控制中间包扇形段中图分类号:f416.4 文献标识码:f 文章编号:1009-914x(2012)29- 0060-01连续铸钢技术经历了“从上世纪40年代的试验开发、50年代开始步入工业生产、60年代弧形铸机的出现、70年代由能源危机推动的大发展、到80年代日趋成熟的技术和90年代面临新的变革”的60年历史发展历程。
80年代连铸技术日趋成熟连铸已不再是一种“保密的工艺”。
开始普遍建立人员培训和教育制度以及预防性维护。
同时也出现结晶器自动调宽、流式结晶器液面控制、漏钢预报、中间包等离子加热等。
90年代以后连铸技术又面临一场新的革命。
目前所能预测的发展方向大致包括近终形连铸(尤其是薄板坯,薄带铸轧)、高速浇铸、高清洁性产品的连铸、低过热度浇铸、半凝固加工技术和过程与质量系统控制技术等。
为了改善铸坯质量,在弧形连铸机上采用直结晶器,在结晶器下口设2-3m垂直线段,带液芯的铸坯经多点弯曲,或逐渐弯曲进入弧形段,然后再多点矫直。
垂直段可使液相穴内夹杂物充分上浮,因而铸坯夹杂物的不均匀分布有所改善,偏析减轻。
下面简介提高铸坯质量的措施。
1、对钢水质量的要求钢水要进行脱硫、脱磷、脱夹杂物的控制级温度控制。
钢水成分要进行调整,主要是调整钢水中的c、mn、si、al 等成分,称之为合金微调。
钢水进行真空冶炼,主要是脱去氢气、氧气和氮气。
对钢水进行吹氩处理,目的是均匀钢水温度,并使夹杂物上浮。
经过上述处理的高质量合格钢水,由炼钢厂送入连铸厂大包回转台上,准备浇铸。
2 、浇铸温度的控制影响铸坯质量的重要因素是: 浇铸温度、浇铸速度、冷却水量、保护渣、耐火材质等。
其中浇铸温度是十分关键的要素。
钢水的铸造温度高低与钢坯中夹杂物的多少、产生内外裂纹和中心偏析及生产操作的稳定性有十分密切的关系。
板坯连铸机保护浇注工艺优化
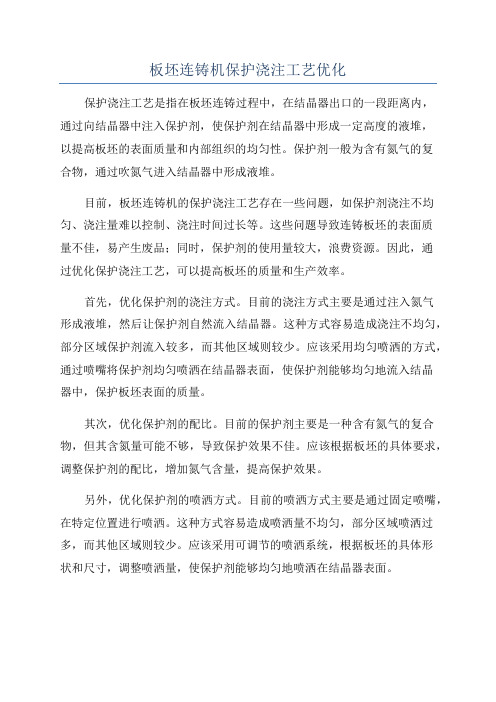
板坯连铸机保护浇注工艺优化保护浇注工艺是指在板坯连铸过程中,在结晶器出口的一段距离内,通过向结晶器中注入保护剂,使保护剂在结晶器中形成一定高度的液堆,以提高板坯的表面质量和内部组织的均匀性。
保护剂一般为含有氮气的复合物,通过吹氮气进入结晶器中形成液堆。
目前,板坯连铸机的保护浇注工艺存在一些问题,如保护剂浇注不均匀、浇注量难以控制、浇注时间过长等。
这些问题导致连铸板坯的表面质量不佳,易产生废品;同时,保护剂的使用量较大,浪费资源。
因此,通过优化保护浇注工艺,可以提高板坯的质量和生产效率。
首先,优化保护剂的浇注方式。
目前的浇注方式主要是通过注入氮气形成液堆,然后让保护剂自然流入结晶器。
这种方式容易造成浇注不均匀,部分区域保护剂流入较多,而其他区域则较少。
应该采用均匀喷洒的方式,通过喷嘴将保护剂均匀喷洒在结晶器表面,使保护剂能够均匀地流入结晶器中,保护板坯表面的质量。
其次,优化保护剂的配比。
目前的保护剂主要是一种含有氮气的复合物,但其含氮量可能不够,导致保护效果不佳。
应该根据板坯的具体要求,调整保护剂的配比,增加氮气含量,提高保护效果。
另外,优化保护剂的喷洒方式。
目前的喷洒方式主要是通过固定喷嘴,在特定位置进行喷洒。
这种方式容易造成喷洒量不均匀,部分区域喷洒过多,而其他区域则较少。
应该采用可调节的喷洒系统,根据板坯的具体形状和尺寸,调整喷洒量,使保护剂能够均匀地喷洒在结晶器表面。
最后,优化保护剂的浇注时间。
目前的浇注时间一般较长,导致保护剂的使用量较大,浪费资源。
应该根据板坯的具体要求,调整浇注时间,使保护剂的使用量能够减少,提高资源利用率。
综上所述,板坯连铸机的保护浇注工艺可以通过优化保护剂的浇注方式、配比、喷洒方式和浇注时间等方面来改善。
通过这些优化措施,可以提高板坯的表面质量和内部组织的均匀性,降低废品率,提高生产效率。
同时,通过减少保护剂的使用量,可以节约资源,实现可持续发展。
怎样提高连铸坯质量
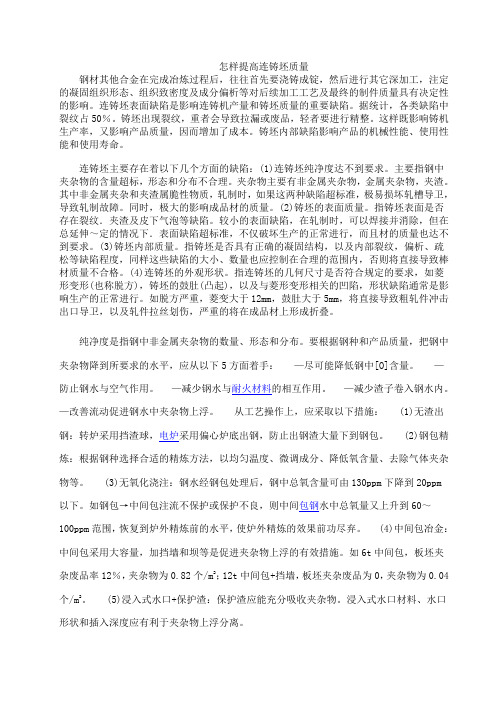
怎样提高连铸坯质量钢材其他合金在完成冶炼过程后,往往首先要浇铸成锭,然后进行其它深加工,注定的凝固组织形态、组织致密度及成分偏析等对后续加工工艺及最终的制件质量具有决定性的影响。
连铸坯表面缺陷是影响连铸机产量和铸坯质量的重要缺陷。
据统计,各类缺陷中裂纹占50%。
铸坯出现裂纹,重者会导致拉漏或废品,轻者要进行精整。
这样既影响铸机生产率,又影响产品质量,因而增加了成本。
铸坯内部缺陷影响产品的机械性能、使用性能和使用寿命。
连铸坯主要存在着以下几个方面的缺陷:(1)连铸坯纯净度达不到要求。
主要指钢中夹杂物的含量超标,形态和分布不合理。
夹杂物主要有非金属夹杂物,金属夹杂物,夹渣。
其中非金属夹杂和夹渣属脆性物质,轧制时,如果这两种缺陷超标准,极易损坏轧槽导卫,导致轧制故障。
同时,极大的影响成品材的质量。
(2)铸坯的表面质量。
指铸坯表面是否存在裂纹.夹渣及皮下气泡等缺陷。
较小的表面缺陷,在轧制时,可以焊接并消除,但在总延伸~定的情况下.表面缺陷超标准,不仅破坏生产的正常进行,而且材的质量也达不到要求。
(3)铸坯内部质量。
指铸坯是否具有正确的凝固结构,以及内部裂纹,偏析、疏松等缺陷程度,同样这些缺陷的大小、数量也应控制在合理的范围内,否则将直接导致棒材质量不合格。
(4)连铸坯的外观形状。
指连铸坯的几何尺寸是否符合规定的要求,如菱形变形(也称脱方),铸坯的鼓肚(凸起),以及与菱形变形相关的凹陷,形状缺陷通常是影响生产的正常进行。
如脱方严重,菱变大于12mm,鼓肚大于5mm,将直接导致粗轧件冲击出口导卫,以及轧件拉丝划伤,严重的将在成品材上形成折叠。
纯净度是指钢中非金属夹杂物的数量、形态和分布。
要根据钢种和产品质量,把钢中夹杂物降到所要求的水平,应从以下5方面着手:—尽可能降低钢中[O]含量。
—防止钢水与空气作用。
—减少钢水与耐火材料的相互作用。
—减少渣子卷入钢水内。
—改善流动促进钢水中夹杂物上浮。
从工艺操作上,应采取以下措施: (1)无渣出钢:转炉采用挡渣球,电炉采用偏心炉底出钢,防止出钢渣大量下到钢包。
连铸坯表面质量缺陷及处理措施

连铸坯表面质量缺陷及处理措施【摘要】对于连铸板坯而言,振痕和裂纹是其主要的质量缺陷问题。
虽然这个缺陷在大多数情况下对连铸坯的质量影响不大,但是如果不及时有效的处理调还会带来很多附加的质量问题。
尤其是在生产不锈钢和高强度钢品种时,这种质量缺陷所带来的弊端更加明显。
【关键词】连铸坯;振痕;质量影响1振痕形成机理在连铸坯生产中,振痕和裂纹是两种最为常见的质量缺陷问题,主要是由于弯月面顶端溢流造成的,该缺陷形成以后会附带其他质量缺陷一并产生。
2振痕对铸坯质量的影响振痕对连铸坯的质量影响会导致后期出现列裂纹,包括横裂纹、角部横裂纹及矫直裂纹。
如果连铸坯内掺杂的杂质较多,会导致大规模网状裂纹的出现,甚至出现穿钢现象。
如果在连铸坯出现振痕的地方晶粒很大,就会产生晶间裂纹现象,在这样的情况下需要对连铸坯修磨,从而提高成材率。
3影响振痕深度的因素振动参数对振痕形状和深度有重要影响。
其中振幅、频率、负滑脱时间及振动方式最为重要;结晶器保护渣的耗量、粘度、保温性能及表面性能等有着重要影响;.钢的凝固特性对振痕有着重要影响,特别是当钢中碳含量和钢中Ni/Cr 比影响最突出。
当钢中碳含量为0.1%左右,Ni/Cr≈0.55左右,铸坯表面振痕最深。
4减少振痕深度的措施采用小振幅(s)、高频率(f)及减少负滑脱时间(tN),可以有效的减少振痕的深度;采用非正弦振动方式可以减少振痕的深度,这是因为非正弦振动其负滑脱时间tN比正弦振动短;采用渣耗量低,粘度高的保护渣,可以使振痕深度变浅。
采用保温性能好和能增加弯月面半径的保护渣可以减少振痕深度;提高不锈钢、钢液的过热度,尤其是含钛和含铝的不锈钢对减少该钢表面振痕深度是有效的。
提高结晶器进出冷却水的温差,对减少振痕深度是有利的。
5铸坯表面裂纹5.1表面纵裂纹铸坯表面纵裂纹是铸坯最主要表面缺陷,对铸坯质量影响极大,特别是板坯和圆坯最为突出,报废量和整修量很大。
5.1.1纵裂纹类型铸坯表面沟槽纵裂纹。
连铸板坯裂纹的可能原因

连铸板坯裂纹的可能原因连铸板坯裂纹是指在连铸过程中板坯表面或内部出现的裂纹现象。
连铸板坯是制造板材的重要中间产品,其质量直接关系到最终产品的质量。
因此,了解连铸板坯裂纹的可能原因对于提高板材质量具有重要意义。
连铸板坯裂纹的可能原因主要包括以下几个方面:1. 温度控制不当:温度是连铸过程中最重要的控制参数之一。
如果连铸板坯的冷却速度过快或过慢,都会导致板坯表面或内部的温度梯度过大,从而引起裂纹的产生。
此外,连铸机的冷却水温度和流量的不稳定也会对板坯的温度分布产生影响,进而导致裂纹的形成。
2. 铸造过程中的应力:连铸板坯在冷却过程中由于温度变化而产生应力,如果应力超过了材料的承受能力,就会引起裂纹。
铸造过程中的应力主要包括热应力、冷却应力和收缩应力。
热应力是由于连铸板坯的非均匀冷却引起的,冷却应力是由于冷却水的不均匀冷却引起的,而收缩应力是由于连铸板坯的收缩引起的。
3. 材料质量问题:连铸板坯的质量直接关系到裂纹的产生。
如果原料中存在夹杂物、气孔或其他缺陷,都会在连铸过程中发展为裂纹。
此外,连铸板坯的化学成分和物理性能也会对裂纹的形成起到重要影响。
4. 连铸工艺参数调整不当:连铸过程中的各项工艺参数对于连铸板坯的质量具有重要影响。
如果连铸机的浇注速度、结晶器的冷却强度、结晶器的振动频率等参数调整不当,都会导致连铸板坯出现裂纹。
为了避免连铸板坯裂纹的产生,可以采取以下措施:1. 合理控制连铸过程中的温度,保证板坯的均匀冷却。
2. 优化连铸工艺参数,确保连铸板坯的质量稳定。
3. 加强原料检验,确保原料的质量达标。
4. 定期检查和维护连铸机设备,确保设备的正常运行。
5. 引入先进的控制技术,如自动化控制系统和智能监测设备,提高连铸过程的稳定性和可控性。
连铸板坯裂纹的产生是由多种因素共同作用的结果。
通过合理控制连铸过程中的温度、调整工艺参数、优化原料质量以及加强设备维护,可以有效地避免连铸板坯裂纹的产生,提高板材的质量。
连铸基础知识及提高连铸坯质量措施

连铸基础知识及提高连铸坯质量措施1.钢水由液体转变为固体的条件是什么?我们把一杯水(如20℃)放在-20℃的冷库里,当水的温度降到0℃时,杯子里就有晶体出现,此时是水和水的晶体共存,温度仍是0℃,只有当水完全结冰后,杯子整个温度下降到与冷库温度相同。
所以,把水开始结冰的温度叫凝固温度。
钢水的凝固结晶过程也同水一样,当温度降到凝固温度(1535℃)时,就有晶体出现。
由此可知,要实现液体转变为固体的过程,必须满足两个条件,即一定的过冷度和结晶核心。
所谓过冷度,就是实际温度低于凝固温度的度数。
如纯铁,只有过冷度达到295℃时,液体金属中许多体积很小、近程有序排列的原子集团才能形成胚胎晶核作为结晶核心而逐渐长大。
然而在实际生产中,把钢水浇到模子里,结晶所需的过冷度只有几度,这是因为:1)模子温度低,钢水温度高,模壁提供了冷却动力。
2)模型表面的凸凹不平,提供了“依托”,有利晶核形成。
3)钢水中悬浮的质点也可作为结晶核心。
2.钢水凝固过程中的收缩包括哪些?钢水由液态转变为固态,随着温度下降,收缩可分为: (1)液态收缩:由浇注温度降到液相线温度的收缩。
对于低碳钢一般为1%; (2)凝固收缩:液体完全变为固体的体积收缩。
对于钢一般为3~4%。
体积收缩会在钢锭中留下缩孔。
(3)固态收缩:从固相线温度冷却到室温的收缩。
一般为7~8%。
固态收缩表现为整个钢锭的线收缩,它与钢冷却过程的相变有关。
对钢锭产生裂纹有重要影响。
液体钢密度为7.0g/cm3,固体钢密度为7.8g/cm3,则液体变为固体收缩量为:((7.8-7.0)/7.0)×100%=11.4%,其中液态收缩量约1%,凝固收缩3~6%,固态收缩7~8%。
凝固时3~4%的体积收缩在钢锭中会留下缩孔,采用保护帽使缩孔集中在钢锭头部。
而连铸时钢水不断补充到液相,故连铸坯中无集中缩孔。
而带液芯的铸坯继续凝固时的线收缩对铸坯质量和生产安全性有重要影响。
因此结晶器应保持一定的倒锥度,二次冷却区支承辊的辊缝从上到下应符合铸坯线收缩的规律。
提高铸坯质量的措施

一、判断题1、提高铸坯质量的措施,主要是采用提高铸坯柱状晶的比率。
()2、小方坯使用刚性引锭杆时,在二冷区上段不需要支承导向装置,而二冷区下段需要导板。
()3、等表面温度变负荷冷水是指二冷区各段给水量保持不变而达到铸坯表面温度均衡的目的。
()4、钢水凝固过程中的收缩包括液态收缩、凝固收缩和固态收缩三部分。
()5、CAS—OB工艺是指在钢包内吹氩搅拌并合金化。
()6、浇注过程中结晶器水突然压力上升,流量减少的原因是水管破裂或脱落。
()7、铸坯含C量小于或等于0.17%时,方能允许进冷库冷却。
()8、结晶器长度,主要取决于拉坯速度,结晶器出口安全坯壳厚度和结晶器的冷却强度。
()9、全面质量管理的五大要素是人、机、料、法、环。
()10、炼钢中[Si]+[O2]=(SiO2)是吸热反应。
()11、含碳量在0.17~0.22%的碳素钢铸坯对热裂纹的敏感性最大。
()12、事故冷却水的水流量应不小于正常水流量的1/5。
()13、事故冷却水的冷却部位有结晶器冷却水和机械闭路水。
()14、连铸计算贡控制系统的基本结构形式有主机控制和程序控制两种类型。
()15、按正弦方式振动的结晶器,其结晶器内铸坯的平均拉速为结晶器振幅×振动频率。
()16、钢水的浇注温度就是液相线温度。
()17、CaF2在结晶器保护渣中主要起到调节碱度作用。
()18、弧形连铸机的铸坯变形量=铸坯厚度×1/弧形半径。
()19、弧形连铸机铸坯夹杂物往往聚集在1/4处的内弧位置。
()20、连铸二冷水冷却强度越大,铸坯中心等轴晶越发达,而柱状晶越窄。
()21、径电磁搅拌的铸坯等轴晶率提高,柱状晶率降低。
()22、普碳钢按技术条件所分的甲类钢是指保证化学成份,但不保证机械性能的钢。
()23、钢包底吹氩透气砖放在底面正中比放在偏心处搅拌效果要好。
()24、中间包永久层损坏修补后马上即可投用。
()25、中包修砌前必须检查包壳及耳轴是否有损坏,发现损坏必须进行焊补后方可上线使用。
连铸坯质量控制

连铸坯质量控制连铸坯质量控制1. 引言2. 连铸坯质量特点连铸坯的质量特点主要包括以下几个方面:2.1 凝固结构连铸坯是通过冷却凝固过程形成的,其凝固过程直接影响到坯体的凝固结构。
凝固结构的好坏会对后续的加工以及材料性能产生重要影响。
2.2 化学成分均匀性连铸坯的化学成分均匀性是其质量的重要指标之一。
成分不均匀容易导致后续钢材性能不稳定,从而影响到产品的质量。
2.3 表面缺陷由于连铸坯制造过程中的一些不可避免的因素,气体夹杂、氧化皮等,会在坯体表面形成一些缺陷。
这些表面缺陷会对后续产品的外观质量产生负面影响。
2.4 尺寸偏差连铸坯的尺寸偏差是指坯体的实际尺寸与标准尺寸之间的差异。
尺寸偏差会影响到钢材的加工工艺和成形质量。
3. 连铸坯质量控制因素及措施连铸坯质量的影响因素众多,包括原料质量、连铸工艺参数、设备状况等。
针对这些影响因素,可以采取以下控制措施来提高连铸坯的质量:3.1 原料质量控制通过严格控制原料的化学成分和物理性能,确保连铸坯的化学成分均匀性和机械性能达到要求。
3.2 连铸工艺参数控制连铸工艺参数的合理设置对坯体的凝固结构和表面质量具有决定性影响。
需要通过优化连铸工艺参数,如冷却水流量、浇注速度等,来控制连铸坯的质量。
3.3 设备维护与改进连铸设备的状态对连铸坯质量也有重要影响。
定期进行设备维护和检修,及时处理设备故障,可以保证设备处于良好状态,进而提高连铸坯的质量。
3.4 检测手段与技术利用先进的检测手段和技术,如超声波检测、磁力检测等,可以对连铸坯进行质量检测,及时发现问题并采取相应措施。
4.连铸坯质量控制是钢铁生产中至关重要的环节。
通过对连铸坯质量特点的分析和影响因素的控制,可以采取相应的措施来提高连铸坯的质量。
这不仅对于保证下游产品质量,还对于提高工业生产效益和降低资源消耗具有重要意义。
开展连铸坯质量控制工作是必不可少的。
连铸质量保障措施

连铸质量保障措施连铸质量保障措施引言:连铸是现代钢铁工业中重要的生产工艺,它能够高效地将熔化的钢水通过连续浇注,快速形成连续的铸坯。
然而,连铸过程中存在着各种各样的问题,如铸坯表面缺陷、内部结构不均匀等,这些问题会直接影响到最终的产品质量。
因此,为了保证连铸的质量,需要采取一系列的保障措施。
一、钢水质量控制钢水是连铸的原料,其质量直接关系到最终产品的质量。
因此,需要严格控制钢水的质量。
首先,在钢水的炼制过程中加入合适的合金元素,调整钢水的成分,保证其合金元素含量符合要求。
其次,要控制钢水的温度,以确保其在连铸过程中能够适当地流动和凝固。
最后,还需要对钢水进行连铸前的化学分析,判断其质量是否符合要求。
二、连铸机的控制系统连铸机是进行连铸的关键设备,其控制系统的稳定性和准确性对于连铸质量的保障至关重要。
为了保证连铸机的正常运行,需要采取一系列的措施。
首先,连铸机的控制系统需要精确地控制钢水的流量和速度,以确保连铸坯的形状和尺寸符合要求。
其次,需要及时检测和调整连铸机的温度,使其保持在适宜的范围内。
此外,还需要对连铸机的压力、振动等工艺参数进行监控,及时发现和解决问题。
三、结晶器的设计和改进结晶器是连铸过程中钢水凝固的关键部位,其设计和改进直接影响到连铸质量。
为了提高连铸的质量,需要采取以下的措施。
首先,结晶器的几何形状需要合理设计,以确保钢水在结晶器内的流动和凝固过程稳定和均匀。
其次,需要对结晶器进行定期的清理和维护,以保证其表面的光滑和无污染,减少对连铸坯表面缺陷的影响。
另外,还可以通过改变结晶器的冷却方式和参数,来控制钢水的凝固速率和晶粒尺寸,进一步提高连铸的质量。
四、连铸坯的在线检测和质量控制在连铸过程中,需要对连铸坯的质量进行在线检测和控制,以及时发现和解决问题。
首先,可以通过超声波检测仪器,对连铸坯进行超声波探伤,判断其内部是否存在缺陷和杂质。
其次,可以利用热像仪等仪器,对连铸坯的温度分布进行监控,以及时发现凝固不均匀等问题。
宝钢分公司4_连铸机提高板坯质量的措施
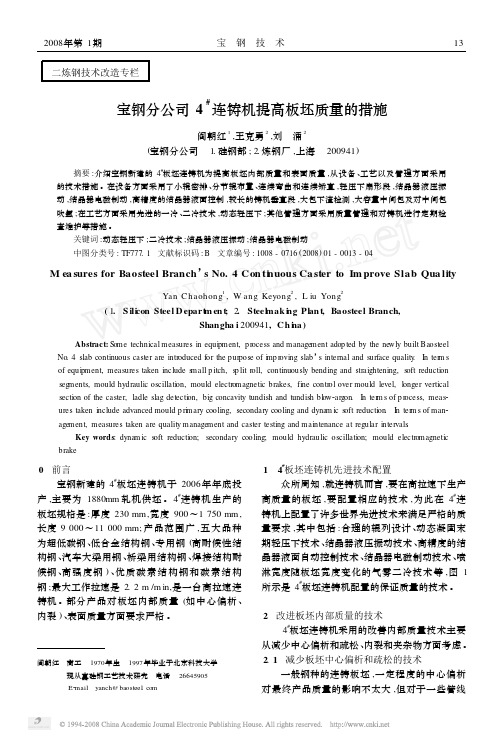
2008年第1期宝 钢 技 术二炼钢技术改造专栏宝钢分公司4#连铸机提高板坯质量的措施阎朝红1,王克勇2,刘 涌2(宝钢分公司 1.硅钢部;2.炼钢厂,上海 200941) 摘要:介绍宝钢新建的4#板坯连铸机为提高板坯内部质量和表面质量,从设备、工艺以及管理方面采用的技术措施。
在设备方面采用了小辊密排、分节辊布置、连续弯曲和连续矫直,轻压下扇形段,结晶器液压振动,结晶器电磁制动,高精度的结晶器液面控制,较长的铸机垂直段,大包下渣检测,大容量中间包及对中间包吹氩;在工艺方面采用先进的一冷、二冷技术,动态轻压下;其他管理方面采用质量管理和对铸机进行定期检查维护等措施。
关键词:动态轻压下;二冷技术;结晶器液压振动;结晶器电磁制动中图分类号:TF777.1 文献标识码:B 文章编号:1008-0716(2008)01-0013-04M ea sures for Baosteel Branch’s No.4Con ti n uous Ca ster to Im prove Slab Qua lityYan C haohong1,W ang Keyong2,L iu Yong2(1.S ili con Steel D epart m en t;2.Steel m ak i n g Pl an t,Baosteel Branch,Shangha i200941,Ch i n a) Abstract:Some technical measures in equi pment,p r ocess and manage ment adop ted by the ne wly built Baosteel No.4slab continuous caster are intr oduced f or the pur pose of i m p r oving slab’s internal and surface quality.I n ter m s of equi pment,measures taken include s mall p itch,s p lit r oll,continuously bending and straightening,s oft reducti on seg ments,mould hydraulic oscillati on,mould electr omagnetic brakes,fine contr ol over mould level,l onger vertical secti on of the caster,ladle slag detecti on,big concavity tundish and tundish bl ow2argon.I n ter m s of p r ocess,meas2 ures taken include advanced mould p ri m ary cooling,secondary cooling and dyna m ic s oft reducti on.I n ter m s of man2 age ment,measures taken are quality manage ment and caster testing and maintenance at regular intervals.Key words:dyna m ic s oft reducti on;secondary cooling;mould hydraulic oscillati on;mould electr omagnetic brake0 前言宝钢新建的4#板坯连铸机于2006年年底投产,主要为1880mm轧机供坯。
《改善连铸板坯缺陷的轧制工艺》范文

《改善连铸板坯缺陷的轧制工艺》篇一一、引言随着现代工业的快速发展,钢铁行业作为国民经济的重要支柱,其产品质量和生产效率的提升显得尤为重要。
连铸板坯作为钢铁生产中的重要环节,其质量直接影响到后续轧制工艺的效率和产品质量。
因此,如何有效改善连铸板坯的缺陷,优化轧制工艺,成为了业界关注的焦点。
本文旨在探讨连铸板坯的常见缺陷及原因,并分析轧制工艺的改进措施,以提高钢铁产品的质量和生产效率。
二、连铸板坯常见缺陷及原因分析1. 中心裂纹:中心裂纹是连铸板坯的主要缺陷之一,其形成原因主要是板坯凝固过程中的温度梯度和热应力过大。
此外,铸坯的化学成分、夹杂物、铸机振动等因素也会对中心裂纹的产生造成影响。
2. 表面裂纹:表面裂纹主要出现在板坯的表面,其形成原因包括钢水质量、结晶器振动、二次冷却制度等因素。
此外,钢中合金元素和夹杂物的含量也会对表面裂纹的产生造成影响。
3. 夹渣和夹杂物:夹渣和夹杂物主要来源于钢水的精炼过程和浇注过程中的夹杂物。
此外,铸模的质量、涂料的性能以及连铸机的维护保养也会影响夹渣和夹杂物的产生。
三、轧制工艺的改进措施针对上述连铸板坯的常见缺陷,轧制工艺的改进措施主要包括以下几个方面:1. 优化轧制参数:通过合理设定轧制温度、轧制速度、压下量等参数,使轧制过程更加稳定,减少轧制过程中的变形和裂纹等缺陷的产生。
2. 调整轧辊质量:选用高质量的轧辊,提高轧辊的硬度和耐磨性,减少轧制过程中的磨损和振动,从而降低板坯的表面裂纹和内部缺陷。
3. 强化轧前准备:在轧制前对连铸板坯进行充分的预热和除鳞处理,以去除表面的夹杂物和氧化皮,提高板坯的表面质量。
4. 优化冷却制度:根据板坯的化学成分、尺寸和轧制要求,制定合理的冷却制度,控制板坯的冷却速度和温度分布,以减少中心裂纹和表面裂纹的产生。
5. 引入无损检测技术:在轧制过程中引入无损检测技术,如超声波检测、X射线检测等,对板坯进行实时监测,及时发现并处理缺陷,提高产品的良品率。
《改善连铸板坯缺陷的轧制工艺》范文
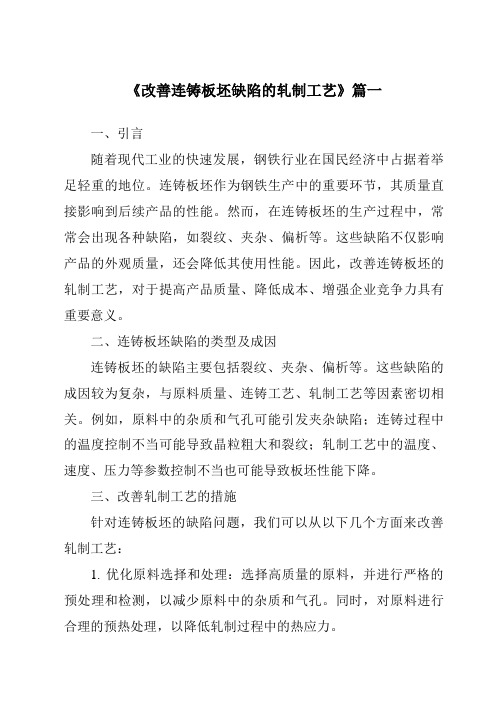
《改善连铸板坯缺陷的轧制工艺》篇一一、引言随着现代工业的快速发展,钢铁行业在国民经济中占据着举足轻重的地位。
连铸板坯作为钢铁生产中的重要环节,其质量直接影响到后续产品的性能。
然而,在连铸板坯的生产过程中,常常会出现各种缺陷,如裂纹、夹杂、偏析等。
这些缺陷不仅影响产品的外观质量,还会降低其使用性能。
因此,改善连铸板坯的轧制工艺,对于提高产品质量、降低成本、增强企业竞争力具有重要意义。
二、连铸板坯缺陷的类型及成因连铸板坯的缺陷主要包括裂纹、夹杂、偏析等。
这些缺陷的成因较为复杂,与原料质量、连铸工艺、轧制工艺等因素密切相关。
例如,原料中的杂质和气孔可能引发夹杂缺陷;连铸过程中的温度控制不当可能导致晶粒粗大和裂纹;轧制工艺中的温度、速度、压力等参数控制不当也可能导致板坯性能下降。
三、改善轧制工艺的措施针对连铸板坯的缺陷问题,我们可以从以下几个方面来改善轧制工艺:1. 优化原料选择和处理:选择高质量的原料,并进行严格的预处理和检测,以减少原料中的杂质和气孔。
同时,对原料进行合理的预热处理,以降低轧制过程中的热应力。
2. 合理控制连铸工艺参数:在连铸过程中,要严格控制温度、速度、冷却等工艺参数,以避免晶粒粗大和裂纹的产生。
同时,采用先进的连铸技术,如电磁搅拌、结晶器振动等,以改善板坯的内部质量。
3. 改进轧制工艺:在轧制过程中,要合理控制温度、速度、压力等参数,以保证板坯的轧制质量。
同时,采用先进的轧制技术,如轧制力控制、轧制速度控制等,以提高轧制过程的稳定性和精度。
4. 强化质量检测与监控:在轧制过程中,要加强质量检测与监控,及时发现并处理板坯的缺陷。
同时,建立完善的质量管理体系,对生产过程进行全面监控和管理。
四、实施效果与展望通过上述措施的实施,我们可以有效改善连铸板坯的轧制工艺,减少缺陷的产生,提高产品的质量。
具体而言,我们可以看到以下实施效果:1. 产品质量明显提高:通过优化原料、控制连铸和轧制工艺参数以及强化质量检测与监控等措施,连铸板坯的缺陷率得到有效降低,产品性能得到显著提高。
薄板坯连铸连轧设备中板表面质量改善方法探究
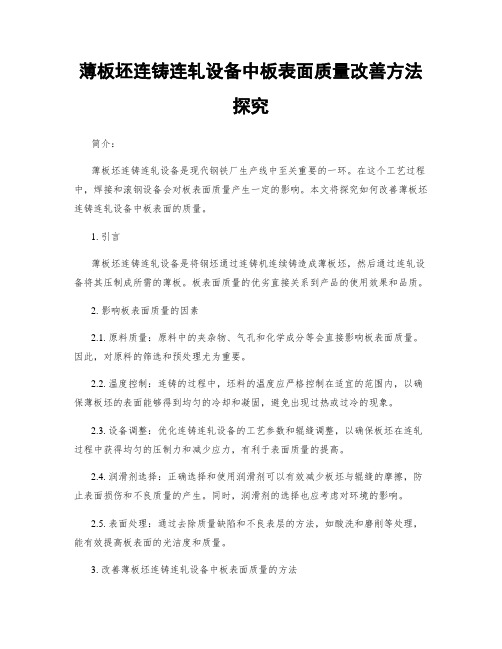
薄板坯连铸连轧设备中板表面质量改善方法探究简介:薄板坯连铸连轧设备是现代钢铁厂生产线中至关重要的一环。
在这个工艺过程中,焊接和滚钢设备会对板表面质量产生一定的影响。
本文将探究如何改善薄板坯连铸连轧设备中板表面的质量。
1. 引言薄板坯连铸连轧设备是将钢坯通过连铸机连续铸造成薄板坯,然后通过连轧设备将其压制成所需的薄板。
板表面质量的优劣直接关系到产品的使用效果和品质。
2. 影响板表面质量的因素2.1. 原料质量:原料中的夹杂物、气孔和化学成分等会直接影响板表面质量。
因此,对原料的筛选和预处理尤为重要。
2.2. 温度控制:连铸的过程中,坯料的温度应严格控制在适宜的范围内,以确保薄板坯的表面能够得到均匀的冷却和凝固,避免出现过热或过冷的现象。
2.3. 设备调整:优化连铸连轧设备的工艺参数和辊缝调整,以确保板坯在连轧过程中获得均匀的压制力和减少应力,有利于表面质量的提高。
2.4. 润滑剂选择:正确选择和使用润滑剂可以有效减少板坯与辊缝的摩擦,防止表面损伤和不良质量的产生。
同时,润滑剂的选择也应考虑对环境的影响。
2.5. 表面处理:通过去除质量缺陷和不良表层的方法,如酸洗和磨削等处理,能有效提高板表面的光洁度和质量。
3. 改善薄板坯连铸连轧设备中板表面质量的方法3.1. 优化原料:3.1.1. 加强原料筛选,在原料的供应环节对钢坯进行严格的质量控制,确保夹杂物和气孔等缺陷的最低限度。
同时,检测和控制化学成分的稳定性也非常重要。
3.1.2. 进行预处理,如脱硫和脱氧等工艺,以减少板坯内部的夹杂物和氧化物含量,提高坯料的纯净度。
3.1.3. 优化连铸工艺参数,控制铸坯温度和浇注速度,以获得更为均匀的板坯结构。
3.2. 控制温度:3.2.1. 在连铸过程中,确保板坯的温度能够适当降低,有利于表面质量的改善。
通过合理设置水冷速度和水量,调整坯料表面的冷却速度,从而减少表面凝固物的形成。
3.2.2. 对于连轧过程中温度的控制,应根据板坯的材质和厚度进行调整,避免过热和过冷导致的不均匀变形和应力积累。
连铸坯的质量控制
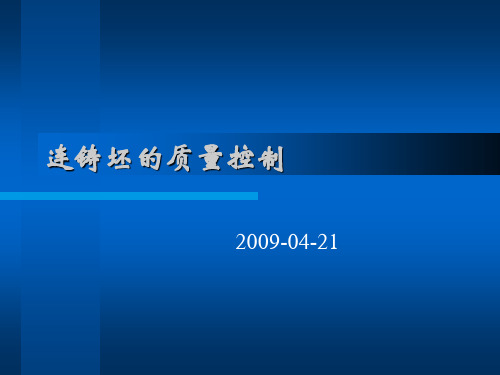
连铸坯的质量控制
2009-04-21
1、液相穴末端采用收缩 、 辊缝; 、 辊缝;2、改善铸坯导向 支撑系统; 、 支撑系统;3、更换弯曲 辊子; 、 辊子;4、调整浇铸温度 和速度; 、 和速度;5、维持正确的 结晶器锥度; 、 结晶器锥度;6、检查喷 水冷却系统; 、 水冷却系统;7、降低钢 水硫含量
夹杂物的控制
控制炼钢炉下渣量 钢包精炼渣的成分控制 保护浇铸 中间包控流装置 中间包覆盖剂 碱性包衬 钢种微细夹杂物去除 防止浇铸过程下渣和卷渣 防止Ar气泡吸附夹杂物 防止 气泡吸附夹杂物 结晶器钢水流动控制
缺
陷
原
因
主要影响因素
预防措施
内部横向裂纹
坯壳变形; 坯壳变形;坯壳受挤压
1、铸坯受弯曲力和矫 、 直力过大; 、 直力过大;2、支承辊 对正不良; 、 对正不良;3、坯壳鼓 肚;4、辊子偏心;5、 、辊子偏心; 、 钢水含硫量过大(> 钢水含硫量过大(> 0.02%) )
1、改善铸坯导向支撑系 、 统;2、更换弯曲辊子; 、更换弯曲辊子; 3、调整浇铸温度与速度; 、调整浇铸温度与速度; 4、降低钢水硫含量;5、 、降低钢水硫含量; 、 降低辊子接触压力
内 容
铸坯表面质量及控制 铸坯内部质量及控制 连铸坯形状缺陷及控制
铸坯表面质量
控制表面质量的必要性 表面缺陷形成原因:较为复杂, 表面缺陷形成原因:较为复杂,但总体 来讲, 来讲,主要是受结晶器内钢液凝固所控 制。
连铸坯质量攻关方案

连铸坯质量攻关方案
连铸坯是钢铁工业的原材料之一,其质量直接影响到后续生产工艺和产品质量。
因此,连铸坯质量攻关方案的制定至关重要。
应该在原料的选择和准备上下功夫。
应选用优质的原料,如高品质的钢坯或铁合金,并且要对原料进行充分的预处理,包括去除杂质、调整成分、控制温度等。
这样可以有效地提高连铸坯的质量。
需要重视浇注过程的控制。
在浇注过程中,应该控制铁水的流速和流量,保证铁水充分分散和均匀流动,并且要控制浇注速度和温度,以保证连铸坯的形状和内部结构。
同时,要加强对连铸坯的实时监测,包括温度、形状、结构等方面的监测,及时发现问题并进行调整。
第三,应该注重连铸坯的后续处理。
在连铸坯的冷却过程中,应该控制冷却速度和温度,以保证连铸坯的内部结构和性能。
同时,要加强对连铸坯的加工和检测,包括切割、去除表面缺陷等方面的加工和化学成分、机械性能等方面的检测,确保连铸坯的质量达到要求。
需要加强对连铸坯质量的管理和评估。
应该建立完善的质量管理体系,包括质量控制点的设立、过程控制、质量评估等方面的管理,保证连铸坯的质量稳定和可控。
同时,要加强对连铸坯质量的评估和反馈,及时发现问题和优化改进措施。
连铸坯质量攻关方案的制定和实施是钢铁工业生产过程中的重要环节。
只有加强原材料的选择和准备、控制浇注过程、注重后续处理、加强质量管理和评估等方面的工作,才能有效地提高连铸坯的质量,为钢铁生产提供优质的原材料。
- 1、下载文档前请自行甄别文档内容的完整性,平台不提供额外的编辑、内容补充、找答案等附加服务。
- 2、"仅部分预览"的文档,不可在线预览部分如存在完整性等问题,可反馈申请退款(可完整预览的文档不适用该条件!)。
- 3、如文档侵犯您的权益,请联系客服反馈,我们会尽快为您处理(人工客服工作时间:9:00-18:30)。
的试验冷却制度 ,可以消除板坯表面过冷,包括局
部过冷(低于 920℃)。
从高温测量的结果中,得出结论 :采用原冷却
制度时,在 909—943 ̄C温度范围内,板坯塑性值在
25%~35%范围中;采用试验冷却制度时,在 938—
975 ̄C温度范 围内,板坯塑性值在 30%~65%范围
按上述 布置喷嘴 ,以避免板坯垂直段 区域 与
结 果 如表 1所示 。
表 1些里垩塑 廑
/m/min 原冷却制度 试 验冷却制度
0.6 0.7 O.8
909 922 943
938 953 975
由表 1可见 ,与原冷却制度相 比,采用试验冷
5号板坯连铸机带有垂直段和弯曲段 ,板坯表 0.8m/min时 ,采用红外测温仪(TC.800)N温。测温
面在弯曲处要承受附加 的拉应力 ,这不 同于弧型连 铸 机 。
5号连铸机所生产的板坯规格为 250 ̄1 250 2 350mm,二次冷却系统分为垂直段冷却区和弯曲 段 9个冷却 区,二冷参数取决板坯断面尺寸 、钢号 及浇铸速度 。垂直段冷却区采用水冷 ,该冷却区用 于冷却所有规格板坯 的宽边和窄边 ,其余弯曲段 9 个冷却 区均采用水 、汽混合 的气雾冷却方式。
锰 含 量 <0.80%的低 碳 和 中碳 钢 ,宽度 为 1 250~1 750mm 的板坯 ,其冷却制度按下述流程进 行 :
在弯曲段第 1个冷却 区,宽边侧每边有 4个中 心喷嘴和 2个平面射流喷嘴 ,通过调整总喷流宽度 (能盖过整个板坯宽度)来冷却板坯窄边 ;从第 2个 冷却区至第 9个冷却 区,宽侧均采用两个喷嘴(达到 总射流宽度),能冷却板坯表面的 75%区域 ;板坯窄 边侧的第 2个冷却 区中采用 5个串行排列的圆形射 流 喷嘴 。
幅 ;振频 ;横 向裂纹
参数(减小板坯振痕深度和降低铸机故障率)等。
冶金行业为降低生产成本,采用 了各种节能降
降低板坯冷却强度可采用 “弱冷”制度和减少
耗措施 ,并采取缩减基建费用 、减少废品、改善产 二冷区数 。板坯冷却 区从第 1区到第 6区,窄侧不
品生产工艺等手段 ,从而达到减产增效的 目的。
冷却 。这样 ,板坯表面二冷水单耗降低了 33.5%(相
俄罗斯马格尼托哥尔斯克钢铁公司炼钢厂的 5 对地 )。
号连铸机 ,依照设计能力 ,可通过提高板坯质量、
在浇铸 20钢时 ,对比原冷却制度和试验冷却
开 发新 品种 ,来满 足 用户要 求 。
制度下 ,弯曲段板坯表面温度的变化。在拉速 0.6~
却制度时 ,其冷却水单位消耗量更低 ,板坯在弯曲
段 的温度为 938~975 ̄C(随拉速而变),平均增加了
31℃ 。
俄罗斯一些研究单位发现 :板坯表面温度降至
1000 ̄C以下时 ,其塑性降低(相对收缩率 ),大部
分试样在 775℃ 900 ̄C时其塑性最低(Il,=l5%)。根
据获得的 “温度——塑性”特点的关系 ,建议采用
晶器振动等 ,通过对这些工艺参数的优化 ,减少了 生在靠近角区。
板坯缺陷,降低 了热轧板在 “结疤”和 “裂纹”方
为了进一步减少裂纹的产生 ,必须提高板坯进
面 的缺陷 率 。
入弯曲段的温度 ,可以通过如下措施来实现 :如,
关键词:板坯连铸 ;二次冷却 ;板坯拉速;振 提高板坯拉速 、降低二冷水单耗 、调整结晶器振动
42
本钢 技术
2011年第 4期
改善连铸板坯表 面质量 的措施
M。M 3axapo基, 丑.t3 tope ̄ o等 马格尼 托哥 尔斯克 钢铁公 司
(俄 罗斯 ,马 格尼托 哥 尔斯 克 市)
摘 要 :为改善连铸板坯质量 ,对浇铸工艺参 水、汽射流的直接作用 ,可 以降低垂直段 的冷却强 数进行了研究和确定 ,如板坯拉速 、二冷制度及结 度 ,避免在弯曲段区形成横向裂纹 ,这种裂纹常发