甲醇生产技术第四章变换
净化工艺介绍-变换

27
• 1.10.2压力: • 变换反应前后气体体积不变,所以提高压
力不能改变反应过程的平衡状态,但提高 压力后,反应物浓度增加,促进了分子间 的接触,并且还能增加催化剂内表面的利 用率及气体与催化剂的接触时间,故其空 速随压力提高而加大,从而提高了催化剂 的生产强度。
体 积 33. 50.67 13.86 0.03 0.56 0.1 1.19 0.0
比 47
4
8
9
进入第一中压废热锅炉(E2001),与锅炉给 水换热、降温后经第一水分离器(V2001)分离掉 冷凝液后工艺气压力约为6.44MPa左右,温度 为235℃左右,汽气(干)比约为1.12,煤气总 量约:257604Nm3/h、其中,水汽: 136530Nm3/h,干气:121074 Nm3/h。冷凝液 :干气成分如下:
24
T2003
• 来自水洗塔(T2001A/T2001B)的低温冷凝液经 汽提塔(T2003)塔顶冷凝器(E2017)与上升 的汽提气换热后进入冷凝液汽提塔(T2003)上 部。来自气化渣水处理工序的闪蒸气进入冷凝液 汽提塔(T2003)中部,0.3MPa(G)的低压水 蒸汽通入冷凝液汽提塔(T2003)下部气提出闪 蒸气和冷凝液中的NH3及H2S,汽提气送往硫回 收工序。汽提塔(T2003)底部液体经低压冷凝 液泵(P2006A/B)升压至1.58MPa(G),送至气 化渣水除氧器。
的氨洗去后送低温甲醇洗工段。出变换工 段变换气压力:6.32Mpa、温度:40℃、 煤气总量:148473Nm3/h、成分如下:
成分 H2 CO CO2
体 积 47. 20.06 31.32 比 09
煤制甲醇变换工段原理

煤制甲醇变换工段原理今天咱们来唠唠煤制甲醇里超级有趣的变换工段原理呀。
你知道吗,煤制甲醇这个事儿可复杂又神奇啦。
那变换工段呢,就像是一个魔法转换站。
咱们从煤开始说起哈,煤经过一系列处理得到的原料气里有一氧化碳(CO)呢。
这一氧化碳在变换工段里可有大文章可做啦。
变换工段主要就是把一氧化碳和水蒸气(H₂O)进行反应。
这个反应就像是一场有趣的舞会。
一氧化碳和水蒸气这俩小伙伴在合适的条件下,就开始欢快地互动起来。
它们的反应方程式是CO + H₂O = CO₂+ H₂,这个反应是可逆反应哦。
这就好比两个人跳舞,一会儿向左转(正向反应),一会儿向右转(逆向反应)。
那这个反应为啥要在变换工段发生呢?这是因为呀,在煤制甲醇的整个流程里,后面的反应对原料气的组成有要求呢。
这个反应能把一氧化碳转化成二氧化碳和氢气,这样氢气的量就增加啦。
氢气可是制造甲醇的重要原料呢,就像盖房子的重要砖块一样。
而且呀,调整一氧化碳和氢气的比例,能让后面的合成甲醇反应更顺利地进行。
在这个变换工段里,反应得有合适的温度、压力和催化剂这些“小助手”。
温度就像舞会的音乐节奏一样,不能太快也不能太慢。
如果温度太低,一氧化碳和水蒸气就懒洋洋的,不太愿意反应;要是温度太高呢,又会有一些不好的副反应发生,就像舞会上突然来了几个捣乱的人。
一般来说,这个温度会控制在一个比较合适的范围,不同的工艺可能会有一些小差异。
压力呢,就像是舞会的场地大小。
合适的压力能让一氧化碳和水蒸气靠得更近,更容易反应。
压力太大或者太小都不太好。
就像人太多或者太少的场地都不适合愉快地跳舞一样。
催化剂就更神奇啦,它就像是舞会的主持人。
有了它,一氧化碳和水蒸气反应的速度就会大大加快。
常见的变换催化剂有铁铬系催化剂和铜锌系催化剂。
铁铬系催化剂就像一个很有经验的老主持人,比较适合在高温下工作。
铜锌系催化剂呢,就像是年轻活力的主持人,在低温下表现很棒。
这个变换工段里的设备也很有趣呢。
有变换炉,就像一个巨大的反应城堡,一氧化碳和水蒸气就在这个城堡里进行它们的神奇反应。
甲醇的工艺流程
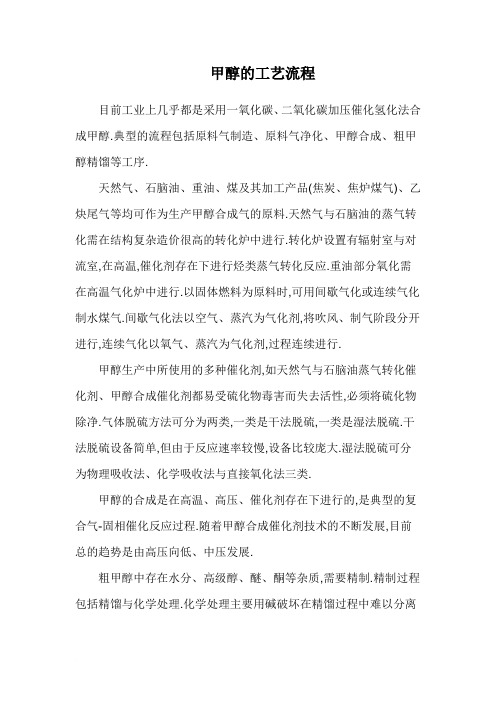
甲醇的工艺流程目前工业上几乎都是采用一氧化碳、二氧化碳加压催化氢化法合成甲醇.典型的流程包括原料气制造、原料气净化、甲醇合成、粗甲醇精馏等工序.天然气、石脑油、重油、煤及其加工产品(焦炭、焦炉煤气)、乙炔尾气等均可作为生产甲醇合成气的原料.天然气与石脑油的蒸气转化需在结构复杂造价很高的转化炉中进行.转化炉设置有辐射室与对流室,在高温,催化剂存在下进行烃类蒸气转化反应.重油部分氧化需在高温气化炉中进行.以固体燃料为原料时,可用间歇气化或连续气化制水煤气.间歇气化法以空气、蒸汽为气化剂,将吹风、制气阶段分开进行,连续气化以氧气、蒸汽为气化剂,过程连续进行.甲醇生产中所使用的多种催化剂,如天然气与石脑油蒸气转化催化剂、甲醇合成催化剂都易受硫化物毒害而失去活性,必须将硫化物除净.气体脱硫方法可分为两类,一类是干法脱硫,一类是湿法脱硫.干法脱硫设备简单,但由于反应速率较慢,设备比较庞大.湿法脱硫可分为物理吸收法、化学吸收法与直接氧化法三类.甲醇的合成是在高温、高压、催化剂存在下进行的,是典型的复合气-固相催化反应过程.随着甲醇合成催化剂技术的不断发展,目前总的趋势是由高压向低、中压发展.粗甲醇中存在水分、高级醇、醚、酮等杂质,需要精制.精制过程包括精馏与化学处理.化学处理主要用碱破坏在精馏过程中难以分离的杂质,并调节PH.精馏主要是除去易挥发组分,如二甲醚、以及难以挥发的组分,如乙醇高级醇、水等.甲醇生产的总流程长,工艺复杂,根据不同原料与不同的净化方法可以演变为多种生产流程.下面简述高压法、中压法、低压法三种方法及区别高压法高压工艺流程一般指的是使用锌铬催化剂,在300—400℃,30MPa高温高压下合成甲醇的过程.自从1923年第一次用这种方法合成甲醇成功后,差不多有50年的时间,世界上合成甲醇生产都沿用这种方法,仅在设计上有某些细节不同,例如甲醇合成塔内移热的方法有冷管型连续换热式和冷激型多段换热式两大类,反应气体流动的方式有轴向和径向或者二者兼有的混合型式,有副产蒸汽和不副产蒸汽的流程等.近几年来,我国开发了25-27MPa压力下在铜基催化剂上合成甲醇的技术,出口气体中甲醇含量4%左右,反应温度230-290℃.中压法中压法是在低压法研究基础上进一步发展起来的,由于低压法操作压力低,导致设备体积相当庞大,不利于甲醇生产的大型化.因此发展了压力为10MPa左右的甲醇合成中压法.它能更有效地降低建厂费用和甲醇生产成本.例如ICI公司研究成功了51-2型铜基催化剂,其化学组成和活性与低压合成催化剂51-1型差不多,只是催化剂的晶体结构不相同,制造成本比51-1型高贵.由于这种催化剂在较高压力下也能维持较长的寿命,从而使ICI公司有可能将原有的5MPa的合成压力提高到l0MPa,所用合成塔与低压法相同也是四段冷激式,其流程和设备与低压法类似.低压法ICl低压甲醇法为英国ICl公司在1966年研究成功的甲醇生产方法.从而打破了甲醇合成的高压法的垄断,这是甲醇生产工艺上的一次重大变革,它采用51-1型铜基催化剂,合成压力5MPa.ICl法所用的合成塔为热壁多段冷激式,结构简单,每段催化剂层上部装有菱形冷激气分配器,使冷激气均匀地进入催化剂层,用以调节塔内温度.低压法合成塔的型式还有联邦德国Lurgi公司的管束型副产蒸汽合成塔及美国电动研究所的三相甲醇合成系统.70年代,我国轻工部四川维尼纶厂从法国Speichim公司引进了一套以乙炔尾气为原料日产300吨低压甲醇装置(英国ICI专利技术).80年代,齐鲁石化公司第二化肥厂引进了联邦德国Lurge公司的低压甲醇合成装置.编辑本段甲醇的具体生产方法1. 天然气制甲醇的生产方法天然气是制造甲醇的主要原料.天然气的主要组分是甲烷,还含有少量的其他烷烃、烯烃与氮气.以天然气生产甲醇原料气有蒸汽转化、催化部分氧化、非催化部分氧化等方法,其中蒸汽转化法应用得最广泛,它是在管式炉中常压或加压下进行的.由于反应吸热必须从外部供热以保持所要求的转化温度,一般是在管间燃烧某种燃料气来实现,转化用的蒸汽直接在装置上靠烟道气和转化气的热量制取.由于天然气蒸汽转化法制的合成气中,氢过量而一氧化碳与二氧化碳量不足,工业上解决这个问题的方法一是采用添加二氧化碳的蒸汽转化法,以达到合适的配比,二氧化碳可以外部供应,也可以由转化炉烟道气中回收.另一种方法是以天然气为原料的二段转化法,即在第一段转化中进行天然气的蒸汽转化,只有约1/4的甲烷进行反应,第二段进行天然气的部分氧化,不仅所得合成气配比合适而且由于第二段反应温度提高到800℃以上,残留的甲烷量可以减少,增加了合成甲醇的有效气体组分.天然气进入蒸汽转化炉前需进行净化处理清除有害杂质,要求净化后气体含硫量小于0.1mL/m3.转化后的气体经压缩去合成工段合成甲醇.2. 煤、焦炭制甲醇的生产方法煤与焦炭是制造甲醇粗原料气的主要固体燃料.用煤和焦炭制甲醇的工艺路线包括燃料的气化、气体的脱硫、变换、脱碳及甲醇合成与精制.用蒸汽与氧气(或空气、富氧空气)对煤、焦炭进行热加工称为固体燃料气化,气化所得可燃性气体通称煤气是制造甲醇的初始原料气,气化的主要设备是煤气发生炉,按煤在炉中的运动方式,气化方法可分为固定床(移动床)气化法、流化床气化法和气流床气化法.国内用煤与焦炭制甲醇的煤气化——般都沿用固定床间歇气化法,煤气炉沿用UCJ炉.在国外对于煤的气化,目前已工业化的煤气化炉有柯柏斯-托切克(Koppers-Totzek)、鲁奇(Lurge)及温克勒(Winkler)三种.还有第二、第三代煤气化炉的炉型主要有德士古(Texaco)及谢尔-柯柏斯(Shell--Koppers)等.用煤和焦炭制得的粗原料气组分中氢碳比太低,故在气体脱硫后要经过变换工序.使过量的一氧化碳变换为氢气和二氧化碳,再经脱碳工序将过量的二氧化碳除去.原料气经过压缩、甲醇合成与精馏精制后制得甲醇.3.油制甲醇的生产方法工业上用油来制取甲醇的油品主要有二类:一类是石脑油,另一类是重油.原油精馏所得的220℃以下的馏分称为轻油,又称石脑油.以石脑油为原料生产合成气的方法有加压蒸汽转化法,催化部分氧化法、加压非催化部分氧化法、间歇催化转化法等.目前用石脑油生产甲醇原料气的主要方法是加压蒸汽转化法.石脑油的加压蒸汽转化需在结构复杂的转化炉中进行.转化炉设置有辐射室与对流室,在高温、催化剂存在下进行烃类蒸汽转化反应.石脑油经蒸汽转化后,其组成恰可满足合成甲醇之需要.既无需在转化前后补加二氧化碳或设二段转化,也无需经变换、脱碳调整其组成.重油是石油炼制过程中的一种产品,根据炼制方法不同,可分为常压重油、减压重油、裂化重油及它们的混合物.以重油为原料制取甲醇原料气有部分氧化法与高温裂解法两种途径.裂解法需在1400℃以上的高温下,在蓄热炉中将重油裂解,虽然可以不用氧气,但设备复杂,操作麻烦,生成炭黑量多.重油部分氧化是指重质烃类和氧气进行燃烧反应,反应放热,使部分碳氢化合物发生热裂解,裂解产物进一步发生氧化、重整反应,最终得到以H2、CO为主,及少量CO2、CH4的合成气供甲醇合成使用.重油部分氧化法所生成的合成气,由于原料重油中碳氢比高,合成气中一氧化碳与二氧化碳含量过量,需将部分合成气经过变换,使一氧化碳与水蒸气作用生成氢气与二氧化碳,然后脱除二氧化碳,以达到合成甲醇所需之组成.合成后的粗甲醇需经过精制,除去杂质与水,得到精甲醇.4.联醇生产方法与合成氨联合生产甲醇简称联醇,这是一种合成气的净化工艺,以替代我国不少合成氨生产用铜氨液脱除微量碳氧化物而开发的一种新工艺.联醇生产的工艺条件是在压缩机五段出口与铜洗工序进口之间增加一套甲醇合成的装置,包括甲醇合成塔、循环机、水冷器、分离器和粗甲醇贮槽等有关设备,工艺流程是压缩机五段出口气体先进人甲醇合成塔,大部分原先要在铜洗工序除去的一氧化碳和二氧化碳在甲醇合成塔内与氢气反应生成甲醇,联产甲醇后进入铜洗工序的气体一氧化碳含量明显降低,减轻了铜洗负荷,同时变换工序的一氧化碳指标可适量放宽,降低了变换的蒸汽消耗,而且压缩机前几段气缸输送的一氧化碳成为有效气体,压缩机电耗降低.联产甲醇后能耗降低较明显,可使每吨氨节电50kw.h,节省蒸汽0.4t,折合能耗为200万kJ.联醇工艺流程必须重视原料气的精脱硫和精馏等工序,以保证甲醇催化剂使用寿命和甲醇产品质量。
甲醇装置操作规程 变换单元

变换单元操作规程第一章产品说明变换装置是煤气化的下游装置,其目的和作用是把粗煤气中过高的CO变换成CO2,同时副产H2,以调整粗煤气中CO和H2的含量,满足甲醇合成装置对氢碳比的要求。
来自煤气化装置的粗煤气经过三台变换炉变换后,变换气去低温甲醇洗装置。
装置运行期间,需要外界提供循环冷却水、锅炉给水、中压蒸汽、低压蒸汽、高压蒸汽、脱盐水、低压氮气、中压氮气、仪表空气、工厂空气。
生产过程中产生的变换冷凝液汇合冷却后送至污水处理系统。
1 生产能力变换装置对粗煤气的额定处理能力为241348.8Nm3/h,装置的操作弹性为50%至120%,粗煤气、变换气的组成和工艺参数情况如下表:表1 粗煤气的工艺参数表表2 变换气的工艺参数表2、物料消耗及能耗变换装置在生产过程中消耗变换催化剂QDB-04;催化剂在使用初期需要进行升温硫化还原,硫化剂采用纯品二硫化碳。
见下表:表3 化工原、辅材料消耗表表4 公用工程消耗表3、催化剂的特性表5:QDB-04催化剂物化性能表6:QXB-01吸附剂物化性能催化剂QDB-04有以下特点:(1)添加特殊助剂并使用活性载体,由于助剂、活性载体与活性组份三者的协同效应,提高了催化剂的变换活性,特别是提高了催化剂在高温低硫下的变换活性及活性稳定性。
(2)添加复合碱性物料,增强了催化剂的表面碱性,提高了催化剂的有机硫氢解和水解功能,特别是在反应温度较低的条件下,催化剂对有机硫的氢解和水解活性。
同时由于有机硫转化活性的提高,在原料气中H2S较低的情况下,能保持自身的硫化形态,从而可以提高催化剂的脱氧性能。
(3)添加抗水合助剂,减弱了Al2O3组份的水合反应能力,从而提高了催化剂的抗水合性能,使催化剂在压力较高的苛刻条件下使用时,不水合、不相变,具有较高的抗水合性和结构稳定性。
新鲜催化剂中活性组份钴、钼以氧化钴、氧化钼的形式存在,使用时要先进行硫化,使活性金属组份由氧化物转变成硫化物。
通常的硫化方法对QDB-04催化剂都适用,即:可以用含硫工艺气体硫化,也可用硫化剂单独硫化。
甲醇原料气中一氧化碳的变换—变换的原理

三、 甲醇原料气变换的催化剂
✓ (三)耐硫变换催化剂—— 2.硫化
钴钼系耐硫催化剂其主要活性组分氧化钴和氧化钼在使用前,需将其转化为硫化钴硫化钼才具
有变换活性,这一过程称为硫化。对催化剂进行硫化,可用含氢的二硫化碳,也可直接用硫化氢或用
未脱硫的原料气。为了缩短硫化时间,保证活化的好,工业上一般都采用在干半水煤气中加CS2为硫
=-41.19kJ/mol (1)
✓ 该反应特点为可逆、放热、反应前后体积不变,反应速率比较慢,只有在催化剂的作用下才
能实现工业生产。
✓ 此外,一氧化碳与氢之间还可发生下列反应
✓
CO + H2 = C +H2O
✓
CO + 3H2 = CH4 +H2O
二、甲醇原料气变换的基本原理
1.化学平衡
✓ 由于变换催化剂对反应(1)具有良好的选择性,降低了反应温度,抑制了其它副反应的发生。 因此,仅需考虑反应(1)的化学平衡。
-△H/
( kJ/mol
41.19
)
40.07
39.67
39.25
38.78
38.32
37.86
37.30
36.82
三、 甲醇原料气变换的催化剂
✓ (一)高(中)温变换催化剂——1.催化剂的性能 铁-铬系催化剂的一般化学组成为: Fe2O3
80%~90%, Cr2O3 7%~11%,并含有少量的K2O、 MgO、Al2O3等。四氧化三铁是铁-铬系催化剂的活性 组分,还原前以氧化铁的形态存在。氧化铬是重要的 结构性促进剂 。
晶。但单纯的铜微晶在操作温度下极易烧结,导致微晶增大,比面积减小,活性下降和寿命缩短。 为此,在催化剂中加入氧化锌、氧化铝、氧化铬等添加物。
2020年智慧树知道网课《甲醇生产技术》课后习题章节测试满分答案

绪论单元测试1【单选题】(5分)甲醇的物理性质正确的为()。
A.分子量为32.042B.无色无味C.不易挥发D.不与水混溶2【单选题】(5分)以下对于甲醇的贮存论述的是()。
A.干燥、通风、低温B.隔绝热源和火源C.贮存期1年D.避免日光直射3【单选题】(5分)甲醇的闪点(闭口)为()℃。
A.12.2B.30C.35D.20.54【单选题】(5分)合成甲醇原料气的有效气体成份是()。
A.二氧化碳、一氧化碳和氢气B.一氧化碳和水蒸汽C.一氧化碳和氢气D.二氧化碳和氢气5【单选题】(5分)工业甲醇的蒸汽含量在空气中的爆炸范围是()。
A.13.5%~30.5%B.8.5%~50.5%C.10%~40%D.6%~36.5%6【判断题】(5分)目前工业上几乎都是采用一氧化碳、二氧化碳加压催化法合成甲醇。
A.对B.错7【判断题】(5分)CO能使人中毒。
A.对B.错8【判断题】(5分)甲醇对人体主要作用于神经系统,因此可用做麻醉剂。
A.对B.错9【判断题】(5分)甲醇结构简单,不能与大部分化合物发生化学反应。
A.对B.错第一章测试1【判断题】(5分)对于SHELL炉来说,煤的灰熔点越高越好。
A.错B.对2【单选题】(5分)德士古水煤浆气化法属于()A.固定床气化B.流化床气化C.气流床气化【判断题】(5分)石灰石的添加,可以降低煤的灰熔点,但是,用量不能太大,否则会造成系统结垢现象加剧。
A.错B.对4【判断题】(5分)为防止腐蚀,水煤浆PH值一般控制为酸性。
A.错B.对5【判断题】(5分)德士古气化温度选择的原则应该是在保证液态排渣的前提下,尽可能维持较低的操作温度。
A.B.对6【判断题】(5分)在水煤浆制备过程中,磨煤的方式分为干法磨煤和湿法磨煤,目前工业上应用比较广泛的是干法磨煤。
A.对B.错7【判断题】(5分)旋风分离器工作的原理是利用气流在旋转的过程中产生的惯性离心力来实现气固、气液分离。
A.错B.对8【判断题】(5分)急冷式德士古气化炉是用急冷室的水,与高温水煤气直接接触,水煤气被急速冷却,并除去大部分灰渣。
甲醇生产操作PPT学习教案
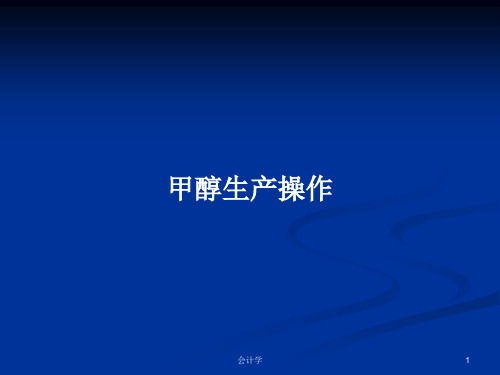
二、精脱硫的方法
1、钴钼加氢串氧化锌高温精脱硫(传统方法) 缺点:能耗高,开车时间长,脱硫效率受温度影响明显, 催化剂需要硫化处理,容易出现冷热病。
2、COS水解串联常温氧化锌脱硫 3、JTL-1常温精脱硫
开发了比常温氧化锌硫容高4倍,而价格仅为其1/4的特种 活性碳和特种氧化铁。 4、JTL-4常温精脱硫 5、JTL-5常温精脱硫
第19页/共78页
§3.4脱除氯
一、脱氯的原因
低压甲醇合成用铜基催化剂,氯易与其中的锌反应生成氯化锌,其熔点很低,在催化剂操 作温度下易为熔融体,破坏了对铜基催化剂的活性。另外,氯化锌是水溶性的,会使整 颗催化剂内外中毒,比硫毒更为厉害,所以铜基催化剂特别重视脱除微量氯。
第20页/共78页
二、脱氯的方法 1、物理吸附性脱氯剂,一般采用活性氧化铝、分子筛、和
如果采用较低的空速,催化剂生产强度较低,但动力消耗小,热能的利用价值 高。如果采用较高的空速,催化剂的生产强度提高,但动力消耗增加,热能 的利用价值降低。
另外,空速增大到一定程度后,催化床温度将不能维持,在甲醇合成中,空速 一般控制在10000~30000h-1。
第33页/共78页
7、氢碳比的控制对甲醇合成的影响
1、甲醇是重要的一碳化工基础产品和有机化工原料,广泛应用于有机合成、燃料、医药、 涂料和国防等工业。
2、甲醇是清洁燃料,可以作为汽油的添加剂。 3、是较好的人工合成蛋白的原料,蛋白转化率高,无毒性,价格便宜。 4、是直接合成乙酸的原料。 5、甲醇化工已成为化学工业中一个重要的领域,而其潜在的耗用量远远超过其化工用途。
第21页/共78页
第四章 甲烷及烃类气的转化
§4.1一段转化和二段转化 §4.2原料气的变换 §4.3多余二氧化碳的脱除
甲醇生产操作规程

甲醇生产操作规程甲醇是一种重要的工业原料,其生产操作过程需要严格的规范和注意事项。
为了确保甲醇生产过程的稳定性和安全性,制定和执行甲醇生产操作规程是必要的。
甲醇生产操作规程的主要目的是规范甲醇生产的步骤、工艺参数、操作方法和相关安全事项,保证每一步操作都符合标准和要求。
具体包括以下几个方面的内容:一、甲醇生产的步骤甲醇的生产步骤主要包括燃气蒸汽重整、变换反应、分离纯化和输送四个步骤。
在每个步骤中,都有严格的工艺要求和操作步骤,需要进行详细的说明和规范。
1.燃气蒸汽重整操作规程燃气蒸汽重整是甲醇的重要生产工艺之一,其操作规程需要包括进料温度、进料压力、出料温度和压力、蒸汽流量、空气流量等关键参数的规定,并对操作人员的职责进行明确的安排。
2.变换反应操作规程变换反应是甲醇生产过程中的核心步骤,需要严格控制反应温度、压力、进料流量、空气流量等操作参数。
在操作规程中,需要详细说明每个操作参数的上限和下限,确保反应的稳定性和效率。
3.分离纯化操作规程分离纯化是甲醇生产过程中一个非常重要的步骤,需要规范化的操作。
需要详细说明各种分离设备、级数以及温度、压力控制等参数,确保甲醇可以被有效地分离和纯化。
4.输送操作规程甲醇生产过程中,输送是核心步骤之一,需要明确的规范化操作。
需要详细说明输送的管道、阀门、流量计等设备的使用和维护方法,确保甲醇能够被从生产区域输送到存储和使用的区域。
二、工艺参数的监控甲醇生产经常需要在特定的环境下进行,需要充分的监控和记录工艺参数。
比如,需要进行定期的振动监测、温度检测、压力检测、流量检测等,确保甲醇制造的时候运转顺畅。
三、安全规范甲醇的生产过程涉及到高温、高压、易燃和易爆等安全隐患,需要建立对应的安全规范,确保操作人员的人身安全和设备的稳定性。
需要设立相应的应急预案,定期进行应急演练,权威人员对操作人员进行培训,督促操作规范执行。
同时,对于安全设备的配备、操作前的检查、注意事项进行详尽的说明。
20万吨年甲醇的生产技术

20万吨/年甲醇的生产技术01生产工艺路线选择1)原料来源生产甲醇的原料为合成气,是指主要成分为H2和CO的气体混合物主要有以下三种制取方式1、天然气制甲醇天然气是制造甲醇的主要原料。
天然气的主要成分是甲烷,还含有少量的其他烷烃、烯烃与氮气。
以天然气生产甲醇原料气有蒸汽转化、催化部分氧化、非催化部分氧化等方法,其中蒸汽转化法应用最广泛。
但是由于天然气大多作为民用燃料,且资源量越来越少,政府已经在07年出台相关规定禁止使用以天燃气为原料生产甲醇。
2、煤、焦炭制甲醇煤与焦炭是制造甲醇粗原料的主要固体燃料。
用煤和焦炭制甲醇的工艺路线包括燃料的气化、气体的脱硫、变换、脱碳及甲醇合成与精制。
用蒸汽与氧气对煤、焦炭进行气化,气化所得可燃性气体即为制造甲醇的初始原料气。
3、油制甲醇油制甲醇主要包括石脑油和重油。
,石石脑油生产甲醇原料气的主要方法是加压蒸汽转化法;以重油为原料制取甲醇原料气有部分氧化法与高温裂解法两种途径。
由于近年来石油消费的不断增长,油供应日趋紧张,石油价格不断上涨,采用石油产品生产大宗化工产品面临着原料枯竭、成本上涨等矛盾。
综上,由于能源结构为缺油、少气、富煤,世界煤资源远远超过天然气和石油储量,随着科技进步,煤制气中的净化手段日益提高以及甲醇需求量的大幅度增加,煤将成为甲醇生产的主要原料。
因此,从长远角度分析,我组决定选用煤制甲醇原料气。
2)催化剂性能,安全丶环保分析,经济分析甲醇的生产方法介绍1、高压法用一氧化碳与氢在高温(340~420℃)高压(30.0~50.0MPa)下用锌-铬氧化物作催化剂合成甲醇。
2、低压法一氧化碳与氢气为原料在低压(5.0MPa)和275℃左右的温度下,采用铜基催化剂合成甲醇。
低压法成功的关键是采用了铜基催化剂,铜基催化剂比锌-铬催化剂活性好得多,是甲醇合成反应能在较低的压力和温度下进行。
3、中压法中压法合成甲醇的工艺流程中,操作压力范围为10.0~27.0MPa,温度为235~315℃。
变换、、低温甲醇洗培训教材(新能)

温度对变换反应的速度影响较大,而且对正逆反应速度的影响不一样。温度升高,放热反应即变换反应速度增加得慢,逆反应(吸热反应)速度增加得快。同时,CO变换率随温度的升高而降低。因此当变换反应开始时,反应物浓度大,提高温度可加快变换速度。反应末期,须降低反应温度,使逆反应速度减慢,这样可得到较高的变换率。
短期停车按下列步骤进行:
(1)关闭气化入变换工序大阀EV2001,通知净化工序关死其入工段大阀。
(2)关闭中压废锅PV2002自调阀,关闭LV2001、LV2003、LV2004自调阀,液位控制在高限。停磷酸盐加药泵。
锅炉给水经中压锅炉给水泵(P2002AB)升压至3.0MPa后去锅炉给水加热器(E2005A)升温后去E2001产2.5MPa饱和蒸汽、送至E2004产1.2MPa饱和蒸汽。
由低压锅炉给水泵(P2001AB)升压到0.8MPa送(甲醇)低压废热锅炉(E2006),产生0.4MPa的蒸汽。
由密封水泵(P2004AB)升压到8.6MPa分为两股,一股直接送至气化作为热密封水,一股经E2009密封水冷却器降温至40℃送至气化作为冷密封水及T2001作为洗涤用水。
(3)当压力升到操作压力6.4MPa时,用PV2008控制压力至平稳,直至气体全部由PV2008放空。
(4)通知仪表投用在线分析仪。
3、变换冷凝液送至气化。
4、蒸汽并入管网。
5、工况调整
(1)利用E2001蒸汽管线压力控制E2002入口温度。
(2)通过调节E2002调节入变换炉的温度,以控制变换炉床层温度至正常。
CO在某种条件下,能发生下列副反应:
CO+H2=C+H2O
CO+3H2=CH4+H2O
CO+4H2=CH4+2H2O
甲醇生产技术第四章变换

控制好汽、气比。给系统加蒸汽前,必须将蒸汽管内的
冷凝水排净,方可加入。
三、全低变工艺操作条件
5)开车初期炉温较低,使用冷煤气付线调温易使变换炉 入口温度低而带水,应以蒸汽量调节。 6)调节蒸汽加入量,使炉温在正常范围之内,出系统CO含 量达标后,联系调度,缓慢打开系统出口阀,关放空阀,向
后工序送气。
二、影响变换反应平衡的因素
3.压力的影响 由于变换反应是等分子反应,反应前后气体的总体积不 变,生产中压力对变换反应的化学平衡并无明显的影响。 4.CO2的影响
在变换反应过程中,如能把生成的CO2及时除去,就可以
使变换反应向右进行,提高CO变换率。
二、影响变换反应平衡的因素
5.副反应的影响 CO变换过程中,可能发生CO分解析出碳和生成甲烷等副 反应,其反应式如下:
三、全低变工艺操作条件
3、根据催化剂使用情况,调整适当汽、气比和适当床层 温度。 4、要充分发挥催化剂的低温活性,在实际操作中关键是
稳定炉温,控制好汽气比。
5、生产中如遇突然减量,要及时减少或切断蒸汽供给。 6、临时停车,先关蒸汽阀,计划停车可在停车前适当减 少蒸汽,系统要保正压。
三、全低变工艺操作条件
一、变换反应的物理化学基础
表4 —1
一氧化碳变换反应热效应
温度/℃ —Δ Η R/
25
200
250
300
350
400
(kJ/mol)
41.16
40.04
39.64
39.23
38.76 38.30
一、变换反应的物理化学基础
2.变换反应的平衡常数 变换反应是在压力不太高时进行的,故计算化学平衡常 数Kp时,各组分用分压表示已足够准确。
甲醇原料气中一氧化碳的变换工艺分析
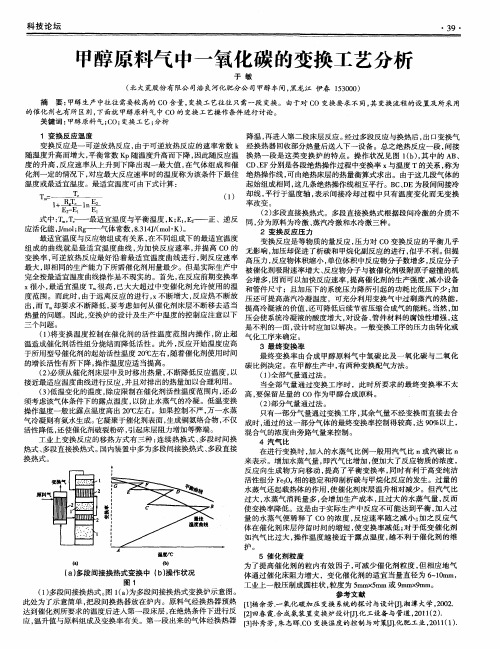
变换、、低温甲醇洗培训教材(新能)

新能凤凰(滕州)能源有限公司新能风凰(滕州)能源有限公司技术工人培训教材变换、低温甲醇洗培训教材编写:王磊李国方审核:吴萍批准:庄乾海新能风凰(滕州)能源有限公司合成车间第一章变换部分第一节变换工段的任务及意义本工段主要是将水煤浆气化来的煤气在变换工段把一氧化碳转化为用于生产甲醇的合成气,煤气中的一氧化碳与水蒸气在变换催化剂的作用下发生变换反应转化氢和二氧化碳,采用配气路线使出变换工段的合成气中CO含量约为20%(V干基),且H2/CO≈2.15(V/V),同时将部分有机硫转化成无机硫送至低温甲醇洗工段。
第二节变换工段的生产原理原理:一氧化碳的变换反应是一个放热反应,其反应方程式为:CO+H2O==CO2+H2+Q COS+H2O==H2S+CO2+Q一氧化碳变换是一个放热、摩尔数不变的可逆反应。
从化学平衡来看,降低温度、增加蒸汽量和除去二氧化碳,可使平衡向右移动,从而提高一氧化碳变换率;从反应速度看,提高温度有利于反应速度的增加。
CO在某种条件下,能发生下列副反应:CO+H2=C+H2OCO+3H2=CH4+ H2OCO+4H2= CH4+2H2O这几个副反应都是放热反应,副反应的发生对变换操作的正常进行是不利的。
由于这些副反应都是放热反应和体积减小的反应,所以低温高压有利于副反应的进行。
在变换的正常操作中,提高反应温度或是选用对变换反应具有良好选择性的催化剂就可以防止或减少副反应的发生。
下面就温度、压力、汽气比等对变换反应的影响作进一步说明。
1、温度温度对变换反应的速度影响较大,而且对正逆反应速度的影响不一样。
温度升高,放热反应即变换反应速度增加得慢,逆反应(吸热反应)速度增加得快。
同时,CO变换率随温度的升高而降低。
因此当变换反应开始时,反应物浓度大,提高温度可加快变换速度。
反应末期,须降低反应温度,使逆反应速度减慢,这样可得到较高的变换率。
同时,反应温度的确定还和汽气比、气体成份、触媒的活性温度范围等因素有关。
变换满足甲醇生产后工艺指标的变化 陈1-7-22

变换满足甲醇生产后工艺指标的变化根据给定的煤气组份及变换要求:造气总共有2台φ3300;7台φ3200;7台φ3000的UGI煤气炉,改造后的纯氧连续常压煤气炉,可以做到15开1备,平均煤气产量10000Nm3/h·台。
煤气组份及量见表1-1。
表1-1 初煤气组份及量名称CO2CO H2N2O2CH4H2S 合计组份(%)18.5 38.0 42.0 0.2 0.3 1.0 0.06 100.00 量(Nm3/h)27750 57000 63000 300 450 1500 90.0 150000表1-2 变换后气体组份及量名称CO2CO H2N2O2CH4H2S 合计组份(%)26.2 24.0 48.0 0.18 0.27 0.90 0.0003量(Nm3/h)41314 37564 82436 300 450 1500 0.51 169436表1-3 精脱硫后气体组成及量名称CO2CO H2N2O2CH4H2S 合计组份(%) 2.0 24.0 48.0 0.0 0.0量(Nm3/h)2436 37564 82436 300 0.0 1500 0.0 124236 可以生产的甲醇量为:(57000+63000)÷2210=54.3吨/h;43.4万吨/年。
建议改造后可按如下工艺指标控制:高压机来的煤气<40℃→油水分离器→除油器除油→中温换热器,~80℃→中间换热器,添加蒸汽,~210℃→预变炉→变换一段至~290℃,CO~33%→喷水增湿至~260℃→变换二段至~290℃,CO~30%→喷水增湿至~220℃→变换三段至~270℃,CO~24% →中间换热器,150~160℃→变换四段(作为水解用,没有变换反应)→气体分二股,其中约50%的气体进中温换热器加热半水煤气,另外约50%的气体去冷激水加热器将增湿用水加热到~130℃,气体降温到~108℃→脱碳煮沸器按该指标控制,蒸汽消耗单套(处理水煤气量75000Nm3/h)约2500~3000kg/h.鉴于水气比很低,一二段间可不喷水,则蒸汽消耗单套(处理水煤气量75000Nm3/h)约3000~3200kg/h.。
第四章甲醇原料气的一氧化碳变换.

第四章甲醇原料气的一氧化碳变换[知识目标]1.熟悉一氧化碳变换反应的原理、热力学和动力学;2.熟悉变换炉结构特性;熟悉放热反应热交换的常用方法;3.熟悉变换工段的工艺流程图(PFD)。
4.掌握一氧化碳变换反应的工艺影响因素及其工艺条件;掌握控制和调节工艺条件的方法;5.掌握变换工段原始开车、正常开停车、事故开停车技术;6.掌握一氧化碳变换催化剂使用技术;[能力目标]1.能够分析一氧化碳变换反应的工艺影响因素,并能够分析和判断影响工艺条件变化的因素;2.能够适时正确地控制和调节工艺条件;3.能够完成变换工段原始开车、正常开停车、事故开停车;4.能够正确地使用一氧化碳变换催化剂;[重点、难点]1.一氧化碳变换反应原理、热力学和动力学;2.一氧化碳变换工段的工艺流程图(PFD);第一节一氧化碳变换基本原理水煤气中的一氧化碳在一定的温度条件下,借助催化剂的催化作用,与水蒸汽进行交换反应,生成二氧化碳和氢气,调节二氧化碳和氢气的比例,制得合格的变换气,满足甲醇生产用气要求。
在保证生产的同时,要维护好催化剂,以延长催化剂的使用寿命。
1.2 反应方程式主反应 CO+H20= CO2+H2+ Q副反应 2CO = C + C02+Q2CO+2H2=CH4+ C0+QCO + 3H2== CH4+ H2OC02 + 4H2== CH4+ 2H2O + Q水解反应 CS2 + 2H20== 2H2S + C02COS+ H20==H2S+ C021.3 工艺流程简述1.气相流程:来自压缩机二段压力为 0.8MPa,温度为40 ℃左右的水煤气,由中部进入油水分离器,分离掉油水后,从顶部出来,进入除油器顶部,进一步分离掉油水后,从下部出来,进入煤气换热器Ⅰ顶部走管内与变换气换热,从底部出来后进入煤气换热器Ⅱ底部走管内与变换气进一步换热,从顶部出来的水煤气温度为210 ℃左右,与汽水分离器出来的水蒸汽混合通过低变电炉进入变换炉一段,经过脱毒,吸附后,进入变换炉二段触媒层,气体在二段进行变换反应,气体再进入三段触媒层继续反应,最后经变换后的气体从底部出来的温度在 350 — 360 ℃,进入余热回收器,加热软水付产蒸汽,出余热回收器温度在250—260℃从上部进入煤气换热器Ⅱ管间与水煤气换热后的温度在180—200℃左右进入中温水解炉,在水解剂的作用下,有机硫转化成无机硫后进入煤气换热器Ⅰ继续降温,然后进入水冷器进一步冷却,再进入变换气液分离器分离冷凝水后再进入变换气脱硫塔。
化工变换操作规程(甲醇厂变换装置岗位操作规程)

目录第一部分变换工序的任务和目的第二部分一氧化碳变换反应基本原理第三部分一氧化碳变换反应催化剂第四部分一氧化碳变换工艺条件的选择第五部分变换工序的开停车第六部分变换催化剂的装填方案第七部分安全卫生及环保第八部分变换主要设备第九部分工艺参数第十部分安全阀一览表第十一部分CO泄露应急预案第一部分变换工序的任务和目的一. 岗位概况从气化工序来的煤气,干基总量95027.139NM3/h,湿基总量196739.110NM3/h。
干基成分大致为表1:水煤气具有压力高、温度高、水气比高、含硫高、含CO2高等特点。
因此,直接进行耐硫变换,在高含硫量的条件下进行CO变换反应。
使氢碳比例满足甲醇合成的要求。
变换气中的有机硫也转化为无机硫(H2S)。
这样即减少了换热设备,简化了流程,也降低了能耗。
虽然水煤气经过二级除尘,但水煤气中还会有微量的灰尘,经过变换炉时就沉积在催化剂表面,时间一长,催化剂将失去活性,根据经验,制取甲醇时CO 的变换率不高时,可以先经煤气冷却,洗涤掉气体中的尘,同时,用水煤气废热锅炉来控制水煤气中的含水量,也控制CO的变换率,基本可以满足甲醇需要的CO的含量,如不能满足要求,可以通过旁路进行微调。
本工序采用的变换反应是在催化剂的作用下进行,从气化工序过来的原料气直接进入本工序进行变换反应。
因原料气中会有一定量的H2S、COS等硫化物,因而采用以Co、Mo为主体的催化剂,反应温度在200~465℃范围内进行,反应后的变换气中的CO为19%。
二、工艺特点本变换工序采用的是宽温耐硫部分变换工艺技术,这是由粗煤气中CO含量高、下游工序对CO含量的要求和装置低投资的要求来决定的,其特点是:(1)、采用的催化剂是耐硫变换催化剂。
可以满足粗煤气中含有硫化物的要求,对粗煤气中的硫化物只有低限要求,而没有高限规定,同时还可达到简化工艺路线的目的;(2)、采用部分变换工艺,以满足后序装置对原料气中CO含量的要求,操作灵活方便;(3)、蒸汽消耗低;(4)、对热量采用分级回收,热利用率高。
甲醇转化操作规程更改A4

目录1.岗位任务2.基本原理3.工艺流程概述4.工艺操作指标5.生产操作要点5.1开车前的准备工作5.2正常开车5.3正常生产操作5.4停车步骤5.5转化催化剂升温还原5.6 TC-22脱硫剂开车6.生产常见事故处理7.设备一览表8.安全技术规程转化操作规程1.岗位任务将焦炉气中的CH4及烃类在转化炉内与纯O2进行部分氧化及蒸汽转化反应,生成H2、CO、CO2。
通过氧气和焦炉气、蒸汽量的控制,调节好水汽比,以满足合成甲醇生产的需要。
同时利用转化气的热量,通过废热锅炉副产2.5Mpa饱和中压蒸汽,除供给转化炉使用外,余量经减压后送至低压蒸汽管网。
2.基本原理2.1甲烷转化基本原理焦炉气部分氧化亦称自热转化,即在转化炉上部燃烧室内,焦炉气中的部分H2与纯氧进行燃烧,温度达1200-1400℃,放出大量的热,以供给甲烷转化所需热量,上部高温气体进入下部催化剂层,焦炉气中CH4在镍基催化剂的作用下,与蒸汽进行转化反应〈水/气≥0.9〉,使转化出口气体中CH4≤0.6%(V)。
转化炉上部燃烧反应:H2+1/2O2 = H2O + Q甲烷转化反应主要在催化剂层中进行,甲烷蒸汽转化反应为:CH4 + H2O = CO + 3H2 -QCH4 + CO2 = 2CO + 2H2 -QCH4 + 2H2O = 2CO2 + 4H2 -QCO + H2O = CO2 + H2 + QCnHm + nH2O = nCO + (m/2 + n)H2 -Q2.2氧化锌脱硫基本原理氧化锌脱硫槽D60602,上层装T-407脱氯剂,主要吸收无机氯(HCl),下层装TC-22常温氧化锌脱硫剂,主要吸收硫化氢,为转化气最后把关至总硫≤0.1ppm,以满足甲醇合成触媒的要求。
2.2.1转化反应COS + H2 = H2S + CO +QRSH + H2 = RH + H2S +Q2.2.2吸收反应ZnO + H2S = ZnS + H2OM x O y+2yHCl=M x Cl2y+yH2O3.工艺流程概述3.1 气体流程:精脱硫来的14198Nm3/h焦炉气(总硫﹤0.1ppm)和转化废热锅炉部分自产蒸气混合,进入焦炉气预热器C60602〈壳程〉预热到 450℃,进入预热炉B60601辐射段预热至660℃,进入转化炉D60601混合燃烧室,经过B60601预热炉对流段预热的蒸汽和来自空分的3000m3/h纯氧混合后,温度约300℃进入转化炉与焦炉气进行纯氧部分氧化燃烧,温度达1200℃左右的高温气体进入催化剂床层,在镍基催化剂作用下,进行甲烷转化反应,转化气经过废热锅炉C60601回收热量,每小时产生2.5Mpa的蒸汽约13.5t/h,供转化自用和外管网用。
变换工段文字说明m
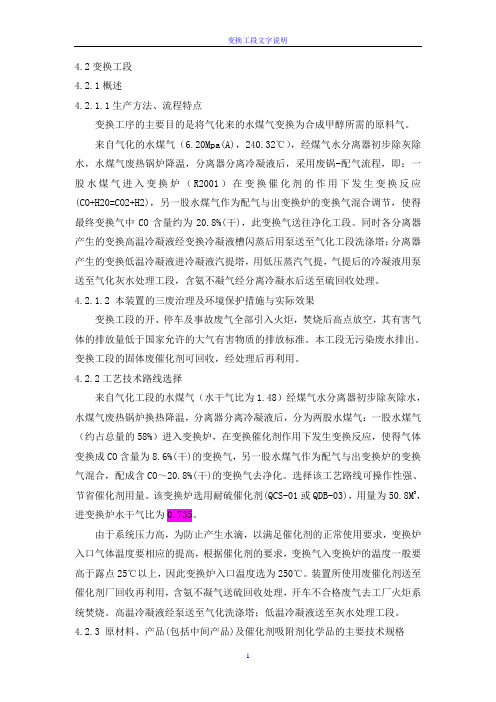
4.2变换工段4.2.1概述4.2.1.1生产方法、流程特点变换工序的主要目的是将气化来的水煤气变换为合成甲醇所需的原料气。
来自气化的水煤气(6.20Mpa(A),240.32℃),经煤气水分离器初步除灰除水,水煤气废热锅炉降温,分离器分离冷凝液后,采用废锅-配气流程,即:一股水煤气进入变换炉(R2001)在变换催化剂的作用下发生变换反应(CO+H20=CO2+H2),另一股水煤气作为配气与出变换炉的变换气混合调节,使得最终变换气中CO含量约为20.8%(干),此变换气送往净化工段。
同时各分离器产生的变换高温冷凝液经变换冷凝液槽闪蒸后用泵送至气化工段洗涤塔;分离器产生的变换低温冷凝液进冷凝液汽提塔,用低压蒸汽气提,气提后的冷凝液用泵送至气化灰水处理工段,含氨不凝气经分离冷凝水后送至硫回收处理。
4.2.1.2 本装置的三废治理及环境保护措施与实际效果变换工段的开、停车及事故废气全部引入火炬,焚烧后高点放空,其有害气体的排放量低于国家允许的大气有害物质的排放标准。
本工段无污染废水排出。
变换工段的固体废催化剂可回收,经处理后再利用。
4.2.2工艺技术路线选择来自气化工段的水煤气(水干气比为1.48)经煤气水分离器初步除灰除水,水煤气废热锅炉换热降温,分离器分离冷凝液后,分为两股水煤气:一股水煤气(约占总量的58%)进入变换炉,在变换催化剂作用下发生变换反应,使得气体变换成CO含量为8.6%(干)的变换气,另一股水煤气作为配气与出变换炉的变换气混合,配成含CO~20.8%(干)的变换气去净化。
选择该工艺路线可操作性强、节省催化剂用量。
该变换炉选用耐硫催化剂(QCS-01或QDB-03),用量为50.8M3,进变换炉水干气比为0.735。
由于系统压力高,为防止产生水滴,以满足催化剂的正常使用要求,变换炉入口气体温度要相应的提高,根据催化剂的要求,变换气入变换炉的温度一般要高于露点25℃以上,因此变换炉入口温度选为250℃。
甲醇变换工段工艺计算
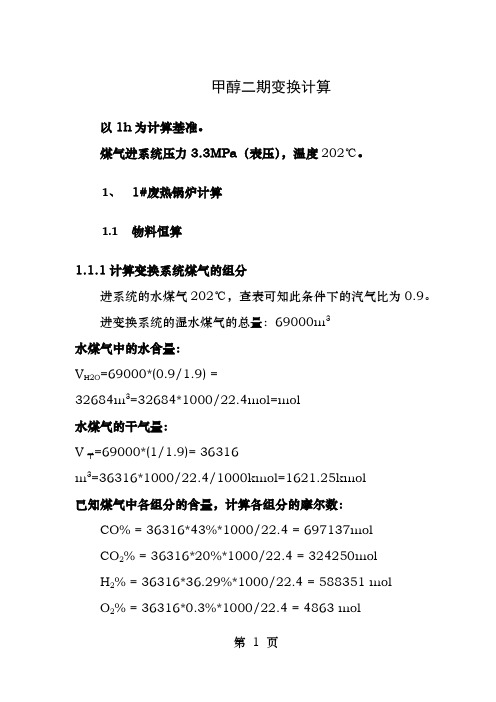
甲醇二期变换计算以1h为计算基准。
煤气进系统压力3.3MPa(表压),温度202℃。
1、1#废热锅炉计算1.1物料恒算1.1.1计算变换系统煤气的组分进系统的水煤气202℃,查表可知此条件下的汽气比为0.9。
进变换系统的湿水煤气的总量:69000m3水煤气中的水含量:V H2O=69000*(0.9/1.9) =32684m3=32684*1000/22.4mol=mol水煤气的干气量:V干=69000*(1/1.9)= 36316m3=36316*1000/22.4/1000kmol=1621.25kmol已知煤气中各组分的含量,计算各组分的摩尔数:CO% = 36316*43%*1000/22.4 = 697137molCO2% = 36316*20%*1000/22.4 = 324250molH2% = 36316*36.29%*1000/22.4 = 588351 molO2% = 36316*0.3%*1000/22.4 = 4863 molH2S% = 36316*0.29%*1000/22.4 = 4701 mol COS% = 36316*0.031%*1000/22.4 =502 mol Ar% = 36316*0.09%*1000/22.4 = 1459 mol表1.1 干基煤气的组分表1.2 湿基煤气的组分1.1.2计算经过废热锅炉后煤气的组分水煤气通过废热锅炉的进口温度202℃,出口温度174℃,则:出废热锅炉的水煤气的温度为174℃,此温度的饱与蒸汽压为900kPa(绝压),出气液分离器之后,干水煤气中与水蒸气含量比值为:0.9/(3.3+0.1-0.9)=0.36水煤气中H2O蒸汽含量为:1621.24* 0.36=607.97kmol液态水含量为:1459.11-607.97=851.14kmol=851.14*18kg=15320.52kg≈15.32t表1.3 经过废热锅炉的湿基煤气组分1.2、热量恒算水煤气放热量的计算水煤气通过废热锅炉的进口温度202℃,出口温度174℃,则:CO放出的热量:Q1=30.5*697.14*(202-174)= 591454KJ CO2放出的热量:Q2=46.8 * 324.25 *(202-174)= 424897KJH2放出的热量:Q3=29.2* 588.35 *(202-174)= 481035KJO2放出的热量:Q4=30.8* 4.86*(202-174)= 4191KJ H2S放出的热量:Q5= 36.5* 4.70*(202-174)= 4803KJ COS放出的热量:Q6= 30.5* 0.50 *(202-174)= 427KJ Ar放出的热量:Q7= 33* 1.46 *(202-174)= 1349KJH2O放出的热量:Q H2O= Q8+Q9+Q10=Q8为H2O蒸气的冷凝热,Q9为H2O蒸气冷却放出的显热,Q10为液态H2O冷却放出的显热。
- 1、下载文档前请自行甄别文档内容的完整性,平台不提供额外的编辑、内容补充、找答案等附加服务。
- 2、"仅部分预览"的文档,不可在线预览部分如存在完整性等问题,可反馈申请退款(可完整预览的文档不适用该条件!)。
- 3、如文档侵犯您的权益,请联系客服反馈,我们会尽快为您处理(人工客服工作时间:9:00-18:30)。
采用正压循环硫化法升温硫化。
三、全低变工艺操作条件
该法的原理是升温硫化时,以干水煤气为载体,以CS2为硫 化剂,在200℃左右,CS2与水煤气中所含的H2反应,产生高 浓度的H2S气体:
4H2+CS2=2H2S+CH4+240.6KJ/mol
生成的H2S与CoO和MoO3反应生成CoS和MoS2 MoO3+2H2S+H2=MoS2+3H2O+48.1KJ/mol CoO+H2S=CoS+H2O+13.4KJ/mol
甲醇生产技术
第四章 变换
第四章 变换
1 一氧化碳变换的基本原理 2 一氧化碳变换催化剂 3 一氧化碳变换工艺操作条件的选择
第四章 变换
一氧化碳变换工序的主要作用有两个: (1)调整氢碳比例 合成甲醇的原料气组成应保持一定的氢碳比例,甲醇合
成反应中,一氧化碳与二氧化碳所需的氢的化学当量是
不同的,应使M= =2.0~2.05。当以重油或煤、焦为原料 生产甲醇时,气体组成偏离上述比例,须通过变换工序 使过量的一氧化碳变换成氢气。
(四)催化剂保护措施 1、稳定操作,确保出系统变换气中CO在指标范围内,并保 证水煤气中总硫含量≥80mg/Nm3。
2、生产过程中如遇减气量时,应立即减小蒸汽加入量,否
则短期内使汽、气比过大引起反硫化。
三、全低变工艺操作条件
3、禁止对工况不正常情况采用增大蒸汽的办法进行处理, 如氧含量跑高用蒸汽压温,都会造成反硫化,应正确判断, 果断采取相应措施。
三、全低变工艺操作条件
(三)操作要点 1、根据气量大小及水煤气成分分析情况,调节适量汽、 气比,保证变换气中CO含量在控制指标内。
2、随时注意观察变换炉床层灵敏点和热点温度的变化情
况,以增减蒸汽,配合煤气付线阀和变换炉近路阀开度大 小调整炉温,使炉温波动在±10℃/h范围内,尤其在加减 量时要特别注意。
1、正常生产流程 从压缩来的水煤气,温度40℃左右,总硫80mg/Nm3左右, CO≈36%,经焦炭过滤器除去油污杂质,进入水煤气换热 器Ⅰ管内与管间的变换气换热至180℃左右后,进入蒸汽
水煤气混合器与220℃水蒸气混合增湿提温。
四、水煤气全低变工艺流程
2、升温硫化流程 钴、钼催化剂的硫化是在一定温度下(200℃左右),利 用煤气中的氢气和补入的硫化氢与催化剂作用生成具有 高活性的硫化物,其主要反应式为:
一、中温变换催化剂
3.催化剂的中毒和衰老 硫化氢与催化剂的反应如下
4.催化剂的维护与保养
(1)在装填前,要进行过筛除去粉尘和碎粒。 (2)在开、停车时,要按规定的升、降温速度进行操作, 严防超温。 (3)正常生产中,原料气必须经过除尘和脱硫(氧化型
的催化剂),并保持原料气成分稳定。
一、中温变换催化剂
第四章 变换
(2)有机硫转化为无机硫 甲醇合成原料气必须将气体中总含硫ቤተ መጻሕፍቲ ባይዱ控制在0.2ppm以 下。以天然气与石脑油为原料时在蒸汽转化前,用钴钼
加氢转化,串联氧化锌的方法可达到要求。以煤制得的
粗水煤气中,所含硫的总量中硫化氢约占90%,尚含10% 左右的硫氧碳(COS)、及微量其他有机硫化物。
第一节 一氧化碳变换的基本原理
三、宽温耐硫变换催化剂
表4 —4
国别 型号 CoO MoO3 K2O 其他 Al2O3 尺寸,mm 颜色 堆密度kg/L 比表面m2/g 比孔容ml/g 使用温度℃ 德国 K8-11 ~3.0 ~8.0 — —
国内外耐硫变换催化剂
丹麦 SSK ~1.5 ~10.0 适量 — 美国 B301 2~5 6~11 适量 — 余量 ∮5×5条 型 蓝灰 1.2~1.3 148 0.18 210~500 中国 B302Q >1 >7 适量 — 余量 ∮3~5球 型 墨绿 1.0 + (-)0.1 173 0.21 180~500
二、影响变换反应平衡的因素
3.压力的影响 由于变换反应是等分子反应,反应前后气体的总体积不 变,生产中压力对变换反应的化学平衡并无明显的影响。 4.CO2的影响
在变换反应过程中,如能把生成的CO2及时除去,就可以
使变换反应向右进行,提高CO变换率。
二、影响变换反应平衡的因素
5.副反应的影响 CO变换过程中,可能发生CO分解析出碳和生成甲烷等副 反应,其反应式如下:
四、水煤气全低变工艺流程
3、流程图
图(4—3)
水煤气全低变工艺流程图
Thank you
C25-2-02 ~3.0 ~12.0 适量 加有稀土元 素 专用载体 余量 余量 ∮4×10条 ∮3×5球型 ∮3×10条 型 型 绿 墨绿 黑 0.75 1.0 0.70 150 0.5 280~500 79 0.27 200~475 122 0.5 270~500
三、宽温耐硫变换催化剂
硫化操作的好坏对硫化后催化剂的活性有很大关系,除 在含氢气条件下用CS2外,也可以直接用H2S或用含硫化 物的工艺气。硫化为放热过程,这样反应有:
备注
出口气 H2S~5g/Nm3 40~70 出口气 H2S~15g/Nm3 降到300。C,停 止加入CS2
三、宽温耐硫变换催化剂
Co-Mo系变换催化剂经过硫化后具有活性,而活性组分 MoS2 和 CoS在一定条件下会发生水解反应,实际上是反 硫化反应,它构成了这一类催化剂失活的重要原因:
若将反应式(4-21)中的MoO3用H2还原成MoO2,再按式 (4-24)式逆反应将MoO2硫化为MoS2,其平衡常数为
(一)铁铬系催化剂 1.组成与性能 (1)颗粒外形与尺寸。
(2)堆密度
(3)颗粒密度 (4)真密度 (5)比表面积 (6)孔隙率
(7)比孔体积:=催化剂的微孔体积/催化剂质量
一、中温变换催化剂
2.催化剂的还原与氧化 一般利用煤气中的氢和一氧化碳进行还原,其反应式如 下:
氧能使还原后的催化剂氧化生成三氧化二铁,反应式如 下:
若在温度较高时(如300。C)加入CS2,因发生氧化钴的 还原反应而生成金属钴
三、宽温耐硫变换催化剂
表4 —5 B302Q催化剂的快速硫化程序
阶段 升温 初期 主期 降温置换
时间/h ~4 ~8 ~2 ~2 ~4
床层温度/C 100~200 200~300 300~400 400~450
进料气中 CS2,g/Nm3 20~40
炉内,油水分离器和焦炭过滤器要每小时排放一次,并将 水排净。
三、全低变工艺操作条件
(五)停车 1、短期停车 2、长期停车 3、紧急停车
三、全低变工艺操作条件
(六)故障判断和处理 1、变换炉系统着火 2、催化剂失活 3、变换系统压差大
4、炉内温度剧烈变化
5、出口一氧化碳超标
四、水煤气全低变工艺流程
一、变换反应的物理化学基础
表4 —2 温度/℃ Kp 25 1.03×103
一氧化碳变换反应的平衡常数 200 227.9 250 96.5 300 39.2 350 24.5 400 11.7
一、变换反应的物理化学基础
3.变换率与平衡变换率 一氧化碳的变换程度可用变换率表示,它定义为反应中 变换了的一氧化碳量与反应前气体中一氧化碳量之比。
三、全低变工艺操作条件
3、根据催化剂使用情况,调整适当汽、气比和适当床层 温度。 4、要充分发挥催化剂的低温活性,在实际操作中关键是
稳定炉温,控制好汽气比。
5、生产中如遇突然减量,要及时减少或切断蒸汽供给。 6、临时停车,先关蒸汽阀,计划停车可在停车前适当减 少蒸汽,系统要保正压。
三、全低变工艺操作条件
(二)钴钼系催化剂
(见第三节)
二、低温变换催化剂
1.组成和性能 目前工业上采用的低温变换催化剂均以氧化铜为主体, 经还原后具有活性组分的是细小的铜结晶。
2.催化剂的还原与氧化
二、低温变换催化剂
3.催化剂的中毒 硫化物、氯化物是低温变换催化剂的主要毒物,硫对低 变催化剂中毒最明显,各种形态的硫都可与铜发生化学 反应造成永久性中毒。
三、变换反应动力学
各组分浓度对正反应速率的影响情况大致如下: (1)正反应速率与CO浓度近乎成正比,即r ∝ pco。 (2)正反应速率与H2O浓度的关系为r ∝ pmH2O, m=0~0.5。
(3)除少数学者认为H2抑制正反应速率外,大多数研究
证实H2浓度不影响正反应速率。
三、变换反应动力学
(4)大部分研究者证实CO2抑制正反应速率。 (5)正反应速率的表观级数在大部分动力学方程中为 0.5~1.0。国内学者得出国产中变催化剂上一氧化碳变换 反应的动力学方程为
差、使用寿命短、成本也较高,一般不选用铜锌系低温
变换催化剂。
三、全低变工艺操作条件
(一)正常工艺条件 1、压力 2、温度 3、汽气比
4、空速
三、全低变工艺操作条件
(二)岗位正常操作 1、原始开车 全低变催化剂,宽温耐硫,其主要活性组份为钴和钼,使用 前呈氧化态,须经升温硫化为硫化态后才具有活性。据此,
取1摩尔干原料气为基准,加入nmol水蒸气进行变换反应
(n称为汽气比或水气比),当一氧化碳变换率为a时, 可得
反应达到平衡时的变换率为平衡变换率,用a′表示:
二、影响变换反应平衡的因素
1.温度的影响
图 4-1 温度与平衡变换率的关系
二、影响变换反应平衡的因素
2.蒸汽添加量的影响
图4-2 不同温度下蒸汽加入量与CO平衡变换率的关系
三、全低变工艺操作条件
2、正常开车 1)全面检查系统所属设备、管线、阀门,应符合开、停 车要求,联系有关人员检查仪表、电器设备灵敏好用。 2)联系调度送中压蒸汽暖管,排放冷凝积水,待炉温达
200℃可导气。
三、全低变工艺操作条件
3)无论何种情况床层温度不得低于露点温度(0.75MPa— 120℃,1.35MPa—140℃),否则煤气中的蒸汽将冷凝成水 导致催化剂中钾的流失而影响活性。 4)根据系统气量大小、压力高低情况,调整蒸汽加入量,