精馏作业
烯烃精馏系统操作与控制—作业丙烯精馏
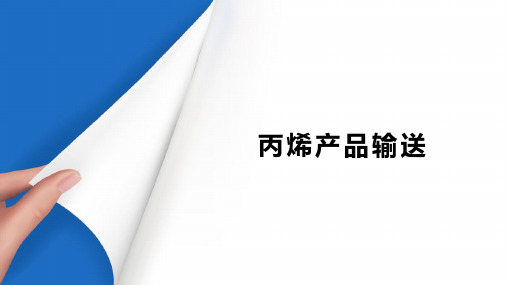
2.减小再沸量
3.回流量小
3.加大回流量
4.采出量大
4.减小采出量
5.仪表故障
5.切至手动,联系仪表处理
丙烯精馏塔结构 及工艺流程
ONTENTS
目 录
1 丙烯精馏塔结构 2 丙烯精馏塔任务 3 丙烯精馏塔工艺流程描述
01丙 烯 精 馏 塔 结 构
结构
1 本装置设置有两个丙烯精馏塔,串联操作。 1#丙烯精馏塔160T603设置有77 层四溢流浮阀
2 塔盘。 2# 丙烯精馏塔160T604设有162 层四溢流浮阀塔
1
通过丙烯产品泵160P606A/B送出。
经丙烯产品冷却器160E615进行冷却,然后通过 2 丙烯产品保护床160D602A/B进行精制。
从床层上部经过,在过滤器160S601A/B过滤 3 后由160FC649(聚合级丙烯采出流控器)控制采出量。03 丙烯产品输送条件
温度40℃,压力 2.1MPag
1#丙烯精馏塔的塔顶气相进入2#丙烯精馏塔塔釜。 4 来自脱乙烷塔160T601塔釜的物料进入到2#丙烯精
馏塔的第146层塔盘。
2#丙烯精馏塔塔顶冷凝器160E614A/B的出料进入2# 5 丙烯精馏塔回流罐160V604,回流罐中的部分液相通
过回流泵160P607A/B打回2#丙烯精镏塔塔顶。。
聚合级丙烯产品通过丙烯产品采出泵160P606A/B送 6 出,经丙烯产品冷却器160E615冷却、经丙烯产品保
调节方法
1.调整进料量 2.调整再沸量 3.调整采出量 4.调整回流量
异常情况处理
现象 液位上升
液位下降
异常情况处理
原因
处理方法
1.进料量增加
1.减小进料量
精馏作业题
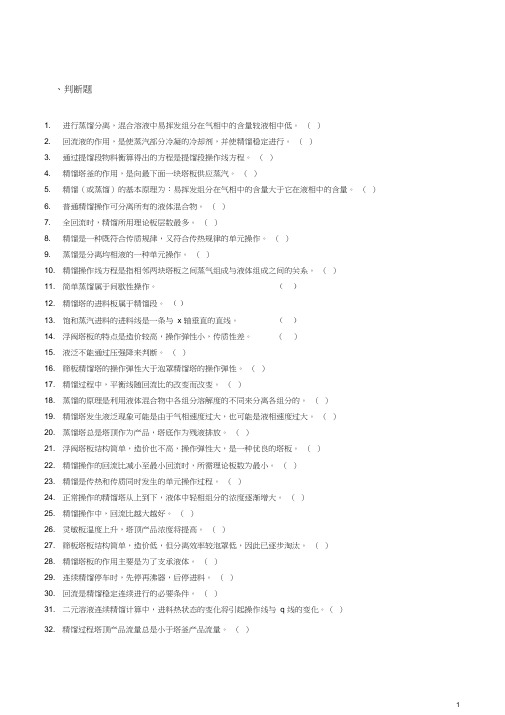
、判断题1. 进行蒸馏分离,混合溶液中易挥发组分在气相中的含量较液相中低。
()2. 回流液的作用,是使蒸汽部分冷凝的冷却剂,并使精馏稳定进行。
()3. 通过提馏段物料衡算得出的方程是提馏段操作线方程。
()4. 精馏塔釜的作用,是向最下面一块塔板供应蒸汽。
()5. 精馏(或蒸馏)的基本原理为:易挥发组分在气相中的含量大于它在液相中的含量。
()6. 普通精馏操作可分离所有的液体混合物。
()7. 全回流时,精馏所用理论板层数最多。
()8. 精馏是一种既符合传质规律,又符合传热规律的单元操作。
()9. 蒸馏是分离均相液的一种单元操作。
()10. 精馏操作线方程是指相邻两块塔板之间蒸气组成与液体组成之间的关系。
()11. 简单蒸馏属于间歇性操作。
()12. 精馏塔的进料板属于精馏段。
()13. 饱和蒸汽进料的进料线是一条与x 轴垂直的直线。
()14. 浮阀塔板的特点是造价较高,操作弹性小,传质性差。
()15. 液泛不能通过压强降来判断。
()16. 筛板精馏塔的操作弹性大于泡罩精馏塔的操作弹性。
()17. 精馏过程中,平衡线随回流比的改变而改变。
()18. 蒸馏的原理是利用液体混合物中各组分溶解度的不同来分离各组分的。
()19. 精馏塔发生液泛现象可能是由于气相速度过大,也可能是液相速度过大。
()20. 蒸馏塔总是塔顶作为产品,塔底作为残液排放。
()21. 浮阀塔板结构简单,造价也不高,操作弹性大,是一种优良的塔板。
()22. 精馏操作的回流比减小至最小回流时,所需理论板数为最小。
()23. 精馏是传热和传质同时发生的单元操作过程。
()24. 正常操作的精馏塔从上到下,液体中轻相组分的浓度逐渐增大。
()25. 精馏操作中,回流比越大越好。
()26. 灵敏板温度上升,塔顶产品浓度将提高。
()27. 筛板塔板结构简单,造价低,但分离效率较泡罩低,因此已逐步淘汰。
()28. 精馏塔板的作用主要是为了支承液体。
()29. 连续精馏停车时,先停再沸器,后停进料。
甲醇精馏岗位安全操作规程

甲醇精馏岗位安全操作规程1、甲醇精馏岗位任务:是通过预精馏塔的加水萃取精馏,除去精醇中轻组分(即低沸点物质,通过主塔除去粗甲醇中重组分(即高沸点物质),得到精甲醇产品,把合格的精甲醇产品送成品库,不合格的甲醇送粗甲醇储罐。
2、精馏原理:精馏又称为分馏,是蒸馏方法的―种。
精馏原理是利用液体混合物中各组分具有不同沸点,在一定温度下,各组分具有不同的蒸汽压,当液体混合物受热时,部分液体气化,液相与气相平衡,在气相中易挥发物质所占比例较大,将此蒸汽部分冷凝所得到的液相含易挥发物质较多,这就是进行了一次简单蒸馏。
重复将此液再生气化,又进行了一次气液平衡,蒸汽又重新冷凝得到液体,其中易挥发的组分又增加了。
如此继续往复,最终就能得到接近组分的物质。
二、工艺流程图(见下页)。
三、岗位工艺指标:‘ 1、预精馏塔:塔底温度:79~81℃ 塔底压力:<0.06MPa 放空温度:35~55℃ 予后比重:0.86~0.88g/mL 预后PH值:7~9 入料量:2―2.5m3/h(视生产情况定) 加水量:30~50%/h(根据预后调节) 加碱量:5%(根据PH值调:1宁) 回流量:3―3.5m3/h 2、精馏塔:塔底温度:108~112℃ 采出温度: (26块板温度)76~78℃ 塔底压力:<0.07MPa 主塔放空温度:<55~C残液比重:≥0.996g/mL 进料量:3~3.5m3/h流量:7~8m3/h 3、蒸汽稳压:0.36~0.38MPa 四、本岗位正常开停车步骤:正常开车步骤:1、开各冷却器冷却水阀,送冷却水。
2、开粗醇罐出口阀门,开预塔入料泵,向预塔进料,使塔釜液位达1/2---2/3。
3、开总蒸汽阀门,开预塔再沸器蒸汽阀,并用压力自调阀拧制蒸汽压力,控制塔釜温度在80℃左右。
4、当预塔回流槽出现液位,开预回流泵,建立回流。
5、当软水收集槽中出现液位,开萃取水泵,水量控制在予塔进料的10~20%。
最新精馏实验报告.
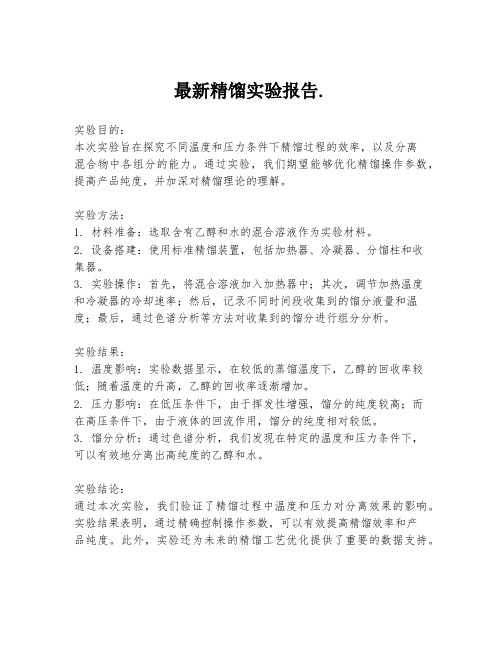
最新精馏实验报告.
实验目的:
本次实验旨在探究不同温度和压力条件下精馏过程的效率,以及分离
混合物中各组分的能力。
通过实验,我们期望能够优化精馏操作参数,提高产品纯度,并加深对精馏理论的理解。
实验方法:
1. 材料准备:选取含有乙醇和水的混合溶液作为实验材料。
2. 设备搭建:使用标准精馏装置,包括加热器、冷凝器、分馏柱和收
集器。
3. 实验操作:首先,将混合溶液加入加热器中;其次,调节加热温度
和冷凝器的冷却速率;然后,记录不同时间段收集到的馏分液量和温度;最后,通过色谱分析等方法对收集到的馏分进行组分分析。
实验结果:
1. 温度影响:实验数据显示,在较低的蒸馏温度下,乙醇的回收率较低;随着温度的升高,乙醇的回收率逐渐增加。
2. 压力影响:在低压条件下,由于挥发性增强,馏分的纯度较高;而
在高压条件下,由于液体的回流作用,馏分的纯度相对较低。
3. 馏分分析:通过色谱分析,我们发现在特定的温度和压力条件下,
可以有效地分离出高纯度的乙醇和水。
实验结论:
通过本次实验,我们验证了精馏过程中温度和压力对分离效果的影响。
实验结果表明,通过精确控制操作参数,可以有效提高精馏效率和产
品纯度。
此外,实验还为未来的精馏工艺优化提供了重要的数据支持。
精馏作业及复习思考题

作业(计算题)1、用常规精馏分离下列烃类混合物:组分甲烷 乙烯 乙烷 丙烯 丙烷 丁烷 ∑ 摩尔分数/%工艺规定塔顶馏出液中丁烷浓度不大于,塔釜残液中丙烷浓度不大于,试应用清晰分割法估算塔顶塔釜产品的量和组成。
2、脱丁烷塔分离下列混合液:组分丙烷 异丁烷 丁烷 异戊烷 戊烷 己烷 iFx (摩尔分数) iDX (摩尔分数) 50.3410-⨯ 4i a 平均值工艺规定丁烷为轻关键组分,异丁烷为重关键组分。
分离所得的塔顶产物组成已列于上表,各组分相对于重关键的相对挥发度也列于表中。
料液为饱和液体。
试求最小回流比m R 。
并应用清晰分割法进行塔顶和塔釜产品的量和组成的估算。
已知轻关键组分丁烷在塔顶产品中的回收率%,重关键组分异戊烷在塔釜产品中的收率为%。
进料量F=983kmol/h 。
3、进料中含正辛烷(1),正庚烷(2),正己烷(3)(摩尔分数)。
今要馏出液中正庚烷浓度2,0.01D x ≤,釜液中正己烷3,0.01W x ≤,试求所需最少理论级数及在全回流条件下馏出液和釜液之组成。
已知各组分之相对挥发度为1,1 1.00a =,2,1 2.27a =,3,1 5.25a =。
4、某分离乙烷和丙烯连续精馏,其进料组成(摩尔分率)如下:组分甲烷 乙烷 丙烯 丙烷 异丁烷 正丁烷 ∑ 组成a 平均要求馏出液丙烯浓度 2.5%≤,釜液中乙烯浓度5%≤,并假定釜液中不出现甲烷,在馏出液中不出现丙烷及其更重的组分。
试求:(1)进料量为100kmol/h ,馏出液,馏出液和釜液的组成级流量;(2)若按饱和液体进料,进料温度为26℃,平均操作压力为,试用简捷法计算理论级数(塔顶采用全凝器);(3)确定进料位置。
5、拟以水为溶剂对醋酸甲酯(1)-甲醇(2)溶液进行萃取精馏分离,已知料液的x1F=,此三元系中各组分的端值常数为:A 12=;A21=;A2S=A S2=;A1S=;AS1=试问当全塔萃取剂浓度为xS=时,水能作为该体系的萃取剂吗?若当全塔萃取剂浓度为xS=时,其萃取效果可提高多少?6、以水为溶剂对乙酸甲酯(1)-甲醇(2)溶液进行萃取精馏分离,料液的x1,F =(摩尔分数),呈露点状态进塔。
精馏作业任务答案解析

6-3. 甲醇(A)—丙醇(B)物系的气—液平衡服从拉乌尔定律。
试求: (1)温度t=80℃、液相组成x =0.5(摩尔分数)时的汽相平衡组成与总压;(2)总压为101.33kPa 、液相组成x =0.4(摩尔分数)时的汽—液平衡温度与汽相组成;(3)液相组成x=0.6、汽相组成y=0.84时的平衡温度与总压。
组成均为摩尔分数。
用Antoine 方程计算饱和蒸汽压(kPa )甲醇 86.23899.157419736.7lg +-=t P oA丙醇 19314.137574414.6lg +-=t P oB式中,t 为温度,℃。
解:(1) 当t=80℃时,甲醇258.286.23899.157419736.7lg =+-=t P oA1.181=⇒oA P (KPa) 丙醇70.119314.137574414.6lg =+-=t P oB ??????9.50=⇒o B P (KPa)又∵液相组成5.09.501.1819.50=--=--=p P P P P x o B o A o B∴所求的总压116=p (kPa) ∴汽相平衡组成PxP y o A =1161.1815.0⨯=78.0=(2)总压oB oA P P P 6.04.033.101+==联立Antoine 方程可解得 汽液平衡温度C t o 6.79=,可得:甲醇饱和蒸汽压53.178=oA P (KPa)丙醇饱和蒸汽压07.50=oB P (KPa)∴汽液组成为pxP y oA =33.10153.1784.0⨯=705.0=(3)∵液相组成6.0=x ,汽相组成84.0=y∴P P P oB oA =+4.06.0,P P oA 84.06.0= 联立二式可求得27=o B o A P P 即oB o A o B o A P P P T P lg 27lg lg 2+=⇒=即19314.137574414.627lg 86.23899.157419736.7+-+=+-t t ∴平衡温度=t 总压=P6-7. 甲醇和丙醇在80℃时的饱和蒸气压分别为181.1kPa 和50.93kPa 。
精馏操作规程

精馏操作规程
《精馏操作规程》
一、目的
精馏是一种有效分离液体混合物成分的方法,本规程的目的是规范和指导精馏操作,保证操作的安全性和实验结果的准确性。
二、适用范围
本规程适用于化学实验室中进行的各种液体混合物的精馏操作,包括但不限于有机物的分离和提纯。
三、安全注意事项
1. 在进行精馏操作前,应仔细检查设备是否完好,确保操作台面整洁,通风情况良好。
2. 液体混合物在进行精馏时可能产生高温或高压,操作人员应穿戴防护装备,避免受伤。
3. 使用高温的精馏设备时,应小心触碰,避免烫伤。
4. 在使用火焰加热时,要注意防范火灾,设备周围不得堆放易燃物品。
四、操作步骤
1. 将液体混合物倒入精馏烧瓶中,加入适量的填充料。
2. 安装冷却管和接收瓶,并确保密封良好。
3. 加热精馏烧瓶,使混合物开始汽化。
4. 蒸馏出的气体通过冷却管冷凝成液体,并流入接收瓶中。
5. 精馏操作结束后,关闭火源,等待设备冷却后,将接收瓶中的纯净物质收集起来。
五、设备清洗
精馏设备操作结束后,应及时清洗设备和玻璃器皿,彻底清除残留物,以便下一次使用。
六、附加说明
1. 操作人员在进行精馏操作时,应遵循实验室现行的安全操作规程和相关规定。
2. 操作人员应对待精馏设备和试剂负责,保护实验室设备的完好和试剂的浪费。
3. 对于特殊的精馏操作,应根据具体情况制定个别的操作规程。
七、变更通知
如有本规程的变更和修订,将通过适当的渠道通知实验室人员。
以上是《精馏操作规程》的主要内容,请操作人员严格按照规程的要求进行操作,以确保实验的顺利进行和实验结果的准确性。
化工原理 精馏练习题

化工原理精馏练习题一、问题描述在一个精馏塔中,对乙酸和甲醇进行分馏。
原料含有10%的乙酸和90%的甲醇。
要求设计一个塔,使得在出口处乙酸的含量为90%以上。
二、基本原理精馏是一种通过分离液体混合物中各种组分的技术。
通常使用精馏塔来实现这一过程。
精馏塔可以分为两个部分:初级分馏区和精馏区。
初级分馏区将液体混合物分为两个相,其中一个相富集乙酸,另一个相则富集甲醇。
精馏区进一步加热液体混合物,产生的蒸汽经过冷凝器后得到两个部分:富含乙酸的液体和富含甲醇的液体。
通过不断回流和再沸腾,可以实现将乙酸含量提高到所需的目标。
三、塔的设计1. 确定精馏塔的高度:- 初级分馏区的高度:根据乙酸和甲醇的相对挥发度,在塔底部设定一个管理区,用于分离液相。
在此区域温度和压力较低,适合乙酸富集。
根据经验法则,初级分馏区的高度应该是整个塔高度的1/3至1/2。
- 精馏区的高度:根据所需乙酸的含量和其他操作参数来确定此区域的高度。
通常,较高的塔设计可以提供更高的分离效果。
2. 确定进料位置:- 进料位置应该位于初级分馏区与精馏区之间的合适位置,以实现较好的分离效果。
通常情况下,进料点应该位于塔的上部,以允许较高的沸点组分从上部释放,从而改善塔的效率。
3. 选择合适的回流比:- 回流比是进入塔中再沸腾的液体与从塔顶冷凝回流的液体的质量比。
适当的回流比对提高分离效果非常重要。
较高的回流比可以提供更高的塔效率,但会增加能耗。
- 在本例中,根据乙酸和甲醇的性质和要求,选择合适的回流比是至关重要的。
四、其他操作参数除了塔的设计之外,还有一些其他操作参数需要考虑:1. 温度和压力:温度和压力的选择取决于乙酸和甲醇的性质。
通常情况下,高温和低压有利于乙酸的分离。
2. 冷凝器的设计:冷凝器用于冷却塔顶的蒸汽,并将其转变为液体。
这样,可以通过回流将纯度较高的乙酸送回塔底。
冷凝器的设计要应对不同的工艺要求和流量。
3. 分离回流液的处理:分离回流液中可能含有乙酸和甲醇。
化工原理:精馏作业

精馏习题1、苯酚(C 6H 5OH )(A )和对甲酚(C 6H 4(CH 3)OH )(B )的饱和蒸汽压数据(假设此物系为理想物系)为:试按总压P=75mmHg (绝压)计算该物系的“t—x —y”数据,并计算在x=0至x=1范围内各点的相对挥发度α,和平均相对挥发度;写出相平衡方程式。
2、若苯-甲苯混和液在45℃时沸腾,外界压力为20.3kpa 。
已知在45℃时,纯苯的饱和蒸气压kpa p 7.220=苯,纯甲苯的饱和蒸气压kpa p 6.70=甲苯。
求其气液相的平衡组成。
3、某二元物系,原料液浓度F x =0.42,连续精馏分离得塔顶产品浓度D x =0.95。
已知塔顶产品中易挥发组分回收率η=0.92,求塔底产品浓度W x 。
以上浓度皆指易挥发组分的摩尔分率。
4、混合液含易挥发组分0.35,泡点进料,经连续精馏塔分离,塔顶产品浓度x D =0.96, 塔底产品浓度x w =0.025(均为易挥发组分的摩尔分率),设满足恒摩尔流假设。
试计算塔顶产品的采出率D/F ;若回流比R=3.2,泡点回流,写出精馏段与提馏段操作线方程。
5、苯-甲苯理想溶液在总压为101.3kpa 下,饱和蒸气压和温度的关系如下:在85℃时,kpa p9.1160=苯,kpa p 460=甲苯;在105℃时,kpa p 2.2040=苯,kpa p 860=甲苯。
求:(1)在85℃和105℃时该溶液的相对挥发度及平均相对挥发度;(2)在此总压下,若85℃时,78.0=苯x ,用平均相对挥发度值求y6、在连续精馏塔中分离含苯50%(质量百分数,下同)的苯-甲苯混和液。
要求馏出液组成为98%,釜残液组成为1%(均为苯的组成)。
M 苯=78,M 甲苯=92。
求:甲苯的回收率。
7、在一两组分连续精馏塔中,进入精馏段中某层理论板n 的气相组成y n +1为0.75,从该板流出的液相组成x n 为0.65(均为摩尔分数),塔内气液比V/L=2,物系的相对挥发度α为2.5,求:(1)从该板上升的蒸气组成y n;(2)流入该板的液相组成x n-1;(3)回流比R。
精馏操作——精选推荐

精馏操作⼀、精馏操作(⼀)设备1、静设备⼀览表2、动设备⼀览表(⼆)⼯艺过程原槽内⽔和⼄醇的混合液,经原料泵输送⾄原料加热器中,预热后,由精馏塔中部进⼊精馏塔,进⾏分离。
⽓相由塔顶馏出,经冷凝器冷却后,进⼊冷凝液槽,经产品泵,⼀部分送⾄精馏塔上部第⼀块塔板做回流,另⼀部送⾄塔顶产品槽作为产品采出。
塔釜残液经塔底换热器冷却后送⾄残液槽。
(三)设备原理1、冷凝器:精馏塔分离后的⽓相物质经冷凝器冷却。
冷凝器进的是⽔,,冷凝器中⽔是下⼝进上⼝出,这样有利于热的⽓体通过玻璃管壁于冷⽔充分接触,冷凝效果更好。
2、再沸器:再沸器也称加热釜或重沸器,使被蒸馏液体⽓化的加热设备。
3、塔底换热器:通过热交换将加热或待冷却的介质与换热器⼯作介质进⾏热交换。
4、精馏塔:在⼀定压⼒下利⽤互溶液体混合物各组分沸点或饱和蒸汽压不同,使轻组分汽化,经多次部分液相汽化和部分⽓相冷凝,使⽓相中的轻组分和液相中的重组分浓度逐渐升⾼,从⽽实现分离。
精馏塔以进料塔为界,上部为精馏段,下部为提溜段,⼀定温度和压⼒的料液进⼊精馏塔后,轻组分在精馏段逐渐压缩,离开塔顶后全部冷凝进⼊回流罐,⼀部分作为塔顶产品,另⼀部分被送⼊塔内作为回流液,回流液的⽬的是补充塔顶上的轻组分,使塔板上的液体组成保持稳定,是精馏操作连续稳定的进⾏。
5、离⼼泵:依靠叶轮的不断运转,液体不断的被吸⼊和排出。
液体在离⼼泵中获得的机械能量最终静压能提⾼流速增⼤。
(四)注意事项1、开车前:对所有设备、阀门、仪表、电⽓、管道等按⼯艺流程图要求和专业技术要求进⾏检查。
2、开车时:确认各阀门是否正常开启关闭,观察⽣产过程中各⼯艺操作指标是否在正常范围内。
3、停车时:系统停⽌加料原料预热器停⽌加热,关闭原料液泵进出⼝阀,停原料泵。
根据塔内物料情况再沸器停⽌加热,塔顶温度下降时⽆冷凝液流出后,关闭塔顶冷凝器冷却⽔进⽔阀,停冷却⽔停回流泵,关泵进出⼝阀。
在物料冷却后开再沸器和预热器排污阀放出预热器及再沸器内物料,开塔底冷凝器排污阀,塔底产品槽排污阀,放出塔底冷凝器内物料、塔底产品槽内物料。
影响精馏操作的主要因素及精馏节能技术浅析

影响精馏操作的主要因素及精馏节能技术浅析摘要:精馏作业是化工生产中的一个重要作业单元,由于其高能耗和节能效果,引起了化工行业的关注。
减少市场产品生产过程中的能源消耗对于降低成本和提高市场竞争力至关重要效果。
关键词:精馏;节能;发展;趋势精馏是多级分离过程,即同时进行多次部分汽化和部分冷凝的过程,因此可以使混合液得到几乎完全分离。
精馏可视为多次蒸馏演变而来,不管何种操作方式,混合液中组分间挥发度差异是精馏分离的前提和依据。
精馏是一个多阶段的分离过程,即多个部分汽化和同时部分冷凝的过程,从而使混合物几乎完全分离。
精馏可以看作是几次蒸馏的过程,无论采用何种工艺,混合物成分之间挥发性的差异都是精馏分离的先决条件和基础。
一、精馏的操作和影响因素1.蒸馏原理。
在大多数工艺操作和设备中,蒸馏塔的操作形式是最常见的。
他的工作过程包括在塔的结构中进行适当的蒸馏。
操作程序分为连续蒸馏塔和间歇蒸馏塔。
上升的蒸汽通过塔的底部进入,并与塔入口的液体接触。
分离是在高沸点和低沸点的气相中进行的。
一部分液体被送回蒸馏塔,一部分被除去。
蒸馏过程。
化工行业的能源消耗最高。
数据显示,精馏和分离过程的能耗占整个化工行业的40%,其中精馏占95%。
在美国,工业蒸馏过程的能源消耗几乎占全国能源消耗的3%。
因此,必须在实际生产条件下考虑节能技术和作业对运行的影响需要在实际生产条件下加以解决。
2.影响蒸馏塔的因素。
(1)实际操作只能在一定的柱压下进行,因此蒸馏通常必须保持恒定的压力。
操作过程中的压力变化会改变不同板的气液成分,影响气相轻组分的浓度。
一般来说,压力的增加或减少对蒸馏塔的分离浓度有很大的影响。
(2)进料量大小也是一个决定因素。
不应超过塔顶冷凝器和加热釜的范围。
同时,饲料成分的变化会影响精馏过程。
进料量成分的变化可能导致头等产品不符合规定。
进料量成分的变化也会改变整个塔的物质平衡和工艺。
(3)温度变化对精馏作业有很大影响。
材料温度越低,塔底的热负荷越高,塔顶的冷负荷越低。
精馏操作规程
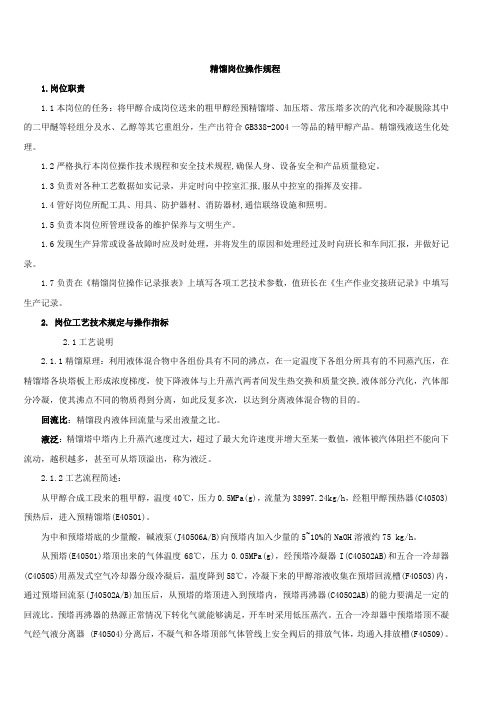
精馏岗位操作规程1.岗位职责1.1本岗位的任务:将甲醇合成岗位送来的粗甲醇经预精馏塔、加压塔、常压塔多次的汽化和冷凝脱除其中的二甲醚等轻组分及水、乙醇等其它重组分,生产出符合GB338-2004一等品的精甲醇产品。
精馏残液送生化处理。
1.2严格执行本岗位操作技术规程和安全技术规程,确保人身、设备安全和产品质量稳定。
1.3负责对各种工艺数据如实记录,并定时向中控室汇报,服从中控室的指挥及安排。
1.4管好岗位所配工具、用具、防护器材、消防器材,通信联络设施和照明。
1.5负责本岗位所管理设备的维护保养与文明生产。
1.6发现生产异常或设备故障时应及时处理,并将发生的原因和处理经过及时向班长和车间汇报,并做好记录。
1.7负责在《精馏岗位操作记录报表》上填写各项工艺技术参数,值班长在《生产作业交接班记录》中填写生产记录。
2. 岗位工艺技术规定与操作指标2.1工艺说明2.1.1精馏原理:利用液体混合物中各组份具有不同的沸点,在一定温度下各组分所具有的不同蒸汽压,在精馏塔各块塔板上形成浓度梯度,使下降液体与上升蒸汽两者间发生热交换和质量交换,液体部分汽化,汽体部分冷凝,使其沸点不同的物质得到分离,如此反复多次,以达到分离液体混合物的目的。
回流比:精馏段内液体回流量与采出液量之比。
液泛:精馏塔中塔内上升蒸汽速度过大,超过了最大允许速度并增大至某一数值,液体被汽体阻拦不能向下流动,越积越多,甚至可从塔顶溢出,称为液泛。
2.1.2工艺流程简述:从甲醇合成工段来的粗甲醇,温度40℃,压力0.5MPa(g),流量为38997.24kg/h,经粗甲醇预热器(C40503)预热后,进入预精馏塔(E40501)。
为中和预塔塔底的少量酸,碱液泵(J40506A/B)向预塔内加入少量的5~10%的NaOH溶液约75 kg/h。
从预塔(E40501)塔顶出来的气体温度68℃,压力0.05MPa(g),经预塔冷凝器I(C40502AB)和五合一冷却器(C40505)用蒸发式空气冷却器分级冷凝后,温度降到58℃,冷凝下来的甲醇溶液收集在预塔回流槽(F40503)内,通过预塔回流泵(J40502A/B)加压后,从预塔的塔顶进入到预塔内,预塔再沸器(C40502AB)的能力要满足一定的回流比。
精馏岗位安全操作规程

精馏岗位安全操作规程(共33页)--本页仅作为文档封面,使用时请直接删除即可----内页可以根据需求调整合适字体及大小--编号:TC2019-01版本号:GC-B/0寿光市天成精细化工厂精馏岗位安全操作规程编制:编制小组修订:审核:批准:发布日期:2019年04月2日实施日期:2019年04月05日前言本厂岗位安全操作规程最初的编制是从2007年的安全标准化工作开始,中间经过几个修订、完善,整个结构是十二部分。
本次的修订依据BD37/T 2401和AQ/T 3034标准要求,结合本厂管理的实际,进行的系统升级。
本次修订的规程将取代以前版本的规程,与上版规程相比,变化的内容包括结构性调整和技术性调整,分别包括以下内容结构性调整:——按照BD37/T 2401标准采用十部分的结构形式。
技术性调整:——细化了原料及产品化学品危害信息的内容;——主要设备操作参数控制范围的规范。
本次岗位操作规程的修订结合岗位作业危害分析的内容,以及风险分级管控和隐患治理排查的信息要求,对内容的修改更加细化、完善。
本版规程从2019年04月05日开始实施。
目录1. 岗位设置 .................................................................................................................... ..1岗位名称、任务及管辖范围 .. (1)岗位定员及分工 (1)岗位职责及任职条件 (2)2. 工艺操作方法 (3)工艺安全信息 (3)工艺技术信息 (6)工艺设备信息 (8)操作方法 (9)3. 开停车、故障及异常情况处理 (10)开车程序 (10)正常停车程序 (10)紧急停车程序及处理方法 (11)故障及异常情况处理 (11)4.巡回检查 (11)巡回检查制度 (11)岗位巡检内容 (12)5. 设备维护保养制度 (12)设备维护可按班、周维护 ........................................................... 错误!未定义书签。
精馏车间技术操作规程

精馏车间技术操作规程1、工艺流程及技术指标锌是一种白而略带蓝灰色的金属,质地较软。
纯锌具有良好的延展性,其化学性质较为爽朗,广泛应用于化工、医药等行业。
本车间是以ISP熔炼车间产出的粗锌为原料,采纳精镏法生产合格精锌的过程。
精镏法是目前广泛采纳的一种粗锌精炼方法。
精馏法的精炼原理是利用粗锌中的杂质各具不同沸点的特性,要紧金属的沸点为:锌的沸点为906.97℃,镉的沸点为767.58℃,铅的沸点为1525℃,铁的沸点为3235℃,铜的沸点为2270℃,锡的沸点为2735℃。
通过分馏过程,使锌与其他杂质分离,从而得到高纯度的锌,并使铅、镉、铟等金属分别得到富集。
锌的精馏过程分为两个时期,在两种结构不同,原理相似的密闭作业的精馏塔内进行。
第一时期是在铅塔中进行,使粗锌中的锌、镉与其他高沸点的杂质铅铁等分离,产出馏余锌与含镉锌;第二时期是在镉塔中进行,使锌与镉分离,产出高镉锌和高纯度的精馏锌。
产出的馏余锌经熔析炉精炼,并辅之锌精馏加铝工艺,去掉杂质铁,富集铅、铟等有价金属,产出B#锌(也叫无镉锌)。
1.1工艺流程作业程序概述:第一将粗锌加入熔化炉内,经自动给料器、铅塔加料器、加料管流入铅塔。
由上层蒸发盘之溢流孔至下层蒸发盘时,一面受燃烧室加热升温,一面与上升金属蒸汽进行热交换,从而使锌充分受热,镉与锌大部分蒸发,同时与上升气流夹带的高沸点金属铅雾一并上升至回流部分,利用回流盘的分凝回流作用,铅雾被洗涤下来,锌镉蒸汽进入铅塔冷凝器得到含镉锌。
部分锌和高沸点的杂质,经铅塔底部、下延部进入精炼炉,经加铝熔析精炼后,得到#B锌、硬锌和富铟粗铅。
#B锌作为原料返回熔化炉,含镉锌经镉塔加料器、加料管进入镉塔。
在镉塔内同样进行分凝与回流过程后进入大冷凝器,使锌与镉蒸汽进一步分离富集,高镉锌蒸汽进入小冷凝器,产出高镉锌,做为精镉生产的原料。
由镉塔脱去镉的纯锌液经下延部进入纯锌炉,按时放出铸锭、得到精锌。
1.2要紧经济技术指标1)一座单铅塔日处理粗锌量:54—63吨。
烯烃精馏系统操作与控制—作业乙烯精馏
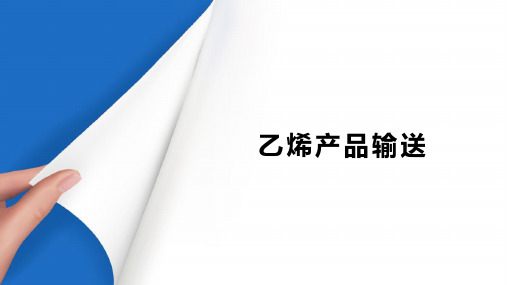
异常情况处理
乙烯精馏塔回流罐 液位控制
ONTENTS
目 录
1 控制目的 2 相关参数 3 控制方式
01 控制目的
保证回流罐液位,确保回流不中断,稳定塔顶温度、 压力。
02 相关参数
1
相关
2
参数
3
4
回流量大小 塔顶冷凝量大小 160-P-603故障 塔釜温度高低
4
相关 参数
5
160P601抽空 塔釜温度高低
03 控制方式
160LC610与160FC616组成串级控制
正常调节
异常情况处理
乙烯精馏塔塔釜 液位控制
ONTENTS
目 录
1 控制目的 2 相关参数 3 控制方式
01 控制目的
保证正常液位,防止空塔或满塔,造成塔底轻组分过多 或塔顶乙烷含量多,同时保证侧线采出量稳定。
02 相关参数
1
进料负荷的大小
4
相关
参数
5
6
进料温度高低 进料中轻组分含量
侧线采出量
03
控制方式
联系压缩岗位保证冷剂温度。
控制 方式
通过160E510的液位160LC520控制160LV520开
1
度大小来调节丙烯冷剂的量
2 通过控制160PC530控制160T503的压力
正常调节
异常情况处理
异常情况处理
1 乙烯产品紧急汽化器 2 不合格乙烯汽化器
主要参数
设计工况
乙烯产品 乙烯产品1号蒸发器
乙烯产品 丙烯冷剂 乙烯产品2号蒸发器 乙烯产品
丙烯冷剂
流量 kg/hr 39.019
38.520 170.950
38.520 273.730
作业活动清单精馏

编制人:审核人:
作业活动清单﹙十一﹚
部门:甲醇车间
序号
作业活动地点
作业活动名称
主要活动内容
备注
11
精馏岗位
精馏岗位停车
〈1〉停止向预塔进料,
停碱液泵〈2〉切采出至粗
醇槽〈3〉关闭预塔再沸器
加压塔再沸器蒸汽总阀。
〈4〉停回流泵〈5〉常压塔
底残液打回粗甲醇槽〈6〉
向加压塔送液至低限5~10%
时停预后甲醇泵〈7〉停止向
加压塔送液,关闭加压塔向
常压塔进料前后切断阀,关
闭采出切换阀〈8〉关闭残液
泵出口前后切断阀〈9〉关闭
预塔前后切断阀和杂醇采出
阀〈10〉排塔和排净〈11〉
关闭预塔空器
至排放槽前后切断阀及加压
塔回流槽排放槽,视情况充
氮气进行保护〈13〉关闭循
环水上水、回水阀〈14〉停
连续精馏塔装置安全操作及保养规程

连续精馏塔装置安全操作及保养规程连续精馏塔操作是一项高风险作业,为确保装置的安全持续运行和人身安全,需要遵守一系列的安全操作规程和保养要求。
本文将详细介绍连续精馏塔装置的安全操作和保养规程。
安全操作规程1. 安全准备1.1 在工作人员进入精馏塔作业区域前,必须穿戴好相关劳保用品,包括安全鞋、安全帽、防护服和手套等。
1.2 在工作人员进入作业区域前应严格按照操作规程进行安全培训并通过岗位考试。
1.3 在作业前工作人员应清理作业区域内杂物,保持作业区域的整洁和安全。
2. 操作步骤2.1 严格按照程序进行操作,不得修改或省略任何环节。
2.2 在操作过程中,应当注重观察和监测设备运行情况,如发现异常及时上报。
2.3 在操作过程中,应严格遵守火源禁入规定,禁止吸烟和使用明火。
3. 突发事件处理3.1 在突发事件发生时,应迅速切断设备电源,并采取相应的应急措施。
3.2 发生火灾、爆炸等严重事故时,应立即进行报警和组织人员撤离。
3.3 在发生事故后,全体从业人员应当主动参与事故调查并积极配合事故处置工作。
4. 工艺操作规程4.1 在精馏塔操作中,应根据原料的性质和特点,确保精馏塔内气体成分和温度的稳定。
4.2 在操作过程中,应随时检查各类阀门的开合情况,确保其正常运行。
4.3 严格按照工艺要求进行加料、加热、冷凝等操作。
4.4 在操作过程中,应严格遵守操作规程中的各项条件和要求,以确保装置的安全稳定运行。
保养规程为保证连续精馏塔的正常运行和设备的寿命,需要按照一定规律进行定期保养和维护。
1. 定期检查1.1 对设备部件进行定期检查,如加热器、冷凝器、管道等。
1.2 对设备进行清洗,确保设备内外的清洁和卫生。
1.3 对设备内各类阀门、接头定期检查,确保其正常开启和关闭。
2. 保养工作2.1 轴承、电机等机械部件定期进行润滑保养,确保设备的正常运转。
2.2 对设备进行清洗、消毒工作,确保装置内外卫生洁净。
2.3 定期进行漏气和泄漏检查,及时更换、修理损坏的部件。
化工原理精馏作业

化工原理精馏作业精馏是一种在化工领域中常用的分离技术,通过不同组分在液相和气相之间的分配系数差异,将混合物中的各种组分进行有效分离的方法。
在精馏过程中,液体混合物首先被加热至沸点,然后通过蒸馏,将沸点低的组分蒸发出来,然后再冷凝成液体,从而实现各种组分的分离。
精馏操作常用于石油化工、化学制药、食品饮料等领域。
作为一名化工工程专业的学生,我经常接触到精馏操作,并且在实验室中也进行了一定数量的精馏操作。
在这次的作业中,我们需要对一个给定的混合物进行精馏操作,并确定各组分的塔顶和塔底流量、温度和组分浓度变化。
这将对我们的理论知识和实验操作能力提出很高的要求,下面我将详细描述这次精馏作业的过程。
首先,我们需要准备实验所需的设备和试剂。
在这次的精馏实验中,我们使用的是一座直管式精馏塔,内部填充了填料用于增加塔板数,提高分馏效率。
另外,我们还需要一个加热炉、冷凝器和采样瓶等设备,以及乙醇和水的混合物作为原料。
在实验操作之前,我们要对设备进行检查和清洁,确保设备处于良好的状态。
接下来,我们将开始进行实验操作。
首先,将混合物倒入精馏塔中,并通过加热炉将其加热至混合物的沸点。
随着加热的进行,混合物中沸点低的组分将首先蒸发出来,然后通过冷凝器冷凝成液体,从而得到塔顶产物。
而沸点高的组分则会继续停留在塔中,形成塔底产物。
在精馏过程中,我们会对塔顶和塔底的流量、温度和组分浓度进行连续监测和采样。
通过对这些参数的监测,我们可以得到混合物中不同组分的分离情况,确定精馏效果的好坏。
在实验过程中,我们需要不断调整加热功率和冷却水的流量,以确保精馏过程的顺利进行。
最后,在实验结束时,我们将收集和分析所有的数据,并绘制出流量、温度和组分浓度随时间变化的曲线图。
通过这些数据,我们可以对精馏塔的操作情况进行评估,找出操作中存在的问题并提出改进措施。
同时,我们还可以计算出各组分的分离效率和收率,对实验结果进行总结和分析。
通过这次精馏作业的实践,我对精馏操作有了更深入的了解,不仅使我对化工原理有了更深的认识,同时也提高了我的实验操作技能。
- 1、下载文档前请自行甄别文档内容的完整性,平台不提供额外的编辑、内容补充、找答案等附加服务。
- 2、"仅部分预览"的文档,不可在线预览部分如存在完整性等问题,可反馈申请退款(可完整预览的文档不适用该条件!)。
- 3、如文档侵犯您的权益,请联系客服反馈,我们会尽快为您处理(人工客服工作时间:9:00-18:30)。
精馏习题
1、苯酚(C 6H 5OH )(A )和对甲酚(C 6H 4(CH 3)OH )(B )的饱和蒸汽压数据(假设此物系为理想
物系)为:
试按总压P=75mmHg (绝压)计算该物系的“t—x —y”数据,并计算在x=0至x=1范围内各点的相对挥发度α,和平均相对挥发度;写出相平衡方程式。
2、若苯-甲苯混和液在45℃时沸腾,外界压力为20.3kpa 。
已知在45℃时,纯苯的饱和蒸气压
kpa p 7.220=苯,纯甲苯的饱和蒸气压kpa p 6.70=甲苯。
求其气液相的平衡组成。
3、某二元物系,原料液浓度F x =0.42,连续精馏分离得塔顶产品浓度D x =0.95。
已知塔顶产品中易挥发组分回收率η=0.92,求塔底产品浓度W x 。
以上浓度皆指易挥发组分的摩尔分率。
4、混合液含易挥发组分0.35,泡点进料,经连续精馏塔分离,塔顶产品浓度x D =0.96, 塔底产品浓度x w =0.025(均为易挥发组分的摩尔分率),设满足恒摩尔流假设。
试计算塔顶产品的采出率D/F ;若回流比R=3.2,泡点回流,写出精馏段与提馏段操作线方程。
5、苯-甲苯理想溶液在总压为101.3kpa 下,饱和蒸气压和温度的关系如下:在85℃时,kpa p
9.1160=苯
,
kpa p 460=甲苯;在105℃时,kpa p 2.2040=苯,kpa p 860=甲苯。
求:
(1)在85℃和105℃时该溶液的相对挥发度及平均相对挥发度;(2)在此总压下,若85℃时,78.0=苯x ,用平均相对挥发度值求y
6、在连续精馏塔中分离含苯50%(质量百分数,下同)的苯-甲苯混和液。
要求馏出液组成为98%,釜残液组成为1%(均为苯的组成)。
M 苯=78,M 甲苯=92。
求:甲苯的回收率。
7、在一两组分连续精馏塔中,进入精馏段中某层理论板n 的气相组成y n +1为0.75,从该板流出的液相组
成x n为0.65(均为摩尔分数),塔内气液比V/L=2,物系的相对挥发度 为2.5,求:(1)从该板上升的蒸气组成y n;(2)流入该板的液相组成x n-1;(3)回流比R。