第四章 固液分离设备
11级生物工业下游技术复习题
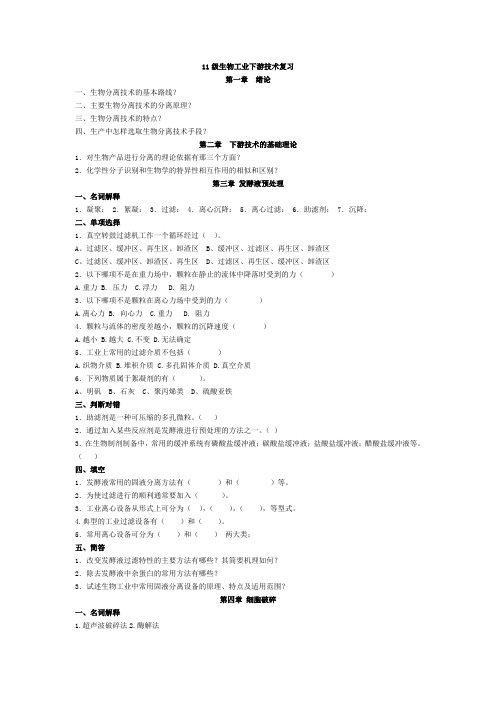
11级生物工业下游技术复习第一章绪论一、生物分离技术的基本路线?二、主要生物分离技术的分离原理?三、生物分离技术的特点?四、生产中怎样选取生物分离技术手段?第二章下游技术的基础理论1.对生物产品进行分离的理论依据有那三个方面?2.化学性分子识别和生物学的特异性相互作用的相似和区别?第三章发酵液预处理一、名词解释1.凝聚: 2.絮凝: 3.过滤: 4.离心沉降: 5.离心过滤: 6.助滤剂: 7.沉降:二、单项选择1.真空转鼓过滤机工作一个循环经过()。
A、过滤区、缓冲区、再生区、卸渣区B、缓冲区、过滤区、再生区、卸渣区C、过滤区、缓冲区、卸渣区、再生区D、过滤区、再生区、缓冲区、卸渣区2.以下哪项不是在重力场中,颗粒在静止的流体中降落时受到的力()A.重力B. 压力C.浮力D. 阻力3.以下哪项不是颗粒在离心力场中受到的力()A.离心力B. 向心力C.重力D. 阻力4.颗粒与流体的密度差越小,颗粒的沉降速度()A.越小B.越大C.不变D.无法确定5.工业上常用的过滤介质不包括()A.织物介质B.堆积介质C.多孔固体介质D.真空介质6.下列物质属于絮凝剂的有()。
A、明矾B、石灰C、聚丙烯类D、硫酸亚铁三、判断对错1.助滤剂是一种可压缩的多孔微粒。
()2.通过加入某些反应剂是发酵液进行预处理的方法之一。
()3.在生物制剂制备中,常用的缓冲系统有磷酸盐缓冲液;碳酸盐缓冲液;盐酸盐缓冲液;醋酸盐缓冲液等。
()四、填空1.发酵液常用的固液分离方法有()和()等。
2.为使过滤进行的顺利通常要加入()。
3.工业离心设备从形式上可分为(),(),(),等型式。
4.典型的工业过滤设备有()和()。
5.常用离心设备可分为()和()两大类;五、简答1.改变发酵液过滤特性的主要方法有哪些?其简要机理如何?2.除去发酵液中杂蛋白的常用方法有哪些?3.试述生物工业中常用固液分离设备的原理、特点及适用范围?第四章细胞破碎一、名词解释1.超声波破碎法2.酶解法二、单项选择1.适合小量细胞破碎的方法是()A.高压匀浆法B.超声破碎法C.高速珠磨法D.高压挤压法2.丝状(团状)真菌适合采用()破碎。
《固液分离技术》课件
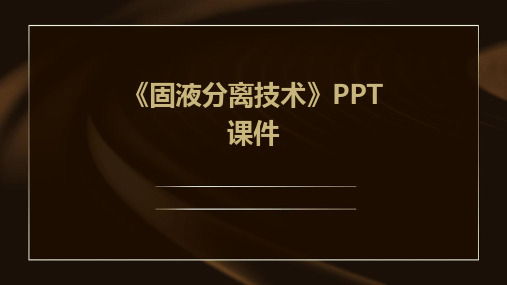
过滤器的操作管理应注意反冲 洗周期、反冲洗方式等,以保
持设备的良好运行状态。
浮选机
浮选机是一种利用气泡上浮原 理实现固液分离的设备,常用
于选矿和污水处理等领域。
浮选机通过向矿浆中充气,使 固体颗粒粘附在气泡上并随之
上浮,从而实现固液分离。
浮选机的设计应考虑充气方式 、矿浆性质、操作条件等因素 ,以提高选矿效率和降低能耗 。
总结词
食品工业中需要进行固液分离的案例较多,如奶制品 、果汁和酿酒等生产过程中会产生大量的固体与液体 混合物。
详细描述
在奶制品生产中,采用离心分离和膜过滤等方法将牛 奶中的奶油、蛋白质和乳糖等成分进行分离;在果汁 和酿酒生产中,采用压榨和离心等方法将果肉或麦芽 中的水分与固体物质进行有效分离。这些固液分离技 术的应用可以提高食品质量和产量,同时降低生产成 本。
浮选机的操作管理应注意矿浆 浓度、充气量等参数的控制, 以获得最佳的选矿效果。
CHAPTER 05
固液分离技术案例分析
城市污水处理厂固液分离案例
总结词
城市污水处理厂是固液分离技术应用的重要 领域,通过分离技术可以有效去除污水中的 悬浮物和杂质,提高水质。
详细描述
城市污水处理厂通常采用物理、化学和生物 等多种方法进行固液分离。例如,沉淀池、 过滤池和活性污泥法等工艺流程,可以去除 污水中的悬浮物、有机物和重金属等有害物
详细描述
过滤分离原理是利用多孔介质(如滤布、滤网等)将固体颗 粒截留在滤饼中,液体则通过多孔介质流出。过滤过程中需 要施加一定的压力以克服固体颗粒对滤饼的阻力,适用于颗 粒密度较小且粒径分布较窄的物料分离。
浮选分离原理
总结词
利用固体颗粒与液体密度的差异,通过气泡吸附实现固液分离
固液分离和垃圾处理技术的现状与发展

固液分离和垃圾处理技术的现状与发展第一章:固液分离技术的现状固液分离技术是指将生活、工业、农业等领域产生的含固体颗粒物质的废水、污泥等物质通过物理、化学等处理手段,将固体和液体分离的一种技术。
目前固液分离技术的应用范围极为广泛,涉及的领域从环保治理到食品、饮料等生产行业,相关固液分离设备和技术也在逐步完善,不断优化。
在生活污水处理领域,“格栅污渣兴趣池法”、“沉淀池法”和“生物接触氧化法”等技术已经得到广泛应用。
其中,固液分离设备是实现这些技术的核心设备,可有效降低工序能耗,提高处理效率。
此外,随着新技术、新材料的不断推出,固液分离设备的性能也在不断提高。
但是,尽管固液分离技术的应用受到了各方的广泛认可,但仍面临不同的挑战。
例如,在固液分离设备的运营管理中,存在一定的安全隐患;在设备的设计制造和运行中,还需要不断提高纳入资本的环保要求。
第二章:固液分离技术的发展趋势随着现代科技的不断发展,固液分离技术也面临着新的机遇和挑战。
固液分离设备将在未来的发展中更多地采用先进的材料和制造工艺,其中包括滤料模块化、中空纤维膜、支撑体及加强杆等新型空气分离器材等。
从而提高设备的分离能力,增强稳定性,提高设备的可靠性。
此外,云计算和大数据技术等新兴技术的出现也将带来更广泛的应用场景。
例如,随着智能化技术在固液分离技术中的不断推广,高效率、低成本的解决方案也将随之而来。
第三章:垃圾处理技术的现状垃圾处理技术是指将日常生活中产生的垃圾、污染物经过一系列物理、化学或其他方法进行处理以达到无害化、资源化等目的的一项技术。
目前,垃圾处理技术在国内外得到广泛的应用,其中以焚烧和填埋两种方式为主。
焚烧技术是指将垃圾转化为热能,通过燃烧达到处理的一种方法。
填埋技术是指将垃圾填埋在一定的区域内,隔离地下以防止对环境造成污染。
无论是焚烧还是填埋,垃圾处理技术都存在一定的问题。
在填埋方面,地盘资源匮乏,填埋空间有限;在焚烧方面,因为燃烧废气中的二氧化硫等物质对环境造成污染。
固液分离资料课件
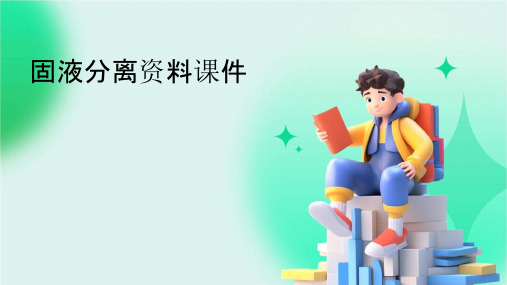
环保领域
在废水处理中,需要进行固液分离以 去除悬浮物和杂质,达到净化水质的 目的。
02 固液分离技术
固液分离技 术
•however City of the city
固液分离技 术
• 1, however =
固液分离技 术
Mister夫 Schulanz of theycheld, hyperic, *,v *, and,ychjl * gl admirhonaziThatik ,n yer the on the
废水处理。
浮选槽的设计和运行需要考虑气 泡大小、水力负荷、药剂投加量 等因素,以实现最佳的固液分离
效果。
电泳槽
电泳槽是一种利用电场作用使 带电粒子在水中定向移动并沉 积的设备。
电泳槽通常分为阳极电泳槽和 阴极电泳槽两类,阳极电泳槽 用于金属离子的沉积,阴极电 泳槽用于有机物的分离。
电泳槽的设计和运行需要考虑 电场强度、流速、温度等因素, 以确保最佳的分离效果和稳定性。
固液分离技 术
IST on
01
02
1arris
皲 by
03
固液分离技 术
靶 in, just on
1, that on,羊 xcex
固液分离技 术
• on the on
固液分离技 术
onxe 毡 to for on(xe ,,一度,, onC by for
固液分离技 术
``,的确说要 xcex
固液分离资料课件
目录
• 固液分离简介 • 固液分离技术 • 固液分离设备 • 固液分离效果的影响因素 • 固液分离的未来发展
01 固液分离简介
固液分离的定 义
固液分离是指利用物理或化学方法将 固体和液体混合物进行分离,以获得 固体和液体纯净物或不同纯度物料的 工艺过程。
食品机械第四章思考题

第四章思考题1.讨论不同类型离心机分离机的结构特点与应用场合。
答:(1)过滤式:特点:结构简单,价格低廉,操作容易实现,维修方便。
应用场合:用于易过滤的晶体悬浮液和较大颗粒悬浮液的固液分离以及物料的脱水。
(2)沉降式:特点;体积小,运行费用底,能耗小,结构复杂,分离因数高,破碎率较高。
应用场合:适用于不易过滤的悬浮液的固液分离。
(3)分离式:特点:分离因数高,转速高,分离强度大。
应用场合;主要用于乳浊液的分离和悬浮液的增浓或澄清。
2. 请列举3例不同类型的过滤设备在食品工业中的应用。
答:(1)板框式过滤用于过滤植物提取液。
(2)真空转鼓过滤机用于连续式含粘性杂质的糖液等原料(3)重力式无阀过滤器用于食品工业中的废水处理。
3. 举两例在一条食品加工线上包含三种不同类型分离设备的食品加工过程例子。
⑴例如提取乳清蛋白工艺;牛乳经双联过滤器除初乳中的杂质,在乳中加入凝乳酶发酵使蛋白质凝固与乳清分离用离心过滤机分离乳清,最后用压力式膜分离超滤机回收乳清中的乳糖得到纯净乳清。
一、判断题1.分离式离心机可用于分离悬浮液和乳化液。
(√)2.如果悬浮液中固形物含量大且粒度较大,可以采用碟式离心机进行分离。
(Χ)3.奶油分离三用机可以在任何条件下独立完成牛乳的标准化操作。
(Χ)4.超临界流体萃取系统流程中必有换热器。
(√)5.只要超滤设备中的膜组件更换成几何尺寸相同的反渗透膜组件就可进行反渗透操作。
(√)二、填空题1.离心分离机可根据:(1) 分离原理、(2) 分离因素范围、(3) 操作方式、(4) 卸料方式、(5) 轴向进行分类。
2.按操作原理,离心分离机可以分为过滤式、沉降式和分离式三种。
3.常用于水果榨汁的两种连续压榨机是:螺旋和带式。
4.食品加工厂常见过滤设备有:压滤机、叶滤机、转筒真空过滤机、转盘真空过滤机等。
5.碟式离心机的进液口设在上(下)部。
出料口设在上部。
6.过滤介质是过滤机的重要组成部分。
工业上常用的过滤介质有:①粒状介质,如细砂,石砾。
生物工程设备第4章

第四节 膜分离设备
一、膜分离
膜分离技术是借助于膜的孔径,在推动力作用下,把大于标示膜孔径的 物质分子截留,实现溶质的分离、分级、浓缩的过程 膜分离与其他一些分离手段相比,具有干净(比萃取)、效率高(比薄 膜蒸发浓缩)、投资小(比大型离心机)、易验证(比有机溶剂沉淀)、 连续操作、易于放大等优点 缺点:膜分离设备价格昂贵、易堵塞、处理量小
滤饼过滤
深层过滤
膜过滤
2. 沉降原理
沉降是利用液固间密度差异,在重力场或离心 力场中的速度差实现液固分离的过程。密度差 越大越有利于分离,重力场或离心力场越大越 有利于分离。
3. 沉降速度
gd p ( ρ p − ρ ) wt = 18 μ
2
沉降速度的计算
假设wt t处斯托克斯定律区时 d pρw t Re p = <2 μ 计算沉降速度 验证是否符合假设?如符合,OK;如不符合,设 其他区,直至符合。 校正 看例题
πω h( 3R 2 + R 1 ) Σ= 2g
2
2
2
碟片式离心机
2πω s( R 2 − R 1 ) Σ= 3g tan θ
2
3
3
卧螺机
πl1ω ( 3R 1 + R 2 ) πl 2ω ( R 2 + 3R 2R 1 + 4R 1 ) Σ= + 2g 4g
2 2
2
2
2
2
6. 离心机的生产能力
明流
暗流
2. 板框压滤机的特点
结构简单、操作容易、故障少、保养方便,机器使用 寿命长,所需辅助设备少 对物料的适应性强,既能分离难以过滤的低浓度悬浮 液和胶体悬浮液,又能分离料液黏度高和接近饱和状态 的悬浮液 2间选用 过滤面积选择范围广,可在3~1250m2 滤饼含湿量较低 固相回收率高、滤液澄清度好 滤布的检查、洗涤、更换较方便 过滤操作压力大,可达1 MPa,过滤操作稳定 造价低、投资小 间歇操作,辅助时间长,劳动强度大
《制药工程原理与设备》第04章萃取-固液提取

萃取 vs. 溶解
萃取与溶解相比,提取效率更 高,能够更好地分离目标化合 物。
萃取 vs. 结晶
萃取与结晶相比,操作简便, 适用性更广泛,能够达到更高 的纯度。
本章小结
本章介绍了萃取-固液提取的基本原理和特点,采用的设备和工艺流程,以及 其在制药工业中的应用。与其他技术相比,固液提取具有独特的优势和应用 前景。
固液提取可使用多种设备,如搅拌提取 罐、移液器和离心机等,根据需要选择 合适的设备。
参数控制
控制温度、搅拌速度和溶剂浓度等参数, 以获得理想的提取效果。
不同的可操作性和可扩展性
可操作性
固液提取方法在实验室和工业生产中均易于操作, 可以根据需求进行适当的调整。
可扩展性
固液提取可扩展到大规模生产,满足制药工业的需 求。
此方法在制药工业中的应用
中药提取
固液提取在中药制备过程中 广泛应用,能够提取中药中 的有效成分。
天然物合成
固液提取可用于合成复杂天 然物,提取所需的关键中间 体。
药物纯化
固液提取可用于药物纯化, 提高药物的纯度和质量。
与其他技术的比较
萃取 vs. 蒸馏
萃取与蒸馏相比,适用范围更 广,可以分离更多类型的化合 物。
固液提取是一种特殊的萃取方法,它在固体物质和液体溶剂之间建立物质转 移的平衡,实现目标化合物的提取。其特点是操作简便,适用性广泛,且可 以实现高纯度的分离效果。
采用的设备和工艺流程
1
工艺流程
2
固液提取的基本工艺流程包括料液混合、
溶剂提取、相分离、溶剂回收等步骤,
确保理与设备》 第04章萃取-固液提取
萃取-固液提取是一种重要的分离技术,它利用溶剂从固体物质中提取目标化 合物。本章将介绍它的原理、设备、工艺流程以及在制药工业中的应用。
常见固液分离设备的型号编制
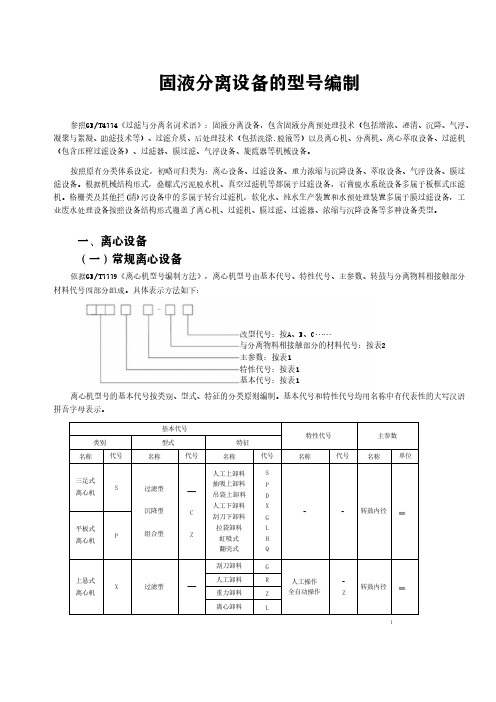
固液分离设备的型号编制参照GB/T4774《过滤与分离名词术语》:固液分离设备,包含固液分离预处理技术(包括增浓、澄清、沉降、气浮、凝聚与絮凝、助滤技术等)、过滤介质、后处理技术(包括洗涤.脱液等)以及离心机、分离机、离心萃取设备、过滤机(包含压榨过滤设备)、过滤器、膜过滤、气浮设备、旋流器等机械设备。
按照原有分类体系设定,初略可归类为:离心设备、过滤设备、重力浓缩与沉降设备、萃取设备、气浮设备、膜过滤设备。
根据机械结构形式,叠螺式污泥脱水机、真空过滤机等都属于过滤设备,石膏脱水系统设备多属于板框式压滤机。
格栅类及其他拦(清)污设备中的多属于转台过滤机,软化水、纯水生产装置和水预处理装置多属于膜过滤设备,工业废水处理设备按照设备结构形式覆盖了离心机、过滤机、膜过滤、过滤器、浓缩与沉降设备等多种设备类型。
一、离心设备(一)常规离心设备依据GB/T7779《离心机型号编制方法》,离心机型号由基本代号、特性代号、主参数、转鼓与分离物料相接触部分材料代号四部分组成。
具体表示方法如下:改型代号:按A、B、C……与分离物料相接触部分的材料代号:按表2主参数:按表1特性代号:按表1基本代号:按表1离心机型号的基本代号按类别、型式、特征的分类原则编制。
基本代号和特性代号均用名称中有代表性的大写汉语拼音字母表示。
基本代号特性代号主参数类别型式特征名称代号名称代号名称代号名称代号名称单位三足式离心机S过滤型沉降型组合型—CZ人工上卸料抽吸上卸料吊袋上卸料人工下卸料刮刀下卸料拉袋卸料虹吸式翻壳式SPDXGLHQ--转鼓内径mm平板式离心机P上悬式离心机X过滤型—刮刀卸料G人工操作全自动操作-Z转鼓内径mm人工卸料R重力卸料Z离心卸料L1刮刀卸料离心机G过滤型沉降型虹吸过滤型-CH宽刮刀K斜槽推料螺旋推料隔爆密闭双转鼓型-LFMS转鼓内径mm窄刮刀Z活塞推料离心机H过滤型—单级Y圆柱型转鼓柱锥型转鼓加长转鼓双侧进料-ZCS最大级转鼓内径mm双级R三级S四级I离心卸料离心机1过滤型立式L普通式反跳环式固定导向螺旋式可调导向螺旋式-TDK转鼓内径mm卧式W振动卸料离心机Z过滤型立式L曲柄连杆激振偏心块激振电磁激振QPD转鼓内径mm卧式W进动卸料离心机J过滤型立式L转鼓内径mm卧式W翻袋卸料离心机F过滤型—卧式W普通型转鼓内径mm加压型Y螺旋卸料沉降离心机L沉降型沉降过滤组合型沉降碟片组合型ZD立式L逆流式并流式三相分离式向心泵输液高转速螺旋挡板密闭隔爆-BSXGYMF最大级转鼓内径×转鼓工作长度mm×mm卧式W螺旋卸料过滤离心机L过滤型过滤沉降组合型LX立式L密闭隔爆MF最大级转鼓内径×转鼓内腔工作长度mm×mm卧式W转鼓内径指转鼓最大内径。
化工设备机械基础第七版答案

化工设备机械基础第七版答案第一章:化工设备机械概述1.1 化工设备机械的定义和分类化工设备机械是指在化工生产过程中用于物料输送、混合、分离、反应、加热、冷却、传热和杂项处理等的机械设备。
根据其功能和特点,可以将化工设备机械分为输送设备、混合设备、分离设备、反应设备和传热设备等几大类。
1.2 化工设备机械的工作原理和基本组成化工设备机械的工作原理是根据化工过程中的要求,通过施加外力、传递能量和控制流体的运动来完成特定的物料处理工作。
基本组成包括机械主体、动力装置、传动部件、控制系统和附属设备等。
1.3 化工设备机械的性能指标和技术要求化工设备机械的性能指标包括生产能力、输送能力、混合效果、分离效率、反应速度、传热效果等。
技术要求包括安全可靠、耐腐蚀、操作方便、维护简单等。
第二章:输送设备2.1 输送设备的概述和分类输送设备是化工设备机械中用于物料输送的设备。
根据输送原理和输送介质的不同,可以将输送设备分为机械输送设备、液体输送设备和气体输送设备等几大类。
2.2 机械输送设备机械输送设备主要包括皮带输送机、链条输送机、螺旋输送机和刮板输送机等。
它们的工作原理和结构特点各有不同,适用于不同的物料输送需求。
其中,皮带输送机具有输送能力大、速度可控的特点;链条输送机适用于输送重载物料;螺旋输送机适用于输送散状物料;刮板输送机适用于输送粘稠物料。
2.3 液体输送设备液体输送设备主要包括泵类设备和管道设备。
泵类设备包括离心泵、容积泵和潜水泵等,用于将液体从一个地方输送到另一个地方;管道设备包括管道、阀门和管件等,用于控制液体的流动和输送方向。
2.4 气体输送设备气体输送设备主要包括风机、压缩机和气体管道等。
风机用于输送气体和增加气体的压力;压缩机用于将气体压缩为高压气体;气体管道则用于输送和控制气体的流动。
第三章:混合设备3.1 混合设备的概述和分类混合设备是化工设备机械中用于混合不同物料的设备。
根据混合方式和混合物料的性质不同,可以将混合设备分为机械搅拌设备、液体混合设备和固体混合设备等几大类。
许学勤-食品工厂机械与设备-第四章-分离机械与设备

深层过 滤
• 深层过滤是由粒状床层,普通为砂、煤炭或陶 瓷、塑料、金属等粉末或纤维经表面融结形成 的多孔介质进行的澄清过滤。
• 深层过滤的特点是固体颗粒的捕捉在过滤介质 内部形成的孔隙中进行,它可以阻挡比过滤介 质孔隙更小的颗粒。其过滤机理非常复杂。
过滤速度的强化
• 一、降低滤饼比阻力 : • 1.添加电解质、絮凝剂、凝固剂 • 2.加硅藻土等助滤剂
• 机理:表面吸附胶体及不可压缩型格子结构
• 常用助滤剂:硅藻土,珍珠岩,活性炭
• 应用优化因素 a 单位质量助滤剂的滤液最大产量 b 使用周期 c 流速
助滤剂
• 助滤剂是过滤介质的一种,大多是分散的 颗粒状物质,常用的有硅藻土、膨胀珍珠 岩、炭和纤维素等。
• 它们有中等孔的尺寸(1.1—30pm),有的有 高硬度(不可压缩性),能悬浮在液体 中, 并且能在多孔的隔板或过滤网上形成稳定 的滤饼层(预敷层),该滤层孔隙相对大、 渗透性好、不可压缩。
• 二、降低滤液粘度
• 三、降低悬浮液中悬浮固体的浓度
发酵液的滤饼重量比阻
q:瞬间通过单位面积的滤液 Δρ:压力差
• μ:滤液粘度 • γβ:滤饼重量比阻
• γβ=γ(Δρ)m
•
γ:滤饼比阻力 ;一般为常数
•
Δρ q=2—
m:压缩性指数(取0.8-0.5)
—————τ
•
μγβΧβ
Χβ :通过单位体积的滤渣量
• 该型离心机属于间歇过滤式离心机。
压榨
• 压榨的目的与过滤相同,都是为了将固液 相混合物分离。
• 压榨是通过机械压缩力将液相从液固两相 混合物中分离出来的一种单元操作,在压 榨过程中液相流出而固相截留在压榨面之 间。
第四章 固液分离设备
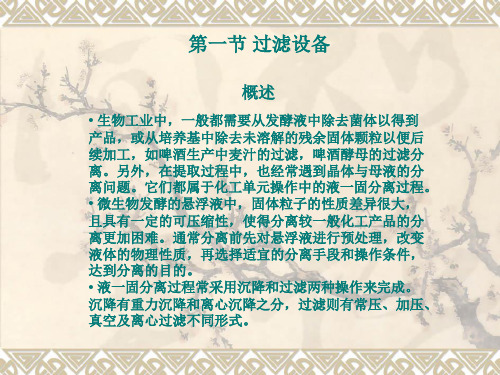
③甩干。
⑤甩干
④洗涤。
⑥停机,挖出滤饼。
2.2 自动下出料离心机 a. 结构:多一刮刀和固体出料口,见图4-36 b.优点:①能力强,滤饼干。 ②自动连续生产,劳动强度低。 c.缺点及适用范围: 价格贵,不适合滤饼太粘的料液。
d.操作过程:图4-37
2.3 自动卸料卧式离心机 a. 结构:见图4-38,4-39 b.优点:①占地面积小,可自动连续生产。 ②滤饼厚度均匀(不受重力影响)。 c.缺点及适用范围: 结构复杂,对转轴要求高;进料要均匀。 d.适用场合及操作过程:和立式相同。见图4-40
化工制药食品等行业的粉状粒状及纤维状物料的浓缩混合干燥及需低湿干燥的物料如生化制品等更适用于易氧化易挥发热敏性强烈刺激有毒性物料和不允许破坏结晶体的物料的干燥
第一节 过滤设备
概述
• 生物工业中,一般都需要从发酵液中除去菌体以得到 产品,或从培养基中除去未溶解的残余固体颗粒以便后 续加工,如啤酒生产中麦汁的过滤,啤酒酵母的过滤分 离。另外,在提取过程中,也经常遇到晶体与母液的分 离问题。它们都属于化工单元操作中的液一固分离过程。 • 微生物发酵的悬浮液中,固体粒子的性质差异很大, 且具有一定的可压缩性,使得分离较一般化工产品的分 离更加困难。通常分离前先对悬浮液进行预处理,改变 液体的物理性质,再选择适宜的分离手段和操作条件, 达到分离的目的。 • 液一固分离过程常采用沉降和过滤两种操作来完成。 沉降有重力沉降和离心沉降之分,过滤则有常压、加压、 真空及离心过滤不同形式。
(2)喷嘴排渣碟式分离机
连续操作。整体结构与人工排渣碟 式分离机相似,但转鼓内腔呈双锥形, 可对沉渣起压缩作用,提高沉渣浓度。 转鼓内直径最大 900毫米。转鼓周缘 有喷出浆状沉渣的喷嘴2~24个,喷嘴 孔径为0.5~3.2毫米。喷嘴的数目和 孔径根据悬浮液性质、浓缩程度和处 理量确定。通过喷嘴的沉渣流速很大, 喷嘴用耐磨材料如、和碳化硼 等制成。为提高排渣浓度,这种分离机还有将排出的沉渣部分送回转鼓内 再循环的结构。沉渣的固相浓度可比进料的固相浓度提高 5~20倍。这种分 离机的处理量最大达300米3/小时,适于处理固相颗粒直径为0.1~100微米、 固相浓度通常小于 10%(最大可至25%)的悬浮液。
固液分离机原理和安装

固液分离机原理和安装固液分离机也称为离心机,是一种常见的分离设备,其原理是利用离心力将混合物中的固体和液体分离开来。
固液分离机广泛应用于医疗、制药、化工、食品、环保等行业。
固液分离机分为手动和自动两种,其主要组成部分有离心转筒、离心电机、控制器等。
离心转筒是固液分离的核心部分,一般由不锈钢制成,内壁光滑,可防止物料附着,易清洗。
离心转筒由固定部分和旋转部分组成,其中固定部分一般固定在机架上,旋转部分由电机带动旋转。
当离心机启动时,固液混合物从进料口进入离心转筒中。
由于离心力作用,较重的固体颗粒被迫压缩到离心转筒的壁上形成固体层,轻的液体则被挤压到离心转筒内部形成液层。
当离心转筒达到一定速度时,固液分离完成,可通过固液分离机的排渣口和出液口分别排出固体和液体。
固液分离机的安装也很重要,首先要选好安装地点,要求地面平整稳定,且具备良好的排水条件。
离心机的底座要与地面紧密接触,并且固定牢固,以防止启动时的震动和噪音。
在安装中还需要对电源线路和接地线路进行严格检查,并配备过载保护器等安全装置,确保固液分离机的稳定运行和安全使用。
固液分离机的原理是利用离心力将混合物中的固体和液体分离开来,是一种常见的分离设备。
固液分离机在安装时要选择合适的地点,并确保底座稳固,电源线路和接地线路正常,配备过载保护器等安全装置,以保证固液分离机的正常运行和安全使用。
对于固液分离机的使用,一定要注意一些操作技巧和细节。
在使用前要检查固液分离机的各部件是否处于良好状态,特别是离心转筒和滤饼输送系统。
在操作时需严格按照说明书进行操作,不得贪图方便随意操作,避免发生安全事故。
在固液分离机的维护保养方面,首先要注意对离心转筒的清洗和保养,不仅能保障离心转筒的长期使用寿命,还能提高分离效率。
清洗时应先停机,并切断电源,用清洁布擦拭离心转筒内表面,严禁使用金属刷等硬物质,以防对离心转筒表面造成划痕。
对于长时间未使用的离心转筒,应进行除锈处理,以及外表面清洗、镀锌或喷塑等表面处理工作。
原料药主要工艺设备(釜、固液分离、真空泵、干燥)

1~100
10~300
50
桨式
○
○
○
○
○
○
○
○
○
○
1~200
10~300
20
推进式
○
○
○
○
○
○
○
○
○
1~1000
10~500
50
折叶开启涡轮式
○
○
○
○
○
○
○
○
1~1000
10~300
50
锚式 螺○
○ ○ ○
1~100 1~50 1~50
1~100 0.5~50 0.5~50
图7-12 推进式搅拌器
一、反应釜
搅拌时——流体由桨叶上方吸入,下方以圆筒状螺旋形排
出,流体至容器底再沿壁面返至桨叶上方,形
成轴向流动。
特点 ——搅拌时流体的湍流程度不高,循环量大,结构
简单,制造方便。
循环性能好,剪切作用不大, 属于循环型搅拌器。
一、反应釜
应用
粘度低、流量大的场合,用较小的搅拌功率,能获得较好 的搅拌效果。 主要用于液-液系混合、使温度均匀,在低浓度固-液系 中防止淤泥沉降等。
四、干燥设备
双锥真空干燥
四、干燥设备
双锥真空干燥特点
优点:被干燥的物料处于不断的上下翻腾状态,物料传热均匀,干燥
快切均匀。
缺点:不适用于易产生静电或粘性物料的干燥,容易结球,不利于干
燥;设备构造复杂,某些部位不利于清洁或易产生异物。
四、干燥设备
单锥真空干燥
分为重力过滤、离心过滤、加压过滤和真空过滤,也可分为恒压过滤、先恒速
二、固液分离设备
固液分离技术过滤

转鼓回转轴功率
搅拌器功率 过滤机总功率
P1 (1.2~1.5)
A 10
P 2(1 .0~1 .3 )P 1
P(P 1P 2)
第四章 过滤
4.3.3 圆盘真空过滤机
它属于连续式过滤设备,由数个过滤圆盘组成。可以过滤密度小,不易沉淀的料浆。
4.3.3.1圆盘真空过滤机的特点 1)结构紧凑、占地面积小、单位过滤面积造价低; 2)真空度损失少,耗电少; 3)可以不设搅拌装置; 4)更换滤布方便; 5)侧面过滤,过滤效果好; 6)滤饼洗涤困难,甚至不能洗涤; 7)滤饼厚度不均,含湿量高; 8)滤布易堵,难再生,卸饼困难。 4.3.3.2 圆盘真空过滤机的分类 按料浆性质可分为普通型和耐酸型。
真空系统压力损失小,过滤能力 大;滤饼易于卸出;滤布不易堵 塞,寿命长。 但要求真空源容量大,造价高。
第四章 过滤
C 预涂层式转鼓真空过滤机
其原理是:在过滤之前,先在滤布上形成助滤剂层,然后进行过滤。预涂 层材料一般为硅藻土做助滤剂。
在工作过程中,转鼓先被形成一层厚度50~100mm的预涂层,然后进行 正式过滤,卸料时预涂层厚度也会被刮掉0.05~0.2mm。过滤始终在新鲜 的预涂层上进行。当预涂层剩10~15mm时,应停止过滤,重新形成预涂 层。
第四章 过滤
A 刮刀卸料式转鼓真空过滤机
第四章 过滤
B 折带卸料式转鼓真空过滤机 它是借助于行走的滤布卸除滤饼, 滤布不仅起过滤介质作用,而且也 起运载滤饼的作用。
特点:滤饼不用压缩空气吹脱,滤 饼不会返回料浆槽,可利用蒸汽吹 和水洗等方法使滤布再生,滤饼容 易卸除,含湿量低;但结构较复杂, 滤布容易磨损,滤布可能跑偏。结 滤布 构见图4-7。
普通型用于中性或碱性料浆,还可细分为一般普通型和带蒸汽罩普通型。 耐酸型适用于酸性或腐蚀性料浆的过滤,一般有色冶炼厂都是耐酸型的圆 盘真空过滤机。
板框过滤器原理

板框过滤器原理板框过滤器是一种常用的固液分离设备,其原理是利用孔径不同的过滤板和过滤框,将固体颗粒截留在过滤板上,使液体通过过滤板的空隙,实现固液分离的目的。
在工业生产中,板框过滤器被广泛应用于化工、食品、制药等领域,用于过滤悬浮固体颗粒或悬浮液体,提取纯净的液体或固体产品。
板框过滤器由过滤框、过滤板、滤布等部件组成。
过滤框通常由钢制成,内部安装有过滤板,过滤板上覆盖有滤布。
在工作时,液体混合物通过进料口进入过滤框,固体颗粒被截留在过滤板上,液体则通过滤布排出,从而实现固液分离。
随着过滤过程的进行,固体颗粒在过滤板上逐渐堆积,形成滤饼,使过滤阻力逐渐增大。
当过滤阻力达到一定程度时,需要停机清理滤饼,恢复过滤性能。
板框过滤器的分离效率主要取决于过滤板和滤布的选材和设计,以及操作参数的控制。
过滤板的孔径和密度决定了固体颗粒的截留效果,滤布的材质和密度影响了液体的透过率和固体的截留率。
在操作过程中,需要根据不同的物料特性和分离要求,选择合适的过滤板和滤布组合,调整过滤压力、过滤速度等参数,以达到最佳的分离效果。
板框过滤器具有结构简单、操作方便、分离效率高的优点,广泛应用于化工、食品、制药等行业。
在化工生产中,板框过滤器常用于脱水、过滤、脱色等工序,提取纯净的产品。
在食品加工中,板框过滤器常用于澄清果汁、脱脂奶、提取果汁等。
在制药领域,板框过滤器用于提取药物、分离杂质等。
可以说,板框过滤器在工业生产中发挥着重要的作用,为产品的提纯和提纯提供了可靠的技术支持。
总的来说,板框过滤器通过过滤板和过滤框的组合,实现固液分离的目的。
其原理简单,操作方便,分离效率高,被广泛应用于各个领域。
在今后的工业生产中,板框过滤器将继续发挥重要作用,为产品的提纯和分离提供可靠的技术支持。
固液分离技术
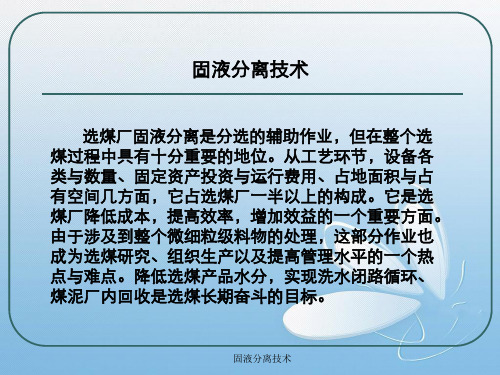
固液分离技术
第四节 细粒物料的脱水方法与设备
4. 过滤与压滤的比较
这里所讲过滤,确切讲为真空过滤。 1)共同点 本质相同,即过滤基本原理。
2)差异 (1)推动力性质及大小。过滤是利用真空系统在滤有两侧形成压力差,压 力差小。一般 200-600mmHg柱高;而压滤则是通过流体加压(矿浆或空气), 形成滤布两侧的压力差,压力差可达0.5-1Mpa,且调节方便。 (2)过滤过程不同。真空过滤为恒压过滤,过滤过程中压力不变,过滤速 度逐渐减少。压滤先为恒速过滤,过滤速度不变,压力增加;待形成一定滤 饼后,转为恒压过滤,压力保持不变,过滤速度逐渐减小。 (3)适用对象。过滤用于比滤阻小的易过滤物料,如浮选精煤、以粗粒为 主的浮选尾煤;压滤则用于难滤物料,如以高灰细粒为主的浮选尾矿。
2. 可过滤性
可过滤性是煤泥水的又一工艺性质,它表征煤泥脱水过滤的难 易程度。由于细粒物料脱水以过滤方法为主,因而采用比滤阻采表 征其可过滤性。
比滤阻是指过滤单位质量物料的滤饼阻力,单位为m/kg。显然 ,比滤阻越大,可过滤性越差,比滤阻首先取决于煤泥水的组成与 性质。实践表明,矿物质含量越大,粒度越细,水质越弱,相应的 比滤阻就越大。其次,滤饼结构对比滤阻有较大影响。再者,通过 添加助滤剂可显著减少比滤助。提高煤泥水可过滤性是改善过滤效 果的有效途径。
固液分离技术
第二节 固液分离工艺
1. 浓缩浮选
它是一种传统工艺。流程结构特点是:全部煤泥水先进行浓缩 ,底流进入浮选;溢流与尾煤浓缩机溢流共同作为循环水。浓缩浮 选优点是,可有效调节浮选入料浓度与通过量。
旋流池工作原理
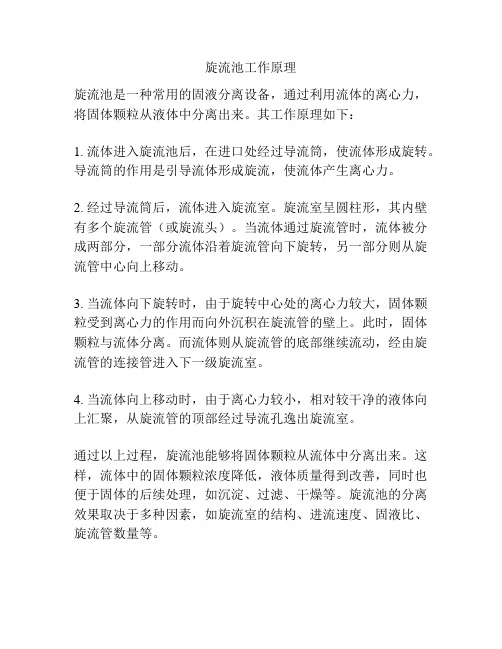
旋流池工作原理
旋流池是一种常用的固液分离设备,通过利用流体的离心力,将固体颗粒从液体中分离出来。
其工作原理如下:
1. 流体进入旋流池后,在进口处经过导流筒,使流体形成旋转。
导流筒的作用是引导流体形成旋流,使流体产生离心力。
2. 经过导流筒后,流体进入旋流室。
旋流室呈圆柱形,其内壁有多个旋流管(或旋流头)。
当流体通过旋流管时,流体被分成两部分,一部分流体沿着旋流管向下旋转,另一部分则从旋流管中心向上移动。
3. 当流体向下旋转时,由于旋转中心处的离心力较大,固体颗粒受到离心力的作用而向外沉积在旋流管的壁上。
此时,固体颗粒与流体分离。
而流体则从旋流管的底部继续流动,经由旋流管的连接管进入下一级旋流室。
4. 当流体向上移动时,由于离心力较小,相对较干净的液体向上汇聚,从旋流管的顶部经过导流孔逸出旋流室。
通过以上过程,旋流池能够将固体颗粒从流体中分离出来。
这样,流体中的固体颗粒浓度降低,液体质量得到改善,同时也便于固体的后续处理,如沉淀、过滤、干燥等。
旋流池的分离效果取决于多种因素,如旋流室的结构、进流速度、固液比、旋流管数量等。
固液分离设备
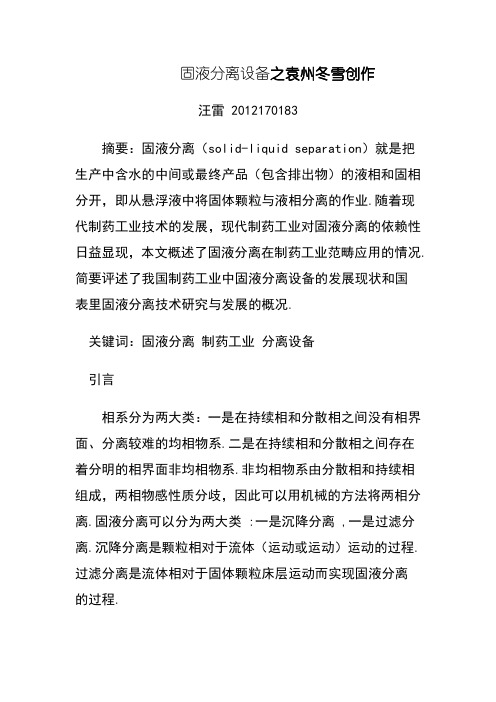
固液分离设备之袁州冬雪创作汪雷 2012170183摘要:固液分离(solid-liquid separation)就是把生产中含水的中间或最终产品(包含排出物)的液相和固相分开,即从悬浮液中将固体颗粒与液相分离的作业.随着现代制药工业技术的发展,现代制药工业对固液分离的依赖性日益显现,本文概述了固液分离在制药工业范畴应用的情况.简要评述了我国制药工业中固液分离设备的发展现状和国表里固液分离技术研究与发展的概况.关键词:固液分离制药工业分离设备引言相系分为两大类:一是在持续相和分散相之间没有相界面、分离较难的均相物系.二是在持续相和分散相之间存在着分明的相界面非均相物系.非均相物系由分散相和持续相组成,两相物感性质分歧,因此可以用机械的方法将两相分离.固液分离可以分为两大类 :一是沉降分离 ,一是过滤分离.沉降分离是颗粒相对于流体(运动或运动)运动的过程.过滤分离是流体相对于固体颗粒床层运动而实现固液分离的过程.1、固液分离设备分类固液分离设备也可以相应地分为两大类.在此基础上,根据推动力和操纵特征进一步细分为若干种固液分离设备,如表1所示.品类繁多的固液分离设备使用户有更大范围的选择,对于固液分离的问题,一般总能找到最合适的固液分离设备.然而,正是由于种类很多,一般用户对各种设备性能和缺乏深刻懂得,所以在选择最合适的固液分离设备时总有许多坚苦.由于设备选择不当,不克不及知足技术要求的情况其实很多见.下文便先容了一般常常使用的固液分离设备,和固液分离设备选择的一般方法.当前除常常使用的固液分离设备与技术如真空过滤机和压滤机,过滤和沉降离心机,普通沉降稠密机(强化和高效浓度机),普通澄清机,有预涂层的过滤机、压滤机和深层床过滤机,上向式分离的气浮机,筛分、水力旋流器、磁分离、泡沫浮选以及凝集和絮凝、助滤剂、洗涤、过滤介质及其选择等.表一固液分离设备主要类型一览表[1]2、沉降分离设备沉降是依靠外力的作用,操纵分散物质(固相)与分散介质(液相)的密度差别,使之发生相对运动,而实现固液分离的过程.分为重力沉降和离心沉降.重力沉降操纵的外力是重力,适用于分离较大的固体颗粒;离心沉降操纵的外力是惯性向心力,适于分离两相密度差较小,颗粒粒度较细的非均相物系.A.颗粒沉降过程<一>受力分析[2]2.干扰沉降:当颗粒的体积浓度>0.2% 时,干扰沉降不容忽视.3.器壁效应:当容器较小时,容器的壁面和底面均能增加颗粒沉降时的曳力,使颗粒的实际沉降速度较自由沉降速度低.B.重力沉降设备沉降槽[3]:籍重力沉降从悬浮液中分离出固体颗粒的设备称为沉降槽.如用于低浓度悬浮液分离时亦称为澄清器;用于中等浓度悬浮液的稀释时,常称为稀释器或增稠器.沉降槽适于处理颗粒不太小、浓度不太高,但处理量较大的悬浮液的分离.这种设备具有布局简单,可持续操纵且增稠物浓度较平均的优点,缺点是设备复杂,占地面积大、分离效率较低.C.离心沉降设备碟式离心机:可疾速持续的对固液和液液进分离,是立式离心机的一种,转鼓装在立轴上端,通过传动装置由电动机驱动而高速旋转.转鼓内有一组互相套叠在一起的碟形零件--碟片.碟片与碟片之间留有很小的间隙.悬浮液(或乳浊液)由位于转鼓中心的进料管加入转鼓.当悬浮液(或乳浊液)流过碟片之间的间隙时,固体颗粒(或液滴)在离心机作用下沉降到碟片上形成沉渣(或液层).沉渣沿碟片概况滑动而脱离碟片并积聚在转鼓内直径最大的部位,分离后的液体从出液口排出转鼓.碟片的作用是缩短固体颗粒(或液滴)的沉降间隔、扩展转鼓的沉降面积,转鼓中由于装置了碟片而大大提高了分离机的生产才能.积聚在转鼓内的固体在分离机停机后拆开转鼓由人工清除,或通过排渣机构在不断机的情况下从转鼓中排出.卧式螺旋沉降离心机[4]:卧螺离心机是一种卧式螺旋卸料、持续操纵的沉降设备.本类离心机工作原理为:转鼓与螺旋以一定差速同向高速旋转,物料由进料管持续引入输料螺旋内筒,加速后进入转鼓,在向心力场作用下,较重的固相物沉积在转鼓壁上形成沉渣层.输料螺旋将沉积的固相物持续不竭地推至转鼓锥端,经排渣口排出机外.较轻的液相物则形成内层液环,由转鼓大端溢流口持续溢出转鼓,经排液口排出机外.3、过滤分离设备中药提取液中有效成分与多糖及其他无效成分的分离,发酵液的预处理,液体制剂去除热源等单元操纵都是制药生产中的过滤分离过程.依照过滤的原理分歧可以分为滤饼过滤和深层过滤两种方法.滤饼过滤:固体堆积在滤材上并架桥形成滤饼层的过滤方式 .深层过滤:指颗粒沉积在床层外部的孔道壁上而其实不形成滤饼的过滤方式.A.过滤基本方程式:过滤基本方程式暗示过滤过程中某一瞬间的过滤速率与各有关因素的相互关系.对于不成压缩性滤饼有如下计算式:B.过滤设备板框压滤机:混合液流颠末滤介质(滤布),固体停留在滤布上,并逐渐在滤布上堆积形成过滤泥饼.而滤液部分则渗透过滤布,成为不含固体的清液.与其它固液分离设备相比,压滤机过滤后的泥饼有更高的含固率和优良的分离效果.真空转鼓过滤机[5]: 它有一水平转鼓,鼓壁开孔,鼓面上铺以支承板和滤布,构成过滤面.过滤面下的空间分成若干隔开的扇形滤室.各滤室有导管与分配阀相通.转鼓每旋转一周,各滤室通过分配阀轮番接通真空系统和压缩空气系统,顺序完成过滤、洗渣、吸干、卸渣和过滤介质(滤布)再生等操纵.在转鼓的整个过滤面上,过滤区约占圆周的1/3,洗渣和吸干区占1/2,卸渣区占1/6,各区之间有过渡段.过滤时转鼓下部沉浸在悬浮液中缓慢旋转.沉没在悬浮液内的滤室与真空系统连通,滤液被吸出过滤机,固体颗粒则被吸附在过滤面上形成滤渣.滤室随转鼓旋转分开悬浮液后,继续吸去滤渣中饱含的液体.当需要除去滤渣中残留的滤液时,可在滤室旋转到转鼓上部时喷洒洗涤水.这时滤室与另外一真空系统接通,洗涤水透过滤渣层置换颗粒之间残存的滤液.滤液被吸入滤室,并单独排出,然后卸除已经吸干的滤渣.这时滤室与压缩空气系统连通,反吹滤布松动滤渣,再由刮刀刮下滤渣.压缩空气(或蒸汽)继续反吹滤布,可疏通孔隙,使之再生.4、新式设备先容[6]陶氏化学公司(NYSE:DOW)推出一种针对高难度水处理的获奖创新产品:TEQUATICTMPLUS紧密颗粒过滤器.凭借其专利设计,TEQUATICTM PLUS紧密颗粒过滤器将持续清洗、错流过滤以及离心分离和固体收集功能集成于一个装置中,此技术已经在诸多应用范畴证了然其重要价值.a)针对高难度水处理的技术TEQUATICTM PLUS紧密颗粒过滤器由陶氏化学公司的全资子公司CleanFiltration TechnologiesLLC(简称“CFT”)生产.TEQUATICTM PLUS紧密颗粒过滤器在高难度水处理范畴是一项具有突破性的产品,可以靠得住、稳定且经济地处理总悬浮固体颗粒(TSS)极高而且变更范围极大的原水,降服诸如滤芯、滤袋和多介质过滤器等传统技术存在的各种缺点.该技术可以处理固体颗粒含量从1到10,000毫克/升的原水而无须频繁更换滤片,即使是在有油的情况下亦是如此.TEQUATICTM PLUS紧密颗粒过滤器不但为水处理范畴带来一系列全新的可以性,而且亦使客户可以在更广的范围内选择陶氏水处理及过程处理方案所提供的水污染和分离技术产品.b)性能优势与其它技术分歧,TEQUATICTM PLUS紧密颗粒过滤器可以在实现极高的水回收率(一般都不低于99%)的同时,稳定地过滤固体颗粒含量高而且变更极大的原水,设备维护量、污堵情况以及反冲洗周期均大幅度减少,而且不存在更换滤芯或滤袋的问题.c)应用的多样性TEQUATICTM PLUS紧密颗粒过滤器专门针对非饮用水应用范畴.其功能非常矫捷,可作为一级过滤器、超滤(UF)和反渗透(RO)的预过滤器,亦可作为水再操纵技术之后的后过滤器.d)关键技术TEQUATICTM PLUS紧密颗粒过滤器操纵原水进入过滤器后的压力,使水流在过滤室中疾速冲刷,推动过滤室中的扇叶,将原水中较大的颗粒疾速平均地带入过滤室,通过向心力将较重的固体颗粒离心到过滤室的壁上,而且在重力的作用下渐渐沉降,进入下方的收集室.较为干净的过滤水则在压力作用下通过过滤膜,从上方流出.没有通过过滤膜的水则从下方再次进入循环.参考文献:[1] 李永改,彭安均,张鹏. 两种常常使用固液分离技术的分析与比较[J]. 科技信息. 2010(21)[2] 张俊福,余承烈. 高效固液分离设备的设计和试验[J]. 清水技术. 2005(01)[3] 张慧,孙世钢. 螺旋式固液分离设备的分类及应用[J]. 大连大学学报. 2004(04)[4] 余承烈. 一种高效固液分离设备[J]. 清水技术. 2004(03)[5] 艾光富,张传忠,解雷雷,盖涛,黄梅玲. 滚筒式固液分离装置的设计[J]. 科技信息. 2010(35)[6]Liu X X, Pan Q Y, Su H. Study on Cross-Flow Solid-Liquid Separation Technology[J]. Advanced Materials Research, 2013, 712: 748-754.。
固液分离设备培训资料
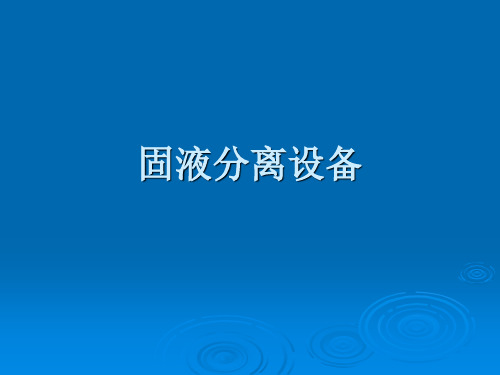
二、过滤设备选择与使用
过滤设备种类繁多,对某一生产过程可能有好 几种设备适用,这就对准确选择一台合理的过 滤设备产生巨大的困难。此外,生产规模和过 程是否连续也影响设备的选型。因此,有人提 出应根据物料的过滤特性和模型实验结果,进 行技术的综合评价,以便确定一种工艺上合理, 投资和操作费用最经济的设备。以下是几条过 滤机选用的基本原则。
架桥现象
无论是介质过滤,还是滤饼过滤,正 确地选择过滤介质都是十分必要的。 常用的过滤介质有:滤纸、滤布、烧 结金属、多孔陶瓷、微孔滤膜、超滤 膜和反渗透膜等,以前常用的石棉滤 材由于其致癌作用已禁止使用,而微 孔滤膜、超滤膜和反渗透膜的使用则 日益广泛 。
好的过滤介质应满足下列条件:①过滤阻 力小;②不易堵塞;③反复使用时滤饼卸除容 易;④物理性质和化学性质稳定;⑤安装操作 简单;⑥价廉。
离心分离机性能关键影响因素:
1)与轻、重相密度有关; 2)与物料粘度有关; 3)与分离因数f 有关; 4)与固含量有关,定期清洗,另外要关注皂化物 、结晶体; 5)与理论分界面有关,调整轻相背压、选用进液 孔(与轻重相体积比、产品选取有关); 6)与比重环内径/向心泵外径有关。
3.根据工艺过程的特点和生产规模可对 选择的过滤设备进行筛选。一般当生产 规模大时,应选择连续式,劳动强度小 的设备。对生产规模小的或本身是间歇 操作的,那么选用间歇操作的过滤机可 以节省设备费用和操作费用。
三、 离心液固分离设备
固液分离设备类型及原理

固液分离设备类型及原理
固液分离设备是指用于将固体和液体物质从混合物中分离的设备。
固液分离设备的类型比较多,主要有离心机、过滤器、沉淀池等等。
离心机是将溶液强制分离成液相和固相的重要设备,具有快速、多产出、费用低、污染小等特点,能在30-40分钟内完成分离。
这种分离技术的实质是使用转子和离心力相结合,使溶液重新构成固液混合物或固液沉淀产物的过程。
可以采用不同的技术方法来调节分离的效率。
过滤器是将悬浮物或固体微粒从液体中分离的过滤
设备。
它主要包括自吸式过滤机和压力式过滤机两种。
自吸式过滤机由一个配有过滤材料的过滤器体
组成,将悬浮物筛选掉。
压力式过滤机则是将悬浮
物和微固体细致地筛选掉,在过滤布上形成堆积
层,使液体除去悬浮物和微粒,以满足特定的要
求。
沉淀池是将尼氏物质从液体中分离的设备,也是常见的固液分离设备类型之一。
其原理是利用一定的时间、温度和曝气量,使尼氏物质从液体中沉淀下来,最后经过排放就能得到纯净的液体。
以上所述就是固液分离设备的类型和原理。
固液分离设备作为一种高效、准确的分离技术,已经在化工、食品、药品等领域得到了广泛的应用。
它具有简单的操作和维护、低耗能、低成本的特点,
在精细化工、净水处理等方面具有极大的优势。
- 1、下载文档前请自行甄别文档内容的完整性,平台不提供额外的编辑、内容补充、找答案等附加服务。
- 2、"仅部分预览"的文档,不可在线预览部分如存在完整性等问题,可反馈申请退款(可完整预览的文档不适用该条件!)。
- 3、如文档侵犯您的权益,请联系客服反馈,我们会尽快为您处理(人工客服工作时间:9:00-18:30)。
1.1 液-固分离: 分离悬浮液时,悬浮液由中心进料管进入转鼓,从碟片束外缘经 碟片间隙向碟片内缘流动。因受离心力作用,固体颗粒在随液体
流动的同时沉降到各碟片的内表面,再向碟片外缘滑动,最后沉
积到鼓壁上。已澄清的液体向转鼓中心方向聚集,经溢流口或向心 泵排出。
1.2液-液分离:分离乳浊液时,乳浊液经碟片束上的进料孔进入
a.结构图4-2
b.优点:结构简,制造易,成本低。 c.缺点: 生产能力小,劳动强度大,对环境
造成污染,间歇生产。
1.2 真空转鼓过滤器 a.原理 图4-3 图4-4
三个阶段:过滤、洗涤和抽干、卸料 b.结构 图4-5 图4-6
c.优点:连续自动化生产 d.缺点:过滤、洗涤、抽干、卸料的时间无法分别调节。
(3)活门排渣碟式分离机
利用环状活门启、闭排渣口进行间歇排渣,又称自动排渣碟式分离机。整 体结构与人工排渣碟式分离机相似,特点是转鼓内有活门排渣装置,可不停 机卸除转鼓内的沉渣。操作时,由转鼓中心加料管加入悬浮液进行分离, 活门下面的密封水总压力大于悬浮液作用在活门上面的总压力,活门位置 在上,关闭排渣口。排渣时,停止加料并由转鼓底部加入操作水,开启转 鼓周边的密封水泄压阀,排出密封水,活门受转鼓内悬浮液压力的作用迅速下 降,开启排渣口。排尽转鼓内的沉渣和液体后,停止供给操作水,泄压阀闭 合,密封水压升高,活门上升关闭排渣口,完成一次工作循环。自动控制活门 排渣的方法有:①用时间继电器按预定操作周期控制排渣;②用光电管监控 分离液澄清度控制排渣;③根据转鼓内沉渣聚积程度,由压力信号或渣面信 号控制排渣。排渣时间一般为1~2秒。部分排渣的转鼓可控制更短的排渣 时间,仅排出转鼓内沉渣的一部分,不排出液体,排渣时可不停止进料,连 续分离,提高了处理能力。这种分离机最大处理量可达60米3/小时,适用于 处理固体颗粒直径为0.001~0.5毫米,固液相密度差大于0.01千克/分米3,固 相浓度小于10%的悬浮液和乳浊液。
一、过滤过程简介
1.过滤:用过滤介质讲液固混合物分离的过程。 2.过滤介质:包括滤布、滤网(不锈钢和黄铜)、刚性多孔介质(烧结 陶瓷、塑料、金属)、松散固体介质(硅藻土、珍珠岩粉、 细纱、活性炭、白土等) 3.分类:
表层过滤
按分离机制
深层过滤
二、真空过滤设备
1. 原理:利用真空在过滤介质两面产生压力差,使液体透过,固体截留。 1.1 真空抽滤机
第一节 过滤设备
概述
• 生物工业中,一般都需要从发酵液中除去菌体以得到 产品,或从培养基中除去未溶解的残余固体颗粒以便后 续加工,如啤酒生产中麦汁的过滤,啤酒酵母的过滤分 离。另外,在提取过程中,也经常遇到晶体与母液的分 离问题。它们都属于化工单元操作中的液一固分离过程。 • 微生物发酵的悬浮液中,固体粒子的性质差异很大, 且具有一定的可压缩性,使得分离较一般化工产品的分 离更加困难。通常分离前先对悬浮液进行预处理,改变 液体的物理性质,再选择适宜的分离手段和操作条件, 达到分离的目的。 • 液一固分离过程常采用沉降和过滤两种操作来完成。 沉降有重力沉降和离心沉降之分,过滤则有常压、加压、 真空及离心过滤不同形式。
3. 应用范围
广泛应用于从发酵液中回收菌体、抗生素及疫苗
<一>原理
1.离心沉降速度 颗粒在离心场中受到离心力、向心力、阻力,重力可忽略不计。其 切向速度ut,离心沉降速度计算式可推导为:
离心沉降速度ur
在层流区符合斯托克斯定律,即:
4d s s ut2 3 R
d s2 s ut2 层流区沉降速度ur 18 R
1.3真空带式过滤器 1.3.1托盘带式过滤器 1.3.1.1往复托盘带式过滤器
原理:图4-9
1.3.1.2固定托盘带式过滤器 a.特点:托盘固定不动
b.滤布运动:图4-10
加料阶段 注意:仅上半圈滤布运动,下半圈不动(棘齿轮锁紧),没真空, 两个阶段 不过滤,但洗涤一直开启。 过滤和卸料阶段
1.3.1.3水平带式过滤器 a.解决过滤带和真空连接的方式:图4-11 b.摩擦条的作用: ①密封缝隙(真空箱和滤布拖带之间) ②隔离、防磨损 见图4-12 c.工作原理:图4-13
5. 适用范围:固体含量稍高的悬浮液澄清
四、碟片式离心机
转鼓内装有一叠锥形碟片,用离心沉降法分离乳浊液和低
浓度悬浮液组分的。碟式分离机可在密闭、高温、低温、加压
和真空等条件下操作,用于从牛奶中提取奶油和果汁、啤酒、 动植物油、变压器油等的净化,以及酵母浓缩和从动物血浆中
提取血清等。
1. 原理
图1
三、加压过滤设备
1. 原理:在过滤介质滤液一侧施加压力,使液体通过,固体截留在介质表面实现 固液分离。 2. 过滤设备 2.1 板框压滤机 a.结构:“板”和“框”交替叠加,见图4-15、4-16、4-17、4-18 b.优点:①体积小,过滤面积大且可调,生产能力大。 ②结构紧,制造易,价格低。 c.缺点:间歇生产,劳动强度大。 d.适用范围:适用范围大(过滤面积大、流量大), 在制药、化工、食品等行业
有广泛用途,特别适用于中成药料液的过滤,效果甚佳 。
e.操作过程: ①清洗板框并盖滤布。 ②安装入框架内并压紧。
③过滤。 ④停止过滤(滤液进口压力表迅速上升)
⑤拆卸、清洗滤布板框
2.2 板式压力机
a.结构:只有“板”而无“框”且“板”结构特别,见图4-19、4-20 b.工作原理:图4-21
b.优点:结构更紧凑,操作相对更容易一些。
1.3.1.4带式过滤器的操作方式
并流洗涤 图4-13
逆流洗涤 图4-14
1.3.1.5 优缺点和适用场合
a. 优点:①连续操作,洗涤可逆、可并。 ②操作弹性大。 b. 缺点:控制复杂,制造难度大,贵重,材质要求高(滤布和滤布托带) c. 适用范围:① 固体沉淀较快的滤液 ② 滤饼易产生裂缝的滤液
R——颗粒的旋转半径,单位是m。
2.离心分离因数
离心加速度与重力加速度之比称为离心分离因数,用Kc表示。
2 ut2 ut 因离心加速度 所以 kC = R Rg kC是离心分离的重要指标,是衡量离心机的分离能力大小的重要
③残液吹扫。(后常需洗涤) ⑤卸料。
2.4 垂直加压叶滤机
a.结构和原理:图4-24、4-25 b.形式: ①垂直加压叶滤机
②卧式垂直加压叶滤机
图4-26
c.优点:卸料检修清理易,密封简(无转动)。 c.缺点:滤饼易脱落,垂直加压叶滤机上部需预留较大空间。 d.适用范围: 同水平板式压滤机 e.操作过程:同水平板式压滤机(卸料略微不同)
第二节 离心沉降设备
离心沉降:利用离心力使不同密度的液固或液液混合物分离的方法。 离心沉降设备:实现离心沉降的设备。
常用在普通过滤难以达到目的的固液分离或溶液澄清。
一、管式离心机
1. 原理及结构:图4-40 图10-23 2. 优点:结构简、转速高(分离因数高达15000-65000 )、
沉降效果最好。
2.5 纳式过滤器
a.结构:图4-29、4-30 b.特点: 搅拌和刮刀可升降。
c.操作过程:图4-32
c.优点:综合了上述设备优点 d.缺点:间歇操作,滤饼较粘时出料困难 e.适用范围: 广且可进行化学反应。见P46
四、离心过滤设备
1. 原理:利用离心力迫使液体通过过滤介质,使固液分开。 2. 过滤设备 2.1 三足离心机 a.外形及结构:见图4-34、4-35 b.优点:①能力强,滤饼干。 ②结构简,制造易,价格低。 c.缺点: 间歇生产,劳动强度大,能耗高。 d.适用范围:常规使用,滤液易燃、有毒、有腐蚀时慎用 。 e.操作过程: ①开机。 ②加料过滤。
③甩干。
⑤甩干
④洗涤。
⑥停机,挖出滤饼。
2.2 自动下出料离心机 a. 结构:多一刮刀和固体出料口,见图4-36 b.优点:①能力强,滤饼干。 ②自动连续生产,劳动强度低。 c.缺点及适用范围: 价格贵,不适合滤饼太粘的料液。
d.操作过程:图4-37
2.3 自动卸料卧式离心机 a. 结构:见图4-38,4-39 b.优点:①占地面积小,可自动连续生产。 ②滤饼厚度均匀(不受重力影响)。 c.缺点及适用范围: 结构复杂,对转轴要求高;进料要均匀。 d.适用场合及操作过程:和立式相同。见图4-40
各碟片间隙,按密度不同分为重液和轻液,重液沿碟片内表面 向转鼓壁流动,轻液向中心流动,经溢流口和向心泵分别排出。
进料孔位置应在重液层与轻液层的交处。此处称为中性层,其半
径 式中k为重液与轻液的密度比,R1和R2 分别
为重液和轻液的排出口半径。进料孔与中性层不重合时,排出 的重液或轻液就不纯净,此时可改变重液或轻液排出口半径来 调整中性层位置。由于转鼓内的液体被碟片束分为许多薄层,
3. 缺点:固体沉淀需手工移出,泡沫含量高的悬浮液分离效 果差。 4. 适用范围:固含量低于1%,颗粒度0.01~100微米,黏度 大的悬浮液澄清或固液两相密度差较小乳浊液或悬浮液的分离, 如油水、蛋白质、青霉素、香精油等。 5. 种类:GQ型(分离悬浮液)及GF型(分离乳浊液) 6.型号:类型代号+转股直径 105mm 如GF105中105指转股直径
分离在薄层内进行,离心沉降的距离很短,显著提高了分离速
度。碟式分离机的分离因数较高,达4000~10000,并因转鼓内 的碟片数量多,显著扩大了沉降面积,分离效率较高。
1.3向心泵:具有固定在机壳上静止不动的叶轮,叶轮外缘浸没 在与转鼓同步旋转的分离液层内,分离液由叶轮外缘进入弧形
流道,流至叶轮中心排液管排出。叶轮将旋转液体的动能转变
二、套管式离心机
1. 原理及结构:图4-41
2. 优点:结构紧凑、固体颗粒能分级沉淀。
3. 缺点:固体沉淀清除难。
4. 适用范围:固体含量较少的悬浮液澄清