简述磨削平面的方法
不锈钢的平面磨床磨削方法
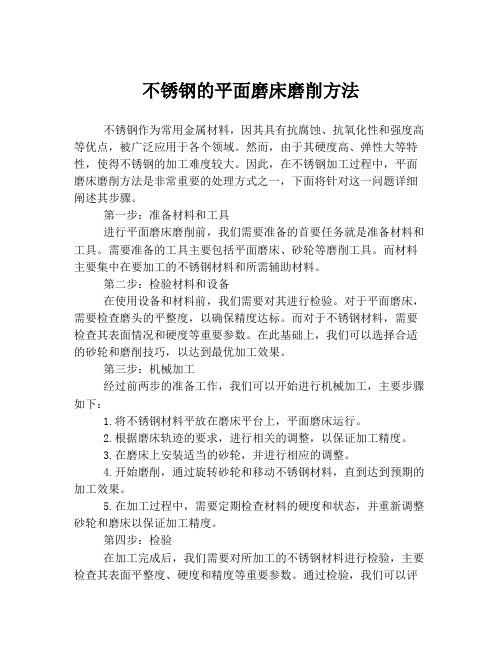
不锈钢的平面磨床磨削方法不锈钢作为常用金属材料,因其具有抗腐蚀、抗氧化性和强度高等优点,被广泛应用于各个领域。
然而,由于其硬度高、弹性大等特性,使得不锈钢的加工难度较大。
因此,在不锈钢加工过程中,平面磨床磨削方法是非常重要的处理方式之一,下面将针对这一问题详细阐述其步骤。
第一步:准备材料和工具进行平面磨床磨削前,我们需要准备的首要任务就是准备材料和工具。
需要准备的工具主要包括平面磨床、砂轮等磨削工具。
而材料主要集中在要加工的不锈钢材料和所需辅助材料。
第二步:检验材料和设备在使用设备和材料前,我们需要对其进行检验。
对于平面磨床,需要检查磨头的平整度,以确保精度达标。
而对于不锈钢材料,需要检查其表面情况和硬度等重要参数。
在此基础上,我们可以选择合适的砂轮和磨削技巧,以达到最优加工效果。
第三步:机械加工经过前两步的准备工作,我们可以开始进行机械加工,主要步骤如下:1.将不锈钢材料平放在磨床平台上,平面磨床运行。
2.根据磨床轨迹的要求,进行相关的调整,以保证加工精度。
3.在磨床上安装适当的砂轮,并进行相应的调整。
4.开始磨削,通过旋转砂轮和移动不锈钢材料,直到达到预期的加工效果。
5.在加工过程中,需要定期检查材料的硬度和状态,并重新调整砂轮和磨床以保证加工精度。
第四步:检验在加工完成后,我们需要对所加工的不锈钢材料进行检验,主要检查其表面平整度、硬度和精度等重要参数。
通过检验,我们可以评估加工的效果,确定是否需要进行相关的修正或二次加工。
总体来说,平面磨床磨削方法是加工不锈钢材料最为常用的一种方式。
通过上述步骤的详细介绍,我们可以更好地了解和掌握其操作技巧和加工流程,以更好地应用于实际工作中,提高加工效率和精度。
平面锉削有哪几种方法

平面锉削有哪几种方法平面锉削是一种常见的金属加工方法,通过锉刀对工件表面进行切削加工,以达到精确的形状和尺寸要求。
在实际的生产加工中,平面锉削有多种方法,下面将对其进行详细介绍。
首先,最常见的平面锉削方法是手工锉削。
手工锉削是一种传统的加工方法,操作简单,成本低廉。
工人使用锉刀手持工件,通过手工的方式对工件表面进行锉削,可以根据需要调整锉刀的角度和压力,以达到所需的加工效果。
手工锉削适用于小批量生产和精密加工,但由于其劳动强度大,效率低,不适用于大规模生产。
其次,机械化锉削是一种自动化的平面锉削方法。
机械化锉削通过专用的锉削设备进行加工,可以实现自动送料、自动锉削、自动退料等功能,大大提高了生产效率和加工精度。
机械化锉削适用于大规模生产和重复加工,可以减少人工成本,提高生产效率,但设备投资较大,对操作人员的技术要求也较高。
另外,电脑数控(CNC)锉削是一种高精度、高效率的平面锉削方法。
CNC锉削通过预先编程的数控系统控制锉刀的运动轨迹和锉削参数,实现对工件表面的精确加工。
CNC锉削具有高速、高精度、自动化程度高的特点,适用于复杂形状和高精度要求的工件加工,但设备和技术投资都比较高。
最后,化学锉削是一种特殊的平面锉削方法。
化学锉削是利用化学腐蚀原理对工件表面进行加工,可以实现对特定形状和尺寸的工件进行精确加工,适用于特殊材料和特殊形状的工件加工,但对加工环境和设备要求较高。
综上所述,平面锉削有多种方法,包括手工锉削、机械化锉削、CNC锉削和化学锉削等。
不同的加工方法适用于不同的生产需求,企业在选择平面锉削方法时,需要根据自身的生产情况和加工要求进行综合考虑,以实现最佳的加工效果和经济效益。
维修钳工考试题及答案

维修钳工考试题及答案一、选择题(每题2分,共20分)1. 钳工常用的量具不包括以下哪一项?A. 卡尺B. 千分尺C. 游标卡尺D. 测电笔2. 维修钳工在进行零件拆卸时,应该遵循什么原则?A. 随意拆卸B. 先外后内,先易后难C. 先内后外,先难后易D. 只拆不装3. 钳工在进行钻孔操作时,应使用什么工具?A. 锉刀B. 手锯C. 钻头D. 砂轮机4. 以下哪项不是钳工的基本操作技能?A. 锉削B. 锯削C. 车削D. 钻孔5. 钳工在进行平面磨削时,通常使用什么工具?A. 砂轮B. 砂纸C. 砂带D. 砂轮机6. 维修钳工在进行零件装配时,应该遵循什么原则?A. 随意装配B. 先难后易,先内后外C. 先易后难,先外后内D. 只装不拆7. 钳工在进行螺纹加工时,应使用什么工具?A. 螺丝刀B. 扳手C. 丝锥D. 手锯8. 以下哪项是钳工常用的测量工具?A. 直尺B. 卷尺C. 量角器D. 温度计9. 钳工在进行零件修复时,通常使用什么方法?A. 焊接B. 粘接C. 热处理D. 冷加工10. 钳工在进行零件加工时,应遵循什么原则?A. 随意加工B. 按图加工C. 按经验加工D. 按感觉加工二、判断题(每题1分,共10分)1. 钳工在进行零件加工时,可以不按照图纸加工。
()2. 维修钳工在拆卸零件时,应该先拆卸外部零件,再拆卸内部零件。
()3. 使用游标卡尺测量时,需要将游标与尺身对齐。
()4. 钳工在进行钻孔操作时,必须使用钻头。
()5. 钳工在进行螺纹加工时,可以使用螺丝刀。
()6. 钳工在进行平面磨削时,可以使用砂轮机。
()7. 钳工在进行零件装配时,应该先装配内部零件,再装配外部零件。
()8. 钳工在进行零件修复时,可以使用焊接方法。
()9. 钳工在进行零件加工时,必须按照图纸加工。
()10. 钳工在进行螺纹加工时,必须使用丝锥。
()三、简答题(每题5分,共30分)1. 钳工在进行零件加工时,应遵循哪些基本原则?2. 维修钳工在进行零件拆卸时,应注意哪些事项?3. 简述钳工在进行平面磨削时的操作步骤。
角磨机磨刀的正确方法与技巧
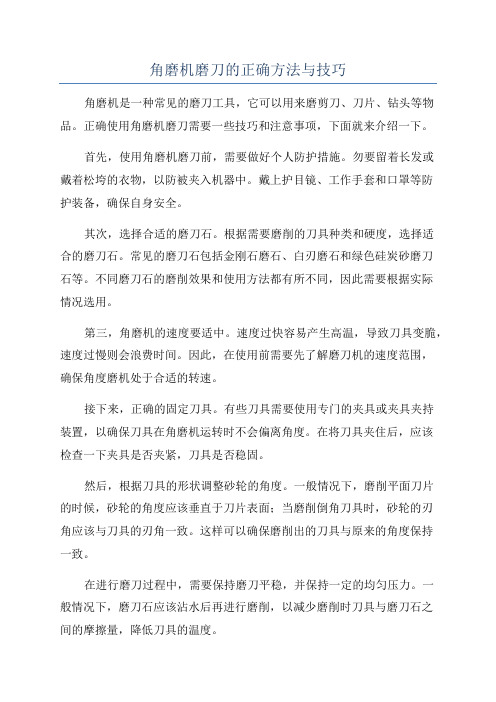
角磨机磨刀的正确方法与技巧角磨机是一种常见的磨刀工具,它可以用来磨剪刀、刀片、钻头等物品。
正确使用角磨机磨刀需要一些技巧和注意事项,下面就来介绍一下。
首先,使用角磨机磨刀前,需要做好个人防护措施。
勿要留着长发或戴着松垮的衣物,以防被夹入机器中。
戴上护目镜、工作手套和口罩等防护装备,确保自身安全。
其次,选择合适的磨刀石。
根据需要磨削的刀具种类和硬度,选择适合的磨刀石。
常见的磨刀石包括金刚石磨石、白刃磨石和绿色硅炭砂磨刀石等。
不同磨刀石的磨削效果和使用方法都有所不同,因此需要根据实际情况选用。
第三,角磨机的速度要适中。
速度过快容易产生高温,导致刀具变脆,速度过慢则会浪费时间。
因此,在使用前需要先了解磨刀机的速度范围,确保角度磨机处于合适的转速。
接下来,正确的固定刀具。
有些刀具需要使用专门的夹具或夹具夹持装置,以确保刀具在角磨机运转时不会偏离角度。
在将刀具夹住后,应该检查一下夹具是否夹紧,刀具是否稳固。
然后,根据刀具的形状调整砂轮的角度。
一般情况下,磨削平面刀片的时候,砂轮的角度应该垂直于刀片表面;当磨削倒角刀具时,砂轮的刃角应该与刀具的刃角一致。
这样可以确保磨削出的刀具与原来的角度保持一致。
在进行磨刀过程中,需要保持磨刀平稳,并保持一定的均匀压力。
一般情况下,磨刀石应该沾水后再进行磨削,以减少磨削时刀具与磨刀石之间的摩擦量,降低刀具的温度。
此外,在磨削过程中需要不断转动刀具,以保持刀具磨削均匀。
当进行切削刀具的磨削时,可以轻轻将刀具从左到右来回移动,以保持其均匀磨削。
但是要注意力度要适中,不要用太大的力来推动刀具,以免刀具变形。
最后,在磨削刀具之前和之后,需要进行清理工作。
清理可以用钢丝球轻轻刷去磨削过程中产生的刀屑和残渣。
而一些细小的刀具,则可以使用硬毛刷来进行清理。
总之,磨刀是一种技术活,需要一定的经验和技巧。
以上是使用角磨机磨刀的正确方法与技巧的简要介绍,希望能对您有所帮助。
简述磨削加工

磨削加工1. 简介磨削加工是一种常见的金属加工方法,通过使用磨料对工件表面进行摩擦磨损,以达到加工的目的。
它可以用于改善工件表面质量、调整尺寸精度和形状精度,以及去除杂质和残余应力等。
磨削加工广泛应用于机械制造、航空航天、汽车制造、模具制造等领域。
2. 磨削原理磨削加工是利用切削性能较差的材料(磨料)对工件进行切削,通过与工件表面的相对运动来实现切削作用。
其主要原理包括以下几个方面:•切削颗粒:磨料是由硬度较高的颗粒组成,通常为氧化铝、碳化硅等材料。
这些颗粒与工件表面摩擦产生很高的切向力,从而实现切削作用。
•切向力:当磨料与工件表面接触时,由于相对运动产生了摩擦力,使得磨料在切向方向上产生了切削力。
这种力对工件表面进行了切削作用。
•磨屑形成:在磨削过程中,磨料与工件表面的摩擦力和切向力使得工件表面的材料被切削下来,形成了磨屑。
这些磨屑会随着磨料的运动带走,并通过冷却液进行排出。
•热效应:由于切削过程中的摩擦力和切向力,会产生较高的温度。
为了避免温度过高引起工件变形或损坏,通常需要使用冷却液进行冷却。
3. 磨削方法根据加工目标和工件材料的不同,磨削加工可以采用多种方法。
下面介绍几种常见的磨削方法:3.1 平面磨削平面磨削是最基本、最常用的磨削方法之一。
它主要用于对平面工件进行加工,如平面零件、平底孔等。
平面磨削通常采用平面砂轮进行加工,通过对工件表面进行连续的摩擦来实现加工效果。
在平面磨削过程中,需要注意保持磨削面与砂轮之间的良好接触,以确保加工质量。
3.2 内圆磨削内圆磨削是用于加工孔内表面的一种方法。
它通常使用内圆砂轮进行加工,通过对孔内表面进行旋转磨削来实现加工效果。
在内圆磨削过程中,需要注意选择合适的砂轮尺寸和形状,并控制好加工参数,以确保加工质量。
3.3 外圆磨削外圆磨削是用于加工轴类零件外表面的一种方法。
它通常使用外圆砂轮进行加工,通过对零件外表面进行旋转磨削来实现加工效果。
在外圆磨削过程中,同样需要注意选择合适的砂轮尺寸和形状,并控制好加工参数。
锉削平面的操作方法

锉削平面的操作方法
锉削平面的操作方法如下:
1. 准备工作:先确保锉具的齿面是干净且锋利的。
可以使用刷子或布擦拭锉具的齿面,如果发现锉具齿面钝了,可以使用锉刀磨削工具将其磨削出锋利的齿面。
2. 定位要削平的工件表面:将要削平的工件放在平整的工作台上,通过触摸和视觉定位好要削平的表面。
可以使用工作台上的夹具将工件固定住,以确保工件的稳定性。
3. 初始锉削:首先在要削平的表面上选择一个起始点,通常从一个角开始进行锉削。
将锉刀对准起始点,保持锉刀与工件表面之间约30度的角度,轻轻地推动锉刀沿着一个方向削减表面,注意保持锉刀与工件表面始终保持接触。
轻轻推动锉刀,不要用力过猛,以免过早损坏锉刀齿面。
4. 均匀锉削:在初始锉削的基础上,逐渐将锉刀向其他方向移动,保证锉削的表面均匀。
可以使用锉刀上的齿面来指导锉削的方向,以确保表面的平整和光滑。
5. 交替锉削:为了保持表面的平整,可以使用交替锉削的方法。
即在一个方向上削平后,再在垂直的方向上进行锉削,以全部覆盖表面,并确保削平的均匀性。
6. 注意细节:在进行锉削时,注意细节的处理。
例如,锉削边缘时,应特别小
心,以免过度削减或损坏细小的部件。
还要注意锉削的深度,避免过度削减或不足削减。
7. 定期检查:在锉削过程中,定期检查工件表面的平整度和光滑度。
如发现不平整的地方,可以进一步锉削,直至达到所需的平整度和光滑度。
8. 清洁工作:锉削完毕后,用刷子或布擦拭工件和锉具,将剩余的金属屑清除掉,并确保锉具的齿面干净。
以上是锉削平面的操作方法,希望能对您有所帮助。
平面研磨技巧

加工一. 加工前确认:1.1 加工工件要否留成型余量,如:成型去队量过多的应留余量0.03_0.05mm. 二: 成型2.1 六面体. 1.1铁料选用46K(S)粒度砂轮,用直径10mm钻石笔修砂轮,初修砂轮转速1800-2400转/分钟.修切量为0.04-0.1mm,切削铁料粗磨进刀量为0.03-0.1mm精磨时,精修砂轮轮转速在2500-3000转/分钟.修切量为0.04-0.1mm.很慢移动精磨进刀量为0.001-0.005mm. 1.2 碳化钨选用D100-D180粒度砂轮,用钼块修砂轮,修砂轮时砂轮转速为1100-1300转/分钟.下刀量为0.002-0.01mm.切削碳化钨,转速为3000-3400转/分钟下刀量为0.001-0.01mm. 2.2. 切槽.2.1.铁料选用46,60,80,100,120,150,180,220粒度砂轮.a. 46,60粒度砂轮用于留量粗切,修刀转速为1800-2400转/分钟,下刀量为0.05-0.04mm.切削转速为2400-3000转/分钟,下刀量为0.001-0.015mm.b. 80,100,120,粒度砂轮用于槽宽大于或等于0.7mm的槽.修刀转速为2000-2400侧壁进刀量为0-0.005mm,底面切削转速为2700-3000转/分钟.下刀量为0.001-0.01mm.c. 150,180,220粒度砂轮用于小于或等于0.7mm的槽及清角,槽宽越小粒度越高,修切转速为1800-2200转/分钟,侧壁进刀量为0-0.003mm,底面下刀量为0-0.005mm,切削转速为3000-3200转/分钟,下刀量为0.001-0.003mm. 2.2. 碳化钨材料选用D220-D400粒度砂轮,修刀转速为1100-1300转/分钟,修刀使用钼棒,侧壁修刀进刀量为0-0.003mm,底面下刀量为0-0.005mm切削转速为3000-3600转/分钟,下刀量为0-0.005mm. 2.3. 磨斜度: 铁料选用46,60,80,100,120粒度砂轮.46,60粒度砂轮一般用于正弦台上磨削修刀转速为2200-2400转/分钟,下刀量为0.005-0.02mm.磨削转速为2700-3000转/分钟.80,100,120粒度砂轮可用于正弦台上成型去量少的斜度.主要用件写成型斜度砂轮,用角度器修,修刀转速为2000-2400转/分钟,下刀量为0-0.01mm,切削转速为2700-3000转/分钟,下刀量为0-0.005mm.2.3.1.碳化钨材料选用D150-D320,D400粒度砂轮,视角度大小都可用在正弦台上磨削.修刀转速为1100-1300转/分钟,用钼块棒修刀,下刀量为0.001-0.01mm.D320,D400主要用作带直边,带斜度的成型,用角度器,钼棒修刀,修刀时一切同上. 2.4.做圆R.铁料一般选用80,100,120粒度砂轮,用R器修刀,修转速为2000-2400转/分钟.下量为0-0.005mm.切削转速为2800-3200转/分钟.下刀量为0-0.003mm.2.4.1 碳化钨材料一般选用D400粒度砂轮,以手执钼棒修刀,修刀转速为1200-1400转/分钟,以钼棒碰触要求圆的凸出部分,以投影机监测.切削转速为3200-3600转/分钟.下刀量为0-0.005mm.2.4.3 完工处理,去毛头.退磁,上油.填写加工检验表. 2.4.4修工作台:B-1. 将砂轮转速调至2000-2400转/分钟,按0.005-0.01mm.进刀量粗修一次平台见光. B-2, 精磨时将砂轮转速调至1800-2000转/分钟左右,走刀要连续勿冲罄.前后走刀应慢,应均匀,砂轮不得在平台上停留,可加润滑油研磨平台.最后涂奇异笔迹.B-3.对刀时应小心谨慎,应选平台的最边沿为对刀面,以免伤到平台的工作部分. 2.5.修靠板:B-1.1.方法:修靠板一律选用46k(J)砂轮,将砂轮修至如图A所示之形状,转速为2800-3200转/分钟砂轮应进至靠板底部;如图所示,b面须略高于a面,然后开始修磨,进刀量选0.001-0.003mm为宜,慢慢修直到靠板侧面全部见光,再缓慢进刀继续修磨直到为火花很小,声音均匀时为止,注意勿使靠板发热.B-1.2.用一直角度标准之档块的一角,靠隹靠板,目视其接触面,看光线是否等宽,若上宽下宽侧靠板为倾斜面,需重修,反之修好了.B-2 对刀. 在靠板面上涂一层奇异笔液在奇异笔液上擦上粉笔,将砂轮慢慢靠近靠板,磨掉粉笔的痕迹,然后以0.001mm进刀量慢慢进刀.目测耳听,直到奇异笔迹被磨掉,发生连续不断的均匀声音,数理归零.对刀完毕,也可以二件对刀或试切对刀.加工方法与上一样.。
不同类型平面磨床的区别及磨削操作特点

不同类型平面磨床的区别及磨削操作特点不同类型平面磨床的区别及磨削操作特点一、平面磨削的方式按照平面磨床和工作台的结构特点和配置形式,可将平面磨床分为五种类型,即卧轴矩台平面磨床、卧轴圆台平面磨床、立轴矩台平面磨床、立轴圆台平面磨床及双端面磨床等。
1、平面磨床的类型简介(1)卧轴矩台平面磨床砂轮的主轴轴线与工作台台面平行,工件安装在矩形电磁吸盘上,并随工作台作纵向往复直线运动。
砂轮在高速旋转的同时作间歇的横向移动,在工件表面磨去一层后,砂轮反向移动,同时作一次垂向进给,直至将工件磨削到所需的尺寸。
(2)卧轴圆台平面磨床砂轮的主轴是卧式的,工作台是圆形电磁吸盘,用砂轮的圆周面磨削平面。
磨削时,圆形电磁吸盘将工件吸在一起作单向匀速旋转,砂轮除高速旋转外,还在圆台外缘和中心之间作往复运动,以完成磨削进给,每往复一次或每次换向后,砂轮向工件垂直进给,直至将工件磨削到所需要的尺寸。
由于工作台是连续旋转的,所以磨削效率高,但不能磨削台阶面等复杂的平面。
(3)立轴柜台平面磨床砂轮的主轴与工作台垂直,工作台是矩形电磁吸盘,用砂轮的端面磨削平面。
这类磨床只能磨简单的平面零件。
由于砂轮的直径大于工作台的宽度,砂轮不需要作横向进给运动,故磨削效率较高。
(4)立轴圆台平面磨床砂轮的主轴与工作台垂直,工作台是圆形电磁吸盘,用砂轮的端面磨削平面。
磨削时,圆工作台匀速旋转,砂轮除作高速旋转外,定时作垂向进给。
(5)双端面磨床该磨床能同时磨削工件两个平行面,磨削时工件可连续送料,常用于自动生产线等场合。
2、平面磨削的形式以砂轮工作表面的不同,平面磨削可分为周边磨削、端面磨削以及周边一端面磨削三种方式。
①周边磨削:又称圆周磨削,是用砂轮的圆周面进行磨削。
卧轴的平面磨床属于这种形式。
②端面磨削:用砂轮的端面进行磨削。
立轴的平面磨床均属于这种形式。
③周边一端面磨削:同时用砂轮的圆周面和端面进行磨削。
磨削台阶面时,若台阶不深,可在卧轴矩台平面磨床上,用砂轮进行周边一端面磨削。
平面磨床的操作方法及注意事项
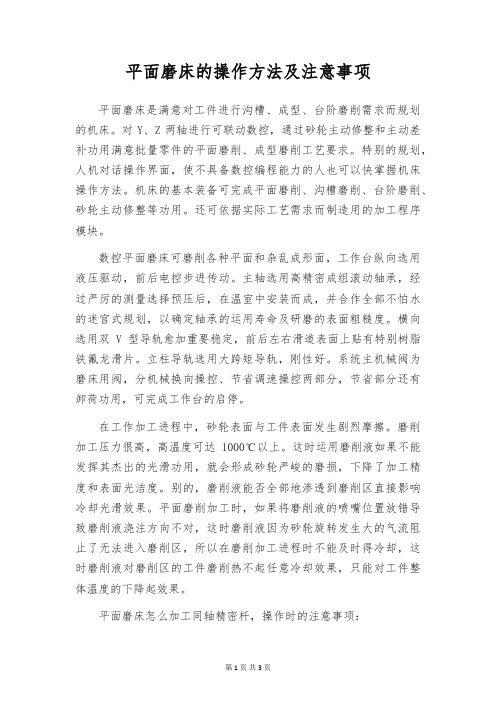
平面磨床的操作方法及注意事项平面磨床是满意对工件进行沟槽、成型、台阶磨削需求而规划的机床。
对Y、Z两轴进行可联动数控,通过砂轮主动修整和主动差补功用满意批量零件的平面磨削、成型磨削工艺要求。
特别的规划,人机对话操作界面,使不具备数控编程能力的人也可以快掌握机床操作方法。
机床的基本装备可完成平面磨削、沟槽磨削、台阶磨削、砂轮主动修整等功用。
还可依据实际工艺需求而制造用的加工程序模块。
数控平面磨床可磨削各种平面和杂乱成形面,工作台纵向选用液压驱动,前后电控步进传动。
主轴选用高精密成组滚动轴承,经过严厉的测量选择预压后,在温室中安装而成,并合作全部不怕水的迷宫式规划,以确定轴承的运用寿命及研磨的表面粗糙度。
横向选用双V型导轨愈加重要稳定,前后左右滑道表面上贴有特别树脂铁氟龙滑片。
立柱导轨选用大跨矩导轨,刚性好。
系统主机械阀为磨床用阀,分机械换向操控、节省调速操控两部分,节省部分还有卸荷功用,可完成工作台的启停。
在工作加工进程中,砂轮表面与工件表面发生剧烈摩擦。
磨削加工压力很高,高温度可达1000℃以上。
这时运用磨削液如果不能发挥其杰出的光滑功用,就会形成砂轮严峻的磨损,下降了加工精度和表面光洁度。
别的,磨削液能否全部地渗透到磨削区直接影响冷却光滑效果。
平面磨削加工时,如果将磨削液的喷嘴位置放错导致磨削液浇注方向不对,这时磨削液因为砂轮旋转发生大的气流阻止了无法进入磨削区,所以在磨削加工进程时不能及时得冷却,这时磨削液对磨削区的工件磨削热不起任意冷却效果,只能对工件整体温度的下降起效果。
平面磨床怎么加工同轴精密杆,操作时的注意事项:1、工件的旋转方向要和砂轮的旋转方向同向。
2、初步加工前或每次测量后继续加工时,工件都要在砂轮初步旋转前旋转。
各次加工完成后,工件都要在砂轮间断旋转后间断旋转。
3、每次对工件进行测量时,要等砂轮全部间断旋转后方能从Y 轴方向退刀。
4、测量时要轻、稳,削减量具的摇摆,以防折弯或折断工件。
常见的3种磨削方法介绍
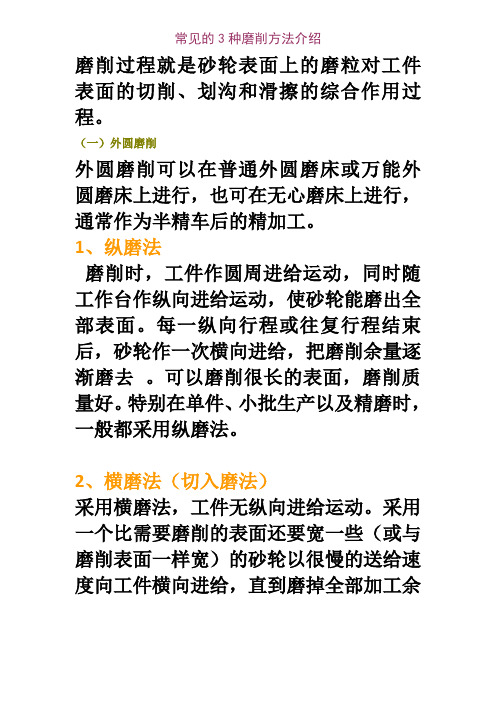
常见的3种磨削方法介绍磨削过程就是砂轮表面上的磨粒对工件表面的切削、划沟和滑擦的综合作用过程。
(一)外圆磨削外圆磨削可以在普通外圆磨床或万能外圆磨床上进行,也可在无心磨床上进行,通常作为半精车后的精加工。
1、纵磨法磨削时,工件作圆周进给运动,同时随工作台作纵向进给运动,使砂轮能磨出全部表面。
每一纵向行程或往复行程结束后,砂轮作一次横向进给,把磨削余量逐渐磨去。
可以磨削很长的表面,磨削质量好。
特别在单件、小批生产以及精磨时,一般都采用纵磨法。
2、横磨法(切入磨法)采用横磨法,工件无纵向进给运动。
采用一个比需要磨削的表面还要宽一些(或与磨削表面一样宽)的砂轮以很慢的送给速度向工件横向进给,直到磨掉全部加工余量。
横磨法主要用于磨削长度较短的外圆表面以及两边都有台阶的3、深磨法特点是全部磨削余量(直径上一般为~0.6mm)在一次纵走刀中磨去。
磨削时工件圆周进给速度和纵向送给速度都很慢,砂轮前端修整成阶梯形或锥形。
深磨法的生产率约比纵磨法高一倍,能达到IT6级,表面粗糙度的Ra值在~之间。
但修整砂轮较复杂,只适于大批、大量生产,磨削允许砂轮越出被加工面两端较大距离的工件。
4、无心外圆磨削法工件放在磨削砂轮和导轮之间,下方有一托板。
磨削砂轮(也称为工作砂轮)旋转起切削作用,导轮是磨粒极细的橡胶结合剂砂轮。
工件与导轮之间的摩擦力较大,从而使工件以接近于导轮的线速度回转。
无心外圆磨削在无心外圆磨床上进行。
无心外圆磨床生产率很高,但调整复杂;不能校正套类零件孔与外圆的同轴度误差;不能磨削具有较长轴向沟槽的零件,以防外圆产生较大的圆度误差。
因此,无心外圆磨削多用于细长光轴、轴销和小套等零件的大批、大量生产轴径。
(二)内圆磨削内圆磨削除了在普通内圆磨床或万能外圆磨床上进行外,对大型薄壁零件,还可采用无心内圆磨削;对重量大、形状不对称的零件,可采用行星式内圆磨削,此时工件外圆应先经过精加工。
内圆磨削由于砂轮轴刚性差,一般都采用纵磨法。
不锈钢的平面磨床磨削方法
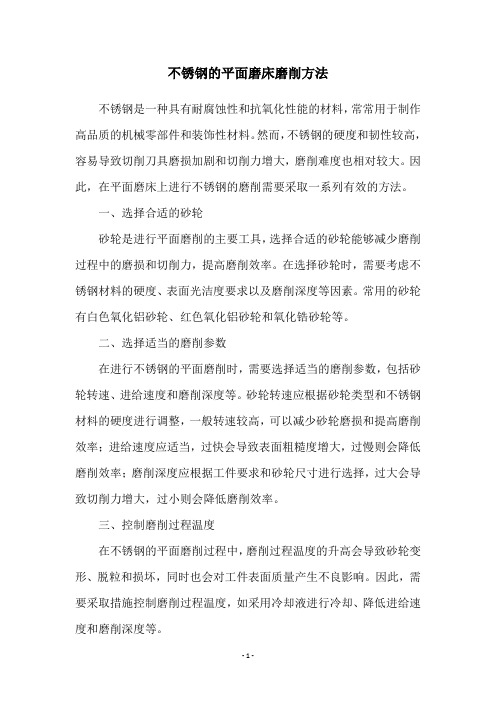
不锈钢的平面磨床磨削方法
不锈钢是一种具有耐腐蚀性和抗氧化性能的材料,常常用于制作高品质的机械零部件和装饰性材料。
然而,不锈钢的硬度和韧性较高,容易导致切削刀具磨损加剧和切削力增大,磨削难度也相对较大。
因此,在平面磨床上进行不锈钢的磨削需要采取一系列有效的方法。
一、选择合适的砂轮
砂轮是进行平面磨削的主要工具,选择合适的砂轮能够减少磨削过程中的磨损和切削力,提高磨削效率。
在选择砂轮时,需要考虑不锈钢材料的硬度、表面光洁度要求以及磨削深度等因素。
常用的砂轮有白色氧化铝砂轮、红色氧化铝砂轮和氧化锆砂轮等。
二、选择适当的磨削参数
在进行不锈钢的平面磨削时,需要选择适当的磨削参数,包括砂轮转速、进给速度和磨削深度等。
砂轮转速应根据砂轮类型和不锈钢材料的硬度进行调整,一般转速较高,可以减少砂轮磨损和提高磨削效率;进给速度应适当,过快会导致表面粗糙度增大,过慢则会降低磨削效率;磨削深度应根据工件要求和砂轮尺寸进行选择,过大会导致切削力增大,过小则会降低磨削效率。
三、控制磨削过程温度
在不锈钢的平面磨削过程中,磨削过程温度的升高会导致砂轮变形、脱粒和损坏,同时也会对工件表面质量产生不良影响。
因此,需要采取措施控制磨削过程温度,如采用冷却液进行冷却、降低进给速度和磨削深度等。
四、定期更换砂轮
砂轮的磨损程度会影响磨削效率和工件表面质量,因此需要定期更换砂轮,以保证磨削效率和磨削质量。
同时,在更换砂轮时也需要注意选择合适的砂轮规格和类型。
不锈钢的平面磨床磨削方法需要综合考虑多种因素,采取有效的措施进行控制和调整,方可达到理想的磨削效果和工件表面质量。
平面研磨技巧
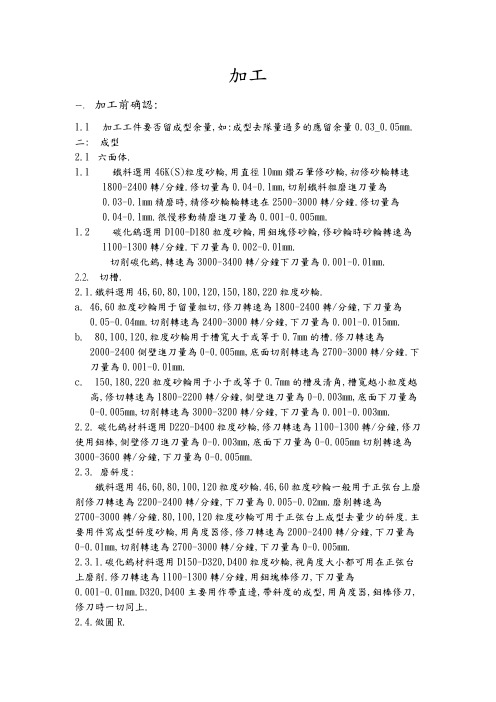
加工一. 加工前确認:1.1加工工件要否留成型余量,如:成型去隊量過多的應留余量0.03_0.05mm. 二: 成型2.1六面体.1.1鐵料選用46K(S)粒度砂輪,用直徑10mm鑽石筆修砂輪,初修砂輪轉速1800-2400轉/分鐘.修切量為0.04-0.1mm,切削鐵料粗磨進刀量為0.03-0.1mm精磨時,精修砂輪輪轉速在2500-3000轉/分鐘.修切量為0.04-0.1mm.很慢移動精磨進刀量為0.001-0.005mm.1.2碳化鎢選用D100-D180粒度砂輪,用鉬塊修砂輪,修砂輪時砂輪轉速為1100-1300轉/分鐘.下刀量為0.002-0.01mm.切削碳化鎢,轉速為3000-3400轉/分鐘下刀量為0.001-0.01mm.2.2. 切槽.2.1.鐵料選用46,60,80,100,120,150,180,220粒度砂輪.a.46,60粒度砂輪用于留量粗切,修刀轉速為1800-2400轉/分鐘,下刀量為0.05-0.04mm.切削轉速為2400-3000轉/分鐘,下刀量為0.001-0.015mm.b.80,100,120,粒度砂輪用于槽寬大于或等于0.7mm的槽.修刀轉速為2000-2400側壁進刀量為0-0.005mm,底面切削轉速為2700-3000轉/分鐘.下刀量為0.001-0.01mm.c.150,180,220粒度砂輪用于小于或等于0.7mm的槽及清角,槽寬越小粒度越高,修切轉速為1800-2200轉/分鐘,側壁進刀量為0-0.003mm,底面下刀量為0-0.005mm,切削轉速為3000-3200轉/分鐘,下刀量為0.001-0.003mm.2.2. 碳化鎢材料選用D220-D400粒度砂輪,修刀轉速為1100-1300轉/分鐘,修刀使用鉬棒,側壁修刀進刀量為0-0.003mm,底面下刀量為0-0.005mm切削轉速為3000-3600轉/分鐘,下刀量為0-0.005mm.2.3. 磨斜度:鐵料選用46,60,80,100,120粒度砂輪.46,60粒度砂輪一般用于正弦台上磨削修刀轉速為2200-2400轉/分鐘,下刀量為0.005-0.02mm.磨削轉速為2700-3000轉/分鐘.80,100,120粒度砂輪可用于正弦台上成型去量少的斜度.主要用件寫成型斜度砂輪,用角度器修,修刀轉速為2000-2400轉/分鐘,下刀量為0-0.01mm,切削轉速為2700-3000轉/分鐘,下刀量為0-0.005mm.2.3.1.碳化鎢材料選用D150-D320,D400粒度砂輪,視角度大小都可用在正弦台上磨削.修刀轉速為1100-1300轉/分鐘,用鉬塊棒修刀,下刀量為0.001-0.01mm.D320,D400主要用作帶直邊,帶斜度的成型,用角度器,鉬棒修刀,修刀時一切同上.2.4.做圓R.鐵料一般選用80,100,120粒度砂輪,用R器修刀,修轉速為2000-2400轉/分鐘.下量為0-0.005mm.切削轉速為2800-3200轉/分鐘.下刀量為0-0.003mm.2.4.1 碳化鎢材料一般選用D400粒度砂輪,以手執鉬棒修刀,修刀轉速為1200-1400轉/分鐘,以鉬棒碰触要求圓的凸出部分,以投影机監測.切削轉速為3200-3600轉/分鐘.下刀量為0-0.005mm.2.4.3完工處理,去毛頭.退磁,上油.填寫加工檢驗表.2.4.4修工作台:B-1. 將砂輪轉速調至2000-2400轉/分鐘,按0.005-0.01mm.進刀量粗修一次平台見光.B-2, 精磨時將砂輪轉速調至1800-2000轉/分鐘左右,走刀要連續勿沖罄.前后走刀應慢,應均勻,砂輪不得在平台上停留,可加潤滑油研磨平台.最后涂奇异筆跡.B-3.對刀時應小心謹慎,應選平台的最邊沿為對刀面,以免傷到平台的工作部分.2.5.修靠板:B-1.1.方法:修靠板一律選用46k(J)砂輪,將砂輪修至如圖A所示之形狀,轉速為2800-3200轉/分鐘砂輪應進至靠板底部;如圖所示,b面須略高于a面,然后開始修磨,進刀量選0.001-0.003mm為宜,慢慢修直到靠板側面全部見光,再緩慢進刀繼續修磨直到為火花很小,聲音均勻時為止,注意勿使靠板發熱.B-1.2.用一直角度標准之檔塊的一角,靠隹靠板,目視其接触面,看光線是否等寬,若上寬下寬側靠板為傾斜面,需重修,反之修好了.B-2 對刀.在靠板面上涂一層奇异筆液在奇异筆液上擦上粉筆,將砂輪慢慢靠近靠板,磨掉粉筆的痕跡,然后以0.001mm進刀量慢慢進刀.目測耳听,直到奇异筆跡被磨掉,發生連續不斷的均勻聲音,數理歸零.對刀完畢,也可以二件對刀或試切對刀.加工方法与上一樣.修砂輪:鑽石修刀的擺放:圖A,圖B特殊材料(碳化鎢)加工工序加工條件設定一覽表研磨平面研磨直角:1.利用杠杆千分表抓直角.2.利用精密虎鉗抓直角.3. 利用正角器抓共同點:先磨出兩基准面再磨另四面,先粗磨一面后,再精磨另一面后必須再精磨該平面,以防工件粗磨時因切削切力過大或發熱而導致工件位置變動,使角不正.切槽的研磨加工:A.修砂輪側面:A-1. 用單面修刀修砂輪的側面:A-1.1 修側面時根据槽的深度要求,應晝量保証砂輪側面高度适中.一般應多几個毫米.A-1.2 上下打砂輪法:利用砂輪切削鑽石尖以達到修整砂輪的目的.粗修時進刀量一般為0.1-1.0mm精修時進刀量一般為0.001-0.02mm.粗修應盡量快以体察砂輪能承受的沖擊力和心軸無异樣的振動為前提.一般若砂輪厚度大于0.7mm則雙邊余量為0.1進入精修用有鋒銳角的鑽石,注意修刀的擺放位置應斜對著砂輪旋轉的逆方向,可用手指尖感覺修刀尖是否有一种微刺感,修整時應上下進刀小(0.005-0.01)左右走刀快穩,隨時順听聲音狀況,若感覺砂輪中部分聲音比外緣聲音大,則應從砂輪中部進刀,從上往下打.直到感覺中部聲音比外緣聲音稍小為止,最后還得用左右修整法.不須上下進刀.只走動大拖把左右來回慢慢地刮整砂輪側面叫精刮,使砂輪表面面粗度均勻平整,去除表面松動浮力,然后測砂輪厚度,根据各自机台性能,找出砂輪厚度与砂輪運轉時所切槽之寬度之間的關系,利用其之間的修正值修正,以保証成型槽的尺寸精度必要時也可以試切法投影.砂輪實際厚度与槽應小0.002-0.005mm為宜.A-1.3 若砂輪厚度<0.7mm時,特別應考慮砂輪的強度雙邊余量為0.1mm進入精修.方法同(A-1.2)一樣,但必須注意砂輪段差不能等高,以免降低砂輪強度或把砂輪打破.斷差不一樣高A-1.4 砂輪在修整過程中應适時耳聞,体察鑽石尖与砂輪之間的運作狀況,特別是薄砂輪修整時應适時調整鑽石尖与砂輪的接触點,以确保修刀的鋒利,砂輪修好后應驗証其是否平直可有意將修刀向砂輪方向進給0.001mm;体察其聲音狀況,若進0.001則聲音很大,而退0.001則聲音明顯很小,接近無聲狀況,說明砂輪已OK.圖(1) 圖(2) 圖(3) 切槽:通常在研磨加工中將槽分為兩种圖(1) 圖(2)C-1.如圖(1)所示通常稱為台階或斷差對于塑模零件,自動机零件加工斷差時,只需修砂輪底部和砂輪一個側面,先粗切留0.03-0.30mm余量再精修砂輪底部,精修台階以進刀量0.001-0.005mm為宜.加工時由里往外精磨出來.加工件無過精磨到位后.若有圖中所示之跳角則將砂輪按圖(3)所示方法修砂輪底部.根据尺寸要求目測砂輪底部所留量的寬度和深度其尺寸應比圖紙尺寸在0.1mm左右,進行跳角對沖模零件台階側面需絕對垂直于底面,故精磨時a尺寸應留余量0.005mm 左右,b尺寸到位后,修側面砂輪,然后慢慢靠近側面進刀量為0.001-0.002mm.邊靠邊測量尺寸合格為止.控制勿使工件發熱.C-2. 如圖(2)所示根据槽寬之不同分以下三种情況:C-2.1. 槽寬大于6mm可分段粗切,精磨時按C-1之加工法,將工件調頭后,則槽的兩邊即到.C-2.2. 槽寬小于6mm,修成型砂輪直接成型,對于大于1.5mm槽寬的沖模零件,精磨時須留0.01-0.15mm的余量.加工方法按C-1中沖模的切槽加工方法,修砂輪兩側面進行貼邊.保証槽的各尺寸精度.C-2.3. 對槽位尺寸精度要求很高的工件,可將沿槽邊心距余量,槽磨到位后,修外型保証槽位尺寸.成型斜面的加工:基本成型斜面可分為如圖所示三种:(1) (2) (3)B-1.砂輪角度之成型:1.1.使用治工具為角度成型器計算公式為h=LxSina. h=所塊規之高度.L=角度成型器之中心距. A=斜面与水平方向組成之夾角.1.2.粗修,精修砂輪后應試切塑料片并進行投影.1.3.當圖中h>10時修成型砂輪對刀后,因砂輪寬度不夠.應分几次成型,第一次成型斜面尺寸到位在如圖所示位置涂奇异筆跡.第二次輕擦筆跡既可.圓弧成型加工:A.采用透視砂輪圓弧成型器之調試將擋塊千分表,圓弧器以及薄片放置如圖所示.圓弧成型器兩邊各擺15°若千分表上讀數在兩邊15°應讀數一致則鑽石修刀在圓弧成型器中心,反之則應調試.B.修磨圓弧成型砂輪:圓弧成型器之基面到軸心O之距离為定值L,h為所墊塊規的高度,成型砂輪外圓時如圖B1中所示h=L-R. 成型砂輪內圓弧時如圖B2 h=L+R 加工方法:按原理計算需墊塊規高度,將R器一側面緊靠靠板,。
平面磨削方法

2).用圆柱角尺找正垂直面
把圆柱角尺和工件都放在平板上,使其靠近, 观察间隙,然后在工件下面垫纸,使间隙均匀.再 磨削上平面.
圆 柱 角 尺
工件 垫纸 平板
3).用专用百分表座找正垂直面
1.先把圆柱角尺和百分表座放在平板上,让百分表 座定位点顶住工件下部最大外圆处,表头接触工 件的上部,调到零. 2.圆柱角尺移走,把工件放到原位置,看百分表上的 读数. 3.然后在工件下面垫纸 ,使百分表上读数几乎接近 零.然后再磨削上平面.
作业:
第129页:1.2.3.题
百分表
工件 圆柱角尺
垫纸
百分表座定位点
注意事项:
1.用阶台砂轮磨削法时机床的刚性必须符合要求. 2.用精密平口钳,精密角铁,导磁直角铁.精密V型架之前先了解一 下夹具的精度,磨削之前找正夹具侧面要与工作台纵向方向平行, 然后再找正工件的位置. 3.用垫纸法时,要用很薄的油光纸.
三、平面磨削方法的应用
2.用精密角铁装夹
特点:精密角铁具有两个互相垂直的工作平面,它的垂直 度为0.005毫米,可达到较高的加工精度. 适用:适合装夹大小重量都比角铁小的导磁或非磁性垂 直面工件.
3.导磁直角铁装夹
特点:导磁角铁有四个面互相垂直,黄铜把纯铁隔开,距离与 电磁吸盘一样,磁力线可以延伸到上面. 适用:磨削不易找正的小零件,或比较光滑的工件.
砂轮
工件
2.切入磨削法 定义:磨削时,砂轮不作横向进给, 工作台在纵向行程的终了 砂轮垂直进给一次.把所有的余量磨完. 特点:生产效率低,表面质量差. 适用:适合磨削比较狭窄的工件.
砂轮
工件
3.阶台砂轮磨削法
定义:是按工件余量的大小,将砂轮修
整成阶梯形,大大提高垂直进给量 . 特点:效率高,磨削效果好.
钳工中级考试题库及答案
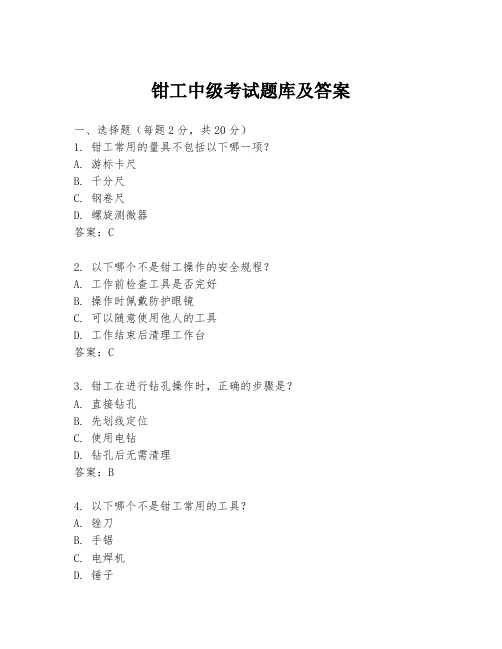
钳工中级考试题库及答案一、选择题(每题2分,共20分)1. 钳工常用的量具不包括以下哪一项?A. 游标卡尺B. 千分尺C. 钢卷尺D. 螺旋测微器答案:C2. 以下哪个不是钳工操作的安全规程?A. 工作前检查工具是否完好B. 操作时佩戴防护眼镜C. 可以随意使用他人的工具D. 工作结束后清理工作台答案:C3. 钳工在进行钻孔操作时,正确的步骤是?A. 直接钻孔B. 先划线定位C. 使用电钻D. 钻孔后无需清理答案:B4. 以下哪个不是钳工常用的工具?A. 锉刀B. 手锯C. 电焊机D. 锤子答案:C5. 钳工在进行锉削操作时,应如何操作?A. 随意锉削B. 保持锉刀与工件垂直C. 用力过猛D. 锉削时不使用润滑剂答案:B6. 钳工在进行螺纹加工时,应使用哪种工具?A. 锉刀B. 手锯C. 丝锥D. 钻头答案:C7. 钳工在进行装配时,应遵循的原则是什么?A. 随意装配B. 先大后小C. 先易后难D. 先紧后松答案:C8. 钳工在进行平面磨削时,应使用哪种磨具?A. 砂纸B. 砂轮C. 锉刀D. 钢刷答案:B9. 钳工在进行工件测量时,应如何读取游标卡尺的读数?A. 直接读取主尺上的数值B. 读取游标上的数值C. 读取主尺与游标上的数值之和D. 读取游标上的数值减去主尺上的数值答案:C10. 钳工在进行工件的热处理时,以下哪个步骤是不必要的?A. 加热B. 保温C. 冷却D. 抛光答案:D二、判断题(每题1分,共10分)1. 钳工在进行锉削操作时,应保持锉刀与工件平行。
(×)2. 钳工在进行钻孔操作时,必须先划线定位。
(√)3. 钳工在进行螺纹加工时,可以使用电钻进行。
(×)4. 钳工在进行装配时,应先装配小件后装配大件。
(×)5. 钳工在进行平面磨削时,应使用砂纸进行。
(×)6. 钳工在进行工件测量时,应读取游标卡尺的主尺与游标上的数值之和。
(√)7. 钳工在进行工件的热处理时,不需要进行冷却步骤。
薄片零件平面磨削的几种装夹方式word精品
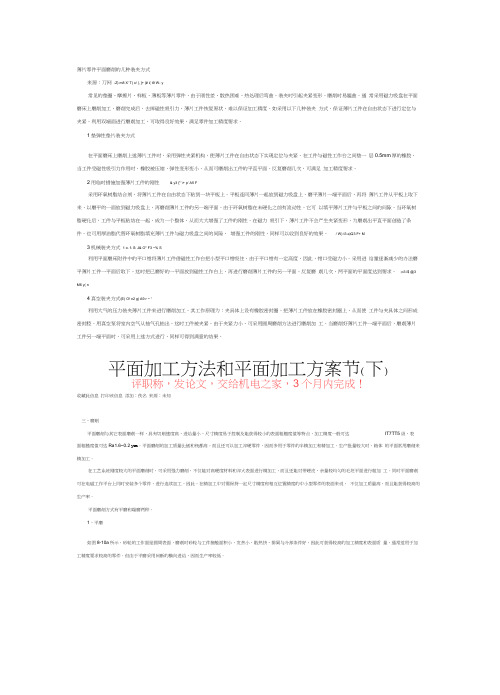
薄片零件平面磨削的几种装夹方式来源:刀网-Z) m8 X' T( x/ |, ]+ |# i( t9 W- y常见的垫圈、摩擦片、样板、薄板等薄片零件,由于刚性差、散热困难、热处理后弯曲,装夹时引起夹紧变形,磨削时易翘曲,通常采用磁力吸盘在平面磨床上磨削加工,磨削完成后,去掉磁性吸引力,薄片工件恢复原状,难以保证加工精度。
如采用以下几种装夹方式,保证薄片工件在自由状态下进行定位与夹紧,利用双端面进行磨削加工,可取得良好效果,满足零件加工精度要求。
1垫弹性垫片装夹方式在平面磨床上磨削上述薄片工件时,采用弹性夹紧机构,使薄片工件在自由状态下实现定位与夹紧。
在工件与磁性工作台之间垫一层0.5mm厚的橡胶,当工件受磁性吸引力作用时,橡胶被压缩,弹性变形变小,从而可磨削出工件的平直平面。
反复磨削几次,可满足加工精度要求。
2用临时措施加强薄片工件的刚性& y3 {* \+ p' A5 F采用环氧树脂结合剂,将薄片工件在自由状态下粘到一块平板上。
平板连同薄片一起放到磁力吸盘上。
磨平薄片一端平面后,再将薄片工件从平板上取下来,以磨平的一面放到磁力吸盘上,再磨削薄片工件的另一端平面。
由于环氧树脂在未硬化之前有流动性,它可以填平薄片工件与平板之间的间隙。
当环氧树脂硬化后,工件与平板粘结在一起,成为一个整体,从而大大增强了工件的刚性。
在磁力吸引下,薄片工件不会产生夹紧变形,为磨削出平直平面创造了条件。
也可用厚油脂代替环氧树脂填充薄片工件与磁力吸盘之间的间隙,增强工件的刚性,同样可以收到良好的效果。
/ W) t3 a)Q3 F+ M 3机械装夹方式 1 o. f- S: J& O* F3 ~% S利用平面磨床附件中的平口钳将薄片工件借磁性工作台把小型平口钳吸住,由于平口钳有一定高度,因此,钳口受磁力小。
采用进给量逐渐减少的办法磨平薄片工件一平面后取下,这时把已磨好的一平面放到磁性工作台上,再进行磨削薄片工件的另一平面,反复磨削几次,两平面的平面度达到要求。
平面磨床磨薄板变形的技巧

平面磨床磨薄板变形的技巧
1. 控制磨削过程中的温度:平面磨床磨薄板时会产生热量,容易使薄板变形。
因此,在磨削过程中应缓慢进给、逐步加工,控制切削速度和磨削压力,同时要保证冷却液的流量和温度,避免过高的温度使薄板变形。
2. 磨削路径的选择:为了防止薄板在磨削过程中发生变形,应选用合适的磨削路径。
可以采用交错式的磨削路径,将每次磨削的厚度控制在一定范围内,同时还可以适时调整磨削方向,利用逆方向的磨削来消除薄板的变形。
3. 适当的磨削力:平面磨床在磨削时需要适当的磨削力,但是磨削力过大也容易使薄板变形。
因此,应根据薄板的材料和厚度等因素来控制磨削力大小,避免造成薄板的变形。
4. 磨石的选择:平面磨床磨削薄板时,选择适合薄板磨削的磨石也很重要。
一般应选择结构紧密、硬度适中、颗粒细小、形状规整的磨石,这样可以在磨削时更好地保持薄板的平整度。
5. 安全措施的落实:为确保操作人员的安全,平面磨床操作时应做好防护措施,同时还应随时检查设备的故障情况,及时解决,以避免磨床磨削薄板时出现异常情况导致薄板的损坏和变形。
角磨机打磨平面技巧【秘籍】

粗抛:先用百叶打平,不用打太狠,表面大致打平即可.中抛:再用麻轮(特殊纤维轮)较细地打,要把细缝打没,轮面与表面稍有角度就行,可稍用力压在表面上,并且要注意打磨方向要一致使磨纹有规则不凌乱,,以保证美观,细抛:最后用棉轮,先在轮上打上抛光膏,再打表面,轮面要与表面相平接触,不用往下压,扶住角磨机就行,要多打几次抛光膏,抛完后用电焊手套狠擦,擦出来就很亮..这三抛尽量拉长线,保证痕迹均匀,美观.扩展资料:角磨机的正确使用方法如下:1.使用角磨机,起动前必须两手将手柄握紧,防止起动转矩作用而掉落,确保人身机具安全。
2.角磨机必须安装防护罩,否则不得使用。
3.砂轮机工作时,操作人员不要站在出屑的方向,防止铁屑飞出伤到眼睛,使用时最好戴防护目镜。
4.磨削薄板构件时,砂轮应轻轻接触工作,不能用力过猛,并密切注视磨削部位,以防磨穿。
5.使用角磨机要轻拿轻放,用后及时切断电源或气源,妥善放置,严禁乱丢乱放甚至摔砸。
角磨机的使用注意事项如下:1.带保护眼罩,长头发职工一定要先把头发扎起。
不能用手捉住小零件对角磨机进行加工。
2.操作员在操作时,要注意配件是否完好,绝缘电缆线有无破损,有无老化等现象。
检查过后,插上电源,要等待砂轮转动稳定后才能工作,才可以进行作业。
3.切割及打磨作业时,周围一米内不能有人员以及易爆物品,不要对着有人的方向进行工作、以防造成人员伤亡。
4.当的砂轮片使用完以后,需要更换的时候,须断电的电源来进行更换,以防不小心,按下的开关,造成不必要的人员事故。
5.在危险且易燃物品工作时,须配备一个以上的灭火器,防患未然。
做到安全第一、生产第二的原则。
6.在长时间30分钟后使用,应该停止休息20分钟以上,待冷却后方能进行作业。
防止在长期使用的过程中,温度过高,容易使易损坏、造成工伤事故。
7.在使用的时候,我们要按照使用规范和说明书去使用,定时的检查、维修、保证完好的情况下进行工作,减少事故的发生。
平磨磨削知识

我们“一般情况切削深度选择0.014左右”(材料淬火或非淬火钢、砂轮处于50-60宽直径450左右、工件速度10m/min,纵向进给量 20mm/st、工作台充满系数0.4、加工精度0.03、加工余量0.25) 二、回转式平面磨ap(端面磨削、单行程mm,工作台进给mm/r) 粗磨切削深度 影响因素:砂轮宽度、纵向进给量、工件速度、工件材料、砂轮直径、工作台充满系数。 最大极限深度,不准超过0.049*1.17*1.4=0.08(条件最为宽松时,指铸铁、砂轮窄32直径大600、工件速度低8m/min,纵向进给量比 小0.5、工作台充满系数低0.25) 最小极限深度,不得低于0.0039*0.7*0.71=0.002(条件最为苛刻时,指耐热铁、砂轮宽100直径小320、工件速度高30m/min,纵向进 给量比大0.8、工作台充满系数高1.0) 我们“一般情况切削深度选择0.021左右”(材料淬火或非淬火钢、砂轮处于50-60宽直径450左右、工件速度10m/min,纵向进给量 20mm/st、工作台充满系数高0.4、加工精度0.03、加工余量0.25),最合理的磨挺柱顶面粗磨计算为0.018,可以理解为粗磨余量0.6,在 30-35圈完成粗磨,粗磨旋转速度24r/min,单盘节拍实动时间应该为1.5分钟左右. 精磨切削深度 影响因素:砂轮宽度、纵向进给量、工件速度、工件材料、砂轮直径、工作台充满系数、加工精度及余量。 最大极限深度,不准超过0.067*2.5*1.75*1.6=0.47(条件最为宽松时,指铸铁、砂轮窄32直径大600、工件速度低5m/min,纵向进给 量小8m/min、工作台充满系数低0.2、加工精度0.08、加工余量0.7) 最小极限深度,不得低于0.0025*0.32*0.56*0.71=0.0003(条件最为苛刻时,指耐热铁、砂轮宽100直径小320、工件速度高40m/min, 纵向进给量大50、工作台充满系数高1.0、加工精度0.02、加工余量0.08) 我们“一般情况切削深度选择0.012左右”(材料淬火或非淬火钢、砂轮处于50-60宽直径450左右、工件速度15m/min,纵向进给量 20mm/st、工作台充满系数0.4、加工精度0.03、加工余量0.25),最合理的磨挺柱顶面计算为0.015,标准理解到加工余量0.4,在26圈完成 粗磨,粗磨旋转速度24r/min,单盘节拍实动时间应该为1分钟左右.
平面抛光路径
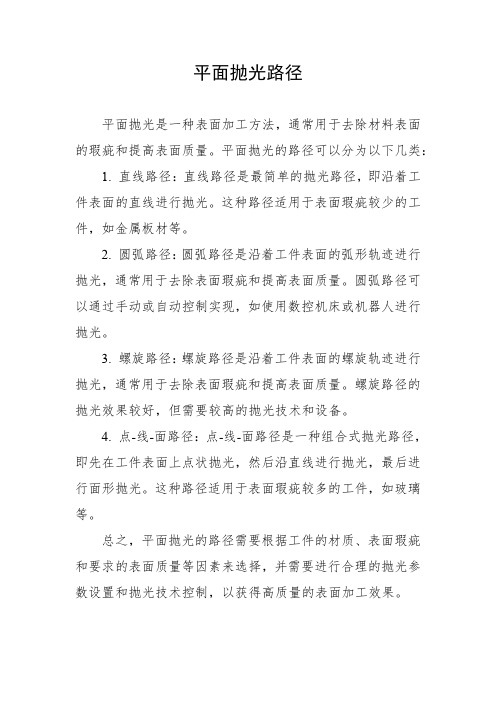
平面抛光路径
平面抛光是一种表面加工方法,通常用于去除材料表面的瑕疵和提高表面质量。
平面抛光的路径可以分为以下几类:
1. 直线路径:直线路径是最简单的抛光路径,即沿着工件表面的直线进行抛光。
这种路径适用于表面瑕疵较少的工件,如金属板材等。
2. 圆弧路径:圆弧路径是沿着工件表面的弧形轨迹进行抛光,通常用于去除表面瑕疵和提高表面质量。
圆弧路径可以通过手动或自动控制实现,如使用数控机床或机器人进行抛光。
3. 螺旋路径:螺旋路径是沿着工件表面的螺旋轨迹进行抛光,通常用于去除表面瑕疵和提高表面质量。
螺旋路径的抛光效果较好,但需要较高的抛光技术和设备。
4. 点-线-面路径:点-线-面路径是一种组合式抛光路径,即先在工件表面上点状抛光,然后沿直线进行抛光,最后进行面形抛光。
这种路径适用于表面瑕疵较多的工件,如玻璃等。
总之,平面抛光的路径需要根据工件的材质、表面瑕疵和要求的表面质量等因素来选择,并需要进行合理的抛光参数设置和抛光技术控制,以获得高质量的表面加工效果。
- 1、下载文档前请自行甄别文档内容的完整性,平台不提供额外的编辑、内容补充、找答案等附加服务。
- 2、"仅部分预览"的文档,不可在线预览部分如存在完整性等问题,可反馈申请退款(可完整预览的文档不适用该条件!)。
- 3、如文档侵犯您的权益,请联系客服反馈,我们会尽快为您处理(人工客服工作时间:9:00-18:30)。
简述磨削平面的方法
磨削平面是机械加工中常用的一种方法,它可以使工件表面光滑、平整、精度高。
下面将详细介绍磨削平面的方法。
一、准备工作
在进行磨削平面前,需要做好以下准备工作:
1.选择合适的磨削工具和砂轮。
根据被加工材料的硬度和形状,选择合适的砂轮和磨削工具。
2.调整机床。
调整机床的刀架高度和角度,使其与被加工材料表面垂直,并且旋转方向与材料运动方向相反。
3.清洁被加工材料表面。
清除被加工材料表面上的油污和灰尘,以保证磨削效果。
二、粗加工
1.粗选合适的砂轮。
根据被加工材料的硬度和形状,选择合适的粗砂轮,并将其安装到机床上。
2.调整刀架高度和角度。
将刀架调整到与被加工材料表面垂直,并且旋转方向与材料运动方向相反。
3.开始粗加工。
打开机床,将砂轮轻轻地接触到被加工材料表面,然后逐渐增加砂轮的压力,直到达到所需的粗磨效果。
4.检查粗加工效果。
停止机床,检查被加工材料表面的平整度和光滑度。
如果需要进一步精加工,则进行下一步操作。
三、精加工
1.选择合适的砂轮。
根据被加工材料的硬度和形状,选择合适的细砂轮,并将其安装到机床上。
2.调整刀架高度和角度。
将刀架调整到与被加工材料表面垂直,并且旋转方向与材料运动方向相反。
3.开始精加工。
打开机床,将细砂轮轻轻地接触到被加工材料表面,然后逐渐增加砂轮的压力,直到达到所需的精磨效果。
4.检查精加工效果。
停止机床,检查被加工材料表面的平整度和光滑度。
如果需要进一步提高平整度和光滑度,则进行下一步操作。
四、抛光
1.选择合适的抛光材料。
根据被加工材料的硬度和形状,选择合适的抛光材料,如毛毡轮、绒布轮等。
2.调整刀架高度和角度。
将刀架调整到与被加工材料表面垂直,并且旋转方向与材料运动方向相反。
3.开始抛光。
打开机床,将抛光材料轻轻地接触到被加工材料表面,然后逐渐增加压力,直到达到所需的抛光效果。
4.检查抛光效果。
停止机床,检查被加工材料表面的平整度和光滑度。
如果需要进一步提高平整度和光滑度,则进行下一步操作。
五、清洗
在完成磨削平面后,需要对被加工材料进行清洗。
清洗可以去除残留物和污垢,并保持被加工材料表面的平整度和光滑度。
以上就是磨削平面的详细方法。
在进行操作时需要注意安全事项,并根据不同情况选择合适的砂轮和磨削工具。
通过精细的操作可以获得高质量的磨削平面效果。