磨削加工中的磨削方式
简述磨削加工

磨削加工1. 简介磨削加工是一种常见的金属加工方法,通过使用磨料对工件表面进行摩擦磨损,以达到加工的目的。
它可以用于改善工件表面质量、调整尺寸精度和形状精度,以及去除杂质和残余应力等。
磨削加工广泛应用于机械制造、航空航天、汽车制造、模具制造等领域。
2. 磨削原理磨削加工是利用切削性能较差的材料(磨料)对工件进行切削,通过与工件表面的相对运动来实现切削作用。
其主要原理包括以下几个方面:•切削颗粒:磨料是由硬度较高的颗粒组成,通常为氧化铝、碳化硅等材料。
这些颗粒与工件表面摩擦产生很高的切向力,从而实现切削作用。
•切向力:当磨料与工件表面接触时,由于相对运动产生了摩擦力,使得磨料在切向方向上产生了切削力。
这种力对工件表面进行了切削作用。
•磨屑形成:在磨削过程中,磨料与工件表面的摩擦力和切向力使得工件表面的材料被切削下来,形成了磨屑。
这些磨屑会随着磨料的运动带走,并通过冷却液进行排出。
•热效应:由于切削过程中的摩擦力和切向力,会产生较高的温度。
为了避免温度过高引起工件变形或损坏,通常需要使用冷却液进行冷却。
3. 磨削方法根据加工目标和工件材料的不同,磨削加工可以采用多种方法。
下面介绍几种常见的磨削方法:3.1 平面磨削平面磨削是最基本、最常用的磨削方法之一。
它主要用于对平面工件进行加工,如平面零件、平底孔等。
平面磨削通常采用平面砂轮进行加工,通过对工件表面进行连续的摩擦来实现加工效果。
在平面磨削过程中,需要注意保持磨削面与砂轮之间的良好接触,以确保加工质量。
3.2 内圆磨削内圆磨削是用于加工孔内表面的一种方法。
它通常使用内圆砂轮进行加工,通过对孔内表面进行旋转磨削来实现加工效果。
在内圆磨削过程中,需要注意选择合适的砂轮尺寸和形状,并控制好加工参数,以确保加工质量。
3.3 外圆磨削外圆磨削是用于加工轴类零件外表面的一种方法。
它通常使用外圆砂轮进行加工,通过对零件外表面进行旋转磨削来实现加工效果。
在外圆磨削过程中,同样需要注意选择合适的砂轮尺寸和形状,并控制好加工参数。
磨削加工中的高效磨削技术

磨削加工中的高效磨削技术随着生产和科技的不断发展,机械加工业也在不断进步。
磨削加工作为机械加工过程中重要的环节,对于加工质量的影响非常大。
在过去,由于磨削加工效率低下,长时间的手工操作不仅浪费时间,而且也增加了劳动强度,同时精度也不易保证。
而随着高科技的到来和加工事业的不断进步,经过长时间的探索研究,高效磨削技术逐步发展起来,使磨削加工成为一种高度自动化的加工方式。
高效磨削技术主要采用的是高能量磨削方式。
它的基本原理是通过增加切削速度,提高磨削力,使其获得更高的能量密度,从而使磨削效率大幅提高。
在具体的应用中,高效磨削技术的出现在很大程度上解决了过去磨削加工中很难处理的问题。
一方面,高能量的磨削方式能够有效地降低磨削加工的时间,缩短了加工周期,降低了生产成本;另一方面,高效磨削技术能够改善加工表面的粗糙度,提高加工精度,保持加工品质的稳定性。
高效磨削技术的应用高效磨削技术的应用范围非常广泛,在各个行业都有着广泛的应用。
在汽车制造和航空航天领域,需要高精度、高强度、高刚度的轮毂,并且需要保证车轮在高速行驶中的安全。
在这种情况下,高效磨削技术展现了其独特的技术价值。
此外,在模具制造、机械零部件制造、船舶工业等领域中也广泛应用。
高效磨削技术也为未来高速磨削领域带来了无限的可能性。
高效磨削技术的应用除了有着广泛的范围外,还拥有许多的优势。
首先,高效磨削技术不仅可以节约加工时间,同时大大降低了生产成本。
其次,高效磨削技术能够帮助实现精度控制和质量控制,确保加工品质的稳定性。
再次,高效磨削技术还可以降低工人的劳动强度,提高了工人的工作效率和生产效率。
高效磨削技术的发展方向在未来的发展中,随着技术的不断提升,高效磨削技术将会得到更广泛的应用和发展。
随着生产工艺要求的日益提高,越来越多的厂商开始寻求解决方案来支持高质量、高效率的制造。
因此,随着技术的不断创新和开发,高效磨削技术未来的发展将会朝着更加高精度、更加自动化和更加环保等方面进行探索和发展。
磨削加工类型与运动
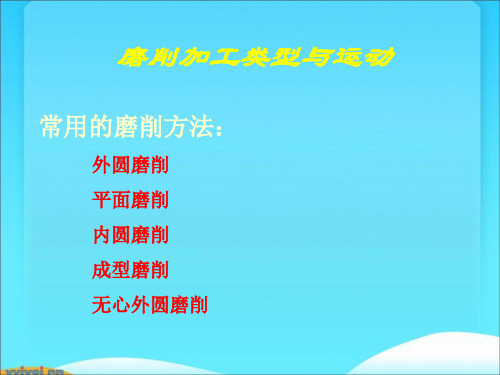
2、内圆磨削
磨内孔视频
主运动——砂轮旋转 进给运动——工件旋转作圆周进给,工件或砂轮纵向 往复移动和横向进给运动。
磨削加工类型与运动
常用的磨削方法:
外圆磨削 平面磨削 内圆磨削 成型磨削 无心外圆磨削
纵磨法磨外圆
周边磨削平面
磨削的主运动
vc do no m / s 1000
工件的切向进给运动
VW m / s 或m/min
工件轴向进给运动
fa mm/ r 或 mm/st
径向进给量
fr mm
1、外圆磨削
磨外圆视频
主运动——砂轮旋转
进给运动——工件旋转、移动
吃刀运动——砂轮、工件的相对径向移动
工艺范围:圆柱面、圆锥面、轴肩端面、球面、特殊形状回转面
1、外圆磨削
外圆磨削按不同的进给方向分为纵磨海参和横磨法。
纵磨法:磨外圆时,工件同时作圆周进给和沿轴向作纵 向进给,每单行程或往复行程终了,砂轮作周期的横向 进给。(磨削力小,散热条件好,运用广泛)
切入磨削:将工件放在托板和导轮之间,使磨削砂 轮横向切入进给,来磨削工件表面。导轮中心线需 偏转一个很小的角度(约定30′)使工件在微小轴向 摩擦力的作用下紧靠挡块,得到可靠的轴向定位。来自外圆无心磨削方法特点:
1)工件不需打中心孔,支承刚性好,磨削余量小而均 匀,生产率高,易实现自动化,适合成批生产; 2)加工精度高,其中尺寸精度可达IT5-IT6,形状精 度也比较好,表面粗糙度Ra1.25-0.16μm ; 3)不能加工断续表面,如花键、单键槽表面。 4)只能加工尺寸较小形状简单的零件。
磨削加工中的超硬磨削技术

磨削加工中的超硬磨削技术随着工业的不断发展,各种材料的使用愈加广泛,但是这些材料的硬度也越来越高,传统的磨削工艺难以满足现代工业对材料加工的需求。
因此,超硬磨削技术应运而生。
本篇文章就超硬磨削技术进行深度分析,探讨它在磨削加工中的应用与发展。
第一节:超硬磨削技术的概述超硬磨削技术是一种采用高速旋转的砂轮对高硬度材料进行加工的先进技术。
它能够高效地加工各种硬度材料,如高速钢、硬质合金、非金属材料等。
与传统的磨削工艺相比,超硬磨削工艺能够达到更高的加工精度及表面质量,同时还能降低对材料的损伤和变形。
超硬磨削技术的主要设备是CNC磨床,它能够高速旋转砂轮,并在磨削过程中自动调整刀具的位置和角度。
这样一来,超硬材料的加工就变得更为精准和高效。
除此之外,超硬磨削技术还应用了液压系统、自动化系统等多种先进技术,进一步提高了加工质量和效率。
第二节:超硬磨削技术的种类超硬磨削技术包括金刚石砂轮磨削、碳化硅砂轮磨削、立方氮化硼砂轮磨削等几种类型。
在这些磨削方式中,金刚石砂轮磨削是最常见的磨削方式之一,它具有高硬度、高耐磨性和高热稳定性等优点,可以用于加工各类热敏性材料和脆性材料。
碳化硅砂轮磨削和立方氮化硼砂轮磨削则适用于加工各种金属材料。
碳化硅砂轮磨削具有高硬度、高耐磨性、高温稳定性等特点,可以用于加工大型、高硬度的锻造铸件等;立方氮化硼砂轮磨削则由于其高硬度、高温稳定性和低摩擦系数等优点,成为加工难度较大的高精度测量仪器的理想工具。
第三节:超硬磨削技术的应用超硬磨削技术主要应用于机械制造、航空航天、汽车制造、工业钻探以及医疗器械等领域。
其中,在机械制造领域中,超硬磨削技术已经成为高精度加工的首选,并广泛应用于模具制造、齿轮加工、精密陶瓷等高端领域。
在航空航天领域中,超硬磨削技术则被广泛应用于加工高温合金等难加工材料,大大提高了零件加工的精度和质量。
第四节:超硬磨削技术的优势和未来发展方向超硬磨削技术具有高效、精确、高品质、低损伤等优点,在工业制造中是一项首屈一指的高端技术。
常见的3种磨削方法介绍
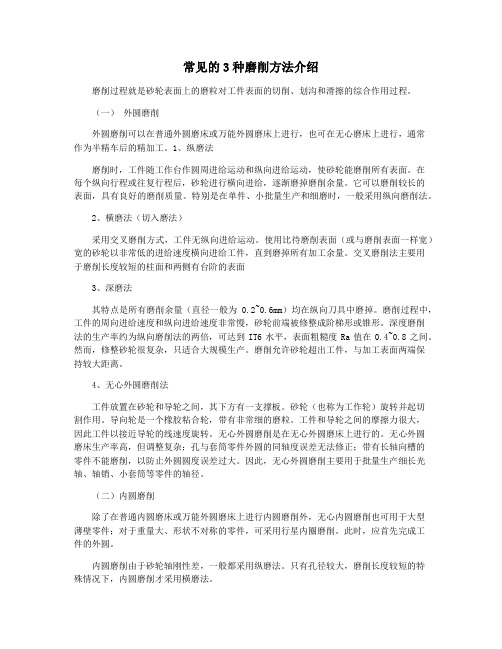
常见的3种磨削方法介绍磨削过程就是砂轮表面上的磨粒对工件表面的切削、划沟和滑擦的综合作用过程。
(一)外圆磨削外圆磨削可以在普通外圆磨床或万能外圆磨床上进行,也可在无心磨床上进行,通常作为半精车后的精加工。
1、纵磨法磨削时,工件随工作台作圆周进给运动和纵向进给运动,使砂轮能磨削所有表面。
在每个纵向行程或往复行程后,砂轮进行横向进给,逐渐磨掉磨削余量。
它可以磨削较长的表面,具有良好的磨削质量。
特别是在单件、小批量生产和细磨时,一般采用纵向磨削法。
2、横磨法(切入磨法)采用交叉磨削方式,工件无纵向进给运动。
使用比待磨削表面(或与磨削表面一样宽)宽的砂轮以非常低的进给速度横向进给工件,直到磨掉所有加工余量。
交叉磨削法主要用于磨削长度较短的柱面和两侧有台阶的表面3、深磨法其特点是所有磨削余量(直径一般为0.2~0.6mm)均在纵向刀具中磨掉。
磨削过程中,工件的周向进给速度和纵向进给速度非常慢,砂轮前端被修整成阶梯形或锥形。
深度磨削法的生产率约为纵向磨削法的两倍,可达到IT6水平,表面粗糙度Ra值在0.4~0.8之间。
然而,修整砂轮很复杂,只适合大规模生产。
磨削允许砂轮超出工件,与加工表面两端保持较大距离。
4、无心外圆磨削法工件放置在砂轮和导轮之间,其下方有一支撑板。
砂轮(也称为工作轮)旋转并起切割作用。
导向轮是一个橡胶粘合轮,带有非常细的磨粒。
工件和导轮之间的摩擦力很大,因此工件以接近导轮的线速度旋转。
无心外圆磨削是在无心外圆磨床上进行的。
无心外圆磨床生产率高,但调整复杂;孔与套筒零件外圆的同轴度误差无法修正;带有长轴向槽的零件不能磨削,以防止外圆圆度误差过大。
因此,无心外圆磨削主要用于批量生产细长光轴、轴销、小套筒等零件的轴径。
(二)内圆磨削除了在普通内圆磨床或万能外圆磨床上进行内圆磨削外,无心内圆磨削也可用于大型薄壁零件;对于重量大、形状不对称的零件,可采用行星内圈磨削。
此时,应首先完成工件的外圆。
内圆磨削由于砂轮轴刚性差,一般都采用纵磨法。
机械制造技术--磨削加工概述

机械制造技术–磨削加工概述简介磨削加工是机械制造中常用的一种加工方法。
通过磨削将工件的表面剥离,实现工件的加工精度提高和表面质量改善。
磨削加工通常用于硬度较高、形状复杂、精度要求较高的工件加工,如汽车发动机曲轴、齿轮、精密模具等。
磨削加工的原理磨削加工的原理是利用磨削颗粒的高速旋转和工件的间隙之间的相互作用力,使工件表面颗粒被剥离。
磨削加工主要应用砂轮作为磨削工具,通过磨削工具和工件之间的相对运动,实现对工件表面的切削。
砂轮的分类砂轮是磨削加工中常用的磨削工具,根据不同的磨削任务和工件材料,砂轮可以分为不同的类型,包括磨削砂轮、抛光砂轮、磨床砂轮等。
砂轮的选择不仅取决于工件的材料和形状,还取决于磨削的精度要求和表面质量要求。
砂轮的组成和结构砂轮通常由磨削颗粒、结合剂和孔隙三个部分组成。
砂轮的磨削颗粒可以是石英、氧化铝等硬质颗粒,结合剂可以是陶瓷、橡胶、金属等材料,孔隙可以提高砂轮的散热性能和剥离颗粒的能力。
砂轮的结构可以分为两种类型:单层结构和多层结构。
单层结构的砂轮由一层磨削颗粒和结合剂构成,适用于较粗糙的磨削。
多层结构的砂轮由多层磨削颗粒和结合剂构成,适用于较精细的磨削。
磨削加工的过程磨削加工通常包括粗磨、半精磨和精磨三个阶段。
在粗磨阶段,砂轮的颗粒与工件表面进行大范围的剥离,以消除工件的毛刺和大尺寸误差。
在半精磨阶段,砂轮的颗粒与工件表面进行中等范围的剥离,以改善工件的表面质量和减小尺寸误差。
在精磨阶段,砂轮的颗粒与工件表面进行微小范围的剥离,以获得工件的高精度和高表面质量。
磨削加工的优点和局限性磨削加工具有以下优点:1.可以实现高精度和高表面质量的加工。
2.可以加工复杂形状和高硬度的工件。
3.可以控制加工过程中的温度和应变。
然而,磨削加工也有一些局限性:1.加工效率低,加工速度慢。
2.磨削过程中产生的热量和应力可能会导致工件表面的损伤和变形。
3.砂轮的磨损较快,需要经常更换。
磨削加工的应用磨削加工广泛应用于各个行业,特别是需要高精度和高表面质量的领域。
第三节外圆磨床的磨削方法

第三节外圆磨床的磨削方法外圆磨床是一种用于对工件外圆进行磨削的专用机床。
它可以对各种形状和材质的工件进行加工,并能在精度要求较高的情况下实现高效率的加工。
外圆磨床的磨削方法主要包括平面磨削、对中磨削和深入磨削等。
平面磨削是外圆磨床最基本的磨削方法之一、它适用于对平面、圆弧、齿廓等工件进行磨削。
在平面磨削时,工件经过定心装置定位后,砂轮通过工作台和电机驱动系统旋转,并向工件表面施加磨料。
根据工件的形状和要求,可以选择不同形状和粒度的砂轮,以达到不同的磨削效果。
平面磨削具有操作简单、加工效率高的特点,广泛应用于各种工件的加工。
对中磨削是外圆磨床的另一种常用磨削方法。
它适用于对轴类工件进行加工,如轴瓦、滚珠轴承等。
在对中磨削中,工件通过工件夹持装置实现定位,并通过定心装置进行对中。
砂轮则通过工作台和电机驱动系统旋转,同时沿工件轴向进行移动,对工件进行磨削。
对中磨削可以提供高精度的加工,尤其适用于工件轴向精度要求高的场合。
深入磨削是外圆磨床的一种高级磨削方法。
它适用于对孔、槽等工件内壁进行加工。
深入磨削的主要原理是通过砂轮的旋转和工作台的升降来实现对工件内壁的磨削。
在深入磨削时,砂轮的选择和工艺参数设置非常重要。
需要根据工件的材质、尺寸和形状等因素来确定合适的砂轮类型和粒度,以及合适的砂轮进给量和磨削速度,以保证加工品质和效率。
除了上述基本的磨削方法外,外圆磨床还可以进行多道磨削、联合磨削和光学磨削等特殊磨削方法。
多道磨削是指通过多个砂轮的连续磨削来实现工件的加工。
联合磨削是指将磨削与切割、磨齿、磨位等工艺相结合,以提高磨削效率和加工精度。
光学磨削是指利用光学装置对工件进行检测和测量,以实时调整磨削参数,提高加工品质。
外圆磨床的磨削方法是根据工件的形状、材质和要求等因素来确定的。
不同的磨削方法有各自的特点和适用范围,可以根据具体情况选择合适的磨削方法。
通过合理选择磨削方法和优化磨削工艺参数,可以提高外圆磨床的加工精度和效率,满足各种工件的加工需求。
磨削的加工范围

磨削的加工范围磨削是一种常见的金属加工方法,通过磨削工具对工件进行摩擦切削,以达到精密加工的目的。
磨削工艺可以用于加工不同材料的工件,具有广泛的应用范围。
在磨削的加工范围中,首先要提到的是平面磨削。
平面磨削是指将工件表面磨削成平整的加工方法。
它适用于各种工件的平面加工,如平面零件、平面连接面等。
平面磨削可以采用手动磨削、半自动磨削和全自动磨削等不同方式进行。
除了平面磨削,还有圆柱磨削。
圆柱磨削是指对圆柱形工件进行加工的方法。
圆柱磨削广泛应用于轴类零件、套筒类零件等的加工过程中。
圆柱磨削可以分为外圆磨削和内圆磨削两种形式。
其中,外圆磨削是将工件外圆表面进行磨削,而内圆磨削则是将工件内圆表面进行磨削。
还有曲面磨削。
曲面磨削是指对工件曲面进行加工的方法。
曲面磨削可以分为平面曲面磨削和非平面曲面磨削。
平面曲面磨削是将工件表面进行平整磨削,使其达到规定的平面度和光洁度。
而非平面曲面磨削则是对工件的非平面曲面进行加工,常见的有球面磨削、锥面磨削等。
磨削还可以用于加工各种形状的齿轮。
齿轮磨削是一种特殊的磨削工艺,用于加工各种齿轮。
齿轮磨削可以分为外齿轮磨削和内齿轮磨削。
外齿轮磨削是将齿轮的外齿面进行磨削,内齿轮磨削则是将齿轮的内齿面进行磨削。
齿轮磨削可以提高齿轮的精度和光洁度,提高齿轮的传动效率和使用寿命。
磨削还可以用于加工各种形状的孔。
孔磨削是指对工件孔进行加工的方法。
孔磨削可以分为外孔磨削和内孔磨削。
外孔磨削是将工件外孔进行磨削,内孔磨削则是将工件内孔进行磨削。
孔磨削可以提高孔的精度和光洁度,提高工件的使用性能。
磨削的加工范围非常广泛,可以用于加工不同形状和材料的工件。
通过磨削工艺,可以获得更高的加工精度和表面质量,提高工件的使用性能。
磨削在机械制造、航空航天、汽车制造等行业中都有着重要的应用。
随着科技的发展,磨削技术也在不断创新和改进,将为各个行业的发展提供更多的支持。
坐标磨加工的磨削方式汇总
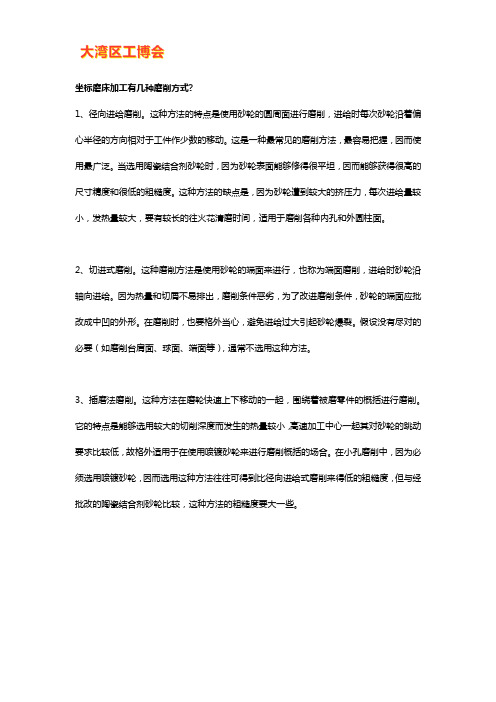
坐标磨床加工有几种磨削方式?
1、径向进给磨削。
这种方法的特点是使用砂轮的圆周面进行磨削,进给时每次砂轮沿着偏心半径的方向相对于工件作少数的移动。
这是一种最常见的磨削方法,最容易把握,因而使用最广泛。
当选用陶瓷结合剂砂轮时,因为砂轮表面能够修得很平坦,因而能够获得很高的尺寸精度和很低的粗糙度。
这种方法的缺点是,因为砂轮遭到较大的挤压力,每次进给量较小,发热量较大,要有较长的往火花清磨时间,适用于磨削各种内孔和外圆柱面。
2、切进式磨削。
这种磨削方法是使用砂轮的端面来进行,也称为端面磨削,进给时砂轮沿轴向进给。
因为热量和切屑不易排出,磨削条件恶劣,为了改进磨削条件,砂轮的端面应批改成中凹的外形。
在磨削时,也要格外当心,避免进给过大引起砂轮爆裂。
假设没有尽对的必要(如磨削台肩面、球面、端面等),通常不选用这种方法。
3、插磨法磨削。
这种方法在磨轮快速上下移动的一起,围绕着被磨零件的概括进行磨削。
它的特点是能够选用较大的切削深度而发生的热量较小,高速加工中心一起其对砂轮的跳动要求比较低,故格外适用于在使用喷镀砂轮来进行磨削概括的场合。
在小孔磨削中,因为必须选用喷镀砂轮,因而选用这种方法往往可得到比径向进给式磨削来得低的粗糙度,但与经批改的陶瓷结合剂砂轮比较,这种方法的粗糙度要大一些。
磨削加工中的磨削工艺优化

磨削加工中的磨削工艺优化磨削加工作为一种基本的金属加工工艺,在现代制造业中占据着重要的位置。
它可以对工件进行高精度、高表面质量的加工,能够满足很多产品的需求。
但是,磨削加工与其他加工方法相比,存在着耗能高、生产成本高、加工效率低等问题。
因此,如何优化磨削加工中的磨削工艺,提高加工效率和降低成本,一直是制造业工程师关注的问题。
一、磨削加工中的磨削机理磨削加工的基本原理是通过磨粒与工件之间的摩擦,将工件表面的金属加工掉。
一般磨削机的机械切削方式有两种:形状磨和旋转磨。
其中,形状磨是使用磨轮上凸起的磨粒与工件接触进行切削的;旋转磨是使用磨轮在工件表面滚动中切削的。
磨削加工的基本步骤是:磨粒与工件接触,磨粒将工件表面的金属切削掉,并产生摩擦和热量;磨屑与冷却液被排放出去。
这个步骤需要很高的磨粒和工件之间的接触力,磨轮的生产成本也较高。
因此,如何减少摩擦和热量,提高磨削效率是磨削加工中磨削工艺优化的关键。
二、磨削工艺优化的方法1.磨削润滑磨削润滑可以降低磨削加工中的热量和摩擦,提高加工效率。
磨削润滑主要有两种:油性润滑和水性润滑。
油性润滑主要是使用液体油和半固体膏状物来降低磨削加工过程中的温度和摩擦,增加工件表面的光滑度和表面质量。
水性润滑则主要是使用清洗水和冷却液来降低磨削加工的过程中的温度和摩擦系数。
不同的液体润滑剂的效果不同,需要根据具体的工件材质和磨削加工的要求选择。
2.磨削刀具优化磨削刀具的优化主要是针对磨削润滑剂的应用进行的。
通过选择合适的刀具设计,可以在不同润滑剂下获得最佳的磨削性能。
具体来说,磨削刀具的优化可以包括刀具自身的结构优化和润滑剂的选择搭配优化。
3.机械参数优化机械参数优化是通过调整机械参数来优化磨削加工的效率。
这些参数包括磨削轮的材料、粒度大小和硬度、加工转速、进给速率和切削深度等。
在优化机械参数时,需要根据具体的工件材料和不同的磨削要求来选择。
4.刀具磨损监测与诊断刀具磨损监测与诊断是一种有效的磨削工艺优化方法。
磨削的几种分类

磨削的几种分类磨削可以根据不同的标准进行分类,以下是几种常见的分类方式:1. 粗磨、半精磨、精磨和超精加工:这是根据磨削的精度进行的分类。
粗磨主要用于去除大量的余量,半精磨用于在粗磨之后进一步加工,精磨则用于在半精磨之后进一步减小余量并提高精度,超精加工则用于在精磨之后进一步提高表面光洁度。
2. 切入磨削、纵向磨削、缓进给磨削、无进给磨削、定压研磨、定量研磨:这是根据磨削的进给形式进行的分类。
切入磨削是刀具沿工件表面作连续的切线运动,纵向磨削则是刀具在工件表面沿纵向作连续的切线运动,缓进给磨削则是刀具以缓慢的速度沿工件表面作进给运动,无进给磨削则是刀具在工件表面作无进给的固定旋转运动,定压研磨和定量研磨则分别对应一定的压力和研磨量。
3. 砂带磨削、无心磨削、端面磨削、周边磨削、宽砂轮磨削、成型磨削、仿形磨削、振荡磨削、高速磨削、强力磨削、恒压力磨削、手动磨削、干磨削、湿磨削、研磨、珩磨等:这是根据磨削的形式进行的分类。
砂带磨削使用砂带作为刀具进行加工,无心磨削则是使用无心砂轮进行加工,端面磨削主要针对工件的端面进行加工,周边磨削则是对工件的周边进行加工,宽砂轮磨削则是使用宽砂轮对大面积的表面进行加工,成型磨削和仿形磨削则是根据工件的形状进行仿形加工,振荡磨削则是使用振荡砂轮进行加工,高速磨削则是在高速下进行加工,强力磨削则是在强力下进行加工,恒压力磨削则是保持恒定的压力进行加工,手动磨削则是手动操作进行加工,干磨削和湿磨削则是根据是否加水或其它液体进行加工,研磨和珩磨则是通过研具和珩轮进行加工。
4. 外圆磨削、内圆磨削、平面磨削和刃磨(齿轮磨削和螺纹磨削):这是根据加工表面进行的分类。
外圆磨削主要针对工件的外圆面进行加工,内圆磨削则是对工件的内圆面进行加工,平面磨削则是对工件的平面进行加工,刃磨则是针对工件的刃口进行加工。
磨削加工的纵磨法

磨削加工的纵磨法
磨削加工是一种制造过程,通过将工件放在磨削工具上,对其表面执行磨削操作来制造细微的几何形状,以及达到要求的表面质量。
其中,纵向磨削法是其中一种常见的磨削加工方法。
纵向磨削法又称为长轴磨削法,是一种将磨削工具纵向移动来削除工件材料的过程。
这个过程是通过将工件固定在工作台上,并将磨削工具夹在磨削头或轮中完成的。
在一些应用中,纵向磨削法利用旋转工作台,使其产生圆锥或锥形表面。
纵向磨削法非常适合大面积的磨削加工。
在此过程中,磨削头沿着工件的长度方向移动,以平均分布磨削量。
这种磨削方法非常适合需要处理较大面积工件,例如平板和管子等。
纵向磨削法有许多不同的应用。
它可以用于生产各种各样的工业产品,例如汽车零部件、飞机发动机和液压元件等。
此外,该技术还被广泛应用于生产高度精密仪器、零部件和器具等精密设备。
使用纵向磨削法进行磨削加工需要的是一些特定的工具和设备。
一个常见的磨削工具是磨削头或磨削轮。
其他设备,例如磨削机和数控机床,通常也用于执行这个过程。
在进行纵向磨削加工过程中,有几个因素需要被考虑。
这些因素包括工件材料、磨削头或轮的材料、磨削液、磨削运动的速度和方向等。
每个因素都必须被正确选择,以确保工件的质量得到保证。
总的来说,纵向磨削法是磨削加工的一个重要过程。
它是制造高精密和高质量产品的理想工艺,广泛应用于各个行业中。
如果正确使用和管理,这种方法将有效地提高产品的外观和性能,提高工艺效率,降低制造成本。
机械结构的磨削加工过程分析与优化

机械结构的磨削加工过程分析与优化引言:磨削加工是一种常见的工艺,在制造业中起着重要作用。
它通过研磨材料表面,改善精度和表面质量,以满足工件的几何尺寸和粗糙度要求。
本文将探讨机械结构的磨削加工过程的分析与优化,包括材料选择、磨削方式、磨削参数以及磨具的选择等方面。
一、材料选择在机械结构的磨削加工中,材料选择是最基础也是最重要的一步。
不同的工件材料对磨削加工过程会有不同的要求和特点。
常见的机械结构材料包括金属材料(如铁、铜、铝等)和非金属材料(如陶瓷、塑料等)。
对于金属材料,一般选择高硬度、高韧性的磨料,如刚玉和碳化硅等。
对于非金属材料,由于其磨削性能较差,常常采用金刚石或立方氮化硼等超硬材料进行磨削。
二、磨削方式机械结构的磨削加工可以分为平面磨削、外圆磨削和内圆磨削等多种方式。
平面磨削适用于工件表面的加工,外圆磨削适用于工件外圆的加工,内圆磨削适用于工件内孔的加工。
在选择磨削方式时,需要根据工件的几何形状和加工要求来确定。
同时,还需考虑磨削方式对工件的变形和残余应力的影响,以保证工件的几何精度和质量。
三、磨削参数磨削参数是指磨削过程中的工艺参数,包括磨削速度、进给量和磨削深度等。
磨削速度决定了磨削切削速度的快慢,进给量则决定了磨削速度的加工精度和表面质量。
磨削深度是指每次磨削时所去除的工件材料量,一般要由工件的加工要求和磨具的耐磨性来确定。
在确定磨削参数时,还需综合考虑材料的硬度、韧性和热导率等因素,以确保磨削过程的稳定性和效果。
四、磨具选择磨具是进行磨削加工时使用的工具,直接影响到磨削加工效果和工件的加工质量。
根据不同的磨削要求和工件材料,可以选择不同类型的磨具,如砂轮、砂带、砂纸等。
砂轮适用于对硬度较低的工件进行粗糙磨削,砂带适用于对长而狭窄的工件进行磨削,砂纸适用于对手工操作的小型工件进行磨削。
磨具的选择一般要考虑磨削效率、磨损情况和磨削质量等因素。
五、加工液的使用在机械结构的磨削加工过程中,常常需要使用加工液来冷却和润滑切削区域,以提高加工效率和工件加工质量。
浅析磨削加工技术
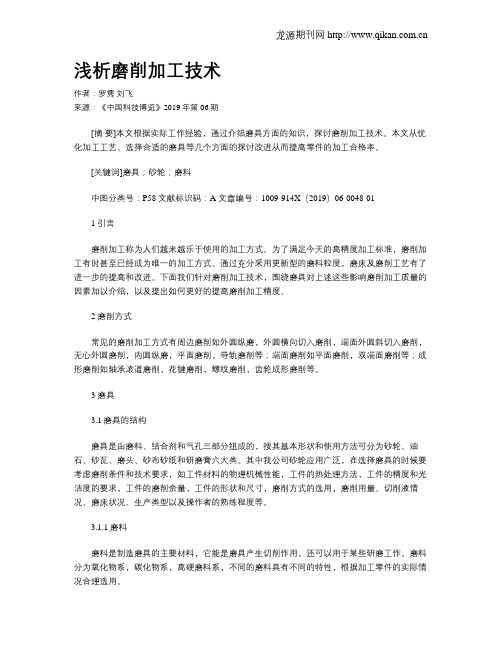
浅析磨削加工技术作者:罗隽刘飞来源:《中国科技博览》2019年第06期[摘要]本文根据实际工作经验,通过介绍磨具方面的知识,探讨磨削加工技术。
本文从优化加工工艺、选择合适的磨具等几个方面的探讨改进从而提高零件的加工合格率。
[关键词]磨具;砂轮;磨料中图分类号:P58 文献标识码:A 文章编号:1009-914X(2019)06-0048-011 引言磨削加工称为人们越来越乐于使用的加工方式。
为了满足今天的高精度加工标准,磨削加工有时甚至已经成为唯一的加工方式。
通过充分采用更新型的磨料粒度,磨床及磨削工艺有了进一步的提高和改进。
下面我们针对磨削加工技术,围绕磨具对上述这些影响磨削加工质量的因素加以介绍,以及提出如何更好的提高磨削加工精度。
2 磨削方式常见的磨削加工方式有周边磨削如外圆纵磨,外圆横向切入磨削,端面外圆斜切入磨削,无心外圆磨削,内圆纵磨,平面磨削,导轨磨削等;端面磨削如平面磨削,双端面磨削等;成形磨削如轴承滚道磨削,花键磨削,螺纹磨削,齿轮成形磨削等。
3 磨具3.1磨具的结构磨具是由磨料、结合剂和气孔三部分组成的,按其基本形状和使用方法可分为砂轮、油石、砂瓦、磨头、砂布砂纸和研磨膏六大类。
其中我公司砂轮应用广泛,在选择磨具的时候要考虑磨削条件和技术要求,如工件材料的物理机械性能,工件的热处理方法,工件的精度和光洁度的要求,工件的磨削余量,工件的形状和尺寸,磨削方式的选用,磨削用量、切削液情况、磨床状况、生产类型以及操作者的熟练程度等。
3.1.1磨料磨料是制造磨具的主要材料,它能是磨具产生切削作用,还可以用于某些研磨工作。
磨料分为氧化物系,碳化物系,高硬磨料系,不同的磨料具有不同的特性,根据加工零件的实际情况合理选用。
3.1.2粒度粒度是指磨粒的尺寸。
用筛选法可获得磨粒,粒度号是用一英寸长度上有多少个孔眼的筛网来确定的。
磨料的粒度与加工光洁度、成型精度、生产效率、磨削方法及被加工材质等诸多因素有关。
磨削加工的方法范文

磨削加工的方法范文磨削加工是一种常见的金属加工方法,用于加工高精度、高光洁度的零件表面。
下面将介绍几种常见的磨削加工方法。
1.平面磨削:平面磨削是最基本的磨削方法之一,适用于平面、平行度要求高的零件。
平面磨削的主要设备是平面磨床,通过砂轮对工件表面进行切削,以达到所需的平整度和精度。
2.内外圆磨削:内外圆磨削主要用于加工圆形零件,如轴、套等工件。
内圆磨削通常使用的设备是内圆磨床,通过砂轮对工件内径进行切削,以达到所需的圆度和精度。
外圆磨削通常使用的设备是外圆磨床,通过砂轮对工件外径进行切削。
3.面磨削:面磨削主要用于加工平面、倾斜面等具有特殊形状的零件。
面磨削的设备有平面磨床、中心磨床等,通过不同的磨削方式和工艺参数,可以实现不同形状的零件加工。
4.锥度磨削:锥度磨削主要用于加工锥形零件,如圆锥孔、锥形阀座等。
锥度磨削的设备有内圆磨床、外圆磨床等,通过不同的磨削方式和工艺参数,可以实现不同锥度的零件加工。
5.轮廓磨削:轮廓磨削适用于加工具有复杂曲线形状的零件,如齿轮、凸轮等。
轮廓磨削的设备有轮廓磨床、数控磨床等,通过砂轮和工件相对运动的轨迹,可以实现复杂曲线形状的零件加工。
6.内外表面磨削:内外表面磨削是对工件内、外表面进行磨削处理,以提高工件的光洁度和平整度。
内外表面磨削的设备有内圆磨床、外圆磨床等,通过磨削的过程,可以去除工件表面的凹凸不平和毛刺,得到光洁、平整的表面。
7.光学磨削:光学磨削是一种精密磨削方法,用于加工高精度和高光洁度要求的光学元件,如透镜、反射镜等。
光学磨削需要使用高精度的磨削设备和砂轮,以及细腻的研磨液,通过不同的磨削工艺,可以实现高质量的光学元件加工。
总之,磨削加工方法种类繁多,适用于不同形状、尺寸、材质的零件加工。
各种磨削加工方法都有其特点和适用范围,合理选择适合的磨削方法和工艺参数,可以提高零件的加工质量和生产效率。
磨盘的不同磨削方式及其应用
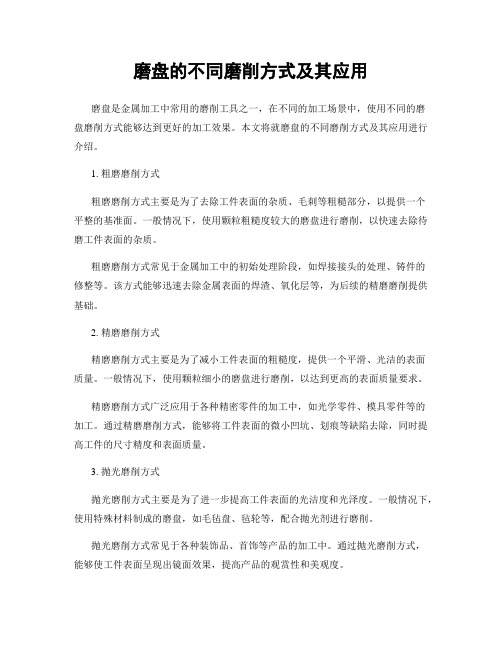
磨盘的不同磨削方式及其应用磨盘是金属加工中常用的磨削工具之一,在不同的加工场景中,使用不同的磨盘磨削方式能够达到更好的加工效果。
本文将就磨盘的不同磨削方式及其应用进行介绍。
1. 粗磨磨削方式粗磨磨削方式主要是为了去除工件表面的杂质、毛刺等粗糙部分,以提供一个平整的基准面。
一般情况下,使用颗粒粗糙度较大的磨盘进行磨削,以快速去除待磨工件表面的杂质。
粗磨磨削方式常见于金属加工中的初始处理阶段,如焊接接头的处理、铸件的修整等。
该方式能够迅速去除金属表面的焊渣、氧化层等,为后续的精磨磨削提供基础。
2. 精磨磨削方式精磨磨削方式主要是为了减小工件表面的粗糙度,提供一个平滑、光洁的表面质量。
一般情况下,使用颗粒细小的磨盘进行磨削,以达到更高的表面质量要求。
精磨磨削方式广泛应用于各种精密零件的加工中,如光学零件、模具零件等的加工。
通过精磨磨削方式,能够将工件表面的微小凹坑、划痕等缺陷去除,同时提高工件的尺寸精度和表面质量。
3. 抛光磨削方式抛光磨削方式主要是为了进一步提高工件表面的光洁度和光泽度。
一般情况下,使用特殊材料制成的磨盘,如毛毡盘、毡轮等,配合抛光剂进行磨削。
抛光磨削方式常见于各种装饰品、首饰等产品的加工中。
通过抛光磨削方式,能够使工件表面呈现出镜面效果,提高产品的观赏性和美观度。
4. 切割磨削方式切割磨削方式主要是为了通过磨削将工件切割成所需的形状和尺寸。
一般情况下,使用带有切割刃的磨盘进行磨削。
切割磨削方式常见于金属加工中的切割操作,如管材、板材等的切割。
通过切割磨削方式,能够实现高效、精确的切割操作,并具有较好的切割平整度和切割质量。
总结起来,磨盘的不同磨削方式在金属加工中起到了举足轻重的作用。
粗磨磨削方式去除工件粗糙部分,精磨磨削方式提供更高的表面质量,抛光磨削方式提升光洁度和光泽度,切割磨削方式实现快速、精确的切割操作。
这些磨削方式能够满足不同加工场景的需求,并在金属加工领域发挥重要作用。
曲面磨床加工原理

曲面磨床加工原理
曲面磨床是一种用于加工曲面的机床。
它能够实现高精度的加工,并可用于加工各种形状的工件,如球体、椭球体、锥面、滑动轴面、螺旋面等。
曲面磨床的加工原理主要包括以下几个方面:
1. 磨削方式
曲面磨床的磨削方式主要有两种:一种是逐点磨削,即每次只磨削工件上的一个点;另一种是全面磨削,即在工件表面进行全面磨削。
逐点磨削适用于形状较为复杂的工件,而全面磨削则适用于形状相对简单的工件。
2. 磨削刀具
曲面磨床的磨削刀具主要分为两种:一种是固定磨轮,另一种是可移动磨轮。
固定磨轮适用于加工形状相对简单的工件,而可移动磨轮则适用于加工形状较为复杂的工件。
在使用可移动磨轮时,操作人员需要根据工件形状不断调整磨轮的位置,以确保磨削的精度和质量。
3. 磨削参数
曲面磨床的磨削参数包括磨削速度、进给速度、磨削深度等。
这些参
数的设置直接影响到磨削质量和效率。
在设定磨削参数时,需要根据具体工件的形状、材料和要求来进行调整,以达到最佳的磨削效果。
4. 加工控制
曲面磨床的加工控制采用数控技术,可以实现高精度的加工。
在加工过程中,可以通过数控系统对磨削参数进行实时监测和调整,使磨削精度更高、效率更高,同时还可以减少因人为因素导致的误差和不良品率。
总之,曲面磨床的加工原理包括磨削方式、磨削刀具、磨削参数和加工控制。
这些方面的优化和改进可以使曲面磨床的加工效率和精度更高,为机械加工行业的发展提供更好的技术支持。
圆周磨削和端面磨削的特点

圆周磨削和端面磨削的特点圆周磨削和端面磨削是两种常见的磨削方式,它们在加工过程中有各自的特点和应用范围。
下面将对这两种磨削方式进行详细的解释和比较。
一、圆周磨削的特点圆周磨削是将砂轮沿工件的周边进行磨削的一种加工方法。
其特点如下:1.适用范围广:圆周磨削适用于各种形状的工件,包括圆柱形、圆锥形、曲面等。
只要工件具有轴对称性或旋转对称性,都可以使用圆周磨削进行加工。
2.高精度加工:圆周磨削可以实现较高的精度要求,尤其适用于对工件直径、圆度、圆柱度等要求较高的加工。
由于砂轮在加工过程中沿工件周边运动,因此能够保持较好的圆度和尺寸稳定性。
3.高效率加工:圆周磨削具有较高的加工效率,能够快速去除工件表面的金属材料,提高加工效率。
同时,由于砂轮的边缘有一定的弧度,因此可以同时进行粗磨和精磨,减少了工序,提高了加工效率。
4.表面质量好:圆周磨削能够获得较好的表面质量,可以实现工件表面的光洁度要求。
砂轮在加工过程中的高速旋转和前进运动,可以将工件表面的凹凸不平和毛刺去除,得到平整、光滑的表面。
5.易于自动化加工:圆周磨削可以通过自动化设备实现加工过程的自动化,提高生产效率和加工精度。
自动化设备可以控制砂轮的进给速度、磨削力和加工路径,实现精确的加工控制。
二、端面磨削的特点端面磨削是将砂轮沿工件的端面进行磨削的一种加工方法。
其特点如下:1.适用范围广:端面磨削适用于各种形状的工件,包括平面、圆柱形、圆锥形等。
只要工件具有平面或端面,都可以使用端面磨削进行加工。
2.高精度加工:端面磨削可以实现较高的平面度和垂直度要求,尤其适用于对工件平面度和垂直度要求较高的加工。
由于砂轮在加工过程中沿工件端面运动,因此能够保持较好的平面度和垂直度稳定性。
3.高效率加工:端面磨削具有较高的加工效率,能够快速去除工件端面的金属材料,提高加工效率。
同时,由于砂轮的边缘有一定的直径,因此可以同时进行粗磨和精磨,减少了工序,提高了加工效率。
- 1、下载文档前请自行甄别文档内容的完整性,平台不提供额外的编辑、内容补充、找答案等附加服务。
- 2、"仅部分预览"的文档,不可在线预览部分如存在完整性等问题,可反馈申请退款(可完整预览的文档不适用该条件!)。
- 3、如文档侵犯您的权益,请联系客服反馈,我们会尽快为您处理(人工客服工作时间:9:00-18:30)。
磨削加工中的磨削方式
磨削加工是一种精密的金属加工方法,不仅可以用于加工金属
材料,还可以用于加工陶瓷、玻璃等非金属材料。
它的基本原理
是在切削工具与工件之间施加外力,并且在介质中进行磨磨擦削,以达到加工的目的。
磨削加工中的磨削方式有很多种,下面将对
其进行一一介绍。
1. 平面磨削
平面磨削是一种磨削工艺,主要用于加工平面及其上的孔和槽。
这种加工方式通过旋转磨削轮,使其与工件表面接触,施加相应
的压力和剪切力来进行磨削。
平面磨削的加工精度高,工件表面
质量好,适用于加工超精密配件。
2. 内圆磨削
内圆磨削是一种在工作件内部进行磨削的加工方式,主要用于
加工内径大小不同的圆柱体。
这种加工方式的主要设备是内圆磨床,通过不断旋转工作件和磨削轮,结合适当的压力、速度等参数,来进行磨削加工。
3. 外圆磨削
外圆磨削是一种在工作件外部进行磨削的加工方式,主要用于加工外径大小不同的圆柱体。
这种加工方式的主要设备是外圆磨床,通过不断旋转工作件和磨削轮,结合适当的压力、速度等参数,来进行磨削加工。
4. 中心磨削
中心磨削是一种在两个中心点之间进行磨削加工的方式,主要用于加工圆锥体、圆柱锥体等形状的工件。
这种加工方式的主要设备是中心磨床,在加工过程中,需要较高的精度控制及对磨削力的稳定性要求。
5. 轮廓磨削
轮廓磨削是一种根据工件轮廓进行磨削的加工方式,主要用于加工各种不规则形状的工件。
这种加工方式的主要设备是数控磨
床,通过对工件进行高精度的三维扫描和轮廓学习,来得到工件的三维形状。
随后,根据得到的轮廓数据进行加工。
6. 微型磨削
微型磨削是一种在微米尺度下进行磨削的加工方式,主要用于加工高精度、超细的微件。
这种加工方式的设备应具有高精度、高速度、低摩擦等特点,常用于制造高端光学元件、半导体芯片等高端应用领域。
总之,磨削加工中的磨削方式有很多种,不同的加工方式适用于不同的工件加工需求,需要精确控制加工参数,以保证加工效果。
随着技术的不断进步,相信未来还会涌现更多更精密的磨削加工方式,为各行各业的高精度加工需求提供更多的选择。