挤出机螺杆的几个重要几何参数
挤出机螺杆参数及影响
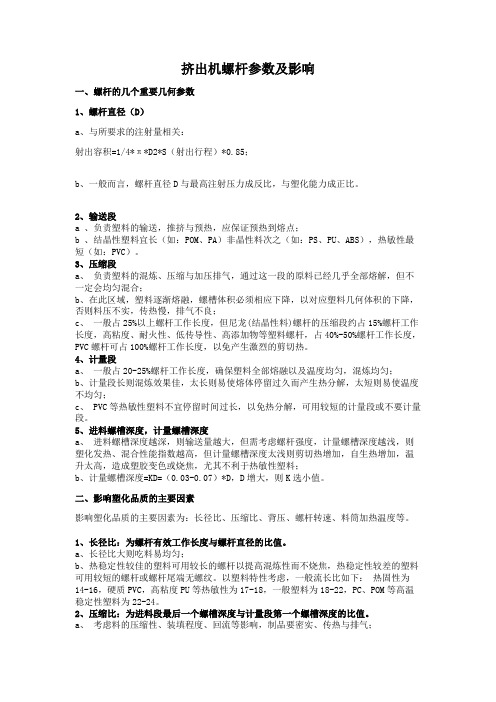
挤出机螺杆参数及影响一、螺杆的几个重要几何参数1、螺杆直径(D)a、与所要求的注射量相关:射出容积=1/4*π*D2*S(射出行程)*0.85;b、一般而言,螺杆直径D与最高注射压力成反比,与塑化能力成正比。
2、输送段a 、负责塑料的输送,推挤与预热,应保证预热到熔点;b 、结晶性塑料宜长(如:POM、PA)非晶性料次之(如:PS、PU、ABS),热敏性最短(如:PVC)。
3、压缩段a、负责塑料的混炼、压缩与加压排气,通过这一段的原料已经几乎全部熔解,但不一定会均匀混合;b、在此区域,塑料逐渐熔融,螺槽体积必须相应下降,以对应塑料几何体积的下降,否则料压不实,传热慢,排气不良;c、一般占25%以上螺杆工作长度,但尼龙(结晶性料)螺杆的压缩段约占15%螺杆工作长度,高粘度、耐火性、低传导性、高添加物等塑料螺杆,占40%-50%螺杆工作长度,PVC螺杆可占100%螺杆工作长度,以免产生激烈的剪切热。
4、计量段a、一般占20-25%螺杆工作长度,确保塑料全部熔融以及温度均匀,混炼均匀;b、计量段长则混炼效果佳,太长则易使熔体停留过久而产生热分解,太短则易使温度不均匀;c、 PVC等热敏性塑料不宜停留时间过长,以免热分解,可用较短的计量段或不要计量段。
5、进料螺槽深度,计量螺槽深度a、进料螺槽深度越深,则输送量越大,但需考虑螺杆强度,计量螺槽深度越浅,则塑化发热、混合性能指数越高,但计量螺槽深度太浅则剪切热增加,自生热增加,温升太高,造成塑胶变色或烧焦,尤其不利于热敏性塑料;b、计量螺槽深度=KD=(0.03-0.07)*D,D增大,则K选小值。
二、影响塑化品质的主要因素影响塑化品质的主要因素为:长径比、压缩比、背压、螺杆转速、料筒加热温度等。
1、长径比:为螺杆有效工作长度与螺杆直径的比值。
a、长径比大则吃料易均匀;b、热稳定性较佳的塑料可用较长的螺杆以提高混炼性而不烧焦,热稳定性较差的塑料可用较短的螺杆或螺杆尾端无螺纹。
挤出机螺杆基础知识讲解

挤出机螺杆基础知识讲解
1、基础知识挤出机螺杆是由外螺纹和圆柱形构成的。
丝杆沿轴线有长孔,可通冷却循环水。
丝杆的尾端装在止推轴承内,防止挤橡时造成反冲力把丝杆发布。
挤出机螺杆的直徑比整体机身的蒸汽保温管公称直径稍小,即丝杆的直徑与蒸汽保温管内表层要有空隙,其空隙一般调节在丝杆直徑的0.002~0.004倍。
空隙过小会导致丝杆“扫膛”,造成损坏,乃至造成卡住丝杆的状况;空隙很大塑胶粒流回危害挤压量,生产率低,还会继续危害产品质量。
2、挤出机螺杆的外螺纹特点外螺纹深层与机器设备生产量有立即关联,外螺纹深层大,在一定的压力下,挤压塑胶粒多。
但塑胶粒熔融艰难,丝杆抗压强度也差。
丝杆外螺纹深层一般调节在丝杆直徑的0.18~0.25倍。
外螺纹的推动面应当垂直平分丝杆的中心线,而推动面的相对性面应当有一定的倾斜度。
邻近外螺纹的径向间距称之为牙距,塑胶挤出机螺杆一般为定距不一深多头外螺纹丝杆。
3、丝杆的长径比丝杆的长径比是丝杆的长短L与丝杆的直徑D比例。
丝杆长径比大,也就是丝杆工作中一部分长,塑胶粒熔融好,混和匀称,塑胶粒受压力很大,产品品质好。
但丝杆长易造成塑胶粒脆化,丝杆生产加工艰难,提升挤压输出功率。
用以热上料挤橡机的丝杆一般取长径比4~6倍,用以冷上料挤橡机的丝杆一般取长径比8~12倍。
挤出机螺杆型号及尺寸规格表及挤出量
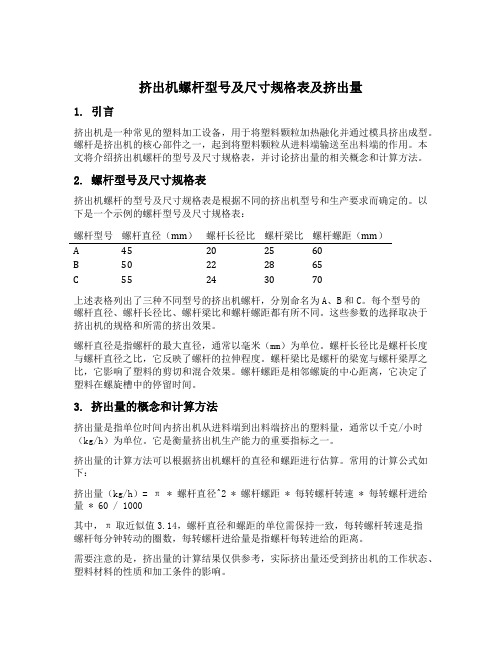
挤出机螺杆型号及尺寸规格表及挤出量1. 引言挤出机是一种常见的塑料加工设备,用于将塑料颗粒加热融化并通过模具挤出成型。
螺杆是挤出机的核心部件之一,起到将塑料颗粒从进料端输送至出料端的作用。
本文将介绍挤出机螺杆的型号及尺寸规格表,并讨论挤出量的相关概念和计算方法。
2. 螺杆型号及尺寸规格表挤出机螺杆的型号及尺寸规格表是根据不同的挤出机型号和生产要求而确定的。
以下是一个示例的螺杆型号及尺寸规格表:螺杆型号螺杆直径(mm)螺杆长径比螺杆梁比螺杆螺距(mm)A 45 20 25 60B 50 22 28 65C 55 24 30 70上述表格列出了三种不同型号的挤出机螺杆,分别命名为A、B和C。
每个型号的螺杆直径、螺杆长径比、螺杆梁比和螺杆螺距都有所不同。
这些参数的选择取决于挤出机的规格和所需的挤出效果。
螺杆直径是指螺杆的最大直径,通常以毫米(mm)为单位。
螺杆长径比是螺杆长度与螺杆直径之比,它反映了螺杆的拉伸程度。
螺杆梁比是螺杆的梁宽与螺杆梁厚之比,它影响了塑料的剪切和混合效果。
螺杆螺距是相邻螺旋的中心距离,它决定了塑料在螺旋槽中的停留时间。
3. 挤出量的概念和计算方法挤出量是指单位时间内挤出机从进料端到出料端挤出的塑料量,通常以千克/小时(kg/h)为单位。
它是衡量挤出机生产能力的重要指标之一。
挤出量的计算方法可以根据挤出机螺杆的直径和螺距进行估算。
常用的计算公式如下:挤出量(kg/h)= π * 螺杆直径^2 * 螺杆螺距 * 每转螺杆转速 * 每转螺杆进给量 * 60 / 1000其中,π取近似值3.14,螺杆直径和螺距的单位需保持一致,每转螺杆转速是指螺杆每分钟转动的圈数,每转螺杆进给量是指螺杆每转进给的距离。
需要注意的是,挤出量的计算结果仅供参考,实际挤出量还受到挤出机的工作状态、塑料材料的性质和加工条件的影响。
4. 结论本文介绍了挤出机螺杆型号及尺寸规格表以及挤出量的相关概念和计算方法。
螺杆的型号和尺寸规格表是根据不同的挤出机型号和生产要求而确定的,螺杆直径、螺杆长径比、螺杆梁比和螺杆螺距的选择取决于挤出机的规格和所需的挤出效果。
sj高效单螺杆挤出机技术参数

sj高效单螺杆挤出机技术参数SJ高效单螺杆挤出机是一种广泛应用于塑料加工领域的设备,具有高效、稳定、可靠的特点。
它通过将塑料材料加热融化后,通过螺杆的旋转推进,将熔融的塑料挤出成型。
下面将从技术参数的角度来介绍SJ高效单螺杆挤出机。
1. 机器型号:SJ高效单螺杆挤出机的机器型号通常以SJ开头,后面跟着一组数字,表示机器的规格和型号。
不同型号的机器适用于不同种类和规格的塑料材料挤出加工。
2. 螺杆直径:螺杆直径是指螺杆的最大外径,通常以毫米(mm)为单位。
螺杆直径的大小影响着挤出机的产能和挤出效果。
一般来说,螺杆直径越大,挤出机的产能越高,但也会增加设备的投资成本。
3. 长径比:长径比是指螺杆的有效长度与其直径之比。
它是衡量挤出机螺杆结构合理与否的重要参数。
长径比合理的螺杆可以提高塑料的熔融均匀性,减少材料的变质和气泡产生。
4. 螺杆转速:螺杆转速是指螺杆每分钟旋转的圈数。
螺杆转速的大小直接影响着挤出机的产能和挤出压力。
适当调整螺杆转速可以使塑料熔融均匀,提高挤出效果。
5. 电机功率:电机功率是指挤出机所使用的电机的功率大小。
电机功率的大小与挤出机的产能和能耗密切相关。
一般来说,电机功率越大,挤出机的产能越高,但也会增加能耗。
6. 最大挤出量:最大挤出量是指挤出机在单位时间内能够挤出的最大塑料量。
最大挤出量与螺杆直径、长度、螺杆转速等因素密切相关。
提高最大挤出量可以提高挤出机的产能。
7. 加热功率:加热功率是指挤出机所需要的加热功率大小。
加热功率的大小与挤出机的加热系统有关,通常用来提供螺杆和机筒的加热能量,使塑料材料能够被加热熔融。
8. 控制系统:SJ高效单螺杆挤出机通常配备先进的控制系统,用于控制挤出机的运行状态和参数。
控制系统可以实现自动控制、数据采集、故障诊断等功能,提高设备的稳定性和生产效率。
9. 自动送料系统:自动送料系统是SJ高效单螺杆挤出机的一个重要组成部分,用于将塑料原料自动送入挤出机进行加工。
挤塑机螺杆的的基本参数

挤塑机螺杆的的基本参数1、螺杆直径Ds 螺杆直径即螺纹的外径,挤塑机的生产能力(挤塑量)近似与螺杆直径的平方成正比,在其它条件相同时,螺杆直径少许增大,将引起挤出量的显著增加,其影响甚至比螺杆转数的提高对挤出量的影响还大。
故常用螺杆直径来表征挤塑机规格大小的技术参数。
2、螺杆长径比L/Ds 螺杆工作部分长度L与螺杆直径Ds之比称为长径比,在其它条件一定时(如螺杆直径),增大长径比就意味着增加螺杆的长度。
L/Ds值大,温度分布合理有利于塑料的混合和塑化,此时塑料在机筒中受热的时间也较长,塑料的塑化将充分、更均匀。
从而提高机塑质量。
如果在塑化质量要求不变的前提下,长径比增大后,螺杆的转速可提高,从而增加了塑料的挤出量。
但是,选择过大的长径比,螺杆消耗的功率将相应增大,而且螺杆和机筒的加工和装配鸡难度增加;螺杆弯曲的可能性也会增加,将会引起螺杆与机筒内壁的刮磨,降低使用寿命。
另外,对于热敏性塑料,过大的长径比因停留时间长而热分解,影响塑料的塑化和挤出质量。
因此,在充分利用长径比加大后的优点,选取时要根据加工塑料的物理性能和对产品的挤塑质量要求而定。
3、压缩比ε亦称为螺杆的几何压缩比,是螺杆加料段第一个螺槽容积与均化段最后一个螺槽容积之比。
它是由塑料的物理压缩比――即制品的密度与进料的表现密度之比来决定的。
使挤塑机压缩比较大,目的是为了使颗粒状塑料能充分塑化、压实。
加工塑料的种类不同时,压缩比的选择也应不同。
按压缩比来分,螺杆的型式可分为三种:等距不等深、等深不等距、不等深不等距。
其中等距不等深是最常用的一种,这种螺杆加工容易,塑料与机筒的接触面积大,传热效果好。
信息来源:东莞华鸿塑料机械厂。
双螺杆挤出机比较常见基本参数了解多少
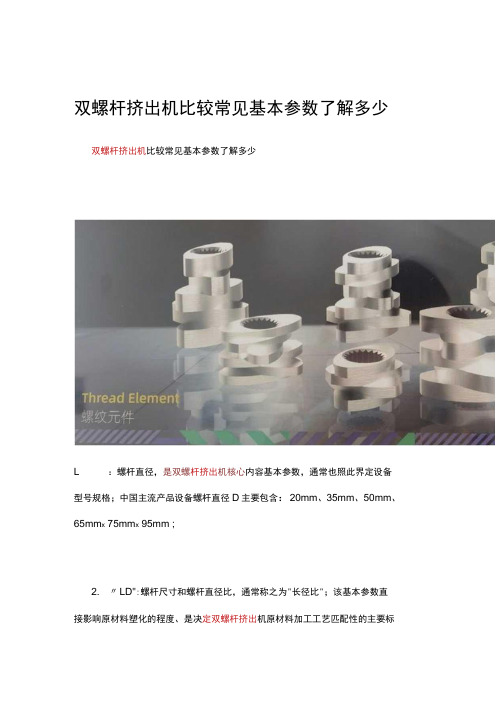
双螺杆挤出机比较常见基本参数了解多少双螺杆挤出机比较常见基本参数了解多少
L :螺杆直径,是双螺杆挤出机核心内容基本参数,通常也照此界定设备型号规格;中国主流产品设备螺杆直径D主要包含:20mm、35mm、50mm、65mm x 75mm x 95mm ;
2. 〃LD":螺杆尺寸和螺杆直径比,通常称之为"长径比";该基本参数直
接影响原材料塑化的程度、是决定双螺杆挤出机原材料加工工艺匹配性的主要标
识。
通常高聚物的改性塑料作业,长径比D/L在28〜48间,特殊工艺要L/D可以实现68或者更大;
3. "H〃:螺槽深度,可反映螺杆内原材料填充空间大小;
4. :主机转动速度,一般是指最大值,通常反映双螺杆挤出设备使用性能,近些年来在国际上双螺杆挤出机发展趋向是高转速,中国常规厂家主要是以600rpm转动速度的双螺杆挤出机为主导;
5. "P〃:电机功率及加热功率,通常反映双螺杆挤出机的能耗状况。
单螺杆挤出机的规格型号与基本参数

单螺杆挤出机的规格型号与基本参数一、规格型号1.挤出量:挤出量是衡量单螺杆挤出机生产能力的重要指标,通常以千克/小时来表示。
挤出量的大小取决于单螺杆挤出机的规格型号和生产过程中的要求。
2. 螺杆直径:螺杆直径是指单螺杆挤出机螺杆的直径大小,通常以毫米(mm)来表示。
螺杆直径的选择需根据所处理物料的性质和生产要求来确定。
3.螺杆长径比:螺杆长径比是指螺杆长度与螺杆直径的比值。
螺杆的长径比会影响到挤出机的性能和挤出物料的质量。
在实际生产中,根据不同的物料和生产要求,选择合适的长径比是十分重要的。
二、基本参数除了规格型号外,单螺杆挤出机的基本参数也是评估其性能和适用性的重要指标。
以下是一些常见的基本参数:1.驱动功率:驱动功率是指单螺杆挤出机所需的功率大小,通常以千瓦(kW)来表示。
驱动功率的大小与挤出机的规格型号、生产能力和物料粘度等因素有关。
2.加热功率:加热功率是指单螺杆挤出机加热装置所需的功率大小,通常以千瓦(kW)来表示。
加热功率的大小取决于加热方式和生产要求等因素。
3.温控系统:单螺杆挤出机通常配备有温控系统,用于控制挤出机的温度。
温控系统通常由温度控制器和加热装置等组成,以确保挤出过程中的温度稳定性。
4.单螺杆转速:单螺杆挤出机的螺杆转速是指螺杆每分钟旋转的圈数,通常以转/分钟或转/秒来表示。
螺杆转速的大小与物料的熔融温度、挤出量和挤出速度等因素有关。
5.模具尺寸:单螺杆挤出机的模具尺寸通常由模具的宽度和高度来表示,用于指导挤出过程中塑料物料的形状和尺寸。
6.机器重量和外形尺寸:机器重量和外形尺寸是指单螺杆挤出机的重量和外部尺寸,用于评估设备的可移动性和适用范围。
这些规格型号和基本参数是评估单螺杆挤出机性能和适用性的重要指标,在选择和使用时需要根据具体的生产需求和物料特性来确定。
在购买和使用单螺杆挤出机时,需要根据实际情况,选择合适的规格型号和基本参数,以确保生产过程的高效性和塑料制品的质量。
挤出机螺杆参数及影响

挤出机螺杆参数及影响挤出机是一种常见的塑料加工设备,用于将塑料料粒加热熔化后通过挤出机螺杆的旋转运动,将熔融的塑料挤出成型。
1.螺杆直径:螺杆直径是指螺杆的最大直径,是挤出机螺杆的一个重要参数。
螺杆直径的选择与挤出机的规格有关,一般来说,较大直径的螺杆能提供更大的挤出压力和产量,适用于大规模生产。
而较小直径的螺杆则适用于小规模生产或特殊工艺要求。
2.螺杆长度与直径比:螺杆长度与直径比是指螺杆的长度与其直径之比。
该参数对挤出机的熔融效果和输出能力有着重要影响。
较大的螺杆长度与直径比能够提供更大的塑化能力和更好的熔融效果,适用于高粘度塑料料粒的加工。
而较小的比值则适用于低粘度塑料料粒。
3.螺杆混合段长度:挤出机螺杆一般由若干个区域组成,其中最后一个区域是混合段。
混合段是指将塑料料粒加热熔化并充分混合的区域,其长度对挤出成品的均匀度和质量有着重要影响。
较长的混合段长度有助于提高熔融和混合效果,但也会增加能耗和成本。
因此,混合段长度的选择需要考虑生产要求和经济性。
4.螺杆螺距:螺杆螺距是指螺杆的螺线间距,影响着螺杆的输送能力和熔融均匀度。
较大的螺距可以提供更大的产量,但也可能导致熔融不均匀和混合不充分。
适当的螺距选择应根据塑料的特性和生产需求来确定。
5.螺杆转速:螺杆转速是指螺杆的旋转速度,对挤出机的生产能力和挤出产品的质量起着重要影响。
较高的转速可以提高产量,但也可能导致熔融温度升高和产品品质下降。
因此,选择适当的螺杆转速需要综合考虑生产需求和产品要求。
螺杆的参数选择对挤出机的性能和生产效果有着重要的影响。
不同的塑料料粒和生产要求需要不同的螺杆参数来优化挤出过程。
因此,在选择和调整挤出机螺杆参数时,需综合考虑原料特性、产品要求和经济性,通过实际生产验证和调整来获得最佳的挤出效果和产品质量。
第三节挤出机常规螺杆设计
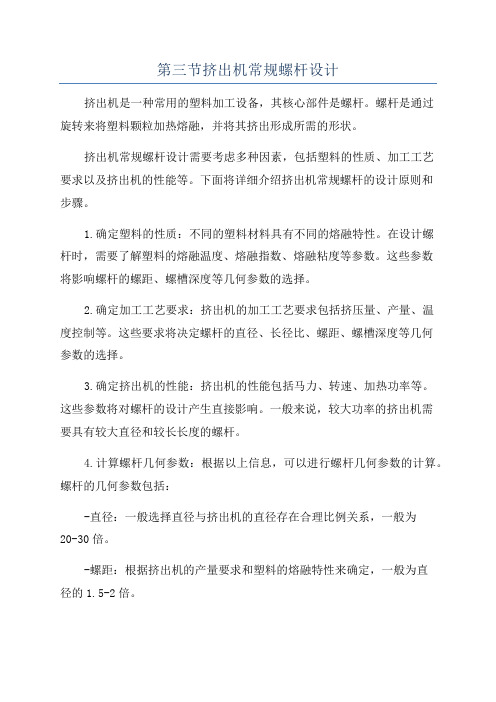
第三节挤出机常规螺杆设计挤出机是一种常用的塑料加工设备,其核心部件是螺杆。
螺杆是通过旋转来将塑料颗粒加热熔融,并将其挤出形成所需的形状。
挤出机常规螺杆设计需要考虑多种因素,包括塑料的性质、加工工艺要求以及挤出机的性能等。
下面将详细介绍挤出机常规螺杆的设计原则和步骤。
1.确定塑料的性质:不同的塑料材料具有不同的熔融特性。
在设计螺杆时,需要了解塑料的熔融温度、熔融指数、熔融粘度等参数。
这些参数将影响螺杆的螺距、螺槽深度等几何参数的选择。
2.确定加工工艺要求:挤出机的加工工艺要求包括挤压量、产量、温度控制等。
这些要求将决定螺杆的直径、长径比、螺距、螺槽深度等几何参数的选择。
3.确定挤出机的性能:挤出机的性能包括马力、转速、加热功率等。
这些参数将对螺杆的设计产生直接影响。
一般来说,较大功率的挤出机需要具有较大直径和较长长度的螺杆。
4.计算螺杆几何参数:根据以上信息,可以进行螺杆几何参数的计算。
螺杆的几何参数包括:-直径:一般选择直径与挤出机的直径存在合理比例关系,一般为20-30倍。
-螺距:根据挤出机的产量要求和塑料的熔融特性来确定,一般为直径的1.5-2倍。
-螺槽深度:根据挤出机的产量要求和塑料的熔融特性来确定,一般为螺距的0.2-0.3倍。
-螺杆长度:一般根据挤出机的马力和转速来确定,一般为直径的20-30倍。
5.确定螺杆结构:根据以上几何参数,可以确定螺杆的结构。
常见的螺杆结构有标准型、混合型、倒模型等。
不同的结构适用于不同的加工工艺和塑料材料。
6.进行材料选择:根据螺杆的工作环境和要求,选择适合的螺杆材料。
常用的螺杆材料有38CrMoAlA、42CrMo等。
7.进行螺杆加工和组装:根据螺杆的设计图纸和参数,进行螺杆的加工和组装工作。
螺杆的加工工艺包括车削、镗削、磨削等。
总结起来,挤出机常规螺杆的设计需要考虑塑料性质、加工工艺要求、挤出机的性能等多种因素。
通过对这些因素的分析和计算,可以确定螺杆的几何参数和结构,进而进行螺杆的加工和组装。
橡胶冷喂料挤出机螺杆结构几何参数分析与选择

在设计中要注意到:同一螺杆,螺纹升角也应该有所不同,喂料段适用于弹性态固体
输送理论,此段的摩擦系数较大,因此其螺纹升角应比较大;塑化段适用于粘弹态的输送理
论,摩擦系数变小,其螺纹升角应适当减小;到了挤出段物料基本上是粘流态,摩擦系数最
小。其螺纹升角也应最小。表 2 列举了几种螺杆各段的螺纹升角。
升角 规格 一种φ90 销钉螺杆
3
程都会导致螺杆摩擦系数的变化,因此最佳的螺纹升角是相对的。
从粘性流体输送理论可知,螺纹升角的大小既可影响正流流量也可影响逆流流量。如
果要得到最大生产能力,则要求正流流量有最大值,而逆流流量有最小值。单纯从理论上推
导,若正流流量要达到最大值,则要求 d( cosθ sinθ )/dθ =0,这时θ=45°,换句话说,螺杆螺
化段的塑化能力是否均匀以及挤出段的挤出是否稳定。
当前导程和升角都有变大的趋势, 这是因为传统的螺杆为了增加胶料的剪切效果,充
分塑化胶料,只能通过减小螺槽升角,增加螺纹的长度;但是当今的螺杆,完全可以通过很
多其他的方式来增加胶料的塑化效果,比如:在塑化段设置销钉、设置传递螺纹或者设置主
副螺纹等。这些都是有效的增加胶料塑化的方法。
等距等深 等距等深
从统计角度看,喂料段升角可在 22°~26°选取,塑化段升角可在 20°~24°选取, 挤出段升角可在 18°~22°选取。从提高生产能力而言,门尼粘度偏高的胶料宜选偏大升 角,门尼粘度和硬度偏低的,宜选较小的升角;从提高塑化效果而言,门尼粘度偏高的胶料 宜选偏小升角,门尼粘度和硬度偏低的胶料宜选偏大的升角。 2-5 螺杆的几何压缩比(ξ)
几种螺杆的设计参数

几种螺杆的设计参数螺杆是一种常用的机械传动元件,广泛应用于各种机械设备中。
以下是几种常见的螺杆设计参数。
1.螺距:螺杆的螺距是指螺杆上两个螺纹峰之间的距离。
螺距决定了单位长度螺杆上的螺纹个数。
螺距越大,单位长度上的螺纹个数越多,转动时移动的距离也越大。
2.螺杆直径:螺杆的直径是指螺杆周围外径的大小。
螺杆直径的选择取决于所需的扭矩和受力要求。
直径越大,螺杆的扭矩和受力能力越大。
3.导程:导程是指螺杆上两个螺纹之间的轴向移动距离。
导程决定了单位转动角度下的移动距离。
导程越大,单位角度转动时移动的距离越大。
4.螺纹形状:螺杆的螺纹形状通常分为三种,分别是三角形螺纹、矩形螺纹和梯形螺纹。
三角形螺纹常见于低速传动,矩形螺纹常见于中速传动,而梯形螺纹则常见于高速传动。
5.材料选择:螺杆的选择也与所使用的材料有关。
常见的螺杆材料有钢材、铝材、塑料等。
不同的材料具有不同的物理和化学性质,选择适当的螺杆材料可以满足不同的工作环境和要求。
6.螺杆端部设计:螺杆的端部设计也十分重要。
常见的螺杆端部设计包括平头、圆头、圆锥头等。
端部设计将直接影响螺杆与被连接物的接触面积和连接方式,进而影响整个传动系统的性能。
7.精度要求:螺杆的精度要求取决于其应用领域和工作环境。
精度要求包括制造精度和使用精度。
制造精度一般包括轴线误差、直线度、螺纹粗糙度等;使用精度则决定了螺杆的运动平稳性和精度损失。
8.表面处理:螺杆的表面处理可以提高其耐磨性和抗腐蚀性。
常见的表面处理方式包括镀铬、硬化等。
表面处理的选择将根据螺杆的工作环境和要求来决定。
上述是螺杆的几种设计参数,不同的设计参数将根据具体的应用场景和要求来选择,以满足机械设备的传动需求。
设计参数的合理选择将直接影响螺杆的工作性能和寿命。
挤出成型工艺与设备 螺杆挤出机的主要参数

二、螺杆的主要参数
θ是螺纹与螺杆横截面之间的夹角,通常在100~300之间。随着θ增大, 出料快,生产能力提高,但挤压剪切作用减少,停留时间短,塑化效果下降。
e大,动力消耗大; e小,漏流增加。一般e=0.08~0.12D。
δ值大生产效率低,δ值过小时,强烈剪切,会引起过热降解,一般δ与 螺杆直径之比为0.0005~0.002左右。
二、螺杆的主要参数
螺杆长度:
对普通螺杆来说,根据物料在挤出机中经历的三个阶段,人们 常常把螺杆的有效工作长度L分为三段。
1 加料段L1(feeding zone):
其作用是将松散的物料逐渐压实并送入下一段;减小压力和
产量的波动,从而杆的主要参数
2 熔融段(压缩段)L(compression zone):
其作用是把物料进一步压实;将物料中的空气推向加料段排出;
使物料全部熔融并送入下一段。
3 均化段(计量段)L3(metering zone):
其作用是将已熔融物料进一步均匀塑化,并使其定温、定压、
定量、连续地挤入机头。
螺杆的长度用mm作单位。
一、螺杆挤出机的技术参数
机器中心高度:
用H表示,指螺杆中心线到地面的高度,单位mm。
机器外形尺寸:
长、宽、高,表示为长×宽×高,单位mm。
机器质量 (重量):
用W表示,单位为t或kg。
目录
01 螺杆挤出机的技术参数 02 螺杆的主要参数
二、螺杆的主要参数
D—螺杆外径;d—螺杆根径;t—螺距;W—螺槽宽度;
螺杆直径D :
指螺杆外径,代表挤出机的规格。随着直径增大,生产能力提高。
螺杆长径比L/D :
橡胶挤出机螺杆构型分析及其几何参数的确定

橡胶挤出机螺杆构型分析及其几何参数的确定吕柏源郑晓斐闵鹏峰崔静(青岛科技大学高分子材料加工机械研究所)摘要:螺杆是冷喂料挤出机的一个核心部件,它在挤出机的性能参数中起着决定性的作用。
本文将螺杆从宏观功能上分成三个功能段,依据挤出理论结合生产实践分别对螺杆的喂料功能段、塑化功能段和挤出功能段的各种螺杆构型进行了较详尽较系统的分析,以便更容易理解和掌握各种螺杆构型的工作原理,希望对螺杆设计和选型有所帮助。
另一方面螺杆又是由众多的结构几何参数所组成。
因此螺杆几何参数的确定和选择直接关系着挤出机的使用性能。
本文分析了螺杆几何参数影响挤出过程的理论依据,进而对各几何参数进行选择和确定,为螺杆和挤出机的设计、选型提供依据和参考。
1.前言在橡胶工业中,螺杆挤出机是橡胶加工的重要设备,它广泛应用在轮胎制造、胶管制造、密封胶胶条制造、电线电缆和防水材料制造等等。
在挤出机中,螺杆是一个核心部件,它在挤出机的性能参数中起着决定性的作用。
从挤出机的发展史中就充分证明了这一点:最早使用的是短长径比的等距不等深或收敛螺杆,因没有塑化功能,只能用在橡胶制品的压型功能上,即出现了最早的热喂料挤出机;由于热喂料挤出机需要庞大的供胶设备,既浪费能源,浪费占地面积,劳动强度大,挤出制品质量低等问题,因此,加大了螺杆的长径比,提高了胶料在挤出过程中的剪切历程,以便提高螺杆的塑化能力,出现了大长径比的普通螺纹螺杆,即从热喂料挤出机发展到普通冷喂料挤出机;由于普通冷喂料挤出机的螺杆没有塑化元件结构,塑化能力达不到挤出工艺要求,在此背景下,螺杆的塑化段增加了主副螺纹结构,出现了主副螺杆(即强力剪切)冷喂料挤出机;主副螺纹挤出机虽然解决了塑化能力问题,但它只是简单的剪切作用,对塑化和混合作用还满足不了高质量橡胶制品的要求,因此,又将螺杆的塑化段发展成机筒销钉螺杆,则出现了销钉冷喂料挤出机。
并为此,先后出现了繁多的挤出机品种,如:挡板挤出机、传递型挤出机,销钉/主副螺纹型挤出机等等。
挤出机螺杆重要的参数是长径比

长径比是挤出机螺杆重要的参数,选用有一定的技巧,要正确选用螺杆长径比,需要了解长径比(L/D)在挤出过程所起到的作用。
在螺杆转速(n)一定的条件下,长径比增大,意味着物料在螺杆中的运动时间增加,有利于塑料的塑化和混合,可减少熔料的逆流和漏流,提高生产能力。
螺杆长径比的选取要根据被加工物料的性能和对产品质量的要求来考虑。
对于热敏性物料的加工,如PVC等宜选用较小的螺杆长径比,因过大的螺杆长径比易造成停留时间过长而产生分解;对于要求较高温度和压力的物料,如含氟塑料等,就需要用较大长径比的螺杆加工;对于产品质量要求不太高(如废旧料回收造粒)时,可选用较小的螺杆长径比,否则应选用较大的螺杆长径比;对于不同几何形状的物料,螺杆长径比的要求也不一样,如对于粒状料,由于经过塑化造粒,螺杆长径比可选小些,而对于未经塑化造粒的粉状料,则要求螺杆长径比大些,一般螺杆的长径比取值范围为20-30 。
从塑料挤出机喂料方式角度考虑:由于胶料的粘度较高,在压出过程中在剪切力的作用下会产生大量的热量。
于是,缩短镙杆的长度,可以使温度的升高保持在一定的限度之内。
因此,所需要螺杆的长径比就比较小。
螺杆长径比的大小,取决于热喂料方式,还是冷喂料方式。
对热喂料方式来说,需要螺杆的直径较大,长径比就较小,螺杆的长度通常是
50以下。
对于冷喂料方式来说,需要螺杆的长度较长,其长径比就较大。
螺杆的长度大约在(10-15)的范围之内。
随着挤出技术的发展,螺杆的长度有增长的趋势。
恒锐螺杆:。
螺杆的各部分名称、代号及参数

塑料类型加料段塑化段均化段⾮结晶型20%~30%螺纹长45%~50%螺纹长25%~30%螺纹长结晶型40%~60%螺纹长(3~5)螺距30%~45%螺纹长螺杆的各部分名称、代号及参数螺杆螺纹部分⼏何形状、尺⼨参数的确定及代号参照图1。
图1:螺杆螺纹部分⼏何形状及代号① 螺杆直径 螺杆的直径数值是表⽰挤出机的规格⼤⼩,是指螺杆的螺纹部分直径尺⼨。
⽤5来表⽰,单位为mm 。
② 长径⽐ 螺杆的螺纹部分长度与螺杆直径的⽐值,即L/D 。
专业标准JB/T8061—1996中规定,螺杆的长径⽐值为(20~30):1。
挤出聚烯烃类塑料制品时取长径⽐(25~30):1;挤出聚氯⼄烯塑料制品时,取长径⽐(20~25):1。
③ 螺杆的螺纹部分分段 按螺杆转动塑化原料时的功能作⽤,把螺纹部分分为加料段、塑化段和均化段三部分。
加料段(图1中⽤L 1表⽰)是指接受料⽃供料后输送给塑化段部分。
塑化段(图1中⽤L 2表⽰)的温度逐渐提⾼,由加料段输送过来的原料在这⾥被搅拌、挤压和升温,被逐渐塑化成熔融态,同时,随螺杆的转动被推⼊均化段。
塑化段也称压塑段。
均化段(图1中⽤L 3表⽰)是指由塑化段输送到均化段的物料,在这⾥进⼀步得到均匀塑化后,被等量、等压、均匀地推⼊成型模具内。
加料段、塑化段和均化段,三段长度的确定是在长径⽐选定的条件下再分配。
塑化段长度选取要符合塑料熔融速率要求,与螺杆选择的压缩⽐有关。
对⾮结晶型塑料,⼀般取螺纹长的45%~50%;对结晶型塑料,取(3~5)D;对于尼龙,取(1~2)D 。
均化段选取长⼀些对物料塑化质量有利,可减少熔融料的压⼒和挤出熔料量的波动。
但均化段⼜不宜过长,否则会减少塑化段和加料段的长度;塑化段长度偏⼩,要影响物料的塑化质量。
所以,三段长度的选择,⼀定要综合考虑。
较合理的长度分配⽐例见表1。
表1:螺杆三段长度的⽐例分配④螺距 螺距是指两个螺纹间同⼀位置的距离,见图1,⽤t 表⽰。
在渐变型螺杆中,⼀般取t=D ,此时的螺纹升⾓为17°42。
双螺杆挤出机的主要参数

双螺杆挤出机的主要参数
①螺杆直径:指螺杆外径,单位mm。
对于变化的直径或锥形双螺杆来说,这是一个变值,应当指明是哪一端直径。
双螺杆挤出机的螺杆直径为28~340mm。
直径越大,表征设备的挤出量越大。
②螺杆长径比:指螺杆的有效长度与螺杆外径之比。
对于整体式双螺杆,长径比是固定的,一般为7~18;对于组合式双螺杆,长径比是可变的,有的甚至可达36:1。
③螺杆转向:分为同向旋转和异向旋转。
同向选装的双螺杆挤出机多用于混料,异向旋转的双螺杆挤出机多用于挤出制品。
④驱动功率:指驱动螺杆的电动机功率,单位kW。
⑤螺杆承受的扭矩:双螺杆挤出机承受的扭矩载荷较大。
为表征其承载能力和保护挤出机安全运转,一般在其规格参数中要列出螺杆所能承受的最大扭矩,工作时不能超过。
单位公斤.米。
⑥推力轴承的承载能力:推力轴承在双螺杆挤出机中是个重要部件,一般在产品规格说明中都会给出这个指标。
⑦螺杆转数范围:n min~n max,n min是最低转数,n max是最高转数。
⑧加热功率和加热段数:加热功率的单位是kW。
⑨产量:单位是kg/h。
几种螺杆的设计参数

一、注塑螺杆的基本型式及主要参数一般螺杆分为三段即加料段,压缩段,均化段。
加料段——底经较小,主要作用是输送原料给后段,因此主要是输送能力问题,参数(L1,h1),h1=(0.12-0.14)D。
压缩段——底经变化,主要作用是压实、熔融物料,建立压力。
参数压缩比ε=h1/h3及L2。
准确应以渐变度A=(h1-h3)/L2。
均化段(计量段)——将压缩段已熔物料定量定温地挤到螺杆最前端、参数(L3,h3),h3=(0.05-0.07)D。
对整条螺杆而言,参数L/D-长径比L/D利弊:L/D与转速n,是螺杆塑化能力及效果的重要因素,L/D大则物料在机筒里停留时间长,有利于塑化,同时压力流、漏流减少,提高了塑化能力,同时对温度分布要求较高的物料有利,但大之后,对制造装配使用上又有负面影响,一般L/D为(18~20),但目前有加大的趋势。
其它螺距S,螺旋升角φ=πDtgφ,一般D=S,则φ=17°40′。
φ对塑化能力有影响,一般来说φ大一些则输送速度快一些,因此,物料形状不同,其φ也有变化。
粉料可取φ=25°左右,圆柱料φ=17°左右,方块料φ=15°左右,但φ的不同,对加工而言,也比较困难,所以一般φ取17°40′。
棱宽e,对粘度小的物料而言,e尽量取大一些,太小易漏流,但太大会增加动力消耗,易过热,e=(0.08~0.12)D。
总而言之,在目前情况下,因缺乏必要的试验手段,对螺杆的设计并没有完整的设计手段。
大部分都要根据不同的物料性质,凭经验制订参数以满足不同的需要,各厂大致都一样。
下面就几种专用螺杆的设计结合其物料特性作简单介绍:1、PC料(聚碳酸酯)特点:①非结晶性塑料,无明显熔点,玻璃化温度140°~150℃,熔融温度215℃~225℃,成型温度250℃~320℃。
②粘度大,对温度较敏感,在正常加工温度范围内热稳定性较好,300℃长时停留基本不分解,超过340℃开始分解,粘度受剪切速率影响较小。
- 1、下载文档前请自行甄别文档内容的完整性,平台不提供额外的编辑、内容补充、找答案等附加服务。
- 2、"仅部分预览"的文档,不可在线预览部分如存在完整性等问题,可反馈申请退款(可完整预览的文档不适用该条件!)。
- 3、如文档侵犯您的权益,请联系客服反馈,我们会尽快为您处理(人工客服工作时间:9:00-18:30)。
性、低传导性、高添加物等塑料螺杆,占40%50%螺杆工作长度,PVC螺杆可占100%螺杆工作长度,以免产生激烈的剪切热。
4、计量段
a、一般占2025%螺杆工作长度,确保塑料全部熔融以及温度均匀,混炼均匀;
b、计量段长则混炼效果佳,太长则易使熔体停留过久而产生热分解,太短则易使温度不均匀;
c、 PVC等热敏性塑料不宜停留时间过长,以免热分解,可用较短的计量段或不要计量段。
5、进料螺槽深度,计量螺槽深度
a、进料螺槽深度越深,则输送量越大,但需考虑螺杆强度,计量螺槽深度越浅,则塑化发热、混合性能指数越高,但计量螺槽深度太浅则剪切热增加,自生热增加,温升太高,造成塑胶变色或烧焦,尤其不利于热敏性塑料;
b、计量螺槽深度=KD=(0.03.07)*D,D增大,则K 选小值。
二、影响塑化品质的主要因素
影响塑化品质的主要因素为:长径比、压缩比、背压、
螺杆转速、料筒加热温度等。
1、长径比:为螺杆有效工作长度与螺杆直径的比值。
a、长径比大则吃料易均匀;
b、热稳定性较佳的塑料可用较长的螺杆以提高混炼性而不烧焦,热稳定性较差的塑料可用较短的螺杆或螺杆尾端无螺纹。
以塑料特性考虑,一般流长比如下:热固性为1416,硬质PVC,高粘度PU等热敏性为1 718,一般塑料为1822,PC、POM等高温稳定性塑料为2224。
2、压缩比:为进料段最后一个螺槽深度与计量段第一个螺槽深度的比值。
a、考虑料的压缩性、装填程度、回流等影响,制品要密实、传热与排气;
b、适当的压缩比可增加塑料的密度,使分子与分子之间结合更加紧密,有助于减少空气的吸取, 降低因压力而产生的温升,并影响输出量的差异,不适当的压缩比将会破坏塑胶的物性;
c、压缩比值越高,对塑料在料管内塑化过程中产生的温升越高,对塑化中的塑料产生较佳的混炼均匀度,相对的出料量大为减少。
d、高压缩比适于不易熔塑料,特别具低熔化粘度,热稳定性塑料;低压缩比适于易熔塑料,特别具高熔化粘度、热敏性塑料。
3、背压
a、增加背压可增加螺杆对熔融树脂所做的功,消除未熔的塑胶颗粒,增加料管内原料密度及其均匀程度;
b、背压被运用来提高料筒温度,其效果最为显著;
c、背压过大,对热敏性较高的塑料易分解,对低粘度的塑料可能会产生流涎现象,背压过小,注塑出的成品可能会有气泡。
4、螺杆转速
a、螺杆的转动速度直接影响塑料在螺旋槽内的切变;
b、小型螺杆槽较浅吸收热源快速,足够促使塑料在压缩段时间软化,螺杆与料筒壁间的摩擦热能较低,适宜高速旋转,增加塑化能力;
c、大型螺杆则不宜快速旋转,以免塑化不匀及造成过度摩擦热;
d、对热敏性较高的塑料,螺杆转速过大的话,塑料
b、料筒内熔胶温度通常高于筒外控制的温度。
三、塑化料管组选用原则及过胶头组件设计
(一)考虑要点:输送段、压缩段、计量段、三段比值、压缩比、计量段螺槽深、长径比、螺牙数.
(二)选用原则
a、欲得混炼效果佳的采用长径比大,螺牙数多,压缩比大,计量段螺槽浅的设计,例如:PA、PE、PP、POM;
b、欲防止剪切过热现象的采用长径比小,螺牙数少,压缩段长,压缩比小,计量段螺槽较深的设计,例如:PC、PMMA、硬质PVC、加玻璃纤维或防火料;
c、欲得高塑化率者,采用压缩比较小,计量段螺槽较深的设计。
(三)过胶头组件设计
好的止逆阀应具备:
a、快速止逆速度能力;
b、完全止逆能力,以维持最小的塑料回流现象;
c、料流顺畅,无死角以避免局部剪切热,而造成塑料劣化现象;。