博士隆-新能源全铝车身铆接技术解决方案
车身材料铆接工艺 SPR FDS
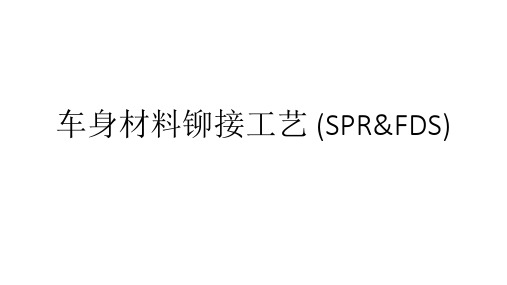
车身材料铆接工艺(SPR&FDS)
成本
201520252030汽车车身板材应用整体趋势预测2015-2030
凯迪拉克CT6 车身先进连接工艺应用概括
工艺SPR FDS铝电焊铝螺柱焊铝弧焊铝激光钎焊结构胶单位个个个个mm mm mm
工艺要求双面可达单面可达双面可达单面可达单面可达单面可达单面可达
对应材料铝-铝
铝-铁铝-铝
铝-铁
铝-铝铝-铝铝-铝铝-铝铝-铝
铝-铁
铁-铁
车身用量合计373726193314499053046311547
3施压
6完成
4刺穿
SPR特性:
可以连接金属和非金属材料,可以连接不同厚度的材料;动态疲劳强度高;碰撞能量吸收性能好;
可无损检测连接性能质量;
其质量由设备决定。
工艺难点:
1.铝薄板连接处易变形
2.铸件连接容易开裂
3.铆钉种类和数量多前期选择难度大
4.材料时效影响连接点质量稳定性
FDS特性:
单面连接工艺;
可以连接不同材料;很高的松开扭矩;气密性和水密性好;动态承载性好。
【聚焦】车身一体式“安全”门环技术及应用前景解读

【聚焦】车⾝⼀体式“安全”门环技术及应⽤前景解读车⾝是汽车最重要的组成部分,其可有效保护驾乘⼈员安全,营造安全舒适的驾乘空间。
随着中国汽车⾏业对于汽车碰撞安全和碳排放量的标准不断提⾼,汽车制造企业纷纷开始寻求更加轻量化、更加安全、更加环保的⽩车⾝解决⽅案。
其中最⼤的⼀个创新就是⼀体式的门环。
相⽐传统焊接⼯艺,究竟是门是⼀体成型的耐撞还是焊接的车门更结实呢?何为“焊接”式车门?说⽩了就是将“车门的下半部”与“窗户框⼦”焊接到⼀起,这就叫“焊接式车门”,⽽即使是“焊接”的车门,下半部分依旧是“⼀体成型”的,只不过“窗户框”是焊接上的。
“⼀体式车门”就⽐较容易理解了,车门的“下半部分”与“窗户框”是⼀体“冲压”出来的,见下图。
(1)⼀体冲压还是焊接?材料、⼯艺如何选择?在⼀些铁⼯⼚⼯作过的朋友就会很明⽩,“冲压技术”是具有局限性的,⽐如当“原料⾦属”的“刚性”太强、“厚度”过⼤的情况下就根本不适合采⽤“⼀体式冲压”技术。
⽐⽅说⼀些⾼端车型,⽐如5系、奔驰E等等,车门都是采⽤“焊接”技术的,因为材料的质地好,⽤“⼀体式冲压”反⽽⽆法加⼯,德系⾼端车的做法是先⼀次冲压车门下半部,然后进⾏焊接窗框、加强筋。
使⽤“⼀体式冲压”必须要保证钢材具有良好的“延展性”,⽽“延展性”好,“刚性”就必须要降低,两种属性本⾝就是对⽴的。
严格来说⽬前的⾦属车⾝不存在⼀体成型的,因为车⾝框架结构复杂,根本没有哪个⼚家可以将整块⾦属板⼀次冲压成球笼型的车⾝框架。
都是采⽤钢板冲压出车⾝的各个组成部分,然后通过焊接将这些部件组成车⾝,然后安装车⾝覆盖件和各种配件,组装出⼀辆完整的汽车。
所以说再⽜逼的⼚家他的车也要焊接。
上图,奔驰的⽣产线,先是底盘部件,前后纵梁等部件焊接,这⼀步将底盘焊接牢固。
然后将冲压好的车⾝侧围构件,车顶构件组装上去再进⾏焊接。
上图就是冲压成的车体侧围构件,我们开的车都是从⼀块钢板开始,冲压出平⾯的构件,然后⼀步步组装焊接才形成了各种各样的车⾝造型。
轻量化连接装备之自冲铆接设备
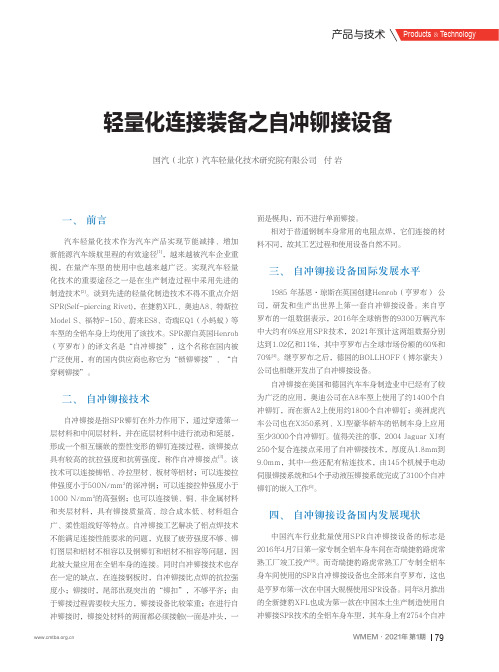
Products & Technology产品与技术轻量化连接装备之自冲铆接设备国汽(北京)汽车轻量化技术研究院有限公司 付 岩一、前言汽车轻量化技术作为汽车产品实现节能减排、增加新能源汽车续航里程的有效途径[1],越来越被汽车企业重视,在量产车型的使用中也越来越广泛。
实现汽车轻量化技术的重要途径之一是在生产制造过程中采用先进的制造技术[2]。
谈到先进的轻量化制造技术不得不重点介绍SPR(Self-piercing Rivet),在捷豹XFL、奥迪A8、特斯拉Model S、福特F-150、蔚来ES8、奇瑞EQ1(小蚂蚁)等车型的全铝车身上均使用了该技术。
SPR源自英国Henrob (亨罗布)的译文名是“自冲铆接”,这个名称在国内被广泛使用,有的国内供应商也称它为“锁铆铆接”、“自穿刺铆接”。
二、自冲铆接技术自冲铆接是指SPR铆钉在外力作用下,通过穿透第一层材料和中间层材料,并在底层材料中进行流动和延展,形成一个相互镶嵌的塑性变形的铆钉连接过程,该铆接点具有较高的抗拉强度和抗剪强度,称作自冲铆接点[3]。
该技术可以连接铸铝、冷拉型材、板材等铝材;可以连接拉伸强度小于500N/mm2的深冲钢;可以连接拉伸强度小于1000 N/mm2的高强钢;也可以连接镁、铜、非金属材料和夹层材料,具有铆接质量高、综合成本低、材料组合广、柔性组线好等特点。
自冲铆接工艺解决了铝点焊技术不能满足连接性能要求的问题,克服了疲劳强度不够、铆钉图层和铝材不相容以及钢铆钉和铝材不相容等问题,因此被大量应用在全铝车身的连接。
同时自冲铆接技术也存在一定的缺点,在连接钢板时,自冲铆接比点焊的抗拉强度小;铆接时,尾部出现突出的“铆扣”,不够平齐;由于铆接过程需要较大压力,铆接设备比较笨重;在进行自冲铆接时,铆接处材料的两面都必须接触(一面是冲头,一面是模具),而不进行单面铆接。
相对于普通钢制车身常用的电阻点焊,它们连接的材料不同,故其工艺过程和使用设备自然不同。
保隆科技汽车轻量化结构件技术升级之路

保隆科技汽车轻量化结构件技术升级之路保隆科技作为汽车轻量化结构件技术领域的领军企业,一直致力于提供先进的轻量化解决方案。
为了满足市场需求和产品创新,保隆科技一直在不断进行技术升级。
本文将从四个方面介绍保隆科技汽车轻量化结构件技术升级之路。
首先,保隆科技积极引进和研发新材料。
新材料的应用是实现汽车轻量化的重要途径。
保隆科技与多家研究院和大学合作,不断探索新的材料应用。
例如,保隆科技与国内高校合作,成功研发了一种新型镁合金材料,该材料具有优异的强度和轻量化特性,可以替代传统的铝合金材料,达到更轻量化的车身结构设计要求。
其次,保隆科技不断改进和优化设计技术。
通过引入先进的设计软件和仿真分析工具,保隆科技能够更精确地预测产品性能和结构受力情况,从而减少不必要的材料使用,实现轻量化。
同时,保隆科技还建立了完善的设计和开发团队,通过不断的技术培训和人才引进,提升设计师们的技术水平和创新能力。
第三,保隆科技加大了自动化生产设备的引进和应用。
自动化生产设备可以提高生产效率,降低劳动成本,并且能够保证产品质量的稳定性。
为此,保隆科技在生产线上引入了多个机械臂和自动化装配设备,实现了生产过程的智能化和自动化,提高了产品的生产效率和质量。
最后,保隆科技积极拓展国际市场和合作伙伴。
作为一家具有全球竞争力的企业,保隆科技意识到与国际合作伙伴的紧密合作对于技术升级至关重要。
因此,保隆科技积极参加国际展览会和技术交流会,与世界各地的汽车厂商和供应商建立了广泛的合作关系。
通过合作,保隆科技可以获取更多的技术支持和市场信息,提高公司的竞争力和产品的创新能力。
综上所述,保隆科技在汽车轻量化结构件技术升级之路上通过引进新材料、改进设计技术、加大自动化生产设备的应用以及拓展国际市场和合作伙伴,不断提高产品的竞争力和创新能力。
相信在保隆科技的努力下,未来将会有更多的轻量化解决方案出现,为全球汽车行业的可持续发展做出贡献。
博士隆-新能源汽车轻量化结构铆接技术解决方案
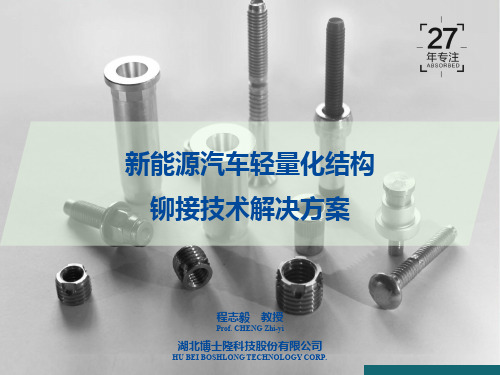
奥迪A8材料应用
< 5>
02 轻量化结构连接技术概述
三、汽车轻量化结构连接要求
• 强度 刚度 耐久可靠性 耐腐蚀性 工艺性 经济性等
四、汽车轻量化结构机械连接类型及连接力学特征
• 实体厚实结构 局部强度及耐久性加强
• 框架(型材)结构 发挥整体刚度效应下的局部强度加强
• 板(壳)结构 面与面连接局部强度与耐久性加强
<>
03 轻量化结构连接工艺及应用
二、框架(型材)结构连接工艺
2、无凸缘挤涨式套筒螺母(专利产品)
• 压头挤胀筒体,筒体顶部限位,避免脱出 • 筒体嵌入型材内,型材形变嵌入锁紧槽,防松脱、防转动 • 套筒两端接触薄壁型材内表面,提供优良支撑
优点:
• 双面平齐,无凸台 • 高拉脱力、高抗扭防转 • 强支撑,提升薄壁型材的结构
微观和宏观性能对比
电磁自冲铆接与传统自冲铆接对比:
电磁
传统
自冲
自冲
接头底切量Δt3较高(互锁性更好)
铆接
铆接
最大剪切力更大
< 26>
04 结构连接前沿技术简介
❑ 胶铆复合连接工艺
• 发挥胶接抗腐蚀、应力均匀、剪切强度高等特性,结合铆接接头的抗剥离能 力和十字拉伸性能。
• 胶铆复合胶层非连续分布,外围胶层较厚有效阻碍水、气进入,提高抗腐蚀能力 • 胶铆复合接头的剪切性能显著优于纯胶接和纯铆接的,是纯铆接两倍以上 • 胶铆复合接头的十字拉伸强度略低于纯SPR 接头,显著高于纯胶接接头的性能。
民用认证齐全,行业内唯一一家通过军工质量管理体系认证、保密体系认证
< 4>
02 轻量化结构连接技术概述
轻量化是新能源汽车产业最为关注、最为核心问题之一
汽车行业车辆铝车身连接工艺技术方法大全
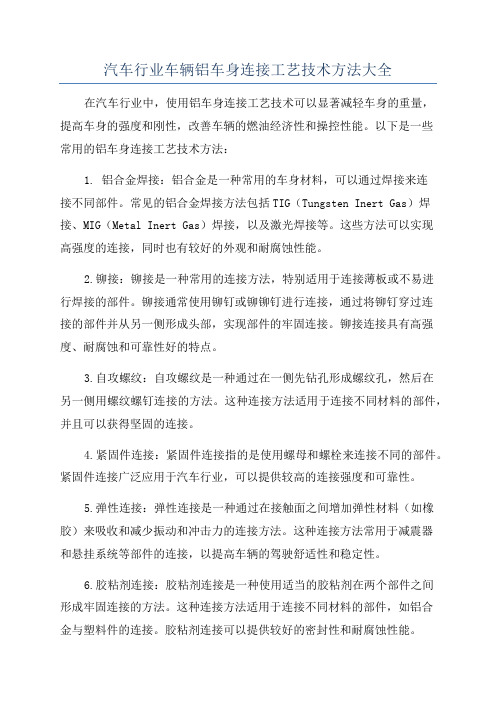
汽车行业车辆铝车身连接工艺技术方法大全在汽车行业中,使用铝车身连接工艺技术可以显著减轻车身的重量,提高车身的强度和刚性,改善车辆的燃油经济性和操控性能。
以下是一些常用的铝车身连接工艺技术方法:1. 铝合金焊接:铝合金是一种常用的车身材料,可以通过焊接来连接不同部件。
常见的铝合金焊接方法包括TIG(Tungsten Inert Gas)焊接、MIG(Metal Inert Gas)焊接,以及激光焊接等。
这些方法可以实现高强度的连接,同时也有较好的外观和耐腐蚀性能。
2.铆接:铆接是一种常用的连接方法,特别适用于连接薄板或不易进行焊接的部件。
铆接通常使用铆钉或铆铆钉进行连接,通过将铆钉穿过连接的部件并从另一侧形成头部,实现部件的牢固连接。
铆接连接具有高强度、耐腐蚀和可靠性好的特点。
3.自攻螺纹:自攻螺纹是一种通过在一侧先钻孔形成螺纹孔,然后在另一侧用螺纹螺钉连接的方法。
这种连接方法适用于连接不同材料的部件,并且可以获得坚固的连接。
4.紧固件连接:紧固件连接指的是使用螺母和螺栓来连接不同的部件。
紧固件连接广泛应用于汽车行业,可以提供较高的连接强度和可靠性。
5.弹性连接:弹性连接是一种通过在接触面之间增加弹性材料(如橡胶)来吸收和减少振动和冲击力的连接方法。
这种连接方法常用于减震器和悬挂系统等部件的连接,以提高车辆的驾驶舒适性和稳定性。
6.胶粘剂连接:胶粘剂连接是一种使用适当的胶粘剂在两个部件之间形成牢固连接的方法。
这种连接方法适用于连接不同材料的部件,如铝合金与塑料件的连接。
胶粘剂连接可以提供较好的密封性和耐腐蚀性能。
7.激光焊接:激光焊接是一种高精度的焊接方法,通过激光光束将两个部件熔合在一起。
这种连接方法适用于连接较小的部件或进行高精度的连接,可以实现较高的焊接质量和外观。
总的来说,汽车行业的车辆铝车身连接工艺技术涉及到多种方法,每种方法都有其适用的场景和特点。
在实际应用中,根据具体的车身设计和需求,可以选择合适的连接方法,以提高车身的性能和可靠性。
汽车车身轻量化用锁铆连接工艺及设备

中图分 类号 :U 6 .20 4 38 . 6
■
一浦 莱斯 精 密技 术 ( 深圳 ) 限公 司 有
王云 庆
1 汽 车轻 量 化 三 要 素
汽车 轻量 化 的 目的是在 保证 汽车 强度 、 刚性 和安
量 化应 用 的结 果是 否成 功 。
2 车身轻量化 中存在 的工艺 问题
A T&M 钡 界
接和 传统 铆 接工 艺 的不 足。 锁铆 连 接还 可 以使结 构胶
c涂 胶粘 合 工 艺在 抗 高温 ,耐 冲 击 、抗 老 化性 能 .
方面 存在 安全 隐 患。
粘合 层快 速定 型 ,实 现高 效率流 水作 业 。 d与传 统 铆 接工 艺 相 比 ,减 少 了34工 序 ,无需 . /
度 ,具 有如 下特 点。 a强度 高 。 . b适于 外观质 量检 查 。 . c无 需钻 孔 ,一次成 形 。 .
多,效率低 ,综合生产和物流成本高。
c涂 胶粘 合 工艺 ,凝胶 固化 时间长 ( 1 . 约 8h),
严重影响流水作业效率 ,综合成本高。
( 轻 量化 生产 过程 质量 控 制 问题 5) a焊 接 工 艺 , 由于 影 响 质 量 因素 多 ( 员 、 材 . 人
质量。
b传统铆接工艺对被铆接材料组合的外观、功能 .
和动 态 疲劳 强度 产 生很 大 的制约 。 c涂胶 粘合 工 艺仅 能满 足一 定 的连 接要 求 。 .
b轻量 化 材 料应 用 :选 用铝 镁 合金 材 料 、高 强度 . 钢 板和 非 金属 材 料等 轻量 化材 料 。
( 锁 铆连 接 点特性 2) 锁铆 铆 钉在 外 力 的作 用 下 ,通 过 穿透第 一层 材 料 和 中 间层材 料 ,并 在底 层材 料 中进 行流 动延 展 ,形成 相 互镶嵌 的永 久塑性 变形 的铆钉 连 接过程 ,这一 过程 称作 锁铆 连 接 。铆接 点具 有 较高 的抗 拉 强度 和抗 剪 强
新能源全铝车身铆接技术解决方案

编号
1
2
图片
编号
6
7
图片
图 1 高温烘烤设置
图 2 低温冷冻设置
编号
11
12
图片
编号
16
17
图片
图 3 60 次拆卸试验
图 4 防水测试
编号
21
22
图片
高低温实验温度:-40~150° 反复拆卸次数:60次
第一组 (拉铆后)
测试数量
30
合格数量
30
合格率
100%
编号
26
27
图片
第二组 (高低温后)
30 30 100%
防电化学腐蚀原理:
铝钉壳与铝基材为第一腐蚀通道,因同种材料,几乎不存在电位差,故而几乎不会发生电化学腐蚀
碳钢镀锌镍钉杆与铝钉壳为第二腐蚀通道,由于钉壳铝材将挤入钉杆沟槽中,加上较长的过盈连接面,形
成气密级的密封效果,腐蚀性介质难以进入,可以很好的防电化学腐蚀
11
<>
01 乘用车铝车身连接技术
铝框架车身铆钉应用实例:
BOM铆钉安装方法
<19>
02 铝合金大巴车身连接技术
关键焊接部位局部加强
挤
压
密
封
区
铝型材刚度加强
✓ 具有高紧固力,很强的抗剪、抗拉、抗震性
能;
✓ 适用于高强度连接,抗震防松要求高的钣
材铆接。
<
2 0
>
02 铝合金大巴车身连接技术
高强度钣材连接抗拉强度
80000
60000
40000
20000
0 5
新能源汽车全铝车身和铝合金电池包 连接解决方案
车身铸铝件铆接工艺检测标准及应用
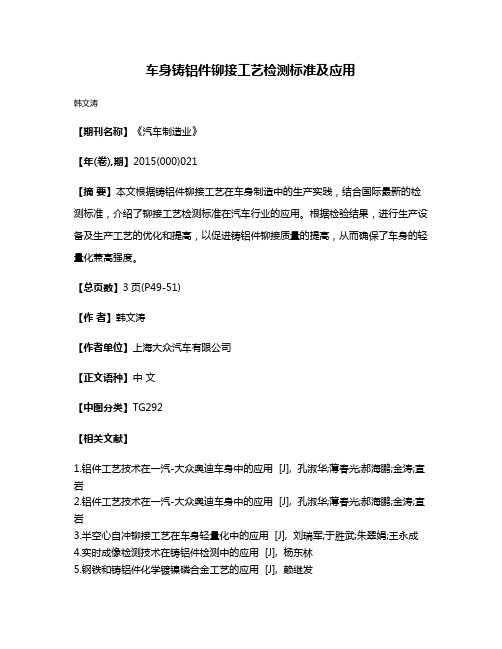
车身铸铝件铆接工艺检测标准及应用
韩文涛
【期刊名称】《汽车制造业》
【年(卷),期】2015(000)021
【摘要】本文根据铸铝件铆接工艺在车身制造中的生产实践,结合国际最新的检测标准,介绍了铆接工艺检测标准在汽车行业的应用。
根据检验结果,进行生产设备及生产工艺的优化和提高,以促进铸铝件铆接质量的提高,从而确保了车身的轻量化兼高强度。
【总页数】3页(P49-51)
【作者】韩文涛
【作者单位】上海大众汽车有限公司
【正文语种】中文
【中图分类】TG292
【相关文献】
1.铝件工艺技术在一汽-大众奥迪车身中的应用 [J], 孔淑华;薄春光;郝海鹏;金涛;宣岩
2.铝件工艺技术在一汽-大众奥迪车身中的应用 [J], 孔淑华;薄春光;郝海鹏;金涛;宣岩
3.半空心自冲铆接工艺在车身轻量化中的应用 [J], 刘瑞军;于胜武;朱翠娟;王永成
4.实时成像检测技术在铸铝件检测中的应用 [J], 杨东林
5.钢铁和铸铝件化学镀镍磷合金工艺的应用 [J], 赖继发
因版权原因,仅展示原文概要,查看原文内容请购买。
铝合金PMIG焊接时,解决焊缝根部撕裂现象的研究王喜峰
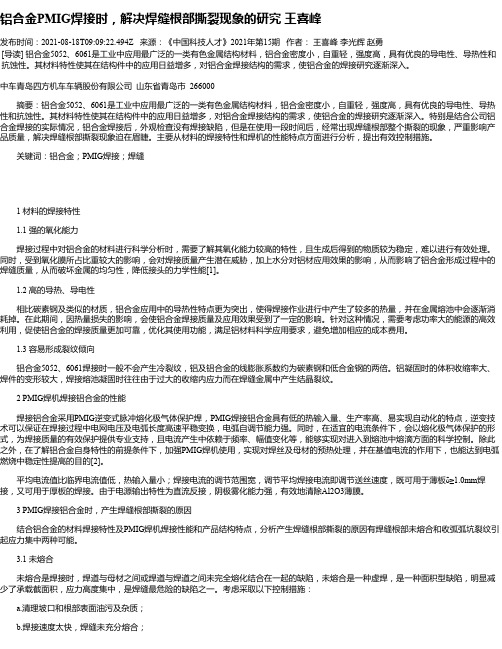
铝合金PMIG焊接时,解决焊缝根部撕裂现象的研究王喜峰发布时间:2021-08-18T09:09:22.494Z 来源:《中国科技人才》2021年第15期作者:王喜峰李光辉赵勇[导读] 铝合金5052、6061是工业中应用最广泛的一类有色金属结构材料,铝合金密度小,自重轻,强度高,具有优良的导电性、导热性和抗蚀性。
其材料特性使其在结构件中的应用日益增多,对铝合金焊接结构的需求,使铝合金的焊接研究逐渐深入。
中车青岛四方机车车辆股份有限公司山东省青岛市 266000摘要:铝合金5052、6061是工业中应用最广泛的一类有色金属结构材料,铝合金密度小,自重轻,强度高,具有优良的导电性、导热性和抗蚀性。
其材料特性使其在结构件中的应用日益增多,对铝合金焊接结构的需求,使铝合金的焊接研究逐渐深入。
特别是结合公司铝合金焊接的实际情况,铝合金焊接后,外观检查没有焊接缺陷,但是在使用一段时间后,经常出现焊缝根部整个撕裂的现象,严重影响产品质量,解决焊缝根部撕裂现象迫在眉睫。
主要从材料的焊接特性和焊机的性能特点方面进行分析,提出有效控制措施。
关键词:铝合金;PMIG焊接;焊缝1 材料的焊接特性1.1 强的氧化能力焊接过程中对铝合金的材料进行科学分析时,需要了解其氧化能力较高的特性,且生成后得到的物质较为稳定,难以进行有效处理。
同时,受到氧化膜所占比重较大的影响,会对焊接质量产生潜在威胁,加上水分对铝材应用效果的影响,从而影响了铝合金形成过程中的焊缝质量,从而破坏金属的均匀性,降低接头的力学性能[1]。
1.2 高的导热、导电性相比碳素钢及类似的材质,铝合金应用中的导热性特点更为突出,使得焊接作业进行中产生了较多的热量,并在金属熔池中会逐渐消耗掉。
在此期间,因热量损失的影响,会使铝合金焊接质量及应用效果受到了一定的影响。
针对这种情况,需要考虑功率大的能源的高效利用,促使铝合金的焊接质量更加可靠,优化其使用功能,满足铝材料科学应用要求,避免增加相应的成本费用。
浅谈储能式超级巴士铆接车体组装方法

图 5 车体吊装前后内高变化
22 截面对角线控制 如图 6所示,车体横截面对角线的难点在于车组装都是各
部件底漆完成之后进行铆接,组装前侧墙因单刚性弱导致轮廓 度有误差,铆接之后难矫正。所以要在组装过程中进行控制。
1-侧墙 2-连接板 3-底架 4-顶盖 图 6 截面对角线
23 选择合理的组装顺序 为保证整车关键尺寸和组装效率,我们摸索到了合理的车
图 1 巴士车体
21 车体内高控制 车体内高是车体在组装时要把控的关键项点。 1)增加组装工装胎具的支撑定位功能。一般的机车车辆
和城轨车辆组装工装都为方便操作者作业调节,而无太多的应 用装配上的支撑定位功能。如图 3和 4所示,考虑巴士车体采 用铆接工艺,需对车体组装部件进行精确定位并固定,防止铆 接前配钻孔时产生振动移位及方便检测零部件形状尺寸误差, 利用工装对底架和顶盖进行完全定位和夹紧,再进行侧墙的装 配。此方法有利于保证贯通道的内高尺寸和对角线尺寸。
(中车株洲电力机车有限公司,湖南 株洲 412001)
摘 要:储能式超级巴士车体组装全部采用铆接工艺,铆接相比焊接区别很大,主要体现在铆接装配前需要对产品精确 定位与夹紧,再进行现场配钻孔,产品一旦钻孔铆接就很难返工,甚至有可能造成产品的报废,带来重大损失。以超级巴 士车体在组装时遇到的重点和难点问题入手,通过提供相对应的解决措施和方法,来提高产品生产质量和效率。 关键词:巴士车体;组装方法;铆接工艺 doi:10.3969/j.issn.1006-8554.2020.05.019
1-底架水平支撑墩 2-登高作业平台 3-底架中心定位墩 4-顶盖旋转支撑臂 图 3 巴士铆接车体与一般焊接车体吊装胎具区别 2)车体内高放量。如图 5所示,由于顶盖在吊装时完全由 工装进行支撑,而侧墙成鼓形刚度偏弱,所以在内高控制上要 适当偏大,防止组装后因顶盖自重而引起内高缩小。
铝车身连接工艺方法大全
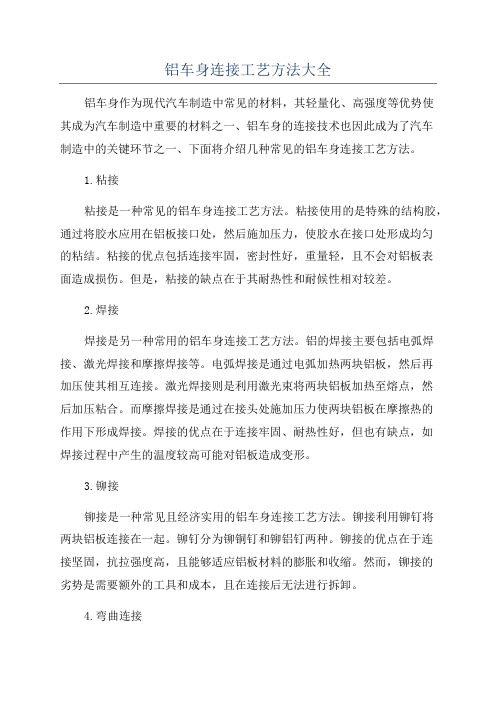
铝车身连接工艺方法大全铝车身作为现代汽车制造中常见的材料,其轻量化、高强度等优势使其成为汽车制造中重要的材料之一、铝车身的连接技术也因此成为了汽车制造中的关键环节之一、下面将介绍几种常见的铝车身连接工艺方法。
1.粘接粘接是一种常见的铝车身连接工艺方法。
粘接使用的是特殊的结构胶,通过将胶水应用在铝板接口处,然后施加压力,使胶水在接口处形成均匀的粘结。
粘接的优点包括连接牢固,密封性好,重量轻,且不会对铝板表面造成损伤。
但是,粘接的缺点在于其耐热性和耐候性相对较差。
2.焊接焊接是另一种常用的铝车身连接工艺方法。
铝的焊接主要包括电弧焊接、激光焊接和摩擦焊接等。
电弧焊接是通过电弧加热两块铝板,然后再加压使其相互连接。
激光焊接则是利用激光束将两块铝板加热至熔点,然后加压粘合。
而摩擦焊接是通过在接头处施加压力使两块铝板在摩擦热的作用下形成焊接。
焊接的优点在于连接牢固、耐热性好,但也有缺点,如焊接过程中产生的温度较高可能对铝板造成变形。
3.铆接铆接是一种常见且经济实用的铝车身连接工艺方法。
铆接利用铆钉将两块铝板连接在一起。
铆钉分为铆铜钉和铆铝钉两种。
铆接的优点在于连接坚固,抗拉强度高,且能够适应铝板材料的膨胀和收缩。
然而,铆接的劣势是需要额外的工具和成本,且在连接后无法进行拆卸。
4.弯曲连接弯曲连接是一种适用于铝薄板连接的工艺方法。
通过将两块铝薄板进行弯曲连接,使其互相扣合。
弯曲连接的优点在于简单易于操作,无需额外的连接材料,且能够良好地保持铝板的整体性能。
但是,弯曲连接的强度相对较低,对板材的刚性要求较高。
5.机械连接机械连接是一种常用的铝车身连接工艺方法,包括螺栓连接和螺母连接。
这种连接方法需要在铝板上预先开孔,然后将螺栓和螺母通过孔洞连接。
机械连接的优点在于连接牢固,方便拆卸和维修。
但是,机械连接需要额外的连接部件,增加了制造成本。
综上所述,铝车身连接工艺方法有粘接、焊接、铆接、弯曲连接和机械连接等多种。
地铁车辆铝合金车体的铆接工艺
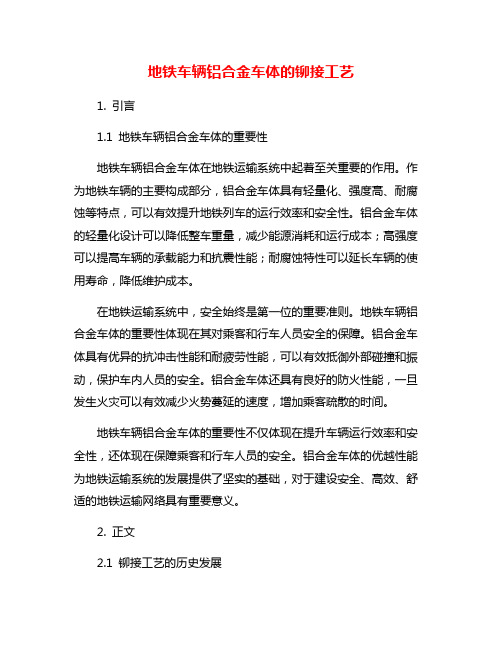
地铁车辆铝合金车体的铆接工艺1. 引言1.1 地铁车辆铝合金车体的重要性地铁车辆铝合金车体在地铁运输系统中起着至关重要的作用。
作为地铁车辆的主要构成部分,铝合金车体具有轻量化、强度高、耐腐蚀等特点,可以有效提升地铁列车的运行效率和安全性。
铝合金车体的轻量化设计可以降低整车重量,减少能源消耗和运行成本;高强度可以提高车辆的承载能力和抗震性能;耐腐蚀特性可以延长车辆的使用寿命,降低维护成本。
在地铁运输系统中,安全始终是第一位的重要准则。
地铁车辆铝合金车体的重要性体现在其对乘客和行车人员安全的保障。
铝合金车体具有优异的抗冲击性能和耐疲劳性能,可以有效抵御外部碰撞和振动,保护车内人员的安全。
铝合金车体还具有良好的防火性能,一旦发生火灾可以有效减少火势蔓延的速度,增加乘客疏散的时间。
地铁车辆铝合金车体的重要性不仅体现在提升车辆运行效率和安全性,还体现在保障乘客和行车人员的安全。
铝合金车体的优越性能为地铁运输系统的发展提供了坚实的基础,对于建设安全、高效、舒适的地铁运输网络具有重要意义。
2. 正文2.1 铆接工艺的历史发展铆接工艺的历史发展可以追溯到古代,最早可以追溯到公元前3000年的埃及时期。
在古代,人们已经开始使用铆接工艺来连接金属部件,以制造农具、武器和建筑结构等。
随着工业革命的到来,铆接工艺得到了进一步的发展和应用。
19世纪初,随着蒸汽机和机床的发展,铆接工艺逐渐被工业界广泛采用。
特别是在铁路、船舶和桥梁建设中,铆接工艺成为连接金属结构的主要方法。
随着科学技术的不断进步,现代铆接工艺也得到了快速发展,涌现出了许多新的铆接技术和设备。
20世纪起,随着航空航天、汽车制造和电子设备行业的快速发展,铆接工艺得到了广泛的应用。
特别是对于地铁车辆铝合金车体的制造,铆接工艺更是成为了不可或缺的一部分。
铆接工艺的发展不仅提高了生产效率,降低了生产成本,而且还提高了产品的质量和可靠性。
铆接工艺的历史发展是一个不断演变和创新的过程。
地铁车辆铝合金车体的铆接工艺
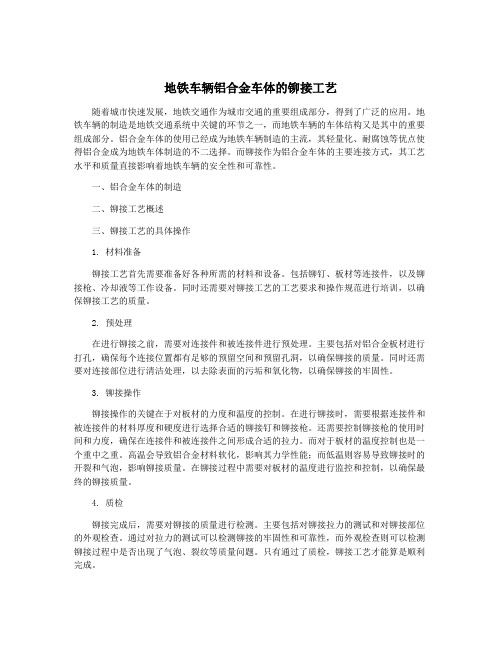
地铁车辆铝合金车体的铆接工艺随着城市快速发展,地铁交通作为城市交通的重要组成部分,得到了广泛的应用。
地铁车辆的制造是地铁交通系统中关键的环节之一,而地铁车辆的车体结构又是其中的重要组成部分。
铝合金车体的使用已经成为地铁车辆制造的主流,其轻量化、耐腐蚀等优点使得铝合金成为地铁车体制造的不二选择。
而铆接作为铝合金车体的主要连接方式,其工艺水平和质量直接影响着地铁车辆的安全性和可靠性。
一、铝合金车体的制造二、铆接工艺概述三、铆接工艺的具体操作1. 材料准备铆接工艺首先需要准备好各种所需的材料和设备。
包括铆钉、板材等连接件,以及铆接枪、冷却液等工作设备。
同时还需要对铆接工艺的工艺要求和操作规范进行培训,以确保铆接工艺的质量。
2. 预处理在进行铆接之前,需要对连接件和被连接件进行预处理。
主要包括对铝合金板材进行打孔,确保每个连接位置都有足够的预留空间和预留孔洞,以确保铆接的质量。
同时还需要对连接部位进行清洁处理,以去除表面的污垢和氧化物,以确保铆接的牢固性。
3. 铆接操作铆接操作的关键在于对板材的力度和温度的控制。
在进行铆接时,需要根据连接件和被连接件的材料厚度和硬度进行选择合适的铆接钉和铆接枪。
还需要控制铆接枪的使用时间和力度,确保在连接件和被连接件之间形成合适的拉力。
而对于板材的温度控制也是一个重中之重。
高温会导致铝合金材料软化,影响其力学性能;而低温则容易导致铆接时的开裂和气泡,影响铆接质量。
在铆接过程中需要对板材的温度进行监控和控制,以确保最终的铆接质量。
4. 质检铆接完成后,需要对铆接的质量进行检测。
主要包括对铆接拉力的测试和对铆接部位的外观检查。
通过对拉力的测试可以检测铆接的牢固性和可靠性,而外观检查则可以检测铆接过程中是否出现了气泡、裂纹等质量问题。
只有通过了质检,铆接工艺才能算是顺利完成。
四、铆接工艺存在的问题及改进方案在实际的铆接工艺中,可能会遇到一些问题,主要包括以下几个方面:1. 铆接拉力不足铆接拉力不足将影响车体的整体稳定性和使用寿命。
- 1、下载文档前请自行甄别文档内容的完整性,平台不提供额外的编辑、内容补充、找答案等附加服务。
- 2、"仅部分预览"的文档,不可在线预览部分如存在完整性等问题,可反馈申请退款(可完整预览的文档不适用该条件!)。
- 3、如文档侵犯您的权益,请联系客服反馈,我们会尽快为您处理(人工客服工作时间:9:00-18:30)。
电池模组与托盘之间的连接
电池下托盘与上盖体的密封连接
电池箱体与车架之间的连接
<2 2>
03
铝合金电池包连接技术
连接性能要求: • IP67以上密封等级 • 耐高低温 • 耐多次重复拆卸
电池下托盘与上盖体的密封连接
圆柱滚花型拉铆螺母
外六角型拉铆螺母
六方形抗扭力矩
>
圆柱形抗扭力矩
• 圆柱滚花型因涂覆耐落胶,其转动力矩会进一步降低,容易出现打转失效 • 外六角型开孔较为困难,需用专用开孔器/专用钻孔设备,目前主流应用
铝合金防撞梁-变截面套筒(博士隆专利)
沃尔沃S90L连接方案
新型变截面连接方案
拉脱力可达21KN,推出力7KN,抗扭85Nm, 剪切力可达65KN
< 8>
01
乘用车铝车身连接技术
铝合金CCB(仪表盘)主梁
公差调节器
结构(螺纹)形成
<>
01
乘用车铝车身连接技术
搭铁螺栓连接
钢车身搭铁螺栓: • • 冲压翻边,专用设备工装 异种金属连接,耐电化学腐蚀性不强 防电化学腐蚀搭铁螺栓
铆接后试验480小时,母体金属无腐蚀
<25>
03
铝合金电池包连接技术
编号 图片 编号 图片
<23>
03
铝合金电池包连接技术
挤压密封区
挤压力大
涂胶式
密封圈式
专利产品
胶密封
橡胶圈密封
• 密封圈式:密封橡胶圈高弹性,受力均匀,端面密封,非填充式密封,抗老化效果好、
耐拆卸性好
机械式密封拉铆螺母,无老化、耐拆卸、防水
<24>
03
铝合金电池包连接技术
电池包托盘密封拉铆螺母(试验方法)
•将铆螺母拉铆完成后的样件放于150°的烤箱中烘烤1小时,取出自然冷却后在-40度环 境中冷冻1小时,将10.9级标准内六角螺栓拧入型材上的铆螺母,对铆螺母施加12N.m
<13 >
01
乘用车铝车身连接技术
<1 4>
02
铝合金大巴车身连接技术
机械连接
焊接 <1 5>
02
铝合金大巴车身连接技术
加强筋局部加强连接(钢-铝)
双面连接,两侧须有足够的安装空间 具有高紧固力,很强的抗剪、抗拉、 抗震性能; 适用于高强度连接,抗震防松要求
高的钣材铆接。
<1 6>
02
应对高强度材料连接,如碳纤维、高强钢、 铝合金等混合材料的薄板链接
闭合开关,电容充电 充电完成
❑ 电磁自冲铆接技术:E-SPR,博士隆专利
开关闭合瞬间,电容放电
铜线圈和驱动片之间 产生强大互斥磁场力
冲头向下冲击
优点:
(1)提供近音速/超音速高速连接 (2)提供瞬态冲击与断裂,适用于高强度、 脆性材料连接,提供低裂纹密度连接 (3)如高强钢、超高强钢与其他材料的互连, (4)脆性材料如碳纤维与其他材料的互连
11
<>
01
乘用车铝车身连接技术
铝框架车身铆钉应用实例:
加强筋局部连接
焊接部位局部加强
钢-铝型材连接(吸能盒)
加强筋局部连接
焊接部位局部加强
• 可应用口杯(拉丝)、挤压型等结构型铆钉,提供较高的抗拉抗剪的连接 • 易于对孔部位,可用于替代FDS工艺,成本投入更低,操作便捷
<1 2>
01
乘用车铝车身连接技术
80000
60000 40000 20000 0
高强度钣材连接剪切强度
80000
60000 40000 20000
5
拉丝铆钉
6
8
BOM铆钉
10
12
0 5 拉丝铆钉 6 8 BOM铆钉 10 12 环槽铆钉
环槽铆钉
连接强度
拉丝铆钉 BOM铆钉 环槽铆钉
抗振性能
安装效率
密封性能
成本
<21>
Hale Waihona Puke 03铝合金电池包连接技术
<18>
02
铝合金大巴车身连接技术
BOM铆钉安装方法
<19>
02
铝合金大巴车身连接技术
关键焊接部位局部加强
挤 压 密 封 区
具有高紧固力,很强的抗剪、抗拉、抗震性能; 适用于高强度连接,抗震防松要求高的钣
铝型材刚度加强
材铆接。
<2 0>
02
铝合金大巴车身连接技术
高强度钣材连接抗拉强度
框架(型材)结构连接工艺
< 3>
01
乘用车铝车身连接技术
北汽LITE为北极之狐(ARCFOX)
奇瑞eQ1小蚂蚁
长城华冠
蔚来汽车
< 4>
01
乘用车铝车身连接技术
铝框架车身连接-挤涨式套筒螺母(博士隆专利技术):
普通油压机压铆
压铆后型材
5
<>
01
乘用车铝车身连接技术
铝框架车身套筒螺母应用实例:
替代焊接
• • •
气孔、热裂纹、焊接部位强度下降 同等6系铝材焊接,螺纹强度不足 对焊工操作要求高
<>
01
乘用车铝车身连接技术
铝合金防撞梁 主流连接方式:防撞梁和吸能盒焊接在 一起后,通过螺栓和纵梁相连接
主流连接方式-焊接
量产沃尔沃S90L,防撞梁日字型结构,套筒支撑螺栓连接
< 7>
01
乘用车铝车身连接技术
<>
01
乘用车铝车身连接技术
2
碳钢镀锌镍钉杆 铝基材
1
铝钉壳
防电化学腐蚀原理:
铝钉壳与铝基材为第一腐蚀通道,因同种材料,几乎不存在电位差,故而几乎不会发生电化学腐蚀 碳钢镀锌镍钉杆与铝钉壳为第二腐蚀通道,由于钉壳铝材将挤入钉杆沟槽中,加上较长的过盈连接面,形 成气密级的密封效果,腐蚀性介质难以进入,可以很好的防电化学腐蚀
铝合金大巴车身连接技术
环槽铆钉安装方法
<17>
02
铝合金大巴车身连接技术
钢-封闭铝型材连接
局部结构安装连接
焊接部位加强筋连接
• 两侧有足够安装空间,优先选择环槽铆钉,封闭空间, 只适应单面连接,可选择BOM铆钉 • 具有高紧固力,很强的抗剪、抗拉、抗震性能; • 适用于高强度连接,抗震防松要求高的钣材铆接。
的扭矩反复拆装60次后旋出,然后进行气密性测试(测试气压0.7MPa)。
性能 保证载荷 头部结合力 剪切力 破坏扭矩 转动扭矩 M6拉铆螺母指标 >16500N >6149N >3800N >15N.m >10N.m 铆接后在160度下烘烤25min,并反复拆卸60次,满足 IP67要求
防水性能 盐雾试验要求
新能源汽车全铝车身和铝合金电池包
连接解决方案
程志毅 教授
Prof. CHENG Zhi-yi
湖北博士隆科技股份有限公司
Hu Bei Boshlong Technology Corp.
01
乘用车铝车身连接技术
< 2>
01
乘用车铝车身连接技术
• 框架(型材)结构连接最主要解决连接件使框架刚度和强度得到充分保 障,同时加强局部强度,提供强螺纹支撑 • 车身框架应用铝型材壁厚通常在2~5mm,用于较强承载部位,其连接螺 纹M8~M10,铆螺母等无法提供该级别螺纹加强