微三维结构电火花铣削关键技术研究
先进制造—微细电火花加工技术

微机械和微制造的基础——微细电火花加工技术摘要:作为一种实用的微细加工技术,微细电火花加工在加工微细轴、微小孔等小尺度的零件时具有独特的优越性。
本文简略地介绍了微细电火花加工技术的原理,分析了微细电火花加工的特点和优点,研究了微细电火花加工的关键技术,并详细介绍了一种微细电火花加工装置及其应用。
关键词:微细电火花加工原理特点关键技术装置应用0.引言微细加工技术是先进制造技术的重要组成部分,是实现微机械产品的最基本技术,不仅直接影响着尖端技术和国防工业的发展,而且还影响到机械产品的加工精度和加工表面质量,影响产品的国际竞争力。
目前,世界各国都非常重视微细加工技术,将其作为发展先进制造技术中的优先发展内容。
作为微细加工技术的一个重要分支,微细电火花加工技术因其具有设备简单、可控性好、无切削力、适用性强等一系列优点,在微小尺度零件的加工中获得大量应用,受到国内外学者的广泛关注。
1.微细电火花加工的原理及特点1.1微细电火花加工原理电火花加工(Electrical Discharge Machining)是指在绝缘介质中,通过工具电极和工件之间脉冲性火花放电时的电蚀现象对工件材料进行蚀出,以达到一定的形状尺寸和表面粗糙度要求的一种加工方法。
微细电火花加工(micro Electro Discharge Machining,简称micro-EDM)的原理与普通电火花加工并无本质区别。
电火花加工中电极材料的蚀除过程是火花放电时的电场力、磁力、热力、流体动力、电化学及胶体化学等综合作用的过程。
当脉冲电压施加到工具与工件电极之间时,极间介质被击穿并形成一个极为细小的放电通道。
放电通道是由数量大体相等的带正电粒子(正离子)和带负电粒子(电子)以及中性粒子(原子或分子)组成的等离子体。
在极间电场作用下,通道中的正离子与电子高速地向阴极和阳极运动并发生剧烈碰撞,从而在放电通道中产生大量的热;同时,阳极和阴极表面分别受到电子流和离子流的高速冲击,动能也转换为热能,在电极放电点表面产生大量的热,整个放电通道形成一个瞬时热源,其温度可达℃以上。
三维微细电火花加工精密运动系统的设计研究

现代 制造技 术 的发 展 , 使学 科交叉 、 合加 工技 复
术 的特点 日益 突出 , 尖端 技术 和产 品 的需 求下 , 在 开 拓新 的加工机 理 , 入 到纳 米 级 和 亚 纳米 级 加 工 精 进 度 是先 进制 造业必 然 的选择 。如今 国外 的微 细 电火 花加工 已步人 工 业应 用 阶段 , 我 国微 细 电火 花 加 而
工 艺・ 备 装
《 电加工与模具}08 20 年第 6 期
三 维微 细 电火 花 加 工 精 密 运 动 系统 的设 计 研 究
林 海 波 '
(1 .台州 职业技 术学 院机 电工 程学 院 , 江 台州 3 8 0 ; 浙 1 0 0
2 ,浙 江工业 大学 机 电工程 学院 , 浙江 杭州 3 0 1 1 0 4)
giswa o nu eee t i p r o mi y tm .Op i z d t p o e sn y t m ’ o r la d b — e y ftmi t lc rc s a k f r ng s se tmie he r c s i g s se S c nto n a sc e hn lgia a a tr e t b ihme t it c oo c lp r me e — sa ls n. Ke r s y wo d :mir c o EDM ; lr — r cso sa e; ir s r t u ta p e iin; t g m c o tucur
微制造系统中的微细电火花加工技术

微制造系统中的微细电火花加工技术*Micro EDM Machining Techn olgy in Micro Manu factu rin g System王振龙赵万生(哈尔滨工业大学)摘要:文章系统地研究和综述了微细电火花加工技术的研究现状和发展趋势,论述了微细电火花加工技术在微三维结构制作及微制造系统中的应用。
关键词:微细电火花加工微制造现代制造技术的发展呈现两大趋势,一是现代制造系统的自动化技术;另一个就是寻求固有制造技术的自身微细加工极限[1]。
微型机械中,特别是其中的敏感器件、控制仪表、动力系统、执行机构等关键器件要使用到大量的微制造技术,如微型机器人、微型工具、微型飞机等。
这些微型机械的需求对现代制造技术提出了新的挑战。
解决这一制造难题的主要途径有两条,一方面是采用微机电系统技术,另一方面是采用微细特种加工技术。
从世界范围的微细加工技术的发展应用而言,欧美等国倾向于硅微结构的制作,即微细电子机械领域;而日本则更注重用传统的加工方法和特种加工方法从宏观尺寸零件的加工向微观尺度的零件加工逼近(如微小齿轮、微小模具、微细轴、孔等)[2,3]。
微机电系统技术是基于半导体平面工艺的一种加工方法,适合于将微传感器、微执行器、信息处理器件集成于一个微小单元。
从工艺角度上看有集成度高、便于大批量生产等优点。
但是这种方法难以加工出真三维曲面形状,也难以处理各种性能卓越的金属材料,特别是一些极限作业环境下所要求的高强度、高韧性、高耐磨、耐高温、耐冲击、抗疲劳等性能,一般单一的半导体材料是很难达到的。
因此其应用范围受到了一定限制。
国外目前采取了微机电系统与微细加工并重的策略,以充分发挥各种加工方法的优点。
由于传统的机械加工过程存在着宏观的切削力,因此在加工微小零件,特别是微米尺度零件时,容易产生变形、发热等问题,精度控制较为困难。
另外,表面容易产生应力而影响产品的使用性能。
特种加工方法采用各种物理的、化学的能量及其各种理化效应,直接去除或增加材料以达到加工的目的。
典型微结构的微细电火花加工
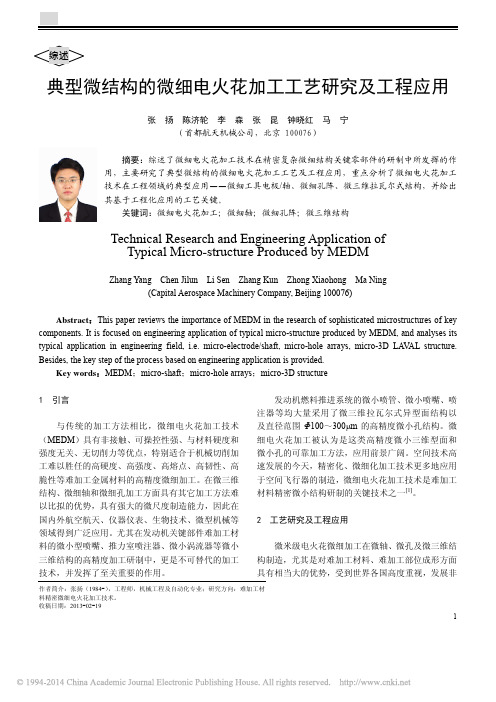
表 4 锥电极粗—半精—精反拷工艺参数
参数
粗反拷加工
半精反拷加工
精反拷加工
开路电压 U/V
200
150
100
电容 C/pF
47000
10000
1000
脉宽 ton/s
2 工艺研究及工程应用
微米级电火花微细加工在微轴、微孔及微三维结 构制造,尤其是对难加工材料、难加工部位成形方面 具有相当大的优势,受到世界各国高度重视,发展非
作者简介:张扬(1984-),工程师,机械工程及自动化专业;研究方向:难加工材 料精密微细电火花加工技术。 收稿日期:2013-02-19
1
2.3 微三维拉瓦尔式异型面结构 微三维拉瓦尔式异型面结构在发动机微小型喷
嘴、喷注器上应用广泛。图 3a 是微三维拉瓦尔式异 型面结构加工样件示意图,材料为钛合金 TC4,其内 壁表面粗糙度要求全部 Ra0.8μm,进口端最大直径为 Φ0.8mm,出口端最大直径为 Φ0.3mm,其喉部直径 仅为 Φ0.16±0.01mm 且要保证光滑过渡。
表 2 EEDG 法粗—精反拷工艺参数
参数
粗反拷加工
精反拷加工
开路电压 U/V
70
25
电容 C/pF
470
0
脉宽 ton/s
20
10
脉间 toff/s
200
150
图 1b 是 Φ0.0317mm 微细轴,长径比为 27。为兼
图 1c 是采用 BEDG 法制作阶梯电极(转速为
顾制备精度和制备效率,采用 BEDG 法作为粗加工, 3000r/min)时的实况照片。图 1d 是锥度为 120°的锥
a 微三维拉瓦尔式异型面结构样件示意图 b 32°锥电极(200×)
微细电火花成形加工关键技术

微细电火花成形加工关键技术西安航空动力控制公司工艺处 胡 磊 张晓东西北工业大学现代设计与集成制造技术教育部重点实验室 吴宝海 罗 明随着未来微型机械的发展壮大,作为一种经济实用的微细加工技术,微细电火花加工受到世界上各国学者的普遍关注和重视。
微细电火花加工技术以其独特的技术优势经几十年的发展已经在微细加工领域取得了较为广泛的应用。
到亚微米级的加工精度及表面粗糙度,因此,必须使单个脉冲的放电能量控制在 10-6~10-7J 数量级之间[3-4]。
由于放电过程中,极间电压一般可视为常数,因此可调整的参数只有放电电流和脉冲宽度。
为满足微细电火花成形加工要求,放电电流一般应不小于数百毫安,而脉冲宽度则应减小到 1μs 左右。
为满足此要求.目前实用的微细电火花成形加工系统一般均采用 RC 弛张式脉冲电源形式。
在此方面的研究中,目前的主要工作集中在如何有效地减小极间杂散电容上,比如采用非金属材料床身结构、使用尽可能短的屏蔽电缆等。
但是RC 电源存在可控性差、电极损耗较大等缺陷。
针对精密微细电火花成形加工发展的需要,国内外已经开展了有关微能电源方面卓有成效的研究工作,并已经形成工业产品。
如山东工业大学开发的可控 RC 微能电源;瑞胡 磊硕士,助理工程师,主要从事数控及特种加工技术研究。
Key Technology of Micro-EDM Forming Machining电火花加工技术是实现难加工材料、复杂零件、模具精密加工和特殊零件加工的有效手段,在机械制造领域中起着越来越重要的作用。
电火花加工由于其非机械接触加工的特点,适应于微型机械制造的要求。
国内外对微细电火花加工技术的不断研究探索[1-2],已使微细电火花加工在与微型机械制造结合及实用化方面取得了较大的进展。
早在 20 世纪 60 年代末,荷兰Philips 研究所Dsenbruggen 等人利用微细电火花成形加工技术成功地加工出了直径30μm,精度为0.5μm 的微孔。
电火花铣削加工
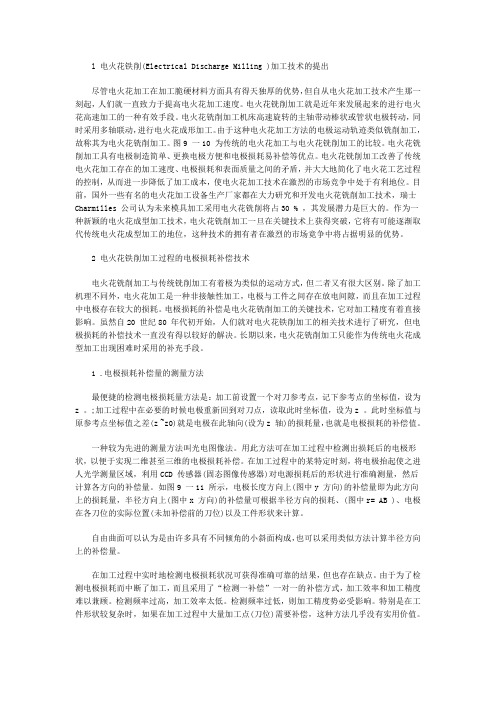
l 电火花铁削(Electrical Discharge Milling )加工技术的提出尽管电火花加工在加工脆硬材料方面具有得天独厚的优势,但自从电火花加工技术产生那一刻起,人们就一直致力于提高电火花加工速度。
电火花铣削加工就是近年来发展起来的进行电火花高速加工的一种有效手段。
电火花铣削加工机床高速旋转的主轴带动棒状或管状电极转动,同时采用多轴联动,进行电火花成形加工。
由于这种电火花加工方法的电极运动轨迹类似铣削加工,故称其为电火花铣削加工。
图9 一10 为传统的电火花加工与电火花铣削加工的比较。
电火花铣削加工具有电极制造简单、更换电极方便和电极损耗易补偿等优点。
电火花铣削加工改善了传统电火花加工存在的加工速度、电极损耗和表面质量之间的矛盾,并大大地简化了电火花工艺过程的控制,从而进一步降低了加工成本,使电火花加工技术在激烈的市场竞争中处于有利地位。
目前,国外一些有名的电火花加工设备生产厂家都在大力研究和开发电火花铣削加工技术,瑞士Charmilles 公司认为未来模具加工采用电火花铣削将占30 % ,其发展潜力是巨大的。
作为一种新颖的电火花成型加工技术,电火花铣削加工一旦在关键技术上获得突破,它将有可能逐渐取代传统电火花成型加工的地位,这种技术的拥有者在激烈的市场竟争中将占据明显的优势。
2 电火花铁削加工过程的电极损耗补偿技术电火花铣削加工与传统铣削加工有着极为类似的运动方式,但二者又有很大区别。
除了加工机理不同外,电火花加工是一种非接触性加工,电极与工件之间存在放电间隙,而且在加工过程中电极存在较大的损耗。
电极损耗的补偿是电火花铣削加工的关键技术,它对加工精度有着直接影响。
虽然自20 世纪80 年代初开始,人们就对电火花铁削加工的相关技术进行了研究,但电极损耗的补偿技术一直没有得以较好的解决。
长期以来,电火花铣削加工只能作为传统电火花成型加工出现困难时采用的补充手段。
1 .电极损耗补偿量的测量方法最便捷的检测电极损耗量方法是:加工前设置一个对刀参考点,记下参考点的坐标值,设为z 。
三维微结构微细电火花和电解组合加工实验研究
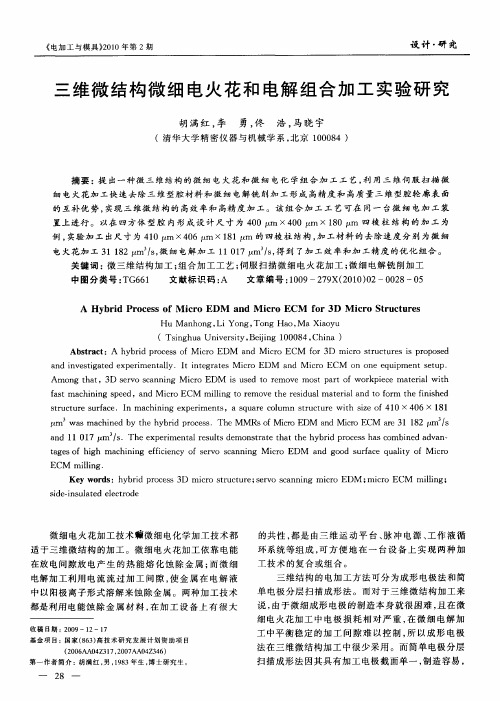
设 计 ・ 究 研
三 维 微 结 构 微 细 电火 花 和 电解 组 合 加 工 实 验 研 究
胡满红 , 李 勇 , 佟 浩 , 晓 宇 马
(清华 大学 精密仪 器与机 械学 系 , 北京 1 0 8 0 0 4)
摘 要 : 出一 种 微 三 维 结 构 的微 细 电 火 花 和 微 细 电 化 学 组 合 加 工 工 艺 , 用 三 维 伺 服 扫 描 微 提 利
ECM li mi ng. l
K e r s:h b i r c s D ir t u t r ; e v c nn n ir y wo d y rd p o e s3 m c o s r c u e s r o s a i g m c o EDM ; ir m co ECM il g; m li n Sd —n 1 a e lcr d ie i s1 t d ee to e 1
(Tsn h aUnv ri , ej g 1 0 8 Chn ) ig u ies y B in 0 0 4, ia t i
Ab ta t sr c :A b i r c s fM ir hy rd p o e so c o EDM n ir a d M c o ECM o f r3D c o s r c u e s p o o e mir t u t r s i r p s d
A b i o e sO ir Hy rd Pr c s f M c o EDM n ir a d M c o ECM 0 D ir tu t r s fr3 M c o Sr cu e
H U M a ho g, n To a M a Xio n n LiYo g, ng H o, a yu
微尺度电火花加工技术的研究与应用

微尺度电火花加工技术的研究与应用电火花加工技术是一种非传统的制造技术,它通过电火花的放电放热效应将工件上的材料加热至熔点或沸点,从而实现去除材料的目的。
微尺度电火花加工技术是电火花加工技术在微小尺度下的应用,具有高精度、高效率和微尺度特点。
本文将对微尺度电火花加工技术的研究与应用进行详细介绍。
首先,微尺度电火花加工技术的研究是为了满足现代制造业中对微细零件加工的需求而进行的。
随着科学技术的不断进步和微电子学、生物医学等领域的发展,对微细零件的需求越来越高。
传统的机械加工方法难以满足这种需求,而微尺度电火花加工技术因其在微尺度下具有高精度、高效率的特点而备受关注。
研究人员通过对微尺度电火花加工机理的深入研究,不断优化加工参数和改进设备,使微尺度电火花加工技术得以应用于微细零件的制造,推动了现代制造业的发展。
其次,微尺度电火花加工技术的应用领域十分广泛。
在微电子学领域,微尺度电火花加工技术被广泛用于芯片、集成电路和MEMS器件等微细零件的加工。
微尺度电火花加工技术能够在高精度下去除微组织表面的氧化层和污染物,确保微细零件的质量和性能。
在生物医学领域,微尺度电火花加工技术被应用于生物芯片、生物传感器的制造,可以实现微细结构的加工、印刷和微阵列的定位等功能。
此外,微尺度电火花加工技术还被用于珠宝、钟表、眼镜和光纤等微尺度零件的制造。
然而,微尺度电火花加工技术在实际应用中还存在一些问题需要解决。
首先,由于微尺度电火花加工是一种高温加工过程,容易引起工件热变形和表面质量问题。
因此,需要通过优化工艺参数和控制放电能量密度等措施来解决这一问题。
其次,微尺度电火花加工技术在加工精度上还有待提高,目前尚难以实现纳米级甚至亚纳米级的加工。
针对这个问题,研究人员正在探索新的电火花放电机制和新的加工方法,以提高微尺度电火花加工技术的加工精度。
为了解决上述问题,研究人员正在开展微尺度电火花加工技术的相关研究。
首先,研究人员通过改进电极材料和加工液等手段来优化微尺度电火花加工工艺参数,以提高加工精度和表面质量。
微细钻削铣削关键技术及应用基础研究

3、质量研究:通过控制原材料质量、优化加工参数等方式,提高加工质量。 在微细钻削铣削中,加工质量受到原材料性能、切削条件、刀具质量等多种因 素的影响。研究这些因素对加工质量的影响规律,有助于实现高质量加工。
参考内容
一、引言
随着科技的发展,制造业对零件的精度和性能要求越来越高,微细加工技术在 此领域中扮演着越来越重要的角色。微细铣削工艺,作为一种典型的微细加工 技术,被广泛应用于各种材料和零件的制造过程中。本次演示将探讨微细铣削 工艺的基础知识和实验研究。
微细钻削铣削关键技术及应用 基础研究
目录
01 引言
03
微细钻削铣削关键技 术
02
微细钻削铣削技术概 述
04 参考内容
引言
微细钻削铣削技术是一种先进的制造工艺,适用于精密零件的加工。随着科技 的不断进步,微细钻削铣削技术在航空、汽车、医疗等领域得到了广泛的应用。 本次演示将围绕微细钻削铣削关键技术及应用基础研究展开讨论,旨在深入探 讨微细钻削铣削技术的优势、关键技术、应用基础研究等方面,为相关领域的 研究和实践提供有益的参考。
2、刀具状态监测
刀具状态监测是微细钻削铣削技术的另一个关键技术。在加工过程中,刀具会 受到磨损、温度、应力等多种因素的影响,这些因素可能影响加工精度和表面 质量。因此,需要对刀具状态进行实时监测,以便在刀具磨损或破损时及时更 换刀具,从而确保加工过程的稳定性和精度。常用的刀具状态监测方法包括直 接监测法和间接监测法两种。
我们也需要加强跨学科合作,借鉴其他领域的最新技术和理论,推动微细加工 技术的发展和应用。
谢谢观看
四、结论与展望
本次演示通过对微细铣削工艺基础和实验研究的探讨,揭示了微细铣削过程中 的主要影响因素和不同材料的加工特性。然而,微细铣削工艺在实际应用中仍 存在许多问题需要解决,如刀具磨损、加工表面粗糙度等。未来,我们需要在 深入研究微细铣削工艺的基础上,通过不断改进和创新,提高微细铣削的加工 效率和精度,以满足制造业对零件精度和性能的更高要求。
微细及小孔电火花加工的关键技术研究的开题报告

微细及小孔电火花加工的关键技术研究的开题报告1. 研究背景微细及小孔电火花加工(Micro-Electrical Discharge Machining,简称Micro-EDM)是一种高精度、高效率、非接触的微细加工技术,可用于加工半导体材料、陶瓷材料、硬质合金材料以及其他难加工材料。
然而,Micro-EDM加工仍存在许多技术瓶颈,特别是在加工大深度、小直径(Diameter<20μm)的细微孔道时,加工效率和精度均面临巨大挑战。
为了解决这些技术难题,需要深入研究Micro-EDM过程的关键技术,提高Micro-EDM加工的效率和精度。
2. 研究目的本研究旨在探究Micro-EDM加工中的关键技术,针对大深度、小直径孔道加工难题,研究并优化Micro-EDM加工参数,提高加工效率和精度,从而为微细及小孔电火花加工技术的发展提供技术支撑。
3. 研究内容(1)Micro-EDM关键技术研究本文将从放电控制方法、电极、工作液以及辅助气体等方面对Micro-EDM关键技术进行研究,探讨各项技术对加工效率和精度的影响。
(2)大深度、小直径孔道加工技术研究本文将研究各项Micro-EDM加工参数对大深度、小直径孔道加工的影响,分析加工过程中的孔道直径误差、加工深度误差等问题,并提出相应的加工优化方案,提高Micro-EDM加工效率和精度。
4. 研究方法(1)理论分析法本文将从Micro-EDM加工过程的放电机理、放电脉冲参数、工作液理论等角度进行理论分析,明确放电控制方法以及其他关键技术。
(2)实验室实验法本文将在微细加工实验中采用一系列微细加工实验,探讨Micro-EDM加工的关键技术和影响因素,进行加工参数优化,提高加工效率和精度。
5. 研究意义研究Micro-EDM加工技术的关键技术,探讨大深度、小直径孔道加工技术优化方案,对提高Micro-EDM加工效率和精度,推动微细及小孔电火花加工技术的发展具有重要意义。
三维微结构微细电火花和电解组合加工实验研究
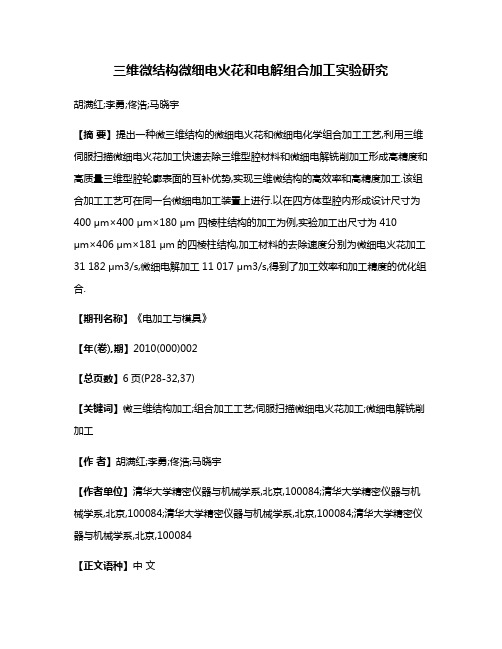
三维微结构微细电火花和电解组合加工实验研究胡满红;李勇;佟浩;马晓宇【摘要】提出一种微三维结构的微细电火花和微细电化学组合加工工艺,利用三维伺服扫描微细电火花加工快速去除三维型腔材料和微细电解铣削加工形成高精度和高质量三维型腔轮廓表面的互补优势,实现三维微结构的高效率和高精度加工.该组合加工工艺可在同一台微细电加工装置上进行.以在四方体型腔内形成设计尺寸为400 μm×400 μm×180 μm四棱柱结构的加工为例,实验加工出尺寸为410μm×406 μm×181 μm的四棱柱结构,加工材料的去除速度分别为微细电火花加工31 182 μm3/s,微细电解加工11 017 μm3/s,得到了加工效率和加工精度的优化组合.【期刊名称】《电加工与模具》【年(卷),期】2010(000)002【总页数】6页(P28-32,37)【关键词】微三维结构加工;组合加工工艺;伺服扫描微细电火花加工;微细电解铣削加工【作者】胡满红;李勇;佟浩;马晓宇【作者单位】清华大学精密仪器与机械学系,北京,100084;清华大学精密仪器与机械学系,北京,100084;清华大学精密仪器与机械学系,北京,100084;清华大学精密仪器与机械学系,北京,100084【正文语种】中文【中图分类】TG661微细电火花加工技术和微细电化学加工技术都适于三维微结构的加工。
微细电火花加工依靠电能在放电间隙放电产生的热能熔化蚀除金属;而微细电解加工利用电流流过加工间隙,使金属在电解液中以阳极离子形式溶解来蚀除金属。
两种加工技术都是利用电能蚀除金属材料,在加工设备上有很大的共性,都是由三维运动平台、脉冲电源、工作液循环系统等组成,可方便地在一台设备上实现两种加工技术的复合或组合。
三维结构的电加工方法可分为成形电极法和简单电极分层扫描成形法。
而对于三维微结构加工来说,由于微细成形电极的制造本身就很困难,且在微细电火花加工中电极损耗相对严重,在微细电解加工中平衡稳定的加工间隙难以控制,所以成形电极法在三维微结构加工中很少采用。
微细电火花三维成型加工系统的研制

由于传统 的机械 加工过 程存 在着宏 观 的切削 力 , 因此在加 工微小零件 ,特别是微 米尺 度零件 时 ,容易 产 生变形 、发热 等问题 ,精 度控 制较 为 困难 。另 外 , 表面容易产生应 力而影 响产品的使用性能 。特种加工 方 法采用 各 种物 理 的 、化学 的能量 及其 各 种理 化 效 应 ,直接 去除或增加材 料 以达 到加工的 目的 。特种加 工方法多属于非接触加工 ,一般没有宏观的切削力作 用 ,因此在微小尺度零件的加工 中有着不可替代 的优
工实验 的条件 ,所 以对加 工系统的主要模块 进行了集 成设计 ,因为运动控制 系统对 整个加 工系统无论在 软 硬件方面都有较 强的功 能支持和开放性 ,所 以整个 加
水平 ,并普 遍提 高 了机 械产 品 的质 量 、性 能 和 竞争 力 。超精 密加 工 已达 到 了纳 米 级 ,甚 至 是亚 纳 米级
( 阳 工业 大学机械 工程 学院 ,沈 阳 102 ) 沈 103
摘要 :设计一 个三维微 细成 型电火花加工系统 ,搭建 了该 系统 的原型样 机 ,并进行 了初步 的加 工实验 。系统 由三维 运
动平 台 、带 间隙伺 服的加工头 、纳秒级脉宽的等脉宽 晶体管脉 冲电源及环境 保障 系统组 成。实验 证明该系统 运行 良好 ,运 动平 台能够达到较高的精度 ,并实现 了简单 的极微细 电火花加 工。
n n y tm. T e ma h n n x r n h w h t h r ttp i i i o d w r ig od r t e sa e c n r a h v r ih p e iin. i g s se h c iige p i e me ts o s t a e p ooy es s n g o o k n r e , h tg a e c e y h g r c s t o
UV-LIGA和微细电火花加工技术组合制造三维金属微结构的研究的开题报告
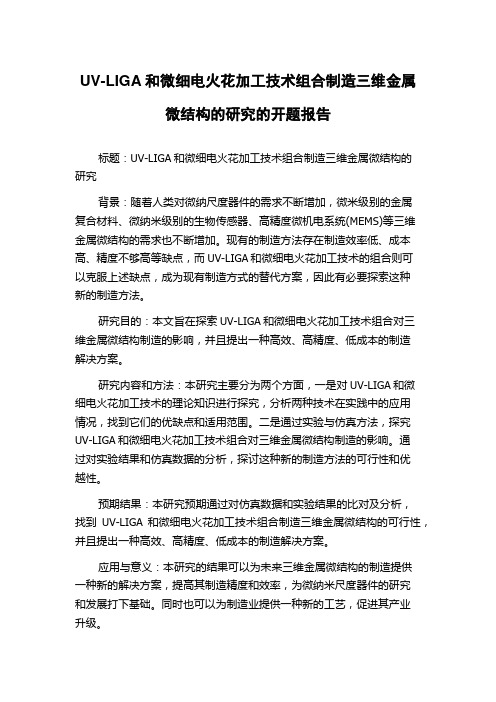
UV-LIGA和微细电火花加工技术组合制造三维金属
微结构的研究的开题报告
标题:UV-LIGA和微细电火花加工技术组合制造三维金属微结构的
研究
背景:随着人类对微纳尺度器件的需求不断增加,微米级别的金属
复合材料、微纳米级别的生物传感器、高精度微机电系统(MEMS)等三维
金属微结构的需求也不断增加。
现有的制造方法存在制造效率低、成本高、精度不够高等缺点,而UV-LIGA和微细电火花加工技术的组合则可
以克服上述缺点,成为现有制造方式的替代方案,因此有必要探索这种
新的制造方法。
研究目的:本文旨在探索UV-LIGA和微细电火花加工技术组合对三
维金属微结构制造的影响,并且提出一种高效、高精度、低成本的制造
解决方案。
研究内容和方法:本研究主要分为两个方面,一是对UV-LIGA和微
细电火花加工技术的理论知识进行探究,分析两种技术在实践中的应用
情况,找到它们的优缺点和适用范围。
二是通过实验与仿真方法,探究UV-LIGA和微细电火花加工技术组合对三维金属微结构制造的影响。
通
过对实验结果和仿真数据的分析,探讨这种新的制造方法的可行性和优
越性。
预期结果:本研究预期通过对仿真数据和实验结果的比对及分析,
找到UV-LIGA和微细电火花加工技术组合制造三维金属微结构的可行性,并且提出一种高效、高精度、低成本的制造解决方案。
应用与意义:本研究的结果可以为未来三维金属微结构的制造提供
一种新的解决方案,提高其制造精度和效率,为微纳米尺度器件的研究
和发展打下基础。
同时也可以为制造业提供一种新的工艺,促进其产业
升级。
微细电火花加工的关键技术分析
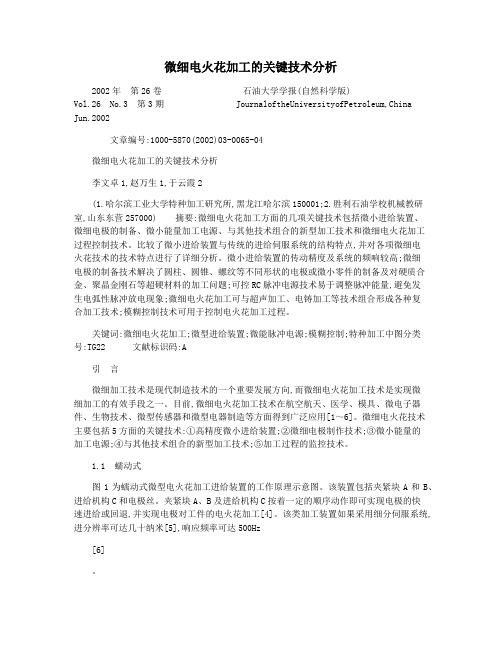
微细电火花加工的关键技术分析2002年第26卷石油大学学报(自然科学版)Vol.26 No.3 第3期JournaloftheUniversityofPetroleum,China Jun.2002文章编号:1000-5870(2002)03-0065-04微细电火花加工的关键技术分析李文卓1,赵万生1,于云霞2(1.哈尔滨工业大学特种加工研究所,黑龙江哈尔滨150001;2.胜利石油学校机械教研室,山东东营257000) 摘要:微细电火花加工方面的几项关键技术包括微小进给装置、微细电极的制备、微小能量加工电源、与其他技术组合的新型加工技术和微细电火花加工过程控制技术。
比较了微小进给装置与传统的进给伺服系统的结构特点,并对各项微细电火花技术的技术特点进行了详细分析。
微小进给装置的传动精度及系统的频响较高;微细电极的制备技术解决了圆柱、圆锥、螺纹等不同形状的电极或微小零件的制备及对硬质合金、聚晶金刚石等超硬材料的加工问题;可控RC脉冲电源技术易于调整脉冲能量,避免发生电弧性脉冲放电现象;微细电火花加工可与超声加工、电铸加工等技术组合形成各种复合加工技术;模糊控制技术可用于控制电火花加工过程。
关键词:微细电火花加工;微型进给装置;微能脉冲电源;模糊控制;特种加工中图分类号:TG22 文献标识码:A引言微细加工技术是现代制造技术的一个重要发展方向,而微细电火花加工技术是实现微细加工的有效手段之一。
目前,微细电火花加工技术在航空航天、医学、模具、微电子器件、生物技术、微型传感器和微型电器制造等方面得到广泛应用[1~6]。
微细电火花技术主要包括5方面的关键技术:①高精度微小进给装置;②微细电极制作技术;③微小能量的加工电源;④与其他技术组合的新型加工技术;⑤加工过程的监控技术。
1.1 蠕动式图1为蠕动式微型电火花加工进给装置的工作原理示意图。
该装置包括夹紧块A和B、进给机构C和电极丝。
夹紧块A、B及进给机构C按着一定的顺序动作即可实现电极的快速进给或回退,并实现电极对工件的电火花加工[4]。
微细电火花铣削电极运动轨迹加工工艺实验
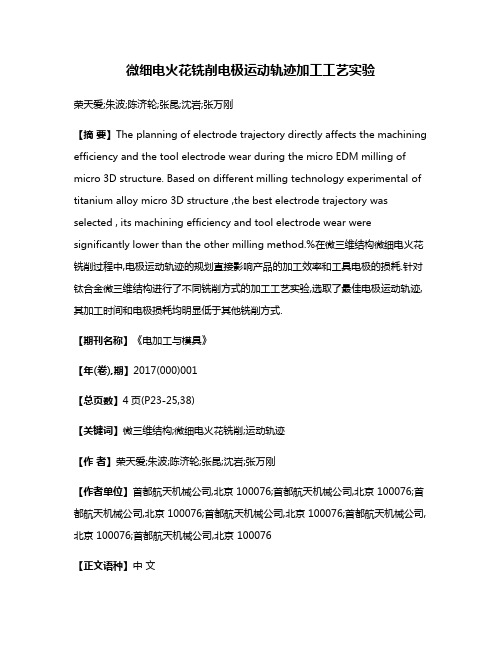
微细电火花铣削电极运动轨迹加工工艺实验荣天爱;朱波;陈济轮;张昆;沈岩;张万刚【摘要】The planning of electrode trajectory directly affects the machining efficiency and the tool electrode wear during the micro EDM milling of micro 3D structure. Based on different milling technology experimental of titanium alloy micro 3D structure ,the best electrode trajectory was selected , its machining efficiency and tool electrode wear were significantly lower than the other milling method.%在微三维结构微细电火花铣削过程中,电极运动轨迹的规划直接影响产品的加工效率和工具电极的损耗.针对钛合金微三维结构进行了不同铣削方式的加工工艺实验,选取了最佳电极运动轨迹,其加工时间和电极损耗均明显低于其他铣削方式.【期刊名称】《电加工与模具》【年(卷),期】2017(000)001【总页数】4页(P23-25,38)【关键词】微三维结构;微细电火花铣削;运动轨迹【作者】荣天爱;朱波;陈济轮;张昆;沈岩;张万刚【作者单位】首都航天机械公司,北京 100076;首都航天机械公司,北京 100076;首都航天机械公司,北京 100076;首都航天机械公司,北京 100076;首都航天机械公司,北京 100076;首都航天机械公司,北京 100076【正文语种】中文【中图分类】TG661传统的电火花成形加工是利用成形工具电极对工件进行“拷贝”加工,其优势体现在复杂、不规则型腔及窄、微、薄结构的加工上[1]。
- 1、下载文档前请自行甄别文档内容的完整性,平台不提供额外的编辑、内容补充、找答案等附加服务。
- 2、"仅部分预览"的文档,不可在线预览部分如存在完整性等问题,可反馈申请退款(可完整预览的文档不适用该条件!)。
- 3、如文档侵犯您的权益,请联系客服反馈,我们会尽快为您处理(人工客服工作时间:9:00-18:30)。
第3期2003年9月 微细加工技术M ICROFABRICAT ION T ECH NOLOGYNo.3Sep.,2003收稿日期:2003O 05O 29基金项目:国家自然科学基金重点资助项目(59935110)作者简介:赵万生(1957-),男,黑龙江人,教授,博士生导师,主要研究方向为特种加工与机电控制技术。
文章编号:1003O 8213(2003)03O 0049O 07微三维结构电火花铣削关键技术研究赵万生,李志勇,王振龙,杨 洋,张 勇(哈尔滨工业大学特种加工研究所,哈尔滨150001)摘要:为解决电火花方法加工微三维结构时工具电极的制备、测量和损耗补偿问题,研究了块反拷法和线电极磨削法(WEDG)相配合的电极加工工艺,设计了通过4点接触感知实现的电极在线测量系统,提出了由数控系统对放电状态进行实时监测、统计并根据统计结果预测电极损耗状况的自动补偿策略。
此技术方案在计算电极加工路径时无需作任何补偿考虑,因此可选用普通金属铣削CAM 软件生成加工代码,特别适合复杂自由曲面微结构的加工。
综合采用此技术设计了专用微细电火花数控系统,制备了直径30L m,长度3mm 的工具电极,使用此电极加工出1mm @0.3mm @0.18mm 的雕塑头像。
关 键 词:微细加工;电火花加工;数控系统中图分类号:T P27 文献标识码:A1 引言在微细加工领域,电火花加工(EDM )是一种制作微小三维结构器件的有效方法。
微细EDM 可加工材料的范围比较广,可加工各种金属、单晶硅、多晶硅等导电材料;与LIGA 工艺相比,不需要昂贵的同步辐射源,设备成本低廉;若采用分层铣削技术,可以加工自由曲面。
日本东京大学的增氵尺隆久、余祖元采用EDM 方法加工了球径为<150L m 的1/8球瓣[1]、0.5mm @0.2mm @0.2mm 的汽车模具[2];比利时鲁文大学采用EDM 方法加工出带力传感器的微钳、长宽1mm 的/庙宇0结构[3];美国Sandia 国家实验室则制作出10mm @10mm @5mm 微型步进电机[4]等等。
这些研究成果显示了微细EDM 方法的重要技术价值和应用前景,为此,各国都非常重视微细EDM 技术及加工设备的开发研制,例如松下精机生产的MG-ED82W 型微细电火花机床可稳定加工直径10L m 微孔和宽度10L m 的槽,在电极直径小于50L m 时可加工孔的深径比为5B 1[5]。
EDM 方法铣削加工微小三维结构与通常情况下的宏观金属铣削有很大不同,首先电火花加工要在线制备刀具)))微细加工电极,零件的尺寸不同,所需制备的电极直径也不同;更重要的是,EDM 加工过程中微细电极损耗极其严重,必须考虑如何实时的进行补偿,而宏观金属铣削一般不需考虑实时的铣刀磨损补偿问题。
因此工具电极的制作方式以及铣削过程中的电极损耗补偿策略是微细EDM系统设计的关键。
2工具电极在线制作与测量方法无论是加工简单的轴、孔或槽缝,还是铣削微三维结构,必须首先制作微细工具电极。
考虑到电极的直径在微米尺度,国内外各种微细EDM机床和试验装置几乎全部采用了在线制作电极的方法,以防止产生二次装卡误差。
加工微细工具电极的方法有块反拷法和线电极磨削法(Wire Electro Disc harge Grind-ing,WEDG)。
二者的主要不同在于块反拷法是使用成型反拷电极块加工工具电极,而WEDG方法是使用连续移动的电极丝。
一般认为,使用WEDG方法加工时线电极与工具电极间为点接触放电,易于实现线电极与工具电极间的微能放电,可控性比较好。
由于线电极的连续移动,不需考虑线电极损耗,获得的工具电极无锥度,可以通过数控程序来加工出圆柱形、削边或棱形电极。
但是WEDG方法中,线电极和工具电极是点接触,放电面积小,加工速度不高。
加工效率偏低这一缺点将直接影响微细EDM机床实用性。
考虑到这一点,我们所研制的微细EDM 机床可以同时采用块反拷法和WEDG法两套电极制备方法。
表1是本文机床的典型电极制备工艺。
初始电极长度3mm,直径0.5 mm,采用RC电源,煤油工作液。
经过一次粗加工至约0.1mm,在距离电极底部0.5 mm处的直径测量值为0.102mm,而在距离电极底部2.5mm处的直径测量值达0.135 mm,可见电极锥度较大。
经过中规准加工至0.05mm,精规准加工至0.03mm,此时在距离电极底部0.5mm处的直径测量值为0.032m m,在距离电极底部2.5mm处的直径测量值为0.035mm,锥度已经基本消除,但精加工时间仅为14min。
此电极可直接用来加工微孔和三维结构,如果需要直径更小的电极,可采用WEDG方法进一步加工,但从表1中可以看到,加工到直径15L m时需要约170min,效率较低。
表1使用块反拷配合W EDG方式的典型工具电极制备工艺加工方法电极材料反拷材料工作液电极初始直径(mm)加工结束电极直径(自底部测量)(mm)0.51 1.5 2.5电容(pF)开路电压(V)加工时间(min)0.50.1020.1150.1240.135400009527块反拷银钨合金铜钨合金煤油约0.10.0430.0480.0510.0565*******约0.050.0320.0340.0350.0354007014W EDG铜钼合金约0.030.0150.0160.016-10065170工具电极的在线测量是微细电极制备过程中必须解决的问题,接触感知测量是一种有效的测量方法。
图1示意了这种方法的原理。
此方法使用一标准圆柱定位规,假定定位规直径为D,在机床坐标系中位置为P (x P,y P),安装并调整使定位规轴线与工具电极回转轴线平行。
测量时,首先粗略估计定位规的位置为P c(x c P,y c P),使电极自点A(x A,y c P)接触感知至点B(x B,y c P),然后图1工具电极的在线测量原理50微细加工技术2003年再使电极自点D(x D,y c P)接触感知至点C(x C,y c P),那么显然有x P=x B+x C2,移动电极至点E(x P,y E),自点E接触感知至点F (x P,y F),然后再使电极自点H(x P,y H)接触感知至点G(x P,y G),由于直线EFGH过定位规圆心,那么电极直径d=y F-y G-D。
使用这种方法的测量误差D为:D=e2g+e2p+e2s(1)其中,e g表示放电间隙,在1L m以内;e p表示由于定位规的轴线不能完全与电极轴线平行而引起的误差;由于接触感知时坐标轴具有一定移动速度,当电极与定位规接触时需要一定减速距离才能停止,显然这将造成电极变形,e s表示由此引起的误差,而e s 往往是引起测量误差的主要因素。
加工不同直径的电极,误差D可以通过比较接触感知测量值和扫描电子显微镜(SEM)实测值获得,据此可标定误差曲线。
从图1可以看到,如果用手动方法来测量电极直径,步骤十分繁琐,因此设计EDM 机床数控系统时引入一条扩展G指令,此指令以定位规直径D,估计位置(x c p,y c p)等为参数可以自动完成测量。
表1中的电极直径即是采用这种方法测量得到的。
3分层铣削电极补偿与控制3.1分层铣削的加工方式与等损耗补偿普通电火花机床的加工方式是使用成型电极在工件上进行拷贝加工,但当工件的尺寸减小到毫米量级之下时,这种加工方式极难实现。
除成型电极不易制作的原因之外,电极尖角、棱边由于放电集中而变钝的现象严重影响形状精度。
借鉴各种快速原型制造方法(RPM)的逐层增材原理,EDM分层铣削的加工方法是使用简单的圆柱或方形电极分层扫描而实现逐层减材。
由于不需制作成型电极,分层铣削现在几乎成为EDM加工微三维构件的唯一方法。
为减小电极损耗对加工精度的影响,人们进行了大量的理论探索和实验研究,端面放电铣削的等损耗模型使用比较广泛[6]。
根据分层厚度的不同,EDM分层铣削时有侧面放电和端面放电两种加工方式,分别如图2a、2b所示。
侧面放电时分层数较少,分层间距大;端面放电时分层间距小于放电间隙,依靠电极底部放电蚀除材料。
图2分层铣削的放电方式端面放电加工电极的损耗仅仅表现为轴向缩短,因此损耗情况比较简单。
端面放电加工的情况如图3所示,假定放电间隙为图3端面放电时的等损耗示意图h g,分层厚度为h l,初始加工位置为位置B,随加工进行,首先电极端部棱角将被损耗倒钝,如位置C所示,如果工具电极没有轴向补偿,那么电极底部圆角将继续损耗,直至最后底部成为平面不再放电,也即发生所谓电极端面等损耗现象,如位置D、E所示。
等损耗电极补偿模型试图引入电极和工件材料的体积损耗比来实现实时的损耗补偿。
为去除厚度h w的工件材料,由于电极51第3期赵万生等:微三维结构电火花铣削关键技术研究损耗,显然有工具电极轴向总进给量H> h w,设电极损耗长度为h t,那么:H=h w+h t(2)假定已知工具电极和工件材料的体积损耗比为常数K,如果工具电极截面积为S t,工件当前加工层截面积为S w,那么有:K=h t#S th w#S w(3)进而可得到电极轴向进给量:H=(1+S w#K/S t)h w(4)于是在设计CAM软件时,对于一个给定的分层厚度h w,可以计算得到对应的Z 坐标进给量H。
在实际应用中,这种补偿策略的不足在于:(1)在不同机床、不同加工规准和不同两极材料的情况下,K显然不同,为得到一个粗略的K值,需要大量工艺实验。
(2)即使上述条件完全相同,当加工零件尺寸不同时,K亦不相同,特别在大深径比加工时,由于蚀除产物排除困难,K将随深度增加成倍增长。
在目前对电火花加工机理仍然有待继续认识的情况下,设计CAM软件时很难在生成数控代码时对K的变化作出精确预测,如果K比实际值偏大,那么Z向将过切。
(3)对于自由曲面来说,若要获得所有分层面上的面积S w,计算量相当巨大。
(4)显然,由于在CAM中需考虑电极损耗,因此不能采用通用的金属铣削CAM软件来生成微细EDM的分层铣削代码。
这在很大程度上影响微细EDM铣削的实用性。
由于以上几点,等损耗补偿模型的使用受到了一定限制,仅仅适用于有限的场合如简单的矩形型腔、球体的加工等等。
为实现一般情况下的自由曲面铣削加工,本文引入了一种基于放电状态统计的方法,来实现电极的损耗补偿。
3.2电火花铣削加工的放电状态统计规律微细EDM加工的放电状态由正常放电、短路、开路几种状态组成,由于工具电极的高速旋转,微细EDM只在深微孔加工中才会发生稳定拉弧。
若在单位时间T内,检测系统检测到正常放电状态、短路、开路次数分别为d n、d s和d o,那么可以定义开路率为:r=d od n+d s+d o@100%(5)图4是端面放电时伺服系统记录的开路率和平均进给速度变化曲线。