烂钢分析[1]
钢铁化学分析方法1

一、钢铁化学分析方法铸铁中七元素的联合测定一、试剂(溶解样品)1、溶解混合酸:硫酸50毫升,硝酸8毫升,加入水中并稀至1升。
2、过硫酸铵:15%当天配制。
3、过氧化氢:3% 。
二、溶样方法称取试样0.5克于250毫升锥形瓶中,加溶解混合酸85毫升及过硫酸铵溶液10毫升,加热溶解完毕后(约15分钟),再加过硫酸铵溶液10毫升,煮沸2—3分钟,使锰呈褐色二氧化锰析出后,滴加过氧化氢使褐色沉淀澄清且过量一滴,继续煮沸1分钟,流水冷却至室温,将溶液稀至100亳升后仍倒入原锥形瓶中,并以快速干滤纸过滤于干的100毫升容量瓶中,供下述各元素测定之用。
注:1、日常分析中为加快溶解度可将溶解酸预热后加入。
2、加入溶解酸后应立即加入过硫酸铵,防止磷呈磷化氢逸出,使磷结果偏低。
硅的测定一、试剂1、钼酸铵溶液:5% 。
2、草酸溶液:5% 。
3、硫酸亚铁铵溶液:6% [每1升中需有(1:1)硫酸5毫升]。
4、定硅补充酸:取溶解混合酸100毫升,以水稀至1升即可。
二、分析方法于150毫升锥形瓶中预置补充酸30毫升,用1毫升刻度移液管吸取试样溶液1毫升,加入钼酸铵溶液5毫升,放置10—15分钟后,加入草酸溶液10毫升,硫酸亚铁铵5毫升。
以水为比较液,以波长650µm,0.5厘米比色皿测定消光值。
三、计算带一标准样品按同样操作后换算,或用标准样品绘制标准曲线。
注:1、加入钼酸铵溶液后的放置时间应随室温变化而变化,室温低于10℃应放置半小时,夏天则需放置5分钟即可。
2、加草酸后应立即加入硫酸亚铁铵,并边摇边加。
锰的测定一、试剂1、定锰混合酸:磷酸30毫升,硝酸60毫升,加入水中,加入硝酸银2克,溶解后以水稀至1升。
2、过硫酸铵溶液:15%当天配制。
二、分析方法于50亳升锥形瓶中预置定锰混合酸10毫升及过硫酸铵溶液5毫升,吸取试样溶液5毫升,加热煮沸1分钟,流水冷却至室温,以水稀至50毫升。
以水为参比液,以波长530 µm,2厘米比色皿测定消光值。
轧钢质量缺陷、产生原因心得

轧钢质量缺陷、产生原因心得
轧钢产生质量缺陷这一问题,我对此有所体会。
我认为轧钢质量缺陷产生的原因主要是:
1.板坯加热制度不合理或加热操作不当生成较厚且较致密的铁皮,除鳞时难以除尽,轧制时被压入钢板表面上。
2.由于高压除鳞水压力低、水咀堵塞、水咀角度安装不合理或操作不当等原因,使钢坯上的铁皮未除尽,轧制时被压入到钢板表面上。
3.氧发生较多,含硅化铁皮在沸腾钢中较高的钢中易产生红铁皮。
4.轧辊表面粗糙。
5.辊形曲线不合理,轧辊磨损不均匀。
6.压下量分配不合理。
7.轧辊辊缝调整不良或轧件跑偏。
8.轧辊冷却不均。
9.轧件温度不均。
10.卷取机前的侧导板开口度过小等。
11.板坯上原有的裂缝、针状气孔等缺陷未清理干净,轧制后残
留在轧件表面上。
12.含铜钢因加热温度控制不当,易产生网裂。
13.因轧辊受热不均、冷却不当及疲劳破坏等,造成轧辊产生裂纹,轧制后在轧件表面上呈凸起的龟纹。
对于轧钢质量问题我总结出以上可能造成的原因,我相信,只要合理规避这些问题,就能很好地解决轧钢质量缺陷的问题。
高强钢切边过程中的缺陷问题分析与解决
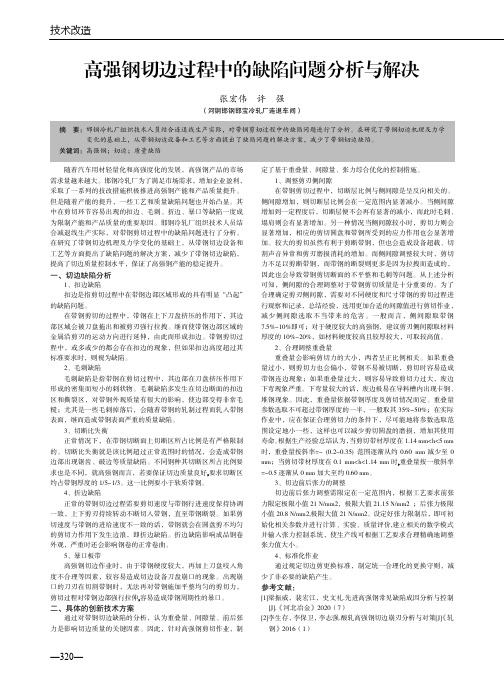
技术改造—320—高强钢切边过程中的缺陷问题分析与解决张宏伟 许 强(河钢邯钢邯宝冷轧厂连退车间)随着汽车用材轻量化和高强度化的发展,高强钢产品的市场需求量越来越大。
邯钢冷轧厂为了满足市场需求,增加企业盈利,采取了一系列的技改措施积极推进高强钢产能和产品质量提升。
但是随着产能的提升,一些工艺和质量缺陷问题也开始凸显。
其中在剪切环节容易出现的扣边、毛刺、折边、暴口等缺陷一度成为限制产能和产品质量的重要原因。
邯钢冷轧厂组织技术人员结合减退线生产实际,对带钢剪切过程中的缺陷问题进行了分析。
在研究了带钢切边机理及力学变化的基础上,从带钢切边设备和工艺等方面提出了缺陷问题的解决方案,减少了带钢切边缺陷,提高了切边质量控制水平,保证了高强钢产能的稳定提升。
一、切边缺陷分析1、扣边缺陷扣边是指剪切过程中在带钢边部区域形成的具有明显“凸起”的缺陷问题。
在带钢剪切的过程中,带钢在上下刀盘挤压的作用下,其边部区域会被刀盘拖出和被剪刃强行拉拽。
继而使带钢边部区域的金属沿剪刃的运动方向进行延伸,由此而形成扣边。
带钢剪切过程中,或多或少的都会存在扣边的现象,但如果扣边高度超过其标准要求时,则视为缺陷。
2、毛刺缺陷毛刺缺陷是指带钢在剪切过程中,其边部在刀盘挤压作用下形成的密集而短小的刺状物。
毛刺缺陷多发生在切边断面的扣边区和撕裂区,对带钢外观质量有很大的影响,使边部变得非常毛糙;尤其是一些毛刺掉落后,会随着带钢的轧制过程而轧入带钢表面,继而造成带钢表面严重的质量缺陷。
3、切断比失衡正常情况下,在带钢切断面上切断区所占比例是有严格限制的。
切断比失衡就是该比例超过正常范围时的情况,会造成带钢边部出现锯齿、破边等质量缺陷。
不同钢种其切断区所占比例要求也是不同,就高强钢而言,若要保证切边质量良好,要求切断区约占带钢厚度的1/5~1/3。
这一比例要小于软质带钢。
4、折边缺陷正常的带钢切边过程需要剪切速度与带钢行进速度保持协调一致,上下剪刃持续转动不断切入带钢,直至带钢断裂。
典型钢材失效分析案例详解
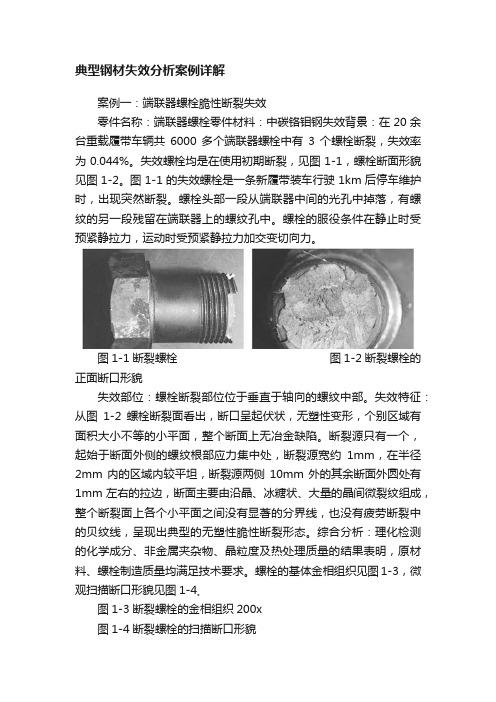
典型钢材失效分析案例详解案例一:端联器螺栓脆性断裂失效零件名称:端联器螺栓零件材料:中碳铬钼钢失效背景:在20余台重载履带车辆共6000多个端联器螺栓中有3个螺栓断裂,失效率为0.044%。
失效螺栓均是在使用初期断裂,见图1-1,螺栓断面形貌见图1-2。
图1-1的失效螺栓是一条新履带装车行驶1km后停车维护时,出现突然断裂。
螺栓头部一段从端联器中间的光孔中掉落,有螺纹的另一段残留在端联器上的螺纹孔中。
螺栓的服役条件在静止时受预紧静拉力,运动时受预紧静拉力加交变切向力。
图1-1断裂螺栓图1-2断裂螺栓的正面断口形貌失效部位:螺栓断裂部位位于垂直于轴向的螺纹中部。
失效特征:从图1-2螺栓断裂面看出,断口呈起伏状,无塑性变形,个别区域有面积大小不等的小平面,整个断面上无冶金缺陷。
断裂源只有一个,起始于断面外侧的螺纹根部应力集中处,断裂源宽约1mm,在半径2mm内的区域内较平坦,断裂源两侧10mm外的其余断面外圆处有1mm左右的拉边,断面主要由沿晶、冰糖状、大量的晶间微裂纹组成,整个断裂面上各个小平面之间没有显著的分界线,也没有疲劳断裂中的贝纹线,呈现出典型的无塑性脆性断裂形态。
综合分析:理化检测的化学成分、非金属夹杂物、晶粒度及热处理质量的结果表明,原材料、螺栓制造质量均满足技术要求。
螺栓的基体金相组织见图1-3,微观扫描断口形貌见图1-4。
图1-3断裂螺栓的金相组织200x图1-4断裂螺栓的扫描断口形貌查找生产作业,发现当初螺栓拧紧装配时,实际拧紧力矩远大于设计规定的力矩。
为对比分析,取9枚螺栓实物(8枚已使用无问题的螺栓,1枚未使用螺栓),进行强断拉伸试验。
螺栓拉伸试验断口的断裂源也同样位于一侧螺纹根部应力集中处,属于线断裂源,断口形貌平齐,见图1-5。
断口微观形貌见图1-6。
两种断口形貌对比见表1-1。
图1-5合格螺栓断口形貌(一) 图1-6合格螺栓断口形貌(二)表1-1两种断口形貌对比断口 失效件断口 无问题实物断口断口典型 形貌 断裂源附近的断面主要为沿晶断裂,呈冰糖 状,无明显塑性变形,还有少量韧窝。
Q235B钢板冷弯开裂原因分析及预防措施

Q235B钢板冷弯开裂原因分析及预防措施摘要:2011年初,临钢生产的12~40 mm厚钢板在冷弯时发生开裂现象。
在开裂部位取样分析发现钢板开裂主要原因是钢中存在带状偏析和硫化物、硅酸盐夹杂过多阻断了钢基体的连续性,导致受力断裂。
通过采取适当措施可以减少夹杂物的产生。
2011年1~3月份,山西新临钢钢铁有限公司(全文临钢)生产的产品共发生26起质量异议,其中因Q235B冷弯加工裂纹开裂11起,占42.3%。
裂纹开裂见图1。
1 Q235B钢板检验结果1.1钢板氧、氮、磷、硫含量情况(见表1)从分析结果来看,钢板氧含量较高。
1.2 Q235B质量异议取样分析结果(见表2)从成分对比情况看,两次分析结果存在一定差异,但偏差不大,在同一钢种成分范围内。
出现偏差与取样位置、成分出现偏析等原因有关。
经市场调研,临钢Q235B成分与国内其他19家钢厂(质量证明书)的差别,碳质量分数:临钢平均为0.17%,其他厂在0.15%以上(平均为0.16%),临钢基本持平;硅质量分数:临钢平均为0.18%,其他厂家平均为0.22%,临钢略低;锰质量分数:临钢平均为0.44%,其他厂家平均为0.61%,临钢明显偏低;磷质量分数:临钢平均为0.025%,其他厂家磷质量分数平均为0.018%,临钢高;硫质量分数:临钢平均为0.027%,其他厂家平均为0.013%,临钢高。
1.3 夹杂物检验情况(见表3)从所取试样的整体检验情况分析,试样都存在较严重的硫化物分布。
在距离表皮1~2 mm处,硫化物夹杂很少,距离表面约6~7 mm处,硫化物夹杂开始增多,到中心处最为严重。
1.4金相分析结果从金相分析结果和夹杂物的评级上看,试样硫含量偏高;硅酸盐夹杂物含量较高,尺寸较大,但晶粒度与正常试样区别不明显,夹杂物沿轧制方向与铁素体和珠光体呈带状分布(见图2)。
1.5电镜分析结果有的试样断口表面有黄色氧化铁,微观断口以脆性断裂为主;试样宏观断口上有夹杂存在,微观断口形貌为韧性断裂;有的钢板断面上有空洞缺陷,应该为钢板中存在疏松或中间裂纹。
钢材公司质量分析报告
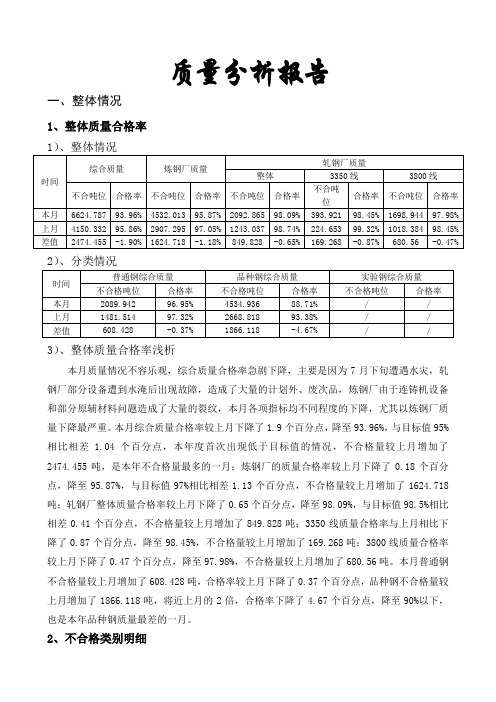
质量分析报告一、整体情况1、整体质量合格率1)、整体情况2)、分类情况3)、整体质量合格率浅析本月质量情况不容乐观,综合质量合格率急剧下降,主要是因为7月下旬遭遇水灾,轧钢厂部分设备遭到水淹后出现故障,造成了大量的计划外、废次品,炼钢厂由于连铸机设备和部分原辅材料问题造成了大量的裂纹,本月各项指标均不同程度的下降,尤其以炼钢厂质量下降最严重。
本月综合质量合格率较上月下降了1.9个百分点,降至93.96%,与目标值95%相比相差 1.04个百分点,本年度首次出现低于目标值的情况,不合格量较上月增加了2474.455吨,是本年不合格量最多的一月;炼钢厂的质量合格率较上月下降了0.18个百分点,降至95.87%,与目标值97%相比相差1.13个百分点,不合格量较上月增加了1624.718吨;轧钢厂整体质量合格率较上月下降了0.65个百分点,降至98.09%,与目标值98.5%相比相差0.41个百分点,不合格量较上月增加了849.828吨;3350线质量合格率与上月相比下降了0.87个百分点,降至98.45%,不合格量较上月增加了169.268吨;3800线质量合格率较上月下降了0.47个百分点,降至97.98%,不合格量较上月增加了680.56吨。
本月普通钢不合格量较上月增加了608.428吨,合格率较上月下降了0.37个百分点,品种钢不合格量较上月增加了1866.118吨,将近上月的2倍,合格率下降了4.67个百分点,降至90%以下,也是本年品种钢质量最差的一月。
2、不合格类别明细1)、按浇铸形式由上表可见:过连铸产品质量较差,占总不合格量的98.16%,模铸产品占1.84%,较上月下降了3.38个百分点,本月在生产模铸产品时加强了过程工艺控制,对模铸产品从炼钢到轧钢逐炉、逐批跟踪工艺,使得模铸产品质量好转,模铸不合产品主要是内部质量较差,主要是探伤不合,本月出现的7批不合格品,有5批是探伤不合,另外包括1批长不合,1批性能不合。
Q345钢性能分析综合报告1

Q345钢性能分析综合报告摘要本次实验采用埋弧焊中不开坡口对接接头悬空双面焊的方法将两块均为9.5mm的Q345钢板对接。
用手工锯的方法切取焊接接头金属试样,试样尺寸为⨯⨯。
将切取的试样在砂轮机上粗磨,并将四周倒成圆角。
再399.527mm mm mm将试样在1至6号砂纸上进行细磨。
经细磨后的试样,用清水冲洗以除去磨粒,再进行机械抛光。
然后,将抛光后的试样用4%的硝酸酒精溶液浸蚀10~15s,再用酒精擦拭浸蚀部位,用吹风机吹干试样。
最后将制备好的试样放在金相显微镜上观察并拍摄焊接接头不同部位的照片,并用维氏硬度计测量焊接接头不同部位的硬度。
在拍摄焊接接头不同部位显微组织的照片之前,先拍摄接头宏观组织,直观观察和分析接头宏观缺陷、焊缝成形以及焊缝金属结晶方向。
根据拍摄到的焊接接头母材、焊缝和焊接热影响区的显微组织的照片分析焊缝的结晶形态、焊接热影响区金属的组织变化和焊接接头的微观缺陷等。
在维氏硬度计上测定焊接接头母材、焊缝和焊接热影响区的硬度。
根据硬度值在不同区域内的变化可大概知道不同区域的组织与硬度的关系。
根据硬度与不同组织的对应关系,分析得到热影响区的晶粒长大,引起该区的强度、硬度增大,该区的塑性、韧性降低。
母材与焊缝硬度接近,基本满足等强匹配的原则。
其中,热影响区硬度最高,是接头的薄弱环节。
关键词:显微组织分析,维氏硬度,金相试样制备,埋弧焊1、实验过程简述实验过程中,采用埋弧焊中不开坡口对接接头悬空双面焊的方法将两块均为9.5mm的Q345钢板对接。
待钢板冷却,用手工锯的方法切取焊接接头金属试样,试样尺寸为399.527⨯⨯。
随后,用切取的试样制备金相样品。
切取的mm mm mm试样表面凹凸不平极为粗糙,需要在砂轮机上进行粗磨,将试样四周倒成圆角,以免在细磨或抛光时撕裂砂纸或抛光布。
再将试样在1至6号砂纸上进行细磨。
经细磨后的试样,用清水冲洗以除去磨粒,再进行机械抛光。
然后,将抛光后的试样用4%的硝酸酒精溶液浸蚀10~15s,再用酒精擦拭浸蚀部位,用吹风机吹干试样。
钢结构脆性破坏事故分析(1)

工程事故分析钢结构脆性破坏事故分析王元清(清华大学土木工程系 100084) 钢结构的破坏通常可分为塑性和脆性两种形式。
其中脆性破坏是结构极限状态中最危险的破坏形式之一,这主要由于它的发生往往很突然、没有明显的塑性变形,而且构件破坏时的承载能力很低,带来的损失也十分惊人。
1 钢结构脆性事故的原因分析钢结构,特别是焊接钢结构受材料性质、加工工艺等方面因素影响,不可避免地存在各种缺陷,加之使用条件的不利作用(如超载、低温、动载等),易发生各类事故。
而在钢结构的事故中,脆性破坏占相当大的比例。
文献[5]给出了钢结构事故中各种破坏类型所占的比例(见表1)。
可见,有必要深入开展钢结构的脆性破坏方面的研究。
表1 钢结构各破坏类型在工程事故中所占的百分比破坏类型1951~197759起事故1951~195969起事故1950~1975100起事故整体或局部失稳224441母材破坏 塑性破坏脆性破坏62717814钢材的疲劳破坏1653(考虑焊缝)焊接连接的破坏152624螺栓连接的破坏43其它类型破坏1087早在1971年国际焊接协会(International Insti-tute of W elding)就对60个焊接钢结构脆性破坏实例进行了统计分析[1],并根据所占比例总结出14个最主要的影响因素(参见表2)。
其中每个脆性破坏的实例并不是由单一因素引起的,而是多个因素共同作用的结果,所以表中列举的实例总数不是60个,而是126个。
表2 国际焊接协会对焊接钢结构脆性破坏的实例统计分析结果序号影响因素实例数 百分比1钢材对裂纹的敏感性2620.62结构构造缺陷1814.33构件的焊接残余应力1713.54钢材冷作与变形硬化1411.15疲劳裂纹97.26其它焊缝缺陷97.27结构工艺缺陷97.28结构超载8 6.39构件的热应力6 4.810焊接热影响区的裂纹3 2.411钢材的热处理3 2.412焊缝的裂纹2 1.613钢材的冷加工10.714腐蚀裂纹10.7总 计126100.0 作者在留学期间曾对前苏联223个工程中发生的350个钢结构脆性破坏实例进行了统计分析[2]。
热轧带钢的表面缺陷分析1
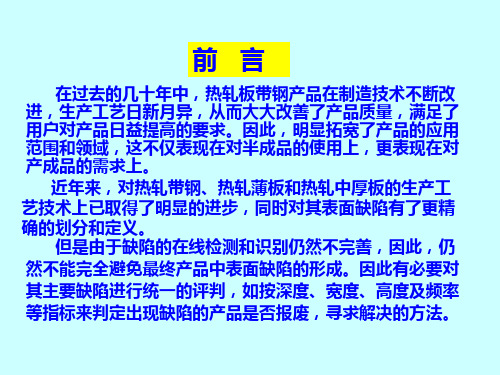
鉴别
在表面检查过程中用肉眼即可辨别。 在有氧化铁皮的带钢上往往难于识别压入 氧化铁皮。当酸洗或喷砂处理后,这种缺陷会 以表面凹陷的形式显现出来,有时与未除净的 残余氧化铁皮一起出现。
成
因
可能误判
如果是轻度的话,可能会将一次氧化铁皮压 入同二次氧化铁皮压入相混淆。
压入的氧化铁皮来自加热炉或粗轧中未 除净的氧化铁皮。
成因
定义与外观
边裂是垂直于表面且贯穿整个板带厚度 的位于边部的裂纹,在厚板轧制时,也 会出现于轧件头尾。 边裂易出现在连铸方坯或板坯轧制过程, 也会出现在冷却过程。这类缺陷形成的更进 一步原因在于材料边部的局部区域受到超过 其强度极限的应力。
鉴别
在表面检查过程中用肉眼即可辨别。
可能误判
会与边部过烧(热脆性)混淆。
鉴别
在表面检查过程中用肉眼即可辨别。如果缺 陷很轻微,则轧件在酸洗后,可更容易看到。
可能误判
气孔可能与带状表面夹层混淆。
表面夹层
Shell (Peel, scab, slivers, surface lamination)
定义与外观
材料搭叠区域为表面夹层,其形状和大小
成因
轧制表层含有大量非金属夹杂的坯 料时会产生表面夹层。这些夹杂在轧制 过程中被破碎而形成夹层状折叠。坯料 表面划伤也会产生表面夹层。
气孔
Pitting (Pores, voids, pits)
定义与外观
气孔是坯料近表面细小的气体夹杂。根据 不同的变形程度,这些细小气体夹杂在轧制 过程中被拉长,并露出表面,在厚板中则以 凸透镜状的气泡出现。在热轧带钢中,气孔 通常在除鳞后以亮条纹的形式出现。
成因
气孔是钢在浇注与凝固过程中因气 体含量高而形成的。有时,气孔可被氧 化并充满氧化铁皮,此时,根据不同钢 种,在坯料加热时可能引起一定程度的 脱碳。
棒材冷床乱钢、头尾弯钢现象分析及性能优化

•酒钢科技2019年第3期•棒材冷床乱钢、头尾弯钢现象分析及性能优化梁新建,康开军(酒钢集团宏兴股份公司炼轧厂,甘肃,嘉峪关,735100)摘要:通过对大棒线棒材冷床乱钢、头尾弯钢现象分析及改进,介绍涉及冷床乱钢、头尾弯钢的诊断思路、步骤及运行机理,并对此类故障现象进行了诊断与分析,提高设备运行稳定性及工艺控制指标。
简单介绍冷床乱钢、头尾弯钢现象控制技术。
关键词:冷床;乱钢;头尾弯钢;改进措施;性能优化Analysis and Performance Optimization of Bar Chaos and Head-tailBending at Bar Cooling BedLiang Xinjian,Kang Kaijun(Steel-making and Rolling Plant of Hongxing Iron&Steel Co.Ltd..Jiuquan Iron and Steel(Group)Corporation,Jiayuguan,Gansu,735100)Abstract::Through the analysis and improvement of bar chaos and head-tail bending at cooling hed,the diagnosis ideas,steps and operation mechanism of the phenomenon are introduced.The diagnosis and analysis of such fault phenomena were carried out to improve equipment operation stability and process control indicators.Its control technology is introduced Briefly.Key words:cooling bed;bar chaos;head-tail bending;improvement measures;performance optimization1«•*刖g酒钢集团宏兴钢铁公司炼轧厂大棒线作业区设计能力年产100万吨。
钢管等钢材的钢的低倍组织缺陷识别及解决方法

钢管等钢材的钢的低倍组织缺陷识别及解决方法钢管等钢材的钢的低倍组织缺陷识别及解决方法借助肉眼或借助低倍放大镜,可以观察到棒料、盘条及坯料上存在的疏松、偏析、气泡和缩孔残余、夹杂、白点等明显缺陷,把这种宏观检查出的缺陷称之为钢的低倍组织缺陷。
目前钢材的质量检查和判定,尽管有先进的仪器设备和方法,但因为低倍组织缺陷检查的简单和直接,依然在生产实践中被广泛应用。
最新颁布的新国标GB/T226-2015《钢的低倍组织及缺陷酸蚀检验法》和GB/T1979-2001《结构钢低倍组织缺陷评级图》等就是用来指导宏观检验的。
以下对常见钢的低倍组织缺陷的识别、产生原因、对钢的性能影响及消除方法进行粗浅地阐述。
1.疏松。
疏松是钢在致密性方面的缺陷。
一般发生在钢锭的上部及中部,这些地方集中了较多的杂质和气体造成的孔隙,试样经酸浸后这些杂质和孔隙为酸液溶解和侵蚀,扩大成许多洞穴。
在横向试样上,如果疏松分布在整个截面上,称之为一般疏松;如果集中在钢材中心相当于钢锭最后结晶的等轴晶区,称之为中心疏松。
形成疏松的主要原因是钢中的低熔点杂质和气体。
在形成钢液过程中,由于体积收缩和气体析出会形成树枝状的晶间空隙和显微孔隙,如果钢液中的杂质聚积在其中,而未被钢液填充,则造成组织的不致密性。
防止钢材产生严重疏松的办法,主要是要减少钢中的杂质和气体。
2.偏析。
偏析是钢在均匀性方面的缺陷,在碳素结构钢和合金钢中均可见到。
钢的试样经酸浸后的偏析一般有树枝状、方框型、点状偏析,当今随着冶炼技术的提高,点状偏析已极少发现。
树枝状偏析多数情况是浇注温度过高和冷却缓慢所致。
在钢液凝固结晶过程中,首先形成树枝状晶轴。
然后在一次晶轴上沿一定角度长出二次晶轴,再派生出三次、四次形同树枝状的晶轴,液体逐渐占据枝晶空隙填满到结晶结束,于是就构成了树枝状晶轴与晶粒之间成分的不均匀性。
当树枝状偏析非常严重时,会严重恶化钢的机械性能。
方框型偏析与碳的偏析产生铁素体和珠光体多少有关,由于铸锭结晶时,在柱状晶的末端与锭心等轴晶区之间聚积较多杂质和孔隙而形成。
钢热处理十种组织缺陷分析及对策

钢热处理十种组织缺陷分析及对策钢的力学性能、物理性能和化学性能决定钢的热处理组织。
正常组织赋予钢优异性能;组织缺陷恶化钢的性能,降低产品质量和使用寿命,甚至发生事故。
钢热处理主要有十种组织缺陷.分析原因,采取对第,有显著技术经济效益。
一、奥氏体晶粒粗大钢奥氏体晶粒定为13级,一级最粗,13 级最细。
晶粒愈细,强韧性愈佳,淬火得到隐晶马氏体;晶粒禽粗,强韧性愈差、脆性大,淬火得到粗马氏体。
实践证明.奥氏体形成后,随着温度升高和长时间保温,奥氏体晶粒急剧长大当加热温度一定时,快速加热奥氏体晶粒细小;慢速加热,奥氏体晶粒粗大奥氏体晶粒随钢中含C、Mn元素增加而增大,随钢中含W、Mo、V元素增加而细化。
钢最终淬火前未经预处理,奥氏体晶粒易粗化,淬火得到粗马氏体,强韧性低,脆性大。
晶粒粗化,降低晶粒之闻结合力,力学性能恶化。
对策——合理选择加热温度和保温时间。
加热温度过低,起始晶粒大,相转变缓慢;加热温度过高,起始晶粒细,长大倾向大,得到粗大奥氏体晶粒。
加热温度应按钢的临界温度确定,保温时间接加热设备确定。
合理选择加热速度,根据过热度对奥氏体形核率和长大速率影响规律,采用快速加热和瞬时加热方法细化奥氏体晶粒,如铅浴加热、盐浴加热、高频加热、循环加热、激光加热等。
淬火前预处理细化奥氏体晶粒,如正火、退火、调质处理等。
选用细晶粒钢和严格控温等措施。
二、残余奥氏体量过多钢件淬火后过冷奥氏体已转变成淬火马氏体.未完全转变者为残余奥氏体。
残余奥氏体在回火过程可部分转变成马氏体,但因材料与工艺不同,残余奥氏体可多可少保留在使用状态中。
保留少量残余奥氏体有利增加强韧性、松驰残余应力、延缓裂纹扩展、减少变形等。
但过量残余奥氏体将降低钢的硬度、耐磨性、疲劳强度、屈服强度、弹性极限和引起组织不稳定,导致使用时发生尺寸变化等不利因素。
园此,残余奥氏体含量不宜过多。
高合金钢中有大量降低Ms点的台金元素,会增加淬火钢残余奥氏体量,如高速钢淬火后残余奥氏体量高达50%以上;过高的淬火加热温度会使钢中C和合金元素大量溶入高温奥氏体中,提高了台金化奥氏体稳定性,不易发生马氏体相变,保留在淬火组织中,增加残余奥氏体量;等温淬火较普通淬火残余奥氏体量多;淬火冷却速度慢,残余奥氏体量多等。
2008冰雪灾害对钢结构工程破坏案例分析_(1)
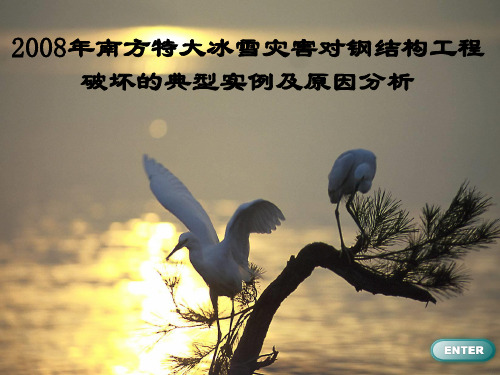
二、结构选型、计算简图不合理 1、许多门式刚架的中柱都是按照摇摆柱设计的,但是 实际的构造却没有做到铰接,而是一种半刚性连接,这 样便会导致中柱顶部承受巨大弯矩而破坏。
2、一些变截面构件的设计不合理,刚度突变太大,在 刚度突变处容易产生破坏。
3、檩条设计未考虑扭转,但因为屋面荷载并未通过檩 条的剪切中心,所以会使檩条产生扭转。
一:输电塔及通信塔在本次雪灾中的破坏 二:门式刚架轻型房屋在本次雪灾中的破坏 三:桁架及网架结构在本次雪灾中的破坏
输电塔及通信塔在本次雪灾中的破坏:
受严重冰雪灾害影响,南方各省多处高压输电塔及移 动通信塔倒塌。铁塔的破坏情况基本上都是从中间弯倒, 塔颈部发生扭折,角钢断裂,下半截还正常,上半截从中 间耷拉。
厂 房 垮 塌
厂 房 垮 塌
厂房垮塌
屋面垮塌
刚架垮塌
刚架垮塌
刚架垮塌
檩条挠曲
柱脚拔出
梁柱扭曲
梁柱扭曲
钢梁挠曲
桁架及网架结构在本次雪灾中的破坏
本次雪灾中钢桁架及网架结构破坏的主要原因还是因 为雪荷载过大,超出规范规定的荷载取值,以至结构构件 在过大雪载作用下挠曲严重,甚至扭曲,从而引起结构的 局部垮塌或整体垮塌。
桁架变形
桁架变形
桁架变形
桁架变形
桁架变形
桁架垮塌
桁架垮塌
桁架垮塌
桁架垮塌
桁架垮塌
事故发生的原因是多方面的,虽然特大冰雪,冻雨是 偶然性的诱发因素,但是设计、制作、安装等过程中所留 下来的安全隐患却是事故发生的内在原因。
一、设计条件与实际不符合 1、根据有关人员的实地测量数据,本次南方冰雪灾害 中屋面雪荷载达到70-120kg/m2,这就造成了设计荷载 与实际荷载的较大差值,从而也就给结构留下了较大的 安全隐患。 2、同时,关于雪荷载的不均匀分布问题在本次雪灾事 故中得到了充分体现,其具体的取值还有待进一步研究。
所有钢材常见缺陷及原因

所有钢材常见缺陷及原因钢材是一种常用的金属材料,广泛应用于建筑、制造等领域。
然而,由于生产过程中的各种因素,钢材可能会出现各种缺陷。
以下是常见的钢材缺陷及其原因:1.气孔:气孔是在钢材中形成的空洞,通常由高温熔化过程中的气体造成。
这可能是由于钢材在熔化和凝固过程中产生的气体没有被完全排出。
2.夹杂物:夹杂物是在钢材中发现的杂质,如氧化物、硫化物、硅酸盐等。
这些杂质会降低钢材的强度和韧性,并可能导致断裂。
3.结晶偏析:在钢材中,存在着不同成分的偏析现象。
这是由于不同元素在熔融过程中的浓度差异所导致的。
结晶偏析可能导致钢材中局部区域的成分不均匀,从而降低材料的性能。
4.热裂纹:热裂纹是在钢材冷却过程中形成的裂纹,通常发生在高温的条件下。
这可能是由于钢材受到过快或不均匀的冷却导致的。
5.焊接缺陷:钢材在焊接过程中可能出现焊接缺陷,如焊缝内的气孔、夹杂物和裂纹。
这可能是由于焊接过程中的温度和应力造成的。
6.疲劳裂纹:疲劳裂纹是由于长期的应力加载和卸载造成的,通常在结构或机械部件中发现。
这可能是由于钢材的低韧性和高应力环境导致的。
7.化学成分偏差:钢材的化学成分对其性能有重要影响。
如果生产过程中的化学成分控制不当,可能会导致钢材的力学性能不稳定。
8.表面缺陷:钢材在加工、运输和存储过程中可能会出现表面缺陷,如划痕、凹痕和腐蚀。
这可能是由于人为因素、机械磨损或化学腐蚀造成的。
9.剥离:剥离是在钢材上发现的一种缺陷,表现为钢材表层的剥离或分离。
这可能是由于材料的粘结性能不足或加工过程中的热应力造成的。
10.形状缺陷:钢材的形状缺陷包括弯曲、弯曲和扭曲等问题。
这可能是由于生产过程中的机械应力和热应力引起的。
以上是常见的钢材缺陷及其原因。
这些缺陷可能会对钢材的性能产生负面影响,并可能导致结构不安全或使用寿命缩短。
因此,在钢材的生产、加工和使用过程中,需要严格控制这些缺陷的发生,并采取有效的措施来预防和修复这些缺陷。
钢材破坏形式

钢材破坏形式钢材是一种非常重要的建筑和制造材料,它广泛应用于工程、建筑、交通运输、航空航天、造船和军工等领域。
但是,由于各种因素的影响,钢材可能会出现破坏。
本文将介绍常见的钢材破坏形式,并探讨其成因、危害和防范措施。
一、钢材的弯曲断裂弯曲断裂是钢材最常见也是最致命的一种破坏形式。
弯曲断裂通常发生在受力过程中,钢材的截面受到弯曲应力而发生断裂。
这种破坏形式常见于桥梁、建筑结构和机械设备等领域。
弯曲断裂的成因多种多样,可能与材料质量、设计参数、生产工艺、使用环境等有关。
例如,材料的锻造、浇铸和淬火等工艺过程中的缺陷或瑕疵,会导致钢材的内部结构不均匀,从而影响了其强度和韧性。
此外,如果设计参数不合理,超过了材料的承载能力,也会导致弯曲断裂的发生。
弯曲断裂的危害非常严重,一旦发生会导致设备的损毁、人员伤亡甚至公共安全事故的发生。
因此,预防弯曲断裂是非常重要的。
一方面,应严格控制制造工艺,确保材料质量符合标准。
另一方面,需要根据实际情况合理设计、选择、使用材料以及制定安全措施。
二、钢材的腐蚀腐蚀是钢材的另一种常见破坏形式。
腐蚀通常发生在湿度、氧气、盐水等环境中,钢材所处的环境越容易使其腐蚀得越快。
腐蚀不仅会降低钢材的强度和韧性,而且还会影响其外观和美观度。
这种破坏形式通常会出现在桥梁、建筑结构和机械设备等领域。
腐蚀的成因与环境因素、材料质量、生产工艺等有关。
例如,如果钢材表面没有喷涂防腐涂料,湿度大、氧气多的环境中容易被氧化腐蚀。
此外,如果材料质量差,内部夹杂物多,也容易引起腐蚀。
为了预防腐蚀,需要采取一系列措施。
首先,应确保材料表面涂有防腐涂料,以防止腐蚀。
其次,如果钢材接触到盐水、酸雨等腐蚀性环境,需要采取合适的防腐方式,如喷涂、电镀等。
最后,应定期检查钢材的表面和内部,及时发现并修补腐蚀造成的损害。
三、钢材的疲劳断裂疲劳断裂是一种特殊的钢材破坏形式,通常发生在反复受力的情况下。
疲劳断裂的成因可追溯于材料内部缺陷,如夹杂物、划痕等。
热镀锌板质量缺陷分析(1)

镀层质量缺陷
为什么厚板入锌锅温度要低一些
厚板因其本身体积大,热含量很高,带钢横断面 上的温度分布不易均匀,其内芯温度一般要高出表面温 度,这种现象称为核心热。带钢存在核心热直接影响到 高温计测温的准确度,因为实际测量温度仅仅是带钢表 面温度,与内芯温度差别较大,造成检测到的温度低, 实际温度高的现象。而且这个核心温度可以一直维持到 带钢出锌锅,铁锌化合物层将继续长大。另外厚板的板 温对锌锅温度影响很大,极易使锌锅温度超出范围。这 些因素导致铁锌化合物层超厚,产生灰色镀层类的缺陷。
美钢联法立式炉
热镀锌简介
感应加热炉
感应加热通过电磁感应的方式直接 对带钢加热,加热速度非常快,生 产效率高,炉区设计短小紧凑,加 热后采用电辐射管保温,炉内气氛 纯净,氢气需求量较小,立式炉的 设计避免带钢在炉内变形,由于采 用直接加热的方式,对带钢的厚度 适应性很强,优势显而易见。
感应加热的整个过程包括三次能量 转换:最初,由交变电源供给的电 能,通过感应线圈回路转变为磁场 能量;然后磁力线切割金属导体, 产生感应电流而将磁场能量转化为 电能;最后电能克服金属内部电阻 又转化为热能,实现对金属的加热。 这就是电,磁,热能的转化过程。
镀层质量缺陷
一般情况下两种作用都有,有时泵吸作用强些,有时振动作用强些。薄板时速 度较快,振动作用强些;厚板时速度较慢,泵吸作用强些。炉鼻灰是有限的, 一片灰或渣被吸走,就会有较长一段时间锌液面是洁净的,直到后继的灰或渣 再次出现。所以这种缺陷是周期性出现,但又没有准确的周期。
镀层质量缺陷
钢带表面落灰
镀实锌—不但保证镀层牢固附着还要保证镀层与钢板之间
槽钢受力分析计算
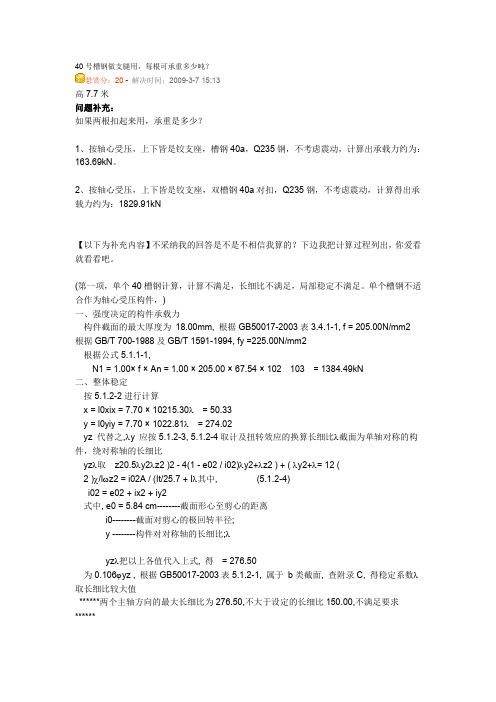
40号槽钢做支腿用,每根可承重多少吨?悬赏分:20 - 解决时间:2009-3-7 15:13高7.7米问题补充:如果两根扣起来用,承重是多少?1、按轴心受压,上下皆是铰支座,槽钢40a,Q235钢,不考虑震动,计算出承载力约为:163.69kN。
2、按轴心受压,上下皆是铰支座,双槽钢40a对扣,Q235钢,不考虑震动,计算得出承载力约为:1829.91kN【以下为补充内容】不采纳我的回答是不是不相信我算的?下边我把计算过程列出,你爱看就看看吧。
(第一项,单个40槽钢计算,计算不满足,长细比不满足,局部稳定不满足。
单个槽钢不适合作为轴心受压构件,)一、强度决定的构件承载力构件截面的最大厚度为18.00mm, 根据GB50017-2003表3.4.1-1, f = 205.00N/mm2根据GB/T 700-1988及GB/T 1591-1994, fy =225.00N/mm2根据公式5.1.1-1,N1 = 1.00× f × An = 1.00 × 205.00 × 67.54 × 102 103 = 1384.49kN二、整体稳定按5.1.2-2进行计算x = l0xix = 7.70 × 10215.30λ= 50.33y = l0yiy = 7.70 × 1022.81λ= 274.02yz 代替之,λy 应按5.1.2-3, 5.1.2-4取计及扭转效应的换算长细比λ截面为单轴对称的构件,绕对称轴的长细比yzλ取z20.5λy2λz2 )2 - 4(1 - e02 / i02)λy2+λz2 ) + ( λy2+λ= 12 (2 )χ/lωz2 = i02A / (It/25.7 + Iλ其中, (5.1.2-4)i02 = e02 + ix2 + iy2式中, e0 = 5.84 cm--------截面形心至剪心的距离i0--------截面对剪心的极回转半径;y --------构件对对称轴的长细比;λyzλ把以上各值代入上式, 得= 276.50为0.106ϕyz , 根据GB50017-2003表5.1.2-1, 属于b类截面, 查附录C, 得稳定系数λ取长细比较大值******两个主轴方向的最大长细比为276.50,不大于设定的长细比150.00,不满足要求******根据规范公式5.1.2-1,A = 1.00 × 205.00 × 0.106 × 75.04 × 102 × 10-3 = 163.69kNϕN2 = 1.00f三、局部稳定翼缘板自由外伸宽度b与其厚度t之比:bt = 89.50 18.00 = 4.97 < )235fy = (10 + 0.1×100.00)×235225.00 = 20.44λ(10+0.1 -------两主轴方向长细比的较大值;λ式中,λ当< λ = 30; 当λ30 时,取> = 100.λ100 时,取根据规范5.4.1-1, 翼缘稳定满足腹板净高h0与其厚度tw之比:h0tw = 364.0010.50 = 34.67 > )235fy = (25 + 0.5×100.00)×235225.00 =76.65λ(25+0.5-------两主轴方向长细比的较大值;λ式中,λ当< λ = 30; 当λ30 时,取> = 100.λ100 时,取根据规范5.4.2-1, 腹板稳定满足**********根据规范5.4.2-1, 腹板稳定不满足!!!**********四、构件承载力N1 > N2, 整体稳定起决定作用, 构件承载力为N2 = 163.69kN(第二项计算,双槽钢40a,可)一、强度决定的构件承载力构件截面的最大厚度为21.00mm, 根据GB50017-2003表3.4.1-1, f = 205.00N/mm2 根据GB/T 700-1988及GB/T 1591-1994, fy =225.00N/mm2根据公式5.1.1-1,N1 = 1.00× f × An = 1.00 × 205.00 × 135.08 × 102 103 = 2769.16kN二、整体稳定按5.1.2-2进行计算x = l0xix = 7.70 × 10215.30λ= 50.33y = l0yiy = 7.70 × 1028.02λ= 96.01双轴对称截面,按5.1.2-2进行计算为0.595ϕy , 根据GB50017-2003表5.1.2-1, 属于b类截面, 查附录C, 得稳定系数λ取长细比较大值两个主轴方向的最大长细比为96.01,不大于设定的长细比150.00根据规范公式5.1.2-1,A = 1.00 × 205.00 × 0.595 × 150.09 × 102 × 10-3 = 1829.91kNϕN2 = 1.00f三、构件承载力N1 > N2, 整体稳定起决定作用, 构件承载力为 N2 = 1829.91kN。
- 1、下载文档前请自行甄别文档内容的完整性,平台不提供额外的编辑、内容补充、找答案等附加服务。
- 2、"仅部分预览"的文档,不可在线预览部分如存在完整性等问题,可反馈申请退款(可完整预览的文档不适用该条件!)。
- 3、如文档侵犯您的权益,请联系客服反馈,我们会尽快为您处理(人工客服工作时间:9:00-18:30)。
烂钢分析
烂钢主要体现在11月两个时间段,14日~15日,一高线共计出现12次影响328分钟,高棒3次共计影响336分钟;22~24日共计产生烂钢5.5支,高棒烂钢表现为开裂,高线烂钢表现为出粗轧后表面有孔洞,具体情况如下:
一、14日~15日烂钢
1、烂钢炉次过程控制情况
高线普碳钢烂钢情况:
从上表看出:
⑴、本次出现烂钢的炉次多体现在铁水S不稳定,导致一倒S高或成品S 偏高。
⑵、近期铁水成分波动大,高S铁水多,并且频繁出现一倒S高于铁水S 或高S铁水加锰铁也达不到脱S效果的情况,造成较多S出格炉次,严重影响了炼钢的操作。
从连铸坯样分析结果看,出现烂钢回炉的铸坯S偏析较大,是造成裂纹的主要原因。
另外对近期抽材样分析结果进行统计,S元素偏差在0~0.026%之间,平均偏差在0.008%,超过0.010%的有66炉,占总数的31%,S 元素偏析严重。
⑶、出现烂钢的主要是Mn0.55%的HRB400和HPB300,因为成分设计Mn 较低,当S偏高时Mn/S偏低,无法达到工艺要求的15,S元素在连铸坯凝固过程中出现偏析,同时易造成裂纹。
(注:HPB300实际成份落在包晶钢范围内,天生的裂纹倾向较重)
⑷、从烂钢和退废铸坯来看,造成烂钢的主要原因是铸坯内部质量较差,内部裂纹严重。
通过对连铸生产过程的工艺数据与电脑曲线的反查,连铸的生产工艺过程控制正常,未发现有工艺违规现象,测矫前温度在960~980℃。
15日7点左右,连铸结晶器水流量由90 t/h调整到85t/h,通过提高矫前温度来减小产生裂纹的机率。
⑸、部分炉次由于倒炉S高点吹时间延长,出钢温度升高,高温加剧了裂纹的产生。
从上表看出,近两天也体现S出格炉次较多,主要原因:一是由于铁水S 高,在调整热平衡和加入锰铁的情况下,倒炉S高导致出格;二是铁水S正常由于铁水渣多或受高炉上炉铁水影响导致倒炉S高出格。
3、裂纹判废情况
由于产生烂钢,回炉坯经检查后有裂纹的退废77支;出坯时发现有裂纹落地的铸坯坯判废30支(取样S0.053~0.055%)。
1、转炉冶炼情况
从转炉冶炼情况看,A111414358炉次铁水S高,一倒S0.074%,成品S0.041%。
2、连铸控制情况
包温度偏高,A111414434炉次拉速偏高。
3、异常情况分析性
⑴、A321414662为中间包第一炉,出烂钢为本炉头坯,头坯在套管前有轻微脱方。
⑵、A111414358炉次铁水S高,一倒S0.074%,点吹时间长,中间包温度1549℃偏高。
⑶、A211414076炉次前一炉成品S0.055%判废,铸坯有轻微裂纹落地待处理,经检查后送轧。
三、结论
1、14~15日连续性出现烂钢主要是由于S高铸坯产生裂纹,炼钢在铁水S 波动时应对不及时,铸坯质量没有得到有效控制,导致不合格铸坯流入轧制后出
现烂钢。
2、22~24日烂钢
高线烂钢:A321414662炉次为中间包第一炉头坯在套管前有轻微脱方造成;A321414634、A121414391炉次转炉控制正常,主要是二冷冷却不均匀造成裂纹在轧制后出现孔洞。
高棒烂钢:A111414358、A211414076炉次是由于S高产生裂纹导致烂钢;A111414434炉次为拉速提较高,冷却没有及时跟上,特别是I流拉速2.14m/min 比水量在工艺要求下限,导致铸坯出现裂纹。
四、改进措施
1、针对近期偶尔铁水S高的情况,炉前适当调高热平衡,铁水S高炉次加
入锰铁并增加一定量的石灰,通过高碱度、高温达到去S的目的。
2、冶炼普碳和HRB400-a时,尽量挑选低S铁水使用,如果倒炉S高则把
Mn适当配高增加Mn/S比(建议参照一钢,按Mn%≮0.58控制、锰低炉次应喂
入硅钙线85米以上并延长吹氩时间)。
S高时加强信息传递,转炉、连铸及时进行调整。
(要处理好质量与成本的关系,建议:1. HPB300钢C%≥0.20,尽量避开包晶钢区域,缓解天生的裂纹倾向;2. 延长吹氩时间4分钟/炉;3. 硫高的炉次应喂入硅钙线。
)
3、控制好出钢温度和吹气后温度,降低浇注过热度,制定相应的考核制度,
减少高温拉坯。
4、连铸定期测量进拉矫前温度,连铸结晶器水由90t/h调整到85t/h、HPB300
钢种比水量控制在1.30L/Kg左右,HRB400钢种二冷水比水量控制在1.25L/Kg 左右。
(建议:1.浇注上述钢种时,结晶器铜管寿命须≤200炉;2.关注结晶器装配过程水缝达标率;3.严格要求中间包液面稳定、结晶器内浸入式水口对中、结晶器液面稳定和保护渣“黑面”操作;4.近期产量高,拉速时常达2.1~2.2米/分钟,钢水过热度一定要控制低一些;5.裂纹产生于结晶器内,过大的足辊水量使得裂纹快速发展,应考虑优化)
5、连铸高度重视整机工作,有一小时停机时间必须由机长开会布置整机工
作,两小时以上必须由车间副主任开会布置整机工作,技术科对连铸工况进行评
价。